Челябинский Завод Грунторезной Техники. Hrc 40 45
Таблица соответствия HB - HRC
Твёрдость - это сопротивление тела внедрению индентора - другого твёрдого тела. Способы испытания твёрдости подразделяются на статические и динамические.
К статическим относятся способы измерения твёрдости по Бринеллю, Викерсу, Роквеллу, Кнупу; к динамическим - способы измерения твёрдости по Шору, Шварцу, Бауману, Польди, Морину, Граве.
Измерения твёрдости осуществляют при 20±10°С.
Измерение твёрдости по Бринеллю
Бринелля метод [по имени шведского инженера Ю.А.Бринелля (J.A.Brinell)] - способ определения твёрдости материалов вдавливанием в испытываемую поверхность стального закалённого шарика диаметром 2,5; 5 и 10 мм пр нагрузке P от 625 H до 30 кН. Число твёрдости по Бринеллю HB - отношение нагрузки (кгс) к площади (мм2) поверхности отпечатка. Для получения сопоставимых результатов относительной твёрдости материалы (HB свыше 130) испытывают при отношении P:D2=30, материалы средней твёрдости (HB 30-130) - при P:D2=10, мягкие (HB<30) - при P:D2=2,5. Испытания по методу Бринелля проводят на стационарных твердомерах - прессах Бринелля, обеспечивающих плавное приложение заданной нагрузки к шарику и постоянство её при выдержке в течение установленного времени (обычно 30 секунд).
Метод измерения твердости металлов по Бринеллю регламентирует ГОСТ 9012-59 "Металлы. Метод измерения твердости по Бринеллю": Стандарт устанавливает метод измерения твердости по Бринеллю металлов с твердостью не более 650 единиц. Сущность метода заключается во вдавливании шарика (стального или из твердого сплава) в образец (изделие) под действием усилия, приложенного перпендикулярно к поверхности образца, в течение определенного времени, и измерении диаметра отпечатка после снятия усилия. ГОСТ 9012-59, в частности, определяет требования, предъявляемые к отбору образцов металла для измерения твёрдости по Бринеллю - размер образцов, шероховатость поверхности и др.
Измерение твёрдости по Роквеллу
Роквелла метод [по имени американского металлурга С.Роквелла (S.Rockwell), разработавшего этод метод] - способ определения (измерения) твёрдости материалов (главным образом металлов) вдавливанием в испытываемую поверхность алмазного индентора с углом при вершине 120° (шкалы А и С) или стального закалённого шарика диаметром 1/16 дюйма или 1,588 мм (шкала B. Твёрдость по Роквеллу выражается в условных единицах. За единицу твёрдости принята величина, соответствующая перемещению индентора на 0,002 мм. Испытание методов Роквелла проводят на специальном настольном приборе, снабжённом индикатором, который показывает число твёрдости. ГОСТ 23677-79.
Таблица соответствия HB – HRC (Перевод значений твёрдости) (соотношение твёрдости по Бриннелю твёрдости по Роквеллу,определяемых методами в соответствии с ГОСТ 8.064-79) |
Твердость по Роквеллу (эталонная) | Твердость по Роквеллу | Твердость по Бринеллю | |
HRCэ | HRC | D=10мм HB | Р=3000кг диаметр отпечатка в мм |
- | - | HB 95,0 | 6 |
- | - | HB 100 | 5,87-5,89 |
- | - | HB 111 | 5,60-5,62 |
- | - | HB 115 | 5,51-5,53 |
- | - | HB 116 | 5,49-5,50 |
- | - | HB 120 | 5,41-5,42 |
- | - | HB 125 | 5,31-5,42 |
- | - | HB 130 | 5,22 |
- | - | HB 135 | 5,13 |
- | - | HB 137 | 5,09-5,10 |
- | - | HB 138 | 5,07-5,08 |
- | - | HB 140 | 5,04-5,05 |
- | - | HB 141 | 5,02-5,03 |
- | - | HB 142 | 5,01 |
- | - | HB 143 | 5 |
- | - | HB 143 | 4,99 |
- | - | HB 144 | 4,98 |
- | - | HB 144 | 4,97 |
- | - | HB 145 | 4,96 |
- | - | HB 146 | 4,95 |
- | - | HB 152 | 4,86 |
- | - | HB 161 | 4,72-4,73 |
- | - | HB 164 | 4,68-4,69 |
- | - | HB 167 | 4,64-4,65 |
- | - | HB 170 | 4,60-4,61 |
- | - | HB 174 | 4,55-4,56 |
- | - | HB 179 | 4,49-4,50 |
- | - | HB 185 | 4,42-4,43 |
- | - | HB 197 | 4,29-4,30 |
- | - | | 4,28 |
- | - | HB 199 | 4,27 |
- | - | HB 200 | 4,26 |
- | - | HB 201 | 4,25 |
- | - | HB 202 | 4,24 |
- | - | HB 203 | 4,23 |
- | - | HB 204 | 4,22 |
- | - | HB 205 | 4,21 |
| HRC 17,9 | HB 206 | 4,2 |
HRCэ 20,5 | HRC 18,3 | HB 209 | 4,18 |
HRCэ 21,0 | HRC 19,0 | HB 212 | 4,15 |
HRCэ 21,5 | HRC 19,7 | HB 215 | 4,12 |
HRCэ 22,0 | HRC 20,1 | HB 217 | 4,1 |
HRCэ 22,5 | HRC 20,5 | HB 219 | 4,08 |
HRCэ 23,0 | HRC 20,9 | HB 222 | |
HRCэ 23,5 | HRC 21,3 | HB 224 | 4,04 |
HRCэ 24,0 | HRC 22,0 | HB 229 | 4 |
HRCэ 24,5 | HRC 22,4 | HB 231 | 3,98 |
HRCэ 25,0 | HRC 22,8 | HB 234 | 3,96 |
HRCэ 25,5 | HRC 23,6 | HB 239 | 3,92 |
HRCэ 26,0 | HRC 24,0 | HB 241 | 3,9 |
HRCэ 26,5 | HRC 24,4 | | 3,88 |
HRCэ 27,0 | HRC 24,8 | HB 246 | 3,86 |
HRCэ 27,5 | HRC 25,6 | HB 252 | 3,82 |
HRCэ 28,0 | HRC 26,0 | HB 255 | 3,8 |
HRCэ 28,5 | HRC 26,4 | HB 257 | 3,78 |
HRCэ 29,0 | HRC 27,3 | HB 263 | 3,74 |
HRCэ 30,0 | HRC 28,1 | HB 269 | 3,7 |
HRCэ 30,5 | | HB 272 | 3,68 |
HRCэ 31,0 | HRC 29,0 | HB 275 | 3,66 |
HRCэ 31,5 | HRC 29,4 | HB 278 | 3,64 |
HRCэ 32,0 | HRC 29,9 | HB 282 | 3,62 |
HRCэ 32,5 | HRC 30,3 | HB 285 | 3,6 |
HRCэ 33,0 | HRC 30,8 | HB 288 | 3,58 |
HRCэ 33,5 | HRC 31,6 | HB 295 | 3,54 |
HRCэ 34,0 | HRC 32,1 | HB 298 | 3,52 |
HRCэ 34,5 | HRC 32,5 | HB 302 | 3,5 |
HRCэ 35,0 | HRC 33,0 | HB 306 | 3,48 |
HRCэ 35,5 | HRC 33,8 | HB 313 | 3,44 |
HRCэ 36,0 | HRC 34,3 | HB 317 | 3,42 |
HRCэ 36,5 | HRC 34,7 | HB 321 | 3,4 |
HRCэ 37,0 | HRC 35,2 | HB 325 | 3,38 |
HRCэ 37,5 | HRC 35,6 | HB 329 | 3,36 |
HRCэ 38,0 | HRC 36,0 | HB 333 | 3,34 |
HRCэ 38,5 | HRC 36,5 | HB 337 | 3,32 |
HRCэ 39,0 | HRC 36,9 | HB 341 | 3,3 |
HRCэ 39,5 | HRC 37,8 | HB 350 | 3,26 |
HRCэ 40,0 | HRC 38,2 | HB 354 | 3,24 |
HRCэ 40,5 | HRC 38,7 | HB 359 | 3,22 |
HRCэ 41,0 | HRC 39,1 | HB 363 | 3,2 |
HRCэ 41,5 | HRC 40,0 | HB 373 | 3,16 |
HRCэ 42,0 | HRC 40,5 | HB 378 | 3,14 |
HRCэ 42,5 | HRC 40,9 | HB 383 | 3,12 |
HRCэ 43,0 | HRC 41,4 | HB 388 | 3,1 |
HRCэ 43,5 | HRC 41,9 | HB 393 | 3,08 |
HRCэ 44,0 | HRC 42,4 | HB 398 | 3,06 |
HRCэ 44,5 | HRC 42,9 | HB 403 | 3,04 |
HRCэ 45,0 | HRC 43,3 | HB 409 | 3,02 |
HRCэ 45,5 | HRC 43,8 | HB 415 | 3 |
HRCэ 46,0 | HRC 44,4 | HB 420 | 2,98 |
HRCэ 46,5 | HRC 44,9 | HB 426 | 2,96 |
HRCэ 47,0 | HRC 45,4 | HB 432 | 2,94 |
HRCэ 47,5 | HRC 45,9 | HB 438 | 2,92 |
HRCэ 48,0 | HRC 46,5 | HB 444 | 2,9 |
HRCэ 48,5 | HRC 47,0 | HB 451 | 2,88 |
HRCэ 49,0 | HRC 47,6 | HB 457 | 2,86 |
HRCэ 49,5 | HRC 48,2 | HB 464 | 2,84 |
HRCэ 50,0 | HRC 48,8 | HB 470 | 2,82 |
HRCэ 50,5 | HRC 49,4 | HB 477 | 2,8 |
HRCэ 51,0 | HRC 50,0 | HB 484 | 2,78 |
HRCэ 51,5 | HRC 50,6 | HB 492 | 2,76 |
HRCэ 52,0 | HRC 50,7 | HB 502 | 2,74 |
HRCэ 52,5 | HRC 51,5 | HB 503 | 2,73 |
HRCэ 52,0 | HRC 51,8 | HB 506 | 2,72 |
HRCэ 53,5 | HRC 52,5 | HB 514 | 2,7 |
HRCэ 54,0 | HRC 53,1 | HB 522 | 2,68 |
HRCэ 54,5 | HRC 53,5 | HB 526 | 2,67 |
HRCэ 55,0 | HRC 53,8 | HB 530 | 2,66 |
HRCэ 55,5 | HRC 54,1 | HB 534 | 2,65 |
HRCэ 56,0 | HRC 54,5 | HB 538 | 2,64 |
HRCэ 56,5 | HRC 55,1 | HB 547 | 2,62 |
HRCэ 57,0 | HRC 55,8 | HB 555 | 2,6 |
HRCэ 57,5 | HRC 56,5 | HB 564 | 2,58 |
HRCэ 58,0 | HRC 57,2 | HB 573 | 2,56 |
HRCэ 58,5 | HRC 57,6 | HB 578 | 2,55 |
HRCэ 59,0 | HRC 57,9 | HB 582 | 2,54 |
HRCэ 59,5 | HRC 58,6 | HB 592 | 2,52 |
HRCэ 60,0 | HRC 59,3 | HB 601 | 2,5 |
HRCэ 60,5 | HRC 59,7 | HB 606 | 2,49 |
HRCэ 61,0 | HRC 60,0 | HB 611 | 2,48 |
HRCэ 61,5 | HRC 60,4 | HB 616 | 2,47 |
HRCэ 62,0 | HRC 60,7 | HB 621 | 2,46 |
HRCэ 62,5 | HRC 61,1 | HB 627 | 2,45 |
HRCэ 63,0 | HRC 61,4 | HB 632 | 2,44 |
HRCэ 63,5 | HRC 62,1 | HB 643 | 2,42 |
HRCэ 64,0 | HRC 63,2 | HB 659 | 2,39 |
HRCэ 64,5 | HRC 63,6 | HB 665 | 2,38 |
HRCэ 65,0 | HRC 63,9 | HB 670 | 2,37 |
HRCэ 65,5 | HRC 64,3 | HB 676 | 2,36 |
mtkarmada.com
Закалка и отпуск стали 45: твердость, HRC, режимы, технология
Обработка стали, осуществляемая в процессе термообработки, является одной из важнейших операций в металлургической отрасли и машиностроении. При соблюдении технологии PC 45 изделие приобретает достаточную прочность, значительно расширяя область использования изготовляемых изделий. При необходимости можно осуществлять закалку изделия из стали, в домашних условиях строго соблюдая технологию. При закалке лезвия ножа в домашних условиях вполне допустимо добиться повышения прочностных характеристик изделия в 3-4 раза.
Структурные изменения металла
При нагревании конструкционной специальной стали 45 до аустенитного уровня, происходит изменение состояния структурной решетки железа с переходом из объемно-центрированной в гранецентрированную структуру. Осуществляется перемещение углерода входящего в перлит и представляющего собой мельчайшие кристаллы Fe3C (цементита) в гранецентрированную измененную решетку железа.
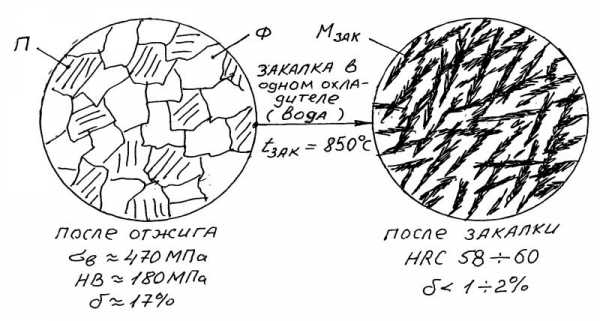
Структура стали 45 после отжига и закалки
В ходе охлаждения происходит быстрое снижение температуры обрабатываемой стали, но из-за замедления скорости перемещения атомов углерода они остаются внедренными в новую решетку железа, образуя твердую пересыщенную структуру, имеющую внутреннее напряжение. Решетка преобразуется в тетрагональную с ориентацией в одном направлении.
Происходит образование игольчатых мелких структур имеющих название мартенсит. Данный вид кристаллов придает металлу высокую прочность, твердость и улучшенные характеристики. Происходит образование одновременно двух видов кристаллов аустенита и мартенсита, которые воздействуют друг, на друга создавая внутреннее избыточное напряжение. При активном влиянии на металл внешних сил происходит взаимная компенсация двух видов кристаллов, придавая структуре прочность.
Термическая обработка металла
Для изменения характеристик стали производится термическая обработка с соблюдением необходимых режимов воздействия.
Процесс термической обработки состоит из процессов:
- отжига;
- нормализации;
- старения;
- закалки и отпуска.
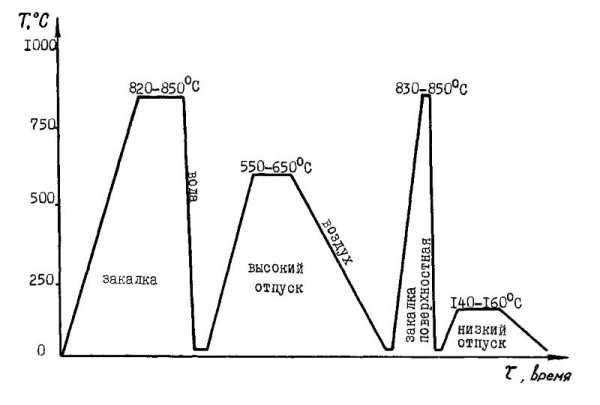
Режимы термообработки стали 45
Закалка и отпуск стали во многом зависят от ряда факторов:
- температурного режима;
- скорости повышения температуры;
- временного промежутка воздействия на металл высоких температур;
- процесса охлаждения (скорости изменения температуры охлаждения среды или жидкости).
Закалка стали
Процесс закалки стали заключается в проведении термообработки заготовок с нагреванием до температуры выше критической с дальнейшим ускорением охлаждения. Данное состояние способствует повышению прочности и твердости (HRC) стали с одновременным снижением пластичности и улучшением потребительских характеристик.
Режим воздействия температуры охлаждения металла зависит от количества содержания углерода и легирующих присадок в стали.
После проведения закалки стали заготовки покрываются налетом окалины и частично теряют содержащийся углерод, поэтому технология обязательно должна соблюдаться согласно установленному регламенту.
Охлаждение металла должно проходить быстро, для предотвращения преобразования аустенита в сорбит или троостит. Охлаждение должно производиться точно по графику быстрое остывание заготовок, приводит к образованию мелких трещин. В процессе охлаждения от 200 °C до 300 °C происходит искусственное замедление при постепенном остывании изделий для этого, могут использоваться охлаждающие жидкости.
Закалка стали с помощью ТВЧ
При проведении поверхностной закалки с помощью ТВЧ процесс нагрева изделий осуществляется до более высокой температуры.
Это вызвано двумя факторами:
- Нагрев осуществляется за короткое время с ускоренным изменением и переходом перлита в аустенит.
- Реакция перехода должна осуществляться в сжатые сроки за небольшой промежуток времени при высокой температуре.
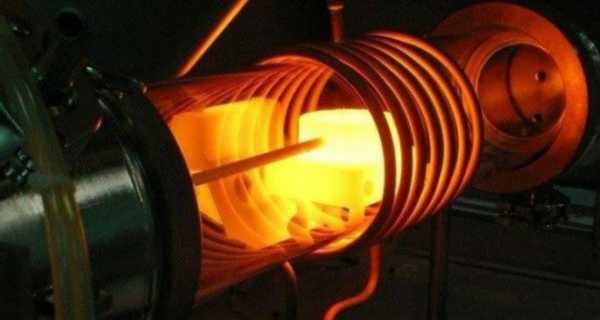
Закалка ТВЧ (токами высокой частоты)
Процессы, протекающие при обычной закалке в печи с использованием ТВЧ, имеют различные характеристики и ведут к изменению твердости (HRC) заготовок:
- При нагреве в печи скорость составляет, 2-3 °С/сек до 840 – 860 °С.
- С использованием ТВЧ – 250 °С/сек до температуры 880 – 920 °С или в режиме при 500 °С/сек – до 980 – и 1020 °С.
Нагрев деталей при использовании ТВЧ осуществляется до более высокой температуры, но перегрева заготовки не происходит. В процессе обработки с применением ТВЧ время операции нагрева значительно сокращается, что способствует сохранению размера и структуры зерна. В ходе выполнения операции закалки ТВЧ твердость металла ( HRC) возрастает на 2-3 един. по Роквеллу.
Процесс нагрева
Заготовки из стали нагреваются в печах. При нагреве инструмента используется предварительный подогрев отдельных частей с использованием
- печей с температурой рабочей среды от 400 °С до 500 °С;
- в специальных соляных ваннах с погружением на 2-4 сек. 2-3 раза.
Обязательно должно соблюдаться условие равномерного прогрева всего изделия. Строго выдерживаться условие одновременного помещения деталей в печь с соблюдением времени нагрева деталей.
Применение защитных мер
В процессе термической обработки происходит постепенное выгорание углерода и образование налета окалины. Для предотвращения ухудшения качества металла и его защиты используются защитные газы, которые закачиваются в ходе процесса закаливания. В печь имеющую герметичную камеру, где происходит термообработка с помощью специального генератора, закачивается газ аммиак или метан.
При отсутствии герметичных печей операции обработки производятся в специальной герметичной таре, куда предварительно засыпается чугунная стружка для предотвращения выгорания углерода.
При обработке заготовок в соляных ваннах металл защищен от окисления, а для создания необходимых условий для сохранения уровня углерода содержание ванной 2-х кратно в течение суток раскисляется борной кислотой, кровяной солью или бурой. При температуре обработки в диапазоне температур 760-1000 °С в качестве раскислителя может использоваться древесный уголь.
Использование специальных охлаждающих жидкостей
В ходе проведения технологического процесса для охлаждения деталей в основном используется вода. Качество охлаждающей жидкости можно изменить, добавив соду или специальные соли, что может повлиять на процесс охлаждения заготовки.
Для сохранения процесса закалки категорически запрещается использовать содержащуюся в нем воду для посторонних операций. Вода должна быть чистой и иметь температуру от 20 до 30 °С. Запрещено использовать для закалки стали проточную воду.
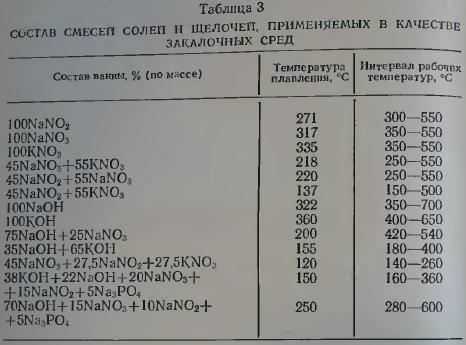
Состав смесей солей и щелочей, применяемых в качестве закалочных сред
Данный способ закалки применяется только для цементированных изделий или имеющих простую форму.
Изделия, имеющие сложную форму, изготовленные из конструкционной специальной стали охлаждаются в 5% растворе каустической соды при температуре 50-60 °С. Операция закалки, проводится в помещении, оснащенном вытяжной вентиляцией. Для закалки заготовок выполненных из высоколегированной стали применяют минеральные масла, причем скорость охлаждения в масленой ванне не зависит от температуры масла. Недопустимо смешивание масла и воды, что может привести к появлению трещин на металле.
При закалке в масляной ванне необходимо выполнять ряд правил:
- Остерегаться воспламенения масла.
- При охлаждении металла в масле происходит выделение вредоносных газов (обязательно наличие вытяжной вентиляции).
- Происходит образование налета на металле.
- Масло теряет свои свойства при интенсивном использовании для охлаждения металла.
При проведении процесса закалки стали 45 необходимо соблюдать технологический процесс с соблюдением всех операций.
Отпуск стали 45
Технологический процесс отпуска стали проводится в зависимости от необходимой температуры:
- в печах с принудительной циркуляцией воздуха;
- в специальных ваннах с селитровым раствором;
- в ваннах с маслом;
- в ваннах заполненных расплавленной щелочью.
Температура для проведения процесса отпуска зависит от марки стали, а сам процесс изменяет структуру и способствует снижению напряжения металла, а твердость снижается на малую величину. После проведения всех операций заготовка подвергается техническому контролю и отправляется заказчику.
При закалке и отпуске металла в домашних условиях необходимо строго соблюдать технологию и технику безопасности проведения работ.
Если вы нашли ошибку, пожалуйста, выделите фрагмент текста и нажмите Ctrl+Enter.
stankiexpert.ru
Таблица твердости металлов по Бринеллю, Роквеллу, Виккерсу, Шору
Твердостью металла называют его свойство оказывать сопротивление пластической деформации при контактном воздействии стандартного тела-наконечника на поверхностные слои материала.
Испытание на твердость - основной метод оценки качества термообработки изделия.
Определение твердости по методу Бринелля. Метод основан на том, что в плоскую поверхность под нагрузкой внедряют стальной шарик. Число твердости НВ определяется отношением нагрузки к сферической поверхности отпечатка.
Метод Роквелла (HR) основан на статическом вдавливании в испытываемую поверхность наконечника под определенной нагрузкой. В качестве наконечников для материалов с твердостью до 450 HR используют стальной шарик. В этом случае твердость обозначают как HRB. При использовании алмазного конуса твердость обозначают как HRA или HRC (в зависимости от нагрузки).
Твердость по методу Виккерса (HV) определяют путем статического вдавливания в испытуемую поверхность алмазной четырехгранной пирамиды. При испытании измеряют отпечаток с точностью до 0,001 мм при помощи микроскопа, который является составной частью прибора Виккерса.
Метод Шора. Сущность данного метода состоит в определении твердости материала образца по высоте отскакивания бойка, падающего на поверхность испытуемого тела с определенной высоты. Твердость оценивается в условных единицах, пропорциональных высоте отскакивания бойка.
Числа твердости HRC для некоторых деталей и инструментов
Головки откидных болтов, гайки шестигранные, рукоятки зажимные | 33...38 |
Головки шарнирных винтов, концы и головки установочных винтов, оси шарниров, планки прижимные и съемные, головки винтов с внутренними шестигранными отверстиями, палец поводкового патрона | 35...40 |
Шлицы круглых гаек | 36...42 |
Зубчатые колеса, шпонки, прихваты, сухари к станочным пазам | 40...45 |
Пружинные и стопорные кольца, клинья натяжные | 45...50 |
Винты самонарезающие, центры токарные, эксцентрики, опоры грибковые и опорные платики, пальцы установочные, цанги | 50...60 |
Гайки установочные, контргайки, сухари к станочным пазам, эксцентрики круговые, кулачки эксцентриковые, фиксаторы делительных устройств, губки сменные к тискам и патронам, зубчатые колеса | 56...60 |
Рабочие поверхности калибров - пробок и скоб | 56...64 |
Копиры, ролики копирные | 58...63 |
Втулки кондукторные, втулки вращающиеся для расточных борштанг | 60...64 |
Таблица соотношений между числами твердости по Бринеллю, Роквеллу, Виккерсу, Шору
Указанные значения твердости по Роквеллу, Виккерсу и Шору соответствуют значениям твердости по Бринеллю, определенным с помощью шарика диаметром 10 мм.
65 | 84,5 | - | 2,34 | 688 | 940 | 96 |
64 | 83,5 | - | 2,37 | 670 | 912 | 94 |
63 | 83 | - | 2,39 | 659 | 867 | 93 |
62 | 82,5 | - | 2,42 | 643 | 846 | 92 |
61 | 82 | - | 2,45 | 627 | 818 | 91 |
60 | 81,5 | - | 2,47 | 616 | - | - |
59 | 81 | - | 2,5 | 601 | 756 | 86 |
58 | 80,5 | - | 2,54 | 582 | 704 | 83 |
57 | 80 | - | 2,56 | 573 | 693 | - |
56 | 79 | - | 2,6 | 555 | 653 | 79,5 |
55 | 79 | - | 2,61 | 551 | 644 | - |
54 | 78,5 | - | 2,65 | 534 | 618 | 76,5 |
53 | 78 | - | 2,68 | 522 | 594 | - |
52 | 77,5 | - | 2,71 | 510 | 578 | - |
51 | 76 | - | 2,75 | 495 | 56 | 71 |
50 | 76 | - | 2,76 | 492 | 549 | - |
49 | 76 | - | 2,81 | 474 | 528 | - |
48 | 75 | - | 2,85 | 461 | 509 | 65,5 |
47 | 74 | - | 2,9 | 444 | 484 | 63,5 |
46 | 73,5 | - | 2,93 | 435 | 469 | - |
45 | 73 | - | 2,95 | 429 | 461 | 61,5 |
44 | 73 | - | 3 | 415 | 442 | 59,5 |
42 | 72 | - | 3,06 | 398 | 419 | - |
40 | 71 | - | 3,14 | 378 | 395 | 54 |
38 | 69 | - | 3,24 | 354 | 366 | 50 |
36 | 68 | - | 3,34 | 333 | 342 | - |
34 | 67 | - | 3,44 | 313 | 319 | 44 |
32 | 67 | - | 3,52 | 298 | 302 | - |
30 | 66 | - | 3,6 | 285 | 288 | 40,5 |
28 | 65 | - | 3,7 | 269 | 271 | 38,5 |
26 | 64 | - | 3,8 | 255 | 256 | 36,5 |
24 | 63 | 100 | 3,9 | 241 | 242 | 34,5 |
22 | 62 | 98 | 4 | 229 | 229 | 32,5 |
20 | 61 | 97 | 4,1 | 217 | 217 | 31 |
18 | 60 | 95 | 4,2 | 207 | 206 | 29,5 |
- | 59 | 93 | 4,26 | 200 | 199 | - |
- | 58 | - | 4,34 | 193 | 192 | 27,5 |
- | 57 | 91 | 4,4 | 187 | 186 | 27 |
- | 56 | 89 | 4,48 | 180 | 179 | 25 |
tekhnar.ru
Термообработка стали 45, 40х, 20, 30хгса, 65г, 40, 40хн, 35, и стали 20х13
В машиностроении чаще всего подвергают термообработки сталь 45 (в качестве заменителя 40Х, 50, 50Г2), сталь 40х (в качестве заменителя стали 38ха, 40хр, 45х, 40хс, 40хф, 40хн), сталь 20 (в качестве заменителя 15, 25), сталь 30хгса (заменители 40хфа, 35хм, 40хн, 25хгса, 35хгса), сталь 65г, сталь 40хн, сталь 35, и сталь 20х13, также
Термообработка стали 45
Термообработка стали 45 - конструкционная углеродистая. После предварительной термообработки стали 45 - нормализации, довольно легко проходит механическую обработку. Точение, фрезеровку и т. д. Получают детали, например,типа вал-шестерни, коленчатые и распределительные валы, шестерни, шпиндели, бандажи, цилиндры, кулачки.После окончательной термообработки стали 45 (закалка), детали приобретают высокую прочность и износостойкость. Часто шлифуются. Высокое содержание углерода (0,45%) обеспечивает хорошую закаливаемость и соответственно высокую твёрдость поверхности и прочность изделия. Сталь 45 калят «на воду». То есть после калки деталь охлаждают в воде. После олаждения деталь подвегается низкотепмературному отпуску при температуре 200-300 градусов Цельсия. При такой термообработки стали 45 получают твердость порядка 50 HRC.
Термообрабтка стали 45 и применение изделий: Кулачки станочных патронов, согласно указаниям ГОСТ, изготовляют из сталей 45 и 40Х. Твёрдость Rc = 45 -50. В кулачках четырёхкулачных патронов твёрдость резьбы должна быть в пределах Rс = 35-42. Отпуск кулачков из стали 45 производится при температуре 220-280°, из стали 40Х при 380-450° в течение 30-40 мин.
Расшифровка марки стали 45: марка 45 означает, что в стали содержится 0,45% углерода,C 0,42 - 0,5; Si 0,17 - 0,37;Mn 0,5 - 0,8; Ni до 0,25; S до 0,04; P до 0,035; Cr до 0,25; Cu до 0,25; As до 0,08.
Термообработка стали 40Х
Термообработка стали 40Х - легированная конструкционная сталь предназначена для деталей повышенной прочности такие как оси, валы, вал-шестерни, плунжеры, штоки, коленчатые и кулачковые валы, кольца, шпиндели, оправки, рейки, губчатые венцы, болты, полуоси, втулки и прочих деталей повышенной прочности. Сталь 40Х также часто используется для производства поковок, штампованных заготовок и деталей трубопроводной арматуры. Однако последние перечисленные детали нуждаются в дополнительной термической обработке, заключающейся в закалке через воду в масле или просто в масле с последующим отпуском в масле или на воздухе.
Расшифровка марки стали 40Х. Цифра 40 указывает на то, что углерод в стали содержится в объеме 0,4 %. Хрома содержится менее 1,5 %. Помимо обычных примесей в своем составе имеет в определенных количествах специально вводимые элементы, которые призваны обеспечить специально заданные свойства. В качестве легирующего элемента в данном случае используется хром, о чем говорит соответствующая маркировка.
Термообработка стали 20
Термообработка стали 20 - сталь конструкционная углеродистая качественная. Широкое применение в котлостроении, для труб и нагревательных трубопроводов различного назначения, кроме того промышленность выпускает пруток, лист. Температура начала ковки стали 20 составляет 1280° С, окончания - 750° С, охлаждение поковки - воздушное. Сталь 20 нефлокеночувствительна и не склонна к отпускной способности.После цементации и цианирования из стали 20 можно изготавливать детали, от которых требуется высокая твёрдость поверхности и допускается невысокая прочность сердцевины: кулачковые валики, крепёжные детали, шпиндели, звёздочки, шпильки, вилки тяг и валики переключения передач, толкатели клапанов, валики масляных насосов. Сталь 20 применяют для производства малонагруженных деталей ( пальцы, оси, копиры, упоры, шестерни ), цементуемых деталей для длительной и весьма длительной службы (эксплуатация при температуре не выше 350° С), тонких деталей, работающих на истирание и другие детали автотракторного и сельскохозяйственного машиностроения.
Термообработка стали 30хгса
Термообработка стали 30хгса - относится к среднелегированной конструкционной стали. Сталь 30хгса проходит улучшение – закалку с последующим высоким отпуском при 550-600 °С, поэтому применяется при создании улучшаемых деталей (кроме авиационных деталей это могут быть различные корпуса обшивки, оси и валы, лопатки компрессорных машин, которые эксплуатируются при 400°С, и многое другое), рычаги, толкатели, ответственные сварные конструкции, работающие при знакопеременных нагрузках, крепежные детали, работающие при низких температурах.Сталь 30хгса обладает хорошей выносливостью, отличными показателями ударной вязкости, высокой прочностью. Она также отличается замечательной свариваемостью.
Сварка стали 30хгса тоже имеет свои особенности. Она осуществляется с предварительным подогревом материала до 250-300 °С с последующим медленным охлаждением. Данная процедура очень важна, поскольку могут появиться трещины из-за чувствительности стали к резким перепадам температуры после сварки. Поэтому по завершении сварных работ горелка должна отводиться медленно, при этом осуществляя подогрев материала на расстоянии 20-40 мм от места сварки. Также, не более, чем спустя 8 часов по завершении сварки сварные узлы стали 30ХГСА нуждаются в закалке с нагревом до 880 °С с последующим высоким отпуском. Далее изделие охлаждается в масле при 20-50 °С. Отпуск осуществляется нагревом до 400 - 600 °С и охлаждением в горячей воде. Сварку же необходимо выполнять максимально быстро, дабы избежать выгорания легирующих элементов.После прохождения термомеханической низкотемпературной обработки сталь 30хгса приобретает предел прочности до 2800 МПа, ударная вязкость повышается в два раза (в отличии от обычной термообработки стали 30хгса), пластичность увеличивается.
Термообработка стали 65г
Термообработка стали 65г - Сталь конструкционная рессорно-пружинная. Используют в промышленности пружины, рессоры, упорные шайбы, тормозные ленты, фрикционные диски, шестерни, фланцы, корпусы подшипников, зажимные и подающие цанги и другие детали, к которым предъявляются требования повышенной износостойкости, и детали, работающие без ударных нагрузок. (заменители: 70, У8А, 70Г, 60С2А, 9ХС, 50ХФА, 60С2, 55С2).
Термообработка стали 40 - Сталь конструкционная углеродистая качественная. Использование в промышленности: трубы, поковки, крепежные детали, валы, диски, роторы, фланцы, зубчатые колеса, втулки для длительной и весьма длительной службы при температурах до 425 град.
Термообработка стали 40хн - Сталь конструкционная легированная Использование в промышленности: оси, валы, шатуны, зубчатые колеса, валы экскаваторов, муфты, валы-шестерни, шпиндели, болты, рычаги, штоки, цилиндры и другие ответственные нагруженные детали, подвергающиеся вибрационным и динами ческим нагрузкам, к которым предъявляются требования повышенной прочности и вязкости. Валки рельсобалочных и крупносортных станов для горячей прокатки металла.
Термообработка сталь 35 - Сталь конструкционная углеродистая качественная. Использование в промышленности: детали невысокой прочности, испытывающие небольшие напряжения: оси, цилиндры, коленчатые валы, шатуны, шпиндели, звездочки, тяги, ободы, траверсы, валы, бандажи, диски и другие детали.
Термообработка стали 20Х13 - Сталь коррозионно-стойкая жаропрочная. Использование в промышленности: энергетическое машиностроение и печестроение; турбинные лопатки, болты, гайки, арматура крекинг-установок с длительным сроком службы при температурах до 500 град; сталь мартенситного класса Сталь марки 20Х13 и другие стали мартенситного класса: жаропрочные хромистые стали мартенситного класса применяют в различных энергетических установках, они работают при температуре до 600° С. Из них изготовляют роторы, диски и лопатки турбин, в последнее время их используют для кольцевых деталей больших толщин. Существует большое количество марок сталей данного класса. Общим для всех является пониженное содержание хрома, наличие молибдена, ванадия и вольфрама. Они эффективно упрочняются обычными методами термообработки, которая основана на у - a-превращении и предусматривает получение в структуре мартенсита с последующим улучшением в зависимости от требований технических условий. (заменители: 12Х13, 14Х17Н2)
xn--80aafddgcctbhpvrdabo8b4bh1e8f.xn--p1ai
Вопрос к опытным в мехобработке
Sergey13 21-02-2006 11:57Хочу изготовить новые болт и винты крепления ложи к ствольной коробке. Посоветуйте сталь и величину закалки в HRC. Спасибо.
tex 21-02-2006 12:57Сталь 50, закалка до 40-50 HRc. У тебя есть откуда брать такое
Counter-Striker 21-02-2006 13:02Можно из стали 45 тоже. А вообще неважно. Эти болты не затягиваются большими моментами и особых нагрузок не несут.
Sergey13 21-02-2006 13:12quote:Originally posted by tex:Сталь 50, закалка до 40-50 HRc. У тебя есть откуда брать такое Есть. Спасибо, пошел чертить.Serjant 21-02-2006 14:21Здря. я бы лучше Сталь 30 или 35 взял бы. 45 при калке ведёт сильно. 35...38 HRC достаточно для втулок. На винты поболе твёрдости. 40..45 HRC
Sergey13 21-02-2006 17:49А это пусть потом шлифовщик ...ся.
Зуб 21-02-2006 21:38Сталь 45,40Х. Закалка: нагрев до 840 Цельсия охлождение масло.Отпуск 450 Цельсия, охладить на воздухе или в масле значения не имеет.С Уважением.
Valent 22-02-2006 02:45Лучше остановится на 40Х или 40ХС, 38ХС. Если термист грамотный, то закалку производит на мартенсит и уж потом при помощи отпуска получает любую структуру. Так вот, Ст.45 в виду отсутствия в достаточных кол-вах легирующих элементов, калят на воду, для того чтобы получить высокую скорость охлаждения необходимую для получения мартенсита. Из-за этого деталь из Ст.45 ведёт. При наличии легирующих элементов, в Ст.40Х это хром, для получения мартенсита нужна меньшая скорость охлаждения и калят её по этой причине не на воду, а на масло. По этим причинам Ст.40Х более правильный выбор. Твёрдость в 38-40 HRC будет оптимальна. Единственно 40Х склонна к отпускной хрупкости и термисту лучше напомнить об этом чтобы он деталь не передержал или не оставил остывать вместе с печью. Иначе всех достоинств, которые даёт хром, можно лишится.
errrero 22-02-2006 15:05quote:Originally posted by Зуб:Сталь 45,40Х. Закалка: нагрев до 840 Цельсия охлождение масло.Отпуск 450 Цельсия, охладить на воздухе или в масле значения не имеет.С Уважением.Оптимальный режим и вариант.
Sergey13 22-02-2006 15:44А 40x нормально воронится?
errrero 22-02-2006 16:12quote:Originally posted by Sergey13:А 40x нормально воронится?Нормально.
Трофимыч 22-02-2006 17:05Может и мне подскажете - собираюсь делать кронштейн тигровый уже доделываю деталировку, боязнь одна, чтобы не утащило посли термички(сталь 45). Может есть какой совет конкретный по данному вопросу?С Уважением. Олег
P.S. С наступающим праздником, счастливых выходных!
errrero 22-02-2006 17:12quote:Originally posted by Трофимыч:Может и мне подскажете - собираюсь делать кронштейн тигровый уже доделываю деталировку, боязнь одна, чтобы не утащило посли термички(сталь 45). Может есть какой совет конкретный по данному вопросу?С Уважением. ОлегP.S. С наступающим праздником, счастливых выходных!
Не утащит. Поводка конечно будет, но это не страшно, отрихтуете потом и припилите. Отпуск при 400 - 450 минут 40-60.
Трофимыч 22-02-2006 17:42Думаю поднять ее едениц до 50-55, как ее потом рихтовать. Может сделать оправку для крона(важно сохранить заданную линейность м-ду ластохвостом и осью полуколец)
errrero 22-02-2006 18:49quote:Originally posted by Трофимыч:Думаю поднять ее едениц до 50-55, как ее потом рихтовать. Может сделать оправку для крона(важно сохранить заданную линейность м-ду ластохвостом и осью полуколец)Зачем такая твердость? Достаточно 28 - 32 HRC.Оправку поведет еще сильнее, чем крон. Не морочьте себе голову.
Трофимыч 22-02-2006 19:25Олег добрый день.Хотел сбросить в П.М. но не нашел.Знаниями по термообработке и металловедению обладаю на абсолютно дилетанском уровне, поэтому возможно и погорячился, но ведь потому за советом и обращаюсь. Если не составит труда может скину эскизы и поможете более менее с технологией
С Уважением Олег
errrero 23-02-2006 02:53quote:Originally posted by Трофимыч:Олег добрый день.Хотел сбросить в П.М. но не нашел.Знаниями по термообработке и металловедению обладаю на абсолютно дилетанском уровне, поэтому возможно и погорячился, но ведь потому за советом и обращаюсь. Если не составит труда может скину эскизы и поможете более менее с технологиейС Уважением Олег
Олег, Вам мой e-mal нужен?
Трофимыч 23-02-2006 17:10Ну да, если не затруднит. Я хотел бы пообщаться с понимающим человеком и получить ответы на свои вопросы, а на форуме опять в баян все превратится.
С Уважением Олег
Трофимыч 23-02-2006 17:12О Олег извиняюсь. Заглянул только на почту там все есть. Сейчас привезу эскизы с работы, отсканю и вопросы напишуОлег
Sergey13 23-02-2006 17:26quote:Originally posted by Трофимыч: Я хотел бы пообщаться с понимающим человеком и получить ответы на свои вопросы, а на форуме опять в баян все превратится.С Уважением Олег
Довольно обидны слова ваши... И напрасно вы его прелесным ругаете...Трофимыч 23-02-2006 19:132 Сергей
Язык мой-враг мой (иногда)
guns.allzip.org
№п/п | Наименование | Варианты исполнения |
1 | Звезда ведущая АТ 01.01.120Звезда шнековая 2086.01.07.020-01Применяются на грунторезах 2086.31.000,2085.00.000,2087.00.00,агрегате траншейномАТ-00.00.000 | 1.Две сваренные цельнокованые половинки. Сталь 40Х.Шлицы выполнены протяжкой.Сварочный шов проходит по середине горизонтальной проекции изделия. Твердость после закалки 35-40 HRC.2. Две фрезерованные из лист заготовки приварены по краям выполненной из кругляка середины. Сталь 40Х. Шлицы выполнены долблением. Сварочные швы проходят по краям горизонтальной проекции изделия. Твердость после закалки 40-45 HRC.3. Две фрезерованные из листа заготовки приварены по краям выполненной из крягляка середины. Сталь 40Х. Шлицы выполнены долблением. Сварочные швы прохдят по краям горизонтальной проекции изделия. Твердость после закалки 40-45 HRC.После закалки по рабочим кромкам звезды наваривается твердосплавное покрытие твердостью 55-60 HRC. |
2 | Звезда ведущая 39.04.000.Применяется на ЭТЦ-1609 БД, ТКЦ-165,ЭЦУ-150 с зимним органом. | 1.Две цельнокованые половинки. Сталь 40Х. Твердость после закалки 35-40 HRC.2.Фрезерованные из листа заготовки приварены по краям выполненные из кругляка середины. Сталь 40Х. Твердость после закалки 40-45 HRC.3.Фрезерованные из листа заготовки приварены по краям выполненной из кругляка середины. Сталь 40Х. Твердость после закалки 40-45 HRC. После закалки по кромкам звезды наваривается твердосплавное покрытие твердостью 55-60 HRC. |
3 | Звезда ведущая 004.900.020 (шаг 100мм.).применяется на ЭТЦ-1609, ТКЦ-165, ЭЦУ-150 с летним и универсальным органом. | 1.Цельнолитая заготовка.Фрезеровка.Сталь 40ХЛ. Твердость после закалки 35-40 HRC.2.Цельнофрезерованная из кругляка. Сталь 45. Твердость после закалки 40-45 HRC.3. Фрезерованная/отплазменная из толстого листа заготовка приварена по центру выполненной из кругляка середины. Сталь 40Х. тврдость после закалки 40-45 HRC. |
4 | Звезда ведомая 32.03.004 (11 зубов,шаг 100мм).Звезда ведомая 165А.32.05СБ/УКИС(8 зубов,шаг 100мм).Применяются на ЭТЦ-1609, ТКЦ-165, ЭЦУ-150 с летним и универсальным органом. | 1.Цельнолитая заготовка. Фрезеровка.Сталь 40Х. Твердость после закалки 35-40 HRC.2. Цельнофрезерованная из кругляка. Сталь 45. Твердость после закалки 40-45 HRC.3.Фрезерованная/отплазменная из толстого листа заготовка приварена по центру выполненной их кругляа середины. Сталь 40Х. Твердость после закалки 40-45 HRC. |
5 | Цепи режущие 20.00.000, 21.00.000,22.00.000 (шаг 100 мм.,ширина 200,270,400 мм.).Применяется на ЭТЦ-1609, ТКЦ-165, ЭЦУ-150 с летним органом. | 1.Скребки выполнены из листа шириной 14 мм. Щека выполнены из листа 10мм. Сталь 40Х.Форма краев щек-трапецевидная.Твердость щек 35-40 HRC.Твердость скребков 30-35 HRC.2.Скребки выполнены из стали 40Х толщиной 16мм. Щеки выполнены из листа 10мм. Сталь 40Х. Форма краев щек-овальная. Твердость щек и скребков 40-45 HRC.3. Скребки выполнены из стали 40Х толщиной 16мм. Щеки цепи выполнены из листа 10мм. Сталь 40Х. форма краев щек-овальная.Твердость щек и скребков 40-45 HRC. Помле закалки по рабоичм кромкам скребков наваривается твердосплавное покрытие твердостью 55-60 HRC. |
6 | Цепь режущая универсальная 38.00.000 (шаг 100мм,ширина 210мм.)Применяется на ЭТЦ-1609, ТКЦ-165, ЭЦУ-150 с летним и универсальным органом. | 1.Щеки,ролики,втулки,перемычки выполнены из стали 45. Держатели резцов из стали 3СП.Твердость закаленных деталей 35-40 HRC.2.Щеки,ролики,втулки,перемычки выполнены из стали 40Х. Держатели резцов из стали 3СП.Твердость закаленных деталей 40-45 HRC.3.Щеки,ролики,втулки,перемычки выполнены из стали 40Х.Оси цепи и держатели резцов из стали 38ХН.Твердость всех деталей 42-48 HRC. |
7 | Натяжное устройство зимнее.Применяется на ЭТЦ-1609 БД, ТКЦ-165, ЭЦУ-150 с зимним органом, грунторез 2086.31.000, агрегате траншейном АТ-00.00.000.Все устройства полностью взаимозаменяемы. | 1.Головка бара У33.20.25.000-01. По бокам рамы установлены две звездочки диаметром 315 мм. Звездочки крепятся друг к другу спецболтом через раму.2.Натяжное устройство 39.03.000. По бокам рамы приварены неподвижные диски диаметром 450мм., между дисков по центру установлен ролик диаметром 315 мм.3.Натяжное устройство рабочего органа "Бара" в сборе.Рама выполнена в виде двухзубой вилки, между зубьями которой установлен круглый ролик диаметром 315 мм. |
chzgt.3dn.ru
Лекция 19
Инструментальные стали
-
Стали для режущего инструмента.
-
Углеродистые инструментальные стали (ГОСТ 1435).
-
Легированные инструментальные стали.
-
Быстрорежущие стали.
-
Стали для измерительных инструментов.
-
Штамповые стали.
-
Стали для штампов холодного деформирования.
-
Стали для штампов горячего деформирования.
-
Твердые сплавы.
-
Алмаз как материал для изготовления инструментов.
Стали для режущего инструмента.
Инструментальная сталь должна обладать высокой твердостью, износостойкостью, достаточной прочностью и вязкостью (для инструментов ударного действия).
Режущие кромки могут нагреваться до температуры 500 900oС, поэтому важным свойством является теплостойкость, т. е., cпособность сохранять высокую твердость и режущую способность при продолжительном нагреве (красностойкость).
Углеродистые инструментальные стали (ГОСТ 1435).
Содержат 0,65 1,35% углерода.
Стали У7 У13А обладают высокой твердостью, хорошо шлифуются, дешевы и недефицитны.
Из сталей марок У7, У8А изготавливают инструмент для работы по дереву и инструмент ударного действия, когда требуется повышенная вязкость пуансоны, зубила, штампы, молотки.
Стали марок У9 У12 обладают более высокой твердостью и износостойкостью используются для изготовления сверл, метчиков, фрез.
Сталь У13 обладает максимальной твердостью, используется для изготовления напильников, граверного инструмента.
Для снижения твердости и создания благоприятной структуры, все инструментальные стали до изготовления инструмента подвергают отжигу.
Для заэвтектоидных сталей проводят сфероидизирующий отжиг, в результате которого цементит вторичный приобретает зернистую форму. Регулируя скорость охлаждения можно получить любой размер зерен.
Окончательная термическая обработка закалка с последующим отпуском.
Закалку для доэвтектоидных сталей проводят полную, а для заэвтектоидных неполную. Структура закаленных сталей или мартенсит, или мартенсит и карбиды.
Температура отпуска выбирается в зависимости от твердости, необходимой для инструмента.
Для инструментов ударного действия, требующих повышенной вязкости, из сталей У7, У8 отпуск проводят при температуре 280 300oС, что обеспечивает твердость HRC 56 58.
Для напильников, метчиков, плашек отпуск проводят при температуре 150 200oС, при этом обеспечивается получение максимальной твердости НRC 62 64.
Основными недостатками углеродистых инструментальных сталей является их невысокая прокаливаемость (5 10 мм), низкая теплостойкость (до 200oС), то есть инструменты могут работать только при невысоких скоростях резания.
Легированные инструментальные стали.
Содержат 0,9 1,4 % углерода. В качестве легирующих элементов содержат хром, вольфрам, ванадий, марганец, кремний и другие. Общее содержание легирующих элементов до 5%.
Высокая твердость и износостойкость в основном определяются высоким содержанием углерода. Легирование используется для повышения закаливаемости и прокаливаемости, сохранения мелкого зерна, повыщения прочности и вязкости.
Термическая обработка включает закалку и отпуск.
Проводят закалку с температуры 800 850oС в масло или ступенчатую закалку, что уменьшает возможность коробления и образования закалочных трещин.
Отпуск проводят низкотемпературный, при температуре 150 200oС, что обеспечивает твердость HRC 61 66. Иногда, для увеличения вязкости, температуру отпуска увеличивают до 300oС, но при этом наблюдается снижение твердости HRC 55 60.
Для деревообрабатывающего инструмента из сталей 6ХС и 9ХФ рекомендуется изотермическая закалка, значительно улучшающая вязкость.
Повышенное содержание кремния (сталь 9ХС) способствует увеличению прокаливаемости до 40 мм и повышению устойчивости мартенсита при отпуске. Недостатками сталей, содержащих кремний, являются чувствительность их к обезуглероживанию при термообработке, плохая обрабатываемость резанием и деформированием из-за упрочнения феррита кремнием.
Повышенное содержание марганца (стали ХВГ, 9ХВСГ) способствует увеличению количества остаточного аустенита, что уменьшает деформацию инструмента при закалке. Это особенно важно для инструмента, имеющего большую длину при малом диаметре, например, протяжек.
Хром увеличивает прокаливаемость и твердость после закалки.
Стали используются для изготовления инструмента и ударного, и режущего.
Алмазная сталь ХВ5 содержит 5% вольфрама. Благодаря присутствию вольфрама, в термически обработанном состоянии имеет избыточную мелкодисперсную карбидную фазу. Твердость составляет HRC 65 67. Cталь используется для изготовления инструмента, сохраняющего длительное время острую режущую кромку и высокую размерную точность (развертки, фасонные резцы, граверный инструмент).
Быстрорежущие стали.
Стали получили свое название за свойства. В следствии высокой теплостойкости (550 650oС), изготовленные из них инструменты могут работать с достаточно высокими скоростями резания.
Стали содержат 0,7 1,5 % углерода, до 18 % основного легирующего элемента вольфрама, до 5 % хрома и молибдена, до 10 % кобальта
Добавление ванадия повышает износостойкость инструмента, но ухудшает щлифуемость. Кобальт повышает теплостойкость до 650oС и вторичную твердость HRC 67 70.
Микроструктура быстрорежущей стали в литом состоянии имеет эвтектическую структурную составляющую. Для получения оптимальных свойств инструментов из быстрорежущей стали необходимо по возможности устранить структурную неоднородность стали карбидную ликвацию. Для этого слитки из быстрорежущей стали подвергаются интенсивной пластической деформации (ковке). При этом происходит дробление карбидов эвтектики и достигается более однородное распределение карбидов по сечению заготовки.
Затем проводят отхиг стали при температуре 860 900oС. Структура отожженной быстрорежущей стали мелкозернистый (сорбитообразный) перлит и карбиды, мелкие эвтектоидные и более крупные первичные. Количество карбидов около 25 %. Сталь с такой структурой хорошо обрабатывается резанием. Подавляющее количество легирующих элементов находятся в карбидной фазе. Для получения оптимальных свойств стали в готовом инструменте необходимо при термической обработке обеспечить максимальное насыщение мартенсита легирующими элементами. При закалке быстрорежущие стали требуют нагрева до очень высоких температур, около 1280oС. Нагрев осуществляют в хорошо раскисленных соляных ваннах BaCl2/, что улучшает равномерность прогрева и снижает возможность обезуглероживания поверхности. Для снижения термических фазовых напряжений нагрев осуществляют ступенчато: замедляют нагрев при температурах 600 650oС и при 850 900oС. График режима термической обработки быстрорежущей стали представлен на рис. 19.1.
Рис.19.1. График режима термической обработки быстрорежущей стали
Охлаждение от закалочной температуры производится в масле. Структура стали после закалки состоит из легированного, очень тонкодисперсного мартенсита, значительного количества (30 40 %) остаточного аустенита и карбидов вольфрама. Твердость составляет 60 62 HRC. Наличие аустенита остаточного в структуре закаленной стали ухудшает режущие свойства.
Для максимального удаления аустенита остаточного проводят трехкратный отпуск при температуре 560oС. При нагреве под отпуск выше 400oС наблюдается увеличение твердости. Это объясняется тем, что из легированного остаточного аустенита выделяются легированные карбиды. Аустенит при охлаждении от температуры отпуска превращается в мартенсит отпуска, что вызывает прирост твердости. Увеличению твердости содействуют и выделившиеся при температуре отпуска мелкодисперсные карбиды легирующих элементов. Максимальная твердость достигается при температуре отпуска 560oС.
После однократного отпуска количество аустенита остаточного снижается до 10%. Чтобы уменьшить его количество до минимума, необходим трехкратный отпуск.
Твердость стали после отпуска составляет 64 65 HRC. Структура стали после термообработки состоит из мартенсита отпуска и карбидов.
При термической обработке быстрорежущих сталей применяют обработку холодом. После закалки сталь охлаждают до температуры 80 100oС, после этого проводят однократный отпуск при температуре 560oС для снятия напряжений.
Иногда для повышения износостойкости быстрорежущих сталей применяют низкотемпературное цианирование.
Основными видами рехущих инструментов из быстрорежущей стали являются резцы, сверла, долбяки, протяжки, метчики машинные, ножи для резки бумаги. Часто из быстрорежущей стали изготавливают только рабочую часть инструмента.
Стали для измерительных инструментов.
Основными требованиями, предъявляемыми к сталям, из которых изготавливаются измерительные инструменты, являются высокая твердость и износоустойчивость, стабильность в размерах в течение длительного времени. Последнее требование обеспечивается минимальным температурным коэффициентом линейного расширения и сведением к минимуму структурных превращений во времени.
Для изготовления измерительных инструментов применяются:
-
высокоуглеродистые инструментальные стали, легированные и углеродистые (стали У12, Х, Х9, ХГ), после закалки и стабилизирующего низкотемпературного (120 170 oС ) отпуска в течение 10 30 ч. До отпуска желательно провести обработку холодом. Получают твердость 62 67 HRC;
-
малоуглеродистые стали (сталь 15, 20) после цементации изакалки с низким отпуском;
-
нитралои (сталь 38ХМЮА) после азотирования на высокую твердость
Штамповые стали.
Инструмент, применяемый для обработки металлов давлением (штампы, пуансоны, матрицы) изготавливают из штамповых сталей.
Различают стали для штампов холодного и горячего деформирования.
Стали для штампов холодного деформирования.
Стали должны обладать высокой твердостью, износостойкостью, прочностью, вязкостью (чтобы воспринимать ударные нагрузки), сопротивлением пластическим деформациям.
Для штампов небольших размеров (до 25 мм) используют углеродистые инструментальные стали У10, У11, У12 после закалки и низкого отпуска на твердость 57 59 HRC. Это позволяет получить хорошую износостойкость и ударную вязкость.
Для более крупных изделий применяют легированные стали Х, Х9, Х6ВФ. Для повышения износостойкости инструмента после термической обработки проводят цианирование или хромирование рабочих поверхностей.
Для уменьшения брака при закалке необходимо медленное охлаждение в области температур мартенситного превращения (например, закалка из воды в масло для углеродистых сталей, ступенчатая закалка для легированных сталей).
Если штамповый инструмент испытывает ударные нагрузки, то используют стали, обладающие большей вязкостью (стали 4ХС4, 5ХНМ). Это достигается снижением содержания углерода, введением легирующих элементов и соответствующей термической обработкой. После закалки проводят высокий отпуск при температуре 480 580oС, что обеспечивает твердость 38 45 HRC.
Стали для штампов горячего деформирования.
Дополнительно к общим требованиям, от сталей этой группы требуется устойчивость против образования трещин при многократном нагреве и охлаждении, окалиностойкость, высокая теплопроводность для отвода теплоты от рабочих поверхностей штампа, высокая прокаливаемость для обеспечения высокой прочности по всему сечению инструмента.
Для изготовления молотовых штампов применяют хромоникелевые среднеуглеродистые стали 5ХНМ, 5ХНВ, 4ХСМФ. Вольфрам и молибден добавляют для снижения склонности к отпускной хрупкости. После термической обработки, включающей закалку с температуры 760 820oС и отпуск при 460 540oС, сталь имеет структуру сорбит или троостит и сорбит отпуска. Твердость 40 45 HRC.
Штампы горячего прессования работают в более тяжелых условиях. Для их изготовления применяются стали повышенной теплостойкости. Сталь 3Х2В8Ф сохраняет теплостойкость до 650oС, но наличие карбидов вольфрама снижает вязкость. Сталь 4Х5В2ФС имеет высокую вязкость. Повышенное содержание хрома и кремния значительно увеличивает окалиностойкость стали.
Твердые сплавы.
В качестве материалов для инструментов используются твердые сплавы, которые состоят из твердых карбидов и связующей фазы. Они изготавливаются методами порошковой металлургии.
Характерной особенностью твердых сплавов является очень высокая твердость 87 92 HRC при достаточно высокой прочности. Твердость и прочность зависят от количества связующей фазы (кобальта) и величины зерен карбидов. Чем крупнее зерна карбидов, тем выше прочность. Твердые сплавы отличаются большой износостойкостью и теплостойкостью. Основными твердыми сплавами являются группы ВК (WC + Co), TK (WC + TiC + Co), TTK (WC + TiC + TaC + Co). Наиболее распространенными сплавами группы ВК являются сплавы марок ВК3, ВК6, ВК8, ВК20, где число показывает содержание кобальта в процентах, остальное карбиды вольфрама WC. Сплавы группы ТК марок Т30К6, Т14К8 первое число показывает содержание карбидов титана в процентах, второе содержание кобальта в процентах. Сплаы этой группы лучше противостоят изнашиванию, обладают большей твердостью, тепло- и жаростойкостью, стойкостью к коррозии, но меньшей теплопроводностью и большей хрупкостью. Используются на средних и высоких скоростях резания.
Сплавы с малым количеством кобальта обладают повышенной твердостью и износостойкостью, но минимальной прочностью, Поэтому их используют для чистового точения (ВК3, Т30К4).
Сплавы с повышенным содержанием кобальтаиспользуют для чернового точения (ВК8, Т14К8).
Сплав ВК20 начинают использовать для армирования штампов, что повышает их износостойкость.
Износостойкость инструментов из твердых сплавов превышает износостойкость инструментов из быстрорежущих стале в 10 20 раз и сохраняется до температур 800 1000oС.
Алмаз как материал для изготовления инструментов.
80 % добываемых природных алмазов и все синтетические алмазы используются в качестве инструментальных материалов.
Основное количество алмазов используется в виде алмазного порошка для изготовления алмазно-абразивного инструмента шлифовальных кругов, притиров, хонов, надфилей и др., для обработки особо твердых металлов и горных пород. Большое значение имеют заточные круги для твердосплавного инструмента, это увеличивает производительность труда и срок службы инструмента. Повышение стойкости твердосплавного инструмента обеспечивается высокой чистотой (отсутствие зазубрин, мелких трещин) лезвия инструмента.
Алмазный инструмент изготовляется в виде алмазосодержащих кругов с бакелитовой или металлической связкой.
Также изготавливают алмазные резцы (для обработки корпусов часов), фильеры (для волочения проволоки из высокотвердых и драгоценных металлов) и др.
nwpi-fsap.narod.ru