Для чего нужны гидравлические испытания трубопроводов? Как производится проверка собранного трубопровода
Проверка - трубопровод - Большая Энциклопедия Нефти и Газа, статья, страница 1
Проверка - трубопровод
Cтраница 1
Проверка трубопровода на недопустимые пластические деформации выполняется. [1]
Проверка трубопровода пневмотранспорта на плотность производится при включенных в действие воздуходувных агрегатах или вакуум-насосе с тщательным осмотром всех стыков трубопровода. [3]
Проверку трубопроводов на плотность производят не ранее чем через 24 ч после наполнения водой. [4]
Проверку трубопроводов на герметичность, как правило, следует проводить вместе с оборудованием после проведения монтажа, ремонта и ревизии трубопроводов, запорной арматуры и оборудования. [5]
Проверку телефонного трубопровода производят перед сдачей его в эксплуатацию. После проверки исправности все каналы во избежание засорения и проникновения газов плотно закрывают деревянными или бетонными пробками и обмазывают замазкой. [7]
Необходимость проверки трубопровода на герметичность вызывается тем, что не все дефекты проявляются и обнаруживаются в процессе испытания на прочность. Для выявления малых по размеру дефектов на трубах и стыках ( поры, свищи), а также несплош-ностей конструктивных элементов ( фланцевых, сальниковых и др.) требуются более длительное время испытания и специальная технология при менее опасных условиях производства работ. [9]
При проверке трубопроводов значительной протяженности нужно проверить полный напор. [10]
Существенным недостатком проверки трубопровода на герметичность погружением в ванну являются большие затраты труда на неизбежные подготовительно-заключительные операции. Проверка может быть механизирована, если применить более современные методы обнаружения негерметичности. [11]
Если в отношении проверки трубопроводов на герметичность можно ответить утвердительно, то в отношении других, стоящих перед испытанием задач, дать однозначный ответ невозможно. [12]
Осмотр трассы с делью проверки трубопровода на герметичность следует производить только после снижения испытательного давления до рабочего. [13]
Осмотр трассы с целью проверки трубопровода на герметичность следует производить только после снижения испытательного давления до рабочего. [14]
Гидравлическое испытание проводится с целью проверки трубопровода на прочность и герметичность. В соответствии с требованиями СНиП Ш-42-80 испытания трубопроводов подводных переходов газопроводов, нефте - и продуктопроводов через водные преграды и прилегающие прибрежные участки должны производиться в три этапа. [15]
Страницы: 1 2 3 4
www.ngpedia.ru
Собранный трубопровод - Большая Энциклопедия Нефти и Газа, статья, страница 1
Собранный трубопровод
Cтраница 1
Собранный трубопровод, к которому труба подсоединяется муфтой, необходимо приподнять вагой, подложить под него доски или брусья так, чтобы конец трубопровода был расположен наклонно. Затем на конец трубопровода следует навернуть муфту и после этого в муфту завернуть трубу. [1]
Собранный трубопровод подвергают испытанию давлением, целью которого является проверка прочности и плотности соединений. В зависимости от назначения трубопровод испытывается гидравлическим или пневматическим давлением. [2]
Собранные трубопроводы, сборочные единицы и детали испытывают на прочность и плотность в заготовительном предприятии. Устранение дефектов в трубопроводах, сборочных единицах и деталях, находящихся под давлением, не допускается. Подварка шва на изогнутых участках труб и подчеканка сварных швов также не допускаются. [3]
Полностью собранные трубопроводы присоединяют к контуру защитного заземления не менее чем в двух местах, обычно в начале и конце трубопровода. Работы по электросварке и пайке выполняют до затяжки в трубы проводов и кабелей во избежание их повреждения. [4]
Для собранных трубопроводов пара и горячей воды рпр: 1 2брраб - Таким же давлением испытывают сварные блоки и собранные узлы паропроводов и трубопроводов горячей. При этом для питательных линий ( и водопроводов) за рабочее давление рраб дринимают напор, который создают насосы, когда задвижки закрыты. [5]
В правильно собранных трубопроводах не должно быть переломов в местах стыков. [6]
Гидравлическое испытание собранного трубопровода проводится после окончания всех сварочных работ, термообработки, установки и окончательного закрепления его на постоянных опорах и подвесках. Трубопроводы подвергаются гидравлическому испытанию без наложения изоляции давлением, равным 1 25 рабочего давления. Сосуды, являющиеся неотъемлемой частью трубопровода, испытываются тем же давлением, что и трубопроводы. Для питательных трубопроводов за рабочее давление принимается давление, которое могут развить питательные насосы при закрытых задвижках. [7]
Гидравлическое испытание собранного трубопровода производят после закрепления его на постоянных опорах и подвесках. Трубопроводы из бесшовных труб подвергают гидравлическому испытанию с изоляцией, но с открытыми сварными стыками. Трубопроводы из сварных труб испытывают до наложения изоляции. [8]
Гидравлическое испытание собранного трубопровода производят после закрепления его на постоянных опорах и подьесках. Трубопроводы из бесшовных труб подвергают гидравлическому испытанию с изоляцией, но с открытыми сварными стыками. Трубопроводы из сварных труб испытывают до наложения изоляции. [9]
Гидравлическое испытание собранного трубопровода производят после закрепления его на постоянных опорах и подвесках. Трубопроводы из бесшовных труб подвергают гидравлическому испытанию с изоляцией, но с открытыми сварными стыками. Трубопроводы из сварных труб испытывают до наложения изоляции. [10]
Компенсатор растягивают на собранном трубопроводе, как описано выше ( см. рис. 94), в стыке, удаленном от компенсатора. На трубопроводах с рабочим давлением не более 7 кгс / см2 устанавливают линзовые компенсаторы. [11]
Растяжку производят на собранном трубопроводе и закрепленном на неподвижных опорах. [13]
Не допускается также подгибка труб путем нагрева, врезка в собранные трубопроводы штуцеров и бобышек. [14]
Страницы: 1 2 3
www.ngpedia.ru
Гидравлические испытания трубопроводов: этапы проверок, составление акта
Гидравлические испытания трубопроводов — это комплекс мероприятий, которые могут проводиться на разных этапах эксплуатации трубопроводов, но чаще всего эти испытания выполняются сразу после прокладки коммуникации, перед её запуском. Сети, которые работают под давлением, в обязательном порядке должны проверяться (в соответствии с положениями СНиП) на различные дефекты. Это нужно для того, чтобы предотвратить возникновение аварийной ситуации.
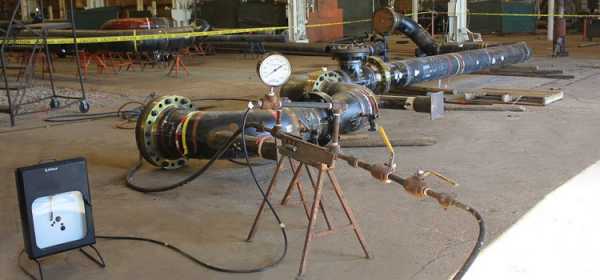
Гидравлические испытания — это проверка состояния и работоспособности магистрали при помощи давления, превышающего рабочее
Для чего проводят гидравлические испытания?
Во время гидравлических испытаний определяется прочность и герметичность конструкции, также определяется её объём. Подобные проверки проходят все виды трубопроводов на разных эксплуатационных этапах.
Существует три варианта, когда гидравлические проверки выполняются в обязательном порядке, независимо от направленности коммуникации:
- в процессе производства труб в обязательном порядке проводится проверка на качество. Также соответствующие испытания проходят прочие комплектующие к трубопроводам;
- испытание трубопроводов также производится во время эксплуатации в профилактических целях.
Такие испытания способны выявить определённые несоответствия труб или комплектующих к ним со стандартами качества, прописанными в законах. Проведение проверочных мероприятий является необходимым пунктом эксплуатации оборудования, работающего под давлением.
Как правило, процедура проверки включает в себя несколько важных пунктов. Для гидравлического испытания создают экстремальные условия, чтобы точно определить надёжность трубопроводной магистрали. Проверочное давление в таком случае может быть больше обычного в 1,25–1,5 раза.
Особенности гидравлических испытаний
Проверочное давление нагнетается в трубопровод медленно и плавно, чтобы не вызвать гидроудар или не создать другую аварийную ситуацию. Показатели давления, как уже было сказано выше, превышают стандартные эксплуатационные нормы.
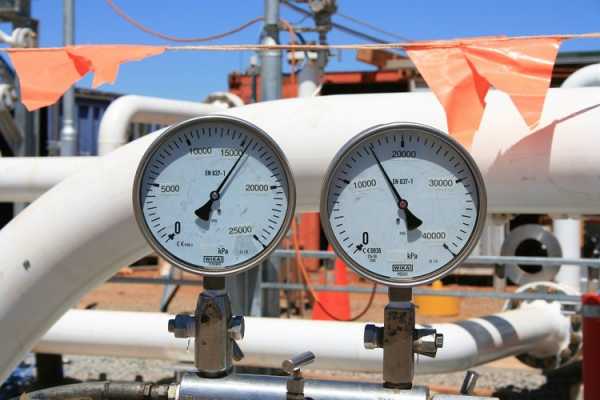
Оборудование для испытаний комплектуется приборами, позволяющими контролировать давление в системе
Сила подачи жидкости фиксируется на измерительных приборах (манометрах), поэтому можно осуществлять контроль и регулировать процесс. По СНиП, подача жидкости сопровождается скоплением газа в разных точках коммуникации. Это очень важный момент, который необходимо контролировать, чтобы избежать непредвиденных ситуаций.
После наполнения трубопроводной конструкции водой оборудование находится под повышенным, проверочным давлением. Этот период называют временем выдержки.
Важно! Существует одно важное правило — во время выдержки оборудования необходимо исключить возможность скачков проверочного давления. Показатели проверочного давления должны быть неизменными.
По окончании выдержки производится работа по снижению давления до обычных показателей. Во время проверки запрещается находиться кому-либо в непосредственной близости от испытуемого трубопровода. Рабочий персонал располагается в безопасном месте.
Когда гидравлическое испытание проведено, производится осмотр коммуникации на наличие повреждений и оценка полученной информации в соответствии со СНиП.
В каких условиях необходимо проводить гидравлическую проверку трубопроводов?
Гидравлические испытания трубопроводов являются сложным мероприятиям, которое требует определённой подготовки. Испытания должны соответствовать строительным нормам и правилам, поэтому такие проверки производят только высококвалифицированные специалисты.
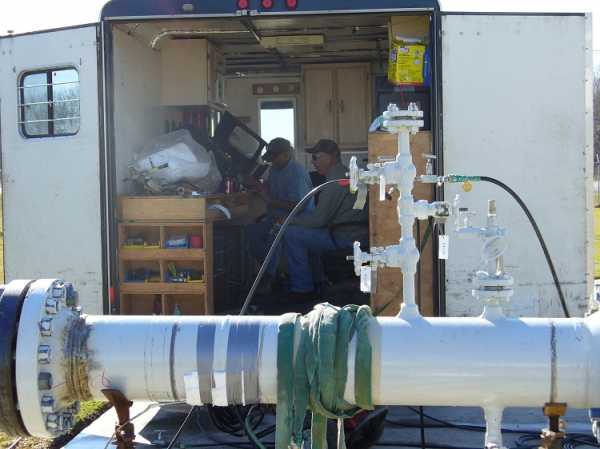
Испытания проводятся строго по принятым нормам и правилам и к процессом руководят специалисты
Для проведения такой проверки трубопроводной магистрали необходимо придерживаться следующих условий:
- точки пользования в стояке активизируются одновременно для испытания, однако, это положение не всегда является обязательным и определяется индивидуально в зависимости от конкретного случая;
- характеристики устройств для сушки полотенец проверяются при испытании систем горячего водоснабжения;
- температурные замеры выполняются только по крайним точкам в конструкции;
- после проведения испытательных работ необходимо полностью удалить воду из системы;
- наполнение коммуникации производится снизу вверх. Такое правило необходимо для правильного вытеснения воздуха и позволяет избежать аварийных ситуаций, связанных с переизбытком давления, а также воздушных пробок.
- начальный этап по заполнению коммуникации относится только к главному стояку, и только на следующих этапах производится наполнение стояков, ответвляющихся от главного.
- во время гидравлических испытаний температура окружающей среды не должна быть ниже, чем +5 °C.
Эти условия должны быть соблюдены независимо от типа трубопровода и рабочей среды, которую он транспортирует.
Гидравлические проверки проводят для следующего оборудования:
- внутренних пожарных водопроводов;
- систем горячего и холодного водоснабжения;
- отопительных систем.
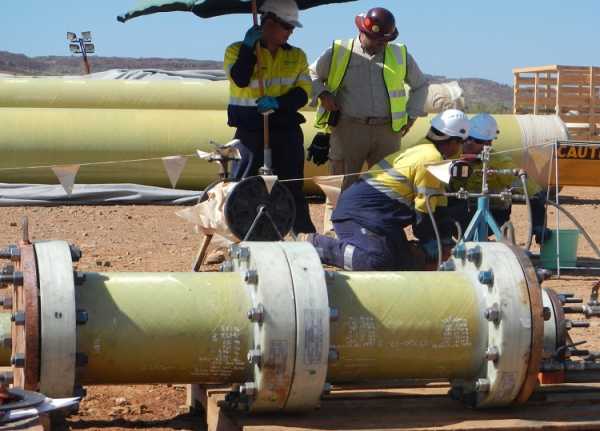
Испытаниям подвергаются разные типы трубопроводов, в том числе отопительные и сети ГВС
Последовательность проведения работ
Мероприятия по гидравлической проверке выполняются в определённой последовательности. Рассмотрим основные этапы этого процесса:
- Очистка трубопроводной сети.
- Монтаж кранов, заглушек и измерительного оборудования (манометров).
- Подключение воды и гидравлического пресса.
- Наполнение коммуникации водой до нужного уровня.
- Проверка трубопроводной конструкции на наличие повреждений (деформированные места отмечаются).
- Ремонт проблемных участков.
- Выполнение повторной проверки.
- Отключение от трубопровода и удаление жидкости из системы.
- Демонтаж кранов, заглушек и манометров.
Все эти манипуляции необходимо производить в соответствии со строительными нормами и правилами, чтобы исключить халатность и аварийные ситуации.
Подготовительные работы
Перед проведением гидравлических испытаний обязательно нужно выполнить ряд подготовительных этапов. Рассмотрим последовательность проведения подготовительных работ:
- Трубопровод разделяют на условные части.
- Производится поверхностный визуальный осмотр коммуникации.
- Выполняется проверка технической документации.
- На конструкцию фиксируют в (местах условных делений) вентили, а также необходимые заглушки.
- К прессовочным аппаратам и наполнителям присоединяется временная коммуникация.
- Испытуемый участок отключают от магистрали и оборудуют необходимой запорной арматурой (заглушками).
- Далее испытуемый сегмент трубопровода отключают от оборудования.
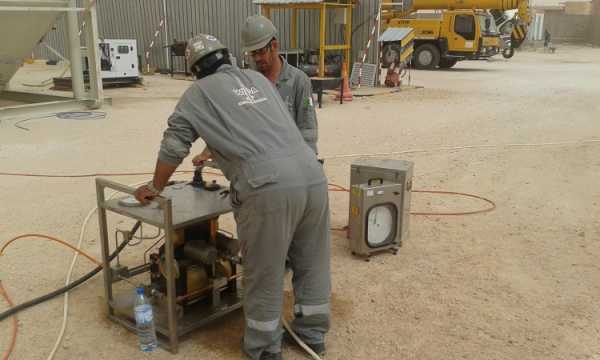
Для работ используют оборудование для увеличения давления в трубах — насосы, компрессоры и прочие приборы
Важно! Категорически запрещается оборудование испытуемого участка коммуникации запорной арматурой того же трубопровода.
Для проверки показателей прочности трубопроводной конструкции её подключают к различной гидравлической аппаратуре (компрессорам, насосным станциям и т. д.), которая способна создавать необходимое давление в трубопроводе на расстоянии двух вентилей.
Испытания на прочность и герметичность
Предварительную проверку коммуникации на прочность и показатели герметичности проводят в такой последовательности:
Проверка прочности. Для этого в трубопроводе создают проверочное, усиленное давление и выдерживают его около 10 минут. Как уже было сказано выше, во время выдержки нельзя допускать, чтобы давление понижалось. Как правило, проверка нарушается, если давление понижается более чем на 0,1 МПа. По истечению времени проверочное давление понижают до стандартных показателей и поддерживают их с помощью непрерывной подкачки жидкости. После этого выполняется осмотр конструкции, который направлен на выявление повреждений. Если дефекты не обнаружены — выполняется второе испытание на прочность. При обнаружении деформаций в трубопроводной конструкции — их устраняют и проводят повторное испытание. Отдельные части трубопроводной коммуникации проверяются в разное время. Продолжительность гидравлической проверки не может быть меньше, чем 10 минут.
Проверка на герметичность. После того, как коммуникация прошла испытания на прочность, производится проверка на герметичность трубопровода. Герметичность проверяется так:
- Производится фиксация времени начала проверки.
- В измерительном бачке определяется начальный уровень жидкости.
- Когда первые два пункта выполнены, начинается наблюдение за уменьшением показателя давления в конструкции.
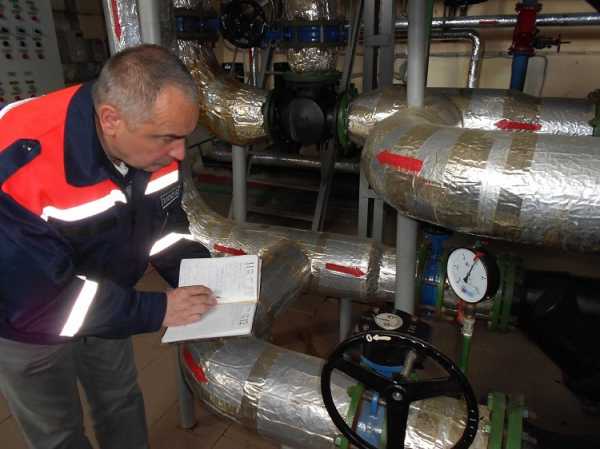
Во время испытания необходим строгий контроль давления, его показатель не должен меняться весь период выдержки
При гидравлических испытаниях трубопроводов необходимо чётко следовать этой последовательности.
Определение дополнительного объёма воды
После выполнения проверки на герметичность, как правило, следует расчёт дополнительного объёма жидкости в системе. Этот процесс проходит в такой последовательности:
- Уровень давления в конструкции снова увеличивают за счёт подкачки жидкости из измерительного бачка. Показатель давления должен быть таким же, как и при гидравлической проверке, то есть превышать стандартные показатели в 1,25–1,5 раза.
- Время, когда закончилась проверка на герметичность, необходимо запомнить.
- На третьем этапе производится замер конечного уровня воды в измерительном бачке.
- Далее определяется временной отрезок, который заняла проверка коммуникации (в минутах).
- Расчет объёма жидкости, подкачанной из измерительного бачка (для 1 случая).
- Высчитывание разницу между подкачанной и удалённой из трубопровода жидкости (для 2 случая).
- Вычисление фактической траты дополнительно закачанной жидкости по формуле: qn=Q/(Tk-Tn).
Составление акта
После проведения гидравлических испытаний необходимо составить акт, указывающий, что проверки проходили с учётом строительных норм и правил, а также содержащий отчёт о том, что трубопроводная конструкция выдержала их. Этот документ составляется инспектором.
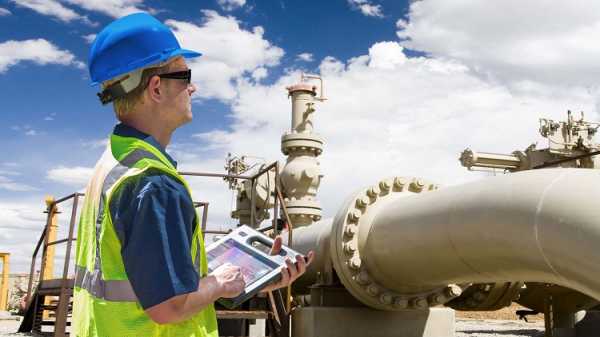
По результатам испытаний составляется акт, который подтверждает исправность трубопровода и безопасность его эксплуатации
Акт, в обязательном порядке, должен включать в себя следующие позиции:
- название трубопровода;
- наименование компании, которая осуществляет технадзор;
- необходимые данные, повествующие о показателях проверочного давления и длительности испытаний;
- данные об уменьшении давления;
- описание дефектов, выявленных при проверке или же запись об их отсутствии.
- дату испытаний;
- заключение комиссии.
Гидравлические проверки могут проводиться двумя способами:
- Манометрический. Проверка проходит с использованием специальных измерительных приборов. Они фиксируют показатели давления во время всех испытательных манипуляций.
Манометрический способ проверки трубопровода позволяет инспектору произвести необходимые расчёты и вымерять давление в конструкции во время тестирования.
- Гидростатический. Проверка таким методом показывает, как именно поведёт себя коммуникация в нестандартных эксплуатационных условиях (при повышенном давлении и т. п.). Такой способ является наиболее популярным.
Испытания внутреннего пожарного водопровода
Готовые и уже эксплуатируемые пожарные водопроводы проверяются посредством создания проверочного давления. Условия для проведения испытания пожарного водопровода, соответствуют гидравлическим условиям.
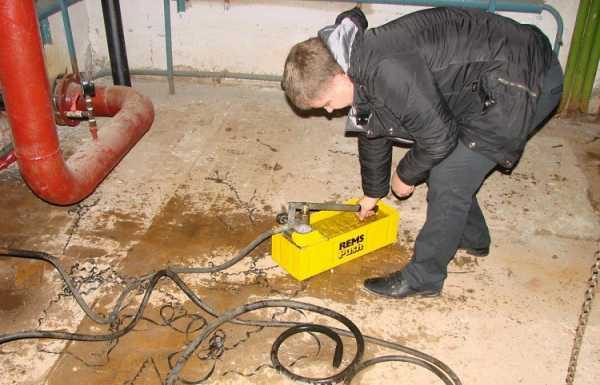
Испытания противопожарного водопровода также проводятся под высоким давлением
Важно! Гидравлические проверки готового пожарного трубопровода нужно проводить не менее 2 раз в год.
Такие испытания производятся и в уже эксплуатируемых зданиях, поэтому для проверки противопожарной коммуникации используют пониженный показатель давления. Кроме этого, испытательная процедура включает в себя замеры на специальном кране, который называют диктующим.
Также проводятся проверки, которые определяют водоотдачу в противопожарной системе, они необходимы для самых удалённых от источника воды пожарных кранов. В обязательном порядке выполняется проверка, которая направлена на выявление возможных протечек в противопожарной системе. Все полученные данные заносятся сначала в испытательный журнал, а затем — в акт. После этого они сравниваются с прописанными в СНиП нормативами.
Испытания систем водоснабжения
Проверка систем водоснабжения тоже производится в соответствии со строительными нормами и правилами. Гидравлические испытания проводят: после прокладки коммуникации, перед засыпкой канала, после засыпки канала (до монтажа соответствующих комплектующих). Проверка трубопроводных коммуникаций, которые относятся к напорным, проводится в соответствии со СНиП В III–3–81.
Трубы, выполненные из чугунного материала или асбоцемента, проверяются в случае, если длина трубопровода не превышает 1 километра (за 1 испытание). Полиэтиленовые (ПЭ) трубопроводы испытываются отрезками по 500 метров. Трубопроводы из любых других материалов проверяются отрезками, которые имеют длину до 1 километра.
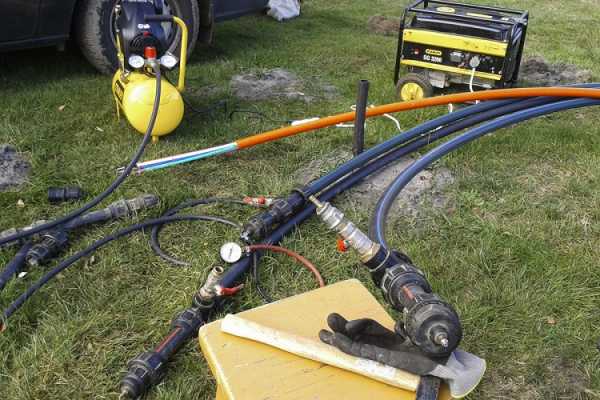
Время выдержки зависит от материала, из которого изготовлены трубы испытуемой магистрали
А также стоит отметить, что время выдержки для металлических и асбоцементных труб составляет не менее 10 мин, а для ПЭ труб — не меньше 30 мин.
Испытания систем отопления
Гидравлические испытания отопительных коммуникаций производятся непосредственно после их установки. Наполнение коммуникации водой выполняется снизу вверх. Это способствует спокойному выводу воздуха из системы. Важно знать, что наполнение системы водой не должно происходить слишком быстро, иначе могут возникнуть воздушные пробки.
Проверки отопительных коммуникаций выполняются с учётом СНиП и предполагают задействование следующих показателей давления:
- стандартное, рабочее давление, составляющее 100 кПа;
- проверочное давление со значением 300 кПа.
Важным моментом считается то, что испытание трубопроводов теплосетей должно производиться при отстыкованном котле. Также необходимо заранее отсоединить расширительный бак. Проверочные мероприятия, направленные на выявление и устранение дефектов в системах отопления, не проводятся в зимний период. Если теплосеть нормально функционировала в течение 3 месяцев — ее эксплуатация может производиться без гидравлических проверок. Проверка закрытого отопительного трубопровода выполняется до засыпки траншеи, а также до монтажа теплоизоляционного материала.
Обратите внимание! Измерительная аппаратура должна в обязательном порядке подвергаться проверке перед началом гидравлических испытаний.
Согласно со строительными нормами и правилами, после проведения всех этапов испытаний, теплосеть промывают и устанавливают в её нижней точке специальный соединительный элемент — муфту (с сечением от 60 до 80 мм). Через эту муфту производится удаление жидкости из системы. Промывка отопительной коммуникации выполняется несколько раз холодной водой.
trubamaster.ru
Контроль качества соединений стальных трубопроводов
4.8.Контроль качества сварных соединений стальных трубопроводов должен производиться путем: систематического операционного контроля; механических испытаний образцов, вырезанных из пробных стыков; проверки сплошности стыков с выявлением внутренних дефектов одним из неразрушающих методов контроля, а также последующих гидравлических или пневматических испытаний согласно разд. 5 настоящих правил. Методы контроля качества сварных соединений приведены в ГОСТ 3242—79.
Проверка качества сварных швов трубопроводов Vкатегории ограничивается осуществлением операционного контроля.
В случаях, оговоренных в проекте, следует производить испытание сварных соединений из нержавеющих сталей на склонность к межкристаллитной коррозии в соответствии с ГОСТ 6032—75и ведомственными нормативными документами.
4.9.Операционный контроль должен предусматривать проверку состояния сварочных материалов, качества подготовки концов труб и деталей трубопроводов, точности сборочных операций, выполнения заданного режима сварки.
4.10.Контроль сварных соединений стальных трубопроводов радиографическим или ультразвуковым методом следует производить после устранения дефектов, выявленных внешним осмотром и измерениями, а трубопроводов РYсвыше 10МПа (100кгс/см2) —после выявления дефектов магнитопорошковым или цветным методом.
Сварные швы не должны иметь трещин, прожогов, кратеров, грубой чешуйчатости, подрезов глубиной более 0,5мм. [В сварных швах трубопроводов РYсвыше 10МПа (100кгс/см2)подрезы не допускаются].
4.11.Объем контроля сварных соединений стальных трубопроводов неразрушающими методами в процентах к общему числу стыков, сваренных каждым сварщиком (но не менее одного стыка),должен составлять для трубопроводов:
Рyопыте 10МПа (100 кгс/см2) ...................100
Iкатегории ..................................................20
II „ .......................................................10
III „ ........................................................2
IV „ .........................................................1
В качестве неразрушающих методов контроля следует с учетом конкретных условий применять преимущественно ультразвуковой, электрорентгенографический и рентгенографический с использованием фотобумаги.
Контролю должен подвергаться весь периметр стыка.
Для трубопроводовI-IVкатегории контролю подлежат стыки, наихудшие по результатам внешнего осмотра.
Контроль корня шва сварных соединений трубопроводов Рyсвыше10МПа (100кгс/см2) из сталей всех групп при толщине стенки 16мм и более следует производить радиографическим методом, а окончательный контроль готовых сварных соединений из сталей групп С, ХГ, ХМ —преимущественно ультразвуковой дефектоскопией.
Готовые сварные соединения трубопроводов Рyсвыше 10МПа(100кгс/см2 )перед проведением радиографического или ультразвукового контроля следует контролировать магнитопорошковым или цветным методом. При этом контролю подлежат поверхность шва и прилегающая к нему зона шириной 20мм от краев шва.
4.12.Оценку качества сварных соединений стальных трубопроводов по результатам радиографического контроля следует производить по балльной системе согласно обязательному приложению 4.Сварные соединения должны быть забракованы, если их суммарный балл равен или больше для трубопроводов:
Рyсвыше 10МПа (100кгс/см2) ............ 2
Iкатегории ...........................................3
II „ .................................................3
III „ .................................................5
IV „ .................................................6
Сварные соединения, оцененные указанным или большим баллом, подлежат исправлению, после чего дополнительному контролю подвергают удвоенное от первоначального объема контроля количество стыков, выполненных сварщиком, допустившим брак.
Сварные соединения трубопроводов IIIи IVкатегории, оцененные соответственно суммарным баллом 4и 5,исправлению не подлежат, но дополнительному контролю подвергают удвоенное количество стыков, выполненных этим сварщиком.
Если при дополнительном контроле хотя бы один стык будет забракован (а для трубопроводов IIIи IVкатегории оценен соответственно суммарным баллом 4и 5),контролю подвергают 100 %стыков, выполненных данным сварщиком. Если при этом будет забракован хотя бы один стык, сварщика отстраняют от сварочных работ на трубопроводах.
4.13.Чувствительность радиографического контроля должна соответствовать (по ГОСТ 7512-82)для трубопроводовPyсвыше 10МПа(100кгс/см2), Iи IIкатегории -классу 2,для трубопроводов IIIи IVкатегории —классу 3.
4.14.По результатам ультразвукового контроля сварные соединения трубопроводов Рyсвыше 10МПа (100кгс/см2) считаются качественными, если отсутствуют:
а) протяженные плоскостные и объемные дефекты;
б)объемные непротяженные дефекты с амплитудой отраженного сигнала, соответствующей эквивалентной площади 2мм2и более —при толщине стенки трубы до 20мм включительно и 3мм2и более —при толщине стенки свыше 20мм;
в) объемные непротяженные дефекты с амплитудой отраженного сигнала, соответствующей эквивалентной площади до 2мм2 —при толщине стенки трубы до 20мм включительно и до 3мм2 —при толщине стенки свыше20мм, в количестве более трех на каждые 100мм шва.
Сварные соединения стальных трубопроводов I—IVкатегории должны удовлетворять требованиям, установленным отраслевыми стандартами. При получении неудовлетворительных результатов контроля ультразвуковым методом хотя бы одного стыка производят контроль удвоенного количества стыков, выполненных данным сварщиком. При неудовлетворительных результатах повторного контроля производят контроль 100% стыков. Сварщик, допустивший брак, может быть допущен вновь к сварке трубопроводов только после сдачи испытаний по программам, утвержденным министерством (ведомством) СССР.
4.15.Исправлению путем местной выборки и последующей полварки (без повторной сварки всего соединения) подлежат участки сварного шва стальных трубопроводов, если размеры выборки после удаления дефектного участка шва не превышают значений, указанных в табл. 1.
Таблица 1
Глубина выборки, % к номинальной толщине стенки труб или расчетному сечению шва | Суммарная протяженность, % к номинальному наружному периметру сварного соединения |
Для трубопроводов Рyсв. 10 МПа (100 кгс/см2) | |
До 15 Св. 15до 30 „30 „ 50 Св. 50 | Не нормируется До 35 „ 20 „15 |
Для трубопроводов I—IVкатегории | |
До 25 Св.25до 50 Св. 50 | Не нормируется До 50 „ 25 |
Сварное соединение, в котором для исправления дефектного участка требуется произвести выборку размером более допустимой по табл. 1, должно быть полностью удалено, а на его место вварена „катушка".
Исправлению подлежат все дефектные участки сварного соединения, выявленные при внешнем осмотре и измерениях, контроле ультразвуковым, магнитопорошковым или цветным методом.
В стыках, забракованных по результатам радиографического контроля, исправлению подлежат участки шва, оцененные наибольшим баллом, определяемым согласно п. 4.12 и обязательному приложению 4.В случае, если стык забракован по сумме одинаковых баллов, исправлению подлежат участки с непроваром.
Одно и то же место стыка допускается исправлять не более одного раза. Исправление дефектов подчеканкой запрещается.
Все подвергавшиеся исправлению участки стыков должны быть проверены неразрушающими методами.
Сведения об исправлении и повторном контроле стыков должны быть внесены в производственную документацию согласно обязательному приложению 2.
4.16.Испытаниям на твердость металла шва должны подвергаться сварные соединения стальных трубопроводов Рyсвыше 10МПа (100кгс/см2), а также трубопроводов Рyдо 10МПа вкл. (100кгс/см2) из сталей групп ХМ и ХФ, прошедших термическую обработку.
По результатам измерения твердости сварные соединения считаются качественными при выполнении следующих условий:
а) снижении твердости наплавленного металла не более чем на 25НВ нижнего значения твердости основного металла;
б) превышении твердости наплавленного металла не более чем на 20НВ верхнего значения твердости основного металла;
в) превышении разности в твердости основного металла и металла в зоне термического влияния не более чем на 50НВ.
При разности в твердости, превышающей допустимую, соединения следует вновь подвергать термической обработке, и, если разность в твердости превышает допустимую после повторной термической обработки, следует произвести стилоскопирование металла шва и основного металла всех однотипных соединений, сваренных данным сварщиком за время после последней контрольной проверки. При несоответствии химического состава наплавленного металла заданному стыки бракуют.
studfiles.net
Гидравлические испытания трубопроводов
Гидравлические испытания проводятся в соответствии со СНиП. После их окончания составляется акт, указывающий на работоспособность системы.
Ручной опрессовщик для испытания трубопроводов
Они выполняются на разных этапах эксплуатации коммуникаций. Параметры проверки вычисляются для каждой системы отдельно, в зависимости от ее типа.
Cодержание статьи
Зачем и когда проводить гидравлические испытания?
Гидравлические испытания – это вид неразрушающего контроля, который осуществляется для проверки прочности и плотности трубопроводных систем. Им подвергается все работающее оборудование на разных этапах эксплуатации.
В целом, можно выделить три случая, в которых испытания должны проводиться в обязательном порядке, в независимости от назначения трубопровода:
- после завершения производственного процесса по выпуску оборудования или деталей трубопроводной системы;
- после завершения установочных работ трубопровода;
- во время эксплуатации оборудования.
Испытания гидравлическим способом – это важная процедура, которая подтверждает или опровергает надёжность эксплуатируемой системы, работающей под давлением. Это необходимо для предотвращения аварии на магистралях и сохранения здоровья граждан.
Осуществляется проведение процедуры на гидравлическое испытание трубопроводов в экстремальных условиях. Давление, под которым оно проходит, называют проверочным. Оно превышает обычное, рабочее давление в 1,25-1,5 раза.
Особенности гидравлических испытаний
В систему трубопровода пробное давление подается плавно и медленно, чтобы не спровоцировать гидроударов и образования аварийных происшествий. Величину давления определяют не на глаз, а по специальной формуле, но на практике, как правило, оно на 25% больше рабочего давления.
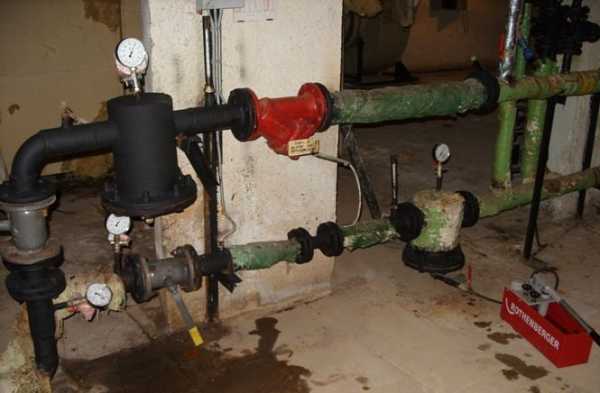
Гидравлические испытания выявляют ненадежные соединения
Силу подачи воды контролируют на манометрах и каналах измерения. Согласно СНиП, допускаются скачки показателей, так как возможно быстрое измерение температуры жидкости в трубопроводном сосуде. При его наполнении нужно обязательно следить за скоплением газа на разных участках системы.
Такую возможность следует исключить еще на начальном этапе.
После заполнения трубопровода наступает, так называемое, время выдержки – период, во время которого испытуемое оборудование находится под повышенным давлением. Важно следить, чтобы оно находилось на одном уровне во время выдержки. После его окончания давление минимизируют до рабочего состояния.
Пока проходит испытание, возле трубопровода не должно находиться никого.
Обслуживающий его персонал должен ждать в безопасном месте, так как проверка работоспособности системы может быть взрывоопасна. После окончания процесса наступает оценка полученных результатов согласно СНиП. Трубопровод осматривается на наличие течей, взрывов металла, деформаций.
Параметры гидравлических испытаний
При проведении проверки качества трубопровода необходимо определить показатели следующих параметров работ:
- Давления.
- Температуры.
- Времени выдержки.
Нижняя граница проверочного давления вычисляется по следующей формуле: Ph = KhP. Верхняя граница не должна превышать сумму общих мембранных и изгибных напряжений, которая достигнет 1,7 [δ]Th. Формула расшифровывается так:
- Р – расчетное давление, параметры которого предоставлены изготовителем, или рабочее давление, если испытания осуществляются после монтажа;
- [δ]Th – номинальное напряжение, которое допускается при температуре испытаний Th;
- [δ]T – допускаемое напряжение при расчетной температуре T;
- Kh – условный коэффициент, принимающий разное значение для разных объектов. При проверке трубопроводов он равен 1,25.
Температура воды не должна опускаться ниже 5˚С и не подыматься выше 40˚С. Исключением являются лишь те случаи, когда температура гидро компонента указана в технических условиях исследуемого объекта. Как бы там ни было, температура воздуха при проведении проверки не должна опускаться ниже тех же 5˚С.
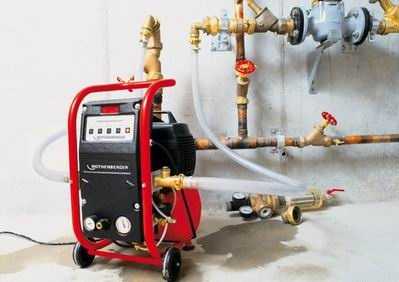
Воздушный компрессор для опрессовки систем водоснабжения или отопления
Время выдержки должно быть указанно в проектной документации на объект. Оно не должно быть меньше 5 мин. Если точные параметры не предусмотрены, то время выдержки рассчитывается, исходя их толщины стенок трубопровода. Например, при толщине до 50 мм, проверка под давлением длиться не менее 10 мин, при толщине свыше 100 мм – не менее 30 мин.
Испытания пожарных гидрантов и магистралей водоснабжения
Гидрант – оборудование, отвечающее за быстроту устранения пожарных воспламенений, поэтому оно должно всегда находиться в рабочем состоянии. Главная задача пожарных гидрантов – обеспечить оптимальное количество воды для борьбы с пожаром на его начальном этапе.
Гидравлические испытания пожарного оборудования осуществляются на этапе его монтажа, а также два раза в год на протяжении всего срока эксплуатации, преимущественно весной и осенью.
Испытания пожарных гидрантов должны выявить уровень водоотдачи, которую может обеспечить сеть. При этом во внимание берётся расход жидкости, сила напора и рабочий радиус действия. Также они направлены на выявление целостности рукавов тушения.
Что качается проведения проверки магистралей водоснабжения, то их стоит проверять сразу после монтажа, перед засыпкой траншеи и еще раз после засыпки, но до установки арматуры. Вместо нее можно использовать временные заглушки.
Проверка напорных трубопроводов происходит в соответствии со СНиП В III-3-81.
Трубы, изготовленные из чугуна и асбеста, испытываются при длине трубопровода не более 1 км за один прием. Полиэтиленовые магистрали водопровода проверяются участками по 0.5 км. Все остальные системы водоснабжения проверяются отрезками не более 1 км. Время выдержки для труб водоснабжения из металла и асбеста должно составлять не менее 10 м, для полиэтиленовые – не меньше 30 м.
Испытания систем отопления
Проверка тепловых сетей производится сразу после окончания их монтажа. Заполнение водой систем отопления происходит через обратный трубопровод, то есть снизу вверх.
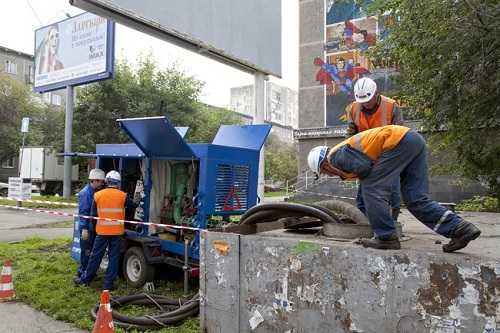
Гидравлические испытания трубопроводов магистралей центрального отопления
При таком способе жидкость и воздух идут в одном направлении, что, согласно законам физики, способствует отводу воздушных масс из системы. Отвод происходит одним и способов: через выпускные устройства, бак или вантузы систем отопления.
Если наполнение тепловых сетей происходит слишком быстро, возможно возникновение воздушных мешков из-за заполнения стояков водой быстрее, чем нагревательных приборов систем отопления. Гидравлические испытания тепловых сетей проходят под нижним значением рабочего давления в 100 кило Паскаль и проверочного – 300 кило Паскаль.
Проверка тепловых сетей происходит только при отсоединённом котле и расширительном баке.
Контроль систем отопления не проводится в зимнее время. Если они проработали без поломок до около трех месяцев, то принятие тепловых сетей в эксплуатацию может проводиться без гидравлических испытаний. При проверке закрытых систем отопления, работы по контролю нужно проводить до закрытия борозд. Если планируется изоляция тепловых сетей, то — перед ее установкой.
Согласно СНиП после окончания испытаний систем отопления, их промывают, а в их нижней точке монтируется муфта с сечением от 60 до 80 мм2. Через нее происходит спуск воды. Промывание тепловых сетей осуществляется холодной водой несколько раз, до приобретения ею прозрачности. Одобрение систем отопления наступает в случае, если на протяжении 5 мин проверочное давление в трубопроводе не изменится больше, чем на 20 кило Паскаль.
Гидравлическое испытание системы отопления и водоснабжения (видео)
Гидравлические испытания тепловых сетей и систем подачи воды
После завершения гидравлических испытаний систем отопления по СНиП, составляется акт гидравлических испытаний тепловых сетей и систем подачи воды, указывающий на соответствие параметров трубопровода.
Согласно СНиП его бланк содержит такую информацию:
- название должности руководителя предприятия, оказывающего обслуживание тепловых сетей;
- его подпись и инициалы, а также дату проверки;
- данные о председателе комиссии, а также ее членах;
- информацию о параметрах тепловых сетей: протяжности, наименования и т.д.;
- выводы о проведении контроля, заключение комиссии.
Регулировка характеристик магистралей отопления осуществляется СНиП 3.05.03-85. Согласно указанному СНиП его правила действуют в отношении всех магистралей, которые транспортируют воду температурой до 220˚С и пара — до 440˚С.
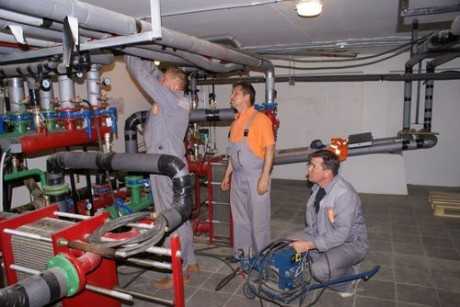
Испытания трубопроводов на герметичность в тепловом пункте
Для документального завершения гидравлических испытаний водопровода составляется акт для наружного водопровода в соответствии со СНиП 3.05.01-85. Согласно СНиП акт содержит следующую информацию:
- наименование системы;
- название организации технического надзора;
- данные о величине проверочного давления и времени испытания;
- данные о падении давления;
- наличии или отсутствии признаков повреждении трубопровода;
- дату проверки;
- вывод комиссии.
Акт заверяется представителем организации надзора.
Другие похожие статьи по теме:
trubypro.ru
Проверка - прочность - трубопровод
Проверка - прочность - трубопровод
Cтраница 1
Проверка прочности трубопровода проводится по наибольшему из вычисленных моментов. [1]
Проверку прочности трубопровода, определяя усилия от расчетных нагрузок и воздействий, возникающих в отдельных элементах трубопроводов согласно указаниям СНиП 2.04.12 - 86 [113] необходимо производить методами строительной механики расчета статически неопределимых стержневых систем. [2]
Требуется проверка прочности трубопровода по напряжениям категории ( ст) 2 Для условий гидроиспытания. Расчет выполняют на совместное действие давления и массовой нагрузки. [3]
Для проверки прочности трубопроводов и плотности их стыков проводят гидравлическое испытание. [5]
При проверке прочности трубопровода в продольном направлении напряжения ст будут суммироваться с продольными растягивающими напряжениями, возникающими в нем помимо влияния горных разработок. [6]
При проверке прочности трубопровода в продольном направлении напряжения от сейсмического воздействия, найденные по формуле (4.178), будут суммироваться с напряжениями от всех других силовых воздействий. [7]
При пневматическом испытании производится проверка прочности трубопровода внутренним давлением и герметичности наружным осмотром трубопровода и определением величины падения давления. [8]
Таким образом, для проверки прочности подрабатываемого трубопровода на основании определения его предельного состояния необходимо по формуле (4.177) найти величину максимальной деформации и сравнить ее с предельно допустимой. [9]
Величина пробного давления при проверке прочности трубопроводов устанавливается индивидуально для каждого трубопровода в соответствии с указаниями, имеющимися в проекте. [10]
При предварительном пневматическом испытании производятся проверка прочности трубопровода внутренним давлением, значение которого устанавливается в зависимости от расчетного рабочего давления трубопровода и материала труб, и наружный осмотр трубопровода с фиксацией выявленных дефектов. [11]
В этих случаях необходимо производить проверку прочности трубопровода от воздействия на него внешних нагрузок. [12]
Выявление дефектов различного уровня, не обнаруженных при неразрушающем контроле, а также проверка прочности трубопровода для оценки его возможности работать с проектной пропускной способностью, т.е. при проектных рабочих давлениях, могут быть обеспечены только при проведении гидравлических переиспытаний. [13]
Однотрубным жидкостным манометром следует измерять давление при проверке герметичности трубопровода после его засыпки. При проверке прочности трубопровода и наружном осмотре жидкостный маиометр должен быть отключен. [14]
Таким образом, получена расчетная формула для определения напряжения изгиба в стенке трубопровода а месте соединения его с муфтой. Полученная зависимость позволяет выполнить проверку прочности трубопровода и выбрать конструкцию муфты, при которой напряжения в трубопроводе не превысят нормативные значения. [15]
Страницы: 1 2
www.ngpedia.ru
Проверка качества работ по ремонту трубопроводов
Проверка качества работ по ремонту трубопроводов [c.267]Резкое понижение температуры наружного воздуха отрицательно сказывается на проведении ремонтных работ технологического и сантехнического оборудования. Возникают трудности при подготовке оборудования к ремонту, а также при проведении испытаний аппаратов и трубопроводов после ремонта. Обычные способы подготовки оборудования для ремонта (промывка водой, пропарка водяным паром), а также проверка качества ремонта путем гидравлического испытания в зимнее время имеют ограниченное применение, в связи с чем приходится прибегать к упрощенным способам, которые иногда не соответствуют требованиям техники безопасности. [c.280]
После окончания капитального ремонта трубопроводов, а также монтажа новых участков производят проверку качества работ, промывку или продувку и [c.161]ПРОВЕРКА КАЧЕСТВА РАБОТ ПО РЕМОНТУ ТРУБОПРОВОДОВ [c.225]
После окончания капитального ремонта трубопроводов проводятся проверка качества работ, промывка или продувка, а затем испытание на прочность и плотность. Технологическая аппаратура перед испытанием отключается, концы трубопровода закрываются заглушками. Заглушаются все врезки для контрольно-измерительных приборов. В наиболее низких точках ввариваются штуцеры с арматурой для спуска воды при гидравлическом испытании, а в наиболее высоких — воздушки для выпуска воздуха. В начальных и концевых точках трубопровода, а также на насосах [c.253]
Перед установкой новой прокладки не была зачищена уплотняющая поверхность фланцев. Остатки старой прокладки ослабили затяжку новой прокладки. Начальник смены и мастер по ремонту не проконтролировали качество проведенной работы по замене прокладки. Кроме того, на линии водорода давлением 3 МПа в период капитального ремонта сняли для проверки предохранительный клапан, который после ремонта не поставили на место, что привело к превышению давления в линии. Комиссия, принимавшая цех после капитального ремонта (за месяц до аварии), формально отнеслась к приемке оборудования, поэтому указанное нарушение не было устранено. Участок трубопровода не был испытан на герметичность после замены прокладки во фланцевом соединении. В трубопроводе водорода имелись механические примеси, которые послужили импульсом воспламенения водорода. Трубопроводы водорода имели гладкие фланцы, а не фланцевые соединения типа выступ — впадина, т. е. имелась потенциальная возможность прорыва прокладки. [c.193]
Правила технической эксплуатации теплоиспольз щих установок и тепловых сетей содержат следующие разделы 1. Э1. Организация эксплуатации 2. Э2. Распределение и преобразование тепловой энергии 3. ЭЗ. Использование тепловой энергии Приложения 1. Окраска и надписи для трубопроводов 2. Па-роконденсатный баланс 3. Сроки периодической проверки приборов 4. Список мер и измерительных приборов, подлежащих государственной проверке в органах Комитета стандартов, мер и измерительных приборов Совета Министров СССР, вновь изготовленных, после ремонта и находящихся в обращении, цри-меняемых в качестве основных (исходных) образцовых 5. Категорийность трубопроводов 6. Краткая таблица соотношения между единицами измерения СИ (ГОСТ 9867—61) и другими единицами, принятыми в настоящих Правилах. Правила техники безопасности при эксплуатации теплоиспользующих установок и тепловых сетей содержат следующие разделы 1. 51. Общие положения 2. 52. Основные требования безопасности при обслуживании и ремонте теплоиспользующих установок и оборудования 3. 53. Требования безопасности при обслуживании тепловых сетей и тепловых пунктов. Приложения 1. Приказ Министра здравоохранения СССР № 400 от 30 мая 1969 г. 2. Журнал проверки знаний ПТЭ и ПТБ 3. Удостоверение о проверке знаний 4. Форма наряда 5. Выписки из Инструкции о ме15ах пожарной безопасности при проведении огневых работ... 6. Нормы и сроки испытаний подъемных механизмов и приспособлений [c.168]
Техническую документацию и изготовление сосудов Техническую документацию на изготовление и ремонт трубопроводов (акт приемки ведомость ревизии труб, фланцев, крепежа, фасонных деталей ведомость учета труб высокого давления после механической обработки ведомость учета гнутых труб высокого давления журнал сварочных работ протокол механических испытаний сварных образцов журнал проверки качества электродов, сварочной проволоки, флюса, аргона для проведения сварочных работ акт проверки технологических [c.562]
Качество очистки поверхности стальных сооружений проверяется внешним осмотром качество нанесенного покрытия — по мере его наложения путем внешнего осмотра, измерения толщины покрытия, а также сплошности и прилипаемости к металлу. Сплошность покрытий трубопроводов контролируется искровым дефектоскопом. Она проверяется выборочно во время движения изоляционной машины и ее остановок. При этой проверке должно быть установлено, что режим работы изоляционной машины отработан правильно и качество покрытия соответствует требованиям к нему. При наличии брака работа приостанавливается для обследования дефекта и ремонта изоляции. При каждой технологической остановке по причине брака покрытия проверка дефектоскопом производится на участке трубопровода длиной не менее 10 м непосредственно у изолировочной машины. При этом следует проверить возможно большую поверхность нижней части трубопровода. [c.61]
По окончании ремонтных работ заполняют удостоверение о качестве ремонта и подшивают его в паспорт или эксплуатационный журнал трубопровода. При передаче удостоверения представителю технического надзора исполнитель работ предъявляет также документы, подтверждающие качество применяемых материалов и результаты проверки состояния сварных швов. [c.25]
После устранения всех дефектов на трубопроводе окончательно проверяют качество выполненных работ. Кроме того, в горизонтальной и вертикальной плоскостях проверяют прямолинейность расположения и уклон трубопровода, отсутствие изгибов и переломов. Неирямолинейность трубопровода в горизонтальной плоскости устраняют передвижением направляющих и неподвижных опор. Выпучивание, провисание и неирямолинейность в вертикальной плоскости устраняют путем установки под опоры подкладок соответствующей толщины пли изменением длины подвесок. Переломы в сварных стыках выше нормы являются браком, допущенным нри сборке трубопровода, так как для его устранения необходим ремонт не только данного стыка, но и стыка на участке холодного натяга трубопровода. Кроме внешнего осмотра предусматриваются механические испытания образцов, вырезанных из контрольных стыков или сварных соединений трубопровода, а также проверка качества сварных швов неразрушающими методами контроля, рассмотренными выше. [c.302]
Техническую документацию на изготовление сосудов Техническую документацию на изготовление и ремонт трубопроводов (акт приемки ведомость ревизии труб, фланцев, крепежа, фасонных деталей ведомость учета труб высокого давления после механической обработки ведомость учета гнутых труб высокого давления журнал сварочных работ протокол механических испытаний сварных образцов журнал проверки качества электродов, сварочной проволоки, флюса, аргона для проведения сварочных работ акт проверки технологических свойств электродов журнал режима термообработки сварных швов заключение по неразрушающим методам контроля сварных швов акт гидрав- лического испытания трубопоо-водов высокого давления ведомость проверки гнутых труб высокого давления) Техническую документацию на изготовление детален и запасных частей (акт приемки, паспорт, чертеж) [c.562]
chem21.info