Типы штамповочных прессов и специальное оборудование для ковки. Пресс штамп
Классификация штампов, пресс-форм и их деталей
Штампы и пресс-формы служат оснасткой для одного из самых прогрессивных и распространенных способов обработки материалов - обработки давлением. Обработке давлением подвергаются металлы и их сплавы, а также различные неметаллические материалы, находящие все большее и большее распространение в машиностроении.
Назначение
Штампы преимущественно служат для придания формы металлическим изделиям; роль пресс-форм в производстве значительно шире: в пресс-формах производится не только отливка деталей под давлением или прессование их, но и изготовление всевозможных изделий из таких неметаллических материалов, как резина, кожа и различные пластмассы.
В инструментальном цехе машиностроительного завода главный объем работ занимает изготовление штампов. Однако и производству пресс-форм принадлежит видное место. В связи с развитием химической промышленности все большим применением в машиностроении пластических масс удельный вес изготовления пресс-форм в общем объеме продукции инструментальных цехов будет непрерывно увеличиваться.
Прессование пластмасс позволяет получать изделия самой сложной конфигурации и рельефа без механической обработки. В связи с этим конструкции пресс-форм для пластмасс отличаются высокой трудоемкостью и сложностью технологического процесса.
Штампы и пресс-формы представляют собой дополнительные устройства к машинам, придающие деталям заданную форму без снятия металлической стружки. Особенность названной оснастки прежде всего состоит в том, что в ее конструкции одновременно сочетаются и рабочие инструменты, изменяющие форму детали, и приспособления, устанавливающие и закрепляющие деталь или ее арматуру при штамповке и прессовании.
Штампы применяются для изменения формы детали в холодном и горячем состоянии. В первом случае их называют штампами холодной штамповки, во втором - штампами горячей штамповки. Поскольку последние представляют особую область технологической оснастки, а их изготовление носит специфический характер и часто производится в особых штамповочных цехах или мастерских, в этом разделе будет рассказано только о конструкции и производстве штампов холодной штамповки.
Типы штампов
Штампы холодной штамповки можно разделить на следующие типы:
- Вырубные штампы, с помощью которых производят вырезку из листового металла деталей различных конфигураций, а также заготовок, поступающих после вырубки на другие операции. Следовательно, эта группа может быть разделена на собственно вырубные штампы, отрезные штампы, дыропробивные штампы и штампы обрезные.
- Гибочные штампы, которые изменяют форму детали, изгибая ее вокруг одной или нескольких осей.
- Вытяжные штампы, в которых детали придается выпуклая или вогнутая сосудообразная форма.
- Обжимные и чеканочные штампы, которые изменяют форму детали за счет перераспределения металла заготовки. К обжимным штампам, например, относятся штампы для высадки головок заклепок, а к чеканочным - штампы для образования рельефных рисунков на поверхности деталей.
- Комбинированные штампы одновременно выполняют две или несколько из перечисленных выше функций штампов.
Пресс-формы различают по технологическому назначению (для вулканизации резинотехнических изделий, для прессования пластических масс и т. д.), а также по способу их обогрева при прессовании изделий (электрический или паровой обогрев).
Детали штампов и пресс-форм
Штампы холодной штамповки и пресс-формы состоят из большого количества различных деталей. По своему назначению эти детали могут быть объединены в несколько групп, выполняющих вполне определенные функции при штамповке:
- рабочие части, непосредственно образующие форму детали заготовки и состоящие из пуансонов, матриц или их отдельных секций. Сюда же относятся и детали, создающие загрузочные камеры пресс-формы;
- корпусные детали, связывающие с машиной-орудием и друг с другом все рабочие части и остальные детали штампа или пресс-формы; эти детали состоят из нижней и верхней плиты и хвостовика, а также направляющих втулок и колонок;
- установочные детали, облегчающие установку детали или заготовки по отношению к обрабатываемому контуру рабочих частей;
- съемно-удаляющие детали, облегчающие высвобождение деталей или отходов после выполнения операций и состоящие из съемников и выталкивателей различных конструкций;
- конструктивные детали, необходимые для скрепления отдельных групп деталей с корпусными деталями; в состав этих деталей входят различные конструкции пуансонодержателей и матрицедержателей, а также и все остальные крепежные детали, применяемые для соединения отдельных элементов конструкции друг с другом;
- детали пресс-форм, обеспечивающие температурный режим прессования.
Похожие материалы
www.metalcutting.ru
Пресс штамповочный и другое оборудование для ковки и штамповки
Пресс штамповочный, при помощи которого выполняется ковка металлических заготовок, работает по достаточно простой схеме. Принцип его работы, по сути, схож с принципом действия обычного молотка, которым наносятся удары по металлическому изделию, чтобы деформировать его и придать ему требуемую конфигурацию.
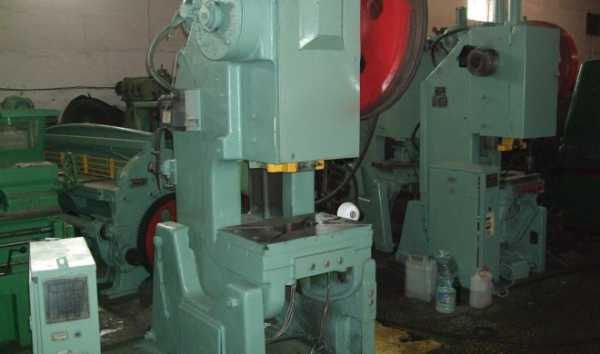
Механические прессы типа К2130 применяются на участках холодной листовой штамповки
Штамповочные прессы гидравлического и кривошипного типа
С того момента, как люди научились выполнять обработку металла давлением, работа специалиста, который ей занимался, считалась одной из самых почетных. С течением времени потребность в металлических изделиях, полученных по технологии ковки, только возрастала, в них стала нуждаться и активно развивающаяся промышленность. Все это привело к тому, что для ковки стал использоваться не ручной труд кузнецов, а специальное оборудование для штамповки.
Достаточно распространенным типом устройств, используемых для ковки, является своеобразный аналог молота – штамповочный пресс. Применяя такое штамповочное оборудование, можно выполнять целый перечень технологических операций, а именно: изменение формы заготовки путем ее пластической деформации, формирование на ее поверхности заданного рельефа, вырубание отдельных фрагментов и др. На таком устройстве, в частности, придают форму заготовкам, для изготовления которых было использовано литье. Прессы, применяемые для штамповочных операций, могут быть кривошипными или гидравлическими.
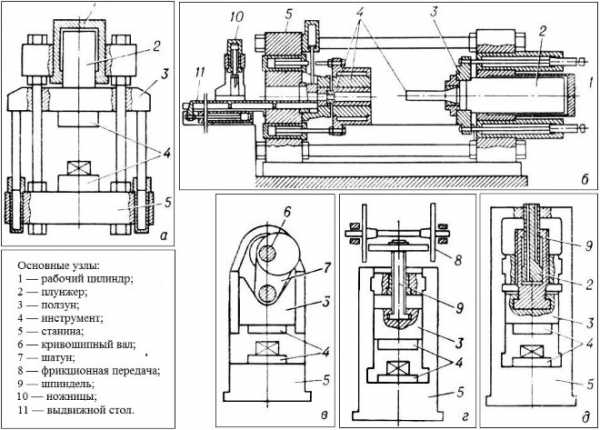
Схемы прессов: а – вертикальный гидравлический; б – горизонтальный; в – кривошипный; г – фрикционный; д – гидровинтовой
Пресс кривошипный применяют в тех случаях, когда необходимо выполнить несложную обработку металла давлением. Основным элементом такого оборудования, который преобразует вращательное движение вала приводного электродвигателя в возвратно-поступательное перемещение ползуна, является кривошипно-шатунный механизм. Именно поэтому пресс кривошипный часто называют штамповочным кривошипно-шатунным прессом. Он очень популярен как среди производственников, так и среди частных мастеров, существуют даже модели настольного кривошипного пресса. Объясняется такая популярность не только высокой эффективностью и функциональностью этого оборудования, но также и тем, что обслуживание и ремонт кривошипных прессов не вызывает особых проблем.
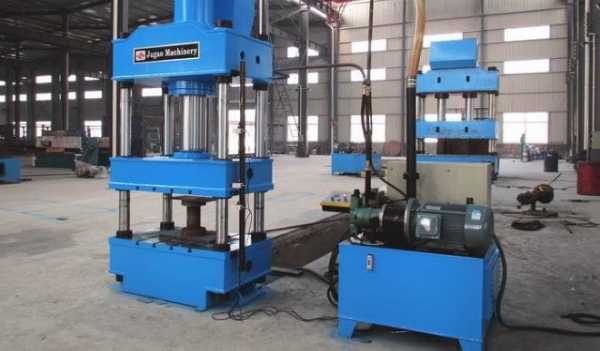
Пресс штамповочный гидравлический 4-х колонный
Гидравлические штамповочные прессы оснащаются двумя рабочими камерами, в которых в рабочей жидкости создается требуемое давление. Жидкость под давлением поступает в цилиндр с другим поршнем, посредством которого и сообщается возвратно-поступательное движение ползуну.
Радиально-ковочное оборудование для горячей обработки металла
Радиально-ковочный станок используется для того, чтобы с высокой производительностью изготавливать валы различного диаметра. На таком агрегате можно наладить производство до 300 тысяч готовых изделий в год, чего вполне достаточно для того, чтобы обеспечить ими крупное производственное предприятие.
Ограниченность использования такого станка для штамповки металла объясняется не только его высокой стоимостью, но еще и тем, что настройка его рабочих режимов представляет собой достаточно сложный процесс, поэтому выполнять ее целесообразно лишь в том случае, если планируется выпускать изделия определенного диаметра большими партиями.
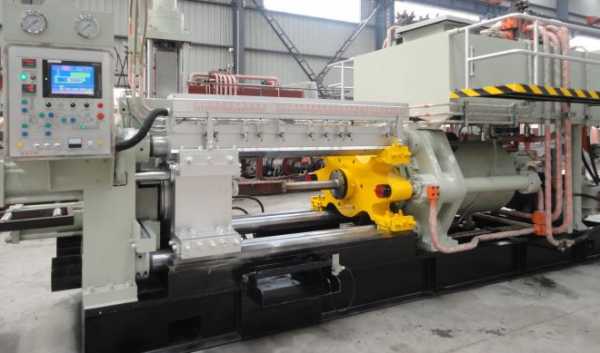
Радиально-ковочная машина (РКМ) обеспечивает высокую точность штамповки, выдавая детали с минимальными припусками
Последовательность действий, в процессе которых выполняется радиальная ковка, выглядит следующим образом.
- Деталь, чтобы довести ее до требуемой температуры нагрева, подают в индукционное устройство.
- После того как металл приобретет требуемую степень пластичности, деталь по роликовому контейнеру (рольтангу) отправляют к захватному устройству, с помощью которого она подается в зону обработки.
- Там заготовка фиксируется элементами другого захватного устройства, после чего на нее воздействуют посредством специальных бойков.
- Для равномерной обработки со всех сторон деталь постоянно вращают, для чего используется специальный захватный механизм.
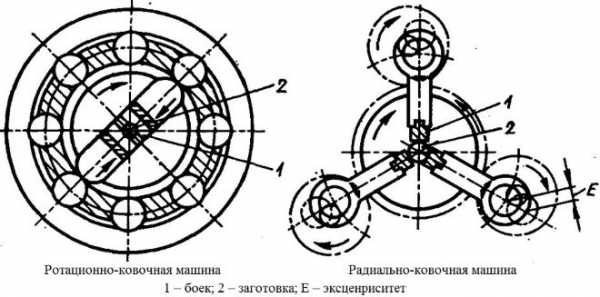
Схемы действия ковочных машин радиального и ротационного типа
Для того чтобы привести в движение рабочий механизм оборудования для радиальной ковки, используют кинематическую схему, элементами которой являются:
- приводной электродвигатель;
- клиноременная передача;
- четыре установленных вертикально вала с эксцентриковыми буксами;
- шатун с закрепленными на нем бойком и ползуном.
Основные элементы автоматики станка – это копирные барабаны, которые отвечают как за синхронное сближение бойков, так и за последующее движение заготовки. Вращение захвату, в котором удерживается обрабатываемая деталь, сообщается электродвигателем через элементы червячной передачи. Торможение данного механизма, которое осуществляется в момент ковки, обеспечивает пружинная муфта.
Одной из разновидностей ковочного оборудования является горизонтально-ковочный станок, в котором обрабатываемая деталь также располагается параллельно земле. Устройства данного типа используются преимущественно для формирования торцевых утолщений на заготовках стержневого типа. Деталь при обработке располагается в разъемной матрице, каналы которой ориентированы в горизонтальной плоскости.
Процесс обработки, выполняемой на таком станке, происходит в следующей последовательности.
- Заготовка укладывается в неподвижную часть матрицы.
- Подвижная часть матрицы, соединенная с ползуном, приводится в действие посредством коленчатого вала.
- Приближаясь к неподвижной половине формы, подвижная часть матрицы плотно охватывает обрабатываемый стержень.
- После зажима детали верхней частью формы коленчатый вал, соединенный с шатуном, приводит в действие ударные пуансоны.
- По окончании обработки все подвижные части станка возвращаются в исходное положение, а подвижная и неподвижная части формы размыкаются.
Ковочный молот с пневмоприводом
Пневматический пресс – это эффективное, но в то же время доступное по стоимости ковочное оборудование, отличающееся, кроме того, компактными габаритами. Работает такой станок за счет энергии сжатого воздуха, за подачу которого к механизмам отвечает встроенный компрессор. Работу компрессора, поршни которого, двигаясь в его главном цилиндре, как раз и создают поток воздуха с требуемым давлением, обеспечивает приводной электродвигатель.
Поскольку работу ударного механизма пневматического ковочного станка обеспечивает кривошип, то его конструкция напоминает устройство кривошипного пресса. Перед запуском такого оборудования компрессорный и рабочий поршни в главном цилиндре находятся в крайнем верхнем и крайнем нижнем положениях. Когда станок запускается в действие, поршни начинают двигаться по направлению друг к другу, сжимая находящийся между ними воздух, давление которого передается на кривошип, напрямую соединенный с бойком. На один удар рабочей части молота пневматического станка приходится один оборот кривошипного механизма. Соответственно, чтобы воздействие молота на заготовку выполнялось с более высокой частотой, необходимо обеспечить более интенсивную работу компрессора. Даже несмотря на свои небольшие габариты, пневматический пресс может обеспечить массу удара молота, доходящую до 1 тонны.
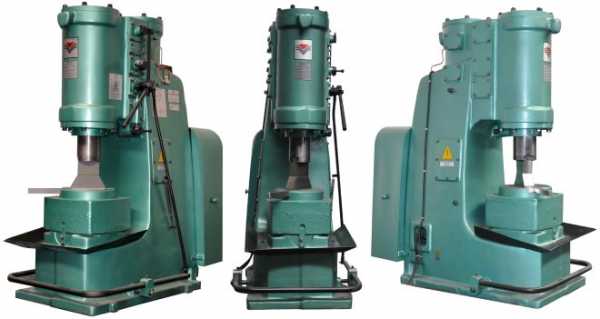
Молот кузнечный пневматический МА-4129 предназначен для горячей штамповки в открытых штампах
По похожему с пневматическим прессом принципу работает паровоздушный молот, в котором энергию удара обеспечивает горячий пар, подающийся непосредственно из котла или через специальный компрессор. Масса ударов, которой позволяет добиться такое оборудование, может доходить до 8 тонн, а скорость их нанесения составляет 50 м/сек. Работать оно в зависимости от модели может в автоматическом режиме, когда удары по детали наносятся непрерывно, или в ручном, когда для запуска в действие бойка необходимо нажать на соответствующую кнопку или педаль.
Механические молоты могут использоваться для:
- свободной ковки или ковочных операций, при выполнении которых для формирования готового изделия используется прессформа;
- штамповочных операций с деталями из листового металла – резки по ровной или кривой линии, вырубки по различному контуру, пробивки отверстий (дыропробивной пресс) и др.;
- выколотки – изготовления изделий с использованием специального шаблона.
Ковочное оборудование ротационного и вальцевого типа
На крупных производственных предприятиях для выполнения ковочных операций часто применяется конвейерное оборудование вальцевого типа. Заготовки на нем обрабатываются методом обжима, который выполняют вращающиеся вальцы. По похожему принципу работают и ротационно-ковочные машины, обработка деталей в которых также осуществляется в процессе вращения рабочих органов.
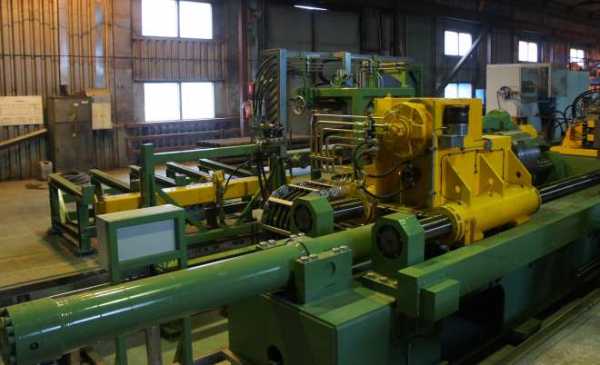
Метод ротационной ковки обеспечивает безотходную обработку заготовок
Специалистам, которые профессионально занимаются ковочными и штамповочными операциями, приходится решать целый ряд вопросов, чтобы получить изделие требуемого качества. В числе таких вопросов, в частности, находятся выбор оборудование, разработка и изготовление пресс-форм, оснащение станков различными инструментами и приспособлениями.
Оценка статьи:
Загрузка...Поделиться с друзьями:
met-all.org
Штамповочный пресс для металла: устройство и принцип работы
Содержание статьи:
Штамповка — это один из наиболее частых видов обработки металла, который представляет собой деформацию, придающую детали необходимую форму методом выдавливания на поверхности определенного рельефа, узора, отверстий. Процесс этот осуществляется на специальных прессах различной конструкции.
Виды штамповки и оборудования
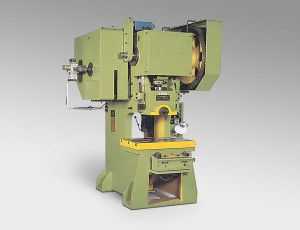
однокривошипный штамповочный пресс
На производстве используются два вида штамповки:
- горячая;
- холодная.
При горячем способе обрабатывается нагретый металл. При этом улучшаются качества материала: он становится плотнее, однороднее. Плюс холодного метода в том, что на поверхности не появляется слой окалины, размеры детали получаются точнее, поверхность глаже.
Штамповка может быть листовой или объемной. Листовым методом производят: посуду, ювелирные изделия, детали часов, климатической техники и микросхем, оружие, медицинское оборудование, детали для автомобиле-, машино- и станкостроения. Полученные детали не требуют дальнейшей обработки. В ходе объемного прессования холодный или раскаленный металл продавливается в формах.
В металлообработке прессы используются для:
- производства поковок;
- запрессовки шестеренок, подшипников;
- объемной и листовой штамповки.
Станки для прессования могут основываться на принципах механики или гидравлики, обрабатывать материалы статическим или ударным способом.
Механические бывают:
- эксцентриковые;
- кривошипными.
Кривошипные станки выполняют холодную и горячую штамповку металла давлением: вытяжку, вырубку и прорубку. Гидравлические прессы используются для объемной кузнечной обработки металла. Согласно технологическим возможностям прессы делятся на: универсальные, специальные и специализированные. Универсальные можно использовать практически для любых видов ковки (пример — гидравлический ковочный станок). Специализированные станки выполняют только один технологический процесс (пример — кривошипные вытяжные). Специальные прессы производят конкретный вид изделий, используя одну технологию.
Принцип работы и устройство прессов различных типов
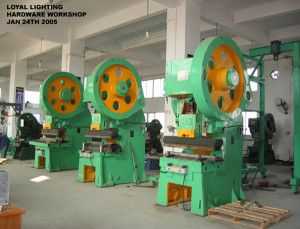
цех по штамповке металла
Любой стандартный штамповочный станок состоит из следующих основных узлов: мотора, передачи, исполнительного механизма. Передача и двигатель вместе составляют «привод». Главная характеристика привода — это вид связи двигателя и исполнительного механизма: механическая или не жесткая (жидкость, газ, пар). Рабочие органы прессов: валки, ползун, траверсы, ролики, бабы.
Кривошипно-шатунный пресс
Привод станка вращается, движение на ползуне преобразуется в возвратно-поступательное. Под действием этого движения при помощи штампа обрабатывается металл. Все детали станка производят из прочной стали и оснащаются ребрами жесткости. Движение ползуна происходит по жесткому графику. Усилие по ползуну достигает 8 тысяч тонн. Кривошипные ковочные установки позволяют ускорить, упростить и удешевить производство деталей, сэкономить до 30% проката. Все кривошипные станки делятся на простые, с двойным и тройным действием.
Кривошипно-шатунный пресс способен выполнять следующие виды работ:
- штамповку в открытых и закрытых матрицах;
- формирование заусенца;
- выдавливание;
- прошивку;
- комбинированную обработку.
Механический пресс воздействует на материал ударом, тогда как гидравлический, прилагая меньшую силу, получает больший эффект. Поэтому вторые используют для изготовления крупных изделий с толстыми стенками.
Гидравлические прессы
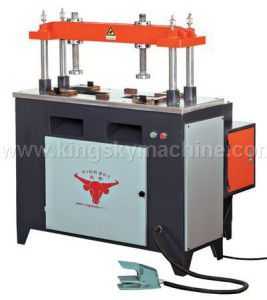
гидравлический пресс
Способны проштамповывать поверхность, продавливать и ковать изделия из металла. Они также применяются для переработки металлических отходов. Действие станка основано на увеличении силы давления на металл во множество раз. Пресс представляет собой два сообщающихся цилиндра с водой, между которыми проходит труба. В цилиндрах установлены поршни. Принцип работы пресса основан на законе Паскаля.
Радиально-ковочный аппарат
Обрабатывает металл горячим способом. Болванка поступает в нагревательный модуль, функционирующий по принципу индукции. Здесь она нагревается, когда металл становится достаточно податливым, подается через конвейер на механизм захвата, подающий заготовку прямо в зону обработки. Ковка или штамповка осуществляется бойками, в процессе заготовка все время крутится, благодаря чему она обрабатывается равномерно со всех сторон. Пресс работает от электромотора, соединенного клиноременной передачей с валами. Они размещены вертикально и направляют движение на шатун и боек, между которыми установлен ползун. Чтобы все движения механизма были синхронными, существуют копирные барабаны. Держатель болванки вращается электромотором посредством червячных передач. Пружинная муфта в нужные моменты притормаживает движение.
Электромагнитный пресс
Это новейшая разработка, которая только начинает использоваться в промышленности. Рабочий орган станка — сердечник электромагнита, который совершает движения под действием электромагнитного поля. Сердечник двигает ползун или штамп, пружины возвращают ползун в исходное положение. Такие станки отличаются высокой производительностью и экономичностью. На сегодняшний день существуют модели с небольшой амплитудой движения рабочего органа — 10 мм и усилием не более 2,5 тонны.
Работа штамповочного станка черновой обработки в видеоролике:
Обзор прессов IPONMAC и их характеристик
Серия модели | KD 23D | HL41 | ПГ41 |
Номинальное усилие, т | 10-80 | 40-315 | 40-315 |
Высота открытия/просвет, мм | 130-280 | 800-1600 | 800-1600 |
Размер стола/нижней плиты, мм | до 520*860 | до 1400*1200 | до 1400*1200 |
Мощность привода, кВт | 1,1-7,5 | 5,5-30 | 5,5-30 |
Масса, кг | 600-5280 | 3000-36000 | 3-36000 |
stanokgid.ru
Пресс для штамповки листового металла – виды штамповочного оборудования
Для получения различных изделий из плоской металлической заготовки применяются прессы для штамповки листового металла. Оборудование оказывает механическое воздействие на лист, вызывая пластическую деформацию материала. В результате изменяются размеры и форма детали по заданным параметрам. Методом штамповки можно получить изделия любой геометрической формы, которые отличаются точностью размеров и высокими прочностными характеристиками.
Разновидности штамповочных технологий
Штамповочный процесс обработки заготовок может осуществляться горячим или холодным методом. Эти технологические разновидности предполагают использование специального оборудования и применение определённых условий обработки металла.
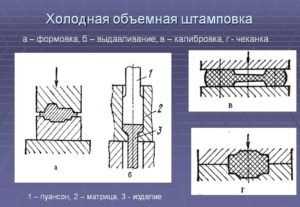
Холодная штамповка является одним из разновидностей штампования
Методом горячей штамповки обрабатываются заготовки, предварительно нагретые в специальных устройствах до заданной температуры. Горячая штамповка необходима, когда для обработки холодного сплава не хватает мощности оборудования. Нагревательными устройствами могут служить электрические или плазменные печи. Такой метод требует точного расчёта параметров готовой детали с учётом усадки металла в процессе остывания.
При холодной штамповке детали формируются за счёт механического давления элементов штамповочного пресса. Холодный вариант штамповки считается более распространённым методом обработки металла. Он не требует дополнительного оборудования, сложных расчётов и механической доработки деталей. Благодаря этому методу увеличиваются прочностные показатели материала. Полученные изделия отличаются высоким качеством поверхности и точностью.
Разновидности технологических операций
Технологические операции с металлическим листом бывают разделительные и формоизменяющие.
Разделительные штамповочные операции выполняются на оборудовании, которое оснащено специальным инструментом. В результате от заготовки отделяется определённая часть по прямой линии или заданному контуру. Отделение части листа происходит в следующих процессах:
- Отрезка. Для выполнения этого действия оборудование оснащено дисковыми, вибрационными устройствами или гильотинными ножницами.
- Обрезка. Эта операция отделяет крайние части полученного изделия.
- Пробивка. В металлическом листе с помощью штампа создаются отверстия различной конфигурации.
- Вырубка. Из заготовки получают фигурную деталь с замкнутым контуром.
Формоизменяющие операции предназначены для создания изделия с иными параметрами и размерами без механического разрушения. Различают следующие виды этих операций:
- Отбортовка. Контур заготовки или внутренние отверстия подвергаются воздействию штампа для формирования бортов определённых размеров.
- Вытяжка. Эта операция является разновидностью объёмной штамповки, при которой из плоского материала получают пространственный элемент.
- Обжим. Для сужения торцов полой заготовки применяется штамп с матрицей конического типа, имеющей сужающую рабочую область.
- Гибка. В результате операции изменяется кривизна поверхности путём гибки металла и деформирования заготовки.
- Формовка – это изменение формы отдельных участков за счёт уменьшения толщины детали без нарушения внешнего контура изделия.
- Пуклёвка. Соединение штампом двух пластинок без использования дополнительных элементов.
Типы штамповочного оборудования
Для получения изделий из металлического листа применяются прессы, оснащённые различными штампами. В процессе работы оборудования верхняя составляющая штампа двигается, нижняя часть остаётся неподвижной.
Деформирование заготовки происходит в момент соприкосновения частей оборудования. Существуют разнообразные модели штамповочных прессов, что позволяет выбрать подходящий станок для изготовления требуемых деталей.

Гидравлическая штамповочная машина
Прессы для штамповки металла бывают:
- кривошипно-шатунного типа;
- гидравлические;
- радиально-ковочного типа;
- электромагнитного типа.
Кривошипные прессы являются оборудованием простого типа и могут быть двойного или тройного действия. Своё название прессы получили от кривошипно-шатунного механизма, который представляет собой основной конструктивный элемент станка. Принцип работы механизма основан на преобразовании вращательного движения от привода в возвратно-поступательное периодичное движение элемента пресса – ползуна.
Механизмы для обработки металла
Гидравлический пресс способен развивать значительное усилие до 2 тыс. тонн. Он применяется для операций гибки или объёмной штамповки толстостенных изделий. Действие механизма основано на перемещении поршней двух сообщающихся гидроцилиндров, которые имеют разный диаметр. Именно разница диаметров определяет величину усилия, которое может развивать пресс для штамповки металла.
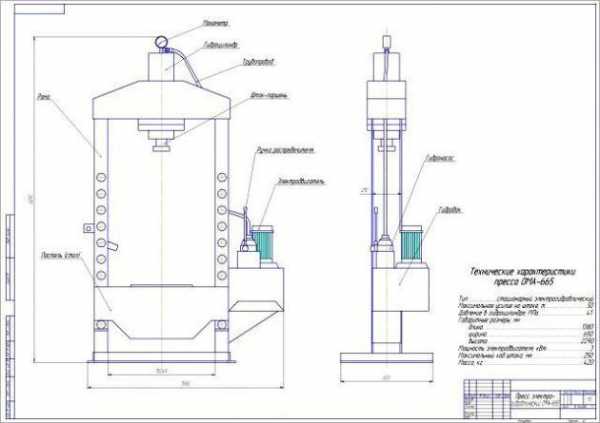
Чертёж гидравлического пресса
Радиально-ковочный станок предназначен для выполнения формоизменяющих операций в целях получения цилиндрических изделий. В конструкцию механизма входит индукционная печь для предварительного нагрева детали. В процессе обработки обеспечивается вращение заготовки от электродвигателя при прохождении через зону ковки.
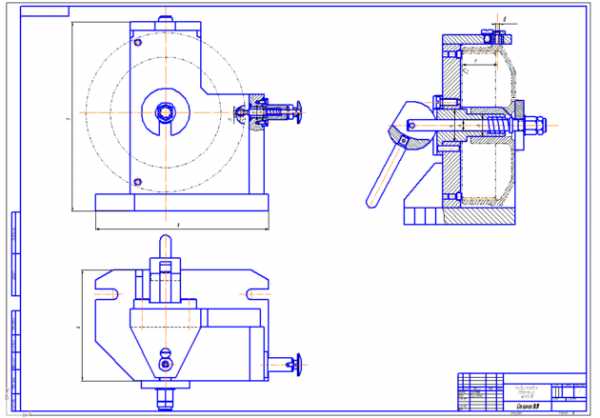
Чертёж радиально-ковочного станка
Электромагнитные прессы – новое высокопроизводительное экономичное оборудование для штамповки. Принцип действия основан на движении электромагнитного сердечника, который направляет исполнительный механизм станка к металлической детали.
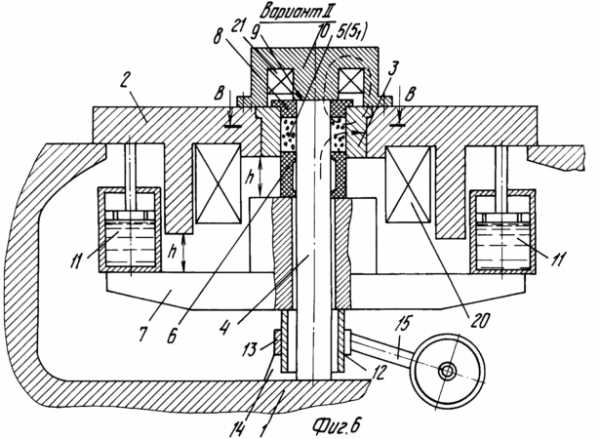
Чертёж электромагнитного пресса
Особенности открытых и закрытых штампов
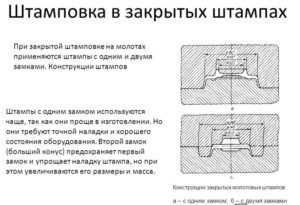
Штамповка закрытым способом
Штамповочное оборудование может быть оснащено открытыми или закрытыми штампами. В открытом штампе избыточный металл вытекает в заусенец или облой, который выполняет определённую функцию. Основными недостатками этой технологии являются: потеря сплава на облой, снижения качества изделия из-за перерезанных волокон при удалении заусенцев.
Закрытые штампы используются для изготовления изделий простой формы. Эта безоблойная технология отличается экономией металла, отсутствием затрат на обрезку заусенцев, высоким качеством продукции из-за всестороннего сжатия. Волокна металла не подвергаются перерезанию. Метод обработки в закрытом штампе применяется для малопластичных сплавов. Основными недостатками считаются: необходимость точной дозировки сплава, сложная конструкция штампа.
В современном производстве штамповка является преимущественно подготовительной операцией, которая позволяет изготавливать детали как для электроники, так и для воздушных или водных судов. Полученная продукция в дальнейшем подвергается сварке, резке, клёпке и другим методам обработки в зависимости от технологического процесса.
Видео по теме: Листовая штамповка
promzn.ru
Пресс-Штамп - Кто мы
Предприятие «Пресс-штамп» было создано в 2000 г, как холодно-штамповочное производство. Наша производственная база — 14 прессов с усилием от 25 до 100 тонн, а также заготовительное оборудование на резку металла на полосы.
Предприятие включает в себя конструкторское и технологическое бюро. Эти бюро занимаются разработкой и изготовлением штампов для холодной листовой штамповки. При проектировании и изготовлении используется система ADEM.
Для изготовления штампов у нас имеется инструментальный участок, включающий всё что необходимо для изготовления. А именно:
- вертикальный обрабатывающий центр с ПУ по 3-м координатам X; Y; Z с перемещением 720x460x510 мм; максимальный вес заготовки — 500 кг.
- электроэрозионный станок проволочной резки с ПУ 2-х координат и наклона проволоки 22º (Нmax=270мм, зона резания 350x550 мм, стол 500x800 мм.)
- универсальные фрезерные станки с размерами стола 700x250 мм и 1200x400 мм.
- токарные станки с max - D=250, L=500 мм; D=400, L=1000 мм.
- сверлильные станки: (в т. ч. консольный с L поперечн.=850, Нmax=1000).
- расточной станок: рабочий стол 800x400 мм, перемещение стола 710x400x200 мм (mах вес заготовки 320кг и Н=450мм, горизонтальный поворотный стол D=400мм, универсальный поворотный стол D=280 мм). -плоскошлифовальный станок (продольное перемещение max — 1000 мм, поперечное перемещение max — 500 мм).
При изготовление используется современные высокотехнологичные материалы фирмы «BOHLER» (Австрия), что позволит увеличить срок эксплуатации штамповочной оснастки.
Испытания и наладка штампов производится на наших 14 кривошипных прессах усилием от 25 до 100 тс. Настройка и наладка производится опытным наладчиком.
В процессе десятилетней истории мы много узнали о сварке и используем у нас на предприятии контактную сварку до h 5+5 и d 10+10, аргоную сварку (титан, медь, алюминий и т.д.), электродуговую сварку, полуавтоматическую сварку в среде углекислого газа.
Производим работы по нанесению покрытия высококачественными порошковыми эмалями с высокими показателями укрывистости и розлива, хорошей коррозийной стойкостью, высокой ударостойкостью и адгезией (цвет — по желанию заказчика).
В наших планах изготовление пресс-форм для пластиковых деталей, литьевых, порошковых, резино-технических, пробковых и т. д.
Более подробную информацию по каждому виду услуг вы можете найти на соответствующих вкладках.
press-shtamp.ru
Пресс-Штамп - Изготовление пресс-форм
Пресс-штамп занимается инструментальным производством, в частности — производством пресс-форм, изготовлением штампов и прочей технологической оснастки. Мы готовы предложить изготовление пресс-форм большинства типов. Как правило, технологическая оснастка изготавливается по стандартным чертежам. Однако мы также практикуем изготовление прессформ по эскизам и технической документации заказчика. Современное производство дает нам возможность воплощать в конкретные изделия даже наиболее сложные проекты. По сути, наше предприятие — это современный завод штампов, обладающий мощным техническим потенциалом и широкими возможностями.
Изготовление пресс-форм производится на современном высокотехнологичном оборудовании.
Конструкторская документация обрабатывается с использованием современных средств компьютерного проектирования. Сотрудники компании обладают опытом в области проектирования и изготовления пресс-форм. После приобретения нового уникального высокоскоростного обрабатывающего центра, с рабочей зоной обработки 720×460 мм, и мощной системой ЧПУ «FANUC» цех расширил свои возможности и теперь способен изготавливать пресс-формы повышенной сложности. Большое значение при обработке недоступных поверхностей оказывает наличие в цехе электроэрозионного станка AU-500iA. Размеры ванны составляют 1000×500 × 270, стол 500×700, зона реза 550×350, максимальный наклон проволоки составляет 22°. Проволочные электроэрозионные станки используются для финишных операций не только при вырезании оформляющих матриц и пуансонов, но и калибров, приспособлений для слесарной доводки готовой продукции.
Изготовление пресс-форм для пластиковых деталей, литьевых, порошковых, резино-технических, пробковых и т. д.
При изготовление используется современные высокотехнологичные материалы фирмы «BOHLER» (Австрия), что позволит увеличить срок эксплуатации пресс-форм.
press-shtamp.ru
Штамп - Процесс изготовления штаповки для металла
Штамповка это технологическая обработка металла давлением. На промышленных предприятиях используется объемная холодная и объемная горячая штамповка. Для металлообработки методом штамповки используются специальные штампы и оснастка.
Холодная штамповка изделий производится из калиброванного прутка или проволоки. Использование метода холодной объемной штамповки позволяет получить детали со стабильными механическими свойствами. Объясняется это тем, что в металле отсутствует рекристаллизация материала, который к тому же под воздействием давления упрочняется. Изделия (гайки, болты, соединительные элементы), полученные методом холодной штамповки, не имеют поверхностной окалины, их поверхность отличается высоким качеством и не имеет шероховатостей.
Горячая штамповка на объемных штампах производится при нагреве металла до температуры 200- 1200 градусов, в зависимости от сплава металла и условий его обработки. Материалом для изготовления служат прокатные прутки, которые делят на мерные заготовки, соответственно размерам будущей поковки. Масса изделий может быть от нескольких грамм (гайка, шуруп) до 8 тонн (оборудование для гидростанций).
Точность работ зависит от массы, конфигурации изделия и, может быть повышена при последующей калибровке. Горячая штамповка позволяет получить изделия сложной конфигурации с высокой точностью и однородные по структуре. В процессе металлообработки для изготовления отдельных деталей и узлов используются различные методы штамповки. Для горячей объемной штамповки и холодной листовой штамповки изделий необходимо иметь определенное количество штампов, шаблонов и штамповой оснастки. Изготовлением штампов Днепропетровск и оснастки штамповочного производства занимаются предприятия, которые имеют на своем вооружении высокотехнологичное современное оборудование и штат работников с высокими профессиональными знаниями.
Штамп – это инструмент, который используется в массовом производстве для получения идентичной детали, заготовки или поковки методом пластической деформации. Ресурс изготовленных штампов составляет до 200-300 тысяч ударов за период между двумя капитальными ремонтами. Штампы состоят из двух половинок, пуансона и матрицы, классифицируются на молотовые и прессовые штампы.
К штампам предъявляются следующие требования:
- Прочность и стойкость конструкции
- Технологичность
- Надежность крепления деталей
- Удобная загрузка заготовки
- Быстрая и легкая замена изношенных деталей
- Легкое удаление готового изделия из штампа
- Безопасность работ
- Высокая экономичность изготовления.
Эти требования обеспечиваются рациональной конструкцией при изготовлении штампа в Днепропетровске и других городах Украины. Конструкторы предусматривают решение вопросов по правильности формы и размера заготовки по переходам, точность фиксирования, надежность зажима заготовки, безопасность и удобство закладывания заготовки в штамп, и ее удаление. Предусматривается возможность транспортировки тяжелых и объемных штампов.
press-shtamp.ru