Рекомендуемые режимы резания при резьбонарезании. Подача при нарезании резьбы метчиком
Лекция 17. Нарезание резьбы.
Нарезание резьбы может производиться резьбовыми резцами методом точения, вихревым методом, метчиками или плашками. Резьбовыми резцами нарезаются как крепежные, так и ходовые резьбы. Вихревым методом с помощью специальных вихревых головок нарезаются в большинстве случаев ходовые резьбы на деталях типа ходовых винтов металлорежущих станков. Метчиками и плашками нарезаются, как правило, крепежные резьбы.
Нарезание резьбы резцами(методом точения) может производиться по профильной или генераторной схемам (рис.17.1).
а) б)
Рис.17.1. Нарезание резьбы резцами: а) по профильной и б) генераторной схемам.
Полный профиль резьбы нарезается за несколько проходов резца. После каждого прохода резец совершает холостой ход и возвращается в исходное положение, смещается на величину глубины резания и снова «проходит» по резьбе. Число проходов i зависит от шагаР нарезаемой резьбы и примерно равно удвоенному его значению. Глубина резания равна доле высоты профиля, приходящейся на один проход. Подача равна шагу резьбыР.
Расч¨т оптимальной скорости резания вед¨тся по известной вам формуле расч¨та скорости при точении:
, м/мин.
Основное технологическое время определяется с учетом времени на обратный ход резца и числа заходов резьбы.
,
где: L– длина хода, мм;
p– шаг резьбы, мм;
np.x.– частота вращения шпинделя при рабочем ходе резца, об/мин.;
nx.x.– частота вращения шпинделя при холостом ходе резца, об/мин.;
i– число проходов;
q– число заходов резьбы.
Нарезание резьбы метчиками и плашкамиможет проводиться на токарных, сверлильных и многооперационных станках.
Рис. 17.2.Схемы нарезания резьбы: а) метчиком и б) плашкой.
nм-частота вращения метчика; nu- частота вращения изделия, на котором нарезается резьба.
Главное движение (вращательное) может придаваться как изделию, так и режущему инструменту. Движение подачи – поступательное вдоль оси. Глубина резания равна высоте профиля резьбы, подача – ее шагу.
Вихревое нарезание резьбыосуществляется с помощью специальных вращающихся (вихревых) головок, которые устанавливаются на поперечных салазках токарных станков.
Нарезаемый винт пропускается через отверстие головки и закрепляется в центрах или в патроне и центре задней бабки станка. Главным движением является вращательное движение вихревой головки с закрепленными в ней резцами. Движение круговой подачи придается нарезаемому винту, а продольной – вихревой головке вдоль оси вращения винта. Вихревое нарезание резьбы по сути своей есть процесс фрезерования канавки между витками резьбы.
1 - вихревая головка,
2 - нарезаемое изделие- винт,
3 - резьбовой резец,
Dг- диаметр головки,
d- диаметр изделия нарезаемого винта,
Sкр – круговая подача, мм/зуб,
Sпр– продольная подача, мм/об.
Рис. 17.3. Схема вихревого нарезания резьбы.
Глубина резания при нарезании резьбы за один проход равняется высоте профиля резьбы, а при нарезании за несколько проходов – части профиля.
Величина продольной подачи равняется шагу резьбы:
Скорость резания зависит от частоты вращения вихревой головки:
;
Расч¨т оптимальной скорости резания вед¨тся по формуле:
где: H – высота профиля нарезаемой резьбы, мм;
A – припуск на чистовой проход, мм;
Р – шаг нарезаемой резьбы, мм;
Dг.– диаметр рабочей окружности головки, на которой располагаются вершины резцов головки, мм;
nг – частота вращения головки, об/мин;
sZ – круговая подача, мм./зуб.
Величина круговой подачи на зуб – перемещение поверхности резания за время поворота головки на один зуб, регулируется путем изменения частоты вращения обрабатываемого изделия nu. Величину ее можно определить исходя из следующих рассуждений. За время одного оборота нарезаемого изделия – винта, резцами прорезается канавка длинойl0, в течение одной минуты прорезается канавка длиннойlk вnuраз большая.
;
;
За время одной минуты все резцы сделают Nсрезов, число которых равно произведению числа резцовZ в головке и частоты ее вращенияN=Z. nг.Доля длины канавки, приходящаяся на один срез и есть подача на зубsZ. Для определения ее величины остается лишь разделить длину прорезанной в течение одной минуты канавкиlkна число срезовN, сделанных в течение одной минуты.
;
;
На основании этой зависимости следует назначить частоту вращения изделия (винта) , соответствующую выбранной и принятой величине подачи на зубsZ.
,
где: nu- частота вращения шпинделя станка и нарезаемого винта, об/мин;
sZ— выбранная величина подачи на зуб, мм/зуб;
?— угол подъема резьбы;
Z- число резцов в головке;
nг.— частота вращения головки, об/мин.;
du— наружный диаметр нарезаемой резьбы, мм.
Величина sZвыбирается по таблицам справочной литературы в пределах от 0,4 до 1,2 мм. на зуб в зависимости от механических свойств обрабатываемого материала.
Основное технологическое время определяется по формуле
Вихревое нарезание резьбы обеспечивает высокое качество ее и высокую производительность за счет малого числа проходов.
studfiles.net
Подача - метчик - Большая Энциклопедия Нефти и Газа, статья, страница 1
Подача - метчик
Cтраница 1
Подача метчика должна быть равномерной с минимальной осевой силой. По возможности следует применять принудительную подачу. [1]
Подача метчиков для нарезания резьбы на агрегатных станках производится иногда при неподвижном состоянии силовой головки путем осевого перемещения по копирной гайке каждого шпинделя. Реверсирование метчиков достигается за счет реверсирования двигателя. Выдвижные шпиндели применяются при нарезании отверстий метчиками, имеющими различные размеры; выдвижные шпиндели позволяют производить нарезание резьбы при помощи шпиндельных коробок, установленных на гидравлических силовых головках. [2]
При нарезании резьбы подача метчиков осуществляется по индивидуальным ко-пирным гайкам, шаг которых равен шагу нарезаемой резьбы. Эти гайки закрепляются в копирной плите, устанавливаемой на скалках, которые крепятся к шпиндельной коробке. Для реверсирования электродвигателя в момент окончания нарезания резьбы и для его отключения в исходном положении применяют счетный механизм. Этот механизм имеет вал, кинематически связанный с одним из промежуточных валов шпиндельной коробки, и два бесконтактных конечных выключателя, на которые воздействуют расположенные на валу экраны. Вращение от электродвигателя к резьбонарезным шпинделям передается через электромагнитный тормоз, который включается при выключении электродвигателя. [3]
Неподвижный резьбонарезной агрегат с подачей метчиков индивидуальными маточными гайками ( завод Станкоконструкция): 1 - электродвигатель; 2 - червяк, приводимый от нормализованного шпинделя или валика и вращающий диски с упорами, управляющими с помощью конечных переключателей реверсом и остановкой двигателя 7; 3 - выдвижные оправки, вращающие ходовые винты 4, перемещающие метчики через плавающие по оси патроны; 5 - индивидуальные маточные гайки. [4]
Скос пера обеспечивает совпадение направления схода стружки с направлением подачи метчика. Стружка не скопляется на режущей части, а отводится вниз. Такая конструкция уменьшает величину крутящего момента за счет лучшего резания, правильного отвода стружки и меньшей опасности ее защемления. [5]
При нарезании резьбы в сквозном отверстии стружка выводится из отверстия в направлении подачи метчика. [6]
При нарезании резьбы в сквозном отверстии сгружка выводится из отверстия в направлении подачи метчика ( поз. При нарезании резьбы в глухих отверстиях целесообразно применять метчики с противоположным направлением наклона винтовой канавки ( лоз. [7]
При нарезании резьбы в сквозном отверстии стружка выводится из отверстия в направлении подачи метчика. При нарезании резьбы в глухих отверстиях следует применять метчики с противоположным направлением наклона винтовой канавки, тогда и стружка будет выводиться в противоположном направлении ( фиг. [8]
При нарезании резьбы в сквозном отверстии стружка выводится из отверстия в направлении подачи метчика. [9]
Калибрующая часть / 2 служит для зачистки и окончательной калибровки нарезаемой резьбы, а также для подачи метчика. [10]
Данные устройства приобретают существенное значение не только как ускорители рабочего процесса на станке, но и как точные ограничители подачи метчиков при нарезке резьб в глухих отверстиях. [11]
Кроме того, сверлится и нарезается коническая трубная резьба в отверстии под углом 603 к нижней плоскости. Подача метчиков при нарезке осуществляется по копирным гайкам. [12]
Загрузка контрольного автомата осуществляется специальным загрузочным механизмом, имеющим вид наклонного лотка, в который метчики загружаются вручную рабочим, работающим на резьбонакатном станке, или непосредственно из резьбонакатного автомата при полной автоматизации резьбонакатного станка. Механизм загрузки автомата предназначен для подачи метчиков на подготовительную позицию. Застревание метчика в механизме загрузки наиболее часто происходит в тот момент, когда метчик из лотка выпадает не полностью на подготовительную позицию, что является также причиной остановки автомата. Имеется несколько возможных вариантов конструктивного оформления этого узла. [13]
Такая заточка обеспечивает отвод стружки в направлении подачи метчика. [14]
Метчиками с левыми канавками рекомендуется нарезать резьбу в сквозных отверстиях, а метчиками с правыми винтовыми канавками - резьбу в глухих отверстиях. В этом случае направление движения стружки совпадает с направлением подачи метчика, а нарезание сквозной резьбы значительно улучшается. [15]
Страницы: 1 2
www.ngpedia.ru
Рекомендуемая скорость резания при нарезании резьбы
, мм | 2,5 | 3,0 | 4,0 | 5,0 | 6,0 | 8,0 | 10,0 | 12,0 | 14,0 | |
, м/мин | 3.7 | 4,6 | 5,0 | 5,4 | 6,0 | 6,0 | 6,0 | 6,0 | 6,0 | 12,0 |
подача с самозатягиванием. При нарезании резьбы с самозатягиванием на станке устанавливается подача на оборот, равная шагу нарезаемой резьбы. При подаче с самозатягиванием метчик крепится в специальном «плавающем» патроне. Если нарезание выполняется вручную, то метчик самозатягивается в отверстие. Однако в начальный период обработки метчик требует осевого при-жатия для нарезания в отверстии первых витков резьбы.
Затраты рабочего времени
Затраты времени на изготовление или ремонт деталей, за исключением затрат на обеденный перерыв, подразделяются на нормируемые и ненормируемые. К нормируемым относятся те, которые необходимы для выполнения заданной работы и включаются в состав норм времени.
К ненормируемым относятся потери времени на случайные и непроизводительные работы, на хождение по цеху, на простои из-за отсутствия материалов и электроэнергии, из-за поломки станка, из-за разговоров, перекуров и др.
Время, которое непосредственно затрачивается на выполнение технологической операции, называется оперативным. В табл. 2.7 приведены диаметры сверл, которые следует использовать для сверления отверстий под последующее нарезание метрических резьб. Рекомендуемые скорости резания при нарезании резьб машинно-ручными метчиками приведены в табл. 2.8.
В случае обработки чугуна скорость резания следует увеличить в 1,7 раза, а мягкой стали 10 – уменьшить на 30 %.
Оперативное время разделяется на основное и вспомогательное. Вспомогательное время тратится на действия, которые создают возможность выполнения основной работы: установку и снятие со станка детали, подвод и отвод инструмента, пуск и выключение станка и др. Вспомогательное время определяется по нормативным таблицам, то оперативное время рассчитывается по формулам, используя схему сверлильной обработки (рис. 2.7).
Рис. 2.7. Схема сверлильной обработки
где: ТМ - машинное время;
Li - длина пути инструмента;
- длина обрабатываемой поверхности;
- величины врезания и перебега инструмента;
- минутная подача;
- глубина резания;
- подача на один оборот шпинделя;
- припуск на сторону.
Сумма основного и вспомогательного времени составляет оперативное время:
ТОП = ТО + ТВ.
При определении нормы выработки НВ все временные затраты суммируются и сводятся к норме штучного времени ТШ , которое характеризует количество продукции, изготавливаемой в единицу времени (мин, ч и др.):
НВ = ТСМ / ТШ ,
где: ТСМ – продолжительность рабочей смены, мин, ч.
Вопросы для самопроверки
1. Назовите виды станков для обработки отверстий.
2. Назовите виды инструментов для обработки отверстий.
3. Как оценивается скорость резания при сверлении ?
4. Какие геометрические параметры присущи спиральному сверлу ?
5. Какие геометрические параметры присущи зенкер ?
6. Какие геометрические параметры присущи развертке ?
2.7. Учебные задания
Перечень учебных заданий представлен в табл. 2.9.
infopedia.su
Поиск Лекций
В общем виде выбор режимов резьбонарезания сводится к определению скорости резания, глубины резания, подачи инструмента относительно заготовки, числа рабочих ходов. Для большинства резьбонарезных инструментов – метчиков, резьбонарезных головок, круглых плашек – глубина резания и подача определяются их конструкцией и размером резьбы: подача (осевая) численно равна шагу нарезаемой резьбы, глубина резания определяется конструкцией заборной части. Резьба нарезается за один рабочий ход (плашками). Рассчитывают только скорость резания. Частота вращения заготовки или инструмента при резьбо-нарезании n = 1000 V/(π·d), где V – скорость резания, м /мин; d – диаметр нарезаемой резьбы, мм. Таблица 2.1 Скорость резания при нарезании резьбы метчиками
В табл. 2.1 приведена скорость резания (Vт) при обработке различных материалов машинными метчиками со шлифованным профилем из стали Р6М5. Выбранную скорость резания корректируют с учетом механических характеристик обрабатываемого материала (K1), точности нарезаемой резьбы (K2). Фактическая скорость резания V = Vт K1 K2 Определенная таким образом скорость резания является базовой и может изменяться в зависимости от конкретных условий обработки.
Ниже приведены значения K1.
Значения K2 (при степени точности по ГОСТ 16093 – 81): 4 – K2 = 0,8, 6 – K2 = 1,0; 8 – K2 = 1,2. Скорость резания для гаечных метчиков с изогнутым хвостовиком при нарезании резьб М3 – М30 назначают 10 ÷ 35 м /мин, а для метчиков с С - образным хвостовиком – 40 ÷ 100 м/мин. Конкретное значение скорости резания зависит от условий обработки – марки и твердости обрабатываемого материала, размера резьбы. При нарезании резьбы в гайках, полученных холодной высадкой, из сталей 08, 10, 20, 10Кп рекомендуется следующая скорость резания: для метчиков с изогнутым хвостовиком – 10 ÷ 15 м/мин; для С – образных метчиков – 40 ÷ 60 м/мин. Скорость резания при нарезании резьбы винторезными головками с дисковыми гребенками и круглыми плашками. В табл. 2.2 приведены значения скорости резания (Vт) при нарезании резьбы на заготовках из конструкционных сталей винторезными головками. Фактическая скорость резания V = Vт K1 K2 K3, где K1и K2 выбирают, как для машинных метчиков; K3 – коэффициент, зависящий от угла заборного конуса (φ) гребенок: при φ = 10° K3 = 1,4, при φ = 20° K3 = 1,0, при φ = 30° K3 = 0,5, при φ = 45° K3 = 0,25. При нарезании резьбы круглыми плашками из стали ХВСГ на заготовках из стали скорость резания принимают 4 ÷ 6 м /мин, при обработке заготовок из цветных сплавов 8 ÷ 15 м /мин. Режимы резания при нарезании резьбы резцами. В табл. 2.3 приведены режимы нарезания метрической резьбы напроход резцами с пластинками из твердого сплава Т15К6 на заготовках из конструкционной углеродистой стали, резание – без охлаждения. Движение подачи резца – радиальное врезание. При врезании под углом параллельно одной стороне профиля скорость резания следует увеличить на15%. Поле допуска нарезаемой резьбы 6g, 8g, 6Н, 7Н. При нарезании более точных резьб следуетдобавить два – три рабочих хода.
Таблица 2.2 Скорость резания при нарезании резьбы винтовыми Головками и круглыми плашками
Таблица 2.3 Режимы резания при нарезании резьбы резцами (Т15К6)
В табл. 2.4 приведены режимы нарезания метрической и трапецеидальной резьбы напроход резцами из сталей Р18, Р6М5 на заготовках из конструкционной углеродистой стали. Резание сохлаждением. Скорость резания для калибрующих рабочих ходов V = 4м/мин.
Таблица 2.4 |
|
poisk-ru.ru
НАРЕЗАНИЕ РЕЗЬБЫ МЕТЧИКАМИ И ПЛАШКАМИ
Образование и классификация резьб
Резьба представляет собой винтовую канавку определенного профиля, прорезанную на цилиндрической или конической поверхностях. На токарных станках ее выполняют посредством двух равномерных движений — вращения заготовки и поступательного перемещения режущего инструмента вдоль ее оси. Применяемые резьбы можно разделить на ряд групп: 1) по расположению — на наружные и внутренние; 2) по назначению — на крепежные и ходовые; 3) по форме исходной поверхности — на цилиндрические и конические; 4) по направлению — на правые и левые; 5) по форме профиля — на треугольные, прямоугольные, трапецеидальные, круглые; 6) по числу заходов — на одно и многозаходные. Крепежные резьбы чаще всего имеют треугольный профиль. Они используются для соединения различных деталей.- Ходовые резьбы служат для преобразования вращательного движения в поступательное. К ним относятся резьбы с трапецеидальным и реже прямоугольным профилем. Конические резьбы обеспечивают высокую герметичность соединения и поэтому применяются в местах, находящихся под повышенным давлением жидкостей и газов. У правых резьб винтовая канавка имеет направление по ходу часовой стрелки (если смотреть с торца детали), у левых — наоборот. Однозаходными называются резьбы, имеющие одну винтовую канавку. В многозаходных резьбах выполнено несколько параллельных винтовых канавок, равномерно расположенных по окружности. Число заходов резьбы можно определить по количеству начал винтовых канавок на торце детали.Нарезание резьб круглыми плашками
1. Область применения и инструменты.
Круглые плашки применяются для нарезания наружных резьб треугольного профиля на деталях, к которым не предъявляют высоких требований соосности резьбы с другими поверхностями. Пределы выполняемых резьб ограничиваются механическими свойствами обрабатываемого металла. Так, например, на токарных станках' круглыми плашками нарезают резьбы на стальных деталях с шагом примерно до 2 мм. Для более мягких цветных металлов этот предел может быть увеличен. Резьбы с крупным шагом предварительно прорезают резцом, а затем калибруют плашками. Круглые плашки (рис. 118, а) по внешнему виду напоминают гайку, в которой для создания режущих кромок просверлены стружечные отверстия (от 3 до 8 в зависимости от размера). Рабочая часть плашки для цилиндрических резьб состоит из трех участков: двух крайних — режущих и среднего — калибрующего. Режущие части плашки конические с углом конуса 2ф = 50—60°. Калибрующая часть цилиндрическая, Она придает резьбе окончательные размеры и обеспечивает направление плашке в процессе резания. Геометрическая форма зуба плашки создается передним углом у который выполняют заточкой в пределах 15—20° (для плашек централизованного изготовления). При резании твердых металлов его рекомендуется уменьшать до 10—12°, а для мягких — увеличивать4 до 20—25°. Задний угол а выполняют затылованием только на режущих частях в пределах 6—8°. Для крепления в плашкодержателе или резьбонарезном патроне на наружной поверхности плашки предусмотрены конические углубления и угловой паз. Угловой паз плашки позволяет при необходимости разрезать плашку шлифовальным кругом по перемычке (рис. 118, б) и регулировать ее диаметр в пределах 0,1— 0,3 мм. Круглые плашки общего назначения изготавливаются для следующих резьб: метрических с крупным шагом Ml — М68; метрических с мелкими шагами М1Х0,2 — М135Х6; дюймовых 1/4—2'; трубных 1/8—1l/2'. Плашки должны обеспечить нарезание резьб 2-го класса точности. Плашки для конических резьб более широкие и имеют только одну режущую часть со стороны большего диаметра. Особенность работы плашек состоит в том, что в процессе прорезания винтовой канавки участвует не только режущая, но и калибрующая часть. Такие плашки изготавливаются для резьб от 1/16' до 2'. Плашки выполняются из легированной стали 9ХС или быстрорежущих сталей Р9 и Р18. На плашках маркируются обозначение резьбы, класс точности (только 3-й), марка стали (9ХС не указывается), буква Л для левых резьб.2. Приемы нарезания резьбы плашкой.
Перед нарезанием заготовка чисто обтачивается до размера на 0,1—0,4 мм меньше наружного диаметра резьбы. Большое занижение диаметра заготовки следует выполнять для резьб с большим шагом и более пластичных обрабатываемых металлов. Это делают с целью предотвращения срыва вершинок резьбы вследствие частичного выдавливания металла при резании. Для лучшего центрирования плашки на конце заготовки протачивают небольшую фаску под углом 30—40° к оси. Процесс нарезания цилиндрических резьб плашками имеет некоторые особенности. После того как плашка врежется в заготовку примерно на половину своей ширины, резьба нарезается самозатягиванием. Это означает, что для дальнейшего продвижения плашка не нуждается в принудительной подаче и навинчивается на заготовку, как гайка на винт. Однако в момент врезания плашку необходимо подавать на заготовку равномерным усилием. При этом величина подачи должна быть примерно равна шагу резьбы. В противном случае может произойти срыв первых витков. Кроме того, во время врезания важно совместить плашку с осью заготовки. Этому до некоторой степени помогает центрирующая фаска на заготовке. Если плашка врежется с переносом, профиль нарезаемой резьбы исказится или произойдет срыв витков. Нарезание резьб плашками на токарных станках выполняют с помощью резьбонарезных патронов, одна из конструкций которых приведена на рис. 119. Плашкодержатель 1 и цилиндрическая оправка с конусным хвостовиком 4 соединены подвижно в осевом направлении призматической шпонкой 8, закрепленной винтом 7 в пазу держателя. На цилиндрической части оправки выполнен продольный паз, оканчивающийся кольцевой канавкой 9, в которой установлен подпружиненный упор 10 одностороннего действия. Врезание плашки в заготовку осуществляется подачей держателя 1 вперед поворотом рукоятки 3 с эксцентриком 5. Затем при самозатягивании инструмента держатель скользит по оправке. В конце нарезания резьбы шпонка 8 заскакивает в кольцевую канавку 9 и держатель, увлекаемый плашкой, свободно проворачивается При включении обратного вращения шпинделя шпонка останавливается упором 10 против паза оправки, входит в него и позволяет держателю продвигаться назад во время свинчивания плашки. Патрон настраивается на длину нарезаемой резьбы установкой указателя 2 в необходимое положение по шкале, нанесенной вдоль паза держателя. Сквозной вырез 11 в держателе предназначен для очистки патрона от стружки. Для крепления в патроне плашек меньших размеров в посадочное отверстие держателя 1 устанавливают специальные переходные кольца. Нарезание резьбы плашкой обычно ведется за одну установку непосредственно после подготовки заготовки под резьбу. Для этого следует: 1) убедиться, что пиноль задней бабки и шпиндель станка соосны; 2) установить заднюю бабку возможно ближе к заготовке и закрепить на станине; 3) закрепить плашку в резьбонарезном патроне и установить в пиноль задней бабки; 4) настроить резьбонарезной патрон на требуемую длину нарезания по первой заготовке из партии. После выполнения подготовительных действий плашку подводят к вращающейся заготовке ручной подачей, производят равномерный поджим до нарезания 2—3 полных витков резьбы. После этого подачу прекращают, так как дальнейшее нарезание осуществляется самозатягиванием. Конические резьбы нарезаются с принудительной подачей почти на всей длине обработки. В конце резания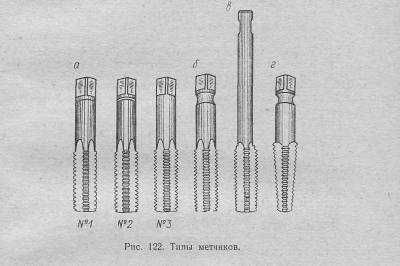
Нарезание резьб метчиками
1. Область применения и инструменты. Метчики, выпускаемые централизованно по действующим стандартам, предназначены для нарезания внутренних крепежных резьб. По форме они делятся на цилиндрические и конические; по назначению—на ручные, машинно-ручные и гаечные; по числу инструментов— на одинарные и комплектные (из 2—3 штук). Комплектные метчики используются для последовательного нарезания всех предусмотренных резьб ручным способом и машинным— резьб с крупным шагом свыше 3 мм и в труднообрабатываемых металлах. Метчик для цилиндрических резьб (рис. 121) состоит из рабочей части и хвостовика. Рабочая резьбовая часть с продольными или реже винтовыми стружечными канавками в свою очередь делится на режущую (коническую) и калибрующую (цилиндрическую) части. Для уменьшения трения калибрующая часть снабжена небольшим обратным конусом 0,05—0,1 мм на 100 мм длины, который выполняется по всему резьбовому профилю. Цилиндрический хвостовик оканчивается квадратом или лысками для передачи усилия резания. С целью создания нормальных условий резания зубьям метчика придают определенную геометрическую форму заточкой. Задний угол а на режущей части создают затылованием по наружному диаметру в пределах 6—10°. Передний угол имеет одинаковую величину на всей длине рабочей части. Его выполняют в зависимости от свойств обрабатываемого материала: для сталей 5—15°; для чугуна • и бронзы 0—5°; для легких сплавов 25—30°. Большие значения в указанных пределах принимают для более мягких материалов. Метчики для цилиндрических резьб выпускаются четырех степеней точности: С, Д, Е и Н. Метчики первых двух степеней точности имеют шлифованный профиль и позволяют нарезать резьбы со-ответственно 1-го и 2-го классов точности. Резьбы 3-го класса точности нарезаются метчиками со степенями точности Е и Н. На рис. 122 изображены основные типы метчиков. Ручные метчики (рис. 122, а) используются для нарезания резьб вручную в сквозных и глухих отверстиях. Иногда их применяют для аналогичных работ на токарных станках. Такие метчики выпускаются комплектами из 2—3 штук. Для распределения нагрузки в комплекте у чернового и среднего метчиков наружный и средний диаметры занижены и удлинена режущая часть соответственно до 6 и 4 ниток. Чистовой метчик имеет полный профиль резьбы и короткую режущую часть — 2 нитки. Порядковый номер метчика в комплекте (кроме чистового) обозначается рисками на хвостовике (см. рис. 122, а). Ручные метчики предусмотрены для нарезания следующих резьб: метрических — до М52; дюймовых — до 2'; трубных — до 1 1/2'. Их изготавливают из сталей У10А — У12А со степенью точности Е и Н. Машинно-ручные метчики (рис. 122, б) предназначены для нарезания резьб в сквозных и глухих отверстиях машинным способом всех предусмотренных размеров и ручным—с шагом до 3 мм включительно; Они изготавливаются двух видов: одинарные для сквозных отверстий с длиной режущей части 6 ниток и для глухих отверстий — 3 нитки; комплектные из 2 штук с числом ниток на режущей части 6 и 2; На хвостовике такие метчики имеют радиусную канавку для крепления в резьбонарезном патроне. Машинно-ручные метчики изготавливаются из стали Р18 по степеням точности С и Д и предназначены для резьб: метрических — до М52; дюймовых и трубных — до 2'. Гаечные метчики (рис. 122, в) применяются для нарезания резьб за один проход в гайках и сквозных отверстиях глубиной не более диаметра. Они отличаются удлиненной режущей частью (12 ниток) и длинным хвостовиком для нанизывания гаек с целью экономии времени на вывинчивание метчика из
отверстия. Изготавливаются из стали Р18 по степеням точности С и Д для резьб: метрических— до диаметра 52 мм,, дюймовых—до 1 1/4. Конические резьбы до 2' нарезаются коническими метчиками (рис. 122, г) за один проход. Калибрующая часть их участвует в резании, поэтому ее затылуют по профилю для создания заднего угла. Материал конических: метчиков — быстрорежущая сталь Р18. На хвостовике: метчиков маркируются обозначение резьбы, номер метчика в комплекте (кроме чистового) посредством рисок, степень точности и марка стали. 2. Приемы нарезания резьб метчиками. Перед нарезанием в заготовке сверлят отверстие размером немного больше внутреннего диаметра резьбы. Такое, завышение диаметра отверстия необходимо для предотвращения срыва вершинок резьбы в результате частичного выдавливания металла в процессе резания. С достаточной для практики точностью диаметр сверл под метрические резьбы можно определить по формуле
где а — наружный диаметр резьбы, мм, S—шаг резьбы, мм: Для других крепежных резьб необходимые диаметры сверл выбирают по соответствующим таблицам справочника. Глубину сверления глухого отверстия под резьбу определяют из ФОРМУЛЫ
где lo — длина резьбы, мм; l1 — длина режущей части метчика, мм;. с — гарантированный зазор в мм, принимаемый не менее шага резьбы. Нарезание резьб метчиками осуществляется аналогично выполнению резьб плашками, Метчик закрепляется в резьбонарезном патроне (см. рис. 119) посредством переходной втулки.2 (рис. 123), в отверстии которой имеются цилиндрический и квадратный участки. Во втулке метчик удерживается штифтом 4, заскакивающим в кольцевую канавку хвостовика под действием пружинного кольца 3. Для крепления метчиков без кольцевых канавок предусмотрен винт 1. Совместно с патроном метчик устанавливают в пиноль задней бабки, ось которой должна быть совмещена с осью шпинделя.
Заднюю бабку закрепляют на станине возможно ближе к заготовке. Затем ручной подачей пиноли метчик подводят к вращающейся заготовке, выполняют врезание на длину 2—3 полных витков поворотом рукоятки патрона. Дальнейшее нарезание ведется самозатягиванием, в течение которого метчик ввертывается в заготовку, как винт в гайку. В конце нарезки резьбы метчик вывинчивается из отверстия включением обратного вращения шпинделя. Настройка резьбонарезного патрона на длину резьбы выполняется, в начале работы по первой заготовке из партии. Если резьба нарезается комплектом метчиков, необходимо соблюдать последовательность их работы и своевременно очищать отверстие от стружки капроновой щеточкой или струей эмульсии перед каждым следующим метчиком. При единичном изготовлении деталей нарезание резьб небольших размеров иногда выполняют ручными метчиками при помощи слесарного воротка 1, как показано на рис. 124. В этом случае метчик с надетым на него воротком опирают центровым отверстием на задний центр, а рукоятку воротка на верхние салазки суппорта. Удерживая метчик левой рукой, подают его вперед пинолью задней бабки. Выполняют врезание метчика в отверстие заготовки на 2—3 полных витка с принудительной подачей. Дальше нарезание осуществляется самозатягиванием, в течение которого метчик следует непрерывно поддерживать центром, так как иначе может произойти перекос и поломка метчика. При нарезании резьбы в глухом отверстии вращение шпинделя выключают немного раньше конца нарезки. Оставшуюся часть дорезают вручную. Скорость резания для нарезания резьб метчиками принимают в следующих пределах: для машинно-ручных и гаечных метчиков — 8—12 м/мин; для ручных —.3—4 м/мин. Охлаждение: по стали — эмульсия, сульфофрезол; по чугуну — керосин.
Автор - nastia19071991
mgplm.org
нарезание резьбы метчиком | Строительный Портал
Образование и классификация резьб
Резьба представляет собой винтовую канавку определенного профиля, прорезанную на цилиндрической или конической поверхностях. На токарных станках ее выполняют посредством двух равномерных движений — вращения заготовки и поступательного перемещения режущего инструмента вдоль ее оси. Применяемые резьбы можно разделить на ряд групп: 1) по расположению — на наружные и внутренние; 2) по назначению — на крепежные и ходовые; 3) по форме исходной поверхности — на цилиндрические и конические; 4) по направлению — на правые и левые; 5) по форме профиля — на треугольные, прямоугольные, трапецеидальные, круглые; 6) по числу заходов — на одно и многозаходные. Крепежные резьбы чаще всего имеют треугольный профиль. Они используются для соединения различных деталей.- Ходовые резьбы служат для преобразования вращательного движения в поступательное. К ним относятся резьбы с трапецеидальным и реже прямоугольным профилем. Конические резьбы обеспечивают высокую герметичность соединения и поэтому применяются в местах, находящихся под повышенным давлением жидкостей и газов. У правых резьб винтовая канавка имеет направление по ходу часовой стрелки (если смотреть с торца детали), у левых — наоборот. Однозаходными называются резьбы, имеющие одну винтовую канавку. В многозаходных резьбах выполнено несколько параллельных винтовых канавок, равномерно расположенных по окружности. Число заходов резьбы можно определить по количеству начал винтовых канавок на торце детали.
Нарезание резьб круглыми плашками
1. Область применения и инструменты.
Круглые плашки применяются для нарезания наружных резьб треугольного профиля на деталях, к которым не предъявляют высоких требований соосности резьбы с другими поверхностями. Пределы выполняемых резьб ограничиваются механическими свойствами обрабатываемого металла. Так, например, на токарных станках’ круглыми плашками нарезают резьбы на стальных деталях с шагом примерно до 2 мм. Для более мягких цветных металлов этот предел может быть увеличен. Резьбы с крупным шагом предварительно прорезают резцом, а затем калибруют плашками. Круглые плашки (рис. 118, а) по внешнему виду напоминают гайку, в которой для создания режущих кромок просверлены стружечные отверстия (от 3 до 8 в зависимости от размера). Рабочая часть плашки для цилиндрических резьб состоит из трех участков: двух крайних — режущих и среднего — калибрующего. Режущие части плашки конические с углом конуса 2ф = 50—60°. Калибрующая часть цилиндрическая, Она придает резьбе окончательные размеры и обеспечивает направление плашке в процессе резания. Геометрическая форма зуба плашки создается передним углом у который выполняют заточкой в пределах 15—20° (для плашек централизованного изготовления). При резании твердых металлов его рекомендуется уменьшать до 10—12°, а для мягких — увеличивать4 до 20—25°. Задний угол а выполняют затылованием только на режущих частях в пределах 6—8°. Для крепления в плашкодержателе или резьбонарезном патроне на наружной поверхности плашки предусмотрены конические углубления и угловой паз. Угловой паз плашки позволяет при необходимости
разрезать плашку шлифовальным кругом по перемычке (рис. 118, б) и регулировать ее диаметр в пределах 0,1— 0,3 мм. Круглые плашки общего назначения изготавливаются для следующих резьб: метрических с крупным шагом Ml — М68; метрических с мелкими шагами М1Х0,2 — М135Х6; дюймовых 1/4—2″; трубных 1/8—1l/2″. Плашки должны обеспечить нарезание резьб 2-го класса точности. Плашки для конических резьб более широкие и имеют только одну режущую часть со стороны большего диаметра. Особенность работы плашек состоит в том, что в процессе прорезания винтовой канавки участвует не только режущая, но и калибрующая часть.
Такие плашки изготавливаются для резьб от 1/16″ до 2″. Плашки выполняются из легированной стали 9ХС или быстрорежущих сталей Р9 и Р18. На плашках маркируются обозначение резьбы, класс точности (только 3-й), марка стали (9ХС не указывается), буква Л для левых резьб.
2. Приемы нарезания резьбы плашкой.
Перед нарезанием заготовка чисто обтачивается до размера на 0,1—0,4 мм меньше наружного диаметра резьбы. Большое занижение диаметра заготовки следует выполнять для резьб с большим шагом и более пластичных обрабатываемых металлов. Это делают с целью предотвращения срыва вершинок резьбы вследствие частичного выдавливания металла при резании. Для лучшего центрирования плашки на конце заготовки протачивают небольшую фаску под углом 30—40° к оси. Процесс нарезания цилиндрических резьб плашками имеет некоторые особенности. После того как плашка врежется в заготовку примерно на половину своей ширины, резьба нарезается самозатягиванием. Это означает, что для дальнейшего продвижения плашка не нуждается в принудительной подаче и навинчивается на заготовку, как гайка на винт. Однако в момент врезания плашку необходимо подавать на заготовку равномерным усилием. При этом величина подачи должна быть примерно равна шагу резьбы. В противном случае может произойти срыв первых витков. Кроме того, во время врезания важно совместить плашку с осью заготовки. Этому до некоторой степени помогает центрирующая фаска на заготовке. Если плашка врежется с переносом, профиль нарезаемой резьбы исказится или произойдет срыв витков.
Нарезание резьб плашками на токарных станках выполняют с помощью резьбонарезных патронов, одна из конструкций которых приведена на рис. 119. Плашкодержатель 1 и цилиндрическая оправка с конусным хвостовиком 4 соединены подвижно в осевом направлении призматической шпонкой 8, закрепленной винтом 7 в пазу держателя. На цилиндрической части оправки выполнен продольный паз, оканчивающийся кольцевой канавкой 9, в которой установлен подпружиненный упор 10 одностороннего действия. Врезание плашки в заготовку осуществляется подачей держателя 1 вперед поворотом рукоятки 3 с эксцентриком 5. Затем при самозатягивании инструмента держатель скользит по оправке. В конце нарезания резьбы шпонка 8 заскакивает в кольцевую канавку 9 и держатель, увлекаемый плашкой, свободно проворачивается
При включении обратного вращения шпинделя шпонка останавливается упором 10 против паза оправки, входит в него и позволяет держателю продвигаться назад во время свинчивания плашки. Патрон настраивается на длину нарезаемой резьбы установкой указателя 2 в необходимое положение по шкале, нанесенной вдоль паза держателя. Сквозной вырез 11 в держателе предназначен для очистки патрона от стружки. Для крепления в патроне плашек меньших размеров в посадочное отверстие держателя 1 устанавливают специальные переходные кольца. Нарезание резьбы плашкой обычно ведется за одну установку непосредственно после подготовки заготовки под резьбу. Для этого следует: 1) убедиться, что пиноль задней бабки и шпиндель станка соосны; 2) установить заднюю бабку возможно ближе к заготовке и закрепить на станине; 3) закрепить плашку в резьбонарезном патроне и установить в пиноль задней бабки; 4) настроить резьбонарезной патрон на требуемую длину нарезания по первой заготовке из партии. После выполнения подготовительных действий плашку подводят к вращающейся заготовке ручной подачей, производят равномерный поджим до нарезания 2—3 полных витков резьбы. После этого подачу прекращают, так как дальнейшее нарезание осуществляется самозатягиванием. Конические резьбы нарезаются с принудительной подачей почти на всей длине обработки. В конце резания
станок переключают на обратное вращение шпинделя и свинчивают плашку. Иногда приходится нарезать длинные резьбы, выполнить которые при помощи резьбонарезного патрона невозможно. В таком случае плашку можно закрепить в слесарном плашкодержателе (рис. 120, а) и производить нарезание, как показано на рис. 120, б. Плашкодержатель удерживают левой рукой за рукоятку, которую опирают на верхние салазки суппорта или стержень, закрепляемый продольно в резцедержателе. Включив вращение шпинделя, правой рукой вращают маховичок задней бабки и пинолью подают плашку вперед. Убедившись, что конус режущей части плашки совместился с центрирующей фаской заготовки, производят врезание на 2—3 полных витках с принудительной подачей. После чего поджим плашки прекращают, так как нарезание продолжается самозатягиванием. По окончании нарезания включают обратное вращение шпинделя для свинчивания плашки. Если резьба нарезается до уступа, вращение шпинделя следует выключать, когда до окончания нарезания остается несколько витков, которые затем дорезают вручную. Для нарезания резьб плашками рекомендуются следующие скорости
по стали 2—4 м/мин; по цветным металлам — 8—12 м/мин. Нарезание следует выполнять с применением смазывающе-охлаждающих жидкостей: для сталей — эмульсии или сульфофрезола; для алюминиевых сплавов— керосина.
Нарезание резьб метчиками
1. Область применения и инструменты. Метчики, выпускаемые централизованно по действующим стандартам, предназначены для нарезания внутренних крепежных резьб. По форме они делятся на цилиндрические и конические; по назначению—на ручные, машинно-ручные и гаечные; по числу инструментов— на одинарные и комплектные (из 2—3 штук).
Комплектные метчики используются для последовательного нарезания всех предусмотренных резьб ручным способом и машинным— резьб с крупным шагом свыше 3 мм и в труднообрабатываемых металлах. Метчик для цилиндрических резьб (рис. 121) состоит из рабочей части и хвостовика. Рабочая резьбовая часть с продольными или реже винтовыми стружечными канавками в свою очередь делится на режущую (коническую) и калибрующую (цилиндрическую) части. Для уменьшения трения калибрующая часть снабжена небольшим обратным конусом 0,05—0,1 мм на 100 мм длины, который выполняется по всему резьбовому профилю. Цилиндрический хвостовик оканчивается квадратом или лысками для передачи усилия резания. С целью создания нормальных условий резания зубьям метчика придают определенную геометрическую форму заточкой. Задний угол а на режущей части создают затылованием по наружному диаметру в пределах 6—10°. Передний угол имеет одинаковую величину на всей длине рабочей части. Его выполняют в зависимости от свойств обрабатываемого материала: для сталей 5—15°; для чугуна • и бронзы 0—5°; для легких сплавов 25—30°. Большие значения в указанных пределах принимают для более мягких материалов. Метчики для цилиндрических резьб выпускаются четырех степеней точности: С, Д, Е и Н. Метчики первых двух степеней точности имеют шлифованный профиль и позволяют нарезать резьбы со-
ответственно 1-го и 2-го классов точности. Резьбы 3-го класса точности нарезаются метчиками со степенями точности Е и Н. На рис. 122 изображены основные типы метчиков. Ручные метчики (рис. 122, а) используются для нарезания резьб вручную в сквозных и глухих отверстиях. Иногда их применяют для аналогичных работ на токарных станках. Такие метчики выпускаются комплектами из 2—3 штук. Для распределения нагрузки в комплекте у чернового и среднего метчиков наружный и средний диаметры занижены и удлинена режущая часть соответственно до 6 и 4 ниток. Чистовой метчик имеет полный профиль резьбы и короткую режущую часть — 2 нитки. Порядковый номер метчика в комплекте (кроме чистового) обозначается рисками на хвостовике (см. рис. 122, а). Ручные метчики предусмотрены для нарезания следующих резьб: метрических — до М52; дюймовых — до 2″; трубных — до 1 1/2″. Их изготавливают из сталей У10А — У12А со степенью точности Е и Н. Машинно-ручные метчики (рис. 122, б) предназначены для нарезания резьб в сквозных и глухих отверстиях машинным способом всех предусмотренных размеров и ручным—с шагом до 3 мм включительно; Они изготавливаются двух видов: одинарные для сквозных отверстий с длиной режущей части 6 ниток и для глухих отверстий — 3 нитки; комплектные из 2 штук с числом ниток на режущей части 6 и 2; На хвостовике такие метчики имеют радиусную канавку для крепления в резьбонарезном патроне. Машинно-ручные метчики изготавливаются из стали Р18 по степеням точности С и Д и предназначены для резьб: метрических — до М52; дюймовых и трубных — до 2″. Гаечные метчики (рис. 122, в) применяются для нарезания резьб за один проход в гайках и сквозных отверстиях глубиной не более диаметра. Они отличаются удлиненной режущей частью (12 ниток) и длинным хвостовиком для нанизывания гаек с целью экономии времени на вывинчивание метчика из
отверстия. Изготавливаются из стали Р18 по степеням точности С и Д для резьб: метрических— до диаметра 52 мм,, дюймовых—до 1 1/4. Конические резьбы до 2″ нарезаются коническими метчиками (рис. 122, г) за один проход. Калибрующая часть их участвует в резании, поэтому ее затылуют по профилю для создания заднего угла. Материал конических: метчиков — быстрорежущая сталь Р18. На хвостовике: метчиков маркируются обозначение резьбы, номер метчика в комплекте (кроме чистового) посредством рисок, степень точности и марка стали. 2. Приемы нарезания резьб метчиками. Перед нарезанием в заготовке сверлят отверстие размером немного больше внутреннего диаметра резьбы. Такое, завышение диаметра отверстия необходимо для предотвращения срыва вершинок резьбы в результате частичного выдавливания металла в процессе резания. С достаточной для практики точностью диаметр сверл под метрические резьбы можно определить по формуле
где а — наружный диаметр резьбы, мм, S—шаг резьбы, мм: Для других крепежных резьб необходимые диаметры сверл выбирают по соответствующим таблицам справочника. Глубину сверления глухого отверстия под резьбу определяют из ФОРМУЛЫ
где lo — длина резьбы, мм; l1 — длина режущей части метчика, мм;. с — гарантированный зазор в мм, принимаемый не менее шага резьбы. Нарезание резьб метчиками осуществляется аналогично выполнению резьб плашками, Метчик закрепляется в резьбонарезном патроне (см. рис. 119) посредством переходной втулки.2 (рис. 123), в отверстии которой имеются цилиндрический и квадратный участки. Во втулке метчик удерживается штифтом 4, заскакивающим в кольцевую канавку хвостовика под действием пружинного кольца 3. Для крепления метчиков без кольцевых канавок предусмотрен винт 1. Совместно с патроном метчик устанавливают в пиноль задней бабки, ось которой должна быть совмещена с осью шпинделя.
Заднюю бабку закрепляют на станине возможно ближе к заготовке. Затем ручной подачей пиноли метчик подводят к вращающейся заготовке, выполняют врезание на длину 2—3 полных витков поворотом рукоятки патрона. Дальнейшее нарезание ведется самозатягиванием, в течение которого метчик ввертывается в заготовку, как винт в гайку. В конце нарезки резьбы метчик вывинчивается из отверстия включением обратного вращения шпинделя. Настройка резьбонарезного патрона на длину резьбы выполняется, в начале работы по первой заготовке из партии. Если резьба нарезается комплектом метчиков, необходимо соблюдать последовательность их работы и своевременно очищать отверстие от стружки капроновой щеточкой или струей эмульсии перед каждым следующим метчиком. При единичном изготовлении деталей нарезание резьб небольших размеров иногда выполняют ручными метчиками при помощи слесарного воротка 1, как показано на рис. 124. В этом случае метчик с надетым на него воротком опирают центровым отверстием на задний центр, а рукоятку воротка на верхние салазки суппорта. Удерживая метчик левой рукой, подают его вперед пинолью задней бабки. Выполняют врезание метчика в отверстие заготовки на 2—3 полных витка с принудительной подачей. Дальше нарезание осуществляется самозатягиванием, в течение которого метчик следует непрерывно поддерживать центром, так как иначе может произойти перекос и поломка метчика. При нарезании резьбы в глухом отверстии вращение шпинделя выключают немного раньше конца нарезки. Оставшуюся часть дорезают вручную. Скорость резания для нарезания резьб метчиками принимают в следующих пределах: для машинно-ручных и гаечных метчиков — 8—12 м/мин; для ручных —.3—4 м/мин. Охлаждение: по стали — эмульсия, сульфофрезол; по чугуну — керосин.
Статья прочитана 130 раз(a).
skosr.ru
Операция 010 - нарезание резьбы
⇐ ПредыдущаяСтр 5 из 7Следующая ⇒Исходные данные:
1. Деталь: передняя крышка блока цилиндров КАМАЗ-740;
2. Материал: алюминиевый сплав АЛ4;
4. Размеры обрабатываемой поверхности: нарезать резьбу М10х1,25;
5. Оборудование: вертикально-сверлильный станок 2Н-135, тиски;
6. Режущий инструмент: специальный метчик.
Операция 010 резьбонарезная
Таблица 5
№ перехода | Содержание перехода |
Установить деталь. Нарезать резьбу под спиральную вставку М10х1,25 мм на глубину 15мм. Снять деталь. |
Расчет режимов резания
Скорость резания выбирают по таблице Vрез=7,2м/мин.
Табличное значение скорости резания корректируют с учетом условий обработки детали.
где Км = 1,2 – учитывает марку обрабатываемого материала (табл. 4,5)
Кмр = 0,8 – учитывает материал режущей части метчика (табл. 6)
Кх=1– учитывает характер заготовки и состояние ее поверхности (табл. 7)
Kох = 0,8 – учитывает применение охлаждения (табл. 8)
Определяем число оборотов детали
,
Назначают фактическое число оборотов детали по паспорту станка:
n=285об/мин, n0=450об/мин
Определяем основное время:
Машинное время Т0 при нарезании резьбы метчиком определяют по следующим формулам:
где L =12– глубина (длина) нарезаемого отверстия, мм;
l1 = 2 – длина заборной (режущей) части, равная (1÷3) ⋅ S,мм;
l2 = 3 – величина перебега, равная (2÷3) ⋅ S,мм;
n – частота вращения метчика при рабочем ходе , мин ;
n0 – частота вращения метчика при обратном ходе, мин ;
S = 1,25 – шаг нарезаемой резьбы, мм.
Рассчитываем основное время То.
Определяем вспомогательное время:
Тв = Тсув + Тпрв = 0,5+0,2 = 0,7мин;
Тсув = 0,5мин (Л-3 с.102, табл.65).
Тпрв= 0,2мин.
Определяем дополнительное время
Тд= К× (Т0 + Тв)/100 = 6× (0,08+0,7)/100 = 0,047мин.
К – процент дополнительного времени, К=6% для сверлильных работ ([3], табл. 7).
Определяем штучное время на обработку одной детали:
= 0,08+ 0,7 + 0,047 = 0,83мин.
Норма времени определяем по формуле:
Тnз= 8 – подготовительно-заключительное время (время на получение задания, ознакомление с чертежом, наладка инструмента и т.д.), определяется по таблицам [3, 5], мин.
Х =50 – размер производственной партии деталей, шт.
Получаем:
Тн = 0,08 + 0,7 + 0,047 + 8/50 = 0,99мин.
mykonspekts.ru