Производство чугуна в России, история развития. Производства чугуна
Технология производства чугуна и стали
Скачать
1.Производство чугуна и стали.
Железо имело промышленное применение уже до нашей эры. В древние времена его получали в пластичном состоянии в горнах. Шлак отделяли, выдавливая его из губчатого железа, ударами молота.
По мере развития техники производства железа постепенно повышалась температура, при которой велся процесс. Металл и шлак стали плавиться; стало возможным разделять их гораздо полнее. Но одновременно в металле повышалось содержание углерода и других примесей, - металл становился хрупким и нековким. Так появился чугун.
Позднее научились перерабатывать чугун; зародился двухступенчатый способ производства железа из руды. В принципе он сохраняется до настоящего времени: современная схема получения стали состоит из доменного процесса, в ходе которого из руды получается чугун, и сталеплавильного передела, приводящего к уменьшению в металле количества углерода и других примесей.
Современный высокий уровень металлургического производства основан на теоретических исследованиях и открытиях, сделанных в различных странах, и на богатом практическом опыте. Немалая доля в этом процессе принадлежит русским ученым. Например, российские ученые первыми широко применили природный газ для доменной плавки.
2. Производство чугуна.
2.1. Исходные материалы.
Железные руды. Главный исходный материал для производства чугуна в доменных печах – железные руды. К ним относят горные породы, содержащие железо в таком количестве, при котором выплавка становится экономически выгодной.
Железная руда состоит из рудного вещества и пустой породы. Рудным веществом чаще всего являются окислы, силикаты и карбонаты железа. А пустая порода обычно состоит из кварцита или песчаника с примесью глинистых веществ и реже – из доломита или известняка.
В зависимости от рудного вещества железные руды бывают богатыми, которых используют непосредственно, и бедными, которых подвергают обогащению.
В доменном производстве применяют разные железные руды.
Красный железняк (гематит) содержит железо в виде безводной окиси железа. Она имеет разную окраску( от темно-красной до темно-серой). Руда содержит много железа(45-65 %) и мало вредных примесей. Восстановим ость железа из руды хорошая.
Бурый железняк содержит железо в виде водных окислов. В нем содержится 25- 50% железа. Окраска меняется от желтой до буро-желтой. Пустая порода железняка глинистая иногда кремнисто-глиноземистая.
Магнитный железняк содержит 40-70% железа в виде закиси-окиси железа.
руда обладает хорошо выраженными магнитными свойствами, имеет темно-серый или черный с различными оттенками цвет. Пустая порода руды кремнеземистая с примесями других окислов. Железо из магнитного железняка восстанавливается труднее, чем из других руд.
Шпатовый железняк (сидерит) содержит железо в виде углекислой соли. В этом железняке содержится 30-37 % железа. Сидерит имеет желтовато-белый и грязно-серый цвет. Он легко окисляется и переходит в бурый железняк. Из всех железных руд он обладает наиболее высокой восстановимостью.
Марганцевые руды содержат 25-45% марганца в виде различных окислов марганца. Их добавляют в шихту для повышения в чугуне количества марганца.
2.2. Производство чугуна в доменной печи.
Выплавка чугуна производится в огромных доменных печах, выложенных из огнеупорных кирпичей достигающих 30 м высоты при внутреннем диаметре около 12 м.
Разрез доменной печи схематически изображен на рисунке.
Верхняя ее половина носит название шахты и заканчивается наверху отверстием – калашником, которая закрывается подвижной колонкой – кколашниковым затвором. Самая широкая часть печи называется распаром, а нижняя часть – горном. Через специальные отверстия в горне(фурмы) в печать вдувается горячий воздух или кислород.
Доменную печь загружают сначала коксом, а затем послойно агломератом и коксом. Агломерат – это определенным образом подготовленная руда, спеченная с флюсом. Горение и необходимая для выплавки чугуна температура поддерживаются вдуванием в горн подогретого воздуха или кислорода. Последний поступает в кольцевую трубу, расположенную вокруг нижней части печи, а из нее по изогнутым трубкам через фурмы в горн. В горне кокс сгорает, образуя СО2, который, поднимаясь вверх и проходя сквозь слои наколенного кокса, взаимодействует с ним и образует СО. Образовавшийся оксид углерода и восстонавливает большую часть руды, переходя снова в СО2.
Процесс восстановления руды происходит главным образом в верхней части шахты. Его можно выразить суммарным уравнением:
Fe2O3 + 3CO = 2Fe + 3CO2
Пустую породу в руде образуют, главным образом диоксид кремния SiO2.
Это – тугоплавкое вещество. Для превращения тугоплавких примесей в более легкоплавкие соединения к руде добавляются флюс . Обычно в качестве флюса используют CaCo3. При взаимодействии его с SiO2 образуется CaSiO2, легко отделяющийся в виде шлака.
При восстановлении руды железо получается в твердом состоянии. Постепенно оно опускается в более горячую часть печи – распар - и растворяет в себе углерод; образуется чугун. Последний плавится и стекает в нижнюю часть горна, а жидкие шлаки собираются на поверхности чугуна, предохраняя его от окисления. Чугун и шлаки выпускают по мере накопления через особые отверстия, забитые в остальное время глиной.
Выходящие из отверстия печи газы содержат до 25% СО. Их сжигают в особых аппаратах-кауперах, предназначенных для предварительного нагревания вдуваемого в печь воздуха. Доменная печь работает непрерывно. По мере того как верхние слои руды и кокса опускаются, в печь добавляют новые их порции. Смесь руды и кокса доставляется подъемниками на верхнюю площадку печи и загружается в чугунную воронку, закрытую снизу колошниковым затвором. При опускании затвора смесь попадает в печь. Работа печи продолжается в течение нескольких лет, пока печь не потребует капитального ремонта.
Процесс выплавки может быть ускорен путем применения в доменных печах кислорода. При вдувании в доменную печь обогащенного кислородом воздуха предварительный подогрев его становится излишним, а значит, отпадает необходимость в громоздких и сложных кауперах и весь процесс упрощается. Вместе с тем производительность печи повышается и уменьшается расход топлива. Такая доменная печь дает в 1,5 раза больше железа и требует кокса на ¼ меньше чем обычная.
3 Производство стали.
В стали по сравнению с чугуном содержится меньше углерода, кремния, серы и фосфора. Для получения стали из чугуна необходимо снизить концентрацию веществ путем окислительной плавки.
В современной металлургической промышленности сталь выплавляют в основном в трех агрегатах: конвекторах, мартеновских и электрических печах.
3.1. Производство стали в конверторах.
Конвертор представляет собой сосуд грушевидной формы. Верхнюю часть называют козырьком или шлемом. Она имеет горловину, через которую жидкий чугун и сливают сталь и шлак. Средняя часть имеет цилиндрическую форму. В нижней части есть приставное днище, которое по мере износа заменяют новым. К днищу присоединена воздушная коробка, в которую поступает сжатый воздух.
Емкость современных конвекторов равна 60 – 100 т. и более, а давление воздушного дутья 0,3-1,35 Мн/м. Количество воздуха необходимого для переработки 1 т чугуна, составляет 350 кубометров.
Перед заливкой чугуна конвектор поворачивают до горизонтального положения, при котором отверстия фурм оказываются выше уровня залитого чугуна. Затем его медленно возвращают в вертикальное положение и одновременно подают дутье, не позволяющее металлу проникать через отверстия фурм в воздушную коробку. В процессе продувки воздухом жидкого чугуна выгорают кремний, марганец, углерод и частично железо.
При достижении необходимой концентрации углерода конвектор возвращают в горизонтальное положение и прекращают подачу воздуха. Готовый металл раскисляют и выливают в ковш.
Бессемеровский процесс. В конвертор заливают жидкий чугун с достаточно высоким содержанием кремния (до 2,25% и выше), марганца (0,6-0,9%), и минимальным количеством серы и фосфора.
По характеру происходящей реакции бессемеровский процесс можно разбить на три периода. Первый период начинается после пуска дутья в конвертор и продолжается 3-6 мин. Из горловины конвертора вместе с газами вылетают мелкие капли жидкого чугуна с образованием искр. В этот период окисляются кремний, марганец и частично железа по реакциям:
Si + O2 = SiO2,
2Mn + O2 = 2MnO,
2Fe + O2 = 2FeO.
Образующаяся закись железа частично растворяется в жидком металле, способствуя дальнейшему окислению кремния и марганца. Эти реакции протекают с выделением большого количества тепла, что вызывает разогрев металла. Шлак получается кислым (40-50% SiO2).
Второй период начинается после почти полного выгорания кремния и марганца. Жидкий металл достаточно хорошо разогрет, что создаются благоприятные условия для окисления углерода по реакции C + FeO = Fe + CO, которая протекает с поглощением тепла. Горение углерода продолжается 8-10 мин и сопровождается некоторым понижением температуры жидкого металла. Образующаяся окись углерода сгорает на воздухе. Над горловиной конвектора появляется яркое пламя.
По мере снижения содержания углерода в металле пламя над горловиной уменьшается и начинается третий период. Он отличается от предыдущих периодов появлением над горловиной конвертора бурого дыма. Это показывает, что из чугуна почти полностью выгорели кремний, марганец и углерод и началось очень сильное окисление железа. Третий период продолжается не более 2 – 3 мин, после чего конвектор переворачивают в горизонтальное положение и в ванну вводят раскислители (ферромарганец, ферросилиций или алюминий) для понижения содержания кислорода в металле. В металле происходят реакции
FeO + Mn = MnO + Fe,
2FeO + Si = SiO2 + Fe,
3FeO + 2Al = Al2O3 + 3Fe.
Готовую сталь выливают из конвектора в ковш, а затем направляют на разливку.
Чтобы получить сталь с заранее заданным количеством углерода (например, 0,4 – 0,7% С), продувку металла прекращают в тот момент, когда из него углерод еще не выгорел, или можно допустить полное выгорание углерода, а затем добавить определенное количество чугуна или содержащих углерод определенное количество ферросплавов.
Томасовский процесс. В конвертор с основной футеровкой сначала загружают свежеобожженную известь, а затем заливают чугун, содержащий 1,6-2,0% Р, до 0,6%Si и до 0,8% S. В томасовском конвекторе образуется известковый шлак, необходимый для извлечения и связывания фосфора. Заполнение конвектора жидким чугуном, подъем конвертора, и пуск дутья происходят также как и в бессемеровском процессе.
В первый период продувки в конвекторе окисляется железо, кремний, марганец и формируется известковый шлак. В этот период температура металла несколько повышается.
Во второй период продувки выгорает углерод, что сопровождается некоторым понижением температуры металла. Когда содержание углерода в металле достигнет менее 0,1%, пламя уменьшится и исчезнет. Наступает третий период, вовремя которого интенсивно окисляется фосфор
2P + 5FeO + 4CaO = (CaO)4*P2O5 + 5Fe.
В результате окисления фосфор переходит из металла в шлак, поскольку тетрафосфат кальция может раствориться только в нем. Томасовские шлаки содержат 16 – 24% Р2О5.
Данная реакция сопровождается выделением значительного количества тепла, за счет которого происходит более резкое повышение температуры металла.
Перед раскислением металла из конвертора необходимо удалить шлак, т.к. содержащиеся в раскислителях углерод, кремний, марганец будут восстанавливать фосфор из шлака, и переводить его в металл. Томасовскую сталь применяют для изготовления кровельного железа, проволоки и сортового проката.
Кислородно-конверторный процесс. Для интенсификации бессемеровского и томасовского процессов в последние годы начали применять обогащенное кислородом дутье.
При бессемеровском процессе обогащения дутья кислородом позволяет сократить продолжительность продувки и увеличить производительность конвертора и долю стального скрапа, подаваемого в металлическую ванну в процессе плавки. Главным достоинством кислородного дутья является снижение содержания азота в стали с 0,012-0,025(при воздушном дутье) до 0,008-0,004%(при кислородном дутье). Введение в состав дутья смеси кислорода с водяным паром или углекислым газом позволяет повысить качество бессемеровской стали, до качества стали, выплавляемой в мартеновских и электрических печах.
Большой интерес представляет использование чистого кислорода для выплавки чугуна в глуходонных конверторах сверху с помощью водоохлаждаемых фурм.
Производство стали кислородно-конверторным способом с каждым годом увеличивается.
3.2.Производство стали в мартеновских печах.
В мартеновских печах сжигают мазут или предварительно подогретые газы с использованием горячего дутья.
Печь имеет рабочее (плавильное) пространство и две пары регенераторов(воздушный и газовый) для подогрева воздуха и газа. Газы и воздух проходят через нагретую до 1200° С огнеупорную насадку соответствующих регенераторов и нагреваются до 1000-1200° С. Затем по вертикальным каналам направляются в головку печи, где смешиваются и сгорают, в результате чего температура под сводом достигает 1680-1750° С. Продукты горения направляются из рабочего пространства печи в левую пару регенераторов и нагревают их огнеупорную насадку, затем поступают в котлы-утилизаторы и дымовую трубу. Когда огнеупорная насадка правой пары регенераторов остынет, остынет так что не сможет нагревать проходящие через них газы и воздух до 1100° С, левая пара регенераторов нагревается примерно до 1200-1300° С. В этот момент переключают направление движения газов и воздуха. Это обеспечивает непрерывное поступление в печь подогретых газов и воздуха.
Большинство мартеновских печей отапливают смесью доменного, коксовального и генераторного газов. Также применяют и природный газ. Мартеновская печь, работающая на мазуте, имеет генераторы только для нагрева воздуха.
Шихтовые материалы (скрапы, чугун, флюсы) загружают в печь наполненной машиной через завалочные окна. Разогрев шихты, рас плавление металла и шлака в печи происходит в плавильном пространстве при контакте материалов с факелом раскаленных газов. Готовый металл выпускают из печи через отверстия, расположенные в самой низкой части подины. На время плавки выпускное отверстие забивают огнеупорной глиной.
Процесс плавки в мартеновских печах может быть кислым или основным. При кислом процессе огнеупорная кладка печи выполнена из динасов ого кирпича. Верхние части подины наваривают кварцевым песком и ремонтируют после каждой плавки. В процессе плавке получают кислый шлак с большим содержанием кремнезема (42-58%).
При основном процессе плавки подину и стенки печи выкладывают из магнезитового кирпича, а свод – из динасов ого или хромомагнезитового кирпича. Верхние слои подины наваривают магнезитовым или доломитовым порошком и ремонтируют после каждой плавки. В процессе плавки получают кислый шлак с большим содержанием 54 – 56% СаО.
Основной мартеновский процесс. Перед началом плавки определяют количество исходных материалов (чушковый чугун, стальной скрап, известняк, железная руда) и последовательность их загрузки в печь. При помощи заливочной машины мульда (специальная коробка) с шахтой вводится в плавильное пространство печи и переворачивается, в результате чего шихта высыпается на подину печи. Сначала загружают мелкий скрап, затем более крупный и на него кусковую известь (3 – 5 % массы металла). После прогрева загруженных материалов подают оставшийся стальной лом и предельный чугун двумя тремя порциями.
Этот порядок загрузки материалов позволяет их быстро прогреть и расплавить. Продолжительность загрузки шихты зависит от емкости печи, характера шихты, тепловой мощности печи и составляет 1,5 – 3 ч.
В период загрузки и плавления шихты происходит частичная окисление железа и фосфора почти полное окисление кремния и марганца и образования первичного шлака. Указанные элементы окисляются сначала за счет кислорода печных газов и руды, а затем за счет закиси железа растворенной в шлаке. Первичный шлак формируется при расплавлении и окислении металла и содержит 10 –15% FeO, 35 –45% CaO, 13 – 17% MnO. После образования шлака жидкий металл оказывается изолированным от прямого контакта с газами, и окисление примесей происходит под слоем шлака. Кислород в этих условиях переносится закисью железа, которая растворяется в металле и шлаке. Увеличение концентрации закиси железа в шлаке приводит к возрастанию ее концентрации в металле.
Для более интенсивного питания металлической ванны кислородом в шлак вводят железную руду. Кислород, растворенный в металле, окисляет кремний, марганец, фосфор и углерод по реакциям, рассмотренным выше.
К моменту рас плавления всей шихты значительная часть фосфора переходит в шлак, так как последний содержит достаточное количество закиси железа и извести. Во избежание обратного перехода фосфора в металл перед началом кипения ванны 40 – 50% первичного шлака из печи.
После скачивания первичного шлака в печь загружают известь для образования нового и более основного шлака. Тепловая нагрузка печи увеличивается, для того чтобы тугоплавкая известь быстрее перешла в шлак, а температура металлической ванны повысилась. Через некоторое время 15 – 20 мин в печь загружают железную руду, которая увеличивает содержание окислов железа в шлаке, и вызывает в металле реакцию окисления углерода
[C] + (FeO) = Coгаз.
Образуется окись углерода выделяется из металла в виде пузырьков, создавая впечатление его кипения, что способствует перемешиванию металла, выделение металлических включений и растворенных газов, а также равномерному распределению температуры по глубине ванны. Для хорошего кипения ванны необходимо подводить тепло, так как данная реакция сопровождается поглощением тепла. Продолжительность периода кипения ванны зависит от емкости печи и марки стали, и находится 1,25 – 2,5 ч и более.
Обычно железную руду добавляют в печь в первую периода кипения, называемого полировкой металла. Скорость окисления углерода в этот период в современных мартеновских печах большой емкости равна 0,3 – 0,4% в час.
В течение второй половины периода кипения железную руду в ванну не подают. Металл кипит мелкими пузырьками за счет накопленных в шлаке окислов железа. Скорость выгорания углерода в этот период равна 0,15 – 0,25% в час. В период кипения, следя за основностью и жидкотекучестью шлака.
Когда содержание углерода в металле окажется несколько ниже, чем требуется для готовой стали, начинается последняя стадия плавки – период доводки и раскисления металла. В печь вводят определенное количество кускового ферромарганца (12% Mn), а затем через 10 – 15 мин ферросилиций (12-16% Si). Марганец и кремний взаимодействуют с растворенным в металле кислородом, в результате чего реакция окисления углерода приостанавливается. Внешним признаком освобождения металла от кислорода является прекращение выделения пузырьков окиси углерода на поверхности шлака.
При основном процессе плавки происходит частичное удаление серы из металла по реакции
[FeS] + (CaO) = (CaO) + (FeO).
Для этого необходимы высокая температура и достаточная основность шлака.
Кислый мартеновский процесс. Этот процесс состоит из тех же периодов, что и основной. Шихту применяют очень чистую по фосфору и сере. Объясняется это тем, что образующийся кислый шлак не может задерживать указанные вредные примеси.
Печи обычно работают на твердой шихте. Количество скрапа равно 30 – 50% массы металлической шихты. В шихте допускается не более 0,5% Si. Железную руду в печь подавать нельзя, так как она может взаимодействовать с кремнеземом подины и разрушать ее в результате образования легкоплавкого соединения 2FeO*SiO2. Для получения первичного шлака в печь загружают некоторое количество кварцита или мартеновского шлака. После этого шихта нагревается печными газами; железо, кремний, марганец окисляются, их окислы сплавляются с флюсами и образуют кислый шлак, содержащий до 40 –50 % SiO2. В этом шлаке большая часть закиси железа находится в силикатной форме, что затрудняет его переход из шлака в металл. Кипение ванной при кислом процессе начинается позже, чем при основном, и происходит медленнее даже при хорошем нагреве металла. Кроме того, кислые шлаки имеют повышенную вязкость, что отрицательно сказывается на выгорании углерода.
Так как сталь выплавляется под слоем кислого шлака с низким содержанием свободной закиси железа, этот шлак защищает металл от насыщения кислородом. Перед выпуском из печи в стали содержится меньше растворенного кислорода, чем в стали, выплавленной при основном процессе.
Для интенсификации мартеновского процесса воздух обогащают кислородом, который подается в факел пламени. Это позволяет получать более высокие температуры в факеле пламени, увеличивать ее лучеиспускательную способность, уменьшать количество продуктов горения и благодаря этому увеличивать тепловую мощность печи.
Кислород можно вводить и в ванну печи. Введение кислорода в факел и в ванну печи сокращает периоды плавки и увеличивает производительность печи на 25-30%. Изготовление хромомагнезитовых сводов вместо динасовых позволяет увеличивать тепловую мощность печей, увеличить межремонтный период в 2-3 раза и повысить производительность на 6-10%.
3.3. Производство стали в электрических печах.
Для выплавки стали используют электрические печи двух типов: дуговые и индукционные (высокочастотные). Первые из них получили более широкое применение в металлургической промышленности.
Дуговые печи имеют емкость 3 - 80 т и более. На металлургических заводах устанавливают печи емкостью 30 –80 тонн. В электрических печах можно получать очень высокие температуры (до 2000° С), расплавлять металл с высокой концентрацией тугоплавких компонентов иметь, иметь основной шлак, хорошо очищать металл от вредных примесей, создавать восстановительную атмосферу или вакуум (индукционные печи) и достигать высокого раскисления и дегазации металла.
Нагревание и расплавление шихты осуществляется за счет тепла, излучаемого тремя электрическими дугами. Электрические дуги образуются в плавильном пространстве печи между вертикально подвешенными электродами и металлической шихтой.
Дуговая печь имеет следующие основные части: сварной или клепанный кожух цилиндрической формы, со сфероидальным днищем; подины и стенок; съемный арочный свод с отверстиями для электродов; механизм для закрепления вертикального перемещения электродов; две опорные станины; механизм наклона печи, позволяющий поворачивать печь при выпуске стали по желобу и в сторону загрузочного окна для скачивания шлака.
В сталеплавильных печах применяют угольный и графитированные электроды. Диаметр электродов определяется мощностью потребляемого тока и составляет 350 – 550 мм. В процессе плавки нижние концы электродов сгорают. Поэтому электроды постепенно опускают и в необходимых случаях наращивают сверху.
Технология выплавки стали в дуговых печах. В электрических дуговых печах высококачественную углеродистую или легированную сталь. Обычно для выплавки стали, применяют шихту в твердом состоянии. Твердую шихту в дуговых печах с основной футеровкой используют при плавке стали с окислением шихты и при переплавке металла без окисления шихты.
Технология плавки с окислением шихты в основной дуговой печи подобна технологии плавки стали в основных мартеновских печах (скрап-процессам). После заправки падины в печь загружают шихту. Среднее содержание углерода в шихте на 0,5 –0,6% выше, чем в готовой стали. Углерод выгорает и обеспечивает хорошее кипение ванны. На подину печи загружают мелкий стальной лом, затем более крупный. Укладывать шихту в печи надо плотно. Особенно важно хорошо уложить куски шихты в месте нахождения электродов. Шихту в дуговые печи малой и средней емкости загружают мульдами или лотками через завалочное окно, а в печи большой емкости через свод, который отводят в сторону вместе с электродами. После загрузки шихты электроды опускают до легкого соприкосновения с шихтой. Подложив под нижние концы электродов кусочки кокса, включают ток, и начинают плавку стали.
При плавки стали в дуговых печах различают окислительный и восстановительный периоды.
Во время окислительного периода расплавляется шихта, окисляется кремний, марганец, фосфор, избыточный углерод, частично железо и другие элементы, например хром, титан, и образуется первичный шлак. Реакция окисления такие же, как и при основном мартеновском процессе. Фосфор из металла удаляется в течение первой половины окислительного периода, пока металл в ванне сильно не разогрелся. Образовавшийся при этом первичный фосфористый шлак в количестве 60 – 70% удаляют из печи.
Для получения нового шлака в основную дуговую печь подают обожженную известь и другие необходимые материалы. После удаления фосфора и скачивания первичного шлака металл хорошо прогревается и начинается горение углерода. Для интенсивного кипения ванны в печь забрасывают необходимое количество железной руды или окалины и шлакообразующих веществ.
Во время кипения ванны в течение 45-60 мин избыточный углерод сгорает, растворенные газы и неметаллические включения удаляются. При этом отбирают пробы металла для быстрого определения в нем содержания углерода и марганца и пробы шлака для определения его состава. Основность шлака поддерживается равной 2-2,5, что необходимо для задержания в нем фосфора.
После удаления углерода скачивают весь шлак. Если в металле в период окисления углерода содержится меньше, чем требуется по химическому анализу, то в печь вводят куски графитовых электродов или кокс.
В восстановительный период плавки раскисляют металл, переводят максимально возможное количество серы в шлак, доводят химический состав металла до заданного и подготовляют его к выпуску из печи.
Восстановительный период плавки в основных дуговых печах при выплавке сталей с низким содержанием углерода проводится под белым (известковым) слоем шлаком, а при выплавке высокоуглеродистых сталей – под карбидным шлаком.
Для получения белого шлака в печь загружают шлаковую смесь, состоящую из извести и плавикового шпата. Через некоторое время на поверхности образуется слой шлака с достаточно высокой концентрацией FeO и MnO. Пробы шлака имеют темный цвет.
Перед раскислением металла в печь двумя-тремя порциями забрасывают второю шлаковую смесь, состоящей из кусковой извести, плапикового шпата, молотого древесного угля и кокса. Через некоторое время содержание Feo и MnO понижается. Пробы шлака становятся светлее, закись железа из металла начинает переходить в шлак. Для усиления раскисляющего действия к концу восстановительного периода в печь забрасывают порошок ферросилиция, под влиянием которого содержание FeO в шлаке понижается. В белом шлаке содержится до 50 – 60% СаО, а на поверхности его плавает древесный уголь, что позволяет эффективно удалять серу из металла.
Во время восстановительного периода плавки в металл вводят необходимые добавки, в том числе и легирующие. Окончательно металл раскисляют в печи алюминием.
Выплавка стали под карбидным шлаком на первой стадии восстановительного процесса происходит так же, как и под белым шлаком. Затем на поверхность шлака загружают карбидообразующую смесь, состоящую из кокса, извести и плавикого шпата. При высоких температурах протекает реакция
CaO + 3C = CaC2 + CO.
Образующийся карбид кальция увеличивает раскислительную и обессеривающую способность карбидного шлака. Для ускорения образования карбидного шлака печь хорошо герметизируют. Карбидный шлак содержит 55 –65% СаО и 0,3 – 0,5% FeO; он обладает науглероживающей способностью.
При выплавке стали методом переплава, в печь не загружают железную руду; условия для кипения ванны отсутствуют. Шихта состоит из легированных отходов с низким содержанием фосфора, поскольку его нельзя будет удалить в шлак. Для понижения содержания углерода в шихту добавляют 10 – 15% мягкого железа. Образующийся при расплавлении шихты первичный шлак из печи не удаляют. Это сохраняет легирующие элементы (Cr, Ti, V), которые переходят из шлака в металл.
Устройство и работа индукционных печей. Индукционные печи отличаются от дуговых способом подвода энергии к расплавленному металлу. Индукционная печь примерно работает так же как обычный трансформатор: имеется первичная катушка, вокруг которой при пропускании переменного тока создается переменное магнитное поле. Магнитный поток наводит во вторичной печи переменный ток, под влиянием которого нагревается и расплавляется металл. Индукционные печи имеют емкость от 50 кг до 100 т и более.
В немагнитном каркасе имеются индуктор и огнеупорный плавильный двигатель. Индуктор печи выполнен в виде катушки с определенным числом витков медной трубки, внутри которой циркулирует охлаждающая вода. Металл загружают в тигель, который является вторичной обмоткой. Переменный ток вырабатывается в машинных или ламповых генераторах. Подвод тока от генератора к индуктору осуществляется посредством гибкого кабеля или медных шин. Мощность и частота тока определяются емкостью плавильного тигля и состава шихты. Обычно в индукционных печах используется ток частотой 500 – 2500 гц. Крупные печи работают на меньших частотах. Мощность генератора выбирают из расчета 1,0 – 1,4 квт/кг шихты. Плавильные тигли печей изготавливают из кислых или основных огнеупорных материалов.
В индукционных печах сталь выплавляют методом переплава шихты. Угар легирующих при этом получается очень небольшим. Шлак образуется при загрузке шлакообразующих компонентов на поверхность расплавленного металла. Температура шлака во всех случаях меньше температуры металла, так как шлак не обладает магнитной проницаемости и в нем не индуцируется ток. Для выпуска стали из печи, тигель наклоняют в сторону сливного носка.
В индукционных печах нет углерода, поэтому металл не науглероживается. Под действием электромагнитных сил металл циркулирует, что ускоряет химические реакции и способствует получению однородного металла.
Индукционные печи применяют для выплавки высоколегированных сталей и сплавов особого назначения, имеющих низкое содержание углерода и кремния.
4. Новые методы производства и обработки стали.
Электроннолучевая плавка металлов. Для получения особо чистых металлов и сплавов используют электроннолучевую плавку. Плавка основана на использовании кинетической энергии свободных электронов, получивших ускорение в электрическом поле высокого напряжения. На металл направляется поток электронов, в результате чего он нагревается и плавится.
Электроннолучевая плавка имеет ряд преимуществ: электронные лучи позволяют получить высокую плотность энергии нагрева, регулировать скорость плавки в больших пределах, исключить загрязнение расплава материалом тигля и применять шихту в любом виде. Перегрев расплавленного металла в сочетании с малыми скоростями плавки и глубоким вакуумом создают эффективные условия для очистки металла от различных примесей.
Электрошлаковый переплав. Очень перспективным способом получения высококачественного металла является электрошлаковый переплав. Капли металла, образующиеся при переплаве заготовки, проходят через слой жидкого металла и рафинируются. При обработке металла шлаком и направленной кристаллизации слитка снизу вверх содержание серы в заготовке снижается на 30 – 50%, а содержание неметаллических включений – в два-три раза.
Вакуумирование стали. Для получения высококачественной стали, широко применяется вакуумная плавка. В слитке содержатся газы и некоторое количество неметаллических включений. Их можно значительно уменьшить, если воспользоваться вакуумированием стали при ее выплавке и разливке. При этом способе жидкий металл подвергается выдержке в закрытой камере, из которой удаляют воздух и другие газы. Вакуумирование стали производится в ковше перед заливкой по изложницам. Лучшие результаты получаются тогда, когда сталь после вакуумирования в ковше разливают по изложницам так же в вакууме. Выплавка металла в вакууме осуществляется в закрытых индукционных печах.
Рафирование стали в ковше жидкими синтетическими шлаками. Сущность этого метода состоит в том, что очистка стали от серы, кислорода и неметаллических включений производится при интенсивном перемешивании стали в ковше с предварительно слитым в него шлаком, приготовленном в специальной шлакоплавильной печи. Сталь после обработки жидкими шлаками обладает высокими механическими свойствами. За счет сокращения периода рафинирования в дуговых печах, производительность которых может быть увеличена на 10 – 15%. Мартеновская печь, обработанная синтетическими шлаками, по качеству близка к качеству стали, выплавляемой в электрических печах.
Список используемой литературы.
- «Технология металлов и других конструкционных материалов» В.Т.Жадан, Б.Г. Гринберг, В.Я. Никонов Издание второе.
- «Общая химия» Н.Л. Глинка Издание двадцать третье.
- «Металлургия» А.П. Гуляев 1966 год.
vsempomogu.ru
Производство чугуна
Металлургия
Металлургия – это наука о способах получения металлов и металлических сплавов. Сплав – это соединение двух или более компонентов, главным из которых является металл.
Основоположник металлургии – Д.К.Чернов
История человечества неразрывно связана с использованием металлов.
тысячелетие до н.э. – медный век (выплавка меди и олова)
3-2 тысяч. до н.э. – бронзовый век (сплав меди с оловом)
2-1 тыс. до н.э. – железный век ( железо восстановленное из руды, сталь – сплав железа с углеродом)
В настоящее время известно около 80 металлов.
Среди металлов железо занимает третье место по распространенности в земной коре (4,2 %) после кремния(26 %) и алюминия(7,4 %). Железо в недрах земли в чистом виде не встречается. Оно входит в состав горных пород в различных химических соединениях. В природе известно более 300 разновидностей горных пород, содержащих железо, но далеко не все они представляют собой железные руды. Железными рудами принято называть такие горные породы, из которых экономически выгодно извлекать железо методом плавки. Экономическая целесообразность извлечения железа из руд зависит от уровня развития техники и характеристики месторождений.
Краткая классификация металлов и сплавов.
I Черные металлы и сплавы (Fe+C)
1. Сталь (содержит до 2,14% С)
2. Чугун (содержит от 2,14 до 6,67% С)
3. Ферросплавы (> 6,67% С)
II – Цветные металлы и сплавы
Легкие
а) на основе Al (Al+Si) – силумин
б) на основе Mg (↑ корозион. стойкость)
и т.д.
Тяжелые
а) на основе Cu
- Cu+Sn (свинец) →бронза
- Cu+Zn (цинком)→латунь
б) на основе Sn
в)на основе Pb
и т. д.
Тугоплавкие
а) На основе Ti – титана (↑ тверд.)
б) На основе Mo – молибдена
в) На основе Ni – никеля
г) На основе Со – кобальта
Металлы склонны к окислению, поэтому в земной коре они содержатся виде химических соединений (исключение золото, платина, серебро, медь.)
Общая масса металлов в земной коре – 25% из них:
Al = 7,4% Zn=0,005%
Fe=4,2% Ag=0,00001%
Cu=0,01% Au=0,0000005%
Производство чугуна
Чугун – сплав железа с углеродом содержащем углерода более 2,14% с присутствием Si=4%, Mn=2%, S, P.
Получение железа из руды с помощью сыродутного процесса было изобретено в Западной Азии во 2-м тысячелетии до нашей эры. Период с 9 – 7 века до нашей эры, когда у многих племен Европы и Азии развилась металлургия железа, получил название железного века, пришедшего на смену бронзовому веку.
Цель доменного производства состоит в получении чугуна из железных руд путем их переработки в доменных печах. Железные руды вносят в доменную печь химически связанное с другими элементами железо. Восстанавливаясь и науглераживаясь в печи, железо переходит в чугун. С марганцевой рудой в доменную печь вносится марганец для получения чугуна требуемого состава.
Чугун производят в
доменных печах
Исходные материалы для плавки
Сырыми материалами доменной плавки являются
1.Руда – природное минеральное сырьё содержащие металл, который необходимо извлечь наиболее экономичным способом.
В земной коре железо распространено достаточно широко — на его долю приходится около 4,1% массы земной коры (4-е место среди всех элементов, 2-е среди металлов). Известно большое число руд и минералов, содержащих железо. Наибольшее практическое значение имеют красные железняки (руда гематит, Fe2O3; содержит до 70% Fe), магнитные железняки (руда магнетит, Fe3О4; содержит 72,4% Fe), бурые железняки (руда гидрогетит НFeO2•nh3O), а также шпатовые железняки (руда сидерит, карбонат железа, FeСО3; содержит около 48% Fe).
Среди известных видов руд наиболее распространены в природе руды осадочного происхождения. Из этих руд выплавляется более 90 % чугуна. Железная руда состоит из минерала (орудняющего вещества), пустой породы и примесей. Главной частью руды является рудный минерал, в состав которого входит железо. Чаще всего железо в минерале химически связано с кислородом, реже с другими элементами и соединениями. Пустая порода состоит из кремнезема, глинозема, извести. Примеси руд делятся на полезные и вредные. Полезными примесями считаются марганец, хром, никель, ванадий, вольфрам, молибден и др. Вредные примеси – сера, фосфор, мышьяк, цинк, свинец и в большинстве случаев медь – либо ухудшают качество металла, либо разрушающе действуют на огнеупорную футировку доменной печи.
Состав руды: 1. Рудный минерал
2.Пустая порода – минералы не осложняющие
переработку руды→ легко переходят в шлаки
3.Примеси. Вредные примеси сера, фосфор,
мышьяк → осложняющие переработку
В зависимости от типа рудного минерала железные руды делятся на четыре основные группы:
а) Красный железняк (гематит)
45-65% Fe
Красный железняк или гематитовая руда. Минерал гематит – безводный оксид железа, в чистом виде содержит 70 % железа и 30 % кислорода. Это наиболее распространенная железная руда.
б) Бурый железняк (лимонит)
25-50% Fe
Бурый железняк представлен железосодержащими минералами водных оксидов железа, которые содержат от 59,8 % до 69 % железа.
в) Магнитный железняк (магнетит)
40-70% Fe
Магнитный железняк или магнетитовая руда. Минерал – магнетит (72,4 % железа и 27,6 % кислорода)
Чем выше содержание железа в железной руде, тем экономичнее и производительнее работает доменная печь
Кроме перечисленных разновидностей железных руд, железо в значительном количестве (46,6%) содержится в серном колчедане или пирите. Однако пирит в доменную плавку не дают, его используют в качестве сырья в сернокислотной промышленности, а отходы в виде окисленного железа применяют при производстве агломерата. Также находят промышленное применение бедные железные руды: магнетитовые и гематитовые кварциты, в которых содержится до 45 % кремнезема в виде свободного кварца. Кварциты обогащают, получая железнорудный концентрат, содержащий более 60 % железа.
Критерием оценки железных руд являются:
1. Содержание железа.
2. Тип основного железосодержащего минерала.
3. Состав и свойства пустой породы.
4. Содержание вредных примесей.
5. Стабильность химического состава.
2.Флюсы - необходимы для удаления из доменной печи тугоплавких пустых пород. Сплавляясь с ними они образуют легко выводимые шлаки. Флюсы – окатыши из известняка.
Флюсом называются добавки, загружаемые в доменную печь для понижения температуры плавления пустой породы руды, офлюсования золы кокса и придания шлаку требуемых технологией выплавки чугуна физико-химических свойств. Для руд с кремнеземистой (кислой) пустой породой в качестве флюса используют материалы, содержащие оксиды кальция и магния: известняк и доломитизированный известняк. Важнейшим требованием, предъявляемым к основным флюсам, является низкое содержание в них кремнезема и глинозема и вредных примесей серы и фосфора.
3.Кокс – из каменного угля. Является топливом, а также восстанавливает оксиды железа. (Вместо кокса может использоваться природный газ.)
Его роль состоит в обеспечении процесса теплом и восстановительной энергией. Кроме того кокс разрыхляет столб шихтовых материалов и облегчает прохождение газового потока в шихте доменной печи.
В качестве топлива в современной доменной плавке применяют кокс, мазут, природный и коксовый газы и каменноугольную пыль. Основным видом топлива является кокс. Коксом называется пористое спекшееся вещество, остающееся после удаления из каменного угля летучих веществ при нагревании его до 950-1200С без доступа воздуха. Это единственный материал, который сохраняет форму куска в доменной печи на всем пути движения от колошника к горну. Благодаря этому обстоятельству обеспечивается прохождение газового потока через слой жидких, полужидких и твердых материалов в доменной печи. В нижней части печи раскаленный кокс образует своеобразную дренажную решетку, через которую в горн стекают жидкие продукты плавки. Высота столба шихты в современной доменной печи достигает 30 м, поэтому кокс, особенно в нижней части печи, воспринимает большие нагрузки. Отсюда вытекает основное требование, предъявляемое к коксу: высокая механическая прочность как в холодном, так и в нагретом состоянии.
Загружаемый в доменную печь кокс не должен содержать ни мелких кусков, ухудшающих газопроницаемость шихты, ни чрезмерно крупных кусков, которые, как правило, поражены трещинами и легко разрушаются в печи с образованием мелких фракций.
Кокс должен быть пористым для обеспечения хорошей горючести в горне печи и обладать высокой теплотой сгорания для получения требуемого количества тепла и необходимой температуры. Теплота сгорания кокса зависит от содержания в нем углерода, которое определяется содержанием золы, вредных примесей и летучих веществ в коксе. Чем выше содержание золы, вредных примесей и летучих веществ в коксе, тем меньше в нем углерода и меньше теплота его сгорания. Кроме того, с увеличением содержания золы и серы в коксе возрастают количество шлака, расход тепла на его расплавление и снижается механическая прочность кокса, а с увеличением содержания серы и фосфора в коксе ухудшается качество чугуна. Повышенное содержание летучих веществ в коксе свидетельствует о незавершенности процесса коксования, что приводит к снижению механической прочности кокса. Чрезмерно низкое содержание летучих в коксе, получающееся при пережоге кокса, также отрицательно сказывается на его качестве. Поэтому кокс должен содержать по возможности меньше золы, серы, фосфора и умеренное количество летучих веществ.
В коксе всегда содержится влага, поступающая в кокс при его тушении на коксохимическом заводе или из атмосферы. В связи с тем, что кокс в доменной печи загружают по массе, содержание влаги в коксе должно выдерживаться постоянным для сохранения заданного теплового режима печи.
Подготовка исходных материалов к плавке
Шихта- подготовленные к плавке исходные материалы (руда, флюсы и топливо)
Дробление – измельчение руды до 30-80мм.
и сортировка руды по размеру кусков.
Доменная печь работает нормально, если она загружена кусковым материалом оптимального размера. Слишком крупные куски руды за время опускания их в печи не успевают прогреваться на всю длину, часть материала расходуется бесполезно. Слишком мелкие куски плотно прилегают друг к другу и нет выхода для газов. Оптимальный кусок 30-80 мм. Поэтому руду с кусками больше 100 мм подвергают дроблению.
Мелочь также не пригодна к плавке и ее подвергают окускованию. Для этого в металлургии применяют агломерацию – окускование путем спекания.
Исходный материал для агломерации рудная мелочь и колошниковая пыль (отход доменного производства) + мелкий кокс (до 3 мм) + недопекшийся агломерат + измельченный известняк (до 20 мм) = шихта.
Слегка увлажненную и перемешенную шихту слоем 200-300 мм загружают на решетки тележек образующих рабочую ленту агломерационной машины, затем поджигают. Воздух для горения просасывается через слой шихты с помощью вакуумных устройств, расположенных под решетками
В зоне горения t=1500°C происходит спекание шихты в пористый продукт –
агломерат.
Достоинства агломерата:
пористость и прочность кусков
введение флюса - известняка увеличивает производительность доменной печи и снижает расход кокса.
Еще один способ окускования – брикетирование. Это путем прессования смеси порошковых мат-лов со связующими материалами (глиной, жидким шлаком, смолой и т.д.)
Следующий способ окускования производство окатышей. Это перемешивание рудной мелочи и пыли небольшим количеством глины или извести. После увлажнения эту смесь помещают в барабан или наклонную чашку. Шихта при перемещении слипается, образуя окатыши 25-30 мм. Затем их сушат или обжигают для упрощения.
2. Усреднение
Железные руды по условиям залегания и добычи всегда имеют непостоянный химический состав. Значительные и частые колебания содержания железа и пустой породы в рудах вызывают нарушение теплового состояния доменной печи и химического состава шлака. Это приводит к нарушению ровного хода печи, при котором неизбежны повышение расхода кокса, снижение производительности печи и ухудшение качества выплавляемого чугуна.
Чтобы уменьшить отрицательное влияние непостоянства химического состава руд на показатели доменной плавки, руды подвергают усреднению. Усреднением называют перемешивание железорудных материалов с целью выравнивания химического и гранулометрического составов. В связи с тем, что почти все добываемые руды подвергают окуксованию, основное назначение усреднения состоит прежде всего в уменьшении колебаний содержания железа и кремнезема в рудах. Необходимо добиться такого усреднения руд, при котором колебания содержания железа и кремнезема в руде не превышали бы 0,5 % от среднего значения.
3.. Обогащение руды - выделение пустой породы с получением концентрата, содержащего 65-66% Fe
Обогащением называется процесс разделения рудного минерала и пустой породы с целью повышения содержания металла в руде и уменьшения содержания пустой породы, а в некоторых случаях и вредных примесей. Все способы обогащения основаны на различии физических свойств рудных минералов и пустой породы. В результате обогащения руды получают:
концентрат – продукт, в котором содержится большая часть извлекаемого металла;
хвосты – отходы при обогащении руды, в которых содержится незначительное количество металла;
промежуточный продукт, в котором содержание металла больше, чем в хвостах и меньше, чем в концентрате.
Основной способ обогащения – магнитный. Минералы отделяют магнитом или электромагнитом.
Другой способ обогащения – гравитационный. (основан на осаждении минерала, т.к. он имеет большую плотность)
Основан на различии плотности и скорости падения зерен в жидкости и на воздухе. Т.е. рудной минерал тонет, а частицы пустой породы всплывают. Простейший вид - это промывка водой железной руды для удаления песчано-глинистой пустой породы.
Ещё один способ обогащения – флотация. (основан на способности некоторых минералов прилипать к водным пузырькам) используется метод редко
Основан на избирательном применении некоторых минеральных частиц, взвешенных в водной среде, к поверхности пузырьков воздуха и поднятия их частиц на поверхность.
Доменная плавка
Доменный процесс представляет собой совокупность механических, физических и физико-химических явлений, протекающих в работающей доменной печи. Загружаемые в доменную печь шихтовые материалы – кокс, железосодержащие компоненты и флюс – в результате протекания доменного процесса превращаются в чугун, шлак и доменный газ.
В химическом отношении доменный процесс является восстановительно- окислительным: из оксидов восстанавливается железо, а окисляются восстановители. Однако доменный процесс принято называть восстановительным, так как цель его состоит в восстановлении оксидов железа до металла.
Агрегатом для осуществления доменного процесса служит печь шахтного типа (см. приложение 2). Рабочее пространство доменной печи в горизонтальных сечениях имеет круглую форму, а в вертикальном разрезе – своеобразное очертание, называемое профилем.
Важнейшим условием осуществления доменного процесса в рабочем пространстве печи является непрерывное встречное движение и взаимодействие опускающихся шихтовых материалов, загружаемых в печь через колошник, и восходящего потока газов, образующегося в горне при горении углерода кокса в нагретом до 1000 – 1200( С воздухе (дутье), который нагнетается в верхнюю часть горна через расположенные по его окружности фурмы. К дутью может добавляться технический кислород, природный газ, водяной пар.
Домна – грандиозная конструкция – это шахтная печь высотой 30-50 метро позволяют выплавить в сутки до 5000 т. чугуна. Толстые стены (70 см) из огнеупорной глины, снаружи обшиты кожухом из стальной брони.
Рис. 1. Химия и технология доменного процесса: а – состав чугуна; б – схема доменной печи; в – химические реакции доменного процесса; г – условия оптимизации процессов |
Снизу через фурму (устройство для подвода дутья) поступают горячий воздух, кислород, метан, а навстречу движется шихта – смесь, состоящая из кокса (источник энергии и восстановитель), подготовленного рудного концентрата и флюса (последний для связывания пустой породы в шлаки). Домну через колошник (верхняя часть шахтных доменных плавильных печей) покидает доменный газ, содержащий до 30% СО. Домна – сложнейшее инженерное сооружение высотой более 60 м и диаметром 10 м, снабженное системой контроля и управления, предназначенное для выплавки чугуна – продукта химико-восстановительных процессов. Далее на схеме показаны основные химические реакции доменного процесса (рис. 1, в). Это – горение кокса в зоне над горном (нижняя часть домны, где происходит горение топлива). Шлак выполняет также функцию защиты чугуна от окисления. Далее происходит собственно восстановление железа, затем – восстановление примесных элементов и науглероживание железа и, наконец, образование шлаков. Главное в любой технологии – это оптимизация процессов и высокая производительность аппаратов, экономичность производства. Остановимся на этом вопросе (рис. 1, г). Как видно, на производительность доменной печи Пр влияют ее объем Vд.п и скорости химических реакций .
|
Рис. 2. Факторы оптимизации доменного процесса |
Подготовленные исходные материалы называются шихта.
Сущность доменной плавки:
раздельная загрузка шихты→горение кокса→нагрев шихты→взаимодействие её с горячими газами→ восстановление железа из окислов и соединение его с углеродом→образование в нижней части печи 2-х жидких слоев – чугун + шлак.
Схему доменной печи можно подробно рассмотреть в литературе по данной дисциплине
Основные части доменной печи: колошник , шахта, распар, заплечики, фурменный пояс, горн, лещадь.
1) В верхней части расположен засыпной аппарат , состоящий из двух поочередно опускающихся конусов (чтобы доменные газы не могли вырваться в атмосферу) Шихтовые материалы загружают в доменную печь при помощи засыпного аппарата отдельными порциями – подачами. Они располагаются на колошнике чередующимися слоями кокса, руды или агломерата и флюса при работе на не полностью офлюсованном агломерате. Загрузку подач производят через 5 – 8 мин. по мере освобождения пространства на колошнике в результате опускания материалов.Материалы на колошник подают специальными тележками – скипами, перемещающимися по рельсам наклонного моста. Объем материалов одной подачи соответствует объему нескольких скипов, поэтому подача на колошник подается по частям несколькими скипами. При этом одну часть скипов подачи загружают коксом, а другую – железосодержащими компонентами и флюсом. При полностью офлюсованном агломерате подача состоит только из скипов с агломератом и коксом.
Два подъемника с ковшами доставляют шихту в верхнюю воронку → конус опускается →шихта загружается в нижнюю и в печь.
2) Для осуществления процесса горения через фурменные отверстия подается в горн горячий кислород (1200°С)→ горение → образуется углекислота, которая взаимодействует с коксом.
CO2+C=2CO
Кокс поступает в горн нагретым до 1400 – 15000С. В зонах горения кокса углерод взаимодействует с кислородом дутья. Образующийся в зонах горения диоксид углерода при высокой температуре и избытке углерода неустойчив и превращается в оксид углерода. Таким образом, за пределами зон горения горновой газ состоит только из оксида углерода, азота и небольшого количества водорода, образовавшегося при разложении водяных паров или природного газа. Смесь этих газов, нагретая до 1800 – 2000( С , поднимается вверх и передает тепло материалам, постепенно опускающимся в горн
При взаимодействии жидких продуктов плавки с раскаленным коксом в заплечиках и горне происходит усиленное восстановление кремния, марганца и фосфора из их оксидов, растворенных в шлаке. Здесь же поглощенная металлом в ходе плавки сера переходит в шлак. Железо и фосфор печи полностью восстанавливаются и переходят в чугун, а степень восстановления кремния и марганца и полотна удаления из чугуна серы в большой мере зависят от температурных условий, химического состава шлака и его количества.
Жидкие чугун и шлак разделяются в горне благодаря различным удельным массам. По мере скопления их в горне чугун выпускают через чугунную летку, а шлак – через шлаковые летки (верхний шлак) и чугунную летку во время выпуска чугуна (нижний шлак).
Все перечисленные процессы протекают в доменной печи одновременно, оказывая взаимное влияние.
3) В нижней половине шахты - ЛЕЩАДИ начинается образование жидкого шлака из составных частей пустой породы руды и флюса. Понижению температуры плавления шлака способствуют невосстановленные оксиды железа и марганца. В стекающем вниз шлаке под действием возрастающей температуры постепенно расплавляется вся пустая порода и флюс, а после сгорания кокса – и зола.
Цель химических превращений – восстановление железа из окислов и соединение его с углеродом
Одним из условий получения чугуна в доменной печи является удаление кислорода из оксидов, металлы которых входят в состав чугуна. Процесс отнятия кислорода от оксида и получения из него элемента или оксида с меньшим содержанием кислорода называется восстановлением. Наряду с восстановлением протекает окисление вещества, к которому переходит кислород оксида. Это вещество называется восстановителем.
Восстановительные процессы сопровождаются выделением или поглощением тепла. Химическая прочность оксида определяется силами химической связи данного элемента с кислородом.
при температуре выше 5700
Fe2O3 → Fe3O4 → FeO →Fe
3Fe2O3+CO = 2Fe3O4+CO2+Q
3Fe3O4+CO = 3FeO+CO2+Q
FeO+CO = Fe + CO2+Q
Эти реакции обратимы, при снижении температуры равновесие сдвигается влево.
3) В нижней части горна образуется жидкий слой чугуна, который через каждые 2-3 часа выпускается через чугунные летки – специальные желоба. Чугун сливается в ковши.
Шлак сливается через шлаковые летки. Шлаки используют для производства цемента, теплоизоляции – шлакоблоки.
4)Газообразные продукты реакции – колошниковые газы (окись углерода + азот + пыль) выводится через колошник, очищается и используется для подогрева воздуха, подающегося в горы.
Газовый поток
Высокопроизводительная и экономичная работа доменной печи в значительной мере зависит от того, как организовано движение и распределение газов и шихты в ее рабочем пространстве. Движение газов и распределение их в печи определяется множеством факторов, но главным из них являются гранулометрический состав шихты и ее распределение на колошнике во время загрузки и перераспределение при движении в доменной печи. В свою очередь и движущийся газовый поток влияет на распределение шихты.
Газы в доменной печи движутся через слой шихты снизу вверх под действием разности давлений, зависящей от величины сопротивления загруженной в печь шихты и количества воздуха, нагнетаемого в горн воздуходувной машиной. Проходя путь 24 – 26 м в течение нескольких секунд, газовый поток должен выполнить тепловую и восстановительную работу и обеспечить ровный сход шихтовых материалов от колошника к горну. Исходя из этих функций газового потока к распределению газов предъявляются противоречивые требования. Для наиболее полного использования тепла и восстановительной способности газового потока газы по сечению печи должны распределяться равномерно, иными словами, температура и состав газов во всех точках сечения доменной печи должны быть одинаковыми, а шихта – в равной мере нагретой и восстановленной.
Для обеспечения ровного схода шихты газовый поток по сечению печи должен распределяться неравномерно, проходя в большем количестве у стен и в осевой зоне печи, т. е. там, где чаще всего бывает меньше руды или агломерата.
В действительности же в доменной печи невозможно достичь равномерного распределения газов по сечению вследствие специфических особенностей доменного процесса и конструкции доменной печи.
Наиболее важным показателем, характеризующим распределение газового потока по сечению столба шихты, является сопоставление количества газов, проходящих через равновеликие площади заполненного шихтой сечения печи в единицу времени.
studfiles.net
Процесс производства чугуна
Чугун – железоуглеродистый сплав, содержащий более 2% углерода. Кроме углерода, в нем всегда присутствуют кремний (до 4%), марганец (до 2%), а также фосфор и сера. Чугун является основным исходным материалом для получения стали, на что расходуется примерно 80-85% всего чугуна.Руды, флюсы и топливо
Железные руды – основной исходный материал для выплавки чугуна. Пустая порода обычно состоит из кварца и песчаников с примесью глин, т.е. является кислой (избыток SiO2).
Железные руды в отличие от медных и многих других относительно богаты. Наиболее богатые руды содержат 60% железа и больше, наиболее бедные 30-40%.
В железных рудах всегда присутствуют вредные примеси – сера и фосфор. По типу рудного минерала руды бывают следующих основных видов.
Красный железняк. Рудный минерал – гематит, безводная окись железа Fe2O3 (70% Fe). Руда обычно содержит 50-60% Fe. Это наиболее распространенный вид руды во всем мире.
Магнитный железняк. Рудный минерал – магнетит, магнитная окись железа Fe3O4 (72,4% Fe), в руде 55-60% Fe.
Бурый железняк. Рудный минерал – водные окислы железа nFe2O3 · mh3O (52-66% Fe). В руде обычно содержится 30-50% Fe.
Шпатовый железняк. Рудный минерал – сидерит, карбонат железа FeCO3 (48,3% Fe), в руде обычно 30-40% Fe.
Доменные флюсы необходимы для удаления из доменной печи тугоплавкой пустой породы руды и золы топлива. Сплавляясь с флюсом, они образуют легкоплавкий сплав – доменный шлак; в расплавленном состоянии он удаляется из печи через шлаковую летку. Кроме того, флюс должен обеспечить получение шлака с необходимым химическим составом и физическими свойствами, что в значительной мере определяет состав чугуна.
Флюсы выбирают в зависимости от пустой породы руды. В отечественных железных рудах пустая порода, как правило, содержит избыток SiO2. Поэтому в качестве флюса используют сильноосновные материалы, главным образом известняк CaCO3. Типичный металлургический известняк после обжига содержит 50-55% CaO. Избыток извести в доменном шлаке способствует также удалению из чугуна серы. На отечественных заводах флюсы вводят в доменную печь главным образом в виде офлюсованного агломерата и офлюсованных окатышей.
Топливо в доменных печах служит не только источником тепла, но реагентом, обеспечивающим восстановление железа из руды и образования чугуна (путем науглероживания железа).
Основные требования к доменному топливу – высокая теплотворность, малое содержание золы, чистота по содержанию вредных примесей. Топливо должно иметь высокую механическую прочность, так как его дробление и образование мелочи препятствует нормальному движению печных газов, а также высокую пористость для обеспечения интенсивного горения. Топливо должно быть недефицитным и иметь невысокую стоимость.
Кокс является главным видом топлива в доменных печах и в среднем содержит 10-13% золы, 0,5-2% серы. Он достаточно прочен, что позволяет строить крупные доменные печи объемом до 5000 м3. На выплавку 1т чугуна расходуется около 550 кг кокса. При этом стоимость кокса составляет 45-55% себестоимости чугуна.
Вдувание 60-100 м3 природного газа на 1т выплавляемого чугуна снижает расход кокса на 10-15%, повышает восстановительную способность доменных газов, обеспечивает более высокую производительность доменной печи. Наиболее эффективным оказалось применение природного газа в сочетании с высокотемпературным дутьем, обогащенным кислородом.
Подготовка руды к плавкеВ настоящее время для выплавки чугуна используют лишь около 5% сырой железной руды; 95% всей руды до плавки подвергают предварительной подготовке. Подготовка железной руды является одним из эффективных направлений в совершенствовании доменного производства и дает возможность использовать более бедные руды. Подготовка руд включает дробление, сортировку и другие операции.
Дробление обеспечивает нужную степень измельчения руды. Для плавки в доменной печи размер кусков руды должен составлять 10-18 мм, для агломерации – менее 5-10 мм, для магнитного обогащения – 0,1 мм.
Сортировку руды по классам крупности при размерах кусочков более 1-3 мм проводят на механических грохотах. Для более тонко измельченных материалов используют гидравлическую классификацию. Разделяемый материал подают вместе с водой в специальные устройства, где крупные зерна быстрее оседают, отделяясь от более мелких. В устройствах типа гидроциклон разделение частиц по крупности происходит под действием центробежной силы.
Усреднение материалов по химическому составу и свойствам необходимо для обеспечения ровного хода доменной печи. Одним из основных методов усреднения руды является ее послойная укладка в штабеля большой емкости.
Обогащение руды приобретает все большее значение. В настоящее время до плавки обогащают около 80% всей руды. Это связано с использованием все более бедных руд, а также руд с тонковкрапленными в пустой породе рудными зернами. Так, например, в результате обогащения бедных криворожских железистых кварцитов с 20-45% Fe получают концентраты с 60-65% Fe. Основным способом обогащения железной руды в нашей стране является магнитный. Сущность сухой магнитной сепарации состоит в том, что тонкоизмельченную руду помещают в магнитное поле, где магнитные частицы руды отделяются от пустой породы. При мокрой сепарации руда при воздействии на нее магнитного поля одновременно промывается водой. Этот способ более гигиеничен, чем предыдущий, при котором выделяется много пыли. Магнитное обогащение можно непосредственно использовать только для так называемых сильномагнитных магнетитовых и титаномагнетитовых руд. Для других руд – средне- и слабомагнитных – перед обогащением производят магнетизирующий обжиг.
Среди других методов обогащения наиболее распространен гравитационный: отсадка и разделение в тяжелых суспензиях (взвесях), в которых рудный минерал тонет, а частицы пустой породы всплывают.
Для удаления рыхлой песчаной и глинистой пустой породы применяют также наиболее простой и дешевый способ – промывку водой.
Устройство доменной печиДоменная печь (рис. 6) – вертикальная печь шахтного типа. Ее высота (до 35 м) примерно в 2,5-3 раза больше диаметра.
Стенки печи выкладывают из огнеупорных материалов – в основном из шамота. Нижнюю часть горна и его основание (лещадь) выполняют из особо огнеупорных материалов – углеродистых (графитизированных) блоков. Для повышения стойкости огнеупорной кладки в ней устанавливают (примерно на ¾ высоты печи) металлические холодильники, по которым циркулирует вода. Для уменьшения расхода воды (для крупных печей до 70000 м3 в сутки) применяют испарительное охлаждение, основанное на том, что поглощаемое тепло используется для парообразования.
Кладка печи снаружи заключена в стальной кожух толщиной до 40 мм. Для уменьшения нагрузки на нижнюю часть печи ее верхнюю часть (шахту) сооружают на стальном кольце, опирающемся на колонны.
С увеличением полезного объема (рабочего пространства) доменных печей повышается их экономичность.
Современные крупные доменные печи имеют объем 2000-3000 м3.
На Криворожском заводе с 1974 г. работает печь объемом 5000 м3.
Воздух для горения топлива вдувается через 14-36 фурм в верхнюю часть горна печи.
В современную доменную печь для выплавки 1т чугуна вдувается около 3000 м3 воздуха; его расход на крупных печах достигает 6000-7000 м3/мин, что обеспечивается быстроходными турбовоздуходувными машинами (3500-4500 об/мин). Воздух нагревается в специальных воздухонагревателях. Каждую доменную печь обслуживают три-четыре автоматически переключающихся воздухонагревателя.
Значительный эффект дало повышение давления под колошником примерно до 2,5 атм., приводящее к уменьшению скорости газа, улучшению теплообмена и интенсификации физико-химических процессов. Крупнейшим усовершенствованием явилось обогащение дутья кислородом (до 30%). Наибольший эффект дало комплексное использование этих мер при применении природного газа. Производительность печей повысилась примерно на 50%, а расход кокса снизился на 25-30%.
Доменная печь работает непрерывно в течение 5-10 лет. Для этого по мере необходимости в нее загружают отдельными порциями (колошами) шихтовые материалы, периодически выпускают чугун и шлак, непрерывно удаляют доменные газы.
Для выплавки 1т передельного (мартеновского) чугуна в среднем расходуется около 1,8т офлюсованного агломерата, 550 кг кокса. Таким образом, печь объемом 3000 м3 в сутки потребляет примерно 8500т шихтовых материалов и выплавляет около 5000-5500т чугуна.
В современных доменных печах все процессы по подготовке и загрузке шихтовых материалов полностью механизированы.
К вспомогательным устройствам, обеспечивающим работу печи, относятся: шихтовые дворы, оборудованные погрузочно-разгрузочными устройствами; бункерные эстакады с вагон-весами для автоматического взвешивания шихтовых материалов, подъемные механизмы, доставляющие самоопрокидываааающиеся тележки-скипы с шихтой к загрузочному аппарату доменной печи. Для нормальной работы печи необходимы также воздухонагреватели и другие устройства для осуществления горячего дутья, литейный двор, ковши – чугуновозы и шлаковозы, разливочные машины и т.д.
biofile.ru
Производство чугуна в России, история развития
На протяжении нескольких сотен лет Российская Федерация находится в числе мировых лидеров по производству чугуна. Данный сплав применяется в самых разных сферах промышленности, используется для создания художественных и декоративных изделий. Эксперты говорят: чугун – это неотъемлемая часть жизни человека, он заслуженно считается одним из самых востребованных материалов. Сегодня мы предлагаем поговорить о черной металлургии, производстве чугуна и стали, их влиянии на человека. Обратимся и к хронике развития литейного дела в целом: вас ждут исторические факты и интересная информация!
История: медно-каменный век
Чугун – это металл, история которого насчитывает тысячи лет, ее корни уходят в эпохи до нашей эры. Вообще, историки датируют первые свидетельства возникновения металлургии VI-V тысячелетием до нашей эры. Тогда человек еще использовал камень для создания орудий, но ему уже попадались медные самородки. Принимая самородки за обычные камни и обрабатывая их тем способом, что применялся к любым камням, – просто ударяя друг от друга – человек понимал: данные камни не откалываются, а лишь деформируется, а потому им можно придать практически любую форму. Такой метод историки позднее назовут холодной ковкой. Так медь стала заменой камню, изготавливать рыболовные крючки, наконечники копий и кинжалы стало гораздо проще, к тому же качество таких изделий значительно превышало качество аналогов из камня и кости. В то же время усовершенствовалась обработка дерева, появилась возможность изготавливать мелкие детали. Кстати, ученые доказали: на тех территориях, где активно использовалась медь, появление колеса произошло существенно раньше. Это доказывает тот факт, что развитие человечества неразрывно и тесно связано с развитием металлургии.
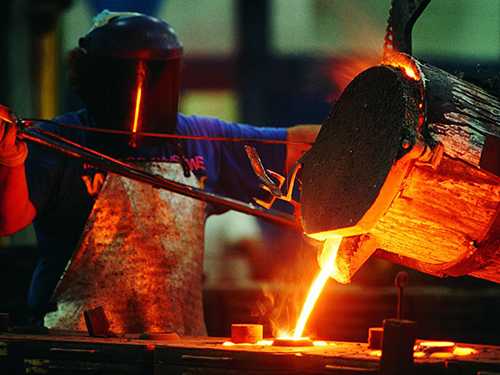
Бронзовый век
Когда люди научились создавать бронзу – сплав, состоящий из меди и олова, человечество вступило в Бронзовый век. Сегодня историки не могут ответить на вопрос о том, как именно человек изобрел такой сплав. Большая часть исследователей считает: произошло это по чистой случайности, когда в емкость с расплавленной медью попало олово. Факт остается фактом: на протяжении целой тысячи лет люди воевали бронзовыми мечами и готовили еду в бронзовых котелках.
Железный век
Историки утверждают: добыть железо было куда проще, чем медь или олово. Все дело в том, что она встречается в виде окиси и закиси повсеместно. Так почему люди не начали применять железо раньше? Ответ прост: производство этого металла – процесс невероятно сложный и трудоемкий, проходящий в несколько этапов. На изучение данного процесса потребовалось не одно столетие развития. Потому неудивительно, что металлурги тех времен в народе считались настоящими колдунами, горящими магические вещи.
Первые упоминания о чугуне
Страной, в которой началось производство чугуна, сегодня считается Китай. Историки говорят, что произошло это примерно в пятом веке до нашей эры. В Поднебесной были крайне популярны монеты, предметы домашней утвари и разнообразное оружие, производимые из чугуна. До наших времен дошло множество чугунных отливок, к примеру, великолепный чугунный лев, высота которого составляет 6 метров, а длина – 5. Ученые доказали: эта статуя была отлита за один раз, что, несомненно, свидетельствует о большом мастерстве первых китайских металлургов.
Интересный факт: во всем мире началом производства ковкого чугуна считается XIX век нашей эры, хотя достоверно известно, что в Китае из него делали мечи еще до Рождества Христова!
Зарождение производства в России
Когда же началось производство чугуна в России? Археологические раскопки, проводимые на территории крупных городов Золотой Орды, доказывают: появление и развитие данного производства в России началось еще во времена татаро-монгольского ига! Определенную роль в этом сыграла близость монгольского царства к Китаю.
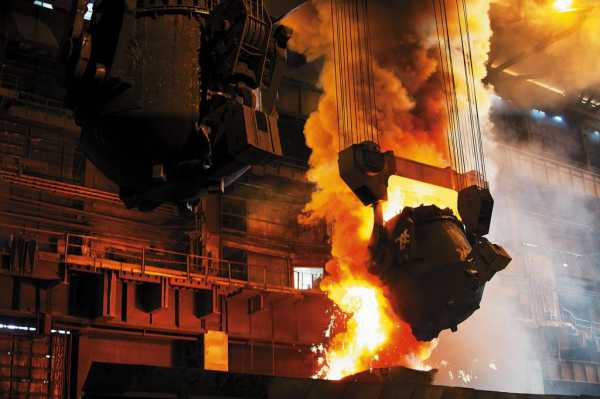
Практически во всех татаро-монгольских городах проживали русичи, которые имели здесь и собственные мастерские, и торговые ряды. Они не только перенимали знания местных мастеров, но и делились своими. После того как Орда пала, технологии продолжили развиваться и совершенствоваться. Уже в XVI веке, при Василии Третьем и Иване Грозном, производство литейного чугуна стало активно применяться в артиллерии, в основном из него изготавливались ядра и небольшие пушки. Тогда же, говорят историки, чугун применялся и в отливке колоколов. Основное производство проходило в таких городах, как Москва и Тула. Стоит отметить, что вплоть до XVII века подобных технологий Европа не знала, а потому заводы России могли активно экспортировать различные орудия и ядра из чугуна в европейские страны.
Активное развитие
Во времена Петровской эпохи началось активное развитие производства чугуна и стали. Царь понимал: увеличение металлургических мощностей приведет Россию к развитию. Для реализации невероятных планов у Петра I было все необходимое: и материалы, и технологии производства. Именно при этом царе началось активное строительство заводов в Сибири, на Урале. За все время правления Петра Великого объемы производства чугуна и стали были увеличены в 770 раз, в России появилось 16 крупных металлургических заводов. Развитие продолжалось и после смерти императора, в конце XVIII века на территории Российской империи находилось более сотни заводов, страна стала мировым лидером в данной сфере. Одновременно с развитием отрасли развивались и отрасли применения металла. Из чугуна теперь изготавливали не только оружие, но и посуду, памятники, ворота и ограды.
Стоит отметить, что отечественные доменные печи, применяемые для производства чугуна, были признаны лучшими в мире. Для них была характерна наибольшая производительность даже при минимальных затратах. В XIX веке литейные были отделены от доменных, что позволило не только специализировать процесс, но и механизировать его. Именно в этот период появились труболитейные предприятия, цеха, производящие отливки ковкого чугуна.
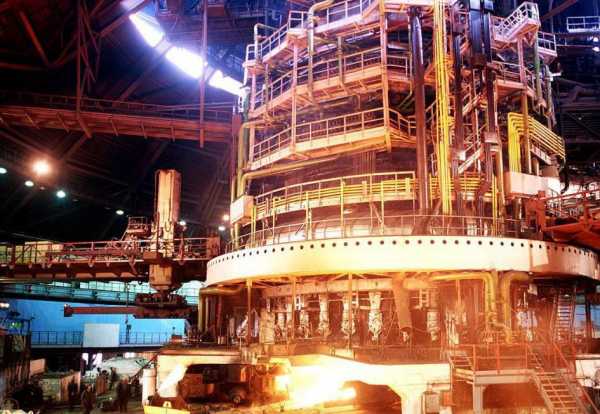
Россия – мировой лидер
В XX веке Россия оборотов не сбавила и осталась лидером по отливке чугуна. В СССР от общего количества литья металлов объемы чугуна составляли порядка 75%.Он был сырьем номер один, его основными потребителями являлись оборонная промышленность и сельское хозяйство. Именно из чугуна специалисты изготавливали детали и различные агрегаты для техники. Стоит отметить, что и сегодня Россия сохраняет лидирующие позиции по объему производства и применения чугуна. Из него делают не только крупногабаритную продукцию, но и такую тонкую работу, как элементы ворот, украшения, печное литье и сувениры!
Производство чугуна: необходимое оборудование
Начнем с определения. Чугуном принято называть сплав железа с углеродом, причем углерода здесь должно быть не менее 2%. Так как же происходит процесс производства чугуна? В первую очередь для этого необходима огромная доменная печь. Ее габариты поражают: высота такой печи составляет 30 м, а внутренний диаметр равен 12 м. Самая широкая часть печи называется распаром, нижняя, через которую в печь попадает горячий воздух, - горн, верхняя – шахта. Кстати, на верхней части находится специальное отверстие – колошник, который закрывается специальным затвором. Принцип работы доменной печи заключается в противотоке: снизу в нее подается воздух, а сверху – материалы. Необходимые для производства чугуна материалы включают в себя флюс (без него не может образоваться шлак), кокс (он необходим для нагрева воды, ее расплавления и восстановления) и руду (которая, собственно, и является основным сырьем).
Для производства также потребуются:
- вагонетки;
- транспортеры;
- бункеры;
- специальный кран и др.
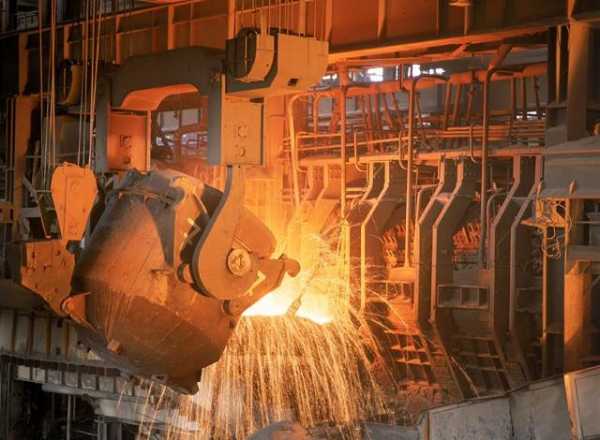
Сырье
Знакомство со сплавами, производством чугуна и стали начинается еще в школе – эта тема предусмотрена в рабочей программе по химии. В учебниках рассматриваются состав железной руды: это само рудное вещество, то есть карбонаты железа, силикаты и окислы, и пустая порода, состоящее из доломита, песчаника, известняка и кварцита. Следует отметить, что в разной руде может присутствовать разное количество рудного вещества. Именно по этому критерию руду разделяют на бедную и богатую. Первая отправляется на обогащение, а вторая может сразу использоваться в производстве.
Для того чтобы произвести тонну чугуна, потребуются: три тонны руды, тонна кокса, двадцать тонн воды. Количество флюса зависит от того, к какому типу относится руда.
Виды железных руд
Прежде чем мы перейдем к знакомству с процессом производства чугуна, предлагаем информацию о видах железных руд. Это может быть:
- Бурый железняк. Для него характерно содержание 25-50% железа в форме так называемых водных окислов. Пустая порода отличается глинистостью.
- Гематит (его еще называют красным железняком). Это безводная окись, содержание вредных примесей здесь минимально. Железа здесь около 45-55%.
- Магнитный железняк. Содержание железа составляет здесь около 30-37%. Пустая порода – кремнеземистая масса.
- Сидерит (второе его название – шпатовый железняк) крайне легко окисляется, переходя при этом в форму бурого известняка.
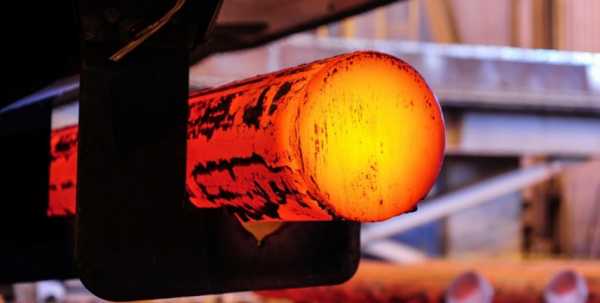
Технология производства
Технология производства чугуна состоит из нескольких этапов. Начинается все с подготовки руды: ее сортируют по химическому составу и, конечно, размеру. Крупное сырье дробят, а мелкие частицы или рудную пыль окусковывают. На этом же этапе происходит и обогащение бедных руд. Кроме того, в процессе подготовки удаляется значительная часть пустой породы, соответственно, содержание железа при этом увеличивается. Следующий этап технологии производства чугуна – подготовка топлива. Начинается все с кокса. В ходе данного этапа кокс подвергается грохочению – из него удаляют всю ненужную мелочь, которая может привести к потере топлива. Следующий этап доменного производства чугуна подготовка флюсов. Плюсы измельчается, из него отсеивают мелочь. После проведения этой процедуры все материалы загружаются в печь. Затем начинается непосредственно доменное производство чугуна: печь заправляют коксом, добавляют агломератор (так называется спеченная с флюсом руда), и снова вносят кокс.
Температуру, необходимую для выплавки, поддерживают с помощью вдувания подогретого воздуха. В процессе сгорания кокса в горне образуется углекислый газ. CO2, проходя через кокс, становится CO. Далее окись углерода восстанавливает основную часть руды. При этом процессе железо становится твердым, переходя в ту часть печи, воздух в которой очень горячий. Здесь железо растворяется углерод внутри себя. Собственно, так и выглядит производство чугуна в доменной печи. Жидкий чугун из печи попадает в специальные ковши, из которых его выливают в предварительно подготовленные формы. Возможно выливание в специальные сборники-смесители, в которых сплав на протяжении некоторого времени будет сохраняться в жидком виде. Одновременно с доменным производством чугуна восстанавливается кремний, марганец и ряд других примесей.
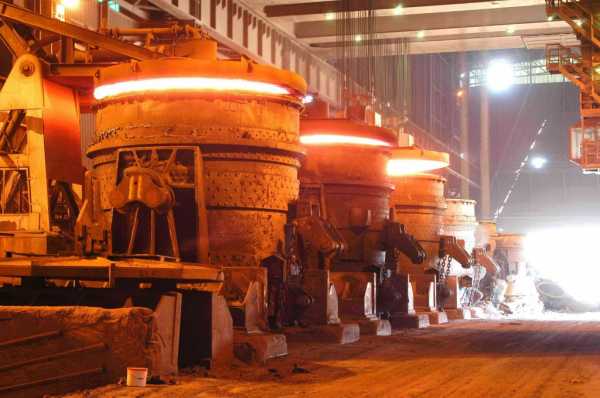
Виды чугуна
Существует всего два вида чугунов: белые и серые. Разница между ними заключается в химическом составе и процессе термической обработки. Так, белые чугуны – результат очень быстрого охлаждения, тогда как серые получаются в результате медленного охлаждения. Для белых характерны такие качества, как хрупкость и твердость. Они крайне тяжело поддаются резке, в ее процессе от них откалываются куски. Потому белые чугуны используются только в качестве заготовок для производства других марок чугуна. Например, в результате обжига данного вида получаются ковкие чугуны. Обратите внимание: название «ковкий» не имеет ничего общего с процессом ковки. По мнению историков, появилось оно из-за того, что прежде из чугуна с такими характеристиками делали подковы. Такой вид активно применяется в сельскохозяйственном машиностроении и в автопромышленности. Главное отличие серых чугунов – пластичность, сочетающаяся с высокой прочностью. Это позволяет использовать их в таких сферах, как станкостроение, сельское хозяйство и автомобильная промышленность, бытовое использование.
Кстати, существуют так называемые половинчатые чугуны. Они имеют промежуточные свойства белых и серых видов. К тому же, регулируя интенсивность охлаждения данного сплава, можно получить разнообразные отливки, которые будут отличаться прочностью, пластичностью и другими свойствами. К чугунам со специальными свойствами относятся:
- антифрикционные, применяемые для изготовления втулок, валов, подшипников;
- износостойкие, необходимые для создания насосного оборудования, различных деталей для азотной промышленности, печного литья;
- жароскойкие, которые используются при изготовлении печного литья, трубокомплексов и газотурбинных двигателей;
- жаропрочные, подходящие для того, чтобы изготовить из них обжиговые печи детали арматуры и котлов;
- стойкие к коррозии, незаменимые для изготовления различных деталей в химической и авиационной промышленности, которые используются в агрессивных средах.
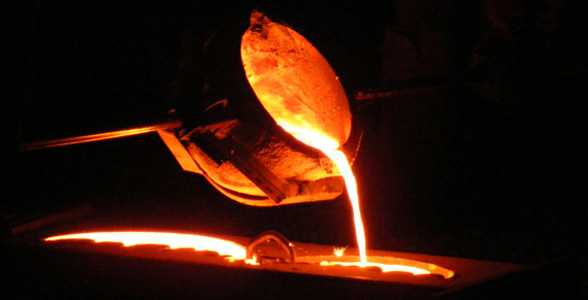
Характеристики чугуна
Для качественного чугуна характерны следующие качества:
- отличная теплоемкость;
- неплохая устойчивость к появлению коррозии;
- повышенная жаростойкость.
Эти и другие характеристики позволяют применять чугун и в быту, и в тяжелой промышленности. Особой популярностью пользуется посуда из чугуна российского производства. Из этого материала изготавливают не только сковороды и кастрюли, встречаются фондю, жаровни, формы для запекания, сотейники и грили.
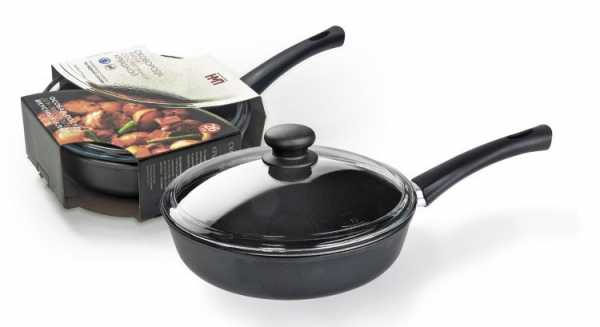
Стоит отметить, что посуда из данного материала одинаково хорошо подходит для жарки блинов, приготовление тушеного мяса, каш, для томления плова. Дело в том, что чугун достаточно медленно нагревается, однако превосходно аккумулирует тепло и равномерно его распределяет. Эксперты говорят: производство посуды из чугуна занимаются разные компании. Все они выпускают изделия примерно одинакового качества. Из всего этого многообразия особо выделяется продукции петербургского завода «Нева». Именно этот завод является одним из крупнейших производителей чугунной посуды на территории Российской Федерации.
fb.ru
Технологии производства чугуна постоянно совершенствуются
Чугун является сплавом железа, содержащим углерод. Его состав может кроме них включать марганцевые, фосфорные, кремниевые, серные и др. компоненты. Изначально материалами для производства чугуна служат железосодержащие руды, топливные материалы, флюсы. Как правило, в виде сырья для производств чугуна применяются железняки, имеющие в составе от 30 до 70% железа и прочих химических веществ в пустой породе, а также вредных серо- и фосфоросодержащих соединений. Топливным материалом для производства чугуна служит кокс, представляющий собой результат сухой, то есть без участия воздуха, переработки каменного коксугля. Применяемые флюсы, чаще всего это кварц, доломит, песчаники и известняки, позволяют снизить температуру расплавления пустой породы, а также привести ее вместе с золой от топлива к шлаку.
Доменное производство чугуна
Наибольшее применение нашел в производстве чугуна доменный процесс. Он включает ряд физических, физико-химических, а также механических проявлений, наблюдаемых в действующей доменной печи. Помещенные в эту печь исходные компоненты (кокс, железосодержащие материалы с флюсами) при прохождении всех операций преобразуются в сплав чугуна, выделяющиеся доменные газы со шлаками. Задача доменного производства чугуна – создание этого сплава из железосодержащих компонентов посредством их переплавления в доменных печах в очень высокой температуре.
Поэтому доменный цех – один из важнейших в структуре завода по производству чугуна. Помимо этого производство чугуна в доменной печи – основа для изготовления стали, прокатных изделий – конечной продукции металлургического цикла других предприятий. Часть чугуна является товарным продуктом, поставляемым в твердом виде в форме небольших слитков (чушек). Их получают на разливочных машинах, установленных в стороне от доменного цеха в специальном разливочном отделении. Другая часть чугуна идет на производство сталей. Газ, получаемый в ходе процесса производства чугуна, используют в мартеновском и коксохимическом производствах в металлургии. Он служит основным топливом нагревательных устройств прокатных цехов, доменных воздухонагревателей.
Чугун выплавляется в печах, куда помещаются, чередуясь слоями, железосодержащие компоненты с флюсами, топливом. От воздействия своей массы они спускаются в низ печи, куда в особые отверстия подается подогретый воздух под определенным давлением. Он поддерживает нужные условия горения загруженного кокса. Технологический процесс производства чугуна предполагает восстановление железа, а также других элементов из их окислов. В процессе восстановления кислород отнимают от окислов и получают из них компоненты или окислы меньшего содержания кислорода.
Одним из ведущих способов производства чугуна считается восстановление железа от действия окиси углерода. Она образуется от сгорания в горне печи природного газа. Еще стоит отметить, что восстановление железа, предусмотренное технологией производства чугуна для данных печей, осуществляется постепенно, в процессе поэтапного извлечения кислорода из окислов. Доменный процесс предполагает, что в процессе восстановления железа участвуют как окиси углерода, так и непосредственно сам твердый углерод.
Определенное количество железа также восстанавливается с помощью водорода. В схеме производства чугуна восстановление железа от действия водорода или окиси углерода считается непрямым (то есть косвенным), а восстановление с помощью твердого углерода называют прямым. На самом деле восстановление железа в данном случае осуществляется двумя стадиями. К моменту достижения железорудным составом зоны распада доменной печи, где установилась температура около 1000°С и больше, окислы железа успевают частично восстановиться непрямым путем в зоне, где действуют менее высокие температуры. В результате их прямого разложения углеродом получается полное восстановление железа.
Производство высокопрочного чугуна
При производстве высокопрочного чугуна большое место отводится науглероживанию железа. Чугун с такими характеристиками образуется, когда восстановленное в доменной печи из рудного материала железо принимает в себя много углерода и прочих элементов. Начало процесса науглероживания железа характеризуется его образованием в губчатом состоянии на участке печи, где действует температура до 500°С. Только что восстановленное железо выступает в качестве катализатора, способствующего распаду окиси углерода на два компонента: двуокись и сажистый углерод. В итоге распада окиси углерода от температуры 550-650°С получаются карбиды железа, прочих металлов. Наделенный особой активностью, сажистый углерод активно вступает в химическое взаимодействие с частицами железа.
При температуре в 1000°С и больше карбид железа распадается на железо с углеродом. С ростом количества углерода температура в процессе плавления становится существенно ниже. Так, чистое железо расплавляется при температуре от 1539°С, а сплав его с углеродом способен плавиться уже от 1147°С. Плавление сплава происходит в зонах доменных печей, где действуют высокие температуры, то есть внизу шахты. Образующийся жидкий сплав и есть чугун. При стекании вниз он, омывая раскаленные части кокса, еще больше науглероживается.
Науглероживание металла завершается ниже уровня шлаковой летки – в металлоприемнике. Здесь на соотношение углерода с металлом оказывает влияние содержание других компонентов. Итоговое наполнение углеродом при производстве серого чугуна, например, может зависеть от стойкости карбидов, которая в большой степени определяется содержащимися в чугуне примесями. Например, примесь марганца способствует науглероживанию металла, так как он входит в состав карбида, растворяющегося в чугуне. Аналогичное действие оказывают ванадий, хром, титан. Кремний с фосфором или сера препятствуют образованию карбидов. Из-за этого ферромарганец и зеркальные чугуны всегда содержат больше углерода, чем чугуны передельные, ферросилиций или полученные в литейном производстве чугуны.
В ходе плавления восстанавливается не только само железо, но и ряд различных элементов, находившихся в рудной массе. В составе шихтовых материалов в печи, помимо окислов железа, поступают еще окислы и отдельные химические элементы, такие как марганец, хром, ванадий, титан, свинец, медь, цинк, мышьяк и др. Они в полностью или частично восстановленном виде вместе с частицами серы попадают в чугун и влияют на его свойства в худшую или в лучшую сторону. В основах производства чугуна считается, что чаще всего ценными примесями служат кремний с марганцем, а вредоносными – сера с фосфором.
Наличие в чугуне серных компонентов можно уменьшить до оптимального предела путем внедоменного обессеривания. Если выдержать чугун с 2% марганца в ковше-чугуновозе или миксере, то некоторый объем серы в различных ее соединениях с марганцем перейдет из состава металла в шлак. Это возможно благодаря уменьшению растворяемости данного соединения в металлах от снижения температуры. Подобное обессеривание в ковше чугуна может достичь 60%. Кроме этого существуют еще методы внедоменного обессеривания чугунов. В производствах чугуна в мире довольно часто в этих целях используют обессеривающие присадки, такие как известь, кальцинированная сода или металлический магний.
Особенности процесса производства чугуна
В процессе плавления в горн с общей смесью стекает расплавленный шлак. Благодаря его плотности, меньшей, чем у чугуна, он всплывает поверх него. Это явление наблюдается в районе распара печи. Первоначальный шлак получается от сплавления находившихся в пустых породах руд, а также флюсах окислов. При стекании вниз, в процессе накапливания шлак значительно меняется по составу. Благодаря реакциям с компонентами не полностью прогоревшего кокса, расплавляющегося чугуна в нем получают восстановление из своих окислов марганец с железом, а кроме того растворяются соединения серы, зола и кокс.
Равномерность работы доменных печей, качественное производство отливок из чугуна с его видом зависят от таких свойств шлака, как плавкость, вязкость, текучесть, температура плавления, серопоглотительная способность. Данные качества шлака продиктованы его химическим наполнением, минералогическими свойствами исходных шихтовых компонентов. Химическое содержание шлака предопределяет итоговый состав чугуна, этим объясняется тот факт, что для производства различных чугунов (литейного, передельного и др.) обычно выбирают шлак с определенными свойствами. Расплавленные шлаки и получаемый чугун поочередно выпускаются в особые отверстия – шлаковую и чугунную летки, сначала шлак, потом чугун.
promplace.ru
Общие сведения о производстве чугуна и стали
Общие сведения о производстве чугуна и стали
Производство чугуна. Сырьем для производства черных металлов является железная руда. Из нее вначале получают чугун, а затем в специальных печах, уменьшая содержание углерода, из чугуна выплавляют сталь.
Для производства чугуна служат доменные печи, которые по принципу действия не отличаются от шахтных печей.
Железные руды представляют собой природную смесь окислов железа, например Ре20з (красный железняк), с горной породой. Задача доменного процесса сводится к тому, чтобы из окислов железа получить чистое железо, т.е. восстановить его. Роль восстановителя выполняет углерод (кокс).
Восстановленное железо в нижних слоях печи вступает во взаимодействие с углеродом, образуя карбид железа — основной химический компонент чугуна.
Одновременно углерод восстанавливает и другие вещества: марганец, кремний, фосфор, серу, -содержащиеся в руде. Карбид железа вместе с этими веществами и представляет собой чугун.
Для понижения температуры плавления пустой породы в печь загружаются флюсы (обычно известняк).
В результате взаимодействия пустой породы с флюсами образуются легкоплавкие соединения (шлаки). Обладая меньшим удельным весом, шлаки располагаются выше жидкого чугуна и по мере накопления удаляются через шлаковую летку, после чего сливают чугун.
В результате доменного процесса получают чугун, шлак и доменный (колошниковый) газ, который используется в качестве топлива на металлургических заводах.
Чугуны в зависимости от свойств и назначения подразделяют на белые и серые. В белых чугунах весь углерод находится в химически связанном состоянии с железом, а в серых — часть углерода находится в свободном состоянии в виде графита.
Рис. 1. Доменная печь: 1 — верхняя часть печи (колошник), 2 — загрузочный аппарат, 3 — газоотводные трубы, 4 — шахта печи, 5 — цилиндрическая часть печи (распор), 6 — нижняя конусная часть печи (заплечики), 7 — горн, 8 — отверстие для выпуска шлака, 9 — отверстие для выпуска чугуна, 10 — кольцевая труба для подачи воздуха
Белые чугуны в основном переплавляются на сталь, поэтому их называют еще передельными — Серые чугуны (или литейные) обладают высокими литейными свойствами и их используют для отливки строительных изделий.
Производство стали. Процесс выплавки стали заключается в уменьшении содержания вредных примесей (серы, фосфора), углерода, кремния и марганца в чугуне.
Рис. 2. Конвертер: 1 — вращающийся грушевидный сосуд, 2 — футеровка, 3 — воздухопровод, 4 — трубки для подачи воздуха в конвертер, 5 — днище конвертера, 6 и 7 — рейка и зубчатое колесо для поворота конвертера
Основным сырьем при производстве сталей служат передельный чугун и стальной лом.
В настоящее время различают три способа производства стали: конвертерный, мартеновский и электроплавильный.
При конвертерном способе производства стали расплавленный чугун продувается сжатым воздухом. При этом кислород взаимодействует, с примесями, окисляет их и переводит в шлак.
Конвертер представляет собой грушевидный сосуд, поворачивающийся вокруг горизонтальной оси для заливки чугуна и выпуска стали. Емкость конвертера достигает 35 г. и более. Качество конвертерной стали уступает мартеновской, так как она содержит пузырьки воздуха, образующиеся при продувке, а также фосфор и серу, повышающие хрупкость стали. Это ограничивает ее применение для конструкций, подвергающихся ударным нагрузкам (подкрановые балки, мосты). Из конвертерной стали готовят прокатные профили, листовую сталь, трубы и др.
Рис. 3. Мартеновская печь: 1 — свод. 2 — под, 3 — отверстия для загрузки печи, 4 — воздушные каналы
В настоящее время благодаря достоинствам конвертерного способа — высокой производительности и низкой стоимости стали — изыскиваются пути повышения качества конвертерной стали с тем, чтобы этот способ стал основным в сталелитейной промышленности. Одним из средств повышения качества конвертерной стали является применение кислородного дутья.
Мартеновский способ отличается от конвертерного выплавкой стали на поду пламенной мартеновской печи. Печь имеет свод, отражающий тепловой поток на материал, расплавляя его. Для получения требуемой температуры в печи сжигают газ. Устройство современной мартеновской печи показано на рис. 3.
Сырьем при мартеновском способе служат чугун и стальной лом. Возможность использовать стальной лом является большим преимуществом мартеновского способа.
В мартеновскую печь последовательно загружают стальной лом, флюсы и чугун. Флюсы и образующаяся при окислении железа FeO вступают в химическую реакцию с вредными примесями и переводят их в шлак, который всплывает, скапливаясь на поверхности стали. В результате взаимодействия с вредными примесями переходит в железо.
В настоящее время достиг, нуты огромные успехи в области сталеварения. Применение кислородного дутья позволило значительно увеличить производительность мартеновских печей.
При мартеновском способе не только используют стальной лом, но и получают высококачественные стали требуемого химического состава и свойств. Эти стали применяются для изготовления наиболее ответственных строительных конструкций ферм, мостов, подкрановых балок, рельсов для железных дорог и т. д.
Электроплавка. Специальные легированные стали высокого качества получают в электрических печах. Наиболее распространены дуговые печи, в которых материалы плавятся за счет тепла электрической дуги, образующейся между электродами и металлом.
Процесс получения стали в электропечах аналогичен мартеновскому способу, но в этом случае нет надобности в топливе и воздухе для его сжигания.
Стоимость электростали значительно выше конвертерной и мартеновской. Это объясняется значительным расходом электроэнергии (на выплавку 1 т стали расходуется до 1000 квт-ч электроэнергии). Однако высокое качество электростали определяет большое будущее этого способа сталеварения.
Читать далее:Битуминозные кровельные и гидроизоляционные материалыАсфальтовые и дегтевые растворы и бетоныДегти и пекиПриродные битумыБитуминозные материалыНеорганические теплоизоляционные материалыОрганические теплоизоляционные материалыАсбестоцементные изделияМатериалы и изделия на основе магнезиальных вяжущих веществИзделия на основе гипса
stroy-server.ru
Производство чугуна: химия и физика
Первичный чугун получают в доменных печах путем восстановления окислов железа в металлическое железо. Условия в этих печах таковы, что железо чрезмерно насыщается углеродом и выходит из домны в виде чугуна. Этот чугун, кроме того, содержит повышенное содержание различных примесей кремния, марганца, фосфора и других.
Принцип производства чугуна практически не изменился с самых древних времен. Древние доменные печи были из глины и производили несколько килограммов чугуна в сутки. Современные доменные печи — самые большие печи в мире — способны производить в сутки до 6000 тонн чугуна.
Чугун производят путем проведения в доменной печи химических реакций железных и марганцевых руд с восстановителями – окисью углерода и атомарным углеродом. Эти восстановители образуются в результате сжигания в печи топлива — кокса, мазута, природного газ и измельченного каменного угля. Кроме железной руды и топлива применяют и другие материалы, в первую очередь, флюсы. Флюсы необходимы для понижения температуры плавления пустой породы железной руды, перевода в шлак серы, фосфора, золы, сжигаемого топлива и образования легкоплавкого жидкотекучего шлака, который удаляется из печи.
Основные материалы для доменной печи
1) Железняки – источник железа.2) Кокс – топливо и восстановитель.3) Известняк – при высокой температуре разлагается в образованием СаО, который действует как флюс и переводит кремнистые пустые породы в шлак CaSiO3.4) Воздух – поддерживает горение кокса с выделением тепла. Удаляет некоторые неметаллические примеси (кремний, мышьяк) в виде летучих оксидов. Окисляет окись железа FeO в руде до Fe2O3, что способствует сохранению железа в руде. Окись железа FeO, основная по природе, реагирует с SiO2 c образованием шлака FeSiO3. Воздух делает руду пористой, что способствует однородному восстановлению железа.
Железные руды
В земной коре содержится около 50 % железа в виде окислов, сульфидов и других соединений – всего около 200 различных минералов. Горные породы, из которых технически возможно и экономически целесообразно извлекать металлы называют рудами.
К железным рудам относят красный, бурый, магнитный и шпатовый железняки. Эти руды содержат много соединений железа, из которых его извлекают, и пустой породы, которая относительно легко отделяется при переработке.
Минералы в железных рудах
Основными рудообразующими минералами железа являются гематит, лимонит и магнентит.
Гематит – красный железняк. Содержит железо в виде безводной окиси железа Fe2O3. Содержание железа в красных железняках составляет 45-65 % при небольшом количестве вредных примесей.
Лимонит – бурый железняк. Содержит железо в форме водных окислов типа nFe2O3×mh3O. В буром железняке – 25-50 % железа.
Магнетит – магнитный железняк. Содержит железо в основном в виде закись-окиси железа Fe3O4, обладающего магнитными свойствами. Магнетиты – самые богатые железные руды – содержат 40-70 % железа.
Подготовка руды для производства чугуна
Для нормальной работы доменной печи она должна загружаться кусковым материалом оптимальных размеров. Слишком крупные куски руды и других материалов не успеют должным образом прореагировать, и часть материала уйдет бесполезно. Слишком мелкие куски слишком плотно прилегают друг к другу, не оставляя необходимых проходов для прохождения газов, что затрудняет работу печи.
Оптимальными считают размер кусков шихты 30-80 мм. Более крупные куски измельчают до оптимального размера.
С другой стороны, при дроблении материалов и при добыче руды наряду с крупными кусками образуется мелочь, также не пригодная к плавке. Такие материалы окусковывают до нужных размеров методами агломерации и скатывания.
Кроме агломерации и скатывания производят обогащение руды. Обогащением называют предварительную обработку руды без изменения химического состава основных минералов и их агрегатного состояния. Обогащение руды производят для повышения содержания в ней железа. При этом из руды удаляется значительная часть пустой породы. При обогащении руд применяют различные методы: промывание руды, метод флотации, гравитационный метод и магнитное обогащение.
Конструкция доменной печи
Доменная печь представляет собой печь шахтного типа. Типичная доменная имеет внизу диаметр 6-8 м и высоту 20-36 м. Самая большая домна, японская, имеет диаметр 14,9 м. Профиль доменной печи и ее температурные зоны показаны на рисунке 1.
Рисунок 1 – Профиль доменной печи. Материалы на входе и выходе.Основные химические реакции
Доменная плавка
Доменная плавка заключается в раздельной загрузке в верхнюю часть печи (колошник) офлюсованного агломерата и кокса. Их располагают в печи слоями. Шихта нагревается за счет тепла горения кокса в горячем воздухе, который вдувается в нижней части домны. Шихта постепенно опускается вниз. В результате физико-химического взаимодействия компонентов шихты и поднимающихся газов в нижней части печи – горне – образуются два несмешивающихся жидких слоя – чугун на лещади горна и шлак – над чугуном.
Жидкий чугун выпускают каждые 2-3 часа, в больших печах – каждый час. Шлак из печи выпускают вместе с чугуном. Их разделяют с помощью специальных затворов.
Доменная печь обычно работает непрерывно в течение нескольких лет — до 10 лет.
Физико-химические процессы в доменной печи
В доменной печи одновременно происходят следующие процессы:
1) горение углерода топлива и образование восстановителей;2) разложение компонентов шихты;3) восстановление окислов;4) науглероживание железа и образование чугуна;5) образование шлака.
Горение топлива и образование восстановителей
Горение углерода топлива происходит в нижней части печи при взаимодействии воздуха при температуре 1000-1300 ºС с коксом:
С + О2 = СО2 .
Образующийся углекислый газ поднимается к раскаленному коксу и взаимодействует с ним по реакции с образованием восстановителя СО:
СО2 + С = 2СО.
Восстановитель СО в присутствии железа разлагается по реакции с образованием атомарного сажистого восстановителя С:
2СО = С + СО2.
Восстановление окислов железа
Главная задача доменного процесса – восстановление железа из его оксидов. Основную роль в восстановлении железа играют окись углерода и атомарный сажистый углерод, которые образуются в результате доменного процесса.
Зоны реакций восстановления и их температуры в доменной печи показаны на рисунке 2.
Рисунок 2 – Схема восстановления окислов железапри производстве чугуна в доменной печи
Восстановление окислов железа идет в следующей последовательности:
Fe2O3 → Fe3O4 → FeO → Fe
Основными реакциями восстановления являются следующие:
Fe2O3 + 3C = 2Fe + CO3Fe2O3 + CO = 2Fe3O4 + CO2Fe3O4 + CO = 3FeO + CO2FeO + CO = Fe +CO2
В восстановлении железа также участвует водород, который образуется из воды, которая содержится в шихте.
Науглероживание железа
Науглероживание железа происходит за счет взаимодействия твердого губчатого железа с углеродом:
3Fe + 2CO = Fe3C + CO2.
Сплав железа с углеродом имеет температуру плавления ниже, чем у чистого железа. В результате этого образуются капли жидкого чугуна, которые стекают на дно горна (лещадь) через слой раскаленного кокса, насыщаясь при этом углеродом.
Образование доменного шлака
Основными реакциями образования шлака являются следующие:
CaCO3 → CaO + CO2CaO + SiO2 = CaSiO3
Побочные реакции восстановления примесей
В результате побочных реакций происходит восстановление примесных элементов – марганца, кремния и фосфора:
MnO2 + 2C = Mn + 2COSiO2 + 2C = Si + 2COCa3(PO4)2 + 3SiO2 = 3CaSiO3 + P2O5P2O5 + 5C + 2P + 5CO
Таким образом, в доменной печи мы получаем своего рода загрязненное примесями железо, то есть чугун, который содержит больших количествах свободный углерод, а также примесные элементы — марганец, кремний и фосфор.
Доменный чугун
Типичный химический состав доменного первичного чугуна:Железо (Fe) = 93,5-95,0%Кремний (Si) = 0,30-0,90%Сера (S) = 0,025-0,050%Марганец (Mn) = 0,55-0,75%Фосфор (P) = 0,03-0,09%Титан (Ti) = 0,02-0,06%Углерод (C) = 4,1-4,4%
Из доменного первичного чугуна выплавляют сталь. Процесс выплавки стали, грубо говоря, заключается в снижении в железе содержания углерода и очистке его от чрезмерного содержания марганца, кремния, фосфора и других примесей.
steel-guide.ru