Как сделать лазерный резак по металлу своими руками? Резак для резки металла
Лазерный резак по металлу своими руками
Лазерный резак, сделанный своими руками, пригодится в каждом доме.
Конечно же, самодельный прибор не сможет обрести большую мощность, которую имеют производственные аппараты, но все же кое-какую пользу в быту от него можно будет получить.
Как сделать лазерное режущее устройство из указки?
Самое интересное, что изготовить лазерный резак можно с помощью старых ненужных предметов.
Например, своими руками изготовить лазерный прибор позволит применение старой лазерной указки.
Чтобы процесс по созданию резака продвигался как можно быстрее, необходимо подготовить следующие предметы и инструменты:
- указка лазерного типа;
- фонарик на аккумуляторных батареях;
- старый CD/DVD-RW пишущий, можно вышедший из строя, – из него понадобится привод с лазером;
- электропаяльник и комплект отверток.
Процесс по изготовлению резака своими руками начинается с разборки привода, откуда необходимо достать прибор.
Извлечение нужно сделать по максимуму аккуратным, при этом придется проявить терпение и быть внимательным. В устройстве присутствует много разных проводов с практически одинаковой структурой.
Выбирая DVD привод, нужно учитывать, чтобы он был пишущим, так как именно такой вариант позволяет делать записи с помощью лазера.
Видео:
Запись выполняется в ходе испарения тонкого металлического слоя с диска.
В процессе чтения, лазер функционирует наполовину своих технических возможностей, слегка освещая диск.
В процессе демонтажа верхнего крепежного элемента взгляд упадет на каретку с лазером, который может передвигаться в нескольких направлениях.
Каретку необходимо бережно извлечь, аккуратно снять разъемы и шурупы.
Затем можно перейти к снятию красного диода, за счет него происходит прожиг диска – это легко можно сделать своими руками при помощи электропаяльника. Извлеченный элемент не стоит встряхивать, а тем более ронять.
После того как основная деталь будущего резака находится на поверхности, нужно сделать тщательно продуманный план сборки лазерного резака.
При этом необходимо учесть следующие моменты: как лучше поместить диод, как подсоединить его к источнику питания, ведь для диода пишущего устройства требуется больше электроэнергии, чем для основного элемента указки.
Данный вопрос можно решить несколькими методами.
Чтобы сделать ручной резак с более-менее высокой мощностью, необходимо достать находящийся в указке диод, после чего поменять его на элемент, извлеченный из DVD привода.
Поэтому лазерную указку разбирают также осторожно, как и привод пишущего DVD устройства.
Предмет раскручивают, затем разделяют его корпус на две половины. Сразу же на поверхности можно будет увидеть деталь, которую и нужно заменить своими руками.
Для этого родной диод из указки снимается и аккуратно заменяется более мощным, его надежное крепление можно выполнить с использованием клея.
Возможно, снять старый диодный элемент сразу не получится, поэтому его можно подковырнуть бережно кончиком ножа, затем слегка встряхнуть корпус указки.
На следующем этапе изготовления лазерного резака нужно сделать для него корпус.
Для этой цели пригодится фонарик с аккумуляторными батарейками, что позволит лазерному резаку получить электроподпитку, приобрести эстетичный вид, и удобство использования.
Для этого в корпус фонарика своими руками необходимо внедрить модифицированную верхнюю часть бывшей указки.
Затем нужно подключить к диоду зарядку, посредством находящейся в фонарике аккумуляторной батареи. Очень важно в процессе подключения точно установить полярность.
До того как фонарик будет собран, необходимо снять стекло и прочие лишние элементы указки, которые могут стать помехой лучу лазера.
На завершающем этапе проводится подготовка лазерного резака к использованию.
Для комфортной ручной работы все этапы работы над прибором необходимо строго соблюдать.
Видео:
С этой целью нужно проконтролировать надежность фиксации всех внедренных элементов, правильность полярности и ровность установки лазера.
Итак, если все вышеизложенные в статье условия сборки были точно соблюдены, резак готов к применению.
Но так как самодельный ручной прибор наделен невысокой мощностью, то вряд ли из него получится полноценный лазерный резак по металлу.
Что идеально сможет выполнять резак, так это сделать отверстия в бумаге или полиэтиленовой пленке.
А вот наводить на человека лазерное приспособление, сделанное своими руками нельзя, здесь его мощности будет достаточно, чтобы навредить здоровью организма.
Как можно усилить самодельный лазер?
Чтобы сделать своими руками более мощный лазерный резак для работы по металлу, нужно использовать приборы из следующего списка:
- DVD-RW привод, нет разницы рабочий или нет;
- 100 пФ и мФ – конденсаторы;
- 2-5 Ом резистор;
- 3 шт. аккумуляторные батареи;
- паяльник, провода;
- коллиматор;
- стальной фонарь на светодиодных элементах.
Сборка лазерного резака для ручной работы происходит по следующей схеме.
С применением указанных приборов происходит сборка драйвера, впоследствии он посредством платы сможет обеспечивать лазерному резаку определенную мощность.
При этом к диоду ни в коем случае нельзя подсоединять электропитание напрямую, так как диод сгорит. Также нужно принять во внимание, что диод должен брать подпитку не от напряжения, а от тока.
В качестве коллиматора используется корпус, оснащенный оптической линзой, за счет которой будут скапливаться лучи.
Данную деталь легко отыскать в специальном магазине, главное, что в ней присутствует паз для установки диода лазера. Цена данного устройства небольшая, примерно составляет 3-7$.
Кстати, лазер собирается так же, как и вышерассмотренная модель резака.
В данном случае рекомендуется применять специальные браслеты, которые позволят убрать с диода статическое напряжение.
В качестве антистатического изделия также может применяться проволока, ею обматывают диод. После чего можно приступать к компоновке драйверного устройства.
Прежде чем перейти к полной ручной сборке лазерного резака, нужно проверить работоспособность драйвера.
Сила тока замеряется с помощью мультимера, для этого берут оставшийся диод и проводят измерения своими руками.
С учетом скорости тока, подбирают его мощность для лазерного резака. К примеру, у одних вариантов лазерных устройств сила тока может равняться 300-350 мА.
Видео:
У других, более интенсивных моделей, она составляет 500 мА, при условии использования другого драйверного устройства.
Чтобы самодельный лазер выглядел более эстетично, и им можно было удобно пользоваться, для него нужен корпус, в качестве которого вполне может использоваться стальной фонарик, функционирующий на светодиодах.
Как правило, упомянутый прибор наделен компактными размерами, которые позволят поместиться ему в кармане. Но во избежание загрязнений линзы, заранее нужно приобрести или сшить своими руками чехол.
Особенности производственных лазерных резаков
Не каждому по карману цена лазерного резака по металлу производственного типа.
Такое оборудование применяют для обработки и разделки металлических материалов.
Принцип действия лазерного резака строится на выработке инструментом мощного излучения, наделенного свойством испарять или выдувать металлический расплавленный слой.
Такая производственная технология при работе с разными типами металла способна обеспечить высокое качество среза.
Глубина обработки материалов зависит от вида лазерной установки и характеристик обрабатываемых материалов.
На сегодняшний день используется три вида лазеров: твердотельные, волоконные и газовые.
Устройство твердотельных излучателей основывается на использовании в качестве рабочей среды конкретных сортов стекла или кристаллов.
Здесь в пример можно привести недорогие установки, эксплуатируемые на полупроводниковых лазерах.
Волоконные – их активная среда функционирует за счет применения оптических волокон.
Данный тип устройства является модификацией твердотельных излучателей, но как утверждают специалисты, волоконный лазер успешно вытесняет свои аналоги с области металлообработки.
При этом оптические волокна являются основой не только резака, но и гравировального станка.
Видео:
Газовые – рабочая среда лазерного устройства сочетает углекислый, азотный и гелиевый газы.
Так как КПД рассматриваемых излучателей не выше 20%, их используют для резки и сварки полимерных, резиновых и стеклянных материалов, а также металла с высокой степенью теплопроводности.
Здесь в пример можно взять резак по металлу выпускаемый компанией Ханса, применение лазерного устройства позволяет резать медь, латунь и алюминий, в данном случае минимальная мощность станков только выигрывает у своих аналогов.
Схема работы привода
Эксплуатироваться от привода может лишь настольный лазер, данный тип устройства представляет собой портально-консольную машину.
По направляющим рейкам устройства лазерный блок может перемещаться как вертикально, так и горизонтально.
В качестве альтернативы портальному устройству была изготовлена планшетная модель механизма, ее резак перемещается только по горизонтали.
Другие существующие варианты лазерных станков имеют рабочий стол, оснащенный приводным механизмом и наделенный свойством перемещаться в разных плоскостях.
На данный момент имеется два варианта управления приводным механизмом.
Первый обеспечивает перемещение заготовки за счет эксплуатации привода стола, или перемещения резака выполняется за счет функционирования лазера.
Видео:
Второй вариант предусматривает одновременное перемещение стола и резака.
При этом первая модель управления по сравнению со вторым вариантом считается намного проще. Но вторая модель все-таки отличается высокой производительностью.
Общей технической характеристикой рассмотренных случаев является необходимость внедрения в устройство блока ЧПУ, но тогда цена для сборки прибора для ручной работы станет выше.
rezhemmetall.ru
виды (кислородные, плазменные, лазерные, сабельные), как резать
В зависимости от применяемой технологии и особенностей выполняемых работ могут применяться различные резаки для резки металла.
При этом от выбора требуемой модели оборудования во многом зависит качество и скорость процесса.
Виды промышленной резки металла
Для раскроя металлических заготовок и изделий может быть использовано различное оборудование, чаще всего для резки применяют следующие технологические схемы:
- Механическая резка — для ее выполнения могут применяться сабельные резаки по металлу, специальные гильотины. Данная технология требует приложения значительных усилий, при этом область ее применения достаточно ограничена, поэтому рассматривать ее более детально не будем.
- Кислородная резка.
- Плазменная резка.
- Лазерная резка.
- Гидроабразивная резка
Для каждой технологии используется различное оборудование, в том числе и разные виды резаков для резки металла, имеющие отличающуюся конструкцию и принцип работы.
Газовая резка
Технология основана на применении смеси горючего газа и кислорода для разогрева заготовки до требуемой температуры и отдельного кислородного потока для удаления продуктов сгорания металла в обогащенной среде.
Кислородные (газовые) резаки для резки металла имеют похожую конструкцию, основные отличия заключаются в размере мундштука и диаметре проходного канала для газовой смеси.
Конструктивно они состоят из следующих элементов:
- Шланги от источника кислорода и горючего газа подключаются к специальным ниппельным устройствам.
- Образование горючей смеси (обогащение газа или паров керосина) происходит в смесительной камере, при этом регулировка расхода компонентов осуществляется специальными вентилями.
- Через патрубок полученная смесь попадает на головку резака, которая состоит из внутреннего и наружного мундштука. Именно конструкция этого узла позволяет формировать различный по свойствам факел огня, при помощи которого и происходит нагрев металла и сжигание его окислов.
- Режущий поток кислорода подается на мундштук по отдельной трубке, его регулировка осуществляется еще одним вентилем.
Кислородная резка резаком металла технически более проста, чем выполнение сварочных работ.
Основные требования — необходимость подобрать оптимальную температуру горения смеси, объем подаваемого режущего кислорода и скорость перемещения резака вдоль заготовки.
При этом особое внимание стоит уделить и подготовке поверхности (удаление масла, ржавчины, краски).
Плазменная резка
Более совершенный с технической стороны способ — плазменная резка. Она широко применяется для резки нержавейки, титана, алюминия и других металлов. Отличается более высокой точностью и скоростью реза.
Плазменные резаки для резки металлов имеют следующую конструкцию:
- В специальную насадку (плазмотрон) подается сжатый воздух, который является плазмообразующей смесью.
- В конструкцию насадки входит электрод, на который подается электрический разряд определенной силы.
- Благодаря этому образуется электрическая дуга, способствующая переходу сжатого воздуха в плазменное состояние.
- Температура раскаленной плазмы может достигать 30 0000С, благодаря чему обеспечивается высокая скорость выполнения резки. При этом такая температура позволяет избежать нагрева других зон заготовки, что особенно важно, например для нержавейки.
- Стоит отметить, что края разрезанного металла в большинстве случаев будут нуждаться в последующей механической обработке, повысить чистоту можно применением плазмообразующей смеси с аргоном или углекислым газом. Но данный шаг приводит к увеличению стоимости работ.
В состав оборудования входят и электрический блок (трансформатор или инверторная установка), который обеспечивает создание сварочного тока необходимой величины. Инвертор обеспечивает более высокую скорость реза, но его применение ограничено толщиной обрабатываемых деталей (до 3 см).
Лазерная резка
На сегодняшний день это один из самых высокотехнологичных способов резки. Лазерный резак по металлу позволяет получить тонко сфокусированный луч излучения, благодаря чему стало возможным существенно повысить качество резки.
Принцип работы основан на нагреве поверхности до температуры плавления при помощи лазерного луча. Из зоны резки расплав удаляется при помощи потока газа, подаваемого под высоким давлением, или он просто испаряется под воздействием лазерного импульса высокой мощности.
Гидроабразивная резка
Такая технология может использоваться для резки не только различных металлов, но и других материалов. Ее применение позволило решить задачу, как резать металл резаком с высокой скоростью, но без применения термических способов обработки.
Принцип действия основан на подаче смеси обыкновенной воды и абразивных материалов под высоким давлением. При этом воздействие на разрезаемый материал происходит на микроуровне, что позволяет исключить возможные деформации.
Такое оборудование широко применяется не только в промышленных целях, оно используются представителями служб спасения в условиях, когда нельзя применять термические способы резки.
Отличается такая технология высокой производительностью и хорошим качеством кромки поверхности.
Любое из перечисленных видов оборудования позволяет выполнять эффективную резку металла. Поэтому выбор чаще всего основан экономическими соображениями, и останавливается на более дешевой кислородной резке.
steelguide.ru
Как выбрать газовый резак (автоген) для ручной резки
Как выбрать газовый резак (автоген) для ручной резки Р1, Р3? Как это сделать по внешнему виду?
Прежде всего, невозможно сделать выбор, глядя на рекламный проспект или картинку. Чтобы выбрать резак правильно нужно как минимум взять его в руки.Определитесь, какой толщины металл вы будете резать:• До 100 мм выбирают резак Р1• До 300 мм – Р3
На что нужно обратить внимание в первую очередь?
Материал, из которого изготовлен наружный мундштук. Согласно требованиям ГОСТа это должна быть хромистая бронза или аналог, который ей не уступает по своим физико-механическим свойствам (медь). Некоторые производители делают наружный мундштук из латуни, однако срок его службы в 3 раза меньше, чем медного.Понять при визуальном осмотре, какой перед вами материал достаточно просто: медный или бронзовый мундштук имеет красноватый цвет, латунный –желтый. Внутренний мундштук, если вы работаете на ацетилене, также должен изготавливаться из хромистой бронзы или меди.
Если вы работаете на пропан-бутановых смесях или метане, допускается изготовление внутреннего мундштука из латуни. Это тем, что температура горения пропано-кислородной смеси на 1000 оС меньше, чем ацетилено-кислородной.
Допускается изготовление трубки резака из латуни, меди или коррозионностойкой стали. Применение других материалов не рекомендуется ввиду их быстрой изнашиваемости и выхода из строя, а, например, использование алюминия может быть даже небезопасным для жизни.
Обратите внимание, что инструмент не должен быть покрашен. Под слоем лакокрасочных покрытий скрываются дефекты металла или пайки, а также невозможно определить материалы, из которых сделан резак. Краска носит декоративный характер.
Резак должен быть разборной, т.е. состоять из разъемных соединений на тот случай, если у вас вышел из строя наконечник, износилась головка, прогорела трубка. В таком случае вы сможете без труда разобрать и почистить все составные элементы (наконечник, внутренние каналы и т.д.) или заменить прохудившуюся деталь. В противном случае вам придется идти в магазин за новой покупкой.
Некоторые автогены имеют моноблочную конструкцию, то есть все соединения паянные. Это плохо тем, что в случае прогара трубки или износа какой-либо детали вы не сможете ее отремонтировать. Если такой «моноблок» засорился, то прочистить его можно, но все это достаточно «геморройно», неудобно и сложно.
Если вы покупаете профессиональный резак, допустим, типа «Маяк», то обратите внимание, что кислородный режущий вентиль должен быть диаметром не менее 40 мм –это обусловлено удобством в процессе работы. Оборудование с пометкой «профи» подразумевает, что его эксплуатируют постоянно и регулярно, т.е. не менее 5-6 часов непрерывной работы. Большой диаметр вентиля КР позволит вам лучше контролировать процесс, так как резчик работает не голыми руками, а в рукавицах или крагах. Кроме того, большой барашек проще крутить и меньше устает рука. Маховики должны вращаться легко и без большого усилия и при этом не болтаться.Если вентиль вращается слишком легко, вы можете нечаянно задеть его рукой или зацепить одеждой – и ранее сделанные вами настройки собьются, а состав пламени поменяется. Вам придется резак постоянно подстраивать, что очень неудобно! Если вентиль вращается с большим усилием, то за рабочий день у вас сильно устанет кисть – это тоже большой минус!
Обратите внимание на материал из которого изготовлен шпиндель резака. Согласно рекомендациям он должен быть сделан из нержавеющей стали (15000-45000 циклов в зависимости от рабочих режимов).Срок службы латунного шпинделя не более 3 тыс. циклов. Существуют комбинированные варианты (изготовленные из латунного сплава и нержавейки) – это средний вариант, который служит от 8000 до 10000 циклов.
И еще пара полезных советов…
Сравните паспортные данные о расходных характеристиках резаков с требованиями ГОСТ 5191-79 (pdf). В этом государственном стандарте есть таблица с указанием номеров мундштуков и толщин для которых они предназначены, а также расход по кислороду и газам.
Уточните у продавца, есть ли возможность обеспечения запасными частями. Если запчастей нет – это значит, что вы покупаете разовое оборудование. Например, выйдет из строя мундштук, который является расходным материалом. Вы не сможете купить и заменить его на новый. Остается разве что вариант самостоятельного изготовления, что не для всех доступно. Что касается других деталей, некоторые вы сами сделать не сможете ввиду сложности технологии их производства.
Источник: Донмет
svarka-master.ru
устройство и виды (инжекторные, портативные ), сколько стоит
Несмотря на развитие новых технологий резания металла (плазменная, лазерная резка), доля применения оборудования для кислородной резки в общем объеме выполняемых работ не уменьшается. Основанием для такой популярности данного метода является низка себестоимость выполняемых работ при вполне допустимом качестве.
Кроме того, само оборудование (резаки по металлу газовые) имеет вполне доступную цену, а период окупаемости оснащения для выполнения работ по такой технологии, минимальное.
Физика газовой резки и область применения
Данная методика основана на расплавлении металла под воздействием температуры открытого пламени, получаемого при сгорании обогащенной кислородом смеси горючих газов.
При этом резаки для газовой резки металла выполняют две основные рабочие функции:
- Разогрев металла до температуры плавления.
- Удаление расплава из зоны резки потоком кислорода.
Благодаря этому существенно снижаются энергозатраты на выполнение работ, и повышается скорость резания.
Технология газовой резки может применяться для работы и с черными, и с цветными металлами, а так же различными сплавами.
При этом основное внимание стоит уделять выбору основного горючего газа, так как при горении они обеспечивают различную температуру.
В качестве топлива (источника тепловой энергии) применяют следующие газообразные вещества:
- Пропан.
- Водород.
- Ацетилен.
- Пары керосина.
Газовый резак по металлу применяется при выполнении монтажных работ на строительных площадках и в заводских условиях при изготовлении металлоконструкций.
Устройство резаков
Несмотря на то, что существуют различные модели оборудования, отличающиеся габаритами и производительностью, устройство газового резака во всех случаях однотипное:
- Поступающие по подающим шлангам газы (основной горючий и кислород) смешиваются в специальной камере. После чего они подаются в выпускное устройство (мундштук), которое обеспечивает необходимые параметры потока (скорость истечения смеси).
- Получаемый в результате горения факел пламени воздействует на металл и приводит к его плавлению.
- Регулировка состава смеси, а, следовательно, и температуры ее горения, осуществляется при помощи двух вентилей (на каждый газ отдельный).
- Непосредственная резка (выдувание расплава из рабочей зоны) осуществляется потоком кислорода, который подается на мундштук по отдельной линии. Количество режущего газа регулируется отдельным вентилем.
Все существующие виды газовых резаков имеют именно такую конструкцию, исключение составляет только рабочее устройство керосинорезов, хотя принцип работы такой горелки тот же, различия заключается именно в технических конструктивных решениях. Наиболее производительными считаются инжекторные газовые резаки, получение рабочей смеси осуществляется путем подсоса кислорода потоком рабочего газа.
Существующие типы резаков
В зависимости от применяемого горючего газа конструкция устройства может несколько меняться, но основные различия заключаются в форме и размерах мундштука, а также диаметре выпускного сопла.
Небольшие размеры имеет портативный мини-газовый резак по металлу, работающий на ацетиленовой смеси. Именно ацетилен обеспечивает наибольшую температуру пламени, поэтому даже небольшие по размерам резаки могут применяться для работы даже с толстым металлом.
Резак для резки пропаном считается одним из самых распространенных, он отличается невысокой стоимостью, но обеспечивает вполне достаточную производительность. Существуют даже туристические газовые резаки такого типа, которые работают от малолитражных баллонов с пропаном, такое оборудование отличается компактными размерами.
Керосинорезы имеют более сложное устройство и применяются в основном в промышленных целях, в условиях, когда по соображениям безопасности не допускается применение газовой аппаратуры (например, резка металла в угольных шахтах).
Постоянное усовершенствование оборудование приводит к выпуску более простых и удобных в эксплуатации устройств.
Так, сравнительно недавно на рынке появился газовый резак с пьезоподжигом, который запускается в работу простым нажатием кнопки, мелочь конечно, но приятная.
Основы технологии резки
Выполнять работы такими агрегатами можно после минимальной подготовки, главное правильно установить требуемый режим резки, который зависит от физических свойств металла и его толщины. Перед тем, как резать газовым резаком, необходимо установить требуемую температуру горения. Она определяется визуальным путем, по размерам ядра факела пламени. Для разных газов этот показатель несколько отличается, но в среднем ядро (участок пламени синего цвета) должно иметь длину 10-20 мм, в этом случае будет получена оптимальная температура для работы с большинством металлов.
Скорость резания определяется количеством подаваемого на выдув расплава кислорода. Для увеличения скорости выполнения работ необходимо увеличить подачу режущего газа.
Дать ответ на общий вопрос, сколько стоит газовый резак, невозможно. Цена зависит от обеспечиваемой производительности устройства, его габаритов, наличия дополнительных функций, упрощающих выполнение работ.
Но в любом случае стоимость данного оборудования вполне демократична, что и обеспечивает популярность данной технологии резки металлов.
steelguide.ru
Резаки для ручной резки газовой (кислородной), промышленные устройства
Предназначение резаков состоит в разрезании металла путем его нагрева и рассечения струей газа. Так можно разрезать металлические изделия практически любой формы за короткое время. Все резаки для ручной резки работают по общему принципу. Внутрь аппарата подаются кислород и горючий газ, которые смешиваются.
Данная смесь призвана обеспечить соответствующий нагрев поверхности металла по определенной линии. После нагрева на место будущего реза подается кислород, который окисляет и вытесняет своим напором расплавленный металл. Образуется достаточно ровный рез. Работа проводится быстро и эффективно. По своему предназначению различают устройства для ручной, механизированной резки, а также аппараты специального назначения. Мы рассмотрим подробно бытовые и промышленные резаки для ручной резки.
Какими бывают резаки для ручной резки металла?
Существует множество модификаций данных устройств.
Они квалифицируются по множеству признаков, которые мы сейчас постараемся перечислить:
- По виду реза. Резаки для ручной газовой резки подразделяются на следующие типы: поверхностные, разделительные и кислородно-флюсовые.
- По принципу своего действия. Различают инжекторные и безинжекторные устройства.
- По конструкции мундштуков (наконечников). Бывают многосопловые и щелевые.
- По виду используемого горючего. Существуют аппараты для жидкого топлива, для газов-заменителей, а также для ацетилена.
- По уровню давления кислорода. Низкое или высокое давление.
Устройство газового резака
Резаки для ручной кислородной резки, независимо от квалификации, имеют схожее устройство, ведь все они работают по схожему принципу.
Резак состоит из корпуса, на котором расположены регулирующие подачу газов клапаны, газовых трубок, рукоятки и головки для навинчивания мундштука. К корпусу крепится смесительная камера с инжектором. Поступающий в трубки кислород идет в двух направлениях. Часть его, предназначенная для подогрева, подается в главный канал инжектора. Кислород в смесительной камере создает разрежение, из-за чего происходит подсос ацетилена. Смесь направляется к мундштуку и выходит через него в виде подогревающего пламени.
Вторая часть кислорода проходит в головку, откуда уже выходит через канал мундштука с образованием режущей кислородной струи.
Виды мундштуков для резаков
Многосопловые мундштуки
Такие мундштуки имеют несколько каналов (сопел), имеющих диаметр от 0,7 до 1 мм. Сопла расположены вокруг канала, по которому проходит кислород. Могут быть цельными или составными. Различные газы поступают по различным соплам, смешиваясь и сгорая на выходе. Такие мундштуки используют с газами-заменителями, которые обладают невысокими скоростями горения.
Есть и недостаток — сопла при частом использовании забиваются шлаками. Это может вызывать обратное направление пламени или хлопки.
Щелевые мундштуки
Состоят из двух отдельных мундштуков, входящих друг в друга. Между ними находится кольцевой зазор, по которому проходит смесь кислорода с ацетиленом. Воспламененная смесь выбрасывается через головку и служит для нагрева металла. По каналу внутреннего мундштука идет поток кислорода, которым осуществляется непосредственная резка.
steelguide.ru
Пропановый резак - как выбрать лучший газовый резак
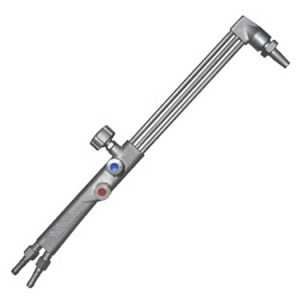
Как выбрать пропановый резак
Содержание статьи
На сегодняшнее время существуют различные виды резаков для газовой сварки, поэтому для того чтобы выбрать лучший газовый резак придется постараться. Все газовые резаки имеют свои технические особенности и характеристики.Одни их виды подходят идеально для выполнения различного рода монтажных работ, а другие напротив, предназначены исключительно для разрезания металлов.
Итак, о том, какие бывают виды резаков для газовой сварки и как выбрать пропановый резак, будет рассказано ниже.
Как выбрать пропановый резак. Лучший газовый резак
Сегодня для газовой сварки чаще всего используются следующие разновидности резаков:
Кислородный резак – является бюджетным вариантом для резки металла, а его конструкция представляет собой инжекторную установку для формирования горящей струи посредством кислорода.
Резак керосиновый – чаще всего используется в промышленных целях из-за своих сложных конструктивных особенностей. Применим для резки металла не толще чем 20 сантиметров, а сам процесс разрезания металлических частей происходит под воздействием керосинового пара.
Пропановый резак – подходит для резки, как черных, так и цветных металлов. Резак пропановый отличается от всех остальных видов своей надежностью и безопасностью, что делает его очень популярным инструментом при выполнении газосварочных работ.
Ацетиленовый резак – в большинстве случаев применяется для резки толстых металлов. Имеет вентили, которые можно регулировать по отдельности, тем самым, увеличивая или уменьшая мощность и скорость подачи газа.
Резак пропановый Корд-Р-01П-L535
Вопрос – как выбрать пропановый резак непростой, тем более что на сегодняшнее время на рынках данное оборудование представляет множество различных производителей. Поэтому чтобы выбрать лучший газовый резак необходимо отталкиваться от множества нюансов.
Хорошие пропановые резаки предлагает сегодня потребителю такой производитель сварочного оборудования как компании «Корд». Это надёжный и проверенный временем производитель.
Отзывы о продукции «Корд» только положительные, это объясняется тем, что компания за все годы своей упорной работы всегда использовала в производстве своей продукции только качественное сырьё, соответствующее всем нормам и правилам безопасности, установленным согласно государственным стандартам и требованиям.
Резак пропановый Корд-Р-01П-L535 отличается своей надёжностью при эксплуатации, а также мобильностью. Это удобное приспособление для ручной резки углеродистых, а также низколегированных сталей.
Основные характеристики пропанового резака модели «Корд-Р-01П-L535» таковы:
- Оборудование имеет рычаг, предназначенный для включения подачи режущего газа – кислорода. Рычажный способ включения намного удобнее и предпочтительней вентильного, так как способствует сокращению затрат газа, экономит режущий кислород.
- Стандартный пропановый резак этой модели имеет вес, равный 1,12 килограмм. Такой вес позволяет легко производить действия и работу с оборудованием, а параметры размера резака способствуют производству более точной и качественной резки стальных изделий.
- Головка пропанового резака наклонена под оптимальным для работы углом, равным ста десяти градусам.
- Устройство работает достаточно тихо, уровень шума, который достигается в работе с оборудованием такого типа, очень низкий, не превышает восьмидесяти децибел. Это полноценно обеспечивает комфортную работу и меньшее напряжение для рабочего.
В плюс ко всем преимущественным сторонам резаков от компании «Корд» можно добавить и то, что цены на данную продукцию невысокие, но с лихвой оправдывают высокое качество оборудования.
Оценить статью и поделиться ссылкой:samastroyka.ru
Самодельный плазменный резак: устройство и работа
Резка металла различных разновидностей для людей, которые занимаются ремонтом всевозможных механизмов, и в первую очередь автомобилей, составляет неотъемлемую часть работы. А выкроить из металлического листа сложную фигурную деталь или прорезать в изделии из цельного металла отверстие нужной формы в условиях гаража или небольшой мастерской лучше всего поможет ручной плазменный резак.
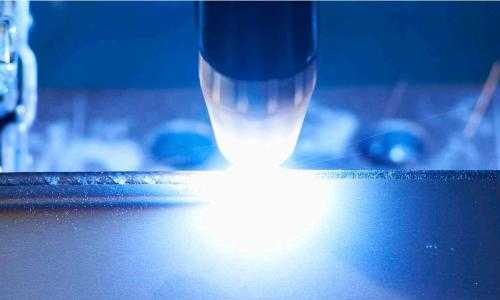
Ручной плазменный резак с легкостью сделает металлическую деталь или отверстие любой сложности.
Поскольку такой инструмент в фирменном исполнении стоит значительной суммы денег, становится более рентабельным изготовить его самостоятельно. Мощность его при этом будет не намного ниже, чем у аналога заводского изготовления, а помощь в работе он сможет оказать неоценимую. Скорость резки намного выше, чем у газового или иного резака, а затрат труда требуется меньше.
Принципы действия и преимущества плазменной резки
В качестве режущей поверхности в ней применяется плазменная струя. Она образуется, когда между электродом и соплом горелки зажигается электрическая дуга, а через нее под давлением проходит газ, нагреваясь от 3000 до 50000° и превращаясь в плазму.
Принцип действия плазменного резака.
В качестве подаваемого газа могут выступать как азот или кислород, так и водяной пар или просто воздух. Кислородом удобно резать мягкое железо и нелегированную сталь, поскольку он легче удаляет расплавленный металл из образуемого разреза.
При применении азота для разрезания металла аналогичной толщины требуется меньшая сила тока, а электроды меньше нагреваются, что существенно увеличивает их сроки эксплуатации. Однако в кромках разрезаемого металла накапливается при этом азот, что плохо влияет на его качество. Сжатый воздух же является наиболее дешевым вариантом, однако быстро изнашивает электроды и само сопло.
В отличие от других видов агрегатов для резки металла, резак, работающий с помощью плазмы, универсален. Он может резать как электропроводные материалы, так и не проводящие электричество, как все виды черных, так и цветных металлов и сплавов. Кроме того, им можно резать дерево, разные виды пластмасс или керамическую плитку.
Помимо резки он может спаивать поверхности разных видов металла с помощью высокотемпературных видов припоя, производить поверхностную закалку, отжиг или термическую очистку. К тому же он очень экономичен. При резке плазменной струей единица длины разреза обходится дешевле, чем при работе другими видами резаков.
Устройство, сборка и работа плазменного резака
Основные составляющие части агрегата представляют собой специальные блоки: катодный и анодный. Между катодом, который делается из максимально тугоплавкого материала, и анодом, который нуждается в постоянном и сильном охлаждении, и вспыхивает электрическая дуга. Катод лучше всего сделать из вольфрамового стержня толщиной не менее 4 мм, поскольку более тонкий быстро сгорит.
Составляющие самодельного плазменного резака.
Его можно легко изготовить из сварочного электрода. Анодный блок можно сделать из бронзы, а сам анод из меди. В блоке должна быть полость для постоянной прогонки охладителя, в роли которого можно применить обычную воду, но лучше тосол. Диаметр сопла должен составлять около 2 мм, поскольку меньший будет периодически забиваться.
К анодному блоку подходит две трубки, через которые прогоняется охладительная жидкость. Через них же подключается электрическое питание. К катоду оно подключается проводом, конец которого припаян на держатель. Катод крепится на резьбовом соединении подвижно, в момент включения его стыкуют с анодом, а затем отводят на 3-4 мм, в этом промежутке горит дуга. По шлангу на катод подается сжатый воздух или пар с помощью воздушного компрессора, а на анод — охладитель из специального резервуара, под который можно использовать пластиковую канистру. Прокачку охладителя вполне может производить омыватель стекол, снятый со старого автомобиля.
Для успешной работы такого резака необходим будет еще балластный резистор, подсоединенный к нему через диодный мост. В качестве такого резистора вполне можно использовать электрическую плиту мощностью 4-5 кВт. Диоды можно взять практически любые, способные работать на токе выше 50 А. Электричество на такой самодельный резак подается от обычной бытовой электросети через трансформатор 12 В, к которому подключается выпрямитель с дросселем. Последний наматывается из толстой медной проволоки в количестве около 100 витков и выдерживает ток до 20 А.
При наличии некоторых знаний и технических навыков плазменный резак можно собрать с применением подручных материалов и устройств своими руками.
moyasvarka.ru