Чем резать металл: выбираем ручной инструмент. Металл который режется ножом
Хороший металл для самодельного холодного оружия
Здравствуйте! Сегодня я хочу поделиться накопленным опытом по использованию и добыванию материала для ножей и вообще оружия. Т.к. заказать на заводе штучно малые куски почти что невозможно или жутко дорого, то приходится искать аналоги, заменители…и оказывается халявного металла вокруг – пруд пруди! И качественного и всякого разного. Начнем с самого простого и распространенного.
Этюд 1. Черняга или Ода водопроводным трубам
Здесь поле для захвата широченное: это и полоса со стройки, уголки, трубы от батарей, швеллера, арматура. Этого добра всегда можно везде найти в сколь угодно большом количестве. «А зачем?» - спросят поклонники высокотехнологичных сплавов и сталей. А очень просто. Из чего делать накладки, всякие кольца и прочее? Ясно, что самое простое и дешевое – черняга.
Теперь поговорим о том, как можно улучшить качество нашего материала. Вышеперечисленные изделия сделаны из ковкого железа и хорошо обрабатываются прессовкой и ковкой. При этом от деформаций, металл приобретает более высокую твердость и прочность. Да, я поклонник холодной ковки, что делать? Но это реально работает! Например, для изготовления накладок на какой-нибудь нож для выживания я бы взял не просто пластину нужной толщины, а полосу раза в 2 толще, чем надо и разогнал бы ее до нужной толщины холодной ковкой, тем самым упрочнил металл и значительно увеличил качество моего изделия. Вообще качество металла в большой степени зависит от того, как его обрабатывают. Можно и из арматурины выковать классный штык-нож хорошего заводского качества, а можно и высокотехнологичную сложнолегированную сталь испортить так, что только в мусор и годится.
Холодной ковкой мне удалось довести по прочности кромки лезвия сталь 3 до рессорно-пружинной 65Г (сырой, с завода).
Еще один пример полезного наклепа – хромоникелевая нержавейка. Отличить ее не сложно: она не полируется болгаркой, а покрывается сизой пленкой окислов. После расковки в 2-3 раза она становится пружинистой и упругой, лично проверял. Про латунь уже писал, повторяться не буду.
Ниже – нож-меч, кованный из хромоникелевой нержавейки.
Но, но, но…важно, как и везде иметь чувство меры! Здесь правда подскажет только опыт. Если перебить и измочалить сталь чрезмерной уковкой или неправильной техникой ковки, то ничего хорошего не выйдет, треснет и сломается. Здесь работает только одно правило: чем тверже сталь, тем хуже и меньше она прессуется, тем вероятнее ее растрескивание.
Техника ковки хорошо описана у Кузнецова, но это для горячей. Для холодной достаточно взять молоток с круглым бойком.
Еще один вариант применения холодной обработки – это проделывание отверстий. Можно конечно взять дрель и за минуту наковырять дырок, где надо. А можно пробить их. Это трудно, долго, но зато отверстие не будет ослаблять наше изделие и само по себе будет лучше держать форму. Придется правда стачивать розочки рядом с дыркой, но оно того стоит. Пробивать можно обычным строительным гвоздем для бетона, они копейки стоят. Желательно конечно сделать специальную приспособу под это дело, но при должной сноровке можно и с помощью плоскогубцев и молотка справиться. Забегая вперед, скажу, что этот способ выручает там, где нужно просверлить уже закаленную тонкую (1-3 мм) сталь, режим термообработки которой неизвестен или нет возможности (или желания) перезакаливать. Нужно только под дырку подложить гайку чуть большего номера, чем отверстие, иначе вашу заготовку просто разорвет трещиной.
Отдельно стоит сказать об арматуре. В ней металл содержит довольно много углерода и первичная закалка у нее неплохая. При наличии горна и угля из нее можно делать очень хорошие вещи.
Теперь пару слов про защиту от коррозии. Это больное место любых сталей, кроме разве что нержавейки и высоколегированных металлов (сия участь не избежала и цветных сплавов, лично видел прогнивший насквозь уголок из дюраля)
Неплохой способ придумали сварщики-автомобилисты: пока металл еще горячий (светится) нужно быстро намазать его солидолом. Довольно длительное время так обработанная сталь не поддается ржавчине. Вот, в общем-то, и все о водопроводных трубах.
Этюд 2. У10 и иже с ней
Здесь материала тоже много. Но и обработка сложнее. Здесь уже необходимо уметь проводить термообработку и знать ее режимы. Но что собственно обрабатывать?
Начнем с гаража и дачи. Для кухонных ножей (а также каких-нибудь скрытых лезвий-стилетов) хорошо подойдет старая тупая пила, которую точить ну никак не охота. Здесь радует простота обработки: закаливать ее не надо, достаточно вырезать, наклепать спуски и кромки, отшлифовать и можно спокойно заниматься всякими резными рукоятями, зеркальной полировкой и прочими художественными изысками. Наклепка производится, пока торец не станет в 2 раза тоньше, чем остальная пила. Здесь так же лучше поэкспериментировать, благо, что материала хватает.
Хорошую твердость и качество имеет пружинная сталь. Ленточные пружины от часов, обычные от стиральных машин…свою боевую цепь я делал именно из пружины. Из нее же можно сделать классный стилет-иглу (тоже когда-то делал)
Далее несколько сложнее.
Циркулярные диски стоит перезакаливать, т.к. с современной логикой «экономии» режущие кромки у диска из твердых сплавов, а остальной металл – недокаленный, вязкий, но углерода там, в принципе достаточно. В этом плане очень выигрывает советский инструмент, который в отличие от современного закаливали полностью. Если вы купили участок в какой-нибудь глухой деревне, то вам может о-о-очень сильно повезти: я на своем нашел огромный циркулярный диск (смотри статью «боевой тесак»), 6 (!) лезвий от шпоночного станка. Последнее – изумительный материал для ножей! Древнегерманский нож сакс из этих полотен:
Вообще хорошо закаленную сталь, довольно просто отличить от обычной стали по звону. У мягкой черняги звон глухой, а у закаленной – высокий чистый звук. Вся сложность обработки каленого материала заключается в том, чтобы не перегреть, а если сталь хрупкая – то правильно отпустить.
Это кованый кинжал из углеродистой стали с накладками рукояти из стали 3 и дюралевым больстером. Какая конкретно сталь – не скажу, лезвие мне досталось в подарок.
Теперь перейдем к рессорам и напильникам. Это материал для тех, кто планирует заняться ковкой. Рессора изначально довольно мягкая, а у напильника сильная закалка только на поверхности и если вы просто сточите его, то рискуете попасть именно на мягкую сердцевину. Сложные и интересные методы ковки стали описывать здесь не буду, а сделаю ссылочку на специалиста, который уже не один десяток лет занимается кузнечным делом. kuznec.ru или наберите в поисковике Виктор Кузнецов кузнец. Первая ссылка – его сайт.
Добавлю здесь только то, что старую рессору лучше не брать, т.к. на ее поверхности имеется много микротрещин, которые снижают качество и прочность изделия. Рессора плоха для ножей и больше подходит для топоров и мечей.
Этюд 3. Лигатуры или да поможет нам цветмет
Легированные и сложнолегированные стали – большая редкость. Но сразу условимся: мы говорим об углеродистых легированных сталях, т.к. качество режущей кромки определяет именно количество углерода, а не чего-либо еще.
Самое простое и доступное, на мой взгляд – отрезные алмазные диски по камню и бетону. Их основная часть состоит из стали х12 или 100х12 в российской ножевой маркировке. Эта сталь прекрасно закаливается, отжигается и обладает всеми положительными свойствами такой же по углероду обычной стали (У10). Также нет проблем с уковкой по толщине, т.к. диски обычно не толще 3 мм. Обратная сторона медали – наличие слабой токсичности этой стали. Дело в том, что для достижения свойств нержавейки необходимо 13% хрома, в этой стали его меньше. Если после шлифовки нож из этой стали вытереть насухо, то он не заржавеет. Но, с другой стороны, опустите его в горячий чай, и лезвие мигом покроется чем-то невразумительно темным. Это окись хрома, которая, в общем-то, канцероген. Для ножей походных, рабочих, боевых эта сталь идеальна, но на кухне ей делать нечего, и прежде чем отрезать таким ножом себе колбасы стоит подумать. Полубоевой нож из этой стали:
Гарда – нержавейка, рукоять – дюраль.
Далее – гаечные ключи. Их не надо перезакаливать, можно просто вытачивать из них и не париться. Из гаечного ключа идеальными получаются метательные ножи. Они обладают убийственной прочностью, неплохо держат острие, плохо ржавеют и обладают своеобразным голубоватым оттенком (добавка ванадия) Ниже – набор метательных ножей, два бодзе-сюрикена из арматуры и два метательных ножа из гаечных ключей. Третий – отпущенный обломок магазинного ножа.
Оружие делать можно не только из металла. Например, экзотично и необычно смотрится куботан из стекла или дубовый кинжал:
Оба они незаметны для металлоискателей и не считаются холодным оружием. Дубовый кинжал пробивает толстую джинсу, сам проверял.
Если сталь неизвестна
А что делать, если вы нашли лакомый кусочек стали и не знаете, подойдет ли он вам? Есть несколько способов выяснить его качество.
1. холодная ковка и керн.
Мягкая галимая черняга легко сминается молотком, а дыры в ней керном пробиваются на ура. Твердые сплавы же мнутся плохо и скорее расколются, чем помнутся, а кернер по ним скользит и трудно бить дырку в одном и том же месте. Ярким показателем твердости является полное сминание острия гвоздя по бетону об сталь.
2.
Метод искровой пробы помогает установить примерный состав стали и наличие лигатуры. Заключается в следующем: на наждаке (или болгарке) исследуемую сталь обтачивают и смотрят на цвет и характер искр. Ниже таблица данных
металл |
Цвет и характер искр |
Низкоуглеродистая сталь (черняга) |
Непрерывный пучок соломенно-желтых искр, звезд мало. |
Углеродистая |
Светло-желтый пучок со звездами |
У12, У13 |
Плотный короткий пучок с большим количеством разветвленных звезд |
У7, У10 |
Расходящийся пучок светло-желтый , много звезд. |
Хромистая |
Плотный пучок темно-красный, много сильноразветвленных звезд. |
Хромовольфрамовая (быстрорез) |
Прерывистый темно-красный пучок с более светлыми каплевидными звездами |
Пружинная кремнистая |
Широкий темно-желтый пучок со светлыми звездами. |
Кобальтовая быстрорежущая |
Широкий темно-желтый пучок без звезд. |
3. Поговорим о нержавейке. Помнится, в одном из комментов здесь кто-то высказывался о непригодности нержавейки для ножа. Как отличить ферритную (с малым количеством углерода) от аустенитной нержавейки? Все просто: ферритная не магнитится. Именно соединение углерода в сплаве усиливает магнитные свойства железа. Поэтому магниты и делают из высокоуглеродистых сплавов (за исключением современных ноу-хау из неодима или алюмомарганцевых).
4. Еще подскажет личный опыт. Перебрав центнер-другой разного железа, вы научитесь определять «на глаз» то, что подойдет, а с чем лучше и не возиться.
Бонус для любителей ножей и ножеделов
Что определяет качество вашего ножа? Опираясь, на какие характеристики можно сказать: этот нож хороший, а тот – хлам? Начнем с того, что разные ножи сделаны для разных целей. Универсального ножа просто не существует.
Основные характеристики ножа следующие:
- Твердость
- Прочность
- Вязкость
В зависимости от того, какой из признаков ярче, и определяется назначение ножа.
Миф: чем тверже нож, тем лучше режет
Если ваш знакомый на рыбалке перед вами хвастается, что, мол, у него нож 72 единицы по Роквеллу, а ваш всего лишь 54, то совсем не повод расстраиваться и завидовать. Лучше понаблюдать, сколько раз этот знакомый будет точить нож за рыбалку и как быстро он затупится. Очень твердое лезвие имеет неприятное свойство выкрашиваться при сильных нагрузках (кость какая-нибудь). А еще очень твердое лезвие трудно точить. Так что пускай он мучается с заточкой, а мы возьмем помягче, но получше. Да и вязкий нож проще и легче точить, как говорится, провел по голенищу сапога – и он снова бреет.
Прочность ножа складывается из твердости и вязкости. Эти же две характеристики определяют качество режущей кромки, и в то же время взаимоисключающие. Ножи с высокой твердостью целесообразно делать толще и затачивать под большим углом, иначе кромка выкрошится.
Нож для более мягких материалов (колбаса, огурцы и т.д.) лучше сделать несколько мягче. Он будет неплохо держать заточку, а угол можно будет сделать меньше, что значительно облегчает жизнь. Твердые тяжелые ножи больше годятся на порубить-построгать, чем в обычной жизни. Если же рубить и строгать мягким ножом, то очень скоро кромка сомнется и будет не слишком весело ее перетачивать.
Чтобы жало ножа не обламывалось, нужно делать его угол пошире, а спуски под большим углом. На внешний вид это несколько повлияет, но зато прочность повысится.
Неплохой, но жесткий способ проверки на прочность – изгибание лезвия в тисках на угол в 45 градусов. Если нож хороший, то он вернется в прежнее состояние без деформаций или не даст себя согнуть (для тонких), не сломавшись при этом.
На качество реза – проверка на весах. Кладем канат на весы и делаем резы до тех пор, пока нажим на нож не превысит определенное значение (например, 15 кг). Считаем резы и сравниваем.
Постскриптум
Для оружия, если есть возможность, лучше брать импортную сталь, желательно немецкую или японскую.
Что может быть лучше, чем
нож
из перекованного японского старого подшипника от любимой мазды? Наш же металл содержит изрядную долю фосфора и серы, которые вредны для стали. Из-за этого изделие быстрее сгнивает и имеет худшую прочность. А как же иначе? На Урале заводы еще со времен Петра 1 стоят, по тем технологиям гонят. Из нашего же металла лучше брать электросталь (сталь, выплавляемую не углем, из которого сера и идет, а с помощь электролиза). Это все те же подшипники. Для горна стоит нажечь древесного угля, т.к. он чистый, не содержит серы, которая в процессе нагревания может перейти в металл.
Вот и все, что я хотел рассказать о сталях. Удачи в трудах и творчестве!
Автор: Андрей Галкин
sekach.ru
Чем резать металл: выбираем ручной инструмент
В процессе строительства очень часто возникает необходимость в резке металла. Как это сделать дома? Как в процессе резки получить нужное изделие заданной формы и размеров?
Для всего этого нужен ручной инструмент, которому стоит быть у каждого хозяина. К счастью, выбрать сегодня такой инструмент не сложно, так как на рынках таковых приспособлений много.
При помощи него можно разрезать металл с толщиной от 0,7 до одного миллиметра. Если же разрезать нужно алюминий, то его толщина может быть больше — до двух с половиной миллиметров.
В таких ножницах два режущих ножа крепятся под углом. Конечно, есть две рукоядки. Ножи сделаны в форме клина с заострением от 65 до 80 градусов. Благодаря небольшому углу есть возможность резать нетвердые металлы, а благодаря большому — твердые. Такие ножницы бывают разных видов.
Если надо разрезать по прямой линии или по окружности с большим диаметром, нужны специальные ножницы, предназначенные именно для прямого реза. А с криволинейными лезвиями ножницы подходят для того, чтобы вырезать деталь по контуру или криволинейную. Для тех же целей используются пальцевые ножницы, которые бывают с правым или левым срезом.
У них рукоядка состоит из двух рукоядок, соединенных с помощью шарнира. Специальная конструкция позволяет разрезать металл, толщина которого два с половиной миллиметра, однако можно делить и металл толщиной до восьми миллиметров, потому что можно сменять ножи и диски.
Когда нужно резать мягкий металл толщиной до шести миллиметров или стальной лист до четырех миллиметров, то пригодятся рычажные ножницы. Еще есть кровельные ножницы, которые тоже применяются для металла, толщина которого два или три миллиметра. Отличаются эти ножницы особой конструкцией, которая позволяет крепить их к верстаку.
Кроме ножниц есть ручные ножовки, предназначенные для резки по металлу. Они нужны, чтобы резать металл большей толщины, трубы, профильный прокат и прутки. Чтобы выбрать ножовку, нужно знать, какой металл придется резать.
Если же металл имеет разную твердость, то лучше использовать ножовочное полотно с разной длиной зубьев. При замене ножовочного полотна новое полотно нужно устанавливать острием вперед, поле чего регулировать уровень натяжения.
Оцените статью: Поделитесь с друзьями!dm-st.ru
Режем металл листовой: как и чем лучше?
Очень часто мы попадаем в ситуацию, когда мы режем металл в домашних условиях. Тогда мы задаемся вопросом «чем резать металл» чтобы он получился нужной нам формы. Рассмотрим, какой инструмент нам для этого понадобится. Если вы часто занимаетесь резьбой по металлу, то нужный инструмент приобрести вам будет просто необходимо.
Ножницы по металлу
Виды часто используемых режущих инструментов по металлу: это ножницы и ножовки.
Ножницы по металлу – очень часто используемый инструмент для резьбы по металлическим изделиям:
- при помощи этого инструмента можно нарезать листы металла, имеющие толщину до одного миллиметра, также ими режут алюминий толщиной до двух с половиной миллиметров;
- внешне этот инструмент представляет собой два режущих ножа, которые крепятся под нужным углом, также имеются две рукоятки;
- чтобы ножницами было удобно пользоваться, ножи крепятся под углом от семи до двенадцати градусов;
- заостренный клин у ножниц также для удобства расположен под углом от шестидесяти пяти до восьмидесяти градусов;
- ножницами одинаково удобно резать как мягкий металл, так и твердый.
Ножницы подразделяются на пальцевые, силовые, рычажные, стуловые, для прямого реза и криволинейные:
- криволинейные ножницы используются для того, чтобы вырезать фигурную деталь или отверстие в металле;
ножницы по металлу
- ножницы для прямого реза нужны чтобы отрезать металл по прямой;
- пальцевые — также пригодятся для вырезания фигурных деталей;
- стуловые или их еще также называют кровельными, используют при нарезке металлических листов с толщиной от двух до трех миллиметров. У таких ножниц нижняя рукоять имеет изгиб для более удобной работы;
- силовые ножницы имеют специальные рычаги соединенные шарниром. При помощи таких ножниц можно разрезать более толстые листы. достигающие толщины в два с половиной миллиметра. Также у этих ножниц можно заменять режущие ножи и резать прутья при помощи дисков;
- рычажные ножницы. Эти ножницы при работе закрепляются на верстаке. При помощи нажатия на рукоять можно управлять подвижным ножом. Такими ножницами удобно нарезать мягкий металл (латунь) который имеет толщину до шести миллиметров, а также сталь до четырех миллиметров.
Ножовки для резки
Также для нарезки металла хорошо использовать ножовку. Таким инструментом режут более толстые листы, трубы, металлические прутья:
- у ножовки в горизонтальном или наклонном положении закрепляется режущее полотно;
ножовка по металлу
- полотно ножовки можно раздвигать для более удобной работы. Также можно раздвигать и острые зубья, обычно они расположены под стандартным углом в шестьдесят градусов;
- можно сделать разводку по зубьям или разводку полотна. Если делается разводка зубьев, то нужно отогнуть каждые два или три зуба ножовки.
Для каждого вида металла существует свой вид ножовки. Ножовки различаются непосредственно по числу зубьев. Например, чтобы разрезать сталь нужно взять ножовку, имеющую двадцать два зуба длиной по два с половиной сантиметра. Если полотно ножовки испортилось, его можно будет заменить. При переустановке полотно должно быть расположено вперед зубьями, для того чтобы отрегулировать его натяжение. Если нужно разрезать различный по плотности металл используйте разные ножовки.
↑Метчик
метчики по металу
Также можно разрезать металл при помощи метчика. Он помогает нарезать резьбу в уже имеющихся отверстиях. Внешне он похож на винт, который имеет режущие края.
Метчики бывают ручные, трубные, конические, машинные и гаечные.
- Гаечный метчик — нужен чтобы нарезать на гайках резьбу.
- Машинный метчик нарезает более точную резьбу, чем ручной.
- Конический метчик — нарезает коническую резьбу на металле.
- Трубный метчик используется, когда нужно нарезать резьбу в очень прочных металлах, например в стали или чугуне.
По всей длине стержня такого метчика находятся канавки. Резьба нарезается в уже имеющихся в металле глухих отверстиях.
Для разного вида металла нужен свой инструмент. Мы перечислили не все имеющиеся инструменты для резьбы по металлу. Есть много других инструментов. Но важно помнить, что работая с любым режущим инструментом очень важно соблюдать требования техники безопасности.
Советуем почитать по теме:
kreadom.ru
Как и чем режут металл: способы, виды оборудования
Резка - одна из самых обычных операций по обработке металлических заготовок.
Но тут сразу возникает вопрос: как и чем режут металл?
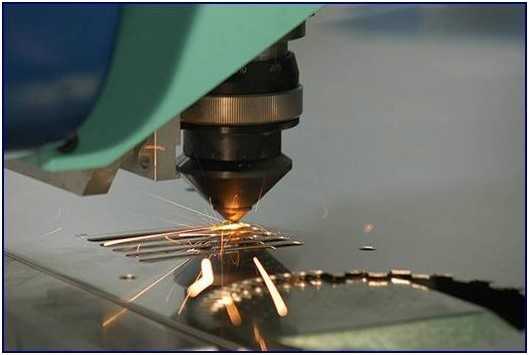
Металл можно резать механическим или термическим путем.
Принято различать две основных группы способов резания:
- Механические - распилка, резка ножницами и т. д.
- Термические, базирующийся на использовании струи какого-либо вещества - газа, воды и т. д.
Механические способы
В основе классификации механических способов резания обычно лежит ответ на вопрос: чем резать металл?Разрезание ножовкой и ножницами по металлу
Разрезание ножницами: а) разрезание листа на полосы; б) разрезание листаножницами.Вырезание круглой формы: в) неправильно; г) правильно
В домашних условиях металл обычно режут обыкновенной слесарной ножовкой. Процесс этот является достаточно трудоемким. Он значительно упрощается, если в распоряжении есть механическая ножовка.
В отличие от ножовок, существует достаточно много видов ножниц по металлу:
- Ручные ножницы позволяют разрезать относительно тонкий листовой металл. Они позволяют делать это быстро и точно, правильно следуя линии реза. Можно выделить несколько типов ручных ножниц: пальцевые, силовые, стуловые, рычажные, для криволинейного реза.
- Шлицевыми ножницами осуществляют как прямолинейную, так и криволинейную резку. Они позволяют резать металл в ограниченном пространстве, сохраняя при этом высокое качество реза. Приводятся в действие электродвигателем.
- Гильотинные ножницы могут разрезать металл с высокой точностью. Основные преимущества - отсутствие дефектов, высокая точность резания, сохранность внешнего покрытия разрезаемого материала.
Типы гильотинных ножниц:
Ручными ножницами можно резать относительно тонкий лист металла.
- Ручные ножницы. Главный недостаток - развиваемое усилие недостаточно для резки, если металл очень прочный.
- Механические ножницы. Приводятся в действие электродвигателем, поэтому производительность значительно выше, чем у ручных гильотин.
- Ножницы с гидравлическим приводом. Обеспечивают очень высокую точность работы. К тому же их можно оснащать ЧПУ, позволяющим заметно увеличить их производительность за счет сохранения в памяти типовых параметров разрезов.
Сабельные и дисковые пилы, углошлифовальные машины
Сабельные пилы по принципу действия похожи на электролобзик. Внешне выглядят как электродрель, только вместо сверла - выдвинутая вперед пила длиной от 10 до 35 см, совершающая возвратно-поступательное движение. Обычно пила питается от сети, но выпускаются и аккумуляторные варианты.
Для точного и быстрого резания металла применяют сабельные пилы.
Для разных видов работ применяются различные виды пильных полотен. Они легко меняются, подобно сверлам в электродрели. Система крепления надежная и рациональная. Зная, с чем предстоит работать, можно правильно выбрать соответствующую пилку. Например, чем больше кривизна разреза, тем уже должно быть полотно.
Для работы с сабельной пилой нужны навык, твердая рука и хороший глазомер.
Проще работать дисковыми пилами. Их режущие диски обычно изготовляют из твердого высоколегированного сплава или специальной быстрорежущей стали. Предназначены пилы для резки разнообразных металлических профилей, изготовленных из самых различных металлов и сплавов, обеспечивают узкий пропил, малое количество стружки.
Чтобы правильно выбрать пилу, следует особое внимание обратить на распиловочный круг, в частности на его диаметр. Чем он больше, тем больше возможности инструмента. После выполнения распила обычно требуется дополнительная обработка по удалению острых кромок. К минусам следует отнести довольно большие габариты и достаточно высокую стоимость.
Дисковой пилой можно пилить медь, алюминий и другие цветные металлы.
Большинство потребителей даже и не подозревает, что «болгарка» - это углошлифовальная машина. Дело в том, что это чудо техники родом из Болгарии, а наши люди длинных названий не любят. В большинстве случаев болгарка, оснащенная диском для распила стали, прекрасно заменяет дисковую пилу по металлу, хотя, судя по названию, изначально она предназначалась для шлифовки.
Сегодня очень многие используют ее именно как пилу, а не для шлифования, хотя современной болгаркой можно и резать, и зачищать, и полировать, и т. п. Причем резать и шлифовать можно практически все материалы. Главное - покупать различные инструменты не нужно. Для различных материалов и работ приобретаются лишь разные расходные материалы, а сама машина нужна только одна.
Термические способы
Способы резки, относящиеся к этой группе, можно разделить на такие виды: газовая и газоэлектрическая резки металлов.
В этих способах резки нагрев металла осуществляется газовым (кислородным) пламенем, а источники электроэнергии не используются. Различают три основных способа такой резки:
Кислородная резка металла предусматривает его нагревание. кислородная горячая струя режет металл и удаляет оксиды которые там возникают.
- Кислородная. При этом способе металл в зоне реза сгорает в кислородной струе, ею же выдуваются образовавшиеся оксиды.
- Кислородно-флюсовая. В область разреза поступает порошок-флюс, который облегчает процесс резки благодаря химическому, термическому и абразивному воздействиям.
- Кислородно-копьевая. Высокая температура создается за счет сгорания так называемого копья - трубки, через которую продувается струя кислорода.
Основные преимущества этих способов:
- низкая стоимость;
- можно резать толстый слой металла.
Основные недостатки:
- большой расход металла;
- низкая точность;
- необходимость дополнительной обработки деталей;
- малая скорость резки;
- большая толщина реза;
- термическая деформация металла.
При газоэлектрической резке металл нагревается за счет источника электроэнергии, а расплав из зоны реза удаляется газовой струей. Существует два способа этой резки:
- Воздушно-дуговая - жидкий металл из зоны плавления удаляется струей сжатого воздуха.
- Кислородно-дуговая - нагретый в пламени дуги металл сгорает в поступающей струе кислорода, ею же выдувается.
Применяется в основном для исправления дефектов сварных швов. Главный недостаток - науглероживание места разреза вследствие сгорания угольных электродов.
Плазменная резка
Плазменная резка на сегодняшний день самый совершенный, быстрый и экономически эффективный способ резки металла.
Весьма перспективный и быстро прогрессирующий метод. Разрезаемый металл плавится струей плазмы - ионизированного газа с температурой в десятки тысяч градусов. Плазменная струя создается в особом устройстве - плазмотроне - из обычной электрической дуги за счет ее сжатия и вдувания в зону реакции плазмообразующего газа. Две основных схемы обработки:
- Резка плазменной струей. При этом способе дуга возникает между электродом и наконечником плазмотрона. Обрабатываемая деталь в электрическую цепь не включена.
- Плазменно-дуговая - дуга возникает между неплавящимся электродом из тугоплавкого материала и разрезаемым металлом. Эффективный и более часто применяемый метод.
Преимущества плазменной резки в сравнении с газовыми способами:
- высокая скорость резки;
- универсальность применения;
- возможность резать с высокой точностью и качеством;
- отсутствие необходимости в дорогостоящих газах;
- возможность вырезания деталей сложной формы;
- безопасность и экологичность.
Недостатки:
- дороговизна и сложность оборудования и его техобслуживания;
- невозможность резки заготовок толщиной более 80-100 мм;
- ограниченный угол отклонения реза от перпендикулярности;
- повышенный уровень шума.
Остальные термические методы вследствие ряда причин, из которых основная - высокая сложность и стоимость оборудования, пока широкого распространения не получили. Ограничимся лишь их перечислением:
- гидро- и гидроабразивная резка;
- лазерная и газолазерная резка;
- метод электрической эрозии;
- криогенная резка.
Резюмируя все вышесказанное, можно сделать вывод: способов и видов оборудования для резки металлов очень много. Правильно выбрать наиболее подходящие способы можно, лишь взвесив множество факторов, прежде всего финансовые возможности.
1metallocherepica.ru
Какой металл в воде не тонет ?
"Литий, натрий и калий легче воды и плавают на ее поверхности, реагируя с ней. " <a rel="nofollow" href="http://www.himhelp.ru/section24/section13/section75/" target="_blank">http://www.himhelp.ru/section24/section13/section75/</a> ЛИТИЙ – самый легкий из металлов, он вдвое легче воды и всплывает даже в керосине. (Плотность лития – 0,54 г/см3). <a rel="nofollow" href="http://experiment.edu.ru/catalog.asp?cat_ob_no=12793&ob_no=12804" target="_blank">http://experiment.edu.ru/catalog.asp?cat_ob_no=12793&ob_no=12804</a> НАТРИЙ легче воды (плотность 0.968) <a rel="nofollow" href="http://glavmetall.ru/blogos/post_1190069653.html" target="_blank">http://glavmetall.ru/blogos/post_1190069653.html</a> КАЛИЙ "Кроме того, потассиум (английское название калия был мягок, как воск, и легко резался ножом. И он оказался так легок, что не всегда тонул даже в керосине, хотя сам керосин легче воды. " ( "Металл, который в воде не тонет, а на льду горит") <a rel="nofollow" href="/" title="486430:##:http://www.dutum.narod.ru/element/elem21.htm" target="_blank" >[ссылка заблокирована по решению администрации проекта]</a>
калий-он по воде бегает, а в большом количестве-бахает...
так оно и есть-ртуть.Интересно, эт прикол, или домашнее задание по химии?
Любой твёрдый металл, обработанный в виде чаши или полусферы (в принципе любая пустотелая форма) с водоизмещением более собственной массы. Металлов плавающих в воде в полнотелых предметов в природе не существует.
Любой металл, который легче двух атомов кислорода. Литий, калий, натрий.
touch.otvet.mail.ru
Какая сталь лучшая для ножа
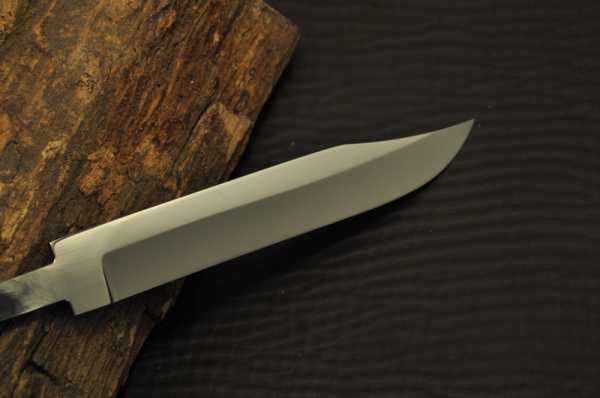
Лезвия ножей всегда работают в тяжёлых условиях. Обусловлено это тем, что в начальный момент резки усилие резко увеличивается от нуля до своего максимального значения, а затем так же стремительно снижается. Вдобавок, если нож используется часто, и в быстром темпе, подобные чередования максимальных нагрузок с нулевыми приводят к появлению в тонком лезвии ножа усталостных напряжений противоположного знака: растяжения и сжатия. Стойкость любой стали в такой обстановке – минимальна.
Так как же выбрать сталь для клинка ножа?
Особенность эксплуатации лезвий ножей
Для обеспечения своей долговечности, клинок ножа должен отвечать ряду требований, многие из которых противоречат одно другому:
- Обладать высокой твёрдостью, причём в достаточно широком диапазоне температур: от -300С до +1000С. Последнее значение связано не с тем, что ножом пытаются разрезать раскалённый материал – хотя и это бывает – но и с тем, что в процессе резки из-за сопротивления разрезаемого материала нож нагревается силами механического трения.
- Иметь повышенную устойчивость от продольного изгиба, особенно, если клинок узкий и достаточно длинный.
- Способствовать минимальной деформации лезвия во время его использования.
- Прочность ножа должна быть наибольшей, поскольку иначе лезвие быстро тупится.
- Материал должен способствовать лёгкой заточке лезвия, с минимальными пореями металла и при наименьшей трудоёмкости процесса.
- Иметь повышенную упругость, что воспрепятствует ломке ножа при критических нагрузках и сделает его пользование безопасным для окружающих.
В полном виде такие требования выполнить невозможно, поэтому производители рассматриваемого инструмента идут на разумный компромисс, и сочетают такие условия, которые бы способствовали максимальной функциональности и работоспособности ножа для конкретных условий его применения.
Стали, применяемые для производства ножей
Горячая резка – случай, достаточно экзотичный, поэтому в дальнейшем будем рассматривать стали, порог эксплуатационной стойкости которых не превышает 2000С.
Нет смысла использовать для изготовления ножей конструкционные стали, процентное содержание углерода и карбидов железа в которых недостаточно для того, чтобы гарантировать приемлемую долговечность лезвия ножа. Остаются инструментальные стали, и ряд специальных, которые по совокупности своих характеристик также могут быть причислены к приемлемым для изготовления ножей.
К таким сталям относятся:
- Углеродистые нелегированные инструментальные стали, которые поставляются в соответствии с требованиями ГОСТ 1435.
- Среднелегированные инструментальные стали пониженной теплостойкости поставляемые по ГОСТ 5950.
- Специальные подшипниковые стали с повышенным содержанием хрома, производство которых ведётся согласно ГОСТ 801.
- Высокоуглеродистые стали с повышенным содержанием кремния и марганца, которые формально относятся к конструкционным, однако фактически ими уже не являются, а входят в группу рессорно-пружинных сталей (ГОСТ 14959).
Практически ко всем вышеперечисленным сталям имеются их зарубежные аналоги.
Ножи из сталей, которые не вошли в приведенный выше перечень, изготавливать не рекомендуется: их сочетание твёрдость — прочность — пластичность будут низкими, даже при условии их закалки на максимально возможную твёрдость.
Особенности технологии ковки ножевых клинков
Ковка клинков считается древнейшей операцией пластической обработки металлов и сплавов. Суть процесса состоит в том, чтобы не только оттянуть и заострить с одной стороны лезвие, но и обеспечить в результате выполнения кузнечных переходов наиболее благоприятные макро- и микроструктуру металла.
Исходной заготовкой для ножа служит стальная полоса, причём лучше горячекатаная: исходный металл получается более высокопластичным, и легче поддаётся последующей ковке. Окалина же легко сбивается ударами молота, и негативного влияния на проковку не оказывает.
Вначале полосу разделяют на штучные заготовки, длина которых определяется расчётным путём, и зависит от требуемых рабочих характеристик самого ножа. Чем прочнее должен быть клинок, тем длиннее заготовка. Для разделки можно использовать любые технические решения – резать металл на пилах, рубить кузнечными топорами, либо использовать резку на кривошипных ножницах. Механическая резка сопряжена с повышенным расходом металла (практически, в зависимости от конструкции пил, отходы составляют 2…8%). Кроме того, в зоне реза происходит естественный отжиг, сопровождающийся снижением прочности стали, и это надо учитывать при выборе последующих переходов ковки.
Рубка кузнечным инструментом не изменяет исходные характеристики стали, но не отличается особой точностью. Кроме того, при рубке (особенно нагретой заготовки) происходит её деформация, что вынуждает перед собственно ковкой вводить переход правки заготовки.
Резка на пресс-ножницах – наиболее современный способ получения заготовок ножей. Точность резки и конфигурация конечного изделия вполне пригодны для изготовления высококачественных клинков. Кроме того, резка сдвигом – самый производительный вариант для получения заготовок под ножи.
Для ножей особенно важно обеспечить мелкозернистую структуру в стали. Для этого производится многократная проковка, причём с каждым последующим ударом молота зерно становится всё более мелким, что повышает однородность свойств металла по всей длине клинка. Таким образом достигают оптимальных характеристик твёрдость — прочность — пластичность стали клинка ножа. На рисунде справа изображена структура металла. В левой части рисунка крупнозернистая, в правой — мелкозернистая.С повышением процентного содержания в стали углерода и легирующих элементов число проходов ковки увеличивается. После проковки следует оттяжка краёв заготовки, и калибровка острой части лезвия клинка. Её ведут при уже несколько подостывшем материале, из-за чего усилие несколько возрастает, но зато одновременно увеличивается и точность течения металла.
Термическая обработка ножей
Именно на этом этапе клинку сообщаются те физико-механические характеристики, которые важны для эксплуатационной долговечности ножа. Среди наиболее часто встречающихся дефектов ножей следующие:
- Хрупкое выкрашивание режущей кромки;
- Трещинообразование;
- Пластический изгиб лезвия;
- Недостаточная твёрдость (затупление или смятие).
Соответственно этому подбирается режим термической обработки. При этом учитывается также и материал ножа.
Далее рассматриваются нюансы термообработки ножей из сталей всех групп, перечисленных ранее.
Ножи из нелегированных инструментальных сталей
Ножи из нелегированных инструментальных сталей. Чаще применяют стали марок для ножей У7, У8А, У9. Ковка таких заготовок производится в температурном диапазоне 11000С…8500С (здесь, и далее первая цифра соответствует температуре начала технологической операции, а вторая – температуре её завершения).
При нарушении температурного режима в стали образуются трещины, как внешние, так и внутренние.
Закалку таких сталей производят с температур 780…8500С, причём с целью снижения окислообразования применяют солевые ванны с расплавами солей BCl2, MgF2 и NaCl. Это снижает упругую деформацию клинка, и практически не влияет на остаточную прочность лезвия. После закалки производят отпуск клинка от температур 150…2000С на твёрдость HRC 63…65.
Готовый нож из таких сталей будет иметь наименьшую себестоимость производства, но и минимальную стойкость, кроме того, ножи из нелегированных сталей не отличаются высокой устойчивостью от коррозии. Положительная особенность – отличная гибкость клинка – позволяет изготавливать из таких сталей достаточно длинные лезвия (при соотношении длины к толщине 1000:1 и даже более).
Ножи из среднелегированных сталей пониженной теплостойкости
Ножи из среднелегированных сталей пониженной теплостойкости. Для изготовления чаще принимают стали марок для клинка ножа типа 4ХС, 9ХС, ХВГ, Х6ВФ, 6Х3ФС и им подобные. Наличие хрома обуславливает повышенную твёрдость готового изделия в сочетании с повышенным пределом текучести, который, к тому же, мало зависит от температуры на режущей кромке ножа. Кроме того, клинки, изготовленные из таких сталей, отличаются повышенной размерной точностью, на значение которой не влияет режим термической обработки.
Нагрев под ковку заготовок из таких сталей производят в довольно узком диапазоне температур: от 1100…11200С до 750…7800С, что обуславливается интервалом аустенитных превращений в данных сталях, с одной стороны, и влиянием легирующих элементов – с другой. Более жёсткими являются и требования к технологии самой закалки: её ведут при 830…8500С на конечную твёрдость 63…65 HRC. Но такая твёрдость для лезвия клинка неприемлема, поскольку резко снижается его упругость, поэтому далее обязательно производится отпуск при 170…2000С. В качестве закалочной среды используют масло; скорость охлаждения клинка при этом несколько снижается, что обезопасит изделие от излишней хрупкости при последующем использовании. Подобная технология применяется и при изготовлении ножей из шарикоподшипниковых сталей типа ШХ6, ШХ9 или ШХ15.
Ножи из рессорно-пружинных сталей
Ножи из рессорно-пружинных сталей типа 70ХФ, 60С2 или нелегированных сталей марок 75, 80 отличаются высокими упругими показателями, что определяется высоким процентом углерода и легирующих элементов, способствующих повышению твёрдости – кремния и марганца. При высоких показателях твёрдости (от 54…58 НRC) такие стали характеризуются повышенными упругими свойствами. Это достигается закалкой со средним (400…5000С) отпуском.
Однако ножи, изготовленные из сталей перечисленных марок, не рекомендуется применять при повышенных температурах более 2000С, из-за склонности к разупрочнению.
www.m-deer.ru
Первые вопросы и ответы
Ну вот, наступило время для продолжения экспериментов... После анализа всей почты выяснилось основное направление... Были, наверное, на моей страничке и те, кто давали "очень умные" советы в интернете, и те, кому так необходима была помощь. Так или иначе, вопрос о продолжении решен, и оно будет. Но сразу хочу предупредить всех, кто просил о помощи в создании холодного оружия... На моей страничке этот вопрос рассматриваться НЕ БУДЕТ!!! Цель моей работы - это попытка рассказать о приемах и способах в производстве ножей, неизвестных широкой аудитории . Хотя, в частном порядке, на некоторые вопросы я постараюсь ответить. Были и заказы... Спасибо и всем тем, кто просто благодарил. Если вдруг так случится, что те, кто задавал вопросы по "мылу", не найдут ответов на свои вопросы - не отчаивайтесь... Это всего лишь значит, что ответ готовится и со временем все появится. А пока все будет несколько сумбурно и скомкано (к сожалению). Со временем постараюсь упорядочить и расположить как следует. Периодически буду добавлять дописанный материал. Вы первые судьи - Вы же и помощники. Те, кто придет после... будут пользоваться плодами Вашего и моего труда. Как правильно вывести спуски и режущую кромку? Чтобы было понятнее, как управлять заготовкой - небольшая картинка. 1.Экран (служит для защиты от отлетающих частиц абразива и металла) 2.Заготовка. 3.Наждачныйкамень. Сами понимаете, что профиль долья стачивается, исходя из диаметра наждачного круга. Было бы неправильно считать, что изменить высоту долья невозможно. После получения некоторых навыков можно достичь и этого.
Тупой угол режущей кромки приведет к тому, что поправить притупившееся изделие для дальнейшей работы - что евнуху растлить девицу. Править придется постоянно и долго. Среди профессионалов толстый спуск с тупой режущей кромкой метко прозван "линейкой". Чтобы испытать удовольствие от резки таким ножом, достаточно заточить кузнечную стальную линейку, и наглядное пособие готово. Грешат подобным конструкционным действом достаточно много "спецов". Даже попадаются конструкторы ножей, считающие изготовление мини-колунов своей основной задачей, забывая об основном требовании к ножу - НОЖ ДОЛЖЕН РЕЗАТЬ. Я для себя установил другое требование: НОЖ ДОЛЖЕН РЕЗАТЬ ВСЕГДА. Докажите, что я неправ, или сделайте нож с толстым спуском и "дубовой" режущей кромкой, который будет обладать небывалой остротой, поставив на клинок любую узорчатку. И я уймусь. Не буду более досаждать Вам своими изысканиями. Недавно на TV в программе "Времечко" был показан сюжет об одном плодовитом на изделия конструкторе ножей. Гордость за свои изделия распирала его так, что он договорился аж до того, что высказал некую идею: неудачный образец попадает только на кухню к жене. Бедная женщина! Перед телекамерой она что-то там шинковала тупыми ножами скинеровой формы, но надо отдать ей должное... она гордилась своим мужем. А он все говорил... А она резала... Моя супруга уже где-то около 10 лет, поправив нож об нож... режет, шинкует и разделывает достаточно острыми ножами не приставая с заточкой. Минус и самой программе "Времечко". У них в титрах проскакивает имя одного человека - СЕРГЕЙ ХАНОВ. Таких людей надо знать... Это бывший кузнец (впрочем кузнец не может быть бывшим). Его мастерству можно позавидовать. Из стального кругляка ШХ15, диаметром где-то 60-70мм, он способен ЗА ОДИН НАГРЕВ(!) отковать и прокатать полосу толщиной до 5мм без микродефектов. Кузнецы и металловеды меня поняли. Как изготовить нож с "нуля", из куска железа?Мне кажется, что это уже будет лишнее. Впрочем, когда будет нечего делать займусь и этим. А пока - причины, по которым я не обьясняю все с самого - самого... Мне бы пришлось объяснять: 1. Правила розжига печей. 2. Правила техники безопасности. 3. Принцип направления текучести стали при деформации в горячем состоянии. И так далее и тому подобное. Наверное в условиях домашней мастерской все это ненужно, да и невозможно. По крайней мере для подавляющего большинства посетителей этих страниц. Когда закончится весь теоретический материал, я скорее всего дам контактный телефон для связи. И те кто захочет практики, возможно испытают это несравнимое ни с чем,вдыхание двуокиси углерода, абразивной пыли и деревянных опилок. Изготавливаете ли вы холодное оружие? Невнимательное чтение страниц привело к тому, что появились заказы на изготовление холодного оружия. К сожалению я этим не занимаюсь вовсе. Наибольшее удовлетворение для меня - это изготовление ножевых изделий с заранее заданными режущими свойствами. Например моей работой - является изготовление опытных образцов (нож,вилка,ложка) комплекта для детей больных ДЦП (Детским Церебральным Параличом). С гордостью могу сказать, что конкурс был выигран и на заводе МЭП (МосЭлектроПрибор) приступают(до сих пор!) к промышленному производству. Впрочем, за это впоследствии и выгнали. Больно не нравятся начальникам с комплексом неполноценности самостоятельные работники. Выгоняли - измывались. Но нет худа без добра. Сейчас у меня своя мастерская, свой рабочий телефон, короче полная свобода. И как приятно работать и делать нужное людям. Ведь самая лучшая оценка моего труда в вашей благодарности. Каковы особенности изготовления метательных ножей?Рассказа о метательных ножах наверное у меня не получится вовсе. Вся конструкция этих ножей сводится к двум принципиальным особенностям. Во-первых: балансировка, во- вторых: достаточная прочность конструкции. Применением "золотого сечения" - добиваемся особой грациозности, а снижением твердости - достигаем прочности. Низкая твердость - обеспечивает надежность при многчисленных тренировках. Кстати скорее всего именно тренировки - наиболее важная особенность применения метательных ножей. Ну, а баланс - это дело наживное. Можно заранее изготовить болванку ножа, далее добиваться балансировки опытным путем, используя снятие ненужного металла высверливанием и стачиванием. Немаловажная деталь - глазомер. На моем жизненном пути встречался некто Петр Васильевич Киселев - машинист на молотах. Путем тренировки глазомера - он с двух - двух с половиной метров, определяет размеры поковок с точностью до +/-1мм. Ну, а про фокусы с закрыванием спичечного коробка я вообще не говорю. После длительного использования и многочисленных заточек, теряется товарный вид изделий. Как же вернуть былой блеск? Используя иллюстрации, попытаюсь объяснить и это. Как видно невооруженным глазом, диаметр круга 300мм. Весь секрет в том, что при заглаживании дольевых рисок (см. долье,желоба), нужно снижать диаметр кругов. Например долье проложили кругом 25А40П диаметром 300мм, далее проходите 24А25П но уже диаметром 150-180мм, и завершаете уже войлочными кругами на "морковке" с накатанным абразивом - диаметром 80-100мм. При снижении диаметров не происходит завалов и проявляется четкость линий. Посмотрите войлочный круг на морковке. Как "поднять нос"? В скинерах и некоторых других моделях, необходимо чтобы нос клинка был задран вверх. Можно конечно взяв заготовку "с запасом" сточить по форме. Но бывает так, что есть возможность или отковать "на горячую", или "на холодную"(т.е. на сыром и не нагретом металле) нагартовать. Нижняя часть рисунка показывает, какая заготовка станет после обработки, а на верхней части, в синеньком кружочке, где закрашено сереньким - показано,куда надо осторожно наносить удары. Как определить марку стали "на глазок" ? Наверное, я бы и сам хотел это узнать. Для того, чтобы приблизительно определить марку стали - мне необходимо, как минимум, проверить ее "на искру" - чиркнуть пластиной или готовым изделием о работающий наждачный камень. По снопу и цвету искр можно приблизительно определить, из чего же все и сделано. Например, "быстрорез" - сталь Р18 - имеет отдельные искорки темно-красного цвета, а ст. 65Г- достаточно плотный пучок искр желтого цвета, со звездочками на концах. У профессиональных термистов всегда в арсенале имеется большой запас пробников практически на любую марку стали. Как-то пробовал делать нож из циркония - плотный пучок искр ослепительно белого цвета. Практически, как у титана. Дамаск и булат без травления можно "почуять" в косых лучах на плоскости. Это, наверное, единственный случай, когда можно визуально определить резкое отличие одной группы стали от другой. Как говорится: "На булате не напишешь, и с булата не сотрешь". Для более пытливых посоветую книгу В.Г.Шмакова "КУЗНИЦА В СОВРЕМЕННОМ ХОЗЯЙСТВЕ" (изд. "МАШИНОСТРОЕНИЕ" 1990). Как закалить пластину без кузницы или "термички"?Бывает так, что нужно закалить полоску, а кузницы или "термички" рядом нет. Но случайно подвернувшаяся пластина 40Х13 не дает покоя, и ой как хочется хучь что сделать из нее. Первым делом идем в магазин и покупаем "литруху" её, родимой. Потом можно взять капустки квашеной, огурчиков, травки (кому какой хочется) зеленой, семужки(рыба), осетринки(рыба), пару банок пива (лекарство) и т.д. и т.п. Ищем сварщика(цу). Все это дело уговариваем, а за разговором так ненавязчиво намекаем: мол, есть пластина, но отсутствие газовой горелки не дает возможности нагреть ее (пластину) до желтого цвета. Я думаю, сварщик не откажет вам в этой услуге (если "оно" начнет кочевряжиться - повторите "первое дело"). После того, как "сварной" равномерно прогреет пластину до желтого цвета, незаметным (но ловким) движением руки вынимаете из кармана лист газеты и пару рельсовых кусков. Газету быстро мочите, чтобы она была влажной, и укладываете на один кусок рельсины таким образом, чтобы один конец свешивался. Прогретую пластину кладете на газету, заботливо накрываете (от сквозняков) свесившимся куском и прижимаете второй рельсиной. Должен получиться "бутерброд": рельс/ газета/ пластина/ газета/ рельс. Перекурите. Далее нужно аккуратно зачистить на пластине небольшой пятачок. Остается последняя операция - отпуск (термин кузнецов и термистов). Необходимо прогреть пластину, опять же равномерно. Как только на зачищенном "пятачке" появится коричнево-желтый налет (этот окисел называется "цвет побежалости"), оставьте пластину в покое - она готова. Если есть возможность добыть несколько шамотных кирпичей, можно соорудить небольшой домик - подобие печи. Нагрев пройдет более качественно. В свое время подобную конструкцию я видел на заводе "Серп и Молот" в начале кооперативной волны. Занимаетесь ли вы ремонтом ножей? В своей практике занимаюсь ремонтом как дорогих импортных моделей, так и полюбившихся недорогих отечественных. В последнее время очень много появилось ножей АО "ТРУД". Мне кажется изменение режимов термообработки - пошло бы только на пользу Нижегородцам. Для нержавейки твердость 40 HRC все-же маловата. Посмотрите проверенную модель Но воскресить я возьмусь не всё. Лет 10, наверное, мы слышим по телевизору о "супер-ножах", гарантия у них не меньше 25 лет, режущей частью является пилка. Мне приносили много подобного вечного... Я отказывал в ремонте. Хвостовик сидит в рукояти не более 30мм. Нагрузка при распиловке продуктов на крепежное соединение достаточно серьезная. Клинок вылетает из ручки в ближайшие полгода. Сообщите мне о местонахождении таких ножей, купленных не 25 лет тому назад, а хотя-бы 2-3 года, покажите, что они режут... И я готов вернуться к этой теме. Почему нож или режет или рубит? Другого и быть не может. Представьте себе профессиональный разделочный нож: у режущей кромки 0,2-0,3 мм. Толще нельзя - просто руки "отвалятся" при правке об мусат. Некоторые изготовители булата пытались меня удивить и предлагали в работу образцы своих сталей... Но после описания тестирования (изготовление образца и передача в работу профессионалу) как-то это дело затихает. Естественно, цена - немаловажная деталь. Ведь "profi", по большому счету, глубоко наплевать, из какой стали сделан нож. Ему важно, чтобы нож резал как можно дольше без правки, тем наипаче без заточки. С моей точки зрения, при толщине режущей кромки 0,2мм рубить гвозди нежелательно - при резке зазубрины дадут о себе знать. Ну, а по поводу рубки гвоздей... Заурядная сталь 30Х13 толщиной 1,5мм, закаленная в японской вакуумной печи "УЛЬВАК" по стандартному режиму, при соответствующей заточке совершенно свободно выполняет роль рубила гвоздей... Но режут ножи с соответствующей заточкой недолго. Да и резать ими трудно. |
prokopenkoff.narod.ru