ГОСТ 9.307-89. ЕСЗКС. Покрытия цинковые горячие. Общие требования и методы контроля. Покрытие цинковое гост
ГОСТ 9.307-89 ЕСЗКС. Покрытия цинковые горячие. Общие требования и методы контроля
ГОСУДАРСТВЕННЫЙ СТАНДАРТ СОЮЗА ССР
ЕДИНАЯ СИСТЕМА ЗАЩИТЫ ОТ КОРРОЗИИ И СТАРЕНИЯ
ПОКРЫТИЯ ЦИНКОВЫЕ ГОРЯЧИЕ
ОБЩИЕ ТРЕБОВАНИЯ И МЕТОДЫ КОНТРОЛЯ
ГОСТ 9.307-89 (ИСО 1461-89, СТ СЭВ 4663-84)
ГОССТАНДАРТ РОССИИ
Москва
ГОСУДАРСТВЕННЫЙ СТАНДАРТ СОЮЗА ССР
Единая система защиты от коррозии и старения ПОКРЫТИЯ ЦИНКОВЫЕ ГОРЯЧИЕ Общие требования и методы контроля Unified system of corrosion and ageing protection. methods of control |
ГОСТ 9.307-89 (ИСО 1461-89; CT СЭВ-1663-84) |
Дата введения 01.07.90
Настоящим стандарт устанавливает общие требования (далее - требования) к защитным покрытиям, нанесенным методом горячего цинкования (далее - покрытиям) на конструкционную сталь, в том числе повышенной прочности, стальные конструкции, изделия из фасонного проката и листовой стали, комплекты труб, трубы большого диаметра, изогнутые или сваренные до нанесения покрытия, контейнеры, изделия из стальной проволоки, крепежные изделия, обрабатываемые в общей массе, стальные и чугунные отливки, поковки, штампованные стальные изделия, а также к основному металлу и методам контроля качества покрытий.
Настоящий стандарт не распространяется на покрытия, нанесенные непрерывным способом.
1.1. Требования к конструкции изделий, подлежащих цинкованию
1.1.1. В конструкциях не должно быть карманов, закрытых полостей и воздушных мешков; все полости должны быть доступны для беспрепятственного поступления и выхода из них жидкостей, расплавленного цинка и газов.
Полые изделия и изделия сложной формы подвергают пробному цинкованию.
Не допускается во избежание взрыва наносить покрытия на изделия, имеющие закрытые полости.
1.1.2. Сварку элементов конструкции следует производить встык либо двусторонними швами, либо односторонним швом с подваркой.
Не допускается цинковать изделия со сварными соединениями внахлестку.
1.2. Требования к поверхности основного металла
1.2.1. На поверхности основного металла не допускаются закатанная окалина, заусенцы, поры, включения, сварочные шлаки, остатки формовочной массы, графита, смазки, металлической стружки, маркировочной краски.
1.2.2. На поверхности литых изделий не должно быть пор и усадочных раковин.
1.2.3. Сварные швы должны быть равномерными, плотными и сплошными по всей длине.
Не допускаются поры, свищи, трещины, шлаковые включения, наплавные сопряжения сварных швов.
1.2.4. Острые углы и кромки изделий, за исключением технически обоснованных случаев, должны быть скруглены радиусом не менее 0,3 мм.
1.2.5. Поверхность изделий, подлежащих горячему цинкованию, должна быть очищена обезжириванием, последующим травлением или струйно-абразивной обработкой, затем офлюсована.
Степень очистки поверхности от окалины и продуктов коррозии - 1 по ГОСТ 9.402.
2.1. Внешний вид покрытия
2.1.1. При внешнем осмотре поверхность цинкового покрытия должна быть гладкой или шероховатой, покрытие должно быть сплошным.
Цвет покрытия от серебристо-блестящего до матового темно-серого.
2.1.2. На поверхности изделий не должно быть трещин, забоин, вздутий.
2.1.3. Наличие наплывов цинка недопустимо, если они препятствуют сборке. Крупинки гартцинка диаметром не более 2 мм, рябизна поверхности, светло-серые пятна и цвета побежалости, риски, царапины, следы захвата подъемными приспособлениями без разрушения покрытия до основного металла не являются дефектами.
Допустимо восстановление непрокрытых участков, если они не шире 2 см и составляют не более 2 % общей площади поверхности. Непрокрытые участки защищают слоем цинк-содержащего лакокрасочного покрытия (минимальная толщина 90 мкм, массовая доля цинка в сухой пленке 80 - 85 %) или газотермическим напылением цинка (минимальная толщина 120 мкм).
2.2. Толщина покрытия
Толщина покрытия должна быть не менее 40 мкм и не более 200 мкм и определяется условиями эксплуатации оцинкованных изделий и нормативно-технической документацией на конкретное изделие.
2.3. Прочность сцепления
Покрытие обладает удовлетворительным сцеплением, если выдерживает испытания по методам, приведенным в п. 4.4.
3.1. Перед нанесением покрытий 2 - 5 % изделий из партии, но не менее трех, а для изделий единичного производства - каждое изделие контролируют на соответствие пп. 1.1, 1.2.
3.2. Полуфабрикаты (проволоку, трубы и т.п.) подвергают входному контролю на соответствие требованиям нормативно-технической документации на поставку и требованиям пп. 1.1, 1.2.
3.3. Нанесенное цинковое покрытие подвергают контролю по внешнему виду, толщине и прочности сцепления.
На контроль предъявляют каждую партию оцинкованных изделий. За партию принимают единицу продукции или груза, состоящую из одного или более изделий одинакового типа и размера, принадлежащих к одному заказу, если на них нанесено покрытие за одну смену и в одной и той же ванне.
3.4. Контроль внешнего вида покрытий проводят на 100 % изделий.
3.5. Контролю толщины и прочности сцепления подвергают:
1) элементы стальных конструкций в количестве до 1 %, но не менее 2 шт. от партии;
2) сварные узлы в количестве до 5 %, но не менее 1 штуки от партии;
3) резьбовые крепежные детали в количестве до 0,5 %, но не менее 3 штук от партии.
Допускается применение методов статистического контроля по ГОСТ 18242.
Контроль толщины покрытия металлографическим методом допускается проводить на одной детали из партии.
3.6. Изделия, на которых проводился контроль качества разрушающими методами, разрешается предъявлять к приемке после восстановления покрытия.
3.7. Контроль толщины покрытия
3.7.1. Контроль толщины покрытия проводят до его дополнительной обработки (хроматирование, нанесение консервационных смазок и т.п.).
3.7.2. Толщину покрытия контролируют на поверхности, но имеющей накатки и резьбы на расстоянии не менее 5 мм от ребер, углов, отверстий и мест контакта с приспособлением. Толщину покрытия на резьбовых крепежных деталях контролируют на головках болтов и на торцах гаек.
3.7.3. Измерительный инструмент для неразрушающего контроля толщины покрытия должен иметь погрешность измерения не более ±10 %.
3.8. При получении неудовлетворительных результатов контроля толщины и прочности сцепления проводят повторный контроль на удвоенном количестве деталей.
При получении неудовлетворительных результатов повторного контроля всю партию оцинкованных изделий бракуют.
3.9. Контроль состава ванны горячего цинкования по требованию заказчика проводят до извлечения изделий из ванны.
4.1. Контроль внешнего вида
Внешний вид покрытий контролируют визуальным осмотром невооруженным глазом при освещенности не менее 300 лк на расстоянии 25 см от контролируемой поверхности.
4.2. Контроль толщины покрытия
4.2.1. Магнитный метод
Метод основан на регистрации изменения магнитного сопротивления в зависимости от толщины покрытия. В качестве измерительных приборов используют магнитные толщиномеры.
За результат измерения толщины покрытия принимают среднее арифметическое значение не менее пяти измерений у краев и в середине контролируемой поверхности одного изделия.
Относительная погрешность метода ±10 %.
4.2.2. Металлографический метод (арбитражный)
Метод основан на измерении толщины покрытия на поперечном шлифе с применением металлографических микроскопов различных типов.
Образец для изготовления шлифа вырезают из оцинкованного изделия.
Толщину цинкового покрытия измеряют на шлифе в трех и более точках, равномерно распределенных на линейном участке длиной около 1 см. За результат принимают среднее арифметическое результатов всех измерений.
Относительная погрешность метода ±10 %.
4.2.3. Среднюю толщину покрытия (Нср ) в микрометрах определяют неразрушающими методами или гравиметрическим методом по разности масс образца до и после получения или до и после снятия покрытия по ГОСТ 9.302 .
Для снятия покрытия применяют раствор: 3,2 г хлористой сурьмы или 2 г трехокиси сурьмы растворяют в 500 см3 соляной кислоты, плотностью 1,19 г/см3, ч.д.а., по ГОСТ 3118 в мерной колбе вместимостью 1 дм3 и доводят до метки дистиллированной водой по ГОСТ 6709.
Относительная погрешность гравиметрического метода ±10 %.
4.3. Контроль химического состава цинкового расплава - по ГОСТ 19251.1 , ГОСТ 19251.2 , ГОСТ 19251.3 , ГОСТ 19251.5 .
Массовая доля цинка в рабочем объеме ванны должна быть не менее 98 %.
4.4. Контроль прочности сцепления покрытий
4.4.1. Метод нанесения сетки царапин (при толщине покрытий до 50 мкм)
На очищенной поверхности контролируемого покрытия инструментом со стальным острием под углом 30° (твердость металла острия должна быть выше твердости покрытия) наносят по четыре - шесть параллельных линий глубиной до основного металла на расстоянии от 2,0 до 3,0 мм друг от друга и перпендикулярно к ним. Линии проводят в одном направлении. Прочность сцепления удовлетворительна, если на контролируемой поверхности не наблюдается отслаивание покрытия.
4.4.2. Метод крацевания
Для метода крацевания применяют стальные и латунные щетки диаметром проволоки 0,1 - 0,3 мм и скоростью вращения щеток - 1500 - 2800 мин-1.
Поверхность покрытия крацуют не менее 15 с. После крацевания на контролируемой поверхности не должно наблюдаться вздутия или отслаивания покрытия.
4.4.3. Метод нагрева
При применении метода нагрева детали с покрытием или образцы-свидетели нагревают до (190 ± 10) °С, выдерживают при данной температуре в течение 1 ч и охлаждают на воздухе. На контролируемой поверхности не допускаются вздутия или отслаивания покрытия.
4.4.4. Метод удара поворотным молотком
Плоскую поверхность изделия с толщиной основного металла не менее 3 мм очищают от пыли, механических загрязнений и обезжиривают органическими растворителями.
На плоскую поверхность изделия устанавливают поворотный молоток массой 212,5 г таким образом, чтобы головка молотка вертикально падала на горизонтальную поверхность изделия. Производят не менее двух ударов молотком так, чтобы расстояние между параллельными отпечатками составляло 6 мм, а расстояние от края отпечатка до края изделия составило не менее 13 мм.
Схема поворотного молотка приведена в приложении
Рекомендуемое
1 - молот; 2 - прижимная плита; 3 - поверхность образца; х - размер, определяемый опытным путем в зависимости от металла, из которого изготовлена головка молотка
ИНФОРМАЦИОННЫЕ ДАННЫЕ
1. РАЗРАБОТАН И ВНЕСЕН Государственным строительным комитетом СССР
РАЗРАБОТЧИКИ
С.В. Марутьян , канд. техн. наук (руководитель темы), С.А. Клочко, Л.Н. Павлова, С.Г. Гутник, Л.М. Белоусова
2. УТВЕРЖДЕН И ВВЕДЕН В ДЕЙСТВИЕ Постановлением Государственного комитета СССР по стандартам от 30.05.89 № 1379
3. Срок первой проверки - 1995 г.
Периодичность проверки - 5 лет
4. Стандарт полностью соответствует международным стандартам ИСО 1461-89, СТ СЭВ 4663-84
5. ВЗАМЕН ГОСТ 9.307-85
6. ССЫЛОЧНЫЕ НОРМАТИВНО-ТЕХНИЧЕСКИЕ ДОКУМЕНТЫ
Обозначение НТД, на который дана ссылка |
Номер пункта |
ГОСТ 9.302-88 |
4.2.3 |
ГОСТ 9.402-80 |
1.2.5 |
ГОСТ 3118-77 |
4.2.3 |
ГОСТ 6709-72 |
4.2.3 |
ГОСТ 18242-72 |
3.5 |
ГОСТ 19251.1-79 |
4.3 |
ГОСТ 19251.2-79 |
4.3 |
ГОСТ 19251.3-79 |
4.3 |
ГОСТ 19251.5-79 |
4.3 |
7. ПЕРЕИЗДАНИЕ. Апрель 1992 г.
СОДЕРЖАНИЕ
1. Требования к основному металлу . 1 2. Требования к покрытию .. 2 3. Требования к контролю основного металла и качества покрытия . 2 4. Методы контроля . 3 Приложение Схема поворотного молотка . 4 |
Еще документы скачать бесплатно
www.gosthelp.ru
Стандарты цинковых покрытий - защита конструкций, ГОСТ, СНИП, рекомендации
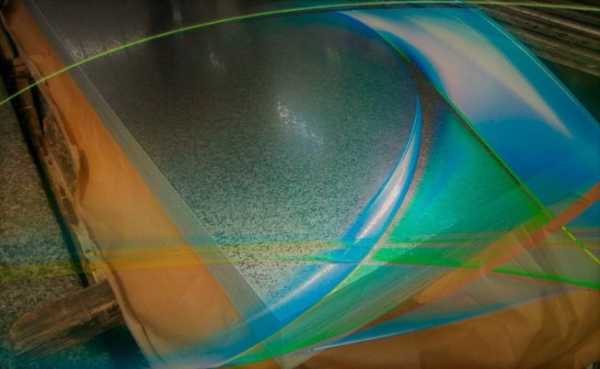
В области стандартизации цинковых покрытий мы заметно отстаем от западных стран и США. Если в этих странах давно существуют стандарты как на процессы горячего нанесения покрытий, так и на особенности проектирования изделий для горячего цинкования, то в СССР (а затем и в России) имеется только один ГОСТ на горячее цинкование, лишь недавно в России появился стандарт на шерардизацию; только относительно электроцинкования и напыления металлических покрытий дела обстоят относительно нормально. Основную нагрузку по нормированию толщины покрытий несут СНиПы, но и в этом случае понятия о необходимой толщине покрытия очень размыты и могут трактоваться по-разному.
В ГОСТ 9.307-89 указывается, что толщина цинкового покрытия должна лежать в пределах от 40 до 200 мкм, в СНиП 2.03.11-85 - что для оцинкованных изделий для зданий и сооружений толщина покрытия должна лежать в пределах от 60 до 100 мкм. В “Общих технических требованиях к ограждающим устройствам на мостовых сооружениях, расположенных на магистральных автомобильных дорогах”, ОДН 218.012-99, указывается толщина покрытия не менее 80 мкм. В то же время связь между условиями цинкования и толщиной покрытия практически отсутствует, если не считать краткой информации в строительных правилах СП 23-101-98, где приведена связь между толщиной покрытия и временем цинкования (таблица № 3.1), причем для температуры, при которой промышленное цинкование не производится (480°С).
Таблица № 3.1. Рекомендуемые толщины покрытий (мкм) при различном содержании кремния в стали (из СП 23-101-98).
Время выдержки, мин |
Толщина цинкового покрытия, мкм, при содержании кремния, % масс. |
|||||||
0,05 |
0,075 |
0,1 |
0,12 |
0,2 |
0,3 |
0,4 |
0,5 |
|
3 |
80 |
140 |
90 |
85 |
90 |
125 |
160 |
200 |
6 |
110 |
240 |
140 |
100 |
120 |
160 |
210 |
280 |
9 |
140 |
360 |
200 |
120 |
200 |
260 |
330 |
400 |
Очевидно, что эти толщины весьма далеки от реальной практики цинкования, тем не менее, некоторые чиновники на основании этого документа создают требования толщины покрытия на отдельных объектах до 200 мкм.
До 80-х годов прошлого столетия разные страны имели свои собственные стандарты на горячее цинкование, причем эти стандарты часто не согласовывались между собой ни в части контроля, ни в классификации областей применения. Отметим, как наиболее разработанные, серию американских стандартов: ASTM A-385/1986/), ASTM A-384 (96), ASTM A-143/94, общеевропейские стандарты по горячему цинкованию EN ISO 1461 и EN ISO 14713. Но ни в этих, ни в большинстве стандартов других стран вообще не рассматривался тип сталей, применяемых в горячем цинковании.
Единственной страной, где в свое время была сделана попытка связать качество покрытия с типом стали, была Франция. Попытки на более низком уровне (уровне рекомендаций) связать тип стали с качеством покрытия были сделаны в Германии, а также в Швеции, где существовал стандарт SMS 2950 “Основные принципы и требования к технологии гальванизации горячим погружением”, в котором существовали два отдельных раздела с толщиной покрытия менее 100 мкм и с толщиной покрытия свыше 215 мкм с указанием об областях использования таких покрытий, но, по- видимому, и в них не было упоминаний о количестве кремния в используемых сталях. В северных странах, где особые требования к морозостойкости сталей, для удобства пользователей пошли по следующему пути: начали производить сталь с интервалом содержания концентрации кремния от 0,15 до 0,25%, особо мелкозернистую. Покрытие для такой стали остается умеренно толстым, матовым и неоднородным по цвету, но в этом случае мы уже не рискуем оказаться в пике Санделина, как при использовании полуспокойных сталей. Необходимо напомнить, что цвет покрытия играет роль только при сдаче объекта, через полгода-год цвет покрытия практически для всех сталей становится темно-серым из-за образования карбонатной пленки, и различия в цвете различных участков изделия становятся не очень заметными.
Из-за неопределенностей с толщиной покрытия во всех стандартах регламентируется минимальная толщина покрытия, но, в отличие от ГОСТ 9.307, как в американском, так и общеевропейском стандартах учитывается зависимость этой минимальной величины от толщины подложки. Эта зависимость определяется нижеследующей таблицей № 3.2.
Таблица № 3.2. Зависимость локальной и средней толщины покрытия на изделиях из стального проката (поз. 1-4), стального литья (поз. 5-6), а также подвергаемых центрифугированию деталей из прутка (поз. 7-9) и плоских изделий (поз. 10, 11).
№ п/п |
Толщина стали (мм) |
Локальная толщина покрытия (мкм) |
Средняя толщина покрытия (мкм) |
1 |
Сталь 6 мм и более |
70 |
85 |
2 |
Сталь от 3 до 6 мм |
55 |
70 |
3 |
Сталь от 1,5 до 3 мм |
45 |
55 |
4 |
Сталь менее 1,5 мм |
35 |
45 |
5 |
Литье более 6 мм |
70 |
80 |
6 |
Литье менее 6 мм |
60 |
70 |
7 |
Диаметр более 20 мм |
45 |
55 |
8 |
Диаметр от 6 до 20 мм |
35 |
45 |
9 |
Диаметр менее 6 мм |
20 |
45 |
10 |
толщина более 3 мм |
45 |
55 |
11 |
толщина менее 3 мм |
35 |
45 |
Эти данные перекликаются с данными американского стандарта ASTM A 123A/123M-97 “Standard Specification for Zinc (Hot-Dip Galvanized) Coatings on Iron and Steel Products”(табл.3.3), поскольку они основаны на реальной практике горячего цинкования.
Таблица № 3.3. Зависимость минимальной толщины покрытия от градации стали в изделии.
Категория материала |
Толщина материала в мм |
||||
<1,6 |
от 1,6 до 3,2 |
от 3,2 до 4,8 |
от 4,8 до 6,4 |
>6,4 |
|
Прокат |
45 |
65 |
85 |
85 |
100 |
Полоса |
45 |
65 |
75 |
85 |
100 |
Труба |
- |
- |
75 |
75 |
75 |
Проволока |
45 |
45 |
65 |
65 |
85 |
Примечание: под градацией понимается отнесение стали по толщине к некоторому интервалу толщины.
Существующие стандарты позволяют учитывать только часть практики горячего цинкования: как следует из рисунка № 3.1, обширная практика двух заводов, чьи данные приведены на рисунке, показывает, что толщины покрытия расположены, в основном, в области выше области нормального цинкования, причем толщины покрытия могут превышать нормальные аж в пять раз. Частично разброс в толщинах покрытия объясняется различной длительностью нахождения изделий или отдельных частей изделий в расплаве (это, кстати, учитывается в стандартах тем, что разрешенная локальная толщина в изделии может быть меньше средней толщины покрытия, рассчитываемой как средняя от суммы толщин различных частей изделия).
Но из рисунка вытекает и другая особенность горячего цинкования - часть покрытий имеет меньшую толщину, чем это допускается стандартами. Объяснить эту особенность горячего цинкования в настоящее время пока не представляется возможным, но с большой вероятностью это связано с особенностями кристаллизации сталей при непрерывной разливке. Борьба с этим отрицательным явлением - расцинковка изделия и его повторное цинкование. В этом случае из-за повышения шероховатости поверхности последующее цинкование идет с несколько большей скоростью, и толщина покрытия будет несколько больше.
Еще до массового применения оцинковки стальных изделий стало ясно, что для цинкового покрытия имеются всего два врага: это сернистый газ, побочный продукт тепловых электростанций, и дистиллированная вода. На рис. 3.2 показана хронологическая зависимость скорости уменьшения толщины цинкового покрытия и наличия сернистого газа в воздухе. Видно, что корреляция весьма и весьма хорошая.
Другая интересная зависимость приведена на рис. № 3.3. Здесь показана скорость коррозии цинкового покрытия, находящегося в воде, имеющей различные значения рН. Видно, что наименьшая скорость коррозии наблюдается в довольно широком интервале рН - от примерно 6 до 11. Но и в этом, оптимальном для покрытия интервале, скорость коррозии очень велика. Это объясняется очень просто - в воде происходит разрушение плотного карбонатно-гидроксидного покрытия, вместо него образуется проницаемое покрытие, и цинк уже не защищен. Таким образом, если цинковое покрытие периодически смачивается дождевой водой или на нем данная дождевая вода скапливается, то такое покрытие довольно быстро разрушается.
Рис. 3.1. Зависимость реально измеренной толщины покрытия от толщины металла для двух предприятий Германии (данные 1940 года).
Рис. 3.2. Скорость атмосферной коррозии цинка (г/м2*сутки) и поглощения диоксида серы из воздуха (г/м2*сутки) по месяцам в Берлине: 1 – поглощение диоксида серы; 2 – потери цинка.
Рис. 3.3. Скорость коррозии цинка в водных растворах в зависимости от значения рН.
Однако на практике оказалось значительно проще. При правильном проектировании изделий избыточной толщины не нужно. Исследования, проведенные за годы эксплуатации оцинкованных изделий, показали, что избыточная толщина цинкового покрытия в большинстве случаев не является оправданной, так как изделие морально устаревает прежде, чем оно начнет разрушаться под воздействием погодных факторов. Оказалось, что толщина покрытия в 60 мкм отражает все требования, предъявляемые к жизнестойкости оцинкованных изделий - в большинстве условий как континентального, так и приморского климата начальные скорости коррозии почти для всех категорий климата не превышают 4 мкм в год, а по мере течения времени скорость коррозии продолжает уменьшаться. Наглядно ожидаемое время жизни оцинкованных изделий наглядно видно из рис. 3.4 и таблицы № 3.4. Ожидаемое время жизни оцинкованного изделия с толщиной покрытия 100 мкм для сельской местности - порядка 100 и более лет, для приморского климата и промышленного города - порядка 50-40 лет, и только для морского климата и насыщенного промышленностью индустриального района - порядка 25-20 лет. Лишь для сооружений, находящихся в морской воде (особенно в зоне приливов) и в подземных сооружениях оцинкованные конструкции не рекомендуются к применению. В то же время в закладных изделиях, находящихся внутри бетона в контакте с солеными водами толщина покрытия в 50 мкм вполне достаточна.
Рис. 3.4. Предположения по времени службы оцинкованных изделий в зависимости от толщины покрытия для различных категорий агрессивности окружающей среды (по ISO 9223): С1- очень слабая; С2 – слабая; С3 – умеренная; С4 – суровая; С5 – очень суровая; Im2 – морская вода в районах умеренного климата.
Таблица № 3.4. Категории агрессивности климата (по ISO 9223, EN ISO 14713).
Климат |
||||
Категория агрессивности |
Среда местонахождения Справочные примеры |
скорость коррозии за первый год |
||
ISO 9223 |
EN ISO 14713 |
|||
Углеродистая сталь, мкм/год |
Цинк, мкм/год |
Цинк, мкм/год |
||
С1 (очень слабая) |
Внутренние помещения: сухие помещения |
<1,3 |
<0,1 |
<0,1 |
С2 (слабая) |
Внутренние помещения: временами конденсация влаги. Наружный климат: внутриконтинентальная cельская местность. |
1,3-25 |
0,1-0,7 |
0,1-0,7 |
С3 (умеренная) |
Внутренние помещения: высокая влажность, небольшое количество загрязнений. Наружный климат: внутриконтинентальный город, приморский климат со слабой засоленностью. |
25-50 |
0,7-2,1 |
0,7-2 |
С4 (суровая) |
Внутренние помещения: предприятия химической промышленности. Наружный климат: внутриконтинен- тальная промышленность, приморский город |
50-80 |
2,1-4,2 |
2-4 |
С5 (очень суровая) |
Наружный климат: Очень влажный промышленный климат, соленый приморский климат |
80-200 |
4,2-8,4 |
4-8 |
Погружные и подземные конструкции |
||||
Категория вредного воздействия |
Окружающая среда Справочные примеры |
|||
Im1 |
Пресная вода. Речныесооружения, гидроэлектростанции |
- |
- |
- |
Im2 |
Морская вода в районах умеренного климата. Сооружения портовой акватории. |
- |
- |
10-20 |
Im3 |
Грунт. Подземные хранилища, стальные сваи, стальные трубы |
- |
- |
- |
ecm-zink.ru
ГОСТ 9.307-89 ЕСЗКС
ГОСТ 9.307-89(ИСО 1461-89)
Группа Т94
МКС 25.220.40ОКСТУ 0009
Дата введения 1990-07-01
1. РАЗРАБОТАН И ВНЕСЕН Государственным строительным комитетом СССРРАЗРАБОТЧИКИ
С.В.Марутьян, канд. техн. наук (руководитель темы), С.А.Клочко, Л.Н.Павлова, С.Г.Гутник, Л.М.Белоусова
2. УТВЕРЖДЕН И ВВЕДЕН В ДЕЙСТВИЕ Постановлением Государственного комитета СССР по стандартам от 30.05.89 N 1379
3. Стандарт полностью соответствует международным стандартам ИСО 1461-89, СТ СЭВ 4663-84
4. ВЗАМЕН ГОСТ 9.307-85
5. ССЫЛОЧНЫЕ НОРМАТИВНО-ТЕХНИЧЕСКИЕ ДОКУМЕНТЫ
6. ПЕРЕИЗДАНИЕНастоящий стандарт устанавливает общие требования (далее - требования) к защитным покрытиям, нанесенным методом горячего цинкования (далее - покрытиям) на конструкционную сталь, в том числе повышенной прочности, стальные конструкции, изделия из фасонного проката и листовой стали, комплекты труб, трубы большого диаметра, изогнутые или сваренные до нанесения покрытия, контейнеры, изделия из стальной проволоки, крепежные изделия, обрабатываемые в общей массе, стальные и чугунные отливки, поковки, штампованные стальные изделия, а также к основному металлу и методам контроля качества покрытий.Настоящий стандарт не распространяется на покрытия, нанесенные непрерывным способом.
1. ТРЕБОВАНИЯ К ОСНОВНОМУ МЕТАЛЛУ
1.1. Требования к конструкции изделий, подлежащих цинкованию
1.1.1. В конструкциях не должно быть карманов, закрытых полостей и воздушных мешков; все полости должны быть доступны для беспрепятственного поступления и выхода из них жидкостей, расплавленного цинка и газов.Полые изделия и изделия сложной формы подвергают пробному цинкованию.Не допускается во избежание взрыва наносить покрытия на изделия, имеющие закрытые полости.
1.1.2. Сварку элементов конструкций следует производить встык либо двусторонними швами, либо односторонним швом с подваркой.Не допускается цинковать изделия со сварными соединениями внахлестку.
1.2. Требования к поверхности основного металла
1.2.1. На поверхности основного металла не допускаются закатанная окалина, заусенцы, поры, включения, сварочные шлаки, остатки формовочной массы, графита, смазки, металлической стружки, маркировочной краски.
1.2.2. На поверхности литых изделий не должно быть пор и усадочных раковин.
1.2.3. Сварные швы должны быть равномерными, плотными и сплошными по всей длине.Не допускаются поры, свищи, трещины, шлаковые включения, наплавные сопряжения сварных швов.
1.2.4. Острые углы и кромки изделий, за исключением технически обоснованных случаев, должны быть скруглены радиусом не менее 0,3 мм.
1.2.5. Поверхность изделий, подлежащих горячему цинкованию, должна быть очищена обезжириванием, последующим травлением или стройно-абразивной обработкой, затем офлюсована.Степень очистки поверхности от окалины и продуктов коррозии - 1 по ГОСТ 9.402.
2. ТРЕБОВАНИЯ К ПОКРЫТИЮ
2.1. Внешний вид покрытия
2.1.1. При внешнем осмотре поверхность цинкового покрытия должна быть гладкой или шероховатой, покрытие должно быть сплошным.Цвет покрытия от серебристо-блестящего до матового темно-серого.
2.1.2. На поверхности изделий не должно быть трещин, забоин, вздутий.
2.1.3. Наличие наплывов цинка недопустимо, если они препятствуют сборке. Крупинки гартцинка диаметром не более 2 мм, рябизна поверхности, светло-серые пятна и цвета побежалости, риски, царапины, следы захвата подъемными приспособлениями без разрушения покрытия до основного металла не являются дефектами.Допустимо восстановление непрокрытых участков, если они не шире 2 см и составляют не более 2% общей площади поверхности. Непрокрытые участки защищают слоем цинксодержащего лакокрасочного покрытия (минимальная толщина 90 мкм, массовая доля цинка в сухой пленке 80%-85%) или газотермическим напылением цинка (минимальная толщина 120 мкм).
2.2. Толщина покрытияТолщина покрытия должна быть нe менее 40 мкм и не более 200 мкм и определяется условиями эксплуатации оцинкованных изделий и нормативно-технической документацией на конкретное изделие.
2.3. Прочность сцепленияПокрытие обладает удовлетворительным сцеплением, если выдерживает испытания по методам, приведенным в п.4.4.
3. ТРЕБОВАНИЯ К КОНТРОЛЮ ОСНОВНОГО МЕТАЛЛА И КАЧЕСТВА ПОКРЫТИЯ
3.1. Перед нанесением покрытий 2%-5% изделий из партии, но не менее трех, а для изделий единичного производства - каждое изделие контролируют на соответствие пп.1.1, 1.2.
3.2. Полуфабрикаты (проволоку, трубы и т.п.) подвергают входному контролю на соответствие требованиям нормативно-технической документации на поставку и требованиям пп.1.1, 1.2.
3.3. Нанесенное цинковое покрытие подвергают контролю по внешнему виду, толщине и прочности сцепления.На контроль предъявляют каждую партию оцинкованных изделий. За партию принимают единицу продукции или груза, состоящую из одного или более изделий одинакового типа и размера, принадлежащих к одному заказу, если на них нанесено покрытие за одну смену и в одной и той же ванне.
3.4. Контроль внешнего вида покрытий проводят на 100% изделий.
3.5. Контролю толщины и прочности сцепления подвергают:
1) элементы стальных конструкций в количестве до 1%, но не менее 2 шт. от партии;
2) сварные узлы в количестве до 5%, но не менее 1 штуки от партии;
3) резьбовые крепежные детали в количестве до 0,5%, но не менее 3 штук от партии.Допускается применение методов статистического контроля по ГОСТ 18242*.________________* На территории Российской Федерации действует ГОСТ Р 50779.71-99**.** На территории Российской Федерации действует ГОСТ Р ИСО 2859-1-2007. - Примечание изготовителя базы данных.
Контроль толщины покрытия металлографическим методом допускается проводить на одной детали из партии.
3.6. Изделия, на которых проводился контроль качества разрушающими методами, разрешается предъявлять к приемке после восстановления покрытия.
3.7. Контроль толщины покрытия
3.7.1. Контроль толщины покрытия проводят до его дополнительной обработки (хроматирование, нанесение консервационных смазок и т.п.).
3.7.2. Толщину покрытия контролируют на поверхности, не имеющей накатки и резьбы на расстоянии не менее 5 мм от ребер, углов, отверстий и мест контакта с приспособлением. Толщину покрытия на резьбовых крепежных деталях контролируют на головках болтов и на торцах гаек.
3.7.3. Измерительный инструмент для неразрушающего контроля толщины покрытия должен иметь погрешность измерения не более ±10%.
3.8. При получении неудовлетворительных результатов контроля толщины и прочности сцепления проводят повторный контроль на удвоенном количестве деталей.
При получении неудовлетворительных результатов повторного контроля всю партию оцинкованных изделий бракуют.
3.9. Контроль состава ванны горячего цинкования по требованию заказчика проводят до извлечения изделий из ванны.
4. МЕТОДЫ КОНТРОЛЯ
4.1. Контроль внешнего видаВнешний вид покрытий контролируют визуальным осмотром невооруженным глазом при освещенности не менее 300 лк на расстоянии 25 см от контролируемой поверхности.
4.2. Контроль толщины покрытия
4.2.1. Магнитный методМетод основан на регистрации изменения магнитного сопротивления в зависимости от толщины покрытия. В качестве измерительных приборов используют магнитные толщиномеры.За результат измерения толщины покрытия принимают средне арифметическое значение не менее пяти измерений у краев и в середине контролируемой поверхности одного изделия.Относительная погрешность метода - ±10%.
4.2.2. Металлографический метод (арбитражный)Метод основан на измерении толщины покрытия на поперечном шлифе с применением металлографических микроскопов различных типов.Образец для изготовления шлифа вырезают из оцинкованного изделия.Толщину цинкового покрытия измеряют на шлифе в трех и более точках, равномерно распределенных на линейном участке длиной около 1 см. За результат принимают среднеарифметическое значение результатов всех измерений.Относительная погрешность метода - ±10%.
4.2.3. Среднюю толщину покрытия () в микрометрах определяют неразрушающими методами или гравиметрическим методом по разности масс образца до и после получения или до и после снятия покрытия по ГОСТ 9.302.Для снятия покрытия применяют раствор: 3,2 г хлористой сурьмы или 2 г трехокиси сурьмы растворяют в 500 см соляной кислоты, плотностью 1,19 г/см, ч.д.а., по ГОСТ 3118 в мерной колбе вместимостью 1 дм и доводят до метки дистиллированной водой по ГОСТ 6709.Относительная погрешность гравиметрического метода - ±10%.
4.3. Контроль химического состава цинкового расплава - по ГОСТ 19251.1, ГОСТ 19251.2, ГОСТ 19251.3, ГОСТ 19251.5.Массовая доля цинка в рабочем объеме ванны должна быть не менее 98%.
4.4. Контроль прочности сцепления покрытий
4.4.1. Метод нанесения сетки царапин (при толщине покрытий до 50 мкм)
На очищенной поверхности контролируемого покрытия инструментом со стальным острием под углом 30° (твердость металла острия должна быть выше твердости покрытия) наносят по четыре-шесть параллельных линий глубиной до основного металла на расстоянии от 2,0 до 3,0 мм друг от друга и перпендикулярно к ним. Линии проводят в одном направлении. Прочность сцепления удовлетворительна, если на контролируемой поверхности не наблюдается отслаивание покрытия.
4.4.2. Метод крацеванияДля метода крацевания применяют стальные и латунные щетки диаметром проволоки 0,1-0,3 мм и скоростью вращения щеток - 1500-2800 мин.Поверхность покрытия крацуют не менее 15 с. После крацевания на контролируемой поверхности не должно наблюдаться вздутия или отслаивания покрытия.
4.4.3. Метод нагреваПри применении метода нагрева детали с покрытием или образцы-свидетели нагревают до (190±10) °С, выдерживают при данной температуре в течение 1 ч и охлаждают на воздухе. На контролируемой поверхности не допускаются вздутия или отслаивания покрытия.
4.4.4. Метод удара поворотным молотком Плоскую поверхность изделия с толщиной основного металла не менее 3 мм очищают от пыли, механических загрязнений и обезжиривают органическими растворителями.На плоскую поверхность изделия устанавливают поворотный молоток массой 212,5 г таким образом, чтобы головка молотка вертикально падала на горизонтальную поверхность изделия. Производят не менее двух ударов молотком так, чтобы расстояние между параллельными отпечатками составляло 6 мм, а расстояние от края отпечатка до края изделия составило не менее 13 мм.Схема поворотного молотка приведена в приложении.
ПРИЛОЖЕНИЕ (рекомендуемое). СХЕМА ПОВОРОТНОГО МОЛОТКА
ПРИЛОЖЕНИЕРекомендуемое
1 - молот; 2 - прижимная плита; 3 - поверхность образца; - размер, определяемый опытным путем в зависимости от металла, из которого изготовлена головка молотка
Электронный текст документа подготовлен ЗАО "Кодекс" и сверен по:официальное изданиеПокрытия металлические.Защита от коррозии:Сб. стандартов. -М.: ИПК Издательство стандартов, 2005
docs.cntd.ru
ГОСТ 9.307-89 - Единая система защиты от коррозии и старения. Покрытия цинковые горячие. Общие требования и методы контроля
ГОСТ ♦.J07-89 с. г
Не допускается цинковать изделия со сварными соединениями в нахлестку.
1.2. Требова ни я к поверхности основного металла
1.2.1. На поверхности основного металла не допускаются закатанная окалина, заусенцы, поры, включения, сварочные шлаки, остатки формовочной массы, графита, смазки, металлической стружки, маркировочной краски
1.2.2. На поверхности литых изделий не должно быть пор и усадочных раковин.
1.2.3. Сварные швы должны быть равномерными, плотными и сплошными по всей длине.
Не допускаются поры, свищи, трещины, шлаковые включения, наплавные сопряжения сварных швов.
1.2.4. Острые углы и кромки изделий, за нсключннем технически обоснованных случаев, должны быть скруглены радиусом не менее 0,3 мм.
1.2.5. Поверхность изделий, подлежащих горячему цинкованию, должна быть очищена обезжириванием, последующим травлением или струйно-абразивной обработкой, затем офлюсована.
Степень очистки поверхности от окалины и продуктов коррозии — 1 по ГОСТ 9.402.
2. ТРЕБОВАНИЯ К ПОКРЫТИЮ
2.1. Внешний вид покрытия
2.1.1. При внешнем осмотре поверхность цинкового покрытия должна быть гладкой или шероховатой, покрытие должно быть сплошным.
Цвет покрытия от серебристо-блестящего до матового темносерого.
2.1.2. На поверхности изделий не должно быть трещин, забоин, вздутий.
2.1.3. Наличие наплывов цинка недопустимо, если они препятствуют сборке. Крупинки гартцинка диаметром не более 2 мм, рябизна поверхности, светло-серые пятна и цвета побежалости, риски, царапины, следы захвата под-ьемнымн приспособлениями без разрушения покрытия до основного металла не являются дефектами.
Допустимо восстановление непрокрытых участков, если они не шире 2 см и составляют не более 2% общей площади поверхности. Иепрокрытые участки защищают слоем цинк-еодержащего лакокрасочного покрытия (минимальная толщина 90 мкм, массовая доля цинка в сухой пленке 80—85%) или газотермическнм напылением цинка( минимальная толщина 120 мкм).
stroysvoimirukami.ru
ГОСТ 9.307-89 Горячее цинкование
ГОСУДАРСТВЕННЫЙ СТАНДАРТ СОЮЗА ССР
ЕДИНАЯ СИСТЕМА ЗАЩИТЫ ОТ КОРРОЗИИ И СТАРЕНИЯ
ПОКРЫТИЯ ЦИНКОВЫЕ ГОРЯЧИЕ
ОБЩИЕ ТРЕБОВАНИЯ И МЕТОДЫ КОНТРОЛЯ
ГОСТ 9.307-89
(ИСО 1461-89, СТ СЭВ 4663-84)
ГОССТАНДАРТ РОССИИ
Москва
Unified system of corrosion and ageing protection.
Hot-dip zinc coatings. General requirements and
methods of control
Дата введения 01.07.90
ИНФОРМАЦИОННЫЕ ДАННЫЕ
1. РАЗРАБОТАН И ВНЕСЕН Государственным строительным комитетом СССР
ИСПОЛНИТЕЛИ:
С.В.Марутьян, канд. техн. наук (руководитель темы), С.А.Клочко, Л.Н.Павлова, С.Г.Гутник, Л.М.Белоусова
2. УТВЕРЖДЕН И ВВЕДЕН В ДЕЙСТВИЕ Постановлением Государственного комитета СССР по стандартам от 30.05.89 N 1379
3. Срок первой проверки -1995 г.
Периодичность проверки - 5 лет
4. Стандарт полностью соответствует международным стандартам ИСО 1461-89, СТ СЭВ 4663-84
5. ВЗАМЕН ГОСТ 9.307-85
6. ССЫЛОЧНЫЕ НОРМАТИВНО-ТЕХНИЧЕСКИЕ ДОКУМЕНТЫ
Настоящим стандарт устанавливает общие требования (далее - требования) к защитным покрытиям, нанесенным методом горячего цинкования (далее - покрытиям) на конструкционную сталь, в том числе повышенной прочности, стальные конструкции, изделия из фасонного проката и листовой стали, комплекты труб, трубы большого диаметра, изогнутые или сваренные до нанесения покрытия, контейнеры, изделия из стальной проволоки, крепежные изделия, обрабатываемые в общей массе, стальные и чугунные отливки, поковки, штампованные стальные изделия, а также к основному металлу и методам контроля качества покрытий.
Настоящий стандарт не распространяется на покрытия, нанесенные непрерывным способом.
1. ТРЕБОВАНИЯ К ОСНОВНОМУ МЕТАЛЛУ
1.1. Требования к конструкции изделий, подлежащих цинкованию
1.1.1. В конструкциях не должно быть карманов, закрытых полостей и воздушных мешков; все полости должны быть доступны для беспрепятственного поступления и выхода из них жидкостей, расплавленного цинка и газов.
Полые изделия и изделия сложной формы подвергают пробному цинкованию.
Не допускается во избежание взрыва наносить покрытия на изделия, имеющие закрытые полости.
1.1.2. Сварку элементов конструкций следует производить встык либо двусторонними швами, либо односторонним швом с подваркой.
Не допускается цинковать изделия со сварными соединениями в нахлестку.
1.2. Требования к поверхности основного металла
1.2.1. На поверхности основного металла не допускаются закатанная окалина, заусенцы, поры, включения, сварочные шлаки, остатки формовочной массы, графита, смазки, металлической стружки, маркировочной краски.
1.2.2. На поверхности литых изделий не должно быть пор и усадочных раковин.
1.2.3. Сварные швы должны быть равномерными, плотными и сплошными по всей длине.
Не допускаются поры, свищи, трещины, шлаковые включения, наплавные сопряжения сварных швов.
1.2.4. Острые углы и кромки изделий, за исключением технически обоснованных случаев, должны быть скруглены радиусом не менее0,3 мм.
1.2.5. Поверхность изделий, подлежащих горячему цинкованию, должна быть очищена обезжириванием, последующим травлением или стройно-абразивной обработкой, затем офлюсована.
Степень очистки поверхности от окалины и продуктов коррозии - 1 по ГОСТ 9.402.
2. ТРЕБОВАНИЯ К ПОКРЫТИЮ
2.1. Внешний вид покрытия
2.1.1. При внешнем осмотре поверхность цинкового покрытия должна быть гладкой или шероховатой, покрытие должно быть сплошным.
Цвет покрытия от серебристо-блестящего до матового темно-серого.
2.1.2. На поверхности изделий не должно быть трещин, забоин, вздутий.
2.1.3. Наличие наплывов цинка недопустимо, если они препятствуют сборке. Крупинки гартцинка диаметром не более2 мм, рябизна поверхности, светло-серые пятна и цвета побежалости, риски, царапины, следы захвата подъемными приспособлениями без разрушения покрытия до основного металла не являются дефектами.
Допустимо восстановление непрокрытых участков, если они не шире2 сми составляют не более 2% общей площади поверхности. Непрокрытые участки защищают слоем цинк-содержащего лакокрасочного покрытия (минимальная толщина 90 мкм, массовая доля цинка в сухой пленке 80-85%) или газотермическим напылением цинка (минимальная толщина 120 мкм).
2.2. Толщина покрытия
Толщина покрытия должна быть нe менее 40 мкм и не более 200 мкм и определяется условиями эксплуатации оцинкованных изделий и нормативно-технической документацией на конкретное изделие.
2.3. Прочность сцепления
Покрытие обладает удовлетворительным сцеплением, если выдерживает испытания по методам, приведенным в п.4.4.
3. ТРЕБОВАНИЯ К КОНТРОЛЮ ОСНОВНОГО МЕТАЛЛА И КАЧЕСТВА ПОКРЫТИЯ
3.1. Перед нанесением покрытий 2-5% изделий из партии, но не менее трех, а для изделий единичного производства - каждое изделие контролируют на соответствие пп.1.1, 1.2.
3.2. Полуфабрикаты (проволоку, трубы и т.п.) подвергают входному контролю на соответствие требованиям нормативно-технической документации на поставку и требованиям пп.1.1, 1.2.
3.3. Нанесенное цинковое покрытие подвергают контролю по внешнему виду, толщине и прочности сцепления.
На контроль предъявляют каждую партию оцинкованных изделий. За партию принимают единицу продукции или груза, состоящую из одного или более изделий одинакового типа и размера, принадлежащих к одному заказу, если на них нанесено покрытие за одну смену и в одной и той же ванне.
3.4. Контроль внешнего вида покрытий проводят на 100% изделий.
3.5. Контролю толщины и прочности сцепления подвергают:
1) элементы стальных конструкций в количестве до 1%, но не менее 2 шт. от партии;
2) сварные узлы в количестве до 5%, но не менее 1 штуки от партии;
3) резьбовые крепежные детали в количестве до 0,5%, но не менее 3 штук от партии.
Допускается применение методов статистического контроля по ГОСТ 18242.
Контроль толщины покрытия металлографическим методом допускается проводить на одной детали из партии.
3.6. Изделия, на которых проводился контроль качества разрушающими методами, разрешается предъявлять к приемке после восстановления покрытия.
3.7. Контроль толщины покрытия
3.7.1. Контроль толщины покрытия проводят до его дополнительной обработки (хроматирование, нанесение консервационных смазок и т.п.).
3.7.2. Толщину покрытия контролируют на поверхности, не имеющей накатки и резьбы на расстоянии не менее5 ммот ребер, углов, отверстий и мест контакта с приспособлением. Толщину покрытия на резьбовых крепежных деталях контролируют на головках болтов и на торцах гаек.
3.7.3. Измерительный инструмент для неразрушающего контроля толщины покрытия должен иметь погрешность измерения не более ±10%.
3.8. При получении неудовлетворительных результатов контроля толщины и прочности сцепления проводят повторный контроль на удвоенном количестве деталей.
При получении неудовлетворительных результатов повторного контроля всю партию оцинкованных изделий бракуют.
3.9. Контроль состава ванны горячего цинкования по требованию заказчика проводят до извлечения изделий из ванны.
4. МЕТОДЫ КОНТРОЛЯ
4.1. Контроль внешнего вида
Внешний вид покрытий контролируют визуальным осмотром невооруженным глазом при освещенности не менее 300 лк на расстоянии25 смот контролируемой поверхности.
4.2. Контроль толщины покрытия
4.2.1. Магнитный метод
Метод основан на регистрации изменения магнитного сопротивления в зависимости от толщины покрытия. В качестве измерительных приборов используют магнитные толщиномеры.
За результат измерения толщины покрытия принимают среднее арифметическое значение не менее пяти измерений у краев и в середине контролируемой поверхности одного изделия.
Относительная погрешность метода ±10%.
4.2.2. Металлографический метод (арбитражный)
Метод основан на измерении толщины покрытия на поперечном шлифе с применением металлографических микроскопов различных типов.
Образец для изготовления шлифа вырезают из оцинкованного изделия.
Толщину цинкового покрытия измеряют на шлифе в трех и более точках, равномерно распределенных на линейном участке длиной около1 см. За результат принимают среднее арифметическое результатов всех измерений.
Относительная погрешность метода ±10%.
4.2.3. Среднюю толщину покрытия () в микрометрах определяют неразрушающими методами или гравиметрическим методом по разности масс образца до и после получения или до и после снятия покрытия по ГОСТ 9.302.
Для снятия покрытия применяют раствор:3,2 гхлористой сурьмы или2 гтрехокиси сурьмы растворяют в500 см соляной кислоты, плотностью 1,19 г/см, ч.д.а., по ГОСТ 3118 в мерной колбе вместимостью 1 дм и доводят до метки дистиллированной водой по ГОСТ 6709.
Относительная погрешность гравиметрического метода ±10%.
4.3. Контроль химического состава цинкового расплава - по ГОСТ 19251.1, ГОСТ 19251.2, ГОСТ 19251.3, ГОСТ 19251.5.
Массовая доля цинка в рабочем объеме ванны должна быть не менее 98%.
4.4. Контроль прочности сцепления покрытий
4.4.1. Метод нанесения сетки царапин (при толщине покрытий до 50 мкм)
На очищенной поверхности контролируемого покрытия инструментом со стальным острием под углом 30° (твердость металла острия должна быть выше твердости покрытия) наносят по четыре-шесть параллельных линий глубиной до основного металла на расстоянии от 2,0 до3,0 ммдруг от друга и перпендикулярно к ним. Линии проводят в одном направлении. Прочность сцепления удовлетворительна, если на контролируемой поверхности не наблюдается отслаивание покрытия.
4.4.2. Метод крацевания
Для метода крацевания применяют стальные и латунные щетки диаметром проволоки 0,1-0,3 мми скоростью вращения щеток - 1500-2800 мин.
Поверхность покрытия крацуют не менее 15 с. После крацевания на контролируемой поверхности не должно наблюдаться вздутия или отслаивания покрытия.
4.4.3. Метод нагрева
При применении метода нагрева детали с покрытием или образцы-свидетели нагревают до (190±10)°С, выдерживают при данной температуре в течение 1 ч и охлаждают на воздухе. На контролируемой поверхности не допускаются вздутия или отслаивания покрытия.
4.4.4. Метод удара поворотным молотком
Плоскую поверхность изделия с толщиной основного металла не менее3 ммочищают от пыли, механических загрязнений и обезжиривают органическими растворителями.
На плоскую поверхность изделия устанавливают поворотный молоток массой212,5 гтаким образом, чтобы головка молотка вертикально падала на горизонтальную поверхность изделия. Производят не менее двух ударов молотком так, чтобы расстояние между параллельными отпечатками составляло6 мм, а расстояние от края отпечатка до края изделия составило не менее13 мм.
ankorltd.ru
ГОСТ 9.307-89 - ЕСЗКС. Покрытия цинковые горячие. Общие требования и методы контроля.
ГОСУДАРСТВЕННЫЙ СТАНДАРТ СОЮЗА ССР
ЕДИНАЯ СИСТЕМА ЗАЩИТЫ ОТ КОРРОЗИИ И СТАРЕНИЯ
ПОКРЫТИЯ ЦИНКОВЫЕ ГОРЯЧИЕ
ОБЩИЕ ТРЕБОВАНИЯ И МЕТОДЫ КОНТРОЛЯ
ГОСТ 9.307-89 (ИСО 1461-89, СТ СЭВ 4663-84)
ГОССТАНДАРТ РОССИИ
Москва
ГОСУДАРСТВЕННЫЙ СТАНДАРТ СОЮЗА ССР
Единая система защиты от коррозии и старения ПОКРЫТИЯ ЦИНКОВЫЕ ГОРЯЧИЕ Общие требования и методы контроля Unified system of corrosion and ageing protection. Hot-dip zinc coatings. General requirements and methods of control |
ГОСТ 9.307-89 (ИСО 1461-89; CT СЭВ-1663-84) |
Дата введения 01.07.90
Настоящим стандарт устанавливает общие требования (далее - требования) к защитным покрытиям, нанесенным методом горячего цинкования (далее - покрытиям) на конструкционную сталь, в том числе повышенной прочности, стальные конструкции, изделия из фасонного проката и листовой стали, комплекты труб, трубы большого диаметра, изогнутые или сваренные до нанесения покрытия, контейнеры, изделия из стальной проволоки, крепежные изделия, обрабатываемые в общей массе, стальные и чугунные отливки, поковки, штампованные стальные изделия, а также к основному металлу и методам контроля качества покрытий.
Настоящий стандарт не распространяется на покрытия, нанесенные непрерывным способом.
1.1. Требования к конструкции изделий, подлежащих цинкованию
1.1.1. В конструкциях не должно быть карманов, закрытых полостей и воздушных мешков; все полости должны быть доступны для беспрепятственного поступления и выхода из них жидкостей, расплавленного цинка и газов.
Полые изделия и изделия сложной формы подвергают пробному цинкованию.
Не допускается во избежание взрыва наносить покрытия на изделия, имеющие закрытые полости.
1.1.2. Сварку элементов конструкции следует производить встык либо двусторонними швами, либо односторонним швом с подваркой.
Не допускается цинковать изделия со сварными соединениями внахлестку.
1.2. Требования к поверхности основного металла
1.2.1. На поверхности основного металла не допускаются закатанная окалина, заусенцы, поры, включения, сварочные шлаки, остатки формовочной массы, графита, смазки, металлической стружки, маркировочной краски.
1.2.2. На поверхности литых изделий не должно быть пор и усадочных раковин.
1.2.3. Сварные швы должны быть равномерными, плотными и сплошными по всей длине.
Не допускаются поры, свищи, трещины, шлаковые включения, наплавные сопряжения сварных швов.
1.2.4. Острые углы и кромки изделий, за исключением технически обоснованных случаев, должны быть скруглены радиусом не менее 0,3 мм.
1.2.5. Поверхность изделий, подлежащих горячему цинкованию, должна быть очищена обезжириванием, последующим травлением или струйно-абразивной обработкой, затем офлюсована.
Степень очистки поверхности от окалины и продуктов коррозии - 1 по ГОСТ 9.402.
2.1. Внешний вид покрытия
2.1.1. При внешнем осмотре поверхность цинкового покрытия должна быть гладкой или шероховатой, покрытие должно быть сплошным.
Цвет покрытия от серебристо-блестящего до матового темно-серого.
2.1.2. На поверхности изделий не должно быть трещин, забоин, вздутий.
2.1.3. Наличие наплывов цинка недопустимо, если они препятствуют сборке. Крупинки гартцинка диаметром не более 2 мм, рябизна поверхности, светло-серые пятна и цвета побежалости, риски, царапины, следы захвата подъемными приспособлениями без разрушения покрытия до основного металла не являются дефектами.
Допустимо восстановление непрокрытых участков, если они не шире 2 см и составляют не более 2 % общей площади поверхности. Непрокрытые участки защищают слоем цинк-содержащего лакокрасочного покрытия (минимальная толщина 90 мкм, массовая доля цинка в сухой пленке 80 - 85 %) или газотермическим напылением цинка (минимальная толщина 120 мкм).
2.2. Толщина покрытия
Толщина покрытия должна быть не менее 40 мкм и не более 200 мкм и определяется условиями эксплуатации оцинкованных изделий и нормативно-технической документацией на конкретное изделие.
2.3. Прочность сцепления
Покрытие обладает удовлетворительным сцеплением, если выдерживает испытания по методам, приведенным в п. 4.4.
3.1. Перед нанесением покрытий 2 - 5 % изделий из партии, но не менее трех, а для изделий единичного производства - каждое изделие контролируют на соответствие пп. 1.1, 1.2.
3.2. Полуфабрикаты (проволоку, трубы и т.п.) подвергают входному контролю на соответствие требованиям нормативно-технической документации на поставку и требованиям пп. 1.1, 1.2.
3.3. Нанесенное цинковое покрытие подвергают контролю по внешнему виду, толщине и прочности сцепления.
На контроль предъявляют каждую партию оцинкованных изделий. За партию принимают единицу продукции или груза, состоящую из одного или более изделий одинакового типа и размера, принадлежащих к одному заказу, если на них нанесено покрытие за одну смену и в одной и той же ванне.
3.4. Контроль внешнего вида покрытий проводят на 100 % изделий.
3.5. Контролю толщины и прочности сцепления подвергают:
1) элементы стальных конструкций в количестве до 1 %, но не менее 2 шт. от партии;
2) сварные узлы в количестве до 5 %, но не менее 1 штуки от партии;
3) резьбовые крепежные детали в количестве до 0,5 %, но не менее 3 штук от партии.
Допускается применение методов статистического контроля по ГОСТ 18242.
Контроль толщины покрытия металлографическим методом допускается проводить на одной детали из партии.
3.6. Изделия, на которых проводился контроль качества разрушающими методами, разрешается предъявлять к приемке после восстановления покрытия.
3.7. Контроль толщины покрытия
3.7.1. Контроль толщины покрытия проводят до его дополнительной обработки (хроматирование, нанесение консервационных смазок и т.п.).
3.7.2. Толщину покрытия контролируют на поверхности, но имеющей накатки и резьбы на расстоянии не менее 5 мм от ребер, углов, отверстий и мест контакта с приспособлением. Толщину покрытия на резьбовых крепежных деталях контролируют на головках болтов и на торцах гаек.
3.7.3. Измерительный инструмент для неразрушающего контроля толщины покрытия должен иметь погрешность измерения не более ±10 %.
3.8. При получении неудовлетворительных результатов контроля толщины и прочности сцепления проводят повторный контроль на удвоенном количестве деталей.
При получении неудовлетворительных результатов повторного контроля всю партию оцинкованных изделий бракуют.
3.9. Контроль состава ванны горячего цинкования по требованию заказчика проводят до извлечения изделий из ванны.
4.1. Контроль внешнего вида
Внешний вид покрытий контролируют визуальным осмотром невооруженным глазом при освещенности не менее 300 лк на расстоянии 25 см от контролируемой поверхности.
4.2. Контроль толщины покрытия
4.2.1. Магнитный метод
Метод основан на регистрации изменения магнитного сопротивления в зависимости от толщины покрытия. В качестве измерительных приборов используют магнитные толщиномеры.
За результат измерения толщины покрытия принимают среднее арифметическое значение не менее пяти измерений у краев и в середине контролируемой поверхности одного изделия.
Относительная погрешность метода ±10 %.
4.2.2. Металлографический метод (арбитражный)
Метод основан на измерении толщины покрытия на поперечном шлифе с применением металлографических микроскопов различных типов.
Образец для изготовления шлифа вырезают из оцинкованного изделия.
Толщину цинкового покрытия измеряют на шлифе в трех и более точках, равномерно распределенных на линейном участке длиной около 1 см. За результат принимают среднее арифметическое результатов всех измерений.
Относительная погрешность метода ±10 %.
4.2.3. Среднюю толщину покрытия (Нср) в микрометрах определяют неразрушающими методами или гравиметрическим методом по разности масс образца до и после получения или до и после снятия покрытия по ГОСТ 9.302.
Для снятия покрытия применяют раствор: 3,2 г хлористой сурьмы или 2 г трехокиси сурьмы растворяют в 500 см3 соляной кислоты, плотностью 1,19 г/см3, ч.д.а., по ГОСТ 3118 в мерной колбе вместимостью 1 дм3 и доводят до метки дистиллированной водой по ГОСТ 6709.
Относительная погрешность гравиметрического метода ±10 %.
4.3. Контроль химического состава цинкового расплава - по ГОСТ 19251.1, ГОСТ 19251.2, ГОСТ 19251.3, ГОСТ 19251.5.
Массовая доля цинка в рабочем объеме ванны должна быть не менее 98 %.
4.4. Контроль прочности сцепления покрытий
4.4.1. Метод нанесения сетки царапин (при толщине покрытий до 50 мкм)
На очищенной поверхности контролируемого покрытия инструментом со стальным острием под углом 30° (твердость металла острия должна быть выше твердости покрытия) наносят по четыре - шесть параллельных линий глубиной до основного металла на расстоянии от 2,0 до 3,0 мм друг от друга и перпендикулярно к ним. Линии проводят в одном направлении. Прочность сцепления удовлетворительна, если на контролируемой поверхности не наблюдается отслаивание покрытия.
4.4.2. Метод крацевания
Для метода крацевания применяют стальные и латунные щетки диаметром проволоки 0,1 - 0,3 мм и скоростью вращения щеток - 1500 - 2800 мин-1.
Поверхность покрытия крацуют не менее 15 с. После крацевания на контролируемой поверхности не должно наблюдаться вздутия или отслаивания покрытия.
4.4.3. Метод нагрева
При применении метода нагрева детали с покрытием или образцы-свидетели нагревают до (190 ± 10) °С, выдерживают при данной температуре в течение 1 ч и охлаждают на воздухе. На контролируемой поверхности не допускаются вздутия или отслаивания покрытия.
4.4.4. Метод удара поворотным молотком
Плоскую поверхность изделия с толщиной основного металла не менее 3 мм очищают от пыли, механических загрязнений и обезжиривают органическими растворителями.
На плоскую поверхность изделия устанавливают поворотный молоток массой 212,5 г таким образом, чтобы головка молотка вертикально падала на горизонтальную поверхность изделия. Производят не менее двух ударов молотком так, чтобы расстояние между параллельными отпечатками составляло 6 мм, а расстояние от края отпечатка до края изделия составило не менее 13 мм.
Схема поворотного молотка приведена в приложении
Рекомендуемое
1 - молот; 2 - прижимная плита; 3 - поверхность образца; х - размер, определяемый опытным путем в зависимости от металла, из которого изготовлена головка молотка
ИНФОРМАЦИОННЫЕ ДАННЫЕ
1. РАЗРАБОТАН И ВНЕСЕН Государственным строительным комитетом СССР
РАЗРАБОТЧИКИ
С.В. Марутьян, канд. техн. наук (руководитель темы), С.А. Клочко, Л.Н. Павлова, С.Г. Гутник, Л.М. Белоусова
2. УТВЕРЖДЕН И ВВЕДЕН В ДЕЙСТВИЕ Постановлением Государственного комитета СССР по стандартам от 30.05.89 № 1379
3. Срок первой проверки - 1995 г.
Периодичность проверки - 5 лет
4. Стандарт полностью соответствует международным стандартам ИСО 1461-89, СТ СЭВ 4663-84
5. ВЗАМЕН ГОСТ 9.307-85
6. ССЫЛОЧНЫЕ НОРМАТИВНО-ТЕХНИЧЕСКИЕ ДОКУМЕНТЫ
7. ПЕРЕИЗДАНИЕ. Апрель 1992 г.
СОДЕРЖАНИЕ
snipov.net
ГОСТ 9.307-89 - Единая система защиты от коррозии и старения. Покрытия цинковые горячие. Общие требования и методы контроля.
ГОСУДАРСТВЕННЫЙ СТАНДАРТ СОЮЗА ССР
ЕДИНАЯ СИСТЕМА ЗАЩИТЫ ОТ КОРРОЗИИ И СТАРЕНИЯ
ПОКРЫТИЯ ЦИНКОВЫЕ ГОРЯЧИЕ
ОБЩИЕ ТРЕБОВАНИЯ И МЕТОДЫ КОНТРОЛЯ
ГОСТ 9.307-89 (ИСО 1461-89, СТ СЭВ 4663-84)
ГОССТАНДАРТ РОССИИ
Москва
ГОСУДАРСТВЕННЫЙ СТАНДАРТ СОЮЗА ССР
Единая система защиты от коррозии и старения ПОКРЫТИЯ ЦИНКОВЫЕ ГОРЯЧИЕ Общие требования и методы контроля Unified system of corrosion and ageing protection. Hot-dip zinc coatings. General requirements and methods of control |
ГОСТ 9.307-89 (ИСО 1461-89; CT СЭВ-1663-84) |
Дата введения 01.07.90
Настоящим стандарт устанавливает общие требования (далее - требования) к защитным покрытиям, нанесенным методом горячего цинкования (далее - покрытиям) на конструкционную сталь, в том числе повышенной прочности, стальные конструкции, изделия из фасонного проката и листовой стали, комплекты труб, трубы большого диаметра, изогнутые или сваренные до нанесения покрытия, контейнеры, изделия из стальной проволоки, крепежные изделия, обрабатываемые в общей массе, стальные и чугунные отливки, поковки, штампованные стальные изделия, а также к основному металлу и методам контроля качества покрытий.
Настоящий стандарт не распространяется на покрытия, нанесенные непрерывным способом.
1.1. Требования к конструкции изделий, подлежащих цинкованию
1.1.1. В конструкциях не должно быть карманов, закрытых полостей и воздушных мешков; все полости должны быть доступны для беспрепятственного поступления и выхода из них жидкостей, расплавленного цинка и газов.
Полые изделия и изделия сложной формы подвергают пробному цинкованию.
Не допускается во избежание взрыва наносить покрытия на изделия, имеющие закрытые полости.
1.1.2. Сварку элементов конструкции следует производить встык либо двусторонними швами, либо односторонним швом с подваркой.
Не допускается цинковать изделия со сварными соединениями внахлестку.
1.2. Требования к поверхности основного металла
1.2.1. На поверхности основного металла не допускаются закатанная окалина, заусенцы, поры, включения, сварочные шлаки, остатки формовочной массы, графита, смазки, металлической стружки, маркировочной краски.
1.2.2. На поверхности литых изделий не должно быть пор и усадочных раковин.
1.2.3. Сварные швы должны быть равномерными, плотными и сплошными по всей длине.
Не допускаются поры, свищи, трещины, шлаковые включения, наплавные сопряжения сварных швов.
1.2.4. Острые углы и кромки изделий, за исключением технически обоснованных случаев, должны быть скруглены радиусом не менее 0,3 мм.
1.2.5. Поверхность изделий, подлежащих горячему цинкованию, должна быть очищена обезжириванием, последующим травлением или струйно-абразивной обработкой, затем офлюсована.
Степень очистки поверхности от окалины и продуктов коррозии - 1 по ГОСТ 9.402.
2.1. Внешний вид покрытия
2.1.1. При внешнем осмотре поверхность цинкового покрытия должна быть гладкой или шероховатой, покрытие должно быть сплошным.
Цвет покрытия от серебристо-блестящего до матового темно-серого.
2.1.2. На поверхности изделий не должно быть трещин, забоин, вздутий.
2.1.3. Наличие наплывов цинка недопустимо, если они препятствуют сборке. Крупинки гартцинка диаметром не более 2 мм, рябизна поверхности, светло-серые пятна и цвета побежалости, риски, царапины, следы захвата подъемными приспособлениями без разрушения покрытия до основного металла не являются дефектами.
Допустимо восстановление непрокрытых участков, если они не шире 2 см и составляют не более 2 % общей площади поверхности. Непрокрытые участки защищают слоем цинк-содержащего лакокрасочного покрытия (минимальная толщина 90 мкм, массовая доля цинка в сухой пленке 80 - 85 %) или газотермическим напылением цинка (минимальная толщина 120 мкм).
2.2. Толщина покрытия
Толщина покрытия должна быть не менее 40 мкм и не более 200 мкм и определяется условиями эксплуатации оцинкованных изделий и нормативно-технической документацией на конкретное изделие.
2.3. Прочность сцепления
Покрытие обладает удовлетворительным сцеплением, если выдерживает испытания по методам, приведенным в п. 4.4.
3.1. Перед нанесением покрытий 2 - 5 % изделий из партии, но не менее трех, а для изделий единичного производства - каждое изделие контролируют на соответствие пп. 1.1, 1.2.
3.2. Полуфабрикаты (проволоку, трубы и т.п.) подвергают входному контролю на соответствие требованиям нормативно-технической документации на поставку и требованиям пп. 1.1, 1.2.
3.3. Нанесенное цинковое покрытие подвергают контролю по внешнему виду, толщине и прочности сцепления.
На контроль предъявляют каждую партию оцинкованных изделий. За партию принимают единицу продукции или груза, состоящую из одного или более изделий одинакового типа и размера, принадлежащих к одному заказу, если на них нанесено покрытие за одну смену и в одной и той же ванне.
3.4. Контроль внешнего вида покрытий проводят на 100 % изделий.
3.5. Контролю толщины и прочности сцепления подвергают:
1) элементы стальных конструкций в количестве до 1 %, но не менее 2 шт. от партии;
2) сварные узлы в количестве до 5 %, но не менее 1 штуки от партии;
3) резьбовые крепежные детали в количестве до 0,5 %, но не менее 3 штук от партии.
Допускается применение методов статистического контроля по ГОСТ 18242.
Контроль толщины покрытия металлографическим методом допускается проводить на одной детали из партии.
3.6. Изделия, на которых проводился контроль качества разрушающими методами, разрешается предъявлять к приемке после восстановления покрытия.
3.7. Контроль толщины покрытия
3.7.1. Контроль толщины покрытия проводят до его дополнительной обработки (хроматирование, нанесение консервационных смазок и т.п.).
3.7.2. Толщину покрытия контролируют на поверхности, но имеющей накатки и резьбы на расстоянии не менее 5 мм от ребер, углов, отверстий и мест контакта с приспособлением. Толщину покрытия на резьбовых крепежных деталях контролируют на головках болтов и на торцах гаек.
3.7.3. Измерительный инструмент для неразрушающего контроля толщины покрытия должен иметь погрешность измерения не более ±10 %.
3.8. При получении неудовлетворительных результатов контроля толщины и прочности сцепления проводят повторный контроль на удвоенном количестве деталей.
При получении неудовлетворительных результатов повторного контроля всю партию оцинкованных изделий бракуют.
3.9. Контроль состава ванны горячего цинкования по требованию заказчика проводят до извлечения изделий из ванны.
4.1. Контроль внешнего вида
Внешний вид покрытий контролируют визуальным осмотром невооруженным глазом при освещенности не менее 300 лк на расстоянии 25 см от контролируемой поверхности.
4.2. Контроль толщины покрытия
4.2.1. Магнитный метод
Метод основан на регистрации изменения магнитного сопротивления в зависимости от толщины покрытия. В качестве измерительных приборов используют магнитные толщиномеры.
За результат измерения толщины покрытия принимают среднее арифметическое значение не менее пяти измерений у краев и в середине контролируемой поверхности одного изделия.
Относительная погрешность метода ±10 %.
4.2.2. Металлографический метод (арбитражный)
Метод основан на измерении толщины покрытия на поперечном шлифе с применением металлографических микроскопов различных типов.
Образец для изготовления шлифа вырезают из оцинкованного изделия.
Толщину цинкового покрытия измеряют на шлифе в трех и более точках, равномерно распределенных на линейном участке длиной около 1 см. За результат принимают среднее арифметическое результатов всех измерений.
Относительная погрешность метода ±10 %.
4.2.3. Среднюю толщину покрытия (Нср) в микрометрах определяют неразрушающими методами или гравиметрическим методом по разности масс образца до и после получения или до и после снятия покрытия по ГОСТ 9.302.
Для снятия покрытия применяют раствор: 3,2 г хлористой сурьмы или 2 г трехокиси сурьмы растворяют в 500 см3 соляной кислоты, плотностью 1,19 г/см3, ч.д.а., по ГОСТ 3118 в мерной колбе вместимостью 1 дм3 и доводят до метки дистиллированной водой по ГОСТ 6709.
Относительная погрешность гравиметрического метода ±10 %.
4.3. Контроль химического состава цинкового расплава - по ГОСТ 19251.1, ГОСТ 19251.2, ГОСТ 19251.3, ГОСТ 19251.5.
Массовая доля цинка в рабочем объеме ванны должна быть не менее 98 %.
4.4. Контроль прочности сцепления покрытий
4.4.1. Метод нанесения сетки царапин (при толщине покрытий до 50 мкм)
На очищенной поверхности контролируемого покрытия инструментом со стальным острием под углом 30° (твердость металла острия должна быть выше твердости покрытия) наносят по четыре - шесть параллельных линий глубиной до основного металла на расстоянии от 2,0 до 3,0 мм друг от друга и перпендикулярно к ним. Линии проводят в одном направлении. Прочность сцепления удовлетворительна, если на контролируемой поверхности не наблюдается отслаивание покрытия.
4.4.2. Метод крацевания
Для метода крацевания применяют стальные и латунные щетки диаметром проволоки 0,1 - 0,3 мм и скоростью вращения щеток - 1500 - 2800 мин-1.
Поверхность покрытия крацуют не менее 15 с. После крацевания на контролируемой поверхности не должно наблюдаться вздутия или отслаивания покрытия.
4.4.3. Метод нагрева
При применении метода нагрева детали с покрытием или образцы-свидетели нагревают до (190 ± 10) °С, выдерживают при данной температуре в течение 1 ч и охлаждают на воздухе. На контролируемой поверхности не допускаются вздутия или отслаивания покрытия.
4.4.4. Метод удара поворотным молотком
Плоскую поверхность изделия с толщиной основного металла не менее 3 мм очищают от пыли, механических загрязнений и обезжиривают органическими растворителями.
На плоскую поверхность изделия устанавливают поворотный молоток массой 212,5 г таким образом, чтобы головка молотка вертикально падала на горизонтальную поверхность изделия. Производят не менее двух ударов молотком так, чтобы расстояние между параллельными отпечатками составляло 6 мм, а расстояние от края отпечатка до края изделия составило не менее 13 мм.
Схема поворотного молотка приведена в приложении
Рекомендуемое
1 - молот; 2 - прижимная плита; 3 - поверхность образца; х - размер, определяемый опытным путем в зависимости от металла, из которого изготовлена головка молотка
ИНФОРМАЦИОННЫЕ ДАННЫЕ
1. РАЗРАБОТАН И ВНЕСЕН Государственным строительным комитетом СССР
РАЗРАБОТЧИКИ
С.В. Марутьян, канд. техн. наук (руководитель темы), С.А. Клочко, Л.Н. Павлова, С.Г. Гутник, Л.М. Белоусова
2. УТВЕРЖДЕН И ВВЕДЕН В ДЕЙСТВИЕ Постановлением Государственного комитета СССР по стандартам от 30.05.89 № 1379
3. Срок первой проверки - 1995 г.
Периодичность проверки - 5 лет
4. Стандарт полностью соответствует международным стандартам ИСО 1461-89, СТ СЭВ 4663-84
5. ВЗАМЕН ГОСТ 9.307-85
6. ССЫЛОЧНЫЕ НОРМАТИВНО-ТЕХНИЧЕСКИЕ ДОКУМЕНТЫ
7. ПЕРЕИЗДАНИЕ. Апрель 1992 г.
СОДЕРЖАНИЕ
snipov.net