Электрооборудование, свет, освещение. Самодельная лазерная резка металла
Лазерная резак своими руками
Резка металла с помощью лазера – самая передовая и современная технология, но и самая дорогостоящая. Ее основное преимущество – это луч, с неограниченными возможностями. Лазерная резка металла своими руками дает возможность резать заготовки в любых направлениях, при этом кромки реза будут аккуратными, и им не требуется дальнейшая обработка. К тому же лазерный луч монохромен, то есть, у него четкая и строгая длина волны (она фиксированная) и постоянная частота. Это дает возможность легко его сфокусировать даже обычными линзами.
Итак, оборудования для лазерной резки по металлу – вещь недоступная многим, слишком дорогое это удовольствие. Поэтому домашние умельцы выходят из положения, используя различные уже почти ненужные предметы, из которых и изготавливают самодельный прибор. Вариантов изготовления лазерных резаков своими руками много, один из них основан на использовании лазерной указки, о нем и пойдет речь.
Изготовления самодельного лазерного резака
Для сборки резака понадобятся:
- лазерная указка;
- фонарик;
- CD/DVD-RW – не обязательно новый, главное, чтобы у него работал лазер с приводом;
- инструменты: паяльник и отвертки.
Обратите внимание, что для сборки аппарата лазерной резки требуется пишущий DVD. Его необходимо разобрать и найти каретку с лазером, который пишет и считывает информация с компактного диска. Рядом с кареткой должен находиться красный диод. Его также надо демонтировать при помощи паяльника, потому что он припаян к схеме в плато. Кстати, с диодом надо обращаться аккуратно, встряхивать его, ронять, ударять и так далее нельзя.
Теперь вот какой момент – лазерный резак (он же диод) потребляет больше тока, чем диод лазерной линейки. Поэтому необходимо позаботиться о том, чтобы этого тока было больше. Здесь несколько вариантов, но так как был приготовлен фонарик, то будут для питания диода использоваться его батарейки. Батарейка в лазерной указке меньше, и она одна.
Теперь можно переходить к сборке лазерного резака.
- Разбирается лазерная указка.
- Из нее извлекается свой диод, а на его место устанавливается диод, демонтированный из DVD.
- Теперь необходимо провести подключение к новому более мощному источнику питания. Для этого переднюю часть указки устанавливают в фонарик, сняв с него предварительно линзу. Она закрепляется на приборе при помощи прижимной гайки, накручиваемой по резьбе.
- Диод подключается проводами от клемм, которые соединяются с батарейками. Здесь важно не перепутать полярность подключения.
- В принципе, все готово. Лазерный миниатюрный резак можно использовать.
Конечно, им резать металл не получится, а вот бумага, полимерные пленки м прожигаются. Даже спички таким приспособлением можно поджигать.
Лазер для резки металла
Добавив несколько приборов к выше используемым, можно изготовить более мощный прибор, почти в 500 раз мощнее. Добавляются:
- оптически коллиматор – это устройство, с помощью которого создается световой поток из параллельных пучков;
- конденсаторы 100пФ и 100мФ;
- один резистор сопротивлением 2-5 Ом.
Из радиодеталей вместе с диодом собирается драйвер, который будет выводить резак на необходимую мощность. Оптический коллиматор снабжен местом, куда можно установить диод, и это его большое преимущество. То есть, вместо лазерной указки в этой установке используется коллиматор. К тому же указка изготавливается из пластика, и в процессе резки ее корпус будет сильно нагреваться. Это приведет к ее короблению, да и охлаждаться сама установка будет плохо.
Вся остальная сборочная технология точно такая же, как и в предыдущем случае. Необходимо отметить, что диод – элемент очень чувствительный, поэтому необходимо с него перед использованием снять статическое электричество. Это можно сделать с помощью антистатического браслета. Если в наличии браслета нет, то можно на диод намотать тонкую проволочку, которая и будет отводить от детали статику.
Полезные советы
Изготовление лазера своими руками для резки металла требует определенных действий, которые отражаться на его качественной дееспособности. В первую очередь нужно протестировать собранный драйвер. Для этого придется найти еще один точно такой же диод. Его присоединяют к устройству и тестируют мультиметром. 300-350 мА – это норма для многих самодельных аппаратов. Но если есть необходимость поднять мощность всего агрегата, то лучше, если мультиметр покажет 500 мА. Правда, для такого резака придется собирать другой драйвер, поддерживающий данную величину тока.
Не забываем и об эстетической стороне вопроса. Вариантов корпуса можно придумать разные. К примеру, светодиодный маленький фонарик. Рекомендуется готовый прибор хранить в специальном чехле, чтобы линза оптического коллиматора не покрылась пылью. Кстати, такой резак может вызвать у соответствующих правоохранительных органов много вопросов, поэтому не стоит его носить с собой в кармане.
Необходимо отметить, что мощность диода зависит от тока, а не от напряжения. При повышении последнего превышается норма яркости свечения диода, а это приводит к разрушению резонатора в конструкции диода. То есть, источник света перестает нагревать, что необходимо ля лазерного резака. Он просто светится, как обычная лампочка. Температуры также влияют на работоспособность диода. При низких температурах его производительность возрастает, при высоких выходит из строя резонатор.
Конечно, говорить о том, что этот лазерный резак будет в домашних условиях резать толстые заготовки, не приходиться. Но тонкую жесть или алюминиевую фольгу он резать будет точно. Такие установки пригодятся дизайнерам, которые из различных ненужных предметов делают разные дизайнерские аксессуары. К примеру, из алюминиевой банки из-под пива можно сделать необычный светильник.
Поделись с друзьями
0
0
1
0
svarkalegko.com
Лазерный резак своими руками
Когда в домашнем хозяйстве возникает необходимость раскроить металлический лист, то тут не обойтись без лазерного резака, своими руками собранного.
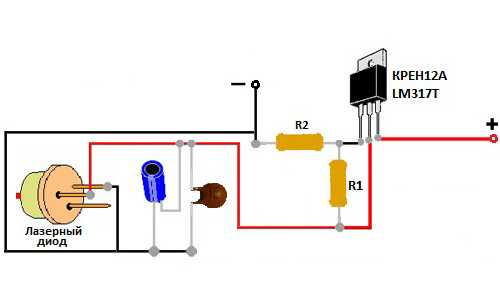
Схема самодельного лазерного резака.
Вторая жизнь простых вещей
Домашний мастер всегда найдет применение даже тем вещам, которые пришли в негодность. Так, старая лазерная указка может обрести вторую жизнь и превратиться в лазерный резак. Для того чтобы воплотить эту идею в жизнь, понадобятся:
- Лазерная указка.
- Фонарик.
- Батарейки (лучше взять аккумуляторные).
- Пишущий CD/DVD-RW рекордер, имеющий привод с рабочим лазером.
- Паяльник.
- Отвертки в наборе.
Работа начинается с извлечения из привода лазерного резака. Это кропотливая работа, требующая максимального внимания. При снятии верхнего крепежа можно наткнуться на каретку с встроенным лазером. Он может двигаться по двум направлениям. Каретка должна быть извлечена с особенной осторожностью, все разъемные устройства и шурупы сняты аккуратно. Далее необходимо снять красный диод, который осуществляет прожиг. Эту работу можно выполнить при помощи паяльника. Следует отметить, что эта важная деталь требует к себе повышенного внимания. Ее не рекомендуется ни встряхивать, ни ронять.
Схема устройства лазерного резака.
Для увеличения мощности лазерного резака в подготовленной указке необходимо заменить «родной» диод на вынутый из рекордера.
Указку следует разбирать последовательно и аккуратно. Она раскручивается и разделяется на части. Деталь, что требует замены расположена вверху. Если извлечь ее сложно, то помочь себе можно ножом, слегка потряхивая указку. На место «родного» диода устанавливается новый. Закрепить его можно при помощи клея.
Следующий этап работы — сооружение нового корпуса. Здесь пригодится старый фонарик. Благодаря ему новым лазером будет удобно пользоваться, подключать его к питанию. Усовершенствованная торцевая часть указки устанавливается в корпус фонарика. Затем от аккумуляторных батареек к диоду подключается питание. При подключении очень важно правильно установить полярность. Перед тем как собирать фонарик, нужно удалить стекло и оставшиеся детали указки, чтобы ничто не мешало прямому ходу луча лазера.
Перед тем как использовать своими руками собранный агрегат, необходимо еще раз проверить прочно ли закреплен и ровно установлен лазер, правильно ли подключена полярность проводов.
Если все выполнено правильно, агрегатом можно пользоваться. Работать по металлу будет сложно, поскольку аппарат имеет небольшую мощность, но прожечь бумагу, полиэтилен или что-то подобное вполне реально.
Вернуться к оглавлению
Усовершенствованная модель
Схема лазерной резки.
Может быть изготовлен более мощный самодельный лазерный резак. Для работы нужно подготовить:
- CD/DVD-RW рекордер (может быть использована нерабочая модель).
- Резисторы 2-5 Ом.
- Батарейки.
- Конденсаторы 100 пФ и 100 мФ.
- Провод.
- Паяльник.
- Коллиматор.
- Светодиодный фонарик в стальном корпусе.
Из этих комплектующих собирается драйвер, что через плату станет обеспечивать резаку нужную мощность. Следует помнить, что источник тока к диоду напрямую не подключается. Иначе он придет в полную негодность. Подключить питание можно только через балластное сопротивление.
В роли коллиматора выступает корпус с линзой. Именно она будет собирать лучи в единый пучок. Эту деталь можно приобрести в специализированном магазине. Деталь хороша тем, что в ней предусмотрено гнездо для монтажа лазерного диода.
Этот лазер изготавливается так же, как и предыдущая модель. Во время работ необходимо использовать антистатические браслеты, позволяющие снимать статическое напряжение с лазерного диода. Если приобрести такие браслеты невозможно, может быть использована тонкая проволока, которую нужно намотать на диод. Затем можно переходить к сборке драйвера.
Перед тем как собрать устройство нужно проверить работу драйвера, замерить силу подаваемого тока. Это можно сделать мультиметром.
Корпус для такого аппарата может быть выбран любой. Но самое разумное решение — это использовать светодиодный фонарик. Благодаря его компактным размерам устройство можно будет носить даже в кармане. Чтобы на линзу не попадала пыль хранить его лучше в специальном чехле.
expertsvarki.ru
Резка металла своими руками | Строительный портал
Каждому промышленному предприятию или частному лицу, которое занимается металлообработкой, требуется станок для резки металла, что отвечает заданным требованиям к стоимости, производительности и безопасности. Сегодня выделяют большое количество разных методов обработки металла - обработка металла плазмой, лазером и давлением, а также ручная резка металла ножницами. Если вы ещё не определились с оптимальным методом и подходящим оборудованием для резки металла, наша статья поможет вам сделать это.
Содержание:
- Виды резки металла
- Газовая резка металла
- Плазменная резка металла
- Лазерная резка металла
- Гильотинная резка металла
Виды резки металла
Процесс резки металла представляет из себя отделение заготовок от металла литого, сортового или листового. Наиболее распространенными и эффективными с экономической позиции на сегодняшний день выступают такие методы, как плазменная, лазерная и газовая резка. Очень часто металл режут пресс-ножницами, которые способны пробивать пазы и отверстия разных форм в стали разнообразной прочности.
При выборе одного метода обработки металла из выше перечисленных рекомендуется ориентироваться на качество самого процесса работы, количество конечных отходов и точность исполнения. Важным моментом выступает и возможность создания небольшой партии деталей в максимально сжатые строки при оптимальной цене резки на профильных производствах.
Более, того выбор одного из них оправдан при учете определенных критериев, таких как эффективность работы, конечный результат, стоимость изделия. При этом существует определенный список металлов и сплавов, с которыми целесообразно работать тем или другим оборудованием.
Газовая резка металла
Газовая резка представляет собой процесс резки металлических изделий, который основан на свойстве металлов, что нагреты до определенной температуры (1200-1300 градусов), гореть в чистом кислороде. Благодаря газовой резке листового металла в наше время можно осуществлять самые разнообразные типы обработки – подготовка кромок для процесса сварки, прямая резка металла, процедура резки под углом.
Сущность технологии
Резку принято начинать с кромки листа. Поверхность, что предназначена для резки, необходимо очистить от ржавчины, окалины и грязи. Кислород и газ в горелки подается из баллонов, где они содержатся в сжатом состоянии. Масса одного баллона равняется 70 кг. Рабочее давление кислорода на один метр квадратный составляет 300 кН, а газа – достигает 50 кН.
Давление при этом можно отрегулировать в редукторе устройства, который навинчен на штуцер кислородного баллона. Редуктор оснащен манометром высокого давления, который показывает давление кислорода в баллоне, а также оборудован манометром низкого давления, что предоставляет информацию о рабочем давлении.
Лист металла прожигается и разрезается струей кислорода, которая подается под большим давлением. Образующиеся окислы железа вытекают в расплавленном состоянии и выдуваются из полости реза. Технология газовой резки металла предполагает использование резака, который представляет собой некую сварочную горелку со специальным устройством для подвода кислорода.
Виды газовой резки
В данном виде сварки традиционно используются водород (коксовый, нефтяной и природный) и ацетилен, пары керосина и бензина, которые могут достигать в процессе горения температуры в 3200 градусов. Зависимо от применяемого горючего газа, выделяют водородно-кислородную, ацетиленокислородную и бензинокислородную резку, а также машинную и ручную резки.
Отдельным видом газовой резки выступает флюсокислородная резка, что позволяет разделять трудно поддающиеся резке металлы – хромоникелевые и высокохромистые стали, алюминиевые сплавы и чугуны. В этом случае процедуру облегчают порошкообразные флюсы, которые вдуваются вместе с кислородом.
Помимо разделительной кислородной резки, когда режущая струя практически перпендикулярна поверхности металла, используют кислородную обработку, в процессе которой режущую струю направляют к поверхности металла под острым углом.
Данным способом режут листы из углеродистых средне- и низколегированных сталей, которые имеют толщину от 1 до 200—300 миллиметров. На видео о газовой резке металла вы увидите, что возможной считается газовая резка стали толще 2 метров. Кислородная резка широко используется в цветной и чёрной металлургии, а также в частном строительстве.
Предъявляемые требования
Чтобы совершить данный процесс, необходимо выполнить ряд требований. Помните, что металл должен обладать большей температурой плавления, чем показатель температуры горения в кислороде. Напротив, оксиды металла должны отличаться температурой плавления меньшей, чем температура плавления выбранного металла.
Следите, чтобы уровень термального воздействия был достаточен для обеспечения непрерывности процесса резки. Обрабатываемый металл не должен обладать слишком высокой теплопроводностью, так как в противном случае тепловая энергия будет быстро отводиться. Соответственно данным критериям, которые предъявляются к газовой резке, для этой процедуры идеально подходят низкоуглеродистые и низколегированные стали и железо.
Достоинства газовой резки
Главным преимуществом газовой резки металла является возможность раскроя листов металла, которые имеют большую толщину - до 200 миллиметров. При этом ширина среза составляет 2-2,5 миллиметров. При помощи оборудования для газовой резки металла можно провести вертикальную кромку среза, что в ходе процесса не будет закаливаться.
Нельзя не вспомнить и об экономической эффективности данной технологии – газовая резка не требует вложения больших финансовых средств. Минимальны требования, что связаны с техническим обслуживанием процесса. Несомненным достоинством газовой сварки металла является и тот факт, что для её проведения не нужна никакая механическая обработка.
Плазменная резка металла
Резка металлов с использованием струи плазмы вместо резца называется плазменной. Поток плазмы формируется в результате обдува сжатой электрической дуги газ, который нагревается и в процессе ионизируется - распадается на положительно и отрицательно заряженные частицы. Плазменный поток обычно имеет температуру близко 15 тысяч градусов Цельсия.
Способы плазменной резки
Выделяют поверхностную и разделительную плазменную резки. Однако на практике широкое использование получила именно разделительная технология резки металла. Сам процесс резки осуществляют двумя методами – плазменной дугой и струей.
При резке металла плазменной дугой он включается в электрическую цепь. Выше упомянутая дуга возникает между изделием и электродом резака из вольфрама. Если вы выбрали вторую методику, то помните, что в резаке дуга формируется между двумя электродами. Разрезаемый лист не включается в электрическую цепь.
По производительности плазменная резка превосходит кислородную. Но если вам нужно порезать титан или металл большой толщины, то рекомендуется отдать предпочтение кислородной резке. При резании цветного металла плазменная резка считается незаменимой. Особенно это касается алюминия.
Аппараты для плазменной резки
Для образования плазмы принято использовать активные и неактивные газы. К первой группе относят воздух и кислород, которые используются при резке черных металлов (меди, стали и алюминия), и неактивные – водород, аргон и азот для резки сплавов и цветных металлов (высоколегированной стали, которая имеет толщину до 50 миллиметров, латуни, меди, алюминия и титана).
Для механизации процедуры были разработаны аппараты для резки металла - полуавтоматы и переносные машины разных модификаций. Полуавтоматы работают с неактивными и активными газами, в то время как переносные машины используют исключительно сжатый воздух.
Резка металла плазмой в домашних условиях осуществляется при помощи ручных аппаратов, в комплект которых входят режущий плазмотрон, коллектор, кабель-шланговый пакет и зажигалка, предназначенная для возбуждения режущей дуги. Такие комплекты позволяют выполнять ограниченный объем работы с загрузкой оборудования не больше чем на 50%. Поэтому их рекомендуется доукомплектовать на время работы сварочными преобразователями и выпрямителями.
Сущность технологии
Началом процедуры резания металлов является момент, когда возбудилась плазменная дуга. Начав резку, следует поддерживать между поверхностью металла и соплом плазмотрона постоянное расстояние, которое составляет 3 - 15 миллиметров.
Стремитесь к тому, чтобы ток был минимальным в процессе работы, потому что при возрастании силы тока и увеличении расхода воздуха падает ресурс работы электрода и сопла плазмотрона. Но уровень тока при этом должен обеспечивать высокую производительность резки. Самой сложной операцией выступает пробивка отверстий, так как возможно образование двойной дуги и выход плазмотрона из строя.
Помните, что инструмент для резки металла при пробивке должен над поверхностью детали подниматься на 20 – 25 миллиметров. В рабочее положение плазмотрон опускается после того, как лист будет насквозь пробит. Если вы пробиваете отверстия в листах, которые имеют большую толщину, рекомендуется использовать защитные экраны, имеющие отверстия диаметром 10-20 миллиметров. Экраны необходимо помещать между плазмотроном и изделием.
При резке алюминия с использованием аргоноводородной смеси для увеличения стабильности горения дуги содержание водорода не должно быть больше 20%. Резку меди принято выполнять с применением водородосодержащих смесей. Латунь нуждается в азотоводородной смеси или азоте. После резки медь в обязательном порядке нужно зачистить на глубину 1-1,5 миллиметра. Но не это требование совсем не обязательно для латуни.
Лазерная резка металла
Резка лазером является принципиально новым видом обработки металла, который отличается крайне высокой точностью и производительностью. Подобные режущие станки в мире металлообработки совершили революцию, сделав процедуру создания сложных металлических конструкций проще, быстрее и доступнее по цене. Лазерная резка в наше время уверенно вытесняет другие разновидности обработки металлических заготовок и становится все более популярной.
Сущность технологии
Технология лазерной резки металла своими руками на сегодняшний день - одна из самых прогрессивных технологий в создании разных деталей из листовых материалов. Процедура хороша своей универсальностью, потому что она позволяет работать с любыми материалами - металлического и неметаллического происхождения.
Лазерный луч является узконаправленным световым потоком маленького диаметра, что обладает высокой интенсивностью. Если лазерный луч навести на металлическую поверхность или другой твердый объект, изделие нагреется до высокой температуры. Её достаточно, чтобы металл начал плавиться в точке контакта. Но вместе с этим участки поверхности, которые прилегают к лучу, остаются горячими, но не повреждаются.
Двигая по поверхности луч, можно создавать очень тонкую качественную линию резки металла с идеально тонкими краями, несмотря на толщину обрабатываемого металла. Площадь лазерного потока, который попал на плоскость, исчисляют буквально квадратными микронами. Но вместе с этим при лазерной резке плотность энергии, которая направляется на металл, чрезмерно высока, что и служит причиной возникновения области разогрева.
В результате локально совершается расплав металла, который сопровождается уносом молекул вещества. Аппараты для лазерной резки представляют собой обычные координатные столы, что сопрягаются с головкой, которая управляется микропроцессором станка и которая перемещается по заданной программе над поверхностью обрабатываемого листа.
Могут выпускаться станки лазерной резки специального назначения, к примеру, пользуются популярностью в последнее время лазерные станки для труб, что являются пригодными для любых профилей. При этом вы можете провести обработку сразу по всей длине детали. Это достаточно эффективный метод, который обеспечивает жесткий контроль геометрии резки при использовании лазерного станка.
Достоинства лазерной технологии
К несомненным преимуществам лазерной технологии относят:
- полное отсутствие физических деформаций и брака при работе станка;
- возможность функционирования станка с пластичными металлами;
- отсутствие на поверхности готового изделия микротрещин;
- прецизионная точность обработки лазерного станка;
- высокая скорость работы;
- малая толщина реза;
- безотходность станка;
- высокий уровень автоматизации процесса лазерной резки;
- приемлемая стоимость резки металла.
Использование лазерной резки
Работа на лазерном станке происходит при помощи прожигания листового материала насквозь лучом лазера. Благодаря отсутствию прямого контакта детали и режущей головки оборудование позволяет обрабатывать безопасно хрупкие изделия, с успехом справляется с твёрдосплавным материалом, легко обеспечивать скоростной раскрой тонколистовой стали.
Технология считается выгодной и в тех ситуациях, когда продукцию выпускают небольшими партиями, потому что исключаются затраты на изготовление дорогостоящих форм для литья. Оборудование способно справиться со сталью любого состояния и качества, хорошо работает с алюминием, сплавами алюминия, медью, латунью.
Очень существенным нюансом подобного технологического процесса выступает простота в отношении работы с плоскими и объемными деталями, а также сложными контурами.
Лазерная резка является одной из технологий, в рамках которых себестоимость продукта при создании сложных изделий почти не зависит от величины партии, что обрабатывается станком. Именно поэтому технологии лазерной резки широко применяются в частном строительстве и домашнем хозяйстве, при этом время до получения конечного результата минимально.
Гильотинная резка металла
Для качественного и быстрого раскроя металла используются специальные листовые ножницы - гильотины. Название подобных металлорежущих станков происходит от сходства работы ножниц со средневековым орудием казни. Но сегодня гильотинные ножницы применяются в безобидных целях.
Выбор листовых ножниц
Главными критериями выбора гильотины выступает вид производства: штучное или серийное, толщина листа металла, длина линии продольной резки металла и механическая прочность. Потребители зависимо от своих целей могут выбрать простые ручные или электромеханические гильотины. Многие модели листовых ножниц бывают дополнительно оборудованы промышленной электроникой и опциями, которые повышают производительность резки металла.
Несмотря на изобилие типов привода, у всех моделей гильотин одинаков принцип работы. Для начала размещается на рабочем столе разрезаемый лист по выставленным упорам между нижней и верхней ножами. Предварительно стоит поджать к столу гильотины лист металла прижимной балкой. Дальше перемещается верхний нож и осуществляется резка металла. Затем можно транспортировать готовые детали из зоны резанья металла.
Точность резания листов металла посредством гильотинных ножниц обеспечена прижимным механизмом листа. Резка, как правило, осуществляется по разметке или упору: на гильотинах принято устанавливать точные задние линейки, позволяющие добиваться высокой точности процедуры реза. Некоторые модели оснащены возвратным поддоном для сбора отрезанного металла.
Выбирая определенную модель ножниц, нужно точно продумать список востребованных функций, потому что не всегда преимущества работы состоят в большом их количестве, тогда как цена такого станка зависит от данного показателя напрямую. Для работы в домашних условиях вполне подойдет гильотина с набором только необходимых функций, многофункциональные ножницы требуются же на крупных производствах.
Виды гильотин
По принципу устройства листовые ножницы могут быть ручными, пневматическими, гидравлическими, механическими, автоматическими, а также сочетать одновременно несколько комбинаций. Ручные и пневматические гильотины относят к самым простым и используются для прямолинейной резки листов металла.
Гидравлические ножницы с электромеханическим приводом отличаются простотой в управлении и высоким уровнем труда, что можно отметить на видео о резке металла. Точность реза обеспечена регулировкой положения ножей. Огромной популярностью пользуются гильотинные гидравлические ножницы с автоматической или ручной регулировкой зазора, который образуется между ножами.
Использование гильотинных ножниц
Гильотины предназначены для резки в поперечном и продольном направлениях металлических листов, которые имеют разную толщину. Некоторые виды листовых ножниц способны резать круглый, квадратный или угловой металлопрокат. Основными характеристиками гильотин, которые используются для резки металла, считаются длина и максимальная толщина реза.
Использование гильотин позволяет получить точный срез материала без зазубрин и вмятин, при этом оборудование не повреждает полимерное покрытие и окраску металла. Зависимо от технических возможностей применяются гильотинные ножницы на массовых и индивидуальных производствах.
Прочитав нашу статью, вы ознакомились с основными видами резки листового металла. Напомнив ещё раз – гильотинная, лазерная, плазменная и газовая резка. Каждый из них имеет свои достоинства и недостатки. Помните, что каждый вид резки металла связан с использованием специального оборудования и инструмента, что требует от потребителя наличия определенных навыков и строжайшего соблюдения техники безопасности.
strport.ru
Фигурная резка металла: лазерная, плазменная
Фигурная резка позволяет создавать оригинальные и изящные рисунки на листах металла.
Фигурная резка металла осуществляется на станках, с которыми можно работать без специальных навыков.
Основными способами резки считаются плазменная, лазерная, гидроабразивная и гильотинная резка. Рассмотрим основные виды фигурной резки металла.
Лазерная технология
Лазерная технология является универсальной, так как дает возможность обрабатывать любые металлические сплавы, ведь на станке устанавливаются определенные параметры для каждого металла.
Главной особенностью лазерной резки является отсутствие контакта металла и режущего устройства.
Лазерная резка материала осуществляется тонким сфокусированным световым лучом, благодаря которому металлический лист нагревается и проплавляется насквозь.
Преимуществами лазерной резки являются:
- минимальные затраты;
- безопасность;
- отсутствие деформации материала;
- возможность вырезания сложных контуров;
- отсутствие последующей обработки.
Оборудование бывает твердотелым и газовым. Твердотелый инструмент довольно простой в управлении и использовании.
Лазерный стержень производится из неодимового стекла, обладающего способностью пропускать импульсный лучевой поток мощностью 6кВт.
В газовом станке установлена газоразрядная трубка вместо стеклянного стержня.
Трубка заполняется углекислым газом, азотом, гелием. Электроимпульсы активизируют молекулы газа, которые начинают излучать энергию, превращающуюся в направленный пучок.
Мощность некоторых моделей оборудования составляет 20 кВт. Такое оборудование отличается дороговизной.
Видео:
Лазерная технология обработки листового металла дает возможность формировать любые сложные фигуры с минимумом отходов.
Благодаря точечному лучевому воздействию получаются гладкие и ровные кромки без неровностей не требующие дополнительной обработки.
Исключением для лазерной обработки является алюминий и сплавы алюминия с нержавейкой. Алюминий плохо поддается лазерной резке в связи с его отражающей способностью.
Плазменная технология
Фигурная плазменная резка листового металла дает возможность обрабатывать плазмой материал толщиной до 10 см.
Различные покрытия, ржавчина, загрязнения не снижают качество резки. Принцип работы следующий: в сопло плазмотрона подается газ под давлением.
Под действием электроимпульсов газ становится плазмой и образуется электрическая дуга между режущей головкой и стальным листом.
Резка осуществляется за счет струи плазмы. Основой метода является воздушно-плазменная дуга постоянного тока прямого действия.
В процессе резки плазмой металл раскаляется до 30000°.
К достоинствам плазменной резки можно отнести:
- вырезка фигур любой сложности;
- высококачественный и чистый разрез;
- обработка любых металлов;
- высокоскоростная обработка;
- отсутствие высокотемпературного воздействия, приводящего к деформации материала;
- безопасность.
По сравнению с резкой лазером, плазменная технология более производительная, менее затратная, имеет больший диапазон обрабатываемых материалов. Плазмой можно резать металл толщиной до 150 мм.
Видео:
К недостаткам плазменной резки можно отнести большую ширину резки, которая способна увеличиваться пропорционально силе тока плазменной дуги, а также конусность кромки, которая образуется из-за формы плазменной струи.
Плазменная резка является самой востребованной для вырезания фигур, так как сочетает в себе основные критерии по соотношению цена-качество.
Гидроабразивная технология
Гидроабразивная резка – это технология обработки тонкой высокоскоростной струей воды с добавлением частиц абразивного материала – абразива.
Оборудование для такой резки позволяет работать не только с металлом, но и с пластмассой, деревом, керамикой.
Следует отметить, что данным способом можно работать с любым металлом, не подверженным коррозии.
На станке есть возможность настроить глубину резки, что особенно актуально, когда требуется резка до определенной толщины, а не насквозь.
Процесс гидроабразивной резки происходит следующим образом: вода под давлением подается в смесительную камеру, в которой вода смешивается с абразивом.
Затем через твердосплавное сопло смесь подается на место среза. После чего струя гасится водой из специального резервуара.
Температура во время резки не превышает 90°.
Достоинствами данной технологии являются:
- экологичность;
- качественный рез;
- безопасность;
- отсутствие деформации материала из-за низких температур резки;
- высокая эффективность;
- высокоточная обработка;
- возможность разрезания металлов толщиной до 3 см, иных материалов – толщиной до 10 см;
- универсальность оборудования, подходящего для резки большого количества материалов;
- наличие оборудования, способного работать автономно, без человека.
Видео:
Однако резка гидроабразивом имеет и недостатки, которые касаются не самой технологии, а оборудования:
- Появление конусности. Срез металла вырезается неровно, а в виде воронки. Устранить конусность можно специальным оборудованием:
- Неизменная скорость. Скорость является одинаковой и для тонкого, и для толстого металла, что влечет за собой большие энергозатраты.
Резка ножницами
Ножницы по металлу довольно часто используются для фигурной резки металла.
Ножницы способны разрезать металл толщиной до 1 мм. Ручной инструмент представляет собой два режущих ножа, расположенных под определенным углом 7-12°.
Для фигурной резки используются криволинейные ножницы и пальцевые ножницы.
Также для фигурной резки применяются гильотинные ножницы, представляющие собой станок, который используется в промышленных условиях.
Такие ножницы имеют максимальную глубину резки до нескольких миллиметров толщиной. Станок может быть ручным и электрическим.
Видео:
При резке гильотинами срез получается ровным, без заусенцев.
Однако данным способом возможно вырезать не все контуры, сложные фигуры выполнить достаточно сложно.
Каждая их технологий фигурной резки металла имеет определенные достоинства и недостатки, что позволяет выбрать оптимальный вариант для каждого случая.
rezhemmetall.ru