Большая Энциклопедия Нефти и Газа. Бурение глубоких отверстий
Бурение отверстий в земле. Процесс бурения отверстий под столбы
На глубине 410-660 километров под поверхностью Земли океан архейского периода. Подобные открытия были бы невозможны без методов сверхглубинного бурения, разработанных и применявшихся в Советском Союзе. Один из артефактов тех времен - Кольская сверхглубокая скважина (СГ-3), которая даже через 24 года с момента прекращения бурения остается глубочайшей в мире. Зачем ее пробурили и какие открытия она помогла совершить, рассказывает «Лента.ру».
Пионерами сверхглубокого бурения выступили американцы. Правда, на просторах океана: в пилотном проекте они задействовали судно Glomar Challenger, сконструированное как раз для этих целей. Тем временем в Советском Союзе активно разрабатывали соответствующую теоретическую базу.
В мае 1970 года на севере Мурманской области в 10 километрах от города Заполярного началось бурение Кольской сверхглубокой скважины. Как и полагалось, это приурочили к столетию со дня рождения Ленина. В отличие от других сверхглубоких скважин, СГ-3 бурили исключительно для научных целей и даже организовали специальную геологоразведочную экспедицию.
Место бурения выбрали уникальное: именно на Балтийском щите в районе Кольского полуострова на поверхность выходят древние породы. Возраст многих из них достигает трех миллиардов лет (самой нашей планете - 4,5 миллиарда лет). Кроме того, тут Печенга-Имандра-Варзугский рифтогенный прогиб - вдавленная в древние породы чашеподобная структура, происхождение которой объясняют глубинным разломом.
Ученым понадобилось четыре года, чтобы пробурить скважину на глубину 7263 метра. Пока ничего необычного не делалось: применялась та же установка, что и при добыче нефти с газом. Потом скважина простояла без дела целый год: установку модифицировали для турбинного бурения. После апгрейда удавалось бурить примерно по 60 метров в месяц.
Глубина в семь километров преподнесла сюрпризы: чередование твердых и не очень плотных пород. Участились аварии, а в стволе скважины возникло множество каверн. Бурение продолжалось до 1983 года, когда глубина СГ-3 достигла 12 километров. После этого ученые собрали большую конференцию и рассказали о своих успехах.
Однако из-за неаккуратного обращения с буром в шахте осталась секция длиной пять километров. Несколько месяцев ее пытались достать, но не преуспели. Было принято решение вновь начать бурение с глубины семь километров. В силу сложности операции бурили не только основной ствол, но и четыре дополнительных. На то, чтобы восстановить утраченные метры, ушло целых шесть лет: в 1990-м скважина достигла глубины 12262 метра, став самой глубокой в мире.
Спустя два года бурение было остановлено, впоследствии скважину законсервировали, а фактически - забросили.
Тем не менее на Кольской сверхглубокой скважине совершили немало открытий. Инженеры создали целую систему сверхглубокого бурения. Сложность заключалась не только в глубине, но и в высоких температурах (вплоть до 200 градусов Цельсия) из-за интенсивности работы буров.
Ученые не просто продвигались вглубь Земли, но и поднимали образцы пород и керны для анализа. Кстати, именно они изучали лунный грунт и выяснили, что по составу он почти полностью соответствует породам, извлеченным из Кольской скважины с глубины около трех километров.
На глубине свыше девяти километров вышли на залежи полезных ископаемых, в том числе и золота: в оливиновом слое его целых 78 граммов на тонну. И это не так мало - добычу золота считают возможной при 34 граммах на тонну. Приятным сюрпризом для ученых, а также для близлежащего комбината, стало обнаружение нового рудного горизонта из медно-никелев
kupildoma.ru
Сверление - глубокое отверстие - Большая Энциклопедия Нефти и Газа, статья, страница 1
Сверление - глубокое отверстие
Cтраница 1
Сверление глубоких отверстий ( длина отверстия больше пяти диаметров) производят на специальных горизонтально-сверлильных станках. При обработке глубоких отверстий спиральными сверлами происходит увод сверла и разбивание отверстия: затрудняются подвод смазочно-охлаждающей жидкости и отвод стружки. Поэтому для сверления глубоких отверстий применяют сверла специальной конструкции. Смазочно-охлаждающая жидкость подается в зону резания и вымывает стружку через внутренний канал сверла. [2]
Сверление глубоких отверстий, глубина которых больше трех диаметров, обычными спиральными сверлами связано с рядом затруднений; ухудшается отвод стружки и тепла, уменьшается жесткость сверла. Наличие поперечного лезвия даже при идеальной заточке сверла приводит к отклонению сверла оси заготовки. [3]
Сверление глубоких отверстий при L I2d производят удлиненными спиральными сверлами, такое сверление, выполняемое на сверлильных станках, не исключает увода сверла и нарушения концентричности, поэтому может быть применено только с последующей обработкой по наружному диаметру ( для деталей типа втулок) или при сверлении неответственных отверстий. [4]
Сверление глубоких отверстий связано с периодическим выведением сверла из изделия для извлечения стружки. Количество вы-аодов колеблется от двух-трех до десяти и больше. Такой сравнительно сложный цикл ( рис. 11 - 3 г) производится автоматически и по окончании обработки изделия силовые головки с инструментами отводятся в исходное положение. [6]
Сверление глубоких отверстий ( длина отверстия больше пяти диаметров) выполняют на специальных горизонтально-сверлильных станках. При обработке глубоких отверстий спиральными сверлами происходят увод сверла и разбивание отверстия: затрудняются подвод смазоч-но-охлаждающей жидкости и отвод стружки. [8]
Сверление глубоких отверстий ( при отношении - j 12) производят специальными сверлами, которые называются пушечными сверлами ( фиг. Эти сверла имеют одну режущую грань и одну канавку для отвода стружки, обычно прямую, а не спиральную. Перед тем как сверлить деталь пушечным сверлом, в ней необходимо расточить неглубокое отверстие, равное диаметру пушечного сверла; это отверстие служит направлением при сверлении. [9]
Сверление глубоких отверстий производят при вращении обрабатываемой заготовки. При сверлении тяжелых неотбалансированных деталей применяют встречное вращение детали и инструмента. [10]
Сверление глубоких отверстий для смазки шеек коленчатого вала выполняется посредством специальных удлиненных сверл. Сверло шлифуется на конус с уменьшением диаметра к хвостовой части на 0 08 - 0 12 мм. Перемычка сверла утолщается к хвостовой части с 2 8 до 4 2 - 4 6 мм. [11]
Более точное сверление глубоких отверстий с получением прямолинейной оси производят ружейными или пушечными сверлами, а при обработке больших диаметров отверстий - расточными блоками. [12]
Для сверления глубоких отверстий могут применяться также насадные головки одностороннего резания с внутренним отводом стружки, оснащенные пластинками твердого сплава. [13]
Для сверления глубоких отверстий от 100 до 3000 мм применяется кислородное копье ( фиг. [14]
Для сверления глубоких отверстий необходимо обеспечить как подведение струи охлаждающей жидкости к лезвию, , так и отвод ее вместе с получающимися стружками. Конструкция борштанги для глубокого сверления изображена на фиг. При вырезании пластинок из полосы необходимо выбирать их положение по отношению к направлению вальцевания стальной полосы согласно фиг. Для сверления отверстий с плоским дном применяют центровое С. [15]
Страницы: 1 2 3 4 5
www.ngpedia.ru
Особенности сверления глубоких отверстий - Токарное дело
Особенности сверления глубоких отверстийКатегория:
Токарное дело
Глубокими называются отверстия, длина которых превышает диаметр в пять и более раз. Глубокими отверстиями являются, например, сквозное осевое отверстие в шпинделе токарного станка, отверстие пиноли задней бабки, осевые отверстия в прогреваемых прокатных валках и др.
Часто к глубоким отверстиям предъявляются высокие требования по прямолинейности оси, но точности формы и размеров. При глубоком сверлении сверлом обычной конструкции неизбежен «увод» сверла в сторону из-за разности радиальных усилий на режущих кромках и это может привести к «разбивке» отверстия (увеличению диаметра), хотя ось отверстия остается прямой.
Поэтому для сверления глубоких отверстий применяют специальные — «пушечные» сверла с прямой стружечной канавкой. Сверло хорошо направляется в отверстии благодаря большой поверхности соприкосновения спинки сверла с обработанной поверхностью отверстия. Охлаждающая жидкость от насоса поступает к режущей кромке через сквозной канал в сверле, охлаждает режущую кромку сверла и принудительно удаляет стружку.
1. ДЕРЖАТЕЛЬ ДЛЯ СТЕРЖНЕВЫХ ИН СТРУМЕНТОВ (СТАНОК 16К20): 1 — держатель. 2 — стопорный винт втулки. 3 — втулка с инструментальным конусным отверстием. 4 хвостовик инструмента. 5 — резцедержатель. 6 — винт резцедержателя
2. СВЕРЛА ДЛЯ ГЛУБОКОГО СВЕРЛЕНИЯ: а —однокромочное («пушечное»). б — шисконое. в четырех ленточное
3. ШТЫКОВАЯ ОПРАВКА ДЛЯ ГЛУБОКО ГО СВЕРЛЕНИЯ:
Применяют также шнековые и че-тырехленточные сверла, работающие с минимальным «уводом», благодаря большой поверхности соприкосновения ленточек со стенками отверстия.
При сверлении глубоких отверстий обычными сверлами периодически извлекают сверло из отверстия для очистки от стружки и охлаждения. С целью сокращения времени на ввод и вывод сверла применяют оправку со штыковым затвором.
Читать далее:
Контроль отверстий
Статьи по теме:
pereosnastka.ru
Сверление - глубокое отверстие - малый диаметр
Сверление - глубокое отверстие - малый диаметр
Cтраница 1
Сверление глубоких отверстий малого диаметра требует частого вывода сверла из отверстия. Для этой цели имеется специальное приспособление 13, которое устанавливается в отверстии переднего кронштейна станины станка. Приспособление 13 приводится в действие от шкива, установленного на валу насоса. Число выводов определяется профилем колокольного кулачка, установленного в приспособлении. Во время выхода сверла из отверстия оно смазывается и охлаждается маслом, которое в то же время смывает стружку. [1]
Сверление глубоких отверстий малого диаметра для улучшения ус - ловий охлаждения сверла и удаления стружки производить за несколько вводов сверла. При первом вводе рекомендуется сверлить на глубину трех диаметров, при втором на глубину двух и при третьем на глубину одного диаметра обрабатываемого отверстия. [2]
Ори сверлении глубоких отверстий малых диаметров обработку изделия ведут с частым выводом сверла из отверстия. Для многократного вывода сверла 13 имеется специальное приспособление, которое устанавливается в отверстие переднего кронштейна станины. [3]
При сверлении точных глубоких отверстий сравнительно малого диаметра применяются так называемые ружейные сверла ( фиг. Вершина такого сверла смещена от его оси на 1 / 4 его диаметра. [4]
Кроме того, оно используется для сверления глубоких отверстий малого диаметра. [5]
Ниже приведены результаты исследований, подтверждающих возможность управления уводом при сверлении глубоких отверстий малых диаметров такими способами. [7]
Желательно перед сверлением производить зацентровку, но обязательной она является при сверлении глубоких отверстий малого диаметра, а также в случае тяжелой поперечной нагрузки, так как центровое сверло большого диаметра служит как бы поддерживающим центром. При сверлении сквозных отверстий малой длины величину хода сверла несколько увеличивают, чтобы получить зацентровку на следующей детали. Внутренние выточки выполняются с дополнительным поперечным перемещением резца. [8]
Во всех случаях желательно перед сверлением производить зацентровку, но обязательной она является при сверлении сравнительно глубоких отверстий малого диаметра, а также в случае тяжелой поперечной нагрузки, так как центровое сверло большого диаметра служит как бы поддерживающим центром. При сверлении отверстий большого диаметра и малой длины величину хода сверла несколько увеличивают с тем, чтобы получить зацентровку на следующем изделии. Внутренние выточки выполняются с дополнительным поперечным перемещением резца. [9]
Из изложенного следует, что конструкция сверла должна находиться в строгом соответствии с режимом работы, рсобенно при сверлении глубоких отверстий малого диаметра. [10]
Примененное на автоматах типа 1А10П и 1П12 двухшпин-дельное качающееся сверлильное устройство предназначено для центрования, сверления или рассверливания отверстий, а также для сверления глубоких отверстий малого диаметра. [11]
Из зависимости (9.7) следует, что охлаждающая способность СОЖ резко возрастает при малых подачах инструмента и высоких скоростях протекания СОЖ. Именно эти условия характерны для сверления глубоких отверстий малого диаметра. Снижение температуры в зоне стружкообразования приводит к увеличению нароста на режущей кромке, а также увеличению фактического переднего угла, что вызывает уменьшение усадки стружки и, как следствие, также уменьшение сил, затрачиваемых на стружко-образование. [12]
Сверление отверстий и зацентровка производятся с револьверной головки. Для получения соответствующих скоростей резания и подач при сверлении глубоких отверстий малого диаметра применяется приспособление для быстрого сверления. [13]
Сверление отверстий и зацентровку выполняют с револьверной головки. Для получения соответствующих скоростей резания и подач при сверлении глубоких отверстий малого диаметра применяют приспособления для быстрого сверления. [14]
Сталь Р6М5К5 имеет пониженное содержание углерода ( см. табл. 50) и меньшие теплостойкость ( до 630 - 635 С) и вторичную твердость ( HRC 65), но большую прочность. Применяют преимущест: венно для резания с обдирочными режимами более мягких сталей, а также для сверления глубоких отверстий малых диаметров. [15]
Страницы: 1 2
www.ngpedia.ru
Получение отверстий большой длины - Глубокое сверление
Получение отверстий большой длиныКатегория:
Глубокое сверление
Получение отверстий большой длиныВо всех областях машино- и приборостроения применяются детали, имеющие глубокие отверстия. Массовыми потребителями деталей с глубокими отверстиями являются общее и специальное машиностроение, судостроение, авиастроение, нефтяное и химическое машиностроение, приборостроение и др.
Детали с глубокими отверстиями встречаются самой разнообразной формы. Производятся они различными методами, с различной точностью и чистотой обработки, из различных материалов и имеют большой диапазон диаметров и длин.
Большинство металлических и неметаллических деталей, имеющих глубокие отверстия, изготовляется без применения глубокого сверления. Чаще всего глубокие отверстия выполняются металлургическими методами: методами литья, гибкой или завивкой листового материала с последующей сваркой в трубы, различными методами прокатки, волочением, экструзией и др.
На рис. 1 в качестве примера показан корпус стеклоочистителя трактора К-700, имеющий два глубоких отверстия. Корпус стеклоочистителя изготовлен литьем под давлением из сплава марки ЦАМ4-1. Для получения глубоких отверстий малых диаметров и глубоких отверстий в труднообрабатываемых материалах в последнее время успешно применяют физико-химические процессы: электроэрозионный, анодномеханический, ультразвуковой и др.
На рис. 2 приведены три полых цилиндра, имеющих глубокие отверстия диаметром 20-80 мкм. Отверстия в них получены электроэрозионным методом. Материал цилиндров — твердый сплав марки ВК20.
В отличие от сверления, многие из указанных методов не требуют для изготовления отверстий относительного вращения заготовки и инструмента, а поэтому позволяют довольно просто получать цилиндрические отверстия не только круглого сечения, но и других профилей.
Применение сверления вместо других упомянутых выше методов образования глубоких отверстий производится либо тогда, когда оно является наиболее производительным, либо тогда, когда сверление обеспечивает наиболее полные требования точности или чистоты обработки. В ряде случаев глубокое сверление, особенно скоростное, превосходит по производительности и качеству выполнения операции все другие существующие технологические процессы.
Самым распространенным методом обычного (неглубокого) сверления является сверление так называемыми спиральными сверлами.
Однако этот метод успешно применяется только при глубине сверления, равной не более 3-5 диаметрам сверла. При сверлении же более глубоких отверстий приходится применять прерывистый процесс, так как необходимо часто выводить спиральное сверло из отверстия для очистки от стружки, смазки и охлаждения. Подобная работа, даже если она производится автоматически, резко снижает производительность сверления.
Важным фактором, от которого зависит непрерывность протекания процесса сверления, является отвод образующейся стружки.
Рис. 1. Корпус стеклоочистителя трактора К-700
Рис. 2. Твердосплавные цилиндры с глубокими отверстиями 0 20-80 мкм
Рис. 3. Спиральное сверло с каналами для подвода охлаждающей жидкости при глубоком сверлении
Рис. 4. Сверло конструкции СКБ-8 1 — 2 — глубокие отверстия и 3,1 мм, длиной 70 мм
Рис. 5. Схемы отвода стружки из зоны резания при глубоком сверлении: а — наружный отвод стружки; б — внутренний отвод стружки: 1 — заготовка; 2 — стебель; 3 — стеблевой суппорт; 4 — насос; 5 — резервуар для охлаждающей жидкости; 6 — стружкоприемиик; 7 — люнет; 8 — сверло; 9 — патрон; 10 — маслоприемник
Чем больше глубина сверления, тем затруднительнее отвод стружки из зоны резания. Спиральные сверла не обеспечивают надежного стружкоотвода. Имеющиеся конструкции спиральных сверл (рис. 3) с внутренними канавками для подвода к режущим кромкам смазочно-охлаждающей жидкости весьма сложны в изготовлении и не получили широкого распространения в промышленности.
В настоящее время некоторое распространение получили сверла конструкции СКБ-8 (рис. 4), отличающиеся от обычных стандартных сверл более крутыми канавками для отвода стружки. По своему виду данное сверло напоминает бурав для сверления древесины. Стружкоотвод у сверл подобного типа лучше, чем у обычных спиральных сверл, но не гарантирует от возможных заклиниваний удаляемой стружки.
На практике глубокие отверстия сверлятся обычно непрерывно с принудительным либо наружным, либо внутренним отводом стружки. Принудительный отвод стружки осуществляется обычно жидкостью, подводимой в зону резания под давлением. Весьма редко вместо жидкости применяют сжатый воздух. Для создания циркуляции жидкости применяется специальная оснастка и оборудование.
На рис. 5 показаны упрощенные схемы обоих методов глубокого сверления.
При наружном отводе стружки (рис. 5, а) жидкость поступает от насоса через внутреннюю полость стебля и сверла в зону резания и вместе со стружкой отводится через зазоры между сверлом со стеблем и поверхностью образующегося глубокого отверстия в стружко-приемник. Стружкоприемник задерживает стружку, а жидкость стекает в отстойник резервуара. В резервуаре (баке) жидкость очищается от механических примесей, охлаждается и вновь насосом направляется через трубопровод (гибкий шланг) и стебель сверла в зону резания.
При внутреннем отводе стружки (рис. 5, б) жидкость направляется насосом в специальное устройство — маслоприемник. Из маслоприемника жидкость поступает в зону резания через зазоры между наружной поверхностью стебля со сверлом и образующейся поверхностью глубокого отверстия. Затем стружка вместе с жидкостью вымывается в стружкоприемник через внутреннюю полость сверла и стебля. Далее путь жидкости до насоса аналогичен описанному выше.
Таким образом, современный процесс глубокого сверленияв общих чертах характеризуется как непрерывный процесс образования в сплошном материале заготовки отверстий с относительной длиной более 3-5 диаметров сверления с применением специальных сверл, оснастки и оборудования, обеспечивающих принудительный отвод стружки из зоны резания.
При глубоком сверлении различают сплошное и кольцевое сверление.
При сплошном сверлении (рис. 6, а) весь материал, расположенный в объеме будущего отверстия, измельчается в стружку. При кольцевом сверлении, которое иногда называют трепанацией, в стружку переводится только кольцевая полость (рис. 6, б). В центре образующегося отверстия остается стержень (или керн), используемый иногда в качестве заготовки для различных деталей.
Если сверление сквозное, то высверливаемый стержень.
Рис. 6. Разновидности глубокого сверления: а — сплошное сверление; б — кольцевое сверление
Рис. 7. Поковка и.высверленный стержень при двустороннем глубоком сверлении
Глубокое сверление занимает особое место среди операций, применяемых при обработке деталей, имеющих большую относительную длину. Специфичность этой операции заключается как в том, что инструмент должен прокладывать себе путь в сплошном материале, не имея заранее подготовленной опоры и жесткого направления, так и в том, что от качества проведения глубокого сверления существенно зависит структура последующего технологического процесса. Типичным для глубокого сверления также является невозможность непосредственного наблюдения за ходом процесса и трудность выполнения данной операции на универсальном оборудовании без его основательной подготовки.
полностью отделяется от заготовки в конце прохода. Если же сверление глухое, то его необходимо удалять специальными приемами.
В большинстве случаев при необходимости сверления глухих отверстий предпочитают применять только сплошное сверление. Когда же необходимо просверлить сквозное отверстие очень большой относительной длины или сверлить детали из труднообрабатываемых материалов, применяют двустороннее сверление.
На рис. 7 показана крупная стальная поковка, предназначенная для двустороннего кольцевого сверления, а слева от нее расположен высверленный стержень, полученный при сверлении подобной заготовки. На торце заготовки показана полость, превращаемая при кольцевом сверлении в стружку.
Запроектированный технологический процесс глубокого сверления обычно оценивается по трем показателям:1) по производительности;2) по соответствию качества выполнения отверстия техническим требованиям на операцию;3) по общей стоимости изготовления детали с глубоким отверстием.
Перечисленные дефекты, кроме эллиптичности, являются следствием уводов сверла от заданного направления. Под уводом оси отверстия в данном сечении или на торцах заготовки после сверления (растачивания) понимают отклонение оси полученного отверстия от оси отверстия, намеченного чертежом.
На рис. 8 показаны детали с правильно просверленным отверстием (рис. 8, а) и отверстиями с дефектами, полученными при глубоком сверлении (рис. 8, 6-8, и).
При выполнении любой технологической операции могут быть получены дефекты, в ряде случаев приводящие к неисправимому браку. Дефекты, которые могут сопровождать операцию глубокого сверления, весьма разнообразны и им поэтому посвящен следующий параграф данной главы.
От качества сверления, а следовательно, и от назначения припусков на последующие операции зависит дальнейший процесс обработки не только отверстия, но и всей детали в целом. Поэтому стоимость выполнения операции глубокого сверления необходимо рассматривать не изолированно, а с учетом стоимости всей обработки детали.
Читать далее:
Дефекты обработки глубоких отверстий
Статьи по теме:
pereosnastka.ru
Глубокое сверление, станки для глубокого сверления, инструменты для глубокого сверления, операция глубокого сверления, Кольцевые сверла, трепанирование, ружейные сверла, эжекторная система, STS
Главная страница » Глубокое сверление
Глубокое сверление
Традиционно глубоким отверстием считается отверстие, у которого соотношение его длины к диаметру превышает 5, т.е. L/D>5. На обычных станках и обрабатывающих центрах возможно сверление подобных отверстий, но для этого необходимо применять различные дополнительные меры, задавать длинному и не жёсткому сверлу направление, и так обеспечивать жёсткость системы. Для этого возможно применение кондукторных втулок, предварительное сверление пилотного отверстия и т.д.
Но когда длина отверстия превышает диаметр в 10 раз, т.е. L/D>10, его необходимо обрабатывать методом глубокого сверления на специальном оборудовании и специальными сверлами.
Это достаточно специфическая операция, но имеющая широкое применение в различных отраслях, особенно в таких, как нефтегазовой, аэрокосмической, металлургической промышленности.
Основными сложностями глубокого сверления являются увод сверла, непрямолинейность оси, получаемого отверстия, разностенность, некруглость отверстия, сложность вывода стружки, и доставки СОЖ в зону резания и т.д.
В глубоком сверлении необходимо обеспечить дробление стружки, чтобы она не пакетировалась и не портила обрабатываемую поверхность.
Инструменты для глубокого сверления
Для глубокого сверления применяются специальные сверла, выделяют 3 типа таких сверл или систем сверления. У данных систем существенно отличается организация подвода СОЖ.
1. Эжекторная система (двуштанговая)
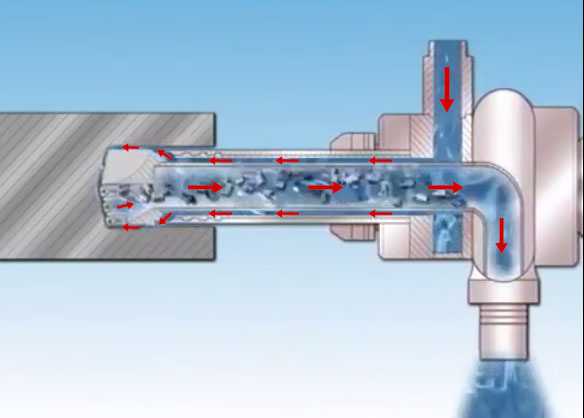
В этой системе используется две штанги одна внутренняя и одна внешняя, т.е. труба в трубе, на конце эти две штанги присоединены к сверлильной головке. СОЖ подается между двумя штангами и движется она внутри корпуса сверла. Вымывание стружки происходит через отверстие внутренней штанги.
В такой системе требуется меньшее давление СОЖ, чем в STS системе. Эжекторная система может применяться на универсальных станках и в основном применяется для средних партий.
2. Система STS (одноштанговая)
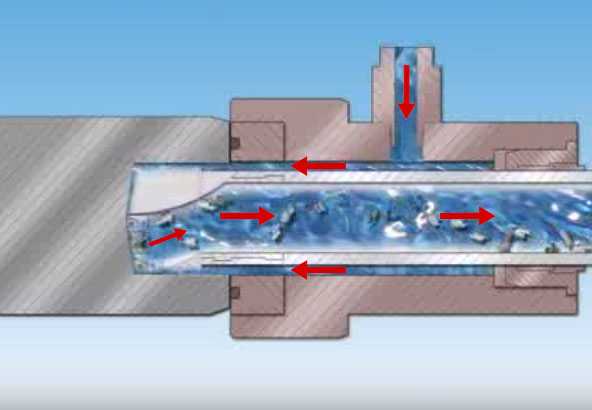
В данной системе применяется одна штанга, а СОЖ поступает через устройство подачи СОЖ, плотно прилегающего через уплотнение к торцу заготовки. СОЖ поступает под высоким давлением между штангой и заготовкой. Вымывание стружки осуществляется также через внутреннее отверстие штанги, как и в системе эжекторного сверления.
В силу высокого давления СОЖ, обеспечивается лучшее удаление стружки, и в этом плане данная система надежнее эжекторной, и она более лучше справляется с обработкой материалов с плохим стружкодроблением, т.е. низкоуглеродистых и нержавеющих сталей, но STS система требует специального оборудования. Поэтому такая система наиболее эффективно подходит для крупносерийного производства.
Это первый выбор для высокопроизводительной обработки и крупносерийного производства
3. Система сверления ружейными сверлами
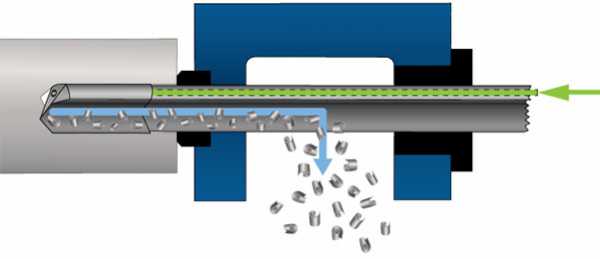
Ружейные (или пушечные) сверла имеют внутренний подвод СОЖ через отверстие в сверле, а вымывание стружки и удаление СОЖ происходит через наружную V-образную стружечную канавку в сверле.
Ружейные сверла могут применяться на обрабатывающих центрах, необходимым условием является наличие достаточного давления внутренней подачи СОЖ.
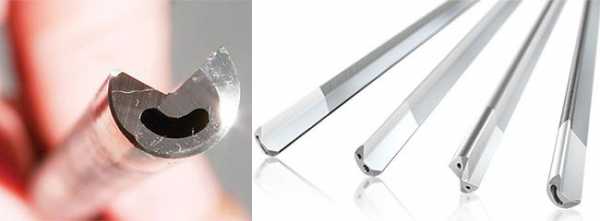
Кольцевые сверла, трепанирование
Для обработки глубоких отверстий, имеющих диаметр отверстия больше 80 мм используют кольцевые сверла, сверление такими сверлами еще называют трепанированием, здесь в стружку переводится только кольцевая полость, а в центре остается стержень. Данный тип сверления более прогрессивный, в будущем он может вытеснять сплошное сверление даже при меньших диаметрах отверстий.
Производительность глубокого сверления
Глубокое сверление, особенно скоростное, в большинстве случаев превосходит по производительности и качеству все другие технологические способы обработки отверстий.
Если взять даже простые спиральные сверла, которые успешно применяются только для неглубоких отверстий (L/DСтанки для глубокого сверления
Существуют различные компоновки станков для глубокого сверления, преобладающая часть создана для обработки отверстий в цилиндрических заготовках, которым придается вращение, а инструмент перемещается с заданной подачей, т.е. по принципу токарного типа, это обеспечивает высокую точность и производительность обработки. Но возможно обрабатывать только отверстия соосные оси заготовки.
Существуют компоновки, где вращение передается и заготовке в противоположном направлении сверла, и самому сверлу, этот вариант достигает лучших показателей точности и производительности.
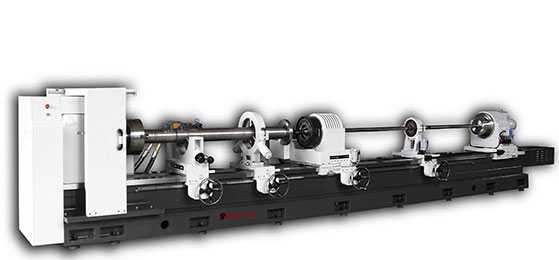
Также применяют многошпиндельные станки глубокого сверления.
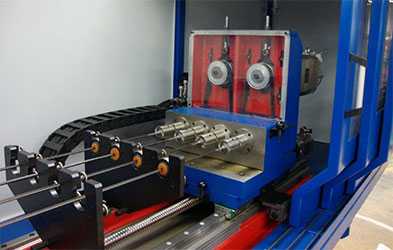
Станки могут быть как одно, так и двухсторонними, т.е. для сверления заготовки с одной или с нескольких сторон.
Для обработки тяжелых заготовок или сверления эксцентричных отверстий используют станки, где вращение задается только инструменту.
Станки глубокого сверления выполняются как горизонтального типа, так и вертикального. Хотя вертикальный тип может сверлить заготовки сравнительно небольшой длинны имеет некоторые преимущества. Так инструмент в вертикальной компоновке не подвергается изгибающим усилиям от собственного веса.
Существуют станки глубокого сверления вертлюжного типа, здесь заготовка устанавливается в полый шпиндель называемого вертлюг, в силу того, что его нельзя сильно вращать, применение в основном получил в деталях, которым нельзя задавать большие крутящие моменты. Принцип схож со станками токарного типа.
Станки для глубокого сверления могут иметь самые различные компоновки, они относятся к группе специальных станков. Также они могут выполнять и операции растачивания отверстия.
Станки занимают большое пространство в цехе, требуют особого внимания к сбору и охлаждению СОЖ, обеспечению высокого давления СОЖ, сбору стружки и т.д. Необходимо учитывать, что в случае неисправности такой станок трудно заменить каким-либо другим, надо быть предусмотрительным и принять меры по этому поводу заранее, возможно приобретение второго подобного станка, заручиться гарантийной поддержкой производителя или поставщика станка, а также проведение каких-либо других мероприятий.
Заключение
Операция глубокого сверления проводится на больших и довольно дорогостоящих заготовках, ее качественное исполнение и стабильность получения результатов имеет огромное значение для различных предприятий. Выбор и внедрение такого станка важный и необходимый момент для многих предприятий.
Главными критериями инвестирования в такой станок являются множество факторов — это конечно же срок окупаемости, повышение производительности и качества продукции, расширение производственных возможностей, повышение статуса и авторитета предприятия, увеличение экономической эффективности производства и, как следствие, увеличение прибыли.
Похожие записи:
vys-tech.ru
Глубокое сверление отверстий
Глубокие отверстия малого диаметра с соотношением - нерационально выполнять спиральными сверлами, т.к. наряду с ранее перечисленными недостатками затруднен выход стружки. При глубоком сверлении необходимо сверло периодически извлекать (для удаления стружки), поэтому для глубокого отверстия применяются сверла одностороннего резания: пушечное, ружейное и кольцевое сверло. Глубокое сверление выполняют при вращающейся детали и неподвижном инструменте, что позволяет повысить точность обработки, т.к. отсутствует биение инструмента в шпинделе станка.
Пушечное сверло (рис. 4.5)
Рис 4.5 Пушечное сверло
Сверло имеет одну рабочую режущую кромку и охватывает дугу отверстия в 180°. Длина рабочей режущей кромки в 5-10 раз больше чем диаметр, при этом задний конус у этой поверхности 0,03-0,05. В теле сверла выполнено отверстие для подачи жидкости, которая охлаждает сверло и вымывает стружку. Р = 20-50 атмосфер.
Ружейное сверло (рис 4.6)
Рис 4.6 Ружейное сверло
В центре сверла выполнено круглое или серповидное отверстие, через которое подается жидкость под давлением 25-40 атмосфер, для вымывания стружки, а также охлаждения зоны резания и инструмента. Сверло охватывает отверстие по дуге 250-260°.
Недостаток:
- высверливание всего массива металла.
Кольцевое сверло (Рис 4.7)
Рис 4.7 Кольцевое сверло
1 – пластинки резцов;2 – трубчатый корпус; 3 – деревянные или бронзовые бруски для направления.
Применяется для увеличения производительности, центральный стержень остается не высверленным. В зазор между наружной поверхностью высверливаемого стержня и внутренней стенкой корпуса подается жидкость (зазор А), а в зазор Б вымывается стружка. Подрезка центрального стержня производиться головкой для трепанирования.
Преимущества глубокого сверления:
- относительно высокая точность Н7-Н8, т.к. нет биения инструмента в шпинделе;
- удаление стружки жидкостью.
Недостаток:
- режимы резания на 20-30% ниже, чем режимы при сверлении спиральными сверлами.
Похожие статьи:
poznayka.org