Качественная пайка резцов в домашних условиях. Напайки на токарные резцы
Пайка резцов в домашних условиях: особенности
Каждый, кто занимается токарным делом, встречается с такой проблемой, как пайка резцов в домашних условиях. Это достаточно-таки нужная процедура, которая осуществляет напайку твердосплавных пластин на держатели токарных резцов, помогает закалить инструмент. В этом деле участвует высокочастотный ток или газовая горелка. Но для последней аппаратуры все же необходимо иметь хороший опыт.
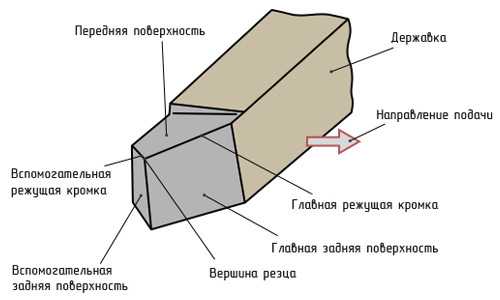
Элементы токарного резца.
Как решить проблему без специализированной техники?
Раньше использовался способ нагрева резцов при помощи контактной машины. Его отлично использовали дома. Пайка происходила посредством теплового воздействия электрического тока на проводник. Чтобы контролировать выделяемое тепло, необходимо просто регулировать величину электротока, сопротивление проводника и смотреть по времени, сколько он будет воздействовать на проводник.
Ориентируясь на эти три фактора, был разработан агрегат, представляющий собой трансформатор понижающего действия. Он имеет первичную и вторичную обмотки. Первая рассчитывается на 220 В, а вторая — на 2 В. Диаметр поперечного магнитного провода равен 50 кв.см. Сам трансформатор крепится на основание, в то время как на прокладке-изоляторе расположены шины контакта.
Конструкция сварочного инвертора.
Из листовой стали толщиной в 5 см выполнена основа трансформатора, которая имеет ножки. Также в данной конструкции присутствуют два окна, выполняющие роль вентиляции.
Для концов вторичной обмотки есть свои отверстия зажимов. Вся конструкция аппарата защищена специальным кожухом, который при помощи уголков крепится к основанию трансформатора. Одно из таких креплений имеет изоляционную колодку.
Вернуться к оглавлению
Различия и особенности видов пайки
Резцы могут соединяться посредством низко- или высокотемпературной пайки. Но если судить объективно, то их физическая природа особых отличий не имеет. Два металла соединяются между собой третьим, который называется припоем. Соединительный металл имеет температуру плавления ниже, нежели соединяемые элементы. Но в зависимости от того какую пайку выбрать, будут зависеть и характеристики полученного изделия.
Как понятно из названий, одним из отличий является температура плавления. Но это еще не все.
Таблица классов сварки.
- В первую очередь использование твердых припоев гарантирует более качественное и надежное соединение деталей, в отличие от мягких.
- Высокотемпературная пайка к тому же обладает более сильной термоустойчивостью соединений. Используемый для такой работы припой отличается высокой температурой плавления, поэтому и температурные нагрузки он может выдержать выше, причем не утеряв своих свойств. Но тут есть и свой нюанс, в такой пайке, который уступает низкотемпературной. В первом случае, под воздействием высоких показателей, могут возникать структурные изменения некоторых металлов. Например, чугунное соединение становится достаточно хрупким.
- Используя высокотемпературную пайку, приходится подбирать и соответствующие инструменты. Для такой процедуры необходимо достигать температуры в 1000 градусов. То есть паяльник уже не подойдет для такого процесса.
Если объединить все вышесказанное, то получается, что высокотемпературная пайка обеспечивает прочность и термоустойчивость соединения, но при этом требует более высококвалифицированного оборудования и умения производить достаточно сложную по технологии спайку. В то время как низкотемпературная пайка имеет более упрощенные требования, но и качество получаемых деталей несколько ниже.
Вернуться к оглавлению
Пайка твердыми припоями
Использование твердых припоев занимает промежуточную позицию между низкотемпературной пайкой и уже сваркой.
Схема пайки твердым припоем.
Они применяются в тех случаях, когда важным становится прочность получаемых соединений и целостность структуры металлов. В таком процессе часто используют твердосплавные пластины, которые при соединении не портят изначальную геометрию конструкции.
Такую технологию применяют для ремонта холодильных или теплообменных систем, стальных или медных трубопроводов и т.д. Ее применяют и в автомобильном ремонте для починки радиаторов, двигателя, трансмиссий, кузова и других аналогичных деталей.
Если возникает необходимость отремонтировать изделия, которые во время эксплуатации поддаются воздействиям высоких температур (например, самовар на дровах), то высокотемпературная пайка просто необходима.
Что касается оборудования, то в этом случае требуется техника, которая способна дать температуру выше необходимой для плавления соединяемых деталей. Средний диапазон может варьироваться от 450 до 1200 градусов, при условии, что вся процедура будет производиться дома. Такие показатели имеют газовые горелки, индукторы и печи.
Вернуться к оглавлению
Виды применяемых припоев
Для того чтобы спаять резец, можно использовать и медь, хотя как альтернативу можно использовать его и с другими металлами (цинк, серебро, кремний, олово и т.д.). Каждый из таких компонентов снижает температуру плавления.
Но следует отметить, что такие припои не рекомендуется использовать, если работа предстоит со сталью или чугуном, так как в этом случае образуются фосфиты, которые влияют на прочность соединения. Такой шов будет очень хрупким, и, при оказании вибрационного или изгибающего давления, соединение может деформироваться или просто лопнуть.
Вернуться к оглавлению
Как спаять резцы самостоятельно?
Для того чтоб выполнить пайку, необходимо придерживаться следующих шагов:
- В первую очередь необходимо зачистить все металлические элементы. Удаляется окисная пленка.
- Державку резца устанавливают на шинах трансформатора. Зона, которая будет поддаваться пайке, должна быть предварительно обработана флюсом. После этого начинает работать припой.
- При помощи пинцета припой вставляется промеж краев, которые требуют соединения. В конкретном случае лучше с этой целью использовать лист латуни.
- Во время работы агрегата зона контакта будет нагреваться. Это способствует расплавлению металла, а как только этот процесс завершится, контакт распадется, и, соответственно, процесс остановится. Поэтому, чтоб пайка была беспрерывной, всю работу производят в импульсном режиме, при этом нагрузка на обмотки должна подаваться постепенно.
Само прогревание производят по всей поверхности, плавно двигаясь из стороны в сторону. Припой должен приобрести цвет от темно-вишневого до светло-вишневого, который будет указывать на разогрев до необходимой температуры.
Визуально контролируя весь процесс, необходимо аккуратно наносить весь припой. Следует знать, что державка нагревается со скоростью 80-100 градусов в секунду. Используя данный метод для соединения резцов, можно быть уверенным в получении отличного качества.
Если флюс был нанесен в достаточном количестве, то припой легко растечется. После окончания выполнения работ швы зачищаются.
Считается, что высокопробное соединение — то, что не превышает 0,1 мм. Как понятно, ничего сложного в домашней пайке нет. Главное, чтоб под рукой имелись все необходимые инструменты и материалы. Но нужно помнить, что во время всего процесса следует соблюдать правила личной безопасности, так как высокие температуры могут навредить паяльщику.
moiinstrumenty.ru
Напайка твердосплавных пластин. | МеханикИнфо
Напайки твердосплавные. Напайка твердосплавных пластин. 4.13/5 (82.50%) проголосовало 8
3-й ЭТАП — НАПАЙКА ПЛАСТИНОК.
Этот этап является наиболее ответственным, так как при неправильном его проведении, во время работы резца, пластинки твердого сплава могут отскакивать или ломаться, вследствие образовавшихся при напайке трещин.
ПРИПОИ.
Припои, применяемые для напайки пластинок твердого сплава, должны иметь температуру плавления на ~ 300° выше температуры, возникающей в процессе резания, сохранять прочность и пластичность при температуре резания, обладать хорошей жыдкотекучестью и обеспечивать быстрый отвод тепла от пластинки твердого сплава к стержню резца.
Рекомендуется применять следующие припои:
Наименование припоя | Состав | Температура плавления | Область применения |
Медно-никелевый (мельхиоровый) | Медь — 68.7%Никель — 27,5%Алюминий — 0,8%Цинк — 3,0% | 1170° | Для работ с большими нагрузками и нагревом режущей части инструмента до 900° |
Электролитическая медь | Медь — 99.9%Примеси — 0,1% | 1083° | Для работ с большими нагрузками и нагревом режущей части инструмента до 700° |
Латунно-никелевый | Медь — 68,0%Цинк — 27,0%Никель — 5,0% | 1000° | |
Латунь Л—62 | Медь — 62.0%Цинк — 38,0% | 900° | Для работ со средними нагрузками и нагревом режущей части инструмента до 600° |
Серебрянный ПСР-45 (ОСТ—2982) | Серебро — 10%Медь — 53%Цинк — 37% | 720° | Для припайки пластинок из высокотитановых твердых сплавов марок Т30К4 |
ФЛЮС.
Чтобы обеспечить хорошую смачиваемость и растекание припоя по поверхностям спаиваемых деталей, для удаления окислов и предохранения от окисления, применяют флюс.
В качестве флюса рекомендуется бура, которую нужно предварительно расплавить, истолочь и просеять через мелкое сито. Хранить буру нужно в закрытых сосудах, предохраняющих ее от влаги и загрязнения.
Бура применяется либо в виде порошка, либо в виде пасты, состоящей из трех весовых частей буры и двух частей вазелина.
Латунные припои паяют с флюсом, который состоит на половину из борной кислоты и на половину из буры. Температура плавления таких флюсов 750 ºС.
При напайке серебряными припоями следует применять флюс, состоящий из 43% фтористого кальция и 57% борной кислоты.
КОМПЕНСАЦИОННЫЕ ПРОКЛАДКИ.
Компенсационные прокладки необходимы для уменьшения термических напряжений. Они возникают при напайке твердосплавных пластинок, различной толщины и размеров, на стержни резцов. Прокладки больших размеров применяют из низкоуглеродистых сортов стали или пермалоя (железо-никелевый сплав). Большим спросом пользуются прокладки при напайке наиболее хрупких высокотитановых твердых сплавов.
Прокладки имеют вид тонкой сеточки или фольги, толщина которых составляет от 0,2 до 0,5 мм. На них имеются отверстия с диаметрами от 1 до 2 мм, расположенные в шахматном порядке.
Компенсационные прокладки имеют несколько достоинств:
Повышают прочность напайки;
Разгружают место спая от напряжений (возникающие при остывании резца).
СПОСОБЫ ПАПАЙКИ.
Нагрев стержня и пластинки и расплавление припоя могут осуществляться следующими способами:
а) в пламенных, газовых или электрических муфельных печах;
б) токами высокой частоты;
в) контактным способом, на стыковых сварочных аппаратах;
г) пламенем ацетилено-кислородной горелки.
Для уменьшения напряжений, возникающих в твердом сплаве при охлаждении после напайки, рекомендуется напаивать высокотитановые сплавы Т60К6 и Т30К4, особенно склонные к трещинообразованию, только по одной опорной плоскости; боковые поверхности пластинки предохраняются от припаивания применением прокладок из слюды или графита.
Напайки твердосплавные. Напайка твердосплавных пластин.
НАПАЙКА В ПЛАМЕННЫХ, ГАЗОВЫХ ИЛИ ЭЛЕКТРИЧЕСКИХ ПЕЧАХ.
Предварительный нагрев стержня.
Головку резца медленно нагревают до температуры плавления буры ~ 800°С.
Подготовка резца к напайке.
Нагретое гнездо посыпают бурой, затем резец вынимают из печи и металлической щеткой очищают образовавшийся жидкий слой шлака на гнезде.
Затем гнездо вновь посыпают бурой, после чего в него устанавливают пластинку твердого сплава, сверху кладут соответствующее количество припоя и вновь посыпают бурой, так, чтобы бура покрыла сплошным слоем припой и всю пластинку.
Эту операцию нужно производить быстро, чтобы стержень не успел охладиться.
Расплавление припоя.
Головку подготовленного к напайке резца помещают в окно печи с температурой 1200° и выдерживают до расплавления припоя.
Прижим пластинки.
Как только припой расплавится и затечет под пластинку, резец быстро вынимают из печи, кладут на подставку, остроконечным стержнем поправляют пластинку в гнезде и плотно прижимают её к опорным поверхностям гнезда. Прижим длится несколько секунд, до затвердения припоя.
Охлаждение резца.
Во избежание резкого охлаждения, ведущего к появлению трещин в пластинке твердого сплава, резец помещают в ящик с крупкой древесного угля или с сухим подогретым песком, где резец медленно остывает.
Значительно лучше резцы, сейчас же после напайки, помещать в камерную печь, нагретую до температуры 250°. Резцы выдерживаются в печи в течение 5—6 часов, после чего охлаждаются вместе с печью.
Очистка резца.
После напайки резец очищают от окалины на пескоструйном аппарате.
НАПАЙКА КОНТАКТНЫМ СПОСОБОМ НА ЭЛЕКТРОСВАРОЧНЫХ АППАРАТАХ.
Контактная напайка производится на стыковых электросварочных аппаратах, которые оборудуются несложным приспособлением, состоящим из 2-х плоских контактных губок, набора торцевых контактов, блока с грузом и педальной кнопки к контактору аппарата. Контакт подводится на 2-3 мм ниже пластинки твердого сплава.
Операция напайки очень похожа на печную и заключается в следующем:
1.Стержень резца зажимается в контактных губках таким образом, чтобы обеспечить возможно большую поверхность соприкосновения торца резца с поверхностью торцевого контакта.
2.Торцевой контакт подводится и прижимается к стержню.
3.Гнездо для пластинки посыпают бурой, а затем путем периодического включения и выключения тока нагревают головку резца до температуры плавления буры (800°). После расплавления буры, металлической щеткой очищают гнездо от окислов и шлаков и опять посыпают бурой; сверху укладывают пластинку твердого сплава, поверх неё припой и сверху опять густо посыпают бурой.ПРАВИЛЬНО. Контакт не касается пластинки твердого сплава
НЕПРАВИЛЬНО. Контакт касается пластинки твердого сплава.
4.Включается ток для расплавления припоя, после чего ток выключается, а пластинка прижимается к гнезду остроконечным металлическим стержнем.
5.Резец освобождается от зажимов и помещается в ящик с крупкой древесного угля или с сухим подогретым песком для медленного остывания.
6.Остывающий резец очищается от окалины на пескоструйном аппарате.
ГАЗОВАЯ НАПАЙКА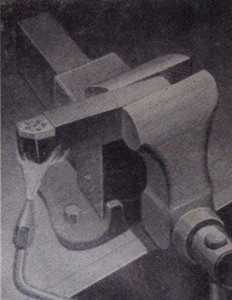
При этом способе источником тепла является ацетилено-кислородная горелка. Следует отметить, что этот способ применяется лишь вслучае отсутствия других, описанных выше, источников тепла, либо когда необходимо напаять небольшое количество инструментов.
Пластинка из твердого сплава нагревается с помощью пламени, направленного на стержень резца. В пламени горелки должно присутствовать большое количество ацетилена.
Процесс напайки аналогичен описанному выше печному.
Напайка этим методом должна быть поручена сварщику с достаточным опытом работы.
При любом способе напайки, в результате её, припой в виде тонкой (до 0,1 мм) сплошной пленки должен соединять все поверхности соприкасания пластинки и гнезда.
Пластинка не должна быть смещена в гнезде.
Если статья оказалась вам полезна — поделитесь ею в социальных сетях.
mechanicinfo.ru
Пайка резцов что нужно знать об устройстве аппарата и принципе работы
Пайка в домашних условиях
Пайка резцов – необходимая процедура, в которой периодически нуждается токарное дело. Для того чтобы напаять твердосплавные пластины на державки токарных резцов, осуществить локальную закалку инструмента, пайку твердыми припоями небольших деталей, применяется нагрев высокочастотными токами, либо пламенем газовой горелки.
Несмотря на то, что аппаратура ТВЧ показывает отличные результаты во время пайки данных элементов, она достаточно громоздка и дорогостоящая, что делает ее практически недоступной для работы в домашних условиях. Относительно газовой горелки, то она должна применяться по большей части профессиональными сварщиками по всем необходимым правилам.
Забытый способ
Однако до сегодняшнего дня дожил еще дин способ обработки резцов путем нагрева, который мы все начали забывать – пайка на контактных машинах. Данный способ является оптимальным для обработки деталей домашних условиях.
Особенности конструкции и принцип действия
Принцип осуществления способа заключается в тепловом воздействии электротока на проводник. При этом количество тепла, выделяемого во время работы в домашних условиях, зависит от величины электрического тока, электрического сопротивления проводника, а также времени его воздействия на проводник.
Опираясь на данную зависимость, был создан специальный аппарат, который представляет собой понижающий трансформатор. Благодаря данному аппарату становится возможной пайка рассматриваемых элементов, воссоздание качественной детали и т. п. Первичная обмотка трансформатора рассчитана на 220 В, а вторичная – на 2 В. Поперечное сечение магнитопровода составляет 50 сантиметров квадратных. Трансформатор закреплен на основании, тогда как контактные шины вторичной обмотки аппарата находятся на прокладке-изоляторе.
Основа трансформатора изготовлена из листовой стали, толщина которой составляет 5 сантиметров. В основание снизу ввернуты ножки. Также основание оборудовано двумя окнами, представляющими собой две вентиляции (предназначением: выход болтов крепления контактных шина текстолитовом изоляторе). Стоит отметить, что отверстия, расположенные по краям изолятора, служат для его крепления к основе.
Концы вторичной обмотки аппарата заводятся в отверстия зажимов. Трансформатор защищен кожухом, а также прикреплен к основанию уголками. К одному из уголков приспособлена изоляционная колодка.
Последовательность работы
Последовательность следующая:
- Державка резца располагается на шинах аппарата. Далее в работу вступает припой.
- Между поверхностями, которые нужно соединить, помещается припой (посредством пинцета). В данном случае припой – лист латуни.
- Зона контакта при включении трансформатора нагревается, тем самым заставляя металл плавиться, после чего контакт нарушается, и, как следствие, контакт прекращается. Предотвращение подобного следующее: работа должна производиться в прерывистом режиме, плавно подается нагрузка на обмотки при помощи ЛАТРа.
Припой наносится аккуратно, контроль за работой ведется исключительно визуально. Скорость нагрева державки в процессе пайки составляет 80-100 гр./сек. Пайка резцов подобным методом дает отличные результаты. Качественное соединение не должно превышать 0,1 миллиметра. Благодаря приспособлению подобная работа становится возможной в домашних условиях.
Похожие статьиgoodsvarka.ru
Пайка резцов в домашних условиях — studvesna73.ru
Напайка твердосплавных пластинок
Подготовка державки или корпуса к пайке заключается в качественной обработке пазов под твердосплавные пластинки. Поверхности пазов должны иметь ровную плоскость, без впадин и выпуклостей, 4—5-го класса чистоты.
Фрезерование пазов и затылков на корпусе производится до напайки пластинок.
При фрезеровании открытых пазов и небольшой длине пластинок рекомендуется оставить перемычку толщиной 1—1,5 мм по передней плоскости паза (рис. 63, а). В этом случае можно закреплять пластинки путем подчеканки по передней плоскости перемычки. В процессе заточки инструмента по передней поверхности перемычку надо удалить. Ширина паза должна соответствовать толщине пластинки. Зазор между плоскостями паза и пластинкой не должен быть более 0,05—0,15 мм. Расположение дна паза должно обеспечивать припайку пластинок под необходимыми углами с тем, чтобы режущие пластинки были использованы более рационально. Так, у резцов паз следует располагать под углом, величина которого больше переднего угла резца на 3—59deg;. Угол наклона режущей кромки к также должен быть учтен при изготовлении паза в корпусе инструмента.
Рис. 63. Открытый паз с перемычкой и крепление винтовой пластинки перед пайкой
Открытый паз для винтовых пластинок не имеет перемычки, так как крепление их осуществляется специальными штифтами (рис. 63, б). Для этого перед винтовой пластинкой 1 засверливается отверстие 3, в которое забивается штифт 2, работающий как клин. Диаметр штифта должен быть не менее 3 мм, так как штифт меньшего диаметра перегревается во время пайки, что вызывает появление трещин на пластинках. Процесс пригонки пазов значительно упрощается, если в паз ввести технологический вкладыш толщиной 1,5—3 мм из углеродистой конструкционной стали. Вкладыш в пазу закрепляют кернением. В этом случае пластинки твердого сплава устанавливают в паз без удара. При напайке инструмента на установках т. в. ч. не допускается крепить пластинки к корпусу проволокой, так как в местах касания проволоки к пластинкам могут возникнуть трещины.
Припои и флюсы. Выбор припоя зависит от инструментального материала и условий работы инструмента.
Припои, рекомендуемые для пайки твердосплавных инструментов
Приведенные в табл. 86 марки припоев нашли применение при изготовлении твердосплавных режущих инструментов. Наиболее широко в качестве припоя используется медь. Если нагрев инструмента в процессе эксплуатации исключается, медь обеспечивает прочность паяных соединений твердого сплава со сталью 16—18 кГ/см 2 ; при температуре 400—6009deg; С прочность паяных соединений снижается до 3—4 кГ/см 2. Следовательно, медь можно применять в качестве припоя для пайки твердосплавных инструментов, которые работают при малых нагрузках и невысоком (до 300° С) нагреве инструмента в процессе его работы.
Рекомендации для выбора припоя в зависимости от условий работы инструмента приведены в табл. 87.
В процессе пайки флюсы действуют как растворители и поглотители окислов и грязи, препятствующие смачиванию поверхности. Кроме того, они предохраняют при нагреве поверхность от окисления и увеличивают жндкотекучесть расплавленного припоя.
При пайке твердосплавных инструментов в качестве флюса находят применение обезвоженная бура, борный ангидрид и их смеси. Эти флюсы растворяют окислы многих металлов, но они недостаточно эффективны при удалении тугоплавких окислов, особенно титана.
При пайке режущих инструментов, оснащенных твердыми сплавами группы ТК или ТТК, для лучшего растворения окислов титана во флюс вводят фториды кальция, натрия, калия или лития. С этой целью ВНИИ разработан флюс, содержащий 6&9mdash;73,2% буры, 21—22,8% борного ангидрида и 5—10% фтористого кальция.
Припои, применяемые в зависимости от условий работы инструмента
В табл. 88 приведены данные растекаемости припоя ПрМНКМц68-4-2 под действием различных флюсов. Из таблицы видно, что растекаемость припоя под действием флюса ВНИИ в 10 раз больше по сравнению с растекаемостью буры или борного ангидрида.
Химический состав, температура плавления флюсов и растекаемость припоя ПрМНКМц 68-4-2
Подготовка припоя и флюса к пайке. Если припой для пайки применяется в виде фольги, то его разрезают на куски в соответствии с размерами паяемого инструмента. Исходя из нормы расхода припоя 0,35— 0,40 г на 1 см 2 поверхности соединения, устанавливают размеры кусков фольги. Флюс в этом случае применяется в виде порошка. Норма расхода флюса 0,15 г на 1 см 2 поверхности соединения.
Для изготовления 1 кг флюса, состоящего из 6&9mdash;73% буры, 21— 22% борной кислоты и 5—10% фтористого кальция, необходимы 1,3 кг буры, 0,55—0,6 кг борной кислоты и 0,1 кг фтористого кальция. Составленную шихту перемешивают, засыпают в коробку из окалиностойкой стали Х18Н9 и расплавляют в электрической печи при температуре 850—9009deg; С. Затем после расплавления и тщательного перемешивания расплава его охлаждают до затвердевания, дробят и размалывают в шаровых или вибрационных мельницах, получая флюс в виде порошка.
Для улучшения качества пайки и повышения производительности применяют припой в виде таблеток. Таблетизированный припой состоит из 75—80% припоя и 25—20% флюса. Технология изготовления таблеток проста. Приготовленные стружку припоя и флюс взвешивают в соотношении 4. 1 (по весу), засыпают в шаровую или вибрационную мельницу и перемешивают в течение 2—2,5 ч.
Для прессования таблеток используют автоматический пресс ударного типа с автоматической подачей порошковой смеси в матрицу. Размеры таблеток: диаметр 10 и 12,5 мм, толщина 2 мм; вес таблеток 0,8— 1,25 г. Норма расхода таблетизированного припоя 0,5 г на 1 см 2 паяемой поверхности.
Пайка режущих пластинок. По способу нагрева пайка режущих инструментов делится на следующие виды: пайка газовым пламенем, в печах, индукционным нагревом и пайка погружением в ванну с расплавленной солью. Пайка в пламени газовой горелки — трудоемкий процесс, требующий навыка, поэтому он не получил широкого применения .
Пайка в печах с безокислительной средой. Этот способ является наиболее прогрессивным. Электрическая печь состоит из камеры нагрева, где поддерживается температура 1100° С, камеры охлаждения, наружные стенки которой охлаждаются проточной водой, приемной и выпускной камер. Для создания в печи безокислительной газовой среды применяется очищенный от примесей водород либо азот, полученный при диссоциации аммиака. Печь оборудуется контрольной аппаратурой: манометром для контроля давления газа в печи, расходомером для контроля расхода газа и термопарой с гальванометром для контроля температуры в печи и диссоциаторе.
Подготовка пластинок твердого сплава и корпуса инструмента под напайку в электрической печи с газовой безокислительной средой производится следующим образом. Гнездо корпуса посыпают флюсом, кладут фольгу и пластинки твердого сплава и закрепляют их в этом положении асбестовым шнуром. Подготовленный таким образом инструмент укладывают на лист окалиностойкой стали и погружают в печь, нагретую до 850—9009deg; С. Температуру в печи постепенно повышают до 1150° С. После 10-минутной выдержки инструмента при 1150°С снижают температуру до &509deg; С и инструмент помещают в камеру охлаждения. Инструмент охлаждается с 950 до 200—3009deg; С, затем его извлекают из камеры.
Пайка индукционным нагревом. Наиболее распространенным и производительным является способ напайки режущих пластинок на высокочастотных установках. При изготовлении большого количества однотипных инструментов применяется ручная непрерывная пайка с подачей инструментов без снятия напряжения с индуктора. При этом способе инструменты помещают в многоместный индуктор одни за другим и по завершении пайки их извлекают и заменяют новыми. В тот момент, когда инструмент 1 (рис. 64) ранее других помещенный в индуктор, нагревают до температуры пайки, все следующие за ним инструменты 2 и 3 еще находятся на предварительном подогреве. Таким образом, каждый из инструментов нагревается до температуры пайки на несколько секунд позже предыдущего.
При изготовлении инструментов небольшими партиями напайка пластинок производится в одноместных индукторах. Форма индуктора зависит от формы и размеров напаиваемого инструмента. Так, например, если корпус инструмента имеет открытый паз (дисковые фрезы, ножи, резцы и т. д.), пластинки напаиваются в каждый паз отдельно в петлевых индукторах (рис. 65, а, б). В этом случае опорную плоскость паза зуба фрезы посыпают флюсом и подогревают в индукторе до температуры 800—8509deg; С.
Рис. 64. Схема непрерывной пайки резцов на двухпозиционном станке
После расплавления флюса поверхность паза очищают от окислов и вновь посыпают флюсом, на который укладывают припой. Слой припоя опять посыпают флюсом и сверху кладут режущую пластинку. Затем зуб фрезы вводят в индуктор для окончательного нагрева до температуры плавления припоя. После расплавления припоя металлическим стержнем исправляют положение пластинки в пазу и прижимают ее к опорным плоскостям.
Рис. 65. Типы индукторов
В корпусах инструментов с открытыми и полузакрытыми пазами с расстоянием между зубьев более 20 мм (зенкеры, развертки и фрезы) напайка пластинок производится в каждый
паз отдельно в петлевом индукторе или круглом двухвитковом индукторе с эксцентричным расположением корпуса для индивидуального нагрева каждого зуба (рис. 66, а и б).
В корпусах инструмента с открытыми и полуоткрытыми пазами с шагом между зубьями менее 20 мм (зенкеры, развертки, подрезки, фрезы концевые) напайка пластинок к корпусу осуществляется одновременно на всех зубьях. Корпус инструмента устанавливается в индукторе в вертикальном положении (рис. 66, в) или же в центрах в горизонтальном положении (рис. 66, г)
Инструменты после напайки охлаждаются в песке, подогретом до температуры 150—2009deg; С или в камерной печи. Окалина и остатки флюса удаляются пескоструйной очисткой.
Рис. 66. Примеры пайки
Термическая обработка корпуса. В исключительных случаях напайку пластинки совмещают с термической обработкой корпуса инструмента, так как повторный нагрев инструмента под закалку снижает прочность паяного шва. Если напайка пластинок на корпус производится т. в. ч. то сразу же после окончания напайки рабочую часть инструмента прогревают в индукторе до температуры закалки. После этого рабочую часть инструмента охлаждают в селитровой ванне таким образом, чтобы пластинки находились над зеркалом ванны. При охлаждении рабочей части корпуса до 500° С инструмент полностью погружают в ванну, а затем подвергают отпуску.
Пайка погружением. При этом способе напайки инструменты сначала подогревают до температуры 350—4009deg; С над зеркалом стального (окалиностойкого) тигля с расплавленной бурой, нагретой до 850° С (рис. 67, а), а затем погружают в тигель и выдерживают их до полного прогревания корпуса с пластинками (из расчета 12 сек на 1 мм среднего сечения инструмента). Нагрев тигля с бурой осуществляется в ванне с расплавленным хлористым барием.
После флюсования и нагрева до температуры 850° С инструменты переносят в другой тигель (рис. 67, б), в котором находится расплавленный припой, нагретый до температуры 1050° С. Инструменты в тигле с припоем выдерживают из расчета 6 сек на 1 мм среднего сечения инструмента. За это время корпус и пластинки должны покрыться тонким слоем припоя. Затем инструменты медленно вынимают из тигля и охлаждают на воздухе до затвердевания припоя. После этого инструменты переносят в печь и выдерживают в ней в течение 8 ч при температуре 200—2509deg; С, а затем медленно охлаждают вместе с печью.
При пайке инструментов погружением в расплавленный припой необходимо следить за тем, чтобы не было натеков на торце и боковой поверхности. Натеки появляются по следующим причинам: низкая температура ванны с припоем и недостаточный прогрев ее; загрязненность припоя железом; слишком быстрое извлечение инструмента из прйпоя. Охлажденные инструменты кипятят в 10-процентном растворе каустической соды, очищают на пескоструйном аппарате и направляют на дальнейшую механическую обработку.
Контроль качества пайки осуществляется внешним осмотром, а также с помощью специальных инструментов и приборов. Внешним осмотром проверяют правильность расположения пластинки на державке, отсутствие грубых завалов и забоин на режущих кромках, выколов и трещин. Мелкие дефекты пайки трудно обнаружить не вооруженным глазом, поэтому паяные соединения осматривают с помощью микроскопа КМ-60.
Для выявления трещин используется люминесцентный метод.
Рис. 67. Схема пайки в соляной ванне
Применение его основано на способности свечения некоторых материалов при ультрафиолетовом облучении в присутствии масел, обладающих способностью проникновения в мелкие поры и трещины.
Для проведения люминесцентного контроля инструмент очищают от флюса и излишков припоя, затем погружают на 4—5 мин в раствор следующего состава (в мл)
После извлечения из раствора инструмент промывают в проточной воде и сушат в струе сжатого воздуха. Затем пластинки твердого сплава покрывают тонким слоем талька, излишки которого удаляют легким встряхиванием инструмента. После этого инструмент подвергают ультрафиолетовому облучению в затемненном помещении. Трещины, имеющиеся на поверхности твердого сплава и паяного шва, при облучении ярко светятся, что облегчает отбраковку некачественного инструмента.
Метод цветных красок основан на способности цветных красителей проникать в мелкие поры и трещины и, кроме того, на их способности изменять цвет других красителей.
Для выявления трещин в твердосплавном инструменте находят применение красная и белая краски. Красная краска состоит из 85 мг бензола, 5 мг авиационного масла МК8 и 1 г темно-красного красителя «Судан 4». При изготовлении красной краски «Судан 4» растворяют в масле МК8, затем в раствор вливают бензол и тщательно его размешивают до полного растворения.
Белая краска состоит из 70 мг коллодия, 10 мг ацетона, 20 мг бензола и 5 г густотертых белил. Белую краску изготовляют следующим образом: 5 г белил и 20 мг бензола тщательно смешивают и в эту смесь вливают 70 мг коллодия.
Способ применения метода цветных красок следующий. На обезжиренные поверхности пластинок твердого сплава наносят красную краску и сушат в течение 1 мин. Затем наносят второй слой этой краски и сушат до полного его высыхания. После этого слой красной краски удаляют тампоном, смоченным в растворе, содержащем 30 мл керосина и 70 мл трансформаторного масла, и на очищенную поверхность наносят тонкий слой белой краски. Если пластинка твердого сплава имеет трещины, то на белой краске появляются красные линии, копирующие расположение трещин на поверхности пластинки.
Смотрите также
-
- 0
-
мутный 01 Май 2013
уважаемые коллеги ,может кто сталкивался со следующей проблемой-при пайке токарных резцов некоторые сплавы не могу спаять(марку сплава не знаю,токарь который подкинул мне эту работу говорит что это самый твердый),сама напайка не облуживается и как бы всплывает над латунью.пробывал все режимы,безрезультатно.остальные напайки паяются отлично.паяю ацителеном,латунью и бурой
-
- 2
-
папаша 01 Май 2013
вот тут можно глянуть
-
- 1
-
аргонавт 01 Май 2013
Есть такой проблемм. Напайка с твердо сплавов тоже имеет окислённую поверхность. которую желательно снять в местах припоя на алмазном наждаке. Обычно при соблюдении температурного режима всё и так без проблем паялось. Но как уже писал ранее пришлось паять вк к 40 х 13. они по определеню не совместимы для твёрдого припоя. Температурный режим для нанесения буры только начинает краснеть. Чуть больше. всё заново зачищай. С вк если не пристаёт припой — не любит перегрев. Система одна. все напайки на резцы раньше не кто окислы не удалял. их в день много паяли. Но несколько раз было что не вышло запаять. возможно эти то же с такого материала.
-
- 0
-
ARGONIUS 02 Май 2013
Попались мне как то раз какие то каадратные твердосплавные пластинки, сменные, от резца с прижимным винтом. Тоже сколько ни старался- латунью и борной припаять не мог. Не залуживается и всё тут. Другие до этого без проблем.
-
- 1
-
LamoBOT 02 Май 2013
Для напайки твердосплавных пластин на державки токарных резцов, локальной закалки инструмента, пайки твердыми припоями мелких деталей используют нагрев токами высокой частоты или пламенем газовой горелки. Однако аппаратура ТВЧ громоздка и дорого стоит, она не для домашней мастерской или школьного кружка. Применить же газовую горелку по всем правилам может только сварщик высокой квалификации.
Но есть и еще один, почти забытый в наше время способ нагрева — на контактных машинах. Он наиболее приемлем в домашней, школьной, колхозной или совхозной мастерской, в техническом кружке.
Суть его в тепловом воздействии электрического тока на проводник. Выделяемое при этом количество тепла зависит от величины тока, времени его действия на проводник и электрического сопротивления последнего.
С учетом этой зависимости мы разработали аппарат, представляющий собой понижающий трансформатор, первичная обмотка которого рассчитана на 220 В, вторичная — на 2 В. Площадь поперечного сечения магнитопровода около 50 см 2. Трансформатор закреплен на основании, а контактные шины вторичной обмотки — на прокладке-изоляторе.
Основание аппарата изготовлено из листовой стали толщиной 5 мм. Снизу в него ввернуты ножки. В основании прорезаны два окна: меньшее — для вентиляции, большее — для выхода болтов крепления контактных шин на текстолитовом изоляторе толщиной 10 мм. Отверстия по краям изолятора служат для его крепления к основанию.
Концы вторичной обмотки трансформатора заведены в отверстия зажимов и зафиксированы болтами (пазы зажимов позволяют деформировать их при затяжке и обеспечивать тем самым надежный электрический контакт).
Трансформатор укрыт защитным кожухом и прикреплен к основанию уголками 25X25 мм. К одному из верхних уголков привинчена изоляционная колодка — для соединения проводов первичной обметки с питающим шнуром и включателем аппарата.
Так как конструкторы-любители не часто имеют все необходимое для повторения описанной самоделки, рекомендуем начать изготовление аппарата с подбора пакета пластин трансформаторного железа (лучше Ш-образной формы), а уж затем заняться расчетом обмоток.
-
- Новичок
- 11 сообщений
- Город: Одесса
- Имя: Каменский Сергей
Как напаять твердосплавную пластину на резец в домашних условиях
Посмотрел видео .Как мне кажется. правильнее было бы вначале место под пластинку облудить латунью. а ужь потом ложить сверху пластинку. При широкой пластинке. под неё припой может и не попасть ,пайка может быть прослабленной. Я так паяю.
#5 Besprizornik
Besprizornik Отправлено 16 June 2011 — 23:51
16 June 2011 — 23:51
- Город: Вологодская
- Имя: Василий
Как напаять твердосплавную пластину на резец в домашних условиях
Я сначала лудил и пласть и пластинку, потом уже спаивал.
Всем Привет! При работе на токарном, часто приходится использовать самодельные резцы из инструментальной быстрорежущей стали, марок; Р6, Р9 — Р18. Есть и у меня в наличии, уже предварительно закаленные бруски различного сечения. Такой материал хорошо годится для изготовления резцов с прямым профилем, но сделать к примеру из такой заготовки проходной упорный или расточной резец трудновыполнимая задача.
Основные виды токарных резцов
В виду отогнутой шейки у такого резца, его необходимо отковать в кузнице, а затем вновь провести термообработку, далеко не у каждого найдутся такие возможности. Самый постой выход, который напрашивается, напаять на стальную державку резца пластину из твёрдого сплава. На картинке в начале статьи показаны основные виды токарных резцов по металлу, в данном случае нам предстоит сделать, что то похожее на тип «д», всего-то пару штук — на пробу. Дело в том, что решено использовать для изготовления резцов твердые пластины, как бы это сказать…, не совсем предназначенные для обработки метала. Но об этом, чуть позже…
Виды твердосплавных напаек для резцов по металлу.
Немало материала по напайке пластин, который есть в сети, связана с применением кислородно-пропановых горелок, что в свою очередь я считаю делом весьма опасным и для домашней мастерской непригодным, кислород штука злая и требует специально оборудованного для этого места или сварочного поста. Мы применим более безопасный нагрев и обойдёмся без кислорода. Во-вторых, мы исключим использование дорогостоящих серебряно-содержащих припоев, а будем использовать в работе более дешевый припой — латунь. Ну, а как бонус к нашей работе, мы сами научимся изготавливать инструмент любой конфигурации, который нам понадобится в процессе работы, а это пожалуй самое важное!
Пластины твердого сплава для фрез по деревообработке.
Не так давно, мои запасы пополнились не совсем обычными твёрдосплавными пластинами, они применялись в промышленных наборных фрезах по дереву. По причине износа кромки они стали не пригодными по прямому назначению и их попросту выкинули. Мне кажется, что эти пластины твёрдого сплава, ещё смогут послужить и в металлообработке.
Толщина пластин от 1.5 до 2 мм. на некоторых хорошо читаются цифры и надписи, позже я попробую найти информацию на этот сплав. Уже сейчас мне удалось обнаружить разницу в химическом составе, оказалось, что пластины не так сильно реагируют на постоянный магнит, как их конкуренты из моих «закромов» предназначенные для обработки стали. Невероятно высокая твёрдость, с лёгкостью царапают стекло. Хотя марку материала и его свойств я конечно не знаю, но мне стало интересно, а что если использовать в качестве основы для режущей кромки токарного резца, именно этот материал. Тем более любопытно сравнить их в работе с гораздо более ранними, ещё «Made in USSR» напайками. Пусть это будет некий сравнительный тест, импортный современный ТВ сплав предназначенный для обработки дерева, против победита. Да, именно так — «Победит», в начале 30 годов в СССР стали называть спекаемый по особой технологии металлокерамический сплав, смесь порошков карбида вольфрама и кобальта. В те времена, внедрение металлокерамики давала огромный толчок развитии всей промышленности и производительности труда в СССР. Ведь стойкость при металлообработки, даже тех твердых сплавов превышала в несколько раз стойкость самых лучших на тот момент высоколегированных инструментальных сталей из которых изготавливался металлорежущий инструмент.
Для работы нам понадобиться газовая горелка с баллоном газа, бура и полоска латуни, латунь у меня толщиной 0.5 мм. какой марки не знаю, но на ощупь мягкая не пружинит.
Так как я буду изготавливать сразу два резца одного типа, то для начала мне нужно отделить две прямоугольные пластины от одной общей большой. Мне удалось сделать это, проточив с обеих сторон бороздки алмазным диском, зажатым через оправку в дремель.
Обворачиваем пропиленную заготовку тканью, дабы избежать разлёта осколков. Зажимаем обернутую пластину в тиски, верхняя кромка губок тисок на уровне пропила, и лёгким ударом молотка ломаем её на три части.
Теперь настало время заняться изготовлением державок для пластин. Для нашей цели вполне подойдёт стальной квадратный пруток 8×8 мм. на нём нужно сделать по два сгиба на каждом конце.Белым красящим маркером отмечаем линию примерно 20 мм. от края прутка, горелкой греем до появления красного свечения, после прогрева зажав пруток по линию в тиски, делаем первый загиб на угол 30°- 35° градусов.
Снова прогреваем конец прутка и теперь уже зажав его на ∼10 мм. ниже первого сгиба, приводим пруток в вертикальное положение.
Получился эдакий зигзагообразный сгиб на конце прутка.
Ножовкой отрезаем лишний припуск.
На фрезерном станке, концевой фрезой обрабатываем полки на глубину 2мм. а уже по отфрезерованному контуру на алмазном круге накладываем радиус на тв. пластине.
Ножницами по металлу, опять же приблизительно. вырезаем две латунные пластинки и укладываем их в отфрезерованные ниши.
Сверху латуни укладываем пластину твердого сплава, весь этот бутерброд накрываем листом асбеста, это необходимо сделать для сохранения тепла и ускорения процесса пайки. Я бы ещё, поставил небольшой тепловой экран из асбеста сзади резца, но ради съёмок этого делать не стал.
Зажигаем горелку и начинаем прогревать резец.
Как только появилось красноватое свечение, необходимо присыпать место спаивания бурой, бура начинает плавится, прилипать к резцу и её уже не сможет сдуть пламя горелки.
Продолжаем нагрев. Расплавленная бура хорошо предохраняет место разогрева от окисления при высокой температуре.
Пока ещё рано заканчивать, температура не достаточна для плавления припоя, хотя видно, что расплавленная бура уже обволокла всю поверхность спаиваемого места.
Вот сейчас, уже можно останавливать процесс, видно, что латунь расплавилась и затекла во все зазоры. При необходимости поправляем положение напайки тонким стальным стержнем и выключаем горелку.
Даём изделию спокойно остыть на воздухе.
Вот, в принципе и всё, цель достигнута, пластины на своем месте, резец готов =) Качеством пайки и формой резцов я очень доволен, осталось заточить их и испытать в деле.
Первый съём стружки новыми резцами даёт весьма обнадёживающий результат, а более полный тест этих пластин может быть только со временем, о чём я непременно сообщу, как только будет ясное представление о преимуществах или недостатках этого материала.
Если Вам понравилась запись и другие страницы этого блога — проголосуйте, нажав на палец вверх. Спасибо!
2 комментария к Напайка твердосплавных пластин.
14.09.2016 в 00:48, александр сказал(а):
все красиво .как в кино. только берут сомнения что такой горелкой латунь любой марки вжизни не расплавишь.да еще прогреть так чтоб что бы она растеклась под напайкой.НЕВЕРЮ.
studvesna73.ru
Резец токарный, напайка. видео Видео уроки
...
4 лет назад
Напайка резца.
...
7 лет назад
Привіт, я - Дядько Максим...... За мат, політику і пропаганду = БАН довічний. Тут тільки позитив і залізяки. Приє...
...
2 лет назад
Этот ролик обработан в Видеоредакторе YouTube (http://www.youtube.com/editor)
...
2 лет назад
Сборка и промежуточное тестирование , аппарата для пайки резцов , из 3 трансформаторов , микроволновых печей .
...
4 лет назад
Показано применение дуги косвенного действия для напайки пластин твердого сплава на резец.
...
10 меc назад
В этом видео я расскажу и покажу как я напаиваю твердосплавные пластины на токарные резцы. При помощи обычн...
...
10 меc назад
Мои эксперименты с напайкой резцов , немного оговорился про принцип работы, ну да ничего исправлюсь в следу...
...
2 лет назад
Процес напайки + лЕкція.
...
3 лет назад
Показано затачивание токарных отрезных резцов на деревянном макете.
...
7 меc назад
Хочу поделиться моим способом пайки токарных резцов.
...
3 лет назад
Дабы не упасть в грязь лицом перед продавцами на рынке,барахолке,магазине - запомните название токарных...
...
4 лет назад
Коли раптово зламався різець якого нема чим замінити і є звичайна дугова сварка можна скористатися цим...
...
4 лет назад
Обзор резцов, применяемых на настольных токарных станках (сечением державки 10х10мм). Фрезеревка державок...
...
2 лет назад
В данном видео показана моя обновка по твердосплаву. В данном видео показан ремонт токарного станка ТВ-4...
...
1 лет назад
Как правильно сделать державки для твердосплавных пластин своими руками Обзор станка 1а616 с коробкой скоро...
...
2 лет назад
Простой способ изготовления токарных, отрезных резцов. Варится обычным электродом для стали.
...
7 лет назад
Очередной видеоурок из серии учебных фильмов по металлообработке. Точильные станки, часть шестая. Заточка...
...
4 лет назад
видео о том как с помощью контактной сварки паять резцы Мой канал: https://www.youtube.com/channel/UCpt4EHBhBdVVWNrmfLK_gJA/videos Самод...
videouroki.su
Пайка резцов в домашних условиях
Для напайки твердосплавных пластин на державки токарных резцов, локальной закалки инструмента, пайки твердыми припоями мелких деталей используют нагрев токами высокой частоты или пламенем газовой горелки. Однако аппаратура ТВЧ громоздка и дорого стоит, она не для домашней мастерской или школьного кружка. Применить же газовую горелку по всем правилам может только сварщик высокой квалификации.Но есть и еще один, почти забытый в наше время способ нагрева — на контактных машинах. Он наиболее приемлем в домашней, школьной, колхозной или совхозной мастерской, в техническом кружке.
Суть его в тепловом воздействии электрического тока на проводник. Выделяемое при этом количество тепла зависит от величины тока, времени его действия на проводник и электрического сопротивления последнего.
С учетом этой зависимости мы разработали аппарат, представляющий собой понижающий трансформатор, первичная обмотка которого рассчитана на 220 В, вторичная — на 2 В. Площадь поперечного сечения магнитопровода около 50 см2. Трансформатор закреплен на основании, а контактные шины вторичной обмотки — на прокладке-изоляторе.
Основание аппарата изготовлено из листовой стали толщиной 5 мм. Снизу в него ввернуты ножки. В основании прорезаны два окна: меньшее — для вентиляции, большее — для выхода болтов крепления контактных шин на текстолитовом изоляторе толщиной 10 мм. Отверстия по краям изолятора служат для его крепления к основанию.
Концы вторичной обмотки трансформатора заведены в отверстия зажимов и зафиксированы болтами (пазы зажимов позволяют деформировать их при затяжке и обеспечивать тем самым надежный электрический контакт).
Трансформатор укрыт защитным кожухом и прикреплен к основанию уголками 25X25 мм. К одному из верхних уголков привинчена изоляционная колодка — для соединения проводов первичной обметки с питающим шнуром и включателем аппарата.
Так как конструкторы-любители не часто имеют все необходимое для повторения описанной самоделки, рекомендуем начать изготовление аппарата с подбора пакета пластин трансформаторного железа (лучше Ш-образной формы), а уж затем заняться расчетом обмоток.
Предположим, что площадь поперечного сечения вашего магнитопровода (Q=a*b) равна 36,8 см2. Тогда мощность вторичной обмотки трансформатора P2 = 36,8*36,8 = 1354,2 Вт, а первичной P1 = 1354,2/0,95 = 1425 Вт. Сила тока I1 = 1425 Вт/220 В = 6,48 А; I2 = 1354,2 Вт/2 В = 677,6 А. Находим площадь поперечного сечения первичной обмотки:
S1 = 6,48 A:2 A/мм2 = 3,24 мм2.
Диаметр провода отсюда
d1 = 4*3,24/3,14 = 2 мм.
Площадь поперечного сечения вторичной обмотки
S2 = 677,6 A:2 A/мм2 = 338,8 мм2,
а диаметр провода
d2 = 4*338,8/3,14 = 20,77 мм.
Соответственно определяем число витков:
n1 = 220 000/222/36,8 = 270 витков,
n2 = 270*2/220 = 2,5 витка.
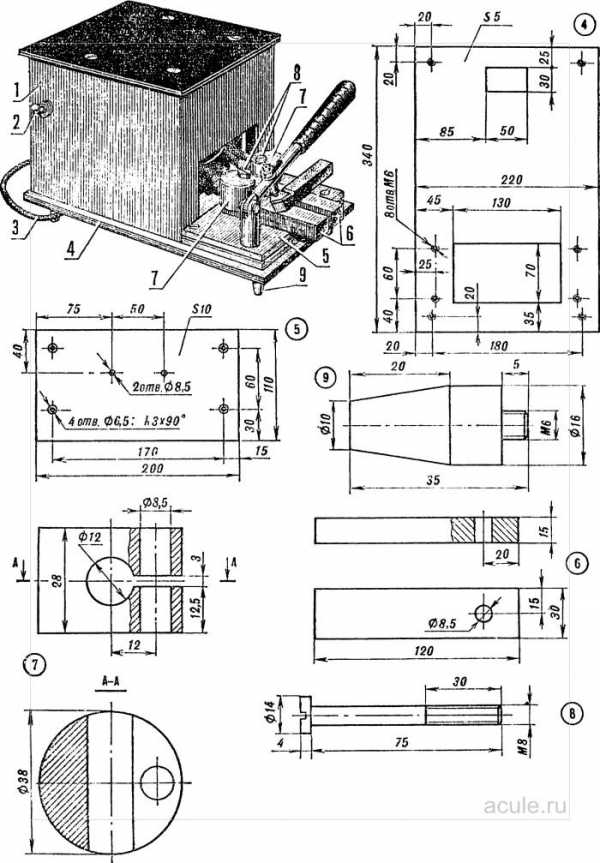
Рис. 1. Аппарат термонагрева:
1 — защитный кожух, 2 — включатель, 3 — шнур электропитания, 4 — основание, 5 — изолятор, 6 — контактные шины, 7 — зажимы, 8 — болты зажимов, 9 — ножка (4 шт.).
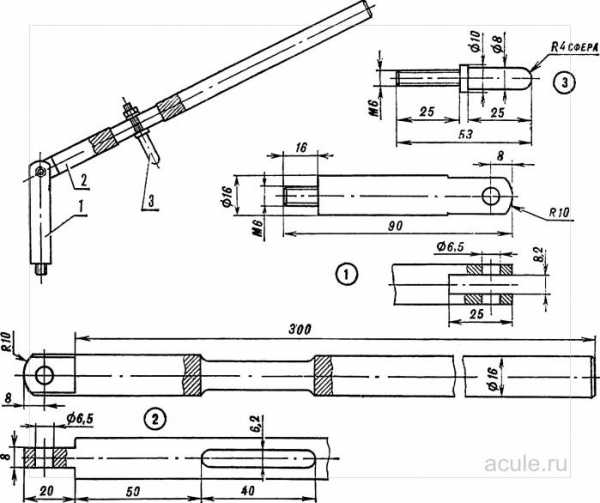
Рис. 2. Прижимной рычаг (устанавливается в дополнительно просверливаемое в изоляторе отверстие с резьбой М6):
1 — стойка, 2 — рычаг, 3 — прижим.
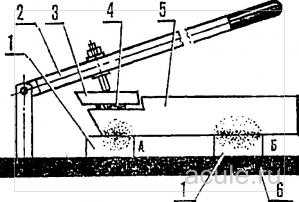
Рис. 3. Контактный участок аппарата:
1 — контактные шины (красная медь), 2 — прижимной рычаг, 3 — твердосплавная пластина, 4 — припой, 5 — державка резца, 6 — изолятор основания; А и Б — зоны нагрева.
Эффективность и экономичность работы аппарата во многом зависят от величины плоскости соприкосновения тела резца с контактными шинами. Количество тепла, выделяемое при прохождении электрического тока, зависит от сопротивления проводника в местах контакта. При большой плоскости соприкосновения выделяется мало тепла при значительном расходе электроэнергии. И наоборот, при малой плоскости выделяется много тепла, что приводит к мгновенному нагреву контактирующего слоя. Чтобы избежать оплавления металла и нарушения контакта, площадь соприкосновения подбирается опытным путем.
При расположении тела резца на шинах, как показано на рисунке 3, очаг возникновения тепла будет располагаться в зоне А; в зоне Б визуально наблюдаемого очага тепла не возникает из-за большой поверхности соприкосновения.
Перед пайкой (в том числе твердосплавных пластин к державкам резцов) необходимо выполнить ряд подготовительных операций, чтобы обеспечить хорошую растекаемость припоя и смачиваемость им соединяемых деталей. Опорную поверхность пластин шлифуют и обезжиривают. Тан же готовят поверхность под пластину на теле резца: она должна быть прямолинейной, без уступов и завалов по краям. Защита поверхностей деталей от окисления при пайке осуществляется флюсом (бурой).
Напайка происходит в такой последовательности. Державку резца располагают на шинах аппарата. Между соединяемыми поверхностями помещают пинцетом припой (обрезок листовой латуни). Для более надежного прижима нагреваемых деталей друг к другу и к контактным шинам служит рычаг, установленный на пластине-изоляторе. В паз рычага вставлен упор, которым и осуществляется прижим твердосплавных пластин к державкам резцов.
При включении аппарата зона контакта быстро нагревается, металл плавится, контакт нарушается и процесс прерывается. Избежать этого можно двумя способами: работая в прерывистом режиме и плавно подавая напряжение на обмотки. В первом случае аппарат включается на 1,5—2 с, затем выключается. В момент отключения тепло передается от места контакта по телу резца, не оплавляя металл.
Плавную подачу напряжения можно обеспечить ЛАТРом. Увеличивая напряжение, добиваются того же результата, что и в первом случае: тепло волнами распространяется по державке от места контакта, обеспечивая нагрев до температуры плавления припоя. Контроль за процессом пайки осуществляется визуально.
Такие режимы дают скорость нагрева державки в пределах 80 — 100 град/с. Это уменьшает внутренние напряжения и предотвращает появление трещин в твердосплавных пластинах. Чтобы избежать появления трещин в паяном шве, необходимо медленное охлаждение.
Качественный паяный шов должен быть не толще 0,1 мм. Протяженность непропаянных мест не должна превышать 10%.
При отсутствии твердых сплавов в качестве режущих пластин можно использовать обломки фрез, сверл и других инструментов. Обломкам придается необходимая форма на заточном станке, или они нагреваются и отковываются до получения стержня прямоугольного сечения, который при повторном нагреве разрубается зубилом на отдельные пластины.
Наш аппарат многоцелевого назначения. Кроме изготовления резцов, его можно использовать и для локальной закалки инструмента (кернов, зубил, отверток и так далее). Достаточно прикоснуться к контактным шинам той частью инструмента, которую необходимо закалить, и подержать так несколько секунд. Температуру нагрева контролируют визуально, по цвету металла. При этом необходимо соблюдать меры предосторожности: работать в рукавицах и защитных очках на заземленном аппарате.
авторы: А. БОБРОВНИКОВ, В. ЗИНЮК
acule.ru
Из какого сплава сделаны токарные резцы???
Применяется: для обработки материалов резанием – чернового точения при неравномерном сечении среза и прерывистом резании, строгании; чернового фрезерования, сверления, чернового рассверливания, чернового зенкерования серого чугуна, цветных металлов и их сплавов и неметаллических материалов; обработки нержавеющих высокопрочных и жаропрочных трудно обрабатываемых сталей и сплавов, в том числе сплавов титана; для оснащения горного инструмента – вращательного бурения геологоразведочных, эксплуатационных и взрывных шпуров и скважин в трещиноватых абразивных горных породах с коэффициентом крепости по шкале Протодьяконова до f= 8. Распиловки мрамора и известняка, а также в камнерезных машинах; для бесстружковой обработки металлов, быстроизнашивающихся деталей машин, приборов и приспособлений – волочения, калибровки и прессования прутков и труб из стали, цветных металлов и их сплавов; быстроизнашивающихся деталей машин, приборов и измерительного инструмента, работающих при небольших ударных нагрузках. Яндекс. Директ
ну смотря для чего и для какой скорости обработки применяется резец
Нет конечно, это материал пластины. Резцы это сталь 45 скорее всего
То, о чём Вы спрашиваете называется тело резца или оправка. Она изготавливается из обычной стали.
простая зализяка
Победит . <img data-big="1" data-lsrc="//otvet.imgsmail.ru/download/u_8d338535e6d54a41616bbc08106f0a58_120x120.jpg" alt="" src="//otvet.imgsmail.ru/download/u_8d338535e6d54a41616bbc08106f0a58_800.jpg">
сталь инструментальная У6 ))) режущая часть ВК8, Т5К10, Т15К6, Эльбор и более сотни сплавов )))
Державки обычных резцов делают из стали 45, отрезных обычно 40Х, для качественного инструмента небольшого и среднего сечения из стали 35ХГС. Если напайные резцы, то, обычно, не калятся, если для сменных мнгогогранных пластин - закалка державки с отпуском обязательна.
touch.otvet.mail.ru