Ручной аппарат для плазменной резки металла. Применение плазменного резака
Аппарат для плазменной резки металла, все о ручных плазморезах
- Содержимое:
- Что такое плазморез, что им можно делать
- Принцип работы плазмореза, как устроен плазморез
- Какой и как выбрать плазморез для дома
- Как правильно резать плазморезом
- Ручная газовая и плазменная резка металла, что лучше
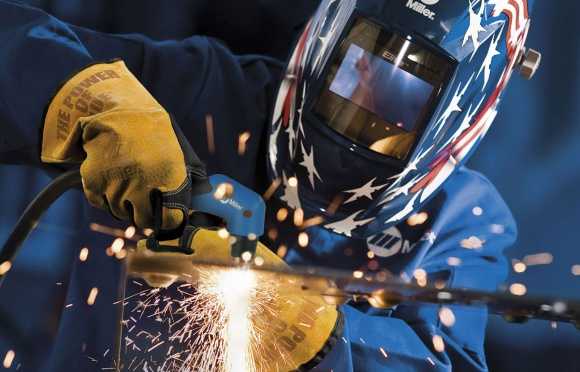
Что такое плазморез, что им можно делать
Переносная ручная плазменная резка металла в бытовых целях используется в основном во время капитального строительства. Плазморез позволяет заменить малоэффективную и опасную болгарку. С помощью плазмореза можно раскраивать необходимый листовой металлопрокат и трубы.Еще одна сфера, где пригодится ручной аппарат плазменной резки металла - это художественная обработка материала. Точность, простота в эксплуатации и доступность использования плазменной установки практически в любых условиях, позволяет использовать оборудование в следующих целях:
- Промышленность - аппарат воздушно-плазменной резки металла в основном применяется в случаях, где существует необходимость в быстром разрезании любого токопроводящего материала. В промышленных целях используют не только аппарат для ручной плазменной резки металла, но и специальные плазменные станки позволяющие автоматизировать и сократить время выполнения работ.
- Бытовые цели - в этой сфере оборудование для ручной плазменной резки металла пока не получило широкого распространения. В основном это связано с тем, что ручные плазморезы сравнительно недавно поступили в свободную продажу. В основном применение плазмореза в бытовых целях связано с фигурной резкой металла. Некоторые строительные бригады используют оборудование во время кровельных, сантехнических и других работ.
В зависимости от основного назначения, аппарат для резки металла плазмой может отличаться техническими характеристиками и возможностями. Перед выбором плазменного оборудования следует определиться, как именно будет использоваться резак.
Принцип работы плазмореза, как устроен плазморез
Воздушно-плазменная резка основана на принципе подачи разогретого воздуха под давлением на обрабатываемую поверхность. Что такое плазма - это воздух, который разогревается до температуры 25 – 30 тыс. градусов с помощью электрической дуги.Что происходит при этом? Принцип действия плазмореза основан на изменении свойств воздуха при его моментальном разогревании до максимально высоких температур. В этот момент воздух ионизируется и благодаря этому начинает пропускать электрический ток.
Двойное воздействие плазмы и электричества позволяет ускорить процесс резки металла. Чтобы это стало возможным в конструкцию резака входят следующие узлы:- Плазмотрон - это резак, с помощью которого и выполняются все основные задачи. Устройство горелки плазмореза может быть прямого и косвенного воздействия:
- Плазморез прямого воздействия используется для обработки токопроводящих материалов, в таких случаях заготовка включается в электрическую цепь и отвечает за возникновение искры.
- Плазморез косвенного воздействия применяется в более дорогих и сложных устройствах и используется для обработки материалов, не проводящих электричество. Электрод в таких устройствах находится непосредственно в резаке.
- Сопло - одна из самых функциональных деталей плазматрона. В зависимости от диаметра сопла, плазморезом можно делать либо простые операции, либо сложную фигурную резку. Скорость разрезания материала в основном зависит от длины сопла. Максимальным считается соотношение 1,5; 1,8 к диаметру сопла.
- Электрод - используется в дорогих моделях плазморезов косвенного воздействия. Преимущественно электроды изготавливаются из гафния.
- Компрессор - чтобы трансформировать воздух в плазму необходимо не только довести его до определенной температуры, но и создать поток определенной скорости. Именно по этой причине для плазмореза нужен компрессор. К качеству компрессора предъявляются высокие требования. Так, чтобы была возможность производства плазмы, воздух в горелку должен подаваться сухой и без примесей машинного масла. Важным является обеспечение равномерного потока воздушных масс без пульсации. Ручные плазменные резаки по металлу со встроенным компрессором являются оптимальным вариантом, так как в них производитель установил оборудование полностью соответствующее требованиям для проведения работ. В плазморезах со встроенным компрессором по умолчанию установлен влагоочиститель или осушитель. Плазморез с компрессором обеспечивает максимальную производительность и увеличивает срок эксплуатации резака.
Для мощных промышленных устройств понадобится отдельно приобрести не только компрессор, но и осушитель воздуха. При выборе плазмореза необходимо проследить, чтобы параметры каждого из этих узлов подходили остальным устройствам.
Какой и как выбрать плазморез для дома
При выборе плазмореза для дома необходимо учитывать не только технические параметры и производительность самой установки, но и комплектующие устройства. Обратить внимание необходимо на следующее:- Тип питания - оборудование может подключаться как к обычной сети в 220В, так и трехфазной в 380В. От этой особенности во многом зависит производительность плазмореза и скорость резки. Для бытовых нужд лучше выбрать ручной плазморез с тем типом подключения, который есть в наличии. Производительности бытовой модели работающей от розетки будет достаточно для проведения всех необходимых работ по дому.
- Параметры мощности - наиболее популярными для бытового применения являются модели с производительностью 60-90 ампер. Бытовые плазморезы легко справляются с толстым металлом толщиной до 3 см. Если планируется ручная резка металла до 100 мм плазмой, тогда лучше выбрать модели, выдающие на выходе 90-170 ампер.
- Продолжительность работы - этот коэффициент можно посмотреть в технической документации установки. Обычно он обозначается сокращением ПВ. Если указано соотношение 80%, тогда плазморезом надо пользоваться в течение 8 минут, не больше. Для бытовых нужд будет достаточно оборудования с индексом ПВ 50-60%.
- Сопло для плазмореза - скорость резки напрямую связано с соплом. На скорость раскроя влияет соотношение диаметра к длине сопла. Скорость резки также указывается в технической документации. Выбор комплектующих зависит от используемой силы тока. Чем больше диаметр сопла, тем больше может быть напряжение на выходе.
- Дополнительные расходники к плазморезу. Стол-копир для ручной плазменной резки позволяет выполнять самые сложные детали, если процесс поставлен на конвейер. Часто даже в домашних условиях требуется воссоздать точную копию сделанной заготовки, для этого и проведения остальных работ, и предназначен стол-копир. Помимо стола понадобится определиться с другими комплектующими и приспособлениями, предназначенными для проведения работ с помощью плазмореза.
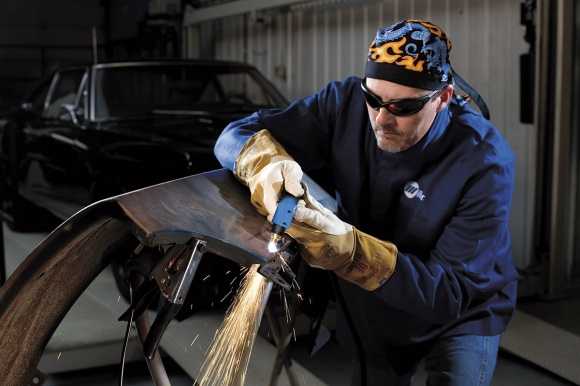
Многие критерии критичные для промышленного оборудования практически не влияют на производительность бытовой модели. Продолжительности работы плазмореза с индексом ПВ 50% будет достаточно для проведения работ в доме. Промышленное оборудование обычно имеет коэффициент равный 100%.
Как правильно резать плазморезом
Правильно работать плазморезом можно научиться практически с первого раза. Качественный рез достигается благодаря практике. Основные принципы работы с плазменным оборудованием следующие:- На начальной стадии работ в аппарат подается сжатый воздух под давлением.
- Выполняется несколько надрезов при более высоком токе, после чего его силу уменьшают до необходимых параметров.
- Разрез делают в соответствии с выбранными параметрами. Неправильно подобранная сила тока или скорость резки свидетельствует окалинами, которые появляются в процессе резки.
- Держак для плазмореза располагают под углом около 40 градусов.
- После окончания резки, на горелку будет еще какое-то время подаваться воздух для охлаждения нагретого элемента.
При работе с плазматроном необходимо соблюдать требования относительно использования средств индивидуальной защиты. Потребуется одевать очки для плазменной резки и перчатки, даже если планируется использовать аппарат относительно короткое время.
Ручная газовая и плазменная резка металла, что лучше
Минусами газовой резки является зависимость от баллонов, что не всегда удобно, а для бытовых условий заправить их часто проблематично.
Плазменная резка имеет свои минусы, связанные в основном с тем, что качество реза напрямую зависит от профессионализма мастера. Также подаваемый воздух должен соответствовать определенным критериям, что требует использования дополнительного оборудования.
При плазменной резке может понадобиться использовать не только очки для работы, но и респираторную маску, и другие средства защиты. Проводить работы в помещении без хорошей вентиляции запрещается.
stroy-plys.ru
10 типичных ошибок при плазменной резке
Опытному оператору, в распоряжении которого имеется правильно обслуживаемое оборудование плазменно-дуговой резки, удается избежать ситуаций, которые могут повлечь многочасовые простои оборудования ремонтной мастерской. Кроме того, он может сэкономить эксплуатационные затраты на тысячи долларов. Такая экономия позволит повысить прибыль выполняемых работ по резке материалов и прибыль вашей компании в целом. Следует избегать ошибок, которые описаны ниже:
- Использование расходных деталей до отказаСреди использованных деталей, которые Вы выбрасываете, наверняка есть те, которые эксплуатировались до отказа. При использовании сильно изношенных расходных деталей могут разрушаться металлические части в хорошем состоянии. Кроме того, это может привести к затратным поломкам резака и длительному простою, которого можно было бы избежать. Эксплуатация деталей до отказа — это ошибка, которую можно легко избежать. Есть несколько признаков износа расходных деталей. Очень часто опытный оператор может выявить износ деталей по звуку или цвету дуги либо по небольшим изменениям высоты резака. Однако самый лучший способ узнать состояние деталей резака состоит в том, чтобы периодически проверять качество кромки реза металла и детали резака, когда качество резки начнет снижаться. Ведите учет среднего срока службы деталей (может выражаться в количестве зажиганий или в фактическом времени «на дуге») и рассчитайте ориентировочные ожидаемые сроки службы деталей в зависимости от силы тока, разрезаемого материала и его толщины. Имея данные среднестатистического срока службы деталей, оператор будет знать, когда проверять и заменять их, не доводя до возникновения неустранимых отказов.
- Замена расходных деталейСреди использованных деталей, которые Вы выбрасываете, наверняка есть те, которые еще можно использовать. Распространенная привычка слишком часто менять расходные детали приводит к неоправданным затратам. Когда оператор меняет детали, ему (ей) необходимо знать, на что обратить внимание. Если на внутренней или внешней поверхности сопла есть выемки либо отверстие в результате износа утратило округлую форму, то такое сопло подлежит замене. При отсутствии таких признаков можно продолжать использовать сопло. Чтобы узнать степень износа электрода, проверьте изъязвление элемента электрода (элемент представляет собой вставку серебряного цвета в медном держателе; если в качестве плазмообразующих газов используются воздух и O2, то вставка выполнена из гафния; если в качестве плазмообразующих газов используются N2 или Ar-h3 — из вольфрама). Как правило, глубина изъязвления не должна превышать 2,38 мм, если в качестве плазмообразующих газов используются воздух и O2, и 3,18 мм для N2 или Ar-h3). Завихрители газа подлежат замене только в тех случаях, когда при тщательном осмотре в отверстиях выявляются грязь или смазка, трещины, дуговые прожоги или чрезмерный износ. Завихрители газа часто заменяются преждевременно. Сказанное точно так же относится к защитным колпачкам, которые должны заменяться только при наличии признаков физического повреждения. Часто защитные колпачки можно очистить от брызг металла и использовать повторно.
- Использование неправильных параметров и деталей для заданияВыбор расходных деталей зависит от разрезаемого материала и его толщины, силы тока, плазмообразующего газа и других параметров резки. В руководстве оператора указано, какие расходные детали подходят для различных типов резки. Использование неподходящих расходных деталей может привести к сокращению срока службы деталей и снижению качества резки.Особенно важно эксплуатировать детали при номинальной силе тока. Наилучшего качества резки и наиболее продолжительного срока службы деталей можно достичь, если установить силе тока значение, которое составляет 95 % от номинальной характеристики для сопла. Если сила тока слишком низкая, разрез будет неоднородным. Слишком высокая сила тока сокращает срок службы сопла.
- Неправильная сборка резакаРезак должен быть собран так, чтобы его детали были выровнены и плотно прилегали друг к другу. Это позволит обеспечить хороший электрический контакт и правильный поток газа и охлаждающей жидкости через резак. Выполняя замену деталей, храните расходные детали в чистом пакете, чтобы не допустить загрязнения резака грязью или металлической пылью. При сборке резака очень важно соблюдать чистоту. Этим часто пренебрегают. При нанесении смазки на уплотнительное кольцо оно должно лишь слегка блестеть. Если нанести много смазки, завихритель газа может забиться, а резак может загрязниться металлической пылью. Это может привести к неконтролируемому зажиганию дуги в плазменной камере и в конечном итоге к выходу резака из строя. Запрещается наносить смазку на резаки, поскольку это может привести к разрушительному воздействию дуги и возгораниям внутри резака.
- Несоблюдение расписания планового техобслуживанияПри должном уходе резаки могут работать на протяжении месяцев или даже лет. Должна соблюдаться чистота резьбы резака, а опорные поверхности необходимо проверять на загрязнение и механические повреждения. Необходимо очистить резак от любой грязи, металлической пыли или излишней смазки уплотнительного кольца. Для очистки резака воспользуйтесь ватной палочкой со средством для очистки электрических контактов или перекисью водорода.
- Игнорирование проверки потока газа или охлаждающей жидкостиПоток и давление газа и охлаждающей жидкости следует проверять каждый день. Если скорость потока недостаточна, расходные детали не будут охлаждаться должным образом, вследствие чего уменьшится срок их службы. Неправильный поток охлаждающей воды из-за закупоренных фильтров, низкого уровня охлаждающей жидкости — это самая распространенная причина выхода из строя деталей и резака. Постоянное давление газа важно для поддержки режущей дуги. Избыточное давление газа — самая распространенная причина затрудненного зажигания дуги. Под этим подразумевается ситуация, при которой резаку не удается зажечь дугу, когда все остальные условия для нормальной работы соответствуют требуемым. Слишком высокое давление газа также приведет к быстрому разрушению электродов. Точно так же, необходимо поддерживать чистоту плазмообразующего газа, чтобы не допустить сокращения срока службы расходных деталей и резака. В системах со сжатым воздухом газы особенно подвержены загрязнению маслом и частицами, а также попаданию влаги.
- Прожиг на слишком низкой высотеРасстояние между заготовкой и наконечником резака (отклонение) имеет решающе важное значение как для качества резки, так и для срока службы расходных деталей. Даже небольшие изменения высоты резака могут повлиять на угловатость поверхности резки. Особенно важна высота резака при выполнении прожига. Одна из распространённых ошибок — выполнять прожиг слишком низко. Это приводит к тому, что расплавленный металл забрызгивает передний край сопла и защитного колпачка, вызывая повреждения деталей и последующее ухудшение качества резки. «Подавление» дуги может происходить, даже если резак выполняет прожиг в контакте с металлом или скользит по поверхности при резке. «Подавленная» дуги приводит к разрушению электрода, сопла, завихрителя газа, в некоторых случаях и самого резака. Прожиг на высоте, которая превышает рекомендуемую в 1,5–2 раза, защищает резак и детали от повреждений.
- Слишком быстрая или слишком медленная резкаСлишком быстрая или слишком медленная резка может привести к ухудшению качества резки. Если скорость резки слишком низкая, на кромках вырезанных деталей образуется «окалина низкой скорости резки», которая представляет собой большие пузырчатые отложения окалины вдоль нижней кромки. Низкие скорости могут также привести к расширению разреза и вызвать чрезмерное верхнее разбрызгивание. Если скорость резки слишком большая, то дуга будет запаздывать с перемещением по разрезу, что приведет к образованию скошенных кромок, узкого разреза и небольших затвердевших полосок окалины вдоль нижней кромки реза. Окалину, образовавшуюся при высокой скорости резки, тяжело удалить. При правильной скорости резки образование окалины будет минимальным, что позволит получить чистую кромку, которая требует меньше доработки перед передачей детали на следующий этап производственного процесса.
- «Растяжение» дугиРастяжение дуги может происходить в начале и конце реза, если дуга должна «растянуться» (отклониться от прямой перпендикулярной траектории), чтобы войти в контакт с металлом. Растяжение дуги может привести к прожигу боковой стенки сопла. При пуске на краю заготовки плазменную дугу нужно зажигать, когда отверстие сопла находится строго по центру над краем заготовки. Об этом важно помнить при комбинированной обработке металла плазменной резкой и вырубным прессом, когда дуга отклоняется от прямой перпендикулярной траектории, чтобы войти в контакт с металлом. Растяжение дуги может привести к прожигу боковой стенки сопла. При пуске на краю заготовки плазменную дугу нужно зажигать, когда отверстие сопла находится строго по центру над краем заготовки. Об этом важно помнить при комбинированной обработке металла плазменной резкой и вырубным прессом, когда дуга зажигается из пробитого отверстия. В таких случаях дуга должна зажигаться на краю, а не в середине пробитого отверстия. Растяжение дуги также может происходить в конце реза, если резак запрограммирован на выход за пределы листа с включенной дугой или «выход» резака следует за разрезом предыдущего листа металла. Выбор времени сигнала гашения дуги и программирование «выхода» могут минимизировать этот эффект.
- Удар резакаУстановка резака на торец и удары резака могут привести к неустранимой поломке резака. Столкновения резака с заготовкой можно предотвратить, запрограммировав траекторию движения системы фигурной резки вокруг вырезанных деталей (а не над ними). Датчики высоты резака также могут обеспечить защиту от ударов резака путем корректировки высоты на отклонения ширины материала. Однако системы регулировки высоты резака на основе напряжения могут не обеспечить защиту резака. Например, если резак слишком долго двигается по траектории разреза, он часто «ныряет» в конце резки. (Система регулировки резака опускает его, чтобы скорректировать возросшее напряжение из-за растяжения дуги). Тщательное программирование выхода и работы системы регулировки высоты резака могут минимизировать этот эффект. И наконец, устройства крепления блока отключения резака могут предотвратить повреждение резака при столкновении.
blog.svarcom.net
Плазменная резка металла это аккуратность и точность исполнения заказа
Одним из популярных видов обработки металла является его резка. Существует множество способов получить требуемую форму из цельного листа, но в этом материале рассмотрим принцип работы плазменной резки. Плазменная резка. Фактически – золотая середина. Преимущества резки металла плазмой сочетают в себе все перечисленные технологии. Главное достоинство – нет ограничений по типу обрабатываемого материала. Разве что по толщине.
- алюминиевые сплавы 120 мм
- медные сплавы 80 мм
- сталь 50 мм
- чугун 90 мм
Оборудование бывает разное – от промышленного до бытового, так что технология доступна всем. Рассмотрим ее подробнее.
Плазменная резка металла – принцип работы
В качестве резца выступает двухкомпонентная среда:
- Электрическая дуга, работающая по классической схеме – разряд между катодом и анодом. Причем в качестве анода может выступать сам материал, если он является проводником.
- Газовая дуга. Нагреваясь под воздействием электрической дуги (температура достигает 25000º С), газ ионизируется и превращается в проводник электротока.
Принцип работы плазменной резки подробно показан в этом видео.
В результате образуется плазма, которая подается под высоким давлением в зону реза. Эта раскаленная струя газа буквально испаряет металл, причем только в рабочей зоне. Несмотря на то, что температура плазменной резки измеряется десятками тысяч градусов, воздействия на пограничную зону практически нет.
Важно! Правильно выбранная скорость, позволяет получить очень узкий разрез без повреждения края материала.
Источник плазменной резки – плазмотрон.Его задача зажечь дугу, поддерживать рабочую температуру, и выдуть из зоны реза расплавленный металл. Поскольку плазморезы предназначены для обработки любых твердых материалов, включая диэлектрики – образование электрической дуги производится двумя способами:
На рисунке а) изображены резак прямого действия. Катодный узел (8) вместе с закрепленным катодом (6) являются одним из электродов. В качестве второго электрода (анода) выступает обрабатываемая деталь (4) – металл, обладающий хорошей электропроводимостью.
К нему подводится питающий кабель плазмотрона. Наконечник плазменной резки (5) в данной схеме выполняет роль корпуса. От отделен от катода изолятором (7). Газ подается внутрь по штуцеру (1) и формирует струю плазмы, состоящую из электрической (2) и газовой (3) дуги.
На рисунке б) изображен резак косвенного действия. Основные элементы такие же, как и на резаке прямого действия, за одним исключением. Анодом является наконечник (5), на который подается питание. Электрическая дуга (2) возникает между ним, и катодом (6).
Газ, проходя через электрический разряд, раскаляется и превращается в плазму (3). Далее происходит разрез по такой же схеме: материал (в данном случае диэлектрик) испаряется, и выдувается из зоны реза давлением плазмы-газа.
Важно! При таком способе обработки, нагревается не только материал, но и рабочий элемент плазмореза. Поэтому в некоторых моделях предусмотрено воздушное или жидкостное охлаждение катода.
Эта технология продлевает срок службы недешёвого узла.В зависимости от используемой среды, существуют различные виды плазменной резки:
- Азотно-воздушный. Используется атмосферный воздух, состоящий в основном из азота). Или же применяется чистый азот, что несколько расширяет возможности плазмореза.При таком способе есть ограничения – толщина металла не может превышать 10 мм. Можно резать мягкие виды стали. Фактически, техника работы такая же, как у обычного кислородного резака.
Только качество обработки на порядок выше. Заусенцев, наплавов или шлаков не образуется, а ширина реза не превышает 1 мм.
- В защитной среде. Используется инертный газ, способный образовывать плазму. Кромка рабочей зоны изолирована от атмосферы (особенно от кислорода, образующего окислы при высокой температуре).Качество обработки позволяет выполнять особо точные задачи, без влияния на структуру металла.
- Водная среда. Жидкость подается в зону работы, и выполняет не только функцию охлаждения, но и поглощает паразитные испарения.
Установка плазменной резки – компоненты и параметры
Основной элемент – сопло
От его параметров зависит точность и качество обработки материала.В корпусе закреплены: электрод с катодным узлом, механизм подачи газа под давлением, и закрутки воздушного потока. От проработанности конструкции зависит, насколько концентрированной получится плазма на входе в сопло.
Кожух удерживает сопло и позволяет фокусировать поток плазмы, в зависимости от типа и толщины обрабатываемого материала. Сопло плазмореза изготавливается из особо прочных и термостойких материалов, как правило, применяются минералы или драгоценные камни.
Промышленный станок плазменной резки металла видео.
Основной параметр – длина рабочего отверстия (от этого зависит скорость работы). Однако увеличение размера сопла приводит к возрастанию стоимости.
Электрод
Самая уязвимая часть в установке плазменной резки. На него ложится вся температурная нагрузка. Это расходный материал – он подвержен износу. Наиболее долговечный материал (при разумной стоимости) – гафний.
Компрессор
Этот узел напрямую не участвует в процессе, однако без него работа плазмореза невозможна в принципе. Воздух или газ, благодаря которому образуется плазма, подается именно с помощью компрессора. Учитывая огромное давление плазмы, производительность этого узла должна быть соответствующей.Кроме того, в состав компрессора входят тонкие фильтры и осушитель воздуха. Оптимальный вариант – встроенный в плазмотрон компрессор. Тогда все параметры будут согласованы и просчитаны уже при создании комплекта. Вам не придется подбирать давление под параметры резака.
Блок питания
Разумеется, это не отдельный агрегат, подключаемый к резаку. Речь идет об общих параметрах устройства. С точки зрения подключения станка плазменной резки, важно правильно выбрать между однофазным и трехфазным напряжением. Разумеется, для домашнего применения – лучше одна фаза.
Сила тока электрической дуги. От этого параметра зависит скорость реза, и самое главное – толщина материала. Для металлов до 35 мм, вполне достаточно 50-60 ампер. Тем более, что большая мощность потребует соответствующих ТУ от вашей энергетической компании. Если вы владелец металлообрабатывающей мастерской – тогда плазморез будет трехфазным, и мощность обеспечит ток от 100 ампер.
Продолжительность непрерывного плазмообразования. По сути – это время одного сеанса, после которого требуется время на охлаждение головки. Величина измеряется в % отношения работа/отдых. Чтобы не запутаться, следует получить консультацию у продавца, и прочитать этот раздел в инструкции.
Несоблюдение режима работы приведет к очень скорой «кончине» режущего узла. А это 30% стоимости прибора.
Технология плазменной резки металла
Подразумевает не только правильность работы агрегата. Не менее важно соблюдать технику безопасности. Плазмотрон может нанести травму, вызвать пожар, и повредить не только заготовку, но и окружающие предметы. Если вы все выполняете правильно, бояться нечего.
- Так же, как и при проведении сварочных работ, необходимо пользоваться защитным костюмом и маской сварщика. Плазменная дуга является мощным излучателем ультрафиолета, поэтому без защиты глаз можно серьезно повредить зрение. Все открытые части тела должны быть покрыты плотным материалом, иначе можно получить ожог, аналогичный солнечному. Такой «загар» очень вреден и болезненно переносится.
- Важно поддерживать плазмотрон в чистом и исправном состоянии.
Влажные элементы конструкции, или провода, могут привести к утечке рабочего тока. Перед началом работ необходимо проверить надежность электрических контактов, соединения всех элементов между собой. Особенно это касается устройств с подачей воздуха высокого давления.
- Учитывая дороговизну рабочего сопла, его не следует подвергать механическим нагрузкам. Не следует обстукивать его молотком для очистки, ронять или ставить на него тяжелые предметы.
- Выдерживая режим непрерывной работы, старайтесь не выключать дугу для кратковременного перерыва. Например, при переносе резака к новой рабочей точке. Каждый запуск плазмы снижает ресурс устройства.
- Правильно выставляйте рабочий ток. Кроме экономии ресурса, вы сможете получить качественную кромку реза. Избыточная его величина приведет к появлению заусенцев, металл будет деформироваться. Рекомендуется выполнить несколько пробных разрезов, чтобы подобрать величину тока.
Самодельный плазморез с ЧПУ управлением — видео.
Что в активе?Сделав выбор в пользу плазменной резки металла, владелец получает следующие преимущества:
- Нет ограничений по материалу, особенно при использовании плазмореза косвенного действия
- Высокая скорость обработки материала
- Возможность получить деталь любой формы, в том числе высокохудожественные изделия
- За счет прямолинейности плазменной струи, можно выполнять разрез под углом, отличным от 90° по отношению к плоскости
- Возможность обработки листов большой толщины – до десятков сантиметров
- Относительная экологичность при выполнении работ – что особенно важно в домашних условиях, в отсутствии промышленной вентиляции
- Работа начинается сразу после включения плазмотрона – предварительный нагрев заготовки не требуется
- Нет необходимости использовать огнеопасный газ, поэтому работа с плазморезом относительно безопасна.
Итог:Мы рассмотрели принцип плазменной резки металла плазмотроном, разновидности оборудования и способы его использования. Материал поможет вам выбрать подходящий комплект, и освоить технику обработки.
Плазменная резка металла видео.
obinstrumente.ru
Типы резаков для плазменной резки - Мои статьи - Каталог статей
Каждая новая технология, от автомобилей до телевизоров, проходит через эволюционный период. Первые проекты чего-либо часто бывают больших размеров, дорогими и очень медленно становятся меньше, быстрее, более изысканными, и ориентированными на конечного пользователя. Вспомните, например, первый компьютер или мобильный телефон. Они не были похожи на те передовые планшеты и смартфоны, к которым мы уже привыкли сегодня.
Эта тенденция прослеживается и в сегодняшних системах плазменной резки. Кабели питания становятся тоньше, менее громоздкими, более надежными, как и сами резаки. Резаки первого поколения были с угловатыми формами, изготовлены из неуклюжих кусков пластика, выглядели наподобие игрушечных молотков, в отличие от «хай-тек» резаков, которые мы привыкли видеть в настоящее время.
Эти плазменные резаки делали свое дело, но, так как плазменная резка и строжка развивались, стало ясно, модернизация резаков также необходима не только для развития технологий, но и для того, чтобы выдерживать более суровые условия и удовлетворять более широкий круг потребностей. Плазмотрон, которым режут листы на столе с ЧПУ не обязательно будет хорошо работать в применениях для 3D плазменной резки. Так и для ручной резки, резак применяемый для резки плоского стального листа, не будет хорошо применим в случае строжки сварных швов на трубопроводе.
Хотя разработчики всегда понимали необходимость различных конструкций резаков, на самом деле изменение конструкции в реальности была сложной задачей. Плазмотроны были разработаны в соответствии с механизмом, который начинает плазменную дугу. Как правило, этот механизм встроен в большинстве плазменных горелок в виде плунжера. При нажатии на курок, внутренний механизм толкает плунжер в электрод, который, в свою очередь на сопло и стартует дугу. Любое изменение конструкции должно было опираться на этот способ запуска.
Инженеры поняли это и приняли решение удалить этот пусковой механизм из корпуса резака и переместить его непосредственно в сам электрод. Это было не легко, но после большой работы, инженеры выяснили способ, чтобы избавиться от плунжера внутри корпуса горелки и заменить его на плунжер в виде пружины в задней части электрода. Эта технология открыла больше возможностей для изменения дизайна резака, и с тех пор разработчики теперь не ограничиваются определенным размером и формой корпуса.
В результате, многие различные модификации доступны сегодня: короткие, длинные, под углом, прямые и др. Они сделаны как для ручной, так и механизированной резки и строжки, а также роботизированной 3D резки. Давайте посмотрим на некоторые из этих плазморезов и рассмотрим варианты их применения.
Резак 75 градусов или 90 градусов – этот традиционный резак «мастер на все руки» имеет форму, примерно, как латинская буква L (как на фото выше). Несмотря на то, что сам резак, и особенно, расходные материалы для него, очень видоизменились, это, по существу тот же самый резак, который был при появлении систем для плазменной резки четыре десятилетия назад. При помощи него можно легко решать наиболее распространенные задачи на рабочих местах. Резак 15 градусов - как следует из названия, этот резак изготовлен с очень небольшим углом 15 градусов, что делает его практически прямым. Вы можете использовать его применительно к строжке.
Его прямая конструкция обеспечивает большую видимость и лучший контроль дуги, сохраняя руку от высокого нагрева, генерируемого в процессе строжки. Он также является хорошим применением для резки в углах.
Резак механизированный длинный 180 градусов. Этот резак является традиционным для использования на портативных средствах автоматизации, таких как каретки и портальные столы резки с ЧПУ.
Механизированный мини-резак 180 градусов является полезным для ситуаций, в которых стандартный не примерим. Его короткая длина (примерно в 2 раза короче стандартного) идеально подходит для небольших станков с ЧПУ и труборезов.
В отличие от резаков, предназначенных для механизированной резки, роботизированные резаки как правило, весят меньше, имеют меньший профиль (короче и тоньше), и имеют некоторые технологические особенности, такие как канавки, отверстия, и зажимы. Эти особенности позволяют проще и быстрее закрепить его на роботизированной руке и обеспечить безопасность крепления, чтобы случайно не произошло отсоединение во время резки.
Как и сами роботы, резаки производятся в полном ассортименте форм, от совершенно прямого к резаку с L-образной формой.
Усовершенствования расходных материалов для плазменного резака
Инженеры также внесли изменения в расходных материалах. Пружинка на конце электрода была только начало усовершенствований. Ярким примером служат расходные детали, сужающиеся и удлиненные, чем стандартные. Такая конструкция используется для резки или строжки металла в месте, где пространство настолько ограничены, что нет места для традиционного резака, не говоря уже о руке оператора.
Еще одним преимуществом данной конструкции является улучшенная видимость при резке. Намного проще резка, когда видны детали. Удлиненные расходные детали также имеют преимущество при резке деталей с глубокими каналами или щелями.
Независимо от применения, модернизированные плазменные резаки и расходные материалы позволяют решать больше задач с меньшими затратами. Впервые пользователи плазменной резки теперь имеют такой же уровень инноваций и гибкости, как и пользователи кислородной резки, которые уже давно имели преимущество, когда дело доходило до резки разных форм и длины.
www.perfect-cut.ru
советы по выбору и использованию
Аппарат плазменной резки применяется для резки и сварки токопроводящих и других металлических материалов.
Используется для термообработки поверхностей, включая закалку металла, отжиг материалов для снижения твердости, зачистки верхнего слоя стали.
Для сварки цветных и черных металлов, а также для иных работ требующих интенсивного концентрированного нагрева твердых материалов.
Принцип действия аппарата плазменной резки описывают по следующей схеме: в канале сопла с узким сечением образуется электродуга, которая затем охлаждается под воздействием движущегося по каналу потока водяного пара.
В результате ионизирования пара вырабатывается струя плазмы,– температура теплового источника составляет около 60000.
При резке металла плазменным устройством, обширные участки обрабатываемого материала не накаляются, так как это происходит при разрезании металла кислородным резаком.
Назначение пара заключается в интенсивном охлаждении основных рабочих элементов горелки – сопла и катода, а также в поддержании устойчивости столба разряда тока и выдувки дуги.
Схема снабжения сопла паром представляет собой следующее действие: из резервуара плазменного аппарата пар самотеком проходит по каналам охлаждения в разрядную камеру, затем посредством канала сопла выходит в атмосферу.
Для эффективной стабилизации электродуги и ее оттискивания от стенок сопла, применяют тангенциальную или осевую схему подачи газа.
Виды аппаратов для плазменной резки металла
Отличительные технические характеристики аппаратов для плазменной резки и сварки металла, позволяют их разделить на виды.
На сегодняшний день потребительским спросом пользуются инверторные аппараты и трансформаторные источники резки.
При этом цена каждой конкретной модели зависит от мощности и продолжительности работы оборудования.
Видео:
Инверторные устройства характеризуются легким весом, компактными размерами и небольшим потреблением энергии.
Минусом использования данного типа аппаратов плазменной резки и сварки является их сверхчувствительность к сбою напряжения, из-за чего цена на подобные отечественные аппараты сравнительно невысокая.
Особенно эта проблема касается фирменных моделей, которые не приспособлены к эксплуатации в условиях наших электросетей.
При этом если из строя выйдет система защиты аппарата, без сервисного обслуживания уже не обойтись.
Кроме того инверторные устройства имеют ограничение по рабочей мощности, которое не превышает 70 А, и небольшой срок включения при большом токе.
Трансформаторные установки для резки и сварки металла считаются надежнее, чем инверторные типы.
Такие аппараты при падающем напряжении теряют рабочую мощность, но не выходят из строя. За счет чего и цена на данный тип плазморезов намного выше.
Трансформаторные устройства имеют высокий показатель продолжительности включения, при этом ПВ может доходить до 100% (при стандартной норме для ручной резки в 70 процентов).
Аппараты применяются для автоматической резки металла с применением ЧПУ.
При этом время беспрерывной эксплуатации плазмотрона намного превышает время функционирования устройства ручной резки.
Минусом трансформаторных установок являются тяжелый вес, большое энергопотребление и габариты.
Трансформаторные аппараты плазменной резки имеют между собой отличия, которые заключаются в разных технологиях охлаждения плазмотрона.
Видео:
Как правило, стационарные установки работают при водяном охлаждении, переносные аппараты – за счет воздушного охлаждения.
Устройства воздушно-плазменной резки имеют компактные размеры и небольшой вес, благодаря чему их можно беспроблемно транспортировать.
Приемлемая цена позволяет приобрести подобные модели для бытовых условий.
Функционирование аппарата воздушно плазменной резки сводится к использованию сжатого воздуха, он необходим для образования плазмы, и охлаждения.
Максимальная толщина металла, с которой воздушно плазменный аппарат может справиться, равняется 50-55 мм.
Рабочая мощность плазмореза составляет 150-180 Ампер.
Как показывает видео, аппарат плазменной резки со встроенным компрессором можно эксплуатировать на любом участке, так как устройство не зависит от пневматической сети.
Оборудование для плазменной резки металла с водяным охлаждением представляет собой мощную установку, способную разрезать твердый материал толщиной от 80 до 100 мм.
Устройства могут эксплуатироваться в составе с комплектом ЧПУ. Более подробно об особенностях их эксплуатации далее в статье и в видео сюжете.
Цена и технические параметры плазморезов
Помимо видов, плазморезы делятся на установки машинной автоматической резки и аппараты воздушно-плазменной ручной резки.
Рассмотрим возможную стоимость и технические характеристики обеих категорий.
Параметры ручных воздушно плазменных аппаратов
Ручной плазморез нашел свое применение в бытовой сфере, его также используют на маленьких предприятиях и в мастерских для вырезки и обработки различных деталей.
Ручной воздушно-плазменный резак не может обеспечить высокую производительность, так как в ходе рабочего процесса задействован труд оператора, который своими руками держит резак на весу и ведет им по линии реза.
В данном случае шов не может получить идеальную ровность.
Чтобы повысить качество результата работ, ручной воздушно-плазменный аппарат для резки дополняют вспомогательным упорным элементом.
Видео:
Упор своими руками одевают на сопло, затем его прижимают к плоскости рабочей заготовки и ведут ручной резак. При этом больше не надо контролировать определенность расстояния между соплом и изделием.
В результате образуется ровный шов, исключающий появление окалин и наплывов. Указанный рабочий процесс можно посмотреть в следующем видео сюжете.
Цена на ручной плазморез устанавливается в зависимости от возможностей аппарата, включая максимальную силу тока и толщину металлического материала, с которой удается справиться ручной модели.
Также на рынке предлагают универсальные модели, которые можно применять как для резки, так и для сварки металлов. Цена на такой ручной плазменный аппарат с дополнительной функцией сварки доходит до 550 $.
Отличить данную модель при выборе позволяет производственная маркировка.
В пример возьмем аппарат FoxWeld Plasma 43 Multi, устройство совмещает в себе:
- Воздушно-плазменная резка, маркировка – CUT;
- функция аргонодуговой сварки – TIG;
- возможность дуговой сварки посредством штучного электрода – MMA.
Параметры аппаратов машинной резки
Установки машинной резки практически всегда дополняют ЧПУ (программное обеспечение).
Станок с ЧПУ функционирует в соответствии с записанной программой, при этом исключается в рабочем процессе участие человека.
Применение установки с ЧПУ позволяет значительно повысить производительность, при этом качество резки аппарат выполняет с идеальной точностью.
После эксплуатации автоматического устройства с ЧПУ нет необходимости дополнительно обрабатывать кромки заготовок.
Оператору достаточно своими руками ввести в ЧПУ специальную схему и установка строго повторит любую геометрическую форму фигуры. Увидеть, как работает такая установка, можно в предложенном видео.
Видео:
Цена на станки с ЧПУ во много раз превышает стоимость ручного плазмореза с функцией сварки.
Оборудование состоит из мощного трансформатора и специальной поверхности, выполненной в виде стола, укомплектованного порталом и направляющими.
Цена на такое устройство с ЧПУ будет зависеть от габаритов и сложности установки. На данный момент цена на аппараты машинной резки с ЧПУ может составлять от 3000$ до 20000$.
Особенности выбора аппаратов по рабочей мощности, скорости и времени резки
Подбор номинальной рабочей мощности аппарата плазмореза рекомендуется проводить с учетом толщины и вида планируемого к обработке металла.
От типа металла будет зависеть тип рабочего потока (воздух или азот), а также величина диаметра сопла.
Если выбранный вами аппарат имеет мощность 60-90 Ампер, его можно будет применять для резки 30-ти мм металла. Данный тип установки доказывают свою пользу во многих промышленных сферах.
С его использованием можно работать в домашних и авторемонтных мастерских.
Для плазменной резки более толстых металлических изделий, рекомендуется выбирать аппарат с рабочей мощностью от 90 до 170 А.
Его применение позволит разрезать 50-ти мм металл.
Выбирая аппарат плазморез, также необходимо обратить внимание на номинальное первичное напряжение и величину силы тока.
Кроме того, стоит определиться с тем, нужен ли для вашей работы аппарат универсального типа, который можно эксплуатировать при разном напряжении.
Как правило, такие устройства можно подключать к любой электросети. Обычно это аппараты зарубежных производителей с функцией Авто-лайн.
Видео:
Упрощенные устройства могут работать только при 220V или 380V, от одно- или трехфазной сети питания.
Показатель скорости резки измеряется в сантиметрах за 1 минуту.
Существуют установки, которые могут разрезать 30-ти мм лист металла в течение 5 минут, в то время как более мощные устройства справляются с этой задачей за минуту.
Также при выборе аппарата для плазменной резки металла смотрят на продолжительность его непрерывной работы. В пример возьмем установку с ПВ непрерывной эксплуатации 60%.
Проценты говорят о том, что аппарат может работать непрерывно 6 минут, при этом для охлаждения ему понадобится 4 минуты.
Как собрать ручной плазменный резак своими руками?
Плазменную резку металла может проводить своими руками человек, не имеющий опыта сварочных работ. Устройство плазменной резки дает возможность помимо металла обрабатывать дерево, керамику или пластик.
Но не всем приходится по карману даже бюджетная цена плазмореза.
Видео:
Найти выход из ситуации можно, выполнив устройство своими руками, все что потребуется — это приобрести сопло и источник питания.
Аппараты плазменной резки, умело собранные своими руками, могут не уступать показателями мощности производственным устройствам.
Рабочим материалом для плазмы послужит воздух, с целью охлаждения берут воду или тосол, которые необходимо залить в емкость блока.
Образование электродуги можно добиться посредством вольфрамового стержня, его делают из сегментов электрода.
Остальные комплектующие элементы можно отыскать в магазине, после чего руководствуясь схемой, собрать все воедино. Дополнить информацию позволит видео материал.
Видео:
rezhemmetall.ru
Ручная плазменная резка - методы, использование резака - Мои статьи - Каталог статей
Методы резки и строжки, использование плазменного резака
Производители, монтажники, обслуживающий персонал, мастера на все руки, которые когда-либо пользовались оборудованием для ручной воздушно-плазменной резкой, редко хотят вернуться к ацетиленовой или механической резке, такой как пилы, отрезные круги, ножницы и пр. оборудование. Плазменная резка может улучшить производительность и снизить затраты на резку. Она не требует подогрева, режет любой металл, сводит к минимуму зоны термического влияния (ЗТВ), и дает разрез с небольшой шириной реза. Также позволяет производить работы по резке на всем участке проводимых работ благодаря мобильности установок. При помощи установок плазменной резки также можно производить строжку, пробивку и вырезку отверстий, делать скос кромок, резать по шаблону.
Технология резки
Шаг 1: Поместите защитный экран на край металлической пластины, или на определенном расстоянии от поверхности (обычно около 3 мм). Направьте дугу вниз.
Шаг 2: Нажмите на кнопку на резаке. После двух секунд предварительной подачи воздуха, зажигается пилотная дуга.
Шаг 3: После того, как начнется процесс резки, перемещайте резак вдоль по поверхности металлического листа.
Шаг 4: Отрегулируйте скорость так, чтобы режущие искры проходили через металл и выходили из нижней части реза.
Шаг 5: В конце реза, наклоните резак немного к кромке, или задержитесь, чтобы полностью отделить металл.
Шаг 6: Для охлаждения горелки, продувка продолжается от 20 до 30 секунд после отпускания кнопки; нажатие на кнопку во время продувки мгновенно перезапускает дугу.
Смотрите рисунок 1 для иллюстрации этих шагов.
Если искры не видны в нижней части пластины, дуга не пробила металл. Это может быть вызвано тем, что перемещение резака происходит слишком быстро, или недостаточная сила тока, или струя плазмы не направлена прямо в металл.
Перемещение резака на правильной скорости производит чистый срез, минимум окалины в нижней части реза, без коробления металла. Медленная скорость движения может привести к перегреву металла, в результате чего будет окалина. Чтобы свести к минимуму появление окалины, увеличьте скорость или уменьшите силу тока. Для того чтобы понять, как быстро двигать резак, обратитесь к таблице зависимости скорости реза от толщины металла, прилагающейся к вашей установке для плазменной резки. Причиной образования окалины может являться использование установки на ее максимальной мощности.
Для того, чтобы этого избежать, используйте установку с большим запасом мощности.
Строжка и пробивка
Для удаления старых или бракованных сварных швов, используйте специальное сопло. Отверстие на его кончике в три-четыре раза шире, чем на обычно сопле, предназначенном для резки. Его конусообразная форма выталкивает плазменную дугу, чтобы удалить больше металла, чем при использовании стандартного сопла.
Многие люди не верят, что плазма хорошо работает применительно к строжке, но этот стереотип может основываться на старых машинах с более слабой дугой. Некоторые новые машины производят плазменную дугу от 25 до 35 мм длиной. Несмотря на то, что угольная строжка удаляет металл быстрее, плазменно-дуговая строжка производит меньше дыма и шума, дает больше контроля над дугой.
Перед строжкой, подведите резак под углом от 40 - 45 градусов к основному металлу. Нажмите на кнопку, после двух секунд предварительной подачи воздуха стартует пилотная дуга. Установите длину дуги от 25 до 35 мм и перемещая резак по металлу, регулируйте скорость, длину дуги, и угол по мере необходимости. Направляйте искры от резака, и не углубляйтесь слишком глубоко на один проход. Сделайте несколько проходов, если это необходимо.
Для пробивки металла поместите резак под углом 40 градусов к обрабатываемой детали. Нажмите на кнопку. После того, как стартует режущая дуга, доведите кончик резака на угол 90 градусов, и дуга пробьет основной металл. Вообще, принято понимать, что предельная толщина пробивки является половиной максимальной толщины резки установки.
Устранение неисправностей и обслуживание
Если при резке дуга останавливается, или если дуга не прорезает металл в том случае, когда раньше это можно было сделать, осмотрите первым делом расходные детали резака. Электрод и сопло изнашиваются немного с каждым циклом зажиганием и остановкой дуги, и должны быть заменены, когда они чрезмерно изношены. Рисунок выше показывает, как проверить расходные детали резака.
Некоторые из возможных проблем, относятся к давлению воздуха. Низкое давление воздуха приводит к снижению производительности, особенно при резке на высоких амперах. Чтобы проверить это, попробуйте увеличить давление на машине. Для обеспечения достаточного давления воздуха на плазменной машине, вы должны использовать газовый шланг, который соответствует или превосходят по рейтингу рекомендованные в руководстве установки. Многие установки имеют встроенные регуляторы с воздушными фильтрами, но практика показывает, что требуются дополнительные фильтры и сепараторы, чтобы удалить воду или другие загрязняющие вещества. Помните, что вода обладает высокой проводимостью, а если вода поступит в плазмотрон, это может привести к возникновению внутренней дуги, которая может повредить весь резак.
www.perfect-cut.ru
Плазменная резка своими руками | Строительный портал
Плазменная резка представляет собой способ резки металлов с применением вместо резца в качестве режущего инструмента струи плазмы. Между электродом и соплом аппарата или поверхностью разрезаемого металла зажигается электрическая дуга. В сопло аппарата в свою очередь подается под давлением газ, который превращается в плазму под воздействием электрической. Плазма нагревается до 5 - 30 тысяч градусов, а скорость работы составляет пределах 500-1 500 метров в секунду.
Содержание:
- Понятие плазменной резки
- Достоинства плазменной резки
- Принцип работы аппарата плазменной резки
- Выбор аппарата плазменной резки
- Использование аппарата плазменной резки
Понятие плазменной резки
Различают поверхностную и разделительную плазменную резку металла. Широкое распространение на практике нашла именно вторая методика. Сама резка может осуществляться двумя способами: плазменной струей или дугой. При резке металла плазменной дугой включается разрезаемый металл в электрическую цепь. Дуга образуется между изделием и вольфрамовым электродом. При резке плазменной струей в электрическую цепь изделие не включается. Дуга в резаке возникает между двумя электродами.
Обычно плазменную резку проводят в атмосфере. Резка при применении дополнительной среды выступает дальнейшим усовершенствованием - при помощи такой среды ограничивается длина дуги. При толщине металлического листа в пару миллиметров и использовании кислорода как параллельность обработанных поверхностей сопоставима с данным параметром при лазерной резке. Получение параллельных поверхностей возможно при резке листов, которые имеют толщину вплоть до 10 миллиметров.
При плазменной резке низколегированных и мягких сталей предпочтительнее использовать в качестве режущего газа кислород. Расплавленное железо отличается пониженную вязкость, поэтому разжиженный материал из паза легче удаляется. В результате кромки образуются практически без заусенцев. Ещё одним преимуществом применения кислорода является уменьшенное содержание в обработанных кромках азота.
Как режущий газ иногда используется азот. При этом для резки аналогичной толщины листа требуется меньшая сила электротока и тратятся меньшие термические нагрузки на электроды, срок службы которых существенно увеличивается. Если не уменьшать нагрузки, то возможно возрастание содержания азота в кромке, что отрицательно сказывается при выполнении дальнейшей работы. Иногда как более дешевый газ используется воздух, но он уменьшает срок службы сопел и электродов, а также повышает содержание на порезанных кромках азота по сравнению кислородом.
Достоинства плазменной резки
С помощью оборудования для плазменной резки вы можете обрабатывать почти любые металлы – черные и цветные, а также тугоплавкие. Посредством плазменной резки можно обрабатывать металлы в несколько раз быстрее газовой резки. Технология плазменной резки позволяет получать заготовки без каких-то ограничений по геометрической форме. Возможен и процесс сложной фигурной резки.
Подобная технология позволяет разрезать металл точно и быстро, причем процедура эффективна при работе с металлом разной толщины — близко 0,5 - 50 миллиметров. Методика плазменной резки в отличие от кислородной технологии резки позволяет разрезать железосодержащие материалы и материалы, что железа не содержат. Применение плазменной технологии для резки металла, не содержащего железа, является более быстрой, безопасной и эффективной альтернативой механической резке.
Плазменная резка металла по техническим характеристикам и скорости резки является особенно эффективной для прямых резов, к примеру, для резания листов и зачистки кромок, для обработки профилей. Серьёзным преимуществом по сравнению с лазерной резкой является возможность обработки более широких листов металла, резки листов под углом для будущей сварки и получения деталей с небольшими дефектами на поверхности, окалинах и загрязнениях.
При плазменной резке получаются намного меньшие затраты на метр длины металла. Поэтому данная методика в последнее время получила широкое распространение на крупных производствах. При использовании дополнительной среды плазменная резка может применяться на воздухе и даже под водой. Именно вода, попадающая между соплом и плазмой, выступает дополнительной средой при резке алюминия и легированных сталей, обработке низколегированных и мягких сталей.
Принцип работы аппарата плазменной резки
Аппарат для плазменной резки предназначается для высокотемпературного местного нагрева струей плазмы поверхностей материалов, которые имеют малую толщину, в процессе термической обработки. Применение аппарата плазменной резки — резка электропроводного и неэлектропроводного материала, пайка и сварка высокотемпературными припоями, поверхностная термообработка (закалка, местный отжиг, огневая зачистка), сварка черного и цветного металла и другие работы, которые связаны с высокотемпературным местным нагревом.
Реализуется в плазменной горелке технология получения из водяного пара плазмы. Принцип плазменной резки металла в общих чертах можно описать так: в узком канале сопла зажигается электрическая дуга, через этот канал продувается водяной пар, интенсивно охлаждая дугу. Водяной пар при этом ионизируется, и в результате чего создается плазменная струя, которая имеет температуру порядка 6000 градусов.
В процессе резки металла плазма не нагревает обширные участки металла. Материал, который разрезается плазменным резаком, способен охлаждать намного быстрее, чем металл, что разрезан кислородной резкой. Функция пара рабочей жидкости сведена к охлаждению самых нагруженных частей горелки – катода и сопла, стабилизации столба разряда и выдуванию из сопла дуги. Система подачи пара действует по «открытой схеме»: из резервуара самотеком пар попадает по каналам охлаждения в разрядную камеру и выбрасывается через сопло в атмосферу.
Стабилизация дуги относительно оси центра сопла обеспечивается соосношением сопла и катода специальной конструкции и спирального потока пара при помощи тангенциальной подачи в камеру. В резервуаре горелки размещен запас рабочей жидкости. В резервуаре горелки находится капиллярно-пористый влаговпитывающий материал, который служит для транспортировки рабочей жидкости к поверхности нагревателя с помощью капиллярного эффекта. Источник питания на катоде имеет отрицательный потенциал и на сопле положительный.
Выбор аппарата плазменной резки
Если вы решили прикупить такое оборудование, для начала стоит тщательно проанализировать некие параметры, которые будут влиять на качество работы аппарата плазменной резки. Есть опции, которые являются принципиально важными для резака, есть – дополнительные, которые в ваших условиях работы могут попросту не понадобиться.
Виды аппаратов плазменной резки
Аппараты плазменной резки делятся на две разновидности: инверторные и трансформаторные.К достоинствам инверторных аппаратов плазменной резки металла относят такие параметры, как компактность, малое потребление энергии, привлекательный дизайн и небольшой вес. К недостаткам причисляют невысокую продолжительность включения особенно на большом токе и ограничение по максимальной мощности - не больше 70 Ампер. Но главным недостатком выступает то, что инверторные плазморезы являются очень чувствительными к перепадам напряжения.
К достоинствам трансформаторных аппаратов плазменной резки относят высокое продолжение включения и значительную надежность. К тому же при падении напряжения поломки аппарата не происходит, только уменьшается его мощность. Установки с продолжением включения больше 70% можно применять для автоматической резки, где длительность непрерывной работы плазмотрона намного больше, чем при ручной резке. К недостаткам относят размеры и вес, который является значительно большим, чем у плазменных инверторов, а также высшее энергопотребление.
Мощность аппарата
Подбирать номинальную мощность аппарата необходимо зависимо от толщины и вида разрезаемого металла. Толщину металла определяет тип газового потока (азот, воздух) и диаметр сопла. Определите, какой вы будете резать металл, и проверьте мощность вашего оборудования. К примеру, аппарат, который имеет входную мощность 60 или 90 Ампер, способен резать металл, что отличается толщиной до 30 миллиметров.
Аппарат подобного типа предназначен для использования в разных отраслях промышленности, при проведении работ в автомобильных ремонтных и домашних мастерских. Если вы желаете резать толстый металл, то стоит выбрать аппарат с номинальной мощностью 90 или 170 Ампер, как на фото плазменной резки металла на нашем сайте. Используя данный аппарат, вы сможете порезать металл, который имеет толщину до 50 миллиметров.
Обязательно стоит проверить первичное напряжение и силу тока, что необходима для источника питания. Также стоит определить, нужен ли вам универсальный аппарат, что способен работать с разным током и напряжением. Некоторые аппараты могут работать только с напряжением 380 или 220 Вольт, однофазным или трехфазным током питания. В некоторых аппаратах зарубежного производства предусмотрена функция Auto-Line, что позволяет подсоединять оборудование к любой электрической сети.
Скорость и время резки
Перед покупкой аппарата сварочной резки нужно проверить скорость резки данного оборудования. Обычно этот показатель измеряется сантиметрами в минуту. Некоторые аппараты могут перерезать металл, который имеет толщину 30 миллиметров, на протяжении 5 минут, другие – за одну минуту. Скорость резки является очень важной характеристикой, особенно когда нужно уменьшать расходы времени.
При покупке аппарата плазменной резки нужно обратить внимание на продолжительность его работы - время, на протяжении которого аппарат может работать без перегрева. Если длительность работы составляет 60 %, то аппарат может работать без перерыва 6 минут, а в течение 4 минут ему нужно охлаждаться. Очень важна высокая продолжительность для выполнения длинных разрезов или использования аппарата при повышенной температуре.
Продолжительность работы указывается, как правило, для максимальной мощности аппарата. Если вы будете использовать оборудование с меньшей мощностью, то продолжительность его работы соответственно увеличится. Температура среды, где эксплуатируется аппарат плазменной резки, также влияет на этот показатель.
Плазменная горелка
Выбирать плазматрон необходимо в зависимости от особенностей продуктов или материалов, которые вы будете резать. Плазменная горелка всегда должна иметь достаточную мощность для обеспечения качественной резки в тяжелых условиях и быть стойкой к ударам при интенсивной эксплуатации. Вы можете использовать плазматроны различной конструкции.
Плазматроны с медным соплом являются более прочными, чем аппараты с керамическим соплом, практически не бьются, имеют воздушное охлаждение. Рукоятки могут комплектоваться дополнительными элементами, что крепятся к плазматрону и поддерживают наконечники на необходимом расстоянии от рабочей поверхности - 1,6-3 миллиметра. Посмотрите видео о плазменной резке металла - это существенно облегчает работу оператора.
Длина дополнительного элемента, то есть расстояние между плазменной горелкой и рабочей поверхностью, зависит от необходимой силы тока и толщины разрезаемого металла. При использовании малых токов можно прикоснуться соплом к поверхности металла. При использовании большого тока (больше 60 Ампер) расстояние между поверхностью металла и плазматроном должно быть минимум 1,6-4,5 миллиметров.
При выборе плазменной горелки рекомендуется выяснить, для какой цели она будет служить, потому что возможны разные конструкционные решения. Если горелка будет использоваться только в пределах малых токов и разрезать исключительно тонкие листы металла, то защитный газ для охлаждения плазматрона не требуется, и в горелку будет подаваться только воздух, что необходим для резки. Если вы используете плазматрон для резки толстого листового металла, то нужен больший ток, и желательно в плазматрон подавать азот, а не воздух.
Внешние параметры аппарата
Для плазменной резки необходим сжатый воздух и другие комплектующие – электроды для резки и сопло горелки. Поврежденные и изношенные запчасти влияют на качество резки. Низкий уровень квалификации оператора, высокая влажность воздуха, процесс резки толстого листа металла с применением интенсивного режима ускоряют износ таких комплектующих частей. Посмотрите видео о ручной плазменной резке металла - оптимального качества резки можно достичь только при одновременной замене электрода и сопла.
Если вам нужен переносной аппарат, очень важными факторами выступают его размеры и вес. Можно купить небольшой переносный агрегат, который весит меньше 40 килограмм. Также в продаже имеются мощные аппараты, которые весят больше, они служат стационарными постами резки и способны качественно выполнять резку металлов, что отличаются толщиной до 50 миллиметров.
Использование аппарата плазменной резки
Ручную плазменную резку металла при помощи специального оборудования может проводить даже человек без сварочного опыта. Имея аппарат плазменной резки в домашнем обиходе, вы можете осуществлять резку металла и других материалов - пластика, древесины, керамической плитки. Но иногда не по карману купить готовый аппарат, потому что его стоимость, а поэтому и цена плазменной резки слишком высока. В этом случае можно изготовить плазменный резак самостоятельно, купив блок питания и сопло.
Плазменные резаки, созданные своими руками, не уступают по мощности заводским. В качестве рабочего материала для плазмы используют в самодельных аппаратах воздух. Для охлаждения применена жидкая система: полость анодного блока принято заполнять тосолом или обычной водой. Дугу в сопле можно получить при помощи вольфрамового стержня, для изготовления которого берут кусочек электрода. Остальные части продаются в магазинах в качестве комплектующих. Остается только собрать их воедино.
Работая с аппаратами плазменной резки, нужно строго придерживаться правил безопасности, потому что при этой работе имеет место большое число факторов, которые представляют опасность для человека: температура, высокое напряжение, расплавленный металл и ультрафиолетовое излучение. Рекомендуется носить одежду сварщика и под рукой иметь сварочный щиток с затемненными стеклами.
Перед началом процесса плазменной резки металла своими руками необходимо осмотреть защитный щиток, электрод и сопло! Нельзя начинать работу, если электрод или сопло недостаточно закреплены. Не желательно стучать плазматроном для удаления брызг металла, потому что можно его повредить. Для экономии материалов нужно избегать обрыва и частого зажигания плазменной дуги.
При подготовке к работе аппарата плазменной резки в него подается сжатый воздух. Можно выбрать один из трех источников сжатого воздуха: подключение к системе сжатого воздуха, которая имеется на заводе, баллоны сжатого воздуха или воздушный компрессор. Львиная доля аппаратов имеют регулятор, который необходим для подачи и распределения воздуха в системе.
При расчете определенного тока и скорости резки рекомендуется выполнить несколько пробных разрезов при высоком токе. При необходимости, зависимо от скорости резки, вы можете уменьшать ток. Если он является слишком высоким или скорость резки выступает маленькой, разрезаемый металл будет перегреваться и может возникать окалина. Правильно определив ток и скорость резки, вы сможете получить чистый разрез, на котором практически не возникает окалины, а разрезаемый металл не деформируется.
Плазменную резку листового металла принято начинать, размещая горелку близко к краю разрезаемого металла. Дальше нужно нажать кнопку выключателя горелки, после этого зажжется дежурная дуга, а потом режущая дуга. После того, как режущая дуга зажглась, нужно медленно двигать горелку вдоль желаемой линии разреза. Регулировать скорость движения необходимо так, чтобы искры виднелись с обратной стороны листового металла. Дугу направляется под прямым углом к металлу и вниз.
Если на обратной стороне металла не заметно искр, то металл насквозь не прорезался. Это может совершаться из-за чрезмерно большой скорости движения, малого тока или направления струи плазмы к поверхности металла не под углом 90 градусов. По окончании резки горелку следует слегка наклонить в сторону конца разреза или остановится на время, чтобы закончить процесс резки. После того, как была отпущена кнопка выключателя на горелке, воздух для охлаждения горелки некоторое время подаваться ещё будет.
Проплавить отверстие в металле получится, если угол наклона горелки достигнет 40 градусов. Необходимо нажать кнопку выключателя горелки аппарата плазменной резки. Когда загорелась режущая дуга, следует наклонить горелку таким способом, чтобы угол ее наклона достигал 90 градусов. Только тогда дуга сможет насквозь проплавить основной металл. Рекомендуется руководствоваться следующим правилом: данным способом вы сможете проплавить металл толщиной не больше самой высокой толщины разрезаемого металла, что указана в паспорте аппарата плазменной резки.
Таким образом, если нужно раскроить металл или сделать отверстие в цельном металлическом изделии, лучшим вариантом для проведения подобных работ является по технологии и стоимости плазменная резка металла. Для осуществления данной процедуры необходим специальный резак, отличительная особенность которого кроется в том, что резка происходит не благодаря электрической дуге, а за счет образования потока раскаленной плазмы.
strport.ru