организация производства раздатки и РГР / поточная линия. Поточные линии
2. Классификация поточных линий
В промышленности применяются разнообразные виды поточных линий. В основу классификации форм поточных линий положены признаки, которые наиболее существенно влияют на организационное их построение: степень специализации производства, способ поддержания ритма, уровень механизации и автоматизации труда и др. (рисунок 2).
1. По степени специализации различают:
- однопредметные и
- многопредметные поточные линии.
Для однопредметных поточных линий, которые являются постоянно-поточными характерно:
- производство одного вида продукции в течение длительного периода времени до смены объекта производства на заводе;
-постоянно действующий, несменяемый технологический процесс;
- большой масштаб производства однотипной продукции.
Эти линии применяются в условиях массового или крупносерийного производства.
Многопредметные поточные линии создаются в тех случаях, когда программа выпуска продукции одного вида не обеспечивает достаточной загрузки линии. В зависимости от метода чередования объекта производства многопредметные линии подразделяются на:
- переменно-поточные и
- групповые.
Переменно-поточная линия – это линия, на которой обрабатывается несколько конструктивно-однотипных изделий разного наименования, обработка ведется поочередно через определенный интервал времени с переналадкой рабочих мест (оборудования) или без их переналадки. В период изготовления предметов определенного наименования такая линия работает по тем же принципам, что и однопредметная.
Групповая линия – это линия, на которой обрабатывается несколько изделий разных наименований по групповой технологии с использованием групповой оснастки либо одновременно, либо поочередно, но без переналадки оборудования (рабочих мест).
2. По степени непрерывности технологического процесса различают:
- непрерывные и
- прерывные (прямоточные) линии.
Как непрерывно-поточными, так и прерывно-поточными могут быть одно- и многопредметные поточные линии.
На непрерывно-поточных линиях предметы труда с операции на операцию непрерывно передаются поштучно или небольшими транспортными партиями через одинаковый промежуток времени, равный такту или ритму потока. Непрерывно-поточные линии используются на всех стадиях производства. Такой технологический процесс называют синхронизированным.
Прерывно-поточные линии создаются, когда отсутствует равенство или кратность длительности операций такту и полная непрерывность производственного процесса не достигается. Для поддержания беспрерывности процесса на наиболее трудоемких операциях создаются межоперационные оборотные запасы.
3. По способу поддержания ритма различают:
- линии с регламентированным и
- свободным ритмом.
Линии с регламентированным ритмом характерны для непрерывно-поточного производства. Здесь ритм поддерживается с помощью конвейеров, перемещающих предметы труда с определенной скоростью, или с помощью световой (звуковой) сигнализации при отсутствии конвейера.
Линии со свободным ритмом не имеют технических средств, строго регламентирующих ритм работы. Эти линии применяются при любых формах потока (непрерывной и прерывной). Соблюдение ритма в этом случае возлагается непосредственно на работников данной линии. Его величина должна соответствовать расчетной средней производительности за определенный период времени (час, смену).
4. По виду использования транспортных средств различают линии:
- со средствами непрерывного действия;
- с транспортными средствами дискретного действия;
- без транспортных средств.
Линии с транспортными средствами непрерывного действия в зависимости от функций, выполняемых этими средствами, подразделяются на:
линии с транспортными конвейерами, которые предназначены для транспортировки предметов труда и поддержания заданного ритма работы линии;
линии с рабочими конвейерами, которые являются не только транспортными средствами, но и представляют собой систему рабочих мест, на которых осуществляются технологические операции без снятия предметов труда;
линии с распределительными конвейерами. Данные конвейеры применяются на поточных линиях с выполнением операций на стационарных рабочих местах и с различным количеством рабочих мест-дублеров на отдельных операциях, когда для поддержания ритмичности необходимо обеспечить четкое адресование предметов труда по рабочим местам.
Линии с транспортными средствами дискретного действия подразделяются на несколько видов:
- бесприводные (рольганги, скаты, спуски):
- подъемно-транспортное оборудование циклического действия (мостовые краны, монорельсы).
Линии без наличия транспортных средств – это линии с неподвижным предметом труда (сборка крупных объектов).
5. По характеру движения конвейера различают линии:
- с непрерывным и
- пульсирующим движением конвейера.
Линии с непрерывным движением конвейера создаются в тех случаях, когда по условию технологического процесса операции должны выполняться во время движения рабочего конвейера без снятия предметов труда с рабочих мест или операции должны выполняться на стационарных рабочих местах.
Линии с пульсирующим движением конвейера создаются в тех случаях, когда по условию технологического процесса операции должны выполняться при неподвижном объекте производства на рабочем конвейере.
6. по уровню механизации процессов различают:
- автоматические и
- полуавтоматические поточные линии.
Автоматические поточные линии характеризуются объединением в единый комплекс технологического и вспомогательного оборудования и транспортных средств с автоматическим централизованным управлением процессами обработки и перемещения предметов труда.
Полуавтоматические поточные линии объединят специальные станки-полуавтоматы (с последовательным, последовательно-параллельным и параллельным движением).
Таблица 1 – Классификация основных видов поточных линий
Признаки классификации | Виды поточных линий | |
1. Степень специализации | Однопредметные | Многопредметные |
1.1 Метод обработки | Непрерывно-поточные | Переменно-поточные Групповые |
2. Степень непрерывности процесса | Непрерывные Прерывные | |
3. Способ поддержания ритма | Регламентированный ритм | Свободный ритм |
3.1 Характер перемещения | Принудительное перемещение | Свободное перемещение |
4. Способ транспортировки предметов труда | Конвейеры | Прочие транспортные средства |
4.1 Тип конвейера | Транспортные Рабочие Распределительные | - |
5. Характер движения конвейера | Непрерывный Пульсирующий | - |
6. Уровень автоматизации и механизации процесса | Автоматические Полуавтоматические | Немеханизированные Механизировано-ручные |
studfiles.net
поточная линия
10.1. Понятие о поточном производстве. Классификация поточных линий.
Поточное производство – это прогрессивная и эффективная форма организации производственного процесса, основанная на ритмичной повторяемости согласованных во времени основных и вспомогательных операций, выполняемых на специализированных рабочих местах, расположенных по ходу технологического процесса.
Основным звеном поточного производства является поточная линия, т.е. цепочка рабочих мест расположенных по ходу технологического процесса, на которой осуществляется производственный процесс обработки или сборки изделий в соответствии с вышеуказанными признаками.
Поточные линии можно классифицировать по многим признакам.
По степени специализации различают: однопредметные и многопредметные.
На однопредметной поточной линии обрабатывается или собирается одно изделие. Такие линии используются в массовом типе производства.
На многопредметных поточных линиях обрабатываются или собираются несколько изделий. Они в свою очередь делятся на переменно-поточные и групповые.
Переменно-поточные линии – это линии, на которых обрабатываются несколько конструктивно-однотипных изделий разного наименования.
Групповые линии – это линия, на которой обрабатываются разные изделия по групповой технологии без переналадки оборудования.
По степени непрерывности технологического процесса различают непрерывные и прерывные (прямоточные) линии.
На непрерывно-поточных линиях время выполнения технологических операций равно или кратно такту поточной линии.
На прерывно-поточных линиях отсутствуют равенство или кратность длительности операций такту поточной линии.
По способу поддержания ритма (такта) различают линии с регламентированным и свободным ритмом (тактом).
Такт на линиях с регламентированным ритмом поддерживается с помощью световой или звуковой сигнализации. Такт на линиях со свободным ритмом поддерживается самими работниками данной линии.
По виду использования транспортных средств различают линии с транспортом непрерывного действия (конвейерами), с транспортными средствами дискретного действия и линии без транспортных средств.
Линии с транспортом непрерывного действия подразделяется на линии с транспортными конвейерами и на линии с рабочими конвейерами.
Линии с транспортными средствами дискретного типа подразделяются на такие виды: линии с использованием гравитационных транспортных средств (рольганги, скаты, спуски) и линии с использованием транспорта прерывного действия (краны, электротележки, автокары и т.д.).
Линии без наличия транспортных средств – это линии, где предметы труда находятся на едином рабочем месте, а переходы осуществляют рабочие, например, при сборке крупных изделий.
По характеру движения конвейера различают линии с непрерывным и пульсирующим движением конвейера.
По уровню механизации технологических операций различают автоматические и полуавтоматические поточные линии.
10.2. Расчет параметров однопредметной поточной линии.
Основным параметром поточной линии является такт (r), который определяется по формуле:
;
где - эффективный (действительный) фонд времени работы поточной линии в плановом периоде, мин.;
- программа запуска изделий, шт.
В тех случаях, когда передача изделий с операции на операцию осуществляется партиями (небольшие детали, малая величина такта) определяют ритм () поточной линии:
;
где - величина передаточной партии, шт.
Для обеспечения непрерывности работы поточной линии осуществляется синхронизация, т.е. достигается равенство или кратность времени выполнения операций технологического процесса такту поточной линии.
При проектировании поточной линии допускаются отклонения от такта в пределах до 10% , окончательная синхронизация осуществляется при отладке линии. Условия синхронизации можно записать так:
;
где ,, - штучное время на выполнение 1,2…..операций, шт.
, ……….- число рабочих мест на операциях.
Расчетное количество рабочих мест на каждой операции определяется по формуле:
;
Если технологический процесс не полностью синхронизирован, то количество рабочих мест получается дробным, оно округляется до целого числа.
Коэффициент загрузки рабочего места () определяется по формуле:
;
где: - принятое количество рабочих мест наоперациях.
Общий коэффициент загрузки рабочих мест () на поточной линии определяется так:
;
При использовании в качестве транспортных средств поточной линии конвейера определяется скорость его движения. При непрерывном движении конвейера его скорость () определяется по формуле:
где: L – шаг конвейера, т.е. расстояние между осями смежных изделий, расположенных на конвейере, м.
При пульсирующем движении конвейера его скорость определяется по формуле:
где: - время транспортировки изделия на один шаг конвейера, мин.
Наиболее оптимальная скорость конвейера от 0,1 до 2,5 м/мин.
Длительность производственного цикла () изготовление изделия на поточной линии определяется по формуле:
где: - длина резервной зоны конвейера, м.
На непрерывных поточных линиях создаются заделы трех видов: технологический, транспортный, страховой.
Технологический задел (Zтех) – это детали (изделия), находящиеся на рабочих местах в процессе обработки или сборки. Он определяется по формуле:
При передаче изделий партиями (р), величина технологического задела определяется по формуле:
;
Транспортный задел () – это детали находящиеся в процессе транспортировки. Его величина при поштучной передаче деталей равна:
;
При передаче транспортными партиями:
;
Резервный (страховой) задел создается на наиболее ответственных и нестабильных по времени выполнения операциях. Его величина в среднем составляет 4-5% от сменного задания или может быть определена по формуле:
;
где: - время , на которое создается резервный запас деталей наi й операции, мин.
10.3. Особенности организации прерывно-поточных линий (ППЛ)
Такие линии создаются в основном в механических цехах, когда не удается достичь полной синхронизации операций. Для них характерны прерывность в движении деталей (изделий) по операциям, прерывность в работе оборудования и рабочих на операциях.
Основные параметры прерывно-поточной линии определяются также, как и для однопредметной непрерывной поточной линии.
Для расчета и организации ППЛ определяют период оборота, составляют план-график ее работы и определяют величину оборотных заделов.
Период оборота () – это время, через которое работа на ППЛ повторяется в том же порядке. Как правило, в практической деятельности за величину периода оборота принимают одну смену (=480 мин.) или полсмены (=240 мин.).
Прежде чем составить план-график работы ППЛ, необходимо определить период оборота, такт ППЛ, расчетное и принятое количество рабочих мест, загрузку рабочих мест и построить график работы оборудования и рабочих в течении выбранного периода оборота. Упрощенный план – график представлен в табл. 3.
Таблица 3.
План – график работы ППЛ.
№ операции | tшт. норма времени (мин.) | Wчисло рабочих мест | № рабочего места | Коэффициент загрузки рабочего места | Рабочие на линии | График работы оборудования и рабочих за период оборота 240 мин. | |||||
расчетное | принятое |
60 120 180 240 0 | |||||||||
1 | 1,0 | А | 240 мин. | ||||||||
1 | 8 | 2 | 2 | 2 | 1,0 | Б | 240 мин. | ||||
2 | 1,2 | 0,3 | 1 | 3 | 0,3 | В | 72 мин. | ||||
3 | 2,0 | 0,5 | 1 | 4 | 0,5 | В | 120 мин. | ||||
4 | 0,8 | 0,2 | 1 | 5 | 0,2 | В | 48 мин. | ||||
5 | 4 | 1 | 1 | 6 | 1,0 | Г | 240 мин. |
где - время работы оборудования и рабочих
- время простоя оборудования;
- переходы рабочих с одного места на другое.
Для ППЛ, показанной в таблице r = 4мин.
Рабочие А,Б и Г полностью заняты выполнением своих технологических операций в течение периода оборота. Рабочий В последовательно выполняет в течение периода оборота 2,3 и 4 операции, при этом на 2ой операции он занят 72 мин. (2400,3), на 3ей операции 120 мин. (2400,5) и на 4ой операции 48 мин. (2400,2).
На смежных операциях вследствие различной их трудоемкости создаются межоперационные оборотные заделы. Величина заделов определяется по формуле:
;
- величина оборотного задела между i и i+1 операциями, шт.;
Т – период времени работы на смежных операциях при неизменном числе работающих станков, мин.;
Wi, Wi+1 – число единиц оборудования, работающих на смежных i и i+1 операциях в течении периода времени Т;
, - норма штучного времени на этих операциях.
Величина может получится со знаком + и со знаком - .
Если получится со знаком +, то за период времени Т величина оборотного задела будет возрастать, еслиполучится со знаком -, то за период времени Т величина оборотного задела будет убывать.
Расчет межоперационных оборотных заделов представлен в таблице 4.
Таблица 4
График движения межоперационных оборотных заделов.
№ операции и заделы | График работы оборудования и рабочих за период оборота 240 мин. |
0 60 120 180 240 | |
1ая | |
Задел между 1ой и 2ой операциями | |
2ая | |
Задел между 2ой и 3ей операциями | |
3ая | |
Задел между 3ей и 4ой операциями | |
4ая | |
Задел между 4ой и 5ой операциями | |
5ая |
Рассчитаем динамику задела между 1ой и 2ой операциями. Между 1ой и 2ой операцией два периода времени, когда на них работает неизменное количество станков – 72 мин. и 168 мин.
В течение 72 мин. на 1ой операции работают два станка, а на второй операции один станок. В течение 168 минут на 1ой операции работают два станка, а на второй операции станок простаивает. Тогда:
Между 2ой и 3ей операцией имеются три периода времени, когда на них работает неизменное количество станков – 72 мин., 120 мин. и 48 мин. В течение 72 мин. на 2ой операции работает один станок, а на 3ей операции станок не работает.
В течение 120 мин. на 2ой операции станок не работает, на 3ей операции работает один станок.
В течение 48 мин. на 2ой и 3ей операциях станки не работают. Определим оборотные заделы.
Аналогично определяют заделы между другими операциями и строят эпюры заделов.
studfiles.net
6.Виды поточных линий и их особенности.
Поточным называется производство, в котором в установившемся режиме над упорядоченно движущейся совокупностью однотипных изделий одновременно выполняются все операции, кроме быть может, незначительного их числа с не полностью загруженными рабочими местами.
Поточное производство в его наиболее совершенной форме обладает совокупностью свойств, отвечающих в максимальной степени принципам рациональной организации производства. Основными такими свойствами являются следующие.
·Строгая ритмичность выпуска изделий. Ритм выпуска- это количество изделий, выпускаемых в единицу времени. Ритмичность - это выпуск изделий с постоянным во времени ритмом.
·Такт выпуска- это промежуток времени, через который периодически производится выпуск одного или одинакового числа изделий определенного типа .
Виды поточных линий.
Поточная линия- это обособленная совокупность функционально взаимосвязанных рабочих мест, на которой осуществляется поточное производство изделий одного или нескольких типов.
По номенклатуре закрепляемых за ПЛ изделий различают:
· Однопредметные ПЛ, каждая из которых специализирована на производстве изделий одного вида
· Многопредметные ПЛ, на каждой из которых одновременно или последовательно изготавливаются изделия нескольких типов, сходных по конструкции или технологии их обработки или сборки.
По характеру прохождения изделиями всех операций производственного процесса различают:
· Непрерывно-поточные линии, на которых изделия непрерывно, т.е. без межоперационных пролеживаний, проходят через все операции их обработки или сборки
· Прерывно-поточные линии, которых имеются межоперационные пролеживания, т.е. прерывность обработки или сборки изделий.
По характеру такта различают:
· Поточные линии с регламентированным тактом, в которых такт задается принудительно с помощью конвейеров, световой или звуковой сигнализации.
· Поточные линии со свободным тактом, на которых выполнение операций и передача изделий с одной операции на другую, могут производится с небольшими отклонениями от установленного расчетного такта.
В зависимости от порядка обработки на них изделий различных типов делятся на:
· Многопредметные поточные линии с последовательно-партионным чередованием партий изделий различных типов, в которых каждый тип изделий монопольно обрабатывается в течении определенного периода, а обработка различных типов изделий осуществляется последовательно чередующими партиями. На линиях такого типа необходимо рационально организовать переход от выпуска изделий одного типа к выпуску другого:
- одновременно на всех рабочих местах поточной линии прекращается сборка изделий нового типа. Достоинством является отсутствие потерь рабочего времени, однако это требует создания на каждом рабочем месте задела изделий каждого типа, находящихся в той стадии готовности, которая соответствует выполненной операции по данному рабочему месту.
-изделия нового типа запускаются на поточную линию до момента окончания сборки партии изделий предыдущего типа, и на поточной линии в переходный период устанавливается максимальный из двух возможных тактов для старого и нового типов изделий. Однако в переходный период возможны простои рабочих на тех рабочих местах, на которых происходит сборка изделий с меньшим требуемым тактом, чем установленный в данный момент.
· Групповые поточные линии, которые характеризуются одновременной обработкой на поточной линии партий изделий нескольких типов.
studfiles.net
ПОТОЧНЫЕ ЛИНИИ, ИХ ЭЛЕМЕНТЫ, ПАРАМЕТРЫ И КЛАССИФИКАЦИЯ
Наиболее прогрессивным методом организации основного производства является поточный метод, который соответствует принципам рациональной организации производства.
Поточное производство имеет следующие основные признаки:
§ расчленение производственного процесса на операции;
§ закрепление каждой операции за определенным рабочим местом, машиной;
§ одновременное выполнение всех операций;
§ немедленная передача предмета труда с одной операции на другую;
§ расположение технологического оборудования по ходу технологического процесса.
Технологическое оборудование, расположенное в последовательности выполнения технологического процесса, образует поточную линию. Расчленение производственного процесса на составные части, повторяющиеся на каждом рабочем месте, вызывает необходимость постоянного перемещения предметов труда от одного рабочего места к другому, которое может осуществляться механизмами и вручную. Чтобы каждое предыдущее рабочее место непрерывно давало работу каждому последующему, необходима согласованность продолжительности выполнения операций на рабочих местах. Этим обеспечивается непрерывность производственного процесса и сокращение перерывов в движении предмета труда. В зависимости от того, как реализуются эти требования, поточные линии подразделяют на ряд видов.
По количеству машин, закрепленных за одним рабочим местом, поточные линии делятся на простые и сложные. Простой поточной линией называется такая, в которой на каждом рабочем месте используется одна машина. К сложным поточным линиям относятся такие, в которых на отдельных рабочих местах установлены не одна, а несколько однотипных машин, выполняющих определенную технологическую операцию.
По степени механизации поточные линии подразделяются на линии с преобладанием ручного труда, частично механизированные, комплексно-механизированные и автоматизированные.
По степени специализации поточные линии делятся на однопредметные и многопредметные. На однопредметных линиях вырабатывается один вид продукции, например хлеб ржаной, батоны рижские, булки городские.
На многопредметных линиях вырабатываются различные, но технологически однородные виды продукции, например, конфеты «Ласточка», «Буревестник», «Весна», сухари сливочные, ванильные, лимонные.
По степени охвата производства линии подразделяют на участковые и сквозные. Участковые поточные линии охватывают какую-либо часть производственного процесса, сквозные — весь производственный процесс.
По расположению в пространстве поточные линии могут быть горизонтальными, вертикальными и смешанными.
По способу перемещения предмета труда от одной операции к другой линии делятся на конвейерные и бесконвейерные. В конвейерных линиях в качестве транспортных средств используется транспортер, в бесконвейерных — тележки, электрокары, рольганги.
По способу поддержания ритма линии могут быть с регламентированным и со свободным ритмом. Регламентированный ритм обеспечивается применением автоматического оборудования не только на технологических, но и на перемещающих операциях, в результате чего предмет труда поступает с одного места к другому через строго определенные промежутки времени. На поточных линиях со свободным ритмом скорость передачи предмета труда определяется рабочим.
По форме поточные линии могут быть прямыми, замкнутыми, змеевидными, собирательными, П-образными и пр.
Производственные поточные линии или их совокупность образуют производственный поток, который может быть однолинейным и многолинейным. Однолинейный поток образует одна простая или сложная линия. Многолинейный поток состоит из нескольких поточных линий и может быть простым и сложным. Простой многолинейный производственный поток состоит из нескольких последовательно расположенных линий.
Сложный многолинейный поток включает в себя несколько поточных линий, расположенных последовательно и параллельно. Производственный поток может быть непрерывным и прерывным.
Прерывный поток имеет все признаки потока, но характеризуется отсутствием согласованной производительности рабочих мест потока и значительным расхождением между ритмами каждого рабочего места и заданного ритма потока. Синхронизации операций в этом случае достичь нельзя. Загрузка оборудования и рабочих мест на таких линиях недостаточно равномерна, и неизбежны простои машин и рабочих на некоторых рабочих местах.
Прерывный поток является наименее совершенной формой поточного производства, но он имеет существенные преимущества перед непоточной формой организации производства. Эти преимущества состоят в том, что резко сокращаются промежутки времени между выпуском двух готовых изделий, следующих одно за другим, или двух порций (партий) продукции.
Непрерывный производственный поток — наиболее совершенная форма организации поточного производства. Он соответствует всем признакам потока, и все рабочие места в нем согласованы по производительности. Ритмы рабочих мест равны между собой и ритму потока. Предмет труда перемещается с одной операции на другую без пролеживания.
Равенство или кратность времени выполнения каждой операции ритму поточной линии обеспечивается синхронизацией технологического процесса. В результате создается возможность организации графика параллельного вида движения предметов труда и непрерывного протекания производственного процесса. Это создает условия для непрерывной работы всех машин потока.
Для организации ритмичной работы поточных линий большое значение имеет выбор вида межоперационного транспорта.
Назначение транспортных средств в поточном производстве состоит не только в обслуживании рабочих мест, но и в поддержании заданного ритма потока путем принудительного перемещения изделий с одной операции на другую.
Средства межоперационного транспорта, применяемого на поточных линиях, разнообразны. Их можно разделить на приводные и бесприводные. Приводные средства делятся на подъемно-транспортные механизмы (например, нории в мукопросеивательном отделении хлебозавода) и конвейеры непрерывного действия (например, конвейеры, перемещающие тестовые заготовки в расстойных шкафах и печах непрерывного действия).
Для перемещения тяжелых грузов (мешки с мукой, сахарным песком и пр., фляги, бочки) используются рольганги. Наиболее распространенное стационарное устройство для перемещения мелких изделий (конфеты, печенье, сухари) — наклонные лотки (склизы), по которым изделия перемещаются под действием собственной массы.
Организация поточных линий предъявляет особые требования как к размещению технологического оборудования, так и к выбору различного вида транспортных средств. Для поточного производства установленного ритма выбирают транспортные средства соответствующей производительности, имеющие соответствующую скорость, обеспечивающую установленный ритм.
Скорость конвейера v (м/мин) определяется по формуле v = l/r,
где l — шаг конвейера, м; r — ритм поточной линии, минут на единицу продукции.
Ритмичность потока или поточной линии отражает показатель затрат времени r, который называется ритмом (тактом). Этот показатель рассчитывается по формуле
rп = В/П,
где В —плановый фонд времени работы в смену (сутки), ч; П —задание потоку (поточной линии) по выработке продукции в смену (сутки), т.
Ритм потока — это промежуток времени между выпуском двух следующих одна за другой единиц готовой продукции с последней операции потока (поточной линии).
Следовательно, темп потока характеризует его производительность. В том случае, если поток является многопредметным, выпускающим несколько видов технологически однородной продукции, величина ритма устанавливается для каждого вида продукции отдельно.
Например, конфетный цех работает в две смены, количество рабочих дней в месяце 22, месячное производственное задание потоку и трудоемкость вырабатываемой продукции следующие:
Вид конфет | План по выработке продукции, т | Трудоемкость 1 т, чел.-ч |
«Ласточка» | ||
«Лето» | ||
«Маска» | ||
Время, которое должно быть затрачено на выработку каждого вида продукции, распределяется в следующем соотношении:
Вид конфет | ||
«Ласточка» | 90*50=4500 чел. ч. | 38,3 % |
«Лето» | 70*57=3990 чел. ч. | 34 % |
«Маска» | 50*65=3250 чел. ч. | 27,7 % |
Всего | 11740 чел. ч. | 100 % |
Загрузка потока по количеству смен в расчете на каждый вид продукции составит:
«Ласточка» | 22*2*0,383= 17 смен |
«Лето» | 22*2*0,34 = 15 смен |
«Маска» | 22*2*0,277= 12 смен |
Отсюда величина ритмов потока rп ( в пересчете на 1 т) будет равна
«Ласточка» | 17*480/90= 91 мин |
«Лето» | 15*480/70= 102 мин |
«Маска» | 12*480/50= 115 мин |
Наряду с ритмом потока (поточной линии) важнейшими характеристиками поточной линии являются ритмы рабочих мест.
Ритм рабочего места rр.м. — это промежуток времени между смежными одинаковыми и повторяющимися частичными процессами труда или операциями, выполняемыми на данном рабочем месте. Он определяется как отношение:
rр.м.= T/Z,
где Т — плановый фонд рабочего времени, на который рассчитано производственное задание рабочему месту, ч, смены, сут; Z — производственное задание рабочему месту, единицы продукции.
Производственное задание рабочему месту — это такое количество предметов труда, которое должно быть обработано на данном рабочем месте в единицу времени, чтобы обеспечить непрерывную работу ведущей машины. Производственное задание Z (в единицах продукции) рассчитывается по формуле
Z= qa,
где q — выработка ведущей машины потока в ту же единицу времени, единицы продукции; а — коэффициент расхождения между выработкой ведущей машины потока и выработкой данного рабочего места.
Производственное задание измеряется в тех единицах предметов труда, которые обрабатываются на данном рабочем месте. Например, производственное задание тесторазделочному отделению измеряется в количестве тестовых заготовок, тестомесильному — в количестве деж теста, варочному отделению карамельного цеха — в тоннах карамельной массы, упаковочному отделению — в количестве коробов упакованной продукции.
Поскольку предметы труда, обрабатываемые на ведущей машине, и предметы труда, обрабатываемые на рабочих местах, по технологической готовности и массе неодинаковы, для обеспечения сопоставимости их вводится коэффициент расхождения между выработкой ведущей машины и выработкой данного рабочего места. Этот коэффициент учитывает расхождения между выработкой ведущей машины и выработкой рабочего места, возникающие в результате технологических и механических потерь в производстве, из-за разного удельного веса продуктов, обрабатываемых на данном рабочем месте, в составе готовых изделий.
Для поточных линий в пищевой промышленности характерно наличие машины, выполняющей наиболее важную и трудоемкую операцию по превращению сырья в готовый продукт. Производительность этой машины определяет производительность всей поточной линии. Такая машина называется ведущей машиной потока. Так, в хлебопекарном производстве ведущей машиной является печь, в карамельном — формующие машины (штампующие, режущие), в конфетном — отливочные и отсадочные машины, размазные конвейеры, в шоколадном — плиточные отливочные агрегаты, в масло-жировом — прессы (при прессовом методе переработки семян) и экстракторы (при экстракционном методе получения масла).
В ряде отраслей пищевой промышленности ведущим в производственном потоке является комплекс машин, а не одна машина. Так, в макаронном производстве к ведущему оборудованию относят сушильные аппараты различных конструкций в комплексе с формовочным оборудованием. В автоматических линиях сушильные аппараты составляют единое целое с прессовым оборудованием и производительность их одинакова. В скомпонованных линиях непрерывно действующие прессы работают в сочетании с непрерывно и прерывно действующими сушильными аппаратами и производительность их может быть различной.
На заводах первичного виноделия ведущим оборудованием являются прессы и емкости для размещения производимых виноматериалов, на спиртовых заводах — солодовни, бродильные чаны, брагоперегонные аппараты. Для рациональной организации потока в первую очередь необходимо обеспечение согласованности этих машин по производительности, так как этим обусловливается одинаковая продолжительность обработки предмета труда на различных машинах.
Продолжительность обработки предмета труда на данном рабочем месте или данной машине может быть равна ритму этого рабочего места или отличается от него. Разница между ритмом и продолжительностью обработки предмета труда обусловлена различием показателей, на основе которых они рассчитываются. Если ритм рассчитывается на основе производственного задания рабочему месту (машине), то продолжительность обработки to6 — на основе производительности машины:
to6 = B / N,
где В— плановый фонд времени работы в смену (сутки), ч; N — производительность машины в смену (сутки), единицы продукции.
Так как производственное задание рабочему месту не всегда соответствует производительности машины на данном рабочем месте, то и ритм не всегда соответствует продолжительности обработки предмета труда на данном рабочем месте.
В том случае, если производственное задание рабочему месту меньше производительности установленной на нем машины, ритм будет превышать продолжительность обработки. Разница между ритмом и продолжительностью обработки представляет собой время простоя или холостого хода машины, повторяющегося с каждым предметом труда.
Например, спиртовой завод располагает бродильными чанами общей вместимостью 1100 м3, позволяющими получать в сутки с 1 м3 2 дал спирта, и бражной колонной брагоперегонного аппарата производительностью 2500 дал спирта в сутки. Отсюда производственное задание брагоперегонному аппарату составляет 2200 дал (1100*2).
Ритм рабочего места в расчете на 1 дал rр. м = 1440/2200 = 0,7 мин, продолжительность обработки 1 дал спирта to6 = 1440/2500 = 0,6 мин. При этих условиях возникнут перерывы в работе оборудования, нарушится основное требование непрерывности потока — согласованность оборудования по производительности.
В целях реализации важнейшего принципа рациональной организации производства — непрерывности — необходимо соблюдать условие, при котором продолжительность обработки предмета труда равна или кратна ритму, а производственное задание равно производительности оборудования.
Если поточная линия простая, то длительность обработки на каждом рабочем месте должна быть одинаковой, а если поточная линия сложная, то продолжительность обработки равна или кратна ритму. На тех рабочих местах, где продолжительность обработки больше ритма или кратна ему, устанавливаются дополнительные машины. Количество дополнительных машин Км.д определяют по формуле
Км.д=tоб/rр. м — 1 ,
Например, ритм рабочего места по завертке конфет 0,15 мин/кг, а продолжительность обработки 0,9 мин/кг. В этом случае потребуется дополнительных машин Км.д= 0,9/0,15—1= 6—1 = 5.
Приведение продолжительности обработки на каждом рабочем месте в соответствие с ритмом рабочего места и ритмом потока, которое носит название синхронизации операций, связано с проведением ряда предварительных расчетов, обеспечивающих сопоставимость этих показателей.
Синхронизация технологических операций является непременным условием организации непрерывного потока.
Синхронизация операций может осуществляться либо путем дифференциации, либо путем концентрации операций технологического процесса. Если длительность операций больше ритма, применяется дифференциация или организуются параллельно действующие рабочие места.
Для обеспечения равенства продолжительности обработки ритму применяют также комбинирование операций, т. е. совмещение выполнения двух или более операций.
Необходимое общее количество машин на каждом рабочем месте Км определяют по формулам
Км = tобр / r р.м.
или
Км = Z/N т.э.
где Z — производственное задание рабочему месту на определенный период времени (смену, сутки), единицы продукции; N т..э. — производительность машины на данном рабочем месте (по технико-экономической норме) за тот же период времени, единицы продукции.
Например, цех должен за год выработать 4000 т ириса. Технико-экономическая норма производительности формующе-завертывающего агрегата 180 кг/ч. Количество рабочих смен за год 488, регламентированные перерывы 0,5 ч в смену. Время работы агрегата за год 488(8—0,5) =3660 ч. Количество машин, необходимое для выполнения годового задания, К= 4000/(0,18Х X 3660) =6.
Коэффициенты загрузки машин Кз могут быть определены по этому же принципу:
где n — количество машин; Км. р — расчетное необходимое количество машин; Км.п. — принятое для установки в потоке количество машин.
4 ОСНОВЫ РАСЧЕТА И АНАЛИЗА ПРОИЗВОДСТВЕННОГО ПОТОКА
Основным условием организации непрерывного производственного потока как высшей формы поточного производства является полная согласованность производительности всех рабочих мест, обеспечивающая равенство ритмов рабочих мест между собой и ритму потока.
Однако ритм рабочего места рассчитывается на единицу предмета труда, обрабатываемого на данном рабочем месте, а ритм потока — на единицу готовой продукции. Значения продолжительности обработки на каждом рабочем месте несопоставимы, так как рассчитываются на единицу предмета труда, находящегося в различной степени технологической готовности. Например, не имеет практического смысла сравнение продолжительности варки 1 т карамельной массы и продолжительности завертки 1 т карамели, как и сравнение ритмов этих рабочих мест.
Между тем составить проект производственного потока или выполнить анализ его организации невозможно, не определив согласованности производительности рабочих мест, соответствия ритмов рабочих мест ритму потока, продолжительности обработки и ритмов на каждом рабочем месте. Только сопоставление этих параметров потока позволяет судить об уровне его организации, о наличии прерывного или непрерывного потока, о неиспользованных резервах. В определении указанных параметров и состоит расчет потока.
Задача расчета потока в общем виде заключается в том, чтобы привести в сопоставимый вид задание по выпуску готовой продукции с производительностью машин потока; определить необходимое количество оборудования и уровень его загрузки, а также необходимую численность рабочих для выполнения задания на тех рабочих местах, где операции выполняются вручную; дать оценку уровня организации потока.
Эта задача может быть решена двумя способами:
1) на основе определения производственных заданий каждому рабочему месту исходя из требования обеспечить непрерывную работу ведущей машины потока;
2) на основе определения приведенной производительности машин потока, обеспечивающей возможность сопоставления их по производительности.
Первый способ предпочтителен при проектировании поточных линий, в которых имеется ведущая машина и высок удельный вес ручных операций, второй — на этапе анализа организации действующего потока и в том случае, если в потоке нет одной ведущей машины. Рассмотрим оба способа расчета потока на примерах.
Пример 1. Расчет потока на основе определения производственных заданий рабочим местам состоит из следующих этапов:
§ расчета загрузки ведущих машин потока и уточнения задания по выработке продукции с учетом возможностей их специализации;
§ определения производственного задания рабочим местам потока и ритмов;
§ организации труда на рабочих местах потока.
В хлебопекарном производстве ведущей машиной потока является хлебопекарная печь. Поэтому расчет потока начинают с расчета загрузки хлебопекарных печей и определения количества печей, необходимых для выполнения задания. За основу расчета принимаются технико-экономическая норма производительности печи и плановый выход изделий. Если суточный заказ по выработке батонов из пшеничной муки составляет 9 т, а технико-экономическая норма производительности печи при выпечке данного сорта 2,9 т в смену, то для выполнения этого заказа потребуется одна печь (2,9*3= 8,7 т), но плановое задание должно быть скорректировано в соответствии с производительностью печи. При плановом задании 8,7 т в сутки печь полностью загружена при работе на одном сорте хлеба и дальнейшие расчеты ведутся с целью выявления условий, необходимых для обеспечения непрерывной работы ведущей машины в течение смены.
Ритм загрузки-разгрузки печи определяют делением продолжительности подооборота на количество люлек в пекарной камере. Продолжительность выпечки батонов 31 мин, количество люлек в печи 24, тогда rп= 31/24 = = 1,3 мин.
Производственное задание мукопросеивательному отделению определяется количеством муки, которое в определенные промежутки времени должно быть просеяно и подано в тестомесильное отделение для обеспечения бесперебойной работы печи. Количество муки ZM (в т) для выпечки батонов в смену определяется по формуле
Zм= П*100 / В,
где П — плановое задание по выработке определенного сорта изделий, т; В— плановый выход изделий, %.
Производственное задание мукопросеивательному отделению при плановом выходе батонов ZM = 2,9*100/134,6 = 2,15 т.
Если мука подается в тестомесильное отделение в мешках, то рассчитывается производственное задание в количестве мешков муки, расходуемой за смену. При массе одного мешка с мукой qмеш=70 кг производственное задание Zмеш = ZM/qмеш = 2150/70 = 31 мешок.
Ритм подвозки и засыпки муки при фонде рабочего времени за смену 460 мин гм=460/31 = 14,8 мин. При наличии силосов для хранения просеянной муки может быть рассчитан ритм подачи муки в расчете на 1 т: rм = 460/2,15=214 мин, а также коэффициент загрузки мукопросеивательного агрегата по формуле
Км = Zм / Nм
Если технико-экономическая норма производительности мукопросеивательного агрегата составляет 2,5 т в смену, то коэффициент его загрузки Км=2,15/2,5 = 0,86.
Производственное задание тестомесильному отделению при порционном способе приготовления теста исчисляется в количестве деж теста ZT, необходимых для бесперебойной работы печи:
ZT = (П* 100) qB,
где q — масса муки в одной деже, кг.
Если масса муки в одной деже 120 кг, то производственное задание тестомесильному отделению ZT= (2,9*100)/(0,12* 134,6) = 18 деж. Ритм замеса теста rт = 460/18 = 25,6 мин.
Производственное задание тесторазделочному отделению устанавливается с учетом потерь некоторого количества кусков теста в результате их отбраковки. Если норма возвратных отходов при разделке составляет 4 %, а масса одного куска теста 0,5 кг, то производственное задание тесторазделочному отделению Zд= 2900*1,04/0,5 = 3016/0,5 = 6031 кусков теста в смену. Ритм работы тестоделителя rд = 460/6032=4,6 с.
Коэффициент использования тесторазделочной машины при ее технико-экономической норме производительности 6100 кусков в смену равен 6032/6100 = 0,98.
Рассмотренная методика расчета потока дает исходный материал, позволяющий судить о согласованности по производительности машин в потоке только по коэффициентам их загрузки. Сопоставление ритмов рабочих мест невозможно, но на основе ритмов рассчитывают коэффициенты возможного использования рабочего времени рабочих и решают вопрос о необходимой численности рабочих.
При обслуживании машины периодического действия коэффициент возможного использования рабочего времени КР определяют по формуле
где tp— норма времени ручных операций, выполняемых в пределах одного ритма рабочего места потока, мин; ∆— норма времени на отдых, % ко времени работы; r — ритм рабочего места потока, мин.
Так, в рассматриваемом примере при величине ритма замеса одной дежитеста 25,6 мин, норме времени ручных операций по обслуживанию тестомесильной машины в пределах одного ритма 10 мин и норме времени на отдых3 %, коэффициент использования рабочего времени тестомеса
Кр = 10(1 +3/100) /25.6 = 0,4
По этой же формуле находят коэффициенты использования рабочего времени рабочих, занятых ручным трудом.
При норме времени на подвозку и засыпку одного мешка муки 5 мин коэффициент использования рабочего времени рабочих Кр = 5(1+3/100)/14,8=0,35.
При обслуживании машин непрерывного действия, когда обязанности рабочего связаны с контролем и регулированием работы машины, коэффициент использования рабочего времени рассчитывают по формуле
где ∑tр— норма времени всех ручных операций, выполняемых в течение смены, мин; ∆ — норма времени на отдых, % ко времени работы; tпер — норма времени регламентированных перерывов в течение смены, мин; Т — продолжительность рабочей смены, мин.
По этой формуле могут быть рассчитаны коэффициенты использования рабочего времени на рабочих местах разделки теста и выпечки хлеба.
После определения коэффициентов возможного использования рабочего времени на всех рабочих местах потока составляют сводную таблицу, в которой дается проектируемая численность рабочих в соответствии со степенью загрузки.
Пример 2. Расчет потока на основе приведенной производительности состоит из следующих этапов:
§ расчет приведенной производительности машин потока;
§ определение приведенных производственного задания и ритма потока;
§ определение продолжительности обработки предмета труда на рабочих местах;
§ определение загрузки оборудования;
§ оценка уровня организации потока.
Поточная линия, вырабатывающая нарезные батоны I сорта, включает следующее оборудование:
Операции | Оборудование | Техническая норма производительности, т/ч |
Просеивание муки | Бурат | 0,70 |
Замес теста | Тестомесильная машина Т-108 | 0,95 |
Брожение теста | Бункер 12-секционный | 1,03 |
Разделка теста | Тестоделитель | 1,60 |
Расстойка теста | Расстойный шкаф | 1,05 |
Выпечка хлеба | Печь БН-40 | 0,83 |
Выход батонов составляет 139,9 %, нормы технологических затрат:
при брожении 1,7%,
при разделке 0,1 %,
при расстойке 1,2%,
упек 8,7%.
Производительность оборудования для сопоставимости должна быть выражена в единых единицах измерения, либо в единицах измерения исходного сырья, либо в единицах измерения готовой продукции.
В нашем примере производительность оборудования измеряется в тоннах просеянной муки (бурат), замешанного теста (тестомесильная машина), разделанных изделий (тестоделитель), выпеченных батонов (печь). Поэтому судить о согласованности машин по производительности путем сопоставления их технических норм производительности нельзя.
Чтобы обеспечить сопоставимость данных о производительности, приведем ее к единым единицам измерения — выразим производительность оборудования поточной линии в тоннах выпекаемых батонов. Для этого рассчитаем коэффициенты перевода полуфабрикатов в готовые изделия.
Поскольку в процессе изготовления батонов к исходному сырью (муке) добавляется вода и ряд компонентов по рецептуре, а затем масса предмета труда на технологических операциях (брожение, разделка, замес, выпечка) уменьшается, расчет коэффициента перевода муки в готовые изделия представляет значительную сложность и аналогичен расчету выхода хлеба.
Для расчета приведенной производительности бурата может быть использована известная норма выхода батонов (139,9%). Коэффициент перевода муки в готовые изделия 1,399 показывает, что из единицы просеянной муки будет получено 1,399 единицы батонов, т. е. приведенная производительность бурата 0,7*1,399 = 0,98 т/ч.
Коэффициенты расчета приведенной производительности остальных машин строятся по другому принципу. На всех остальных машинах поточной линии предмет труда по мере выполнения технологических операций уменьшается. Так, при брожении теста масса его уменьшится на 1,7 %, при разделке—на 0,1%, при расстойке — на 1,2% и при выпечке — на 8,7%, а всего на 1,7+0,1 + 1,2 + 8,7=11,7%. Следовательно, из массы теста, приготовляемого тестомесильной машиной за 1 ч (0,95 т), будет получена масса готовых изделий, которая по величине будет меньше массы теста на 11,7%. Отсюда приведенная производительность тестомесильной машины (выраженная в готовых изделиях) составит 0,95[( 100—11,7) /100]= 0,95*0,883 = 0,84 т/ч.
Коэффициент перевода производительности 12-секционного бункера составит (100—10)/100 = 0,9, так как при брожении теста произошли потери его массы на 1,7%, и приведенная производительность его будет равна 1,03*0,9 = 0,93 т/ч. Коэффициент перевода производительности тестоделителя (100—9,9)/100 = 0,901, расстойного шкафа (100—8,7)/100=0,913, печи—1,00. Расчетные данные приведены ниже.
Оборудование | Производительность, т/ч | Коэффициент перевода | |
в единицах измерения нормы производительности | в единицах готовых изделий | ||
Бурат | 0,70 | 0,98 | 1,399 |
Тестомесильная машина | 0,95 | 0,84 | 0,883 |
Бункер 12-секционный | 1,03 | 0,93 | 0,900 |
Тестоделитель | 1,60 | 1,44 | 0,901 |
Расстойный шкаф | 1,05 | 0,96 | 0,913 |
Печь БН-40 | 0,83 | 0,83 | 1,000 |
Производительность оборудования, выраженная в готовых изделиях, является приведенной и может быть сопоставлена для выявления машины, имеющей наименьшую производительность, и для определения производственного задания и ритма поточной линии.
Производственное задание поточной линии не может превышать 0,83 т/ч готовых изделий и будет одинаковым для всех рабочих мест потока.
Ритм поточной линии также будет единым для всех рабочих мест, так как рассчитан на одно и то же производственное задание в единицах измерения производительности (в т/ч готовых изделий): r = 60/0,83 = 72,2 мин (на 1 т батонов).
При одинаковой величине ритмов поточной линии и всех рабочих мест продолжительность обработки единицы предмета труда на различных операциях будет неодинаковой. Так, продолжительность обработки на различных операциях составит:
просеивания муки t0б= 60/0,98 = 61,2 мин;
замеса теста t0б = 60/0,84 = 71,4 мин;
брожения теста t0б = 60/0,93 = 64,5 мин;
разделки теста t0б= 60/1,44 = 41,7 мин;
расстойки тестовых заготовок t0б — 60/0,96=62,5 мин;
выпечки t0б = 60/0,83 = 72,2 мин.
Сопоставление продолжительности обработки и ритма дает представление об уровне загрузки оборудования:
бурата 61,2/72,2=0,84;
тестомесильной машины 71,4/72,2 = 0,99;
бункера 12-секционного 64,5/72,2 = 0,89;
тестоделителя 41,7/72,2 = 0,58;
расстойного шкафа 62,5/72,2 = 0,87;
печи 72,2/72,2=1,00.
Таким образом, полностью загружена лишь печь, наименее загруженной машиной является тестоделитель. Средний коэффициент загрузки машин поточной линии Кз.ср может быть рассчитан по формуле
![]() |
В идеальном случае этот коэффициент должен быть равен нулю. В нашем примере коэффициент непрерывности показывает, что отклонения продолжительности обработки от ритма в целом по поточной линии составляют 13,7 %.
Согласованность оборудования по производительности может быть также охарактеризована коэффициентом пропорциональности Кпроп, определяемым по формуле
Каждое слагаемое представляет собой коэффициент согласованности с производительностью ведущей машины. В идеальном случае этот коэффициент должен быть равен 1. В нашем примере он показывает, что в целом по поточной линии оборудование недогружено на 20%.
pdnr.ru
Характеристика поточного производства и классификация поточных линий
Стр 1 из 3Следующая ⇒Лекция 12. Организация поточного и автоматического производства
Характеристика поточного производства и классификация поточных линий
Поточное производство является высокоэффективным методом организации производственного процесса. В условиях потока производственный процесс осуществляется в максимальном соответствии с принципами его рациональной организации — прямоточностью, непрерывностью, пропорциональностью и др.
Для поточного производства характерны следующие основныепризнаки:
1. за группой рабочих мест закрепляется обработка или сборка предмета одного наименования или ограниченного количества наименований предметов, родственных в конструктивно-технологическом отношении;
2. рабочие места располагаются по ходу технологического процесса; технологический процесс изготовления изделия разбивается на операции и на каждом рабочем месте выполняется одна или несколько родственных операций;
3. предметы передаются с операции на операцию поштучно или небольшими передаточными (транспортными) партиями в соответствии с заданным ритмом работы поточной линии, благодаря чему достигается высокая степень параллельности и непрерывности;
4. основные и вспомогательные операции вследствие узкой специализации рабочих мест отличаются высоким уровнем механизации и автоматизации. Широко применяется специальный межоперационный транспорт, выполняющий не только функции перемещения обрабатываемых предметов, но и поддержания ритма производства.
Элементы поточной организации производства имели место уже в мануфактурный период капиталистической промышленности. Впервые поточное производство в его наиболее совершенной форме было организовано Г. Фордом в начале нашего века при изготовлении автомобилей. В промышленности дореволюционной России поточного производства не существовало. После Октябрьской революциивместе с развитием промышленности и технического прогресса поточные- методы получают широкое развитие. В годы Великой Отечественной войны они сыграли огромную роль в бесперебойном снабжении фронта боеприпасами и военной техникой. В настоящее время поточные методы широко распространены во многих отраслях промышленности: в машиностроении, например, выпуск продукции поточными методами составляет более 40 %.
Основным звеном поточного производства является поточная линия, представляющая собой группу рабочихмест, за которыми закреплено изготовление одного или ограниченного количества наименований предметов труда и производственный процесс, на котором осуществляется в соответствии с признаками поточного производства.
В зависимости от конкретных производственных условий применяются различные виды поточных линий.
1.По номенклатуре изготовляемых, изделий поточные линии долятся на одно- и многопредметные.
Однопредметной называется поточная линия, на которой обрабатывается или собирается предмет одного типоразмера в течение длительного периода времени. Для перехода на изготовление предмета другого типоразмера требуется перестройка линии (перестановка, замена оборудования, изменение планировки и др.). Однопредметные поточные линии применяются при устойчивом выпуске изделий в больших количествах, т. е. в массовом производстве.
Многопредметной называется поточная линия, за которой закреплено изготовление нескольких типоразмеров предметов, сходных по конструкции и технологии обработки или сборки. Такие линии характерны для серийного производства, когда объем выпуска предметов одного типоразмера является недостаточным для эффективной загрузки рабочих мест линии.
Многопредметные поточные линии могут быть постоянно-поточными (групповыми) и переменно-поточными.
Постоянно-поточной (групповой) называется поточная линия, на которой обрабатывается или собирается группа родственных в технологическом отношении предметов без переналадки оборудования. Для этого каждое рабочее место должно быть оснащено групповыми приспособлениями, необходимыми для обработки изделий, закрепленных за линией.
На переменно-поточной линии различные предметы обрабатываются или собираются последовательно чередующимися партиями. После обработки или сборки партии одних предметов проводится переналадка оборудования и запускается в производство следующая партия.
2. По степени непрерывности процессапоточные линии делятся на непрерывные и прерывные, или прямоточные.
Непрерывнойявляется поточная линия, на которой обрабатываемые или собираемые предметы перемещаются по всем операциям линии непрерывно, т. е. без межоперационного простоя. Такое движение предметов по операциям называют параллельным.
Непрерывное движение предметов по операциям эффективнотолько при непрерывности работы оборудования ирабочих. Условием непрерывности поточной линии является равная производительность па всех операциях линии. Для создания подобного условия необходимо, чтобы продолжительность каждой операциина линии была равна или кратна единому такту работы линии.
Непрерывные поточные линии являются наиболее совершеннойформой поточного производства. Они обеспечивают строгую ритмичность в работе и самую короткую длительность производственного цикла.
Прерывной, или прямоточной, называется поточная линия, операции которой не синхронизированы и, следовательно, не могут быть выровнены по производительности. Между операциями образуются оборотные заделы (запасы) обрабатываемых предметов, вследствие чего непрерывность процесса нарушается. Прямоточные линии применяются при обработке трудоемких деталей на разнотипном оборудовании, когда перераспределение работ между операциями в целях синхронизации невозможно.
3. По способу поддержания ритмаразличают линии с регламентированным и свободным ритмом.
На линии срегламентированным ритмом обрабатываемые или собираемые предметы передаются с операции на операцию через точно фиксируемое время, т. е. с заданным ритмом, поддерживаемым с помощью специальных устройств. Как правило, регламентация ритма достигается определенной скоростью или периодичностью движения конвейера, а также путем звуковой и световой сигнализации, информирующей рабочих об окончании данной операции и необходимости передачи предмета на следующую. Линии с регламентированным ритмом характерны для непрерывно поточного производства.
На линии со свободным ритмомсоблюдение последнего возлагается на рабочих линии и мастера. Передача отдельных предметов может производиться с отклонениями от расчетного ритма работы, тогда на линии образуются межоперационные запасы обрабатываемых предметов. Линии со свободным ритмом применяются как внепрерывно-поточном, так и прямоточном производстве. Заданный ритм в условиях непрерывно-поточного производства обеспечивается обычно стабильной производительностью рабочего на первой операции. Может применяться также звуковая и световая сигнализация для ориентации рабочих (ритм становится полусвободным).
4. Поспособу транспортированияпредметов между операциями различают конвейерные и неконвейерные поточные линии.
Для транспортирования, а также поддержания заданного ритма работы на поточных линиях широко применяются транспортные средства непрерывного действия с механическим приводом, называемые конвейерами. Конвейеры могут быть различных конструкций: ленточные, пластинчатые, тележечные, подвесные и др. Применяемый вид конвейера зависит от многих факторов, и в первую очередь от особенностейобрабатываемого или собираемого изделия: его габаритных размеров, массы и др.
На линиях неконвейерноготипа (в основном прерывно-поточные линии) применяются разнообразные транспортные средства, которые подразделяют на бесприводные гравитационного действия — рольганги, скаты, желоба, склизы и т. д. и циклического действия— краны, электротележки,автопогрузчики и др.
Перемещатьпредметыпо рабочим местам не всегдацелесообразно. При сборке,например, крупных и тяжелых машин проще организовать гак называемуюстационарную поточную линию, на которой собираемое изделие устанавливается неподвижно па сборочном стенде, а перемещаются специализированные бригады рабочих, за которыми закреплены отдельные операции. Число бригад равно или кратно числу сборочных мест на такой линии, Стационарные поточные линии организуются в самолетостроении, судостроении, при производстве тяжелыхстанков.
5. В зависимости от места выполнения операцийразличают поточные линии с рабочими конвейерами и конвейерами со снятием предметов для обработки.
Рабочий конвейер кроме транспортирования и поддержания ритма служит еще местом выполнения операций непосредственно на его несущей части. Типичным примером таких конвейеров являются сборочные конвейеры.
Конвейеры со снятием предметов характерны для обработки деталей на различном оборудовании,
6.Взависимости отхарактера перемещения различаютконвейеры с непрерывным и пульсирующим движением.
На конвейере снепрерывным движениемнесущая его часть движется непрерывно с установленной скоростью.
На конвейере спульсирующим движение во время обработки (сборки) предметов несущая часть конвейера находится в неподвижном состоянии и приводится в движение периодически через промежуток времени, равный такту линии. Конвейеры с пульсирующимдвижением применяются в тех случаях, когда по условиям технологического процесса обрабатываемый или собираемый предмет должен быть неподвижным, например, при сборке точных машин. Пульсирующее движение характерно как для рабочих конвейеров, так и для конвейеров со снятием предметов.
mykonspekts.ru
Поточные линии
Содержание1. Основные виды и особенности организации поточной линии
2. Особенности планирования научно-исследовательских работ
Задача
Список использованных источников
1. Основные виды и особенности организации поточной линииПоточным называют производство, характеризуемое расположением средств технического оснащения в последовательности выполнения операций технологического процесса определенным интервалом выпуска продукции. Это форма организации производства, при которой все операции согласованы во времени, повторяются через строго установленные интервалы, все рабочие места являются специализированными, с закреплением одного или ограниченного количества наименований предмета труда. Она воплощает все основные принципы научной организации производственных процессов, что обеспечивает наибольшую эффективность ее функционирования.
Основным звеном поточного производства является поточная линия - совокупность специализированных рабочих мест (оборудования), на которых производственные операции выполняются с характерными признаками поточного производства. Она может состоять из оборудования (рабочих мест) с равной производительностью в единицу времени и равной.
При равной производительности оборудования его располагают по одному экземпляру на каждой операции поточной линии, при разной, но кратной - их кратное количество. Так на второй и четвертой операциях требуется оборудования (рабочих мест) больше в два раза, на третьей - в четыре раза больше, чем на первой и пятой, то сеть рабочих мест изменяется в соответствии с производительностью оборудования (трудоемкостью операций).
Кратное размещение оборудования в системе машин поточной линии позволяет организовать выпуск одинакового количества продукции в разные промежутки времени, создает условия для организации непрерывного поточного производства.
Классификация поточных линий по признакам, определяющим их организационную форму, приведена на рисунке 1.
По номенклатуре одновременно обрабатываемых предметов труда, поточные линии подразделяются на:
- однопредметные;
- многопредметные.
На однопредметных обрабатываются (изготавливаются, собираются) предметы труда (деталь, узел, изделие) одного наименования (типоразмера) в течение длительного периода времени, определяемого обычно периодом его выпуска. Такие линии широко распространены в цехах и на участках массового производства, например, линии сборки автомобилей, двигателей, отдельных узлов и агрегатов.
Рисунок 1. Классификация поточных линийМногопредметными называют поточные линии, позволяющие одновременно или последовательно обрабатывать предметы труда (детали, сборочные единицы, машины) нескольких наименований. Их подразделяют на:
- групповые, когда детали разных наименований обрабатываются по групповой технологии с использованием групповой оснастки одновременно или поочередно, но без переналадки оборудования;
- переменные (переменно-поточные), на которых закрепленные на них детали (узлы, изделия) разного наименования изготавливаются попеременно, с использованием через определенные промежутки времени (с переналадкой рабочих мест или без переналадки) универсального оборудования и технологически сходных изделий.
На таких поточных линиях после обработки одной партии предметов труда оборудование переналаживается на выпуск другой партии сходных изделий, и таким образом они обрабатываются попеременно. Многопредметные поточные линии находят применение в цехах среднесерийного и крупносерийного производства.
В зависимости от характера движения предмета труда по операциям поточные линии могут быть непрерывными (синхронизированными) и прерывными.
Непрерывно-поточными называются линии, на которых предмет труда находится в процессе обработки или перемещения с предыдущей операции на последующую, то сеть без межоперационного прослеживания и без перерывов в работе оборудования. Исключение составляют лишь предметы труда, находящиеся в страховом заделе на случай непредвиденных перебоев в их снабжении. На этих поточных линиях нормы времени на всех операциях одинаковы или кратны друг другу и равны такту. Такт потока - интервал времени, через который периодически производится выпуск изделий или заготовок определенного наименования, типоразмера и исполнения. Это среднее расчетное время, по истечении которого на поток запускается или с потока выпускается одно изделие или транспортная партия, промежуток времени между выпуском отдельных деталей, узлов или изделий на линии.
При наличии каких-либо перерывов в обработке или перемещении предметов труда вследствие неполной синхронизации операций поточное производство называют прерывно-поточным (прямоточным). На прерывных потоках из-за неравенства и не кратности производительности оборудования на отдельных операциях (несинхронности) предмет труда по окончании обработки на предыдущей операции пролеживает до начала обработки на следующей, образуя межоперационные оборотные заделы. Прерывные потоки применяются в случаях, когда объективные обстоятельства не позволяют полностью уровнять нормы времени на операциях или достичь кратности.
Четкость работы поточных линий определяется соблюдением заданного ритма или такта. По способу их поддержания различают линии с регламентированным и свободным ритмом. На линиях с регламентированным ритмом расчетный такт (ритм) поддерживается принудительно с помощью передвижения транспортных средств с определенной скоростью или с использованием сигнализации, включающейся автоматически через определенный интервал времени.
Линии со свободным ритмом не имеют технических средств, строго регламентирующих такт их работы. Их скорость (такт) регулируется рабочим или мастером, для передачи предмета труда с операции на операцию применяют почти любые транспортные средства (конвейеры, тележки и др.).
Поточные линии могут быть оборудованы конвейерами (непрерывными, пульсирующими) или обычными транспортными средствами-тележками, монорельсами с тельферами, кран-балками и т.д.
При передаче предметов труда с одной операции на другую на рабочих местах поточных линий создают задел - совокупность предметов труда, находящихся на разных стадиях производственного процесса и предназначенных для обеспечения бесперебойной работы цеха, участка, линии. В поточном производстве различают заделы: технологический, транспортный, оборотный и страховой.
Технологический задел - общее количество предметов труда, находящихся в процессе непосредственной обработки (сборки) на всех рабочих местах поточной линии.
Транспортный задел слагается из общего количества предметов труда, находящихся в процессе перемещения между рабочими местами, участками, поточными линиями.
Оборотный задел образуется на прямоточных линиях, когда смежные операции имеют различную по величине производительность и для рабочих устанавливается различный режим работы на этих операциях. Его межоперационная величина определяется как разность количества предметов труда по операциям за определенный период времени.
Страховой задел создается для компенсации различного рода перебоев и отклонений от такта работы линии. Их причинами могут быть, например, смена инструмента, выход из строя оборудования, колебания в производительности труда рабочих и др.
В соответствии с планом выпуска продукции (изделий) на определенный период времени по каждому потоку устанавливается задание в натуральных единицах. Предметы труда, запускаемые в поток, должны последовательно обрабатываться на каждой операции, и в этом случае задание потоку будет являться и заданием для каждой его операции.
Среднее расчетное время, по прошествии которого на рабочее место поступает или сходит с него единица предмета труда в количестве однократного запуска или выпуска иногда называют тактом операции, r0:r0 = T / P = T / Др × Ксм × Тсм;
r0 = t / К;
t = К × r0,где Т - действительный фонд времени работы линии за определенный период;
Р - программа выпуска изделий за тот же период;
Др - число рабочих дней в данном периоде;
Ксм - коэффициент сменности;
Тсм - продолжительность рабочей смены;
t - продолжительность операции;
К - количество рабочих мест на операции.
Основным же расчетным параметром поточной линии является такт потока (выпуска). В зависимости от исходных данных, такт потока r может быть определен одним из следующих способов:
1) если известно задание потока Р, то:r = (Тсм / P) × α,где Тсм - продолжительность функционирования потока в смену;
P - задание потоку или выпуск продукции в смену4
α - транспортная партия;
2) если задано количество рабочих мест в потоке, то сначала определяется задание потоку по формуле:P = Твр × В / Тизд,где Твр - фонд рабочего времени одного исполнителя в течение смены;
В - принятое количество рабочих в потоке;
Тизд - трудоемкость изготовления изделия,
а затем рассчитывается такт потока по формуле:r = (Тсм / P) × α;3) если задана производственная площадь, то сначала находят количество рабочих в потоке (В), которое может разместиться на проектируемой площади в одну смену: В = Пл / Н,где Пл - производственная площадь, на которой размещается поток;
Н - норма площади на одного рабочего,
а затем по формуле:P = Твр × В / Тиздполучают задание потоку и такт потока по формуле:r = (Тсм / P) × α.Такт потока позволяет определить и некоторые другие параметры, характеризующие организацию производственного процесса на поточной линии - количество рабочих мест (оборудования), численность рабочих, рабочую длину поточной линии, скорость конвейера и др.
Количество рабочих мест на каждой операции поточной линии Bi можно найти по формуле:Bi = ti / r,где ti - штучное время на выполнение i-ой операции.
Коэффициент загрузки рабочих мест (оборудования) на каждой операции Кз находят по формуле:Кз = Вр / Вn,где Вр и Вn - расчетное и принятое число рабочих мест на i-ой операции.
Явочное количество основных рабочих i-ой операции Вя рассчитывается из выражения:Вя = Oi / Нi,где Oi - расчетное количество оборудования;
Нi - норма обслуживания рабочих мест одним рабочим на i-ой операции.
Рабочая длина поточной линии (обоз. L) равна произведению шага конвейера (расстояние между рабочими местами) l на общее количество рабочих мест, расположенных по одной стороне линии B0, то сетьL = l × B0.Скорость конвейера (обоз. v) определяется из условия, что за каждый такт транспортирования он продвигается на один шаг,v = l / r.При построении технологической последовательности изготовления изделий, схем разделения труда, организационно-технических структур потоков рекомендуется учитывать следующие основные требования комплектования организационных операций:
- размещение рабочих мест в строгом соответствии с последовательностью технологического процесса;
- разделение производственного процесса на отдельные операции и закрепление их на длительное время за определенным рабочим местом;
- согласование продолжительности выполнения операций;
- использование квалификации исполнителей;
- специализация рабочих мест на выполнение отдельных операций;
- кратность организационных операций.
Эффективность поточного метода обеспечивается действием основных принципов организации производства, что проявляется в повышении производительности труда и сокращении производственного цикла, прежде всего, за счет уменьшения перерывов и времени пролеживания предметов труда при передаче их с одной операции на другую, в ускорении оборачиваемости оборотных средств, снижении себестоимости продукции и увеличении прибыли. Вместе с тем поточной организации производства присущи и определенные недостатки, связанные, например, с необходимостью значительных объемов выпуска продукции, изделий, стабильностью их конструкций, что может не соответствовать требованиям рынка.2. Особенности планирования научно-исследовательских работПодготовка производства представляет собой деятельность различных коллективов по разработке и реализации в производстве инноваций продуктов для удовлетворения постоянно растущих запросов потребителей. Она включает:
- цикл научных исследований;
- техническую подготовку производства.
Содержанием исследовательской стадии подготовки производства являются научные исследования и разработки, связанные с теоретическим обоснованием основных закономерностей технического прогресса. Научно-исследовательские работы (НИР) обусловлены возникновением потребности общества, государства в выполнении продукцией (техникой) новых функций. Они могут носить фундаментальный, поисковый или прикладной характер.
Результатом фундаментальных исследований являются открытия и накопление общих знаний путем изучения законов природы и общественного развития. Появляются изобретения - новые технические решения в различных областях народного хозяйства, принципиально отличающиеся от известных в мировой практике.
Поисковые научно-исследовательские работы проводятся для изучения возможности применения в прикладных исследованиях результатов фундаментальных исследований.
Прикладные исследования и опытно-конструкторские работы осуществляются после проведения поисковых научно-исследовательских работ. Они имеют четкую программу проведения, конкретные цели, экономические расчеты и сроки выполнения.
Основным звеном для проведения научных исследований являются научно-исследовательские институты (НИИ) и организации (НИО), такие, как отраслевые НИИ, научные учреждения Академии наук, НИО при предприятиях, комплексные научные учреждения - научно-производственные объединения, специализированные НИО.
Предприятие может создать новую продукцию путем приобретения патента или лицензии на производство чужого товара со стороны либо благодаря собственным усилиям за счет создания исследовательских подразделений, занимающихся фундаментальной и поисковой НИР. Тогда предприятия приобретают статус научно-производственного.
Основными структурными звеньями предприятия, в котором проводятся научно-исследовательские работы, являются технические лаборатории, решающие целый комплекс задач:
- выполнение НИР по созданию и внедрению прогрессивных технологических процессов;
- проведение НИР по разработке и внедрению новых видов сырья, материалов, новой техники, автоматизации производственных процессов;
- внедрение в производство результатов НИР, выполняемых научно-исследовательскими институтами.
В процессе цикла научных исследований возникают новые идеи, которые должны пройти всестороннюю проверку.
При создании новой продукции зарубежные экономисты рекомендуют ориентироваться на вероятность коммерческого успеха идей, которые вносятся в план научно-исследовательских и опытно-конструкторских работ, в 2,5 %. Отечественные исследования показывают, что вероятность того, что новая идея превратится в коммерческий успех, равна всего 1 %.
Высокий процент неудач новой продукции объясняется различными причинами, прежде всего дефектами самой продукции, более высокими, чем предполагалось, издержками и недостаточностью анализа рынка.
Риск увеличивается в прямой зависимости от степени новизны продукта и от того, насколько технология его производства и распределения отличается от опыта предприятия в этой области.
Основным фактором успеха нового продукта является наличие на предприятии эффективной системы технической подготовки производства, охватывающей все этапы создания и освоения новой техники (СОНТ).
ЗадачаПоточная технологическая линия предназначена для обработки деталей. Суточная программа технологической линии - 240 шт.
Шаг поточной линии - 2,8 м. Режим работы - 2 смены, длительность смены - 8 ч. Регламентированный перерыв - два в смену по 10 мин. Расстояние между центрами двух смежных рабочих мест - 1,2 м. Технологический брак составляет 4,35 %. Ширина поточной линии с учетом проходов и проездов - 3,4 м.
Рассчитать параметры поточной линии, в том числе количество рабочих мест и их загрузку. Технологический процесс обработки деталей представлен в таблице.
Операции | 1 | 2 | 3 | 4 | 5 | 6 | 7 | 8 | 9 | 10 | 11 |
Норма времени | 3,6 | 8,1 | 7,8 | 3,7 | 11,6 | 12,1 | 7,5 | 7,7 | 3,6 | 7,4 | 3,8 |
Решение:
Определим:
1) так поточной линии (r):r = Фд / N,где Фд - действительный фонд времени работы поточной линии за сутки с учетом регламентированных перерывов, мин;
N - программа выпуска изделий в натуральном выражении за этот же период времени, шт.
r = (2 × 8 × 60 мин. - 10 мин. × 2 × 2) / 240 шт. = 3,83 мин.
2) темп поточной линии (): = 1 / r = 1 / 3,83 мин. = 0,26 шт. (в мин.) 3) число рабочих мест на i-ю операцию РМi:РМi = ti / r,где ti - время на i-ю операцию, мин.
РМ1 = 3,6 мин. / 3,83 мин. ≈ 1
РМ2 = 8,1 мин. / 3,83 мин. ≈ 2
РМ3 = 7,8 мин. / 3,83 мин. ≈ 2
РМ4 = 3,7 мин. / 3,83 мин. ≈ 1
РМ5 = 11,6 мин. / 3,83 мин. ≈ 3
РМ6 = 12,1 мин. / 3,83 мин. ≈ 3
РМ7 = 7,5 мин. / 3,83 мин. ≈ 2
РМ8 = 7,7 мин. / 3,83 мин. ≈ 2
РМ9 = 3,6 мин. / 3,83 мин. ≈ 1
РМ10 = 7,4 мин. / 3,83 мин. ≈ 2
РМ11 = 3,8 мин. / 3,83 мин. ≈ 1
4) коэффициент загрузки рабочих мест на каждой операции Кз.оi определяется отношением расчетного количества рабочих мест на i-ю операцию РМрасч i к фактическому РМфакт i, то есть:Кз.оi = РМрасч i / РМфакт irрасч = (2 × 8 × 60 мин. - 10 мин. × 2 × 2) / (240 шт. × (100 - 4,35)) ≈ 4 мин.
Кз.о1 = (3,6 мин. / 4 мин.) / (3,6 мин. / 3,83 мин.) = 95,75 %
Кз.о2 = (8,1 мин. / 4 мин.) / (8,1 мин. / 3,83 мин.) = 95,74 %
Кз.о3 = (7,8 мин. / 4 мин.) / (7,8 мин. / 3,83 мин.) = 95,73 %
Кз.о4 = (3,7 мин. / 4 мин.) / (3,7 мин. / 3,83 мин.) = 95,76 %
Кз.о5 = (11,6 мин. / 4 мин.) / (11,6 мин. / 3,83 мин.) = 95,75 %
Кз.о6 = (12,1 мин. / 4 мин.) / (12,1 мин. / 3,83 мин.) = 95,76 %
Кз.о7 = (7,5 мин. / 4 мин.) / (7,5 мин. / 3,83 мин.) = 95,76 %
Кз.о8 = (7,7 мин. / 4 мин.) / (7,7 мин. / 3,83 мин.) = 95,77 %
Кз.о9 = (3,6 мин. / 4 мин.) / (3,6 мин. / 3,83 мин.) = 95,75 %
Кз.о10 = (7,4 мин. / 4 мин.) / (7,4 мин. / 3,83 мин.) = 95,76 %
Кз.о11 = (3,8 мин. / 4 мин.) / (3,8 мин. / 3,83 мин.) = 95,77 %5) общую длина конвейера поточной линии L, которая зависит от ее шага и числа рабочих мест на линии:
L = 2,8 м × (1 +2 + 2 + 1 +3 +3 + 2 +2 + 1 + 2+ 1) = 56 м
6) скорость движения конвейера поточной линии v, которая зависит от шага и такта линии:v = l / r.v = 2,8 м / 3,83 мин. = 0,731 м/мин.
7) цикл поточной линии Тц:Тц = r / .Тц = 3,8 мин. / (1 +2 + 2 + 1 +3 +3 + 2 +2 + 1 + 2+ 1) = 0,19 мин. Список использованных источников1. Золотогоров В.Г. Организация и планирование производства. Практическое пособие. - Мн.: ФУАинформ, 2001. – 528 с.
2. Ильин А.И., Синица Л.М. Планирование на предприятии: Учебное пособие. В 2-х частях. – Мн.: ООО «Новое знание», 2000. – 728 с.
3. Организация производства. Учебно-практическое пособие/ М.Ю. Пасюк, Т.Н. Долинина, А.А. Шабуня. – Мн.: ООО ФУАинформ, 2002. – 76 с.
4. Организация производства на предприятии; Учеб.-метод. Комплекс. Н.В. Шинукевич, Е.А. Зубелик, Ю.В. Карпилович. Мн.; Издательство МИУ, 2004. – 151 с.
5. Синица Л.М. Организация производства: Учеб. пособие для студентов вузов. – 2- изд., перераб и доп. – Мн.: УП «ИВЦ Минфина», 2004. – 521 с.
www.coolreferat.com
ПОТОЧНАЯ ЛИНИЯ - это... Что такое ПОТОЧНАЯ ЛИНИЯ?
ПОТОЧНАЯ ЛИНИЯкомплекс оборудования, взаимно связанного и работающего согласованно с определ. заданным тактом (ритмом) по единому технологи ч. процессу. На каждом рабочем месте выполняются определ. операции обработки одной или неск. технологически сходных заготовок. Рабочие места размещаются в соответствии с заданной последовательностью технологич. процесса. Заготовки передаются с одного рабочего места на другое при помощи гл. обр. конвейеров. В П. л. включают позиционеры, манипуляторы, трансп. и технологич. роботы. П. л. обеспечивают непрерывность технологич. процесса, позволяют механизировать и автоматизировать его; распространены на пр-тиях с массовым и серийным произ-вом. См. рис.
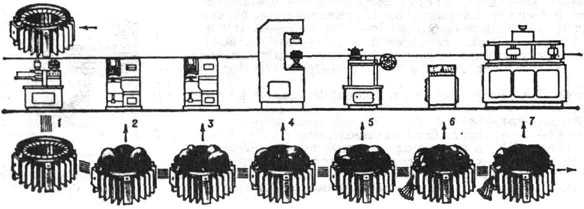
Комплексно-механизированная поточная линия намотки, пропитки и сушки обмоток статоров электродвигателей: 1 - изолирование пазов; 2 - намотка первого яруса обмотки; 3 - намотка второго яруса обмотки; 4 - опрессовка лобовых частей; 5 - заклинивание обмотки в пазах; 6 - испытание обмотки; 7 - пропитка и сушка обмотки
Большой энциклопедический политехнический словарь. 2004.
- ПОТОЛОК
- ПОТОЧНОЕ ПРОИЗВОДСТВО
Смотреть что такое "ПОТОЧНАЯ ЛИНИЯ" в других словарях:
Поточная линия — по производству пончиков Поточная линия комплекс оборудования, взаимосвязанного и работающего согласовано с заданным … Википедия
ПОТОЧНАЯ ЛИНИЯ — комплекс оборудования, взаимно связанного и работающего согласованно с заданным ритмом по единому технологическому процессу. Рабочие места размещаются в последовательности технологических операций. Поточная линия обеспечивает непрерывность… … Большой Энциклопедический словарь
поточная линия — — [http://slovarionline.ru/anglo russkiy slovar neftegazovoy promyishlennosti/] Тематики нефтегазовая промышленность EN production line … Справочник технического переводчика
поточная линия — комплекс оборудования, взаимно связанного и работающего согласованно с заданным ритмом по единому технологическому процессу. Рабочие места размещаются в последовательности технологических операций. Поточная линия обеспечивает непрерывность… … Энциклопедический словарь
ПОТОЧНАЯ ЛИНИЯ — комплекс оборудования, взаимно связанного и работающего согласованно с определенно заданным ритмом по единому технологическому процессу (рис. П 43). На каждом рабочем месте выполняется определенная операция. Заготовки или изготовляемые изделия… … Металлургический словарь
Поточная линия — совокупность обрабатывающих машин или рабочих мест, расположенных по ходу технологического процесса изготовления деталей или сборки изделий. За каждой машиной или рабочим местом П. л. закрепляется одна или несколько операций. П. л. в… … Большая советская энциклопедия
ПОТОЧНАЯ ЛИНИЯ — специализированный участок в поточном производстве … Энциклопедический словарь экономики и права
поточная линия — Syn: конвейер … Тезаурус русской деловой лексики
поточная линия для изготовления книг в мягкой обложке — Автоматическая поточная линия для выполнения брошюровочно переплетных процессов по изготовлению книг бесшвейным клеевым скреплением в мягкой обложке от комплектовки тетрадей до обвязки пачек готовых книг. [ГОСТ Р 51205 98] Тематики полиграфия … Справочник технического переводчика
поточная линия для изготовления книг в твердом переплете — Автоматическая поточная линия для выполнения брошюровочно переплетных процессов по изготовлению книг, сшитых нитками, в твердом переплете от обжима книжных блоков до обвязки пачек готовых книг. [ГОСТ Р 51205 98] Тематики полиграфия … Справочник технического переводчика
dic.academic.ru