Горизонтально- фрезерная операция. Фрезерная операция
Фрезерная операция - Большая Энциклопедия Нефти и Газа, статья, страница 1
Фрезерная операция
Cтраница 1
Фрезерная операция состоит из одного или нескольких переходов. Типовые схемы простейших переходов, выполняемых концевыми фрезами, изображена на рис. 5.7, где а - фрезерование криволинейных контуросложных поверхностей; б - фрезерование плоскостей; в - фрезерование уступа; г - фрезерование паза; t - глубина резания; В - ширина фрезерования. Если произведение глубины фрезерования на ширину фрезерования превышает допустимое значение для технологической системы СПИД, то один и тот же элемент поверхности обрабатывают за несколько рабочих ходов. Экономически целесообразно обрабатывать поверхности детали за один рабочий ход. [1]
Фрезерные операции торцов и плоскостей у деталей из технологических рядов ВС-01, ВШ-01, ТР-01, КР-01 и др. осуществляются по-разному: на горизонтально-фрезерных, вертикально-фрезерных, барабанно-фрезерных и специальных станках с построением операций фрезерования по различным схемам. [2]
При выполнении фрезерных операций наибольшее распространение получили тиски, которые могут быть механические, пневматические и гидравлические. [4]
После окончания фрезерных операций шлицевые валы подвергаются термической обработке. [5]
Все многообразие фрезерных операций по обработке плоскостей на станках обшего назначения может быть производительно выполнено указанными выше типоразмерами торцовых фрез. [6]
Объем рационализации фрезерных операций в серийном производстве по степени важности решения задачи представляется в следующем виде. [7]
Все многообразие фрезерных операций по обработке плоскостей на станках общего назначения может быть производительно выполнено указанными выше типоразмерами торцовых фрез. [9]
Для выполнения тяжелых фрезерных операций, чернового и чистового растачивания, подрезки больших торцов требуются головки более жесткой конструкции, с большим расстоянием между опорами шпинделей в шпиндельных коробках ( или бабках) и небольшим их вылетом относительно направляющих. Рассмотренные силовые головки не отвечают этим требованиям. Поэтому возникла необходимость механизм главного движения отделить от механизма подачи и выполнить силовую головку в виде двух независимых узлов: силового стола и силовой бабки. [11]
При выполнении сверлильных и фрезерных операций возникает опасность захвата сверлом или фрезой и ранения рук. Работать в рукавицах или перчатках, а также с забинтованными пальцами рук недопустимо ввиду опасности захвата режущим инструментом. [12]
Для выполнения сверлильных, расточных, резьбонарезных и фрезерных операций при обработке корпусных деталей значительных размеров, а также различных литых и штампованных деталей более или менее сложной конфигурации и небольших размеров наиболее целесообразно использовать линии из агрегатных станков со сквозным транспортером. [13]
Применяется на фрезерных операциях, когда по условиям обработки допускается смена заготовок за счет машинного времени. Для этого на концах стола устанавливаются приспособления. При повороте рукоятки рычаг перемещается вправо и с помощью шпенька 5 заводит фиксатор б в гнездо. При этом цапфа 9 опускается и прижимает стол в центральной части, а кулачки передвигают ползуны 10 и при помощи сухарей 11 окончательно закрепляют его. Пружины 12 служат для подъема стола при повороте. [14]
Применяют на фрезерных операциях, когда по условиям обработки допускается смена заготовок за счет машинного времени. Для этого на концах стола устанавливают приспособления. Пружины 12 служат для подъема стола при повороте. [15]
Страницы: 1 2 3 4
www.ngpedia.ru
Фрезерование. Основные виды и методы данной обработки металла
Привет! Вот и новая статья которая называется фрезерование и его основные виды потому, что с нее мы начнем изучение этого не простого метода обработки металла.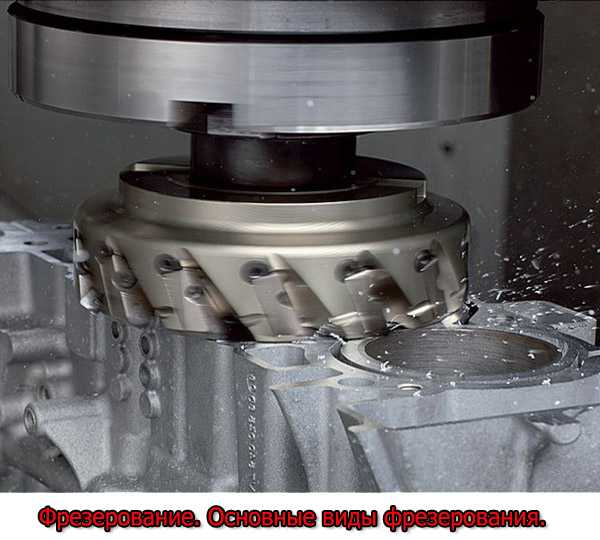
Что такое фрезерование?
Фрезерование — это обработка создающая плоские и фасонные поверхности , путем применения такого режущего инструмента как фреза. Можно много сказать еще про этот вид механической обработки но я думаю, что мы с вами поэтапно будем рассматривать все его составляющие. И когда закончим (что очень не скоро:)) вы будете знать про него практически все.
Фрезерование.Основные виды и методы.
Я не хочу грузить вас теорией и скучными определениями которых и так полно во всякой литературе посвященной резанию металлов. Просто хочу пока рассказать про основные виды фрезерования. И так…
Фрезерование цилиндрической фрезой. Ну как уже понятно из названия для данного метода применяется цилиндрическая фреза. Суть метода заключается в обработке плоских поверхностей правильной формы (квадраты,прямоугольники и др.) Углубляться не будем, пока:).
Фрезерование торцевой фрезой. Этот метод в принципе аналогичен предыдущему но разница в том, что тут для получения таких же поверхностей применяется торцевая фреза. В чем их различие разберемся в следующих постах. Так, что не забываем подписываться на обновления блога.
Фрезерование зубчатого колеса. Что качается изготовления зубчатого венца методом фрезерования на горизонтально-фрезерном станке, то скажу вам сразу, что данный метод давно устарел и применяется разве, что в ремонтных цехах так как он не имеет необходимой производительности и качества получения шестерни. К стати получение зубчатых колес мы тоже будем рассматривать:)
Фрезерование уступа дисковой трехсторонней фрезой. Как уже понятно с названия снятие припуска производится трехсторонней дисковой фрезой. Которая называется так потому, что имеет сразу три режущие кромки — по наружному диаметру и сразу с двух торцев. Это позволяет ей фрезеровать уступы как показано на рисунке.
Фрезерование набором двух трехсторонних дисковых фрез. Этот метод похож на предыдущий но разница в том, что в данном случае производится одновременная обработка двумя фрезами, что очень удобно для изготовления лысок на цилиндрических поверхностях.
Фрезерование паза концевой фрезой. Используется данный вид для получения прямобочных пазов различных размеров и конфигураций как на плоских так и цилиндрических деталях.
Фрезерование пазов шлицевой фрезой. Ну тут скажу, что под шлицевыми пазами подразумеваются шлицы. Данный методом тоже устарел так как является низко производительным и не дает достаточной точности получения детали. Деление осуществляется с помощью делительной головки.
Фрезерование фасонной поверхности. Под фасонными поверхностями как вы уже поняли из моего предыдущего поста про токарную обработку. Это поверхности которые имеют не совсем правильные «фасонные» формы (эллипсы, сферы и др.). И как следствие для их получения необходимы специальные фрезы которые и называют фасонные (имеющие форму которую необходимо получить после фрезеровки).
Фрезеровка наклонной плоскости. Угловые фрезы тоже работаю по принципу копирования, а именно получаемая наклонная поверхность обеспечивается точностью изготовления режущего инструмента. Этот метод применяется для изготовления направляющих скольжения металлорежущих станков.
Фрезеровка криволинейного контура. С помощью концевой фрезы мы сможем получить практически любой сложный криволинейный контур. Тут фреза описывает обрабатываемую деталь по кривой линии которую нам необходимо получить.
Фрезеровка винтовых канавок. С помощью данного способа фрезерования как видно из предлагаемого эскиза изготавливают сверла, зенкера и другой инструмент имеющий винтовые стружкоотводящие канавки. В основном эти операции выполняются на станках с ЧПУ (в настоящее время).
Разрезание отрезной фрезой. Ну в данном случае название говорит само за себя. С помощью отрезной фрезы можно нарезать металлические бруски различных размеров.
Ну все на сегодня информации пожалуй хватит. Я думаю, что не плохо расписал про фрезерование и его основные виды. Если у вас есть какие то предложения чем можно дополнить данный пост ПИШИТЕ!!!
С вами был Андрей!
mextexnologii.ru
РГР ЭУП вал
Материалы и заготовки валов
Валы, в основном, изготовляют из конструкционных и легированных сталей, к которым предъявляются требования высокой прочности, хорошей обрабатываемости, малой чувствительности к концентрации напряжений, а также повышенной износостойкости. Этим требованиям, в определенной степени, отвечают стали марок 35, 40, 45, 40Г, 40ХН и др. В технических требованиях на изготовление валов, прежде всего, указывается твердость материала или необходимость соответствующей термической обработки. Если значение твердости не превышает НВ 200...230, то заготовки подвергают нормализации, отжигу или термически не обрабатывают. Для увеличения износостойкости валов повышают твердость их рабочих поверхностей. Часто это достигается поверхностной закалкой токами высокой частоты, обеспечивающей твердость HRС 48...55. Поверхности валов из малоуглеродистых марок стали подвергают цементации на глубину 0,7...1,5 мм с последующей закалкой и отпуском. Таким способом можно достичь твердости НRС 55...60.
Производительность механической обработки валов во многом зависит от вида материала, размеров и конфигурации заготовки, а также от характера производства.
Для изготовления данного ступенчатого вала мною выбрано единичное производство. Заготовка для вала будет получена путем отрезания от горячекатаных или холоднотянутых нормальных прутков, которые сразу же будут подвергнуты механической обработке.
Прокат будет поступать на завод в виде многометровых прутков, из которых в заготовительных цехах будут нарезаться заготовки необходимой длины. Для этого будут применяться отрезные ножовочные станки.
На машиностроительные заводы прокат поступает с заметными отклонениями от прямолинейности оси. Для устранения кривизны прутки перед резкой будут подвергать правке. Для этой цели служат правильно-калибровочные станки. Нарезанные заготовки перед началом обработки, а иногда и в процессе дальнейшей обработки также будет приходиться подвергать правке. Такую правку будут проводить на прессах.
Технологический процесс изготовления ступенчатого вала
Разработка технологического процесса изготовления вала начинается с детального изучения его служебного назначения в машине и технически условий, которым он должен удовлетворять. Для этого изучают сборочные чертежи машины или той сборочной единицы, в которую в качестве одного из взаимосвязанных звеньев входит обрабатываемый вал, технические требования, нормы точности и требования технологии сборки. Это позволяет установить взаимосвязь между поверхностями вала, которые должны быть обработаны.
Исходя из этого, технологический процесс изготовления заданного вала будет включать в себя следующие операции:
005 Заготовительная операция
010 Фрезерно-центровальная операция
015 Токарно-черновая операция
020 Токарно-черновая операция
025 Шпоночно-фрезерная операция
030 Шпоночно-фрезерная операция
035 Круглошлифовальная операция
040 Круглошлифовальная операция
045 Круглошлифовальная операция
Рассмотрим основные операции механической обработки для изготовления заданного вала.
005 Заготовительная операция
1. Отрезать от прутка 32 заготовку длиной L=230 по технологии машиностроительного цеха.
2. На торце заготовки маркировать марку материала и номер детали по эскизу.
010 Фрезерно-центровальная операция
1. Установить, закрепить, снять деталь.
3. Зацентровать деталь с двух сторон. Центровочное сверло ГОСТ 14952-75.
015 Токарно-черновая операция
020 Токарно-черновая операция
Выполняется за два установа на одной операции или каждый установ выносится как отдельная операция. Производится точение наружных поверхностей, (с припуском под чистовое точение и шлифование) и канавок канавочным резцом ГОСТ 18884-73. Это обеспечивает получение точности IТ12, шероховатости Ra = 6,3. В единичном производстве эту операцию выполняют на токарно-винторезных станках;
1. Установить, закрепить, снять деталь.
2. Точить поверхности и фаски. Проходной упорный резец ГОСТ 18879-73.
3. Наружные резьбы нарезают в единичном производстве на токарно-винторезных станках плашками, резьбовыми резцами или гребенками, резец резьбовой ГОСТ 18885-73.
Далее производится чистовое точение шеек (с припуском под шлифование). Обеспечивается точность IТ11...10, шероховатость Rа = 3,2.
1. Установить, закрепить, снять деталь.
2. Проточить поверхности. Проходной упорный резец ГОСТ 18879-73.
3. Чистовое точение канавок канавочным резцом.
025 Шпоночно-фрезерная операция
030 Шпоночно-фрезерная операция
1. Установить, закрепить, снять деталь.
2. Фрезеровать шестигранник. Шпоночная фреза ГОСТ 9140-78
035 Круглошлифовальная операция
040 Круглошлифовальная операция
045 Круглошлифовальная операция
Шейки вала шлифуют на круглошлифовальных или бесцентрово-шлифовальных станках соответственно шестому квалитету.
Шлицы шлифуются в зависимости от центрирования:
- по наружной поверхности – наружное шлифование на круглошлифовальных станках и шлифование боковых поверхностей на шлицешлифовальном полуавтомате одновременно двумя кругами с делением;
- по поверхности внутреннего диаметра – шлифование боковых поверхностей шлицев и шлифование внутренних поверхностей по диаметру, либо профильным кругом одновременно, либо в две операции.
1. Установить, закрепить, снять деталь.
2. Шлифовать поверхность абразивным кругом.
studfiles.net
Горизонтально- фрезерная операция
⇐ ПредыдущаяСтр 2 из 3Следующая ⇒Для выполнения данной операции выбран универсальный консольно-фрезерный станок модели 6Р82Г. Станок выбран, исходя из того, что он предназначен для выполнения разнообразных фрезерных работ.
Технические характеристики станка модели 6Р82Г: [12, с.45]
- размеры рабочей поверхности стола, мм: ширина 320 , длина 1250
- наибольшее перемещение стола, мм:
продольное 800
поперечные: механическое 240
от руки 250
вертикальное:
механическое 360
от руки 380
- наибольший угол поворота стола +450; -450
- число частот вращения шпинделя 18
- частота вращения , мин-1 31,5-1600
- число подач стола 18 - подача , мм/мин : продольная 25-1250
Поперечная25-1250 вертикальное 8,3-416,6
Для закрепления и базирования детали выбрано следующее приспособление -Специальное. Данное приспособление обеспечивает надежность закрепления и точность обработки.
Для обработки поверхностей 15, 16, 17, 18 выбран режущий инструмент- Фреза 2241-0153 ГОСТ 1669-78 [12, с. 282].
Для измерения обработанных поверхностей выбран следующий мерительный инструмент – Штангенциркуль ШЦ1-125- 0,1 ГОСТ 166- 89 [4].
Режущий инструмент выбран по характеру обработки, по размерам обработки. Мерительный инструмент выбран исходя из диапазона показаний.
Для установки фрезы выбран следующий вспомогательный инструмент- Оправка 6225-0177 ГОСТ 15068-75 [12, с. 360] ; Кольцо 6030-0729 МН 33-64 ; Кольцо 6030-0725 МН 33-64 ; Кольцо 6030-0058 МН 34-64 ; Кольцо 6030-0729 МН 33-64 ; Кольцо 6030-0727 МН 33-64 ; Кольцо 6030-0057 МН 33-64 [3].
2.3.4 Определение операционных припусков и межоперационных размеров
Таблица 7
в миллиметрах
Последовательность обработки | Припуск | Допускаемые отклонения | Шероховатость | Размер после обработки |
1 | 2 | 3 | 4 | 5 |
Æ100h9 заготовка черновое точение чистовое точение тонкое точение | 2,4x2=4,8 2,2х2=4,4 0,125х2=0,25 0,075х2=0,15 | h24 h22 h9 | Æ104,8 Æ100,4 Æ100,15 Æ100 | |
Æ90,8 h9 заготовка черновое точение чистовое точение | 9,35 4,55х2=9,1 0,125х2=0,25 | h24 h9 | Æ100,15 Æ91,25 Æ90,8 | |
14 заготовка черновое точение чистовое точение тонкое точение | 1,7 1,3 0,3 0,1 | h24 h24 h24 | 12,3 13,6 13,9 14 |
2.3.5 Определение режимов резания и норм времени
Вертикально-сверлильная операция 015.На станке 2С132 выполняется сверление четырех отверстий. Обрабатываемый материал - СЧ 15 с твердостью 190НВ [1, с.22].
Расчетно-аналитический метод.
1 Установить и снять деталь
2 Сверлить отверстие 5
3 Повернуть деталь
4 Сверлить отверстие 5
5 Повернуть деталь
6 Сверлить отверстие 5
7 Повернуть деталь
8 Сверлить отверстие 5
9 Проверить размеры…
Рисунок 3 - Эскиз детали на операцию 015
Определяем глубину резания t, мм: t=0,5 . D , (12)
где D - диаметр сверления, мм. t=0,5 . 13=6,5мм
Подача на оборот Sо=0,35-0,41 мм/об [7, с.277]
Корректируем подачу по паспорту станка и принимаем Sо=0,4 мм/об [11, с.422]
Скорость резания, допускаемая режущими свойствами инструмента Vрез,
м/мин, определяется по формуле:
Vрез=Сv Dq Kv / Тm Soy , (13)
где Сv, q, m, y- коэффициент и показатели степени
Сv =17,1; q =0,25; m =0,125; y =0,40 [7, с. 278];
D - диаметр сверления, мм;
Т - стойкость инструмента , Т= 60 мин [7, с. 280];
So – подача на оборот, мм/об;
Kv – поправочный коэффициент.
Kv =Кмv Киv Кlv, (14)
Кмv – коэффициент на обрабатываемый материал;
Киv – коэффициент на инструментальный материал, Киv =1 [7, с. 263];
Кlv - коэффициент, учитывающий глубину сверления, Кlv =1[7, с. 280].
Коэффициент Кмv определяется по формуле:
Кмv = (190/HB)nv, (15)
где HB - фактические параметры обрабатываемого материала, HB = 190 кгс/см2;
nv - показатель степени, nv = 1,3 [7, с. 262].
Кмv =(190/190)1,3 = 1
Тогда по формуле (14)
Кv = 1 1 1 = 1
Тогда по формуле (13)
Vрез = 17,1 130,25 1/600,125 0,40,4 = 28,1 м/мин
Частота вращения шпинделя n, об/ мин, определяется по формуле:
n = 1000 Vрез/ π D, (16)
где обозначения прежние.
n = 1000 28,1/ 3,14 13 = 639,48 об/мин
Корректируем частоту вращения шпинделя по паспорту станка nд = 500 об/мин.
Действительная скорость резания Vд , м/мин, определяется по формуле:
Vд = π D nд/ 1000, (17)
где обозначения прежние.
Vд = 3,14 13 500/ 1000 = 20,4 м/мин
Крутящий момент Мкр, Н м ,определяется по формуле:
Мкр = 10 См Dq Soy Kp, (18)
где См, q, y - коэффициент и показатели степени См = 0,021; q = 2; y = 0,8 [7, с. 281]
Кр - поправочный коэффициент;
остальные обозначения прежние.
Коэффициент Кр определяется по формуле:
Кр = Кмр, (19)
Кмр = (HB /190) n, (20)
где n – показатель степени, n = 0,6 [7, с. 264]
Кмр = (190/190)0,6 = 1
Тогда по формуле (18)
Мкр =10 0,021 132 0,40,8 1 = 17,04 Н м
Мощность резания Nрез, кВт, определяется по формуле:
Nрез = Мкр nд/ 9750, (21)
где обозначения прежние.
Nрез =17,04 500/ 9750 = 0,87 кВт
Мощность резания меньше мощности шпинделя станка
(Nшп = Nд ŋ = 4,5 0,8 = 3,6 кВт),
следовательно обработка возможно.
Основное время tо, мин, определяется по формуле:
tо= (22)
где L - общая длина перемещения инструмента, мм.
L= , (23)
где l – глубина сверления, мм; l = 20 мм;
l1 - врезание инструмента, мм; l1 = 5,2 мм [12, с.620];
l2 - перебег инструмента, мм; l2=2 мм [12, с.620].
L = 20+5,2+2 =27,2 мм
Тогда по формуле (22):
to = мин
to =0,136 4 = 0,544 мин
Вспомогательное время tв, мин, определяется по формуле:
tв=(tуст.+tпер.+t¢пер.+tизм.×Кпер.)×Кв, (24)
где tуст.=0,12 мин - время на установку детали на горизонтальную плоскость в призму [14, с.54]; в специальных приспособлениях
tзакр.=0,04 мин - время на закрепление пневматическим зажимом [14, с.58];
tпер.=0,08 4= 0,32 мин- время на проход при сверление по кондуктору [14, с.95];
t¢пер.=0,02 мин - время на включение и выключение вращения шпинделя кнопкой;
t¢пер.=0,05 мин - время на установку и снятие инструмента в быстросменном патроне без выключения вращения шпинделя;
t¢пер.=0,07 мин - время на постановку и снятие кондукторной втулки;
t¢пер.=0,015 4= 0,06 мин - время на поворот приспособления [14, с.95].
t¢пер.= 0,02+0,05+0,07+0,06 = 0,2 мин
tизм=0,06 мин – время на измерение калибром-пробкой [14, с. 188]
Кпер.=0,02 [14, с.201].
Тогда:
tв=0,16+0,32+0,06+0,06 0,02 = 0,66 мин
Число смен определяется по формуле:
число смен= , (25)
где tо - общее основное время на операцию, мин;
tв - вспомогательное время на операцию, мин;
n - количество заготовок, шт; n=922 шт.
число смен=
Кв=0,87 - поправочный коэффициент на вспомогательное время в зависимости от характера серийности работ.
По формуле (24):
tв=0,66×0,87=0,57 мин
Оперативное время tоп, мин, определяется по формуле:
tоп=tо+tв, (26)
tоп=0,544+0,57=1,14 мин
Время на обслуживание рабочего места tобс., мин, определяется по формуле:
tобс.= , (27)
где а1 - процент на обслуживание рабочего места; а1=4% [14, с.100].
tобс.= мин
Время на отдых и личные надобности tотл., мин, определяется по формуле:
tотл.= , (28)
где а2 - процент на отдых и личные надобности; а2=4%
tотл.= мин
Штучное время tшт, мин, определяется по формуле:
tшт=tо+tв+tобс.+tотл., (29)
tшт=0,544+0,57+0,045+0,045=1,204 мин
Подготовительно-заключительное время Тпз., мин, определяется по формуле:
Тпз.=Тпз1+Тпз2+Тпз3, (30)
где Тпз1=13 мин - время на установку кондуктора [14, с.101];
Тпз2= 0 мин - время на дополнительные приемы [14, с.101];
Тпз3=7 мин - время на получение инструмента и приспособления до начала и сдачу их после окончания обработки [14, с.101].
Тпз=13+0+7=20 мин
![]() |
Штучно-калькуляционное время tшт-к, мин, определяется по формуле:
tшт-к=tшт+ , (31)
где n - количество деталей в партии, шт; n=922 шт.
tшт-к=1,204+ мин
Горизонтально-фрезерная операция 025.На станке 6Р82Г выполняется фрезерование четырех лысок 15, 16,17,18. Обрабатываемый материал - СЧ 15 с твердостью 190НВ [1, с.22].
Табличный метод.
1 Установить и снять деталь
2 Фрезеровать лыски 16 и 18
3 Повернуть деталь
4 Фрезеровать лыски 15 и 17
5 Проверить…
Рисунок 4 - Эскиз детали на операцию 025
Определяем подачу на зуб, Sz = 0,25 – 0,4 мм/зуб [18, с.309].
Принимаем Sz =0,3 мм/зуб
Определяем скорость резания, V = 31 м/мин [18, с.315].
Определяем частоту вращения, n = 110 об/мин [18, с.315].
Определяем минутную подачу, Sм = 370 мм/мин [18, с. 315].
Определяем глубину резания ,t = 13,5 мм.
Определяем мощность резания, Nрез = 2,5 кВт [18, с.317].
Основное время tо, мин, определяется по формуле:
tо= (32)
где L - общая длина перемещения инструмента, мм.
L= , (33)
где l - длина фрезерования, мм; l = 120 мм;
l1 - врезание инструмента, мм; l1 = 30 мм [12, с.620];
l2 - перебег инструмента, мм; l2=3 мм [12, с.620].
L = 125+3+33 =161 мм
Тогда по формуле (32):
to = мин
to =0,44 2 = 0,88 мин
Вспомогательное время tв, мин, определяется по формуле:
tв=(tуст.+tпер.+t¢пер.+tизм.×Кпер.)×Кв, (34)
где tуст.=0,11 мин - время на установку детали на горизонтальную плоскость в призму [14, с.54];
tпер.=0,18 мин - время на установку фрезы на размер [14, с.108];
t¢пер.=0,04 мин - время на поворот приспособления [14, с.109]
tизм=0,32 мин – время на измерение штангенциркулем[14, с. 185].
Кпер.=0,4 [14, с.200].
Тогда
tв=0,11+0,18+0,04+0,32 0,4= 0,458 мин
Число смен определяется по формуле:
число смен= , (35)
где tо - общее основное время на операцию, мин;
tв - вспомогательное время на операцию, мин;
n - количество заготовок, шт; n=922 шт.
число смен=
Кв=0,87 - поправочный коэффициент на вспомогательное время в зависимости от характера серийности работ.
По формуле (34):
tв=0,458 0,87=0,398 мин
Оперативное время tоп, мин, определяется по формуле:
tоп=tо+tв, (36)
tоп=0,88+0,398=1,278 мин
Время на обслуживание рабочего места tобс., мин, определяется по формуле:
tобс.= , (37)
где а1 - процент на обслуживание рабочего места; а1=3,5% [14, с.108].
tобс.= мин
Время на отдых и личные надобности tотл., мин, определяется по формуле:
tотл.= , (38)
где а2 - процент на отдых и личные надобности; а2=4%
tотл.= мин
Штучное время tшт, мин, определяется по формуле:
tшт=tо+tв+tобс.+tотл., (39)
tшт=0,88+0,398+0,045+0,051=1,374 мин
Подготовительно-заключительное время Тпз., мин, определяется по формуле:
Тпз.=Тпз1+Тпз2+Тпз3, (40)
где Тпз1=23 мин - время на установку специального приспособления краном[14, с.111];
Тпз2= 0 мин - время на дополнительные приемы [14, с.111];
Тпз3=7 мин - время на получение инструмента и приспособления до начала и сдачу их после окончания обработки [14, с.111].
Тпз=23+0+7=30 мин
Штучно-калькуляционное время tшт-к, мин, определяется по формуле:
tшт-к=tшт+ , (41)
где n - количество деталей в партии, шт; n=922 шт.
tшт-к=1,374+ мин
2.4 Сравнительная характеристика проектного и базового вариантов
Читайте также:
lektsia.com
5.7.2 Фрезерная операция
025 - фрезерная
1) Заготовка - .
2) Выполняемые переходы:
3) Приспособление.
Деталь базируется в цилиндрической оправке
4) Оборудование.
В качестве оборудования выбран горизонтально-фрезерный станок 6Р82Г
5) Выбор числа ходов.
Операции фрезерования выполняем за один ход, т.е. .
6) Выбор материала режущей части инструмента.
Согласно табл. 14 стр. 57 [1] для фрезерования чугуна рекомендуется твердый сплав ВК6
7) Выбор конструкции и геометрии инструмента.
Согласно табл. 17 стр. 225 [1] и стр. 174 [2] выбираем конструкцию и геометрию дисковой фрезы с числом зубьев ,D=160, B=25мм
8) Выбор СОЖ.
Согласно табл. 24 стр. 233 [1] при фрезеровании чугуна рекомендуется 5-10% раствор Аквол-10М.
9) Назначение глубины фрезерования t.
Дисковая фреза работает с глубиной резания t=2 мм.
Значения глубины резания заносим в сводную табл. 8.1.3.
10) Назначение подачи S.
Для дисковой фрезы согласно табл. 113стр. 305 [1] для сталей 8 группы и :
.
11) Выбор стойкости фрезы Т.
Рекомендуемые значения допустимого износа hз и стойкости Т фрезы выбираем из табл. 22 стр. 231 [1] и заносим в соответствующие графы табл. 3.1.3
12. Назначение скорости резания V.
.
13. Расчёт частот вращения инструмента n.
При фрезерной обработке:
, .
где DФ - диаметр фрезы, мм.
Расчетное значение n должно быть скорректировано по nст:
, .
Рассчитаем фактическую скорость резания:
,
.
Выбранные значения ncт и V заносим в табл. 3.1.3.
14) Расчёт основного времени 0.
Согласно с.613 [3] основное время для различных видов фрезерования определяется выражением:
.
Значения величин врезания L1 и перебега L2 приведены в табл. 6 стр. 622 [3].
В нашем случае согласно табл. 3.4 получаем:
На фрезерование одного паза
На всю деталь .
Значение 0 заносим в табл. 8.1.3.
15. Расчёт силы резания Рz.
Согласно стр. 282 [2]:
.
Выбирая значения постоянных и показателей степеней для различных видов фрезерования из табл.41 стр.291 [2] и выполняя вычисления, получим:
, .
16) Расчёт крутящего момента Мк.
Согласно стр. 270 [2]:
, .
17) Расчёт мощности резания.
.
Полученные значения Рz, МK и Ne заносятся в соответствующие графы табл. 3.1.3.
Таблица 5.1.3. Основные параметры фрезерной операции.
№ ин-та | Параметры | ||||||||||||||||||||||
D | zu | L | t | B | Sz | hз | Т | n | V | τ0 | Pz | Мк | Nе | ||||||||||
мм | - | мм | мм | мин | мин | кг | кг∙м | кВт | |||||||||||||||
1 | 2 | 3 | 4 | 5 | 6 | 7 | 8 | 9 | 10 | 11 | 12 | 13 | 14 | ||||||||||
1 | 160 | 12 | 12 | 2 | 25 | 0,1 | 0,4 | 202 | 200 | 100,5 | 0,9 | 22,9 | 18,3 | 7,46 |
5.7.3 Сверлильная операция
030 - сверлильная
1) Заготовка - .
2) Выполняемые переходы:
сверлить 6 отверстий диаметром 14 мм Н13 и ;
сверлить 4 отверстия диаметр 6 мм Н14 и ;
3) Приспособление.
4) Оборудование.
В качестве оборудования выбран вертикально-сверлильный одношпиндельный станок 2Н125.
5) Выбор числа ходов z при сверлении отверстия.
Согласно табл. 62 стр. 265 [1] отверстия диаметром 6 мм и 14мм в чугунной детали просверливаются за один ход, т.е. .
6) Выбор длины участков L сверления между выводами свёрл.
Согласно табл. 63 стр. 265 [1] в сплошном материале 8 группы сверлом диаметром 7,8 мм можно сверлить отверстие на длину без его вывода для удаления стружки. Поскольку заданная длина сверления 52 > 31,2, то обработка выполняется в два этапа по 26 мм с выводом сверла.
Согласно табл. 63 стр. 265 [1] в сплошном материале 8 группы сверлом диаметром 2 мм можно сверлить отверстие на длину без его вывода для удаления стружки. Поскольку заданная длина сверления 14,2 > 10, то обработка выполняется в два этапа по 7,1 мм с выводом сверла.
7) Выбор инструментального материала.
Согласно табл. 5 стр. 42 [1] для обработки материалов 8 группы сверлением рекомендуется быстрорежущая сталь Р6М5
8) Выбор конструкции и геометрии осевого инструмента.
Согласно стр. 103 [1] выбираем стандартную конструкцию и геометрию осевых инструментов.
9) Выбор СОЖ.
Детали из серого чугуна обрабатываются без СОЖ, т.к. чугунная стружка вредно влияет на износ станков
10) Назначение глубины резания t.
Согласно операционным размерам и параметрам заготовки определяем глубину резания, результаты заносим в сводную табл. 3.3.1.
Таблица 5.3.1. Основные параметры операции осевой обработки.
№ перехода | Параметры | ||||||||||||||
D | Zu | L | IT | Ra | t | S | hз | T | n | V | τ0 | Ρ0 | Mк | Nе | |
мм | - | мм | - | мкм | мм | мм | мин | мин | кг | кг∙м | кВт | ||||
1 | 2 | 3 | 4 | 5 | 6 | 7 | 8 | 9 | 10 | 11 | 12 | 13 | 14 | 15 | |
1 | 14 | 2 | 12 | 13 | 6,3 | 7 | 0,4 | 0,4 | 25 | 499 | 21,94 | 0,54 | 430 | 2,87 | 1,47 |
2 | 6 | 2 | 6 | 14 | 6,3 | 3 | 0,14 | 0,4 | 45 | 1398 | 26,34 | 0,18 | 45 | 0,19 | 0,27 |
11) Назначение подачи S.
Согласно стр.266 [1] условия сверления определяют 1-ю группу подач.
Выполним корректировку рассчитанной подачи по набору подач Sст станка. Рассчитанную подачу корректируем до станочных значений:
, ,
Полученное значение подачи заносим в табл. 8.3.1.
12) Выбор стойкости инструментов Т.
Рекомендуемые значения допустимого износа hз и стойкости Т осевых инструментов
выбираем соответственно из табл. 19 стр. 228 и табл. 20 стр. 229 [1] 5и заносим в сводную табл. 8.3.1.
Назначение скорости резания V.
14) Расчет частоты вращения инструмента n.
Для осевой обработки
где Dи - диаметр инструмента, мм.
Расчетное значение n должно быть скорректировано по nст.
, , .
Рассчитаем фактическую скорость резания:
.
Выбранные значения ncт и соответствующие им V заносим в табл. 8.3.1.
15) Расчет основного времени 0.
Формула для расчета 0 при сверлении приведена на стр. 611 [3]:
16) Расчет осевого усилия Р0.
При сверлении согласно стр. 281 [2]:
;
17) Расчет крутящего момента Мк.
При сверлении согласно стр.277 [2]:
.
Согласно табл. 32 стр. 281 [2]:
.
18) Расчет мощности резания.
Согласно с.280 [2] эффективная мощность резания:
.
Полученные значения Р0, Mk и Ne заносим в табл. 8.3.1.
studfiles.net
Операция - фрезерование - Большая Энциклопедия Нефти и Газа, статья, страница 1
Операция - фрезерование
Cтраница 1
Операция фрезерования центровых шлицев производится тонкой дисковой фрезой ( пилой) толщиной 2 мм, диаметром 75 мм с отверстием для оправки диаметром 27 мм, подобно операции разрезки. [2]
Операции фрезерования и выборки продолговатых гнезд ( пазов) могут меняться местами. Если продолговатые гнезда выбираются на цепнодолбежном станке, то эта операция должна предшествовать фрезерованию ( тогда дефекты обработки гнезд фрезерной цепочкой - сколы - устраняются последующим фрезерованием), а если на сверлильно-пазовальном станке, то ее выполняют после фрезерования. Завершается механическая обработка чистовых заготовок операцией зачистки поверхностей - шлифованием или циклеванием. [3]
Операция фрезерования применяется также для дополнительной обработки сложных контуров деталей из прессованных или литьевых пластиков после их формования. [4]
Операция фрезерования достаточно часто применяется для нарезания зубчатых колес на заготовках, изготовленных из отливок в форме дисков. [5]
Операции фрезерования, так же как и сверления, осуществляют на специальных фрезерных станках, обеспечивающих фрезерование плоских и фасонных поверхностей, изготовление различных кулачков и зубчатых колес, нарезание резьб и прорезание различных канавок. Фрезерные станки разделяют на универсальные или станки общего назначения и специализированные. К первым относятся гори-юн-тально -, вертикально - и продольно-фрезерные станки, ко вторым - зубо -, шпоночно -, шлице - и карусельно-фрезерные станки. Из группы небольших и средних по размерам фрезерных станков широко распространены горизонтально - и вертикально-фрезерные. [7]
Операция фрезерования торцов и зацентровка производятся на станках ФЦ-1 и ФЦ-2 завода им. Шлифование выполняется на круглошлифовальных станках с люнетами. [8]
Операция фрезерования зубьев на цилиндрической заготовке заключается в прорезании фасонных канавок на цилиндре. В этой операции новыми по сравнению с известными нам приемами являются установка рабочей фрезы относительно заготовки и метод деления. [10]
Операция фрезерования зубьев на цилиндрической заготовке заключается в про-резании фасонных канавок на цилиндре. В этой операции новыми по сравнению с известными нам приемами являются установка рабочей фрезы относительно заготовки и метод деления. [12]
Операция фрезерования зубьев на цилиндрической заготовке заключается в прорезании фасонных канавок на цилиндре. В этой операции новыми по сравнению с известными нам приемами являются установка рабочей фрезы относительно заготовки и метод деления. [13]
Операция фрезерования плоскостей в корпусных деталях осуществляется на горизонтально-фрезерных, вертикально-фрезерных и специальных станках, причем операции выполняют по различным схемам. Большое разнообразие структур операций фрезерования, станков и приспособлений, применяемых для крепления и обработки корпусных деталей, приводит к большим изменениям трудоемкости этих операций. [14]
Операции фрезерования канавок и снятия затылков сверл на универсально-фрезерных станках производятся раздельно. Применение специальных многоместных приспособлений для фрезерования канавок сверл на универсально-фрезерных станках позволяет достигнуть значительного увеличения производительности на этой операции. [15]
Страницы: 1 2 3 4
www.ngpedia.ru
Фрезерная операция - Большая Энциклопедия Нефти и Газа, статья, страница 2
Фрезерная операция
Cтраница 2
Применяют на фрезерных операциях, когда по условиям обраСотки допускается смена заготовок. Для этого на концах стола устанавливают приспособления. При повороте рукоятки рычаг перемещается вправо и с помощью шпенька 4 заводит фиксатор 5 в гнездо. При этом цапфа 2 опускается и прижимает стол к корпусу, а кулачки передвигают ползуну бис помощью сухарей / / окончательно закрепляют его. Пружины 12 служат для подъема стола при повороте. [16]
В крупносерийном производстве фрезерные операции выполняют в специальных приспособлениях с механизацией не только элементов крепления, но и других элементов - подвод и стопорение дополнительных опор, подвод и отвод прихватов и пр. [18]
Предназначен для выполнения различных сверлильных и фрезерных операций часовых деталей. [19]
В этой главе рассматриваются основные фрезерные операции, за исключением операции фрезерования плоскостей ( см. в гл. [20]
При выполнении сверлильных или фрезерных операций возникает опасность захвата одежды сверлом или фрезой. Одежда станочника должна быть прилегающей, волосы убраны под головной убор. Работать в рукавицах или перчатках, а также с забинтованными пальцами рук недопустимо ввиду опасности захвата их режущим инструментом и ранения рук. Недопустимо сверлить детали, удерживая их рукой. [21]
При составлении технологического процесса фрезерной операции необходимо иметь в виду, что существуют определенные пределы достижимой степени точности, которые оправдываются экономически. Основным мерилом экономической точности обработки является время или продолжительность обработки. [22]
При выполнении на линии фрезерных операций в качестве рабочего используется ко-ординатносиловой стол с поворотным устройством для осуществления движения подачи детали на обработку с разных сторон. [23]
Проверка размеров при выполнении фрезерных операций осуществляется фрезеровщиком, который обязан производить наладку станка на более узкий допуск, чем задано чертежом, с учетом величины и направления износа инструмента. [24]
Проверка размеров при выполнении фрезерных операций осуществляется фрезеровщиком, который обязан производить наладку станка на более узкий допуск, чем задано чертежом, с учетом при этом характера и степени износа инструмента. [25]
Применение такой головки позволяет совмещать фрезерные операции о операциями, обычно производимыми на карусельных стайках, и повышает точность расположения обрабатываемых поверхностей. [26]
В крупносерийном и массовом производстве фрезерные операции у мелких рычагов часто выполняют по схеме 25 ( см. табл. 3) как более производительной. В этом приспособлении, внедренном на Минском тракторном заводе, осуществляется одновременное фрезерование двух торцов в рычагах. [28]
Поэтому при разработке технологического процесса фрезерной операции выбирают такие методы обработки, которые обеспечивают получение необходимой точности при наименьшей продолжительности этой обработки. Такую точность называют экономической. [29]
Поэтому при разработке технологического процесса фрезерной операции следует всегда стремиться к использованию преимуществ станков непрерывного действия. [30]
Страницы: 1 2 3 4
www.ngpedia.ru