Заточка токарных резцов по металлу. Углы заточки токарных резцов по металлу
Правила заточки токарных резцов по металлу: инструмент, угол, доводка
Из всех технологических процедур, выполняемых над металлическими деталями, точение считается самой популярной. Ввиду этого заточка токарных резцов по металлу имеет большое значение. Ее нужно осуществлять правильно. Порядок проведения заточки токарных резцов зависит от материала, из которого сделан инструмент, назначения резца (фасонный, проходной, для нарезки резьбы, для расточки).
Как сила резания зависит от угла затачивания
Сила резания зависит от углов заточки, в особенности от переднего. Чем больше данный угол, тем меньше сила резания и тем проще отделять металлическую стружку. Однако это не означает, что передний угол возможно неограниченно увеличивать. При чрезмерном увеличении надежность резца по металлу уменьшается. Его кромка подвергается сильному износу, выкрашиванию. Ввиду этого, когда подбирают величину переднего угла, стараются не только уменьшить силу резания, но и получить прочную кромку, стойкий к износу металлорежущий инструмент.
Иногда используют токарные резцы с отрицательным передним углом (от – 5 до -10 градусов). Обычно такие инструменты используются при обточке твердых либо закаленных металлов.
Особенности затачивания
Есть некоторые особенности, которые необходимо принимать во внимание, осуществляя затачивание резцов для токарного станка своими руками. Задняя часть инструмента обрабатывается за 3 шага:
- Сначала выполняют обработку задней части под углом, который равен заднему углу державки. Обычно он больше, чем задний угол резания (примерно на 5 градусов).
- На втором шаге осуществляют обработку задней части режущей пластинки. Ее затачивают под углом, который превышает задний угол резания на 2 градуса.
- Теперь нужный угол формируется посредством доводки. Процедура выполняется на узкой фаске, которая прилегает к рабочей кромке.
За несколько шагов затачивается и передняя часть инструмента для токарного станка. Сначала затачивание осуществляется на угол, который равен углу режущей пластинки. Угол резания, формируемый на передней части инструмента, создают посредством чистового затачивания либо доводки.
Заточка резца облегчается, если применять особые накладки, устанавливаемые промеж опорной поверхности и станочного стола. Для того чтобы точно и качественно заточить инструмент, можете изменить конструкцию стола, добавить возможность регулировать его по высоте и поворотному углу. После подобного изменения использовать накладки будет не нужно.
Для заточки резца рабочая кромка должна быть расположена на одной линии с серединой абразивного круга. Стоит принимать во внимание, в каком направлении вращается точило. Так вы сведете к минимуму шанс того, что режущая пластинка оторвётся от резцовой державки. При вращении точила пластинка должна быть прижата к державке, а не оторвана от нее.
Разумеется, что по окончании затачивания резца нужно выполнять проверку правильности исполнения. Легче всего проделывать это особым шаблоном. Можете сделать его либо купить в магазине. Если будете изготавливать шаблон собственноручно, используйте листовую сталь.
Большая твердость подобного трафарета, которую он приобретет после закаливания, позволит применять его продолжительный срок. Делая шаблон, нужно вырезать на нем отверстия, которые соответствуют ходовым углам затачивания. Лишь после создания отверстий трафарет закаливают. Стоит учесть, что от того, насколько точно изготовлен подобный шаблон, зависит правильность затачивания режущего инструмента.
Для выполнения доводки применяют оселки из меди, присадочные элементы. Для доводки инструментов из твердых сплавов используют особую пасту, борный карбид, который смочен керосином. Для инструментов из иных металлов применяют оселки с малым уровнем абразивности. Их смачивают автомобильным маслом либо керосином.
Типы затачивания
Крупные предприятия, занимающиеся обработкой металлов обязательно располагают необходимыми для затачивания инструментов специалистами и оборудованием. Владельцы небольших мастерских выполняют заточку собственноручно.
Заточка резцов может быть выполнена одним из следующих методов:
- Абразивный (на шлифовочном круге).
- Механико-химический (выполняется обработка специальными средствами).
- С помощью особых приборов.
Абразивное затачивание выполняется на заточном, токарном устройстве либо на шлифовочном брусочке. Вручную трудно наточить резец, соблюдая требуемые углы. Дополнительную сложность создает нагрев металла, приводящий к потере свойств. Ввиду этого качество затачивания прямо зависимо от навыков рабочего.
Резцы из твердых сплавов точат на зеленом карборунде. Инструменты из разных видов стали проходят обработку шлифовочными кругами, сделанными из среднетвердого корунда. Начальное обрабатывание осуществляется оселками с абразивом 36-46, завершающее – 60-80. Перед тем как устанавливать круг на станочное устройство, нужно удостовериться в том, что он целостен. При обработке он может сломаться, травмировать токаря, изменить углы токарного резца.
Механико-химический способ дает возможность эффективно и быстро заточить резец, предотвращает образование сколов, трещинок. Данный метод используется для заточки больших инструментов из твердых сплавов. Они проходят обработку купоросным раствором. В результате химической реакции образуется тончайшая защитная пленка, смываемая частичками абразива, которые присутствуют в растворе. Процедура выполняется в станочном устройстве, которое оборудовано резервуаром с передвижным шлифовальником. Зафиксированный инструмент перемещается возвратно-поступательно. Кроме того, резец прижимается к абразиву (150 г на кв. см).
Заточку алмазных резцов выполняют на специальном оборудовании электрокорундовыми/кремниевыми кругами.
Углы затачивания
Далее будет приведен список углов заточки для всех распространенных материалов. Первая дробь указывает на задний угол при черновом обрабатывании, вторая – на задний угол при чистовой обработке. Третья дробь показывает величину переднего угла. В числителе указываются углы для резцов, которые точат и растачивают детали, а в знаменателе – для инструментов, строгающих заготовки.
- Сталь (твердость меньше восьмисот Мегапаскалей) – 8/6, 12/8, 15/12.
- Сталь (твердость больше восьмисот Мегапаскалей) – 8/6, 12/8, 10/10.
- Сталь (твердость больше тысячи Мегапаскалей) – 8/6, 12/10, 10/8.
- Серый чугун (твердость по Бриннелю меньше двухсот двадцати) – 6/6, 10/10, 12/8.
- Серый чугун (твердость по Бриннелю больше двухсот двадцати) – 6/6, 10/10, 8/5.
- Ковкий чугун – 8/8, 10/10, 8/8.
Основной угол в плане должен составлять 30 – 45 градусов. Ширина фаски зависит от сечения резцовых стержней.
Какие абразивные круги используются для затачивания токарных инструментовЗатачивание проходного инструмента по державке и под углом 5 градусов выполняется кругом из электрокорунда, имеющим зернистость сорок — пятьдесят, твердость СМ1/2. Окружная скорость круга составляет 25 м/с.
Подготовительное затачивание осуществляется изделиями из черного кремниевого карбида, имеющими зернистость двадцать пять — сорок, твердость М3-СМ1. Финальное затачивание отрезного инструмента выполняется кругами из зеленого кремниевого карбида, имеющими зернистость шестнадцать — двадцать пять, твердость М3-СМ1.
Параметры точильных кругов для стальных и твердосплавных резцов прописаны в таблице режимов затачивания. Там же можно посмотреть окружные скорости кручения.
В настоящее время финальное затачивание рекомендуется проводить посредством алмазного круга. В особенности это актуально для пластин из твердых сплавов. Окружная скорость круга при подготовительном/финальном затачивании не должна превышать двенадцать — пятнадцать метров в секунду.
Проведение доводки
После затачивания инструментов их доводят борным карбидом на диске из чугуна, вращающемся со скоростью 1-2 м/с. Диск должен вращаться по направлению от опоры инструмента к рабочей кромке.
При выполнении доводки лезвия и поверхности инструмента последовательно притираются. Кроме того, удаляются неровности, резцы доводятся до блеска.
Для чего проводить доводку? Дело в том, что при токарном обрабатывании инструмент изнашивается и затупляется по причине трения пластины о стружку и заготовку. Чем ровнее пластина, тем слабее трение, медленнее изнашивание инструмента.
Доводка осуществляется абразивными пастами, состоящими из борного карбида. Намочите диск для доводки керосином. Нанесите на него пасту (зигзагообразно), поднесите инструмент к диску. При использовании керосина можете применять пасту ГОИ. В случае если вы применяете современную пасту, смачивать диск керосином необязательно.
Стол подручника должен стоять так, чтобы резцовые лезвия находились чуть ниже либо на одной линии с серединой диска. Диск должен вращаться направлено к резцовой пластине.
При прижатии инструмента и выполнении доводки частички пасты измельчаются. Когда они проходят через кромки, на резце не появляется сколов, потертостей. Зерна пасты обеспечивают устранение неровностей с резцовой поверхности.
Для того чтобы более подробно изучить процедуру доводки, можете посмотреть обучающее видео. Помните, что качественно сделанная доводка обеспечит продолжительную эксплуатацию резца без повторного затачивания.
oxmetall.ru
углы, станки, видео, своими руками
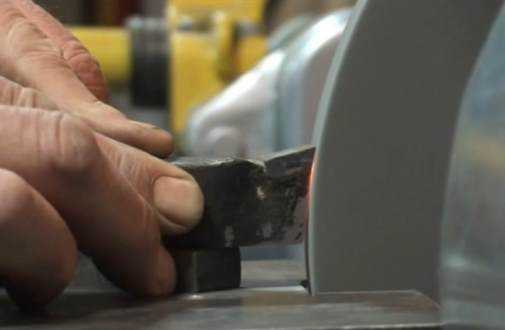
Заточка токарного резца по металлу
Назначение резца, конструкция, виды
Для получения деталей из слитка металла при точении на токарном оборудовании используют специальный инструмент. Изготавливают из стали, причем твердость материала выше, чем этот показатель у обрабатываемой заготовки. Стержень-державка и рабочая головка, главные элементы конструкции резца из металла, за счет первого инструмент закрепляется на токарном станке.
Функция второй составляющей, заключается в срезании слоя поверхности металла при обработке. Стержень-державка или тело резца в сечении квадратной формы или прямоугольной. Основная режущая кромка рабочей головки в сечении фасонная (клин) иди прямая. Режущей части из металла при эксплуатации требуется регулярная заточка. В современных условиях существует достаточный выбор резцов.
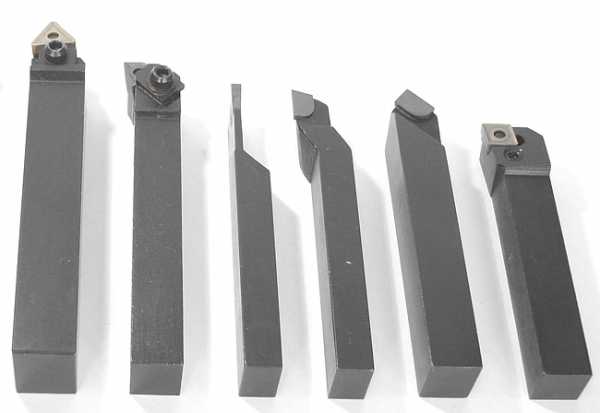
Токарные резцы для обработки металла со сменными пластинами
Подбирая снасть, следует учесть такой показатель, как углы. Классификация видов выглядит следующим образом:
- проходные;
- отрезные;
- подрезные;
- расточной;
- фасонные;
- канавочные:
- фасочные;
- упорный;
Проходные, этим типом устройства обрабатывают цилиндрические болванки. Инструмент отрезного вида используют для обрезки прутков. Обрезка выполняется под заданным углом. Приспособление отрезного типа служит и для прорезания в них канавок различного назначения. Подрезные, данный тип приспособлений используют для торцевания болванок и уменьшения уступов. Расточной, это средство используют для обработки отверстий нужного диаметра в заготовках или деталях токарном станке.
Канавочный — назначение такого устройства состоит в формировании внутренних и наружных канавок на цилиндрической поверхности, выдерживая нужные углы. Иногда требуется функция отрезного типа, когда необходимо убрать часть металла заготовки. Резьбонарезные, этим устройством на токарных станках нарезают резьбу. Фасонный — предназначение этого резца состоит формировании выступов и канавок на обрабатываемой болванке, при это получаются углы с требуемыми параметрами.
Фасочные — этим устройством после заточки выполняют внутренние и наружные фаски на изделии. Упорный используют для точения деталей из металла с уступами небольших размеров. Для снижения вибрации при работе на токарном станке требуется выверять его положение. Упорный применяют для нежестких деталей.
Виды резцов подразделяют еще по направлению обработки токарном оборудовании на левые и правые, по материалу, из которого они изготовлены, по способу присоединения режущей части к державке и другим параметрам.
Порядок и правила заточки инструмента
Для предупреждения появления сколов и задиров на обрабатываемых деталях, поломки и других нежелательных факторов при работе на токарном агрегате, требуется правильная заточка резца. Эта процедура выполняется при изготовлении нового или износе старого устройства. Сам процесс заточки резцов заключается в придании требуемой формы и необходимого угла затупившемуся или новому приспособлению.
Восстановить режущую часть, можно применяя специальное оборудование по металлу при достаточном уровне мастерства и знаний работника. Ведь от правильной заточки токарных резцов зависит трудоемкость и производительность. На крупных предприятиях созданы подразделения занятые подготовкой оснастки. На малых заточка выполняется токарем.
На данный момент существуют следующие способы заточки токарных резцов:
- абразивный;
- химико-механический;
- с использованием специальных приспособлений;
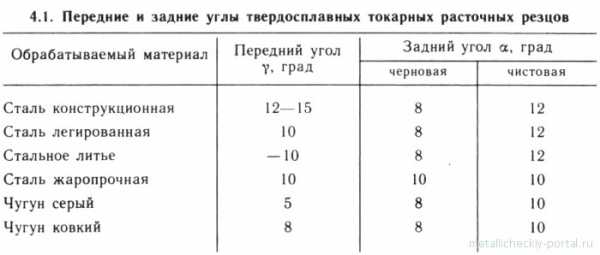
Углы заточки в зависимости от вида точения стали и чугуна
Абразивная заточка резца выполняется на специальном заточном агрегате или стандартном наждаке. При использовании последнего варианта трудно выдержать нужные углы при обработке приспособления. Агрегаты для заточки имеют два круга. Абразив из белого электрокорунда используют для точения резца из быстрорежущей стали. Заточка устройств из твердых сплавов выполняется кругом из карбида кремния зеленого цвета.
Алмазным диском делают финишную шлифовку на токарном или другом агрегате. Химико-механический способ подразумевает точение в специальном составе. Точность заточки проверяют шаблонами.
Если вы нашли ошибку, пожалуйста, выделите фрагмент текста и нажмите Ctrl+Enter.
stankiexpert.ru
Заточка токарных резцов по металлу - инструмент, угля и порядок заточки резцов
Заточка резца необходима для придания требуемой формы и угла рабочей поверхности. Производится она при превышении допустимых параметров износа резца, или перед началом работы новым инструментом. Данная операция позволяет значительно продлить срок эксплуатации оснастки, но требует строго соблюдения технологии работ.
Когда необходима заточка резца
В процессе точения происходит трение стружки о переднюю поверхность инструмента и обрабатываемой детали о заднюю в зоне реза. При одновременном значительном повышении температуры происходит постепенный износ детали.
При превышении максимально допустимой величины износа резец не может быть использован для дальнейшего проведения работ и требует заточки и доводки по передней и задней поверхности.
Допустимая величина износа указана в таблице ниже
Инструмент для заточки
Для абразивной заточки резца может быть использован заточной или токарный станок. Для твердосплавного инструмента используется зеленый карборунд средней твердости. Для первичной обработки абразив круга должен составлять 36-46, при завершении процесса – 60-80. Для высокого качества заточки необходим целый круг, без дефектов и нарушения геометрии.
Для заточки токарных резцов широко применяются и алмазные круги, что обеспечивает высокую чистоту режущих поверхностей. В сравнении с карборундовыми кругами чистота поверхности резца повышается на два класса, увеличивается производительность работ. Применение алмазных кругов увеличивает и ресурс работы инструмента – возможное количество переточек резца увеличивается на 20-30%. Но следует учесть, что экономически целесообразно применение заточки алмазным инструментом при припуске не более 0,2 мм. При большем значении рекомендует предварительная заточка карборундовым кругом.
Порядок и особенности
В зависимости от характера износа и конструкции оснастки производится заточка по передней, задней или обеим поверхностям. На рисунке ниже указаны все поверхности токарного резца
Для стандартных резцов, как правило, применяется заточка по всем режущим поверхностям. При незначительном износе восстанавливается геометрия только задней поверхности. Оснастка для многорезцовых станков восстанавливается только по задней поверхности, фасонная – только по передней.
Стандартный порядок заточки:
- Основная задняя поверхность.
- Вспомогательная задняя поверхность.
- Передняя поверхность.
- Радиус закругления конца.
Параметры заточки задней поверхности указаны на рисунке ниже
На рисунке (а) указана задняя поверхность с одной плоскостью заточки, на рисунке (б) – с несколькими. При напайке твердосплавных пластин задняя поверхность имеет три плоскости:
- по фаске высотой не меньше чем 1,5 мм под углом а;
- по оставшейся высоте под углом а+3°;
- по державке под углом а+5°.
Заточка передней поверхности твердосплавных резцов имеет гораздо большее количество разновидностей (см. рис. ниже).
Основные формы:
- Плоская с положительным передним углом (а).
- Плоская с отрицательным углом (б).
- Криволинейная с отрицательным углом (в).
- Плоская с отрицательным углом для черновой обработки (г).
- Криволинейные с отрицательным углом для нержавеющих сталей (д), и других материалов (е)
В процессе заточки необходимо чтобы режущая кромка обрабатываемого инструмента располагалась на линии центра заточного станка или ниже не более чем на 3-5 мм. Направление вращения круга должно обеспечить прижим пластинки к державке, т. е. идти на пластинку. В процессе работы желательна непрерывная подача охлаждающей жидкости. При периодическом охлаждении возможно перенапряжение структуры материала и появление микротрещин.
При заточке необходим легкий нажим и постоянное перемещение вдоль поверхности круга для формирования ровной поверхности. После завершения заточки геометрия инструмента проверяется с помощью шаблонов или специальных приборов.
Доводка инструмента
После заточки необходима последовательная притирка рабочих поверхностей в том же порядка, как производилась заточка. При доводке необходимо удалить все шероховатости и отполировать поверхность до зеркального блеска. Чем чище поверхность, тем ниже трение при точении и выше стойкость инструмента.
Доводка осуществляется с помощью абразивных паст карбида бора на вращающемся чугунном диске (не более 2 м/с). Может использоваться паста ГОИ или другие специальные материалы для полировки. Для полировки паста наносится на диск. Далее, при вращении диска, резец прижимается и зерна абразивной пасты сглаживают имеющиеся шероховатости. Таким образом, полностью восстанавливается геометрия и первоначальная чистота рабочей поверхности резца, обеспечивается его пригодность к дальнейшей эксплуатации.
mekkain.ru
Угол заточки
Заточка резца и угол заточкиНе будем брать примеры из учебников, так как на самом деле в практике все по другому. Расскажу, как применить тот или иной режущий инструмент и предложу варианты заточки резцов.
Существует обработка внутренних и наружных поверхностей и для обработки необходимы определенные виды резцов например: внутренние расточные, подрезные, прорезные, отрезные, фасонные, резьбовые и много какие еще виды. Умение затачивать и применять на практике режущий инструмент приходит с опытом.
На рисунке 1 показан передний угол, его заточка должна быть от 2 до 15 градусов при этом не желательно уменьшать тело, иначе пластина будет висеть как бы в воздухе (возможен скол режущей кромки при точении детали).
На рисунке 2 показаны варианты канавок.
Рисунок 2а – канавка служит для чистовой отделки. Рисунок 2б – такая канавка как (совковая лопата) применяется на отрезных резцах и резцах черновой обработки, с большой глубиной резания. Рисунок 2в – такой вид канавки применяется при скоростном точении заготовок. Рисунок 2г – применяется такая канавка для разного вида точения, другими словами это классический вид заточки. На рисунке 3 показан угол наклона режущей кромки. Рисунок 3а прямая режущая кромка и стружка при такой заточке будет сходить ровно по канавке. Рисунок 3 б,в режущая кромка делается с наклоном, стружка при точении будет сходить вправо или лево относительно пластины резца.Рисунок 4 это вид сверху. Такая заточка режущей кромки применяется на отрезных резцах. Этот вид заточки применяется в зависимости от обрабатываемых материалов.
Острые кромки необходимо притуплять или делать не большой радиус до 0.3, но режущая кромка должна быть острой. Притупление режущей кромки применяется при обдирке.
Резцы бывают быстрорежущие - применяются для точения мягких сталей или материалов например: алюминий, второпласт, текстолит и некоторые другие. Быстрорежущий отрезной резец можно применять при отрезании заготовок из стали и в некоторых случаях нержавейку. Марки быстрорежущих резцов бывают: Р18, Р6М5К5, Р9К5 и другие.
Резцы твердосплавные – применяются для точения более твердых и прочных материалов например: нержавейка, бериллиевая бронзы, каленые стали и другие. Марки твердосплавных резцов бывают: ВК8, ВК6, ВК6М, ВК6ОМ, ВК10ХОМ и другие. Более хрупкие твердосплавные резцы применяются для точения сырых сталей Ст20, Ст40, Ст45 и другие. Марки резцов: Т5К10, Т15К6, Т10К5 и другие.
Попробуйте заточить резец по образцу и попробуйте его в работе. По стружке можно определить, правильно ли заточен резец или нет. При правильной заточке стружка будет сходить сливная (завитая, плотная, а не хаотичная).
Заточка резцов производится на заточных станках. Заточные станки оборудованы кругами из электрокорунда (белый цвет круга), применяется при заточке быстрорежущих резцов. Круг зеленого цвета (карбида кремния), применяется при заточке твердосплавных резцов. Алмазные круги служат для доводки режущего инструмента.
В теории много не понятного и сложного для восприятия. Конечно же теория не заменит практику, но и без теории ни куда. Ознакомившись с первоначальными навыками теории можно приступать к практическим упражнениям. Для молодых специалистов порекомендую больше пробовать различных заточек резцов, таким образом вы быстро вникните в процесс работы и поймете правильность заточки режущего инструмента.
www.tokar-work.ru
Углы заточки резцов — Инструментальные материалы
Выбор формы передней поверхности можно производить в соответствии с табл. 24. Рекомендуемые величины заднего и переднего углов резцов даны в табл. 25.
Припуск на обработку (глубина резания, | Минимально необходимая длина режущей твердосплавной пластинки, мм, при главном угле в плане, град | |||
45 | 60 | 75 | 90 | |
2 | 4 | 3 | 3 | 3 |
4 | 8 | 6 | 6 | 6 |
6 | 12 | 10 | 9 | 8 |
8 | 15 | 13 | 12 | 11 |
10 | 19 | 16 | 14 | 14 |
12 | 23 | 19 | 17 | 16 |
14 | 27 | 22 | 20 | 19 |
16 | 31 | 25 | 23 | 22 |
18 | 35 | 28 | 25 | 25 |
20 | 38 | 31 | 28 | 27 |
Таблица 24
Примечание. Дополнительные обозначения к рисункам: f – ширина фаски; ?f — передний угол на фаске; R – радиус стружкозавивающей канавки; В – ширина стружкозавивающей канавки.
Таблица 25
Обрабатываемый материал | 3адний угол ?, град | Передний угол ?, град | |
При черновой обработке | При чистовой обработке | ||
Сталь и стальное литье ?В < 800 МПа | 8/6 | 12/8 | 15/12 |
Сталь и стальное литье ?В > 800МПа | 8/6 | 12/8 | 10/10 |
Сталь и стальное литье ?В > 1000 МПа, а также при обработке по корке, загрязненной неметаллическими включениями и при работе с ударами | 8/6 | 12/10 | 10/8 |
Чугун серый HB <220 | 6/6 | 10/10 | 12/8 |
Чугун серый HB > 220 | 6/6 | 10/10 | 8/5 |
Чугун ковкий | 8/8 | 10/10 | 8/8 |
Примечание. В числителе даны значения углов при точении и растачивании, в знаменателе – при строгании.
Главный угол в плане следует выбирать в пределах 30-45°. В случае недостаточной жесткости системы станок – деталь – инструмент главный угол в плане следует устанавливать в пределах 60-90°.
Ширина фаски принимается в зависимости от сечения стержней резцов в следующих размерах: для черновых токарных и строгальных резцов – 0,4-1,2 мм; для черновых расточных резцов – 0,2-0,7 мм; для чистовых токарных, строгальных и расточных резцов – 0,2-0,3 мм.
Положительный угол наклона главной режущей кромки в пределах 12-15° рекомендуется для строгальных и токарных резцов при работе с ударами.
arxipedia.ru
Форма заточки режущей части токарных резцов
Форма заточки режущей части токарных резцов
Форма заточки передней поверхности | Эскиз | Обрабатываемый материал |
Быстрорежущие резцы | ||
Плоская с положительным передним углом | Серый чугун, бронза, сталь с σ>800МПа и другие хрупкие материалы. | |
Сталь с σ≤800МПа, чугун с НВ≤200. | ||
Криволинейная с фаской | Вязкие цветные металлы, легкие сплавы, сталь σ<800МПа при необходимости завивания стружки. | |
Криволинейная | Материалы с σ=900...1000МПа. | |
Резцы с пластинками из твердого сплава | ||
Плоская с положительным передним углом | Серый чугун, бронза и другие хрупкие материалы . | |
Плоская с положительным передним угломи отрицательной фаской | Ковкий чугун, сталь и стальное литье с σ≤800МПа, а так же стали с σ>800МПа при недостаточной жесткой технологической системе. Для отвода и дробления стружки применяется стружколом. | |
Плоская с отрицательным передним углом | Сталь и стальное литье с σ>800МПа , загрязненное неметаллическими включениями. Работа с ударами в условиях жесткой технологической системы - черновая обработка. | |
Плоская с мелкоразмерной канавкойγ=-5°γ=0 | Сталь и стальное литье с σ=600...800МПа. | |
Сталь и стальное литье с σ<600МПа. | ||
Криволинейная с отрицательной фаской | Коррозионно-стойкие стали с σ≤850МПа, другие материалы с σ=700...900МПа. |
Геометрические параметры режущей части токарных резцов для обработки пластмасс
Вид пластмассы | Марка материала инструмента | Углы лезвия резца | |||
Передний γ | Задний α | в плане | |||
Главный φ | Вспомогательный φ1' | ||||
Оргстекло | ВК8 | 10...20 | 15...20 | 45 | 15 |
Фторопласт | 0...10 | 20 | 45 | 15 | |
Стеклотекстолит | 5 | 25 | 45 | 15 | |
Гетинакс | ВК6-М | 8...12 | 20 | 45 | 12 |
Волокнит | ВК-3 | 5 | 25 | 45 | 15 |
www.tokar-work.ru
На заводах резцы затачиваются обычно на точилах или на заточных станках специально обученными заточниками. Но токарь и сам должен уметь затачивать резцы.
При затачивании резца устанавливаются на подручниках 1 (рис. 26, а). Шлифовальный круг 2 должен быть огражден предохранительным кожухом 3. Порядок заточки следующий: сначала затачивают главную заднюю поверхность (рис. 26, а), затем главную вспомогательную (рис. 26, б) и, наконец, переднюю пверхность резца (рис. 26, в). После заточки этимх поверхностей закругляют вершину резца (рис. 26, г). Во время заточки резцов на заточных станках необходимо соблюдать следующие правила:
Проверка правильности углов затачиваемого резца. Наиболее простой способ контроля заточки углов - это проверка шаблоном. Вырезами шаблона проверяют угол заострения (рис. 27, а), а его боковыми гранями, скошенными под углом 6-12°, - задний угол резца (рис. 27, б). Для контроля резец и шаблон устанавливают на плиту и прижимают заднюю поверхность резца к боковой грани шаблона отсутствие просвета между ними говорит о правельности заточки задней поверхности и, следовательно, заднего угла. Недостаток этого способа контоля заглючается в том, что для каждого типа резцов необходимо иметь отдельный шаблон. От этого недостатка свободны резцовые угломеры.
Показанный на рис. 27, в резцовой угломер служит для измерения переднего заднего углов резца. Он состоит из чугунной плиты 8 с вертикальной стойкой 1, по которой перемещается вверх и вниз ползунок 2. На ползунке закреплена пластина 3 с делениями до 90°. Относительно укрепленной в пластине 3 оси 5 можно поворачивать рычаг 4, нижняя часть которого представляет собой угломер с двумя гранями, расположенными под углом 90°. Верхний конец рычага с нанесенной не нем риской скользит вдоль делений пластины 3. При контроле резец устанавливают основной плоскостью на плите и режущей кромкой перпендикулярно к плоскости рычага 4. Чтобы измерить передний угоол, нужно приложить грань 6 к передней поверхности резца, а для измерения заднего угла проложить грань 7 к задней поверхности резца. Правельность прилегания проверяют на просвет. Показания риски рычага 4, отсчитанные по шкале пластины 3, дают величину этих углов. Качество заточки режущей кромки обычно контролируют лупой с 10-20 кратным увеличением. Ружещая кромка после заточки и доводки должна быть острой и не иметь скругления, трещин и рисок. Резцы с такими дефектами нужно переточить снова. |
machinetools.aggress.ru