Можно ли повысить твердость металлов и их сплавов? Сталь 45 твердость 45 hrc
Сталь марки 45
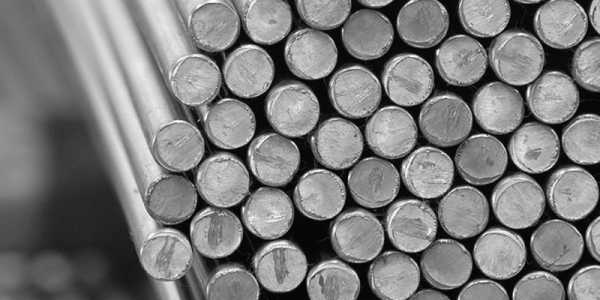
Что такое сталь 45? Сталь 45 — название одной из самых востребованных и популярных марок конструкционных углеродистых сталей. Цифра 45 в названии у данной марки означает процентное содержание углерода в химическом составе. Иными словами, сталь 45 содержит 0,45% углерода на 100% от всего состава. Но если же быть точнее, то процентное содержание углерода в данной марке варьируется в пределах от 0,45% до 0,5%. Естественно, что и другие вещества будут находится в составе этого материала в соответствующих пропорциях.
- железо (Fe) — до 97%;
- углерод (С) — от 0,42% до 0,5%;
- кремний (Si) — от 0,17% до 0,37%;
- хром (Cr) — до 0,25%;
- марганец (Mn) — от 0,5% до 0,8%;
- никель (Ni) – до 0,25%;
- медь (Cu) – до 0,25%;
- фосфор (P) – до 0,035%;
- сера (S) – до 0,04%;
- мышьяк (As) — до 0,08%.
Дело в том, что в своем химическом составе, помимо железа и углерода, сталь 45 содержит и другие примеси, среди которых сера и фосфор. Собственно, фосфор увеличивает хрупкость у материала при низких эксплуатационных температурах (хладноломкость), а также снижает пластичность при высоких значениях температуры. Сера же способствует появлению трещин в материале при высокой температуре. Иначе говоря, в зависимости от содержания в составе двух данных веществ, характеристики этой стали будут серьезно различаться по качеству.
|
Содержание химических веществ |
Маркировка |
|
|
Сера |
Фосфор |
|
Обыкновенного качества |
Не более 0,05% |
«Ст» |
|
Качественные |
Не более 0,035% |
«Сталь» |
|
Высококачественные |
Не более 0,025% |
«А» |
|
Особо высококачественные |
|
Не более 0,02% |
«Ш» |
В соответствии предписанию межгосударственного стандарта ГОСТ 1050-78 качественная углеродистая конструкционная сталь по степени своего раскисления подразделяется на 3 специальные группы, которые маркируются при помощи соответствующих аббревиатур:
- Кипящая сталь — кп;
- Полуспокойная сталь — пс;
- Спокойная — без индекса.
Собственно, марка стали 45 относится к категории спокойных, поэтому в ее обозначении нет дополнительного буквенного индекса. Кроме стали 45 в эту группу спокойных сталей также входят следующие марки: 08, 10, 15, 20, 25, 30, 35, 40, 45, 50, а также стали 55, 58 и 60.
Углеродистые конструкционные стали обычного качества, в свою очередь, имеют точно такое же распределение по степени раскисления. Соответственно, такие марки стали будут иметь аналогичную маркировку буквенными индексами. Однако здесь есть и свои исключения:
Заглавная буква «Г» добавляется к маркировке материала в случае, если содержание массовой доли марганца в стали составляет 0,80%.В данном случае под буквами «Ст» подразумевается сокращение от слова «Сталь». Цифрами же обозначен условный номер марки углеродистой стали, который определяют в зависимости от непосредственного химического состава материала, который может быть следующим:
Марка |
С (углерод) |
Mn (марганец), % |
Si (кремний), % |
S (сера) |
P (фосфор) |
Ст0 |
До 0,023% |
— |
— |
0,070% |
0,060% |
Ст1 |
0,06% - 0,12% |
0,25%-0,50% |
— |
0,045% |
0,55% |
Ст2 |
0,09%-0,15% |
— |
|||
Ст3 |
0,14%-0,22% |
0,30%-0,60% |
0,12%-0,3% |
||
Ст4 |
0,18%-0,27% |
0,40%-0,70% |
|||
Ст5 |
0,28%-0,37% |
0,80%-1,1% |
0,17%-0,35% |
||
Ст6 |
0,38%-0,50% |
0,80%-1,2% |
Несмотря на то, что очень многие потребители, которые не имеют тесного взаимодействия с металлургической отраслью, называют сталь 45 как Ст 45, такое обозначение некорректно! Эту марку углеродистых конструкционных сталей по ГОСТ 1050-88 обозначают как сталь 45.
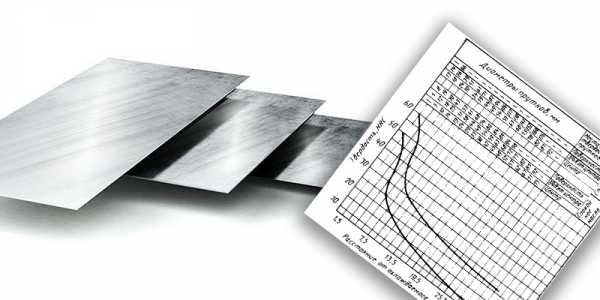
Благодаря наличию в ее составе полезных примесей марганца и кремния, которые понижают внутреннее напряжение, сталь 45 становится менее подверженной образованию трещин. Во многом кремний и марганец влияют также и на эффективность термообработки стали 45. В целом, подобный химический состав из железа, углерода, кремния, хрома, марганца, а также никеля, меди, фосфора, серы и мышьяка обеспечил следующие характеристики стали 45:
Механические свойства стали 45 при t =20°С
Сортамент |
Размер |
sв, МПа |
sT, МПа |
D5, % |
y, % |
Термообработка |
Трубы, ГОСТ 8731-87 |
|
588 |
323 |
14 |
|
|
Пруток калиброванный, ГОСТ 10702-78 |
|
590 |
|
|
40 |
Отжиг |
Прокат, ГОСТ 1050-88 |
До 80 мм. |
600 |
355 |
16 |
40 |
Нормализация |
Прокат нагартованный, ГОСТ 1050-88 |
|
640 |
|
6 |
30 |
|
Прокат отожжен., ГОСТ 1050-88 |
|
|
|
13 |
40 |
|
Лента отожжен., ГОСТ 2284-79 |
|
440-690 |
|
14 |
|
|
Лента нагартованный, ГОСТ 2284-79 |
|
690-1030 |
|
|
|
|
Полоса, ГОСТ 1577-93 |
6 - 60 мм. |
600 |
355 |
16 |
40 |
Нормализация |
Твердость стали 45
Твердость стали 45 |
Трубы ГОСТ 8731-87 |
HB 10-1= 207 МПа |
Прокат горячекатаный ГОСТ 1050-88 |
HB 10-1= 229 МПа |
|
Прокат калиброванный нагартованный ГОСТ 1050-88 |
HB 10-1= 241 МПа |
|
Прокат калиброванный отожженный ГОСТ 1050-88 |
HB 10-1= 207 МПа |
|
Прокат горячекатаный отожженный ГОСТ 1050-88 |
HB 10-1= 197 МПа |
Физические свойства стали 45
T |
E 10- 5 |
a106 |
l |
r |
C |
Градусы |
МПа |
1/Град |
Вт/(м·град) |
кг/м3 |
Дж/(кг·град) |
+20 |
2 |
|
|
7826 |
|
+100 |
2.01 |
11.9 |
48 |
7799 |
473 |
+200 |
1.93 |
12.7 |
47 |
7769 |
494 |
+300 |
1.9 |
13.4 |
44 |
7735 |
515 |
+400 |
1.72 |
14.1 |
41 |
7698 |
536 |
+500 |
|
14.6 |
39 |
7662 |
583 |
+600 |
|
14.9 |
36 |
7625 |
578 |
+700 |
|
15.2 |
31 |
7587 |
611 |
+800 |
|
|
27 |
7595 |
720 |
+900 |
|
|
26 |
|
708 |
Технологические свойства стали 45
Свариваемость |
Трудносвариваемая сталь |
Флокеночувствительность |
Малочувствительная сталь |
Склонность к отпускной хрупкости |
Не склонна |
Расшифровка используемых обозначений
Механические свойства стали 45 : |
|
sв |
- Предел кратковременной прочности , [МПа] |
sT |
- Предел предел текучести для остаточной деформации, [МПа] |
d5 |
- Относительное удлинение при разрыве , [ % ] |
y |
- Относительное сужение , [ % ] |
KCU |
- Ударная вязкость , [ кДж / м2] |
HB |
- Твердость по Бринеллю , [МПа] |
Физические свойства стали 45: |
|
T |
- Температура, при которой получены данные свойства , [Град] |
E |
- Модуль упругости первого рода , [МПа] |
a |
- Коэффициент температурного расширения (диапазон 20°С ) , [1/Град] |
l |
- Коэффициент теплопроводности (теплоемкость материала) , [Вт/(м·град)] |
r |
- Плотность материала , [кг/м3] |
C |
- Удельная теплоемкость материала (диапазон 20°С ), [Дж/(кг·град)] |
R |
- Удельное электросопротивление, [Ом·м] |
Свариваемость |
|
Трудносвариваемая |
Для достижения качественных сварных соединений необходимы дополнительные операции: подогрев до +200-300°С при сварке, а также термообработка стали 45 после сварки, то есть её отжиг |
Таким образом, характеристики стали 45 позволяют использовать ее в условиях достаточно больших температурных перепадов. Поэтому данный материал применяют для изготовления валов, шестерней, а также для коленвалов, распределительных валов, шпинделей, бандажей, цилиндров, кулачков и множества других видов деталей, поверхность у которых может быть термически обработана для повышения прочностных показателей. Цена данного материала невысока, поэтому купить сталь 45 как сырье для производства будет вполне выгодно.
s-agroservis.ru
Cталь 45 механические, технологические, физические свойства, химический состав. Сталь 45 круг стальной пруток,сталь 45 шестигранник,сталь 45 лист стальной
Справочная информация
Характеристика материала сталь 45
Марка стали | сталь 45 |
Заменитель стали | сталь 40Х, сталь 50, сталь 50Г2 |
Классификация стали | Сталь конструкционная углеродистая качественная |
ГП "Стальмаш" поставляет следующие виды металлопроката сталь 45:круг ст 45 ГОСТ 2590-2006 круг (пруток) горячекатаныйкруг ст 45 ГОСТ 7417-75 круг (пруток) калиброванныйкруг ст 45 ГОСТ 14955-77 круг (пруток) со спецотделкой поверхности (серебрянка)шестигранник ст 45 ГОСТ 2879-2006 шестигранник горячекатаныйшестигранник ст 45 ГОСТ 8560-78 шестигранник калиброванныйлист ст 45 ГОСТ 19903-74 прокат листовой горячекатаный | |
Применение стали 45 | вал-шестерни, коленчатые и распределительные валы, шестерни, шпиндели, бандажи, цилиндры, кулачки и другие нормализованные, улучшаемые и подвергаемые поверхностной термообработке детали, от которых требуется повышенная прочность. |
Химический состав в % материала сталь 45
C | Si | Mn | Ni | S | P | Cr | Cu | As |
0.42 - 0.5 | 0.17 - 0.37 | 0.5 - 0.8 | до 0.25 | до 0.04 | до 0.035 | до 0.25 | до 0.25 | до 0.08 |
Температура критических точек материала сталь 45
Ac1 = 730 , Ac3(Acm) = 755 , Ar3(Arcm) = 690 , Ar1 = 780 , Mn = 350 |
Механические свойства при Т=20oС материала сталь 45
Сортамент | Размер | Напр. | sв | sT | d5 | y | KCU | Термообр. |
- | мм | - | МПа | МПа | % | % | кДж / м2 | - |
Лист горячекатан. | 80 | 590 | 18 | Состояние поставки | ||||
Полоса горячекатан. | 6 - 25 | 600 | 16 | 40 | Состояние поставки | |||
Поковки | 100 - 300 | 470 | 245 | 19 | 42 | 390 | Нормализация | |
Поковки | 300 - 500 | 470 | 245 | 17 | 35 | 340 | Нормализация | |
Поковки | 500 - 800 | 470 | 245 | 15 | 30 | 340 | Нормализация |
Твердость материала сталь 45 горячекатанного отожженного , | HB 10 -1 = 170 МПа |
Твердость материала сталь 45 калиброванного нагартованного , | HB 10 -1 = 207 МПа |
Физические свойства материала сталь 45
T | E 10- 5 | a 10 6 | l | r | C | R 10 9 |
Град | МПа | 1/Град | Вт/(м·град) | кг/м3 | Дж/(кг·град) | Ом·м |
20 | 2 | 7826 | ||||
100 | 2.01 | 11.9 | 48 | 7799 | 473 | |
200 | 1.93 | 12.7 | 47 | 7769 | 494 | |
300 | 1.9 | 13.4 | 44 | 7735 | 515 | |
400 | 1.72 | 14.1 | 41 | 7698 | 536 | |
500 | 14.6 | 39 | 7662 | 583 | ||
600 | 14.9 | 36 | 7625 | 578 | ||
700 | 15.2 | 31 | 7587 | 611 | ||
800 | 27 | 7595 | 720 | |||
900 | 26 | 708 | ||||
T | E 10- 5 | a 10 6 | l | r | C | R 10 9 |
Технологические свойства материала сталь 45
Свариваемость: | трудносвариваемая. |
Флокеночувствительность: | малочувствительна. |
Склонность к отпускной хрупкости: | не склонна. |
Зарубежные аналоги материала сталь 45Внимание! Указаны как точные, так и ближайшие аналоги.
США | Германия | Япония | Франция | Англия | Евросоюз | Италия | Бельгия | Испания | Китай | Швеция | Болгария | Венгрия | Польша | Румыния | Чехия | Австрия | Австралия | Швейцария | Юж.Корея | |||||||||||||||||||||||||||||||||||||||||||||||||||||||||||||||||||||
- | DIN,WNr | JIS | AFNOR | BS | EN | UNI | NBN | UNE | GB | SS | BDS | MSZ | PN | STAS | CSN | ONORM | AS | SNV | KS | |||||||||||||||||||||||||||||||||||||||||||||||||||||||||||||||||||||
|
|
|
|
|
|
|
|
|
Обозначения:
Механические свойства : | |
sв | - Предел кратковременной прочности , [МПа] |
sT | - Предел пропорциональности (предел текучести для остаточной деформации), [МПа] |
d5 | - Относительное удлинение при разрыве , [ % ] |
y | - Относительное сужение , [ % ] |
KCU | - Ударная вязкость , [ кДж / м2] |
HB | - Твердость по Бринеллю , [МПа] |
Физические свойства : | |
T | - Температура, при которой получены данные свойства , [Град] |
E | - Модуль упругости первого рода , [МПа] |
a | - Коэффициент температурного (линейного) расширения (диапазон 20o - T ) , [1/Град] |
l | - Коэффициент теплопроводности (теплоемкость материала) , [Вт/(м·град)] |
r | - Плотность материала , [кг/м3] |
C | - Удельная теплоемкость материала (диапазон 20o - T ), [Дж/(кг·град)] |
R | - Удельное электросопротивление, [Ом·м] |
Свариваемость : | |
без ограничений | - сварка производится без подогрева и без последующей термообработки |
ограниченно свариваемая | - сварка возможна при подогреве до 100-120 град. и последующей термообработке |
трудносвариваемая | - для получения качественных сварных соединений требуются дополнительные операции: подогрев до 200-300 град. при сварке, термообработка после сварки - отжиг |
yaruse.ru
Нормализация стали 45: описание процесса, режимы, температура
Термическая обработка – это изменение структуры сплава, стали и цветного металла за счет воздействия большого диапазона температуры, а именно, поэтапное нагревание и охлаждение на определенной скорости. Эта процедура сильно меняет свойство заготовок в лучшую сторону, не меняя химически состав. Иными словами, термообработка – это повышение свойств и характеристик будущих изделий из металла, за определенное время при определенных условиях. Рассмотрим процесс нормализации стали 45.
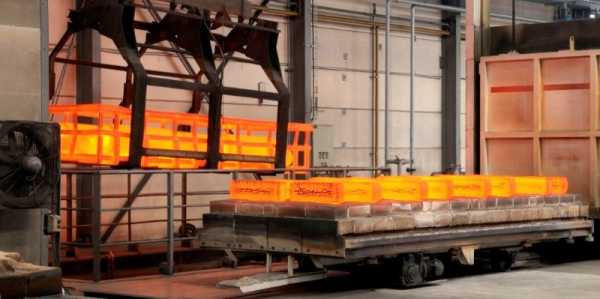
Нормализация стали 45
Особенности нормализация стали марки 45
Сталь этого вида углеродистая конструкционная. Процедура нормализации осуществляется на воздухе, а не в специальной печи, что отлично от других этапов обработки. Сталь 45 быстро и просто поддается специальной механической обработке, например, фрезеровке, точению и сверлению. Из нее производят различные детали: распределительные и коленчатые валы, бандажи, вал-шестерни, шпиндели, кулачки, шестерни и цилиндры.
Что такое нормализация?
Под этим понятием понимается нагрев:
- доэвтектоидной стали более чем Ас3;
- заэвтектоидной стали более чем Аcm на 50 градусов.
После нагрева осуществляется плавное понижение температуры на воздухе. При этом процессе осуществляется перекристаллизация стали, удаляющая крупнозернистую структуру, образовавшуюся при ковке или литье. После охлаждения при достаточно низком уровне температуры улучшается дисперсность смеси за счет распада аустенита на ферритно-цементитную смесь. Нормализовать можно любую сталь, но для определенных видов заготовок она может заменять некоторые стадии термообработки.
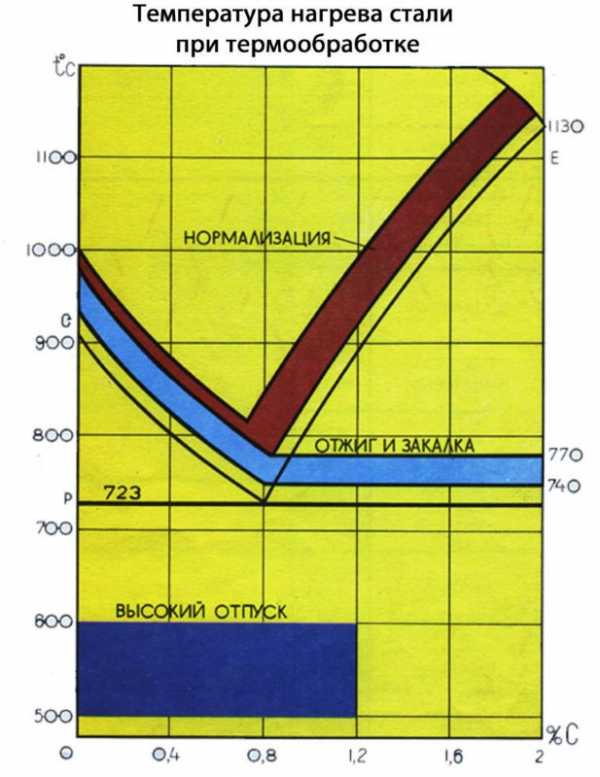
Температура нагрева стали при термообработке
Если производится нормализация стали 45, то эта процедура заменяет высокий отпуск и закалку. При это происходит понижение механических свойств, но за то снижается деформация изделий, чего не скажешь про результат, который получается при закалке. С учетом того, что температура, используемая для нормализации при критической точке Ac3, составляет 770 градусов. За счет этого температура нагревания должна быть не меньше 810 градусов. В таком случае структура аустенита распадается на 100%.
Если понизить температуру до Ar3, то сразу же появятся первые зернышки феррита. Если продолжить понижение до Ar1, то из аустенита выделятся только зерна феррита, а концентрация углерода в остатке будет подниматься, а значит, что при таком же уровне температуры быстро достигнет 0,8%. Если температура нормализации стали 45 еще немного опустится, то начнет выделяться перлит.
Режим нормализации стали 45, подразумевающий медленное нагревание при низких температурах, т.е. ниже линии PSK, не приводит ни к каким превращениям. Если дальше потихоньку нагревать доэвтектоидную сталь, то феррит постепенно растворяется в аустените. Если температура, при которой производится нормализация стали, выше линии GSE, то структура будет представлена только аустенитом.
После нормализации структура среднеуглеродистой стали будет представлена ферритом и перлитом (крупнозернистая смесь цементита и феррита).
Существует несколько стадий обработки будущих изделий:
- отжиг – нагревание до определенной температуры, а после чего медленное охлаждение;
- нормализация – аналог отжига, только охлаждение производится на открытом воздухе;
- закалка – нагревание заготовки до самого высокого уровня температуры, а потом производится быстрое охлаждение;
- отпуск – снижение остатков напряжения, за счет чего снижается твердость и хрупкость металлической заготовки, но увеличивается вязкость;
- старение – после отжига осуществляется повторное нагревание металла до минимальной температуры и последующее медленное остужение.
Инструменты для проведения работы:
- шлифовальная бумага;
- баки с маслом и с водой;
- металлографический микроскоп;
- печь с наличием термоэлектрического пирометра;
- твердомеры по Роквеллу;
- несколько наборов микрошлифов (структура троостит, мартенсит, сорбит, видманштеттовая структура, феррит + мартенсит).
Процедура термообработки
Эта процедура представлена в плавном нагреве деталей, где используется установленная температура, выдержка и затем охлаждение при установленной скорости. Здесь изменяется структура, а значит, механические и технологические показатели будущего изделия.
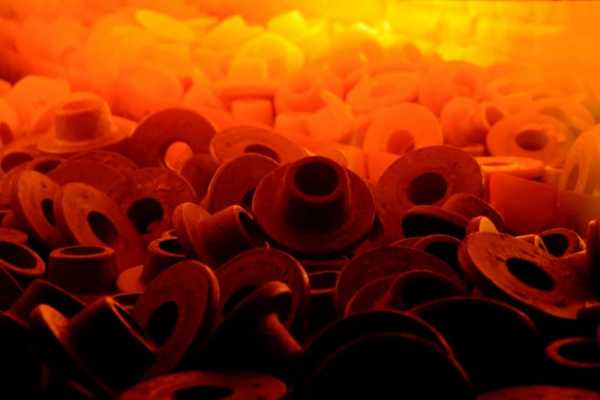
Термообработка стали
Если заготовку охлаждают и нагревают железоуглеродистые сплавы, то начинается превращение при заданном уровне температуры, так называемая критическая точка. Их обычно обозначают Ac1, Ac3, Acm. Все эти изменения при термообработке кристаллизационного характера, а значит, образуются центры зародышей, которые потом постепенно вырастают. Начальная структура каждого вида сталей представлена смесью цементита и феррита.
Характеристика стали 45
Вообще, сталь – это сплав углерода и железа. Сегодня этот материал, за счет своей твердости, пользуется постоянным высоким спросом в различных сферах промышленности. Доля железа в таком сплаве составляет около 45%. Все свойства стадии напрямую зависят от легирующих элементов и содержания углерода, что влияет на будущие изделия для металлопроката. Сталь 45 является самой востребованной маркой. Определенные режимы температурной обработки дают возможность получить прочные изделия. Твердость стали 45 после нормализации напрямую связана с диапазоном температур во время работы.
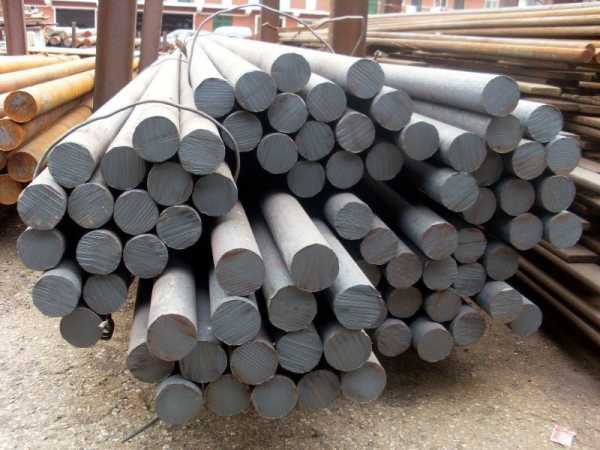
Сталь марки 45
Окончательный режим обработки – это отпуск стали 45. Главной целью этого процесса является снижение закалочных напряжений, чтобы будущая сталь 45, получила твердость, пластичность и прочность. Ее нагревают до предела ниже Ac1, выдерживают, а потом охлаждают на воздухе при заданной скорости. В зависимости от уровня температуры нагрева, данный вид термообработки бывает трех видов:
- Низкий – нагрев 200-250 градусов для получения мартенсита и снятия внутреннего напряжения с сохранением твердости. Сталь используется для режущих и измерительных инструментов.
- Средний – нагрев 350-500 градусов для получения троостита, повышения вязкости и высокой упругости. Его используют для изготовления рессор, пружин и кузнечных штампов.
- Высокий – нагрев 500-600 градусов для получения сорбита, чтобы было лучшее соотношение пластических и прочностных свойств. Она применятся при изготовлении большинства автомобильных деталей, например, шатуны двигателей и оси автомобилей.
Нормализация стали 45 – это основная часть обработки стали. В зависимости от диапазона температуры нагрева используются различные режимы нормализации стали. Здесь производится закалка металла, т.е. улучшение ее свойств и характеристик для дальнейшего их закрепления.
Если вы нашли ошибку, пожалуйста, выделите фрагмент текста и нажмите Ctrl+Enter.
stankiexpert.ru
Влияние термической обработки на твердость сталей 45 и У10
Режим термической обработки | Температура нагрева, 0С | Продолжительность нагрева, мин | Продолжительность выдержки, мин | Охлаждающая среда | HRC | HB | |
Сталь 45 | |||||||
Отжиг Нормализация Закалка Отпуск Отпуск Отпуск | |||||||
Сталь У10 | |||||||
Отжиг Нормализация Закалка Отпуск Отпуск Отпуск | |||||||
Таблица 7.3
Влияние содержания углерода на твердость закаленной
стали
Марка стали | Содержание углерода, % | Твердость | ||
HRB | HRC | HB | ||
У8 У12 | 0,2 0,45 0,8 1,2 |
Содержание отчета
1. Тема и цель работы.
2. Краткие ответы на контрольные вопросы.
3. Область диаграммы состояния сплавов системы Fe – C, относящаяся к сталям с температурными интервалами нагрева сталей под термическую обработку.
4. Режимы отжига, нормализации, закалки и отпуска сталей 45 и У10.
5. Результаты измерения твердости сталей 45 и У8 после различных видов термической обработки в соответствии с заданиями.
6. Выводы.
Лабораторная работа № 8
СТРУКТУРА СТАЛЕЙ В НЕРАВНОВЕСНОМ СОСТОЯНИИ
Цель работы: изучение влияния закалки и отпуска на структуру углеродистых сталей, установление связи между структурой термически обработанных сталей, их диаграммами изотермического распада аустенита и механическими свойствами.
ТЕОРЕТИЧЕСКИЕ СВЕДЕНИЯ
Эксплуатационные свойства стали зависят от ее химического состава и структуры. Желаемое изменение структуры, а, следовательно, и механических свойств, достигается термической обработкой. Различные структуры стали формируются в процессе ее охлаждения из аустенитного состояния.
Незначительная степень переохлаждения или весьма медленное охлаждение обеспечивает получение равновесных структур (лабораторная работа № 7). Чем больше степень переохлаждения аустенита или скорость его охлаждения, тем при более низких температурах происходит превращение аустенита, тем более неравновесная структура получаемой стали. Сталь при этом может приобрести структуры сорбита, троостита, игольчатого троостита (бейнита) илимартенсита.
Закалка, обеспечивающая получение наиболее неравновесной структуры стали – мартенсита, сопровождается возникновением больших внутренних напряжений. Поскольку эти напряжения могут вызвать коробление или разрушение детали, их уменьшают путем отпуска.
Рис. 8.1. Микроструктура закаленной низкоуглеродистой (0,15 % С) стали. Х200
При отпуске из структур закаленной стали образуются структуры отпуска (троостит, сорбит, перлит). Рассмотрим подробнее структуры углеродистых сталей, образующиеся при закалке, а затем при отпуске. Получаемая структура стали зависит не только от скорости охлаждения аустенита, но и от температуры нагрева и химического состава стали.
Низкоуглеродистая сталь, содержащая до 0,15 % углерода, нагретая выше температуры АС3 и закаленная в воде, имеет структуру малоуглеродистого мартенсита (рис. 8.1).
Рис. 8.2. Изменение температурного интервала мартенситного превращения - а (область Мн – Мк заштрихованная, сплошная линия – tкомн) и массовой доли остаточного аустенита – б (возможная доля Аост, заштрихована) от содержания углерода в стали
Мартенсит – это пересыщенный твердый раствор углерода в a-железе. Он содержит столько углерода, сколько было в аустените, т.е. в стали. Мартенсит имеет тетрагональную объемно центрированную решетку. С увеличением содержания углерода тетрагональность кристаллической решетки мартенсита, твердость и прочность закаленной стали возрастают. Он имеет характерное пластинчатое, под микроскопом – игольчатое, строение. Рост пластин мартенсита происходит со скоростью около 1000 м/с по бездиффузионному механизму. Они ориентируются по отношению друг к другу под углом 60 и 120о в соответствии с определенными кристаллографическими плоскостями аустенита пределах аустенитного зерна, и чем выше температура нагрева под закалку и чем, следовательно, крупнее зерно аустенита, то тем более крупноигольчатым и хрупким он будет.
Твердость мартенсита весьма высока, например, для среднеуглеродистой стали – 55...65 HRC, (НВ = 5500...6500 МПа). Превращение аустенита в мартенсит сопровождается увеличением удельного объема стали, поскольку мартенсит имеет больший объем, чем аустенит. В сталях, содержащих более 0,5 % С, не происходит полного превращения аустенита в мартенсит и сохраняется так называемый остаточный аустенит. Чем выше содержание углерода в стали, тем ниже температурный интервал (Мн– Мк) мартенситного превращения (рис. 8.2, а)и больше остаточного аустенита (рис. 8.2, б). При обработке холодом можно достичь температуры Мк и обеспечить переход аустенита остаточного в мартенсит.
В доэвтектоидных сталях, закаленных с оптимальных температур (на 30...50 оС выше АС3), мартенсит имеет мелкоигольчатое строение (рис. 8.3).
Заэвтектоидные стали подвергают неполной закалке (температура нагрева на 30...50 0С превышает АС1). Сталь приобретает структуру мартенсита с равномерно распределенными зернами вторичного цементита и остаточного аустенита (5...10 % Аост.) (рис. 8.4).
После полной закалки заэвтектоидная сталь имеет структуру крупноигольчатого мартенсита и в ней содержится свыше 20 % остаточного аустенита (рис. 8.5) . Такая сталь обладает значительно меньшей твердостью, чем после неполной закалки.
Рис. 8.3. Мартенсит закалки в доэвтектоидной стали. Х600
Рис. 8.4. Микроструктура закаленной заэвтектоидной стали:
мартенсит, аустенит остаточный, зерна цементита вторичного. Х400
Рис. 8.5. Микроструктура перегретой закаленной стали:
мартенсит крупноигольчатый, аустенит остаточный. Х400
Рис. 8.6. Микроструктура троостита закалки:
а – увеличение 500; б – увеличение 7500
Закалка на мартенсит обеспечивается охлаждением углеродистых сталей в воде со скоростью выше критической. При более медленном охлаждении стали из аустенитного состояния, например, в масле со скоростью, меньше критической, аустенит при температурах 400...500 оС распадается на высокодисперсную феррито-цементитную смесь пластинчатого строения, называемую трооститом закалки. Троостит – структура с повышенной травимостью (рис. 8.6, а) и характерным пластинчатым строением (рис. 8.6, б).
Еще более медленное охлаждение стали (например, в струе холодного воздуха) вызывает при температурах 500...650 0С распад аустенита на более грубую, чем троостит, феррито-цементитную смесь также пластинчатого строения, называемую сорбитом закалки. По мере уменьшения скорости охлаждения и перехода от структур мартенсита к трооститу, сорбиту и, наконец, перлиту твердость стали уменьшается.
Рис. 8.7. Микроструктура троостита (а)и сорбита (б) отпуска. Х7500
Сталь с неравновесной мартенситной структурой при нагреве получает равновесную перлитную структуру. При нагреве закаленной стали до температур 150...250 оС (низкий отпуск) образуется структура кубического (отпущенного) мартенсита. Увеличение температуры отпуска (300...400 оС – средний отпуск и 550...650 оС – высокий отпуск) ведет к появлению структуры зернистых трооститаи сорбита отпуска соответственно. Эти структуры показаны на рис. 8.7, а и 8.7, б. Сталь со структурой троостита с твердостью 35...45 HRC (НВ = 3500...4500 МПа) обеспечивает максимальную упругость, необходимую, как правило, при изготовлении рессор, пружин, мембран. Сталь со структурой зернистого сорбита отпуска (25...35 HRC) обладает наилучшим комплексом механических свойств и высокой конструкционной прочностью. Именно поэтому закалку и высокий отпуск называют термическим улучшением.
Нагрев закаленной стали вплоть до температуры АС1 (727 оС) обеспечивает получение равновесной структуры зернистого перлита, т.е. менее дисперсной, чем сорбит и троостит, ферритно-цементитной смеси. Если сталь является доэвтектоидной, в ней обособляются зерна избыточного феррита.
Таким образом, при переохлаждении аустенита по мере увеличения скорости охлаждения образуются перлит, сорбит, троостит пластинчатого строения и мартенсит закалки, а при распаде мартенсита по мере повышения температуры отпуска формируются мартенсит кубический (отпущенный), троостит, сорбит, перлит зернистого строения.
Зернистые структуры, образующиеся при отпуске, характеризуются более высокой пластичностью и ударной вязкостью по сравнению с аналогичными структурами пластинчатого строения.
Порядок выполнения работы
1. Ознакомиться с теоретическими сведениями и в случае необходимости, определяемой преподавателем, сдать теоретический зачет по теме.
2. Вычертить двойную диаграмму состояния железоуглеродистых сплавов, ее участок, соответствующий сталям и нанести на него температурные интервалы нагрева сталей под термическую обработку.
3. Начертить диаграммы изотермического распада аустенита для исследуемых сталей и нанести на них режимы термической обработки (температуры изотермических выдержек, скорости охлаждения).
4. Изучить и зарисовать микроструктуры термообработанных сталей, указать их твердость.
5. Сделать выводы и отчет по работе в соответствии с заданиями.
Контрольные вопросы
1. Что называется мартенситом? Каковы его структура и свойства?
2. Какая фаза называется остаточным аустенитом? Причина появления остаточного аустенита в закаленной стали? Условия, от которых зависит количество остаточного аустенита в структуре закаленных сталей? Влияние остаточного аустенита на свойства закаленных сталей.
3. Оптимальные температуры нагрева под закалку доэвтектоидных и заэвтектоидных сталей. Каковы структура и свойства сталей после закалки?
4. Что называется сорбитом, трооститом закалки, сорбитом и трооститом отпуска? Условия образования этих структур. Каковы их структура и свойства?
5. Что называется низким, средним и высоким отпуском?
Содержание отчета
1. Тема и цель работы.
2. Краткие ответы на контрольные вопросы.
3. Область диаграммы состояния сплавов системы Fe – C, относящаяся к сталям с температурными интервалами нагрева сталей под термическую обработку.
4. Диаграммы изотермического распада аустенита для исследуемых сталей с режимами термической обработки (температуры изотермических выдержек, скорости охлаждения).
5. Результаты микроструктурного анализа сплавов, выполненного в соответствии с заданиями.
6. Выводы.
Лабораторная работа № 9
infopedia.su
параметры прочности, твердости, плотности. Конструкционная сталь 45 и ее характеристики.
Проверенная временем, стойкая конструкционная углеродистая сталь 45 марки очень популярна в современной промышленности. Она идет на изготовление самых разных элементов и узлов агрегатов, для которых твердость материала в HB 10-1 = 170 МПа является оптимальной. Химический состав сплава 45 марки является сбалансированным для получения очень стойкого материал при его низкой себестоимости. Помимо 0,42-0,50% углерода в данном сплаве можно обнаружить:
- Fe – ~97%
- Mn – 0,5-0,8%
- Si – 0,17-0,37%
- Cr – не больше 0,25%
- Cu – не больше 0,25%
- Ni – не больше 0,25%
- As – не больше 0,08%
- S – не больше 0,04%
- P – не больше 0,035%
Физические и механические характеристики
Плотность стали 45, твердость, пределы прочности и другие свойства представлены в следующих таблицах:Выпускается конструкционная качественная углеродистая сталь 45 марки в виде фасонного проката (согласно ГОСТам):
- трубы – ГОСТы 8732-78, 8734-75, 8731-74, 21729-76, 8733-74
- калиброванные прутки – ГОСТы 1050-88, 8560-78, 7417-75, 8559-75
- шлифованные прутки – ГОСТ 14955-77
- тонкие листы – ГОСТ 16523-97
- толстые листы – ГОСТы 19903-74 и 1577-93
- проволока – ГОСТы 5663-79 и 17305-91
- поковки – ГОСТы 1133-71 и 8479-70
- ленты – ГОСТ 2284-79
- полосы – ГОСТы 103-2006, 82-70 и 1577-93
Сталь 45: применение в промышленности
45 марка сплава отлично подходит для выплавки вал-шестерен, распределительных и коленчатых валов, бандажей, шпинделей, цилиндров, кулачков и прочих улучшаемых, нормализованных, подвергаемых поверхностной термообработке деталей, главным требованием к которым является повышенная прочность.
Сталь с 0,45% углерода и незначительным количеством остальных примесей способна демонстрировать относительно высокую твёрдость. Так, для кулачков станочных патронов данный сплав наделяется твёрдостью в Rc=45-50. Для этого производится отпуск сплава при t=220-280° в течение 40 минут. При производстве инструмента – тисков, плоскогубцев, круглогубцев и др. – сталь 45 марки нагревается (закалка) в соляных или свинцовых ваннах. Для дальнейшего отпуска устанавливается температура в 220-320°, а сам процесс занимает не более 30-40 мин. Твёрдость изделий на выходе также достигает Rc=50.Конструкционная улучшенная сталь 45х с повышенным содержанием хрома идет на изготовление шестерней, валов, болтов и осей, которые отличаются повышенной твердостью, прочностью и износостойкостью. При этом такие изделия должны работать в условиях незначительных ударных нагрузок. 45 марка с повышенным содержанием никеля и хрома – сталь 45ХН – идет на производство таких же элементов и узлов, являющихся в агрегатах ответственными деталями.
fx-commodities.ru
показатель высокой прочности и технические характеристики
Сталь — это деформируемый сплав железа (подвергающийся ковке) с углеродом и другими элементами. Ее получают из состава, в котором есть место для чугуна и стального лома, обрабатывают в мартеновских печах, кислородных конвертерах и электрических печках. Если в сплаве железа более 2,14% углерода, тогда это уже чугун.
Классификация стали
На рынке 99% всей стали представлен материал конструкционный в широком смысле. К этой группе относятся стали для возведения строительных сооружений, изготовления деталей машин, упругих элементов, инструментов, а также для особых условий работы, имеющие определенные показатели, например, теплостойкие, нержавеющие и другие.
Главными качествами материала являются:
- Прочность, которая характеризуется способностью к выдерживанию достаточного напряжения.
- Пластичность, эта характеристика позволяет выдерживать деформации без ущерба разрушения как при производстве конструкций, так и в точках перегрузок при их работе.
- Вязкость способствует поглощению работы внешних сил, препятствует распространению трещин.
- Жаропрочность и холодостойкость.
- Упругость и твердость.
Сталь и сплавы классифицируют:
- По составу химическому, структурному.
- По качеству. На данный показатель влияет способ производства и содержание вредных примесей.
- По степени раскисления и затвердеванию металла в изложнице.
- По применению.
Химический состав
В зависимости от содержания углерода делят на группы:
- углерода менее 0,3%С — малоуглеродистые.
- Среднеуглеродистые, когда его от 0,3 до 0,7% С.
- Более 07 %С — высокоуглеродистые.
Чтобы улучшить технологические свойства материала сталь легируют. Что это значит? Кроме обычных примесей в ее состав добавляют в определенных сочетаниях легирующие элементы. Обычно лучшие свойства появляются, когда легируют комплексно.
В легированных сталях классификация происходит благодаря суммарному проценту содержащихся в ней примесей:
- Низколегированные, в которых менее 2,5%.
- Среднелегированные — от 2,5% до 10%.
- Высоколегированные — выше 10%.
Структурный состав
Легированные стали подразделяются на виды по структурному анализу:
- В оттоженном виде — ледебуритный, ферритный, доэвтектоидный, заэвтектоидный, аустенитный.
- В нормализованном виде — аутенитный, мартенситный, перлитный.
Перлитный класс характеризуется низким содержанием легирующих элементов. К нему относятся легированные и углеродистые стали. Мартенситный включает в себя стали с более высоким процентом легирующих веществ. В аутенитный класс входят материалы с высоким значением легирующих элементов.
Содержание примесей
По способу производства и содержании примесей данный материал делится на 4 группы:
- Обыкновенного качества. По химическому составу являются углеродистыми. Они выплавляются посредством кислорода или в мартеновских печах. Данные стали являются недорогими и уступают по своим свойствам другим классам.
- Качественные. По химическому свойству являются углеродистыми или легированными. Так же, как и предыдущий тип, выплавляются в конвертерах или в мартеновских печках, при этом соблюдаются более строгие требования к составу шихты, работам по плавке и разливке.
- Высококачественные. Данный тип выплавляется, как правило, в электрических печах. Очень высокого качества сталь изготавливается благодаря электропечам с электрошлаковым переплавом. Применяются также другие совершенные методы, направленные на повышение чистоты по неметаллическим включениям (сера и фосфор).
- Благодаря электрошлаковому переплаву, который эффективно очищает от сульфидов и оксидов, создаются особовысококачественные стали. Такие стали бывают только легированными. Они проходят обработку в электропечах, к ним применяются специальные методы электрометаллургии.
Применение
Шарикоподшипниковые хромистые стали применяются для изготовления подшипников. Этот вид зарекомендовал себя, как высокопрочный, твердый и контактно-выносливый материал.
Упругой деформацией обладают некоторые виды стали, поэтому они применяются для пружин, рессор и других изделий. Многие из них должны выдерживать циклические нагрузки. Поэтому основными требованиями к данным видам стали являются высокие значения упругости, текучести, выносливости, также необходима пластичность и сопротивление хрупкому разрушению.
Высокопрочные стали обладают прочностью при необходимой пластичности, малой чувствительностью к надрезам, низким порогам хладноломкости, отличной свариваемостью, высоким показателям сопротивления хрупкому разрушению.
Сталь 45
Этот сплав стали отличается от других набором особых характеристик, которые присущи только этой марке. Она отличается применением и высокой функциональностью, уникальным составом химических соединений, совокупностью литейных и других производственных параметров.
Применение
Сталь под номером 45 изготавливается в соответствии со всеми требованиями ГОСТа. Из нее делают валы всех видов, бандажи, шпиндели, цилиндры различных видов, кулачки разнообразной формы. По сути, применяется для конструкций и устройств, функциональным назначением которых является устойчивость к огромным нагрузкам, где требуется демонстрировать повышенные показатели износостойкости, прочности, нечувствительности к коррозии.
В составе стали марки 45 в соответствии с ГОСТ находятся такие элементы, как фосфор, мышьяк, медь, никель, марганец и другие вещества. Данная сталь обладает большим набором механических характеристик. Поэтому она способна вынести практически все климатические и температурные колебания. Испытывают данный вид стали при температурном интервале от 200 до 600 градусов.
Технические характеристики
Данная сталь относится к тем материалам, которые трудно поддаются сварке, однако, при этом у нее отсутствует отпускная способность. Эта ее особенность часто очень хорошо влияет на изготовление сложных форм и деталей. Благодаря характеристикам данной стали, ударная вязкость изделий из нее всецело зависит от толщины взятого листа, причем наибольшим значением будет обладать самый толстый исходник. Но, даже несмотря на данный параметр, можно с уверенностью сказать, что практически любая конструкция, изготовленная из стали этой марки, выдержит практически любые, в том числе и самые интенсивные воздействия.
Это стало возможным благодаря применяемым способам обработки, а также производственному процессу, который разработан в соответствии с ГОСТ. Безусловно, в мире еще не создали материалы, обладающие бесконечной выносливостью к различным воздействиям, поэтому данный металл в этом смысле не исключение. Но благодаря высоким свойствам сырья, из которых производят материал, у него великолепные показатели.
Оцените статью: Поделитесь с друзьями!stanok.guru
Руководство как повысить твердость стали и цветных металлов
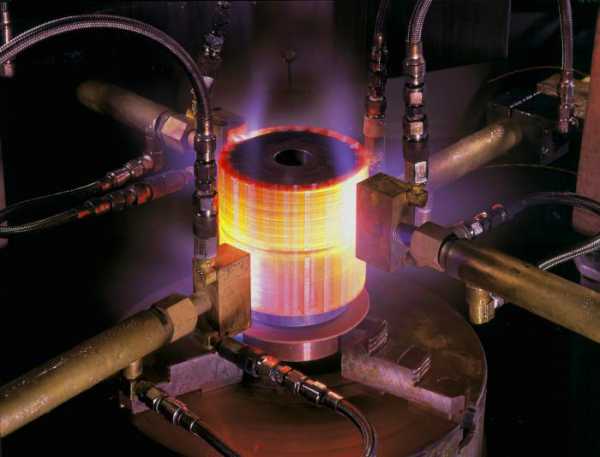
Технологии придания большей твердости металлам и сплавам совершенствовались в течение долгих веков. Современное оборудование позволяет проводить термическую обработку таким образом, чтобы значительно улучшать свойства изделий даже из недорогих материалов.
Закалка стали и сплавов
Закалка (мартенситное превращение) — основной способ придания большей твердости сталям. В этом процессе изделие нагревают до такой температуры, что железо меняет кристаллическую решетку и может дополнительно насытиться углеродом. После выдержки в течение определенного времени, сталь охлаждают. Это нужно сделать с большой скоростью, чтобы не допустить образования промежуточных форм железа.В результате быстрого превращения получается перенасыщенный углеродом твердый раствор с искаженной кристаллической структурой. Оба эти фактора отвечают за его высокую твердость (до HRC 65) и хрупкость.Большинство углеродистых и инструментальных сталей при закаливании нагревают до температуры от 800 до 900С, а вот быстрорежущие стали Р9 и Р18 калятся при 1200-1300С.
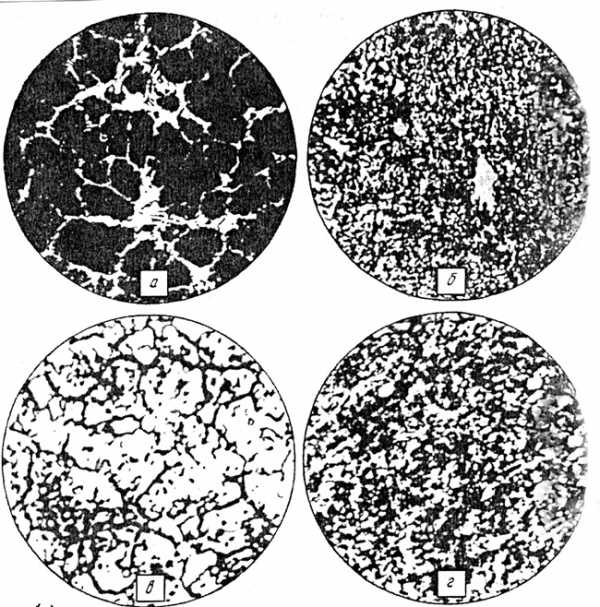
Микроструктура быстрорежущей стали Р6М5: а) литое состояние; б) после ковки и отжига;в) после закалки; г) после отпуска. ×500.
Режимы закалки
- Закалка в одной среде
Нагретое изделие опускают в охлаждающую среду, где оно остается до полного остывания Это самый простой по исполнению метод закалки, но его можно применять только для сталей с небольшим (до 0,8%) содержанием углерода либо для деталей простой формы. Эти ограничения связаны с термическими напряжениями, которые возникают при быстром охлаждении — детали сложной формы могут покоробиться или даже получить трещины.
- Ступенчатая закалка
При таком способе закалки изделие охлаждают до 250-300С в соляном растворе с выдержкой 2-3 минуты для снятия термических напряжений, а затем завершают охлаждение на воздухе. Это позволяет не допускать появления трещин или коробления деталей. Минус этого метода в сравнительно небольшой скорости охлаждения, поэтому его применяют для мелких (до 10 мм в поперечнике) деталей из углеродистых или более крупных — из легированных сталей, для которых скорость закалки не столь критична.
- Закалка в двух средах
Начинается быстрым охлаждением в воде и завершается медленным — в масле. Обычно такую закалку используют для изделий из инструментальных сталей. Основная сложность заключается в расчете времени охлаждения в первой среде.
- Поверхностная закалка (лазерная, токами высокой частоты)
Применяется для деталей, которые должны быть твердыми на поверхности, но иметь при этом вязкую сердцевину, например, зубья шестеренок. При поверхностной закалке внешний слой металла разогревается до закритических значений, а затем охлаждается либо в процессе теплоотвода (при лазерной закалке), либо жидкостью, циркулирующей в специальном контуре индуктора (при закалке током высокой частоты)
Отпуск
Закаленная сталь становится чрезмерно хрупкой, что является главным недостатком этого метода упрочнения. Для нормализации конструкционных свойств производят отпуск — нагрев до температуры ниже фазового превращения, выдержку и медленное охлаждение. При отпуске происходит частичная «отмена» закалки, сталь становится чуть менее твердой, но более пластичной. Различают низкий (150-200С, для инструмента и деталей с повышенной износостойкостью), средний (300-400С, для рессор) и высокий (550-650, для высоконагруженных деталей) отпуск.
Таблица температур закалки и отпуска сталей
№ п/п | Марка стали | Твёрдость (HRCэ) | Температ. закалки, град.С | Температ. отпуска, град.С | Температ. зак. ТВЧ, град.С | Температ. цемент., град.С | Температ. отжига, град.С | Закал. среда | Прим. |
1 | 2 | 3 | 4 | 5 | 6 | 7 | 8 | 9 | 10 |
1 | Сталь 20 | 57…63 | 790…820 | 160…200 | 920…950 | Вода | |||
2 | Сталь 35 | 30…34 | 830…840 | 490…510 | Вода | ||||
33…35 | 450…500 | ||||||||
42…48 | 180…200 | 860…880 | |||||||
3 | Сталь 45 | 20…25 | 820…840 | 550…600 | Вода | ||||
20…28 | 550…580 | ||||||||
24…28 | 500…550 | ||||||||
30…34 | 490…520 | ||||||||
42…51 | 180…220 | Сеч. до 40 мм | |||||||
49…57 | 200…220 | 840…880 | |||||||
<= 22 | 780…820 | С печью | |||||||
4 | Сталь 65Г | 28…33 | 790…810 | 550…580 | Масло | Сеч. до 60 мм | |||
43…49 | 340…380 | Сеч. до 10 мм (пружины) | |||||||
55…61 | 160…220 | Сеч. до 30 мм | |||||||
5 | Сталь 20Х | 57…63 | 800…820 | 160…200 | 900…950 | Масло | |||
59…63 | 180…220 | 850…870 | 900…950 | Водный раствор | 0,2…0,7% поли-акриланида | ||||
«— | 840…860 | ||||||||
6 | Сталь 40Х | 24…28 | 840…860 | 500…550 | Масло | ||||
30…34 | 490…520 | ||||||||
47…51 | 180…200 | Сеч. до 30 мм | |||||||
47…57 | 860…900 | Водный раствор | 0,2…0,7% поли-акриланида | ||||||
48…54 | Азотирование | ||||||||
<= 22 | 840…860 | ||||||||
7 | Сталь 50Х | 25…32 | 830…850 | 550…620 | Масло | Сеч. до 100 мм | |||
49…55 | 180…200 | Сеч. до 45 мм | |||||||
53…59 | 180…200 | 880…900 | Водный раствор | 0,2…0,7% поли-акриланида | |||||
< 20 | 860…880 | ||||||||
8 | Сталь 12ХН3А | 57…63 | 780…800 | 180…200 | 900…920 | Масло | |||
50…63 | 180…200 | 850…870 | Водный раствор | 0,2…0,7% поли-акриланида | |||||
<= 22 | 840…870 | С печью до 550…650 | |||||||
9 | Сталь 38Х2МЮА | 23…29 | 930…950 | 650…670 | Масло | Сеч. до 100 мм | |||
<= 22 | 650…670 | Нормализация 930…970 | |||||||
HV > 670 | Азотирование | ||||||||
10 | Сталь 7ХГ2ВМ | <= 25 | 770…790 | С печью до 550 | |||||
28…30 | 860…875 | 560…580 | Воздух | Сеч. до 200 мм | |||||
58…61 | 210…230 | Сеч. до 120 мм | |||||||
11 | Сталь 60С2А | <= 22 | 840…860 | С печью | |||||
44…51 | 850…870 | 420…480 | Масло | Сеч. до 20 мм | |||||
12 | Сталь 35ХГС | <= 22 | 880…900 | С печью до 500…650 | |||||
50…53 | 870…890 | 180…200 | Масло | ||||||
13 | Сталь 50ХФА | 25…33 | 850…880 | 580…600 | Масло | ||||
51…56 | 850…870 | 180…200 | Сеч. до 30 мм | ||||||
53…59 | 180…220 | 880…940 | Водный раствор | 0,2…0,7% поли-акриланида | |||||
14 | Сталь ШХ15 | <= 18 | 790…810 | С печью до 600 | |||||
59…63 | 840…850 | 160…180 | Масло | Сеч. до 20 мм | |||||
51…57 | 300…400 | ||||||||
42…51 | 400…500 | ||||||||
15 | Сталь У7, У7А | НВ <= 187 | 740…760 | С печью до 600 | |||||
44…51 | 800…830 | 300…400 | Вода до 250, масло | Сеч. до 18 мм | |||||
55…61 | 200…300 | ||||||||
61…64 | 160…200 | ||||||||
61…64 | 160…200 | Масло | Сеч. до 5 мм | ||||||
16 | Сталь У8, У8А | НВ <= 187 | 740…760 | С печью до 600 | |||||
37…46 | 790…820 | 400…500 | Вода до 250, масло | Сеч. до 60 мм | |||||
61…65 | 160…200 | ||||||||
61…65 | 160…200 | Масло | Сеч. до 8 мм | ||||||
61…65 | 160…180 | 880…900 | Водный раствор | 0,2…0,7% поли-акриланида | |||||
17 | Сталь У10, У10А | НВ <= 197 | 750…770 | ||||||
40…48 | 770…800 | 400…500 | Вода до 250, масло | Сеч. до 60 мм | |||||
50…63 | 160…200 | ||||||||
61…65 | 160…200 | Масло | Сеч. до 8 мм | ||||||
59…65 | 160…180 | 880…900 | Водный раствор | 0,2…0,7% поли-акриланида | |||||
18 | Сталь 9ХС | <= 24 | 790…810 | С печью до 600 | |||||
45…55 | 860…880 | 450…500 | Масло | Сеч. до 30 мм | |||||
40…48 | 500…600 | ||||||||
59…63 | 180…240 | Сеч. до 40 мм | |||||||
19 | Сталь ХВГ | <= 25 | 780…800 | С печью до 650 | |||||
59…63 | 820…850 | 180…220 | Масло | Сеч. до 60 мм | |||||
36…47 | 500…600 | ||||||||
55…57 | 280…340 | Сеч. до 70 мм | |||||||
20 | Сталь Х12М | 61…63 | 1000…1030 | 190…210 | Масло | Сеч. до 140 мм | |||
57…58 | 320…350 | ||||||||
21 | Сталь Р6М5 | 18…23 | 800…830 | С печью до 600 | |||||
64…66 | 1210…1230 | 560…570 3-х кратн. | Масло, воздух | В масле до 300…450 град., воздух до 20 | |||||
26…29 | 780…800 | Выдержка 2…3 часа, воздух | |||||||
22 | Сталь Р18 | 18…26 | 860…880 | С печью до 600 | |||||
62…65 | 1260…1280 | 560…570 3-х кратн. | Масло, воздух | В масле до 150…200 град., воздух до 20 | |||||
23 | Пружин. сталь Кл. II | 250…320 | После холодной навивки пружин 30-ть минут | ||||||
24 | Сталь 5ХНМ, 5ХНВ | >= 57 | 840…860 | 460…520 | Масло | Сеч. до 100 мм | |||
42…46 | Сеч. 100..200 мм | ||||||||
39…43 | Сеч. 200..300 мм | ||||||||
37…42 | Сеч. 300..500 мм | ||||||||
НV >= 450 | Азотирование. Сеч. св. 70 мм | ||||||||
25 | Сталь 30ХГСА | 19…27 | 890…910 | 660…680 | Масло | ||||
27…34 | 580…600 | ||||||||
34…39 | 500…540 | ||||||||
«— | 770…790 | С печью до 650 | |||||||
26 | Сталь 12Х18Н9Т | <= 18 | 1100…1150 | Вода | |||||
27 | Сталь 40ХН2МА, 40ХН2ВА | 30…36 | 840…860 | 600…650 | Масло | ||||
34…39 | 550…600 | ||||||||
28 | Сталь ЭИ961Ш | 27…33 | 1000…1010 | 660…690 | Масло | 13Х11Н2В2НФ | |||
34…39 | 560…590 | При t>6 мм вода | |||||||
29 | Сталь 20Х13 | 27…35 | 1050 | 550…600 | Воздух | ||||
43,5…50,5 | 200 | ||||||||
30 | Сталь 40Х13 | 49,5…56 | 1000…1050 | 200…300 | Масло |
Термообработка цветных металлов
Сплавы на основе других металлов не отвечают на закалку столь же ярко, как стали, но их твердость тоже можно повысить термообработкой. Обычно используют сочетание закалки и предварительного отжига (нагрева выше точки фазового превращения с медленным охлаждением).
- Бронзы (сплавы меди) подвергают отжигу при температуре чуть ниже температуры плавления, а потом закалке с охлаждением водой. Температура закалки от 750 до 950С в зависимости от состава сплава. Отпуск при 200-400С производят в течение 2-4 часов. Наибольшие показатели твердости, до HV300 (около HRC 34) можно при этом получить для изделий из бериллиевых бронз.
- Твердость серебра можно повысить отжигом до температуры, близкой к температуре плавления (тусклый красный цвет) с последующей закалкой.
- Различные сплавы никеля подвергают отжигу при 700-1185С, такой широкий диапазон определяется разнообразием их составов. Для охлаждения используют соляные растворы, частички которых потом удаляют водой либо защитные газы, препятствующие окислению (сухой азот, сухой водород).
Металл | Температураотжига, C° | Охлаждающая среда |
МедьЛатунь Л96Латунь Л90-Л62МельхиорНейзильберСереброАлюминийДюралюминий | 500 — 600540 — 600600 — 700650 — 700700 — 750650 — 700300 — 350360 — 380 | ВодаНа открытом воздухеНа открытом воздухеВодаВодаВодаНа открытом воздухеОхлаждение в печи |
Оборудование и материалы
Для нагрева металла при термообработке используются 4 основных типа печей:— соляная электродная ванна— камерная печь— печь непрерывного горения— вакуумная печь
В качестве закалочных сред, в которых происходит охлаждение, используются жидкости (вода, минеральное масло, специальные водополимеры (Термат), растворы солей), воздух и газы (азот, аргон) и даже легкоплавкие металлы. Сам агрегат, где происходит охлаждение, называется закалочная ванна и представляет собой емкость, в которой происходит ламинарное перемешивание жидкости. Важной характеристикой закалочной ванны является качество удаления паровой рубашки.
Старение и другие методы повышения твердости
Старение — еще один вид термообработки, позволяющий повысить твердость сплавов алюминия, магния, титана, никеля и некоторых нержавеющих сталей, которые подвергают предварительной закалке без полиморфного превращения. В процессе старения увеличиваются твердость и прочность, а пластичность понижается.
- Сплавы алюминия, например, дуралюмины (4-5% меди) и сплавы с добавлением никеля и железа выдерживают в пределах часа при температуре 100-180С
- Сплавы никеля подвергают старению в 2-3 этапа, что в сумме занимает от 6 до 30 часов при температурах от 595 до 845С. Некоторые сплавы подвергают предварительной закалке при 790-1220С. Детали из никелевых сплавов помещают в дополнительный контейнеры, чтобы предохранить от контакта с воздухом. Для нагрева используют электрические печи, для мелких деталей могут применяться соляные электродные ванны.
- Мартенситно-стареющие стали (высоколегированные безуглеродистые сплавы железа) стареют около 3 часов при 480-500С после предварительного отжига при 820С
Химико-термическая обработка — насыщение поверхностного слоя легирующими элементами,
- неметаллическими: углеродом (цементация) и азотом (азотирование) применяются для повышения износостойкости колен, валов, шестерней из низкоуглеродистых сталей
- металлическими: например, кремнием (силицирование) и хромом помогает повысить износо- и коррозионную стойкость деталей
Цементирование и азотирование производят в шахтных электропечах. Существуют также универсальные агрегаты, позволяющие проводить весь спектр работ по термохимической обработке стальных изделий.
Обработка давлением (наклеп) — увеличение твердости в результате пластической деформации при относительно низких температурах. Таким образом происходит упрочнение низкоуглеродистых сталей при холодной объемной штамповке, а также чистых меди и алюминия.
В процессе термической обработки изделия из стали могут претерпевать поразительные превращения, приобретая износостойкость и твердость, в разы большую чем у исходного материала. Диапазон изменения твердости сплавов из цветных металлов при термической обработке гораздо меньше, но их уникальные свойства зачастую и не требуют масштабного улучшения.
www.m-deer.ru