Работы, выполняемые на токарных станках. Работы выполняемые на токарных станках
Выполнение работ на токарном станке
Понятие «металлообработка» подразумевает обработку металла с помощью различных станков, приспособлений или вручную. Токарные работы являются одним из самых распространенных способов обработки металла при помощи станков.
Суть самого процесса токарных работ заключается в удалении специальными резцами лишнего металла с металлических заготовок цилиндрической формы при вращении этой заготовки. Обработка заготовки производится до тех пор, пока ее диаметр не будет необходимого размера, то есть, когда заготовка станет готовой деталью.
Помимо своей основной функции, обработки резцами цилиндрических деталей, с помощью токарных станков производится сверловка отверстий в деталях - рабочим инструментом в этом случае является сверло, которое крепится в токарный патрон; с помощью токарных станков можно нарезать внутреннюю и наружную резьбу на деталях - рабочими инструментами в этом случае являются метчики и плашки, причем, для нарезания внутренней резьбы используют метчики, а для внешней - плашки; можно производить зенкование отверстий, то есть, делать их различными по диаметру по толщине заготовки – рабочим инструментом здесь являются специальные резцы. На токарных станках можно изготавливать разнообразные цилиндрические детали: втулки, валы, шайбы, гайки, шкивы. Под «рабочими инструментами» или «станочной оснасткой», подразумевают все те приспособления, при помощи которых заготовки обрабатываются, благодаря которым получаются готовые детали. К этому оборудованию относят металлорежущие резцы, плашки, метчики,зенкеры, сверла. Процесс токарной обработки металлических деталей состоит из нескольких технологических операций. Заготовка, с помощью специальных «губок», закрепляется в шпиндель, вращающуюся часть токарного станка. Шпиндель может совершать только вращательное движение. В подвижной части станка, суппорте, крепится резец, который движется в двух плоскостях. Заготовка, закрепленная в шпинделе, совершает вместе с ним вращательное движение. К ней плавно подводится резец, который, за счет усилия, подаваемого на него, производит поступательное движение вперед и врезается на определенную глубину в «тело» заготовки. Эта глубина может регулироваться перемещением резца. Делая большую подачу резца и увеличивая число оборотов шпинделя, можно снимать большее количество металла, и наоборот. На любой материал (обрабатывать на токарном станке можно не только металл, но и дерево, и пластик), на каждую определенную степень обработки поверхности, можно установить свои определенные усилия подачи резца и скорости вращения.
Техника безопасности на станках
Самым опасным производственным фактором при работе на токарных станках является:
Вращающийся шпиндель, валы, червяки, стружка и если сказать одним словом, то опасность представляют все вращающиеся механизмы станка.
Перед началом работы на токарных станках необходимо знать:
Начните со своей рабочей одежды, приведите ее в порядок, застегните все пуговицы или клепки, плотно подвяжите или закатайте рукава, если имеются длинные волосы уберите их в головной убор.
Подготовьте свое рабочее место:
Проверьте исправность всех защитных щитков, исправность защитных концевиков (при наличии). Защитные очки (должны быть чистыми, без царапин и трещин), за ранее приготовьте режущий, мерительный инструмент, приспособления необходимые для изготовления данной детали, тару для заготовок и годной продукции, посмотрите все ли в порядке с подножной решеткой, пол вокруг станка должен быть чистым и без масляных пятен.
Перед началом работы проверьте:
Тормозные механизмы, устройства управления, смазочную подачу на механизмы и направляющие, натяжение ремней и цепей. Для такой проверке достаточно погонять станок в течении нескольких минут на холостом ходу, и вам сразу станет ясно исправен ли станок или нет по механической части. Приступайте к работе в том случае, если станок полностью исправен.
Во время подготовки станка к работе:
Установку резцов, приспособлений, оснасток и другое, станок должен находиться в выключенном положении. После установки резцов, оснастки прокрутите шпиндель вручную и убедитесь, что резцы не ударяются об патрон, шпиндель и оснастку.
Особенности правил безопасности при работе, наладки на станках с ЧПУ:
Наладчик проверяет станок с ЧПУ перед началом работы тест программами. После наладки снимите все рукоятки и ключи.
Во время работы станка:
Прочно закрепляйте обхватываемые заготовки и детали в патроне, оправках или центрах. При установке снятии заготовок более 20кг пользуйтесь краном или подъемными устройствами. Ни в коем случае не оставляйте ключ в патроне после закрепления или снятия детали. Не трогайте и не притормаживайте руками включенный или не до конца остановленный шпиндель. При уборке стружки необходимо использовать верхонки, металлические крючки. Не делайте уборку, протирку, смазку станка при обработке детали. При измерениях детали выключайте вращение шпинделя и осторожно делайте замеры. Будьте осторожны при замерах, на деталях могут присутствовать острые кромки (можно порезать руки). Закрывайте зону резания предназначенными защитными кожухами, экранами. При скоростном точении следует применять резцы со стружколомающими канавками или резцы стружколомы. При зачистке заусенцев или полировке применяйте зажимы, в руках держать абразивную шкурку запрещено. Не жесткие валы необходимо обрабатывать в люнетах, а выступающие края прутка следует ограждать трубчатыми кожухами. Работать необходимо строго по тех процессу и выставлять те режимы резания которые указаны в технологии. Перед выключением вращения шпинделя отключите автоматическую подачу станка и отведите режущий инструмент от детали. Запрещается работать в перчатках, забинтованных пальцах (можно воспользоваться резиновыми напальчниками). Вытирайте руки чистой ветошью, не используйте ветошь для вытирания рук после протирки станка (можно порезаться мелкой стружкой). При вращении шпинделя более 150об/мин не пользуйтесь жесткими центрами, при обработке крупногабаритных деталей пользуйтесь самосмазывающимися центрами. В момент перерывов отключайте вращение шпинделя. При сбое электроснабжения или утечки масла в срочном порядке отключите оборудование. Запрещается открывать дверки электрошкафов, защитные кожуха электрооборудования. В случаях любых неисправностях сообщайте мастеру или дежурному по смене. До устранения неполадки к работе приступать запрещено. Держите свое рабочее место в чистоте, не заставляйте его деталями и заготовками. Следите за СОЖ чтобы она не попадала на пол и подножную решетку.
Основные виды токарных работ. Основные понятия обработки резанием
Токарный станок - станок для обработки преимущественно тел вращения путем снятия с них стружки при точении. Токарный станок один из древнейших станков в мире, на основе которого создавались другие станки (сверлильный, расточной и др.) Токарь - одна из ведущих профессий в машиностроении и металлообработке, так как многие детали машин и механизмов изготовляются на токарных станках, являющихся наиболее распространенными в производстве среди станков других групп. Токарная обработка является наиболее распространенным методом обработки резанием применяется при изготовлении деталей типа тел вращения (валов, дисков, осей, пальцев, цапф, фланцев, колец, втулок, гаек, муфт и др.). Основные виды токарных работ показаны на рисунке.
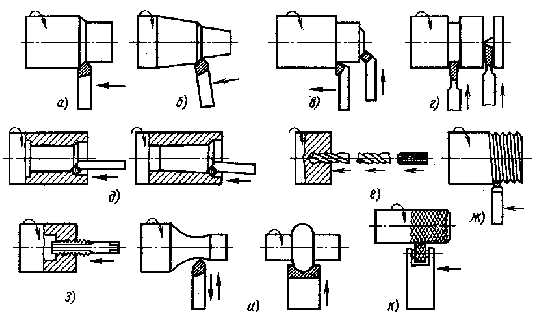
Основные виды токарных работ:
a) - обработка наружных цилиндрических поверхностей, б) - обработка наружных конических поверхностей, в) - обработка торцов и уступов, г) - вытачивание пазов и канавок, отрезка заготовки, д) - обработка внутренних цилиндрических и конических поверхностей, е) - сверление, зенкерование и развертывание отверстий, ж) - нарезание наружной резьбы, з) - нарезание внутренней резьбы, и) - обработка фасонных поверхностей, к) - накатывание рифлений. Cтрелками показаны направления перемещения инструмента и вращения заготовки
В машиностроении большинство деталей получают окончательные формы и размеры в результате механической обработки заготовки резанием, которое осуществляется путем последовательного удаления режущим инструментом (например, резцом) тонких слоев материала (в виде стружки) с поверхностей заготовки. Основным элементом режущего инструмента, отделяющего стружку от заготовки, является заостренный клин. Схема работы клина (a) и резца (b) приведена на рисунке: 1 - стружка, 2 - резец, 3 - заготовка, 4 - снимаемый слой материала; Р - сила, действующая на резец и клин при работе, β - угол заострения Процесс резания на токарных станках осуществляется при вращательном главном движении, сообщаемом обрабатываемой заготовке, и при прямолинейном (поступательном) движении подачи, сообщаемом резцу. Элементами режима резания при точении заготовки являются скорость резания, подача и глубина резания. Скоростью резания называется длина пути, пройденного режущей кромкой инструмента относительно обрабатываемой поверхности заготовки в единицу времени. Скорость резания измеряется в м/мин и обозначается буквой υ.
Подачей называется величина перемещения режущей кромки инструмента за один оборот заготовки (в направлении подачи) или в единицу времени. Подача измеряется в мм/об или в мм/мин, обозначается буквой s и может быть продольной (если инструмент перемещается параллельно оси вращения заготовки) и поперечной (если инструмент перемещается перпендикулярно этой оси). Глубиной резания называется величина срезаемого за один проход резца слоя металла, измеренная по перпендикуляру к обработанной поверхности детали. Глубина резания измеряется в миллиметрах и обозначается буквой t. У заготовки различают следующие поверхности: обрабатываемую (с которой снимают стружку), обработанную (полученную после снятия стружки) и резания (которая является переходной между обрабатываемой и обработанной поверхностями и образуется режущим инструментом). Основные поверхности заготовки и основные движения, осуществляющие процесс резания, показаны на риснке: 1 - обрабатываемая поверхность, 2 - поверхность резания, 3 - обработанная поверхность, 4 - ось вращения заготовки, 5 - продольная подача, 6 - поперечная подача, 7 - резец, 8 - заготовка, 9 - главное (вращательное) движение, t - глубина резания
turner.narod.ru
Основные виды токарных работ » Привет Студент!
Различают следующие основные виды токарных работ: 1) обточка цилиндрических поверхностей; 2) подрезка торцов и уступов; 3) сверление, зенкерование, развертывание, нарезание метчиком резьб и центровка обтачиваемых деталей; 4) расточка цилиндрических поверхностей; 5) нарезание резьбы; 6) коническая обточка и расточка; 7) обточка фасонных поверхностей.
Обточка цилиндрических поверхностей. В зависимости от длины обрабатываемой детали ее обточку можно производить двояко: в центрах в случае длинных деталей или в патроне при небольшой длине детали. На фиг. 456 показана обточка в центрах. В тех случаях, когда длина детали составляет 12 диаметров ее и более, во избежание прогиба детали применяют приспособление, называемое люнетом. На фиг. 457 показано устройство неподвижного люнета, закрепляемого на станине.
На фиг. 458 показан подвижный люнет, закрепляемый на супорте и перемещающийся вместе с ним. Здесь колодки 1 подводятся к детали 2 установочными винтами 3, положение которых фиксируется зажимными винтами 4, В подвижных люнетах только две колодки, уравновешивающие давление на деталь со стороны резца 5.
При обработке коротких деталей применяют патроны с четырьмя, тремя и двумя закрепляющими деталь кулачками. На фиг. 459, а показан простой четырехкулачковый патрон, в котором кулачки 1, 2, 3 и 4 расположены крест-накрест. На фиг. 459, б показан трехкулачковый самоцентрирующийся патрон внутреннее устройство которого показано на фиг. 459, в. На фиг. 459, г показан двухкулачковый патрон.
Двух- и четырехкулачковые патроны применяют при обработке деталей различных конфигураций, а трехкулачковый самоцентрирующийся — только при обработке цилиндрических деталей.
Кроме описанных патронов с ручным зажимом деталей, применяют также патроны с гидравлическим или пневматическим приспособлением для зажима деталей.
Подрезка торцов и уступов. При выполнении этих работ деталь можно закреплять в центрах и патроне одновременно. Выбор способа закрепления определяется габаритами детали.
Сверление, зенкерование, развертывание, нарезание метчиком резьбы и центровка. Для получения на токарных станках отверстий и их обработки применяют сверла, зенкеры, развертки и метчики, закрепляемые в задней бабке с помощью различных приспособлений. На фиг. 460 показаны различные виды обработки отверстий на токарных станках. Как видно из фигуры, крепление детали при таких работах производят в патронах; передвижение инструмента осуществляется вручную передвижением шпинделя задней бабки.
Для крепления деталей на центрах в торцах деталей до установки их на станок делают углубления. Операция образования центровых углублений называется центровкой.
Расточка цилиндрических поверхностей. Расточка внутренних поверхностей деталей подразделяется на расточку сквозных и глухих отверстий (фиг. 461, а и б). Закрепление деталей при этих работах производится в патроне.
Нарезание резьбы. На токарных станках нарезание внутренней резьбы можно производить при помощи метчика (фиг. 460, г) или резцами (фиг. 462). При нарезании резцами продольную подачу осуществляет резец 1, а деталь 2, закрепленная в патроне, вращается. Профиль резьбового резца должен соответствовать профилю нарезаемой резьбы—это значит, что угол при вершине резца для метрической резьбы должен быть равен 60°, а для дюймовой 55°. Для сохранения профиля резца после переточек передний угол его делают равным 0°. На фиг. 463 дана схема нарезания наружной резьбы резцом.
При нарезании наружной резьбы резцу сообщается движение подачи, а движение резания — детали. Подача резца при нарезании резьбы равна шагу нарезаемой резьбы. Если процесс ведут на станке, имеющем коробку подач, и если шаг нарезаемой резьбы будет равен подаче, осуществляемой коробкой подач, то в этом случае настройка станка будет сводиться к установке рукояток, показанных в таблице подач, обычно помещаемой на кожухе. Если же нарезку ведут на станке, не имеющем коробки подач, или на станке с коробкой подач, табличные данные подачи которой не совпадают с требуемым шагом резьбы, то в этих случаях применяют сменные зубчатые колеса. Нарезание резьбы является одним из сложных видов токарных работ, требующим специальных знаний в части подсчетов сменных зубчатых колес.
Скачать реферат: У вас нет доступа к скачиванию файлов с нашего сервера. КАК ТУТ СКАЧИВАТЬ
Пароль на архив: privetstudent.com
privetstudent.com
Работы, выполняемые на токарном станке — Мегаобучалка
Обточка цилиндрических поверхностей
Наружные цилиндрические поверхности обтачивают проходными резцами. При черновой обработке вершина резца может располагаться выше оси центров на 0,01 - 0,03 диаметра заготовки. При этом значение главного угла γ изменяется в сторону отрицательных величин, чем улучшается стойкость резца при работе с ударами и по корке. Резец устанавливают с помощью набора стальных подкладок, число которых для увеличения жесткости его крепления должно быть минимальным, а вылет резца из резцедержателя не должен превышать 1,5 высоты стержня инструмента.
Для получения необходимого диаметра детали резец устанавливают на глубину резания, для чего подводят его до касания с поверхностью вращающейся заготовки, а затем устанавливают поворотное кольцо лимба винта поперечной подачи суппорта в нулевое положение, отводят суппорт вправо и перемещают резец в поперечном направлении на глубину резания. Для обеспечения заданной глубины резания число делений лимба, на которое необходимо повернуть рукоятку винта поперечной подачи:
где t - глубина резания, мм;
с - цена деления лимба, мм (при 100 делениях лимба и шаге винта 5 мм с = 5/100 = 0,05 мм).
После установки глубины резания заготовку обтачивают на длине 2 – 3 мм, останавливают станок и измеряют диаметр обточенной поверхности штангенциркулем или микрометром; затем для обеспечения заданного размера вносят поправку и обтачивают заготовку по всей поверхности.
Обточка конусов
Конические поверхности обрабатывают:
- поворотом поворотной плиты суппорта вместе с резцовыми салазками;
- смещением центра задней бабки;
- с помощью копировальной линейки;
- широким резцом.
Поворотом поворотной плиты суппорта вместе с резцовыми салазками (рис. 7, а) обрабатывают наружные и внутренние поверхности с любым углом уклона, но сравнительно небольшой длины, ограничиваемой длиной хода резцовых салазок суппорта.
Коническую поверхность обтачивают только при ручной подаче салазок, угол поворота которых определяют по формуле
а - поворотом средней части суппорта; б - смещением центра задней бабки
Рисунок 7 – Методы обточки конусов
Недостатками этого метода обработки конусов являются низкая производительность, невысокая точность и большая шероховатости обрабатываемой поверхности, а также ограниченная длина конуса.
Обработка конусов смещением центра задней бабки позволяет получить наружные конусы сравнительно большой длины при малой конусности. Величина смещения (рис. 7, б) задней бабки в обе стороны от ее среднего положения в зависимости от направления уклона обрабатываемого конуса
При α<8° с достаточной степенью точности можно принять cos α = 1, тогда
При точении конуса на токарном станке 1А616 корпус задней бабки может смещаться с линии центров в поперечном направлении в пределах 10 мм.
Корпус задней бабки (рис. 1, узел 40) смещают в нужную сторону;величину смещения измеряют линейкой на контрольной площадке. Обточку конусов этим способом выполняют с механической продольной подачей, однако точность обработки в этом случае невысокая, так как установка заготовки с перекосом приводит к быстрому износу центровых отверстий и к возможному браку при последующей обработке на других станках. Для предотвращения износа центровых отверстий центра станка нужно заменить на специальные, имеющие на своем конце шарики.
Наружные и внутренние конусы с углом уклона до 10 - 12° обрабатывают с помощью копировальной линейкой. Для этого отсоединяют поперечные салазки суппорта от гайки винта поперечной подачи. Движение на суппорт передается от тяги, жестко связанной с ползуном, который в свою очередь свободно перемещается по линейке.
Наружные и внутренние конусные поверхности длиной не более 20 мм обрабатывают широким резцом. При этом длина главной режущей кромки резца должна быть больше длины конуса, а главный угол в плане равен углу уклона конуса.
Сверление отверстий
Перед сверлением отверстия на токарном станке заготовку устанавливают в патроне и прочно закрепляют; затем подрезают торец и производят зацентровку с помощью центровочного сверла, а при его отсутствии - коротким сверлом с углом при вершине 90°, что исключает участие перемычки в работе в момент врезания сверла и способствует более правильному его направлению по оси отверстия.
Включив вращение шпинделя, перемещают заднюю бабку так, чтобы сверло находилось от торца заготовки на расстоянии 5 – 10 мм. После этого вручную, поворотом маховичка задней бабки, плавно подводят сверло к торцу вращающейся заготовки. Быстро подводить сверло нельзя, так как возможен удар и поломка сверла. Подачу сверла после врезания выполнять плавно, без рывков. Если глубина сверления больше трех диаметров сверла, необходимо периодически выводить сверло из отверстия для его охлаждения и удаления стружки. Особую осторожность следует соблюдать при сверлении сквозных отверстий в момент выхода сверла из отверстия, так как может возникнуть неравномерная нагрузка на режущие кромки сверла и их выкрашивание.
В конце обработки сверло необходимо вывести из отверстия и только после этого остановить станок, в противном случае возможно заедание и поломка сверла.
megaobuchalka.ru
5. Виды работ, выполняемых на токарно-винторезных станках. Применяемый нструмент и приспособления
На рис. 3. представлены основные виды обработки, выполняемые на токарно-винторезных станках, для которых используются соответствующие типы токарных резцов.
Наружная цилиндрическая обточка:
рис. 3,1 – проходным прямым резцом;
рис. 3,2 а – проходным отогнутым резцом;
рис. 3,3 – проходным упорным резцом.
Обработка фаски:
рис. 3,2 б – проходным отогнутым резцом.
Подрезка торца (обработка плоской поверхности):
рис. 3,4 – подрезным резцом.
Прорезание внутренних канавок:
рис. 3,5 – канавочным угловым резцом для обработки канавок под сальник (уплотнение).
Расточка внутренних цилиндрических поверхностей:
рис. 3,6 – расточным проходным резцом для обработки сквозных отверстий;
рис. 3,7 – расточным упорным резцом для обработки глухих отверстий.
Обработка фасонных поверхностей:
рис. 3,8 а – фасонным канавочным резцом;
рис. 3,8 б – фасонным резцом для обработки галтели радиуса;
рис. 3,10 – фасонным резцом для обработки выпуклых поверхностей.
Обработка конической поверхности:
рис. 3,9 – прямым проходным резцом путем поворота верхних салазок суппорта.
Отрезка заготовок:
рис. 3,11 – отрезным резцом.
Нарезание резьбы:
рис. 3,12 а – резьбовым резцом для наружной резьбы;
рис. 3,12 б – резьбовым резцом для внутренней резьбы.
Рис. 3. Классификация токарных резцов и поверхностей,
обрабатываемых на токарно-винторезных станках
Приспособления токарно-винторезных станков разделяются на универсальные и специальные. К ним относятся:
На технологических эскизах установка заготовок изображается с помощью условных обозначений согласно ЕСТД ГОСТ 31107-73, которые приведены на рис. 4.
Заготовки небольшой длины (L/D4) закрепляют в токарных патронах: самоцентрирующих и несамоцентрирующих.
Трехкулачковый самоцентрирующий патрон имеет три кулачка, которые одновременно сходятся к центру или расходятся и обеспечивают точное центрирование заготовки, т.е. ее базирование по наружной или внутренней цилиндрической поверхности. На пазах корпуса патрона и на кулачках нанесены цифры (1, 2, 3). При сборке патрона кулачки вставляют в пазы поочередно в порядке возрастания цифр.
На рис. 4,1–4,3 показаны способы закрепления короткой детали в 3- кулачковом патроне.
Четырехкулачковый несамоцентрирующий патрон предназначен для закрепления заготовок с параллельными гранями, имеет четыре зажимных кулачка, которые перемещаются независимо друг от друга в пазах корпуса (рис. 4,4).
Заготовку закрепляют в патроне поворотом ключа, который вводится в гнездо винта каждого кулачка в отдельности.
Заготовки валов с L/D>4 обрабатываются с установкой коническими поверхностями центровых отверстий на центрах станка. Центровые отверстия стандартизованы по ГОСТ 14034-68.
В качестве зажимных приспособлений используют передний и задний опорные центра. Передний опорный центр является жестким (вращается вместе со шпинделем), задний, как правило, подвижный. Для передачи вращения от шпинделя к заготовке, установленной в центрах, применяют поводковые устройства – поводковый патрон (планшайба) и хомутик (рис. 4,5).
Валики небольшого диаметра (до 20 мм) закрепляют в обратных центрах (рис. 4,6). Заготовка увлекается во вращение за счет трения в переднем центре. Возможен также вариант закрепления заготовки из проката в 3-кулачковом патроне с поддержкой центром (рис. 4,7).
При обработке нежестких валов, L/D>10, используют дополнительные приспособления – люнеты, позволяющие исключить отжим заготовки, приводящий к искажению формы детали (бочкообразность).
Люнеты бывают неподвижные, закрепляемые на направляющих станины (рис. 4,8) и подвижные, закрепляемые на каретке суппорта и движущиеся вместе с ним (рис. 4,9).
Приспособление Условное обозначение
на технологических эскизах
Рис. 4. Закрепление заготовок при токарной обработке
studfiles.net
Работы, выполняемые на токарных станках
Современные станки, на которых выполняются токарные работы, сложно заменить, если требуется изготовить сложную деталь с высокой точностью.
Такая обработка выполняется с использованием нескольких видов резцов и сверл, а также других инструментов, помогающих справиться с поставленной задачей лучше и быстрее.
Технические возможности станка для токарных работ
Прежде чем заказать токарные работы, нужно убедиться, что деталь, которая необходима может быть выполнена таким способом и это оправдано с технической и экономической точки зрения. Для этого нужно понять принцип действия такого станка. Процесс начинается с того, что заготовку фиксируют в патроне вала, который обеспечит ее вращение вокруг оси с заданной скоростью. Режущий инструмент поступательно подается в рабочую зону и начинается процесс обработки, который на современных станках для токарных работ идет по заданному алгоритму, а оператор в основном контролирует процесс. Из вышесказанного становится понятно, что механическая металлообработка на таком станке имеет ограничение, связаное со способностью инструмента резать только те заготовки, которые могут вращаться вокруг оси.
Особенности обтачивания гладких поверхностей цилиндрической формы
Это один из самых распространенных видов токарных работ, которые выполняются проходными резцами. Обтачивание происходит в несколько этапов:
- Черновое. Производится обдирка — быстрое удаление основной массы лишнего материала. Черновые проходные резцы отличаются жесткостью и устанавливаются выше центров на расстоянии, которое зависит от размера заготовки и находится в диапазоне 0,3–1,2 мм.
- Чистовое обтачивание. Для выполнения таких токарных работ используют резцы с широкой режущей кромкой, что позволяет вести обработку на больших подачах. Смысл их выполнения заключается в придании изделию нужного размера и формы с гладкой поверхностью. Если режимы резанья правильно выбраны, то такая обработка позволяет достигнуть 3-4 класса точности.
- Тонкое обтачивание. Необходимость выполнения таких токарных работ возникает в том случае, если деталь должна иметь 7-9 класс шероховатости.
Чаще всего обтачивание гладких поверхностей проходит в два этапа, но при изготовлении сверхточных изделий с минимальными допусками без дополнительной обработки не обойтись.
Другие виды токарных работ
Их довольно много, но мы перечислим самые востребованные:
- Резка канавок. Выполняется после предварительной обточки. Используются резцы, у которых режущая кромка имеет такой же размер и профиль, как и канавка.
- Обработка конических поверхностей. Этот вид токарных работ выполняется несколькими способами и зависит от угла конусности.
- Нарезание резьбы. Используются резьбовые резцы и другие специальные инструменты.
Такая услуга, как металлообработка в Нижнем Новгороде предлагается многими компаниями, но доверять ее, особенно если нужна большая партия, нужно профессионалам с хорошей репутацией, которая подтверждена конкретными делами.
otvali.ru
Основные виды токарных работ
На токарных станках можно выполнять точение в центрах, в патроне и на планшайбе; растачивание; торцовое точение, отрезку и подрезку, нарезание резьбы; точение конусов, фасонных поверхностей и другие виды работ с применением соответствующих инструментов и приспособлений.
Точение в центрах. Для обтачивания наружных цилиндрических поверхностей прутковые детали (валы, оси) с отношением L/D > 4 обычно подвергают продольному точению в центрах с использованием проходных резцов. Планшайбу навинчивают на шпиндель. Деталь с просверленными осевыми отверстиями на торцах и надетым хомутиком 5 (рис. 10) зажимают между центрами передней и задней бабок. Хомутик закрепляют на конце детали при помощи винта 2 так, чтобы его палец 4 входил в прорезь поводковой планшайбы 3.
Вместо планшайбы часто применяют поводковый патрон с безопасным хомутиком. Центр и хомутик па передней бабке станка защищены корпусом поводкового патрона; в последнем помещен поводковый палец, вращающий хомутик с деталью.
|
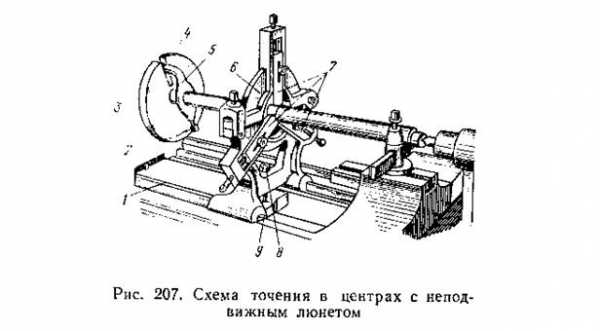
Для предохранения длинных деталей от прогиба (при L/D > 10— 12) применяют направляющие приспособления — неподвижные и подвижные люнеты. Неподвижный люнет 6 (рис. 10) ставят на направляющие станины 1 и при помощи планки 9 и болта с гайкой 8 закрепляют между передней и задней бабками станка. Обрабатываемая деталь охватывается тремя регулируемыми упорами 7 (кулачками). При точении с большими скоростями вместо обычных упоров в люнетах устанавливают роликовые или шариковые подшипники, наружные кольца которых служат роликами, касающимися поверхности вращающейся детали.
Подвижный люнет крепят на каретке суппорта. Люнет имеет два упора, касающихся обработанной поверхности детали и принимающих на себя давление от резца.
|
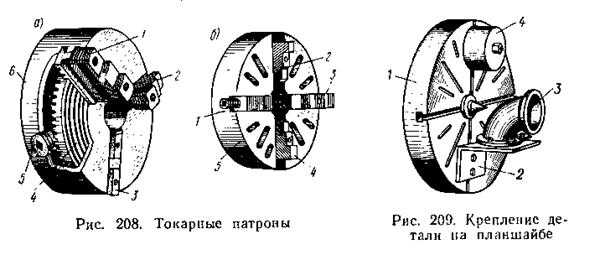
При обработке на токарном станке тяжелых и длинных деталей один конец обычно закрепляют в патроне, а другой поддерживается центром задней бабки. Это необходимо для жесткого закрепления детали.
Точение в патроне. Наружное точение деталей длиной L<D4 осуществляют проходными и подрезными резцами. Такие детали закрепляют только в патроне (без поддержки свободного конца центром задней бабки токарного станка). Для закрепления используют трех и четырехкулачковые патроны, навинчиваемые на шпиндель.
Трехкулачковый самоцентрирующийся патрон (рис. 11,а) используют обычно для закрепления симметричных деталей. В этом патроне кулачки 1—3 имеют радиальное перемещение. Для этой цели служит большое зубчатое коническое колесо 4 с нарезанной плоской спиральной впадиной на торцовой стороне, а также связанные с ним три небольших конических зубчатых колеса 5, вмонтированных в корпус 6 патрона. Выступы кулачков входят в спиральную впадину большого колеса и при вращении последнего вместе с кулачками совершают перемещение в радиальных пазах корпуса патрона.
В четырехкулачковом патроне (рис. 11,б) каждый из кулачков 1—4, укрепленных в радиальных пазах планшайбы 5 имеет независимое перемещение. Эти патроны применяют для установки и закрепления деталей сложной и несимметричной формы.
Обработку плоскостей пластин и других плоских деталей удобно проводить в патронах с постоянным магнитом.
При массовом и крупносерийном производстве некоторых деталей применяют патроны с пневматическими и гидравлическими зажимами, которые значительно облегчают и ускоряют работу.
Точение на планшайбе. При обработке несимметричных деталей и деталей сложной формы, закрепление которых в кулачковых патронах неудобно или невозможно, применяют планшайбу 1 (рис.12), навинчиваемую на шпиндель. Планшайба представляет диск с радиальными пазами. Обрабатываемую деталь укрепляют на планшайбе болтами. Если такое крепление затруднительно, то сначала ставят угольник 2 и к нему прикрепляют обрабатываемую деталь-патрубок 3. Закрепленная деталь уравновешивается противовесом 4. При точении на планшайбе резцы применяют в зависимости от вида выполняемой работы; при обработке фланца патрубка (рис.12) используют подрезной резец.
Растачивание Внутреннее точение осуществляют расточными резцами. Обрабатываемые детали укрепляют в кулачковых патронах или на планшайбе. Иногда растачиванию предшествует сверление отверстия.
Торцовое точение. При торцовом точении на обрабатываемой детали можно получить сплошную торцовую плоскость или частичную кольцеобразную плоскость поперечной подачей резца. Точение торцовых поверхностей производят подрезными резцами; обрабатываемую деталь закрепляют в кулачковых патронах или на планшайбе.
Отрезание и подрезание. При отрезании или подрезании обрабатываемую деталь закрепляют в патроне. Отрезание выполняют при поперечной подаче отрезного резца. Подрезание можно производить перемещением резца к центру детали или от него.
Нарезание резьбы. Перед нарезанием резьбы производят настройку станка в большинстве случаев набором соответствующих сменных зубчатых колес гитары подач.
Расчетное уравнение кинематической цепи шпиндель — суппорт при нарезании резьбы выводится из условия, что за один оборот шпинделя продольное перемещение суппорта станка должно быть равно шагу резьбы (tр, которое определяют по уравнению
tp=tх в. iсм.iоб[8]
Отсюда
iсм = tp /(tх в. iоб) [9]
где tх в — шаг ходового винта станка; iсм — передаточное отношение сменных зубчатых колес; iоб— общее передаточное отношение всех постоянных передач от шпинделя до ходового винта.
Полученное отношение для настройки станка при нарезании резьбы определяет кинематическую связь ходового винта станка со шпинделем. Используя это отношение, можно решать различные задачи настройки станка для нарезания резьб подбором сменных зубчатых колес с соответствующим числом зубьев.
Деталь для нарезания резьбы закрепляют в центрах или патроне, что зависит от ее длины. В качестве режущего инструмента применяют резьбовые резцы соответствующего профиля.
Точение конусов. Конические поверхности можно обрабатывать при повороте верхних салазок суппорта (рис. 13,а), при поперечном смещении корпуса задней бабки (рис. 13,б) при помощи копировальной линейки (рис. 13,в) и других приспособлений.
|
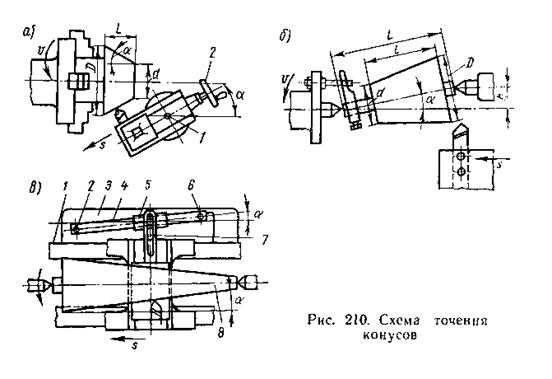
Угол поворота a суппорта определяют по формуле
tga =(D - d)/(2l) [10]
где D и d— больший и меньший диаметры конуса; l —длина конуса.
Затем верхние салазки поворачивают на угол a вокруг оси 1 (рис. 13,а) и закрепляют их в этом положении. Точение производят проходным резцом при ручной подаче вращением рукоятки 2. Этим способом можно обтачивать наружные и внутренние конусы небольшой длины, но с большими углами. Обрабатываемую деталь закрепляют в патроне.
Длинные детали с небольшой конусностью (a < 8°) обычно обрабатывают при поперечном смещении корпуса задней бабки (рис. 13,б) на величину h, определяемую по формуле
h = L(D – d)/(2l) [11]
где L — длина всей детали.
После поперечного смещения корпуса задней бабки на величину h (до 15—20 мм) образующая обрабатываемого конуса параллельна направлению продольной подачи резца, поэтому точение можно вести с механической подачей.
Конусные детали большой длины часто обрабатывают при помощи копировальной (конусной) линейки (рис. 13,в). С этой целью на кронштейне 3, прикрепленном к станине 1, располагают линейку 4 с ползуном 5. Поперечные салазки станка освобождают от связи с гайкой на винте поперечной подачи и через тягу 7 соединяют с ползуном 5. Линейку 4 закрепляют болтами 2 и 6 под углом а, определенным по формуле 10. При продольном движении суппорта ползун 5 скользит по линейке и перемещает резец в направлении, перпендикулярном оси детали 8. В результате сложения двух движений резец перемещается параллельно копировальной линейке и обрабатывает поверхность по заданному конусу.
Точение фасонных заготовок. Фасонные заготовки обрабатывают фасонными резцами или при помощи копировальных приспособлений поперечной подачей.
|
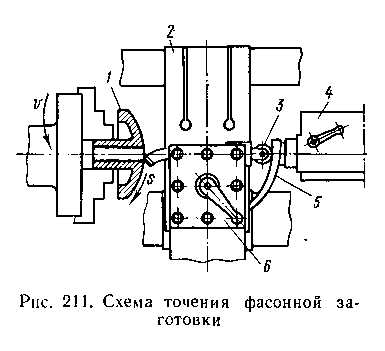
Фасонные резцы обычно применяют в качестве чистовых, поэтому они долговечны и хорошо сохраняют свой профиль. Копировальные приспособления, применяемые для обработки фасонных поверхностей, бывают механические и гидравлические.
На рис. 14 показана схема точения фасонной заготовки при помощи механического копировального приспособления. Копир 5 установлен в пиноли задней бабки 4. В резцедержателе 6 напротив резца укреплен ролик 3, который находится в контакте с копиром 5. Каретка суппорта 2 может свободно перемещаться в продольном направлении. При поперечной подаче резца и постоянном контакте ролика 3 с копиром 5 образуется сферическая поверхность детали 1. С таким приспособлением при замене копира можно обрабатывать другие фасонные заготовки.
Для получения фасонных поверхностей при продольном точении используют те же копировальные приспособления, что и при обработке конусов, но в этом случае копировальную линейку заменяют соответствующим фасонным копиром. Некоторые фасонные заготовки при продольном точении обрабатывают при помощи гидрокопировальных приспособлений, называемых гидрокопировальными суппортами.
Токарные автоматы
Для выполнения ряда токарных работ применяют полуавтоматы и автоматы.У токарных полуавтоматов автоматизированы обычно только рабочие операции по обработке детали (снятие стружки резцом), а вспомогательные операции (установка и закрепление обрабатываемой заготовки, освобождение и снятие ее со станка, пуск станка, контроль размеров обрабатываемой детали и т. д.) выполняются вручную. У автоматов автоматизирован весь цикл обработки детали.
У станков-автоматов различные операции автоматизированы при помощи механических, гидравлических, электрических, пневматических, электронных и смешанных устройств (систем). Работа этих устройств регламентируется программным устройством с применением перфолент или счетно-решающих машин (в системе программного управления).
Рассмотрим схему устройства и работы токарного автомата модели 1С616 (рис. 15 а). Автомат предназначен для обработки валов в центрах по автоматическому циклу (с загрузкой заготовок и разгрузкой деталей) с применением гидрокопирования по программному управлению.
Станок установлен на двух пустотелых тумбах. В левой тумбе 1 смонтирована коробка скоростей с рукоятками для установки числа оборотов шпинделя. Коробка скоростей имеет 12 ступеней чисел оборотов шпинделя (от 90 до 2240 об/мин). В правой тумбе 12 расположено гидрооборудование станка (гидропривод). Выше левой тумбы размещен механизм программирования 16 со штоком 15, получающим перемещение от фартука 14. Механизм программирования 16 (рис. 15,б) подает электрические команды при автоматическом цикле работы. Электрический контакт осуществляется щетками, расположенными на движущейся каретке, через упоры, закрепленные на плите. Каретка со щетками, проходя над упорами, дает соответствующие команды («Подача», «Быстрый обратный ход», «Стоп» и т. д.).
Фартук, получает поступательное движение от ходового валика 13, который в свою очередь получает подачу от отдельного гидромотора МГ-152 с редуктором, смонтированного на правом торце станины. На фартуке расположена панель электроуправления для пуска и остановки станка, а также быстрого хода каретки.
В шпиндельной бабке 3 размещен шпиндель 2 с гидроцилиндром 2а для зажима заготовки, подаваемой на центры станка. С другой стороны заготовка зажимается задней бабкой 8 при помощи гидроцилиндра 8а. Последний осуществляет осевое перемещение пиноли задней бабки.
Заготовки поступают на загрузочный приемник 4 с цепной передачей I7, движение которой сообщает гидроцилиндр 4а через храповик 18. В соответствии с заданной программой заготовка при помощи механизма проталкивания 19 с гидроцилиндром 19а, укрепляемого на заднем торце шпиндельной бабки, проталкивается планками по лотку заготовок к автооператору 7. Последний имеет два подающих механизма с лотками (один над другим) с гидроцилиндрами 7а. Заготовка с нижнего лотка подается на линию центров станка; перед этим верхний лоток убирает готовую деталь, поднимая ее на уровень лотка готовых деталей. Поступившая на линию центров заготовка при помощи гидроцилиндров 8а и 2а зажимается и закрепляется в патроне специальным устройством — цангой (помещается в патроне).
После настройки станка, зажатия и закрепления заготовки пакетный выключатель на щите шкафа 9 с электрооборудованием ставят в положение «Автоматическая работа» и кнопкой «Пуск» (на панели фартука включают главное движение (главный электродвигатель) и движение подачи (подвод гидрокопировального суппорта 6 к заготовке и щупа к копиру). С включением подачи последующие команды выполняются механизмом программирования через упоры плиты и каретку.
Гидрокопировальный суппорт (типа СГП2) (взамен поворотной части обычного суппорта) установлен на токарном автомате под углом 60° к оси центров станка. Гидросуппорт действует по схеме однокоординатного копирования с заданной продольной подачей. В качестве копира применяют плоский стальной шаблон.
При подаче очередной заготовки на нижний лоток механизм проталкивания при помощи пальца 5, находящегося на уровне лотка готовых деталей, проталкивает детали по лотку и подает на лоток сбрасывателя 10, установленного на направляющих станины правее задней бабки. Получив очередную деталь, сбрасыватель при помощи гидроцилиндра 10а опускается, наклоняет лоток и сбрасывает готовую деталь на приемник 11.
|
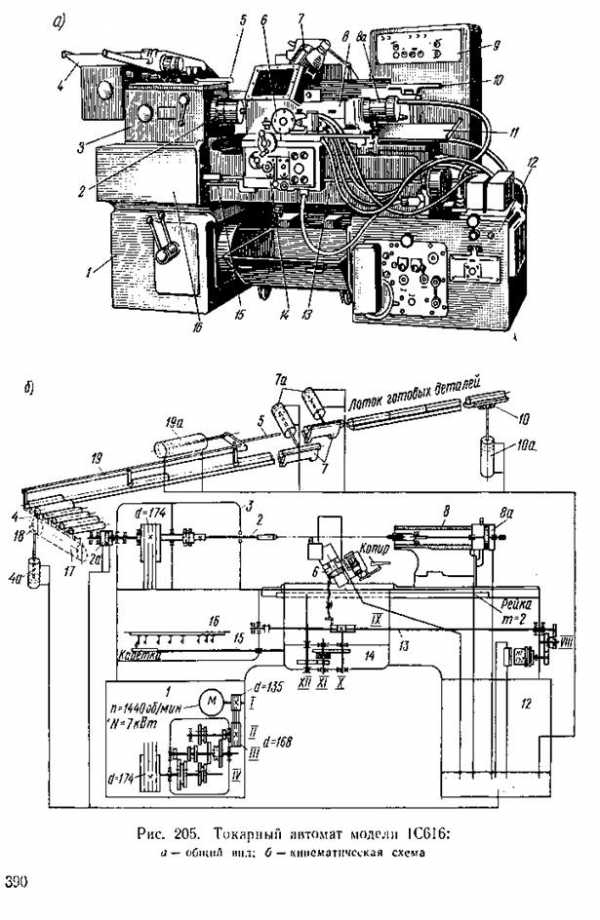
Токарно-затыловочные станки
infopedia.su