ТИПЫ И ХАРАКТЕРИСТИКИ СВАРОЧНОГО ПРОИЗВОДСТВА. Сварочный цех описание
ТИПЫ И ХАРАКТЕРИСТИКИ СВАРОЧНОГО ПРОИЗВОДСТВА
ОСНОВЫ ПРОЕКТИРОВАНИЯ СВАРОЧНЫХ ЦЕХОВ
В разработке проектов сварочного производства большое значение имеет определение наиболее целесообразных форм организации производственных процессов для выпуска заданной продукции.
В зависимости от числа различных заданных видов изделий н повторяемости их изготовления может быть установлена принадлежность проектируемого цеха к определенному типу произ - иодства (единичное, мелкосерийное, серийное, крупносерийное, массовое). Однако нередко в одном цехе предусматривают организацию производств разных типов. Особенно часто в одном цехе совмещают единичное и мелкосерийное производство. Поэтому н практике проектирования принято рассматривать четыре типа производства: 1) единичное и мелкосерийное, 2 серийное, 3) крупносерийное и 4) массовое.
Строгих границ между различными типами серийного производства не существует. Ориентировочные признаки, характеризующие отдельные типы серийного производства, представлены в габл. 1. Краткие организационно-технические характеристики перечисленных выше типов производства сводятся к следующему.
Единичное и мелкосерийное производство отличается большой и неустойчивой номенклатурой выпускаемых изделий. В производственном процессе применяют универсальное оборудование и переналаживаемую оснастку упрощенной конструкции с ручной подачей исходного металла и штучных заготовок. Отсут - ( шует закрепление заготовок и деталей за оборудованием. В основном используют общецеховой транспорт.
В серийном производстве номенклатура выпускаемых изделий ограниченная и достаточно устойчивая. Изготовление изделий производят периодически повторяющимися сериями на специализированных участках, на переменно-поточных линиях с преимущественным применением универсального оборудования. Характерно применение простой и комбинированной оснастки с ручной или механизированной'подачей листов, прутков, полос или штучных заготовок. Используют общецеховой и напольный транспорт.
В крупносерийном производстве номенклатура выпускаемых изделий весьма ограниченная и устойчивая. Изделия производят
Таблица 1 Характеристики программы годового выпуска сварных изделий для различных типов серийного производства (по материалам норм технологического проектирования)
|
периодически повторяющимися крупными сериями на специализированных участках, механизированных переменно-поточных линиях. Применяют специализированное оборудование, комплексно-механизированные поточные линии раскроя и специальное нестандартное оборудование. Характерно применение специальных приспособлений с механизированной подачей листового, сортового и профильного проката. Широко используют подвесной и напольный транспорт.
Массовое производство отличается весьма устойчивой номенклатурой выпуска продукции, включающей один тип (редко два или три типа) изделий в большом количестве. Изделия производят с постоянным ритмом потока на комплексно-механизированных и автоматических поточных линиях с применением специализированного межоперационного транспорта.
Из указанных выше характеристик следует: чем ближе проектируемое производство к типу массового, тем быстрее происходит
и нем продвижение изготовляемых изделий, тем больше и равномернее загрузка производственного оборудования, тем целесообразнее применение механизированных подъемно-транспортных устройств для передвижения сборочных единиц изготовляемых п іделий и использование высокопроизводительных механизированных и автоматизированных способов сборки и сварки продукции, требующих для своего осуществления сложного и дорогого специализированного оборудования и приспособлений, и, наконец, тем целесообразнее весьма подробная разработка технологического процесса производства.
В зависимости от типа производства в нем преобладает либо технологический (единичное и мелкосерийное производство), либо предметный (массовое и крупносерийное производство) принцип формирования цехов. В первом случае в составе машиностроительного завода организуют самостоятельный сборочно- сварочный цех или отделение. Во втором случае для изготовления заданных изделий на заводе организуют общий производственный поток, представляющий собой последовательное выполнение операций различной технологической специализации. В соответствующих местах этого производственного потока по ходу процесса изготовления изделий включают сборочно-сварочные липни, участки или отдельные рабочие места. При этом все этапы производственного процесса изготовления изделий располагают в цехах, сформированных соответственно по предметному принципу (например, в тележечном, рамном, кузовном, каркасном цехе и т. п.). В производствах серийного типа преобладание предметного принципа построения цехов возможно лишь при ниточных методах изготовления изделий (см. п. 19).
Дополнительной характеристикой цехов, изготовляющих сварные изделия, служит их состав по числу основных производственных отделений. К таким отделениям цеха относят заготовительное п сборочно-сварочное. В заготовительном отделении выполняют обработку исходного металла и изготовление из него деталей заданных изделий. В сборочно-сварочном отделении производят сборку готовых деталей и сварку их с целью получения заданных п іделий. В случаях производства достаточно сложных изделий сборочно-сварочное отделение подразделяют на два: отделение узловой сборки-сварки и отделение общей сборки-сварки. В первом из них выполняют сборку готовых деталей и сварку их с целью получения отдельных частей (технологических сборочных единиц) шданных изделий, а во втором — общую сборку изготовленных сОорочных единиц и сварку их для получения выпускаемых изделии в целом (в сборе).
При достаточно большом количестве работ в заготовительном отделении, изготовляющем детали для различных цехов завода, іпкое отделение выделяется в самостоятельный заготовительный цех. Тогда проектируемый цех имеет в своем составе только сбо- рпчпо-сварочные отделения либо участки, линии и отдельные рабочие места в различных (предметных) отделениях цеха. Обособление заготовительных работ от сборочно-сварочных предусматривают также при проектировании специализированных по технологическим признакам производств типа «центрорез» и «центросвар».
Расчетные коэффициенты и характеристики для автоматических сборочно-сварочных линий пока еще не определены. Поэтому помещенные ниже (разработанные А. П. Владзиевским) коэффициенты и характеристики, относящиеся к автоматическим линиям для механической обработки, могут …
На линии из отдельных листовых заготовок собирают и сваривают полотнища, которые тут же, на линии, сворачиваются в транспортабельные рулоны. Линия обеспечивает изготовление полотнищ толщиной 4—16 мм и' ширииой 12 ООО—18 …
Схема технологического процесса сборки и сварки кузова шахтной вагонетки (см. рис. 2) приведена ранее (см. табл. 6 и рис. 3). Работа поточной линии (рис. 92) с применением комплексной механизации производится …
msd.com.ua
Характеристика цеха и сварочного участка — дипломная работа
Освещение– люминесцентное,накладные светильники
Вентиляция- естественная,принудительная:зонт вытяжной
Отопление– автономное,электрические настенные панели
Внутренние помещения:стены, потолок– оцинкованный металлический лист, пол – рифленый металлический лист
Окна– в деревянной раме
наружная дверь – металлическая с замком и ключами
степень огнестойкости– III
Теплостойкость здания: +18 град С при внешней температуре–45 град С.
Сварочный цех представляет собой прямоугольное помещение площадью 54 м2с тремя сварочными кабинами, в каждой из которых находится специальный стол, табурет,сварочный преобразователь,электрододержатель,горелка. Преобразователь состоит из генератора постоянного тока и электродвигателя. Он соединен с электрододержателем посредством сварочных проводов (преобразователь является источником повышенного напряжения, электромагнитного поля, ультразвука.)Вентиляция осуществляется с помощью вытяжных зонтов, трех местных и одного общего. Во входной части цеха располагаются вешалки и обеденный стол.
Заготовки для сварки поставляются из других цехов на специальных тележках. Для сварки алюминиевых радиусных колен используем ручную дуговую сварку металлическим электродом с подогревом изделия. При использовании ручной сварки на рабочем месте уровень шума не превышает допустимых норм.
Прежде, чем приступить к сварке алюминия, сварщик должен знать особенности материала и технологию сварки.
Чистый алюминий проводит электрический ток в четыре раза лучше, чем сталь, поэтому процесс его сварки имеет свои технологические особенности. Способность проводить тепло у алюминия также значительно выше, чем у стали. Поэтому при работе с алюминием опасность поражения электрическим током и опасность получения ожогов от нагретой поверхности материала возрастает. То, что алюминий лучше проводит тепло, делает нежелательным увеличение скорости сварки- уменьшается глубина провара. Для кристаллизации сварочной ванны требуется меньше времени, поэтому происходит неполное газовыделение, что может привести к образованию пор в сварном шве. Чтобы избежать этого, необходимо устанавливать большее значение силы сварочного тока, чем при сварке стали; предварительно нагреть свариваемые детали, и использовать инертный защитный газ, желательно гелий. В начале сварки возможно уменьшение прочности сварного шва из-за отсутствия полного провара по причине недостаточного прогрева кромок свариваемых деталей.
Для ручной дуговой сварки технического алюминия применяются отечественные электроды ОЗА-1и ОЗАНА-1 В этих электродах в обмазке находятся хлоридные и фторидные соли, разрушающие оксидную пленку и способствующие устойчивому горению дуги. С другой стороны, при высоких температурах идет окисление и выделение ионов хлора и фтора, что является негативной стороной этих добавок, т.к они могут вызвать профессиональные заболевания.
Работа сварщика начинается с зачистки кромки свариваемого изделия и прилегающая к ним зон (20-30 мм) от ржавчины, шлака и обезвреживания поверхности бензином или ацетоном. Зачистка проводится при помощи стальных щеток или специального пневматического оборудования. Оно является источником локальной вибрации. Комплект слесарного инструмента, который необходим сварщику, состоит из стальных щеток, зубила и молотка (для очистки швов от шлака и брызг металла), шаблонов(для проверки размеров шва),стального клейма, метра, стальной линейки и др. Слесарный инструмент должен быть уложен в переносном инструментальном ящике. Свариваемые детали до начала сварки должны быть надежно закреплены.
Рекомендуется следующий расход защитного газа:
Диаметр проволоки 1,0мм - 12-14 л/мин
Диаметр проволоки 1,2мм - 14-16 л/мин
Диаметр проволоки 1,6мм - 18-22 л/мин
При сварке деталей из алюминия горелку устанавливают под углом 10-20°к вертикали. Расстояние между соплом горелки и свариваемыми деталями должно быть 10-15 мм. Сварку ведут постоянным током обратной полярности(плюс на электроде),при которой в результате катодного распыления улучшаются условия разрушения оксидной пленки. Обратная полярность применяется при необходимости выделения меньшего количества тепла в свариваемом изделии. На дугу постоянного тока оказывает действие магнитного поля, которое отклоняет ее от оси. Уменьшить действие отклоняющего дугу магнитного поля можно изменением места токоподвода, наклоном электрода в сторону отклонения дуги, уменьшением длины дуги.
Используемый сварочный ток– 25-32 А на 1 мм диаметра электрода, диаметр электрода– 4-6 мм. При сварке алюминия температура дуги должна достигать 660°С и выше, что является источником повышенного светового и теплового излучения. Интенсивность теплового облучения работающих от открытых источников(нагретый металл, стекло, "открытое"пламя и др.) не должна превышать140 Вт/м2,при этом облучению не должно подвергаться более 25%) поверхности тела и обязательным является использование средств индивидуальной защиты, в том числе средств защиты лица и глаз (ГОСТ12.1.005-88).
После сварки во избежание разъедания металла шлак со шва удаляют, промывая горячей или подкисленной водой и тщательно протирая стальными щетками.
Чтобы избежать коробления, образования трещин и улучшить качество сварки, детали из алюминия и его сплавов перед сваркой подогревают до температуры200...350°С (крупные детали до более высокой температуры).Температуру подогрева определяют термопарами или специальными карандашами. Предварительный нагрев приводит к повышенной температуре воздуха рабочей зоны. Концы трещин в деталях засверливают, а кромки разделывают под углом 60...90°.Расплавленный металл удерживают от растекания стальными или глиняными подкладками. Для получения мелкозернистой структуры металла шва деталь после сварки медленно охлаждают, а шов слегка проковывают. Внутренние напряжения снимают нагревом до температуры300...350°С с последующим медленным охлаждением.
Контроль качества
1. Внешний осмотр.
При внешнем осмотре обнаруживаются такие дефекты как трещины в шве и околошовной зоне, незаваренные кратеры, несоответствие конструктивных элементов сварного шва, прожоги, наплывы, непровар в корне шва, подрезы, грубочешуйчатая поверхность сварного шва.
2.Гидравлические испытания.
Испытуемую емкость заполняют водой или керосином(при заполнении сосуда жидкостью должен быть обеспечен выход из него воздуха),а затем с помощью насоса медленно повышают давление в сосуде до заданного по техническим условиям на контроль сварного изделия. Под испытываемым давлением (контролируют по манометру)сосуд выдерживают в течение определенного времени и при этом подвергают тщательному осмотру.
3.Рентгено- и гамма-дефектоскопия.
Рентгеновские лучи обладают свойством проникать через непрозразные тела. Проникая через сварной шов, они ослабляют свою интенсивность, встречая на своем пути пустоты, шлаковые включения, трещины. В зависимости от того или иного дефекта рентгеновские лучи ослабляются по-разному,неодинаково.
Лучи,проникающие через металл,воздействуют на фотопленку,установленную сзади детали,рассматривая которую после проявления судят об обнаруженном дефекте по различной затемненности дефектных мест на фотопленке.
Так обнаруживают наличие в сварных швах трещин, пористости, не проваров, шлаковых включений.
Сущность просвечивания гамма-лучами заключается в том, что, так же как и рентгеновские лучи, лучи некоторых радиоактивных веществ обладают свойством проникать через непрозрачные тела и на фотопленке отражать степень их ослабления. В качестве искусственных радиоактивных веществ получили применение изотопы кобальт-60,цезий-137 и др.
Гамма-установка дефектоскопии материалов представляет собой простейшее устройство. Оно состоит из свинцового контейнера, в котором расположена ампула с радиоактивными веществами. Установкой можно пользоваться в таких местах, где рентгеноустановку не удается использовать; одновременно можно просвечивать несколько деталей или контролировать весь кольцевой шов: гамма-установка легкая, портативная, недорогая.
Однако, при использовании такой дефектоскопии нужно соблюдать все правила безопасности, т.к долговременное и частое радиационное облучение опасно для здоровья человека.
Оценка факторов рабочей среды
Профессия | Фактор рабочей среды и условия труда | Значение показателя | Продолжительность действия фактора, мин |
Сварщик (ручная электродуговая) | Температура воздуха РМ в теплый период года, оС | 25…28 |
350 |
| Токсичное вещество, кратность превышения ПДК, раз | 1,0…2,5 | 350 |
| Промышленная пыль, кратность превышения ПДК, раз | 1…5 | 350 |
| Интенсивность теплового излучения, Вт/м2 | 141. ..1000 | 350 |
| Освещенность РМ на уровне санитарных норм: размер объекта различения, мм разряд зрительной работы | -
> 1,0 5…9 |
350 |
| Физическая статистическая нагрузка, Н-с На две руки х 104 На мышцы корпуса х 104 |
43…86 < 61 |
350 |
| РМ стационарное, поза несвободная- до 50% времени в наклонном положении до 300 |
- |
- |
| Продолжительность непрерывной работы в течение суток, ч |
<8 |
- |
| Длительность сосредоточенного наблюдения % от продолжительности рабочей смены |
75…90 |
- |
| Нервно-эмоциональная нагрузка: Простые действия по заданному плану | - | - |
Расчет интегральной бальной оценки тяжести труда.
Фактор рабочей среды и условия труда (по результатам анализа техпроцесса и рабочего места) | Показатель | Значение показателя
| Балльная оценка фактора
| Продол-жительность действия фактора ti | Удельный вес времени действия фактора tуд i
| Оценка удельной тяжести фактора рабочей среды Хф
|
1 | 2 | 3 | 4 | 5 | 6 | 7 |
Температура воздуха РМ в теплый период года, оС | Х1 | 25…28 | 3 | 350 | 0,73 | 2,19 |
Токсичное вещество, кратность превышения ПДК, раз | Х2 | ≤ 1 | 3 | 350 | 0,73 | 2,19 |
Промышленная пыль, кратность превышения ПДК, раз | Х3 | 1…5 | 3 | 350 | 0,73 | 2,19 |
Интенсивность теплового излучения, Вт/м2 | Х4 | 141. ..1000 | 2 | 350 | 0,73 | 1,46 |
Освещенность РМ на уровне санитарных норм: размер объекта различения, мм разряд зрительной работы |
Х5 Х6 |
-
> 1,0
5…9 |
1 1 | 350 | 0,73 |
1 1 |
Физическая статистическая нагрузка, Н-с На две руки х 104 На мышцы корпуса х 104 |
Х7 Х8 |
43…86
< 61 |
2 1 | 350 | 0,73 |
1,46 1 |
РМ стационарное, поза несвободная- до 50% времени в наклонном положении до 300 | Х9 |
- | 5 | - | - | 5 |
Продолжительность непрерывной работы в течение суток, ч | Х10 |
<8 | 2 | - | - | 2 |
Длительность сосредоточенного наблюдения % от продолжительности рабочей смены | Х11 |
75…90 | 4 | - | - | 4 |
Нервно-эмоциональная нагрузка: Простые действия по заданному плану | Х12 | - | 2 | - | - | 2 |
К сварочным работам допускаются лица не моложе 18 лет после сдачи техминимума по правилам техники безопасности.
Организация каждого рабочего места должна обеспечивать безопасное выполнение робот.
Рабочее места должны быть оборудованы различного рода ограждениями, защитными и предохранительными устройствами и приспособленными.
Для создания безопасных условий робот сварщиков необходимо учитывать кроме общих положений техники безопасности на производстве и особенности выполнение различных сварочных работ. Такими особенностями являются возможные поражения электрическим током, отравления вредными газами и парами, ожоги излучением сварочной дуги и расплавленным металлом, поражения от взрывов баллонов со сжатыми и сжиженными газами.
Электрическая сварочная дуга излучает яркие видимые световые лучи и невидимые ультрафиолетовые и инфракрасные. Световые лучи оказывают ослепляющие действия. Ультрафиолетовые лучи вызывают заболевания глаз, а при продолжительном действии приводят ожогам кожи.
Для защиты зрения и кожи лица применяют щитки, маски или шлемы, в смотровые отверстия вставляют светофильтры, задерживающие и поглощающие лучи. Для предохранения рук сварщиков от ожогов и брызг расплавленного металла необходимо использовать защитные рукавицы, а на тело надевать брезентовую спец. одежду.
В процессе сварки выделяется значительное количество аэрозоля, которое приводит к отравлению организма. Наиболее высока концентрация пыли и вредных газов в облаке дыма, поднимающегося из зоны сварки, поэтому сварщик должен следить за тем, чтобы поток не падал за щиток. Для удаления вредных газов пыли из зоны сварки необходимо устройство местной вентиляции, вытяжной и общеобъемной приточной – вытяжкой. В зимнее время приточная вентиляция должна подавать в помещение подогретый воздух. При отравлении пострадавшего необходимо вынести на свежей воздух, освободить от стесненной одежды и предоставить ему покой до прибытия врача, а при необходимости следует применить искусственное дыхание.
5.2 Электробезопасность
Поражение электрическим током происходит при соприкосновении человека с токоведущими частями оборудования. Сопротивление человеческого организма в зависимости от его состояния ( утомляемость, влажность кожи, состояния здоровья ) меняется в широких приделах от 1000 до 20000 Ом. Напряжение холостого хода источников питания дуги достигает 90В, а сжатой дуги – 200В в соответствии с законом Ома при неблагоприятном состоянии сварщика через него может пройти ток, близкий к предельному:
student.zoomru.ru
1.8. Состав сборочно-сварочного цеха
Крупные сборочно-сварочные цехи могут включать в себя следующие отделения и другие различные помещения и площади:
1. Производственное отделение.
1.1. Заготовительное отделение делится на участки.
1.1.1. Разметки металла.
1.1.2. Резки металла.
1.1.3. Станочной обработки.
1.1.4. Кузнечно-котельный.
1.1.5. Штамповочный
1.1.6. Слесарно-инженерный.
1.1.7. Очистки металла.
1.2. Сборочно-сварочное отделение.
1.3. Отделение.
1.3.1. Узловой сборки.
1.3.2. Общей сборки и сварки.
1.4. Участки.
1.4.1. Термической обработки.
1.4.2. Испытания готовой продукции.
1.4.3. Исправление дефектов.
1.4.4. Нанесение поверхностных покрытий и окончательной отделки продукции.
2. Вспомогательное отделение.
2.1. Цеховой склад металла погрузочно-разгрузочной площадки.
2.2. Промежуточный склад деталей и полуфабрикатов с участком их сортировки.
2.3. Межоперационные складочные участки и места.
2.4. Склад готовой продукции цеха с контрольно-упаковочными отделениями и погрузочной площадкой.
2.5. Кладовые электродов, флюсов, инструментов, приспособлений, запасных частей и вспомогательных материалов.
2.6. Мастерские (ремонтные, электромеханические, изготовления шаблонов).
2.7. Отделения (электромашинные, ацетиленовые, компрессорные, цеховая подстанция).
3. Административно конторские и бытовые помещения;
3.1. Контора цеха.
3.2 Гардеробы.
3.3. Туалет.
3.4. Душевые.
3.5. Буфет.
3.6. Комната отдыха и приема пищи.
3.7. Медпункт.
2. Заготовительное производство
2.1. Приемы выполнения заготовительных операций
Литые, кованые и штампованные заготовки, поступающие на сварку, как правило, не требуют дополнительных операций. Детали же из проката после подбора по размерам и маркам сталей направляются на следующие операции: правку, разметку, резку, обработку кромок, гибку и очистку под сварку.
Листовой прокат требует правки в том случае, если производитель нарушает условия поставки, и при транспортировке возникли значительные деформации (рис. 2.1).
Рис. 2.1. Виды деформаций листовой стали:
а – волнистость; б – серповидность в плоскости; в – местные выпучены; г – заломленные кромки; д – местная погнутость; е – волнистость поперек части листа
Правка осуществляется созданием местной пластической деформации и производится обычно в холодном состоянии.
Для устранения волнистости листов и полос толщиной от 0,5 до 50 мм используются листоправильные вальцы (рис. 2.2).
Рис. 2.2. Схема правки в листоправильных вальцах
Исправление достигается многократным пропусканием листа через валки.
Листы малой толщины (менее 0,5 мм) правят растяжением на прессах с помощью приспособлений или на специальных растяжных машинах.
Серповидность листовой и широкополосной стали в ограниченной степени поддается правке. Ее выполняют на многовалковых листоправильных вальцах с выкладыванием прокладок у вогнутой кромки.
Правку профильного проката производят на роликовых машинах, работающих по схеме листоправильных вальцов (рис. 2.3).
Рис. 2.3. Правка уголка Рис. 2.4. Правка прокатной
в углоправильных вальцах профильной стали (швеллера двутавров)
Для двутавров и швеллеров исправление в плоскости большего момента сопротивления производят изгибом на прессах (рис. 2.4).
При постоянном ходе толкателя 3 задаваемая деформация профиля 2 регулируется изменением расстояния между опорами 1. На таких прессах правят и толстолистовой прокат толщиной более 50 мм.
Разметка. Индивидуальная разметка трудоемка. Наметка по шаблонам более производительна, однако изготовление специальных шаблонов не всегда экономически целесообразно.
Оптический метод позволяет вести разметку без шаблона по чертежу. Имеются разметочно-маркировочные машины с пневмокернером, производящие разметку со скоростью 8–10 м/мин при погрешности ± 1 мм. В этих машинах применяется программное управление.
Без разметки можно обходиться в случае использования приспособлений для мерной резки проката, а также при тепловой резке машинами с фотокопировальной или программной системой управления.
Резка и обработка кромок. Прямолинейные кромки из листов толщиной до 40 мм можно получать с помощью гильотинных ножниц (рис. 2.5).
Верхний нож, опускаясь, производит скалывание металла. Погрешность размера при резке по разметке составляет ± 1,5…2,5 мм. Можно получить прямоугольный рез со скосом под сварку, используя специальные ножницы (рис. 2.6).
Рис. 2.5. Гильотинные ножницы
| 1 – гидроцилиндр; 2 – упор; 3 – ножедержатель; 4, 6 – крепление; 5 – подвеска; 7 – прижим; 8 – регулируемый упор; 9 – нож для прямой резки; 10 – нож для резки под скос |
Рис. 2.6. Специальные ножницы
Листовые заготовки с непрямолинейными кромками толщиной δ = 20…25 мм можно получать с помощью дисковых ножниц (рис. 2.7).
Рис. 2.7. Дисковые ножницы Рис. 2.8. Дисковые ножи
Для получения листовой заготовки заданной ширины с параллельными кромками дисковые ножи целесообразно располагать попарно на заданном расстоянии друг от друга (рис. 2.8).
При резке на ножницах металл подвергается значительной пластической деформации. Поэтому если кромка попадает в зону сварки в последующем и полностью проплавляется, то дополнительной обработки кромок не требуется. Если кромка остается свободной и работает при переменных нагрузках, то целесообразно удалить слой пластически деформированного металла последующей механической обработкой.
В некоторых случаях применяется резка гладким диском либо за счет трения, либо контактно-дуговым оплавлением.
Производительным является процесс вырубки в штампах.
Разделительная термическая резка менее производительна, чем резка на ножницах, но более универсальна и применяется для получения стальных заготовок разных толщин и конфигураций.
Все более широко применяется плазменно-дуговая резка, позволяющая обрабатывать любые металлы и сплавы. Использование сжатого воздуха в качестве плазмообразующего газа дает экономические и технические преимущества – высокое качество газа и большая скорость резки сталей малой и средней толщины (до 60 мм), недостаток воздушно-плазменной резки – насыщение азотом поверхностного слоя кромок, что приводит к образованию пор при сварке. Для устранения недостатка кромки зачищают стальной щеткой и подвергают механической обработке.
Термическую резку используют и при создании скоса кромок, применяя два резака (при разделительной резке) или три – при двухстороннем скосе. После вырезки детали иногда нужно править.
Применяют лазерную резку. Преимущества – малая ширина реза (доли миллиметров) и возможность резки материала малой толщины (0,05 мм).
Механическую обработку на станках (кромкострогальных и торцефрезерных) производят:
– для обеспечения требуемой точности сборки;
– обработки фасок сложного профиля;
– удаления металла, обрезанного ножницами или термической резкой, когда это считается необходимым.
Гибка производится на листогибочных вальцах (с волнами длиной до 13 м) листовых элементов толщиной до 60 мм для получения деталей цилиндрической или конической формы.
При вальцовке в холодном состоянии отношение радиуса изгиба к толщине листа ограничивают допустимым значением пластической деформации. При гибки в вальцах концевой участок листа остается почти плоским.
Более правильное очертание концевого участка может быть получено либо калибровкой уже сваренной обечайки, либо предварительной подгибкой кромок под прессом или на листогибочных вальцах с толстым подкладным листом, согнутым по заданному контуру. Используют также двухвалковые вальцы с эластичным покрытием нижнего валка.
Листовые элементы со сложной пространственной поверхностью получают на специальных вальцах с валками переменного диаметра.
Для получения элементов оболочек больших размеров применяют штамповку взрывом.
При серийном и массовом производстве для получения элементов с поверхностью сложной формы используют холодную штамповку (для материалов δ до 10 мм). Высокая производительность, точность размеров и формы заготовок и низкая себестоимость возможна путем создания технологических штампосварных изделий.
При холодной гибки профильного проката и труб используют роликогибочные и трубогибочные станки. Если возникают трудности, связанные с нарушением формы поперечного сечения, используют станки гибочные с индукционным нагревом изгибаемой заготовки. Нагретый до 950…1000 ºС деформируемый участок имеет небольшую протяженность, обладает малым сопротивлением пластической деформации, что предотвращает образование гофров в зоне сжатия.
Детали из толстого листового металла получают на гибочных вальцах и на прессах в горячем состоянии.
Гофрирование повышает жесткость листов, его производят штамповкой, а не гибкой, чтобы поперечные кромки листов оставались плоскими.
Для очистки деталей и сварных узлов применяют механические и химические методы. Загрязнения, ржавчина, окалина удаляются с помощью дробеструйных или дробеметных аппаратов, используют и зачистные станки с рабочими органами: металлическими щетками, иглофрезами, шлифовальными кругами и лентами. Чугунная и стальная дробь размером от 0,7 до 4 мм применяется в зависимости от толщины металла.
В дробеструйных аппаратах дробь выбрасывается через сопло сжатым воздухом, в дробемётных аппаратах – лопатками ротора (в них производительность выше и дешевле очистка), но происходит износ лопаток. Очистка в обоих случаях осуществляется в камерах. Для крупногабаритных конструкций в мелкосерийном производстве применяют беспыльные дробеструйные аппараты, и можно обходиться без камеры.
Химическими методами производят обезжиривание и травление поверхности ванным и струйным методом. В первом случае (при ванном методе) детали последовательно опускают в ванны с различными растворами и выдерживают в каждом из них определенное время. Во втором случае последовательная подача растворов различного состава на поверхность деталей производится струйным методом, осуществляя непрерывный процесс очистки.
Химический способ эффективен, однако процесс очистки сточных вод при этом дорогостоящ.
Пассивирование или грунтовка предохраняет металл от коррозии (так же, как и очистка) и позволяет осуществлять сварку без удаления защитного покрытия.
Холодная деформация при изготовлении заготовок сопровождается уменьшением пластичности металла. Поэтому относительное остаточное удлинение δ наиболее деформированных волокон необходимо ограничивать. Например, согласно СНиП18-75 при холодной правке δ ≤ 1 %; при холодной гибке δ ≤ 2 %, что соответствует радиусу изгиба не менее 50 толщин листа при правке и не менее 25 толщин листа при гибке. Поэтому существуют предельные значения искривлений, исправление которых не допускается в холодном состоянии.
В случае необходимости создания более значительных деформаций правку и гибку деталей производят в горячем состоянии (900…1000 ºС) при этом происходят процессы рекристаллизации, и пластические свойства металла не снижаются.
Часто правке на вальцах подвергают сварные заготовки из двух или нескольких листов сваренных стыковыми швами. Для ограничения пластической деформации зоны сварного соединения усиление сварного шва должно быть минимальным. В ряде случаев усиление рекомендуется удалять.
Качество подготовки и сборки заготовок под сварку осуществляют внешним осмотром, который является во многих случаях достаточно информативным, наиболее дешевым и оперативным методом контроля.
Внешнему осмотру подвергают материал, который может браковаться при наличии вмятин, заусенцев, окалины, окислов, ржавчины и т.д. Определяется качество подготовки кромок под сварку и сборки заготовок – чистота кромок, соответствие зазоров допускаемым значениям, правильность разделки кромок. Для этого применяются специальные шаблоны или универсальный инструмент. Строгий контроль заготовок и сборки во многом обеспечивает качество сварки.
studfiles.net
Краткая характеристика производства
СОДЕРЖАНИЕ
ВВЕДЕНИЕ
История сварки
Сварочное производство в Старом Осколе
1.Общая часть
1.1 Краткая характеристика производства
1.2 Рабочее место сварщика
2. Специальная часть
2.1 Назначение конструкции и описание сварочных швов
2.2 Материалы, применяемые для изготовления конструкции
2.3 Заготовительные операции
2.4 Подготовка к сварке
2.5 Выбор сварочного оборудования
2.6 Сборка
2.7 Сварка конструкции (режимы сварки и сварочные материалы)
2.8 Контроль сварочных швов
2.9 Техника безопасности при сварочных работах
3. Охрана труда
3.1 Охрана труда на предприятии и промышленная санитария
3.2 Электробезопасность
3.3Пожаробезопасность
4. Экономическая часть
4.1 Структура предприятия
4.2 Расчет расхода сварочных материалов
ЗАКЛЮЧЕНИЕ
ЛИТЕРАТУРА
ВВЕДЕНИЕ
История сварки
Основоположниками сварки являются: В.В. Петров (1731-1834), Н.Н. Бенардос (1842-1905), Н.Г. Словянов (1854-1897).
В 1802 году впервые в мире В.В. Петров открыл и наблюдал дуговой разряд от постоянного и сверхмощного вольтового столба. Этот столб или батарея как называл его Петров, был наиболее мощным источником в то время. Спустя 80 лет Н.Н. Бенардос в 1881 году впервые применил Электрическую дугу между угольным электродом и металлом для сварки.
Почти одновременно с Бенардосом работал другой российский ученый Н.Г. Словянов. Словянов разработал способ дуговой сварки металлическим электродом и защитной сварочной зоны слоем флюса и первый в мире механизм «Электроплавильник – для полуавтоматической подачи электродного прутка в зону сварки. Способ сварки получил название: дуговая сварка по способу - Словяного. Первая демонстрация состоялась в 1882 году. В настоящее время существует большое количество устройств для сварки, например: полуавтомат для дуговой сварки в защитных газах, при котором проволока подается автоматически, а передвижение горелкой производится вручную. Сварочный автомат в этом случае проволока и передвижение горелкой производится автоматически. Газовая сварка – при этом способе детали свариваются пламенем, которое образуется при сгорании газов или паров горючих жидкостей.
Лазерная, плазменная, с дистанционным управлением, подводная сварка.
Общая часть
Краткая характеристика производства
В мастерской изготавливают и сваривают ворота, решетки, контейнеры, также выполняется резка уголка, листов разных размеров и толщин. В мастерской применяют ручную дуговую сварку, есть также газовая сварка и резка. На заготовительном участке применяются механические ножницы. Сварные работы выполняются для нужд лицея, а также выполняются заказы города.
Рабочее место сварщика
Рабочее место сварщика должно быть расположено в специальных сварочных кабинках или непосредственно у сварочного изделия. Сварочная кабина должна иметь размер 2:3 метра, каркас должен быть металлический, стены кабины высотой 2 метра, расстояние от пола 300 мм., стены сделаны из стали или другого несгораемого материала, стены окрашивают в светлые тона огнестойкой краской, дверной проем закрывают брезентовым занавесом. В кабине должна стоять местная вентиляция, внутри кабинки должен стоять стол высотой 500-600 мм., для работы, сидя 900 мм., для работы, стоя к столу приварен болт, служащий для заземления, также должен быть шкафчик для необходимых инструментов и документаций, для удобства работы устанавливают винтовой стул. Все оборудование кабины должно быть заземлено.
Специальная часть
Гост 5264-80-Т6
Тавровое соединение со скосом одной кромки, однастороний.,
Выполнен ручной дуговой сваркой
Заготовительные операции
К заготовительным операциям относят: очистку, гибку, резку, правку, мех. обработку.
Правка необходима для выправления проката. Правка производится путем пластического изгиба или растяжения. Оборудование для правки делят на: ротационные машины, прессы растяжные, правильные машины.
Ротационные машины: листоправильные, многоволковые, сортоправильные, многороликовые машины.
Прессы бывают винтовые, гидравлические, кривошипные.
Гибка: ее выполняют путем пластического изгиба заготовок. По принципу действия оборудование для гибки делят на: ротационные машины и прессы. К ротационным машинам относят: листогибочные, профилегибочные многоволковые станы, зибовочные машины, сортогибочные роликовые машины, трубогибочные машины. Прессы предназначены для гибки различных профилей из листового и полосового материала, на прессах можно выполнить пробивку отверстий, штамповочные операции.
Очистка: её применяют для удаления с поверхности листа средств консервации, загрязнений ржавчины окалины, заусенцев, шлака, которые затрудняют процесс сварки, вызывают дефекты сварных швов и препятствуют нанесению защитных покрытий, для очистки деталей применяют механическую и химическую очистку. К механическим относят: дробеструйную, дробемётную, пескоструйную, на зачистных станках, галтовочных барабанах. К химическим методам относят: обезжиривание, ванный или струйный способ.
Резка. При изготовлении деталей применяют следующие виды резки ножницами на отрезных станках, штампах, на прессах, термическую резку. Ножницы используют при резке листов фасонного профиля малых толщин. Ножницы бывают: однодисковые с наклонным ножом, прессножницы. Отрезные станки применяют для резки труб фасонного и сортового профиля. Термическую резку (газовая и дуговая резка) применяют для резки тугоплавких металлов листового материала и труб большого диаметра.
Механическая обработка. В производстве деталей сварных конструкций металлорежущие станки применяют для выполнения операций сверления отверстий, обработок кромок и поверхностей. Для сверления применяют сверлильные станки, радиальносверлильные, вертикальносверлильные. Многошпиндельные кромки и поверхности обрабатывают на кромкострогальных, продольнострогальных станках, цилиндрические обечайки на токарнокарусельных станках.
Подготовка к сварке
Перед изготовлением деталей используют следующие технологические операции: разметку, резку, штамповку, зачистку, правку, подготовку кромок.
Разметка состоит в нанесении на металл конфигурации заготовки с припуском. Припуск – это разность между размером заготовки и чистовым размером детали. Припуск снимают при последующей обработке. Для разметки применяют разметочные столы или плиты необходимых размеров.
Резку выполняют кислородными резаками по намеченной линии контура детали вручную или газорезательными машинами специального назначения. Резка на металлических станках более производительна и дает высокое качество реза. Для механической прямолинейной резки листового металла применяют прессножницы.
Штамповку заготовок проводят в холодном или горячем состоянии. Стальные листы толщиной до 6-8 мм. штампуют в холодную. Для металла толщиной 8-10 мм. применяют штамповку с предварительным подогревом.
Металл зачищают для удаления заусенцев с кромок деталей после штамповки, а также для удаления с поверхности кромок окалины и шлаков после кислородной резки. Для зачистки мелких деталей используют стационарные установки с наждачными кругами. Крупногабаритные детали зачищают переносными пневматическими или электрическими шлифмашинами.
Детали и заготовки при их искривлении в процессе кислородной резки или резки на механических ножницах правят на листоправильных вальцах или вручную на плите. Правку тонколистового металла проводят в холодном состоянии на листоправильных вальцах или прессах, толстолистового металла – в горячем состоянии вручную на правильных плитах.
Подготовку свариваемых кромок деталей большой толщины выполняют кислородной резкой или обработкой на строгальных или фрезерных станках, для подготовки тонколистового металла используют кромкогибочные прессы или специальные станки. Гибку деталей и заготовок проводят на металлогибочных вальцах. Здесь же изготавливают обечайки для сварки различных емкостей цилиндрической формы. Согласно чертежу производится скос одной кромки под углом 45* сварной шов.
Гост 5264-80-Т6
Сборка
Сборка – это технологическая операция, обеспечивающая подлежащими сварке деталями необходимое взаимное расположение с закреплением их специальными приспособлениями или прихватками.
Существуют следующие приспособления для сборки:
сборочно-сварочная плита – опорное приспособление в виде горизонтальной металлической плиты с пазами;
стеллаж – опорное приспособление с плоской горизонтальной поверхностью для размещения крупногабаритных изделий в цехе;
сборочно-сварочные стенды – устройства для размещения деталей собираемых и свариваемых крупногабаритных изделий и фиксаций их в нужном положении.
Основой сборочного приспособления является жесткий каркас, несущий упоры фиксаторы и прижимы. При сборке детали заводят в приспособления, укладывают по упорам и фиксаторам и закрепляют пружинами.
Последовательность выполнения сборочно-сварочных операций может быть различной:
- Сварку выполняют после полного завершения сборки.
- Сборку и сварку производят переменно, например, при изготовлении конструкций наращиванием отдельных элементов.
- Общей сборке и сварке конструкций предшествует сборка и сварка узлов.
Сварка
Под режимом сварки понимают – совокупность параметров, которые обеспечивают устойчивое горение дуги, получение сварочных швов заданных размеров, формы и качества. Существуют главные параметры и дополнительные параметры.
К главным параметрам относятся: 1) сила сварочного тока; 2) напряжение дуги; 3) скорость сварки.
К дополнительным относятся: 1) диаметр электрода; 2) тип и марка электрода; 3) род и полярность сварочного тока; 4) пространственное положение шва.
Определение режимов сварки для рамы:
По толщине металла определяем диаметр электрода (dэл), так как толщина металла, из которого изготавливается спираль равна 10 мм., значит, будем использовать электрод диаметром 4 мм.
Сила сварочного тока J(А) равна: по формуле Jсв=dэл·k, рассчитываем силу сварочного тока. k – коэффициент пропорциональности зависит от диаметра электрода. Jсв = 30·dэл=30·4=120 А.
Напряжение на дуге (Uд) при ручной дуговой сварке будет равно 24В.
Скорость сварки (Uсв) зависит от квалификации сварщика и толщины свариваемого металла.
Род тока и полярность устанавливаются в зависимости от вида свариваемого металла и от его толщины, при сварке постоянным током обратной полярности на электроде выделяется больше теплоты. Обратная полярность применяется при сварке тонкого металла и при сварке высоколегированных сталей, чтобы не было перегрева.
Положение шва в пространстве при ручной дуговой сварке можно производить по всех пространственных положениях.
При сварке рамы, применяются электроды:
Э42А – тип электрода
Э–электрод
УОНИ 13/45- марка электрода
У – для углеродистой стали
Д – толстое покрытие
Е-412(3) – группа индексов, характеризующая механические свойства
Б- основное покрытие
20 – род и полярность
Контроль сварных швов
Существуют различные методы контроля сварных швов: гидравлические, пневматические, вакуумные, керосиновый. Сварные швы рамы контролируются внешним осмотром. Он заключается в том, что это простейший и не обходимый способ проверки качества сварки в готовом изделий. Внешний осмотр выявляет несоответствие шва требуемых геометрическим размерам, наплывы подрезы, прожоги. Размеры швов должны соответствовать указным на чертеже. Не допускается какое бы ни было уменьшение фактического размера шва по сравнению с заданным размером. При выявлений наружных дефектов (поры, трещины)–нужно удалить шлак, зачистить место сварки удалить поры и трещины с помощью горелки или шлифмашинки, а после удаления и зачистки переварить шов сначала
Охрана труда
Электробезопасность
При электросварочных работах проходы между однопостовыми источниками сварочного тока для сварки плавлением, резки, наплавки должны иметь ширину не менее 0,8 м., между многопостовыми источниками – не менее 1,5 м., расстояние от одно- и многопостовых источников сварочного тока до стены должно быть не менее 0,5 м.
Регулятор сварочного тока может размещаться рядом со сварочным трансформатором или над ним. Запрещается установка сварочного трансформатора над регулятором тока.
Запрещается производство электросварочных работ во время дождя и снегопада при отсутствии навесов над электросварочным оборудованием и рабочим местом.
При электросварочных работах в производственных помещениях рабочие места сварщиков должны быть отделены от смежных рабочих мест и проходов несгораемыми экранами (ширмами, щитами) высотой не менее 1,8 м.
При электросварочных работах в сырых местах сварщик должен находиться на настиле из сухих досок или на диэлектрическом ковре.
При электросварочных работах сварщик и его подручные должны пользоваться индивидуальными средствами защиты: защитной каской из токонепроводящих материалов, которая должна удобно сочетаться со щитком, служащим для защиты лица и глаз: защитными очками с бесцветными стеклами для предохранения глаз от осколков и горячего шлака при зачистках сварочных швов молотком или зубилом; рукавицами с крагами или перчатками, специальной одеждой из искростойких материалов с низкой электропроводностью, кожаными ботинками.
Пожаробезопасность
Причинами пожара при сварочных работах могут быть искры и капли расплавленного металла и шлака, неосторожное обращение с пламенем горелки при наличии горючих материалов вблизи рабочего места сварщика.
Для предупреждения пожаров необходимо соблюдать следующие противопожарные меры: нельзя хранить вблизи от места сварки огнеопасные или легковоспламеняющиеся материалы, а также производить сварочные работы в помещениях, загрязненных промасленной ветошью, бумагой, древесными отходами;
Запрещается пользоваться одеждой и рукавицами со следами масел, жиров, бензина, керосина и других горючих жидкостей; нельзя выполнять сварку и резку свежевыкрашенных масляными красками конструкций до полного их высыхания;
Запрещается выполнять сварку аппаратов, находящихся под электрическим напряжением, и сосудов, находящихся под давлением.
Нужно постоянно иметь противопожарные средства – огнетушители, ящики с песком, лопаты, ведра, пожарные рукава и следить за их исправным состоянием, а также содержать в исправности пожарную сигнализацию; после окончания сварочных работ необходимо выключить сварочный аппарат, а также убедиться в отсутствии горящих или тлеющих предметов.
Экономическая часть
Структура предприятия
Начальник цеха несет ответственность за штатное расписание:
непосредственно обеспечивает руководство всей работы по выполнению планового задания, охране труда, техники безопасности, чтобы все рабочие места были укомплектованы рабочими единицами;
производит анализы безопасности производственного оборудования и трудовых процессов, применяет меры к повышению уровня их безопасности;
ежедневно в санитарном рапорте докладывает о нарушениях и устранении причин нарушений;
проверяет работу по охране труда и принимает меры дисциплинарного взыскания;
контролирует качество работы, проверяет состояние документации по инструкции рабочих в цехе;
контролирует наличие и систематическое обновление наглядной аппаратуры по охране труда на участке и рабочих местах.
Заместитель начальника цеха:
отвечает за выполнение заданий, запланированных работ по участкам, за технику безопасности, за исправность оборудования, следит за качеством и своевременным выполнением заданий.
Начальник участка:
следит за исправностью источников питания;
наблюдает за ходом сварки;
отвечает за технику безопасности на своем участке, несет ответственность за выполнение запланированных работ.
Мастер:
назначает разряд сварщикам;
следит за качеством выполняемой работы;следит за техникой безопасности непосредственно при выполнении какой- либо работы на участке;
докладывает о проделанной в течение дня работе.
ЗАКЛЮЧЕНИЕ
Дипломная работа выполнена по теме:
"Технология изготовления сварной конструкции "Рама"
В водной части дипломной работы охарактеризованы основные виды сварки плавлением, их сущность и способы применения. Представлено развитие сварочного производства в настоящее время.
В общей части представлена классификация сварочных постов в зависимости от вида сварки и вспомогательного оборудования, инструмент и принадлежности сварщика. Основные технологические операции ручной дуговой сварки раскрыты в специальной части. Мной указан и аргументирован выбор сварочных материалов, предназначенных для сварки конструкции, произведен расчет основных параметров сварки, предложены методы и способы контроля качества сварного соединения. Особое внимание уделено вопросам, касающихся техники безопасности, гигиены труда и производственной санитарии.
В экономической части мной произведен расчет сварочных материалов. Представлена схема структуры управления цехом.
Выполняя дипломную работу, закрепил теоретические и практические знания.
ЛИТЕРАТУРА
Виноградов В.С. «Оборудование и технология дуговой автоматической и механизированной сварки»
Маслов В.И. «Сварочные работы»
Попов В.А «Дуговая и газовая сварка сталей»
Чернышов Г.Г. «Сварочное дело»
Кобзев В.А., Коваленко В.В. «Сварочные трансформаторы»
СОДЕРЖАНИЕ
ВВЕДЕНИЕ
История сварки
Сварочное производство в Старом Осколе
1.Общая часть
1.1 Краткая характеристика производства
1.2 Рабочее место сварщика
2. Специальная часть
2.1 Назначение конструкции и описание сварочных швов
2.2 Материалы, применяемые для изготовления конструкции
2.3 Заготовительные операции
2.4 Подготовка к сварке
2.5 Выбор сварочного оборудования
2.6 Сборка
2.7 Сварка конструкции (режимы сварки и сварочные материалы)
2.8 Контроль сварочных швов
2.9 Техника безопасности при сварочных работах
3. Охрана труда
3.1 Охрана труда на предприятии и промышленная санитария
3.2 Электробезопасность
3.3Пожаробезопасность
4. Экономическая часть
4.1 Структура предприятия
4.2 Расчет расхода сварочных материалов
ЗАКЛЮЧЕНИЕ
ЛИТЕРАТУРА
ВВЕДЕНИЕ
История сварки
Основоположниками сварки являются: В.В. Петров (1731-1834), Н.Н. Бенардос (1842-1905), Н.Г. Словянов (1854-1897).
В 1802 году впервые в мире В.В. Петров открыл и наблюдал дуговой разряд от постоянного и сверхмощного вольтового столба. Этот столб или батарея как называл его Петров, был наиболее мощным источником в то время. Спустя 80 лет Н.Н. Бенардос в 1881 году впервые применил Электрическую дугу между угольным электродом и металлом для сварки.
Почти одновременно с Бенардосом работал другой российский ученый Н.Г. Словянов. Словянов разработал способ дуговой сварки металлическим электродом и защитной сварочной зоны слоем флюса и первый в мире механизм «Электроплавильник – для полуавтоматической подачи электродного прутка в зону сварки. Способ сварки получил название: дуговая сварка по способу - Словяного. Первая демонстрация состоялась в 1882 году. В настоящее время существует большое количество устройств для сварки, например: полуавтомат для дуговой сварки в защитных газах, при котором проволока подается автоматически, а передвижение горелкой производится вручную. Сварочный автомат в этом случае проволока и передвижение горелкой производится автоматически. Газовая сварка – при этом способе детали свариваются пламенем, которое образуется при сгорании газов или паров горючих жидкостей.
Лазерная, плазменная, с дистанционным управлением, подводная сварка.
Общая часть
Краткая характеристика производства
В мастерской изготавливают и сваривают ворота, решетки, контейнеры, также выполняется резка уголка, листов разных размеров и толщин. В мастерской применяют ручную дуговую сварку, есть также газовая сварка и резка. На заготовительном участке применяются механические ножницы. Сварные работы выполняются для нужд лицея, а также выполняются заказы города.
Рабочее место сварщика
Рабочее место сварщика должно быть расположено в специальных сварочных кабинках или непосредственно у сварочного изделия. Сварочная кабина должна иметь размер 2:3 метра, каркас должен быть металлический, стены кабины высотой 2 метра, расстояние от пола 300 мм., стены сделаны из стали или другого несгораемого материала, стены окрашивают в светлые тона огнестойкой краской, дверной проем закрывают брезентовым занавесом. В кабине должна стоять местная вентиляция, внутри кабинки должен стоять стол высотой 500-600 мм., для работы, сидя 900 мм., для работы, стоя к столу приварен болт, служащий для заземления, также должен быть шкафчик для необходимых инструментов и документаций, для удобства работы устанавливают винтовой стул. Все оборудование кабины должно быть заземлено.
Специальная часть
infopedia.su
Глава 1. ОРГАНИЗАЦИЯ СВАРОЧНОГО ЦЕХА
Итак, вы решили заниматься сварочными работами. Прежде всего, вам потребуется оборудовать свое рабочее место, по традиции назовем его сварочным цехом. Идеальный вариант – строительство специально предназначенного помещения; однако, если такой возможности не имеется, – не беда. Можно приспособить уже имеющийся гараж или сарай.Видео: "Частный сварочный цех".
Окинем критическим взором имеющееся помещение: все, что относится к категории легко воспламеняющихся материалов, необходимо удалить или хотя бы изолировать.
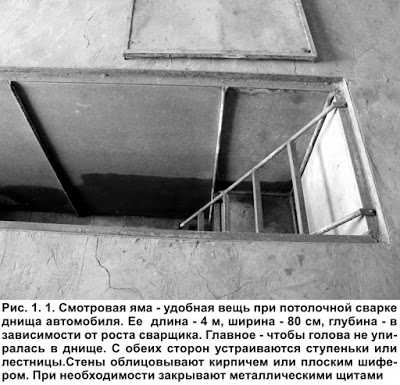
Полы
Наиболее подходящим с точки зрения электро- и теплопроводности является асфальтовый пол. Однако у него есть одна неприятная особенность: он боится капель и брызг расплавленного металла. При проведении сварки такой пол в месте попадания капель необходимо дополнительно изолировать негорючим материалом.
Цементный пол более стоек, но в то же время может интенсивно впитывать влагу, что значительно увеличивает его электропроводность. Лучше всего, если есть такая возможность, выложить пол обожженным красным кирпичом. Такой пол легко ремонтируется, и в то же время он является достаточно теплым и электробезопасным. Категорически запрещается строить сварочный цех в сыром месте: это опасно для жизни!Видео: "Полы сварочного цеха".
Стены
Кирпичные или железобетонные стены – лучший вариант для сварочного цеха. В крайнем случае, можно использовать уже имеющиеся стены деревянного сарая, тщательно оштукатурив их снаружи и внутри. В штукатурке нельзя допускать трещин и выбоин, так как туда обязательно залетят брызги раскаленного металла.
Видео: "Стены сварочного цеха"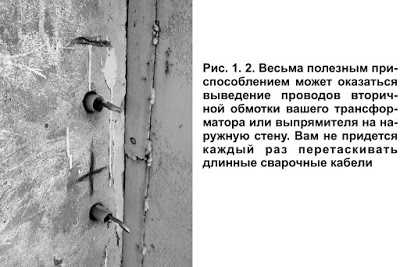
Видео: "Огнестойкие полки в сварочном цехе""
Потолок
Многие сварщики, выполнив вышеуказанные требования к полу и стенам, решают, что потолок высоко и уж туда-то ничто не попадет. Опасное заблуждение! Резка металлов сопровождается таким количеством далеко летящих искр, что ваш деревянный потолок будет подвергаться настоящей бомбардировке! Потолок также необходимо тщательно заизолировать.Видео: "Потолок сварочного цеха"
Размеры сварочного цеха
Поскольку существенной статьей дохода сварщика является сварка легковых автомобилей, то и размеры цеха не могут быть меньше размеров автомобиля. Плюс к этому для удобства работы необходимо дополнительное расстояние хотя бы 1 метр во все стороны от автомобиля.Видео: "Размеры сварочного цеха"
Как и в любом гараже, для доступа к автомобилю снизу необходимо предусмотреть смотровую яму длиной не менее длины автомобиля.
С наружной стороны цеха необходимо построить еще две небольшие пристройки. Они снабжаются вентиляционными отверстиями, и в них располагаются баллоны с техническими газами.Видео: "Пристройки к сварочному цеху"
Ни в коем случае не оставляйте баллоны внутри цеха! Даже если это баллоны с инертными газами, случайное прикосновение к ним находящегося под напряжением неизолированного сварочного провода вызывает ослабление стенок баллона, что чревато взрывом.
Видео: "Площадка перед сварочным цехом"
Освещение
Бытует мнение, что сварка опасна для глаз. Очень часто это связано с недостаточным освещением сварочного цеха. В полумраке зрачок глаза сварщика сильно расширяется, и случайный взгляд на горящую дугу обеспечивает опасную порцию ультрафиолета на внутренней поверхности его глазного яблока. Поэтому здесь может быть только один совет: обеспечить как можно более яркое освещение своего цеха!
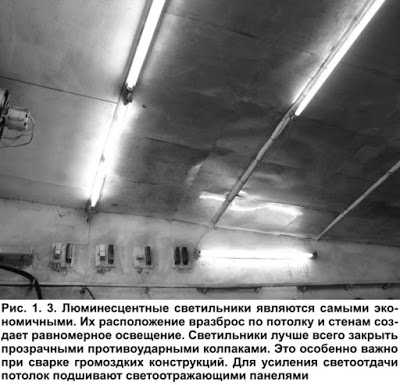
Вентиляция
Этой проблеме многие сварщики, к сожалению, уделяют недостаточно внимания. А зря! Добровольно травить свой организм не совсем полезными газами не лучшее решение. Хотите всегда иметь свежий воздух – поставьте в цехе приточно-вытяжную вентиляцию. Вытяжной вентилятор укрепляется под потолком, приточный – с противоположной стороны цеха вблизи от пола. Нижнее расположение приточного вентилятора объясняется тем, что в зимнее время здесь может быть установлен тепловентилятор.
Кроме этого, желательно иметь еще один небольшой переносной вентилятор. Он служит как для охлаждения сварщика в жаркое время, так и для вентиляции помещения, если работа производится где-то на выезде, вне цеха.
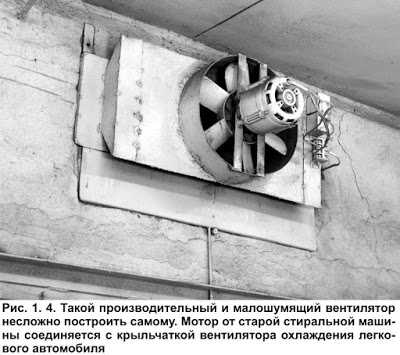
Электропроводка
Электропитание цеха часто является камнем преткновения для сварщиков. Воздушные линии электропроводки строились еще в то время, когда в расчет не брались энергоемкие потребители бытового сектора. В итоге работа сварочного трансформатора вызывает падение напряжения в сети, что внешне фиксируется как «мигание света». Если для электролампочек это и не опасно, то для компьютеров и холодильников, увы, может оказаться смертельным.
Если есть возможность, лучше всего выполнить электропитание цеха отдельным кабелем от силового щита. Минимальное сечение кабеля рассчитывается по токовой нагрузке. Исходя из опыта, такая нагрузка частного сварочного цеха не превышает 40 – 50 А. В этом случае можно использовать медный провод с сечением 6 мм². Однако это минимальное сечение не может удовлетворить сварщика. Оно гарантирует только отсутствие перегрева изоляции, но отнюдь не отсутствие падения напряжения. Я не буду здесь приводить методику расчета проводов по падению напряжения. Сварщик просто должен знать: чем короче проводка и толще ее сечение, тем меньше падение напряжения в сети.
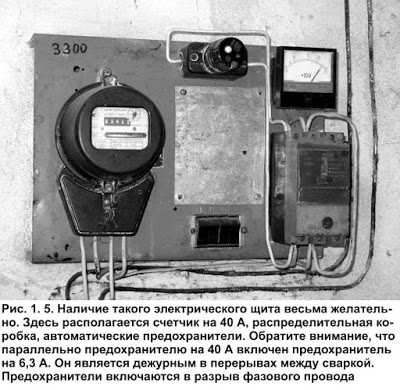
Сечение токопроводящей жилы, мм2 | Для проводов, проложенных | |||||
двух одножильных | трех одножильных | четырех одножильных | одного двухжильного | одного трехжильного | ||
Сечение токопроводящей жилы, мм2 | Для проводов, проложенных | |||||
двух одножильных | трех одножильных | четырех одножильных | одного двухжильного | одного трехжильного | ||
Противопожарные средства
По условиям техники безопасности сварочный цех должен иметь как минимум углекислотный огнетушитель. Однако этого недостаточно. Водители легковых автомобилей для предотвращения коррозии заливают масло во все полости своих машин. При сварке масло воспламеняется, и тушить его обычным огнетушителем часто бывает проблематично. Здесь может выручить обычная пластиковая бутылка, в пробке которой сверлом 1 мм просверлено отверстие. Узкая направленная струя воды тушит полостное возгорание довольно эффективно. Для удобства бутылка должна быть емкостью 1 л, желательно иметь их под рукой не менее трех.Видео: "Средства пожаротушения в сварочном цехе"
Заземление
Это еще одна вещь, которую игнорируют сварщики. Однако, не будь такого заземления у автора этих строк, возможно, писать было бы уже некому.
Для устройства заземления забейте в землю уголок длиной 2 м и толщиной стенки не менее 4 мм. Затем включите автоматический сварочный предохранитель и проверьте на короткое замыкание, соединив фазу и заземление. Если не произошло мгновенного срабатывания предохранителя, последовательно вбивайте еще несколько таких уголков, каждый раз проверяя на короткое замыкание. Уголки соединяйте между собой при помощи сварки.
Сработало? Провод от заземления подсоедините к одному из выводов вторичной обмотки вашего сварочного трансформатора, а если конструкцией предусмотрено, то и к корпусу.Видео: "Заземление в сварочном цехе"
Рабочий стол
Рабочий стол – основное место сварщика при проведении мелких сварочных работ. Лучше всего его сделать металлическим и передвижным. Обязательно на нем должны быть тиски и изолированная подставка для держателя. Верхнюю часть можно сделать ячеистой (Рис. 1. 6.) для улавливания брызг металла (дальше они попадают в поддон). Стул желательно сделать с регулирующимся по высоте сидением. Тогда можно выполнять сварку сидя, даже если деталь значительно возвышается над столом.
К рабочему столу подключается провод сварочного трансформатора, называемый «массой».
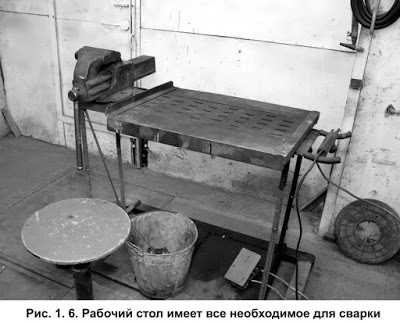
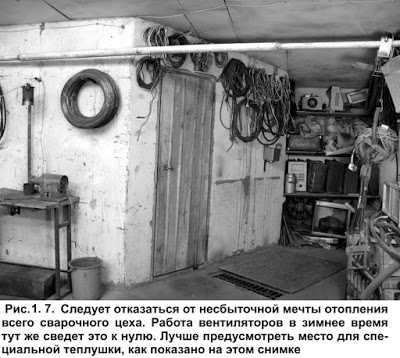
svarnoj.blogspot.com
Характеристика цеха и сварочного участка — дипломная работа
Используются технологические кузнечные операции осадки слитков, всесторонней ковки, вальцовки (прокатки) с использованием валков переменного сечения, штамповки в объемных штампах, прошивки, вырубки и др. Использование штампов с разъемными вставками позволяет получить штамповки сложной конфигурации с минимальными припусками под механическую обработку.
Масса штамповок от 100 г до 3000 кг, площадь проекции от 60 до 12000 см². для термообработки штамповок и поковок кузнечные цеха имеют электрические печи с принудительной циркуляцией воздуха.
КУМЗ выпускает более 1500 наименований штамповок, 1200 типоразмеров поковок, 1600 наименований кольцевых заготовок из 70 марок алюминиевых и магниевых сплавов по стандартам Российской Федерации согласно ОСТ 1 90073-85 «Штамповки и поковки из алюминиевых сплавов» и ТУ 1 92-147-89 «Поковки кованые и штампованные из магниевых сплавов». Имеется техническая возможность для производства штамповок по стандартам BS 1472, DIN 1749, AMS 4127G, ASTM В 247-02а.
Кузнечное производство обеспечивает изготовление штамповок и поковок из алюминиевых сплавов методом объемной штамповки. Заготовкой для кузнечного производства может быть слиток, прессовое изделие или прокат.
Непосредственно перед горячей объемной штамповкой заготовки нагреваются в электрических печах до температуры 240—480 °С в зависимости от используемого сплава. Термическую обработку изделий производят после их нагрева до температуры 470—530 °С в селитровых ваннах или вертикальных — закалочных печах с охлаждением в воде. Горячая объемная штамповка производится за несколько проходов. После штамповки изделие подвергают осветлению поверхности путём травления в растворе каустической соды и последующей обработке в растворе азотной кислоты. Далее изделие зачищают от образовавшихся дефектов, обрезают.
В 2008 на КУМЗе был начат опытный выпуск плит по собственным техническим условиям. Брикетированная смесь алюминиевого порошка с Tih3 вспенивается в специальной печи при стабильной температуре, в результате чего получается пеноалюминий с закрытыми порами. Основная область применения: поглощение ударной и звуковой волн, изоляция, облегчение конструкций.
2 Общая характеристика цеха и сварочного участка (характеристика сварки, основных и вспомогательных технологических материалов, используемых в процессе сварки).
Различают более 150 видов сварочных процессов. ГОСТ 19521- 74 сварочные процессы классифицирует по основным физическим, техническим и технологическим признакам.
Основа классификации по физическим признакам – вид энергии, применяемой для получения сварочного соединения. По физическим признакам все сварочные процессы относят к одному из трех классов: термическому, термомеханическому, и механическому.
Термический класс – все виды сварки плавления, осуществляемые с использованием тепловой энергии (газовая, дуговая, электрошлаковая, плазменная, электроно – лучевая и лазерная).
Термомеханический класс – все виды сварки осуществляемые с использованием тепловой энергии и давления (контактная, диффузионная, кузнечная, газо – и дугопрессовая ).
Механический класс – все виды сварки, давлением, провидимые с использованием механической энергии (холодная, трением, ультразвуковая и взрывом).
По техническим признакам сварочные процессы классифицирует в зависимости от способа защиты металла в зоне сварки, непрерывности процесса и степени его механизации.
Чтоб облегчить труд сварщика и для повышения производительности труда применяют различные высокопроизводительные виды сварки.
- Сварка пучком электрода – два или несколько электрода соединяют в пучёк (двух трех местах сваривают контактные концы друг с другом) и электрододержателем ведут сварку. При сварки пучком электрода контакт происходит между свариваемым изделием и одним стержней электродов по мере оплавления, контакт переходит на следующий стержень. При сварки пучком электрода можно пользоваться повышенной силой тока.
- Сварка с глубоким проваром – на стержень электрода наноситься, более толстый слой покрытия увеличивая этим тепловую силу дуги и повысить её проплавляющие действия, то есть увеличить глубину расплавления основного металла. Сварку ведут короткой дугой, горение которой поддерживается за счет операния козырька покрытия на основной металл применяют при сварки угловых и тавровых соединениях.
- Сварка наклонным электродам – электрод укладывается в разделку шва, для удержания электрода в разделке и для изоляции и защиты дуги применяют медные накладки длина дуги в процессе горения равна толщина слоя покрытия диаметр электрода 6-10мм, а длина электрода 800-1000мм.
- сварка электрода большим диаметров – 8-12мм и величина тока от 350-600А но имеет свои недостатки:
1. Трудно выполнять в узких местах.
2. Быстрое утомляемость сварщика.
3. Возникает значительное магнитное дутье.
- Ванная сварка выполняют одним или несколькими электродами при повышенной величине тока это обеспечивает разогрев свариваемых элементов для образования большой ванны жидкого металла которую удерживают специальной формой в процессе сварки наплавленный металл постоянно находится в жидком состоянии в конце процесса сварки для ускорения и охлаждения сварочной ванны дуги периодически прерывают.
- Безогарковая сварка – электрод не закрепляется в держателе, а приваривается к нему торцом, что позволяет использовать весь стержень.
- Ручная дуговая сварка.
- Газовая сварка и резка.
- Полуавтоматическая сварка
- Автоматическая сварка под слоем флюса и в среде защитных газов.
- Аргона – дуговая сварка
- Электроконтактная сварка
Для 170 трубы я по расчетам сделал три прихватки, прихватка длиной 30мм.
Прихватки наносятся через каждые 30мм.
Для сварки корня шва я выбрал электрод диаметром 3мм.
Для сварки второго шва я выбрал 4мм.
Для прохождения второго шва нужно делать колебательные движения из стороны в сторону для захватывания ( сваривания ) обоих кромок.
3. Технический контроль
3.1 Организация контроля качества
Дефекты в сварных соединениях могут быть вызваны плохим качеством сварных материалов, неточной сборкой и подготовкой стыков под сварку, нарушением технологии сварки, низкой квалификацией сварщика и другими причинами. Задача контроля качества соединений – выявление возможных причин появления брака и его предупреждения.
Работы по контролю качества сварочных работ проводят в три этапа:
- Предварительный контроль, проводимый до начала работ:
- Контроль в процессе сборки и сварки ( по операционный ).
- Контроль качества готовых сварных соединений.
- Предварительный контроль включает в себя: проверку квалификации сварщиков, дефектоокопистов и итр, руководящих работами по сборке, сварке и контролю.
- В процессе изготовления (пооперационной контроль) проверяют качество подготовки кромок и сборки, Режимы сварки, порядок выполнении швов, внешний вид шва, его геометрические размеры, за исправностью сварочной аппаратуры.
- Последнее контрольная операция – проверка качества сварки в готовом изделии: внешний осмотр и измерения сварных соединений, испытания на плотность, контроль ультразвуком, магнитные методы контроля.
Проверка квалификации сварщика: квалификация сварщиков проверяют при установлении разряда. Разряд присваивают согласно требованиям, предусмотренным тарифно – квалификационными справочниками, испытания сварщиков перед допускам к ответственным работам производят по правилам оттистации сварщиков и специалистов сварочного производства.
Контроль качества основного металла. Качество основного металла должно соответствовать требованиям сертификата, который посылают заводы – поставщики вместе с партией металла необходимо произвести наружный осмотр установить механические свойства и химический состав металла.
При наружном осмотре проверяют отсутствие на металле окалины, ржавчины, трещин и прочих дефектов.
Предварительная проверка металла с целью обнаружения дефектов поверхности – необходимое и обязательная операция, благодаря которой можно предупредить применение некачественного металла при сварке изделия.
Механическое свойства основного металла определяют испытаниями стандартных образцов на машинах для растяжения, пессах и копрах в соответствии с ГОСТ 1497 – 73 металла методы испытания на растяжения.
Контроль качества сварочной проволоки: на проволоку стальную наплавочную устанавливают марку и диаметр сварочной проволоки, химический состав правило приемки и методы испытания, требования к упаковке, маркировки, транспортированию и хранению.
Каждая бухта сварочной проволоки должна иметь металлическую бирку на которой указано наименование и товарный знак предприятия – изготовителя сварочную проволоку, на которой нет документации подвергают тщательному контролю.
Контроль качества электрода. При сварке конструкции, в чертежах которых указан тип электрода, нельзя применять электрод, не имеющий сертификата. Электрод без сертификата проверяют на прочность покрытия и сварочные свойства определяют так же механические свойства металла шва и сварочного соединения выполненного электрода из проверяемой партией.
Контроль качества флюсов. Флюс проверяют на однородность по внешнему виду, определяют его механический состав, размер зерна, объем массу и влажность.
Контроль заготовок. Перед поступлением заготовок на сборку проверяют чистоту поверхности металла, и габариты качества подготовки кромок.
Контроль сборки: собранному контролируют: зазор между кромками, притупление и угол раскрытия для стыковых соединений: ширину нахлестки и зазор между местами для нахлесточных соединений.
Контроль качества сварочного оборудования и приборов. Проверяют исправность контрольно – измерительных приборов, надежность контактов и изоляции правильность подключения сварочной дуги, исправность замкнутых устройств, электрододержателя, сварочных горелок, редукторов, проводов.
Контроль технологического процесса сварки: перед тем как преступить к сварке, сварщик знакомится с технологическими картами, в которых указаны последовательность операций, диаметр и марка применяемых электродов, режимы сварки и требуемые размеры сварных швов. Не соблюдения порядка наложение швов может вызвать значительную деформацию.
При выполнении производственных операции за рабочим или бригадой рабочих закрепляется рабочие место в виде определённого участка производственной площади, оснащенной согласно требованием технологического процесса, соответствующим оборудованием и необходимыми принадлежностями. Рабочее место сварщика называют сварочным постом.
Для защиты рабочих от излучения дуги в постоянных местах сварки устанавливают для каждого сварщика отдельную кабину размером 2х2,5 или 2х2.
Стенки кабины могут быть сделаны из тонкого железа, или другого несгораемого материала высотой 1,8- 2,0м, для лучшей вентиляции не доходящих до пола на 0,2-0,3м. Пол должен быть из огнестойкого материла: кирпич, бетон, цемент. Стены окрашивают в светло-серый цвет красками хорошо поглощающими ультрафиолетовые лучи. Кабину оборудуют местной вентиляцией с воздухообменом 40м3/час на одного рабочего.
Вентиляционный отсос располагают так, чтобы газы, выделяющиеся при сварке, проходящим мимо сварщика.
Сварку детали производят на рабочем столе высотой 0,5-0,7м. Крышку стола изготавливают из чугуна толщиной 20-25мм, в ряде случаев на столе устанавливают различные приспособления для сборки и сварки изделий.
К нижней части крышки или ножки стола приваривают стальной болт, служащий для крепления токопроводящего провода от источника сварочного тока и для провода заземления стола. С боку стола имеются гнезда для хранения электродов. В выдвижном ящике стола хранится инструмент и технологическая документация. Для удобства работы в кабине устанавливают металлический стул с подъемным винтовым сидением, изготовленным не электропроводящего материала. Под ногами у сварщика должен находится резиновый коврик.
Сварочный пост оснащен генератором или сварочным трансформатором.
Электродуговая сварка – наиболее широко применяемая группа процессов сварочной технологии.
При электродуговой сварке кромки соединяемых деталей расплавляются электрическим дуговым разрядом.Для сварки необходим сильноточный источник питания низкого напряжения,к одному зажиму которого присоединяется свариваемая деталь, а к другому– сварочный электрод.Электрическая дуга представляет собой устойчивый длительный электрический разряд между двумя электродами в ионизированной газовой среде.Дуга состоит из анодной области, катодной области и столба.Главная роль дугового разряда– преобразование электрической энергии в теплоту.Температура дуги на оси газового столба достигает6000...7500°С, что позволяет расплавить практически все металлы и сплавы. На поверхностях анода и катода температура дуги снижается до 3500 – 4000 0С. Столб дуги окружен пламенем (ореолом).Из-за большого концентрации тепла и высоких температур при сварке тонкого или легкоплавкого металла, а также чувствительных к перегреву высокоуглеродистых,нержавеющих и легированных сталей электрическую дугу питают током обратной полярности.То есть минус источника тока подключают к изделию.
В результате очень высоких температур дуги возникают опасные факторы:интенсивное излучение сварочной дуги в оптическом диапазоне(ультрафиолетовое,видимое, инфракрасное)и интенсивное тепловое(инфракрасное)излучение свариваемых изделий и сварочной ванны.
student.zoomru.ru
Состав исполнителей сборочно-сварочных цехов | Квалификационные характеристики рабочих сварочной специальности
Состав исполнителей сборочно-сварочных цехов
В соответствии с новыми условиями управления строительным комплексом осуществляются крупные мероприятия, направленные на углубление специализации предприятий стройиндустрии по изготовлению конструктивно и технологически однотипных сварных металлических конструкций, что служит основой для существенного повышения уровня концентрации их производства.
Повышение уровня специализации и концентрации производства сварных строительных металлоконструкций является необходимой предпосылкой коренного улучшения его технико-экономических показателей за счет эффективного применения современных высокопроизводительных комплексно-механизированных и автоматизированных поточных линий и наиболее прогрессивных технологических процессов заготовки, сборки и сварки. В то же время оно содействует повышению степени индустриализации строительства и сокращению объемов сварочных работ в монтажных условиях.
Заготовительные цеха современных предприятий по производству стальных строительных конструкций оснащены высокопроизводительным оборудованием для правки, механической и термической резки листового и профильного проката. Коллектив заготовительного цеха, как комплексная бригада по производству полуфабрикатов, комплектуется рабочими, способными совмещать труд такелажника и правщика металла, труд оператора машины для термической резки и разметчика.
Укомплектованность цеха высококвалифицированными и грамотными рабочими, владеющими несколькими профессиями, позволяет обеспечить бесперебойную работу сборочно-сварочного цеха.
В сборочно-сварочных цехах рабочие могут объединяться в комплексные бригады, создаваемые специально для выполнения сборочно-сварочных работ по заданной номенклатуре выпускаемой продукции. Например, бригада по сборке и сварке подкрановых балок; бригада по изготовлению ферм, бригада по изготовлению колонн, связей и т. п.
Необходимый количественный, профессиональный и квалификационный состав исполнителей таких бригад устанавливается при соблюдении следующих требований: соответствие состава исполнителей планируемым объемам, срокам и принятым методам производства работ; оптимальная загрузка рабочих; максимальная загрузка оборудования; соответствие характера работы разряду и квалификации работающих.
Заданный объем сборочно-сварочных работ своевременно и качественно может быть выполнен на современном предприятии, оснащенным напольным транспортом и радиоуправляемыми кранами, всем требуемым сборочно-сварочным оборудованием, инструментами и материалами, рабочими-исполнителями следующего состава: газорезчики; электросварщики ручной сварки; электрогазосварщики; электросварщики на автоматических и полуавтоматических машинах; контролеры сварочных работ и дефектоскописты; наладчики сварочного и газорезательного оборудования; слесари по сборке металлоконструкций. Своевременно и качественно работы будут выполнены, конечно, при наличии на предприятии подсобных рабочих, электриков, механиков и рабочих других профессий, которые поддерживают в рабочем состоянии все оборудование сборочно-сварочных цехов, обеспечивают бесперебойную подачу электроэнергии и технологических газов, обеспечивают благоприятные условия труда основных рабочих — нормальную работу вентиляции, отопления, хорошее освещение и т. п.
www.stroitelstvo-new.ru