Сварочные электроды: советы по выбору. Тугоплавкие электроды
ПЕРВАЯ ГРУППА. Электроды для получения наплавленного металла средней твёрдости со стойкостью при трении металла о металл и ударных нагрузках | ||||
Марка / тип электрода (тип металла)Область примененияТехнологические особенности | Род, полярность тока | Коэффициент наплавки, г/А×ч | Положение в пространстве | |
ОЗН -300М/11ГЗС | Б | ˜= ( + ) | 10,5 | |
Для деталей из углеродистых и низколегированных сталей, работающих в условиях трения и ударных нагрузок, например: валы, оси, автосцепки, крестовины и др. детали автомобильного и ж/д транспорта | ||||
ОЗН -400М/15Г4С | Б | ˜= ( + ) | 10,5 | |
То же, с увеличенной твердостью наплавленного металла | ||||
HP - 70 / Э-30Г2ХМ | Б | = ( + ) | 9,0 | |
Для деталей, работающих в условиях интенсивных ударных нагрузок и трения по металлу: рельсы, крестовины и другое | ||||
ЦНИИН - 4/ Э-65Х25Г13Н13 | Б | = ( + ) | 10,5 | |
Для заварки дефектов литья железнодорожных крестовин и других деталей из высокомарганцовистых сталей 110Г13Л | ||||
ВТОРАЯ ГРУППА. Электроды, обеспечивающие наплавленный металл с увеличенным содержанием углерода в низколегированном наплавленном слое при работе конструкций в условиях трения металла о металл и ударных нагрузках при нормальной и повышенной температурах | ||||
ЭН-60М / Э-70ХЗСМТ | Б | = ( + ) | 8,5 | |
Для штампов всех типов, работающих с нагревом контактных поверхностей до 400°С, и быстроизнашивающихся деталей в станочном оборудовании: шестерни, эксцентрики, направляющие и др. | ||||
ЦН -14 | Б | = ( + ) | 12,0 | |
Для оборудования горячей штамповки и резки, в том числе ножей, ножниц, штампов и др. | ||||
13 КН/ЛИВТ1Э-80Х4С | Б | ˜= ( + ) | 6,5 | |
Для зубьев ковшей экскаваторов, черпаков, земснарядов, ножей дорожных машин, работающих при абразивном износе без значительных ударов и давлений | ||||
ОЗШ-3 / Э- 37Х9С2 | Б | = ( + ) | 9,5 | |
Для обрезных и вырубных штампов холодной и горячей штамповки (до 650°С) и быстроизнашивающихся деталей машин и оборудования | ||||
ОЗИ-3 / Э- 20Х4М4ВФ | Б | = ( + ) | 9,5 | |
Для штампов холодного и горячего (до 650°С) деформирования металлов, а также для быстроизнашивающихся деталей горно-металлургического и станочного оборудования | ||||
ТРЕТЬЯ ГРУППА. Электроды для получения повышенных характеристик наплавленного углеродистого легированного металла, работающего в условиях ударно-абразивного износа, а также наплавки деталей из высокомарганцовистых сталей типа 110Г13Л | ||||
ОЗН 6 / 90Х4Г2С3Р | Б | = ( + ) | 11,0 | |
Для быстроизнашивающихся деталей горно-добывающих, строительных машин и др., работающих при интенсивном абразивном износе и значительных ударных нагрузках | ||||
ОЗН - 7 / 75Х5Г4СЗРФ | Б | = ( + ) | 12,0 | |
Для быстроизнашивающихся деталей преимущественно из высокомарганцовистых сталей 110Г13Л, работающих при интенсивном износе и при значительных ударных нагрузках | ||||
ВСН-6 / Э-110Х14В13Ф2 | П | = ( + ) | 9,5 | |
Для быстроизнашивающихся деталей из углеродистых и высокомарганцовистых сталей при значительных ударных нагрузках в условиях абразивного износа | ||||
Т-590 / Э- 320Х25С2ГР РОТЭКС Н (Т-590) | П | = ( + ) | 9,0 | |
Для деталей, работающих в условиях абразивного износа при умеренных ударных нагрузках | ||||
ЧЕТВЕРТАЯ ГРУППА. Электроды для конструкций, работающих в супертяжелых условиях при больших давлениях и высоких (до 680-850°С) температурах | ||||
ОЗШ-6 / 10Х33Н11М3СГ | Б | = ( + ) | 13,0 | |
Для бойков радиально-ковочных машин, штампов холодного и горячего (до 800-850°С) деформирования металлов, ножей горячей резки металла, быстроизнашивающихся деталей оборудования. работающих в тяжелых термодеформационных условиях | ||||
УОНИ-13/Н1-БК / Э-09Х31НВАМ2 | Б | = ( + ) | 10,5 | |
Для уплотнительных поверхностей арматуры, работающих в контакте со средами высокой агрессивности | ||||
ОЗИ-5 / Э-10К18В11М10ХЗСФ | П | = ( + ) | 10,5 | |
Для металлорежущего инструмента, штампов горячей (до 800-850°С) штамповки и деталей, работающих в особо тяжелых температурно-силовых условиях | ||||
ОЗИ-6 / 100Х4М8В2СФ | Б | = ( + ) | 10,0 | |
Для резцов и многолезвенного металлорежущего инструмента, а также для ремонта тяжелонагруженных штампов холодного и горячего (до 650°С) деформирования металла | ||||
ПЯТАЯ ГРУППА. Электроды, обеспечивающие получение высоколегированного наплавленного металла с высокой стойкостью в условиях коррозионно-эррозионного износа, трения металла о металл при больших давлениях и повышенных температурах | ||||
ЦН-6Л / Э-08Х17Н8С6Г | Б | = ( + ) | 14,0 | |
Для уплотнительных поверхностей деталей арматуры котлов, работающих при температуре до 570°С и давлении до 7800 МПа (780 кг/мм2) | ||||
ЦН-18 / Э-15Х15Н10С5М3Г | Б | = ( + ) | 11,0 | |
ЦН-24 | Б | = ( + ) | 12,0 | |
Для уплотнительных поверхностей арматуры, работающих в пароводяной среде при температуре: ЦН-18 - до 600°С; ЦН-24 -до 565°С | ||||
ШЕСТАЯ ГРУППА. Электроды для получения высоколегированного поверхностного слоя с высокой стойкостью в тяжелых коррозионноактивных и температурно-деформационных условиях (до 950-1100°С) в атомной энергетике и химическом машиностроении | ||||
ОЗШ-6 | Б | = ( + ) | 8,5 | |
Для кузнечно-штамповой оснастки холодного и горячего деформирования металлов, деталей металлургического и станочного оборудования, работающих в тяжелых условиях термической усталости (до 950°С) и больших давлений | ||||
ОЗШ-8 | Б | = ( + ) | 14,0 | |
Для кузнечно-штамповой оснастки горячего деформирования металла, работающего в сверхтяжелых условиях термической усталости (до 1100°С) и больших давлений | ||||
ЭА - 898 / 21Б / 09Х19Н9Г2Б1М | Б | = ( + ) | 10,5 | |
Для получения коррозионностойкого покрытия на поверхности изделий атомно-энергетического и химического машиностроения | ||||
ЭА-855 / 51 (ЭА-582/23) | Б | = ( + ) | 13,0 | |
То же, но для изделий, подвергаемых (не подвергаемых) термообработке |
weldering.com
Сварочные электроды: советы по выбору
Главная страница » Сварочные электроды: советы по выбору
От того, какие сварочные электроды применяются в процессе сварки, напрямую зависит не только скорость, комфортность сварочной работы, но и качество шва.
Если электрод низкого качества, хранился в непригодных для этого условиях, имеет просроченный срок годности, последствием этого станет выход из строя проваренного изделия раньше предназначенного ему срока. Конечно, лучше использовать материал, рекомендуемый компанией, которая производит используемое вами оборудование.
Качество сварочной проволоки является основой электрода, от её химического состава зависят характерные качества электрода. Существует порядка 500 разных видов покрытых и непокрытых, металлических и графитовых электродов. Для покрытых электродов характерен металлический стрежень, с нанесенной обмазкой из разных веществ, которые держатся скрепленными за счет клейкой массы.
Различные марки электродов отличны в своих характеристиках, способствующих достижению поставленных задач. С помощью электродов разных марок, покрытия и проволоки, работать можно со сталью и различными цветными металлами и сплавами.При работе с низколегированными сталями и сплавами используют нержавеющие электроды, покрытие которых может быть основным или смешанным.
Рутиловое покрытие – порошкообразный диоксид титана, способствующий усилению прочности шва и который стабилизирует горение. Электроды с таким покрытием имеют более высокую стоимость, но и ряд значительных преимуществ относительно других типов. При работе с рутиловыми электродами брызги металла меньше, а, следовательно, меньше и его потери.В ильменитовом покрытии используется диоксид титана и железа, образующих прочное соединение, отличающихся эластичностью.
Основное покрытие электродов – это карбонаты, а так же фтористые соединения. Такое сварочное соединение является пластичным, достаточно хорошо переносит изменения температуры среды, но для сварки деталей с ржавыми кромками не применяются.
Для процесса сварки и резки различных цветных металлов используют сварочные неплавящиеся электроды, изготовленные из материалов, процесс плавления которых происходит при высоких температурах. Как правило, в этих случаях, используют вольфрам с различными присадками: WP, WL-15, WZ-8.
Исходя из ГОСТ 9467-75, сварочные электроды по механическим свойствам металлического шва и сварного соединения, разделяются на несколько видов, каждому из которых соответствует несколько марок электродов, так к Э46 относят марки такие как АНО-4, ОЗС-6, АНО-3, МР-3, и пр. Марка электрода определена составом покрытия, маркой стрежня, определенными технологическими свойствами и свойствами металлического шва.
Все, что Вы хотели знать о сварочных электродах.
Электрод сварочный- это стержень из хорошо электропроводного материала, чаще изготовленный из метала. Основной задачей его является подвод тока к изделию, которое подлежит свариванию. На сегодняшний день выпускается огромное количество электродов, под различными марками. Большая часть из них предназначены для дуговой ручной сварки.
Электроды сварочные принято делить на неплавящиеся и плавящиеся. Неплавящиеся изготавливают из тугоплавких материалов, чаще это вольфрам. Синтетический графит и электротехнический уголь. Плавящиеся производят из углеродистой, высоколегированной или легированной сварочной проволоки. В обоих видах методом опрессовки, наносят под давлением на металлический стержень слой защитного покрытияЕще в 1881 году, в эксперименте, впервые был использован электрод при испытаниях электрической дуги, русским ученым Бенардос Николаем Николаевичем.
На сегодняшний день существует огромное разнообразие различных электродов. Их, по техническим паспортам и условиям, подразделяют на марки, не регламентированные стандартами. Но, тем не менее, можно выделить две группы электродов, которые подразделяют на подгруппы. Это неметаллические и металлические.
Неметаллические электроды бывают графитовыми и угольными, оба подкласса неплавящиеся. Металлические же, подразделяются на неплавящиеся (лантанированные, торированные, итрированные и вольфрамовые) и плавящиеся. Плавящиеся, в свою очередь, подразделяют на покрытые (алюминиевые, чугунные, бронзовые, стальные, медные и т.д.) и непокрытые (на сегодняшний день это непрерывная проволока, для сварки в газовой среде).
По назначению электроды сварочные бывают для:
- 1. Сварки низколегированных и углеродистых сталей с сопротивлением разрыву до 60 кгс/мм²,
- Маркируют буквой У.
- 2. Сварки легированных сталей с сопротивлением больше 60 кгс/мм², маркировка Л
- 3. Сварки сталей с высокой теплоустойчивостью. Маркировка Т
- 4. Сварки сталей с особыми свойствами. Маркировка В
- 5. Для наплавки слоев с особыми свойствами. Маркировка Н
Согласно стандартов, электроды делят на типы, в зависимости от механических свойств и состава наплавленного метала. Цифры, которые обозначают каждый из типов, показывают минимальное временное сопротивление разрыву.
По толщине покрытия электроды разделяют на:
- 1. с тонким покрытием (диаметр электрода/ диаметр покрытия < 1,2). Маркировка — М;
- 2. средним покрытием (диаметр электрода/ диаметр покрытия < 1,45). Маркировка – С
- 3. толстым покрытием (диаметр электрода/ диаметр покрытия < 1,8). Маркировка – Д
- 4. особо толстым покрытием (диаметр электрода/ диаметр покрытия >1,8). Маркировка – Г
По типу покрытия электроды бывают с кислым (А), основным (Б), целлюлозным (Ц), рутиловым (Р) покрытиями, также выделяют смешанные виды покрытий (маркируют двумя буквами), прочие виды (П).
Покрытые электроды, по конструкции, являются стержнями длиной 250 – 450 мм. Изготавливаются из сварочной проволоки с нанесенным поверх покрытием. Один из концов электрода не покрыт обмазкой, для возможности крепления в держателе сварочного аппарата.
Покрытия для электродов подразделяют на защитные и магнитные.Виды покрытий: рутиловые, фтористо – кальциевые, руднокислые, органические.
weldelec.com
Как выбрать электроды для сварки?
Июнь 8, 2017
Прочное и надёжное соединение металлов зависит от многих факторов, главным из которых считается соответствие электрода и свариваемых заготовок. До того как выбирать электроды для сварки, нужно определить химический состав деталей, поскольку это поможет подобрать оптимальное сочетание покрытого изделия и заготовок. Также очень важен правильный выбор обмазки, которая наносится на электрод и является одновременно флюсом с легирующими добавками. Это покрытие существенно влияет на сварочный процесс и его верный выбор применительно к конкретным материалам обеспечивает наилучшие показатели прочности и долговечности сварного соединения.
Сварочные аппараты и подбор плавящихся электродов
При квалифицированном подборе режима сварки нужно обязательно учитывать параметры сварочного агрегата, дающие возможность использовать лучшие электроды и наиболее предпочтительные условия для сплавления деталей. Существуют несколько видов сварки, с использованием плавящихся покрытых изделий, неплавящихся вольфрамовых или полуавтоматических способов подачи с применением проволоки с особыми свойствами.Аппаратура для сварки подразделяется на следующие виды:
- понижающий трансформатор переменного тока или с выпрямляющим контуром постоянного тока;
- инверторный аппарат постоянного тока;
- аппарат с применением инвертора, с тугоплавким вольфрамовым электродом и ручной подачей сварочной проволоки в зону расплава;
- полуавтоматический агрегат с подачей проволоки в зону сварочного шва.
У каждого из аппаратов есть технические свойства по силе тока и напряжению, которые и диктуют подбор продукции соответствующего диаметра и состава покрытия. Необходимо отметить, что проволока, которая является электродом при полуавтоматической и ручной подаче в зону плавления, тоже служит цели наилучшего соответствия составу свариваемых деталей. Выбор электродов зависит от способа сварки прямым или обратным подключением напряжения, поскольку глубина проваривания связана с полярностью и от этого напрямую зависит подбор диаметра.
Покрытие стержня, а также состава проволоки служит для реализации определённых задач:
- использование оксидов углерода защищает сварочную ванночку от действия атмосферного кислорода;
- облегчает розжиг и стабилизирует дуговой разряд;
- способствует удалению кислорода из зоны расплава, раскисляя шов;
- с помощью примесей оказывает легирующее воздействие на шов.
Именно эти требования служат определяющими факторами выбора хороших покрытых электродов при выполнении конкретных задач. Российская промышленность производит большой сортамент изделий для сварки различных металлов и сплавов. Для бытовых целей необходимо выбирать приоритетные материалы для сварки. Как правило, это сваривание чёрных металлов, чугуна, нержавеющих сталей и сплавов алюминия и меди. Иногда, прибегают к сварке разнородных по составу заготовок и здесь, следует выбирать электрод с наиболее близкими параметрами к основному составу деталей.
Важно обеспечить чистоту стыка от оксидного слоя, поскольку всевозможные загрязнения создают непрочный, пористый шов, а это отрицательно сказывается на качестве.
Популярные виды электродов
Производятся различные виды продукции для сварки, которые выбираются с учётом особенностей соединяемых материалов и способов сварки. В случае аргонодуговой сварки используется тугоплавкий вольфрамовый стержень, а в зону расплава вручную подаётся проволока. При работе с применением полуавтоматов электродом для инверторной сварки служит проволока разного состава, подаваемая через горелку с регулируемой скоростью. Самым распространённым способом является использование штучных плавящихся электродов, толщина покрытия которых бывает особо толстой (Г), тонкой (М), средней (С) и толстой (Д).
Выбор толщины обмазки сварщиком создаёт условия для изменения степени воздействия на шов для его защиты от влияния кислорода воздуха, следов загрязнений и оксидного слоя. По составу покрытия электроды подразделяются таким образом:
- основного вида для сварки постоянным током и получения пластичного шва;
- тип с кислым покрытием для обеспечения тягучести металла в зоне сварочной ванночки;
- стойкость к ударным воздействиям придаёт целлюлозное покрытие, эти изделия используются также на вертикальном шве;
- рутиловое покрытие способствует устойчивому розжигу дуги;
- специальные электроды для сварки меди и алюминия, а также их сплавов.
При выборе изделия нужно учитывать толщину и состав заготовок, сварочный ток и диаметр электрода, эти параметры необходимо увязывать с характеристиками аппарата. Для сварки стали толщиной 1 мм выбирают электроды диаметром от 1,2 до 2 мм, при этом необходим ток силой 45−55 А. Для заготовок толщиной 2 мм, требуется диаметр 2,5 мм и ток силой 60−80 А, детали от 3 до 5 мм нуждаются в использовании диаметра от 3 до 4 мм и тока от 70 до 130 А. Более толстые заготовки сваривают электродом 5 мм и током 210 А и выше. К наиболее популярным, особенно у новичков, изделиям относятся стержни с рутиловым и основным покрытием, хотя во многом выбор зависит от состава свариваемого материала.
Важно помнить, что материал покрытия чувствителен к содержанию влаги, поэтому стержни перед сваркой необходимо прокаливать, а хранить их нужно в сухом проветриваемом месте.
Основное покрытие электродов марки УОНИ позволяет вести инверторную сварку, как в прямой, так и в обратной полярности, а рутиловая марка МР-3 даёт возможность использовать переменный и постоянный токи и характерна лёгким розжигом дуги.
Свариваемые металлы и выбор электродов
Для качественной сварки необходим определённый опыт, а также знание химического состава заготовок. Поэтому прежде чем выбрать сварочные электроды, нужно выяснить какой именно металл или сплав вы собираетесь соединять. Для разных видов металлов разработаны соответствующие изделия с разным видом покрытия и многие из них являются аналогами. Здесь может помочь различная справочная литература, консультация профессионалов в области продаж или опытных специалистов. В большинстве случаев работают с углеродистыми, нержавеющими сталями, чугуном и сплавами меди и алюминия. Довольно популярна сварка оцинкованной стали, разнородных заготовок и никелированных частей.Высокая прочность и долговечность шва достигается точным подбором материала плавящегося электрода и его покрытия к соединяемому металлу или сплаву и заключается в следующих рекомендациях:
- конструкционные низколегированные, углеродистые стали весьма хорошо свариваются с использованием марок МР-3М, УОНИ-13/55, ОМА-2, ОЗС-30, ВИ-10-6, АНО-21 и ВСФ-65У;
- стали высокопрочные легированные свариваются с применением ЭА-981/5, ЭА-395/9, НИАТ-5, ОШЗ-1 и НИАТ-3М;
- жаропрочные сплавы и теплоустойчивую сталь соединяют марками ЦЛ-39, АНЖР-2, ТМЛ-3У, ОЗЛ-35, ИМЕТ-10 и КТИ-7А;
- для коррозионностойких и нержавеющих материалов подходят электроды ИЖ-15С, НИАТ-1, УОНИ-13НЖ, ЦТ-15 и ЭА-400/10Т;
- детали из разнородных по составу материалов сваривают марками АНЖР-2, ЭА-391/15, ВИ-ИМ-1, ЦТ-28, ОЗЛ-32, НИИ-48Г, ИМЕТ-10, В-56У и;
- для спецсталей используются марки ОЗЛ-44, АНВ-20, ЭА-112/15 и НИИ-48Г;
- для заготовок из чугуна используют ЦЧ-4, ОЗЖН-1, ОЗЧ-2 и МНЧ-2;
- алюминиевые сплавы сваривают с использованием ОЗА-1, ОЗА-2, ОЗАНА-1, ОЗАНА-2;
- медь и её соединения варят с применением АНЦ/ОЗМ-2, ОЗБ-3, Комсомолец-100, для бронзы подходят ОЗБ-2М;
- для сплавов никеля подходят ОЗЛ-32 и В-56У;
- для резки металла пользуются марками АНР-2М, ОЗР-2 и ОЗР-1.
В условиях отсутствия рекомендуемых изделий следует определить возможные аналоги, наиболее подходящие к конкретным условиям, но важно понимать, что качество шва может несколько понизиться.
При сварке тонкостенных листов иногда бывает необходимо сменить полярность на обратную для того, чтобы понизить глубину провара и избавиться от риска прожигания заготовок. В таком случае прибегают к инверторной сварке высокочастотным, импульсным переменным током.
Итог
Мы рассказали об основных принципах выбора покрытых электродов для сварки с применением различных аппаратов. Необходимо учитывать при подборе марки тип покрытия и диаметр стержней, силу тока и состав деталей. С приобретением некоторого опыта и навыков, эффективная работа не вызовет затруднений.
electrod.biz
Электродуговая сварка
Электродуговая сварка — высокопроизводительный метод металлообработки, позволяющий эффективно работать с металлами повышенной толщины. Мы осуществляем сварку как плавким, так и тугоплавким электродом.Электродуговая сварка тугоплавким электродом
Электродуговая сварка металлов в среде газов тугоплавким электродом (GTAW или TIG-процесс) характеризуется дугой, возникающей между вольфрамовым стержнем (вольфрам, легированным торием) и рабочей поверхностью, с последующим расплавлением металла и формированием сварного шва. Инертный газ (смесь газов) подбирается с учетом свойств базовой поверхности, выполняет защитную функцию, вытесняя воздух из зоны сварочных работ, и улучшает качество соединения.Особенности, сфера применения электродуговой сварки тугоплавким электродом
Электродуговую сварку металлов повышенной толщины тугоплавким электродом выполняют с применением присадочного материала: неизолированного прута, проволоки в бухте (для автоматического цикла). Обработка цветных металлов и легированных сталей незначительной толщины (0,5-4 мм) возможна без ввода присадочного прута (проволоки). Сварка вольфрамовым электродом в экранирующей среде аргона — основной вид обработки титана, алюминия, нержавеющей стали; заготовок в виде трубного проката. Для улучшения характеристик сварного шва используют защитную смесь аргона с кислородом (3-5%).Технология
Ручная подача горелки с вольфрамовым электродом и присадочного прута в рабочую зону. Автоматическая подача электрода и присадочной проволоки к месту формирования сварного соединения.Преимущества электродуговой сварки тугоплавким электродом
- Узкая зона плавления. Концентрированный источник нагрева.
- Стабильная электродуга. Надежная изоляция рабочей зоны защитным инертным газом.
- Мало пористый шов высокого качества. Спокойная сварочная ванна без брызг, контроль глубины плавления металла на всех стадиях сварочного цикла.
- Экономичность. Слабый износ электрода, отсутствие этапа финишной обработки швов.
- Соединение разнородных металлов без нарушения их внутренней структуры.
- Бесшумность.
Электродуговая сварка плавким электродом
Электродуговая сварка плавким электродом (GMAW,MIG) характеризуется дугой, сформированной между рабочей плоскостью из металла и проволочным электродом (автоматическая подача) в среде экранирующих газов. Преимущества электросварки легко плавящимся электродом:- высокая скорость и производительность процесса,
- прочность сварного шва,
- возможность сварки в один проход металлов толщиной до 250 мм,
- сварка в узкий зазор («в лодочку»),
- этап подготовки свариваемых кромок отсутствует.
Особенности
Непрерывное расплавление проволочного электрода препятствует образованию окислов и принципиально улучшает качество шва при сварке металлов электродуговым способом. Принцип образования электродуги позволяет регулировать ее длину и влиять на интенсивность процесса сварки. В качестве экранирующей смеси применяются: аргон с кислородом (2%), аргон с углекислым газом (3%). Скорость электродуговой сварки плавким электродом возможно увеличить введением в защитную газовую среду водорода и гелия. Принципиальные отличия электродуговой сварки легко плавящимся электродом от прочих видов сварочных работ:- электротоки повышенной плотности (порядка 90-200 А/мм2),
- высокая температура сварочной дуги,
- ярко выраженная плавкость проволочного электрода (около 8 мм/мин.),
- автоматизированная подача проволоки-электрода (полуавтоматический или автоматический цикл),
- использование защитных газов в зоне сварки,
- процессы окисления в сварочной ванне незначительны.
Нормативная документация
ГОСТ 14771-76. Сварка электродуговая в защитных газах. ГОСТ 5264-80. Ручная дуговая сварка. Конструктивные элементы, типы сварных соединений. ОСТ 26-291-79. Электродуговая сварка. Электроды. ГОСТ 11534-75. Электродуговая сварка (ручная). Конструкция соединений. ГОСТ 11533075. Электродуговая сварка (автоматическая, полуавтоматическая). Конструкция соединений. ГОСТ 9467-75, ГОСТ 9466-75. Электроды, присадочные материалы для электродуговой сварки. ГОСТ 14806-80. Электродуговая сварка алюминия.vsk-service.ru
Тугоплавкое покрытие - Большая Энциклопедия Нефти и Газа, статья, страница 1
Тугоплавкое покрытие
Cтраница 1
Тугоплавкие покрытия применяются для защиты таких элементов конструкции, которые в процессе работы не должны изменять своей формы и размеров. К таким элементам относится, например, горловина сопла ракетного двигателя. [1]
Кроме тугоплавких покрытий, широкое применение в технике получили теплозащитные материалы, которые разрушаются в процессе их взаимодействия с горячим газовым потоком. [2]
Станок предназначен для нанесения тугоплавких покрытий ( вольфрама, молибдена, окиси алюминия, двуокиси циркония) па внутренние и наружные поверхности изделий, имеющих форму тел вращения. [3]
Особенно это относится к тугоплавким покрытиям, наиболее существенно и принципиально изменяющим свойства всего материала в целом; глубина этого изменения определяется и методом нанесения. [4]
Рекомендуется применять электроды с тугоплавким покрытием. [6]
Сварка производится электродами с тугоплавким покрытием, которое при плавлении дает на конце небольшой козырек. [7]
В настоящее время для нанесения тугоплавких покрытий разрабатывают и используют следующие методы: диффузионные ( осуществляемые в вакууме, газовых средах, расплавленных средах, по типу твердофазных взаимодействий), плазменные, детонационные, комбинированные. Из указанных методов трудно отдать предпочтение какому-либо одному, так как каждый из них специфичен, обладает характерными технологическими особенностями и обеспечивает требуемые плотность, структуру, прочность удержания покрытия. Так, плазменные покрытия позволяют получать лишь сильно пористые слои, без дополнительной термообработки плохо удерживаемые на поверхности изделий, но зато предоставляющие возможность импрегнирования какими-либо веществами, придающими покрытию особую техническую ценность, например могут пропитываться сухими смазками для создания повышенной антифрикционности. Для детонационных покрытий, наоборот, характерны высокие плотность и прочность удержания на изделии при обычно тонком слое покрытия. Пожалуй, наиболее универсальным сочетанием свойств отличаются термодиффузионные покрытия, наносимые различными методами и из разных насыщающих сред. Этот метод также наиболее изучен, давно и с успехом используется в машиностроении. [8]
Рассматриваются некоторые свойства, определяющие области применения различных тугоплавких покрытий, нанесенных ва углеродные материалы плазменным напылением, газофазным, химическим и электрохимическим методами. Показано, что покрытие из двуокиси циркония, получаемое путем нанесения на графит методом аргоно-дуговой наплавки циркония и окислением последнего в кислороде, отличается высокой термостойкостью, определяемой металлическими прожилками циркония в двуокиси, а также наличием пластичного металлического слоя, демпфирующего напряжения, возникающие в окисной плевке при эксплуатации. Метод газофазного осаждения может быть использован для нанесения различных тугоплавких покрытий как на графитовые изделия, так и в качестве барьерных на углеродные волокна; при этом толщина покрытия определяется его назначением. [9]
Представим однослойную стенку, не имеющую изоляционных или тугоплавких покрытий. Стенка окружена с обеих сторон холодным газом, допустим, воздухом с температурой Г0 293 К и имеет такую же температуру по всей толщине. [11]
В книге рассмотрены методы и технологические схемы получения тугоплавких покрытий на деталях машин и механизмов. Приведены данные о физических и физико-технических свойствах и обобщен опыт использования тугоплавких покрытий в металлургии, машино - и приборостроении, различных областях новой техники. [12]
В данной главе будут приведены в основном практические примеры нанесения тугоплавких покрытий только методами плазменного и детонационного напыления, поскольку газопламенный метод имеет меньшие технические возможности и перспективы использования для напыления качественных высокотемпературных покрытий. [13]
Содержится в выбросах производств абразивов, сталелитейных, керамики, тугоплавких покрытий на металлах. [14]
Он плавится при температуре около 2000 С, служа надежной защитой тугоплавкого покрытия от окисления. [15]
Страницы: 1 2 3 4
www.ngpedia.ru
Неплавящиеся электродыВольфрамовые электроды. При ручной дуговой сварке в аргоне и плазменной резке широко используются вольфрамовые электроды. Это объясняется прежде всего тугоплавкостью вольфрама и высокой его электро- и теплопроводностью. Температура плавления вольфрама 3500°С, а кипения 5900°С. Вольфрамовые электроды имеют диаметры 0,8—8 мм. Для повышения стойкости электрода, облегчения возбуждения и повышения стабильности горения сварочной дуги применяют электродные стержни не из чистого вольфрама, а с добавлением около 2% тория или лантана и циркония. Наличие тория позволяет значительно повысить плотность тока. Окись тория добавляют перед формовкой и спеканием электрода, а цирконий наносят на поверхность электрода. Однако из-за токсичности окиси тория широко используются лантанированные электроды. Вольфрамовые электроды с присадкой 1—2% окиси лантана имеют высокие технологические характеристики и по своим свойствам подобны ториро-ванному вольфраму. Введение 1—2% окиси лантана в вольфрамовый электрод диаметром 4 мм позволяет увеличить допустимую силу тока на 20—30% и в 10 раз уменьшить расход электродов по сравнению с чистым вольфрамом. Стойкость электрода повышается также при шлифовке его поверхности. Кроме указанных применяются еще электроды из иттрированного вольфрама. Графитовые электроды по сравнению с угольными имеют большую электропроводность и стойкость против окисления при высоких температурах. Это позволяет вести сварку на токах повышенной плотности и снизить расход электродов. Для увеличения стойкости электроды покрывают слоем меди толщиной 0,06—0,07 мм. Электроды имеют круглую форму, конец затачивается на конус. Длина электрода 200—300 мм, диаметр 5— 25 мм. Для стабилизации горения дуги применяют электроды с каналом, заполненным порошкообразными легкоионизирующимися веществами. Канал располагается по центру электрода. Для поверхностной резки наряду с круглыми применяют пластинчатые электроды. — Вольфрамовые электроды применяют при сварке дуговой в инертных газах, атомно-водородной, плазменной, а также при резке и наплавке. Для предупреждения окисления вольфрамовые электроды используют только при защите области дуги инертным газом. Вольфрам — это тугоплавкий металл с температурой плавления 4500 °С и температурой кипения 5900 °С, обладающий высокой тепло- и электропроводностью. Высокие тепло-физические свойства обусловили широкое распространение вольфрамовых электродов для сварки. Добавка к вольфраму окислов лантана, тория, тантала и иттрия снижает эффективный потенциал ионизации, в результате чего облегчается зажигание дуги; увеличивается устойчивость дугового разряда, повышается стойкость электрода, что позволяет значительно повысить плотность тока, так как при этом конец электрода не изменяет формы в процессе сварки. Электроды из чистого вольфрама обычно служат для сварки на переменном токе, а электроды с активирующими добавками — для сварки на переменном и постоянном токе прямой и обратной полярности. Применяют электроды марок ЭВЧ (чистый вольфрам), ЭВЛ-10 и ЭВЛ-20 (с присадкой окиси лантана), ЭВТ-35 (с присадкой окиси тория) и ЭВИ-30 (с присадкой окиси иттрия и металлического тантала). Цифры в марке электрода означают количество активирующей присадки в десятых долях процента. Изготовляют электроды диаметром 0,2—12 мм и длиной 75, 140 и 170 мм. Наилучшие сварочные характеристики имеют электроды с присадкой 3 % окиси иттрия. Итти-рованные электроды по сравнению с торированными и лантинированными дают возможность работать на токах относительно большой плотности при меньшем расходе вольфрама. Расход электродов из чистого вольфрама значительно больше, чем из вольфрама с активирующими присадками. Чтобы уменьшить расход электродов, инертный газ следует начать подавать до включения сварочного тока, а прекращать после выключения тока и охлаждения электрода до его потемнения. Расход электродов составляет 0,04—0,07 г на 1 м сварного шва. Для сварки на постоянном токе конец электрода следует затачивать на конус, а на переменном — в виде сферы. Длина заточки должна быть равна 2— о диаметрам электрода. Работу с электродами с присадкой, окиси тория, их транспортировку и хранение необходимо выполнять в соответствии с санитарными правилами работы с радиоактивными веществами. Угольные и графитовые электроды. Электроды изготовляют из электротехнического угля или синтетического графита. Они имеют высокую температуру плавления и кипения при малой теплопроводности. Электроды выпускают в виде цилиндрических стержней диаметром 5— 25 и длиной 200—300 мм. Конец электрода затачивают на конус. Электроды должны иметь правильную форму и гладкую поверхность без трещин. Электрод хорошего качества создает при ударе по нему чистый металлический звук, не оставляет на бумаге следов. Для улучшения свойств угольные электроды подвергают графитиро-ванию термической обработкой при 26’00 °С, они чище по химическому составу, более мягки, серого с металлическим блеском цвета. Электропроводность графитовых электродов почти в 3 раза больше угольных, они обладают большей стойкостью против окисления на воздухе, при больших температурах, что заметно снижает расход электродов и позволяет применять токи повышенной плотности. Для увеличения стойкости электродов их покрывают слоем меди толщиной 0,06—0,07 мм. Для стабилизации положения дуги применяют угольные электроды с фитилем, представляющим расположенный по центру электрода канал, заполненный порошкообразной массой, содержащей легкоионизируемые вещества. Ток к угольным и графитовым электродам подводят с помощью электрододержателей. Читать далее:Сварочные флюсыСварочные электродыОбщие сведения о сварке арматурыПротивопожарные мероприятия при сваркеБезопасность труда при сварке технологических трубопроводовБезопасность труда при сварке строительных металлических и железобетонных конструкцийЗащита от поражения электрическим током при сваркеТехника безопасности и производственная санитария при сваркеУправление качеством сваркиСтатистический метод контроля |
stroy-server.ru
Виды электродов по типу покрытия
Основной параметр, по которому производится разделение электродов на различные виды – это тип покрытия. Давайте попробуем разобраться во всем этом разнообразии электродов, которые решают абсолютно разные задачи.
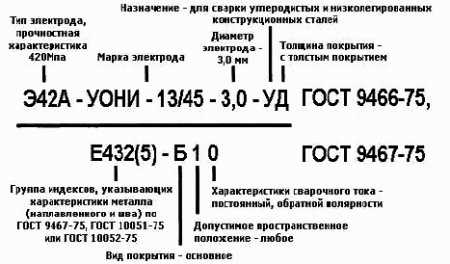
Кроме статьи "Виды электродов по типу покрытия" смотрите также:
nanolife.info