Состав карбюризатора для цементации. Карбюризатор для цементации
Состав карбюризатора для цементации
Изобретение относится к химико-термической обработке, в частности к составам для цементации в твердых карбюризаторах. Цель изобретения - повышение насыщающей способности карбюризатора и улучшение сплавляемости обработанных в нем жеребеек с чугуном. Состав содержит, мас.%: гипофосфит кальция 8-12 углекислый кальций 1-3 углекислый барий 6-10 роданистый марганец 0,8-2,4 гашеная известь 12-16 древесный уголь остальное. 2 табл.
СОЮЗ СОВЕТСКИХ
СОЦИАЛИСТИЧЕСКИХ
РЕСПУБЛИК цд4 С 23 С 8/64
ОПИСАНИЕ ИЗОБРЕТЕНИЯ
К АВТОРСКОМ .К СВИДЕТЕЛЬСТВУ
2С+ О = 2 СО.
ГОСУДАРСТВЕННЫЙ КОМИТЕТ
ПО ИЗОБРЕТЕНИЯМ И OTHPblTHRM
ПРИ ГКНТ СССР
1 (21) 4393395/31-02 (22) 15.03.88 (46) 15.10.89. Бюп. И 38 (71) Краматорский индустриальный институт (72) А.В. Дубинин, И.П. Катасонов, А.В. Грановский и Н.А. Антонов (53) 621.785.52 (088.8) (56) Зуев В.M. Термическая обработza металлов. M. Высшая школа, 1981, с. 102. (54) СОСТАВ КАРВЮРИЗАТОРА ДЛЯ ЦЕ-МЕНТАЦИИ
Изобретение относится к химикотермической обработке металлов; в частности к составам для цементации в твердых карбюризаторах.
Целью изобретения является повышение насыщающей способности карбюриз атора, улучшение сплавляемости обработанных в нем жеребеек с чугуном.
Карбюризатор, содержащий древесный уголь, углекислый кальций, углекислый барий, дополнительно содержит гипофосфит кальция, роданистый марганец, гашеную известь при следу-. ющем содержании компонентов, мас.%:Гипофосфит кальция 8-12
Углекислый кальций 1-3
Углекислый барий 6-10
Роданистый марганец 0,8-2,4
Гашеная известь 12-16
Древесный уголь Остальное
„„Я0„„1514825 А1
? (57) Изобретение относится к химико. термической обработке, в частности . к составам для цементации в твердых карбюризаторах. Цель изобретения-повышенне насыщающей способности карбюризатора и улучшение сплавляемости обработанных в нем жеребеек с чугуном. Состав содержит, мас.%: гипофосфит кальция 8-12 углекислый кальций 1-3 углекислый барий 6-10; роданистый марганец 0,8-2,4 гашеная известь 12-16, древесный уголь остальное. 2 табл.
В предлагаемом составе гашеная известь применяется для ускорения процесса насыщения поверхности жере беек; гипофосфит кальция применяется для снижения температуры плавления поверхности обрабатываемых жеребеек; роданистый марганец применяется с целью улучшения сплавляе-, мости обработанной жеребейки с чугуном.
Древесный уголь является основным источником углерода в составе карбюризатора. Древесный уголь окисляется воздухом, находящимся в порах между частицами карбюризатора:
Окись углерода на поверхности обрабатываемой детали окисляется до углекислого газа, при этом выделяется атомарный углерод
2СО = СО + С.1,514825
Атомарный углерод диффундирует в поверхность жеребейки насыщения ее углеродом.
Углекислый кальций препятствует спеканию карбюризатора, повышает его активность.
Углекислый барий при нагреве выделяет углекислый гаэ, который восстанавливается древесным углем до 10 окиси углерода, способствует переносу углерода на обрабатываемую поверхность.
При содержании углекислого кальция менее 1 не достигается нужный 15 эффект, при содержании углекислого кальция ниболее 3% дальнейшего улучшения свойств карбюризатора не наб>людается. При содержании углекислого бария менее б не достигается 20 желаемый эффект, при содержании углекислого бария более 10Х увеличивается токсичность карбюриэатора без дальнейшего улучшения технологических свойств.
Гипофосфит кальция служит источником фосфора в карбюризаторе. фосфор BoccTBHGBJIHHGeT(древесным углем из гипофосфита кальция до элементарного, причем в момент выделения находится в наиболее активном атомарном виде. Фосфор диффундирует в поверхность жеребейки, где входит в состав эвтектик с железом, мар— ганцем. Эвтектики фосфора легкоплав- 35 .ки, жидкотекучи, обладают самофлюсующими свойствами и поэтому облегчают смачивание жидким чугуном поверхности жеребеек. При содержании гипофос— фита кальция менее 8 желаемый зф- 40 фект не достигается, при содержании гипофосфита кальция б>олее 12 ухудшается качество поверхности обработанной жеребейки.
Гашеная известь является источни- 45 ком водорода, Гашеная известь распадается при нагреве
q с
Са(ОН) CaO + Н О, Образующиеся пары воды реагируют с углеродом:
НО+1 2H+CO.
Водород, выделян>щийся в атомар55 ной форме, реагирует с углеродом, при этом образуются углеводородные соединения, которые являются более эффективным звеном„ передающим углерод к обрабатываемой поверхности, чем окись углерода, Кроме того, водород вступает в реакцию с фосфором и серой и также способствуют их переносу на обрабатываемую поверхность жеребейки. Образующаяся окись кальция препятствует спеканию карбюризатора, При содержании гашеной извести менее 12Х ее влияние оказывается недостаточным, при содержании гашеной извести более 1бХ дальнейшего улучшения свойств карбюризатора не происходит.
Роданистый марганец служит дополнительным источником углерода, а также источником марганца, серы и азота в карбюризаторе.
При распаде роданистого марганца выделяется марганец, проникающий в глубь обрабатываемой поверхности.
Марганец, имея сродство к кислороду большее, чем железо, при заливке жеребейки жидким чугуном восстанавливает окислы железа, образуя легкоплавкие окислы марганца, всплывающие на поверхность чугуна; марганец снижает кипение металла за счет образования окиси углерода, так как вместо газообразной окиси углерода образуются при заливке окислы марган-. ца, находящиеся в жидком состоянии.
Тем самым роданистый марганец способ" ствует герметичности отливки вместе постановки жеребейки. Кроме того, марганец образует легкоплавкие эвтектики с серой и фосфором, улучшая тем самым процесс смачивания поверх» ности жеребейки жидким чугуном. Роданистый марганец является также источником серы. Сера, насыщая поверхность обрабатываемой жеребейки, совместно с фосфором понижает температу- ру ее плавления, способствуя улучшению смачиваемости поверхности жеребейки жидким чугуном. Кроме того, роданистый марганец служит источником азота, насыщающего поверхность жеребейки, что препятствует отбелу чугуна по линии сплавления его с жеребейкой, так как азот является аустенизатором. При содержании роданистого марганца менее 0,8 его влияние оказывается недостаточным, при содержании роданистого марганца более 2,4Х дальнейшего улучшения свойств карбюриэатора не происходит.
1514825 тора ухудшаются.
1-3
12-16 известь
Древесный
Остальное уголь
Таблица l
Содержание компонентв, мас.%, в составе
Компонент
6(прототип) 4 5
Гипофосфит кальция
Углекислый кальций
Углекислый барий
Роданистый марганец
Гашеная
12 14
3 4 3,5
10 12 22
6 8
0,7 1
4 6
2,4
0,6 О;8 1,8
10 12 14
2,8
16 известь
Др ев есный уголь
Осталь-Осталь- Осталь- ОсОсталь- Остапьталь- ное ное ное ное ное ное
Изготовлены пять составов предла- гаемого карбюризатора, а также состав, принятый за прототип, табл. 1.
В карбюризаторе обрабатывались жеребейки из стали 3 при следующем режиме: время обработки 6 ч; температура 950 С. Определялась глубина диффузионно-насыщенного слоя. Жеребейки, обработанные в карбюризаторе, использовались для литья чугунных ппастин толщиной 12 мм, для чего производилась заливка чугуном СЧ15, при 1300 С,Запивалось по 20 жеребеек, обработанных каждым из составов карбюризатора. Отливки проверялись на герметичность керосиновой пробой, подсчитывапось число течей по жеребейкам.
Результаты испытаний приведены в табл.2.
Как видно из табл.2, предложенный состав карбюризатора оптимальных составов 2-4 имеет преимущества перед известным, принятым за прототип. При содержании компонентов в карбюризаторе больше или меньше опткмального состава свойства карбюриэаФо рмул а из обретения
Состав карбюризатора для цементации, содержащий древесный уголь, углекислый барий, углекислый кальций, отлич ающийся тем, что, с целью повышения насыщающей способности состава и улучшения сплавляемости обработанных в нем жеребеек с чугуном, он дополнительно содержит
t5 гипофосфит кальция, роданистый марганец, гашеную известь при следующем соотношении- компонентов, мас.%:
Гипофосфит кальция 8-12
20 Углекислый кальций
Углекислый барий 6-10
Роданистый
25 марганец 0,8-2,4
Гашеная
1514825
Т абл ица2 лубина ементосло чей тав, ф
Примеч ания обанного абослоя, мм анным рейкам
0,16
Налипание карбюризатора на жеребейку
Нет замечанийй
Нет замечаний
Нет замечаний
Окомкование карбюризатора
Спекание карбюриза-.. тора и налипание на жеребейку
0,19
Нет
0,22
Нет
0,21
Нет
0,17
6, 0,11
Составитель И. Дашкова
Редакт ор М. Бандур а. Техред А. Кр авчук Корректор M. Максимишинец
Заказ 6197/29 Тираж 942 Подписное
ВНИИПИ Государственного комитета о изобретениям и открытиям при ГКНТ СССР
113035„ Москва, Ж-35, Раушская наб., д. 4/5
Производственно-издательский комбинат "Патент", г.ужгород, ул. Гагарина, 101
www.findpatent.ru
Твердый карбюризатор - Большая Энциклопедия Нефти и Газа, статья, страница 1
Твердый карбюризатор
Cтраница 1
Твердые карбюризаторы в зависимости от состава имеют различную активность. Наиболее активным считается тот карбюризатор, который при всех прочих равных условиях дает максимальную концентрацию углерода на поверхности цементируемого изделия при небольшой глубине слоя. Наоборот, менее активные карбюризаторы обеспечивают значительно большую глубину слоя при невысокой концентрации углерода на поверхности. [1]
Твердый карбюризатор, применяемый для цементации, должен обладать достаточным цементующим свойством, способностью восстанавливать свои цементующие свойства, механической прочностью и малой усадкой, наименьшим объемным весом и чистотой. [2]
Твердый карбюризатор составляют из древесного угля ( или кокса), смешанного с углекислым барием, с содой или с пота-шем, ускоряющими процесс цементации. По этой же реакции действует окись углерода при газовой цементации. [3]
Наилучшим твердым карбюризатором является такой, в котором содержится 20 - 25 % углекислого бария, 3 5 - 5 0 % углекислого кальция и остальное - березовый или дубовый уголь. [4]
Приготовление твердого карбюризатора производится на специальных установках ( фиг. [5]
Приготовление твердого карбюризатора и очистка от пыли отработавшего карбюризатора должны производиться в отдельном изолированном помещении, оборудованном общей приточной и местной вытяжной вентиляцией от пылящего оборудования. Угольный порошок и химикаты, применяемые для цементации, должны храниться в бункерах с дозирующими устройствами, устраняющими пылеобразование при заполнении ящиков с деталями. Процессы приготовления и транспортировки твердого карбюризатора должны быть механизированы и осуществляться в герметических установках. В помещениях приготовления твердого карбюризатора запрещается курение, применение открытого огня и производство работ, способных вызвать искрообразова-ние. Помещение должно быть оборудовано стационарной угле-кислотной огнегасительнои установкой. Загрузка ( выгрузка) ящиков в цементационные печи должна быть механизирована. [6]
Кроме твердых карбюризаторов, для цементации применяют различные пасты. [8]
Цементация твердым карбюризатором требует длительного времени и является дорогим способом поверхностного упрочнения. [9]
Цементирование твердыми карбюризаторами осуществляется посредством размельченных в порошок: смесей, заключающих в себе, главным образом, уголь. Уголь этот должен быть по возможности чистым, бессернистым и плотным, для чего наиболее пригодным считается древесный - березовый. [10]
Цементация твердыми карбюризаторами заключается в том, что предварительно очищенные детали из низкоуглеродистых сталей ( углерода не более 0 25 %) укладывают в стальные ящики, пересыпают науглероживающим веществом ( карбюризатором, который состоит из древесного угля, углекислого бария и углекислого кальция), затем герметически закрывают и устанавливают в специальную печь. В печи детали нагревают до температуры 800 - 980 С и выдерживают при этой температуре в течение нескольких часов, затем медленно охлаждают. [11]
Цементация твердыми карбюризаторами заключается в том, что изделия из малоуглеродистых сталей с содержанием углерода не выше 0 25 % укладывают в специальные цементационные ящики, пересыпают науглероживающим веществом, называемым карбюризатором, затем герметически закрывают и устанавливают в специальную печь. Изделия в печи нагреваются до температуры 900 - 940 и выдерживаются при этой температуре в течение нескольких часов, затем медленно охлаждаются, после чего они подвергаются закалке и отпуску. Основными факторами, влияющими на результат цементации, являются: температура нагрева изделий, время выдержки, химический состав и качество стали. [12]
Цементация твердым карбюризатором осуществляется следующим образом. Детали закладываются в металлический ящик и пересыпаются карбюризатором. Ящик плотно закрывается крышкой и для герметичности обмазывается огнеупорной глиной. Как же переходит углерод в металл. В ящике всегда имеется немного воздуха. При высокой температуре уголь, соединяясь с кислородом воздуха, дает окись углерода. Этот газ проходит между кусочками угля и, подходя к поверхности металла, разлагается. В этот момент и образуются атомы углерода, которые проникают в поверхность детали. Проникновение атомарного углерода в поверхность науглероживаемых деталей носит название диффузии. [13]
Цементация твердым карбюризатором является наиболее старым способом цементации. Несмотря на невысокую производительность этого способа, его довольно широко применяют в ремонтно-механических цехах, имеющих свои термические участки или мастерские, ввиду несложности и доступности требующегося оборудования. Основной углесодержащей средой в твердых карбюризаторах является древесный уголь. Для активизации процесса науглероживания в карбюризатор добавляют углекислые соли бария или кальция. [14]
Цементацию твердыми карбюризаторами производят в специальных металлических ящиках, наполненных карбюризатором. [15]
Страницы: 1 2 3 4
www.ngpedia.ru
Цементация стали: цель, технология процесса, режимы
Цементация металла – это вид термической обработки металлов с использованием дополнительного химического воздействия. Атомарный углерод внедряется в поверхностный слой, тем самым его насыщая. Насыщение стали углеродом, приводит к упрочнению обогащенного слоя.
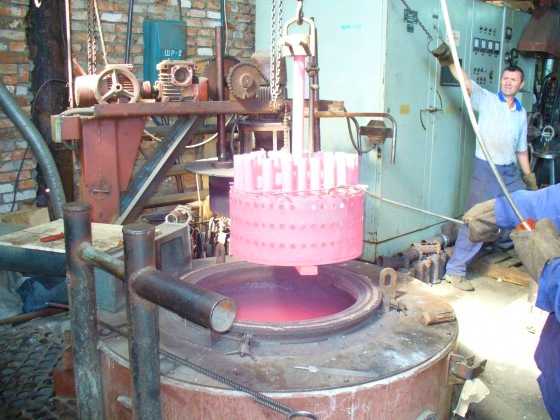
Цементация стали
Процесс цементации
Целью цементация стали является повышение эксплуатационных характеристик детали. Они должны быть твердыми, износостойкими снаружи, но внутренняя структура должна оставаться достаточно вязкой.
Для достижения данных требований требуется высокая температура, среда, выделяющая свободный углерод. Процесс цементации применим к сталям с содержанием углерода не больше двух десятых долей процента.
Для науглероживания слоя наружной поверхности, детали нагревают с использованием печи до температуры в диапазоне 850С — 950С. При такой температуре происходит активизация выделения углерода, который начинает внедряться в межкристаллическое пространство решетки стали.
Цементация деталей достаточно продолжительный процесс. Скорость внедрения углерода составляет 0,1 мм в час. Не трудно подсчитать, что требуемый для длительной эксплуатации 1 мм можно получить за 10 часов.
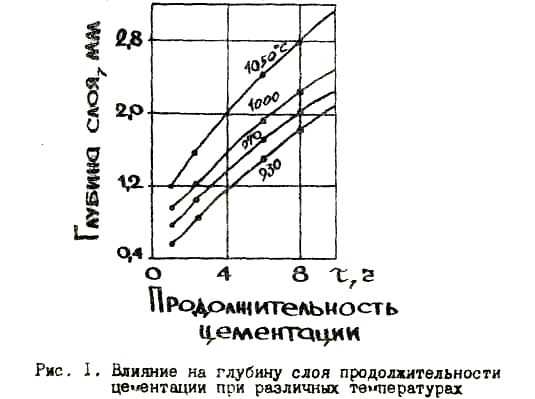
Влияние на глубину слоя продолжительности цементации
На графике наглядно показано на сколько зависит продолжительность по времени от глубины наугрероживаемого слоя и температуры нагрева.
Технологически цементация сталей производится в различных средах, которые принято называть карбюризаторами. Среди них выделяют:
- твердую среду;
- жидкую среду;
- газовую среду.
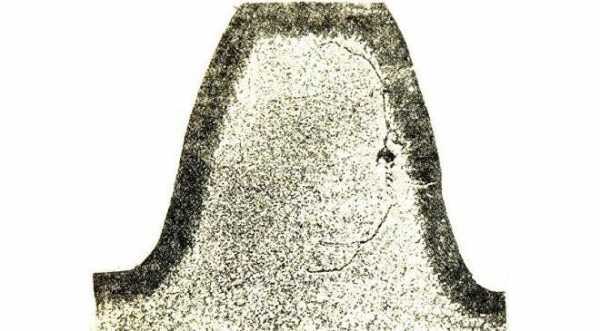
Поверхностный слой, получаемый цементацией
Стали под цементацию обычно берутся легированные или же с низким содержанием углерода: 12ХН3А,15, 18Х2Н4ВА, 20, 20Х и подобные им.
Способы цементации
Цементация получила широкое распространение при обработке зубчатых колес и других деталей, работающих при ударных нагрузках. Высокая твердость рабочих поверхностей обеспечивает продолжительный срок работы, а достаточно вязкая середина позволяет компенсировать ударные нагрузки.
Разработаны множество способов науглероживания. Чаще всего используются следующие:
- в твердой среде;
- в жидкости;
- в газе;
- в вакууме.
Как происходит процесс цементации с использованием твердой среды
В качестве твердого карбюризатора берется смесь древесного угля (береза, дуб) и соли угольной кислоты с кальцием и другими щелочными металлами. Количество древесного угля может достигать 90%. Для приготовления смеси компоненты дробятся для улучшения выхода углерода. Размер частиц не должен превышать 10 мм. Так же не должно быть микроскопических частив в виде пыли и крошек, поэтому смесь просеивается.
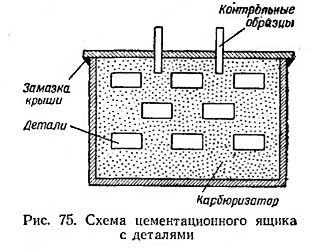
Цементация стали в твердой среде
Для получения готовой смеси пользуются двумя способами. Первый – соль с углем в сухом состоянии тщательно перемешивается. Второй способ – из соли получают раствор. Для этого ее разводят в воде, а после чего этим раствором обильно смачивают древесный уголь. Перед помещением в печь уголь сушат. Его влажность не должна превышать 7%. Получение карбюризатора последним способом более качественно.
Смесь насыпается в ящики. После чего в них помещают детали. Для исключения оттока газа, получаемого во время нагрева, ящики подвергаются герметизации. Плотно закрывающую крышку дополнительно замазывают шамотной глиной.
Ящики подбираются в зависимости от формы детали, их количества и объема засыпанной смеси. Обычно они бывают прямоугольными и круглыми. Материалом для изготовления ящиков может служить сталь как жаростойкая, так и низкоуглеродистая.
Технологический процесс цементации стали можно представить в следующем порядке:
- Детали, предназначенные под цементацию, закладываются в металлические ящики, при этом равномерно пересыпаются угольным составом.
- Ящики герметизируются и подаются в заранее нагретую печь.
- Первоначально производится прогрев до температурных показаний порядка 700С — 800С.
- Контроль прогреваемости производится визуально. Ящики и подовая плита имеют равномерный цвет без затемненных пятен.
- Далее температуры в печи увеличивают до требующихся 850С 950С. В данном диапазоне происходит диффузия внедрения атомов углерода.
- Длительность выдерживания деталей в печи напрямую зависит от требуемой толщины слоя.
Как происходит процесс цементации в газовой среде
Цементация стали в среде газов производится при массовом выпуске деталей. Глубина цементации не превышает 2-х мм. Используемые газы – естественные или искусственные газы, содержащие углерод. Обычно используется газ, получающийся при распаде нефтепродуктов.
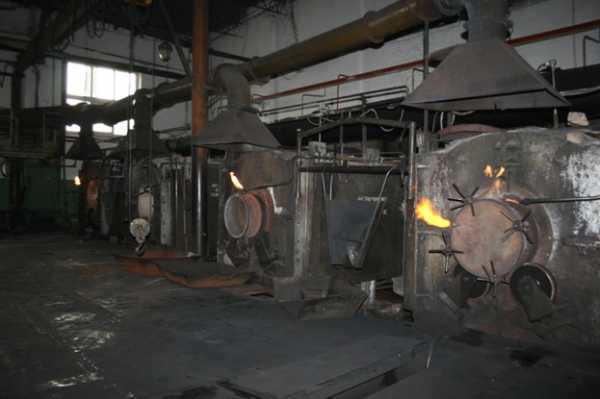
Цементация стали в газовой среде
Его получают в большинстве случаев нагреванием керосина. Больше половины газа подвергают модификации, его крекируют.
Активный углерод при данном способе обработки получается при распаде, и формула имеет следующий вид:
2СО=СО2+С
СН4=2Н2+С
Если пиролизный газ использовался без модифицированного, то в результате обогащенный слой металла будет недостаточным. К тому же пиролизный газ создает обильную сажу.
Печи для данного способа цементации должны быть герметичными. Обычно пользуются стационарными печами, но как вариант методическими.
Цементацию стали и технологический процесс можно представить в следующем порядке:
Подвергаемые цементации изделия помещаются в печь. Температура поднимается порядка 910С — 950С. Производится подача газа в печь. Выдержка в газовой среде определенное время.
Длительность термического воздействия составляет 15 часов при температуре в 920С с получаемым слоем 1,2 мм. Для ускорения производственного процесса температуру поднимают. Уже при 1000С получить такой же науглероженный слой возможно за 8 часов.
В последнее время широкое применение нашел способ проведения процесса в эндотермической среде. Во время активного науглероживания в газовой среде поддерживается значительный потенциал углерода за счет введения природного газа (пропана, бутана или метана). На этот период концентрация газ из нефтепродуктов устанавливается на уровне 1%.
Процесс проведения цементации в жидкой среде
Жидкая среда – это расплавленные соли. В качестве солей используются карбонаты металлов, правда, металлы должны быть щелочными с низкой температурой плавления. Температура проведения цементации при данном методе составляет 850С. Процесс происходит во время погружения деталей в ванну с расплавом и выдерживании их там.
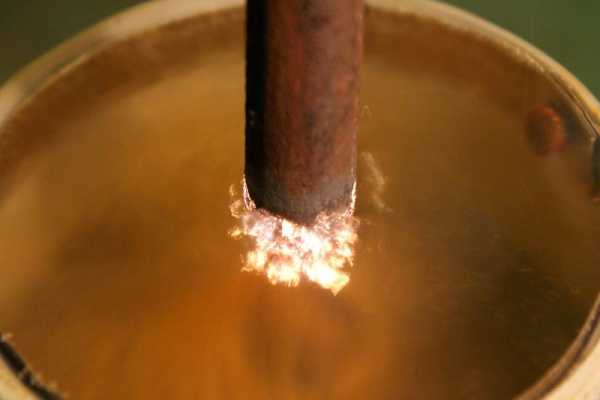
Цементация стали в жидкой среде
Цементация в жидкой среде отличается не большим насыщенным слоем, который не превышает 0,5 мм. Соответственно времени занимает до 3 часов. Среди достоинств следует отметить: обработанные детали имеют незначительную деформацию, а также возможна закалка без промежуточного этапа.
Как происходит процесс цементации в вакууме
Недостаточное давление, создаваемое в печи, значительно сокращает время проведения обработки. Цементацию стали и технологический процесс можно представить в следующем порядке:
- При данном методе детали помещаются в холодную печь.
- После герметизации камеры нагрева в ней создается вакуум.
- Затем производят нагрев до требуемой температуры.
- Производится выдержка, которая занимает до часа по времени. За это время выравнивается температура и с поверхности нагретых деталей осыпаются загрязнения, мешающие науглероживанию.
- Затем подается в камеру углеводородный газ под давлением. За счет чего происходит активная фаза обогащения поверхностного слоя.
- На следующем этапе происходит диффузионное внедрение углерода. На этом этапе в камере опять создают вакуумическое давление.
- За короткий промежуток времени не получается требуемого науглероженного слоя, поэтому процесс повторяют до тех пор, пока не получится требуемая глубина. Обычно результат получается за три стадии.
- Охлаждение до температуры окружающей среды происходит в печи под действием инертных газов под разным давлением.
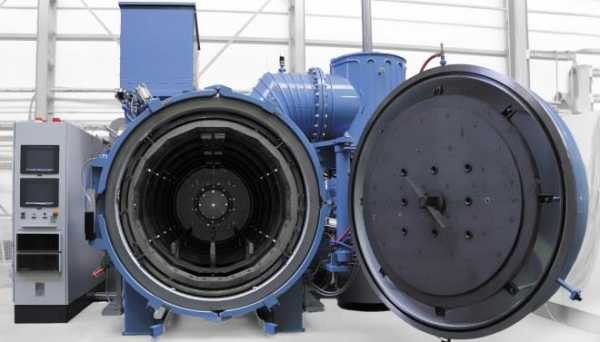
Печь для вакуумной цементации
Процесс полностью компьютеризирован. За подачей газа, температурой, давлением следит программа, отвечающая за весь технологический процесс. Среди достоинств следует отметить:
- регулирование количества углерода;
- отсутствие кислорода предотвращает образование окислов;
- газ проникает даже в отверстия минимального диаметра;
- чередование процессов происходит при равных условиях;
- полная автоматизация; сокращенные сроки.
Процесс проведения цементации пастами
При производстве разовых работ рациональнее пользоваться пастами для проведения цементации. В составе пасты находятся: сажа с пылью древесного угля. Толщина слоя наносимой пасты должна быть восьмикратно увеличена для получения требуемого насыщенного слоя.
После нанесения состав просушивается. Для процесса цементации используются индукционные высокочастотные печи. Температура проведения процесса достигает 1050С.
Как происходит процесс цементации в электролитическом растворе
Процесс во многом схож с гальваническим покрытием. В нагретый раствор электролита помещается заготовка. Подведенный ток вызывает получение активного углерода и способствует его проникновению в поверхность стальной заготовки.
Таким способом подвергают обработке детали, имеющие небольшой размер. Параметры для прохождения цементации: напряжение тока – 150-300В, температура 450-1050С.
Свойства металла после обработки
После проведения цементации твердость науглероженного слоя достигает: 58-61 HRC на легированных сталях и 60-64 HRC на низкоуглеродистых сталях. Длительное нахождение стали при высоких значениях температуры, вызывает изменение структуры металла.
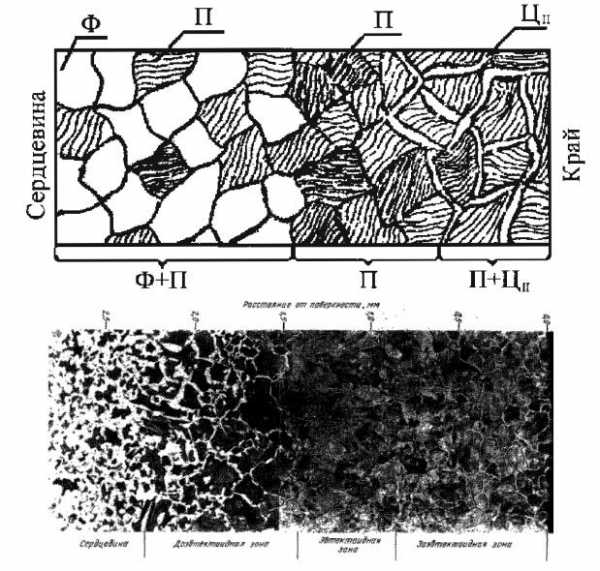
Структура стали после цементации
Для исправления крупного зерна металла детали после цементации подвергаются повторному нагреву и закалке с последующим отпуском или нормализацией.
Закалка производится при температуре, не превышающей 900С. В металле происходит измельчение зерна за счет получения перлита и феррита.
Вместо закалки для легированных сталей производят нормализацию. После сквозного прогрева в середине детали образуется мартенсит. Нагрев детали зависит от марки стали, из которой она была изготовлена.
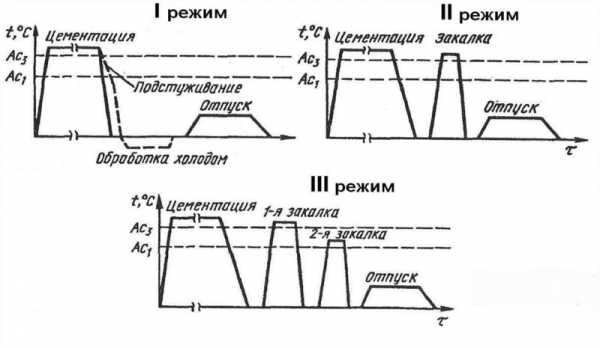
Режимы термической обработки стали после цементации
В качестве заключительной фазы проводят низкотемпературный отпуск, который позволяет устранить поверхностные напряжения и деформации, вызванные высокотемпературной обработкой.
Недостатки цементации
Как было выше сказано основным недостатком после цементации остается изменение структуры металла. В связи с этим требуется дополнительная обработка, что увеличивает время и так длительного процесса цементации.
Для проведения работ требуется обученный и высококвалифицированный персонал. Среди недостатков следует выделить необходимость подготовки карбюризатора.
В заключение стоит отметить, что цементация позволяет использовать, стали с низким содержанием углерода для изготовления ответственных деталей с длительным сроком эксплуатации, что значительно снижает конечную стоимость.
Для защиты поверхностей, не предназначенных под цементацию, пользуются пастами, намеднением или закладывают увеличенные допуски под обработку.
Если вы нашли ошибку, пожалуйста, выделите фрагмент текста и нажмите Ctrl+Enter.
stankiexpert.ru
Способ цементации в твердом карбюризаторе
ОПИСАНИЕ
ИЗОБРЕТЕНИЯ
К АВТОРСКОМУ СВИДЕТЕЛЬСТВУ
Союз Советскнк
Соцналнстнческнк
Республнк
939592 (63) Дополнительное к авт. свид-ву(22) Заявлено 24. 10. 80 (21) 2998620/22-02 с присоединением заявки № (23) Приоритет
Опубликовано 3006.82. Бюллетень ¹ 24
151) М. Кл.
С 23 С 9/06
Государственный комитет
СССР но делам изобретений и открытий (53) УДК 621. 785. .067,5(088,8) Дата опубликования описания 30.06.82
В.К.Афанасьев, Г.Т.Коровин, М.A.Демченйх " " и С.П.Грибин 3
) . с, )
Сибирский металлургический институтим. С.Орджоникидзе (72) Авторы изобретения! с. (7t) Заявитель (54) СПОСОБ ЦЕМЕНТАЦИИ В ТВЕРДОМ
КАРБЮРИЗАТОРЕ
Изобретение относится к химико-тер- мической Обработке в частности к процессу цементации в твердом карбюризаторе.
Цементация в твердом карбюризаторе протекает при нагреве стальных деталей в ящике вместе. с древесным углем, насыщение их поверхности углеродом происходит из газовой фазы, которая образуется при взаимодействии углерода карбюризатора с кислородом воздуха, находящегося в ящике с добавками активиэаторов (ВаСОз, НатСО3, ацетата бария и т.д. ) и с влагой, которая всегда содержится в карбюриэаторе. При этом образуются газы— окись углерода и метан, которые и осуществляют перенос твердого углерода карбюриэатора в сталь 111.
Наиболее близким к предлагаемому является способ цементации в твердом карбюриэаторе (2), включающий нагрев стальных деталей до температуры обработки и выдержку их при этой температуре в твердом карбюризаторе. В качестве карбюризатора используют 25 смесь на основе древесного угля, содержащую, вес.йт
Карбонат бария 20-25
Карбонат кальция 3,5-5
Древесный уголь Остальное 30
Однако процесс цементации в этом карбюризаторе идет недостаточно интенсивно и его можно ускорить.
Цель изобретения — интенсификация процесса цементации в твердом карбюризаторе.
Указанная цель достигается тем, что в способе, включающем нагрев стальных иэделий до температуры обработки и их выдержку при этой температуре в твердом карбюризаторе во время выдержки в твердый карбюризатор выдают 5-20%-ный водный раствор нитрата магния или нитрата алюминия, или их смеси со скоростью 0,25-1,0 мл раствора на 100 г карбюризатора в час.
Цементация по предлагаемому способу значительно увеличивает глубину цементованного слоя при одинаковом времени выдержки. Это обусловлено тем, что вода при температуре цементации разлагается и реагирует- с углеродом карбюриэатора с образованием окиси углерода и метана увеличение концентрации которых в газовой фазе приводит к ускорению цементации. Нитраты магния и алюминия являются поставщиками азота, который также ускоряет диффузию углерода.
939592
Подачу водного раствора во время цементации проводят, равномерно со скоростью 0,25-1,0 мл .раствора на
100 г карбюризатора в 1 ч, эффект ускорения цементации незначителен, а при подаче больше 1 мл раствора.на 5
100 r карбюриэатора в 1 ч. в цементационном ящике образуется газовая атмосфера с низким углеродным потенциалом и возможно окисление поверхности деталей. Оптимальная. концентрация )0 водного раствора нитратов 5-20%. При использовании раствора концентрации менее 5% эффект ускорения цементациинезначителен, из-эа малого количества поступающего с раствором нитрата.
Увеличение концентрации раствора свыше 203 приводит к уменьшению глубины и твердости цементованного слоя, это связано с тем, что с раствором поступает значительное количество кислорода.
Нитрат алюминия и нитрат магния используют отдельно или в смеси при любом соотношении нитратов, поскольку ускоряющее действие их на процессе цементации одинаково.
Пример. Цементации подвергают образцы 15 мм, обработанные на токарном станке, изготовленные иэ сталей 18 ХГТ, СтЗ и Ст35. Образцы
Способ цементации
Глубина слоя, мм Твердость HRC
СтЗ Ст35 18ХГТ СтЗ Ст35 18ХГТ
Известный
0,80
59,0 60,0 60,0
61,0 61,0 62рО
0,70 0,80
1,3 1,4
1,4
4 ч
Предлагаемый
1,20 1,20 60р0 61,0 63,0
1,30
1,35 1,25 1,25 60,0 61,5 63,0
1,20 1,25 61 3 62,0 62,0
li20 (цементация в древесноугольном карбюризаторе (ГОСТ 2407-73) выдержка 2 ч (цементация в твердом карбюриэаторе (ГОСТ
2407-73) с добавками водного раствора а) 5В-ного раствора нитрата магния со скоростью 0,25 мл на 100 г карбюриэатора в час б) 5В-ного раствора нитрата алюминия .со скоростью 1 мл на
100 r карбюризатора в час в) 104-ного раствора нитрата алюминия со скоростью 1 мл на 100 r карбюриэатора в час помещают в металлический контейнер и пересыпают. твердым карбюризато ром. В контейнер вваривают трубу для подачи, водного раствора. Образцы укладывают в контейнер таким образом, чтобы расстояние между образцами и стенкой контейнера было не менее 20-30 мм. Крышку контейнера располагают на противоположной стороне от трубки для подачи водного раствора. Контейнер с упакованными образцами помещают в разогретую до
930-940ОС муфельную.печь.
Цементацию проводят в твердом карбюриэаторе при выдержке 2 и 4 ч (известный способ) и при выдержке
2 ч с подачей водного раствора нитрата.
В таблице показаны примеры цементации при различной концентрации и скорости подачи водного раствора °
Эффективность способа оценивают по глубине и твердости цементованного слоя. Глубину слоя замеряют металлографически по принятой методике до середины переходной зоны. Измерение твердости проводят на закаленных образцах, температура нагрева под закалку 840ОС, охлаждение в воду.
Результаты измерений также приведены в таблице.
939592
Продолжение табллицы
Твердость HRC
Ст3" Ст35 18ХГТ
Глубина слоя, мм
Способ цементации
r) 10%-ного раствора смеси 1:1 нитрата алюминия и нитрата магния со скоростью
0,5 мл на 100 г карбюризатора в час
1,30 д) 5%-ного раствора смеси 3:2 нитрата алюминия и нитрата магния со скоростью
0,75 мл на 100 г кар- . бюризатора в час
1,30 е) 20%-.ного раствора нитрата магния со скоростью 0,25 мл на
100 r карбюризатора в час
1,30
Формула изобретения
Способ цементации в твердом карбюризаторе, включающий нагрев стальных изделий до температуры насыщения
Составитель Н.Шепитько
Техред И. Гайду Корректор В.Синицкая
Редактор И.Ковальчук
Заказ 4605/42 Тираж 1053 Подписное
ВИЛИПИ Государственного комитета СССР по делам изобретений и открытий
113035, Москва, Ж-35, Раушская наб °, д. 4/5
Филиал ППП Патент, r. Ужгород, ул. Проектная, 4
Иэ приведенных примеров, видно, что эффективность способа высокая, время цементации сокращается примерно в 2 раза.
Применение предлагаемого способа на машиностроительных заводах позволит сократить трудовые и энергетические затраты на химико-термическую обработку, при этом механические свойства иэделий не снижаются.
1,25 1,20 61,0 62,0 62,0
1,27 1,25 60,5 61,0 63 0
1,25 1,20 60,0 62,0 62,0 и выдержку их при этой температуре, отличающийся тем, что, с целью интенсификации процесса насыщения, во время выдержки в твердый карбюризатор подают 5-203-ный водный раствор нитрата магния или нит35 рата BJI10MHHHH или их смеси =о скорос» тью 0,25-1 мл на 100 г карбюризатора в 1 ч.
Источники информации, принятые во внимание при экспертизе
1. Котов О.К. Поверхностное упрочнение деталей машины химико-термическими методами. N., Машгиз, 1961, с. 7-9.
2. Справочник металлиста. т.2, М., Машиностроение, 1976, с. 328.
www.findpatent.ru
Карбюризаторы для цементации
Различают цементацию в твердых, жидких и газовых карбюризаторах. Простейшим твердым карбюризатором является древесный уголь, цементация в котором проходит под. воздействием следующих реакций:
Ств + О2 =СО2 ; CO2 + Ств = 2СО; 2СО = Сат + СОз.
При наличии добавок солей Na2CO3, ВаСОз или СаСО3 процесс активизируется за счет дополнительного образования СО и С02: Na2CO3 = Na2O+C02; С02 + Ств = 2СО. При охлаждении происходит частичная регенерация углекислых солей Na2O + CO2 = Na2CO3, и такой карбюризатор достаточно длительное время способен к действию. Основой всех твердых карбюризаторов, применяющихся в промышленности, является древесный уголь твердых пород (береза, дуб и др.), так как уголь мягких пород быстро сгорает. Стандартный (заводского изготовления) карбюризатор состоит также из 12—15% добавок солей ВаСОз и NagCOa (~10:1). Для предохранения от спекания карбюризатора с поверхностью изделий добавляется 1—3% СаСОз.
Добавление 3—5% мазута (или патоки) необходимо для связки компонентов карбюризатора и лучшей адгезии угля с активаторами.
Нежелательным является содержание влаги и серы в таком карбюризаторе, так как эти элементы способствуют разъеданию поверхности деталей. Оптимальным размером гранул карбюризатора считаются фракции 8—12 мм. При отсутствии стандартного заводского карбюризатора возможно его изготовление в местных условиях по тем же рецептам, при отсутствии древесного угля может быть использован торфяной кокс. \
Для целей цементации 100%-ный свежий карбюризатор не применяется вследствие его большой активности, приводящей к пересыщению поверхности углеродом и интенсивному сажевыделению на стальных изделиях. Обычно применяются смеси, состоящие из 80% отработанного и 20% свежего карбюризатора. Упаковка деталей производится в специальные коробки из малоуглеродистых (стойкость 150—200 ч) или жаростойких (стойкость 4000—6000 ч) сталей. При засыпке вокруг детали должен находиться слой карбюризатора от 20 до 30 мм, верхний слой должен составлять 35—40 мм. Коробки закрываются крышками и замазываются глиной, а затем просушиваются — это обеспечивает герметичность и предотвращает подсосы воздуха.
Несмотря на довольно широкое распространение, цементация в твердом карбюризаторе до сих пор обладает существенными недостатками: непроизводительными затратами тепла на прогрев коробок с карбюризатором, отсутствием возможности регулирования концентрации углерода в поверхностном слое вследствие неудовлетворительной стабильности и воспроизводимости результатов; большой трудоемкостью процесса; неоправданно большим расходованием производственных площадей; практической невозможностью механизации и автоматизации процесса; низкой культурой производства.
Цементация в жидких соляных ваннах нашла довольно ограниченное применение, однако оптимальные результаты можно получить при использовании ванны такого состава:
78—85% Na2CO3, 10—15,% NaCI и 6—8% SiC (карборунд), где протекают следующие реакции:
ЗNа2СОз + SiC = Na2SiO3 + 2Na2O + 4СО;
2СО = СОз + Сат.
В такой ванне при 900° в течение 30 мин получается слой глубиной 0,15—0,2 мм. Процесс с большей продолжительностью вести в подобных средах нерационально. Однако эти среды обладают тем преимуществом, что применяемые соли не ядовиты (в отличие от цианистых ванн для цианирования).
Жидкими карбюризаторами являются также углеводородные жидкости: керосин, бензол, этиловый и метиловый спирт (метанол), синтин. В зарубежной практике используются также этилацетат, ацетон, изопропанол и др.
При подаче этих жидкостей в муфельную печь (обычно используются шахтные печи) капельным методом или распылением через форсунки происходит их разложение с образованием газовой фазы, в основном состоящей из СО, На и небольших количеств С02, h3O и СН4. Так, диссоциация метанола идет по реакции СНзОН=СО + 2Н2, образующийся СО далее уже является источником получения атомарного углерода, т. е., вообще говоря, рассмотренные жидкости в принципе являются газовыми карбюризаторами, так как они являются жидкими только до ввода в печь. Из этих карбюризаторов наиболее рекомендуется для отечественного машиностроения синтип, не содержащий вредных сернистых соединений и наименее склонный к сажевыделению.
Однако в серийном производстве наиболее широкое использование находит цементация с применением природного или городского генераторного и нефтяного газов, содержащих 30—90,% СН4, а также эндотермического газа, приготавливаемого в генераторах из природного газа или пропано-бутановых смесей. Большое количество метана в городском или природном газе (70—90%) делает газовый карбюризатор чрезвычайно активным. Основная реакция при науглероживании метаном Ch5 = Сат + 2Н2, однако в равновесии с углеродом γ—Fe при температуре цементации находятся только весьма малые (1—2%) количества этого компонента, поэтому наряду с насыщением стали углеродом до максимальных значений концентрации его в пределах y-твердого раствора при применяемых температурах идет довольно интенсивное сажевыделение по реакции Ch5→Сгр+2Н2. Разбавление метана другими газами положительно сказывается на протекании процесса. Так, например, начинает внедряться процесс так называемой вакуумной цементации. Природный газ или метан подается в печь с небольшим разрежением 30—40 гПа, создаваемым вакуумной системой. При этом процесс протекает с максимальной скоростью при отсутствии сажевыделения, как правило, тормозящего интенсивное протекание процесса взаимодействия газовой среды с поверхностью стали.
Эндотермическая атмосфера состава: 20% СО, 40,% На, СН4 + СО2 = 1%, N2 — остальное, tp = —7 ... 0° С с дополнительными добавками метана (2—10%) или пропана (1—5%) в этом смысле является оптимальной для газовой цементации. Возможность с помощью автоматической системы регулировать состав атмосферы, а следовательно, и углеродный потенциал, дает этому типу газового карбюризатора большие преимущества по созданию стабильного и воспроизводимого технологического процесса цементации с регулируемым содержанием углерода в поверхностном слое. Основные реакции для этой газовой системы Н2—СО—CO2—h3O—СН4 при взаимодействии ее с углеродом γ- твердого раствора были рассмотрены ранее (см. гл. 1). Разработанные для подобных систем диаграммы равновесия позволяют, варьируя соотношение компонентов исходной смеси путем изменения соотношения воздух—газ в генераторе, а также дополнительным регулированием содержания вводимых добавок метана получать заданную активность атмосферы, а следовательно, и заданное равновесное содержание углерода на поверхности.
Прогрессивным процессом цементации в эндотермической атмосфере является комбинированный режим насыщения — вначале (70—80% времени) устанавливается максимально возможный углеродный потенциал атмосферы с помощью добавок, а далее в остальные 20—30,% от времени всего процесса дается рассасывание углерода в поверхности до заданной концентрации. При данном технологическом режиме происходит максимальный выигрыш во времени для этого регулируемого процесса. Газовую цементацию обычно проводят в шахтных печах типа СШЦ, в камерных специализированных агрегатах типа СНЦА, а также в безмуфельных 21, 24 и 40-поддонных агрегатах конструкции ЗИЛа. Расход газа на печь обычно соответствует 5—10-кратному объему атмосферы в час, при избыточном давлении 70—90 гПа.
Для создания одинакового состава атмосферы во всем объеме печи цементационные печи и агрегаты оборудуются специальными вентиляторами.
Выше рассмотрены основные типы карбюризаторов для цементации, однако известен и ряд других способов цементации. К таким способам относится цементация в электролитах ионная цементация в тлеющем разряде и др., однако эти способы промышленного внедрения пока не получили и поэтому рассмотрены здесь не будут.
Дата добавления: 2015-07-08; просмотров: 542 | Нарушение авторских прав
Читайте в этой же книге: ВВЕДЕНИЕ | После преобразования получим | Глава 3. АЗОТИРОВАНИЕ СТАЛИ | Технология азотирования | Стали, подвергаемые азотированию | Свойства азотированной стали | Высокотемпературная нитроцементация | Низкотемпературная нитроцементация | Цианирование стали | Технология процесса хромирования |mybiblioteka.su - 2015-2018 год. (0.007 сек.)mybiblioteka.su
Цементация в газовом карбюризаторе.
Исходную среду для цементации (науглероживания) называют карбюризатором. При газовой цементации в качестве карбюризатора используют разбавленный природный газ (состоящий почти полностью из метана), контролируемые атмосферы, получаемые в специальных генераторах, а также жидкие углеводороды (керосин, бензол и др.), каплями подаваемые в герметичное рабочее пространство печи, где они образуют активную газовую среду. Основная ведущая реакция при наличии метана: СН4=2Н2+С
Участок диаграммы состояния Fe - Fe3C, а также изменение содержания углерода и структуры по толщине цементованного слоя А (схема) tц - температура цементации; t3l> t32 - температура нагрева при первой и второй закалке соответственно.
В зависимости от состава газовой смеси и содержания углерода в стали атмосфера в рабочем пространстве печи может быть науглероживающей, обезуглероживающей и нейтральной. Нейтральному составу соответствует равновесная концентрация углерода на поверхности стали, называемая углеродным потенциалом. Науглероживание будет происходить, если концентрация углерода на поверхности стали будет меньше углеродного потенциала газовой смеси при данной температуре.
Режимы цементации и последующей термической обработки. Для данной марки стали цементацию следует проводить при температуре 1000 °С. Для заданных размеров эффективная толщина цементируемого слоя (за нее принимают сумму заэвтектоидной, эвтектоидной и половины доэвтектоидной зоны) составляет от 1,1 - 1,3 мм. Следовательно, скорость цементации составит 0,75 мм/ч, а время цементации будет составлять 1,2 - 1,7 ч.
Для получения заданного комплекса механических свойств после цементации необходима дополнительная термическая обработка детали. Нужно получить не только высокую поверхностную твердость, но и высокую прочность, а также высокую ударную вязкость. Для обеспечения указанных свойств необходимо мелкое зерно как на поверхности детали, так и в сердцевине. Легирующие элементы данной стали (молибден, вольфрам, ванадий) способствуют уменьшению зерна. Поэтому возможна термическая обработка, состоящая из одной закалки и отпуска, что позволит избежать потери поверхностной твердости. Тем не менее следует проводить две закалки и отпуск, так как это способствует повышению прочности на изгиб.
При первой закалке сталь нагревают до температуры на 30 – 50 °С выше температуры Асз цементируемой стали (1030-1060 °С). При таком нагреве во всём объёме детали образуется аустенит. Нагрев до температур, немного превышающих Асз. вызывает перекристаллизацию сердцевины детали с образованием мелкого аустенитного зерна, что обеспечит мелкозернистость продуктов распада. Чтобы предотвратить выделение цементита, проводят закалку в масле.
При второй закалке деталь нагревают до температуры, превышающей на 30 - 50 °С температуру Aс1. В процессе нагрева мартенсит, полученный в результате первой закалки, отпускается, что сопровождается образованием глобулярных карбидов, которые в определенном количестве сохраняются после неполной закалки в поверхностной заэвтектоидной части слоя, увеличивая его твердость. Вторая закалка обеспечивает также мелкое зерно в науглероженном слое.
Окончательной операцией термической обработки является низкий отпуск при 160 - 200°С, уменьшающий остаточные напряжения и не снимающий твердость стали. После двойной закалки и низкого отпуска поверхностный слой приобретает структуру отпущенного мартенсита с включениями глобулярных карбидов. Сердцевина приобретает структуру бейнита или низкоуглеродистого мартенсита. Из-за низкого содержания углерода будет обеспечена достаточно высокая ударная вязкость.
Рис.7.5. Схема термической обработки ответственных деталей машин после цементация:
studfiles.net
технология процесса, выбор рабочей среды
Во время изготовления металлических конструкций приходится прибегать к различным методам химико-термической обработки. Среди них достаточно распространенным является цементация стали. Этот способ примечателен тем, что может применяться в разных средах при относительно высоких температурах рабочей среды.
Процесс цементации металла — общие сведения
Химико-термическая обработка или цементация, это процедура, при которой на изделия воздействуют высокой температурой при помещении их в жидкую, газовую или твёрдую среду, что делается для придания им измененного химического состава. Причем этот эффект обеспечивает насыщение углеродом поверхностного слоя обрабатываемых объектов. Благодаря такой обработке можно обеспечить изделиям высокие характеристики устойчивости к износу и повышенную твердость. Примечательно то, что сердцевина этих деталей сохраняет свою начальную вязкость.
Эффективность метода цементации наблюдается при условии, что работа проводится с низкоуглеродистыми сталями, в составе которых доля углерода не превышает значения 0,2%. Термическая обработка обеспечивает насыщение поверхностного слоя деталей, причем для этого их помещают в специально подобранную среду, которая может легко выделить активный углерод, где поддерживается температура в диапазоне от 850 до 950 градусов Цельсия.
Создание подобных условий обработки позволяет изменять помимо химического состава обрабатываемых элемента и микроструктуру вместе с фазовым составом. Положительный эффект от такой обработки заключается в повышении прочности, в результате по характеристикам такая деталь не отличается от изделий, прошедших операцию закалки. Для достижения наилучших результатов особое внимание следует уделить грамотному расчету времени, в течение которого деталь должна выдерживаться в создаваемой среде, а также подбору температуры цементации.
Особенностью цементации стали является то, что на эту процедуру уходит достаточно много времени. Чаще всего процесс насыщения поверхности и придания ей специальных свойств проходит со скоростью около 0,1 мм за один полный час выдержки. Многие элементы нуждаются в создании упрочненного слоя толщиной более 0,8 мм, что позволяет говорить о том, что на эту обработку придется потратить как минимум 8 часов. На текущий момент технология цементации металла предусматривает использование нескольких сред:
- газовые;
- пастообразные;
- твердые;
- растворы электролитов;
- кипящий слой.
Обычно при выборе среды для обработки металла используют газовые и твёрдые карбюризаторы.
Цементация металла в твердой среде
В качестве материала для твердого карбюризатора используется смесь углекислого натрия, бария или кальция с древесным углем, который необходимо применять в измельченном виде, представленном фракциями размером порядка 3-10 мм. Причем обязательно эту основу необходимо просеять, чтобы убрать пыль. Обязательной процедурой, которой подвергаются соли, является измельчение с целью придания им порошкообразного состояния, после чего эту массу просеивают через сито.
Для создания смеси могут применяться два основных способа:
- В качестве основных компонентов используется сухая соль и уголь, которые необходимо основательно перемешать друг с другом, тем самым удастся снизить до минимума риск появления пятен во время химико-термической обработки стали;
- На подготовленный древесный уголь нужно лить соль, предварительно смешанную с водой до растворения. Далее созданную на основе этих компонентов массу необходимо поместить для высушивания, причем оптимально, когда влажность смеси не превышает 7%.
Из этих методик наиболее предпочтительной является вторая ввиду ее более высокого качества. Это проявляется в том, что с ее помощью можно создать более равномерную смесь для насыщения поверхности углеродом. В составе готового карбюризатора на долю древесного угля приходится порядка 70-90%, а остальное занимает углекислый кальций и углекислый барий.
Для проведения твердой цементации применяют ящики, куда помещают карбюризатор. Лучше всего использовать ящик, соответствующий форме обрабатываемых изделий. Дело в том, что это поможет улучшить качество цементированного слоя, при этом удастся сократить до минимума время, которое требуется для прогрева тары. Важно позаботиться об отсутствии утечки газов: эту проблему решают путем замазывания ящиков глиной, а затем накрывают сверху герметичными крышками.
Важным моментом является и то, что прибегать к рассматриваемому варианту создания для непосредственного использования тары специальной формы имеет смысл в тех случаях, когда необходимо обработать посредством химико-термического метода большое количество деталей. Наибольшее распространение получили ящики, имеющие стандартную форму, которые различаются геометрическими размерами. Это дает возможность подбирать из них наиболее оптимальный вариант, который в наибольшей степени учитывает количество обрабатываемых изделий и размеры печи.
Обычно ящики изготавливают на основе малоуглеродистой или жаростойкой стали. Причем при выполнении обработки деталей при помощи твердого карбюризатора придерживаются следующей схемы:
- Нуждающиеся в насыщение углеродом детали следует разместить с чередованием в ящике, заполненном заранее приготовленной смесью;
- Далее готовят к работе печь, для чего ее прогревают до температуры 900-950 градусов, затем туда размещается рабочая тара;
- Сама операция по прогреву ящика выполняется при температуре от 700 до 800 градусов. Определить, что ящики прогрелись достаточно, можно по подовой плите, которая должна иметь однородный цвет;
- На заключительном этапе температуру печи увеличивают до отметки 900-950 градусов Цельсия.
Создание указанного температурного режима обеспечивает условия для проникновения диффузии в кристаллическую структуру металла активного углерода. Теоретически этот метод может применяться и для химико-термической обработки зданий, причем отдельные мастера способны справиться с этой задачей и своими силами. Однако в плане эффективности подобная обработка, проводимая в домашних условиях, отличается довольно невысокой эффективностью, причиной чего является долгая обработка и необходимость в создании высокого температурного режима.
Газовая цементация
Авторами теоретических материалов, в которых раскрывается суть подобной цементации, являются С. Ильинский, Н. Минкевич и В. Просвирин. При этом первый опыт практического воплощения имел место на Златоустовском комбинате, где всеми работами руководил П. Аносов.
Особенностью этого метода является использование среды углеродсодержащих газов, в качестве основного рабочего оборудования выступают герметичные нагревательные печи. Среди известных искусственных газов чаще всего используют состав, являющийся результатом разложения нефтепродуктов. Технология его изготовления предусматривает проведение нескольких этапов:
Необходимо взять стальную емкость, нагреть ее и заполнить керосином, далее же приступают к выполнению процесса пиролиза, подразумевающего разложение керосина на смеси газов;
Определенную часть пиролизного газа (примерно 60%) подвергают крекированию, суть которого сводится к изменению состава.
Смесь крекированного газа и чисто пиролизного выступает основой, при помощи которой выполняется химико-термическая обработка, обеспечивающая обогащение углеродом. Заниматься выработкой крекированного газа приходится по той причине, что в случае применения одного пиролизного состава глубина цементирования стали оказывается небольшой, при этом обрабатываемые детали покрываются большим количеством сажи, которую сложно убрать.
В качестве оборудования для выполнения газовой цементации используются конвейерные печи непрерывного действия или же стационарные агрегаты. Детали, которым необходимо придать более прочные характеристики, кладут в муфель печи, а после закрытия доводят температуру внутри до отметки 950 градусов. Далее начинают подавать туда подготовленный газ. Из плюсов этой процедуры, которая отличается на фоне обработки изделий при помощи твердого карбюризатора, необходимо выделить следующие:
- создание более комфортных условий для персонала;
- сокращение времени, необходимого на выполнение обработки, что достигается благодаря уменьшению срока выдерживания деталей и отсутствию необходимости в длительном приготовлении карбюризатора на основе угля.
Цементация в менее популярных карбюризаторах
В ситуации, когда приходится подвергать химико-термической обработке стали 20, 15, а также легированные стали с низким содержанием углерода, допускается использовать следующие карбюризаторы.
Раствор электролита
Суть подобного метода сводится к использованию анодного эффекта, за счет которого можно обогатить при помощи многокомпонентных электролитов углерода изделия, характеризующиеся небольшими размерами. Обработка этих деталей требует создания температурного режима в диапазоне 450-1050 градусов и напряжения 150-300 В. Обязательной операцией является введение в электролит сахарозы, ацетона, глицерина, а также отдельных веществ, имеющих в своем составе углерод.
Кипящий слой
По своей структуре он имеет вид восходящего потока метана и эндогаза, который «пронзает» мелкие частицы корунда, распределяемые на печной газораспределительной решетке.
Пасты
Применение подобного карбюризатора для обработки изделий подразумевает создание на поверхности стальной детали, нуждающейся в обогащении углеродом, слоя пасты, ее последующее просушивание и нагрев током высокой или промышленной частоты. Стоит заметить, что одной цементацией обработку детали не следует заканчивать. Рекомендуемой здесь операцией является термообработка стали в виде отпуска. Также положительный эффект достигается и посредством шлифования металла.
Заключение
Довольно часто определенным конструкциям требуется придать повышенные характеристики прочности, чтобы они смогли успешно выполнять задачу, которая перед ними ставится. Решается же это путем использования различных методов обработки, среди которых достаточно эффективным является цементация металла. При этом для получения необходимого результата нужно учитывать важные особенности этого процесса.
Помимо грамотного подбора рабочей среды, для цементации металла важно в точности следовать технологии проведения подобной обработки. Ведь малейшая ошибка способна негативно повлиять на химический состав изделия, что в дальнейшем может уменьшить срок службы конструкции, в составе которой оно будет применяться. По этой причине важно уделять внимание каждому моменту, не допуская отклонений от действующих норм и правил относительно проведения химико-термической обработки металлических деталей.
Оцените статью: Поделитесь с друзьями!stanok.guru