Основы техники сварки металлов полуавтоматом и инвертором. Полуавтомат дуговой сварки
Как выполняется сварка полуавтоматом: советы по свариванию металла
Сварка полуавтоматом – один из самых удобных способов соединения металлических изделий, особенно для новичков. Полуавтоматическая дуговая сварка происходит за счет плавления электрода, который ведется автоматическим способом. Сейчас рассмотрим основные аспекты, как работает механизированное оборудование и как варить металл с помощью такого аппарата.
Содержание статьи
Типы полуавтоматического сварочного оборудования
Сварка полуавтомат делится на несколько видов, в зависимости от типа материала и перемещения по рабочему изделию. Основная характеристика:
- мобильность: переносные: передвижные и стационарные аппараты. Большое стационарное оборудование применяется в специализированных мастерских для выполнения больших объемов работы. Маленькие агрегаты отлично подходят для домашнего использования соединения небольших площадей изделий;
- защита шва: порошковой проволокой, флюсом, газом. При подаче проволоки, она плавится и образует защитный слой, который оберегает расплавленное железо от агрессивных факторов воздействия окружающей среды;
- тип электрода: стальной, алюминиевый, комбинированный.
Узнать больше о сварке электродами.
Полуавтоматическая сварка происходит за счет образования дуги, которая преобразовывает электроэнергию в тепловую посредством плавления основного сварочного элемента – электрода. Это специальная проволока, которая служит проводником энергии. Ее подача осуществляется автоматически с помощью медной катушки.
Сварочный полуавтомат может работать с газом и без газа. Первый тип применяется для соединения цветных металлов или легированных сталей. В качестве газа используется углекислота, которая подается к пистолету под делением из баллона.
Устройство аппарата
Перед тем, как приступать к разбору, как варить металл, необходимо разобраться в строении самого аппарата. При использовании полуавтомата в сварочных работах можно получить качественный и ровный шов, прикладывая при этом минимум усилий. Его можно происходить как ниточным, так и точечным способом, если нет полноценного доступа к свариваемым деталям. С учетом некоторых «пробелов» или зазоров, все равно получается прочное и долговечное соединения. Это объясняется свойствами оборудования, которое для этого используется. При использовании газа, он попадает в рабочую среду и защищает материал от окисления газов из внешней среды.
Полуавтоматический сварочный аппарат состоит из следующих деталей:
- Газовый баллон, в котором находится газ для защиты металла.
- Трубка для подачи газа – это приспособление, через который и подается газ в рабочую зону.
- Катушка для проволоки.
- Механизм для автоматической подачи проволоки может быть тянущим, толчковым или комбинированным, при котором подача осуществляется двумя приводами.
- Газовая горелка обеспечивает подачу газа в активную зону для защиты металла от внешней среды. Изоляционная рукоятка обеспечивает высокий уровень безопасности для мастера во время сплава материалов.
- Источник питания может быть нескольких видов – инвертор или трансформатор. Это зависит от габаритов и предполагаемой мощности аппарата.
- Блок управления.
- Газовая аппаратура для полуавтомата.
- Провод цепи управления.
Принцип работы данного аппарата заключается в следующем. Изначально важно правильно установить полярность в зависимости от технологии – с газом иле без. Затем необходимо установить катушку с проволокой и газовый баллон. После этого проводится настройка, то есть натягивается проволока, регулируется подача газа. Ток для сварки настраивается в процессе работы.
Технология сварки полуавтоматом зависит от нескольких факторов: типа металла, из которого выполнена рабочая деталь, длина шва, применение или отсутствие баллона. Кроме этого, выполнять швы можно несколькими способами:
- Стыковый метод предусматривает плотное соединение двух частей между собой тонким и практически незаметным швом. При этом качество дорожки остается на высшем уровне. Такой способ чаще всего применяется при ремонте и строении автомобильной техники.
- Внахлест сплавление выполняется точечным методом, когда одна деталь немного «находит» на вторую. В некоторых случаях при этом образую сплошной неразрывный шов.
Режим работы мастер настраивает самостоятельно, ориентируясь на качество деталей, то есть типа металла и их толщину. При толстых изделиях шов необходимо прокладывать в несколько этапов, выстраивая дорожки, плотно прилегающие друг к другу. Тогда соединение будем ровным и прочным.
Плюсы и минусы полуавтоматической сварки
Механизированная сварка становится все популярнее не только у профессионалов, но и у любителей. Сварки полуавтомат имеет ряд преимуществ и недостатков, с которыми обязательно нужно ознакомиться прежде чем приняться за работу. К достоинством данного вида сплавления можно отнести следующие:
- возможность создания неразъемного соединения для оцинкованных изделий, не повреждая при этом покрытие. Сплав происходит с помощью медной проволоки;
- способность варить как конструкционную стать, так и другие металлы – алюминий, чугун;
- возможность работы с тонкими стальными листами, толщиной не более половины миллиметра;
- низкая чувствительность к загрязнениям и коррозии основного материала;
- удобство, при котором шлак не перекрывает шов и оператор сразу видит результат;
- невысокая стоимость, в сравнении с другими типами создания неразъемных соединений.
Кроме этого, стоит отметить некоторые недостатки, которые возникают при работе на полуавтомате:
- при сварке без газа увеличивается разбрызгивание раскаленного железа;
- происходит более сильное излучение дуги, поэтому необходимо применять защитную форму и маску для лица.
Даже с некоторыми недочетами такой тип сварки широко применяется во многих производственных отраслях. Чаще всего такие типы используются в сферах автостроения и ремонта транспортных средств. При этом применяется защитный газ – гелий, аргон или углекислый газ.
Особенности сварки газом и без газа
Полуавтоматическая сварка с газом применяется чаще, так как она может выполнить более широкий спектр функций, чем без газа. Кроме этого, стоит отметить преимущества данного типа сплавления:
- качество сварки намного выше, чем работа без газа, то есть швы получаются практически идеальные и малозаметные;
- умеренная термическая обработка деталей позволяет производить швы даже на тонких изделиях, не деформируя их;
- высокий коэффициент полезного действия за счет быстрой плавки проволоки производительность увеличивается в несколько раз;
- перед соединением не нужно проводить первичную подгонку деталей, что экономит время мастера;
- углекислый газ самый доступный среди всех и широко применяется для сплавления;
- технология работы сварочным полуавтоматом намного проще, чем работа электродом вручную, поэтому данное ремесло легко освоить даже новичку.
Сварка полуавтоматом без газа используется в том случае, если работы проводятся не слишком часто, то есть, нет смысла приобретать баллон. В таком случае для защиты применяется порошковая проволока или флюсовая. Во время спайки металлических изделий она расплавляется под воздействием высокой температуры и создает над швом слой защитного газа.
Выполняя сварочные работы без газа, необходимо учесть некоторые нюансы и секреты, которые помогут в работе:
- для устойчивости качества дуги необходимо контролировать сварочный ток. То есть, применять тонкую проволоку на высокой плотности. Это поможет контролировать дугу и уменьшить разбрызгивание металла. Также значительно снижается риск обрывания дуг;
- тонким электродом нужно производить движения исключительно вдоль шва, тогда дорожка будет ровной и прочной. При использовании проводника большого диаметра допустимо плавные движения из стороны в сторону;
- швы на деталях который расположены вертикально или под углом более 55 градусов по отношению к горизонтальной плоскости нужно варить снизу вверх, чтобы избежать стекание плавленого металла.
Узнать больше о дуговой сварке электродами.
Как выбрать полуавтомат
Чтобы сварка полуавтоматом без газа и с газом была выполнена идеально, необходимо несколько условий. Первое из которых — непосредственно мастерство сварщика, а второе – качество и функциональность самого аппарата. Рассмотрим основные аспекты, на которые следует обратить внимание при выборе сварочного аппарата:
- Мощность оборудования является основным условием для качества работы и КПД. Если данный аппарат будет использоваться в промышленных условиях, тогда рекомендуется приобретать более мощный агрегат. И наоборот, для домашних условий достаточно будет простого переносного полуавтомата.
- Бренд. Важно изучить производителя и ознакомиться с реальными отзывами пользователей.
- Функции. Перед покупкой нужно ознакомиться с технологией работы таким изделием, чтобы выбрать максимально подходящее оборудование.
В завершении хотелось бы отметить, что сваривать металлические детали посредством полуавтоматического оборудования намного легче и быстрее, чем ручными аппаратами. Технология полуавтоматической сварки значительно отличается от ручного способа подачи электрода. Методику накладывания шва выбирает мастер в зависимости от типа деталей, их толщины и качества металла, из которого они произведены.
[Всего голосов: 3 Средний: 4/5]svarkaed.ru
8.3. Полуавтоматы для дуговой сварки
ПШ вмещает 1,5 кг флюса. Для питания используют сварочные агрегаты постоянного тока, а также трансформаторы.
Вшланговых полуавтоматах ПДШ-500иПДШМ-500,выпускаемых заводом
"Электрик", флюс в зону сварки подается по гибкому шлангу сжатым воздухом одновременно со сварочной проволокой или по отдельному шлангу(5-6ат). Воздух очищают от масла и влаги.
Полуавтомат ПДШ-500имеет более простую электрическую схему и постоянную скорость подачи проволоки, регулируемую реостатом.
8.3.2. Полуавтоматы для сварки в защитных газах
Для механизированной сварки в нейтральных газах– аргоне и гелии – применяют полуавтоматы для сварки неплавящимися и плавящимися электродами.
В полуавтоматах ПШВ-1М,ПШВ-В,А-533и др. используется неплавящийся вольфрамовый электрод, а в зону дуги подается сварочная проволока. При сварке держатель полуавтомата передвигается сварщиком вдоль шва вручную с опиранием на изделие присадочной проволокой, непрерывно подаваемой в зону сварки (рис.8.8), при этом скорость передвижения равна скорости сварки.
1 – корпус;
2 – рукоятка;
3 – сопло;
4 – вольфрамовый электрод;
5 – присадочная проволока;
6 – механизм подачи проволоки;
7 – гибкий шланг.
Рис. 8.8. ПолуавтоматПШВ-1
Этот полуавтомат можно использовать при сварке а любых пространственных положениях легированных сталей и алюминиевых сплавов толщиной0,5-4мм. Электродами служат вольфрамовые пруткидиаметром2-6мм, присадочная проволока диаметром1-2,5мм. Скорость подачи проволоки10 - 80 м/ч, питание - постоянным или переменным током.
8.3.3. Полуавтоматы для сварки в защитных газах плавящимся электродом
Полуавтоматы | для | этого | имеют | различную | конструкцию. Передвижение | ||
полуавтомата | осуществляется | вдоль | шва | , вручнуюостальные | операции | ||
автоматизированы. У большинства этих полуавтоматов | ролики подающего механизма |
studfiles.net
Технология сварки полуавтоматом: основные этапы работы
На сегодня сварочное дело распространено повсюду. Сварка используется в различных отраслях промышленности: машиностроение, металлургия. Она нашла широкое применение при прокладке и ремонте трубопроводов, в судостроении, в процессе осуществления монтажных работ. Известно несколько видов сварки: ручная дуговая, газовая, полуавтоматическая, автоматическая. Технология сварки полуавтоматом несколько отличается от простой дуговой. Главное отличие — автоматизация процесса. Если при ручной дуговой сварке всю работу выполняет человек, то здесь требуются меньшие усилия.
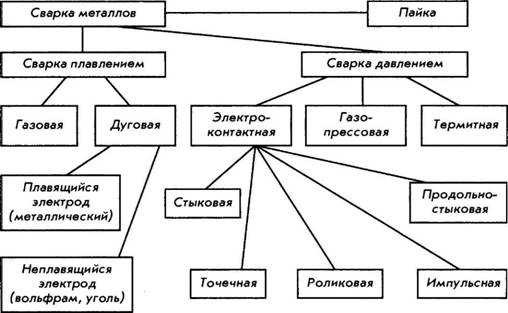
Классификация видов сварки.
В настоящее время сварка полуавтоматом используется в основном для соединения различных деталей из стали, алюминия и железа. Благодаря точно установленному режиму работы сварочного аппарата можно добиться получения отличного сварного шва и прочности конструкции. Чтобы этого достичь, требуется правильно подготовить оборудование и само рабочее место. Большое значение имеет скорость подачи сварной проволоки, а также подаваемая сила тока и напряжение сети. Необходимо более подробно рассмотреть основные этапы работы при сварке полуавтоматом.
Подготовительный этап работы
Подключение сварочного аппарата.
Для сварки полуавтоматом потребуется приобрести необходимое оборудование. В первую очередь понадобится сварочный полуавтомат. Он представляет собой устройство, с помощью которого осуществляется сам процесс сварки. В качестве электрода в данной ситуации выступает проволока. Она может быть различного диаметра. Это во многом зависит от толщины свариваемых изделий. Если при автоматическом процессе все делает сам агрегат, а человек только наблюдает за процессом, то здесь работник должен сваривать сам, аппарат только подает ток и проволоку. Оборудование для сварки таким способом различается по устройству и внешним параметрам.
Выделяют стационарные, передвижные и переносные агрегаты. В зависимости от того, какая используется проволока, различают автоматы со сплошным электродом из стали, алюминия или универсальные. Существует и другая классификация. Она основана на механизме защиты сварного шва. Важно, что сварной шов должен быть защищен специальным газом. Выделяют сварку в среде защитного газа, под флюсом.
Подготовительный этап включает в себя организацию заземления, установление нужного напряжения и силы тока. Режим работы выбирается индивидуально для каждого изделия. Непосредственно до сварки нужно правильно отрегулировать наконечник. Его величина должна превышать размер проволоки. Проволока должна быть цельной. Что же касается подающего механизма, то целесообразно проверить его исправность. Сварка осуществляется с соблюдением всех мер безопасности. При этом используются средства индивидуальной защиты (перчатки, невозгораемая одежда, щиток или маска).
Технология сварки в среде защитного газа
Сварка в среде защищенного газа.
В качестве защитного газа чаще всего выступает углекислота или гелий. Защитный газ в значительной степени снижает окисление металла, что повышает прочность изделия. До сварки деталей из нержавейки или другого металла нужно тщательно очистить поверхность от грязи, мусора, смазочных веществ. Делается это при помощи щетки или ветоши. Если сварка деталей проводится в вертикальном положении или планируется формирование потолочного шва, то проволока берется небольшого сечения. Сила тока тоже не должна быть большой.
Технология сваривания бывает следующих типов:
- непрерывного;
- точечного;
- с помощью коротких замыканий.
Сварочный полуавтомат в углекислой газовой среде.
Чаще всего сварка проводится при подаче переменного тока. Углекислый газ для сварки выпускается в баллонах. Он нетоксичен. Выделение газа из баллона осуществляется при помощи сопла горелки. Необходимый расход газа зависит от режима сварки. Что же касается подачи проволоки, то оптимальный расход ее составляет около 35-40 мм/с. После того как оборудование подготовлено, осуществляется возбуждение электрической дуги. Делается это посредством касания проволоки о поверхность изделия. Движение сварочной проволоки достигается путем нажатия на кнопку «пуск», расположенную на держателе.
Проволока не должна располагаться слишком близко к изделию, так как это ухудшает обзор для работника. Проволоку нужно вести прямо. В целях обеспечения безопасности не рекомендуется направлять сопло горелки на себя. Одной рукой нужно придерживать деталь, а второй — держать горелку. При сварке важно, чтобы между кромками свариваемых деталей соблюдался нужный интервал. Технология работы такова, что при толщине металла до 10 мм зазор должен быть не более 1 мм, при толщине изделий более 10 мм зазор составляет 10% от данной величины. Очень часто детали в лежачем состоянии сваривают на подложке. При этом ее располагают снизу и очень плотно к основному металлу.
Технология сварки алюминия
Сваривать полуавтоматом можно не только сталь, но и алюминий. Сложность сварки этого металла в том, что на его поверхности имеется особый слой амальгамы. Он затрудняет процесс плавления и образования сварного шва. Соединение деталей полуавтоматом осуществляют при подаче защитного газа аргона. В данной ситуации подойдут плавящиеся электроды. Так как металл обладает высокой текучестью, под изделие устанавливается подкладка.
Особенность этого вида сварки в том, что она проводится под действием постоянного тока обратной полярности.
Аргонная сварка.
При этом на горелку подключается «-», а на деталь — «+». Это обеспечивает разрушение поверхностного слоя алюминия и плавление детали. Необходимо помнить, что этот метод будет эффективным только в случае небольшой толщины защитной пленки. Если же слой окиси алюминия значительный, то перед проведением сварочных работ рекомендуется провести механическую или химическую обработку поверхности деталей.
Алюминий лучше сваривать аппаратами с тянущим механизмом подачи проволоки. Технология сварки может проводиться в разных пространственных положениях детали. Если сварка выполняется в вертикальном положении, то горелку нужно двигать сверху вниз. Это обязательное правило, в противном случае шов не удастся. Сопло должно быть направлено несколько вверх. Вертикальные изделия нужно сваривать быстро, чтобы расплавленный металл не успевал стекать вниз.
Как варить полуавтоматом без газа?
Сварка под флюсом.
У сварки полуавтоматом масса достоинств, одним из которых является возможность проведения работ без защитного газа. В последние годы большой популярностью среди сварщиков пользуется сварка под флюсом. Она проводится с применением порошковой проволоки и представляет собой металлическую трубку, внутри которой расположен порошок. Порошок в процессе сварки плавится, в результате чего выделяется газ, который защищает поверхность деталей от окисления. Сам флюс схож по своему химическому составу со смазкой простых электродов.
При этом типе сварки не нужно покупать баллоны с газом. Способ хорош тем, что имеется широкий ассортимент порошковой проволоки. В зависимости от ее состава можно сформировать необходимый шов и организовать оптимальный режим горения дуги. Технология соединения деталей отличается тем, что подача проволоки требует определенного усилия (нажатия). Как и при сваривании алюминия, в этом случае применяется обратная полярность. Это нужно для повышения температуры сварочной дуги и расплавления флюса.
Основные правила при проведении сварочных работ
Техника безопасности при сварочных работах.
Сварщик должен помнить некоторые важные моменты. Во-первых, в самом начале сварочных работ рекомендуется сделать пробный шов на каком-либо ненужном изделии. Это необходимо, для того чтобы отрегулировать режим работы (силу тока, скорость подачи проволоки). Если этого не делать, то можно получить некачественный сварной шов. Во-вторых, сваривать изделия требуется, опираясь на инструкцию, приложенную к аппарату. В-третьих, работать необходимо в специальной одежде. При сварке выделяется большой объем газа, поэтому лучше проводить процедуру на улице или оборудовать помещение вентиляцией.
В-четвертых, для каждого типа сварочной проволоки форма канавки должна иметь определенную форму. Если проволока сплошная и сделана из стали, то канавка должна быть V-образной, при флюсовой проволоке канавка такая же, только с насечками. В-пятых, при горении дуги нельзя прикасаться к сварному шву, так как он очень сильно нагревается. В-шестых, категорически запрещено сваривать изделия, емкости, на поверхности которых имеются горючие материалы. Изделия должны быть очищены. Кроме того, не нужно работать беспрерывно, требуется делать небольшие паузы.
Необходимые инструменты и материалы
Чтобы осуществить сварочные работы, потребуется набор инструментов и материалов:
- сварочный полуавтомат;
- проволока необходимого диаметра;
- источник тока, баллон с защитным газом;
- перчатки;
- маска или щиток;
- молоток;
- щетка.
Нужно убедиться, чтобы газ и проволока были в достаточном объеме. При приобретении сварочного оборудования необходимо обращать внимание на его стоимость. Лучше приобретать товар по средней цене, дешевый агрегат может быть плохого качества.
Полуавтомат должен иметь инструкцию по применению, гарантийный талон. Рекомендуется обращать внимание на производителя. Существуют полуавтоматы с коротким и длинным шлангом. Второй вариант оптимальный. Стационарное оборудование используется только при регулярных сварочных работах. Современные же переносные аппараты являются более компактными и удобными.
Таким образом, технология полуавтоматической сварки сводится к тому, что с помощью оборудования на изделие подается проволока, а работник осуществляет плавление металла и формирует сварной шов. Условно полуавтоматическую сварку можно разделить на газовую и под флюсом. Оба метода очень эффективны и позволяют получить качественный сварной шов. От того, насколько правильно выбран режим работы оборудования, зависят результат работы и прочность полученного изделия. Если соблюдать все вышеописанные правила и опираться на инструкцию к оборудованию, то свариваемые детали не будут иметь дефектов.
moyasvarka.ru
Полуавтоматическая сварка в среде защитных газов (MIG/MAG) – Осварке.Нет
Полуавтоматическая сварка — механизированная дуговая сварка металлическим плавящимся электродом (проволокой) в среде защитных газов. Способ также известен как MIG/MAG сварка. В зависимости от типа используемого защитного газа различают сварку в инертных газах (MIG) и активных (MAG). В качестве активных газов преимущественно используют сварку в среде углекислого газа. В отличии от ручной дуговой сварки покрытыми электродами при механизированной сварке подача электрода в зону сварки выполняется с помощью механизмов, а сварщик перемещает горелку вдоль оси шва и выполняет колебательные движения электродом по необходимости.
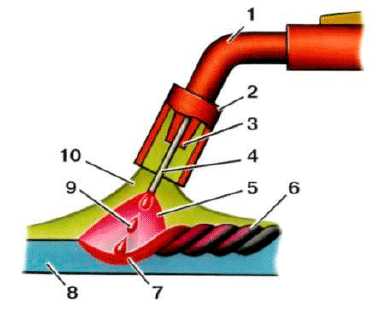
Рис. 1. 1 — горелка, 2 — сопло, 3 — токоподводящий наконечник, 4 — электродная проволока, 5 — дуга, 6 — шов, 7 — ванна, 8 — основной металл, 9 — капля металла, 10 — газовая защита.
Сущность метода и общие принципы полуавтоматической сварки
Механизированная сварка, как и другие виды дуговой сварки, осуществляет за счет большей тепловой энергии сварочной дуги сконцентрированной в месте ее горения. Температура дуги больше температуры плавления металлов, поэтому под ее воздействием кромки сварного изделия плавятся, образуя сварочную ванну из жидкого металла. Дуги при этом горит между основным металлом и сварочной проволокой, которая выполняет функции подвода дуги к зоне сварки и является присадочным металлом для заполнения зазора между кромками.
Сварочная проволока с кассеты непрерывно подается в зону сварки при помощи подающего механизма, который проталкивает ее по каналу в рукаве к соплу сварочной горелки.
Сварочная дуга, расплавленный металл, конец сварочной проволоки, околошовная зона находятся под защитой газа, выходящего с горелки. Для получения более качественного шва, иногда выполняют подачу защитного газа дополнительно с обратной стороны шва.
В отличии от ручной сварки, отсутствие покрытых электродов позволяет механизировать процесс или полностью автоматизировать.
Оборудование для полуавтоматической сварки
В комплект оборудования для механизированной сварки входят источник питания сварочной дуги, подающий механизм, газовое оборудование, горелка. Для повышения производительности и избежания перегрева горелки при серийном производстве могут использоваться системы охлаждения.
Источники питания сварочной дугиДля сварки в среде защитных газов изготавливают источники питания с жесткими внешними вольт-амперными характеристиками. Сварка производится на источниках постоянного тока — сварочные выпрямители, преобразователи, инверторы или специальные установки, содержащие в себе источник питания и подающий механизм, а также блок управления. Источники питания переменного тока практически не используются. | |
Многопостовые источники питанияДля организации работы в цехах на производстве со стационарными сварочными постами целесообразно использовать многопостовые источники питания. Для этих целей можно использовать преобразователи и выпрямители. Существует две схемы организации многопостовой сварки. Первая схема используется когда сварка производиться одинаковыми режимами на каждом посте с частыми замыканиями сварочной цепи (возбуждение дуги). При такой схеме в цепь каждого сварочного поста включают дроссель, который способствует снижению влияния постов друг на друга при одновременной работе. Вторая схема может быть использована для регулирования режимов сварки индивидуально на каждом посте с минимальным влиянием постов друг на друга. В таком случае напряжение холостого хода многопостового источника питания устанавливают на максимум, а снижение силы тока (регулирование) выполняется с помощью балластного реостата на каждом посте. | |
Механизмы подачи проволокиМеханизмы подачи проволоки используются для стабильной подачи проволоки и регулирования скорости подачи в сварочную горелку. Обычно подающий механизм состоит из электродвигателя, редуктора, тормозящего устройства, подающих и прижимных роликов, а также кассеты с проволокой. Существуют различные варианты исполнения подающих механизмов — закрытого и открытого типа.В зависимости от числа роликов различают двухроликовые и четырехроликовые подающие механизмы. Последние более надежные и рекомендуется использовать для проволоки большего сечения или при сварке порошковой проволокой.Для увеличения радиуса проведения сварочных работ и обеспечения стабильной подачи сварочной проволоки могут применяться промежуточные механизмы подачи. Это позволяет увеличить зону проведения сварочных работ от 10 до 20 метров. Промежуточные механизмы синхронизируются с основным что позволяет значительно удалятся от источника питания или полуавтомата и газового оборудования. | |
Сварочные полуавтоматыСварочные полуавтоматы — специальные установки для механизированной сварки в среде защитных газов содержащие в себе источник питания, подающий механизм, горелку и блок управления процессом. Дополнительно полуавтомат может иметь дистанционный пульт управления, включать схемы позволяющие выполнять сварку в импульсно-дуговом режиме и т.д. Сегодня чаще используется схема сварки от сварочного полуавтомата, чем источник питания + подающий механизм. | |
Сварочная горелкаВыполняет несколько функций, среди которых: направление проволоки в зону сварки, подвод тока к сварочной проволоке, подача защитного газа, управление процессом при помощи кнопки управления. Все это возможно благодаря использованию специального шланга внутри которого находится сразу несколько элементов — сварочные кабеля, управляющие провода, спиралеобразный канал для направления проволоки, трубка для подачи газа, а иногда и для подачи воды. | |
Газовое оборудование для полуавтоматической сварки
В состав газового оборудования для сварки полуавтоматом входят: баллон, редуктор, ротаметр, подогреватель, осушитель, смеситель газов, рукава (шланги).
БаллоныВ баллонах хранят и транспортируют сжатые газы. Содержащийся в баллоне газ можно распознать по цвету и надписи на баллоне. | |
Редуктор (регулятор давления)Редуктор присоединяется к вентилю баллона, предназначен для понижения давления от баллонного до рабочего и постоянного его поддержания. Для регулирования расходов газа (давления) вращают маховик на редукторе. | |
![]() | Подогреватель При сварке в среде углекислого газа редуктор дополнительно комплектуется подогревателем газа, чтобы избежать замерзания редуктора. При большем расходе углекислого газа наблюдается резкое снижение температуры, что приводит к замерзанию в редукторе влаги содержащейся в углекислоте. Работает подогреватель от постоянного (20 В) и переменного (36 В) тока. |
Осушитель Для поглощения влаги находящейся в углекислом газе в состав газового оборудования иногда включают осушитель большего или низкого давления. Осушитель высокого давления устанавливается перед редуктором, а низкого — после редуктора. Поглощает влагу специальное вещество — алюмогликоль или силикагель. Свойства обеих веществ можно восстановить путем прокалывания при температуре 250-300 ºC. | |
Ротаметр Ротаметры используются для определения расходов защитного газа, когда на редукторе нет предустановленного расходомера. | |
Рукава (шланги) Гибкие трубки изготавливаемые из вулканизированной резины усиленные льняной тканью. С их помощью защитный газ транспортируется к горелке и другим частям газового оборудования. | |
Смеситель газов Смеситель газов предназначенный для приготовления смеси газов при подаче из нескольких баллонов. | |
Техника полуавтоматической сварки
Сварка стыковых соединений полуавтоматом
Детали не большей толщины 0,8-4 мм сваривают без разделки кромок закрепленными в сборочно-сварочных приспособлениях.Сваривают тонкий металл на подкладках из того же металла что и изделие или на медных и нержавеющих съемных подкладках. Металл толщиной свыше 4мм можно сваривать как на весу, так и на подкладках. | |
Тонкий металл при сварке полуавтоматом гораздо легче сваривается при в вертикальном положении. Сварку ведут углом назад, а горелку передвигают в направлении сверху-вниз. При этом сварщику хорошо видно формирование шва и зону сварки. | |
Для сварки толстого металла лучше использовать газы повышающие тепловую мощность дуги — гелий или смеси гелия и аргона. При этом нужно следить за положением горелки относительно шва. Небольшое отклонение горелки от вертикали способно привести к несплавлению кромок сварных деталей. | |
Сварка угловых и тавровых соединений полуавтоматом
Сварку угловых предпочтительней вести при расположении сварных деталей в лодочку. При этом выпуск электродной проволоки увеличивают на 10-15% по сравнению со сваркой стыковых швов в нижнем положении. | |
Сварка угловых и тавровых швов усложняется плохим наблюдением за формированием шва из-за сопла горелки. Расстояние e = 0, при толщине металла до 5 мм, и e = 0,8-1,5 при толщине металла свыше 5 мм. | |
Сварка нахлесточных соединений
Сварка нахлесточных соединений при толщине металла меньше 1,5 мм выполняется на медной или стальной подкладке за один проход. | |
Сварка деталей толщиной более 1,5 мм выполняется на весу за несколько проходов. | |
Сварка горизонтальных швов полуавтоматом
Сварка горизонтальных швов ведется «углом вперед» без поперечных колебательных движений горелкой. Металл толщиной более 6 мм сваривают за несколько проходов. | |
Сварка деталей до 3 мм ведется под прямым углом горелки оси горелки относительно сварных деталей, без разделки кромок. | |
Сварка деталей более 3 мм в горизонтальном положении сваривается с разделкой верхней кромки, а горелка наклоняется относительно верхней детали под углом примерно 70º. | |
Сварка вертикальных швов
Сварку вертикальных швов рекомендуется выполнять проволокой диаметра 0,8-1,2 мм со свободным формированием шва. Можно применять технику частых коротких замыканий или использовать источники с импульсной дугой. Детали толщиной до 4 мм лучше сваривать способом сверху-вниз без колебательных движений. Если предполагается выполнять сварку односторонним швом, лучше собирать детали с зазором.
Сварка потолочных швов
Потолочные швы толщиной более 6 мм лучше сваривать за несколько проходов. Сварку алюминия и его сплавов полуавтоматом рекомендуется вести углом вперед, а сварку сталей, меди, титана и других металлов — углом назад.
Преимущества и недостатки полуавтоматической сварки
К преимуществам сварки полуавтоматом относят:
- Возможность сравнительно легко получить качественное сварное соединение, в том числе для тонкостенных сварных конструкций.
- Высокая производительность сварки данным методом по сравнению с ручной дуговой сваркой, газовой сваркой и др.
- Механизированную сварку в среде защитных газов можно выполнять во всех пространственных положениях: нижнем, горизонтальном, вертикальном и потолочном.
- Отсутствие флюсов и покрытий, а соответственно операций по очистке шва от шлака.
- Дуга при сварке в защитных газах более сконцентрированная, поэтому зона термического влияния минимальная.
- Сварка сопровождается незначительными напряжениями и деформациями.
- Возможность полной автоматизации процесса сварки.
Недостатки способа:
- При сварке на открытом воздухе или сквозняке повышается вероятность нарушения газовой защиты.
- Разбрызгивание электродного металла во время сварки, особенно при использовании углекислого газа.
- При сварке на режимах с повышенной мощностью возникает потребность в использовании систем водного охлаждения из-за сильного нагрева оборудования.
osvarke.net
Полуавтоматическая сварка – дуговая сварка автоматически подающимся проволочным электродом (проволокой) в среде защитного газа. Общепринятые обозначения полуавтоматической сваркиMIG – Metal Inert Gas (Welding) – металлическая сварка в среде инертного газа MAG – Metal Active Gas (Welding) – металлическая сварка в среде активного газа GMAW – Gas Metal Arc Welding – металлическая дуговая сварка в газовой среде Полуавтоматическая сварка в углекислом газеПолуавтоматическая сварка в углекислом газе (СО2) является основной и наиболее распространенной технологией сварки плавлением на предприятиях машиностроительной отрасли. Она является экономичной, обеспечивает достаточно высокое качество сварных швов, особенно при сварке низкоуглеродистых сталей, возможна в различных пространственных положениях, требует более низкой квалификации сварщика, чем ручная дуговая сварка. Рисунок. Полуавтоматическая сварка, схема процесса Защитный газ, выходя из сопла, вытесняет воздух из зоны сварки. Сварочная проволока подается вниз роликами, которые вращаются двигателем подающего механизма. Подвод сварочного тока к проволоке осуществляется через скользящий контакт. Учитывая, что защитный газ активный и может вступать во взаимодействие с расплавленным металлом, полуавтоматическая сварка в углекислом газе имеет ряд особенностей. |
www.samsvar.ru
Техника сварки полуавтоматом и инвертором
Для получения неразъемного соединения однородных (металлы) или разных по качеству (керамика, металл) деталей применяют сварку. За счет плавления материалов удается получить устойчивый к нагрузкам, недеформируемый и прочный рабочий шов между элементами. В бытовых условиях безопаснее и надежнее для начинающих применять электродуговую сварку, используя специальный сварочный аппарат (инвертор, полуавтомат). Задача оператора не просто соединить два элемента, а создать красивый, прочный, надежный и неразъемный рабочий шов. А для этого должна быть изучена техника сварки полуавтоматом и инвертором различных по толщине материалов.
Расходным материалом при работе с первым видом оборудования будет проволока (тонкостенные детали), со вторым — электроды (сваривание толстых деталей). Нужно освоить:
- Принципы подбора расходных материалов: диаметр, длина.
- Способы поджига дуги.
- Виды сварных швов, их назначение и характеристики.
- Работу с дугой.
Наглядно с процессом дуговой сварки поможет ознакомиться видео.
Определение характеристик электрической дуги
Одно из основных условий получения качественного и надежного рабочего шва — корректный подбор длины дуги и диаметра расходного элемента. Поэтому для начинающих сварщиков важно запомнить следующее правило: габариты дуги должны быть равны 0,5-1,1 от параметров электрода (2.5, 3.25, 4, 5 мм) или проволоки (до 2-2,25 мм). Правила техники сварки полуавтоматом и инвертором гласят, что оператор обязательно должен поддерживать в ходе процесса заданную (корректную) длину электросварочной дуги. Если отступить от правила, то последствия будут следующими:
- окисление оплавленного металла — длинная дуга;
- прерывание дуги — короткая;
- деформация рабочего шва — длинная;
- припай расходного элемента к деталям — короткая дуга;
- азотирование оплавленного материала — длинная;
- повышенная пористость структуры рабочего шва — длинная;
- разбрызгивание оплавленного материала — длинная.
Если сваривать детали, не поддерживая постоянной величину дуги, то процесс дуговой сварки нарушается: неустойчивое, неравномерное горение, некорректная глубина провара, пожароопасность процедуры и т.д. Рабочий шов будет иметь неправильную форму и однородную структуру, размеры. Чтобы облегчить процесс, для начинающих производители расходных материалов (только при работе с электродами большого диаметра) в паспорте указывают желательную величину дуги.
Возбуждение дуги: правила и способы поджига
Если ранее оператором не рассматривалась техника электродуговой сварки с помощью инвертора или полуавтомата, тогда процесс лучше начинать изучать с самых азов — с поджига или возбуждения дуги. Сложности связаны с прикипанием основания стержней к поверхности соединяемых материалов. Поэтому новичкам нужно запомнить главное правило сварки инвертором: при поджиге прикосновение электрода к деталям должно быть кратковременным. Чтобы возбудить дугу используют один из методов поджига:
- слегка (секундная задержка) прикоснуться стержнем к поверхности детали и быстро разделить объекты. Надо отвести электрод на расстояние не менее 4 мм.
- боковое протягивание стержня по поверхности детали и отвод электрода. Расстояние разделения объектов — 4-4,5 мм.
Если секундная задержка не удалась, стержень обязательно прикипит к детали. Отрывать его нужно, применяя вращение. Поворачивая расходный элемент в сторону, резким движением срывают его. На видео показано, как правильно выполнить возбуждение сварочной электрической дуги.
Положение стержня при оформлении различных видов швов
Соединения принято делить на стыковочные, потолочные, угловые, горизонтальные, нахлестные, вертикальные, тавровые и прочие. Характеристики пространства между деталями определяют количество проходов, за которые удастся положить ровный и качественный шов. Меленькие и короткие соединения выполняют одним проходов, длинные — несколькими. Накладывать шов можно непрерывно либо точечно.
Выбранная техника сварки определит прочность, устойчивость к нагрузкам и надежность места соединения деталей. Но прежде чем выбрать схему работы, необходимо определиться с положением стержня. Его определяют:
- пространственное положение места соединения;
- толщина свариваемого металла;
- марка металла;
- диаметр расходного элемента;
- характеристики покрытия электрода.
Корректный выбор положение стержня определяет прочность и внешние данные места соединения, а техника сварки швов в различных положениях будет следующей:
- «От себя», или «вперед углом». Стержень при работе наклонен на 30-600. Инструмент продвигается вперед. Такую технологию применяют при соединении вертикальных, потолочных и горизонтальных стыков. Также применяется эта техника для сварки труб — электросваркой удобно соединять неповоротные стыки.
- Под прямым углом. Способ подходит для сваривания труднодоступных стыков, хотя его считают универсальным (можно сваривать места с любым пространственным расположением). Положение стержня под 900 усложняет процесс.
- «На себя», или «назад углом». Стержень при работе наклонен на 30-600. Инструмент продвигается по направлению к оператору. Эта техника сварки электродом подходит для угловых, коротких, стыковых мест соединения.
Правильно подобранное положение инструмента гарантирует и удобство выполнения запайки стыка, и позволяет следить за корректным проплавлением материала. Последний факт обеспечивает качественное формирование и прочность рабочего соединения. Правильная техника сварки инвертором — проплавление материалов на незначительную глубину, отсутствие брызг, равномерный захват кромок стыка, равномерное распределение расплава. Каким должен получиться соединительный сварочный шов можно увидеть видео для начинающих сварщиков.
Особенности перемещения дуги при выполнении дуговой сварки
Корректное движение сварной электрической дугой обеспечивает качество и надежность соединительного шва. Описываемая техника дуговой сварки предполагает перемещение дуги в следующих направлениях:
- Поступательном — вдоль оси расходного элемента. Служить для поддержания заданной длины дуги. Правило: продвижение электрода должно согласовываться с укорочением стержня.
- Продольном — вдоль оси рабочего шва. Используется для формирования сварочного ниточного валика. Толщина его напрямую будет зависеть от скорости движение стержня и его габаритов (валик толще на 3 мм диаметра расходного элемента). Валик образует первичную спайку.
- Поперечном — поперек соединительного шва. Концом стержень совершают колебательные движения. Характеристики соединяемых материалов, расположение стыка и его размер, требования к рабочему шву и другие параметры определяют размах поперечных движений. Движения завершают формирование сварочного соединения. Его ширина будет колебаться в пределах 1,5-5 диаметров используемого стержня.
Чтобы стала понятной эта техника сварки инвертором для начинающих, уточним: все три движения стержнем постепенно накладываются друг на друга, формируя прочное и неразъемное соединение материалов. Поступательно-колебательные движения концом стержня могут иметь различную фигурную траекторию (классических вариантов 11). Каждый из них подходит (удобен) для определенного вида шва. Но вариант фигурного перемещения стрежня подбирают не только по пространственному положению стыка, но и по прочностным характеристикам будущего шва. Для начинающих сварщиков важно запомнить, что перемещение электрической дуги должно быть таким, чтобы края привариваемых объектов расплавлялись с образованием достаточного объема наплавленного металла. Чрезмерный оплав — неаккуратный стык, недостаточный — слабый шов.
При работе с длинными или сложными стыковочными объектами придется выполнять замену стержня. Процедура следующая:
- процесс прервать;
- сменить расходный элемент;
- сбить шлак с остывшего шва;
- возбудить электрическую дугу — поджиг делают на расстоянии 12-13 мм от воронки, которая появилась в конце шва;
- подвести стержень к воронке;
- сформировать сплав из нового и старого стержня;
- завершить перемещение расходного элемента.
Перемещения дуги, которые использует техника сварки инвертором, на видео для начинающих проиллюстрированы детально.
Коротко о схемах сварки и видах соединительных швов
Схема заполнения места соединения деталей будет определять эксплуатационные и прочностные характеристики сварного шва. Поэтому любая техника сварки, в частности дуговой сварки, классифицирует последние по длине и сложности. Различают:
- Короткие стыки (до 300 мм). Заваривание выполняют в один проход — от начала до конца.
- Стыки средней длины (от 300 до 1000 мм). Процесс начинают от середины стыка и ведут к краям. Может использоваться и обратноступенчатый метод — место соединение условно разбивается на несколько равных промежутков, каждый из которых заваривается последовательно в одном направлении.
- Длинные стыки (свыше 1000 мм). Заваривание шва проводится обратноступенчатым методом (самые короткие), каскадом, горкой, блоками (способы вразброс).
На видео продемонстрировано корректное сваривание стыков несколькими видами швов. После его формирования, важно правильно заварить кратер. Нельзя резко обрывать конец шва. Нужно постепенно удлинять дугу, завершив движения стержнем. Процесс сварки заканчивает с ее обрывом. Закрепить теоретический материал поможет видео.
Поделись с друзьями
0
0
0
0
svarkalegko.com
Полуавтоматическая сварка. Как выбрать полуавтомат сварочный :: SYL.ru
Современная сварочная техника характеризуется тем, что представлена в невероятном разнообразии оборудования, посредством которого реализуются разные способы сварки. В сварочном производстве ведущее место отведено дуговой сварке плавлением. При этом расплавление металла реализуется за счет тепла, которое выделяет электрическая дуга, пылающая между электродом и свариваемыми деталями. В качестве одного из вариантов такого соединения деталей служит полуавтоматическая сварка при помощи плавящегося электрода. Следует рассмотреть этот процесс как можно подробнее.
Особенности
Полуавтоматическая сварка предполагает, что плавящийся электрод будет подаваться механизированным способом. Электрод перемещается вдоль шва с требуемой скоростью посредством ручного управления со стороны сварщика, для чего используется сварочная горелка. От воздействия окружающей среды сварочный шов защищается посредством подачи в зону сварки защитного газа, или гранулированного флюса, или обоих веществ одновременно.
Краткое описание процесса
Если используется аппарат полуавтоматической сварки, то дуга горит плавящимся электродом между электродной проволокой и изделием при непрерывной подаче первой в дугу. Дугой производится расплавление проволоки и кромок изделия, благодаря чему образуется цельная сварочная ванна. Происходит ее затвердевание по мере перемещения дуги с образованием шва, которым соединяются кромки изделий. Электродом обычно служит либо сплошная проволока, либо трубчатая. Защитой сварочной ванны служат флюсы или газы, к примеру аргон, углекислый газ, гелий и смеси.
Стадии процесса
Полуавтоматическая сварка как процесс представляет собой совокупность электрических и физических явлений, которые протекают от начала сварки до ее окончания. У самого процесса можно условно выделить три главные стадии: начало, стабильное течение и завершение. Начало представляет собой отрезок времени, который требуется для установления процесса до конкретно заданного режима сварки. Данная стадия является важнейшей для качества сварного соединения. Начало сварки должно быть минимальным по продолжительности. Эту процедуру выполняют как с касанием электрода и изделия, так и без него.
Стабильная стадия
Под стабильным течением процесса подразумевается отрезок времени, требуемый для сохранения неизменности заданного режима сварки при образовании сварного шва. Этот процесс предназначен для получения сварного соединения, имеющего неизменные заданные свойства и размеры по всей протяженности шва. Процесс считается стабильным, если его тепловые и электрические характеристики не изменяются во времени либо их изменение соответствует определенной программе.
Завершение процесса
Под окончанием процесса сварки понимают отрезок времени, который требуется для перехода от стабильного течения процесса до обрыва дуги в момент прекращения сварки. Обычно используются два способа окончания сварки: посредством естественного обрыва дуги после того, как будет остановлена подача проволоки при включенном источнике питания дуги; посредством принудительного обрыва дуги в момент обесточивания сварочной цепи при одновременной остановке подачи проволоки.
Существует несколько видов, каждый из которых стоит рассмотреть.
Под слоем флюса
В зону сварки подается флюс из воронки, расположенной на специальном держателе. Между используемой проволокой и изделием горит дуга, которая непрерывно подается по рукаву и держателю. Она расплавляет проволоку, кромки изделия и флюс, образуя своеобразную ванну расплавленного металла, которую покрывает слой расплавленного флюса. Последний предназначен для защиты сварочной ванны от вредных внешний воздействий. Флюс вступает в химические реакции с вредными элементами, которые находятся в расплавленном металле шва. Сварщик вручную перемещает дугу вдоль шва посредством держателя с требуемой для этого скоростью. По мере перемещения происходит остывание шлака и расплавленного металла. Сварочный шов, который образуется, покрывает слой шлака. Удалить его довольно легко. Такая полуавтоматическая сварка производится при переменном и постоянном токе. Этот вид сейчас практически не используется, так как требуется производить все работы в нижнем положении, что не позволяет мастеру видеть сам процесс.
Сварка в защитных газах
Этот вид можно еще разделить на работу в активных газах, к которым относится азот, углекислый газ, аргон с кислородом, аргон с углекислым газом, а также в инертных, к которым относят аргон и гелий. Для сваривания стали и чугуна используется первый вариант, то есть с применением активных газов. Азот предназначен только для меди и медных сплавов. Для высоколегированных сталей, цветных металлов и их различных сплавов используются инертные газы.
Для этого нужна специальная горелка для полуавтоматической сварки, которая подает сварочное напряжение, проволоку и защитный газ. Для подачи напряжения используется полюс источника посредством токопровода, представленного в составе горелки. Для подачи проволоки применяется гибкий направляющий канал, где имеется специальный механизм подачи. Защитный газ в зону сварки подается от баллона при помощи регулятора давления, газового рукава, клапана и гибкого газового рукава, размещенного внутри горелки.
Сварщиком подводится горелка к месту соединения, нажимается кнопка, после чего клапан начинает подавать защитный газ для полуавтоматической сварки, от источника питания подается напряжение, а сварочная проволока подается посредством специального механизма. Конец сварочной проволоки, который выходит из токопроводящего мундштука горелки, замыкается на изделии, которое подключается ко второму полюсу источника. Это все приводит к образованию электрической цепи, по которой и происходит замыкание. Этот момент сопровождается моментальным расплавлением с взрывом конца проволоки. Подача проволоки к изделию продолжается, а в момент соприкосновения разогретым до красна концом проволоки производится возбуждение дуги. Дугой подаваемая проволока постоянно расплавляется у кромки изделия. Это приводит к образованию ванны расплавленного металла.
Из сопла горелки вырывается газ, который отвечает за защиту расплава от негативных внешних воздействий. Горелка перемещается сварщиком вдоль шва по мере необходимости. Требуемого качества шва можно добиться при поперечных колебаниях горелки, если в этом есть необходимость. Когда шов требуемой длины и качества наложен, мастер может отпускать кнопку на горелке. Для всех этих операций имеется четко прописанный ГОСТ.
Сварка полуавтоматическая без газа
В этом случае используется трубчатая сварочная проволока, внутри которой имеется флюс. При сварке он всплывает, чтобы вступить в контакт с вредными примесями.
Особенности оборудования
Автоматическая и полуавтоматическая сварка предполагает, что для работы используется определенное оборудование. С каждым годом появляются все более совершенные приборы. Сейчас на рынке можно встретить полуавтоматы инверторного типа, которые показали себя довольно эффективными. Огромный перечень преимуществ позволил этим агрегатам стать самым популярным видом сварочного оборудования среди всех существующих. Это обуславливается конструктивными особенностями. Эти приборы преобразуют переменный ток, входящий в них, в постоянный. С их помощью потом и производится полуавтоматическая сварка. Цена оборудования может составлять от 300 долларов и выше в зависимости от мощности и производительности.
www.syl.ru