Измерение и контроль шероховатости поверхности. Контроль шероховатости поверхности
Контроль шероховатости поверхности
При рассмотрении качеств поверхности следует уделить внимание шероховатости. Этот параметр измеряется на момент производства различной продукции различными методами, предусматривающие применение специальных инструментов контроля. Контроль шероховатости поверхности – часть технологического процесса, предусматривающий применение различных методов оценки параметра шероховатости.
Применяемые методы контроля
Шероховатость поверхности может оцениваться самыми различными методами. Контроль может проводится на различных этапах, в некоторых случаях он визуальный, в других предусматривает применение специальных инструментов. Наиболее распространенными методами контроля шероховатости поверхности можно назвать:
- Компараторы.
- Электронные приборы.
- Микроскопы.
- Метод реплик согласно стандартам ISO.
- Профилометр.
- Профилометр Mahr Marsurf PS1 компаратор СА507 + СА3600A
Шероховатость поверхности контролируют в процессе обработки материала или после выпуска продукции при определении его качества. Наиболее доступный метод оценки визуальный, но он не позволяет определить шероховатость поверхности с высокой точность. Визуальный метод не является разновидностью контроля, а только позволяет определить наличие или отсутствие дефектов. Наиболее доступный метод контроля шероховатости поверхности заключается в применении компараторов ISO, технические показатели которого соответствуют установленному стандарту ИСО 8503-1. Для контроля могут использоваться два типа рассматриваемого измерительного инструмента, которые применимы на различных производствах.
Параметры шероховатости
Для того чтобы проводить измерения шероховатости поверхности следует учитывать то, какой параметр при этом учитывается. Проводимый контроль предусматривает проверку совокупности неровностей, которые образуют рельеф на определенном участке.
Рассматривая поверхность определяется шероховатость, которая обозначается Rz или Ra. Шероховатость Rz – показатель 5-ти наиболее возвышенных точек, с которых берутся усредненные значения. Контроль проводят в пределе линии АВ. Шероховатость Ra представляет собой средний показатель арифметических абсолютных значение, которые касаются отклонения профиля поверхности от средней линии в пределах измеряемой базы.
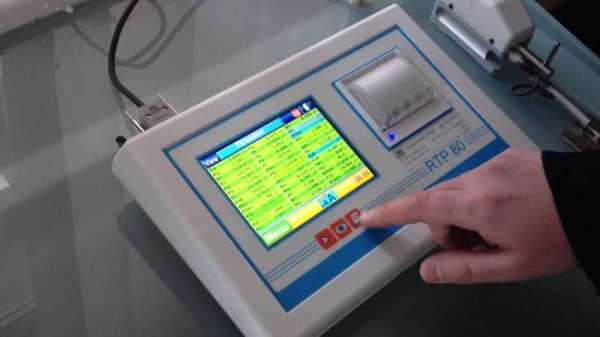
Профилометр ПМ-80 МИКРОТЕХ.
Поверхность оценить визуально для определения всех вышеприведенных показателей практически не возможно. Визуальный способ неприменим в промышленности или в другой производственной деятельности, следует рассматривать особенности инструментального метода определения шероховатости, так как он позволяет определить нужные показатели с высокой точностью.
Методы и средства оценки показателя
Поверхность может иметь самые различные показатели, шероховатость один из наиболее сложных в измерении. Оценивать поверхность, а точнее, рассматриваемый показатель можно двумя наиболее распространенными методами, которые получили название качественный и количественный.
Особенностями качественного метода определения рассматриваемого показателя можно назвать нижеприведенные моменты:
- Визуальный осмотр проводится при наличии эталона. Подобный способ применяется на протяжении многих лет, но сегодня из-за невысокой эффективности встречается крайне редко.
- Поверхность может проверяться при использовании микроскоп или просто визуально. Специалист с высокой вероятностью может на ощупь определить то, к какому классу можно отнести поверхность.
Применение метода визуального осмотра возможно только в случае, есть тонкость обработки поверхности невысока. Контроль рассматриваемым методом определяет использование эталонов, которые должны иметь соответствующую шероховатость. Контролировать показатель можно только в том случае, если эталон изготовлен из того же материала, что и контролируемой детали. При недостаточной эффективности метода контроля при визуальном осмотре используются специальные микроскопы. Но зачастую визуального контроля недостаточно
Контролировать шероховатость можно и количественным методом. Он основан измерение параметра при помощи профилометра и профилографа. Контролировать параметры в данном случае приходится при контакте инструмента с поверхностью.
Профилографы – контактный инструмент, при помощи которого проводится измерение рассматриваемого показателя. Данная методика основана на измерении показателя путем получения изображения микронеровностей профиля. После получения изображения при измерении проводятся определенные расчеты.
Оценка этим прибором проводится следующим образом:
- Он контактный, поверхность ощупывается при помощи алмазной иглы.
- Этот прибор может относиться к оптико-механической группе оборудования. Подобные методики позволяют получить фотографию: деталь ощупывается и изображение наносится на ленту в увеличенном виде. При контактной методике проверка позволяет определить от 4-го до 11-го класс. Проверить подобным способом можно металл и другие материалы.
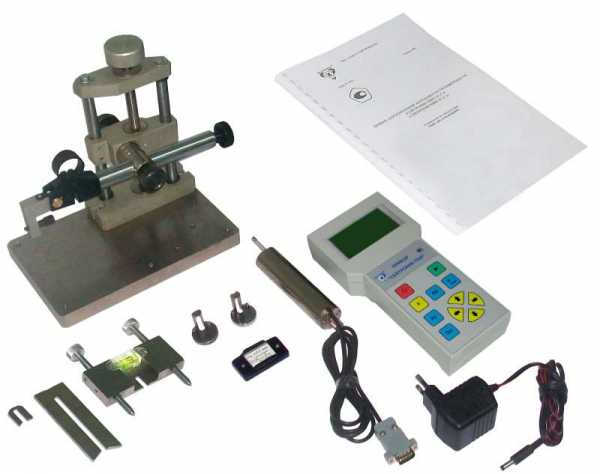
Профилометры: виды и применение
Профилометры – методика, предусматривающая использование инструмента, который не предусматривает получение изображений. Контактный метод позволяет провести точные расчеты для получения нужного результата. Этот инструмент может относиться к контактной группе, имеет следующие особенности:
- Относится оборудование к рассматриваемой группе по причине проверки путем ощупывания поверхности иглой.
- Оценка проводится за счет перемещения иглы вдоль своей оси. При этом оценивается частота и амплитуда колебания. Их определение позволяет определить класс шероховатости.
- Прибор относится к электрическим системам, имеет специальные датчики и процессор для обработки полученной информации. В данном случае для определения Ra или Rz не нужно проводить сложные расчеты. Способ подходит для случая, когда высота микронеровностей находится в пределе от 0,03 до 12 мкм. Можно проверять этим устройство металлы и другие материалы. Определять рассматриваемый показатель данным способом решил В.М. Киселев, который разработал это средство.
Есть довольно много методов определения степени шероховатости. Некоторые средства и методы уже практически не применяются по причине появления более современных инструментов, которые позволяют повысить точность изменения и снизить вероятность ошибки. Некоторое оборудование относится к контактному типу, другие к оптическому и смешанному типу. Выбор зависит от того, насколько высока должна быть точность проведенных измерений.
Если вы нашли ошибку, пожалуйста, выделите фрагмент текста и нажмите Ctrl+Enter.
stankiexpert.ru
5.2 Методы контроля шероховатости поверхностей.
Шероховатость (класс шероховатости) поверхности оценивается путем измерения микронеровностей различными приборами, к числу которых относятся следующие основные: профилометры, профилографы, оптические приборы.
Принцип работы профилометров основан на измерении микронеровностей поверхности путем ощупывания ее алмазной иглой. При перемещении иглы по поверхности обработанной детали игла вследствие неровностей поверхности колеблется вдоль своей оси, причем частота и амплитуда ее колебаний соответствуют шагу и высоте неровностей. Прибор имеет электрическое устройство со специальными датчиками, с помощью которого автоматически определяет величину среднего квадратического отклонения от средней линии профиля обработанной поверхности детали. Шероховатость поверхности оценивается по среднему арифметическому отклонению точек профиля (Rа) и по высоте неровностей Rz. Данные приборы применяют для оценки, шероховатости поверхности с высотой микронеровностей не более 12 мкм и не менее 0,03 мкм. Данный прибор был разработан В.М. Киселевым.
Профилографы также основаны на принципе ощупывания поверхности алмазной иглой. Эти приборы являются оптико-механическими. При помощи оптического устройства профиль поверхности записывается на фотографической ленте в увеличенном виде. На профилограмме увеличение в вертикальном направлении (по высоте) больше, чем в горизонтальном (по длине). К числу таких приборов относятся профилографы К. Л. Аммона и Б. М. Левина: первый рассчитан на измерение шероховатости поверхности от 4-го до 11-го класса, второй — от 3-го до 12-го класса.
Из оптических приборов большее применение нашли двойной микроскоп и микроинтерферометр академика В. П. Линника.
Двойной микроскоп основан на использовании метода «светового сечения»; с его помощью определяют среднюю высоту микронеровностей в пределах 3 – 70 мкм.
Использование микроинтерферометра для измерения неровностей поверхности основано на явлении интерференции света, которое можно наблюдать с помощью специального оптического устройства. Микроинтерферометры применяют в лабораторных условиях для оценки наиболее чистых поверхностей с неровностями высотой в пределах 0,02—2 мкм. Поле зрения у этих приборов малое — до 0,5 мм2.
В производственных условиях шероховатость поверхности деталей часто оценивают путем сравнения их с эталонами чистоты, представляющими собой плоские или цилиндрические образцы, изготовленные из различных материалов (сталь, латунь и др.) с шероховатостью обработанных поверхностей, соответствующей разным классам шероховатости. Наборы образцов – эталонов изготовляют для разных видов механической обработки - точения, фрезерования, шлифования и т.д. Визуальную оценку шероховатости поверхностей деталей, обработанных отделочными методами, при сравнении их с поверхностями эталонов следует производить с помощью лупы с пятикратным или большим увеличением.
Оценку шероховатости поверхности методом сравнения с эталоном можно выполнить более точно, пользуясь сравнительным микроскопом, позволяющим просматривать одновременно обе поверхности - эталона и проверяемой детали.
Контроль - шероховатость - поверхность
Контроль - шероховатость - поверхность
Cтраница 1
Контроль шероховатости поверхностей осуществляют сравнением обрабатываемых поверхностей с образцами шероховатости поверхностей, контактным методом с помощью щуповых приборов ( профилометров и профилогра-фов) и бесконтактным методом с помощью оптических приборов. [1]
Контроль шероховатости поверхности производится с помощью специальных приборов. [2]
Контроль шероховатости поверхности производится по эталону и в необходимых случаях прибором. [3]
Контроль шероховатости поверхностей сравнением с образцами дает надежные результаты для деталей до 6-го класса чистоты включительно, гарантируя выполнение деталей в пределах назначенного класса. [4]
Контроль шероховатости поверхности с помощью образцов осуществляют путем визуального сравнения или на ощупь. Стандарт распространяется на образцы шероховатости, полученные методом механической обработки, снятием позитивных отпечатков гальванопластикой или нанесением покрытий на пластмассовые отпечатки. Стандарт не распространяется на образцовые детали шероховатости поверхности. [5]
Возможен контроль шероховатости поверхностей на основе специальных эталонов, утвержденных в установленном порядке. [6]
Для контроля шероховатости поверхности после хонингования рекомендуется применять контактные щуповые приборы - профи-лометры. С помощью этих приборов можно контролировать шероховатости поверхности деталей из стали, чугуна, цветных металлов и сплавов. Действие такого прибора основано на преобразовании колебаний алмазной иглы при ее движении вдоль образующей измеряемой поверхности в изменение напряжения индуктивного датчика. Московский завод Калибр выпускает профилометры с унифицированной электронной системой мод. Прибор измеряет параметр шероховатости Ra от 10 до 0 02 мкм при наименьшем диаметре измеряемых отверстий 6 мм с глубиной измерения до 20 мм и диаметре 16 мм с глубиной измерения до 130 мм. Этот прибор портативный и может быть использован в цеховых условиях. [7]
Метод контроля шероховатости поверхности с помощью рабочих образцов обычно применяется для относительно грубых поверхностей - примерно до 7-го класса чистоты. [8]
Для контроля шероховатости поверхности в цехе могут быть применены образцы шероховатости и образцовые детали. Чтобы повысить надежность контроля шероховатости по образцам, применяют микроскопы сравнения. [9]
Для контроля шероховатости поверхности режущего инструмента используют приборы и методы, применяемые в общем машиностроении. [11]
Для контроля шероховатости поверхностей режущего инструмента могут использоваться различные методы, применяемые в общем машиностроении. Однако малые размеры шлифованных и доведенных поверхностей на инструменте, их сложная геометрическая форма и неудобное расположение контролируемых поверхностей ( например, на спиральном сверле) затрудняют контроль шероховатости на обычных приборах. [12]
В приборах для контроля шероховатости поверхностей могут быть использованы все приведенные зависимости. Наиболее точным является способ, основанный на определении отношения амплитуд отраженных импульсов, несущие частоты которых различаются в 2 раза. В определенном интервале частот это отношение в значительной степени зависит от шероховатости поверхности. [14]
Весьма важным вопросом контроля шероховатости поверхности является достижение единства измерений на производстве при использовании щуповых приборов различных конструкций. В пре-дыдущих главах были рассмотрены теоретические зависимости, на основе которых можно подсчитать ожидаемое расхождение в показаниях щуповых приборов. [15]
Страницы: 1 2 3 4
www.ngpedia.ru
Методы и средства контроля шероховатости поверхности
Контроль шероховатости поверхности может осуществляться:
1) сравнением (визуально или с помощью микроинтерферометра) реальной поверхности изделия с рабочими образцами
шероховатости, которые имеют стандартизованные значения параметра Ra;
2) измерением параметров шероховатости с помощью щуповых или оптических приборов.
Числовые значения параметров шероховатости определяются либо непосредственно по шкале приборов (профилометров), либо по увеличенному изображению профиля или записанной профилограмме сечения профиля (на приборах – профилографах).
Если в технических требованиях не задано направление измерения шероховатости, то измерения производят в том направлении, где имеется наиболее грубая шероховатость. При механической обработке резанием этому условию соответствует направление измерения, перпендикулярное главному движению при резании (поперечная шероховатость).
Для проведения лабораторной работы используются контактные приборы последовательного преобразования профиля. Эти приборы являются наиболее совершенными для измерения шероховатости поверхности, позволяющими измерить почти все параметры шероховатости, регламентированные ГОСТ 25142 –
82, кроме того, с помощью этих приборов наиболее просто измерять предпочтительный параметр шероховатости Ra.
3.1. Профилометр 283 с унифицированной электронной системой
Профилометр 283 представляет собой контактный щуповой прибор для определения числового значения параметра шероховатости Ra и является высокочувствительным прибором, предназначенным для измерения поверхностей деталей с твердостью не менее НВ 10, сечение которых в плоскости представляет прямую линию.
Принцип действия прибора основан на ошупывании измеряемой поверхности алмазной иглой с радиусом кривизны при вершине 10мкм и преобразовании с помощью механотронного преобразователя механических колебаний иглы в пропорциональные изменения электрического напряжения.
Общий вид профилометра (мод. 283) показан на рис. 4.
Датчик 1 с алмазной ощупывающей иглой закреплен в гнезде штока привода 2. Привод установлен на вертикальной стойке с плитой, на которую устанавливают призму 6 для контролируемой детали.
Привод предназначен для перемещения датчика по измеряемой поверхности и осуществления отсечки шага. Отсечка шага на приводе имеет два значения – 0.8 мм и 0.25мм, соответствующие значениям базовых длин. При отсечке шага
0,25мм скорость перемещения датчика соответствует 0,25мм/с; при отсечке шага 0,8мм – 0,8мм/с; выходные электрические сигналы с датчика поступают на электронный блок 3. Отсчет результатов измерения шероховатости поверхности производится по шкале прибора, которая градуирована по параметру Ra.
3.1.1. Порядок работы на профилометре мод. 283 (рис.4)
Рис. 4. Общий вид профилометра мод. 283
1) установить на призме 6 измеряемую деталь.
2) включить прибор тумблером «сеть». При этом должна загореться сигнальная лампа. Прибор готов к работе через 3-5 мин. после включения в сеть.
3) установить датчик 1, вставленный в привод 2, на измеряемую поверхность детали, при этом, поворачивая маховик стойки 4, добиться совмещения треугольных знаков на штоке и планке привода 7. Застопорить винтом 5 положение датчика.
4) установить на электронном блоке 3 нужный предел измерения, соответствующий заданному параметру шероховатости на чертеже. Переключателем 8 установить заданную отсечку шага, равную базовой длине ℓ.
5) включить нажатием кнопки «пуск» на электронном блоке
3 движение датчика по измеряемой поверхности.
После остановки датчика (сигнальная лампа погаснет) отметить значение параметра шероховатости Ra, зафиксированное стрелкой прибора по выбранной ранее шкале.
Для надежной оценки шероховатости рекомендуется измерения повторить несколько раз в различных местах поверхности. Результатом измерения считается максимальное из всех действительных значений Ra, полученных для данной детали.
3.2. Профилограф – профилометр мод. 252
Профилограф – профилометр мод. 252 является контактным высокочувствительным прибором, предназначенным для измерения шероховатости и волнистости поверхности изделий.
Принцип действия прибора основан на ощупывании исследуемой поверхности алмазной иглой с радиусом кривизны при вершине 10 мкм и преобразовании с помощью дифференциального индуктивного преобразователя механических колебаний иглы в пропорциональные изменения электрического напряжения.
Параметры шероховатости поверхности, определяемые профилографом – профилометром мод. 252:
Ra – среднее арифметическое отклонение профиля,
Hmax – высота наибольшего выступа профиля,
Hmin – глубина наибольшей впадины профиля,
tp – относительная опорная длина профиля,n – число шагов неровностей в пределах длины трассы ощупывания при измерении по базовой линии.
3.2.1.Техническая характеристика прибора
Диапазон измерений профилографа – профилометра по параметрам:
Ra, мкм 0,02 ……..250
Hmax, Hmin 0,1……….100 tp, % 0………….100 n 0………….100
3.2.2. Порядок работы прибора при измерении шероховатости поверхности датчиком с опорой на измеряемую поверхность
Использование прибора в качестве профилометра (рис. 5)
1) на стойке 1 размещен мотопривод 2, на котором с помощью специального разъема следует закрепить датчик 4.
2) включить прибор (кнопка 12 на блоке питания 6) и установить ручку переключателя 15 «Род работы» в положение
«ПП» (настройка прибора).
3) установить ручкой 16 мотопривода скорость движения датчика 60 мм/мин, а ручкой переключателя 25 требуемую длину трассы ощупывания.
4) установить ручкой переключателя 26 требуемый предел измерения и ручкой 24 требуемую отсечку шага, равную базовой длине.
5) вращением маховика 18 опустить датчик на измеряемую поверхность, осторожно, чтобы не повредить иглу, при этом
стрелка индикаторного прибора рабочей зоны 27 должна быть приблизительно в середине шкалы.
Примечание: измерение на приборе возможно, когда стрелка индикаторного прибора рабочей зоны находится в пределах шкалы.
3.2.3. Измерение параметра Ra
1) нажать кнопку «Ra» на счетно-решающем блоке 9, после этого кнопку 21 – «пуск» (зеленого цвета) на блоке питания 6 и после остановки датчика снять показания Ra на цифровом табло счетно-решающего блока 9.
Примечание: при загорании индикаторной лампы 28 «перегрузка» переключить прибор ручкой 26 на режим работы с большим пределом измерения; если значащее число на цифровом табло меньше 90, то перевести прибор на режим работы с меньшим пределом измерения.
3.2.4. Измерение параметра «n»
1) произвести выбор предела измерения по значению параметра Ra.
2) нажать кнопку «n» на счетно-решающем блоке 9 и кнопку 21 «пуск», после остановки датчика снять показания «n».
Примечание: при загорании лампы 28 «перегрузка» ручкой переключателя 25 переключить прибор на более короткую трассу ощупывания.
3.2.5. Измерение параметров Hmax, Hmin
1) нажать кнопку Hmax или Hmin на счетно-решающем блоке 9.
2) опустить датчик на измеряемую поверхность (рабочее положение датчика контролировать по отклонению стрелки индикаторного прибора рабочей зоны 27, которая должна находиться в пределах шкалы).
3) для запуска режима измерения нажать кнопку 21 –
«пуск» (зеленого цвета).
Примечание: при первом проходе датчика на цифровом отсчетном устройстве должны быть зафиксированы нули.
4) нажать кнопку 21 вторично и, после остановки датчика, на цифровом табло счетно-решающего блока 9 снять показания Hmax или Hmin.
Примечание: при загорании лампы 28 переключить прибор на больший предел измерения, а если значащее число на цифровом табло будет менее 90, то переключить на меньший предел измерения.
5) нажать кнопку 21 для следующего измерения.
3.2.6. Измерение параметра «tp»
1) измерить значения «Hmax» и «Hmin».
2) нажать кнопку «tp» на счетно-решающем блоке 9; если значащее число на цифровом табло находится в пределах от
90 до 999, то можно приступить к измерению «tp»; если показания Hmax и Hmin получаются в разных пределах измерения, то необходимо установить больший предел.
3) нажать кнопку 21 – «пуск» (зеленого цвета).
Примечание: при первом проходе датчика на цифровом отсчетном устройстве зафиксированы нули.
4) нажать одну из кнопок 29 требуемого уровня сечения профиля.
5) нажать кнопку 21 на блоке питания и после остановки датчика снять с цифрового табло показание «tp» на установленных уровнях.
3.2.7. Описание прибора
1. Стойка
2. Мотопривод
3. Датчик для измерения отверстий
4. Датчик с опорой
5. Стол
6. Блок питания
7. Блок измерительный
8. Соединительный шланг
9. Блок счетно-решающий
10. Прибор записывающий
11. Приспособление для контролируемой детали
12. Кнопка «включение» на блоке питания
13. Кнопка «реверс» на записывающем устройстве
14. Ручка переключателя вертикального увеличения
15. Ручка переключателя «род работы»
16. Ручка переключателя мотопривода
17. Ручка переключателя скорости движения ленты
18. Маховик
19. Кнопка «включение записывающего устройства»
20. Точная настройка индикатора
21. Зеленая кнопка на блоке питания «пуск»
22. Красная кнопка на блоке питания (аварийная остановка датчика)
23. Кнопка «выключение» на блоке питания
24. Рукоятка переключателя «отсечка шага»
25. Рукоятка переключателя «длина трассы ощупывания»
26. Рукоятка переключателя «предел измерения»
27. Шкала индикатора настройки прибора
28. Индикаторная лампа «перегрузка»
29. Кнопка требуемого уровня сечения профиля
30. Диаграммная бумага
Материал взят из книги Метрология, стандартизация, сертификация (А.И. Аристов)
studik.net
Измерение и контроль шероховатости поверхности.
Аттестация шероховатости поверхности проводят по двум видам контроля:
Качественный контроль параметров шероховатости поверхности осуществляют путем сравнения с образцами или образцовыми деталями визуально или на ощупь.
ГОСТ 9378-75 устанавливает образцы шероховатостей, полученные механической обработкой, снятием позитивных отпечатков гальванопластикой или нанесением покрытий на пластмассовые отпечатки.
Наборы или отдельные образцы имеют прямолинейные, дугообразные или перекрещивающиеся дугообразные расположения неровностей поверхности.
На каждом образце указаны значения параметра Rа и вид обработки образца. Для повышения точности используют щупы и микроскопы сравнения.
Количественный контроль параметров шероховатости осуществляют бесконтактным и контактным средствами измерения.
Для количественной оценки шероховатости поверхности бесконтактным методом используется два способа – увеличение их с помощью оптической системы или использованием отражательных способностей обработанной поверхности.
Приборами, основанными на оценке поверхностных неровностей при увеличении их с помощью оптической системы, являются ”приборы светового сечения”, основанные на отражательной способности (ППС), теневой проекции (ТПС) и интерференции света (МИИ), изготовленные в соответствии с ГОСТ 9847-81.
Принцип действия приборов светового сечения заключается в получении увеличенного изображения профиля измеряемой поверхности с помощью лучей, направленных наклонно к этой поверхности, и измерении высоты неровностей в получаемом изображении. Наиболее распространенным является двойной микроскоп типа МИС-11 и ПСС-2.
Принцип действия микроинтерферометра такой же, как и обычно, но отличается тем, что в качестве одной из поверхностей, которая создает интерференционную картину, используется измеряемая поверхность с малыми неровностями, т.к. на грубых поверхностях интерференцию получить невозможно. В принципе микроинтерферометр представляет сочетание интерферометра и микроскопа (прибор ММИ-4).
Для количественной оценки шероховатости поверхности контактными средствами измерения выделяют профилографы-профилометры и профилометры.
Профилограф-профилометр состоит из двух приборов в зависимости от характера выдаваемой измерительной информации – профилографа и профилометра. Объединяются они вместе для расширения возможностей измерения поверхностных неровностей и в связи с тем, что многие функциональные узлы у них совпадают.
Эти приборы предназначены в основном для работы в лаборатории. Отечественная промышленность изготавливает несколько моделей приборов (201; 202; 252 и др.), связанных на индуктивном методе преобразования колебаний иглы в колебание напряжений.
Профилограф – прибор для измерения величин неровностей поверхности в нормальном к ней сечении в виде профилограммы, обработкой которой определяются параметры, характеризующие шероховатость и волнистость поверхности. В результате измерения на шкале прибора в виде значения одного из параметров, используемых для оценки этих неровностей, по критерию Ra, т.к. оценка шероховатости по параметру Rz связана с трудностями обработки сигнала.
studfiles.net
Контроль шероховатости поверхности
Контроль шероховатости древесины и древесных материалов осуществляется средствами измерения, предусмотренными ГОСТ 15612-85 «Изделия из древесины и древесных материалов. Методы определения параметров шероховатости поверхности». Применяемые средства должны обеспечить получение установленных нормативной документацией характеристик шероховатости. К таким характеристикам для древесины и древесных материалов согласно ГОСТ 7016-82 относятся параметры Rmmax, Rm, Ra и Rz. В соответствии с принятой классификационной схемой приборы и устройства для оценки шероховатости поверхности древесины и древесных материалов делятся на две группы: 1) для измерения шероховатости профильным методом; 2) для оценки шероховатости по поверхности. Они применяются при интегральном методе. В качестве критерия используют образцы сравнения.
Наибольшее практическое значение получили профильные методы, основанные на получении разными способами профиля сечения контролируемой поверхности и оценке ее шероховатости по этому профилю. Чаще получают профиль контролируемой поверхности способом светового сечения поверхности. Имеются две разновидности способа светового сечения поверхности, сущность которого видна из Рис. Один из них контролирует поверхность двойным микроскопом, который имеет два тубуса, расположенных в одной плоскости под углом 45° к контролируемой поверхности. С помощью одного из тубусов на
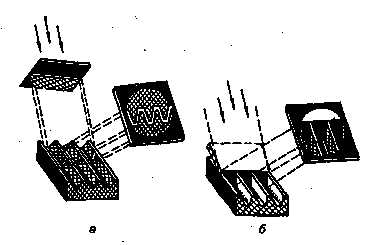
Оптические методы наблюдения профиля поверхности: а — по способу светового сечения; б — по способу «тени от ножа» поверхность проектируется тонкая прямая световая полоса. На неровной поверхности изображение световой полосы оказывается изломанным соответственно профилю поверхности (Рис. а). Изображение световой полосы на поверхности наблюдают через микроскоп и с помощью окулярмикрометра производят измерение неровностей.
При определении шероховатости поверхности по способу «тени от ножа» (Рис.) используется микроскоп теневого сечения (ТСП-4М). По этому способу контролируемая поверхность освещается также под углом 45° пучком света, который падает на лезвие ножа, лежащего на контролируемой поверхности. Кромка ножа отбрасывает на поверхность тень, контуры которой воспроизводят профиль неровностей. Наблюдение и измерение неровностей выполняются, как и в предыдущем случае.
Двойной микроскоп (МИС-11) позволяет измерять в зависимости от объектива неровности высотой 1,5-63 мкм. В основном это поперечные неровности древесины и древесных материалов прессования, плиения, фрезерования, строгания и шлифования. Для контроля более грубых поверхностей с высотой неровностей 60-1600 мкм применяется прибором ТСП-4М. В основном это поперечные и продольные неровности после рамного пиления, лущения и т. п. ...
Оба прибора пригодны для измерения единичных неровностей поверхности и только в случаях, если высота и шаг неровностей поверхности мало отличаются друг от друга. Известно, что эти приборы дают увеличение по высоте неровностей только в 1,4 раза больше увеличения по шагу. Между тем высота неровностей поверхности древесины и древесных материалов в основном на один-два порядка меньше их шага. В этих условиях микроскопы малоэффективны, а использование объективов с различным увеличением результатов не дает.
К приборам для измерения шероховатости профильным методом относятся также щуповые профилометры, профиографы и индикаторный глубиномер, т.е. приборы последовательного преобразования профиля.
Ощупывающим прибором для контроля шероховатости поверхности служит индикаторный глубиномер И402 или И405. При использовании индикаторного глубиномера индикаторную головку закрепляют в колодке так, чтобы ее наконечник выступал над опорной плоскостью на величину хода равную 1,6-2 мм. Прибор устанавливают опорной плоскостью на контролируемую поверхность так, чтобы конец стержня касался дна наибольшей впадины, глубину которой хотят измерить. Индикаторный глубиномер измеряет неровности высотой 500-1600 мкм, т.е. поверхностей, получающихся после рамного пиления, круглопильных станков с большой подачей на зуб и т. п.
Более точные ощупывающие приборы — профилографы и профилометры, в которых щуп (алмазная игла) скользит по контролируемой поверхности, неровности которой вызывают соответствующие им вертикальные колебательные перемещения щупа. Перемещения щупа могут быть записаны на бумаге в виде кривой профиля — профилограммы или зафиксированы на показывающем приборе. Щуповые приборы — профилографы записывают неровности поверхности в виде профилограмм, а щуповые приборы — профилометры дают средний результат измерения неровностей в числовом выражении параметра шероховатости.
Отечественная промышленность выпускает два прибора для измерения параметров профиля технических поверхностей —
гп тэх пазонах 0,02-250 мкм. Профилометр модели 283 контролируй от Ra в диапазонах 0,02-10 мкм. Как уже было сказано, контроль шероховатости поверхности древесных материалов можно выполнить по образцовым деталям. В этом случае контролируемая поверхность сравнивается с поверхность эталона, параметры шероховатости поверхности которого были определены ранее с помощью приборов. Этот способ весьма прост и используется в производственных условиях. Числовые значения параметров шероховатости Rmmax, Rm, Rz, Ra и Sz выбираются по ГОСТ 7016-82, где даны рекомендуемые границы применения параметров по видам обработки. Требования к шероховатости поверхности устанавливаются без учета анатомических неровностей древесины, т.е. не отражают формы неровностей, а также наличия ворсистости или мшистости на поверхности. В тех случаях, когда форма неровности имеет значение, она обусловливается указанием на вид обработки. В технической документации и чертежах на детали и изделия при указании значений параметров должны быть оговорены случаи, когда ворсистость и мшистость на поверхности не допускаются. Требования к шероховатости поверхности в мебельном производстве определяются характером дальнейших операций (например, облицовывание, отделка), а также эксплуатационными требованиями. Так, шероховатость склеиваемых поверхностей для шипа должна быть не более 60 мкм, для гнезда — не более 200 мкм по ГОСТ 7016-82. Шероховатость поверхности плит должна быть не более 200 мкм под облицовывание шпоном строганым или лущеными 60 мкм — под облицовывание пленками на основе бумаг. Шероховатость поверхности деталей, сборочных единиц и изделий мебели, изготовленных из массива древесины, ДСтП, облицованных натуральным шпоном, или из гнутоклееных деталей, подготовленных под отделку нитроцеллюлозными или полиэфирными лаками, должна быть не более 16 мкм. Шероховатость поверхности Rm древесностружечных плит, облицованных шпоном, древесноволокнистой плитой, и деталей и массива, подготовленных под непрозрачную отделку (шпатлевание, окрашивание эмалями и т. п.) — не более 32 мкм. В этом случае от величины параметра шероховатости поверхности зависит трудоемкость обрабатываемой поверхности, ее качество, расход клеевых и лакокрасочных материалов и т. п. Требования к шероховатости поверхности диктуются также ГОСТ 16371-84 «Мебель. Общие технические условия», в котором определены требования к видимым и невидимым поверхностям. Параметр шероховатости видимых при эксплуатации поверхностей деталей из древесины и древесных материалов R, для которых не предусмотрены защитно-декоративные покрытия (например, боковые поверхности выдвижных ящиков), а также невидимых поверхностей, с которыми в процессе эксплуатации соприкасаются человек и предметы, должны быть не более 63 мкм, остальных невидимых поверхностей — не более 200 мкм.Похожие статьи
znaytovar.ru
Контроль шероховатости поверхностей.
Количество просмотров публикации Контроль шероховатости поверхностей. - 521
Шероховатость поверхности проверяется качественным и количественным методами. Параметры шероховатости определяются по профилю поверхности (количественно).
На использовании профильного метода основаны профилометры и профилографы. Профилографом принято называть прибор, записывающий координаты профиля поверхности. Полученная профилограмма несет максимальную информацию о профиле поверхности и является документом для определения параметров. Профилометром принято называть прибор для измерения шероховатости поверхности.
Профилографы и профилометры выпускаются двух типов: А — для измерения прямолинейных поверхностей и Б — для определения шероховатости одной или нескольких непрямолинейных поверхностей.
Оптические приборы работают бесконтактным методом светового сечения, теневой проекции, применением растров, микроинтерференционным методом.
На рабочем месте часто контролируют шероховатость визуально (на глаз) или осязанием (царапаньем ногтем) с помощью лупы или специального микроскопа сравнением изделия с аттестованной деталью или со стандартным образцом шероховатости.
Образцы шероховатости изготовливают с Ra от 10 до 0,02 мкм из стали и чугуна для наружного точения, внутренней расточки, развертывания, торцового и цилиндрического фрезерования, строгания, круглого, плоского, торцового и внутреннего шлифования, полирования, доводки и др. Размещено на реф.рфУчитывая зависимость отвида обработки образцы имеют цилиндрическую или плоскую форму.
Шероховатость недоступных поверхностей проверяют методом слепков, когда специальную массу (целлулоид, легкоплавкие сплавы, гипс-хромпик, лак-цапон, парафин, сера, масляная гуттаперча и др.) с усилием прижимают к контролируемой поверхности и после ее застывания измеряют шероховатость поверхности слепка.
9 Параметры волнистости поверхностей.
Под волнистостью поверхности понимают совокупность периодически повторяющихся неровностей, у которых расстояния между смежными возвышенностями или впадинами превышает базовую длину l, принятую для измерения шероховатости. Волнистость занимает промежуточное положение между отклонениями формы и шероховатостью поверхности.
Высота волнистости Wz — среднее арифметическое из пяти ее значений (W1,W2, …W5), определенных на длине участка измерения LW, равной не менее пяти действительным наибольшим шагам SW волнистости (рис. 3.1):
Wz = (W1 + W2 + W3 + W4 + W5)/5. (5)
Наибольшая высота волнистости Wmax — расстояние между наивысшей и низшей точками измеренного профиля в пределах длины LW, измеренное на одной полной волне.
Средний шаг волнистости SW — среднее арифметическое значение длин отрезков средней линии SWi, ограниченных точками их пересечения с соседними участками профиля волнистости
Обычно волнистость имеет синусоидальный характер из-за колебаний в системе ста-нок—приспособление—инструмент—деталь.
Волнистость нормируется очень редко.
1 Стандартизация подшипников качения.
referatwork.ru