Технология сварки алюминия и его сплавов. Амг5 свариваемость
Технология сварки алюминия и его сплавов
Температура плавления алюминия 660°С, окисной пленки 2060°С
Марка | Свариваемость | Технологические особенности сварки | |
Технически чистый алюминий | Очистка кромок и присадка от окисной пленки | ||
АД00, АД0, АД1 , АД | Хорошая | Присадок Св-А1, СвА000, Св-85Т | |
Деформируемые, термически не упрочняемые сплавы | |||
АМц, АМцС, Д12 | Хорошая | Присадок Св-AMц | |
АМг1, АМг2, АМг3 | Присадок Св-AMг3 | ||
АМг4, АМг5 | Присадок Св-AMг5 | ||
АМг6 | Прксадок Св-АМг6, Св-АМг7 | ||
АД31, АДЗЗ, АД35 АВ, АК6, АК8 | Удовлетворительная | Присадок Св-АК5, Св-1557 | |
АК4, АК4-1 | Ограниченная | ||
В95 | Плохая | Предварительный подогревТермообработка после сварки при t°= 200-250°С Присадок Св-1557, Св-АМг5,. Св-АМг6 | |
1915,1925 | Удовлетворительная | ||
Литейные сплавы | |||
АЛ1, АЛ2, АЛ9, АЛ25, АЛ26 | Хорошая | Присадок той же марки, что и основной металл | |
АЛЗ, АЛ4, АЛ5, АЛ7, АЛ8, АЛ10В | Удовлетворительная |
Марки присадочной проволоки, используемой для сварки алюминия и его сплавов
Св-А1 | Св-1557 | Св-А97 | Св-А5с | Св-АМц |
Св-АМг3 | Св-АМг5 | Св-АМг6 | Св-АМг7 | Св-АК3 |
Св-АК5 | Св-АКЮ | Св-А85Т | Св-А000 | Св-1201П4 |
Толщина металла, мм | до 1,5 | 1,6-3 | 3,1-5 | 5,1-10 | 10-15 |
Рекомендуемый диаметр присадка, мм | 1-2,5 | 2,5-3 | 3-4 | 4-6 | 6-8 |
Ориентировочные расходы сварочных материалов
Толщина свариваемого металла, мм | Диаметр электрода, мм | Расход W-электродов на 100 пог. м шва, г | Расход аргона на 1 пог. м шва, л |
1 | 1,5 | 8,3 | 60-80 |
2 | 2 | 23 | 65-90 |
3 | 3 | 51 | 85-120 |
4 | 3,5-4 | 88 | 95-130 |
6 | 4 | 132 | 105-145 |
Трудности при сварке
- Температура плавления окисной пленки значительно выше, чем алюминия, и она расплавляется позже. Это затрудняет формирование шва
- Высокая теплопроводность алюминия требует увеличения сварочного тока в 1,2-1,5 раза по сравнению, например, со сваркой стали
- Образуются значительные остаточные деформации, что требует специальных мер и приспособлений
- Окисная пленка не растворяется в жидком алюминии. Это мешает формированию шва и служит причиной появления в нем металлических включений
- При нагреве алюминия и его сплавов нет явных признаков их перехода в жидкое состояние. Это требует высокой квалификации сварщика
Несплавление кромок алюминиевых конструкций
Подготовка к сварке. Резка и подготовка кромок ведутся механическим способом. На ширину 100-150 мм их обезжиривают ацетоном, авиационным бензином, уайт-спиритом или другим растворителем. Окисленную пленку удаляют механически или химическим травлением. При механической обработке свариваемые кромки на ширину 25-30 мм зачищают наждачной бумагой, шабером и металлической щеткой из нержавеющей проволоки. Зачистку проводят непосредственно перед сваркой.
Химическое травление проводят в течение 0,5-1 мин в реактиве, состоящем из 50 г едкого натра и 45 г фтористого натрия на 1 л воды. После травления следует промывка в проточной воде, а затем осветление в 30-35%-ном растворе азотной кислоты (для алюминия и сплавов типа АМц) или в 25%-ном растворе ортофосфорной кислоты (для сплавов типа АМг и В-95). После повторной промывки необходима сушка до полного испарения влаги.
Алюминиевую сварочную проволоку перед сваркой также обрабатывают. Сначала ее обезжиривают, а затем подвергают травлению в 15%-ном растворе едкого натра в течение 5-10 мин при температуре 60-70°С. После этого промывают в холодной воде и сушат 10-30 мин при температуре 300°С.
Подготовленные к сварке материалы сохраняют свои свойства в течение 3-4 дней. Затем на поверхности вновь образуется окисная пленка
ПОДКЛАДКИ ДЛЯ ЗАЩИТЫ ОТ ВЫТЕКАНИЯ МЕТАЛЛА ИЗ СВАРОЧНОЙ ВАННЫ
Выбор параметров режима
Метод сварки неплавящимся электродом применяют для изделий из алюминиевых сплавов толщиной до 12 мм. При сварке металла толщиной от 1 до 6 мм применяют вольфрамовые электроды диаметром от 1 до 5 мм. Сварочный ток (А) определяют по формуле:
Iсв=(60÷65)dэ,
где dэ - диаметр электрода, мм
Питание дуги осуществляется от источника переменного тока с осциллятором, что помогает разрушить окисную пленку. Напряжение холостого хода источника должно быть повышенным. Надежность газовой защиты дуги и сварочной ванны зависит от диаметра и формы сопла горелки, расстояния сопла от поверхности свариваемого изделия.
Рекомендуется выдерживать такие соотношения:
Диаметр электрода, мм | 2-3 | 4 | 5 | 6 |
Диаметр сопла, мм | 10-12 | 12-16 | 14-18 | 16-22 |
Длина выступающего из сопла W-электрода (выпуск) должна составлять при сварке стыковых соединений 1-1,5 мм, а тавровых и угловых 4-8 мм. Длину дуги поддерживают в пределах 1,5-3 мм. Скорость сварки выбирают от 8 до 12 м/ч.
Соединения с отбортовкой кромок целесообразно применять при сварке металла толщиной 0,8-2 мм.
Техника сварки
Ручной аргонодуговой сваркой W-электродом выполняют стыковые, угловые и тавровые соединения. Конструкции толщиной до 10 мм сваривают «углом вперед», а более 10 мм - «углом назад». Угол между присадочной проволокой и горелкой должен составлять 90°. Проволоку подают короткими возвратно-поступательными движениями. Поперечные колебания W-электрода недопустимы.
Изделия толщиной до 4 мм включительно сваривают за один проход на стальной подкладке. При толщине от 4 до 6 мм сварку выполняют с двух сторон, а при толщине 6-12 мм подготавливают кромки с V-образной или Х-образной разделкой.
Подачу аргона начинают за 3-5 с до возбуждения дуги, а прекращают через 5-7 с после окончания сварки.
Чтобы снизить вероятность окисления металла шва, размеры сварочной ванны нужно выдерживать минимальными.
ОРИЕНТИРОВОЧНЫЕ РЕЖИМЫ РУЧНОЙ СВАРКИ АЛЮМИНИЕВЫХ СПЛАВОВ
Подготовка кромок и форма шва | Размеры, мм | Сварочный ток, А | Диаметр электрода, мм | Диаметр присадка, мм | Расход аргона, л/мин | Число проходов | ||
S | b | |||||||
2 3 4 | 0+1,0 0+1,5 0+2,0 | - | 70-80 100-140 160-190 | 2 3 4 | 2-2,5 3 3-4 | 5-6 7-8 7-8 | 2 | |
2 3 | 0+1,0 | 80-100 120-140 | 3 | 2,5-3,5 3 | 5-6 7-8 | 1 | ||
2 3 4 | 80-100 120-140 160-210 | 2 3 4 | 2,5-3,5 3 4 | 5-6 7-8 7-8 | 1 1 2 | |||
4 6 8 10 | 1+0,5 1+1,0 1+1,0 1+1,0 | 150-200 250-300 300-350 350-400 | 6 5 5-6 6-7 | 3-4 4 4-5 4-5 | 7-8 8-9 9-10 10-12 | 1 2 2 | ||
4 6 8 10 15 | 1+1,0 1,5+1,0 2,0+1,0 2,0+1,0 2,5+1,0 | 1+0,5 1+1,0 1+1,0 1+1,0 | 220-260 260-300 320-360 380-420 440-480 | 4 4-5 5-6 6-7 8 | 3-4 4 4 4-5 4-5 | 8-10 10-12 12-14 16-18 16-18 | 1 2 2 2 2 | |
10 15 25 | 0+1,0 0+1,5 0+1,5 | 1+0,5 | 350-400 380-420 480-550 | 6-7 7 8 | 4-5 | 10-12 16-18 18-20 | 4 6 6 | |
2 4 6 | 0+0,5 0+1,0 0+1,5 | - | 100-120 170-220 240-280 | 2-3 4 5 | 2 3-4 4 | 5-6 7-8 8-10 | 2 | |
4 10 15 | 0+1,0 0+1,5 0+2,0 | 0,5 0+0,5 1,5 | 170-220 350-400 380-420 | 4 6-7 7 | 4 4-5 4-5 | 8-10 10-12 16-18 | 2 | |
8 10 15 20 | 0+1,0 0+2,0 0+2,0 0+2,0 | 0,5 1,0 1,5 1,5 | 280-320 350-400 380-420 480-550 | 5-6 6-7 7 8 | 4 4-5 4-5 4-5 | 8-10 10-12 16-18 18-20 | 2 2 2 5 | |
2 4 6 | 0+0,5 0+1,0 0+1,5 | 0+1,0 | 100-120 150-200 220-260 | 2-3 4 5 | 2-3 3 4 | 5-6 8-10 8-10 | 2 | |
4 10 15 | 0+1,0 0+1,5 0+2,0 | 0,5 1+0,9 1,5 | 150-200 320-380 360-400 | 4 6-7 7 | 3-4 4-5 4-5 | 8-10 10-12 16-18 | 2 2 3 |
weldering.com
Сплав алюминия АМг5 - деформируемый давлением
Применительно к сплаву системы алюминий - магний (АМг5), подходят такие определения, как: средняя прочность и пластичность, средняя теплопроводность и электропроводность, хорошая свариваемость, но относительно невысокая коррозионная стойкость.
Сравнение АМг5 с другими сплавами системы Al-Mg
Прочность и твёрдость у этого материала выше, чем у АМг2 или АМг3, которые, однако, обладают большей пластичностью, по сравнению с ним. С увеличением содержания магния в сплаве, увеличивается и его прочность, благодаря чему сплавы АМг5 и АМг6 могут успешно применяться для изготовления элементов конструкций средней нагруженности. Также, с повышением твёрдости этого материала, улучшается обрабатываемость заготовок из его механическим способом на станках.
Одновременно с увеличением прочности в зависимости от увеличения состава магния, в сплавах системы Al- Mg происходит ухудшение антикоррозионных свойств. В частности АМг5 и АМг6 плохо противостоят межкристаллитной коррозии, под воздействием напряжения. Сварные швы на поверхности этих материалов также подвержены коррозии, поэтому для обеспечения их защиты, поверхность свариваемого металла, требуется обработать термически, прежде, чем проводить её сварку.
Химический состав сплава и физические свойства
Химический состав АМг5 описывается в ГОСТ 4784-97. Это деформируемый сплав на основе Al, хорошо обрабатывается в холодном или горячем состоянии под давлением, и удовлетворительно обрабатывается на станках.
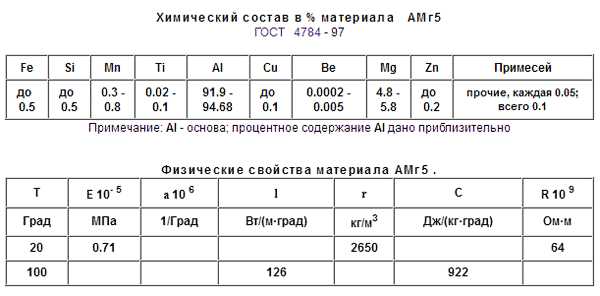
Механические и технологические свойства АМг5
Листы из АМг5, применяемые для изготовления нагруженных элементов конструкций, как правило, плакируются, а заклёпки, изготавливаемые из этого сплава, обязательно проходят процедуру анодирования, так как под нагрузкой на них проявляется межкристаллическая коррозия, если не прибегнуть к дополнительной защите.
То же касается сварных швов. Поверхность металла должна подвергнуться термопоготовке, прежде чем проводить процедуру сварки. При этом желательно пользоваться точечной сваркой.
Несмотря на относительно высокую прочность, среди сплавов системы Al-Mg — сплав АМг5 упрочняется только в холодном состоянии с помощью давления и не может соревноваться по прочности с термоупрочняемыми сплавами. Зато из него выпускают отожжённые заготовки, которые обладают хорошей пластичностью перед обработкой.
АМг5 или АМг2 - что выбрать?
Интересно было бы сравнить механические свойства у прутков из сплавов этой системы. К примеру, прутки из АМг5 выпускаются в обычном и отожжённом состоянии. Согласно информации, представленной на гистограммах ниже, можно заключить, что по пластичности в обычном состоянии АМг5 даже немного превосходит АМг2, а по прочности превосходит его в несколько раз. В отожжённом же состоянии АМг2 проявляет лучшие показатели относительно пластичности, однако эта разница не столь велика. Следовательно, с учётом механических свойств, АМг5 является лучшим выбором, за исключением ситуаций, когда очевидно важна стойкость к коррозии, лучшая свариваемость, лучшая теплопроводность или электропроводность.

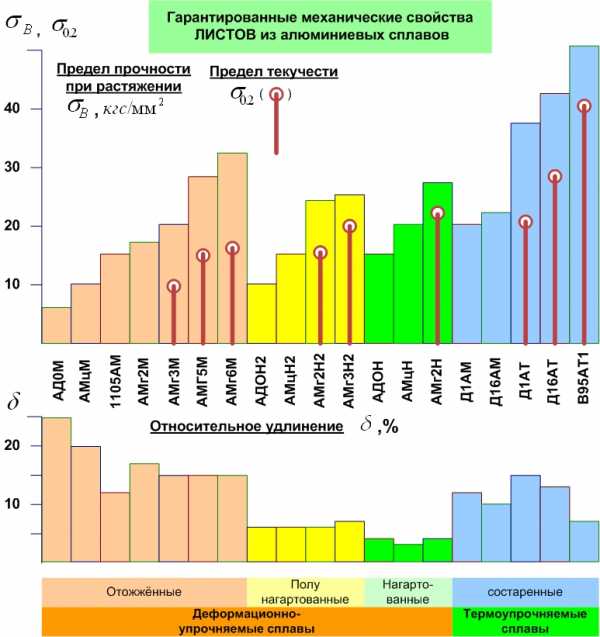
Область применения АМг5
Из АМг5 выпускают:
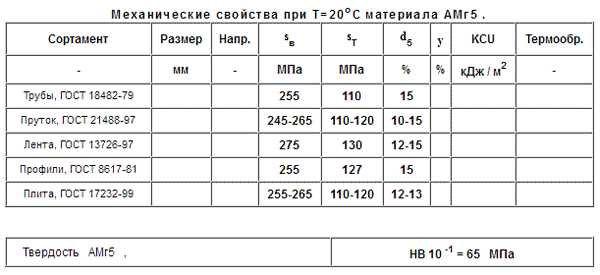
Профили из этого материала обладают средней прочностью и могут применяться в средненагруженных конструкциях. Листы ленты и плиты — хорошо обрабатываются давлением в холодном или горячем состоянии. Пластичные отожжённые листы могут использоваться для изготовления деталей сложной формы. Плакированные плиты, листы и ленты могут применяться при возведении средненагруженных конструкций, рассчитанных для работы в умеренной или влажной среде. Нагартованные заготовки, естественно обладают большей прочностью чем материал в обычном состоянии, но при расчёте прочности обычно ориентируются на состояние самого материала.
Аутсорсинг ВЭД
Другие статьи >>
nfmetall.ru
Амг6 сварка
Сварка алюминиевых сплавов
Даже при нынешних возможностях техники сварка алюминиевых сплавов является нелегким делом. Таким образом, возникло множество различных дополнительных технологий, которые помогают достичь максимально качественного результата при различных условиях. Данный процесс во многом напоминает сварку нержавейки, так как во время него возникает множество различных сложностей. Но сплавы алюминия, в отличие от металла в чистом виде, обладают достаточно хорошей крепостью, при высокой легкости, из-за чего активно применяются во многих сферах промышленности, так что профессиональным сварщикам часто приходится сталкиваться с ними.
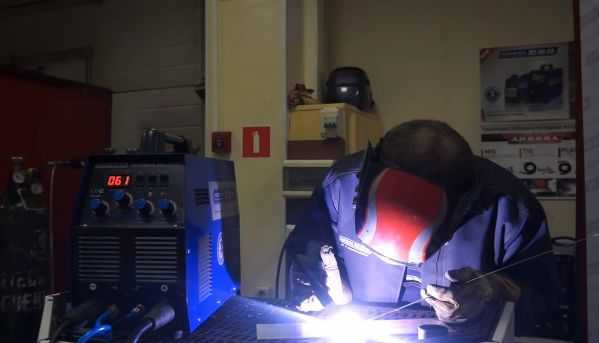
Сварка алюминиевых сплавов
Сварка разнородных алюминиевых сплавов осложняется тем, что они обладает высокой электро- и теплопроводностью. Во время расплавления заготовки даже не меняют цвет, что усложняет их сваривание. Сплавы зачастую имеют высокие механические свойства и для их сохранения требуется правильно проводить процесс соединения. Для этого нужно грамотно подбирать оборудование и расходный материал. В современной промышленности сплавы используются чаще, чем чистый металл. Они производятся согласно ГОСТ 4784-97.
Свариваемость сплавов
Высокая теплопроводность сплавов создает такие условия, в которых требуется увеличивать ток сварки в полтора раза выше стандартного, используемого при работе со сталью.
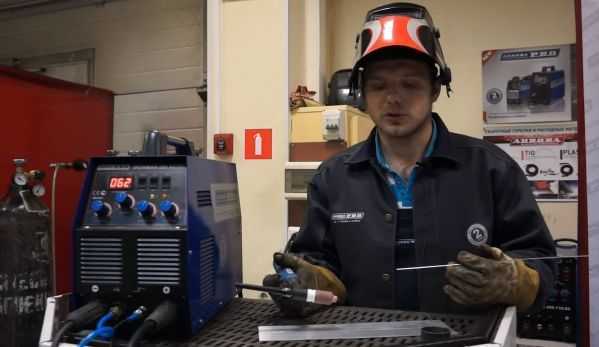
Настройка тока при сварке алюминиевых сплавов
Это вызывает сложности, когда идет сварка тонких листов металла, так как появляется риск прожига. Свариваемость еще зависит от состава сплава и соответствия присадочного материала основному металлу. Как и во время сварки алюминия, здесь возникают сложности с оксидной пленкой, которая может образовывать очень быстро на поверхности заготовки. Сплав плавится намного быстрее, чем сама пленка, так что расплавленный металл просто обволакивается, что понижает качество соединения. Это создает необходимость применения флюсов, или же проводится сварка аргоном.
Материал в расплавленном состоянии, как правило, обладает очень высокой текучестью, с которой очень сложно управляться. Сварочная ванна имеет низкую вязкость, которая по своей консистенции больше напоминает воду. Это требует не только опыта сварщика в таком процессе, но и использование теплоотводящих подкладок. При попадании водорода в шов, может образовываться напряжение, которое приводит к появлению трещин и прочих негативных явлений. Таким образом, есть множество проблем свариваемости, к которым требуется искать свой подход решения. Сплавы производятся согласно ГОСТ 4784-97.
Марки сплавов, которые применяются при сварке
Сварка алюминиевых сплавов предполагает работу со следующими их разновидностями:
- АМг;
- АМг3;
- АМг5п;
- АМг5н;
- АМг6м;
- АМг6т;
Все их можно условно разделить на те, которые упрочняются после термической обработки, и те, которые не упрочняются. Сварка деталей из алюминиевых сплавов можно усложнятся при наличии большого количества магния в сплаве, так как он понижает и без того плохую свариваемость.
Способы сварки алюминия и его сплавов
Сварка алюминиевых сплавов можно производиться при помощи стандартных плавящихся электродов с обмазкой. Для этого потребуется обыкновенный сварочный трансформатор, которые имеет необходимые для работы режимы, а также правильный подбор электродов, состав которых будет максимально приближен к составу основного металла. Надежность данного способа является низкой. Но простота и себестоимость дают ему весьма широкую распространенность, особенно в домашних условиях.
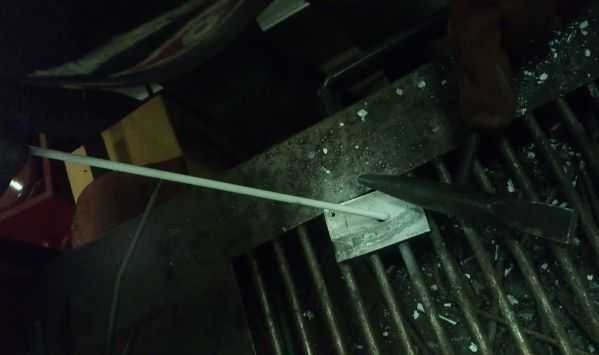
Сварка алюминиевых сплавов электродом
Сварка алюминиевых сплавов аргоном считается одним из лучших вариантов для профессионалов, так как дает соединение высокого качества. Аргон является инертной средой и создает защиту должного уровня, чтобы внешние негативные источники не влияли на состояние шва. Себестоимость такой сварки значительно выше остальных вариантов, но в профессиональной среде это очень оправдывает себя.
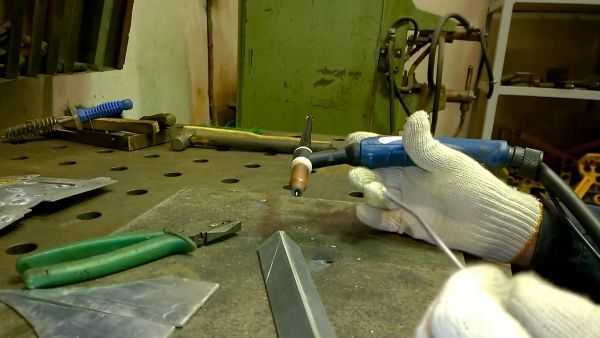
Сварка алюминиевых сплавов аргоном
Газовая сварка алюминиевых сплавов в среде защитных газов считается одной из самых простых, так как помогает бороться с высокой текучестью материала, благодаря относительно низкой скорость приведения процесса. Проволока без обмазки не вызывает риска попадания водорода из-за плохой просушки. Здесь обязательно применение флюса для улучшения свойств свариваемости.
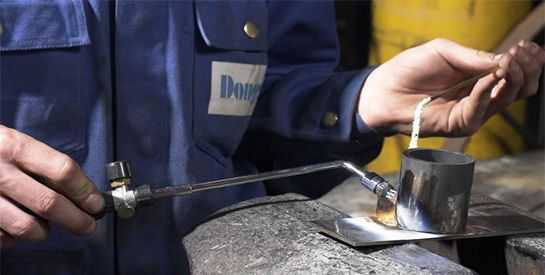
Сварка алюминиевых сплавов газовой горелкой
Подготовка сплавов к сварке
Технология сварки алюминиевых сплавов предполагает проведение подготовительных процедур перед самым процессом. В первую очередь это касается очистки поверхности от различного рода загрязнений, жировых налетов и окислительной пленки, которую легче заранее удалить, чем потом расплавить. Для начала поверхность заготовок зачищается щеткой по металлу, наждачной бумагой или другим приспособлением. Затем может потребоваться обработка растворителями, чтобы ликвидировать все налеты. На самом последнем этапе может потребоваться обработка флюсом, чтобы обеспечит высокое качество соединения.
В некоторых случаях, когда толщина деталей составляет более 4 мм, следует обработать кромки. Для этого их углы скашиваются под углом 30-45 градусов, чтобы обеспечить достаточную глубину приваривания. Тут потребуется большее количество присадочного материала, но качество соединения станет намного более высоким. Место сварки всегда является самым уязвимым, поэтому, непроваренные места сделают соединение более хрупким, а саму деталь очень ненадежной.
Пошаговая
Особенности сварки алюминия и его сплавов требуют особого подхода к некоторым процедурам, но сами этапы сваривания во многом схожи с остальными.
- Все начинается с подготовки металла. Здесь следует очистить заготовки от всего лишнего, что может на них остаться, а затем обезжирить и уничтожить другие налеты, разделать кромки и так далее.
- Затем идет работа с флюсом, так как он нужен для многих типов сварки, но в каждом из них может потребоваться своя разновидность.
- Затем следует подогреть место, где будет идти сваривание, чтобы не было температурных деформаций, а также не создавать условия для образования напряжения в металле.
- После этого можно приступать непосредственно к свариванию, образуя сварочную ванну и проводя шов до самого конца. Здесь есть разница в использовании методов сварки, так как сварка алюминиевых сплавов электродом не позволяет проводить длительные непрерывные швы.
- После окончания сварки не стоит прекращать подогревание металла, так как нужно дать ему остыть постепенно, чтобы избежать напряжений.
- Оббить шлак и зачистить все проблемные места.
«Важно!
Во время сварки следует учитывать высокую текучесть металла, поэтому, все проводится только в горизонтальном положении.»
Техника безопасности
Сварка алюминия с нержавейкой и прочими металлами может стать опасным процессом, если не соблюдать элементарные правила. Средства индивидуальной защиты, такие как сварочная маска и специальная одежда. Газовые баллоны следует держать от источника пламени и электродуги на расстоянии от 5 метров и более, а также всегда проверять шланги в них. Также нельзя проводить работы на открытой местности во время осадков.
svarkaipayka.ru
Технология аргонодуговой сварки алюминия и его сплавов
Аргонодуговым способом сваривают различные типы соединений алюминия и сплавов на его основе. В зависимости от толщины свариваемых элементов применяют аргонодуговую сварку неплавящимся вольфрамовым (с присадкой и без нее), а также плавящимся электродами.
Аргонодуговая сварка неплавящимся вольфрамовым электродом — лучший способ соединения тонколистового алюминия, не уступает по производительности сварке по флюсу и аргонодуговой сварке плавящимся электродом толстолистового алюминия.
Качество швов при аргонодуговой сварке алюминия и сплавов на его основе зависит от чистоты аргона, поэтому он должен не иметь следов влаги и содержать не более 0,03% кислорода и не более 0,3% азота. Хорошие (плотные) швы получаются также при сварке в защитной смеси из 65% гелия и 35% аргона.
При сварке вольфрамовым электродом стыковых соединений металла толщиной до 3 мм кромки не скашиваются. В соединениях металла толщиной до 6 мм делают односторонний скос кромок с общим углом раскрытия 60—90° и притуплением в стыке до 1,5 мм, а при толщине металла до 9 мм — такой же скос кромок, но с притуплением до 2,5 мм.
Металл толщиной до 20 мм сваривают с двусторонним скосом кромок и углом раскрытия 60—90°, с притуплением 3 мм или односторонней рюмкообразной подготовкой кромок с углом раскрытия 40—60°, радиусом закругления у основания разделки 5 мм и притуплением в стыке 3 мм.
Металл толщиной до 6 мм сваривают односторонним швом на подкладке. При толщине металла более 6 мм после выполнения шва с одной стороны вырубают корень этого шва и стык затем сваривают с обратной стороны. В том случае, когда за один проход не удается заполнить разделку, сварку выполняют в два прохода, причем первый проход делают без присадки с полным проплавлением стыка, а второй — с присадкой для заполнения разделки и получения необходимого усиления шва.
При сварке алюминия и его сплавов в инертных газах раскисляющий флюс не применяется. Вместе с тем аргон даже самого высокого качества содержит некоторое количество кислорода, достаточное для образования пленок окислов жидкого металла.
Если в процессе сварки пленки окислов не разрушаются, то металл шва засоряется ими и в отдельных местах сварного соединения может образоваться несплавление кромок, а также несплавление присадочного металла с основным. Разрушить же эти пленки можно лишь в том случае, если сварочная ванна (изделие) будет катодом.
Тогда с поверхности жидкой ванны и соседних с ней зон менее нагретого металла происходит вырывание металлических частиц (катодное распыление металла). Вследствие катодного распыления пленки окислов, образующиеся в сварочной ванне, разрушаются, что обеспечивает хорошее сплавление кромок и формирование шва без применения флюса.
Изделие может быть катодом как при сварке постоянным током обратной полярности, так и при сварке переменным током. В последнем случае катодное распыление и, следовательно, очищение сварочной ванны от окислов происходит в полупериоды обратной полярности тока.
Поскольку ток обратной полярности (плюс на электроде) нельзя использовать из-за перегрева электрода, а прямой из-за необходимости очищения сварочной ванны от пленок окислов, аргонодуговую сварку алюминия вольфрамовым электродом выполняют переменным током.
Аргонодуговая сварка алюминия плавящимся электродом выполняется постоянным током обратной полярности. Переменный ток при такой сварке не применяется. Для питания дуги переменным током используют стандартные сварочные трансформаторы с осцилляторами и стабилизаторами, а для питания постоянным током — преобразователи с падающей, жесткой или возрастающей внешней характеристикой.
Для сварки разноименных алюминиевых сплавов, обеспечивающих сварным соединениям повышенную стойкость против горячих трещин, рекомендуется применять следующие марки проволок:
Марки свариваемых сплавов | Марки сварочной проволоки |
АДО+АМц | СвА5 |
АДО+АМгЗ | СвАМг6 |
АДО+АМг5 | СвАМг6 |
АДО+АМг6 | СвАМг6 |
АДЦ+АМгЗ | СвАМг6 |
АДЦ+АМг5 | СвАМг6 |
АДЦ+АМг6 | СвАМг6 |
Марки свариваемых сплавов | Марки сварочной проволоки |
АМг3+АМг5 | СвАМг6 |
АМг3+АМг6 | СвАМг6 |
АМг5+1915 | СвАМг6, Св1557 |
АМг6+1915 | Св1557 |
АД31+АМцС | СвАК5 |
АД31+АМгЗ | СвАМг6 |
АД31+АМг6 | СвАМг6 |
АД51+АМг6 | СвАМг6 |
Состав газообразного аргона должен быть следующим:
Марка аргона | Содержание, % | |||
Аг | О2 | Н1 | Влага при давлении 760 мм рт.ст., г/м3 | |
А | Не менее 99,99 | Не более 0,003 | 0,01 | 0,03 |
Б | Не менее 99,96 | Не более 0,005 | 0,04 | 0,03 |
Состав газообразного гелия, применяемого для сварки (%):
Содержание | Гелий высокой чистоты |
Гелия (не менее) | 99,985 |
Водорода (не более) | 0,0025 |
Азота (не более) | 0,005 |
Кислорода (не более) | 0,002 |
Углеводородов (не более) | 0,003 |
Неона (не более) | 0,002 |
Точка росы (не выше) | -55°С |
При автоматической аргонодуговой сварке вольфрамовым электтродом горелка (мундштук) обычно располагается вертикально, а присадка подается механизмом автомата со стороны, противоположной направлению сварки.
Сварка плавящимся электродом может выполняться автоматом и шланговым полуавтоматом. При полуавтоматической сварке горелку наклоняют под углом 60—80° к плоскости изделия и перемещают углом вперед или углом назад с небольшими плавными поперечными колебаниями или без колебаний. При автоматической сварке горелку располагают вертикально.
www.prosvarky.ru
Марки и сплавы алюминия которые часто используются в сварке
- Сварка алюминия
- Сварка алюминия инвертором
- Вопросы и ответы
Алюминиевые сплавы часто применяются для создания конструкций разного назначения. Основными достоинствами данных металлов является малая плотность, высокая прочность и высокая устойчивость к коррозии. Чистый алюминий ввиду низкой прочности применяется в разных видах промышленности. Алюминий высокой чистоты широко используется в производстве полупроводников.
Сплавы из алюминия разделяются на литейные и деформируемые. В основном в сварочных конструкциях используются полуфабрикаты, например листы, трубы и профили из деформируемых сплавов. Концентрация легирующих элементов в деформируемых сплавах составляет меньше предела растворимости, а при нагреве данные сплавы могут переводиться в однофазовое состояние, которое обеспечивает высокую деформационную способность.
Большинство элементов, которые входят в состав алюминиевых сплавов, имеют ограниченную растворимость, которая изменяется с температурой. При температуре металла в 1000 градусов по Цельсию, реакция окисления начинает происходить. Окись, которая образовывается в результате окисления, покрывает поверхность деталей плотной и прочной пленки. При температуре 20 градусов окисление происходит по параболическому закону, а при повышенной температуре, процесс протекает немного иначе. Важнейшей характеристикой окисной пленки алюминия является ее способность к адсорбированию газов, например водяного пара. Водяной пар удерживается окисной пленкой до температуры плавления металла.
Коэффициент теплового расширения окисной пленки практически в 3 раза менее коэффициента расширения самого алюминия, поэтому при нагревании металла образовываются трещины. При наличии в алюминии добавок легирующих элементов и добавок, состав окисной пленки может измениться существенным образом. Сложная окисная пленка является рыхлой и гигроскопической, а также обладает худшими защитными свойствами.
К сплавам, которые наиболее часто используются для сварки, являются: АД, АД1, АМц, АМг, АМг3, АМг5В, АМг6, АВ, АД31, АДЗЗ, АД35, М40, Д20, ВАД1, В92Ц. Для проведения успешных сварочных работ применяют проволоку из алюминия и алюминиевых сплавов в соответствии с ГОСТ 7871—75.
АД1 применяются в промышленности для изготовления полуфабрикатов с помощью использования метода горячей или холодной деформации.
Сплав АД33 используется для изготовления деталей разной степени прочности, которые работают в интервале от -70 до 50 градусов во влажной атмосфере и в воде в море.
Для производства полуфабрикатов методом холодной или горячей деформации, а также слитков, слябов и биметаллических листов.
Д20 наиболее часто используется для производства сварных изделий, которые работают при комнатной температуре или кратковременно при повышенной температуре.
Сварка алюминия и сплавов является приоритетной для большинства сварщиков, поэтому необходимо знать, какие сплавы наиболее часто используются для работы.
3g-svarka.ru
Орбитальная сварка АМг6 - Аргонодуговая сварка — TIG
Отправлено 03 Декабрь 2012 13:57
Здравствуйте! Очень нужна консультация по орбитальной сварке АМг6+АМг2, диаметр свариваемых деталей - 10 мм, сварные швы 1 категории. Проблема-порообразование. Перед сваркой производим хим и мех подготовку свариваемых поверхностей, аргон- по ТУ высшей очистки с точкой росы -71. Материал на содержание водорода не проверялся. Что еще можно предпринять для избавления от пор? диаметр сопла 12,5 мм, расход аргона-никаким рекомендациям не соответствует-25 л, диаметр вольфрамового электрода - 2 мм. Начинаем варить на токе 88, снижаем в конце до 55. Выслушаю любые советы. Заранее спасибо. и еще...кто-нибудь подваривал трещины? Как это лучше делать?Отправлено 03 Декабрь 2012 15:11
Ирина Трансформатор, какое красивое имя. Ирина, если Вы добавите фото пор, разделки и т.д. то здесь найдутся люди которые смогут Вам помоч, я могу задать только несколько вопросов за них.Перед сваркой производим хим и мех подготовку свариваемых поверхносте
Добавте подробностей, что за химия, что за мехобработка, абразив, щётка или шабрение?расход аргона-никаким рекомендациям не соответствует-25 л
Много, есть ли у Вас защита (поддув) с обратной стороны? Бесполезное видео +18. - https://www.youtube....KV7hUiDg/videosОтправлено 03 Декабрь 2012 15:40
Ирина Трансформатор, ник - попадание 100%-ное!!! По Вашему вопросу - подождите, знающие пользователи ответят, думаю.Отправлено 03 Декабрь 2012 17:05
Ирина Трансформатор,по какому РД работаете?Отправлено 03 Декабрь 2012 17:34
Чет тишина . Фото брака выкладывайте. Причин может быть множество. Настораживает диаметр сопла Вашего 12,5 мм, существуют такие сопла, если этот диаметр у Вас на выходе, то есть элементарная вероятность плохой защиты сварочной ванны, так как возможность попадания воздуха окружающей среды весьма высока. Работал с такими соплами с распылительной сеткой внутри и малейший сквозняк наносит вред защите сварочной ванны. На нерж. металле еще ничего страшного, почернеет и все, за чистится, а вот на чернухе, да еще и хм.стали например пойдут поры на прогулку и сыр Вам обеспечен. Попробуйте сопла 8, 7, 6 мм на выходе, для чернухи лучше всего. Когда подберете, если получится, возвращайтесь с итогами.Отправлено 03 Декабрь 2012 17:46
Рассказываю: хим подготовка-обезжиривание-едкий натр-промывка-азотная кислота-промывка-сушка. Мех подготовка-если заготовки более 3-х часов на воздухе-пробовали шабрение и средства малой механизации-щеткой металлической зачищали. Сварка без поддува, прихватка деталей беззазорная, торцы обработаны на торцевателе. Работаем по ОСТам 92-1186, 92-1114, По поводу диаметра сопла-идет сопло со сварочной головкой немного на конус (вероятно, создавался турбулентный поток), вставили керамику цилиндрическую, надеясь на ламинарный поток (еще не проверяла на титане поток). Да, действительно, внутри распылительная сетка вкручивается. Пыталась найти, кстати, сопла с резьбой М14 внутри, пок безуспешно, может, кто подскажет, где взять. Сейчас внутри сопло диаметром 8, снизился расход аргона до 17 л.Отправлено 03 Декабрь 2012 17:47
Завтра выложу фото сварочной головки, швовОтправлено 03 Декабрь 2012 17:56
Чет тишина . Фото брака выкладывайте. Причин может быть множество. Настораживает диаметр сопла Вашего 12,5 мм, существуют такие сопла, если этот диаметр у Вас на выходе, то есть элементарная вероятность плохой защиты сварочной ванны, так как возможность попадания воздуха окружающей среды весьма высока. Работал с такими соплами с распылительной сеткой внутри и малейший сквозняк наносит вред защите сварочной ванны. На нерж. металле еще ничего страшного, почернеет и все, за чистится, а вот на чернухе, да еще и хм.стали например пойдут поры на прогулку и сыр Вам обеспечен. Попробуйте сопла 8, 7, 6 мм на выходе, для чернухи лучше всего. Когда подберете, если получится, возвращайтесь с итогами.
да, кстати, сквозняков нет, участок сварки огорожен, влажность на участке 45%, температура 23-все в норме. Движения воздуха нет-наблюдала за сигаретным дымом (просила спец-но зажечь)Отправлено 03 Декабрь 2012 17:59
И еще, на каждую прихватку не забывайте откусить горелый конец проволоки, не толкайте окисленный присадочный металл в прихватку. Даже это может нанести ущерб. А 8 ка должна помочь. Орбитальной сваркой емкости сваривали 8м соплом и все хорошо.Отправлено 03 Декабрь 2012 18:12
Как проверить корректность чистоты аргона, нет ли подсоса воздуха в шланговой системе и некачественного вольфрама? Лучший вариант взять нерж. пластину и прямо под 90 градусов, держа горелку(сопло) зажечь дугу на 100 А на 4мм. например пластине на секунду и выключить. Св. ванночка должна быть желтой, светлой и вокруг ни тени темного и вольфрам не должен измениться. А если все плохо, темное пятно на пластине, вольфрам потемнел сразу, значит либо газ плохой, либо подсос в шлангах, или вольфрам. Бывает и сам аппарат плох. Было как то фроню в упаковке привезли, с охлаждением, ну че только с ним не делали, ну чернит и все, так и вернули производителю и оказался брак. В чем там был брак, одному Богу известно, но работать им было не возможно, хотя вся функциональность в полном порядке. Было так, что и в фольфраме было дело именно на черном металле шли поры, при замене его на другой, все становилось в полный порядок.Отправлено 03 Декабрь 2012 18:18
А что скажете про подварку трещин?!Как проверить корректность чистоты аргона, нет ли подсоса воздуха в шланговой системе и некачественного вольфрама?Лучший вариант взять нерж. пластину и прямо под 90 градусов, держа горелку(сопло) зажечь дугу на 100 А на 4мм. например пластине на секунду и выключить. Св. ванночка должна быть желтой, светлой и вокруг ни тени темного и вольфрам не должен измениться. А если все плохо, темное пятно на пластине, вольфрам потемнел сразу, значит либо газ плохой, либо подсос в шлангах, или вольфрам. Бывает и сам аппарат плох. Было как то фроню в упаковке привезли, с охлаждением, ну че только с ним не делали, ну чернит и все, так и вернули производителю и оказался брак. В чем там был брак, одному Богу известно, но работать им было не возможно, хотя вся функциональность в полном порядке. Было так, что и в фольфраме было дело именно на черном металле шли поры, при замене его на другой, все становилось в полный порядок.
Да, я тоже считала, что дело в аппарате, завтра проверю по вашей рекомендации. Только проверить качество магистральных шлангов и потока советовали проверить напластине из титана и пятно должно быть золотистого цвета.Я не сильна в сварке, поэтому какие то тонкости надеюсь узнать на форуме.Попробую сменить электрод, потому что бывают мелкие вольфрамовые включения на первых образцах.А что скажете про подварку трещин? Трещины образуются уже при ручной сварке, трещит в околошовной зоне. АМг6 склонен к растрескиванию. Сварку производим проволокой диаметром 2 мм, АМг6. И еще вопросик-какая проволока по качеству лучше? ESAB (состав приближен к АМг6) или ГОСТ (в составе только Al, Mg, Ti (вроде) )?Отправлено 03 Декабрь 2012 18:35
На первый взгляд здесь еще должно соблюстись: 1. Проверить - работает ли осциллятор. 2. Присадочная проволока должна быть такого же сплава алюминия AMr6. (Если нет такой проволоки, то можно нарубить с основного металла прутки под сварку этого же сплава алюминия.) 3. Аргон должен быть чистый не по ТУ а по ГОСТу, и замените сопло на более меньший диаметр на выходе. 4. Есть вероятность непрогрева основного металла из-за большой теплопроводности алюминия. Попробуйте сделать предварительный подогрев основного металла перед сваркой.Витек
Отправлено 03 Декабрь 2012 18:40
и замените сопло на более меньший диаметр на выходе.
Я ноль в орбиталке . Но совет странный . на первый взгляд . А ведь в ручном тиге помогало .Отправлено 03 Декабрь 2012 18:41
На первый взгляд здесь еще должно соблюстись:1. Проверить - работает ли осциллятор.2. Присадочная проволока должна быть такого же сплава алюминия AMr6.3. Аргон должен быть чистый не по ТУ а по ГОСТу, и замените сопло на более меньший диаметр на выходе.4. Есть вероятность непрогрева основного металла из-за большой теплопроводности алюминия. Попробуйте сделать предварительный подогрев основного металла перед сваркой.
Да, проволока АМг6 ГОСТ 7871 и варили еще есабовской проволокой Autrod 18.22.Да, действительно аргон должен быть по ГОСТу, но заменила на ТУ из-за содержания аргона, в ГОСТе 10151-99,993, а в ТУшном- 99,998. Аргон, которым завтра будем варить с низким содержанием водяных паров-точка росы -72.Не думаю, что непрогрев-толщина свариваемых деталей 1 мм. Тогда вообще сгорит, я думаю. Есть ли целесообразность подогреть и уменьшить ток?Отправлено 03 Декабрь 2012 19:08
Как то варить пришлось крепление капота от мерседеса, под рукой были только старые алюминевые кабеля в оплетке, содрав ее, зачистил перед сваркой наждачной бумагой проволоку, предварительно приготовив 2 детали, обработав машинкой шлиф кругом и сразу к сварке. Все получилось. Хотя принесли мне все убитое, много раз варенное и с пузырями(порами) В зачистке думаю большой плюс, не стоит ждать после обработки, сразу надо приступать, пока оксид.пленка не затянула приготовленную поверхность.Отправлено 03 Декабрь 2012 19:12
Как то варить пришлось крепление капота от мерседеса, под рукой были только старые алюминевые кабеля в оплетке, содрав ее, зачистил перед сваркой наждачной бумагой проволоку, предварительно приготовив 2 детали, обработав машинкой шлиф кругом и сразу к сварке. Все получилось. Хотя принесли мне все убитое, много раз варенное и с пузырями(порами) В зачистке думаю большой плюс, не стоит ждать после обработки, сразу надо приступать, пока оксид.пленка не затянула приготовленную поверхность.
Под ручную сварку проволоку травим, зачищаем наждачкой, протираем. Под автоматическую орбитальную сварку - травление, не зачищаем, так как тефлоновый шланг небольшого диаметра. И потом, не забывайте, что сварные швы 1 категории-допускается одна пора диаметром 0,3 или скопление пор суммарной площадью не более 0,18 мм^2Отправлено 03 Декабрь 2012 19:15
В вашем случае да, проволоку не зачистишь. Так к примеру написал. Ну проверяйте, пробуйте советы, истина где то рядомОтправлено 03 Декабрь 2012 19:17
vnuk,По книгам два часа после зачистки . любой . А с проводами дело очень старое . е слиб не веб - сварка я так бы и думал что других не бывает кроме тех что со столбов . но в этом есть плюс . после годов проводами насколько иногда легче работать тем чем должно .честно сказать разницы особой не замечал . если не считать трещин . в основном на баках .Отправлено 03 Декабрь 2012 19:41
Ирина Трансформатор,Немного отвлечься от тонкостей. А что это за детали или заготовки? Отрасль, сфера назначения?Отправлено 03 Декабрь 2012 19:44
Завтра выложу фото сварочной головки, швов
Скажите,Вы в этом процессе кто?Исполнитель,технолог,начальник,сварщик?Есть ли на аппарате пульс режим?Сообщение отредактировал митька51: 03 Декабрь 2012 19:48
websvarka.ru
www.samsvar.ru
СВОЙСТВА АЛЮМИНИЕВЫХ СПЛАВОВ
АЛЮМИНИЕВЫЕ СПЛАВЫ
Содержание
- классификация сплавов
- физические свойства
- коррозионные свойства
- механические свойства
- круглый и профильный алюминиевый прокат
- плоский алюминиевый прокат
- интересные интернет-ссылки
Классификация алюминиевых сплавов.
Алюминиевые сплавы условно делятся на литейные (для производства отливок) и деформируемые (для производства проката и поковок). Далее будут рассматриваться только деформируемые сплавы и прокат на их основе. Под алюминиевым прокатом подразумевают прокат из алюминиевых сплавов и технического алюминия (А8 – А5, АД0, АД1). Химический состав деформируемых сплавов общего применения приведен в ГОСТ 4784-97 и ГОСТ 1131.
Деформируемые сплавы разделяют по способу упрочнения: упрочняемые давлением (деформацией) и термоупрочняемые.
Другая классификация основана на ключевых свойствах: сплавы низкой, средней или высокой прочности, повышенной пластичности, жаропрочные, ковочные и т.д.
В таблице систематизированы наиболее распространенные деформируемые сплавы с краткой характеристикой основных свойств присущих для каждой системы. Маркировка дана по ГОСТ 4784-97 и международной классификации ИСО 209-1.
Характеристика сплавов | Маркировка | Система легирования | Примечания | |
СПЛАВЫ УПРОЧНЯЕМЫЕ ДАВЛЕНИЕМ (ТЕРМОНЕУПРОЧНЯЕМЫЕ) | ||||
Сплавы низкой прочности и высокой пластичности,свариваемые, коррозионносойкие | АД0 | 1050А | Техн. алюминий без легирования | Также АД, А5, А6, А7 |
АД1 | 1230 | |||
АМц | 3003 | Al – Mn | Также ММ (3005) | |
Д12 | 3004 | |||
Сплавы средней прочности и высокой пластичности,свариваемые, коррозионносойкие | АМг2 | 5251 | Al – Mg (Магналии) | Также АМг0.5, АМг1, АМг1.5АМг2.5 АМг4 и т.д. |
АМг3 | 5754 | |||
АМг5 | 5056 | |||
АМг6 | - | |||
ТЕРМОУПРОЧНЯЕМЫЕ СПЛАВЫ | ||||
Сплавы средней прочности и высокой пластичности свариваемые | АД31 | 6063 | Al-Mg-Si (Авиали) | Также АВ (6151) |
АД33 | 6061 | |||
АД35 | 6082 | |||
Сплавы нормальной прочности | Д1 | 2017 | Al-Cu-Mg (Дюрали) | Также В65, Д19, ВАД1 |
Д16 | 2024 | |||
Д18 | 2117 | |||
Свариваемые сплавы нормальной прочности | 1915 | 7005 | Al-Zn-Mg | |
1925 | - | |||
Высокопрочные сплавы | В95 | - | Al-Zn-Mg-Cu | Также В93 |
Жаропрочные сплавы | АК4-1 | - | Al-Cu-Mg-Ni-Fe | Также АК4 |
1201 | 2219 | Al-Cu-Mn | Также Д20 | |
Ковочные сплавы | АК6 | - | Al-Cu-Mg-Si | |
АК8 | 2014 |
Состояния поставки Сплавы, упрочняемые давлением, упрочняются только холодной деформацией (холодная прокатка или волочение). Деформационное упрочнение приводит к увеличению прочности и твердости, но уменьшает пластичность. Восстановление пластичности достигается рекристаллизационным отжигом. Прокат из этой группы сплавов имеет следующие состояния поставки, указываемые в маркировке полуфабриката:
1) не имеет обозначения - после прессования или горячей прокатки без термообработки
2) М - отожженное
3) Н4 - четвертьнагартованное
4) Н2 - полунагартованное
5) Н3 - нагартованное на 3/4
6) Н - нагартованное
Полуфабрикаты из термоупрочняемых сплавов упрочняются путем специальной термообработки. Она заключается в закалке с определенной температуры и последующей выдержкой в течение некоторого времени при другой температуре (старение). Происходящее при этом изменение структуры сплава, увеличивает прочность, твердость без потери пластичности. Существует несколько вариантов термообработки. Наиболее распространены следующие состояния поставки термоупрочняемых сплавов, отражаемые в маркировке проката:
1) не имеет обозначения - после прессования или горячей прокатки без термообработки
2) М - отожженное
3) Т - закаленное и естественно состаренное (на максимальную прочность)
4) Т1 - закаленное и искусственно состаренное (на максимальную прочность)
Для некоторых сплавов производится термомеханическое упрочнение, когда нагартовка осуществляется после закалки. В этом случае в маркировке присутствует ТН или Т1Н. Другим режимам старения соответствуют состояния Т2, Т3, Т5. Обычно им соответствует меньшая прочность, но большая коррозионная стойкость или вязкость разрушения.
Приведенная маркировка состояний соответствует российским ГОСТам.
Физические свойства алюминиевых сплавов.
Плотность алюминиевых сплавов незначительно отличается от плотности чистого алюминия (2.7г/см3). Она изменяется от 2.65 г/см3 для сплава АМг6 до 2.85 г/см3 для сплава В95.
Легирование практически не влияет на величину модуля упругости и модуля сдвига. Например, модуль упругости упрочненного дуралюминия Д16Т практически равен модулю упругости чистого алюминия А5 (Е=7100 кгс/мм2). Однако, за счет того, что предел текучести сплавов в несколько раз превышает предел текучести чистого алюминия, алюминиевые сплавы уже могут использоваться в качестве конструкционного материала с разным уровнем нагрузок (в зависимости от марки сплава и его состояния).
За счет малой плотности удельные значения предела прочности, предела текучести и модуля упругости (соответствующие величины, поделенные на величину плотности) для прочных алюминиевых сплавов сопоставимы с соответствующими значениями удельных величин для стали и титановых сплавов. Это позволяет высокопрочным алюминиевым сплавам конкурировать со сталью и титаном, но только до температур не превышающих 200 С.
Большинство алюминиевых сплавов имеют худшую электро- и теплопроводность, коррозионную стойкость и свариваемость по сравнению с чистым алюминием.
Ниже в таблице приведены значения твердости, тепло- и электропроводности для нескольких сплавов в различных состояниях. Поскольку значения твердости коррелируют с величинами предела текучести и предела прочности, то эта таблица дает представление о порядке и этих величин.
Из таблицы видно, что сплавы с большей степенью легирования имеют заметно меньшую электро- и теплопроводность, эти величины также существенно зависят от состояния сплава (М, Н2, Т или Т1):
марка | твердость, НВ | электропроводность в % по отношению к меди | теплопроводность в кал/оС | ||||||
М | Н2 | Н,Т(Т1) | М | Н2 | Н, Т(Т1) | М | Н2 | Н, Т(Т1) | |
А8 - АД0 | 25 | 35 | 60 | 0.52 | |||||
АМц | 30 | 40 | 55 | 50 | 40 | 0.45 | 0.38 | ||
АМг2 | 45 | 60 | 35 | 30 | 0.34 | 0.30 | |||
АМг5 | 70 | 30 | 0.28 | ||||||
АД31 | 80 | 55 | 55 | 0.45 | |||||
Д16 | 45 | 105 | 45 | 30 | 0.42 | 0.28 | |||
В95 | 150 | 30 | 0.28 |
Из таблицы видно, что только сплав АД31 сочетает высокую прочность и высокую электропроводность. Поэтому «мягкие» электротехнические шины производятся из АД0, а «твердые» - из АД31 (ГОСТ 15176-89). Электропроводность этих шин составляет (в мкОм*м):
0,029 – из АД0 (без термообработки, сразу после прессования)
0,031 – из АД31 (без термообработки, сразу после прессования)
0.035 – из АД31Т (после закалки и естественного старения)
Теплопроводность многих сплавов (АМг5, Д16Т, В95Т1) вдвое ниже, чем у чистого алюминия, но все равно она выше, чем у сталей.
Коррозионные свойства.
Наилучшие коррозионные свойства имеют сплавы АМц, АМг, АД31, а худшие – высоко-прочные сплавы Д16, В95, АК. Кроме того коррозионные свойства термоупрочняемых сплавов существенно зависят от режима закалки и старения. Например сплав Д16 обычно применяется в естественно-состаренном состоянии (Т). Однако свыше 80оС его коррозионные свойства значительно ухудшаются и для использования при больших температурах часто применяют искусственное старение, хотя ему соответствует меньшая прочность и пластичность (чем после естественного старения). Многие прочные термоупрочняемые сплавы подвержены коррозии под напряжением и расслаивающей коррозии.
Свариваемость.
Хорошо свариваются всеми видами сварки сплавы АМц и АМг. При сварке нагартованного проката в зоне сварочного шва происходит отжиг, поэтому прочность шва соответствует прочности основного материала в отожженном состоянии.
Из термоупрочняемых сплавов хорошо свариваются авиали, сплав 1915. Сплав 1915 относится к самозакаливающимся, поэтому сварной шов со временем приобретает прочность основного материала. Большинство других сплавов свариваются только точечной сваркой.
Механические свойства.
Прочность сплавов АМц и АМг возрастает (а пластичность уменьшается) с увеличением степени легирования. Высокая коррозионная стойкость и свариваемость определяет их применение в конструкциях малой нагруженности. Сплавы АМг5 и АМг6 могут использоваться в средненагруженных конструкциях. Эти сплавы упрочняются только холодной деформацией, поэтому свойства изделий из этих сплавов определяются состоянием полуфабриката, из которого они были изготовлены.
Термоупрочняемые сплавы позволяют производить упрочнение деталей после их изготовления если исходный полуфабрикат не подвергался термоупрочняющей обработке.
Наибольшую прочность после упрочняющей термообработки (закалка и старение) имеют сплавы Д16, В95, АК6, АК8, АК4-1 (из доступных в свободной продаже).
Самым распространенным сплавом является Д16. При комнатной температуре он уступает многим сплавам по статической прочности, но имеет наилучшие показатели конструкционной прочности (трещиностойкость). Обычно применяется в естественно состаренном состоянии (Т). Но свыше 80 С начинает ухудшаться его коррозионная стойкость. Для использования сплава при температурах 120-250 С изделия из него подвергают искусственному старению. Оно обеспечивает лучшую коррозионную стойкость и больший предел текучести по сравнению с естественно-состаренным состоянием.
С ростом температуры прочностные свойства сплавов меняются в разной степени, что определяет их разную применимость в зависимости от температурного диапазона.
Из этих сплавов до 120 С наибольшие пределы прочности и текучести имеет В95Т1. Выше этой температуры он уже уступает сплаву Д16Т. Однако, следует учитывать, что В95Т1 имеет значительно худшую конструкционную прочность, т.е. малую трещиностойкость, по сравнению с Д16. Кроме того В95 в состоянии Т1 подвержен коррозии под напряжением. Это ограничивает его применение в изделиях, работающих на растяжение. Улучшение коррозионных свойств и существенное улучшение трещиностойкости достигается в изделиях обработанных по режимам Т2 или Т3.
При температурах 150-250 С большую прочность имеют Д19, АК6, АК8. При больших температурах (250-300 С) целесообразно применение других сплавов - АК4-1, Д20, 1201. Сплавы Д20 и 1201 имеют самый широкий температурный диапазон применения (от криогенных -250 С до +300 С) в условиях высоких нагрузок.
Сплавы АК6 и АК8 пластичны при высоких температурах, что позволяет использовать их для изготовления поковок и штамповок. Сплав АК8 характеризуется большей анизотропией механических свойств, у него меньше трещиностойкость, но он сваривается лучше, чем АК6.
Перечисленные высокопрочные сплавыт плохо свариваются и имеют низкую коррозионную стойкость. К свариваемым термоупрочняемым сплавам с нормальной прочностью относится сплав 1915. Это самозакаливающийся сплав (допускает закалку со скоростью естественного охлаждения), что позволяет обеспечить высокую прочность сварного шва. Сплав 1925, не отличаясь от него по механическим свойствам, сваривается хуже. Сплавы 1915 и 1925 имеют большую прочность, чем АМг6 и не уступают ему по характеристикам сварного шва.
Хорошо свариваются, имеют высокую коррозионную стойкость сплавы средней прочности - авиали (АВ, АД35, АД31,АД33).
АЛЮМИНИЕВЫЙ ПРОКАТ.
Из алюминия и его сплавов производятся все виды проката – фольга, листы, ленты, плиты, прутки, трубы, проволока. Следует иметь в виду, что для многих термоупрочняемых сплавов имеет место "пресс-эффект" - механические свойства прессованных изделий выше, чем у горячекатаных (т.е. круги имеют лучшие показатели прочности, чем листы).
Прутки, профили, трубы
Прутки из термоупрочняемых сплавов поставляются в состоянии "без термообработки" или в упрочненном состоянии (закалка с последующим естественным или искусственным старением). Прутки из термически неупрочняемых сплавов производятся прессованием и поставляются в состоянии "без термообработки".
Общее представление о механических свойствах алюминиевых сплавов дает гистограмма, на которой представлены гарантированные показатели для прессованных прутков при нормальных температурах:
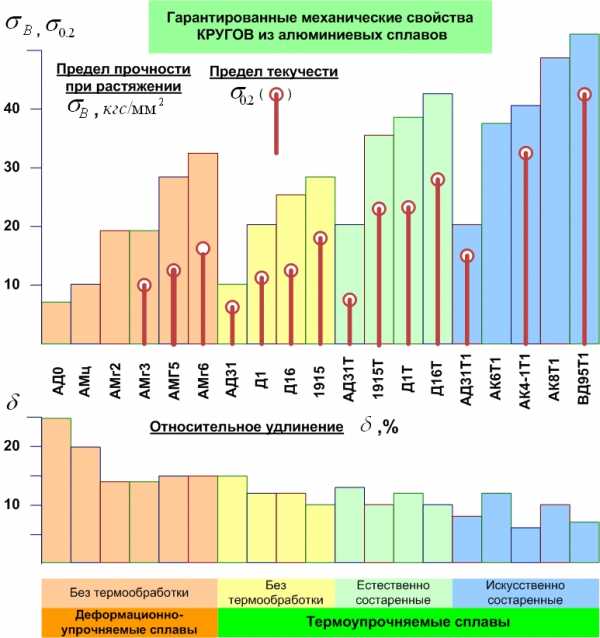
Из всего приведенного многообразия в свободной продаже всегда имеются прутки из Д16, причем круги диаметром до 100 мм включительно обычно поставляются в естественно состаренном состоянии (Д16Т). Фактические значения (по сертификатам качества) для них составляют: предел текучести ?0.2 = (37-45), предел прочности при разрыве ?в = (52-56), относительное удлинение ?=(11-17%). Обрабатываемость прутков из Д16Т очень хорошая, у прутков Д16 (без термообработки) обрабатываемость заметно хуже. Их твердость соответственно 105 НВ и 50 НВ. Как уже отмечалось, деталь, изготовленная из Д16 может быть упрочнена закалкой и естественным старением. Максимальная прочность после закалки достигается на 4-е сутки.
Поскольку дуралюминиевый сплав Д16 не отличается хорошими коррозионными свойствами, желательна дополнительная защита изделий из него анодированием или нанесением лако-красочных покрытий. При эксплуатации при температурах выше 80-100 С проявляется склонность к межкристаллитной коррозии.
Необходимость дополнительной защиты от коррозии относится и к другим высокопрочным сплавам (Д1, В95, АК).
Прутки из АМц и АМг обладают высокой коррозионной стойкостью, допускают возможность дополнительного формообразования горячей ковкой (в интервале 510-380оС).
Разнообразные профили широко представлены из сплава АД31 с различными вариантами термообработки. Применяются для конструкций невысокой и средней прочности, а также для изделий декоративного назначения.
Прутки, трубы и профили из АД31 имеют высокую общую коррозионную стойкость, не склонны к коррозии под напряжением. Сплав хорошо сваривается точечной, роликовой и аргонно-дуговой сваркой. Коррозионная стойкость сварного шва такая же, как у основного материала. Для повышения прочности сварного шва необходима специальная термообработка.
Уголки производятся в основном из АД31, Д16 и АМг2.
Трубы производятся из большинства сплавов, представленных на рисунке. Они поставляются в состояниях без термообработки (прессованные), закаленные и состаренные, а также отожженные и нагартованные. Параметры их механических свойств примерно соответствуют, приведенным на гистограмме. При выборе материала труб кроме прочностных характеристик учитывается его коррозионная стойкость и свариваемость. Наиболее доступны трубы из АД31.
Наличие кругов, труб и уголков - см. на странице сайта "Алюминиевые круги, трубы и уголки"
Плоский алюминиевый прокат.
Листы общего назаначения производятся по ГОСТ 21631-76, ленты - по ГОСТ 13726-97, плиты по ГОСТ 17232-99.
Листы из сплавов с пониженной или низкой коррозионной устойчивостью (АМг6, 1105, Д1, Д16, ВД1, В95) плакируются. Химический состав плакирующего сплава обычно соответствует марке АД1, а толщина слоя составляет 2 – 4% от номинальной толщины листа.
Плакирующий слой обеспечивает электрохимическую защиту основного металла от коррозии. Это означает, что коррозионная защита металла обеспечивается даже при наличии механических повреждений защитного слоя (царапины).
Маркировка листов включает в себя: обозначение марки сплава + состояние поставки + вид плакировки (если она присутствует). Примеры маркировки:
А5 - лист марки А5 без плакировки и термообработки
А5Н2 - лист марки А5 без плакировки, полунагартованный
АМг5М - лист марки Амг5 без плакировки, отожженный
Д16АТ - лист марки Д16 с нормальной плакировкой, закаленный и естественно состаренный.
На гистограмме приведены основные характеристики механических свойств листов в различных состояниях поставки для наиболее используемых марок. Состояние "без термообработки" не показано. В большинстве случаев величины предела текучести и предела прочности такого проката близки к соответствующим значениям для отожженного состояния, а пластичность ниже. Плиты выпускаются в состоянии "без термообработки".
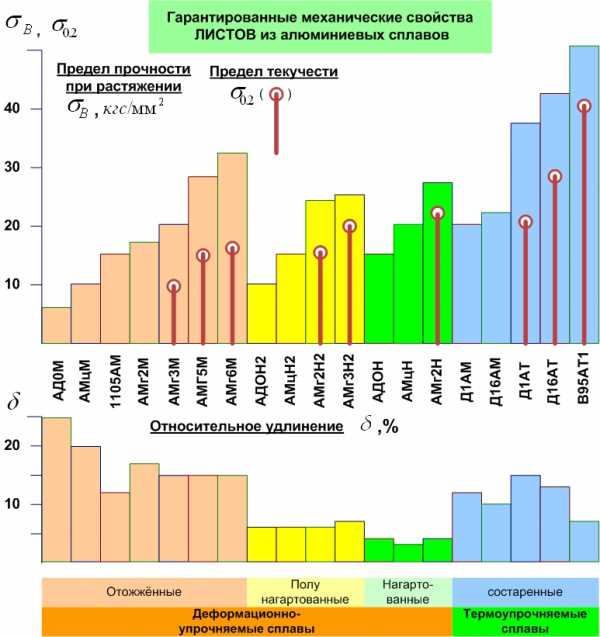
Из рисунка видно, что выпускаемый ассортимент листов дает широкие возможности для выбора материала по прочности, пределу текучести и пластичности с учетом коррозионной стойкости и свариваемости.Для ответственных конструкций из прочных сплавов обязательно учитывается трещиностойкость и характеристики сопротивления усталости.
Листы из технического алюминия (АД0, АД1, А5-А7).
Нагартованные и полунагартованные листы используются для изготовления ненагружен-ных конструкций, резервуаров (в т. ч. для криогенных температур), требующих обеспечения высокой коррозионной стойкости и допускающих применение сварки. Они используются также для изготовления вентиляционных коробов, теплоотражающих экранов (отражательная способность алюминиевых листов достигает 80%), изоляции теплотрасс.
Листы в мягком состоянии используются для уплотнения неразъемных соединений. Высокая пластичность отожженных листов позволяет производить изделия глубокой вытяжкой.
Технический алюминий отличается высокой коррозионной устойчивостью во многих средах (см. страницу "Свойства алюминия"). Однако, за счет разного содержания примесей в перечисленных марках, их антикоррозионные свойства в некоторых средах всё-таки различаются.
Алюминий сваривается всеми методами. Технический алюминий и его сварные соединения обладают высокой коррозионной стойкостью к межкристаллитной, расслаивающей коррозии и не склонны к коррозионному растрескиванию.
Кроме листов, изготавливаемых по ГОСТ21631-76, в свободной продаже имеются листы, произведенные по Евростандарту, с маркировкой 1050А. По химическому составу они соответствуют марке АД0. Фактические параметры (по сертификатам качества) механических свойств составляют (для листов 1050АН24): предел текучести ?0.2 = (10.5-14), предел прочности при разрыве ?в=(11.5-14.5), относительное удлинение ?=(5-10%), что соответствует полунагартованному состоянию (ближе к нагартованному). Листы с маркировкой 1050АН0 или 1050АН111 соответствуют отожженному состоянию.
Листы (и ленты) из сплава 1105.
Из-за пониженной коррозионной стойкости изготавливается плакированным. Широко применяется для изоляции теплотрасс, для изготовления малонагруженных деталей, не требующих высоких коррозионных свойств.
Листы из сплава АМц.
Листы из сплава АМц хорошо деформируются в холодном и горячем состояниях. Из-за невысокой прочности (низкого предела текучести) используются для изготовления только малонагруженных конструкций. Высокая пластичность отожженных листов позволяет производить из них малонагруженные изделия глубокой вытяжкой.
По коррозионной стойкости АМц практически не уступает техническому алюминию. Хорошо свариваются аргонно-дуговой, газовой и контактной сваркой. Коррозионная стойкость сварного шва такая же, как у основного металла.
Листы из сплавов АМг.
Чем больше содержание магния в сплавах этой группы, тем они прочнее , но менее пластичны.
Механические свойства.
Наиболее распостранены листы из сплавов АМг2 (состояния М, Н2, Н) и АМг3 (состояния М и Н2), в том числе рифленые. Сплавы АМг1, АМг2, АМг3, АМг4 хорошо деформируются и в горячем и в холодном состоянии. Листы обладают удовлетворительной штампуемостью. Нагартовка заметно снижает штампуемость листов. Листы этих марок применяются для конструкций средней нагруженности.
Листы из АМг6 и АМг6 в упрочненном состоянии не поставляются. Применяются для конструкций повышенной нагруженности.
Коррозионная стойкость. Сплавы АМг отличаются высокой коррозионной стойкостью в растворах кислот и щелочей. Сплавы АМг1, АМг2, АМг3, АМг4 имеют высокую коррозионную стойкость к основным видам коррозии как в отожженном так и в нагартованном состонии.
Сплавы АМг5, АМг6 склонны к коррозии под напряжением и межкристаллитной коррозии. Для защиты от коррозии листы и плиты из этих сплавов плакируются, а заклепки из АМг5п ставят только анодированными.
Свариваемость.Все сплавы АМг хорошо свариваются аргоннодуговой сваркой, но характеристики сварного шва зависят от содержания магния. С ростом его содержания уменьшается коэффициент трещинообразования, возрастает пористость сварных соединений.
Сварка нагартованных листов устраняет нагартовку в зоне термичес-кого влияния сварного соединения, механические свойства в этой зоне соответствуют свойствам в отожженном состоянии. Поэтому сварные соединения нагартованных листов АМг имеют меньшую прочность по сравнению с основным материалом.
Сварные соединения АМг1, АМг2, АМг3 обладают высокой стойкостью против коррозии. Для обеспечения коррозионной стойкости сварного шва АМг5 и АМг6 требуется специальная термообработка.
Листы и плиты из Д1, Д16, В95.
Высокопрочные сплавы Д1, Д16, В95 имеют низкую устойчивость к коррозии. Поскольку листы из них используются в конструкционных целях, то для коррозинной защиты они плакируются слоем технического алюминия. Следует помнить, что технологические нагревы плакированных листов из сплавов, содержащих медь (например Д1, Д16), не должны даже кратковременно превышать 500 С.
Наиболее распространены листы из дуралюминия Д16. Фактические значения механических параметров для листов из Д16АТ (по сертификатам качества) составляют: предел текучести ?0.2 = (28-32), предел прочности при разрыве ?в= (42-45), относительное удлинение ?=(26-23%).
Сплавы этой группы свариваются точечной сваркой, но не свариваются плавлением. Поэтому основной способ их соединения - заклепки. Для заклепок используется проволока из Д18Т и В65Т1. Сопротивление срезу для них соответственно 200 и 260 МПа.
Из толстолистового проката доступны плиты из Д16 и В95. Плиты поставляются в состоянии "без термообработки", но возможно термоупрочнение уже готовых деталей после их изготовления. Прокаливаемость Д16 допускает термоупрочнение деталей сечением до 100-120 мм. Для В95 этот показатель составляет 50-70 мм.
Листы и плиты из В95 имеют большую (по сравнению с Д16) прочность при работе на сжатие.
Наличие листов и плит - см. на странице сайта "Алюминиевые листы"
********************
Выше кратко рассмотрены свойства алюминиевых сплавов общего назначения. Для специальных целей применяются или другие сплавы, или более чистые варианты сплавов Д16 и В95. Чтобы представить многообразие специальных сплавов, применяемых в авиа-ракетной технике, стоит зайти на сайт http://www.viam.ru.
Подход к выбору материалов для корабля «Буран» интересно отражен на сайте http://www.buran.ru/htm/inside.htm
Очень интересные материалы об истории создания и применении алюминиевых сплавов в масштабных проектах СССР содержатся в воспоминаниях академика Фридляндера:
http://vivovoco.rsl.ru/VV/JOURNAL/VRAN/2004/ALLOYS.HTM http://www.arcan7.ru/library/articles/230.html http://vivovoco.rsl.ru/VV/JOURNAL/VRAN/02_01/FRID.HTM http://scilib.narod.ru/Avia/Fridlyander/contents.htm
На главную
normis.com.ua
Технология сварки алюминия и его сплавов
Температура плавления алюминия 660°С, окисной пленки 2060°С
Марка | Свариваемость | Технологические особенности сварки | |
Технически чистый алюминий | Очистка кромок и присадка от окисной пленки | ||
АД00, АД0, АДД, АД | Хорошая | Электродная проволока Св-А1, Св-А000, Св-85Т. Защитные газы Ar, He и их смеси | |
Деформируемые, термически не упрочняемые сплавы | |||
АМц, АМцС, Д12 | Хорошая | Электродная проволока Св-АМЦ | |
АМг1 ,АМг2, АМг3 | Электродная проволока Св-АМг3 | ||
АМг4, АМг5 | Электродная проволока Св-АМг5 | ||
АМгб | Электродная проволока Св-АМг6, Св-АМг7 | ||
Деформируемые, термически упрочняемые сплавы | |||
АД31, АДЗЗ, АД35 АВ, АК6, АК8 | Удовлетворительная | Электродная проволока Св-АК5, Св-1557Защитные газы Ar, He и их смеси | |
АК4, АК4-1 | Ограниченная | ||
В95 | Плохая | Предварительный подогревТермообработка после сварки при t=200-250°C. Электродная проволока Св-1557, Св-АМг5, Св-АМг6 | |
1915, 1925 | Удовлетворительная | ||
Литейные сплавы | |||
АЛ 1, АЛ2, АЛ9, АЛ 25, АЛ 26 | Хорошая | Электродная проволока той же марки, что и основной металл Защитные газы Ar, He и их смеси | |
АЛЗ, АЛ4, АЛ5, АЛ7, АЛ8, АЛ 10В | Удовлетворительная |
Трудности при сварке
- высокая температура плавления окисной пленки по сравнению с температурой плавления алюминия;
- высокая теплопроводность:
- образование значительных остаточных напряжений и деформаций;
- нерастворимость окисной пленки в жидком металле сварочной ванны;
- при нагреве нет явных признаков перехода алюминия и его сплавов в жидкое состояние;
- образование кристаллизационных трещин.
Подготовка к сварке
Резку и подготовку кромок деталей из алюминия и его сплавов следует вести механическими способами
Стыковое соединение металла разной толщины
Конструктивные элементы подготовки кромок (размеры приведены в мм)
Конструктивные элементы подготовки кромок при сварке со сквозным проплавлсннем н формированием шва на весу
При сварке за один проход может возникнуть надрез корня шва
При снятии фаски с обратной стороны стыкуемых кромок надрез не возникает. Для снятия фасок можно использовать напильник
Свариваемые поверхности тщательно очищают от смазки, на ширине 100-150 мм от кромок обезжиривают ацетоном, уайт-спиритом или другим растворителем.
Пленку окиси алюминия удаляют механически или химическим травлением.
При механической обработке (непосредственно перед сваркой) кромки зачищают на ширину 25-30 мм абразивной бумагой, шабером или щеткой из нержавеющей проволоки диаметром не более 0,15 мм.
Химическое травление проводят в течение 0,5-1 мин в растворе, состоящем из 50г едкого натра и 45г фтористого натрия на 1 л воды. После травления поверхность промывают проточной водой, а затем осветляют в 30-35%-ном растворе азотной кислоты (для алюминия и сплавов типа АМц) или в 25%-ном растворе ортофосфорной кислоты (для сплавов типа АМг и В95). После повторной промывки поверхность сушат до полного испарения влаги.
Алюминиевую сварочную проволоку перед сваркой тоже обрабатывают. Сначала ее обезжиривают, а затем подвергают травлению в 15%-ном растворе едкого натра в течение 5-10 мин при 60-70°С. после чего следует промывка в холодной воде и сушка при температуре 300°С в течение 10-30 мин.
Подготовленные к сварке материалы сохраняют свои свойства 3-4 дня. Позже на поверхности вновь образуется окисная пленка.
Детали из алюминия и его сплавов собирают в приспособлениях или на прихватках, выполняемых аргонодуговой сваркой W-электродом. Расстояние между прихватками должно быть не более 150-180 мм.
Поверхности прихваток непосредственно перед сваркой зачищают металлическими щетками. Обнаруженные дефектные прихватки удаляют, и стыки прихватывают повторно. При сварке прихватки полностью переплавляют.
Выбор параметров режима
Сварку ведут на постоянном токе обрат ной полярности. Защитным газом служит apгон или гелий и их смеси. Непосредственно перед сваркой кромки обезжиривают .
Диаметр сопел горелок выбирают равным не менее 18-22 мм.
Длина дуги должна составлять 2-6 мм, а сварочный ток - быть больше, чем при ручной аргонодуговой сварке W-электродом. Сварку выполняют за один проходили двусторонними швами.
Процесс сварки может быть: импульсно-дуговым (ИДС), струйным (СТР) или с короткими замыканиями дуги (КЗ).
Ориентировочные режимы
Вид соединения | Размеры, мм | Процесс сварки | Газ | Сварочный ток, А | Напряжение на дуге, В | Скорость сварки, м/ч | Диаметр электрода , мм | Вылет электрода, мм | Расход газа, л/мин | |
S | b | |||||||||
2,5-3 | 0+0,5 | ИДС | Ar | 40-80 | 15-18 | 35-45 | 1,2 | 10-13 | 7-9 | |
4 | 0+0,5 | ИДС ИДС СТР | ArНеAr | 80-130120-160150-220 | 18-2024-2623-24 | 30-4015-5045-70 | 1,4-1,6 | 13-18 | 8-1045-5010-20 | |
6 | 0+1 | ИДС ИДС СТР | ArНеAr | 180-250180-200200-320 | 23-2625-3023-30 | 20-3525-4525-35 | 1,6-31,6-21,6-2 | 15-3015-2515-25 | 12-1445-5012-18 | |
8-10 | 0+10+4 | ИДС СТР СТР | ArArНе | 250-320250-400250-320 | 25-3025-3332-36 | 20-3525-4525-35 | 1,6-31,6-41,6-2 | 15-4015-25 | 12-2014-2560-70 | |
12-16 | 0+40+1,50+1,5 | СТР | ArArНеНе+Ar | 320-420400-500280-360300-450 | 26-2828-3534-3630-34 | 20-3025-3520-2520-25 | 242-34 | 18-2525-4026-3025-40 | 20-2520-2560-8070-80 | |
20-30 | 0+1,5 | СТР | ArНе+ArНе | 310-550300-500280-360 | 26-3530-3534-36 | 18-2018-2520-25 | 2-42-42-3 | 20-4020-4020-30 | 18-2560-8070-80 | |
2,5-3 | 0+0,5 | ИДСИДСКЗСТР | ArНеНеAr | 60-10080-10090-12090-120 | 16-1817-1916-1717-19 | 35-4035-4540-4540-45 | 1-1,41-1,20,8-1,20,8-1,2 | 10-15 | 6-835-4035-406-9 | |
4-5 | 0+0,5 | ИДССТРИДС | АгАгНе | 120-220150-220150-200 | 18-2219-2225-30 | 25-3525-3525-40 | 1,2-1,61,2-1,41,2-1,6 | 12-1812-1512-18 | 10-1210-1235-40 | |
8 и более | 0+1 | СТР | АгНе | 280-330280-320 | 27-2932-35 | 20-2520-25 | 1,61,6 | 18-3018-25 | 20-2545-60 |
Техника сварки
При сварке алюминия и его сплавов необходимо использовать чистые и сухие перчатки из спилка или из другого подобного материала
Механизированную сварку стыковых соединений без разделки кромок в нижнем и вертикальном положениях выполняют обычно без поперечных колебаний электрода
При наличии разделки кромок первый шов выполняют также без поперечных колебаний, а последующие - с небольшими (до 5 мм) перемещениями электрода
При сварке угловых швов в нижнем положении угол наклона горелки относительно вертикальной стенки - 30-45°. Угловой шов на вертикальной плоскости ведут снизу-вверх "углом вперед". Однопроходную сварку выполняют с перемещениями конца электрода. Угловые швы больших сечений на вертикальной плоскости делают многопроходными путем выполнения узких швов. Так же сваривают и стыковые горизонтальные швы
С внутренней стороны шов защищают остающимися или съемными подкладками либо защитным газом, подаваемым каким-либо из способов:
1- защитный газ; 2- свариваемые детали; 3- заглушки; 4 - соединительные тросики
Схема установки заглушек в трубопровод для поддува защитного газа
При сварке деталей толщиной 4 мм и более из-за быстрого остывания сварочной ванны в шве образуются поры. Чтобы предотвратить их появление, применяют шаговую сварку с возвратно-поступательными перемещениями горелки. Каждый шаг вперед на 3-6 мм сопровождается перемещением назад на 1,5-3 мм. Такая техника сварки обеспечивает более эффективную защиту и медленную кристаллизацию сварочной ванны, что в конечном счете гарантирует отсутствие пор.
Чтобы уменьшить деформации при соединении длинномерных конструкций, широко применяют обратноступенчатый метод сварки.
Для заварки кратера горелку возвращают в обратном направлении на расстояние, немного превышающее длину кратера, и одновременно снижают скорость подачи проволоки
При сварке угловых и тавровых соединений сварку заканчивают перемещением горелки в обратную сторону по шву, одновременно замедляя подачу проволоки.
Эффективным способом окончания сварки служит вывод конца шва на выводные планки, которые после сварки удаляют
weldering.com
Система | Марка сплава | Химический состав % (по массе) | Свариваемость (сварка плавлением) | Рекомендуемые марки сварочной проволоки | Горячеломкость | |||
без присадки | С присадкой, гр. А. | С присадкой гр. Б | Крестовая проба К, % | Проба МВТУ А, мм/мин | ||||
Алюминиевые сплавы. | ||||||||
А. Термические неупрочняемые | ||||||||
Аl | АД1 | 99,3 Аl | св | св | св | св. А97; св. А85 | 5,0 | 9,0 |
Аl-Мn | АМц | 1,3 Мn | св | св | - | св. АМц | 0,7 | 7,0 |
Аl-Mg | AMгl | 1,1 Mg | св | св | - | св. АМн | 12,0 | 6,0 |
АМг2 | 2,2 Mg; 0,4 Мn | нс | нс | св | св. АМгЗ | 12 | 6,0 | |
АМг3 | 3,6 Mg; 0,6 Si; 0,5 Мn | св | св | - | св. АМгЗ | 8,0 | 8,0 | |
АМг4 | 4,3 Mg; 0,6 Мn; 0,06 Ti | св | св | св | св. АМг4 | 10 | 7,0 | |
АМг5 | 5,3 Mg; 0,6 Мn; 0,06 Ti | св | св | св | св. АМг5 | 10 | 7,0 | |
АМг6 | 6,3 Mg; 0,6 Мn; 0,06 Ti | св | св | св | св. АМг6 | 8,0 | 8,0 | |
Б. Термически упрочняемые | ||||||||
Аl-Сu | Д20 | 6,5 Сu; 0,6 Мn; 0,15 Ti | св | св | - | Д20 | 15 | 6,0 |
1201 | 6,3 Сu; 0,3 Мn; 0,06 Ti; 0,17 Zr; 0,1 V | св | св | - | св. 1201 | 5,0 | 10 | |
1205 | 6,3 Сu; 0,6 Мn; 0,06 Ti; 0,11 Zr; 0,15 Cd | нс | нс | св | св. 1201 | 12 | 6,0 | |
Al-Mg-Si | АД31 | 0,6 Mg; 0,5 Si | нс | нс | св | св. АК5 | 15 | 6,0 |
АД33 | 1,1 Mg; 0,25 Сu; 0,6 Si; 0,25 Сг | нс | нс | св | св. АК5 | 12 | 6,0 | |
АД35 | 1,1 Mg; 1,0 Si; 0,7 Мn; 0,25 Сг | нс | нс | св | св. АК5 | 12 | 6,0 | |
АВ | 0,7 Mg; 0,3 Си; 0,85 Si; 0,25 Мn | нс | нс | св | св. АК5 | 10 | 7,0 | |
Al-Zn-Mg | В92ц | 4,4 Mg; 3,2 Zn; 0,8 Мn; 0,13 Zr; 0,14 Cr | св | св | нс | св. В92ц | 12 | 6,0 |
1915 | 1,1 Mg; 3,7 Zn; 0,4 Mn 0,18 Zr | нс | нс | св | св. 1557 | 10 | 7,0 | |
Al-Mg-Cu | ВАД1 | 2,5 Mg; 4,1 Cu; 0,6 Mn; 0,06 Ti; 0,15 Zr | св | св | нс | ВАД1 | 10 | 7,0 |
Д1 | 0,6 Mg; 4,3 Cu; 0,6 Mn | нс | нс | нс | D1 | 40 | 2,0 | |
Д16 | 1,5 Mg; 4,3 Cu; 0,6 Mn | нс | нс | нс | D16 | 50 | 1,0 | |
Д19 | 2,0 Mg; 4,0 Cu; 0,75 Mn | нс | нс | нс | Д19 | 45 | 2,0 | |
Al-Mg-Cu-Zn | В95 | 2,3 Mg; 1,7 Cu; 6,0 Zn; 0,4 Mn; 0,18 Cr | нс | нс | нс | В95 | 50 | 1,0 |
В96 | 2,6 Mg; 2,3 Cu; 8,5 Zn | нс | нс | нс | В96 | 60 | 1,0 | |
Al-Mg-Si-Cu | АК6 | 0,6 Mg; 2,2 Cu; 0,9 Si;0,6 Mn | нс | нс | нс | АК6 | 45 | - |
АК8 | 0,6 Mg; 4,3 Cu; 0,9 Si; 0,7 Mn | нс | нс | нс | АК8 | 50 | - | |
Al-Mg-Cu-Fe-Si | АК4 | 1,6 Mg; 2,2 Cu; 1,2 e; 1,3 Ni | нс | нс | нс | АК4 | 60 | - |
АК4-1 | 1,6 Mg; 2,2 Cu; 1,2 e; 1,2 Ni | нс | нс | нс | АК4 | 65 | - | |
Магниевые сплавы | ||||||||
А. Термические неупрочняемые | ||||||||
M-Мn | MA1 | 1,9 Мn | св | св | нс | MA1 | 10 | - |
MA8 | 1,9 Мn; 0,25 Се | нс | нс | св | MA2-1 | 20 | - | |
Mg-Zn | MA20 (ВМД8) | 1,25 Zn; 0,2 Се; 0,09 Zr | нс | нс | св | MA20-1 | 10 | - |
Mg-Al-Zn | MA2 | 3,5 Al; 0,5 Zn; 0,3 Мn | нс | нс | св | MA2-1 | 15 | - |
MA2-1 | 4,4 Al; 1,1 Zn; 0,4 Мn | св | св | нс | MA2-1 | 20 | - | |
Mg-Zn-Cd-La | MA15 (ВМД3) | 1,6 Cd; 3,0 Zn; 0,9 La; 0,7 Zr | нс | нс | нс | MA15 | 30 | - |
Mg-Zn-Cd-Nd | MA19 (ВМД6) | 0,6 Cd; 6,2 Zn; 1,7 Nd; 0,7 Zr | нс | нс | нс | MA19 | >30 | - |
Б. Термические упрочняемые | ||||||||
Mg-Zn | MA14 (BM65-1) | 5,5 Zn; 0,6 Zr | нс | нс | нс | MA14 | >40 | - |
Mg-Nd | MA12 | 3,0 Nd; 0,6 Zr | св | св | нс | MA12 | 15 | - |
Mg-Al-Zn | MA5 | 8,5 Al; 0,5 Zn; 0,3 Mn | св | св | нс | MA5 | 20 | - |
Mg-Mn-Nd | МА11 | 3,0 Nd; 2,0 Mn: 0,2 Ni | нс | нс | нс | МА11 | >40 | - |
oitsp.ru
химический состав, свойства. Где применяется сплав АМг5?
Алюминиевомагниевый деформируемый сплав марки АМг5 – это специальный алюминий, идущий на производство изделий методом холодной или горячей деформации. Этот материал наделен очень высокой коррозионной стойкостью, поскольку его химический состав идеально сбалансирован и включает целый ряд взаимодополняющих элементов. На сегодня известны 2 модификации данного алюминиевого сплава:
- АМг5М – мягкий отожженный алюминий
- АМг5Н – нагартованный алюминий
Подобные виды обработки (закалка и старение) способствуют увеличению показателей прочности материала.
Сплав АМг5: химсостав
Расшифровка названия марки АМг5 говорит о том, что основной добавкой к алюминию здесь выступает магний (доля в пределах 5%):
- Al – 91,9-94,68%
- Mg – 4,8-5,8%
- Mn – 0,5-0,8%
- Fe – менее 0,5%
- Si – менее 0,5%
- Zn – менее 0,2%
- Ti – 0,02-0,1%
- Cu – менее 0,1%
- Be – 0,0002-0,005%
В состав сплава марки АМг5 включены такие элементы, как марганец, железо, кремний, цинк, титан, медь и бериллий, что делает материал отлично свариваемым, а значит, подходящим для формирования максимально сложных конструкций.
АМг5: сплав и его характеристики
Отжигается такой алюминий при температуре 305-340oC с охлаждением на воздухе. При удельном весе в 2650 кг/м3 этот сплав обладает достаточно высокой для алюминиевых сплавов твердостью: HB 10-1=65МПа.
В следующих таблицах представлены все основные физические и механические свойства алюминия АМг5:
Применение АМг5
Данный сплав известен своими отличными качествами сваривания, что на практике проявляется отсутствием необходимости применять для создания прочных швов специальные уплотнители. Сплав самостоятельно формирует достаточно герметичное соединение, но, разумеется, для этого необходимо применять проволоку сплава той же марки АМг5. Такая особенность этого алюминиевого сплава сделала его популярным в судостроении, в частности, при изготовлении цельносварных судов, имеющих толстые стенки при относительно небольшом общем весе конструкции.Помимо неограниченной свариваемости сплав АМг5 характеризуется высокой пластичностью и гибкостью. Это, в свою очередь, привлекает архитекторов и дизайнеров, получающих возможность создавать всевозможные изделия интерьера и экстерьера. Благодаря высоким антикоррозийным качествам АМг5 стойко переносит агрессивное воздействие окружающей среды, в том числе контакты с пресной и морской водой.
fx-commodities.ru