Термодиффузионное цинкование металла: технология, оборудование, плюсы и минусы. Термодиффузионное цинкование технология
Термодиффузионное цинкование: технология и оборудование
Термодиффузионное цинкование, которое также называют шерардизацией, является относительно новой технологией нанесения на поверхность изделий из металла слоя цинка. Между тем именно такой способ цинкования среди всех существующих на сегодняшний день признается многими специалистами наиболее перспективным.
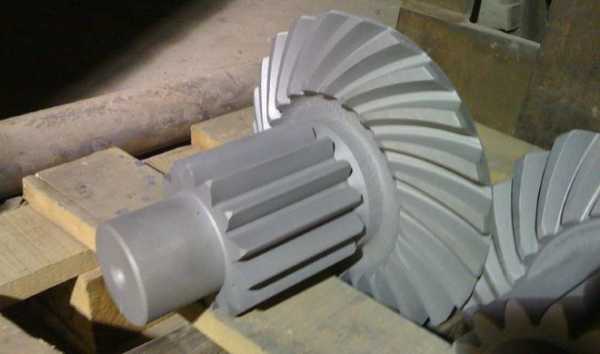
Технология термодиффузионного цинкования предназначена для защиты от коррозии стальных и чугунных изделий
Особенности и сферы применения
Такой метод защиты металлических изделий от коррозии и старения, как термодиффузионное цинкование, общие требования к которому регламентирует ГОСТ Р 9.316-2006, основан на явлении диффузии молекул металла, протекающей при относительно высокой температуре (400–470°). В данном случае в поверхностный слой обрабатываемого изделия диффузируют молекулы легирующего элемента – цинка.
В результате применения такой технологии на поверхности металлической детали формируется однородный цинковый слой. При этом однороден такой слой даже в труднодоступных местах обрабатываемого изделия.
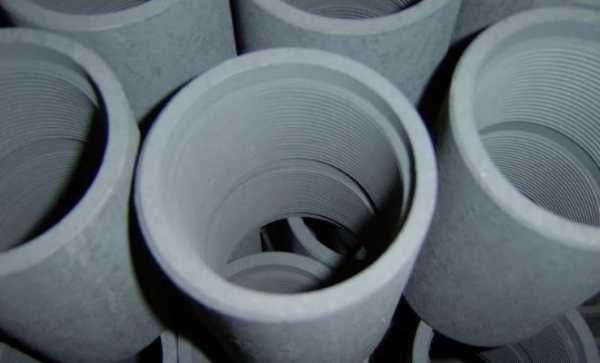
При термодиффузионной обработке детали покрываются равномерном слоем цинка, включая отверстия и внутренние полости
Диффузионному поверхностному цинкованию, выполняемому при термическом воздействии на обрабатываемую деталь, чаще всего подвергают:
- арматуру, применяемую в нефтяной и газовой отраслях;
- ограждающие дорожные и мостовые конструкции;
- элементы трубных коммуникаций и строительную арматуру;
- фурнитуру, используемую для изготовления мебели;
- арматуру, применяемую для укрепления железнодорожного полотна;
- конструктивные элементы автотранспортных средств;
- конструктивные элементы ЛЭП (линии электропередачи).
Термодиффузионное цинкование позволяет получать на поверхности металла цинковый слой минимальной толщины, благодаря чему подвергать такой обработке можно даже детали, отличающиеся очень небольшими размерами.
При повышении температуры обработки по данной технологии до 470° термодиффузия молекул цинка в поверхностный слой металла становится более интенсивной, но полученное в итоге покрытие не обладает требуемыми характеристиками. Оно не только отличается повышенной хрупкостью и легко отслаивается от поверхности изделия, но и не способно обеспечить требуемый уровень антикоррозионной защиты.
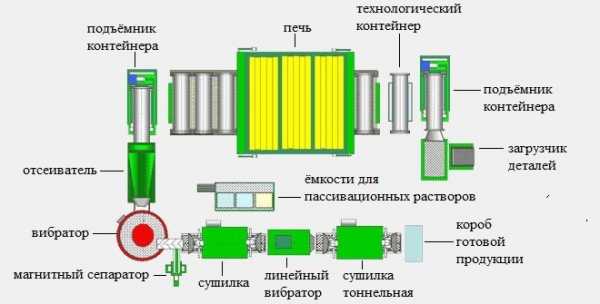
Промышленная линия термодиффузионного цинкования
Чтобы сформировать на поверхности металлического изделия термодиффузионное цинковое покрытие заданной толщины, обладающее высокими защитными характеристиками, необходимо предусмотреть ряд дополнительных процедур.
- Проводится тщательная очистка поверхности изделия, которое будет подвергаться обработке.
- Необходимо обеспечить герметичность контейнера для термодиффузионного цинкования.
- Когда герметичность контейнера обеспечена, в нем необходимо создать инертную или восстановительную среду. Следует иметь в виду, что в окислительной среде цинкование выполнять нельзя.
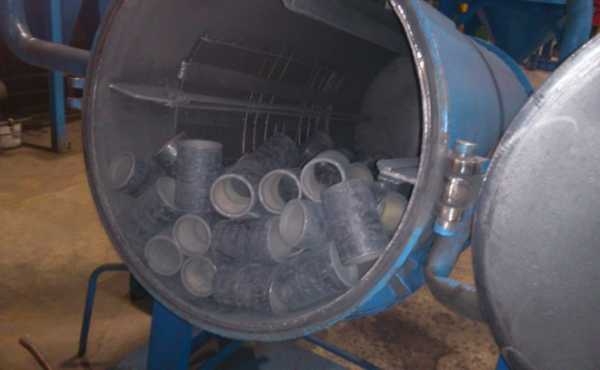
Детали обработаны и загружены в специальную емкость для термодиффузионного цинкования
При выполнении самого термодиффузионного цинкования в рабочую среду желательно вносить специальные флюсующие элементы, которые называют активаторами.
Если придерживаться всех вышеуказанных рекомендаций и строго соблюдать все технологические режимы, то на поверхности металлического изделия можно сформировать термодиффузионное цинковое покрытие, которое будет соответствовать как заданной толщине, так и требуемым защитным характеристикам.
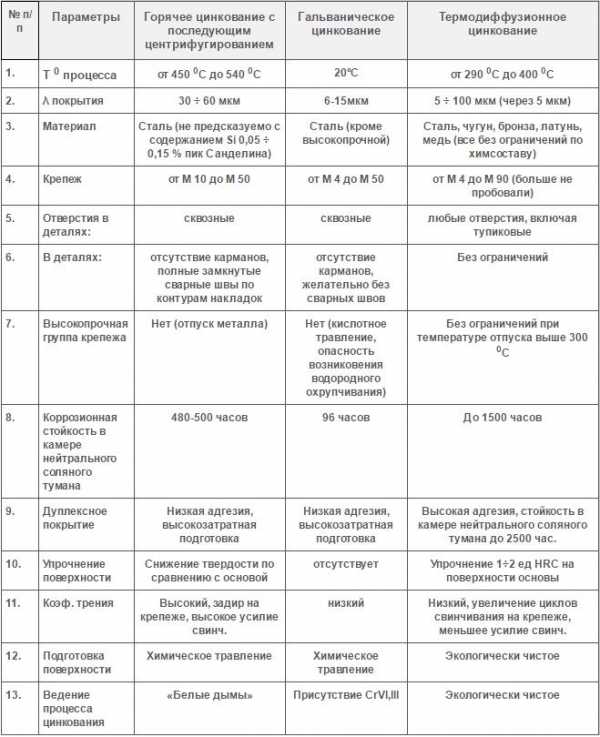
Сравнительный анализ коррозионной стойкости
Алгоритм нанесения термодиффузионного цинкового покрытия выглядит следующим образом.
- Обрабатываемая поверхность тщательно очищается (в производственных условиях для этого используют дробеметные, пескоструйные и ультразвуковые установки).
- Изделие и специальную смесь, за счет которой будет осуществляться насыщение его поверхности цинком, помещают в герметичный контейнер.
- В контейнере создается требуемая температура, при которой и протекает диффузионное поверхностное цинкование.
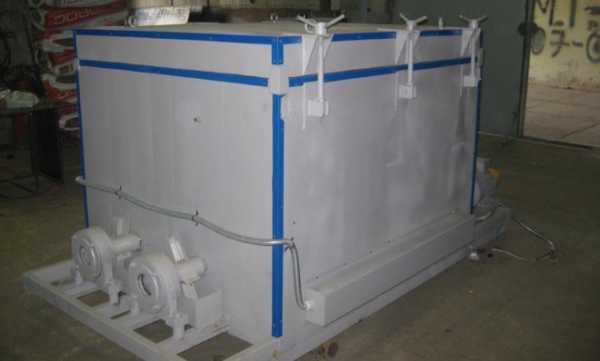
Печь для термодиффузионного цинкования
После окончания цинкования деталь извлекают из контейнера и очищают ее поверхность от остатков использованной смеси. Затем остается выполнить пассивирование уже оцинкованной поверхности и дать ей полностью остыть.
Для выполнения диффузионного поверхностного цинкования используются различные насыщающие смеси, одной из которых является «Левикор». Высокую популярность у отечественных специалистов смесь «Левикор» завоевала благодаря тому, что ее отличает высокая проникающая способность, а ее применение позволяет получать цинковые покрытия требуемой толщины, обладающие исключительными защитными свойствами.
Достоинства и недостатки
Технология цинкования, для реализации которой используется термодиффузия, отличается целым рядом достоинств. Перечислим их.
- Поверхность обработанного изделия и сформированный на ней цинковый слой характеризуются отличной адгезией.
- Данный метод обработки отличается экономичностью, так как для его реализации не требуются большие производственные площади, значительные затраты рабочей силы и электрической энергии.
- Технология термодиффузионного цинкования позволяет получать идеально ровное и однородное по своей толщине покрытие, отличающееся, кроме того, высокими защитными свойствами.
- За счет того, что термодиффузия осуществляется в герметичных контейнерах, данный процесс отличается токсической, химической и экологической безопасностью. При работе с такими установками человек не получит термический ожог, а также не подвергнется воздействию других факторов, которые бы могли негативно отразиться на его здоровье.
- Толщина цинкового слоя при использовании такой технологии хорошо поддается регулировке в достаточно широких пределах.
- Образующиеся в процессе термодиффузионного цинкования отходы легко утилизируются. При этом процесс такой утилизации, выполняемой по стандартной схеме, также не связан с опасностью для человеческого здоровья.
- Для очистки поверхности изделия после термодиффузионного цинкования не используются кислоты и другие агрессивные средства.
- Оборудование, на котором выполняется диффузионное поверхностное цинкование, отличается простотой управления и обслуживания.
- Процедура термодиффузионного покрытия цинком выполняется при более щадящем температурном режиме, если сравнивать ее с другими технологиями нанесения защитных покрытий.
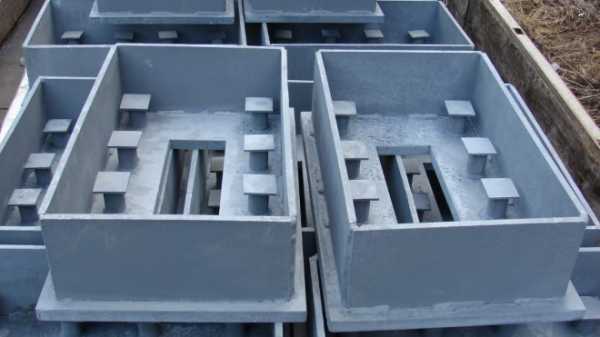
После этого типа цинкования возможна последующая окраска деталей
У данной технологии есть два основных недостатка. Заключаются они в следующем.
- Цинковый слой, формирующийся на поверхности изделия при использовании данной методики, отличается малопривлекательным сероватым цветом. Такая проблема решается путем нанесения на предварительно полученное термодиффузионное цинковое покрытие дополнительного декоративного слоя. Следует, однако, иметь в виду, что возможность нанесения такого слоя не оговаривается положениями ГОСТа. Во многих случаях, когда для оцинкованных металлических изделий эстетический фактор не столь важен, на такой недостаток не обращают внимания.
- Габариты изделий, которые могут быть подвергнуты термодиффузионному цинкованию, серьезно ограничены размерами герметичного контейнера, а также внутренним объемом нагревательной печи.
Требования ГОСТ Р 9.316-2006 к термодиффузионным цинковым покрытиям
В соответствии с положениями нормативного документа, термодиффузионные цинковые покрытия могут быть отнесены к одному из следующих классов:
- 1-й класс – толщиной 6–9 мкм;
- 2-й класс – 10–15 мкм;
- 3-й класс – 16–20 мкм;
- 4-й класс – 21–30 мкм;
- 5-й класс – 40–50 мкм.
Несмотря на то, что в ГОСТе не упомянуты цинковые покрытия большей толщины, потребитель по согласованию с производителем может заказать их нанесение. Однако в таком случае полученное покрытие будет относиться к категории нестандартных.
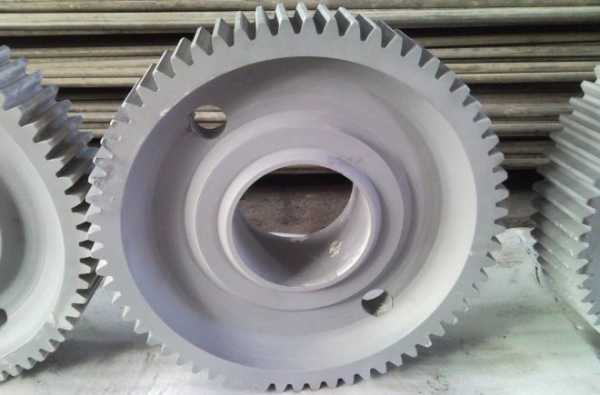
Рассматриваемый метод цинкования позволяет получить качественное цинковое покрытие толщиной 5–100 микрон
Термодиффузионное цинковое покрытие не наносится на те металлические конструкции и изделия, на которых имеются соединения, выполненные при помощи смол или припоя. Нанести цинковый слой на такие детали возможно, но для этого следует применять другие технологии.
В соответствии с положениями ГОСТ, цинковый слой, нанесенный на металлическое изделие по рассматриваемой технологии, не должен иметь следующих дефектов:
- остатков насыщающих смесей, которые не поддаются смыванию;
- вкраплений инородных тел;
- наростов;
- пустот и раковин;
- отслоений;
- трещин на поверхности;
- вздутий;
- даже очень незначительных по площади участков, на которых отсутствует покрытие.
Оценка статьи:
Загрузка...Поделиться с друзьями:
met-all.org
Термодиффузионное цинкование: технология, оборудование
Термодиффузионное цинкование позволяет создать на металлической поверхности некоторый защитный слой, который значительно продлевает срок службы материала.
Особенность цинкового слоя заключается в том, что он обеспечивает как электрохимическую, так и механическую защиту металлической заготовке.
Данный метод достаточно востребован в промышленной сфере, а технология, по которой выполняется термодиффузионное цинкование, успешно испробована на поверхностях различных видов металлов.
Конечно, для того чтобы провести данный вид цинкования материала, потребуется определенное оборудование, для которого высокая температура является рабочей.
Следует отметить, что цинк имеет свойство вступать в химическую реакцию с большим количеством самых разных элементов и является достаточно активным металлом.
Если провести простейшие опыты из школьного курса химии, то можно наблюдать, как при взаимодействии цинка с водой или воздухом поверхность самого металла покроется тонкой пленкой.
Именно таким образом и получают защитное покрытие при помощи термодиффузионного цинкования на поверхностях самых разных видов металлов.
Данная технология используется только в промышленных сферах, так как требуется специальное оборудование и высокая рабочая температура, а также наличие активных смесей.
Особенности процесса
Данный метод достаточно простой, однако требует наличия специального оборудования и определенной рабочей температуры.
Для начала выполняется максимально тщательная очистка той поверхности, которая будет цинковаться.
Если есть на поверхности следы от масла, то они легко удаляются при помощи дигрейзера.
Для того чтобы убрать с материала ржавчину и окалину, необходимо воспользоваться дробометной установкой.
Кроме этого, для удаления грязи с поверхности используют некоторые специфические методы обработки, такие, как пескоструйная или ультратразвуковая.
После того как поверхность станет чистой, ее отправляют на загрузку, и для этого помещают на специальную металлическую тележку.
Также изделие перед обработкой взвешивается. Это делается для того, чтобы правильно определить количество смеси, с помощью которой и будет проводиться данное цинкование.
Видео:
Метод позволяет регулировать количество наносимой смеси в зависимости от количества приготовленного раствора, а также формы и массы детали.
Толщина стандартного слоя для различных типов металлов составляет в среднем около пятидесяти микрон. Технология, несмотря на свою относительную простоту, требует определенных знаний и навыков от исполнителя работ.
Термодиффузионным цинкованием на крупных предприятиях стараются подвергать практически все металлические изделия и заготовки.
После того как заготовка будет очищена и взвешена, ее аккуратно помещают в муфельную печь, непосредственно в которой и происходит само термодиффузионное цинкование.
В некоторых отдельных случаях температура в печи может достигать четырехсот градусов выше нуля.
Сам температурный режим следует подбирать в зависимости от типа заготовки, марки стали и принятых на предприятии стандартов.
Технология предполагает среднее время обработки порядка ста двадцати минут.
На показатели времени нанесения термодиффузионного покрытия цинка влияет, главным образом, мощность используемого оборудования, а также состав используемой смеси.
Данный метод практически невозможно использовать в домашних условиях ввиду того, что требуется специальное оборудование достаточно крупных размеров.
Следует отметить, что в процессе термодиффузионного цинкования необходимо, чтобы контейнер, в который помещены заготовки, находился в непрерывном вращении.
Данный метод предполагает после цинкования обработку поверхности пассивацией.
Такая дополнительная обработка позволяет эффективно защитить металлическую поверхность от воздействия атмосферного воздуха.
Также проводится галтовка, при помощи которой с заготовки удаляются заусеницы.
На завершающем этапе деталь тщательно высушивают.
Плюсы и минусы
При помощи термодиффузионного цинкования можно проводить эффективную обработку целого ряда метизов. Данный метод имеет целый ряд самых разных преимуществ.
В первую очередь, изделия становятся более стойкими к коррозионным процессам, если выдержана требуемая толщина слоя. Кроме этого, покрытие полностью повторяет как контур, так и форму метизов.
За счет термодиффузионного цинкования заготовки приобретают более высокие показатели твердости. Кроме этого, металлы становятся более устойчивыми к абразивному типу разрушений.
Видео:
Технология эффективна для большей части самых разных метизов, притом, что затраты на проведение данного вида цинкования минимальны.
Конечно, необходимое оборудование требует определенных изначальных затрат, однако они достаточно быстро окупаются.
Также к достоинствам данного метода можно отнести высокую адгезию, а также практически полную безопасность в экологическом плане.
Несмотря на огромное количество достоинств термодиффузионного цинкования, данный метод имеет и некоторые недостатки.
Так, данный процесс характеризуется достаточно низкой производительностью по сравнению с другими технологиями цинкования металлов.
Кроме этого, термодиффузионному цинкованию нельзя подвергать различные виды декоративных покрытий.
Это связано с тем, что после проведения данной процедуры первоначальное покрытие приобретет неприятный мышиный цвет.
Следует отметить и то, что после термодиффузионного цинкования образуется большое количество аэрозолей с содержанием цинковой пыли, которая в свою очередь вредна для здоровья.
Несмотря на все недостатки, данная методика достаточно востребована и активно применяется на самых разных крупных предприятиях.
Область применения
Практически на всех крупных промышленных предприятиях, которые работают в сфере обработки металлов, цинкование достаточно востребованный способ защиты металлических изделий.
Он пользуется высоким спросом за счет минимального количества необходимого оборудования и своей относительной простоты.
На выходе изделие приобретает специальный защитный слой, который позволяет значительно продлить его срок службы.
Видео:
Особенно часто его используют для обработки самых разных крепежных систем, использующихся в сфере строительства.
Еще одно преимущество, которое сильно влияет на популярность данного вида защиты, это его дешевизна, а также максимально высокие эксплуатационные свойства, которые приобретает обработанное изделие.
Достаточно активно термодиффузионному цинкованию подвергают различную арматуру, трубы, а также самые разные детали для автомобилей.
Покрытие наносят на поверхность фитингов, а также на полые и резьбовые заготовки самого разного назначения.
Пленка хорошо ложится на детали, которые имеют сквозные и глухие отверстия, а также на самые разные элементы из мебельной фурнитуры.
Достаточно востребован данный вид защитного покрытия при изготовлении железнодорожных и контактных сетей, а также мостовых ограждений.
В настоящее время такая обработка считается наиболее экономически обоснованной и эффективной.
rezhemmetall.ru
Термодиффузионное цинкование: описание и преимущества
Для защиты различных металлоконструкций, металлических изделий (в частности метизов) от коррозии широко применяется покрытие их цинком. Существует масса технологий получения защитного цинкового покрытия. Один из доступных вариантов – шерадизация или термодиффузионное цинкование. Это достаточно новый способ обработки, но несмотря на это, многие специалисты признали его очень перспективным.
Особенности технологии
Термодиффузионное цинкование – это метод, в основе которого лежит физическое явление диффузии легирующей составляющей металла, которая затем переходит на верхний слой изделия или конструкции. Термодиффузия возможна при относительно высоких температурах – от 400 до 470 градусов. В поверхностные слои металла диффузируют молекулы цинка.
Это процесс, при котором молекулы цинка испаряются из цинкосодержащей смеси в специальных контейнерах при высоких температурах, а затем проникают в поверхностный слой металла. В результате образуется слой на основе сложных сплавов цинка и железа.
В результате применения данной технологии на поверхности образуется однородное цинковое покрытие. При этом слой будет однородным даже в местах, в которые доступ затруднен.
Если процесс термодиффузионного цинкования будет проводиться при максимальных температурах, то молекулы покроют поверхность детали более интенсивно. Однако, покрытие не будет иметь нужных характеристик. Такая поверхность отличается не только высокой хрупкостью – слой цинка будет очень легко отслаиваться. Что касается степени антикоррозионной защиты, то он будет очень слабым.
Как происходит процесс обработки?
Технология достаточно проста, но потребуется наличие специального оборудования:
1. Первым делом поверхность тщательно очищают. Если на изделии имеются следы смазывающих материалов, то их легко удалить при помощи специальных составов – дигрейзеров. Для того чтобы удалить с поверхности следы коррозии и окалину, применяют пескоструйную установку. Кроме того, применяется и ультразвуковая чистка.
2. Когда деталь тщательно очищена, она отправляется в специальную тележку. Перед проведением процедуры деталь обязательно взвешивают – это нужно, чтобы точно определить количество состава, с помощью которого и будет проведено нанесение цинкового покрытия. Технология позволяет изменять количество смеси, которая наносится на обрабатываемую поверхность, в зависимости от объема готового раствора, а также от массы, геометрических характеристик детали, ее конструкции.
3. После того как деталь очищена и известен ее вес, она аккуратно помещается в специальную муфельную печь, где непосредственно и осуществляется термодиффузионное цинкование. Температурный режим подбирают исходя от типа обрабатываемой детали, марки сплава и принятых стандартов. Среднее время процесса зависит от мощности оборудования, а также от состава рабочей смеси. В процессе термодиффузии деталь в контейнере постоянно вращается. Толщина цинковой пленки для разных типов металлов составляет в среднем 0,5 мкм.
4. Когда обработка будет окончена, изделия достают и очищают от остатков насыщающих смесей. Цинковые составы могут быть различными. Одна из самых популярных марок такой продукции — «Левикор». Ее широко используют в современной промышленности за счет высокой проникающей способности. «Левикор» позволяет получать защитный цинковый слой различной толщины, при этом уровень защиты от коррозии очень высокий.
Несмотря на относительную простоту, термодиффузионное цинкование требует наличия определенных знаний, а также навыков. В промышленности практически все изделия стараются подвергать именно такой обработке. В домашних условиях использовать данную технологию невозможно ввиду того, что требуется оборудование для термодиффузионного цинкования. Порой оно может достигать огромных размеров.
На видео: пример термодиффузионного покрытия цинком.
Область применения
Чаще всего технология применяется на таких изделиях, как:
- арматура, использующаяся в отраслях добычи газа и переработки нефти;
- ограждающие конструкции;
- элементы трубопроводов, арматура для строительства;
- различные детали мебельной фурнитуры;
- арматура для производства дорожного полотна;
- элементы автомобилей;
- детали ЛЭП;
- большинство метизов.
Преимущества и недостатки
Технология отличается огромным количеством преимуществ:
- Поверхность изделия, подверженного такой обработке, отличается хорошей адгезией.
- Метод очень экономичный, так как при таком цинковании не требуется наличие больших производственных цехов, серьезных затрат ресурса и усилий.
- С помощью обработки получают идеально ровную и однородную поверхность, которая отличается хорошими защитными качествами.
- За счет того, что термодиффузионные процессы проводятся с использованием герметичного оборудования, способ отличается максимальной безопасностью. Люди при работе с оборудованием надежно защищены от термических ожогов, а также других воздействий.
- Толщина защитного покрытия отлично поддается регулировкам в различных пределах.
- Отходы производства легко утилизируются по стандартным схемам утилизации.
- Процесс не требует применения сложного оснащения, а управлять и обслуживать его достаточно просто.
- Процедура проводится при более низких температурных режимах, если сравнивать с другими технологиями.
Любые виды оцинкования – это гарантированная защита металла от коррозионных процессов. Использование термодиффузии делает этот процесс более экономически выгодным, так как не требуется больших затрат ресурсов.
Минусов только два:
- Слой цинка, который формируется посредством диффузии, имеет малопривлекательный серый цвет. Данную проблему решают за счет нанесения на поверхность специального декоративного слоя. Но это никак не оговаривается в ГОСТах и нормативах. В большинстве случаев, когда эстетика не важна, на данный недостаток особого внимания не обращают.
- Габаритные размеры изделий, которые можно обрабатывать таким образом, существенно ограничены параметрами контейнера и его объемами.
Требования к покрытиям
Существует несколько классов покрытий:
- 1-й – от 6 до 9 мкм;
- 2-й – 10-15 мкм;
- 3-й класс – 16-20 мкм;
- 4-й класс -21-30 мкм;
- 5-й класс – 40-50 мкм.
В ГОСТах на данную технологию ничего не упоминается о более толстом покрытии. Но большинство предприятий данную услугу предоставляют. Однако необходимо получить предварительное согласование с заказчиком.
Термодиффузионному воздействию не подергаются те детали, где имеются паяные соединения или любые другие с использованием различных смол. На данных деталях термодиффузионные процессы невозможны.
Также по ГОСТам слой цинка не должен иметь дефектов, а именно:
- остатков насыщающей смеси, которая не смывается;
- инородных вкраплений;
- наростов, раковин и пустот;
- отслоения или вздутия;
- трещин и участков, где отсутствует покрытие.
Данный способ обработки регламентируется следующими документами: ГОСТ Р 9.316-2006. Можно подробней ознакомиться с ним при необходимости. Также следует знать, что в 2008 году утвердили новые стандарты на нанесение цинковых покрытий на метизы.
Что говорит специалист (1 видео)
Оцинкованный металл (20 фото)
gidpokraske.ru
технология процесса нанесения цинкового покрытия, используемое оборудование
Цинкование давно используется для защиты металлов от воздействия атмосферных и агрессивных сред. Разработано множество способов нанесения цинкового слоя. Но сравнительно недавно стала применяться технология термодиффузионного цинкования. Кроме коррозионной защиты, обработанные детали стойки к механическим и электрохимическим повреждениям.
Суть процесса
Термодиффузия представляет собой процесс проникновения атомов цинка в поверхностный слой металла, происходящий под действием высокой температуры в восстановительной или инертной газовой среде.
Рабочая температура зависит от толщины покрытия и варьируется в пределах 280°С-470°С. Внедряясь, в кристаллическую решетку металла,
цинк создает на поверхности защитный слой толщиной в несколько микрон. Процесс протекает в газовой среде водорода.
Толщина покрытия регламентируется государственным стандартом. Согласно ГОСТ Р 9.316-2006 толщина покрытия делится на пять классов:
- 6…9 мкм;
- 10…15 мкм;
- 16…20 мкм;
- 21…30 мкм;
- 40…50 мкм.
Выбор в качестве антикоррозионной защиты пал на цинк неслучайно. Находясь на стальной поверхности, он распространяется по ней со скоростью 2 мм в год, но при температуре окружающей среды 70 °С. Такое свойство позволяет затягивать поверхностные микроповреждения.
Практика показывает, что этот способ более перспективен и имеет свои достоинства.
Технология процесса
Термодиффузионное цинкование технологический процесс которого разбит на шесть последовательных операций. Строгое следование по маршруту залог получения качественного результата.
-
Подготовительный. На этапе подготовки детали подвергаются пескоструйной или ультразвуковой очистке от окалины, ржавчины. Удаление жировых загрязнений осуществляется ацетоном. Если деталь имеет большие размеры возможна дробеструйная обработка.
- Загрузка контейнера. Очищенные и высушенные детали помещаются в герметичный контейнер. Для насыщения внутреннего объема цинком и водородом добавляется насыщающая смесь. Большой популярностью пользуется «Левикор». От количества смеси зависит толщина слоя покрытия. После тщательного перемешивания контейнеры герметизируются и помещаются в печь.
- Процесс насыщения. Температура процесса насыщения зависит от типа сплава и его марки. В среднем процесс длится 60–90 минут. В течение всего времени нагревающая установка вращается, обеспечивая перемешивание деталей с насыщающей смесью.
- Выгрузка и очистка. После окончания процесса насыщения производится выгрузка деталей. Удаление остатков насыщающей смеси.
- Пассивирование. Эта операция предназначена для защиты покрытия от окислительного воздействия воздушной среды. Изделия, предназначенные для окрашивания, подвергаются обработке однократно. Те, что не окрашиваются, обрабатываются два раза. После каждого пассивирования следует промывка.
- Сушка. Во время сушки удаляется влага, и детали остывают.
Достоинства и недостатки
На протяжении применения метода антикоррозионной защиты были выявлены характерные для него черты. Термодиффузионное цинковое покрытие обладает рядом достоинств, среди которых выделяются:
-
высокая адгезия за счет того, что микронеровности поверхности не исчезают;
- экономичность: низкие затраты на подготовку и электроэнергию, малое количество производственных площадей и обслуживающего персонала;
- толщина покрытия равномерна по всей площади изделия;
- экологичность процесса;
- регулирование толщины при образовании защитного покрытия;
- повышение твердости на поверхности;
- минимальные затраты;
- невысокая себестоимость;
- простое в обслуживании оборудование;
- невысокая температура не меняет внутреннюю структуру металла;
- для очищения не используются химические реактивы;
- получаемые отходы утилизируются естественным способом.
На фоне достоинств у метода есть и недостатки:
- в отличие от других методов нанесенное покрытие имеет матовый серый цвет;
- невысокая производительность;
- габариты обрабатываемых изделий ограничиваются размерами объемами оборудования.
Оцинкование деталей различными методами и проведенный сравнительный анализ показал следующие данные.
Сфера использования
Этот способ обработки создает однородный слой даже в труднодоступных местах. Микронная толщина слоя позволяет обрабатывать мелкие детали. Термодиффузионному цинкованию подвергают:
-
арматуру для нефтяной, газовой, строительной и железнодорожной отраслей;
- ограждения мостов, дорог;
- метизы;
- мебельную фурнитуру;
- фитинги;
- конструкции ЛЭП;
- элементы автомобилей.
Оборудование для термодиффузионного цинкования
В промышленных масштабах производимое термодиффузионное цинкование оборудование используется механизированное, а сам процесс максимально автоматизирован. Используемые агрегаты:
-
загрузчик деталей и насыщающего состава;
- конвейер, подающий контейнеры к печи;
- вращающаяся печь;
- выгружающий конвейер;
- отсеиватель;
- вибратор;
- сепаратор магнитный;
- емкости для пассивирования и промывки;
- сушилки;
- приемник готовой продукции.
Требования к защитному слою
К покрытию предъявляются строгие требования. ГОСТ предусматривает отсутствие следующих дефектов на поверхности деталей после термодиффузионного цинкования:
-
выпуклостей;
- отслоений;
- трещин;
- пригоревших остатков;
- пустот;
- раковин;
- сторонних вкраплений;
- отсутствия покрытия.
В современных условия этот вид антикоррозионной защиты считается эффективным и экономически целесообразным.
Оцените статью: Поделитесь с друзьями!remoskop.ru
технология, оборудование, плюсы и минусы
Термодиффузионное цинкование: описание и преимущества
Для защиты различных металлоконструкций, металлических изделий (в частности метизов) от коррозии широко применяется покрытие их цинком. Существует масса технологий получения защитного цинкового покрытия. Один из доступных вариантов – шерадизация или термодиффузионное цинкование. Это достаточно новый способ обработки, но несмотря на это, многие специалисты признали его очень перспективным.
Особенности технологии
Термодиффузионное цинкование – это метод, в основе которого лежит физическое явление диффузии легирующей составляющей металла, которая затем переходит на верхний слой изделия или конструкции. Термодиффузия возможна при относительно высоких температурах – от 400 до 470 градусов. В поверхностные слои металла диффузируют молекулы цинка.
Это процесс, при котором молекулы цинка испаряются из цинкосодержащей смеси в специальных контейнерах при высоких температурах, а затем проникают в поверхностный слой металла. В результате образуется слой на основе сложных сплавов цинка и железа.
В результате применения данной технологии на поверхности образуется однородное цинковое покрытие. При этом слой будет однородным даже в местах, в которые доступ затруднен.
Если процесс термодиффузионного цинкования будет проводиться при максимальных температурах, то молекулы покроют поверхность детали более интенсивно. Однако, покрытие не будет иметь нужных характеристик. Такая поверхность отличается не только высокой хрупкостью – слой цинка будет очень легко отслаиваться. Что касается степени антикоррозионной защиты, то он будет очень слабым.
Как происходит процесс обработки?
Технология д
pellete.ru
технология процесса нанесения цинкового покрытия, используемое оборудование
Цинкование давно используется для защиты металлов от воздействия атмосферных и агрессивных сред. Разработано множество способов нанесения цинкового слоя. Но сравнительно недавно стала применяться технология термодиффузионного цинкования. Кроме коррозионной защиты, обработанные детали стойки к механическим и электрохимическим повреждениям.
Суть процесса
Термодиффузия представляет собой процесс проникновения атомов цинка в поверхностный слой металла, происходящий под действием высокой температуры в восстановительной или инертной газовой среде.
Рабочая температура зависит от толщины покрытия и варьируется в пределах 280°С-470°С. Внедряясь, в кристаллическую решетку металла,
цинк создает на поверхности защитный слой толщиной в несколько микрон. Процесс протекает в газовой среде водорода.
Толщина покрытия регламентируется государственным стандартом. Согласно ГОСТ Р 9.316-2006 толщина покрытия делится на пять классов:
- 6…9 мкм;
- 10…15 мкм;
- 16…20 мкм;
- 21…30 мкм;
- 40…50 мкм.
Выбор в качестве антикоррозионной защиты пал на цинк неслучайно. Находясь на стальной поверхности, он распространяется по ней со скоростью 2 мм в год, но при температуре окружающей среды 70 °С. Такое свойство позволяет затягивать поверхностные микроповреждения.
Практика показывает, что этот способ более перспективен и имеет свои достоинства.
Технология процесса
Термодиффузионное цинкование технологический процесс которого разбит на шесть последовательных операций. Строгое следование по маршруту залог получения качественного результата.
Подготовительный. На этапе подготовки детали подвергаются пескоструйной или ультразвуковой очистке от окалины, ржавчины. Удаление жировых загрязнений осуществляется ацетоном. Если деталь имеет большие размеры возможна дробеструйная обработка.
- Загрузка контейнера. Очищенные и высушенные детали помещаются в герметичный контейнер. Для насыщения внутреннего объема цинком и водородом добавляется насыщающая смесь. Большой популярностью пользуется «Левикор». От количества смеси зависит толщина слоя покрытия. После тщательного перемешивания контейнеры герметизируются и помещаются в печь.
- Процесс насыщения. Температура процесса насыщения зависит от типа сплава и его марки. В среднем процесс длится 60–90 минут. В течение всего времени нагревающая установка вращается, обеспечивая перемешивание деталей с насыщающей смесью.
- Выгрузка и очистка. После окончания процесса насыщения производится выгрузка деталей. Удаление остатков насыщающей смеси.
- Пассивирование. Эта операция предназначена для защиты покрытия от окислительного воздействия воздушной среды. Изделия, предназначенные для окрашивания, подвергаются обработке однократно. Те, что не окрашиваются, обрабатываются два раза. После каждого пассивирования следует промывка.
- Сушка. Во время сушки удаляется влага, и детали остывают.
Достоинства и недостатки
На протяжении применения метода антикоррозионной защиты были выявлены характерные для него черты. Термодиффузионное цинковое покрытие обладает рядом достоинств, среди которых выделяются:
высокая адгезия за счет того, что микронеровности поверхности не исчезают;
- экономичность: низкие затраты на подготовку и электроэнергию, малое количество производственных площадей и обслуживающего персонала;
- толщина покрытия равномерна по всей площади изделия;
- экологичность процесса;
- регулирование толщины при образовании защитного покрытия;
- повышение твердости на поверхности;
- минимальные затраты;
- невысокая себестоимость;
- простое в обслуживании оборудование;
- невысокая температура не меняет внутреннюю структуру металла;
- для очищения не используются химические реактивы;
- получаемые отходы утилизируются естественным способом.
На фоне достоинств у метода есть и недостатки:
- в отличие от других методов нанесенное покрытие имеет матовый серый цвет;
- невысокая производительность;
- габариты обрабатываемых изделий ограничиваются размерами объемами оборудования.
Оцинкование деталей различными методами и проведенный сравнительный анализ показал следующие данные.
№ п.п. | Метод цинкования | |||
Горячее | Гальваническое | Термодиффузионное | ||
1 | Температурный режим протекания процесса, °С | 450–540 | 20 | 280–470 |
2 | Толщина нанесенного слоя, мкм | 30–60 | 6–15 | 5–100 |
3 | На какой материал наносится | Сталь с незначительным содержанием кремния | Сталь (ограничение для высокопрочных марок) | Черные металлы и сплавы на основе меди |
4 | Размер обрабатываемых метизов | М10–50 | М4–50 | М4–90 |
5 | Типы обрабатываемых отверстий | Сквозные | Сквозные | Сквозные, глухие |
6 | Ограничения по обработке | Карманы, сплошные сварные швы | Карманы, отсутствие сварных швов | Без ограничений |
7 | Закаленный крепеж | Не подлежит обработке (температура протекания процесса близка к низкому отпуску) | Не подлежит обработке (кислотная обработка, повышение водородной хрупкости) | Без ограничений |
8 | Стойкость к солям (лабораторный тест), час | 500 | 96 | 1500 |
9 | Свойства покрытия | Сниженная адгезия, ресурсозатратная подготовка | Сниженная адгезия, ресурсозатратная подготовка | Адгезия высокая |
10 | Твердость | Снижается | Отсутствует | Плюс 1…2 HRC |
11 | Коэффициент трения | Повышенный | Пониженный | Пониженный при выкручивании |
12 | Подготовка к нанесению покрытия | Химическая | Химическая | Нейтральная |
13 | Испарения вовремя цинкования | Обильное дымовыделение | Выделение хрома | Отсутствие дымовыделения |
Сфера использования
Этот способ обработки создает однородный слой даже в труднодоступных местах. Микронная толщина слоя позволяет обрабатывать мелкие детали. Термодиффузионному цинкованию подвергают:
арматуру для нефтяной, газовой, строительной и железнодорожной отраслей;
- ограждения мостов, дорог;
- метизы;
- мебельную фурнитуру;
- фитинги;
- конструкции ЛЭП;
- элементы автомобилей.
Оборудование для термодиффузионного цинкования
В промышленных масштабах производимое термодиффузионное цинкование оборудование используется механизированное, а сам процесс максимально автоматизирован. Используемые агрегаты:
загрузчик деталей и насыщающего состава;
- конвейер, подающий контейнеры к печи;
- вращающаяся печь;
- выгружающий конвейер;
- отсеиватель;
- вибратор;
- сепаратор магнитный;
- емкости для пассивирования и промывки;
- сушилки;
- приемник готовой продукции.
Требования к защитному слою
К покрытию предъявляются строгие требования. ГОСТ предусматривает отсутствие следующих дефектов на поверхности деталей после термодиффузионного цинкования:
выпуклостей;
- отслоений;
- трещин;
- пригоревших остатков;
- пустот;
- раковин;
- сторонних вкраплений;
- отсутствия покрытия.
В современных условия этот вид антикоррозионной защиты считается эффективным и экономически целесообразным.
obrabotkametalla.info
Термодиффузионное цинковое покрытие — Википедия Переиздание // WIKI 2
Покрытия термодиффузионные цинковые (ТДЦ)
Определения
Впервые этот метод был применен в Англии в начале XX века и получил название «шерардизация» (по фамилии изобретателя — Шерард (Sherard Cowper-Coles)).
Термодиффузионное цинковое покрытие является анодным по отношению к чёрным металлам и электрохимически защищает сталь. Оно обладает прочным сцеплением (адгезией) с основным металлом за счет взаимной диффузии железа и цинка в поверхностных интерметаллидных фазах Zn-Fe, поэтому покрытие мало подвержено отслаиванию или скалыванию при ударах, механических нагрузках и деформациях обработанных изделий.
Преимущество термодиффузионной технологии покрытий по сравнению с гальваническими состоит не только в её превосходстве по коррозионной стойкости, но и в том, что она не вызывает водородного охрупчивания металла.
Термодиффузионное цинковое покрытие в точности повторяет контуры изделий, оно однородно по толщине на всей поверхности, включая изделия сложной формы и резьбовые соединения.
Суть технологии термодиффузионного цинкового покрытия состоит в том, что антикоррозионное покрытие формируется в результате насыщения цинком поверхности металлических изделий в порошковой среде при температуре 290-450 °C, причем выбор температурного режима зависит от типа стальных изделий, марки стали и требований производителей деталей. Такая технология позволяет получить любую толщину покрытия в диапазоне от 6 до 100 микрон по требованию заказчика без изменения технологического процесса. Процесс происходит в закрытом контейнере с добавлением к обрабатываемым деталям специальной насыщающей смеси. Пассивация (финишная обработка деталей) предназначена для предотвращения образования желтых или белых продуктов коррозии на поверхностях, подвергаемых воздействию атмосфер с высокой влажностью, соленой воды, морских атмосфер или циклам конденсации и высыхания.
Защита металлов от коррозии
Защита металлов от коррозии обеспечивает долговременное функционирование различных деталей, конструкций и сооружений. Около 10% выпускаемых годового выпуска стали и стальных изделий ежегодно теряют свои технические характеристики из-за коррозии, что оценивается десятками миллиардов долларов. Один из наиболее распространенных способов защиты металлов от коррозии — покрытие цинком. Выбор цинка не случаен и объясняется высоким отрицательным значением окислительно-восстановительного потенциала пары Zn2+/Zn. Этот металл защищает основной металл (железо) анодно, то есть в гальванической паре «Fe-Zn» растворяется цинк. Электрохимической альтернативой цинку является кадмий, но его применение во многих странах запрещено из-за высокой токсичности. В РФ кадмирование имеет ограниченное использование и возможно, как правило, только по специальному разрешению. Толщина защитного цинкового покрытия выбирается в зависимости от назначения изделия и условий его эксплуатации. Анализ условий применения различных металлоизделий показывает, что защитное (антикоррозионное) покрытие для этих условий должно обладать не только повышенной коррозионной стойкостью, но быть также устойчивым к абразивному износу и иметь высокую степень сцепления с поверхностью защищаемого изделия.
Методы антикоррозионной защиты
Гальванические (электролитические) покрытия. Покрытия на поверхность изделий наносят в растворах электролитов под действием электрического тока. Основными компонентами этих электролитов являются соли цинка. Гальванический способ защиты металлоизделий имеет низкую коррозионную стойкость (около 140 часов в камере нейтрального соляного тумана), не позволяет нанести покрытие на изделия сложной конфигурации, при подготовке поверхности к оцинкованию на высокопрочных изделиях вызывает водородное охрупчивание, не позволяет производить демонтаж металлоизделий, имеет низкую степень сцепления с поверхностью. Данный вид защиты несет, скорее, декоративную функцию.
Металлизационные покрытия. Покрытия наносят путём распыления струей воздуха или горячего газа расплавленного цинка. В зависимости от способа напыления используют цинковую проволоку (пруток) или порошок цинка. В промышленности используют газопламенное напыление и электродуговую металлизацию.
Цинконаполненные покрытия. Эти покрытия представляют собой композиции, состоящие из связующего и цинкового порошка. В качестве связующих используют различные синтетические смолы (эпоксидные, фенольные, полиуретановые и др.), лаки, краски, полимеры. Проявляют скорее свойства лакокрасочных, чем металлических покрытий.
Горячее цинкование. Как правило, горячее цинковние применяют для защиты от коррозии крупных металлоконструкций. Оцинкование мелких деталей и деталей с резьбой не дает необходимого качества оцинкованной поверхности. После обезжиривания, промывки, травления и повторной промывки, детали в барабане окунают в ванну (обычно керамическую) с расплавленным цинком. Вращением барабана обеспечивают поток цинковой массы относительно деталей для заполнения всех пор и микротрещин. Затем барабан вынимают из ванны и раскручивают для удаления излишков цинка центрифугированием. На деталях образуются наплывы, на внутренних резьбах остаются излишки цинка, резьбу приходится протачивать, снимая таким образом защитный цинковый слой, что в дальнейшем вызывает коррозию. Данный способ неприменим для мелких деталей, например для метрических крепежных изделий. Не применим для деталей из высокопрочной и легированной стали.
Термодиффузионные цинковые покрытия позволяют защищать от коррозии детали из любых марок стали, в том числе высокопрочных, и чугуна без изменения свойств основного металла, детали сложной конфигурации с отверстиями, детали в сборе, сварные и резьбовые. Ограничение размера деталей размером контейнера.
Комбинированные покрытия представляют собой комбинацию цинкового покрытия, лакокрасочного или полимерного. В мировой практике такие покрытия известны как «дуплекс-системы». В таких покрытиях сочетается электрохимический защитный эффект цинкового покрытия с гидроизолирующим защитным эффектом лакокрасочного или полимерного. Следует отметить, что гальванические и металлизационные цинковые покрытия не содержат интерметаллидных соединений (фаз) и состоят из цинка соответствующего химического состава. Горячецинковые покрытия, получаемые методом горячего цинкования (из расплава цинка) и диффузионные покрытия, наносимые из порошковых смесей на основе цинка, имеют аналогичный механизм образования — диффузионный. Однако диффузия цинка в металл различна: с применением горячецинкового покрытия диффузия составляет 0,1÷3%, термодиффузионного цинкования — 50÷70%. В соответствии с диаграммой состояния системы Fe—Zn в структуре этих покрытий присутствует ряд аналогичных фаз (интерметаллических соединений). Однако общее строение этих покрытий все-таки различно, также как их свойства.
Процесс нанесения термодиффузионного цинкового покрытия (ТДЦ)
Процесс нанесения покрытия представляет собой замкнутый технологический цикл, разбитый на несколько операций:
1-й этап: предварительная механическая очистка с помощью дробеметной установки; 2-й этап: загрузка очищенных деталей в контейнер; добавление насыщающей смеси; 3-й этап: проведение термодиффузионного процесса, обеспечивающего нанесение на покрываемую поверхность деталей цинкового слоя; 4-й этап: разгрузка деталей из контейнера с одновременной очисткой их от остатков насыщающей смеси и пассивирование. 5-й этап: остывание готовой продукции. Детали, предназначенные для нанесения следующих видов покрытий (краски, склейки, пластифицирование и др.), как правило, пассивируются 1 раз. Во всех других случаях проводятся две пассивационные операции, с промежуточной промывкой деталей. Для получения качественного антикоррозионного покрытия все технологические этапы имеют одинаково важное значение и являются равными составляющими технологического процесса. Следует отметить, что технология нанесения покрытия не делает исключения ни для одного вида деталей, которые по своим размерам, весу и конфигурации входят в технологический контейнер оборудования, принятого на вооружение в данный момент. Оборудование, предназначенное для обработки деталей другого размера, выполняется на заказ. Соответственно на этапе выработки технического задания определяется габаритный размер контейнера и печей, а также мощность остальных агрегатов в линии, пропускная способность дробемета, пассивационных установок и сушки. Этап подготовки поверхности включает в себя ультразвуковую, дробемётную или пескоструйную очистку деталей, которая особенно важна для металлоизделий, имеющих на себе окалину после термической обработки во время производства.
Технические преимущества
Первое — это способность технологического процесса получить любую толщину покрытия по требованию заказчика. Второе — отсутствие склеивания деталей. Это один из самых негативных моментов, имеющих место в горячем цинке и в гальванике. Третье преимущество касается внешней и внутренней формы деталей. Российский рынок показал, что большинство крепежных и любых других вспомогательных деталей раньше красилось, пластифицировалось или просто оставалось без покрытия, так как они имели резьбовые соединения, полые и глухие отверстия, сложные соединения, сварные швы. Плюсом также является отсутствие каких-либо наплывов цинка в местах углублений или соединений. Четвёртое преимущество относится к возможности последующей обработки деталей разными видами красок, пластификаторов и т. п. Практически все виды промышленных красок хорошо прилегают к термодиффузионному покрытию. Высокая адгезия увеличивает коррозионную стойкость, практически исключается вздутие и отслоение красок с поверхности. Срок службы деталей с двойным покрытием увеличивается, что приводит к значительной экономии при их эксплуатации. Пятое преимущество состоит в экологической чистоте процесса (если нет необходимости в обезжиривании изделия).
Нормы и стандарты
В декабре 2003 года Департаментом электрификации и электроснабжения ОАО «Российские железные дороги» была выпущена инструкция по применению термодиффузионного цинкования деталей и конструкций контактной сети. Данная инструкция распространяется на защитные цинковые покрытия, наносимые методом термодиффузионного цинкования на резьбовые детали, арматуру, конструкции контактной сети и другие изделия из углеродистой и низкоуглеродистой стали, в том числе повышенной прочности, на чугунные и детали из цветных металлов контактной сети, включая чугунные оконцеватели фарфоровых изоляторов. C января 2008 года вышли ГОСТы на высокопрочный крепеж для металлических конструкций, в которых есть указание на применение термодиффузионного покрытия для защиты от коррозии высокопрочных болтов, гаек и шайб.
См. также
Примечания
Литература
- ГОСТ 9.316-2006 «Единая система защиты от коррозии и старения. Покрытия термодиффузионные цинковые. Общие требования и методы контроля».
- ГОСТ 52643-2006 «Болты и гайки высокопрочные и шайбы для металлических конструкций. Общие технические условия».
Ссылки
- ЗАЩИТНЫЕ ЦИНКОВЫЕ ПОКРЫТИЯ: СОПОСТАВИТЕЛЬНЫЙ АНАЛИЗ СВОЙСТВ, РАЦИОНАЛЬНЫЕ ОБЛАСТИ ПРИМЕНЕНИЯ. Е. Проскуркин ГП «НИТИ», Украина журнал «Национальная металлургия» сентябрь, октябрь 2005 г. http://www.nmet.ru/a/2005/10/03/153.html
wiki2.org