Режущий инструмент и режущее сопло для гидроабразивного режущего устройства. Сопло для гидроабразивной резки
Сопла для гидроабразивной резки - В наличии на складе
Сопло гидроабразивной резки — самый быстро изнашиваемый компонент режущей головки. Средний срок службы 30-40 часов непрерывной резки. Он может как увеличиваться (при резке чистой водой), так и уменьшаться (в случае использования большого количества абразива). Различаются сопла конфигурацией и диаметром отверстий. Комбинируя сопла и фокусирующие трубки можно достичь идеальной кромки реза для каждого конкретного материала.
Мы предлагаем сопла по самой низкой цене 5 USD за штуку. Сопла для гидроабразивной резки всегда в наличии на нашем складе в Москве. Оставьте заявку и мы выставим счет.
Как выбрать сопло для гидроабразивной резки?
На рынке представлены два типа сопел: алмазные и сапфировые (рубиновые). Первые имеют длительный срок службы (порядка 2000 часов) и высокую стоимость около 400-500 долларов. Вторые стоят всего 5-15 долларов, а срок их непрерывной работы не более 40-50 часов.
Вопрос «Какие сопла лучше?» задавал хоть раз каждый оператор станков гидроабразивной резки. С одной стороны высокое качество и долгая непрерывная работа, с другой — дешевизна.
Как показывает практика, у каждого их них своя область применения. Алмазные сопла будут эффективны только при резке твердых материалов большой толщины. Такая работа может продолжаться более 20 часов, в течение которых сапфировое сопло износится с вероятностью 80%. Это грозит плохим качеством кромки и необходимостью останавливать программу для замены сопла.
При использовании двойной режущей головки сапфировые сопла тоже будут неудачным выбором. Срок службы одного сопла может составить 20 часов, а другого 30 часов. Таким образом, придется останавливать машину и менять изношенное сопло каждые 10 часов, либо менять сразу оба.
Во всех остальных случаях сапфировые сопла — лучший выбор. При резке широкого спектра материалов приходится часто менять диаметры фокусирующих трубок и сопел, что плохо сказывается на сроке их службы. Низкая стоимость здесь является определяющим фактором выбора.
Зависимость скорости резки (м/мин) от диаметра сопла
Материал | Толщина материала | Диаметр сопла | |||
0.007″ | 0.010″ | 0.012″ | 0.014″ | ||
Алюминий | 6 мм | 0.3-0.48 | 0.58-0.86 | 0.76-1.19 | 0.97-1.47 |
13 мм | 0.15-0.20 | 0.28-0.38 | 0.33-0.53 | 0.43-0.66 | |
20 мм | 0.076-0.10 | 0.13-0.18 | 0.15-0.25 | 0.20-0.30 | |
Нержавеющая сталь | 6 мм | 0.10-0.15 | 0.20-0.30 | 0.25-0.41 | 0.33-0.51 |
13 мм | 0.051-0.076 | 0.10-0.13 | 0.13-0.18 | 0.15-0.23 | |
20 мм | 0.025-0.051 | 0.051-0.076 | 0.051-0.076 | 0.076-0.10 | |
Титан | 6 мм | 0.13-0.18 | 0.23-0.33 | 0.30-0.48 | 0.38-0.58 |
13 мм | 0.051-0.076 | 0.10-0.15 | 0.13-0.20 | 0.18-0.25 | |
20 мм | 0.025-0.051 | 0.051-0.076 | 0.051-0.10 | 0.076-0.13 | |
Мрамор | 6 мм | 0.36-0.43 | 0.56-0.79 | 0.71-1.12 | 0.91-1.37 |
13 мм | 0.15-0.20 | 0.25-0.36 | 0.33-0.51 | 0.41-0.64 | |
20 мм | 0.076-0.10 | 0.13-0.15 | 0.15-0.23 | 0.18-0.28 | |
Гранит | 6 мм | 0.51-0.79 | 0.99-1.42 | 1.44-2.01 | 1.60-2.44 |
13 мм | 0.23-0.36 | 0.46-0.64 | 0.56-0.89 | 0.74-1.09 | |
20 мм | 0.10-0.15 | 0.20-0.28 | 0.25-0.41 | 0.33-0.48 | |
Расход абразива (кг/мин) | 0.18-0.27 | 0.32-0.45 | 0.41-0.68 | 0.59-0.91 |
Примечание: данные приведены для насоса с рабочим давлением 4137 бар.
waterjetparts.ru
Статьи Росмарк-Сталь- Системы гидроабразивной резки Water Jet Sweden
Установки гидроабразивной резки размещаются на станине выполненной из высокопрочной термостабилизированной стали. Станок состоит из стола-резервуара с поддерживающими решетками для размещения обрабатываемой заготовки, станины, и подвижного портала, перемещающегося по направляющим станины (ось Y). Портал также имеет направляющие, по которым перемещается суппорт с одной или несколькими режущими головками для резки водой/ водой с абразивом (ось X). Установка оборудована системой очистки воды от механических примесей, насосом высокого давления, устройством ЧПУ FANUC или SIEMENS, программой CAD/CAM, системой очистки отработанной воды перед сливом в дренаж, бункером высокого давления для хранения и подачи абразива, дозирующими устройствами подачи абразивного песка к режущим головкам и комплектом предохранительных устройств. Станок поставляется с полным комплектом руководств по эксплуатации.
Станина и портал станка гидроабразивной резки
Станина установки гидроабразивной резки Water Jet Sweden выполнена из термостабилизированной стали, обеспечивающей неизменность её формы с течением времени, высокую точность траектории движения портала и параллельность направляющих. Система направляющих станины, защищённая международным патентом, исключает так называемый "эффект увода", который приводит к неконтролируемому перемещению.
Отличительной особенностью установки гидроабразивной резки являетсяшарнирно-петлевая конструкция передвижного портала, обеспечивающая высокую точность перемещений и исключающая вероятность повреждения станка при случайных ударах портала, например, при загрузке листа на стол установки или при аварийном врезании сопла в обрабатываемую поверхность, что может быть вызвано ошибкой оператора. Конструкция портала также предотвращает вероятность заклинивания портала при его температурной деформации.
Станина станка продувается и грунтуется перед нанесением верхнего слоя голубой краски RAL5015. Такие важные узлы, как двигатели, кабели и соединительные блоки встроены в стойку.
Приводы
Привод механических перемещений портала (ось Y), суппорта (ось Х) и режущей головки (ось Z) осуществляетсяпрецизионными шарико-винтовыми парами BOSCH. Шарико-винтовые пары управляются двигателями переменного тока со встроенными круговыми абсолютными датчиками положения. Все станки оснащены запатентованной системой направляющих. Шарико-винтовые пары герметично защищены от воды и грязи резиновыми листами и гофрами.
Такая конструкция привода обеспечивает высокую точность и плавность перемещений. Использование шарико-винтовых пар по сравнению с другими типами механических приводов (шестерня-зубчатая рейка, червячно-реечная передача) означает снижение коэффициента трения в 10 раз, что увеличивает износостойкость и долговечность привода машин гидроабразивной резки Water Jet Sweden на порядок.
В конструкции привода установок гидроабразивной резки Water Jet Sweden с длиной стола свыше 6 м используютсялинейные двигатели, исключающие механические передачи и обеспечивающие высокую точность позиционирования, скорость и плавность перемещений.
Стол-резервуар
Резервуар, наполненный водой, оснащен опорными решетками высотой 200 мм из нержавеющей стали толщиной 2,5 мм. Опорные решетки надежно закреплены в резервуаре для резки для обеспечения максимальной стабильности. На опорных решетках располагаются режущие решетки, на которых размещается заготовка. Максимальная нагрузочная способность стола установок стандартного модельного ряда составляет 800 кг/м2. В случае необходимости нагрузочная способность стола может быть увеличена. Режущие решетки выполнены из материала с цинковым покрытием, их высота - 50 мм. Решетки одинакового размера, и, следовательно, их можно перемещать или поворачивать на 180 градусов на столе. Для обеспечения резки "под водой" резервуар может быть оснащён системой быстрого подъёма воды.
Стол-резервуар для размещения заготовки выполнен из нержавеющей стали и, следовательно, не требует техобслуживания. Стол не соприкасается со станиной станка, что исключает возможность механических и температурных влияний стола на станину и её деформации.
Режущая головка и клапан высокого давления
Режущие головки и сопла, совмещенные со смесительной камерой, были специально разработаны Water Jet Sweden для обеспечения максимальной эффективности режущего действия водоабразивной струи. Отверстие в режущей головке автоматически соосно выставляет сопло. Режущая головка легко переналаживается для резки чистой водой или водой с абразивом. Для обработки фасок на листовом материале, режущая головка может быть оснащена ручным приспособлением для её поворота. По словам пользователей установок гидроабразивной резки Water Jet Sweden в России, срок службы сопла достигает 220 часов в зависимости от режимов резания.
Сопла, применяемые для гидроабразивной резки на машинах Water Jet Sweden, выполнены как единое целое со смесительной камерой, оптимально эффективная форма которой была определена специалистами компании в результате расчётов и подтверждена многолетним опытом. Такая конструкция сопла обеспечивает стабильность гидроабразивной струи и удобство обслуживания по сравнению с конструкцией, где смесительная камера и сопло выполнены отдельно. Кроме того, конструкция сопла Water Jet Sweden позволяет повысить режущую способность гидроабразивной струи на 10-15%, что увеличивает производительность, скорость и качество обработки
Клапан высокого давления, находящийся перед режущей головкой, со встроенным ручным клапаном - также продукт, разработанный Water Jet Sweden. Он сконструирован для повышения личной безопасности оператора. Этот клапан запатентован в большинстве стран мира.
Дозирующее устройство подачи абразива
Устройство подачи абразива - продукт компании Water Jet Sweden - позволяет регулировать количество абразивного материала, подаваемого к режущим головкам. Дозирующее устройство снабжено электронным датчиком контроля прекращения прохождения песка в случае аварийного попадания воды в песковод.
Датчик высоты и датчик предотвращения столкновений абразивного сопла
Датчик высоты предназначен для предотвращения столкновений режущего сопла с поверхностью обрабатываемой заготовки и сохранения постоянного расстояния между соплом и заготовкой в процессе резки. Применение датчика особенно необходимо при большой протяженности реза, где неплоскостность разрезаемого листа может вызвать столкновение сопла с поверхностью заготовки.
Датчик предотвращения столкновений сопла в отличие от датчика высоты не отслеживает постоянное расстояние между соплом и выполняет функцию остановки работы машины при аварийном приближении сопла к поверхности заготовки.
Сверлильная головка
При прошивке технологического отверстия, необходимого для начала вырезки детали, в месте выхода гидроабразивной струи имеется опасность растрескивания, расслаивания или скола материала. К материалам, склонным к образованию подобного рода дефектов, относятся большинство пластиков, слоистые материалы, а также текстолиты и стеклотекстолиты. Для предотвращения вероятности возникновения указанных технологических проблем, при резке перечисленных материалов вместо прошивки начального технологического отверстия гидроабразивной струёй используют предварительное сверление этого отверстия. С этой целью установки гидроабразивной резки Water Jet Sweden могут быть укомплектованы пневматической сверлильной головкой.
Камера (Бункер) для хранения и подачи абразива
Бункер предназначен для подачи абразивного песка под давлением сжатого воздуха (6.5 бар) к устройству дозируемой подачи. Объём бункера - 200 л. Бункер оборудован датчиком низкого уровня песка, предупреждающего оператора о необходимости заполнения бункера, а также датчиком остановки машины при отсутствии песка в бункере.
Для снижения трудоёмкости загрузки абразива в бункер и удобства обслуживания машины, установка может быть снабжена башней-контейнером, вмещающего до 1500 кг абразива. При использовании башни-контейнера абразив поступает в бункер из башни при открытии её заслонки вручную или автоматически.
Система очистки ванны и пакетирования отходов
Удаление шлама и отработанного абразива из ванны установки осуществляется с помощью мембранных пневмонасосов, работающих поочерёдно. Количество насосов зависит от размеров стола установки. Пневмонасосы управляются от шкафа управления. Каналы для удаления отходов оснащены системой очистки и промывки водой, приводимой в действие сжатым воздухом. Насосы откачивают шлам и отходы обработки через фильтр и выпускают их в контейнер для отходов емкостью 1000 литров, где отходы обработки отцеживаются и собираются в мешки (или пакеты), в которых песок поступает на предприятие. Последнее обстоятельство чрезвычайно удобно, поскольку позволяет утилизировать отходы в той же упаковке, в которой песок приходит на предприятие.
Контейнер-отстойник
Перед сливом в дренажную систему избыточная вода вытекает в контейнер-отстойник с шестью ступенчатыми отсеками, где очистка воды происходит за счёт последовательного осаждения отходов в каждом отсеке и перелива в следующий.
Насос высокого давления
Установки гидроабразивной резки Water Jet Sweden оборудованы насосами высокого давления от ведущих производителей и могут иметь различную производительность и развиваемую мощность.
Отличительные черты насосов KMT STREAMLINE V:
- двухсторонний интенсификатор с продолжительной активной фазой перемещения плунжера
- запатентованная "быстрая замена плунжера" сокращающая время обслуживания
- сертифицированный TUF аккумулятор для лучшего сглаживания пульсаций давления
- "медленный старт" насоса для плавного выхода на номинальный режим работы
- два переключаемых уровня давления для "просверливания" хрупких материалов
- плавная регулировка давления
- манометр для индикации давления масла и воды
- быстрое отключение воды низкого давления от интенсификатора
- замкнутый круг циркуляции масла с эффективным теплообменником
- масляный фильтр 10 микрон, расположенный непосредственно в баке
Технические характеристики насоса 50HP STD
Мощность | 50 л.с./37кВт |
Ток двигателя | 80A |
Питание PLC | 24V DC/10A |
Максимальная производительность воды для резки | 3,8 л/мин. |
Максимальное давление | 3.800 бар |
Минимальное давление | 500 бар |
Коэффициент интенсификации | 20 : 1 |
Ёмкость аккумулятора | 1 литр |
Насосы высокого давления могут быть оснащены водяным или воздушным охлаждением.
Рабочие характеристики
Электрическое подключение станка: 3 x 400 В, 25 A, 50 Гц (с нейтральными выводами) Давление поступающей воды: 3…4 бар Расход воздуха: максимум 600 литров в минуту Давление воздуха: минимум 6,5 бар
Система подготовки воды
Для очистки от механических примесей вода, поступающая к насосу высокого давления, проходит очистку в 2-х последовательно расположенных фильтрах 25 мкм и 1/3 мкм.
В случае, если химический состав поступающей к насосу воды не удовлетворяет предъявляемым требованиям, машина должна быть оборудована системой умягчения воды. Система включает в себя фильтры из ионно-обменной смолы, регулирующие химический состав поступающей воды. Автоматическая промывка фильтров соляным раствором осуществляется по объёму проходящей воды.
Устройство ЧПУ
Установка гидроабразивной резки укомплектована системой управления GE FANUC или SIEMENS. Шкаф управления оборудован устройствами ввода ЧПУ и ручного ввода данных, дисплеем времени резания, контролем срока службы сопла, регулируемой компенсацией радиуса во время операции (он-лайн), а также обратной функцией в программе. Система управления базируется на кодах стандарта ISO. Шкаф управления соответствует указаниям по охране труда в машиностроении 89/336/ЕЕС в отношении электромагнитной интерференции, а также требованиям EMC от 01.01.1996.
Предохранительные устройства
Установка гидроабразивной резки оснащена устройствами безопасности, которые отвечают правилам безопасности ЕС для режущих станков такого типа, согласно 89/392/EEC, 72/23/EFC, 89/336/EEG, а также стандартным декларациям EN60204, EN292-1, EN292-2, EN294, EN394, EN418 и prEN983. Установка гидроабразивной резки устанавливается с линиями безопасности, а перед установкой имеется защитное ограждение. По требованию клиента вокруг установки гидроабразивной резки могут быть поставлены защитные щитки высотой 2 метра, сделанные из алюминиевого профиля со стеклянными панелями. Это также соответствуют требованиям СЕ.
Руководства по эксплуатации
Со станком поставляется следующая документация: Часть I - Руководство по обслуживанию и работе на установке гидроабразивной резки Water Jet Sweden ЧастьII - Технические параметры станка, электросхемы, пневмосхема, CNC и PLC параметры
- Руководство по работе и обслуживанию насоса высокого давления
- Руководство по эксплуатации и обслуживанию системы управления ЧПУ
- Руководство по использованию программного обеспечения
Другие статьи
www.rosmark-steel.ru
СОПЛА ДЛЯ ГИДРОАБРАЗИВНОЙ РЕЗКИ | Progk.ru: в г. Краснодар
Я даю согласие ООО «ПРОФЕССИОНАЛ ГРУПП - КРАСНОДАР» на обработку моих персональных данных, указанных в заявке, любыми способами, в том числе третьими лицами, в том числе воспроизведение, электронное копирование, обезличивание, блокирование, уничтожение, а также вышеуказанную обработку иных моих персональных данных, полученных в результате их обработки, с целью:
- идентификации стороны в рамках соглашений и договоров;
- предоставления Пользователю услуг, в том числе, в целях получения Пользователем таргетированной рекламы;
- проверки, исследования и анализа таких данных, позволяющих поддерживать и улучшать сервисы и разделы Сайта, а также разрабатывать новые сервисы и разделы Сайта;
- проведение статистических и иных исследований на основе обезличенных данных;
- отправки Пользователю электронных сообщений по указанным в заявке контактным данным.
Регистрируясь на Сайте и используя Сайт и Сервисы, я даю согласие на обработку своих персональных данных в соответствии с настоящими условиями.
Указанное согласие дано на срок 15 лет, а в случае его отзыва обработка моих персональных данных должна быть прекращена ООО «ПРОФЕССИОНАЛ ГРУПП - КРАСНОДАР» и/или третьими лицами и данные уничтожены при условии расторжения действующих Договоров об оказании услуг и полного погашения задолженности по Договорам.
ООО «ПРОФЕССИОНАЛ ГРУПП - КРАСНОДАР» вправе использовать предоставленную информацию, в том числе персональные данные, в целях обеспечения соблюдения требований действующего законодательства Российской Федерации (в том числе в целях предупреждения и/или пресечения незаконных и/или противоправных действий Пользователей). Раскрытие предоставленной Пользователем информации может быть произведено лишь в соответствии с действующим законодательством Российской Федерации по требованию суда, правоохранительных органов, а равно в иных предусмотренных законодательством Российской Федерации случаях.
progk.ru
Гидроабразивные сопла TetraCore | Центр развития гидроабразивных технологий
23 июня 2017 г. 5:57
Главная проблема сопел (дюз) для гидроабразивных установок - необходимость выбора между дешевыми рубиновыми соплами с коротким сроком службы, и прочными, долговечными, но довольно дорогими алмазными. Компания ЦРГТ предлагает решение - сопла TetraCore
Уже более года компания ЦРГТ поставляет пользователям гидроабразивных станков в России сопла (дюзы) TetraCore. Эти сопла были разработаны компанией DTI, США.
Перед производителем стояла задача разработать дюзу для гидроабразивной установки, которая превосходила бы по своим характеристикам рубиновые сопла, имея при этом стоимость существенно ниже, чем у алмазных сопел.
Результатом стало сопло TetraCore (или, как его называют, “тетракор”). Для сопла TetraCore был разработан абсолютно новый высокопрочный материал. Название “тетракор” имеет своим корнем тетраэдральные молекулярные связи в новом материале. Компания DTI особенно подчеркивает особенность молекулярной решетки в новом материале - тетраэдральные связи обеспечивают потрясающую прочность материала. Что, в свою очередь, приводит к устойчивости дюзы к сколам, трещинам, эрозии.
Сопла TetraCore работают в 14-15 раз дольше, чем традиционные рубиновые сопла. При этом, стоимость “тетракоров” значительно ниже, чем стоимость алмазных сопел и примерно равна стоимости 10 “рубинов”. Сопла показали прекрасную надежность, качество режущей струи и точность реза. Заказчики отмечают, что при использовании сопел TetraCore повышается срок службы фокусирующей трубки, так как подается постоянная водяная струя на протяжении долгого времени.
За год с небольшим, сопла TetraCore для гидроабразивных станков получили значительный успех на рынке в Росси. Мы искренне рекомендуем эти сопла.
В заключение, мы хотим поделиться статистикой. За год продано 78 сопел TetraCore. Получая обратную связь от заказчиков, мы выявили основные причины купить “тетракор”. Вот они:
- срок службы фокусирующих трубок увеличивается вследствие постоянности водяной струи в течение продолжительного срока;
- меньше времени простоя станка, так как экономится время на обслуживание режущей головки;
- экономия денег на соплах, так как цена одного тетракора как 10 рубинов, а время работы как у 15 рубинов;
crgt.ru
Метчив - Гидрообразивная резка
Гидрорезка – вид резки, при котором материал обрабатывается при помощи сверхскоростной подачи водной струи. При гидроабразивной резке на поверхность обрабатываемого материала подаётся струя, состоящая уже из двух фаз: воды и высокотвёрдых абразивных частиц. Такая процедура имеет ещё увеличенную разрушительную силу и оказывает мощное эрозионное воздействие на материал.
Весь принцип гидроабразивной резки основан на том, что частицы материала, на который оказывается воздействие, удаляются при помощи скоростного потока твердофазных элементов, при этом эффект процедуры регулируется рядом параметров: определённым давлением воды, размером и расходом абразивных частиц.
Технология резки водой
Вода нагнетается насосом до давления 1000-6000 атмосфер и подаётся в режущую головку. Со скоростью примерно 900-1200 м/с струя воды вырывается через узкое сопло с диаметром 0,08-0,5 мм и поступает в смесительную камеру, в которой смешивается с абразивными частицами - гранатовым песком, зернами электрокорунда, карбида кремния или другими высокотвердыми материалами. Смесь воды и абразива выходит из смесительной трубки с внутренним диаметром 0,5–1,5 мм и разрезает материал.
Очевидное отличие гидрорезки от гидрообразивной резки состоит в том, что в первом случае вода минует процесс смешивания с абразивными материалами, а сразу выходит под давлением через сопло в направлении разрезаемого изделия.
Абразив придаёт струе большую разрушительную силу, в то время как вода необходима для транспортировки. Обычно для эффективного воздействия струи размер абразивных частиц должен составлять от 10 до 30 % относительно толщины диаметра самой струи.
В изготовлении сопла для гидроабразивной резки используют сапфир, рубин или алмаз. Алмазные сопла могут прослужить до 2000 часов, в то время как максимум работы сапфировых или рубиновых доходит до 200 часов. В процессе гидрорезки применяются сапфировые сопла, срок службы которых может доходить до 400 часов.
Схема гидроабразивной резки
Применение технологии резки водой
Водоструйная резка может быть применена в самых разных областях промышленности. Посредством гидрорезки и гидроабразивной резки
К областям применения гидрорезки можно отнести следующие:
· Лёгкая промышленность: производство тканей, кожи; обуви;
· Автомобильная промышленность: пластики, резиновые изделия;
· Электронная промышленность: электронные платы;
· Авиационная и космическая промышленность: ламинированные материалы;
· Изоляция: теплоизоляционные, уплотнительные и шумопонижающие материалы;
· Пищевая промышленность: замороженные продукты, плотные продукты, шоколад и др.;
· Пластики: термо- и дуропласт;
· Различные материалы: бумага, картон, дерево.
Гидроабразивная резка широко используется во многих областях промышленности:
· Металлургия: листы из сталей, металлов, различные металлические детали;
· Авиационная и космическая промышленность: сплавы алюминия, титана и др., композитные материалы, толстостенные пластмассы;
· Жилое и промышленное строительство: бетон, железобетон, гипсовые блоки, брусчатка, камень, гранит, мрамор и др.
· Пластики: армированные пластики;
· Различные материалы: комбинированные материалы, материалы с покрытием, дерево, стекло, бронированное стекло, керамика;
Некоторые абразивные материалы и их применение
Наименование | Область применения |
Гранатовый песок (состоит из корунда Al2O3, кварцевого песка SiO2, оксида железа Fe2O3 и других компонентов) | Широко распространен для резки различных материалов, в особенности высоколегированных сталей и титановых сплавов |
Зерна электрокорунда (состоит преимущественно из корунда Al2O3, а также примесей) или его разновидности | Искусственные материалы с очень высокой твердостью по Моосу. Используются для резки сталей, алюминия, титана, железобетона, гранита и др. материалов |
Зерна карбида кремния (SiC) – зеленого или черного | |
Кварцевый песок (SiO2) | Резка стекла |
Частицы силикатного шлака | Резка пластика, армированного стекло- либо углеродными волокнами |
Типичная форма реза в зависимости от условий резки:
Занос струи при резке со скоростью выше оптимальной:
Скорость разных видов резки в зависимоста от максимальной скорости может составлять следующее процентое соотношение:
- Разделительная резка: 80–100%;
- Качественная резка: 33–65%;
- Тонкая резка: 25–33%;
- Прецизионная резка: в 10–12,5%
Вид поверхности реза в зависимости от скорости водно-абразивной резки:
Примерные размеры абразива при различных режимах резки
Применение | Размер частиц гранатового песка (Garnet) | Внутр. диаметр водяного сопла | Внутр. диаметр смесительной трубки | |||
mesh (США) | микрон | дюймов | мм | дюймов | мм | |
Стандартная промышленная конфигурация | 80 | 178(300–150) | 0,013–0,014" | 0,330–0,356 | 0,04" | 1,02 |
Высокоскоростная резка | 60 | 249(400–200) | 0,014–0,018" | 0,356–0,457 | 0,05" | 1,27 |
50 | 297(600–200) | |||||
Точная резка | 120 | 125(200–100) | 0,012–0,013" | 0,305–0,330 | 0,036" | 0,91 |
80 | 178(300–150) | |||||
Высокоточная резка | 120 | 125(200–100) | 0,010–0,011" | 0,254–0,279 | 0,03" | 0,76 |
Расход абразива зависит от многих факторов: диаметров смесительной трубки и водяного сопла, условий резки и т. д. Ориентировочные оптимальные значения расхода абразивного материала при некоторых соотношениях диаметров смесительной трубки и сопла являются следующими:
Внутренний диаметр водяного сопла (мм) | Внутренний диаметр смесительной трубки (мм) | Расход абразива (г/мин) |
0,25 | 0,76 | 270–360 |
0,36 | 1,02 | 500–640 |
0,46 | 1,27 | 800–1100 |
Зависимость скорости прямолинейной разделительной (черновой) резки от толщины материала при давлении насоса P = 4100 бар (примерно 4046 атм)
Вид материала | Скорость резки (м/ч)* при толщине | ||||
5 мм | 10 мм | 20 мм | 50 мм | 100 мм | |
Нержавеющая сталь | 52,62 | 28,56 | 13,02 | 3,84 | 1,44 |
Титан | 68,46 | 37,20 | 16,98 | 4,98 | 1,86 |
Алюминий | 142,20 | 77,40 | 35,40 | 10,20 | 3,72 |
Гранит | 251,40 | 137,10 | 62,76 | 18,00 | 6,60 |
Мрамор | 295,20 | 160,80 | 73,50 | 21,24 | 7,80 |
Углепластик | 247,20 | 134,70 | 61,74 | 17,70 | 6,60 |
Стекло | 272,76 | 148,62 | 67,92 | 19,62 | 7,26 |
*: давление – 4100 бар; марка абразива – Kerfjet #80; расход абразива – 250–450 г/мин; внутренний диаметр сопла – 0,25 мм, 0,35 мм; внутренний диаметр смесительной трубки – 0,76 мм, 1,01 мм / данные ООО «ТехноАльянсГрупп», г. Москва, установки ГАР BarsJet |
Зависимость скорости прямолинейной разделительной (черновой) резки от толщины материала при давлении насоса P = 6000 бар (около 5922 атм)
Вид материала | Скорость резки (м/ч)* при толщине | ||||
5 мм | 10 мм | 20 мм | 50 мм | 100 мм | |
Нержавеющая сталь | 86,64 | 47,16 | 21,48 | 6,12 | 2,40 |
Титан | 112,38 | 61,50 | 28,08 | 8,22 | 3,06 |
Алюминий | 233,76 | 127,44 | 58,44 | 16,92 | 6,24 |
Гранит | 413,46 | 225,42 | 103,08 | 29,70 | 10,92 |
Мрамор | 485,28 | 264,60 | 121,02 | 34,80 | 12,84 |
Углепластик | 406,56 | 221,88 | >101,40 | 29,22 | 10,86 |
Стекло | 448,14 | <244,38 | 111,72 | 32,16 | 11,88 |
*: давление – 6000 бар; марка абразива – Kerfjet #80; расход абразива – 250–450 г/мин; внутренний диаметр сопла – 0,25 мм; внутренний диаметр смесительной трубки – 0,76 мм, 1,01 мм / данные ООО «ТехноАльянсГрупп», г. Москва, установки ГАР BarsJet |
Детали, полученные гидроабразивной резкой:
- из нержавеющей стали толщиной 15 мм;
- из сплава алюминия толщиной 6 мм;
- из алюминия толщиной 30 мм;
- из пластика, армированного волокном, толщиной 20 мм;
- из инструментальной стали толщиной 60 мм
Преимущества, недостатки и сравнительная характеристика гидроабразивной и гидрорезки
И гидрорезка, и гидроабразивная резка могут применяться практически к любым материалам, при этом их толщина может достигать 300 мм и даже больше. Гидроабразивная резка допускает обработку объёмных изделий, с помощью этой технологии выполняется резка по сложному контуру с соблюдением высокой точности (от 0,025 мм). Заготовка не подвергается механической деформации ввиду небольшой силы удара струи (1-100 Н), также исключены термические деформации, ведь температура в зоне разреза может достигать не более 90°С.
В сравнении с другими эффективными технологиями резки - кислородной, плазменной, лазерной - гидроабразивная обладает несколькими важными отличительными особенностями:
· Высокое качество реза;
· Обработка пожаро- и взрывоопасные, ламинированные, композитные и других термочувствительных материалов;
· Экологически-чистый метод: отсутствие вредных выделений;
· Безопасность: технология исключает возможность возникновения взрыва или пожара.
При всей своей эффективности у гидрообразивной резки есть и ряд недостатков:
· Малая скорость разрезания стали небольшой толщины;
· Высокие эксплуатационные затраты на электроэнергию, воду, абразивные материалы, смесительные трубки, сопла, уплотнители, в том числе издержки на утилизацию отходов;
· Повышенный шум.
www.metchiv.ru
Режущий инструмент и режущее сопло для гидроабразивного режущего устройства
Изобретение относится к струйно-абразивной резке, а именно к режущему инструменту для режущего устройства высокого давления, содержащего канал для потока жидкости и канал для потока суспензии, содержащей взвешенные в жидкости абразивные частицы. Инструмент содержит смесительную камеру, имеющую входную зону, выполненную с возможностью приема потока жидкости и потока суспензии. Давление во входной зоне определяется давлением потока жидкости и влияет на давление в потоке суспензии так, что давление в потоке суспензии по существу равно давлению в потоке жидкости. В результате обеспечивается почти мгновенный запуск струйно-абразивной резки и ее приостановка. 2 н. и 19 з.п. ф-лы, 9 ил.
Область техники, к которой относится изобретение
Настоящее изобретение относится к резке (например, металлов) струями жидкости, содержащими вовлеченные абразивные частицы.
Уровень техники
Применение высокоскоростных водяных струй с вовлеченными абразивными частицами для резки материалов известно примерно с 1980 г. Известны системы водоструйной резки двух типов: системы гидроабразивной резки ГАР (AWJ) и системы резки с применением абразивных суспензий АСР (ASJ). В системах ГАР (AWJ) воду обычно подают в сопло под очень высоким давлением (порядка 150-600 МПа). На фиг.1 показано типичное сопло 10 системы ГАР (AWJ). Сопло 10 содержит отверстие 12 малого диаметра (0,2-0,4 мм), сообщающееся со смесительной камерой 14. Таким образом, вода протекает через смесительную камеру 14 с высокой скоростью.
Мелкие зерна абразивного материала, обычно граната, подаются в камеру, как правило, самотеком, через загрузочный бункер 16. Высокая скорость потока 18 воды вызывает эффект Вентури, в результате чего абразивный материал затягивается в струю воды.
Затем струя воды протекает через отрезок трубки, именуемый фокусирующей трубкой 20. При прохождении воды и абразива через фокусирующую трубку абразивные частицы ускоряются в направлении течения воды. Затем сфокусированная струя 22 воды выходит через выходное отверстие 24 фокусирующей трубки. Струя 22 воды или точнее ускоренных абразивных частиц может быть использована для резки материалов, например, металла.
Между отверстием 12 и выходным отверстием 24 фокусирующей трубки 20 сопла 10 могут происходить значительные потери энергии.
Кинетическая энергия воды теряется при ускорении абразивного материала, а также при ускорении воздуха, захватываемого под действием эффекта Вентури. "Отскакивание абразивных частиц от стенок фокусирующей трубки 20 вызывает значительные потери на трение в трубке. Это приводит к энергетическим потерям в результате выделения тепла и, кроме того, к износу фокусирующей трубки, которая, как правило, приблизительно после 40 часов работы требует замены.
Таким образом, известные системы ГАР (AWJ) являются крайне неэффективными.
В системах АСР (ASJ) смешиваются два жидких потока, поток жидкости (обычно воды) и поток суспензии. Суспензия представляет собой суспензию абразивных частиц. Оба жидких потока находятся под воздействием давления приблизительно от 50 до 100 МПа, и сливаются, образуя один поток. Объединенный поток выталкивается с усилием через отверстие диаметром, как правило, порядка 1,0-2,0 мм, образуя водную струю с вовлеченными абразивными частицами.
Системы АСР (ASJ) не обладают недостатками присущими системам ГАР (AWJ), так как в них не происходит потерь энергии в результате смешения двух потоков под давлением. Однако, известные системы АСР (ASJ) имеют ограниченную промышленную ценность. Причина этого заключается отчасти в том, что системы АСР (ASJ) работают при значительно меньших давлениях и скоростях, чем системы ГАР (AWJ), что ограничивает количество материалов, которые можно резать с использованием таких систем.
При работе систем АСР (ASJ) также возникают значительные проблемы, в основном, из-за наличия в системе абразивной суспензии под давлением, а также из-за отсутствия эффективных средств для обеспечения контроля характеристик ее потока. Элементы системы, осуществляющие нагнетание, транспортировку и регулирование потока абразивной суспензии очень быстро изнашиваются. Степень износа увеличивается с возрастанием давления, ограничивая, таким образом, давление при котором возможна нормальная работа систем АСР (ASJ).
Еще более значительными проблемами представляются практические затруднения, возникающие при запуске и остановке абразивного потока под давлением. При применении водной режущей струи, например, для механической обработки, необходимо обеспечить возможность частого запуска и останова по требованию. В системе АСР (ASJ) для этого потребуется закрыть клапан, перекрывающий поток абразива под давлением. Используемые таким образом клапаны в очень значительной степени подвержены износу. Очевидно, что при закрытии клапана площадь поперечного сечения потока уменьшается до нуля. В результате такого уменьшения площади сечения потока, соответственно увеличивается скорость потока во время закрытия клапана, что приводит к увеличению локального износа клапана.
При работе с типичными для промышленности станками с числовым программным управлением (ЧПУ) может потребоваться очень частое чередование запусков и остановок устройства резки. Это означает частое открывание и закрывание клапанов, управляющих течением абразивного потока под давлением и, как следствие, быстрый износ этих клапанов. Исходя из вышеизложенного, применение систем АСР (ASJ) при обработке материалов на станке с ЧПУ считается нецелесообразным.
Системы АСР (ASJ) применяются в промышленности, например, в нефте- и газоустановках и при подводной резке, где требуется продолжительная по времени резка. Системы АСР (ASJ) не применяются в промышленных масштабах при промышленной обработке на станках с ЧПУ.
На Фиг.2а и 2b схематично показаны известные системы АСР (ASJ). В базовой одноструйной системе 30, показанной на фиг.2а, водяной насос 32 высокого давления приводит в действие плавающий поршень 34. Поршень 34 вызывает повышение давления в абразивной суспензии 36 и нагнетает ее в режущее сопло 38.
На Фиг.2b проиллюстрирована простая двухструйная система 40. Вода, поступающая от насоса 32 разделяется на два потока, один из которых применяется для повышения давления и нагнетания потока 36 суспензии посредством плавающего поршня 34 аналогично тому, как это происходит в одноструйной системе 30. Другой направленный поток 35 воды, смешивается с потоком 37 суспензии под давлением у места соединения перед режущим соплом 38.
Обе эти системы обладают вышеописанными недостатками, что приводит к очень значительному износу клапана. Еще одной проблемой является неравномерная скорость резки из-за значительного износа трубок и сопла.
В патенте США №4707952 (автор - Краснов (Krasnoff)) предлагается другая конструкция.
Система Краснова аналогична двухструйной системе 40, отличаясь от нее тем, что смешивание струи 35 воды и потока 37 суспензии происходит в смесительной камере 52 в режущем сопле 38.
Более подробно смесительная камера 52 Краснова показана на фиг.3. Сопло 38 обеспечивает возможность двухэтапного ускорения. Сначала поток 35 воды и поток 37 суспензии ускоряются через независимые сопла, ведущие в смесительную камеру 52. Затем смешанный поток воды и абразива ускоряется через оконечное выходное отверстие 54.
Система Краснова выполнена с возможностью работы при давлении около 16 МПа, что значительно ниже, чем в других системах АСР (ASJ). Благодаря этому поток суспензии 37 оказывает повреждающее воздействие на клапаны, но все же не приводит к такому значительному износу, как в системах большего давления. Тем не менее, очевидно, что выходная мощность системы Краснова еще ниже, чем у других систем АСР (ASJ), и поэтому возможности ее промышленного применения невелики. Заявителю неизвестно о случаях коммерческого применения системы Краснова.
Задачей настоящего изобретение является обеспечение системы для создания водяной струи высокого давления с вовлеченными абразивными частицами, в которой устранены, по меньшей мере, отчасти некоторые вышеупомянутые недостатки систем ГАР (AWJ) и АСР (ASJ).
Сущность изобретения
В настоящем изобретении предлагается способ, сочетающий в себе многие преимущества систем ГАР (AWJ) и систем АСР (ASJ), и одновременно устраняющий некоторые недостатки каждой системы.
Согласно первому аспекту настоящего изобретения предлагается режущий инструмент для режущего устройства высокого давления, содержащего канал для потока жидкости и канал для потока суспензии, содержащей взвешенные в жидкости абразивные частицы, причем указанный инструмент содержит смесительную камеру, причем смесительная камера имеет входную зону, выполненную с возможностью приема потока жидкости и потока суспензии, причем давление во входной зоне определяется давлением потока жидкости и влияет на давление в потоке суспензии, осуществляя, таким образом, регулирование давления в потоке суспензии.
Предпочтительно, предусмотрена возможность вхождения потока суспензии и потока жидкости в сопло, причем сопло выполнено удлиненной формы, а поток суспензии и поток жидкости ориентированы в направлении удлинения. Благодаря этому уменьшаются энергетические потери, связанные с изменением направления потока, в частности суспензии.
Режущий инструмент может содержать корпус, удерживающий сопло. Этот корпус может иметь выходное отверстие для смешанного потока, причем выходное отверстие имеет выходную фаску с углом конусности около 45°.
Предпочтительно, режущий инструмент содержит клапан потока суспензии, выполненный с возможностью избирательно пропускать или перекрывать поток суспензии в сопло, и клапан жидкости, выполненный с возможностью избирательно пропускать или перекрывать лоток жидкости в сопло.
Предпочтительно, предусмотрена возможность регулирования положения канала для потока суспензии относительно смесительной камеры.
В соответствии со вторым аспектом настоящего изобретения предложено сопло для режущего устройства высокого давления, содержащего канал для потока жидкости и канал для потока суспензии, содержащей взвешенные в жидкости абразивные частицы, причем указанное сопло содержит смесительную камеру, причем смесительная камера имеет входную зону, выполненную с возможностью приема потока жидкости и потока суспензии, причем давление во входной зоне определяется давлением потока жидкости и влияет на давление в потоке суспензии, осуществляя, таким образом, регулирование давления в потоке суспензии.
Предпочтительно, сопло выполнено удлиненной формы, причем поток суспензии и поток жидкости ориентированы в направлении удлинения.
В предпочтительном варианте осуществления, сопло имеет центральную ось, вдоль которой направлен поток суспензии, причем поток жидкости подается в кольцевой элемент вокруг потока суспензии. Благодаря такой конструкции обеспечиваются эффективные средства воздействия давления потока жидкости на поток суспензии, а также уменьшение износа стенок сопла.
Предпочтительно, сопло представляет собой ускоряющее сопло, диаметр выходного отверстия которого меньше, чем диаметр входной зоны. Это позволяет преобразовывать давление в указанных потоках в потоках в высокоскоростной выходной поток.
Этот эффект дополнительно усиливается благодаря тому, что диаметр выходного отверстия меньше диаметра потока суспензии на входе в сопло.
Предпочтительно, сопло на своем наружном конце имеет фокусирующий участок постоянного диаметра на своем наружном конце и конический ускорительный участок уменьшающегося диаметра между входной зоной и фокусирующим участком. Это позволяет получить желаемую скорость и направление выходного потока.
Угол конусности ускорительного участка не должен превышать 27°. Предпочтительно, угол конусности должен составлять около 13,5°. Благодаря этому обеспечивается приемлемый баланс между эффективным ускорением и поддержанием нетурбулентного потока.
Предпочтительно, отношение длина/диаметр фокусирующего участка сопла составляет более 5:1, еще более предпочтительно более примерно 10:1. Также предпочтительно, чтобы отношение длина/диаметр фокусирующего участка сопла составляла менее, чем приблизительно 30:1.
Предпочтительно, сопло выполнено из двух частей, причем смесительная камера определяет первую часть и фокусирующую часть, содержащуюся внутри второй части.
Предпочтительно, вторая часть представляет собой фокусирующее сопло и содержит ускорительный участок с углом конусности большим или равным углу конусности смесительной камеры. Вторая часть может представлять собой составное сопло, выполненное из более твердого материала, чем фокусирующий участок.
Диаметр фокусирующего участка сопла может быть равен или немного меньше минимального диаметра ускорительного участка, что препятствует возникновению турбулентности.
Предпочтительно, ускорительный участок фокусирующего сопла выполнен из прочного на истирание материала, например, алмаза.
Фокусирующее сопло может содержать выходное отверстие, имеющее выходную фаску с углом конусности около 45°. Благодаря такому углу в выходном отверстии обеспечивается отделение потока.
В соответствии с третьим аспектом настоящего изобретения, предложено фокусирующее сопло для режущего устройства высокого давления, выполненное с возможностью принимать поток жидкости и поток суспензии, содержащее фокусирующий участок постоянного диаметра на его наружном конце, и конический ускорительный участок уменьшающегося диаметра между входной зоной и фокусирующим участком.
Предпочтительно, угол конусности не превышает 27° и может составлять около 13,5°.
Предпочтительно, соотношение длина/диаметр фокусирующего участка сопла более чем 5:1 или даже, чем 10:1.
Предпочтительно, фокусирующий участок сопла выполнен из алмаза.
В соответствии с четвертым аспектом настоящего изобретения, предложено сопло для режущего устройства высокого давления, содержащего канал для потока жидкости и канал для потока суспензии, содержащей взвешенные в жидкости абразивные частицы, причем указанное сопло содержит смесительную камеру и фокусирующий участок, причем смесительная камера выполнена из первого материала, а фокусирующий участок выполнен из второго материала.
Предпочтительно, фокусирующий участок является частью фокусирующего сопла, выполненной из второго материала, причем фокусирующее сопло содержит ускорительный участок по существу смежный со смесительной камерой.
В предпочтительном варианте осуществления, режущий инструмент и сопло используются совместно с режущим инструментом высокого давления, содержащим канал для потока жидкости и канал для потока суспензии, содержащей взвешенные в жидкости абразивные частицы, причем энергия к потоку жидкости поставляется посредством первого энергетического средства, а энергия к потоку суспензии поставляется посредством второго энергетического средства, причем оба указанных энергетических средства выполнены с возможностью приведения в действие избирательным образом, причем предусмотрена возможность смешивания потока жидкости и потока суспензии в режущем инструменте, причем по меньшей мере часть поставляемой энергии преобразуется в режущем инструменте в кинетическую энергию для создания высокоскоростного потока смеси жидкости и суспензии. Использование отдельных энергетических средств позволяет управлять течением потоков в системе.
Предпочтительно, энергию, поставляемую первым энергетическим средством, поставляет насос, еще более предпочтительно, насос с постоянным напором, нагнетающий давление в потоке жидкости. Аналогично, энергию, поставляемую вторым энергетическим средством, также предпочтительно поставляет насос, и еще более предпочтительно, насос с постоянным расходом. В подобной конструкции регулируют скорость и объем смешанного потока, управляя давлением насоса с постоянным напором, в то время как скорость потока абразивного материала задают независимо, управляя расходом насоса с постоянным расходом. Таким образом, обеспечено простое регулирование энергии системы или соотношения жидкость/абразив. В альтернативной конструкции энергию к первому и второму энергетическим средствам может подавать один насос.
В предпочтительном варианте осуществления насос с постоянным напором приводит в действие плавающий поршень, нагнетающий, в свою очередь, давление в потоке суспензии. В этом варианте осуществления между насосом и плавающим поршнем может быть расположен клапан, выполненный с возможностью мгновенной остановки потока жидкости и, следовательно, прекращения подачи энергии от насоса с постоянным напором к плавающему поршню. Этот клапан может также препятствует обратному потоку жидкости от плавающего поршня. Таким образом, давление и течение потока суспензии могут меняться, при сохранении постоянного давления в потоке жидкости. Клапан может просто отклонять постоянный поток жидкости от плавающего поршня, например, возвращая жидкость в резервуар насоса.
Режущий инструмент предпочтительно выполнен таким образом, что предусматривает возможность объединения потоков с возможностью управления давлением потока суспензии главным образом через давление потока жидкости. Режущий инструмент содержит смесительную камеру, в которую, при наличии поступления энергии, подается поток жидкости постоянного давления, и поток суспензии с постоянным расходом. Таким образом, давление потока жидкости задает давление во входной зоне смесительной камеры. Давление воздействует на место входа потока суспензии в смесительную камеру, так что попадание потока суспензии в смесительную камеру предотвращено, пока давление в потоке суспензии не поднимется немного выше давления в месте входа в смесительную камеру. Насос с постоянным расходом нагнетает давление в потоке суспензии до достижения им этой точки. Первое условие равновесия выполнено, когда поток суспензии требуемого давления подается с постоянной величиной расхода в смесительную камеру. При выполнении этих условий насос с постоянным расходом эффективно действует в качестве нагнетательного насоса с постоянным расходом.
Когда второе энергетическое средство приостанавливает подачу энергии к потоку суспензии, например, при перекрывании клапана между насосом и поршнем в предпочтительном варианте осуществления, давление потока жидкости в смесительной камере продолжает действовать на поток суспензии. Суспензия из потока суспензии продолжает поступать в смесительную камеру до тех пор, пока давление в потоке суспензии не падает немного ниже давления в смесительной камере. В этот момент поток суспензии прекращается, однако давление в потоке суспензии сохраняется неизменным.
Очевидно, что приостановка подачи энергии от второго энергетического средства приводит к практически моментальной приостановке течения суспензии из-за небольшой разницы давлений в текущей суспензии и в суспензии, находящейся в статическом состоянии.
Аналогичным образом, при активации второго энергетического средства требуемое течение потока суспензии в смесительную камеру получают практически мгновенно.
Краткое описание чертежей
Ниже изобретение описано более подробно со ссылками на прилагаемые чертежи, на которых проиллюстрированы предпочтительные варианты осуществления режущего устройства высокого давления в соответствии с настоящим изобретением. Следует отметить, что возможны и другие варианты осуществления изобретения и, следовательно, следует понимать, что частные примеры, проиллюстрированные на прилагаемых чертежах не ограничивают объем изобретения, как он изложен в предшествующем описании. На чертежах:
На Фиг.1 схематично в разрезе показан режущий инструмент системы ГАР (AWJ) известной из предшествующего уровня техники.
На Фиг.2a схематично показана известная из уровня техники система АСР (ASJ) с одним потоком жидкости.
На Фиг.2b схематично показана известная из уровня техники система АСР (ASJ) с двумя потоками жидкости.
На Фиг.3 в разрезе показано известное их уровня техники режущее сопло.
На Фиг.4 схематично показано режущее устройство высокого давления согласно настоящему изобретению.
На Фиг.5 показан режущий инструмент режущего устройства, показанного на фиг.4.
На Фиг.6 в разрезе показан участок режущего инструмента, показанного на фиг.5, включающего в себя сопло;
На Фиг.7 показан вид в разрезе фокусирующего сопла режущего инструмента, показанного на фиг.5;
На Фиг.8 в разрезе показано фокусирующее сопло согласно другому варианту осуществления фокусирующего сопла режущего инструмента, показанного на фиг.5; а также
На Фиг.9 показан альтернативный вариант осуществления режущего инструмента для применения в режущем устройстве, показанном на фиг.4.
Предпочтительный вариант осуществления изобретения
На фиг.4 схематически показана режущая система 100 высокого давления. Режущая система 100 оснащена режущим инструментом 110, к которому подключены два впускных канала: по одному проходит поток 112 жидкой среды или воды, а по другому - поток 114 суспензии.
И поток 112 воды и поток 114 суспензии подают к режущему инструменту 110 под давлением.
Давление в потоке 112 воды нагнетают посредством первого энергетического средства, в качестве которого используют насос 116 с постоянным напором. В этом варианте осуществления, насос 116 с постоянным напором представляет собой насос, повышающий давление. Насос 116 с постоянным напором обеспечивает поддержание давления в потоке 112 воды на постоянном заданном уровне. Заданное давление могут изменять регулировкой насоса 116 с постоянным напором. Обычно диапазон давления может составлять от 150 МПа до 600 МПа. При нормальных условиях работы полезный результат обеспечивается при водяном давлении около 300 МПа.
Давление в потоке 114 суспензии нагнетают посредством второго энергетического средства. Второе энергетическое средство содержит плавающий поршень 118, активируемый посредством насоса 120 с постоянным расходом. В этом варианте осуществления изобретения насос 120 с постоянным расходом является многоцилиндровым насосом. Плавающий поршень 118 проталкивает суспензию из взвешенных в воде абразивных частиц по направлению потока 114 суспензии при высокой плотности и низкой скорости потока. Расход 114 суспензии регулируется расходом 122 воды, нагнетаемой насосом 120 с постоянным расходом. Заданный расход суспензии можно изменять посредством регулировки насоса 120 с постоянным расходом. Нормальный расход составляет приблизительно один литр в минуту.
Второе энергетическое средство содержит клапан 124, расположенный по потоку 122 воды между насосом 120 с постоянным расходом и плавающим поршнем 118. При закрытии клапана 124 поток 122 воды перенаправляется от плавающего поршня 118 и обратно к насосу 120 с постоянным расходом. При закрытии клапана 124 нагнетание давления в потоке 114 суспензии приостанавливается. Клапан 124 также предотвращает обратный поток воды от плавающего поршня 118 к насосу 120 с постоянным расходом, и таким образом гидравлически отсекает плавающий поршень 118, предотвращая обратный поток 114 суспензии.
Режущий инструмент 110 включает в себя по существу цилиндрический участок 126 корпуса, имеющий по существу цилиндрическое сопло 128, отходящее от его конца. С внутренней стороны конец участка 126 корпуса соединен с двумя форсунками: осевой форсункой 130 суспензии и кольцевой водяной форсункой 132. Форсунки расположены так, что потоки воды и суспензии могут входить в участок 126 корпуса в осевом направлении с кольцевым расположением потока воды вокруг потока суспензии. Водяная форсунка 132 включает в себя выпрямители потока для того, чтобы по существу исключить турбулентность потока воды перед входом в участок 126 корпуса. В этом варианте осуществления поток воды входит в водяную форсунку 132 в радиальном направлении, а затем перенаправляется в осевом направлении. Несколько небольших трубок, работая в качестве выпрямителей потока, способствуют предотвращению турбулентности, создаваемой таким перенаправлением.
Режущий инструмент 110 содержит клапан 131 суспензии, расположенный перед форсункой 130 суспензии, а также водяной клапан 133, расположенный перед водяной форсункой 132. Клапан 131 суспензии и водяной клапан 133 управляются независимо друг от друга, а также могут открываться или закрываться для пуска или останова потока.
Осевое соединение 135 между клапаном 131 суспензии и форсункой 130 суспензии выполнено таким образом, что его длину можно регулировать.
На фиг.6 показано сопло 128. Сопло содержит смесительную камеру 134 и фокусирующую зону 136. Смесительная камера содержит входную зону 138. Смесительная камера 134 также является конической ускорительной камерой с углом конусности приблизительно в 13,5°.
Фокусирующая зона 136 является частью сопла, имеющей постоянный диаметр и непосредственно прилегающей к выходному отверстию 140 сопла. Соотношение длина : диаметр фокусирующей зоны сопла равно 5:1, предпочтительно около 10:1.
Входная зона 138 выполнена с возможностью приема потока суспензии через осевую впускную трубку 142, имеющую по существу постоянный диаметр. Входная зона также выполнена с возможностью приема воды через соосный кольцевой элемент 144, расположенный вокруг впускной трубки 142. Наружный диаметр кольцевого элемента 144 в три-четыре раза больше диаметра впускной трубки 142. Кольцевой элемент 144 соединен с внутренней стенкой смесительной камеры 134 за единое целое, уменьшая таким образом вероятность возникновения турбулентности в потоке воды.
Предусмотрено, что положение впускной трубки 142, и, следовательно, входной зоны 138 может быть изменено. Это может осуществляться посредством регулировки осевого соединения 135. Осевое расположение входной зоны 138 позволяет потоку воды, проходящему через кольцеобразный элемент 144 ускоряться до требуемой скорости перед входом во входную зону 138. Таким образом, обеспечена калибровка потоков воды и суспензии и возможность для оператора регулировать износ или энергопотери.
В варианте осуществления, проиллюстрированном на чертежах, фокусирующая зона 136 образована отдельным фокусирующим соплом 146, аксиально соединенным со смесительной камерой 134. Фокусирующее сопло 146, показанное на фиг.7, содержит ускорительную зону 148, расположенную непосредственно перед фокусирующей зоной 136. Ускорительная зона 148 имеет угол конусности, больший или равный по размеру углу конусности смесительной камеры 134. Диаметр у впускного отверстия ускорительной зоны 148 равен диаметру у выходного отверстия смесительной камеры 134. Желательно, чтобы входной диаметр ускорительной зоны 148 был незначительно больше выходного диаметра смесительной камеры 134 для предотвращения возможности турбулентности.
Фокусирующее сопло 146 может быть выполнено из более твердого и более износостойкого материала, чем материал смесительной камеры 134. Соответствующие участки сопла 128 могут быть выполнены с возможностью ускорения потока жидкости/суспензии до первой скорости, например, 250 м/сек в смесительной камере, а затем до окончательной скорости в ускорительной зоне 148. Соответствующие скорости могут быть рассчитаны и заданы с учетом износостойкости материалов, используемых в двух участках.
В другом варианте изобретения, показанном на фиг.8, фокусирующее сопло 146 представляет собой составное сопло с ускорительной зоной 148 выполненной из особенно твердого, износостойкого материала, например, алмаза, и фокусирующего участка 135, выполненного из другого подходящего материала, например, керамического материала. В этом варианте осуществления изобретения диаметр фокусирующей зоны 136 рассчитан так, что он равен или слегка меньше минимального (выходного) диаметра ускорительной зоны 148.
В обоих вариантах осуществления сопло 128 выполнено достаточной длины для обеспечения требуемой скорости смеси вода/ суспензия, как правило, до 600 м/сек. Следует отметить, что в варианте осуществления, проиллюстрированном на чертежах, диаметр фокусирующей зоны 136 меньше диаметра впускной трубки 142 для суспензии.
Сопло содержит выход 150 с фаской у выходного отверстия 140. Размер угла конусности фаски достаточен для обеспечения отделения потока у выхода 150. В варианте осуществления, проиллюстрированном на чертежах, этот угол равен 45°.
В альтернативном варианте осуществления, проиллюстрированном на фиг.9, фокусирующее сопло 146 содержится внутри наружного держателя 152. В этом варианте осуществления выход 150 с фаской сформирован в наружном держателе 152.
На практике, насос 116 с постоянным напором создает необходимое давление в потоке воды. Вода нагнетается под этим давлением к режущему инструменту 110, через кольцевую водяную форсунку 126 и затем в кольцевой элемент 144. Из кольцевого элемента она входит во входную зону 138 и устанавливает давление во входной зоне 138 близкое к давлению, при котором она нагнеталась.
Суспензия, приводимая в движение плавающим поршнем 118, нагнетается к режущему инструменту 110 через форсунку 130 суспензии во впускную трубку 142.
Следует понимать, что суспензия попадает во входную зону 138, только когда давление во впускной трубке 142 превышает давление во входной зоне 138. При течении суспензии, плавающий поршень 118 (приводимый в действие насосом 120 с постоянным расходом) увеличивает давление в потоке суспензии до тех пор, пока оно не становится достаточно высоким для входа во входную зону 138 смесительной камеры 134. Следует понимать, что оно незначительно выше давления, создаваемого потоком воды во входной зоне 138. Когда в потоке суспензии установлено такое давление (которое обычно составляет около 300 МПа), насос 120 действует на суспензию, обеспечивая ее непрерывную подачу в камеру 134 на постоянной скорости и при постоянном давлении.
Вода и суспензия будут быстро течь вперед и смешиваться в камере 134. Благодаря кольцевому потоку воды стенки камеры 134 хорошо защищены от абразивного воздействия суспензии, по меньшей мере, во внутренней части сопла 128.
К моменту ускорения потока к фокусирующему соплу 146 вода и суспензия хорошо перемешаны. Следовательно, по меньшей мере, один участок фокусирующего сопла должен быть выполнен из прочного на истирание материала, например, алмаза.
Поток выходит из фокусирующего сопла 146 через выходное отверстие 140 на исключительно высокой скорости, пригодной для резки многих металлов и прочих материалов.
Когда необходимо остановить резку активируют клапан 124 для моментальной приостановки работы плавающего поршня 118. Очевидно, что клапан 124 управляет только потоком воды, а не абразивного материала и, следовательно, не подвергается значительному износу. Остановка плавающего поршня 118 приводит к прекращению добавления энергии в поток 114 суспензии. Это приводит к падению давления в потоке 114 суспензии и впускной трубке 142.
При небольшом падении давления во впускной трубке 142 ниже давления воды во входной зоне 138, давление воды предотвращает течение потока суспензии во входную зону 138. Очевидно, что это происходит практически мгновенно при активации клапана 124. Выходная струя из струи воды/суспензии превращается в струю, состоящую только из воды.
В этой точке в потоке 114 суспензии поддерживается высокое давление, и нулевая скорость. В этих условиях клапан 131 суспензии может быть закрыт, не подвергаясь чрезмерному износу.
При закрытии клапана 131 суспензии водяной клапан 133 может быть закрыт для приостановки потока воды. Последовательностью закрытия клапанов быстро управляют, обеспечивая удобный способ запуска и останова резки у режущей головки 110.
При необходимости повторного запуска резки управление клапаном может быть реализовано в обратной последовательности, так что водяной клапан 133 открывается в первую очередь, после чего открывается клапан 131 суспензии. Последовательное открытие клапана 124 приводит к практически мгновенному повторному запуску потока суспензии в смесительную камеру 134.
Сопло содержит выход 150 с фаской у выходного отверстия 140. Размер угла конусности фаски достаточен для обеспечения отделения потока у выхода 150. В варианте осуществления, проиллюстрированном на чертежах, этот угол равен 45°.
В альтернативном варианте осуществления, проиллюстрированном на фиг.9, фокусирующее сопло 146 содержится внутри наружного держателя 152. В этом варианте осуществления выход 150 с фаской сформирован в наружном держателе 152.
Специалисту в области изобретения очевидно, что возможны различные модификации и варианты осуществления в пределах сущности данного изобретения.
1. Режущий инструмент для режущего устройства высокого давления, содержащего канал для потока жидкости и канал для потока суспензии, содержащей взвешенные в жидкости абразивные частицы, причем указанный инструмент содержит смесительную камеру, причем смесительная камера имеет входную зону, выполненную с возможностью приема потока жидкости и потока суспензии, причем давление во входной зоне определяется давлением потока жидкости и влияет на давление в потоке суспензии, таким образом, что предотвращает попадание потока суспензии в смесительную камеру, пока давление в потоке суспензии не поднимется немного выше давления в месте входа в смесительную камеру.
2. Режущий инструмент по п.1, содержащий клапан потока суспензии, выполненный с возможностью избирательно пропускать или перекрывать поток суспензии в смесительную камеру, и клапан жидкости, выполненный с возможностью избирательно пропускать или перекрывать поток жидкости в смесительную камеру.
3. Режущий инструмент по п.1 или 2, в котором предусмотрена возможность регулирования положения канала для суспензии относительно смесительной камеры.
4. Режущий инструмент по п.1, в котором предусмотрена возможность вхождения потока суспензии и потока жидкости в сопло, причем сопло выполнено удлиненной формы, а поток суспензии и поток жидкости ориентированы в направлении удлинения.
5. Режущий инструмент по п.4, в котором сопло имеет центральную ось, вдоль которой направлен поток суспензии, а поток жидкости подается в кольцевой элемент вокруг потока суспензии.
6. Сопло для режущего устройства высокого давления, содержащего канал для потока жидкости и канал для потока суспензии, содержащей взвешенные в жидкости абразивные частицы, причем указанное сопло содержит смесительную камеру, причем смесительная камера имеет входную зону, выполненную с возможностью приема потока жидкости и потока суспензии, причем давление во входной зоне определяется давлением потока жидкости и влияет на давление в потоке суспензии, таким образом, что предотвращает попадание потока суспензии в смесительную камеру, пока давление в потоке суспензии не поднимется немного выше давления в месте входа в смесительную камеру.
7. Сопло по п.6, которое выполнено удлиненной формы, причем поток суспензии и поток жидкости ориентированы в направлении удлинения.
8. Сопло по п.7, которое имеет центральную ось, вдоль которой направлен поток суспензии, причем поток жидкости подается в кольцевой элемент вокруг потока суспензии.
9. Сопло по любому из пп.6-8, которое представляет собой ускоряющее сопло, диаметр выходного отверстия которого меньше, чем диаметр входной зоны.
10. Сопло по п.9, в котором выходное отверстие имеет меньший диаметр, чем диаметр потока суспензии на входе в сопло.
11. Сопло по п.9, которое имеет фокусирующий участок постоянного диаметра на своем наружном конце и конический ускорительный участок уменьшающегося диаметра между входной зоной и фокусирующим участком.
12. Сопло по п.11, в котором угол конусности ускорительного участка меньше 27°.
13. Сопло по п.12, в котором угол конусности ускорительного участка составляет около 13,5°.
14. Сопло по п.11, в котором отношение длина/диаметр фокусирующего участка сопла составляет более чем 5:1.
15. Сопло по п.14, в котором отношение длина/диаметр фокусирующего участка сопла составляет более чем 10:1.
16. Сопло по п.11, в котором отношение длина/диаметр фокусирующего участка сопла составляет менее чем приблизительно 30:1.
17. Сопло по п.11, которое выполнено из двух частей: первой части, образующей смесительную камеру, и второй части, содержащей фокусирующий участок.
18. Сопло по п.17, в котором вторая часть представляет собой фокусирующее сопло и содержит ускорительный участок с углом конусности, большим или равным углу конусности смесительной камеры.
19. Сопло по п.18, в котором диаметр фокусирующего участка равен или немного меньше минимального диаметра ускорительного участка.
20. Сопло по п.18, в котором ускорительный участок фокусирующего сопла выполнен из прочного на истирание материала, например из алмаза.
21. Сопло по п.18, в котором фокусирующее сопло содержит выходное отверстие, имеющее выходную фаску с углом конусности около 45°.
www.findpatent.ru
Струя Воды Насадки Для Гидроабразивной Резки Части,Cnc Гидроабразивной Резки Запасных Частей 7.14*1.0*76.2 Мм
Насадка для водяного струи для резки водяного струи деталей
Описание продукта
WВодный соплоБлагодаря высокой скорости абразивной эрозии, ее выбор очень важен.WВодный сопло Материал, в целом, должен иметь высокую твердость, высокое сопротивление шлифования.
Карбид из карбида Обладает идеальной поверхностью поверхности, высокой точностью и концентрацией.Внутренняя труба с высокой отделкой взрывной отверстия, и использовать уникальную технологию полировки, чтобы сохранить твердость внутренней воды реактивных насадок так же, как снаружи водяных реактивных насадок. Так что не стоит беспокоиться о использовании продуктов.
Преимущества
1. высокая твердость, отличная износостойкость.
2. Твердость, как высокая, как hra 96.
3. Последовательное и длительный срок службы.Продолжительность работы более 130 час.
4. Стабильная производительность
5. высокая скорость резания
6.Низкие затраты на воду и абразивность.
Спецификация
Обслуживание мы можем предложить вам | |
Быстрая реакция | Ваш запрос будет получен в течение 24 часов. |
Высокое качество | Хорошо обученных работников и более 15 лет опыта. |
Конкурентоспособная цена | Напрямую от фабрики, чтобы сэкономить ваши деньги. |
КороткиеВремя выполнения | Быть эффективным: 5-10 дней для образцов и 10-20 дней для количества заказов. |
Гибкость | Небольшие заказы приемлемы для быстрой доставки и помогут вам снизить стоимость акций. |
Oem и odm | Изготовление на заказ по вашим чертежам, образцам или дизайнам. |
Пожалуйста, выбирайте свободно из широкого ассортимента уже имеющихся в наличии
Закаленное стекло/керамика Режущие Инструменты Вольфрам твердосплавные водяные реактивные режущие насадки
Детальный дисплей:
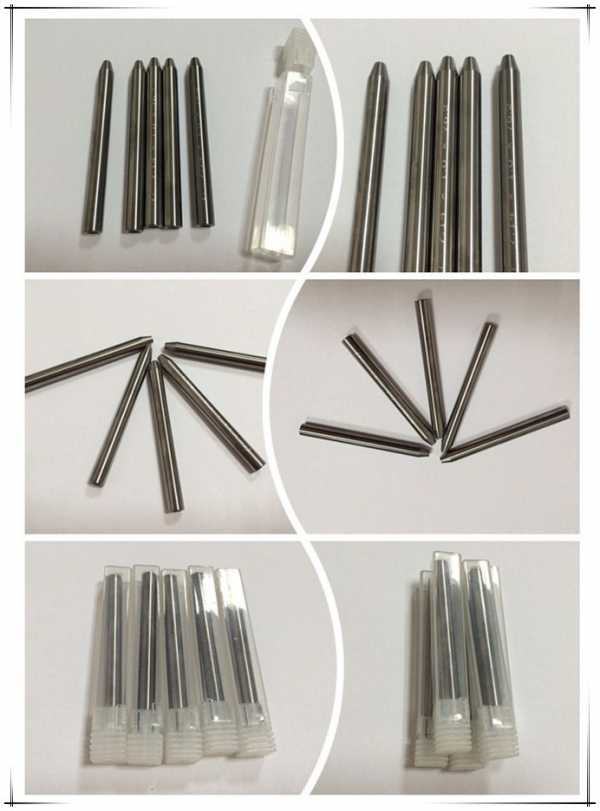
Информация о компании
Zhuzhou NewMetal materials Co., LtdЯвляется огнеупорным производителем, специализирующимся на сырьевом и глубоководном изделии вольфрама, молибденума, тантал, ниобий, рхенум и карбид вольфрама.
• Мы завоевали технологические трудности в сварке между карбидом из карбида вольфрама и нержавеющей стали -на основе и железной основе. Геометрическая толерантность сварных швов можно контролировать на уровне А.
• Полагаясь на институт по производству порошковой металлургии и инженерным материалам центрального Южного университета, мы создали научно-исследовательскую базу для обеспечения мощной технической поддержки продукции r & d. И у нас есть вся Производственная техника от смешивания до обработки, включая самую передовую холодную изостатическую машину, которая может изготовить самую широкую и самую длинную пластину.
• Наш 21 технический сотрудник, 10 послепродажного персонала и 120 работников обрабатывающей промышленности-это все, что у вас на службе.
Часто задаваемые вопросы
Вопрос: Вы торгуете компанией или производителем?
A: мы являемся фабрикой.
Вопрос: Как долго проходит ваше время доставки?
А: Вообще-то 5-10 дней, если товар есть в наличии. Или это 15-20 дней, если товара нет в наличии, оно в зависимости от количества.
Вопрос: Вы предоставляете образцы? Это бесплатно или лишнее?
А: Да, мы могли бы предложить образец бесплатно, но не оплатить стоимость доставки.
Вопрос: каковы ваши условия оплаты?
A: оплата <= 1000 USD, 100% в авансе. Оплата> = 1000 USD, 30% Т./т заранее, баланс перед кораблем.
Свяжитесь с нами
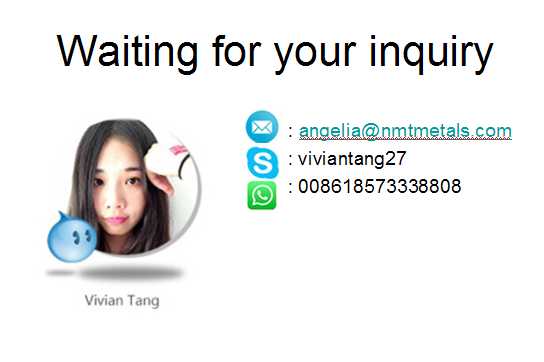
russian.alibaba.com