Большая Энциклопедия Нефти и Газа. Стержни керамические
Способы изготовления керамических стержней - Производство точных отливок
Категория:
Производство точных отливок
Способы изготовления керамических стержнейКерамические стержни изготовляют различными способами, например сухим или полусухим прессованием, прессованием под высоким давлением, прессованием под максимально высоким-давлением и при большой скорости (прессование взрывом), изостатическим прессованием, изостатическим горячим прессованием, литьем, центробежным литьем, вибрационным уплотнением, шприцеванием под давлением (запрессовкой) и в некоторых случаях (при изготовлении трубочек из кварцевого стекла) вытяжкой.
Согласно литературным данным керамические стержни изготовляют почти всеми способами, которые используются для изготовления керамики в других отраслях промышленности (выдавливанием, трамбовкой, литьем и т. п.).
Выбор технологии изготовления стержней определяется главным образом формой стержней и их требуемым количеством.
Изготовление стержней надувкой, или выстреливанием. В работе приведена смесь для изготовления-стержней, состоящая из кварцевого песка и жидкого силиката натрия. Сначала стержни отверждают углекислым газом, затем отвержденные стержни пропитывают гидролизованным раствором этилсиликата 40 в спиртовой среде и окончательно высушивают. Согласно данным другого источника стержни изготовляют подобным способом, но вместо кварцевого песка используют цирконовый.
Надувкой, или выстреливанием, можно изготовлять мелкие стержни простой формы с низкой размерной точностью.
Изготовление стержней запрессовкой. Состав для стержней состоит из молотого огнеупорного материала и пластических связующих. Смесь размешивается в смесителе с подогревом при помощи паровой рубашки. После охлаждения отвердевшую массу измельчают, вакуумируют и выдавливают шприц-машиной. После охлаждения массу разламывают на гранулы, пригодные для заполнения запрессовывающих станков. Запрессованные гранулы некоторое время охлаждаются в пресс-форме, после чего стержень отправляют на тепловую обработку для удаления из них пластификаторов. Стержень медленно с тщательным соблюдением режима нагревают до температуры около 320 °С в течение трех суток в зависимости от величины и формы изделия. Огнеупорная смесь при этом способе изготовления имеет частицы величиной максимум 0,1 мкм. Органическое связующее, точнее, пластификатор, имеет точку плавления до 200 °С при давлении пара 133 Па (1 торр). Пластификаторами могут быть нафталин, камфара или парадихлорбензен, которые применяют в количестве jg_32%. После удаления этого связующего стержни при необходимости обрабатывают, зачищают и обжигают при соответствующей температуре в зависимости от состава смеси (обычно при 1200 °С). После обжига стержни шлифуют и полируют.
Запрессовкой можно получать и тонкостенные стержни со стенками толщиной 0,2—9,5 мм независимо от сложности формы. Производительность от 20 до 200 запрессовок.
Так как стержни после запрессовки не всегда прочные, то их прокаливают в профилированных сушителях или укладывают на песчаную постель, например из корунда. Последним способом изготовляют стержни в научно-исследовательском институте керамических смесей (Градец Краловы) с точностью ±1%. Стержни с узкими размерными допусками получают обработкой предварительно или окончательно обожженных стержней. Шлифованием добиваются размерной точности в пределах до 0,02 мм с чистотой поверхности 1—1,2 мкм.
Изготовление стержней прессованием. Сухие или полусухие смеси прессуют чаще всего на обычных прессах или прессах с изо-статическим прессованием при давлении 20—150 МПа. Формы изготовляют из спеченных карбидов вольфрама. Стержневую прессуемую смесь, которая состоит из огнеупорной составляющей связующего и смазки, засыпают в пресс-форму в виде гранул. В качестве связующего и смазки используют воски, поливиниловый спирт, стеарины, полиэтиленпарафин, декстрины и т. п. Сухое прессование считается (по данным технической температуры) наиболее эффективным и производительным способом формообразования огнеупорных материалов. Полусухое прессование отличается от сухого тем, что прессуемая смесь содержит 5— 25% жидкости; давление запрессовки в пределах 3,5—17,5 МПа. Такое относительно низкое давление позволяет использовать пресс-формы из закаленной стали. Процесс прессования полусухих масс легко механизируется.
При изостатичесром прессовании давление равномерно распределено на все части прессуемых стержневых смесей. Поэтому пресс-формы можно изготовлять из эластичных материалов, например резины. Этот способ изготовления стержней еще только развивается и его трудно механизировать.
Для получения окончательной формы стержни обычно обрабатывают. Температуру обжига стержней принимают в зависимости от состава стержневой смеси, требований к стержням в пределах 850—1780 °С. Чтобы при обжиге не происходило больших объемных изменений и чтобы стержни легко удалялись из отливок выщелачиванием, их обжигают при температуре 1200—1250° С 135]. Последующую отработку, например полирование, обычно производят после предварительного спекания. Сухое прессование позволяет получать без дополнительной обработки цилиндрике стерженьки диаметром 1,3—4,0 мм с размерной точностью —0,025 мм. К сожалению, этот способ пригоден только для стержней простой формы. Более сложные стержни можно изготовлять обработкой предварительно обожженных стержневых заготовок. При прессовании полусухих смесей точность стержней ниже.
Изготовление стержней литьем. Суспензии огнеупорных материалов в воде смешивают с веществами, увеличивающими жидко-подвижность суспензии и позволяющими заливать их в гипсовые формы. Эти вещества — жидкое стекло, ортофосфаты, хлорид алюминия и т. п. Требуемая величина рН выдерживается при помощи соляной кислоты или кислого углекислого аммония. Этот способ изготовления стержней запатентован как способ RAM. Смесь (консистенции глины для гончарного круга) вводится в стержневые гипсовые ящики и периодически подпрессовывается. Стержневые гипсовые ящики вставляют в стальные обечайки и выполняют в них отверстия вставленными хлопчатобумажными пробками. При прессовании выдавливаемая из стержневой массы вода через эти пробки удаляется наружу и обезвоженная стержневая смесь затвердевает в гипсовом стержневом ящике.
Таким способом экономически целесообразно изготовлять лишь простые стержни. Для сложных стержней требуются дорогие стержневые ящики с выталкивателями, чтобы можно было извлекать стержни без повреждений. Смесь после заполнения ею стержневого ящика можно вакуумировать с целью предупреждения образования в ней воздушных пузырей.
Стержни можно изготовлять также литьем в металлических или в пластмассовых стержневых ящиках. Если связующим в стержневой смеси является алкозоль гидролитических продуктов этилсиликата 40, то концентрация в связующем должна быть более 20%. В качестве гелеобразователя — катализатора пригоден алюминат кальция в количестве до 10% от массы огнеупорного материала. Необработанные стержни имеют точность ±0,75% и большую газопроницаемость (пористость около 25%). Если же связующим является гидрозоль кремнезема, то наиболее технологичным гелеобразующим катализатором является небольшая присадка амина, например, диэтилентриамина (0,05% от количества используемого огнеупорного материала). Отверждения смеси можно достичь ее замораживанием при низких (до 6 °С) температурах. Способ пригоден для изготовления простых стержней малыми сериями. Его используют литейные цехи точных отливок.
Изготовление стержней виброуплотнением. Этот способ изготовления стержней подобен прессованию. Наибольшее уплотнение стержневой смеси достигается при частоте 2,5—4,0 кГц. Согласно патенту керамические стержни получают заливкой стержневой суспензии из огнеупорных материалов с гидролизованным этилси-ликатом в выплавляемые модели, служащие своеобразными стержневыми ящиками. Затем модели с залитой керамической массой подвергают вибрации. После затвердевания получается стержень.
Изготовление стержней выдавливанием. Этим способом изго-готовляют в основном стержни цилиндрической формы. По литературным данным, этот способ использует фирма Austenal (США). К выдавливаемым, точнее, вытягиваемым стержням относят также трубочки из кварцевого стекла. Их используют в качестве стержней при получении отверстий диаметром 0,5—2,5 мм. Эти трубочки могут быть изогнутыми и соединенными (пайкой или сваркой) в сложнейшие стержни для получения искривленных и лабиринтных каналов в отливках. Их удаляют из отливок достаточно легко выщелачиванием в расплавленном едком натре.
Трубочки из аморфного кварцевого стекла изготовляет государственное предприятие Kavalier Sazava (ЧССР).
Преимущества применения вставляемых керамических стержней обеспечиваются не только их свойствами, высокой размерной точностью и хорошей чистотой поверхности, но и опытом их применения при формовке.
Читать далее:
Применение вставляемых керамических стержней
Статьи по теме:
pereosnastka.ru
Изготовление керамических стержней - Производство точных отливок
Изготовление керамических стержнейКатегория:
Производство точных отливок
Изготовление керамических стержнейОтверстия и пазы в отливках, получаемых в таких формах, обычно усеяны металлическими наростами, или, если оболочка недостаточно просушена, отливка получается бракованной из-за полного разрушения оболочковой формы.
Этих недостатков можно избежать, применяя вставляемые керамические стержни.
По данным технической литературы, указанные недостатки можно устранить путем нанесения слоев суспензии под вакуумом; в этом случае, как указано в работе [1], необходимость в применении вставляемых керамических стержней снизится наполовину. Процесс Intrishell обеспечивает надежное нанесение суспензии на выплавляемые модели с пазами и отверстиями шириной или диаметром до 0,8 мм при значительной длине.
Нанесение слоев суспензии под вакуумом позволяет заполнить любые узкие отверстия и пазы, но при этом не устраняются трудности, связанные с последующей сушкой слоев оболочки.
Длинный керамический стержень должен быть не только тщательно просушен, но и обладать прочностью, т. е. должен обеспечивать динамический и статический напор заливаемого металла и длительное термическое воздействие без разрушения. Чем больше прочность на’ изгиб у материала стержня, тем длиннее может быть сам стержень.
Суспензия, используемая в процессе Intrishell, содержит в качестве жидкого связующего гидрозоль кремнезема. Если таким связующим является Ludox SM40 с очень мелкой коллоидной Дисперсией кремнезема, то прочность совершенно сухих стержней, полученных послойным нанесением суспензии, всегда ниже (3,2—3,8 МПа) по сравнению с прочностью вставляемых керамических стержней (20 МПа).
Преимущества вставляемых керамических стержней. По сравнению со стержнями, получаемыми нанесением слоев, вставляемые керамические стержни имеют более точные размеры, обеспечивают более качественную поверхность в полостях, отверстиях и пазах отливок; стержни поддаются обработке, шлифованию, устойчивы против эрозии жидким металлом, газопроницаемы, хорошо противостоят тепловым ударам и имеют высокую прочность на изгиб.
Вставляемые керамические стержни позволяют получать такие полости, отверстия и пазы в отливках, которые механической обработкой невозможно получить вообще. Так, например, можно получить отливки с ломаными сквозными каналами или проходным отверстием с внутренним расширением или проходными отверстиями с внутренними витками и т. п.
Эта новая технология расширяет возможности литья по сравнению с обычной технологией литья по выплавляемым моделям и с процессом Intrishell.
Приведенные в таблице величины относятся к сплавам железа. И хотя во многих случаях можно получать стержни при нанесении слоев на выплавляемые модели, тем не менее в этих случаях выгоднее использовать вставляемые керамические стержни. При этом сокращается производственный процесс, так как не увеличивается время сушки.
При использовании вставляемых керамических стержней производство точных отливок более надежно. Строгий контроль готовых стержней позволяет исключать-из дальнейшего производственного цикла бракованные стержни. Точное положение и качество стержней, вложенных в модели, у сложных отливок контролируется рентгеном. Выплавляемые модели с неправильно уложенными стержнями или перекошенными во время запрессовки отбраковываются. Тем самым снижается количество бракованных отливок по причине пороков полостей, пазов и отверстий.
Рис. 1. Вставляемые карамические стержни
Преимущества керамических стержней и их значение при производстве очень сложных и уникальных точных отливок отмечаются в многочисленных технических публикациях.
Вставляемые керамические стержни широко используют при производстве точных отливок для авиационных двигателей. Так, например, английской фирмой Doulton был изготовлен при помощи вставляемых стержней ряД сложных отливок для сверхзвукового самолета Конкорд. За эти достижения фирма была награждена английской королевой знаком почетного внимания «Queens Award to Industry» (Королевская премия индустрии).
На рис. 1, а, б представлены некоторые формы вставляемых стержней, которые изготовляет английская фирма Sherwood Refractories (Cleveland Ohio, США). На рис. 1, а изображены отливка и стержень турбинной лопатки реактивного самолета. Во время эксплуатации лопатка должна охлаждаться, и поэтому в ее теле выполнены 23 канавки; стенки полой лопатки опираются на три тонкие прямоугольные подставки; канавки на стержне имеют ширину 0,5 мм.
Деталь, представленная на рис. 1, б, изготовлена при помощи вставляемого стержня, который оформляет 24 тонких лопатки толщиной 0,96 мм и шириной 0,38 мм. Лопатки расположены относительно сложной конотрукции профилированного полого вала под углом 41° 15’. Допускаемое отклонение лопаток от номинального положения ±0,25 мм на сторону.
На рис. 2, а—в показаны примеры керамических стержней Для получения сложных полостей в отливках ответственного назначения. Наибольшим потребителем и изготовителем керамических стержней является авиационная промышленность, производящая турбины внутреннего сгорания. Там, где точные отливки производятся большими сериями, некоторые фирмы специализируются на производстве готовых керамических стержней (для нужд литейных цехов). Стержни для заказчиков поставляются из материалов со следующими свойствами: содержание А1203 менее 1%, пористость 30,5%, плотность 3 кг/дм3, коэффициент теплопроводности (от 0 до 1100° С) 2-Ю-6 К-1; прочность при изгибе 17,5 МПа (17,5 Н/мм2).
Рис. 2. Примеры отливок, изготовленных с керамическими стержнями
Стержни не вступают во взаимодействие при обжиге с материалом оболочек, а при заливке — с высоколегированными сплавами даже при литье в вакууме. Они термостойки, не деформируются и не повреждаются от тепловых ударов при 1650° С. Минимальная шероховатость поверхности отливок при использовании керамических стержней до 100 RMS позволяет выдерживать заданные размеры в пределах ±0,125 мм. Повторное прокаливание не изменяет качество стержней, и их объем практически постоянен при всех температурах заливки.
Эти стержни быстро удаляют из отливок химическим способом (выщелачиванием), а простые — дробеструйной обработкой.
Английская фирма Marder Foundry Supplies PTY Ltd. Port Melbourne изготовляет готовые стержни с торговым названием Sintox [10] со следующими свойствами: нормальный производственный допуск ±0,6 или 0,25% для всех размеров, допуск, достигаемый обработкой стержней, ±0,120 мм, прочность при изгибе 20 МПа (Н/мм2).
Материал стержней инертен ко всем видам заливаемых сплавов и термоустойчив.
Стержни выщелачиваются из отливок в 30%-ном растворе едкого натра при температуре 80 °С.
Поданным проспектов различных изготовителей готовых стержней, вставляемые керамические стержни должны обладать прежде всего следующими свойствами:1) материал стержней должен быть инертным по отношению к форме и заливаемому металлу и не должен выделять газы при заполнении металлом форм;2) стержни должны противостоять тепловым ударам при заполнении формы металлом и иметь определенную размерную стабильность;3) стержни должны иметь соответствующую форму и чистоту поверхности, чтобы полость отливки выполнялась с заданной точностью и с качественной поверхностью;4) стержни должны легко и просто удаляться из отливок.
Эти свойства обеспечиваются как материалом, так и технологией изготовления стержней.
Читать далее:
Материалы для изготовления керамических стержней
Статьи по теме:
pereosnastka.ru
Китай Керамический Стержень, Китай Керамический Стержень список товаров на ru.Made-in-China.com
Цена FOB для Справки: US $ 5.0-6.0 / шт. MOQ: 10шт.
- Огнеупорность (℃): 1580
- Особенность: Материалы Долгого Времени,Мгновенный Материал
- Тип: Огнеупорный Материал
- Упаковка: Standard Safe Carton or Pallet
- Стандарт: Depends
- Торговая Марка: HEATFOUNDER
-
Поставщики с проверенными бизнес-лицензиями
Поставщики, проверенные инспекционными службами
Heat Founder Group Co., Ltd. - провинция: Shanghai, China
ru.made-in-china.com
Керамические стержни - Большая Энциклопедия Нефти и Газа, статья, страница 2
Керамические стержни
Cтраница 2
Питательное устройство ( рис. 40) состоит из подающих механизмов /, уплотнителей 6 и приводов 4, закрепленных на боковых поверхностях кронштейна 7 симметрично реакционным трубкам и связанных между собой переходными втулками, образующими каналы, по которым транспортируются керамические стержни. [17]
Агрегат I предназначен для подачи с заданным ритмом загрузки керамических стержней и дозированно паров ЭОС в реакционные трубки, а также сообщения вращательно-поступательного движения стержням в трубках. Керамические стержни из многозаход-ных вибрационных загрузчиков поступают по питателям в подающие механизмы и поштучно по каналам питательного устройства, уплотненным со стороны загрузки, продвигаются в реакционные трубки. [18]
Из чистого урана, чаще из его сплавов или интерметаллидов, отливают стержни и пластины, служащие сердечниками твэлов. Сердечником могут быть также керамические стержни из двуокиси урана, спеченной с другими окислами. [19]
Резистивный элемент таких резисторов представляет собой тонкую пленку пиролитическогс углерода ( толщиной в десятые доли микрометра), полученного путем разложения углеводородов при высокой температуре в вакууме или в среде инертного газа, и осажденную на изоляционное основание. В качестве оснований углеродистых резисторов используются керамические стержни или трубки, а основания некоторых типов высокочастотных резисторов изготовляют в виде дисков, шайб или пластин. Для уменьшения распределенной емкости и диэлектрических потерь высокочастотные резисторы в ряде случаев выполняются без защитного покрытия. [20]
Для измерения температур до 630 74 С применяются ТС, чувствительные элементы которых изготовляются из платиновой проволоки диаметром от 0 05 до 0 2 мм, свободной от натяжений, бифилярно намотанной на каркас для устранения влияния магнитных помех. В качестве изоляционного каркаса применяются слюдяные пластины, керамические стержни крестообразной формы сечения из кварца или окиси алюминия с канавками, в которых размещаются спирали. Слюда в естественном состоянии содержит связанную воду и адсорбированные газы. В процессе измерения выделяющиеся газы и водяные пары могут захватываться проволокой чувствительного элемента с одновременным изменением сопротивления. Во избежание этого слюдяные каркасы следует перед навивкой прокалить в вакууме. В общем, слюду не рекомендуется применять при температурах выше 450 С. Кварц, алунд и фарфор лучше сохраняют изоляционные показатели. При 630 С ток, протекающий по изолятору каркаса, обусловливает погрешность порядка Ю-3 К. При дальнейшем повышении температуры погрешность, вызванная потерями изоляционных характеристик каркаса, быстро растет и в значительной мере зависит от технологии изготовления каркаса. [21]
Для испытаний на теплоустойчивость применяют специальные термокамеры или комбинированные термобарокамеры, термовла-гокамеры. Нагрев камер осуществляют нагревательными устройствами в виде спиралей из константановой проволоки, намотанной на керамические стержни и закрытые кожухами. Нагреватели располагают обычно в нижней части камеры. Нагретый воздух подается непосредственно в полезный объем камеры или циркулирует внутри металлической рубашки, окружающей этот объем. Постоянная температура в термостате поддерживается терморегулятором. Воздух нагревается электрическими калориферами достаточной мощности и прогоняется вентиляторами. [22]
Конструктивно высокочастотные дроссели выполняются в виде небольших по размерам цилиндрических катушек с однослойной или многослойной обмоткой. Дроссели с однослойной обмоткой применяются в диапазонах коротких и ультракоротких волн. В качестве каркаса для них часто используют керамические стержни от высокоомных резисторов типа ВС ( см. стр. Ультракоротковолновые дроссели наматываются с шагом. Дроссели с многослойной обмоткой применяются в диапазонах средних и длинных волн. Обмотка их состоит из ряда последовательно соединенных секций. [23]
Особенностью технологического процесса литья по выплавляемым моделям является неразъемная форма. Модель, необходимая для получения формы, одноразовая и обычно ее удаляют из оболочки выплавлением. Формовочные смеси имеют сметанообразную консистенцию и представляют собой суспензию - смесь жидкой и твердой фаз. Керамические стержни вставляют в пресс-форму, чаще всего перед запрессовкой модельного состава. Металл заливают в раскаленные формы. [24]
В Институте автоматики Госплана УССР подобные тензорезисторы используются в силоизмерительных тензометрических преобразователях. Институтом разработана унифицированная серия силоизмерительных тензопреобразователей с тензорезисто-рами со свободным подвесом. Упругий элемент тензопреобразователей имеет стойки стеклянными промежуточными опорами, на которых намотаны тензочувствительные элементы из констан-тановой проволоки диаметром 0 07 мм. Для растягивания проволоки в ряде случаев используются сапфировые или керамические стержни. В патенте [61 ] приведены описания конструкций тензорезисторов со свободным подвесом, у которых тензочувствительные элементы закрепляются только в точках, где на них передаются измеряемые механические напряжения. Между этими точками тензоэлемент практически свободен от связей с конструкцией. Преобразователи этого типа находят применение и в системах автоматического управления производственными процессами в металлургической, химической и других отраслях промышленности. [25]
Литейная керамическая форма может быть монолитной и двухслойной. Двухслойные формы применяют для крупных отливок. Облицовочный слой, соприкасающийся с моделью, делают из керамики, наполнитель ( опорный слой) состоит, например, из дешевой шамотной крошки. Модели перед формовкой для предотвращения прилипания смеси покрывают разделительными составами, например силиконовой жидкостью. Для получения сложных пустотелых отливок применяют керамические стержни, изготовляемые в пресс-формах, а затем спекаемые и устанавливаемые в литейные формы. [27]
Эффективным способом борьбы с токсичностью отработавших газов является дожигание. Дожигатели можно подразделить на каталитические и пламенные. Каталический дожигатель устанавливают около выпускного трубопровода двигателя. Он представляет собой корпус с расположенным внутри него катализатором. Катализатор, изготовленный из платино-алюминиевого сплава, ванадия или окиси кобальта, наносят тонким слоем на керамические стержни, шарики или решетки. Отработавшие газы проходят вместе с засасываемым воздухом через катализатор, который обеспечивает догорание горючих токсических веществ, находящихся в газах. [28]
Стержни должны обладать превосходным сопротивлением термоудару, чтобы без растрескива ния выдерживать напряжения, возникающие при подогреве t заливке. Наконец, стержень должен легко извлекаться и: отлитой детали. Для извлечения стержня пользуются и хими ческими, и механическими методами. Поэтому сегодня стерж ни преимущественно делают из материалов, содержащих боль шую долю оксида кремния; последняя легко выщелачиваете: обычными основаниями ( КОН, NaOH) и / или кислотами, которьк не должны вступать в химическую реакцию с суперсплавами Межзеренное растрескивание суперсплавов в результате воз действия каустиком может вызвать снижение длительно. Подобные затруднения регулируют надле жащим подбором материалов сосуда, химического состава ка устика, рабочих параметров процесса выщелачивания. Круп ные керамические стержни удаляют механически, - путем об дувки песком или мелкими стеклянными шариками. [29]
Для образцов 1 - 4 в центре стержня просверливалось отверстие и оставлялась стенка толщиной 1 мм. Длина таких полуцилиндров варьировалась от 0 5 до 2 5 см. Образцы 5 и 6 срезались с конца твердого графитового стержня в виде тонких пластинок. В результате получалась очень тонкая графитовая оболочка, похожая на карандашную отметку, нанесенную на керамические стержни. [30]
Страницы: 1 2
www.ngpedia.ru
Смесь для изготовления литейных керамических стержней
Изобретение относится к литейному производству и может быть использовано при изготовлении изделий из жаропрочных сплавов, преимущественно лопаток газотурбинных двигателей (ГТД). Смесь в качестве основного компонента содержит порошок твердого раствора на основе плавленого SiO2, содержащего от 5 до 30 мас.% Cr2О3 и/или Al2O3 , и спекающую добавку. Компоненты взяты в следующем соотношении, мас.%: компонент на основе SiO2 75,0-99,5, спекающая добавка 0,5-25,0. Спекающая добавка содержит, по крайней мере, порошок одного из соединений из ряда сиалон, La2О 3, LaB6. В качестве сиалона она содержит, по крайней мере, одно соединение из ряда твердых растворов, образующихся в системе Si-Al-O-N. Преимущественно используют системы на основе оксинитрида кремния с элементной формулой Si2xAl xO1+xN2-x, где х=0-0,2, на основе нитрида кремния с элементной формулой Si6-zAl zOzN8-z, где z=0-4,2, на основе политипоидов нитрида алюминия с элементной формулой AlmSiO 2Nm, где m=4, 5, 6, 8. Применение смеси позволяет повысить предел прочности стержней при изгибе σ изг до 14,0-26,0 МПа, снизить линейную усадку до ≤0,1-0,8%, глубину взаимодействия со сплавом ЖС6У до 0,03-0,05 мм. Технологический процесс изготовления стержней соответствует экологическим и медицинским требованиям. 1 з.п. ф-лы, 3 табл.
Изобретение относится к литейному производству, а именно к составам смесей для изготовления керамических стержней, формирующих внутренние полости (каналы охлаждения) в изделиях из жаропрочных сплавов, преимущественно в лопатках газотурбинных двигателей (ГТД).
Традиционным материалом для изготовления стержней для литья лопаток ГТД из жаропрочных сплавов является керамика на основе плавленого SiO2 (I.C.Huseby, M.P.Borom and C.D.Gresjkovid, High temperature characterization of silica-based core for superalloys, Am. Ceram. Soc. Bull., 58, 448-52, 1979).
Керамика может содержать также до 40 мас.% спекающей добавки из ряда более тугоплавких оксидов: ZrSiO4, ZrO 2, Al2О3. Стержни из плавленого SiO 2 устойчивы к воздействию металлических расплавов, имеют низкий коэффициент температурного линейного расширения и относительно легко удаляются из изделия при помощи водных растворов щелочей. Недостатки данной керамики связаны с низкой прочностью (предел прочности при изгибе обычно составляет 10,0÷12,0 МПа) и фазовой нестабильностью основного компонента. При спекании плавленый аморфный SiO2 частично расстекловывается с образованием кристобалита. На стадии охлаждения данная кристаллическая модификация SiO2 подвержена деструктивному полиморфному превращению с изменением удельного объема. Это проводит к образованию макротрещин, резкому снижению прочности и потере требуемой геометрической конфигурации (коробление) стержня. Максимальное содержание кристаллической фазы, при котором керамические стержни способны сохранять приемлемые прочностные свойства, не превышает 15-30 об.%.
Спекание керамических стержней в условиях минимального или полного отсутствия расстекловывания аморфного SiO2, т.е. при температуре ниже 1100°С, требует усложнения технологической схемы их получения: из-за недостаточной интенсивности спекания для упрочнения полученного материала необходима его пропитка коллоидными растворами оксидов и проведение повторного обжига (N.Lequeux, H.Larose, and P.Boch, Low Shrinkage Refractories by an Infiltration Technique, J. Eur. Ceram. Soc., 14 [1], 23-27, 1994; US 5697418, 16.12.1997; C.H.Chao and H.Y.Lu, Optimal Composition of Zircon-Fused Silica Cores For Casting Superalloys, J. Am. Ceram. Soc., 85 [4], 773-79, 2002).
Степень расстекловывания плавленого аморфного SiO 2 при обжиге керамических стержней зависит и от качества исходного порошка плавленого SiO2. Для получения стержневой керамики используют плавленый SiO2 с содержанием основного вещества не менее 99,95 мас.%. Примеси, особенно щелочные или щелочноземельные элементы, активируют процесс расстекловывания аморфного SiO2 (US 4093017, 06.06.1978). Однако указанные примеси оказывают негативное влияние на прочностные свойства при высоких температурах.
Одним из способов снижения дефектности керамических стержней при высокотемпературном обжиге (Т=1150÷1370°С) является использование смеси для изготовления литейных керамических стержней, которая содержит основной компонент на основе плавленого диоксида кремния (SiO2), до 35 мас.% спекающей добавки ZrSiO4, до 5 мас.% ультрадисперсного порошка SiO 2 и от 1,5 до 6,5 мас.% термически стабильных керамических волокон (US 4989664, 05.02.1991). Ультрадисперсный порошок SiO 2 со средним размером частиц 0,007÷0,014 мкм активирует спекание, а термически стабильные керамические волокна подавляют усадку и образование макротрещин при обжиге. Недостатком известного изобретения, выбранного в качестве наиболее близкого аналога, является применение высокотоксичных веществ. Ультрадисперсные порошки и керамические волокна вызывают профессиональные, в том числе онкологические, заболевания органов дыхания.
Техническим результатом предлагаемого изобретения является разработка смеси для изготовления керамических стержней, обладающих высокими прочностными характеристиками, низкой линейной усадкой в процессе обжига, малой глубиной взаимодействия с жаропрочными сплавами, хорошей растворимостью в водных растворах щелочей, при высокой технологичности процесса изготовления стержней, соответствующего экологическим и медицинским требованиям.
Технический результат достигается тем, что смесь в качестве основного компонента содержит порошок твердого раствора на основе плавленого SiO2, содержащего от 5 до 30 мас.% Cr2О3 и/или Al2 О3, спекающую добавку, в качестве которой содержит по крайней мере порошок одного из соединений из ряда сиалон, La2O3, LaB6, при следующем соотношении компонентов, мас.%:
Основной компонент на основе SiO 2 | 75,0÷99,5 |
Спекающая добавка | 0,5÷25,0 |
при этом в качестве сиалона она содержит по крайней мере одно соединение из ряда твердых растворов, образующихся в системе Si-Al-O-N, преимущественно на основе оксинитрида кремния с элементной формулой Si2-xAlxO1+xN2-x , где х=0÷0,2, на основе нитрида кремния с элементной формулой Si6-zAlzOzN8-z , где z=0÷4,2, на основе политипоидов нитрида алюминия с элементной формулой AlmSiO2Nm , где m=4, 5, 6, 8.
Порошок твердого раствора на основе плавленого SiO2, содержащего от 5 до 30 мас.% Cr 2О3 и/или Al2О3, а также спекающие добавки из ряда сиалонов могут быть получены любыми известными методами, в том числе и в режиме горения.
Содержание в твердом растворе от 5 до 30 мас.% Cr2О3 и/или Al2О3 за счет замещения четырехвалентного кремния трехвалентными элементами увеличивают кинетическую стабильность аморфного SiO2 по отношению к фазоразделению и расстекловыванию, повышают его огнеупорность и сопротивление ползучести.
Указанные порошки сиалонов при обжиге на воздухе в зависимости от соотношения Si и Al в исходном соединении окисляются с образованием кристобалита, муллита и α-Al 2О3. Образуемые оксидные фазы связывают частицы твердого раствора на основе плавленого SiO2 , способствуют получению стержней точной формы из заявляемой смеси и с высоким выходом.
Предлагаемое изобретение было отработано в условиях литейного производства ФГУП ММПП "САЛЮТ". Керамические стержни изготавливали по стандартной схеме, включающей приготовление термопластичного шликера с использованием органического парафино-полиэтиленового пластификатора в количестве 10-15% сверх 100% от массы заявляемой смеси, формование исходных заготовок методом литья под давлением и последующий обжиг на воздухе в туннельной газовой печи при 1350±20°С в течение 7-10 часов в засыпке из глинозема.
Составы исходных смесей представлены таблице 1. Свойства керамических стержней, изготовленных из заявленной смеси (величина линейной усадки образца при обжиге и прочность при изгибе в холодном состоянии после спекания) по примерам, представлены в таблице 2.
Как видно из представленных данных, использование заявленной смеси позволяет получать керамические стержни с минимальными отклонениями от заданных размеров (менее 1%) и высокой прочностью при изгибе (14,0÷26,0 МПа), глубиной взаимодействия со сплавом ЖС6У до 0,03÷0,05 мм, при высокой технологичности процесса изготовления стержней, соответствующего экологическим и медицинским требованиям.
Кроме того, смеси полностью удалялись из формы при растворении в 30%-ном водном растворе КОН при 100÷110°С в течение 1÷2 час.
Дополнительно для иллюстрации изобретения было проведено сравнительное испытание керамических стержней, изготовленных из заявляемой смеси на основе плавленого твердого раствора SiO2 и сиалона с элементной формулой Si5Al1O 1N7 и из смеси на основе электрокорунда, используемой в настоящее время при серийном производстве лопаток ГТД (Специальные способы литья: Справочник. Под ред. В.А.Ефимова, М.: Машиностроение, 1991, с.140-148),
Использовалось следующее соотношение ингредиентов в исходной смеси (мас.%):
Заявляемая смесь на основе плавленого | |
твердого раствора SiO 2 | SiO2-Cr 2O3(15,0)-Al2 O3(5,0) - 92,0 |
Спекающая добавка - сиалон | Si 5Al1O1N 7 - 8,0 |
Известная смесь на основе электрокорунда | Al2 O3 (электрокорунд) - 98,5 |
Спекающая добавка | SiC - 1,5 |
Показателями качества стержней служили: прочность при изгибе в холодном состоянии после спекания, коэффициент термического расширения, интенсивность взаимодействия с никелевым сплавом ЖС6У, величина линейной усадки образца при обжиге, чистота поверхности стержней, время и условия полного удаления стержня из отливки. Результаты испытаний представлены в таблице 3.
Заявленная смесь была опробована для наработки опытных партий керамических стержней различной конфигурации и показала свою пригодность для производства лопаток ГТД. Применение заявленной смеси позволило облегчить условия удаления стержней из отливки и на 10% повысить выход готовых изделий за счет уменьшения числа дефектов в отливках, связанных с качеством стержней.
Таблица 1 | ||
Состав исходной смеси, мас.% | ||
№ примера | Твердый раствор на основе плавленого SiO2 (содержание Cr 2О3 и/или Al2 О3 в твердом растворе, мас.%) | Спекающая добавка мас.% |
1 | SiO2-Cr2O 3(5,0) - 99,5 | LaB6 - 0,5 |
2 | SiO2-Cr2O 3(25,0)-Al2O3 (5,0) - 97,0 | La2O 3 - 3,0 |
3 | SiO2-Cr2O 3(10,0)-Al2O3 (5,0) - 91,0 | Si1,8 Al0,2О1,2N 1,8 -7,5; La2O3 - 1,5 |
4 | SiO2-Cr2O 3(15,0) - 84,0 | Si3 Al3О3N 5 - 15,0; LaB6 - 1,0 |
5 | SiO 2-Al2O3(10,0) - 75,0 | SiAl4O 2N4 - 25,0 |
Таблица 2 | ||
№ примера | Свойства литейных керамических стержней, изготовленных из заявляемой смеси по примерам | |
Предел прочности при изгибе σ изг, МПа | Линейная усадка, % | |
1 | 18,0÷21,0 | 0,4÷0,6 |
2 | 21,0÷26,0 | 0,6÷0,8 |
3 | 19,0÷24,0 | 0,2÷0,5 |
4 | 18,0÷22,0 | ≤0,2 |
5 | 14,0÷18,0 | ≤0,1 |
Таблица 3 | ||
Показатели | Свойства литейных керамических стержней, изготовленных | |
из смеси на основе электрокорунда* | из заявленной смеси | |
Предел прочности при изгибе σ изг, МПа | 14,0÷18,0 | 15,0÷19,0 |
Класс чистоты поверхности стержней | 4÷5 | 5÷6 |
КТР, °С-1 | 8,0·10 -6 | 0,2÷0,5·10 -6 |
Линейная усадка, % | 0,2÷0,5 | 0,2÷0,5 |
Глубина взаимодействия со сплавом ЖС6У, мм | 0,1÷0,2 | 0,03÷0,05 |
Условия удаления стержня из тела лопатки | Расплав бифторида калия (KHF2) Т=250÷310°С, t 6÷70 час | 30%-ный водный раствор КОН Т=100÷110°С, t 1÷5 час |
* Специальные способы литья: Справочник. Под ред. В.А.Ефимова, М.: Машиностроение, 1991, С.140-148 |
Формула изобретения
1. Смесь для изготовления литейных керамических стержней, преимущественно для отливок из жаропрочных сплавов, включающая основной компонент на основе SiO2 и спекающую добавку, отличающаяся тем, что она в качестве основного компонента содержит порошок твердого раствора на основе плавленого SiO2 , содержащего от 5 до 30 мас.% Cr2О3 и/или Al2О3, а в качестве спекающей добавки, по крайней мере, порошок одного из соединений из ряда сиалон, La2О3, LaB6, при следующем соотношении компонентов, мас.%:
Основной компонент на основе SiO 2 | 75,0-99,5 |
Спекающая добавка | 0,5-25,0 |
2. Смесь по п.1, отличающаяся тем, что в качестве сиалона она содержит, по крайней мере, одно соединение из ряда твердых растворов, образующихся в системе Si-Al-O-N, преимущественно, на основе оксинитрида кремния с элементной формулой Si2-x AlxO1+xN2-x, где х=0-0,2, на основе нитрида кремния с элементной формулой Si6-z AlzOzN8-z, где z=0-4,2, на основе политипоидов нитрида алюминия с элементной формулой Alm SiO2Nm, где m=4, 5, 6, 8.
bankpatentov.ru
Заточка на керамических стержнях малого диаметра
Krivdoslav 30-01-2012 08:16Добрый день!Имею в наличии керамические стержни длиной около 90мм и диаметром 7мм, использую для правки ножей вне дома. Точат хорошо, но возникает вопрос, не вредит ли режущей кромке столь малая площадь контакта с абразивом? Допустимо ли их использование в заточных целях?
oldTor 30-01-2012 10:09чем меньше пятно контакта, тем быстрее работа. думаю если не переусердствовать с давлением - всё будет совершенно нормально.
grinderman 30-01-2012 10:45Бруски малого диаметра или круг со сторонами 7х7мм Встреча на углу круглого дома
xopoc 30-01-2012 11:01quote:Originally posted by oldTor:чем меньше пятно контакта, тем быстрее работа. думаю если не переусердствовать с давлением - всё будет совершенно нормально. Пусть меня поправят, если я ошибаюсь, но, по-моему, это не так.Если допустить, что для заточки инструмента, не говоря уже о доводке, требуется усилие порядка 1 - 2 кг/см(2), то на подобные стержни (пятно контакта в десятки, а то и сотню раз меньше квадратного см) надо прилагать исчезающе малое давление - на грани человеческой моторики.И это даже со стержнями дюймового диаметра, а здесь в 3,5 раза тоньше.Иначе получается очень быстрая сточка лезвия плюс крайне грубая работа по режущей кромке. Всё равно, что при работе на обычном бруске оказывать на него давление килограмм в 20 - 25.
Кстати, где-то здесь есть тема про мусаты. Там Николай_К по этому поводу довольно подробно и популярно писал.
Когда-то так и точил - с относительно легким давлением. В итоге, керамический стержень (карманная точилка) где-то между 1000 и 2000 грит затачивал нож в пару движений, но лезвие с трудом пыталось брить предплечье, а стойкость РК была почти никакой.
Вообще, настоятельно рекомендую прочитать тему "мусаты" - именно посты Nikolay_K.http://guns.allzip.org/topic/224/448205.html
quote:Originally posted by grinderman:Бруски малого диаметраВстретимся на углу круглого дома На фоне соседней темы "Впуклая линза" название этой звучит не так уж и "страшно". Двое из ларца, блин. Krivdoslav 30-01-2012 11:44Да, терминология хромает приношу извиненияХорос, спасибо за наводку, полез изучать тему.В целом мнения понятны, заточка на стержнях малого диаметра вредит рк и негативно сказывается на ее стойкости. Верно?
xopoc 30-01-2012 12:21quote:Originally posted by Krivdoslav:В целом мнения понятны, заточка на стержнях малого диаметра вредит рк и негативно сказывается на ее стойкости. Верно?Грубо говоря, "заточка" - да. Правка - напротив. Но править РК на стержнях (мусатах) надо учиться. Удерживать верный угол, равномерно прилагать усилие.По большому счету, с лезвиями S-формы можно нормально работать или сверхредкими слабовыпуклыми камнями (самом делать?), или реально узкими брусками (именно брусками) или же "стержнями". Но в последнем случае желателен как можно больший диаметр стержней и придется потратить немало времени.У самого сейчас есть такая проблема. В наличие широкие бруски и два "стержня". Как-то "не кошерно" получается с S-образным лезвием. С ножами классических форм всё проще и увереннее.
Женя-Кот 30-01-2012 13:12quote:или сверхредкими слабовыпуклыми камнями (самом делать?)Когда я учился в МедУ-лище, наши паталагоанатом с хирургом были обладателями набора брусков, которые, как они уверяли, ранее, в 60-70 гг., специально выпускались (промышленно!) для заточки и правки мединструментария. Так как в руки они их не давали, подробно рассмотреть не удалось, помню только, что они были трёх типов зерна, и с ясно различимой выпуклой линзой. Во время работы, сколько не иска, так и не нашел - везде использовали одноразовый инструмент. А жаль!xopoc 30-01-2012 13:45Извините за OFF-TOPЖеня-Кот, думаю, проще всего самому сделать - довести узкие брусочки на притире алмазным зерном. Не полностью поверхность бруска, а лишь радиусы на углах.Что касается готовых камней, то он встречаются, в основном, за бугром. Чаще - как дополнение к точилкам.
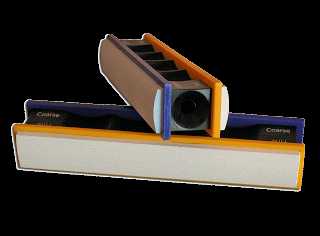
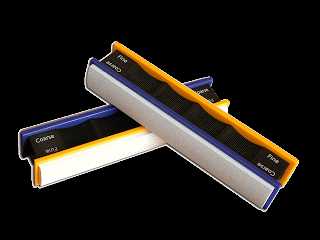
http://www.knifeworks.com/dmtalignercurvedbladeknife.aspx
Но с ними, как мне кажется, та же история, что и со стержнями - давить надо очень слабо.
С другой стороны, Спайдерко Три-англ вообще предполагает первичную работу "на ребро" и лишь потом - на плоскость камня. И ничего...Но у меня, все же, с керамическими мусатами результат получается все-таки хуже, чем с камнями (см выше). Почему так происходит - помогла понять тема про мусаты.
Nikolay_K 30-01-2012 13:49quote:Originally posted by Krivdoslav:В целом мнения понятны, заточка на стержнях малого диаметра вредит рк и негативно сказывается на ее стойкости. Верно?нет. неверно.
проблемы возникают из-за избыточного давленияи только из-за него
работа с узкими камнями BORIDE, SPYDERCO TRIANGLEи тонким мусатом от IDAHONEпоказала, что при разумном и внимательном отношенииможно добиться неплохих результатов и на таких абразивах
более того, они позволяют весьма эффективно и качественно затачиватьинструмент со сложной формой РК (S-образные, серрейторы)
но, ясное дело для такого инструмента требуется специфическая техника работыпозволяющая четко контролировать и удерживать давление
xopoc 30-01-2012 13:56quote:Originally posted by Nikolay_K:работа с узкими камнями BORIDE и тонким мусатом от IDAHONEпоказала, что при разумном и внимательном отношенииможно добиться неплохих результатов и на таких абразивахПо-моему, выдерживать равномерное - и при этом сверхслабое - давление на разном удалении руки от мусата плюс удерживать угол одной рукой при изменении формы лезвия для не самого опытного пользователя - задача из полуфантастических.Вместе с тем, даже у Вас результат получается не более, чем "неплохой". Или я что-то не так понял?Nikolay_K 30-01-2012 14:39quote:Originally posted by xopoc:По-моему, выдерживать равномерное - и при этом сверхслабое - давление на разном удалении руки от мусата плюс удерживать угол одной рукой при изменении формы лезвия для не самого опытного пользователя - задача из полуфантастических.а что мешает держать мусать неподвижнои перемещать затачиваемый инструмент?
посмотрите как эту идею обыграли в SPYDERCO TRIANGLEтам радиусы на ребрах маленькие,но это приспособление работаети работает весьма неплохо и нареканий ни у кого не вызывает
более того, это приспособление очень простое в освоении
quote:Originally posted by xopoc:Вместе с тем, даже у Вас результат получается не более, чем "неплохой".так сказано из-за того,что у меня не было цели довести этот тех. процесс до совершенства
мне было нужно несколько раз заточить такой инструменти я это делал, целью было получить удовлетворительный результатза разумное время
мне удалось этого добитьсярезультат даже немного превзошел ожидания
его можно было улучшить еще,если потратить больше времени,сделать спец. приспособлениядоработать методику и т.д.
но я не стал этим заниматься,так как это была одноразовая задача
quote:Originally posted by xopoc:выдерживать равномерное - и при этом сверхслабое - давление на разном удалении руки от мусата плюс удерживать угол одной рукой при изменении формы лезвия для не самого опытного пользователя - задача из полуфантастических.Дмитрич как-то говорил, что когда работаешь с приспособлениемкоторое четко фиксирует угол, то всё внимание можно сосредоточить на удерживании давления
это в самом позволяет добиться того, что многим кажется фантастическим
я это проверял на своем опытеи честно говоря немного обалделот результата...
попробуйте и не пожалеете.
и не забывайте про очень важный принцип --- двигаться должно то, что легче
Politika 20-12-2015 22:17quote:Изначально написано Чкылчи:У меня такие вот стержниХорошая правилка для ножей из керамических стержней
Отличная правилка! Написал пм по поводу отверстий в подставках
guns.allzip.org
Составной керамический стержень
Изобретение относится к литейному производству, в частности к литью охлаждаемых лопаток газотурбинного двигателя из жаропрочных сплавов с монокристальной структурой методом направленной кристаллизации с использованием керамических стержней сложной конструкции. Предлагаемая конструкция составного керамического стержня содержит основной стержень и дополнительные, расположенные на пере основного, и содержат продольные ряды отверстий и выступов, расположенных в шахматном порядке с внутренней и внешней сторон дополнительных стержней. Выступы с внутренней стороны дополнительных стержней жестко соединены с поверхностью основного стержня. Выступы могут быть выполнены в виде цилиндрических штырьков или полых сфер. Применение различных вариантов предлагаемой конструкции составного керамического стержня позволяет получать цельнолитые тонкостенные охлаждаемые монолопатки с проницаемой системой охлаждения. Использование таких лопаток с проницаемой системой охлаждения, эффективность охлаждения которых 0,6 позволит повысить температуру газа в турбине до 1800oC, увеличив при этом ресурс в 3 - 5 раз на двигателях нового поколения. 2 з.п. ф-лы, 3 ил.
Изобретение относится к литейному производству, в частности к литью охлаждаемых лопаток газотурбинных двигателей и газотурбинных установок из жаропрочных и коррозионных сплавов с монокристальной структурой методом направленной кристаллизации с использованием керамических стержней сложной конструкции.
Известны конструкции стержней для получения лопаток турбины со сложной системой охлаждения внутренней полости. Согласно аналогу [1] для получения охлаждаемой лопатки используют конструкцию керамического стержня, формирующего одну полость охлаждения, а для повышения эффективности охлаждения применяют вставной дефлектор. Эффективность охлаждения в лопатке при использовании такой конструкции стержня обеспечивает температуре газа в турбине не выше 1500oC. Известна конструкция стержня [2] в которой для получения литых охлаждаемых изделий используют составной сложный керамический стержень, состоящий из основного и дополнительных мини-стержней, один конец которых в виде шпильки располагается в углублении основного стержня и восковой модели, а второй в виде пластинки образует дозирующие отверстия в готовой отливке. Недостатками конструкции является недостаточная эффективность охлаждения, обусловленная тем, что выпуск воздуха через сформированные таким стержнем дозирующие отверстия обеспечивает пленочное охлаждение, а также чрезвычайная трудоемкость при установке мини-стержней. Технической задачей изобретения является создание составного керамического стержня для получения профилированного литого изделия, имеющего эффективную проницаемую систему охлаждения, а также снижающего трудоемкость при его изготовлении. Поставленная задача достигается тем, что предлагается составной керамический стержень для получения литых полых изделий, преимущественно лопаток турбины, включающий основной и дополнительные стержни, выполненные в виде керамических пластин и изогнутые по профилю пера. Дополнительные стержни размещены на основном стержне и содержат продольные ряды отверстий и выступов, расположенных в шахматном порядке с внутренней и внешней сторон дополнительных стержней, причем выступы с внутренней стороны дополнительных стержней соединены с поверхностью основного. Выступы с внешней и внутренней сторон дополнительных стержней могут быть выполнены в виде цилиндрических штырьков или полых сфер. Выступы с внутренней стороны дополнительных стержней могут быть выполнены в виде цилиндрических штырьков, а с внешней в виде полых сфер. На фиг. 1 представлена конструкция составного стержня, включающего основной стержень 1, дополнительные стержни 2, отверстия 3, выступы 4 в виде цилиндрических штырьков с внутренней стороны дополнительных стержней, выступы 5 в виде цилиндрических штырьков с внешней стороны дополнительных стержней. На пере основного керамического стержня 1, изготовленного прессованием керамической массы, установлены дополнительные тонкие стержни 2, представляющие собой, например, керамические пластины, изогнутые по профилю пера, на которых в шахматном порядке расположены отверстия 3 и цилиндрические штырьки малого диаметра с внутренней 4 и внешней 5 сторон дополнительных стержней. Высота цилиндрических штырьков с внутренней стороны дополнительных стержней определяется плотным контактом с основным, для чего на последнем в процессе изготовления были предусмотрены углубления. С внешней же стороны установлены равновеликие цилиндрические штырьки, высота которых определяется толщиной стенки лопатки в модели. Зацепляясь с керамикой оболочковой формы в процессе ее изготовления, они образуют после заливки металла отверстия на поверхности пера лопатки. Лопатка после удаления такого стержня из отливки имеет основную охлаждающую полость, сформированную основным стержнем и периферийную, сформированную дополнительными стержнями и представляющую собой полость в самой стенке лопатки. Таким образом, стенка лопатки состоит из двух слоев, в каждом из которых имеются отверстия малого диаметра для прохода охлаждающего воздуха. Для обеспечения жесткости конструкции между слоями расположены штырьки. Воздушный поток в такой лопатке из основной полости поступает через отверстия внутренней стенки в дополнительную полость, турбулизуется на штырьках и через выходные отверстия проникает на внешнюю горячую поверхность лопатки, образуя заградительную воздушную завесу. Для повышения скорости воздушного охлаждающего потока в стенке пера лопатки возможно использование формы выступов в виде полых сфер, располагающихся на дополнительных стержнях в тех же местах, что и цилиндрические штырьки. На фиг. 2 представлен вариант конструкции керамического стержня, имеющий выступы 4 с внутренней стороны дополнительных стержней в виде полых сфер и выступы 5 с внешней стороны дополнительных стержней в виде полых сфер. В этом случае полые керамические сферы обеспечивают контакт основного и дополнительных стержней между собой и керамической оболочкой. На фиг. 3 представлена конструкция керамического стержня, в котором возможна комбинация формы выступов в одном составном стержне при необходимости обеспечить разную толщину стенок у торца и замка лопатки. В этом случае с внутренней стороны они имеют форму цилиндрических штырьков 4, а с наружной - полых сфер 5. Примеры получения лопаток с различными вариантами конструкции предлагаемого составного керамического стержня. Пример 1. Основной керамический стержень изготавливали путем запрессовки стержневой массы из смеси порошков электрокорунда. Дополнительные тонкие стержни получали из той же стержневой массы в форме профиля пера с продольными рядами отверстий. Стержни прокаливали. После прокалки на дополнительном стержне устанавливали керамические цилиндрические штырьки с двух сторон, чередуя их с отверстиями в шахматном порядке. Затем дополнительный стержень крепили на основном, устанавливая его штырьками с внутренней стороны в углубления основного, промазав последние керамической суспензией для обеспечения плотного контакта. Высоту штырьков с внешней стороны проверяли шаблоном и далее изготавливали модель лопатки, например, из воска, проследив, чтобы торцы выступов снаружи были расчищены от модельной массы. Потом изготавливали оболочковую керамическую форму по технологии для направленной кристаллизации и заливали жаропрочным сплавом на никелевой основе в установке для направленной кристаллизации УВНК-8П. Из полученной отливки удаляли керамику в растворе бифторида калия. Полое перо такой лопатки кроме основной охлаждающей полости содержит периферийную, образованную дополнительным стержнем в стенке самого пера, состоящего из двух слоев с отверстиями, обеспечивающих проникающее охлаждение. Для эффективного и равномерного охлаждения диаметр штырьков и отверстий составлял 0,5 1,5 мм, а шаг по профилю 5 10 диаметров отверстий. Пример 2. В отличие от примера 1 для получения выступов на дополнительном стержне использовали полые сферы керамические шары продукт спекания тонкодисперсных порошков Al2O3. Их устанавливали в тех же местах, что и штырьки, предварительно отобрав по размеру с помощью сита. В зависимости от размеров лопатки диаметр полых сфер может меняться в пределах 0,5 1,5 мм. Далее изготавливали лопатку, как в примере 1. Форма отверстий в стенках такой лопатки была получена в форме полых сфер, что способствует увеличению скорости охлаждающего потока в изделии. Пример 3. Для получения стержня с комбинированной формой выступов с внутренней стороны дополнительного стержня устанавливают штырьки, а с наружной полые сферы в том же порядке, как в примере 1. Лопатка после удаления керамики имеет на внутренней стенке пера цилиндрические отверстия, а на наружной выпускные отверстия в виде полых сфер. Пример 4. Изготовление тонкостенного дополнительного стержня можно осуществить зацело с выступами запрессовкой керамической массы в пресс-форму, в матрице которой имеются выемки и штыри. Таким способом получали тонкостенную пластину с отверстиями и двусторонними выступами в шахматном порядке, изгибали по профилю пера основного стержня, прокаливали и устанавливали на основном стержне, как в примере 1. Использование пресс-формы для получения дополнительных стержней зацело с выступами и отверстиями снижает трудоемкость операции изготовления стержня и обеспечивает надежную калибровку отверстий. Применение различных вариантов предлагаемой конструкции составного керамического стержня позволит получать тонкостенные цельнолитые монолопатки газотурбинного двигателя, имеющие дополнительные охлаждающие полости в стенках полого пера, состоящие из двух раздельных слоев. В каждом слое имеются отверстия, расположенные продольными рядами в шахматном порядке по профилю пера для обеспечения эффективного равномерного охлаждения, полученные в процессе литья. Это обеспечит снижение стоимости всего конструктивно-технологического решения и предоставит надежную систему, где нет соединений. Использование таких лопаток с проницаемой системой охлаждения, имеющих эффективность охлаждения 0,6 позволит повысить температуру газа в турбине до 1800oC, увеличив при этом ресурс в 3 5 раз на двигателях нового поколения.Формула изобретения
1. Составной керамический стержень для получения литых полых изделий направленной кристаллизацией, включающий основной и дополнительные стержни, отличающийся тем, что дополнительные стержни выполнены в виде изогнутых по профилю пера лопатки керамических пластин с продольными рядами отверстий и выступов, расположенных в шахматном порядке с их внешней и внутренней сторон, и размещены на основном стержне, причем выступы дополнительного стержня жестко соединены с поверхностью основного стержня. 2. Стержень по п.1, отличающийся тем, что выступы с внешней и внутренней сторон дополнительных стержней выполнены в виде цилиндрических штырьков или в виде полых сфер. 3. Стержень по п.1, отличающийся тем, что выступы с внутренней стороны дополнительных стержней выполнены в виде цилиндрических штырьков, а с внешней стороны в виде полых сфер.РИСУНКИ
Рисунок 1, Рисунок 2, Рисунок 3www.findpatent.ru