Методика ультразвукового контроля сварных швов. Ультразвуковой контроль
метод контроля сварных соединений, швов
Сварные соединения и швы требуют постоянного контроля качества, вне зависимости от давности установки. Проверка производится с помощью различных методов, наиболее точным является ультразвуковой контроль. Методика проверки сварных швов используется с начала прошлого столетия, пользуется популярностью ввиду точных показателей, выявления малейших недочетов. Как показывает практика, внутри сварочного шва могут быть скрытые дефекты, которые напрямую влияют на качество соединения, ультразвуковая дефектоскопия помогает выявить мельчайшие детали, недостатки.
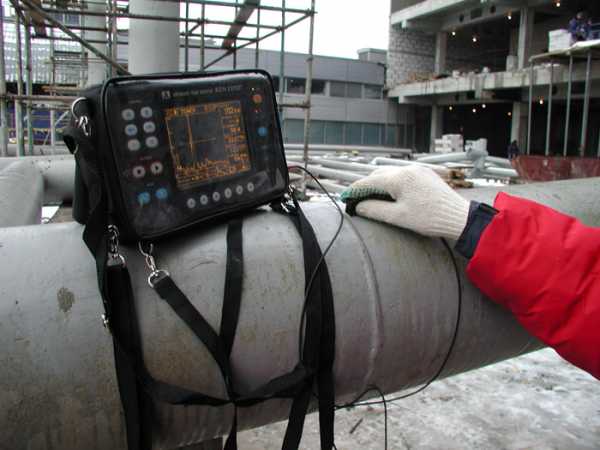
Ультразвуковая дефектоскопия
Ультразвуковой метод и его технология
Технология ультразвукового контроля используется производством, промышленностью с момента развития радиотехнического процесса. Эффект и устройство технологии в том, что ультразвуковые волны акустического типа не меняют прямолинейную траекторию движения при прохождении однородной среды. Ультразвуковой метод используется также при проверке металлов и соединений, имеющих различную структуру. Такие случаи подразумевают, что происходит частичный процесс отражения волн, зависит от химических свойств металлов, чем больше сопротивление звуковых волн, тем сильнее воздействует эффект отражения.
Дефектоскопия или ультразвуковой контроль не разрушают соединения по структуре. Технология проведения ультразвуковой диагностики включает поиск структур, не отвечающих по химическим или физическим свойствам показателям, любые отклонения считаются дефектом. Показания колебаний рассчитываются по формуле L=c/f, где L описывает длину волны, Скорость перемещения ультразвуковых колебаний, f частоту колебаний. Определение дефекта происходит по амплитуде отраженной волны, тем самым возможно вычислить размер недочета.
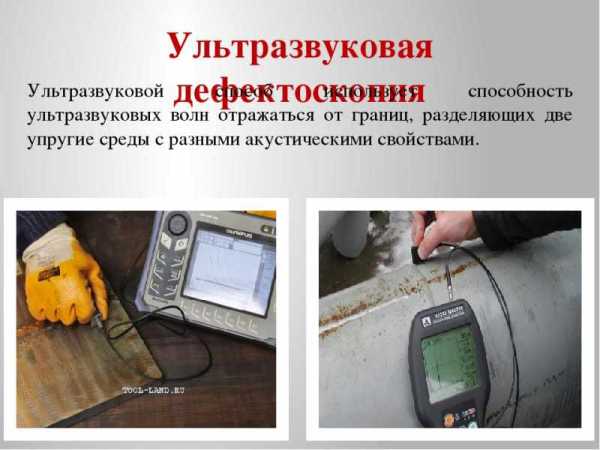
Процесс ультразвукового метода
Сварные соединения подразумевают работу с наличием газовых ванн, испарения которых не всегда успевают удалиться в окружающую среду. Ультразвуковой метод контроля позволяет выявить газообразные вещества в сварных соединениях, за счет сопротивления волн. Газообразная среда веществ обладает сопротивлением в пять раз меньшим по отношению к кристаллической решетке металлических материалов. Ультразвуковой контроль металла позволяет вывить среды за счет отражения колебаний.
Получение и свойства ультразвуковых колебаний
Акустические волны или ультразвуковые колебания выдаются при частоте, превышающей параметр 20 кГц. Механические колебания, способные рассеиваться при упругих, твердых средах, диапазон, как правило, составляет 0,5 – 10 МГц. Распространение волн структурой металла происходит акустическими ультразвуковыми волнами, воздействующими на равновесие центральной точки.
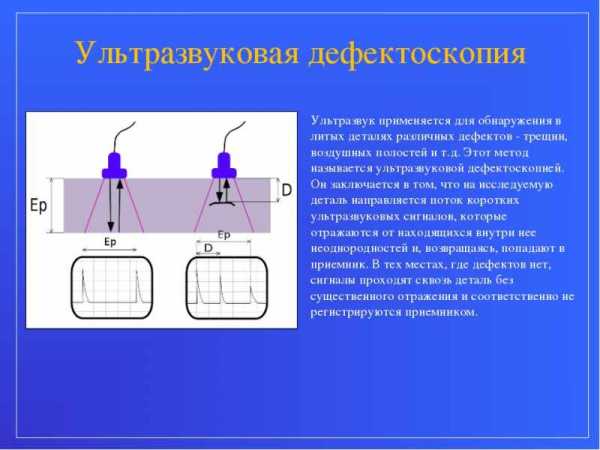
Методика ультразвукового метода
Существуют несколько способов ультразвукового неразрушающего контроля, наиболее распространенный из них пьезоэлектрический. Заряженная электричеством с определенной частотой пластинка вибрирует, механические колебания передаются в окружающую среду при состоянии волны. Генераторы электро волны используется вне зависимости от предназначения, размеров оборудования, могут выдавать различные параметры.
Скорость обращения ультразвукового контроля напрямую зависит от свойств, типа физической среды. Скорость распространения продольной волны вдвое выше, чем поперечной. Прием информации происходит пластиной из пьезоэлектрического элемента, работающей на преобразование энергии в импульсную энергию. Процессом применяются короткие переменные импульсы различного типа колебаний, что позволяет определить глубину, свойства дефекта.
Углы направления ультразвуковых колебаний
На границе разделения двух сред, результатом падения продольной акустической волны при наклонном типе является появление отражения и трансформации ультразвуковых волн. Существуют основные типы контроля:
- отраженные;
- преломлённые;
- сдвиговые поперечные;
- продольные волны.
Процесс происходит путем разделения падающей под углом волны на поперечную и продольную, распространение которых производится непосредственно материалом.
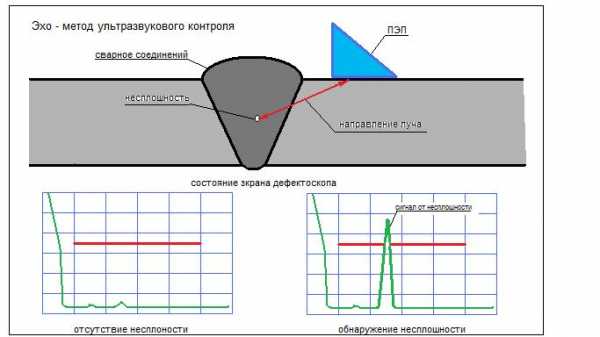
Углы направления ультразвуковых колебаний
Существует определенное значение угла подачи, направления ультразвуковых колебаний, при нарушении которого, ультразвуковой контроль не будет распространяться вглубь металла, а останется на его поверхности. Данный метод используется при определенных параметрах и задачах, волна двигается только по поверхности материала, что позволяет контролировать качество сварного шва.
Виды ультразвукового контроля
Операция контроля сварного шва позволяет определить расстояние до дефекта по временной шкале распространения отражения, размер амплитуды, ширины акустической волны.
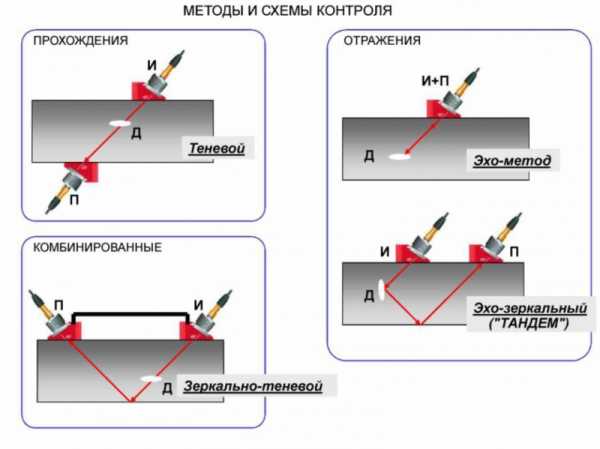
Методы контроля
В настоящем времени существует несколько способов, которыми проводится ультразвуковой контроль, основанием служит ГОСТ-23829, основные отличия происходят в оценке, регистрации данных:
- Диагностика теневым методом производится с использованием двух инструментов, установленных по разные стороны материала. Предназначение первого – излучать волны, второго принимать. Устанавливаются по перпендикулярной плоскости исследуемого сварного соединения. Процесс происходит путем излучения, контроля приема отражений, при тех случаях, когда возникает глухая зона, это означает, что результатом соединении имеется участок другой среды, шов принимается дефектным участком.
- Эхо — импульсный метод применяет один дефектоскоп, параметрами которого обусловлено направление, прем ультразвукового контроля. Технология отражения происходит путем отсвечивания отражения от участков с дефектами. Когда допускается прохождение волн напрямую, участок считается нормальным, если происходит отражение, возврат волны к дефектоскопу, это место помечается как дефект.
- В эхо — зеркальном методе используется такой же принцип работы, что и способом, приведенным выше. Отличительной особенностью является применение отражателя. Устанавливается оборудование под прямым углом, волны посылаются к материалу, в случае наличия повреждений отражаются на приемник. Данный тип проверки зачастую используют при поиске трещин, других вертикальных дефектов.
- Симбиоз зеркального и теневого метода контроля использует два прибора. Оба устанавливаются с одной стороны объекта, посылаются косые волны. Отражение происходит от сетки основного металла, в случае выявления нестандартных зон, место маркируется как дефект.
- В основе дельта метода ультразвукового контроля происходит излучение дефектом направленных отражений внутрь сварного шва. Волны разделяются на подкатегории зеркальных, трансформируемых, продольных и поперечных, приемником удается поймать не все типа волн. Метод не славится популярностью, т.к. требует настройки оборудования, продолжительной расшифровки результатов. Также при контроле дельта методом предъявляются жесткие требования по качеству очистки сварного соединения.
Наиболее популярными являются теневой и эхо – импульсный методы, остальные реже ввиду требуемой настройки оборудования и неудобного использования инструментов.
Как проводится ультразвуковая дефектоскопия
Процесс проверки ультразвуковым оборудованием относится практически ко всем типам металлов, чугуне, меди, стали и других легированных соединениях.
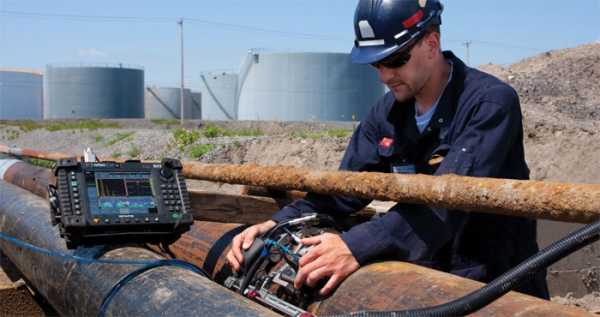
Проведение дефектоскопии ультразвуковым методом
Существует определенный стандарт выполнения проверочных работ, которому необходимо придерживаться:
- зачищается ржавчина, лакокрасочное покрытие со шва на расстоянии 5-7 см;
- для получения достоверных результатов при ультразвуковом контроле сварных соединений, поверхности необходимо обработать турбинным, трансформаторным, либо машинным маслом;
- контролер или прибор подстраивается под определенные параметры проверки;
- стандартные настройки применяются при толщине сварного шва не более 2 см;
- более толстые детали требуют применения АРД диаграмм;
- проверка качества шва выполняется с помощью AVG или DSG параметров;
- излучатель аппарата ультразвукового контроля перемещается вдоль шва зигзагом, проворачивается вокруг своей оси на небольшой угол;
- искатель проводится по материалу до выявления максимально четкого, устойчивого сигнала, после чего разворачивается для поиска максимальной амплитуды;
- контроль, проверку ультразвуковой дефектоскопии сварных швов производят согласно ГОСТу;
- отклонения, дефекты прописываются в регистрационную таблицу.
Сварочные швы основываются на контроле, достаточным проверкой УЗД. При соответствующей квалификации оператора, правильно настроенном оборудовании, возможно получить исчерпывающий ответ о наличии дефектов. При тех случаях, когда применяются более подробные исследования сварных швов, используют гамма — дефектоскопию или рентгенодефектоскопию. Рамки применения теневого метода ультразвуковой дефектоскопии и других способов существуют, основные дефекты, которые возможно выявить с помощью УЗД:
- расслоения наплавленного метала, различные поры;
- трещины, неровности шва, а также не проваренные участки;
- не сплавления, дефекты свище образного происхождения;
- поврежденные окислами и коррозией участки, провисание металла;
- несоответствующий химический состав соединения, поврежденный геометрически размер.
Ультразвуковой диагностике подвержены различные типы швов, плоские, продольные, кольцевые, сварные трубы и стыки, а также тавровые соединения. Методика проверки швов применяется не только крупными производственными предприятиями, а также на строительных площадках, при возведении помещений. Чаще всего УЗД используется:
- в определении степени износа труб в магистралях, сварных соединений;
- диагностика агрегатов, материалов в аналитических целях;
- машиностроение, нефтегазовая, тепловая, химическая и атомная промышленности требуют использование технологии при обеспечении безопасности эксплуатации будущего изделия;
- в соединениях сварного типа с крупнозернистой структурой, сложной геометрией;
- установка и соединение изделий, подверженных крупным физическим, температурным нагрузкам, потребует проверки ультразвуковым контролем.
К работе с дефектоскопом допускаются лица, имеющие удостоверение, ознакомленные с правилами техники безопасности. Сварные стыки могут находиться в замкнутых пространствах, на высоте, труднодоступных местах, перед работой оператор проходит дополнительный инструктаж, работа контролируется отделом охраны труда. Работа производится с заземленным аппаратом, сечением провода не менее 2.5 мм. Категорически запрещается использовать оборудование вблизи сварочных работ в отсутствие специальной защиты.
Параметры оценки результатов
Аппарат настраивается путем определения наименьшего размера дефекта на эталонной детали. В роли эталонов выступают расположенные перпендикулярно направлению прозвучивания отверстия плоскодонного типа. Используются эталонные детали также с боковыми прорезями, зарубками.
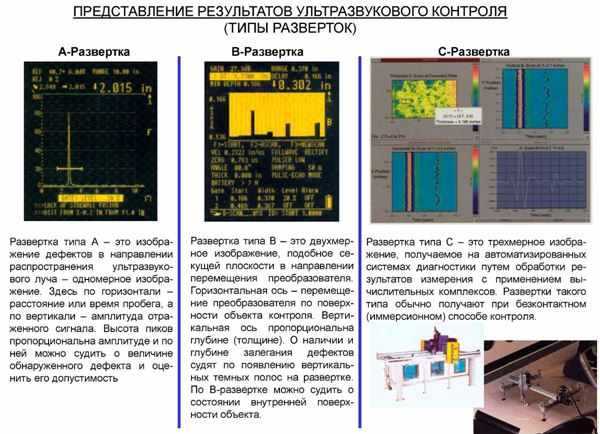
Результаты ультразвукового контроля
Минимальным расстоянием между дефектами обуславливается разрешающая способность для эхо – метода, это делается, чтобы определить несколько различных дефектов.
Оценка качества сварных соединений при ультразвуковом контроле происходит по следующим параметрам:
- условная протяженность;
- ширина, высота дефекта, а также его форма;
- амплитуда звуковой волны.
Длинна сварного дефекта определяется расстоянием перемещения излучателя по отношению к зафиксированному показанию сигналов с прибора. Способ определяется также для определения ширины дефекта. По разнице времени излученной, отраженной форме волны от дефекта определяется высота дефекта.
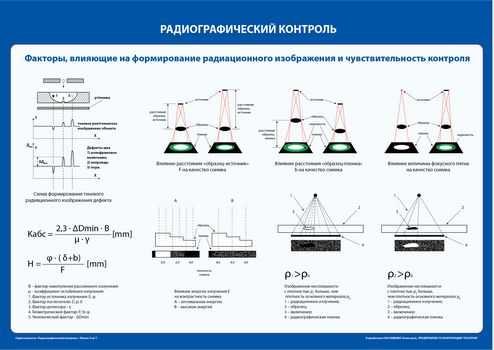
Факторы, влияющие на результат
Определение точного значения дефекта при ультразвуковой проверке практически невозможно. Именно поэтому, за основу берется площадь эталонного изделия. Максимально допустимыми параметрами являются эквивалентные величины, которые сопоставляются с эталоном. Стоит учитывать, что вычисленная площадь, практически во всех случаях, меньше настоящего размера.
Результаты дефектоскопии ультразвукового типа оформляются в специально отведенном журнале, согласно ГОСТ-14782. При регистрации проверки в обязательном порядке проставляются:
- индексы и наименование типа сварного стыка, длина подверженного контролю шва;
- техническое задание, условие, при которых производилась проверка;
- тип, наименование устройства;
- частота колебаний в ГЦ;
- условная, предельная чувствительность, углы ввода в металл, а также тип искателя;
- результаты, дата проверки, а также фамилия оператора.
К описанию характеристик в журналах при проверке применяются сокращения. Прописная буква А указывает на то, что дефект и его протяженность не переступает технические условия. Буквы Б, В характеризуют протяженность дефекта по нарастающей. Цифрами следом обозначается количество дефектов, их размеры, глубину.
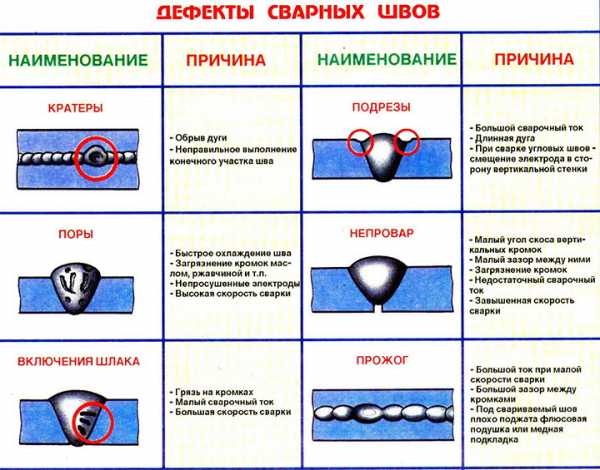
Дефекты сварных швов
Определение формы дефекта происходит за счёт специальной методики, основой данных является эхо-сигнал, отображаемый дефектоскопом. Точность показаний определяется квалификацией оператора, его внимательностью, тщательность проведения. Измеряемые показатели должны быть в соответствии с инструкцией.
Достоинства и недостатки ультразвукового контроля труб
Ультразвуковым контролем возможно определить несоответствия во всех видах соединений, пайке, склейке, сварки и т.к. Процедура позволяет выявить большое количество недочетов:
- поры, воздушные пустоты;
- околошовные трещины, шлаковые отложения;
- неоднородные химические вкрапления;
- расслоения слоями наплавленного металла.
Основными преимуществами проведения неразрушимой акустической дефектоскопии являются:
- возможность проверки соединений как разнородных, так и однородных металлов, материалов;
- оценка качества соединения материалов, состоящих из неметаллов;
- отсутствие разрушения, повреждения поверхности шва, после проверки обследуемый участок необходимо только закрасить;
- отсутствие опасных воздействий на организм человека в сравнении с радио или рентген дефектоскопией.
- Низкая себестоимость, высокая мобильность позволяют проводить контроль швов практически при любых полевых условиях.
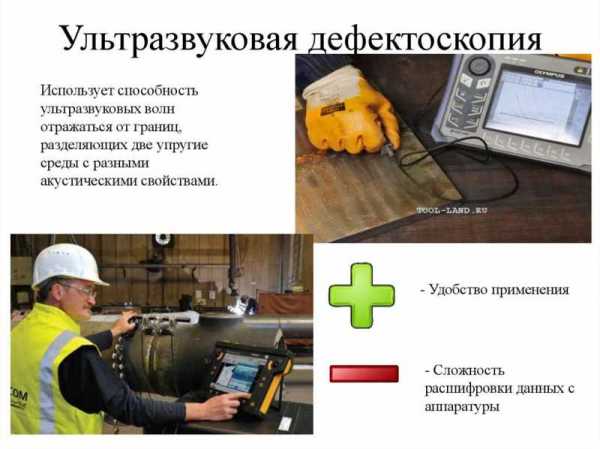
Плюсы и минусы ультразвукового контроля
Проведения работ со сложным оборудованием требует обученного, опытного персонала. Ультразвуковой контроль швов не исключение, а также требуется подготовка сварного шва по определенным показателям:
- Контроль за создание шероховатости не ниже 5 класса, направление полос должно быть перпендикулярно направлению шва;
- Исключение появления воздушного зазора путем нанесения масел или воды, в случае проверти вертикальной поверхности применяется густые массы и клейстеры.
Каждый из способов проверки имеет недостатки, проверка КЗД металлов не исключение. К основным отрицательным сторонам можно отнести:
- При диагностике круглых изделий радиусом менее 10 см, необходимо применять специальные преобразователи пьезоэлектрического типа, радиус кривизны подошвы которых отличается от объекта на 10 процентов в большую или меньшую сторону;
- Крупнозернистые структуры толщиной более 60 мм сложно диагностировать, в связи с затуханием отражения, рассеиванием колебаний при контроле. Такие материалы обычно состоят из аустенита или чугуна.
- Малые изделия, детали со сложными конструктивными особенностями не возможно подвергнуть проверке УЗД;
- Сложный процесс оценки, проверки материалов из неоднородных сталей;
- Расположение в структуре шва дефекта на различной глубине, не дает возможности точно определить диаметр, высоту неровности.
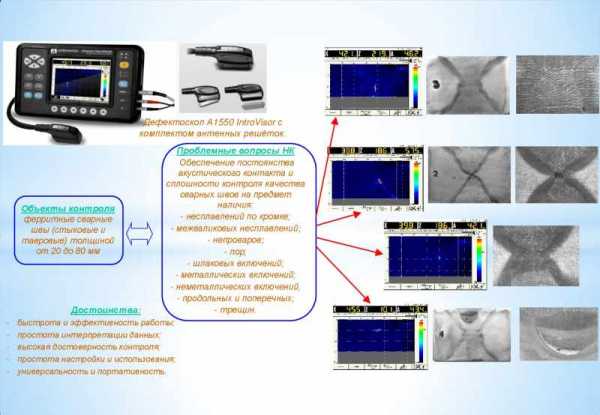
Преимущества и проблемные вопросы метода
Для проверки понадобится дефектоскопы и преобразователи, набор эталонов, образцов, предназначенных для калибровки и настройки оборудования. Определение расположения, места дефектов производится с помощью линейки координатного типа, вспомогательные приспособления понадобятся для зачистки, смазки проверяемого шва.
Проверенный сварной шов гарантирует надежность, прочность конструкции при эксплуатации. Существуют определенные нормативы, по которым изделие вводится в эксплуатацию или дорабатывается дальше.
В особенности проверка применяется в тяжелых условиях использования приспособлений.
Если вы нашли ошибку, пожалуйста, выделите фрагмент текста и нажмите Ctrl+Enter.
stankiexpert.ru
Ультразвуковой контроль сварных соединений
Сварные соединения являются новообразованиями на любых конструкциях и их дальнейшая безопасная эксплуатация во многом зависит от качества их наложения, а это, в свою очередь, можно выявить только специальной проверкой. Качество сварных швов металлических соединений проверяют, используя для этого различные методики дефектоскопии. Из всего существующего на сегодняшний день разнообразия видов дефектоскопии можно выделить ультразвуковой контроль сварных соединений, который является наиболее доступным и недорогим методом диагностики. Причем УЗК практически не уступает по точности измерений таким видам неразрушающего контроля, как рентгеноскопия, гамма-скопия, радиоскопия и другим.
Теоретическое определение УЗК
Методика ультразвукового неразрушающего контроля является далеко не новым видом дефектоскопии и впервые была применена на практике в 1928 году, а с развитием технического прогресса и промышленных технологий стала использоваться во многих сферах деятельности человека.
Весь эффект УЗК основан на том, что акустические ультразвуковые волны при прохождении однородной среды не меняют свою прямолинейную траекторию движения, а вот при разделе сред, имеющих различную структуру и обладающих разными величинами удельного акустического сопротивления, происходит их частичное отражение. При этом чем существеннее разница в физических и химических свойствах материалов, тем больше будет звуковое сопротивление в месте раздела сред, тем ощутимее и заметнее эффект при отражении звуковых волн.
К примеру, при образовании сварного шва в структуре металла обычно остается смесь газов, которая не успела выйти во время затвердевания наружу. При этом газообразная среда обладает фактически в пять раз меньшим волновым сопротивлением прохождению ультразвуковых колебаний, чем металлическая кристаллическая решетка, что и позволяет практически полностью отражаться ультразвуковым колебаниям.
Ультразвуковой контроль, либо дефектоскопия сварных соединений являются неразрушающим их целостность методом по поиску внутренних структур, имеющих химические или физические отклонения от заданных норм, которые при недопустимой величине и определяются как механические дефекты сварных швов.
Достоинства УЗК
С помощью методики ультразвукового контроля осуществляется диагностика всех видов сварки, пайки и склейки, что позволяет выявлять такие дефекты соединений, как:
- воздушные пустоты и поры,
- расслоения в наплавленном металле шва,
- околошовные трещины,
- химически неоднородные вкрапления,
- шлаковые отложения,
- неоднородность структуры,
- искривление геометрических размеров.
Главными преимуществами ультразвуковой дефектоскопии можно назвать возможность проведения контроля:
- соединений как из однородных, так и из разнородных материалов;
- структур, состоящих как из металлов, так и неметаллов;
- без разрушения и без повреждения исследуемых образцов;
- с высокой мобильностью;
- с высокой скоростью исследований;
- при низкой себестоимости;
- без опасных факторов для персонала в сравнении с рентгено- или радио-дефектоскопией.
Недостатки УЗК
Использование ультразвукового контроля имеет ряд особенностей, а именно — требуется существенная подготовка исследуемых поверхностей для прохождения от пьезоэлектрических преобразователей ультразвуковых волн по структуре металла. Необходимо:
- создание шероховатостей 5 класса на поверхности сварного соединения с направлением полос перпендикулярно шву;
- нанесение на исследуемый участок контактной массы (в виде воды, масел) для полного исключения воздушного зазора, а в случае с вертикальной или при сильнонаклоненной поверхности использовать густые клейстеры, неспособные к быстрому стеканию;
Непосредственно к недостаткам этой методики дефектоскопии можно отнести:
- необходимость в использовании специальных пьезоэлектрических преобразователей, имеющие радиус кривизны подошвы в диапазоне величины +-10% от радиуса исследуемого объекта для диагностики округлых форм конструкцией с диаметром менее 200 мм;
- существенные сложности при исследовании крупнозернистых структур металлов, к примеру, чугуна или аустенита при толщине более 60 мм, связанного со значительным затуханием и с существенным рассеванием ультразвуковых колебаний;
- невозможность проведения контроля деталей с малыми и сложными формами;
- затруднительность в оценке соединений разных видов сталей, что связано с неоднородностью основных металлов и сварного шва;
- невозможность установления реальных размеров различных типов дефектов из-за их формы, физических свойств и расположения в структуре сварного шва.
Виды ультразвукового контроля швов
Технология проведения ультразвуковой дефектоскопии основывается на способности акустических колебаний высокой частоты, порядка 20 кГц, проходить однородную структуру и частично отражаться от различных препятствий в виде пор, трещин и других неоднородностей. Существует несколько методов получения отражения ультразвукового сигнала, а именно:
- теневой, который определяет разницу амплитуды между прошедшими и отраженными колебаниями;
- зеркально-теневой, основанный на определении коэффициента затухания отраженных волн;
- эхо-зеркальный или тандемный, использующий для своей работы два аппарата;
- дельта метод, заключающейся в определении энергии отраженных от дефекта колебаний;
- эхо-импульсный, который основывается на регистрации отраженных ультразвуковых волн.
Наиболее распространенными являются два вида дефектоскопии сварных швов при помощи ультразвука — это теневая и эхо-импульсная методика проведения контроля.
Методика проведения УЗК
Несмотря на существование нескольких методик ультразвуковой дефектоскопии их проведение практически схоже и различается лишь в наборе диагностического оборудования. Так, проведение процедуры дефектоскопии можно описать следующей последовательностью:
- Производиться тщательная подготовка исследуемой поверхности путем механического удаления остатков шлака, краски и ржавчины со сварочного шва. Вдобавок очищают полосы по 50 мм с обеих сторон от него.
- Место проведения дефектоскопии обильно покрывают жидкой массой в виде воды, минеральных масел или густых специальных клейстеров — это необходимо для возможности беспрепятственного прохождения ультразвуковых волн.
- Производиться предварительная настройка прибора на определенную методику, рассчитанную на решение конкретных задач.
- Пьезоэлектрический преобразователь УЗК последовательно начинают перемещать по зигзагообразной траектории по сварочному шву.
- После получения устойчивого сигнала необходимо периодически поворачивать пьезоэлектрический преобразователь в разные стороны вокруг своей оси так, чтобы получить на экране прибора сигнал с максимальной четкостью изображения.
- При обнаружении дефектов их фиксируют и записывают соответствующие координаты.
- При необходимости, ультразвуковой контроль сварных швов проводят в один или несколько проходов.
- Полученные результаты дефектоскопии заносятся в журнал проверки.
Оценка статьи:
Поделиться с друзьями:
Поиск записей с помощью фильтра:
ГибкаЗащитаКовкаРезкаСваркаСверление
АрматураКвадратКругЛистПолосаПроволокаТрубаУголокШвеллер/балка
АлюминийЛатуньМедьНержавейкаТитанЧугун
wikimetall.ru
Ультразвуковая дефектоскопия - это... Что такое Ультразвуковая дефектоскопия?
Ультразвукова́я дефектоскопи́я — метод основанный С.Я. Соколовым, позволяющий осуществлять поиск дефектов в материале изделия путём излучения и принятия ультразвуковых колебаний, отраженных от внутренних несплошностей (дефектов), и дальнейшего анализа их амплитуды, времени прихода, формы и других характеристик с помощью специального оборудования — ультразвукового дефектоскопа. Является одним из самых распространенных методов неразрушающего контроля.
Принцип работы
Звуковые волны не изменяют траектории движения в однородном материале. Отражение акустических волн происходит от раздела сред с различными удельными акустическими сопротивлениями. Чем больше различаются акустические сопротивления, тем большая часть звуковых волн отражается от границы раздела сред. Так как включения в металле часто содержат воздух, имеющий на несколько порядков большее удельное акустическое сопротивление, чем сам металл, то отражение будет практически полное.
Разрешающая способность акустического исследования определяется длиной используемой звуковой волны. Это ограничение накладывается тем фактом, что при размере препятствия меньше четверти длины волны, волна от него практически не отражается. Это определяет использование высокочастотных колебаний — ультразвука. С другой стороны, при повышении частоты колебаний быстро растет их затухание, что ограничивает доступную глубину контроля. Для контроля металла наиболее часто используются частоты от 0.5 до 10 МГц.
Возбуждение и прием ультразвука
Существует несколько методов возбуждения ультразвуковых волн в исследуемом объекте. Наиболее распространенным является использование пьезоэлектрического эффекта. В этом случае излучение ультразвука производится с помощью преобразователя, который преобразует электрические колебания в акустические с помощью обратного пьезоэлектрического эффекта. Отраженные сигналы попавшие на пьезопластину из-за прямого пьезоэлектрического эффекта преобразуются в электрические, которые и регистрируются измерительными цепями.
Также используются электромагнитно-акустический (ЭМА) метод, основанный на приложении сильных переменных магнитных полей к металлу. КПД этого метода гораздо ниже, чем у пьезоэлектрического, но зато может работать через воздушный зазор и не предъявляет особых требований к качеству поверхности.
Классификация методов исследования
Существующие акустические методы неразрушающего контроля подразделяют на две большие группы - активные и пассивные.
Активные
Активные методы контроля подразумевают под собой излучение и приём акустических волн.
Отражения
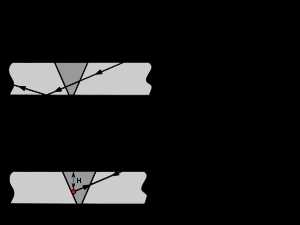
- Эхо-метод или эхо-импульсный метод — наиболее распространенный: преобразователь генерирует колебания (т.е. выступает в роли генератора) и он же принимает отражённые от дефектов эхо-сигналы (приёмник). Данный способ получил широкое распространение за счёт своей простоты, т.к. для проведения контроля требуется только один преобразователь, следовательно при ручном контроле отсутствует необходимость в специальный приспособлениях для его фиксации (как, например, в дифракционно-временном методе) и совмещении акустических осей при использовании двух преобразователей. Кроме того, это один из немногих методов ультразвуковой дефектоскопии, позволяющий достаточно точно определить координаты дефекта, такие как глубину залегания и положение в исследуемом объекте (относительно преобразователя).
- Зеркальный или Эхо-зеркальный метод — используются два преобразователя с одной стороны детали: сгенерированные колебания отражаются от дефекта в сторону приемника. На практике используется для поиска дефектов расположенных перпендикулярно поверхности контроля, например трещин.
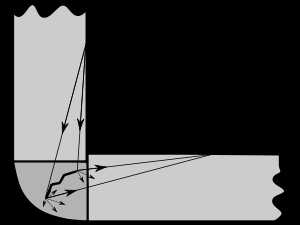
- Дифракционно-временной метод — используется два преобразователя с одной стороны детали, расположенные друг напротив друга. Если дефект имеет острые кромки (как, например, трещины) то колебания дифрагируют на концах дефекта и отражаются во все стороны, в том числе и в сторону приёмника. Дефектоскоп регистрирует время прихода обоих импульсов при их достаточной амплитуде. На экране дефектоскопа одновременно отображаются оба сигнала от верхней и от нижней границ дефекта, тем самым можно достаточно точно определить условную высоту дефекта. Способ достаточно универсален, позволяет производить ультразвуковой контроль на швах любой сложности, но требует специального оборудования для фиксации преобразователей, а также дефектоскоп, способный работать в таком режиме. Кроме того, дифрагированные сигналы достаточно слабые.
- Дельта-метод — разновидность зеркального метода — отличаются механизм отражения волны от дефекта и способ принятия. На практике не используется.
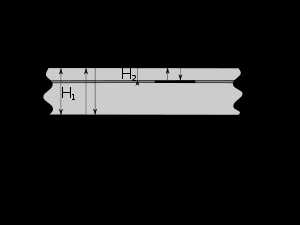
- Ревербационный метод - основан на постепенном затухании сигнала в объекте контроля. При контроле двухслойной конструкции, в случае качественного соединения слоёв, часть энергии из первого слоя будет уходить во второй, поэтому ревербация будет меньше. В обратном случае будут наблюдаться многократные отражения от первого слоя, так называемый лес. Метод используется для контроля сцепления различных видов наплавок, например баббитовой наплавки с чугунным основанием. Основным недостатком данного метода является регистрация дефектоскопом эхо-сигналов от границы соединения двух слоёв. Причиной этих эхо-сигналов является разница скоростей упругих колебаний в материалах соединения и их различное удельное акустическое сопротивление. Например на границе баббит-сталь возникает постоянный эхо-сигнал даже в местах качественного сцепления. В силу конструкционных особенностей некоторых изделий, контроль качества соединения материалов ревербационным методом может быть невозможен именно из-за наличия на экране дефектоскопа эхо-сигналов от границы соединения.
- Акустическая микроскопия благодаря повышенной частоте ввода ультразвукового пучка и применению его фокусировки, позволяет обнаруживать дефекты, размеры которых не превышают десятых долей миллиметра.
- Когерентный метод - помимо двух основных параметров эхо-сигнала, таких как амплитуда и время прихода, используется дополнительно фаза эхо-сигнала. Использование когерентного метода, а точнее нескольких идентичных преобразователей, работающих синфазно, позволяет получить изображение дефекта, близкое к реальному. При использовании специальных преобразователей, таких как преобразователь бегущей волны или его современный аналог - преобразователь с фазированной решёткой, метод позволяет значительно уменьшить время, затрачиваемое на контроль изделия.
Прохождения
Методы прохождения подразумевают под собой наблюдение за изменением параметров ультразвуковых колебаний, прошедших через объект контроля, так называемых сквозных колебаний. Изначально для контроля применялось непрерывное излучение, а изменение его амплитуды сквозных колебаний расценивалось как наличие дефекта в контролируемом объекте, так называемой звуковой тени. Отсюда появилось название теневой метод. Со временем непрерывное излучение сменилось импульсным, а к фиксируемым параметрам помимо амплитуды добавились также фаза, спектр и время прихода импульса и появились другие методы прохождения. Термин теневой потерял свой первоначальный смысл и стал означать один из методов прохождения. В англоязычной литературе метод прохождения называется through transmission technique или through transmission method, что полностью соответствует его российскому названию. Термин теневой в англоязычной литературе не применяется.
- Теневой — используются два преобразователя, которые находятся по две стороны от исследуемой детали на одной акустической оси. В данном случае один из преобразователей генерирует колебания (генератор), а второй принимает их (приёмник). Признаком наличия дефекта будет являться значительное уменьшение амплитуды принятого сигнала, или его пропадание (дефект создает акустическую тень).
- Зеркально-теневой — используется для контроля деталей с двумя параллельными сторонами, развитие теневого метода: анализируются отражения от противоположной грани детали. Признаком дефекта, как и при теневом методе, будет считаться пропадание отраженных колебаний. Основное достоинство этого метода в отличие от теневого заключается в доступе к детали с одной стороны.
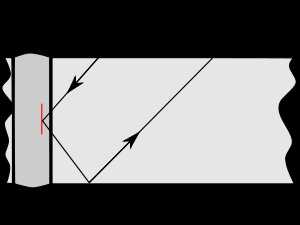
- Временной теневой основан на запаздывании импульса во времени, затраченного на огибание дефекта. Используется для контроля бетона или огнеупорного кирпича.
- Метод многократной тени аналогичен теневому, с тем исключением, что ультразвуковая волна несколько раз проходит через параллельные поверхности изделия.
- При эхо-сквозном методе используют два преобразователя, расположенные по разные стороны объекта контроля друг напротив друга. В случае отсутствия дефекта, на экране дефектоскопа наблюдают сквозной сигнал и сигнал, двукратно отражённый от стенок объекта контроля. При наличии полупрозрачного дефекта, также наблюдают отражённые сквозные сигналы от дефекта.
- Ревербационно-сквозной метод включает в себя элементы ревербационного метода и метода многократной тени. На небольшом расстоянии друг от друга, как правило с одной стороны изделия, устанавливают два преобразователя - передатчик и приёмник. Ультразвуковые волны, посылаемые в объект контроля после многократных отражений, в конечном счете попадают на приёмник. Отсутствие дефекта позволяет наблюдать стабильные отраженные сигналы. При наличии дефекта изменяется распространение ультразвуковых волн - изменяется амплитуда и спектр принятых импульсов. Метод применяется для контроля многослойных конструкций и полимерных композитных материалов.
- Велосиметрический метод основан на регистрации изменения скорости упругих волн в зоне дефекта. Применяется для контроля многослойных конструкций и для изделий из полимерных композиционных материалов.
Собственных колебаний
Вынужденных колебаний
- Интегральный
- Локальный
- Акустико-топографический
Свободных колебаний
- Интегральный
- Локальный
Импендансные
- Изгибных волн
- Продольных волн
- Контактного импенданса
Пассивные
Пассивные методы контроля заключаются в приёме волн, источником которых является сам объект контроля.
Современные дефектоскопы точно замеряют время, прошедшее от момента излучения до приёма эхо-сигнала, тем самым измеряя расстояние до отражателя. Это позволяет добиться высокого лучевого разрешения исследования. Компьютеризированные системы позволяют провести анализ большого числа импульсов и получить трёхмерную визуализацию отражателей в металле.
Преимущества
Ультразвуковой контроль изделий в ГДР, 1977 годУльтразвуковое исследование не разрушает и не повреждает исследуемый образец, что является его главным преимуществом. Возможно проводить контроль изделий из разнообразных материалов, как металлов, так и неметаллов. Кроме того можно выделить высокую скорость исследования при низкой стоимости и опасности для человека (по сравнению с рентгеновской дефектоскопией) и высокую мобильность ультразвукового дефектоскопа.
Недостатки
Использование пъезоэлектрических преобразователей требует подготовки поверхности для ввода ультразвука в металл, в частности создания шероховатости поверхности не ниже класса 5, в случае со сварными соединениям ещё и направления шероховатости (перпендикулярно шву). Ввиду большого акустического сопротивления воздуха, малейший воздушный зазор может стать неодолимой преградой для ультразвуковых колебаний. Для устранения воздушного зазора, на контролируемый участок изделия предварительно наносят контактные жидкости, такие как вода, масло, клейстер. При контроле вертикальных или сильно наклоненных поверхностей необходимо применять густые контактные жидкости с целью предотвращения их быстрого стекания.
Для контроля изделий с внешним диаметром менее 200мм, необходимо использовать преобразователи, с радиусом кривизны подошвы R, равным 0,9-1,1R радиуса контролируемого объекта, так называемые притертые преобразователи, которые в таком виде непригодны для контроля изделий с плоскими поверхностями. Например для контроля цилиндрической поковки, необходимо производить перемещение преобразователя в двух взаимно перпендикулярных направлениях, что подразумевает под собой использование двух притёртых преобразователей - по одному для каждого из направлений.
Как правило ультразвуковая дефектоскопия не может дать ответ на вопрос о реальных размерах дефекта, лишь о его отражательной способности в направлении приемника. Эти величины коррелируют, но не для всех типов дефектов. Кроме того, некоторые дефекты практически невозможно выявить ультразвуковым методом в силу их характера, формы или расположения в объекте контроля.
Практически невозможно производить достоверный ультразвуковой контроль металлов с крупнозернистой структурой, таких как чугун или аустенитный сварной шов (толщиной свыше 60 мм)[1][2] из-за большого рассеяния и сильного затухания ультразвука. Кроме того, затруднителен контроль малых деталей или деталей со сложной формой.
Применение
Ультразвуковой дефектоскоп для контроля железнодорожных рельсПрименяется для поиска дефектов материала (поры, волосовины, различные включения, неоднородная структура и пр.) и контроля качества проведения работ — сварка, пайка, склейка и пр. Ультразвуковой контроль является обязательной процедурой при изготовлении и эксплуатации многих ответственных изделий, таких как части авиационных двигателей, трубопроводы атомных реакторов или железнодорожные рельсы.
Ультразвуковой контроль сварных швов
Сварные швы являются самой массовой областью применения ультразвуковой дефектоскопии. Это достигается за счёт мобильности ультразвуковой установки, высокой производительности контроля, высокой точности, высокой чувствительности к любым внутренним (объёмным - поры, металлические и неметаллические включения; плоскостным - непровары, трещины), а также внешним, т.е. поверхностным дефектам сварных швов (подрезы, обнижения валика усиления и т.п.).
Многие ведомственные документы подразумевают обязательный ультразвуковой контроль сварных швов, либо альтернативный выбор ультразвукового или радиационного контроля, либо контроль обоими методами.
Основным документом в России по ультразвуковому контролю сварных швов является ГОСТ 14782-86, в котором рассмотрены в полном объёме методы контроля стыковых, тавровых, нахлесточных и угловых сварных швов, выполненных различными способами сварки. Также в нём подробно описаны стандартные образцы (эталоны) СО-1, СО-2 (СО-2А), СО-3 и СО-4 и стандартные образцы предприятия, необходимые для настройки дефектоскопа, а также их параметры для их изготовления.
Объёмы контроля и нормы оценки качества сварного соединения устанавливаются различными нормативными документами в соответствии с требованиями прочности к конкретной сварной конструкции. На предприятиях, изготавливающих особо ответственные изделия, а также различными надзорными органами могут выпускаться собственные методические материалы для оценки качества сварных швов. Примером может служить РД РОСЭК-001-96, разработанный Ростехнадзором для оценки качества сварных соединений для грузоподъёмных машин.
Литература и нормативно-техническая документация
Литература
- Клюев В.В. Неразрушающий контроль. Том 3.: Справочник. В 7-и книгах / Под ред. Клюева В.В. — М. Машиностроение 2004
- Гурвич А. К., Ермолов И. Н. Ультразвуковая дефектоскопия сварных швов — Киев: Техшка, 1972
- Выборнов Б. И. Ультразвуковая дефектоскопия - М.: Металлургия, 1985
Нормативно-техническая документация
- ГОСТ 14782-86 Контроль неразрушающий. Соединения сварные. Методы ультразвуковые.
- ГОСТ 24507-80 Контроль неразрушающий. Поковки из черных и цветных металлов. Методы ультразвуковой дефектоскопии.
- ГОСТ 22727-88 Прокат листовой. Методы ультразвукового контроля.
- ГОСТ 21120-75 Прутки и заготовки круглого и прямоугольного сечения. Методы ультразвуковой дефектоскопии.
- РД РОСЭК-001-96 Машины грузоподъемные. Конструкции металлические. Контроль ультразвуковой. Основные положения.
- ОП 501 ЦД-97 Энергетическое оборудование. Сосуды давления. Трубопроводы пара, воды.
- ПНАЭ Г-7-010-89 Оборудование и трубопроводы атомных энергетических установок. Сварные соединения и наплавки. Правила контроля.
- ПНАЭ Г-10-032-92 Правила контроля сварных соединений элементов локализующих систем безопасности атомных станций.
- ПНАЭ Г-7-032-91 Унифицированные методики контроля основных материалов полуфабрикатов), сварных соединений и наплавки оборудования и трубопроводов атомных энергетических установок. Ультразвуковой контроль. Часть IV. Контроль сварных соединений из сталей аустенитного класса.
См. также
Примечания
- ↑ ПНАЭ Г-7-032-91 Ультразвуковой контроль. Часть IV. Контроль сварных соединений из сталей аустенитного класса. П.1.4.
- ↑ Клюев В.В. Неразрушающий контроль. Том 3. П.5.1.3.1.
dic.academic.ru
Ультразвуковой метод контроля качества сварных соединений
Рекомендуем приобрести:
Установки для автоматической сварки продольных швов обечаек - в наличии на складе! Высокая производительность, удобство, простота в управлении и надежность в эксплуатации.
Сварочные экраны и защитные шторки - в наличии на складе! Защита от излучения при сварке и резке. Большой выбор. Доставка по всей России!
Свойства ультразвуковых волн
Метод ультразвуковой дефектоскопии металлов и других материалов впервые был разработан и практически осуществлен в Советском Союзе в 1928—1930 гг. проф. С. Я. Соколовым.
Ультразвуковые волны представляют собой упругие колебания материальной среды, частота которых лежит за пределами слышимости в диапазоне от 20 кгц (волны низкой частоты) до 500 Мгц (волны высокой частоты).
Ультразвуковые колебания бывают продольные и поперечные. Если частицы среды перемещаются параллельно направлению распространения волны, то такая волна является продольной, если перпендикулярно-поперечной. Для отыскания дефектов в сварных швах используют в основном поперечные волны, направленные под углом к поверхности свариваемых деталей.
Ультразвуковые волны способны проникать в материальные среды на большую глубину, преломляясь и отражаясь при попадании на границу двух материалов с различной звуковой проницаемостью. Именно эта способность ультразвуковых волн используется в ультразвуковой дефектоскопии сварных соединений.
Ультразвуковые колебания могут распространяться в самых различных средах — воздухе, газах, дереве, металле, жидкостях.
Скорость распространения ультразвуковых волн C определяют по формуле:
C = fλ
где f — частота колебаний, гц;λ — длина волны, см.
Для выявления мелких дефектов в сварных швах следует пользоваться коротковолновыми ультразвуковыми колебаниями, так как волна, длина которой больше размера дефекта, может не выявить его.
Получение ультразвуковых волн
Ультразвуковые волны получают механическим, термическим, магнитострикционным (Магнитострикция — изменение размеров тела при намагничивании) и пьезоэлектрическим (Приставка «пьезо» означает «давить») способами.
Наиболее распространенным является последний способ, основанный на пьезоэлектрическом эффекте некоторых кристаллов (кварца, сегнетовой соли, титаната бария): если противоположные грани пластинки, вырезанной из кристалла, заряжать разноименным электричеством с частотой выше 20 000 гц, то в такт изменениям знаков зарядов пластинка будет вибрировать, передавая механические колебания в окружающую среду в виде ультразвуковой волны. Таким образом электрические колебания преобразовываются в механические.
В различных системах ультразвуковых дефектоскопов применяют генераторы высокой частоты, задающие на пьезоэлектрические пластинки электрические колебания от сотен тысяч до нескольких миллионов герц.
Пьезоэлектрические пластинки могут служить не только излучателями, но и приемниками ультразвука. В этом случае под действием ультразвуковых волн на гранях кристаллов-приемников возникают электрические заряды малой величины, которые регистрируются специальными усилительными устройствами.
Методы выявления дефектов ультразвуком
Существуют в основном два метода ультразвуковой дефектоскопии: теневой и эхо-импульсный (метод отраженных колебаний.)
Рис. 41. Схемы проведения ультразвуковой дефектоскопииа — теневым; б — эхо импульсным методом; 1 — щуп-излучатель; 2 — исследуемая деталь; 3 — щуп приемник; 4 — дефект
При теневом методе (рис. 41, а) ультразвуковые волны, идущие через сварной шов от источника ультразвуковых колебаний (щупа-излучателя), при встрече с дефектом не проникают через него, так как граница дефекта является границей двух разнородных сред (металл — шлак или металл — газ). За дефектом образуется область так называемой «звуковой тени». Интенсивность ультразвуковых колебаний, принятых щупом-приемником, резко падает, а изменение величины импульсов на экране электронно-лучевой трубки дефектоскопа указывает на наличие дефектов. Этот метод имеет ограниченное применение, так как необходим двусторонний доступ к шву, а в ряде случаев требуется снимать усиление шва.
При эхо-импульсном методе (рис. 41,6) щуп-излучатель посылает через сварной шов импульсы ультразвуковых волн, которые при встрече с дефектом отражаются от него и улавливаются щупом-приемником. Эти импульсы фиксируются на экране электроннолучевой трубки дефектоскопа в виде пиков, свидетельствующих о наличии дефекта. Измеряя время от момента посылки импульса до приема обратного сигнала, можно определить и глубину залегания дефектов. Основное достоинство этого метода состоит в том, что контроль можно проводить при одностороннем доступе к сварному шву без снятия усиления или предварительной обработки шва. Этот метод получил наибольшее применение при ультразвуковой дефектоскопии сварных швов.
Импульсные ультразвуковые дефектоскопы
Контроль сварных соединений осуществляется при помощи ультразвуковых дефектоскопов, которыми можно выявлять трещины» непровары, газовые и шлаковые включения в стыковых, угловых, тавровых и нахлесточных соединениях, выполненных дуговой, электрошлаковой, газовой и контактной сваркой. Контролировать можно как сварку сталей, так и сварку цветных металлов и их сплавов.
Электрическая схема дефектоскопов, состоящая из отдельных электронных блоков, смонтирована в металлическом кожухе, на передней панели которого находится экран электроннолучевой трубки и расположены рукоятки управления. Дефектоскопы укомплектованы призматическими щупами-искателями (рис. 42) с углами ввода ультразвукового луча 30, 40 и 50° (0,53; 0,7 и 0,88 рад). Придаются также и прямые щупы, при помощи которых ультразвуковые колебания вводятся перпендикулярно поверхности контролируемого изделия. Комплект щупов позволяет выбирать для каждого конкретного случая необходимую схему прозвучивания. Во всех щупах в качестве пьезоэлектрического преобразователя используются пластинки титаната бария.
Рис. 42. Конструктивная схема призматического щупа1 — кольцо изоляционное; 2 — асбестовая прокладка; 3 — накладка контактная; 4 — втулка изоляционная; 5 — втулка; 6 — пластинка из титаната бария; 7 — корпус;8 — призма из плексигласа
В зависимости от количества щупов и схемы их включения ультразвуковые дефектоскопы могут быть двухщуповыми, в которых один щуп является излучателем, а другой приемником, или однощуповыми, где функция ввода и приема ультразвуковых колебаний выполняются одним щупом. Это возможно потому, что прием отраженного сигнала происходит во время пауз между импульсами, когда никаких других сигналов, кроме отраженных, на пьезоэлектрическую пластинку не поступает.
В качестве индикаторов дефектов применяются электроннолучевые трубки. Ряд дефектоскопов оснащен также световым (электрической лампочкой на искательной головке щупа) и звуковым (динамиком и телефонными наушниками) индикаторами.
Типовая блок-схема импульсного ультразвукового дефектоскопа, работающего по однощуповой схеме, приведена на рис. 43.
Рис. 43. Блок-схема импульсного ультразвукового дефектоскопа УЗД-7Н1 — задающий генератор; 2 — генератор импульсов; 3 — пьезоэлектрический щуп; 4 — генератор развертки; 5 — приемный усилитель; 6 — электроннолучевая трубка; 7 — контролируемое изделие
Задающий генератор, питаемый переменным током, вырабатывает электрические колебания, передаваемые на генератор импульсов и пьезоэлектрический щуп. В последнем высокочастотные электрические колебания преобразуются в механические колебания ультразвуковой частоты и посылаются в контролируемое изделие. В интервалах между отдельными посылами высокочастотных импульсов пьезоэлектрический щуп при помощи электронного коммутатора подключается к приемному усилителю, который усиливает полученные от щупа отраженные колебания и направляет их на экран электроннолучевой трубки. Таким образом, пьезоэлектрический щуп попеременно работает как излучатель и приемник ультразвуковых волн.Генератор развертки обеспечивает развертку электронного луча трубки, который прочерчивает на экране электроннолучевой трубки светящуюся линию с пиком начального импульса.
При отсутствии дефекта в контролируемом изделии импульс дойдет до нижней поверхности изделия, отразится от нее и возвратится в пьезоэлектрический щуп. В нем механические колебания ультразвуковой частоты снова преобразуются в высокочастотные электрические колебания, усиливаются в приемном усилителе и подаются на отклоняющие пластины электроннолучевой трубки. При этом на экране возникает второй пик донного импульса (как бы отраженного от дна изделия).
Если на пути прохождения ультразвука встретится дефект, то часть волн отразится от него раньше, чем донный сигнал достигнет пьезоэлектрического щупа. Эта часть волн усиливается приемным усилителем, подается на электроннолучевую трубку и на ее экране между начальным и донным импульсами возникнет пик импульса от дефекта.
Благодаря синхронной работе генератора развертки луча, генератора импульсов и других устройств дефектоскопа взаимное расположение импульсов на экране электроннолучевой трубки характеризует глубину расположения дефекта. Расположив на экране трубки масштабные метки времени, можно сравнительно точно определить глубину залегания дефекта.
Методика ультразвукового контроля
Перед началом ультразвукового контроля зачищают поверхность сварного соединения на расстоянии 50—80 мм с каждой стороны шва, удаляя брызги металла, остатки шлака и окалину. Зачистку выполняют ручной шлифовальной машинкой, а при необходимости еще и напильником или наждачной шкуркой.
Чтобы обеспечить акустический контакт между щупом-искателем и изделием, зачищенную поверхность металла непосредственно перед контролем тщательно протирают и наносят на нее слой контактной смазки. В качестве смазки применяют автол марок 6, 10, 18, компрессорное, трансформаторное или машинное масло.
Затем проверяют правильность показаний дефектоскопа на эталонах сварных швов с заранее определенными дефектами.
Контроль стыковых соединений проводят путем поочередной установки щупа по обеим сторонам проверяемого шва.
Рис. 44. Схема проведения ультразвукового контроляа — перемещение призматического щупа по поверхности изделия; б — контроль прямым лучом; в — контроль отраженным лучом
В процессе контроля щуп-искатель плавно перемещают вдоль обеих сторон шва по зигзагообразной линии (рис. 44, а), систематически поворачивая его на 5—10° в обе стороны для выявления различно расположенных дефектов.
Прозвучивание производят как прямым (рис. 44, б), так и отраженным (рис. 44, в) лучом. Стыковые соединения при толщине металла более 20 мм обычно проверяют прямым лучом. При толщине металла менее 20 мм усиление шва не дает возможности установить щуп так, чтобы ультразвуковой луч проходил через корень шва. В этих случаях контроль осуществляют однократно или двукратно отраженными лучами. При толщине металла менее 8 мм его прозвучивают многократно отраженным лучом.
Пределы перемещения щупа поперек шва зависят от угла ввода луча и способа прозвучивания и определяются по номограммам, прилагаемым к инструкции на эксплуатацию дефектоскопа. Чтобы обеспечить перемещение щупов в заданных пределах, их устанавливают в специальный держатель (рис. 45).
Рис. 45. Держатели призматических щупова — для контроля стыковых швов отраженным лучом; б — для контроля стыковых швов прямым лучом; в — для контроля угловых швов
Рис. 46. Схема определения размеров дефекта в стыковом швеа — протяженности l; б — высоты h
Рис. 47. Конструктивная схема жидкостного глубиномера1 — генератор дефектоскопа; 2 — цилиндр; 3 — компенсирующий объем; 4 — глубиномер; 5 — механизм перемещения поршня; 6 — жидкость; 7 — поршень; 8 — пьезоэлектрическая пластинка
При обнаружении дефекта в сварном шве на экране дефектоскопа появляется импульс. Условную протяженность его измеряют длиной зоны перемещения щупаискателя вдоль шва, в пределах которой наблюдается появление и исчезнование импульса (рис. 46, а). Условную высоту дефекта определяют как разность глубин, измеренных в крайних положениях щупаискателя, в которых появляется и исчезает импульс при перемещении щупа перпендикулярно оси шва (рис. 46, б). Условную высоту дефектов, имеющих большую протяженность, измеряют в месте, где импульс от дефекта имеет наибольшую амплитуду.
Глубину залегания дефекта определяют при помощи глубиномеров. Жидкостной глубиномер (рис. 47) состоит из пьезоэлектрической пластинки, которая возбуждается от генератора дефектоскопа одновременно с основной излучающей пьезоэлектрической пластинкой щупаискателя. Эта пластинка помещена в цилиндр с компенсирующим объемом. Цилиндр наполнен жидкостью и имеет поршень, связанный со шкалой глубиномера. При прозвучивании сварного шва на экране электроннолучевой трубки вместе с начальным и донным сигналом появляется так называемый служебный импульс, отраженный от поршня цилиндра глубиномера. Положение его на экране трубки дефектоскопа определяется положением поршня в цилиндре. Передвигая поршень, совмещают служебный импульс с импульсом, отраженным от дефекта, и по шкале глубиномера определяют глубину залегания дефекта. При совмещении поршня с донным импульсом можно определить толщину металла. Подобные глубиномеры могут быть присоединены к любому ультразвуковому импульсному дефектоскопу.
Повышения скорости контроля можно достичь применением несложных устройств (рис. 48), позволяющих осуществлять перемещение дефектоскопа вдоль шва и возвратно-поступательное движение щупа. Щуп-искатель устанавливается на тележке устройства и соединяется с ультразвуковым дефектоскопом. На этой же тележке находится механизм передвижения, состоящий из электродвигателя мощностью 12 вт, червячных пар и кривошипного механизма.
Рис. 48. Схема автоматизированного контроля стыков трубопроводов с помощью специального приспособления1 — контрольный механизм; 2 - труба; 3 — роликовая цепь; 4 — коробка со щупом; 5 — ультразвуковой дефектоскоп
Значительно увеличивается надежность и скорость контроля при использовании автоматического ультразвукового дефектоскопа ДАУЗ-169, позволяющего контролировать сварные соединения при толщине листов от 6 до 16 мм. Он представляет собой датчик, установленный на автоматически передвигающейся каретке, соединенной гибким кабелем со шкафом с электронными блоками.
Дефекты регистрируются записью на диаграммной ленте и краскоотметчиком на контролируемом шве, работа которого дублируется световой сигнализацией. Скорость контроля составляет 1 м/мин. Применение его значительно увеличивает надежность и производительность процесса контроля сварных швов.
Оформление результатов контроля
Результаты ультразвуковой дефектоскопии согласно ГОСТ 14782—69 фиксируют в журнале или в заключении, обязательно указывая:
а) тип сварного соединения; индексы, присвоенные данному изделию и сварному соединению; длину проконтролированного участка шва;
б) технические условия, по которым выполнялась дефектоскопия;
в) тип дефектоскопа;
г) частоту ультразвуковых колебаний;
д) угол ввода луча в контролируемый металл или тип искателя, условную или предельную чувствительность;
е) участки шва, которые не подвергались дефектоскопии;
ж) результаты дефектоскопии;
з) дату дефектоскопии;
и) фамилию оператора.
При сокращенном описании результатов дефектоскопии каждую группу дефектов указывают отдельно.
Характеристика протяженности дефекта обозначается одной из букв А, Б, В. Цифрами обозначают: количество дефектов в шт.; условную протяженность дефекта в мм; наибольшую глубину залегания дефекта в мм; наибольшую условную высоту дефекта в мм.
Буква А указывает, что протяженность дефекта не превышает допускаемую техническими условиями. Буква Б используется для характеристики дефекта большей протяженности, чем типа А. Буквой В обозначают группу дефектов, отстоящих друг от друга на расстоянии не более величины условной протяженности для дефектов типа А.
Ниже приводится пример сокращенной записи результатов дефектоскопии в журнале или в заключении.
На участке шва сварного соединения С15 (ГОСТ 5264—69), обозначенном индексом МН-2, длиной 800 мм обнаружены: два дефекта типа А на глубине 12 мм, один дефект типа Б условной протяженностью 16 мм на глубине 14—22 мм, условной высотой 6 мм и один дефект типа В условной протяженностью 25 мм на глубине 5—8 мм.
Сокращенная запись результатов испытания выглядит так:
С15, МН-2, 800; А-2-12; Б-1-16-22-6; В-1-25-8.
Техника безопасности при ультразвуковом контроле
К работе с ультразвуковыми дефектоскопами допускают лиц, прошедших инструктаж по правилам техники безопасности и имеющих соответствующее удостоверение. Перед проведением контроля на большой высоте, в труднодоступных местах или внутри металлоконструкций оператор проходит дополнительный инструктаж, а его работу контролирует служба техники безопасности.
Ультразвуковой дефектоскоп при работе заземляют медным проводом сечением не менее 2,5 мм2. Работать с незаземленным дефектоскопом категорически запрещается. При отсутствии на рабочем месте розетки подключать и отключать дефектоскоп может только дежурный электрик.
Запрещается проводить контроль вблизи сварочных работ при отсутствии защиты от лучей электрической дуги.
Л.П. Шебеко, А.П. Яковлев. "Контроль качества сварных соединений"
www.autowelding.ru
Ультразвуковой контроль
Ультразвуковой метод контроля был предложен советским физиком С.Я. Соколовым в 1928 году и в настоящее время является одним из основных методов неразрушающего контроля. Методы ультразвуковой дефектоскопии позволяют производить контроль сварных соединений, сосудов и аппаратов высокого давления, трубопроводов, поковок, листового проката и другой продукции. Ультразвуковой контроль является обязательной процедурой при изготовлении и эксплуатации многих ответственных изделий, таких как части авиационных двигателей, трубопроводы атомных реакторов или железнодорожные рельсы.
По сравнению с другими методами неразрушающего контроля ультразвуковой метод обладает важными преимуществами:
- высокая чувствительность к наиболее опасным дефектам типа трещин и непроваров
- низкая стоимость
- безопасность для человека (в отличие от рентгеновской дефектоскопии)
- возможностью вести контроль непосредственно на рабочих местах без нарушения технологического процесса
- при проведении УЗК исследуемый объект не повреждается
- возможность проводить контроль изделий из разнообразных материалов, как металлов, так и неметаллов.
К недостаткам ультразвукового метода контроля можно отнести невозможность оценки реального размера и характера дефекта, трудности при контроле металлов с крупнозернистой структурой из-за большого рассеяния и сильного затухания ультразвука, а также повышенные требования к состоянию поверхности контроля по шероховатости и волнистости. Согласно РД 03-606-03 максимально допустимая шероховатость при ультразвуковом контроле составляет Ra 6,3 / Rz 40
Сущность ультразвукового метода неразрушающего контроля (видео ИКБ Градиент)
Многообразие задач, возникающих при необходимости проведения неразрушающего контроля различных изделий, привело к разработке и использованию ряда различных акустических методов контроля. Согласно ГОСТ 23829-85 акустические методы контроля делятся на 2 большие группы: использующие излучение и приём акустических колебаний и волн (активные методы) и основанные только на приёме колебаний и волн (пассивные методы).
![]() |
Методы | Описание |
Методы прохождения | выявляют глубинные дефекты типа нарушения сплошности, расслоения. |
Методы отражения | выявляют дефекты типа нарушения сплошности, определяет их координаты, размеры, ориентацию путём прозвучивания изделия и приёма отраженного от дефекта эхо-сигнала. |
Импедансный метод | предназначен для контроля клеевых, сварных и паяных соединений, имеющих тонкую обшивку, приклеенную или припаянную к элементам жёсткости. |
Методы свободных колебаний | применяются для обнаружения глубинных дефектов. |
Методы вынужденных колебаний (резонансные) | применяются в основном для измерения толщины изделия и для обнаружения зоны коррозионного поражения, расслоений в тонких местах из металлов. |
Акустико-эмиссионный метод | обнаруживает и регистрирует только развивающиеся трещины или способные к развитию под действием механической нагрузки (квалифицирует дефекты по степени их опасности во время эксплуатации). |
Наиболее широкое распространение в практике ультразвуковой дефектоскопии нашли методы прохождения и отражения (импульсные методы), реже применяют другие методы: резонансный, импедансный и метод акустической эмиссии.
Импульсные методы (прохождения и отражения)
Среди многочисленных методов прохождения и отражения на сегодняшний день наибольшее применение в дефектоскопии нашли: теневой, зеркально-теневой, и эхо-метод. Эхо-метод, в отличии от других, применим при одностороннем доступе к исследуемому объекту, и при этом позволяет определить размеры дефекта, его координаты и характер. В общем случае, суть перечисленных методов заключается в излучении в изделие и последующем принятии отраженных ультразвуковых колебаний с помощью специального оборудования - ультразвукового дефектоскопа и пьезоэлектрического преобразователя (ПЭП) и дальнейшем анализе полученных данных с целью определения наличия дефектов, а также их эквивалентного размера, формы, вида, глубины залегания и пр. Чувствительность ультразвукового контроля определяется минимальными размерами выявляемых дефектов или эталонных отражателей, выполненных в настроечном образце (ранее СОП). В качестве эталонных отражателей обычно используют плоскодонные сверления, ориентированные перпендикулярно направлению прозвучивания, а также боковые сверления или зарубки.
Самой массовой областью применения ультразвуковой дефектоскопии являются сварные соединения. Основным документом в России по ультразвуковому контролю сварных швов является ГОСТ Р 55724-2013 «Контроль неразрушающий. Соединения сварные. Методы ультразвуковые» (pdf), в котором рассмотрены в полном объёме методы контроля стыковых, тавровых, нахлесточных и угловых сварных швов, выполненных различными способами сварки. Также в нём подробно описаны меры (калибровочные образцы) СО-2, СО-3 и СО-3Р, V-1, V-2 и настроечные образцы, а также параметры для их изготовления. Проведение ультразвукового контроля сварных соединений и наплавок оборудования и трубопроводов атомных энергетических установок регламентируется документом ПНАЭ Г-7-030-91 «Унифицированные методики контроля основных материалов (полуфабрикатов), сварных соединений и наплавки оборудования и трубопроводов атомных энергетических установок. Ультразвуковой контроль» (pdf)
В зависимости от области использования, различают ультразвуковые дефектоскопы общего и специального назначения. Дефектоскопы общего назначения могут использоваться для контроля самой разнообразной продукции, а специализированные дефектоскопы созданы для решения узкоцелевых задач. К наиболее популярным моделям ультразвуковых дефектоскопов общего назначения относятся:
Ультразвуковая толщинометрия (резонансный и импульсный метод)
Как правило, ультразвуковой метод толщинометрии применяют в случаях недоступности или труднодоступности объекта для измерения его толщины механическим измерительным инструментом. Ультразвуковая толщинометрия - неотъемлемая процедура при определении толщины стенок труб, котлов, сосудов, то есть объектов замкнутого типа или с односторонним доступом, а также объектов судостроительного и судоремонтного производства. Современные ультразвуковые толщиномеры позволяют измерять толщины от 1 до 50 мм с точностью ±0,001 мм. По физическим принципам, используемым для измерения толщины, акустические толщиномеры делят на резонансные и эхо-импульсные.
Резонансный метод контроля основан на возбуждении и анализе резонансных колебаний в исследуемом объеме изделия, при этом исследование проводится при доступности одной стороны изделия, а погрешность метода составляет менее 1%. Резонансным методом измеряют толщину стенок металлических и некоторых неметаллических изделий (керамика, стекло, фарфор). Кроме того, при помощи резонансной дефектоскопии можно выявлять зоны коррозионного поражения, зоны непроклея и непропоя листовых соединений, зоны расслоения в биметаллах, тонких листах. Резонансные методы вынужденных колебаний в настоящее время не имеют широкого применения, так как задачи дефектоскопии и толщинометрии более точно решают импульсные ультразвуковые методы.
Принцип ультразвуковой импульсной толщинометрии основан на измерении времени прохождения ультразвукового импульса в изделии или в слое и умножении измеренного времени на коэффициент, учитывающий скорость звука в материале изделия. Основные нормативные документы по проведению ультразвуковой толщинометрии:
- ГОСТ Р 55614-2013 «Контроль неразрушающий. Толщиномеры ультразвуковые. Общие технические требования» (pdf).
- ГОСТ Р ИСО 16809-2015 «Контроль неразрушающий. Контроль ультразвуковой. Измерение толщины» (pdf)
- ПНАЭ Г-7-031-91 «Унифицированные методики контроля основных материалов (полуфабрикатов), сварных соединений и наплавки оборудования и трубопроводов атомных энергетических установок. Ультразвуковой контроль. Часть III. Измерение толщины монометаллов, биметаллов и антикоррозионных покрытий» (pdf)
К наиболее популярным моделям ультразвуковых толщиномеров можно отнести:
Импедансные дефектоскопы и твердомеры (импедансный метод)
Импедансный метод разработан советским ученым Ю.В. Ланге в 1958 году. Он основан на использовании зависимости полного механического сопротивления (импеданса) контролируемого изделия от качества соединения отдельных его элементов между собой. Этим методом можно выявлять дефекты в клеевых, паяных и других соединениях, между тонкой обшивкой и элементами жёсткости или заполнителями в многослойных конструкциях. Импедансные дефектоскопы широко используются в авиастроении, автомобильной и космической промышленности. Они способны обнаружить непроклеенные участки, расслоения, нарушения целостности и пустоты в различном оборудовании, приборах, конструкциях. Кроме того, метод ультразвукового контактного импеданса широко применяется для измерения твёрдости изделий из металлов и сплавов, таких как сосуды давления различного назначения (реакторы, парогенераторы, коллекторы, котельные барабаны) роторы турбин и генераторов, трубопроводы, детали различных транспортных средств, промышленные полуфабрикаты (отливки, поковки, листы) и т.д. Метод контактного импеданса основан на измерении режима колебаний преобразователя, соприкасающегося с объектом. По амплитудам и резонансным частотам такого преобразователя (часто имеющего вид стержня) судят о твердости материала изделия, податливости (упругому импедансу) его поверхности.
К наиболее популярным моделям ультразвуковых твердомеров можно отнести:
Средства для проведения ультразвукового контроля
Следующим важнейшим инструментом для проведения ультразвукового контроля являются пьезоэлектрические преобразователи (ПЭП), которые выступают в качестве излучателя и приемника ультразвукового импульса, обрабатываемого дефектоскопом или толщиномером. Принцип действия пьезоэлектрических преобразователей основан на использовании прямого или обратного пьезоэлектрических эффектов. Прямой пьезоэффект представляет собой способность некоторых материалов образовывать электрические заряды на поверхности при приложении механической нагрузки, обратный пьезоэффект заключается в изменении механического напряжения или геометрических размеров образца материала под воздействием электрического поля. В качестве пьезоэлектрических материалов обычно используют естественный материал кварц, турмалин, а также искусственно поляризованную керамику на основе титаната бария (ВаТiO3), титаната свинца (PbTiO3) и цирконата свинца (PbZrO3)
Основные требования к ультразвуковым преобразователям указаны в:
- ГОСТ Р 55725-2013 «Преобразователи ультразвуковые пьезоэлектрические. Общие технические требования» (pdf)
- ГОСТ Р 55808-2013 «Преобразователи ультразвуковые. Методы испытаний» (pdf)
Подробнее о ультразвуковых преобразователях, их классификации, маркировке и применении можно посмотреть здесь.
Для обеспечения хорошего контакта между ультразвуковым преобразователем и контролируемой поверхностью, а также для предотвращения образования воздушного зазора, создающего помехи звуковому импульсу, необходимо использовать различные контактные жидкости или гели. Контактная жидкость должна иметь специальный химический состав, соответствующий диапазону температур той или иной контролируемой поверхности и ее структуре. Так, для контроля арматурных стержней и неровных поверхностей необходимо использовать контактный гель высокой степени вязкости, при контроле нагревающихся поверхностей рекомендуется применять контактные гели на водной основе, а при очень низких температурах (до -60ºC) в качестве контактной жидкости можно использовать пропиленгликоль. Также стоит отметить, что в некоторых случаях (в частности, при контроле оборудования, используемого в ядерной промышленности) требуются контактные среды с ограниченным галогенным и серным составом. Подробнее о контактных жидкостях для ультразвукового контроля можно посмотреть здесь.
Одним из важных факторов качественного ультразвукового контроля изделий является обеспечение достоверности и единообразия при проведении контроля, особенно при диагностике объектов повышенной опасности. Метрологическое обеспечение оборудования подразумевает обязательную проверку работоспособности аппаратуры перед проведением ультразвукового контроля с использованием специальных образцов. Существует два вида образцов: меры (калибровочные образцы) и настроечные образцы (ранее стандартные образцы предприятия СОП).
Комплект калибровочных образцов необходим для проверки основных параметров аппаратуры (разрешающей способности, мертвой зоны, угла ввода, стрелы ПЭП), а по контрольным образцам предприятия СОП осуществляют настройку глубиномера дефектоскопа и определение уровней чувствительности для проведения контроля конкретного изделия по определенному НД. К используемым калибровочным образцам (мерам) относятся:
Контрольные образцы предприятия (СОП) предназначены для настройки глубиномера и чувствительности при проведении ультразвукового контроля конкретного изделия. Наиболее распространенными типами применяемых отражателей при контроле сварных соединений являются: плоскодонные отражатели, «зарубки» и сегменты. Подробнее о назначении, типах и области применения контрольных образцов можно посмотреть здесь.
Помимо технических требований, предъявляемых к процессу ультразвукового контроля, существует и установленный порядок организации работ. Так лаборатории, выполняющие ультразвуковой контроль должны быть аттестованы в соответствии с
- ПБ 03-372-00 «Правила аттестации и основные требования к лабораториям неразрушающего контроля»
Необходимость аттестации лабораторий НК регламентирована Письмом Госгортехнадзора России № 02-35/213 от 27 июня 2001 г. (pdf) в соответствии с которым, для проведения контроля оборудования, материалов и сварных соединений неразрушающими методами (в том числе и для сторонних организаций) организациям необходимо иметь лаборатории неразрушающего контроля, аттестованные в соответствии с вышеуказанным документом. По результатам аттестации лаборатории выдаётся свидетельство об аттестации в соответствующей области. Подробнее о порядке проведения аттестации, перечне необходимых документов и оборудования можно посмотреть здесь.
В зависимости от сферы деятельности, специалисты, проводящие ультразвуковой контроль должны быть аттестованы в соответствии с:
- ПБ 03-440-02 «Правила аттестации персонала в области неразрушающего контроля»
- ПНАЭ Г-7-010-89 «Федеральные нормы и правила в области использования атомной энергии»
Аттестацию специалистов в целях подтверждения их уровня теоретической и практической подготовки, необходимого для выполнения работ по конкретному методу контроля проводят независимые органы по аттестации персонала в сфере неразрушающего контроля (НОАП). НТЦ «Эксперт» является экзаменационным центром Независимого органа по аттестации персонала АЦ «НИКИМТ» АО «НИКИМТ-Атомстрой». При подготовке к аттестации специалистами могут быть использованы следующие учебные материалы:
Подробнее о порядке проведения аттестации персонала, перечне необходимых документов и стоимости аттестации можно посмотреть здесь.
Кроме того, в соответствии с требованиями ПНАЭ Г-7-010-89 и ПБ 03-372-00 для проведения ультразвукового контроля конкретного объекта должны быть разработаны технологические карты, содержащие перечень используемого оборудования, последовательность, параметры и схемы проведения контроля, оценку качества объекта с указанием информативных признаков выявляемых дефектов. Для объектов атомной энергетики технологические карты должны быть согласованы в Головных материаловедческих организациях (ГМО)
Подробнее о разработке и согласовании технологических карт, а также примеры технологических карт на различные методы неразрушающего контроля можно посмотреть здесь.
Купить оборудование и заказать услуги по ультразвуковому контролю можно в следующих городах: Москва, Санкт-Петербург, Екатеринбург, Саратов, Амурск, Ангарск, Архангельск, Астрахань, Барнаул, Белгород, Бийск, Брянск, Воронеж, Великий Новгород, Владивосток, Владикавказ, Владимир, Волгоград, Волгодонск, Вологда, Иваново, Ижевск, Йошкар-Ола, Казань, Калининград, Калуга, Кемерово, Киров, Кострома, Краснодар, Красноярск, Курск, Липецк, Магадан, Магнитогорск, Мурманск, Муром, Набережные Челны, Нальчик, Новокузнецк, Нарьян-Мар, Новороссийск, Новосибирск, Нефтекамск, Нефтеюганск, Новочеркасск, Нижнекамск, Норильск, Нижний Новгород, Обнинск, Омск, Орёл, Оренбург, Оха, Пенза, Пермь, Петрозаводск, Петропавловск-Камчатский, Псков, Ржев, Ростов, Рязань, Самара, Саранск, Смоленск, Сочи, Сыктывкар, Таганрог, Тамбов, Тверь, Тобольск, Тольятти, Томск, Тула, Тюмень, Ульяновск, Уфа, Ханты-Мансийск, Чебоксары, Челябинск, Череповец, Элиста, Ярославль и других городах, кроме того, в Республике Крым. А так же Республики Казахстан, Белоруссия и другие страны СНГ.
www.ntcexpert.ru
Ультразвуковой контроль - это... Что такое Ультразвуковой контроль?
Ультразвуковой контроль Ultrasonic inspection — Ультразвуковой контроль.Неразрушающий метод, при котором лучи высокочастотных звуковых волн проникают в материалы для обнаружения поверхностных и внутренних дефектов. Звуковые волны проходят через материал с некоторыми сопутствующими потерями энергии (затуханием) и отражаются от поверхностей. Отраженный луч принимается и затем анализируется, чтобы определить присутствие и местоположение дефектов или несплошностей. Большинство ультразвуковых проверок выполнены в частотах между 0,1 и 25 МГц — много выше амплитуды человеческого слуха, которая находится приблизительно между 20 Гц–20 кГц.
(Источник: «Металлы и сплавы. Справочник.» Под редакцией Ю.П. Солнцева; НПО "Профессионал", НПО "Мир и семья"; Санкт-Петербург, 2003 г.)
.
- Ultrasonic inspection
- Ultrasonic machining
Смотреть что такое "Ультразвуковой контроль" в других словарях:
Ультразвуковой контроль — одна из разновидностей неразрушающего контроля. Заключается в установлении свойств исследуемого предмета при помощи ультразвука. Выделяют следующие разделы: ультразвуковая дефектоскопия ультразвуковая толщинометрия ультразвуковая томография… … Википедия
ультразвуковой контроль — ультразвуковая дефектоскопия — [А.С.Гольдберг. Англо русский энергетический словарь. 2006 г.] Тематики энергетика в целом Синонимы ультразвуковая дефектоскопия EN ultrasonic testingUST … Справочник технического переводчика
ультразвуковой контроль — 3.37 ультразвуковой контроль : Неразрушающий контроль, основанный на возбуждении в контролируемом материале упругих колебаний и анализ дальнейшего процесса распространения ультразвуковых волн. Источник … Словарь-справочник терминов нормативно-технической документации
ультразвуковой контроль расхода или циркуляции воды — — [А.С.Гольдберг. Англо русский энергетический словарь. 2006 г.] Тематики энергетика в целом EN ultrasonic flow monitoringUFM … Справочник технического переводчика
ультразвуковой контроль толщины — (напр. стенок трубопровода) [А.С.Гольдберг. Англо русский энергетический словарь. 2006 г.] Тематики энергетика в целом EN ultrasonic thickness testingUTT … Справочник технического переводчика
ГОСТ Р ИСО 5577-2009: Контроль неразрушающий. Ультразвуковой контроль. Словарь — Терминология ГОСТ Р ИСО 5577 2009: Контроль неразрушающий. Ультразвуковой контроль. Словарь оригинал документа: 2.8.2 автоматическое сканирование: Перемещение преобразователя по поверхности ввода, реализованное механическими средствами.… … Словарь-справочник терминов нормативно-технической документации
РД 19.100.00-КТН-545-06: Ультразвуковой контроль стенки и сварных соединений при эксплуатации и ремонте вертикальных стальных резервуаров — Терминология РД 19.100.00 КТН 545 06: Ультразвуковой контроль стенки и сварных соединений при эксплуатации и ремонте вертикальных стальных резервуаров: Дефект : здесь: несплошность в металле стенки резервуара, в сварном соединении, отклонение… … Словарь-справочник терминов нормативно-технической документации
контроль ультразвуком — ультразвуковой контроль — [http://slovarionline.ru/anglo russkiy slovar neftegazovoy promyishlennosti/] Тематики нефтегазовая промышленность Синонимы ультразвуковой контроль EN ultrasonic examination … Справочник технического переводчика
контроль качества — (quality control; QC): Проведение проверок или испытаний на соответствие требованиям спецификаций. Источник: ГОСТ Р 52249 2009: Правила производства и контроля качества лекарственных средств … Словарь-справочник терминов нормативно-технической документации
контроль — 2.7 контроль (control): Примечание В контексте безопасности информационно телекоммуникационных технологий термин «контроль» может считаться синонимом «защитной меры» (см. 2.24). Источник … Словарь-справочник терминов нормативно-технической документации
dic.academic.ru
Что такое ультразвуковой контроль
Исследовательская Группа "Безопасность и Надёжность"
Строительные экспертизы, Обследование Зданий, Энергоаудит, Землеустройство, Проектирование
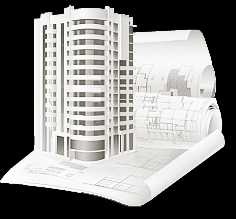
Для того чтобы существенно повысить качество строительства зданий и сооружений, нужно совершенствовать не только технологии, но и методы контроля качества работ на всех этапах строительства. Также должна проводиться экспертиза зданий, срок эксплуатации которых подходит к концу.
К основным методам неразрушающего контроля относят ультразвуковой контроль.
В результате длительной эксплуатации происходит износ материалов или могут иметь место скрытые производственные дефекты, которые со временем доходят до критической точки и в последствии могут привести к разрушению зданий и сооружений. Ультразвуковой контроль дает возможность выявлять такие скрытые дефекты без механического воздействия на материал, не разрушая целостность изделия.
Суть метода
Ультразвуковой метод диагностики позволяет установить свойства исследуемого материала при помощи ультразвука. Ультразвук имеет свойство проникать сквозь материал и отражаться от его имеющихся внутри дефектов и границ. Данный метод также называется ультразвуковая дефектоскопия. Он позволяет контролировать толщину металлоконструкций и обнаруживать глубинные и поверхностные дефекты в металлических материалах (трещины, царапины, поры и др.).
Кроме изделий из металла ультразвук можно эффективно применять для контроля качества пластмассы, композитных материалов и др. Его также используют для определения прочности бетона, глубины трещин в каменной кладке или бетоне. Метод часто применяется для проверки качества сварных швов. В отличие от других методов контроля он более оперативный. Данное исследование не наносит вред контролируемому материалу.
Оборудование для ультразвукового контроля
Специальный прибор для ультразвукового контроля называется ультразвуковой дефектоскоп. Они бывают многоканальные и одноканальные.
Многоканальные дефектоскопы, если сравнивать их с одноканальными, дают возможность осуществлять обследование сразу нескольких зон за один поворот. Также они регистрируют весь процесс контроля. Это помогает разделить обследование на отдельные этапы и оценить их во времени. На выходе получается протокол контроля. Он позволяет максимально точно анализировать результаты.
Наша лаборатория оснащена новейшими современными толщинометрами и ультразвуковыми дефектоскопами, которые позволяют исследовать самые разнообразные материалы. Приборы имеют высокую помехоустойчивость, а также функции записи полученных результатов с последующей возможностью их распечатки.
Ультразвуковой метод позволяет контролировать: сварные, паянные, клеевые соединения; детали машин в процессе эксплуатации в машиностроении; строительные объекты; готовые детали и заготовки.
Ультразвуковой контроль сегодня с успехом применяют чуть ли не во всех отраслях промышленности.
Важным аспектом технического обследования зданий и сооружений является определение характера трещинообразования. Различают следующие типы трещин: макро- и микротрещины, включения инородных предметов, внутренние полости и пустоты. Неразрушающий контроль позволяет установить место нахождения дефектов без вскрытия как в арматуре, так и в самом бетоне.
Большую роль в объективности и правильности получаемых результатов играет работа оператора-дефектоскописта. От его квалификации, навыков практической работы и теоретической подготовки зависит объективность полученных результатов. Проведение дефектоскопии всегда совмещается с проведением визуального контроля.
Мастера в нашей компании имеют высокую степень квалификации и применяют в исследовательской работе только высококачественные приборы. Сотрудники нашей компании являются командой, ориентированной на достижение поставленной цели. Мы предъявляем высокие требования к нашим работникам. Это дает нам возможность предоставлять только качественные услуги по ультразвуковому контролю.
Мы также оказываем широкий спектр услуг по экспертизе зданий на основе инновационных технологий и с применением современного оборудования. Воспользовавшись нашими услугами, вы сможете проверить качество проведения строительных работ и значительно повысить экономическую эффективность строительства.
Читайте также:
1-expertiza.ru