Большая Энциклопедия Нефти и Газа. Зажимное приспособление
Зажимные элементы приспособлений
Назначение зажимных приспособлений – это обеспечение надежного контакта заготовки с установочными элементами и предотвращение смещения и вибрации ее в процессе обработки. На рис.7.6 представлены некоторые виды зажимных устройств.
Требования к зажимным элементам:
- надежность в работе;
- простота конструкции;
- удобство обслуживания;
- не должны вызывать деформацию заготовок и порчу их поверхностей;
- не должны сдвигать заготовку в процессе ее закрепления с установочных элементов;
- закрепление и открепление заготовок должно производиться с минимальной затратой труда и времени;
- зажимные элементы должны быть износостойкими и по возможности сменными.
Виды зажимных элементов:
Зажимные винты, которые вращают ключами, рукоятками или маховичками (см. рис. 7.6)
Рис.7.6 Виды зажимов:
а – зажимной винт; б – винтовой прихват
Быстродействующие зажимы, показанные на рис. 7.7.
Рис.7.7. Виды быстродействующих зажимов:
а – с разрезной шайбой; б – с плунжерным устройством; в – с откидным упором; г – с рычажным устройством
Экцентрированные зажимы, которые бывают круглые, эвольвентные и спиральные (по спирали Архимеда) (рис.7.8).
Рис.7.8. Виды экцентриковых зажимов:
а – дисковый; б – цилиндрический с Г-образным прихватом; г – конический плавающий.
Клиновые зажимы – используется эффект расклинивания и применяется как промежуточное звено в сложных зажимных системах. При определенных углах клиновой механизм обладает свойством самоторможения. На рис. 7.9 изображена расчетная схема действия сил в клиновом механизме.
Рис. 7.9. Расчетная схема сил в клиновом механизме:
а- односкосном; б – двухскосном
Рычажные зажимы применяются в сочетании с другими зажимами, образуя более сложные зажимные системы. С помощью рычага можно изменить как величину, так и направление усилия зажатия, а также осуществлять одновременное и равномерное закрепление заготовки в двух местах. На рис. 7.10 показана схема действия сил в рычажных зажимах.
Рис. 7.10. Схема действия сил в рычажных зажимах.
Цанги представляют собой разрезные пружинные гильзы, разновидности которых показаны на рис.7.11.
Рис. 7. 11. Виды цанговых зажимов:
а – с натяжной трубкой; б – с распорной трубкой ; в – вертикального типа
Цанги обеспечивают концентричность установки заготовки в пределах 0,02…0,05 мм. Базовую поверхность заготовки под цанговые зажимы следует обрабатывать по 2…3 классам точности. Цанги выполняют из высокоуглеродистых сталей типа У10А с последующей термообработкой до твердости HRC 58…62. Угол конуса цанги d = 30…400 . При меньших углах возможно заклинивание цанги.
Разжимные оправки, виды которых изображены на рис. 7.4.
Роликовый замок (рис.7.12 )
Рис. 7.12. Виды роликовых замков
Комбинированные зажимы – сочетание элементарных зажимов различного типа. На рис. 7.13 представлены некоторые виды таких зажимных устройств.
Рис. 7.13. Виды комбинированных зажимных устройств.
Комбинированные зажимные устройства приводятся в действие вручную или от силовых устройств.
Направляющие элементы приспособлений
При выполнении некоторых операций механической обработки (сверления, растачивания) жесткость режущего инструмента и технологической системы в целом оказывается недостаточной. Для устранения упругих отжимов инструмента относительно заготовки применяют направляющие элементы (кондукторные втулки при расточке и сверлении, копиры при обработке фасонных поверхностей и т.д. (см. рис.7.14).
Рис.7.14. Виды кондукторных втулок:
а – постоянные; б – сменные; в – быстросменные
Направляющие втулки изготавливают из стали марки У10А или 20Х с закалкой до твердости HRC 60…65.
Направляющие элементы приспособлений - копиры – применяются при обработке фасонных поверхностей сложного профиля, задача которых направлять режущий инструмент по обрабатываемой поверхности заготовки для получения заданной точности траектории их движения.
Зажимные устройства станков - Металлорежущие станки
Зажимные устройства станковКатегория:
Металлорежущие станки
Зажимные устройства станковПроцесс питания станков-автоматов заготовками осуществляется при тесном взаимодействии загрузочных устройств и автоматических зажимных приспособлений. Во многих случаях автоматические зажимные устройства являются элементом конструкции станка или его неотъемлемой принадлежностью. Поэтому, несмотря на наличие специальной литературы, посвященной зажимным приспособлениям, представляется необходимым вкратце остановиться на некоторых характерных конструкциях,
Подвижные элементы автоматических зажимных приспособлений получают движение от соответствующих управляемых приводов, в качестве которых могут быть использованы механические управляемые приводы, получающие движение от основного привода рабочего органа или от независимого электродвигателя, кулачковые приводы, гидравлические, пневматические и пневмогидравлические приводы. Отдельные подвижные элементы зажимных приспособлений могут получать движение как от общего, так и от нескольких независимых приводов.
Рассмотрение конструкций специальных приспособлений, которые в основном определяются конфигурацией и размерами конкретной обрабатываемой детали, не входит в задачи настоящей работы, и мы ограничимся ознакомлением с некоторыми зажимными приспособлениями широкого назначения.
Зажимные патроны. Имеется большое число конструкций самоцентрирующих патронов в большинстве случаев с поршневым гидравлическим и пневматическим приводом, которые применяются на токарных, револьверных и шлифовальных станках. Эти патроны,, обеспечивая надежный зажим и хорошее центрирование обрабатываемой детали, имеют небольшой расход кулачков, из-за чего при переходе от обработки одной партии деталей к другой патрон необходимо перестраивать и для обеспечения высокой точности центрирования обрабатывать центрирующие поверхности кулачков на месте; при этом закаленные кулачки шлифуются, а сырые — обтачиваются или растачиваются.
Одна из распространенных конструкций зажимного патрона с пневматическим поршневым приводом представлена на рис. 1. Пневматический цилиндр закрепляется с помощью промежуточного фланца на конце шпинделя. Подвод воздуха к пневматическому цилиндру осуществляется через буксу, сидящую на подшипниках качения на хвостовике крышки цилиндра. Поршень цилиндра связан штоком с зажимным механизмом патрона. Пневматический патрон прикрепляется к фланцу, установленному на переднем конце шпинделя. Головка, закрепленная на конце штока, имеет наклонные пазы, в которые входят Г-образные выступы кулачков. При перемещении головки вместе со штоком вперед кулачки сближаются, при движении назад — расходятся.
На основных кулачках, имеющих Т-образные пазы, закрепляются накладные кулачки, которые устанавливаются в соответствии с диаметром зажимаемой поверхности обрабатываемой детали.
Благодаря небольшому числу промежуточных звеньев, передающих движение кулачкам, и значительным размерам трущихся поверхностей патроны описанной конструкции обладают сравнительно высокой жесткостью и долговечностью.
Рис. 1. Пневматическии зажимный патрон.
В ряде конструкций пневматических патронов используются рычажные передачи. Такие патроны обладают меньшей жесткостью и вследствие наличия ряда шарнирных соединений изнашиваются быстрее.
Вместо пневматического цилиндра может быть использован пневмо-мембранный привод или гидравлический цилиндр. Вращающиеся вместе со шпинделем цилиндры, особенно при высоком числе оборотов шпинделя, требуют тщательной балансировки, что является недостатком данного варианта конструкции.
Поршневой привод может быть установлен неподвижно соосно со шпинделем, а шток цилиндра связан с зажимным штоком муфтой, обеспечивающей свободное вращение зажимного штока вместе со шпинделем. Шток неподвижного цилиндра может быть связан с зажимным штоком также системой промежуточных механических передач. Такие схемы применимы при наличии самотормозящихся механизмов в приводе зажимного приспособления, так как в ином случае шпиндельные подшипники будут нагружаться значительными осевыми усилиями.
Наряду с самоцентрирующими патронами применяются также двух-кулачковые патроны со специальными кулачками, получающими движение от указанных выше приводов, и специальные патроны.
Подобные же приводы используются при закреплении деталей на различных разжимных оправках.
Цанговые зажимные устройства. Цанговые зажимные устройства являются элементом конструкции револьверных станков и токарных автоматов, предназначенных для изготовления деталей из прутка. Вместе с тем они находят широкое применение и в специальных зажимных приспособлениях.
Рис. 2. Цанговые зажимные устройства.
В практике встречаются цанговые зажимные устройства трех типов.
Цанга, имеющая несколько продольных надрезов, центрируется задним цилиндрическим хвостом в отверстии шпинделя, а передним коническим — в отверстии колпака. При зажиме труба перемещает цангу вперед и ее передняя коническая часть входит в коническое отверстие колпака шпинделя. При этом цанга сжимается и зажимает пруток или обрабатываемую деталь. Зажимное устройство данного типа имеет ряд существенных недостатков.
Точность центрирования обрабатываемой детали в значительной мере определяется соосностью конической поверхности колпака и оси вращения шпинделя. Для этого необходимо достигнуть соосности конического отверстия колпака и его цилиндрической центрирующей поверхности, соосности центрирующего буртика и оси вращения шпинделя и минимального зазора между центрирующими поверхностями колпака и шпинделя.
Так как выполнение указанных условий представляет значительные трудности, то цанговые устройства данного типа не обеспечивают хорошего центрирования.
Кроме того, в процессе зажима цанга, перемещаясь вперед, захватывает пруток, который перемещается при этом вместе с цангой, что может
привести к изменению размеров обрабатываемых деталей по длине и к появлению больших давлений на упор. В практике имеют место случаи, когда вращающийся пруток, прижатый с большой силой к упору, приваривается к последнему.
Достоинством данной конструкции является возможность использования шпинделя малого диаметра. Однако, поскольку диаметр шпинделя в значительной мере определяется другими соображениями и в первую очередь его жесткостью, то данное обстоятельство в большинстве случаев не имеет существенного значения.
Вследствие указанных недостатков данный вариант цангового зажимного устройства находит ограниченное применение.
Цанга имеет обратный конус, и при зажиме материала труба втягивает цангу в шпиндель. Данная конструкция обеспечивает хорошее центрирование, так как центрирующий конус расположен непосредственно в шпинделе. Недостатком конструкции является перемещение материала вместе с цангой в процессе зажима, что приводит к изменению размеров обрабатываемой детали, однако не вызывает никаких осевых нагрузок на упор. Некоторым недостатком является также слабость сечения в месте резьбового соединения. Диаметр шпинделя увеличивается незначительно по сравнению с предыдущим вариантом.
Вследствие отмеченных достоинств и простоты конструкции данный вариант находит широкое применение на револьверных станках и многошпиндельных токарных автоматах, шпиндели которых должны иметь минимальный диаметр.
Вариант, показанный на рис. 2, в, отличается от предыдущего тем, что в процессе зажима цанга, упирающаяся передней торцовой поверхностью в колпак, остается неподвижной, а под действием трубы перемещается гильза. Коническая поверхность гильзы надвигается на наружную коническую поверхность цанги, и последняя сжимается. Поскольку цанга в процессе зажима остается неподвижной, то при данной конструкции не происходит смещения обрабатываемого прутка. Гильза имеет хорошее центрирование в шпинделе, а обеспечение соосности внутренней конической и наружных центрирующих поверхностей гильзы не представляет технологических трудностей, благодаря чему данная конструкция обеспечивает достаточно хорошее центрирование обрабатываемого прутка.
При освобождении цанги труба отводится влево и гильза перемещается под действием пружины.
Для того чтобы силы трения, возникающие в процессе зажима на торцовой поверхности лепестков цанги, не уменьшали бы усилие зажима, торцовой поверхности придается коническая форма с углом, несколько превышающим угол трения.
Данная конструкция сложнее предыдущей и требует увеличения диаметра шпинделя. Однако вследствие отмеченных достоинств она находит широкое применение на одношпиндельных автоматах, где увеличение диаметра шпинделя не имеет существенного значения, и на ряде моделей револьверных станков.
Размеры наиболее распространенных цанг нормируются соответствующим ГОСТ. Цанги больших размеров выполняются со сменными губками, что позволяет уменьшить количество цанг в комплекте и при износе губок заменять их новыми.
Поверхность губок цанг, работающих при больших нагрузках, имеет насечку, что обеспечивает передачу больших усилий зажимаемой детали.
Зажимные цанги изготовляются из сталей У8А, У10А, 65Г, 9ХС. Рабочая часть цанги закаливается до твердости HRC 58—62. Хвостовая
часть подвергается отпуску до твердости HRC 38—40. Для изготовления цанг применяются также цементируемые стали, в частности сталь 12ХНЗА.
Труба, перемещающая зажимную цангу, сама получает движение от одного из перечисленных видов приводов через ту или иную систему промежуточных передач. Некоторые конструкции промежуточных передач для перемещения зажимной трубы представлены на рис. IV. 3.
Зажимная труба получает движение от сухарей, представляющих собой часть втулки с выступом, заходящим в паз шпинделя. Сухари опираются на хвостовые выступы зажимной трубы, которые удерживают их в требуемом положении. Сухари получают движение от рычагов, Г-образные концы которых заходят в торцовую выточку втулки 6, сидящей на шпинделе. При зажиме цанги втулка перемещается влево и, воздействуя внутренней конической поверхностью на концы рычагов, поворачивает их. Поворот происходит относительно точек контакта Г-образных выступов рычагов с выточкой втулки. При этом пятки рычагов нажимают на сухари. На чертеже механизмы показаны в положении, соответствующем окончанию зажима. В этом положении механизм оказывается замкнутым, а втулка разгружена от осевых усилий.
Рис. 3. Механизм перемещения зажимной трубы.
Регулирование усилия зажима осуществляется гайками, с помощью которых перемещается втулка. Чтобы избежать необходимости увеличения диаметра шпинделя, на него посажено резьбовое кольцо, которое упирается в полукольца, заходящие в канавку шпинделя.
В зависимости от диаметра зажимной поверхности, который может колебаться в пределах допуска, зажимная труба будет занимать различное положение в осевом направлении. Отклонения в положении трубы компенсируются деформацией рычагов. В других конструкциях вводятся специальные пружинные компенсаторы.
Данный вариант находит широкое применение на одношпиндельных токарных автоматах. Имеются многочисленные конструктивные модификации, отличающиеся формой рычагов.
В ряде конструкций рычаги заменяются расклинивающими шариками или роликами. На конце зажимной трубы на резьбе сидит фланец. При зажиме цанги фланец вместе с трубой перемещается влево. Фланец получает движение от гильзы, воздействующей через ролик на диск. При перемещении гильзы влево, ее внутренняя коническая поверхность заставляет бочкообразные ролики перемещаться к центру. При этом ролики, двигаясь по конической поверхности шайбы, смещаются влево, перемещая в этом же направлении диск и фланец с зажимной трубой. Все детали смонтированы на втулке, установленной на конце шпинделя. Усилие зажима регулируется навинчиванием фланца на трубу. В требующемся положении фланец застопоривается с помощью фиксатора. Механизм может быть снабжен упругим компенсатором в виде тарельчатых пружин, что позволяет использовать его для зажима прутков с большими допусками на диаметр.
Подвижные гильзы, осуществляющие зажим, получают движение от кулачковых механизмов токарных автоматов или от поршневых приводов. Зажимная труба может быть также непосредственно связана с поршневым приводом.
Приводы зажимных приспособлений многопозиционных станков. Каждое из зажимных приспособлений многопозиционного станка может иметь свой, обычно поршневой привод, либо подвижные элементы зажимного приспособления могут получать движение от привода, установленного в загрузочной позиции. В последнем случае механизмы зажимного приспособления, попадающие в загрузочную позицию, связываются с механизмами привода. По окончании зажима эта связь прекращается.
Последний вариант широко используется на многошпиндельных токарных автоматах. В позиции, в которой происходит подача и зажим прутка, установлен ползун с выступом. При повороте шпиндельного блока выступ входит в кольцевую канавку подвижной гильзы зажимного механизма и в соответствующие моменты перемещает гильзу в осевом направлении.
Подобный принцип может быть в ряде случаев использован для перемещения подвижных элементов зажимных приспособлений, установленных на многопозиционных столах и барабанах. Серьга зажимается между неподвижной и подвижной призмами зажимного приспособления, установленного на многопозиционном столе. Призма получает движение от ползуна с клиновым скосом. При зажиме плунжер, на котором нарезана зубчатая рейка, перемещается вправо. Через зубчатую шестерню движение передается ползуну, который клиновым скосом перемещает призму к призме. При освобождении зажатой детали вправо перемещается плунжер, который шестерней также связан с ползуном.
Плунжеры могут получать движение от поршневых приводов, установленных в загрузочной позиции, или от соответствующих звеньев кулачковых механизмов. Зажим и освобождение детали может производиться также в процессе поворота стола. При зажиме плунжер, снабженный роликом, набегает на неподвижный кулак, установленный между загрузочной и первой рабочей позициями. При освобождении плунжер набегает на кулак, расположенный между последней рабочей и загрузочной позициями. Плунжеры располагаются в разных плоскостях. Для компенсации отклонений в размерах зажимаемой детали вводятся упругие компенсаторы.
Следует заметить, что подобные простые решения недостаточно используются при проектировании зажимных приспособлений для многопозиционных станков при обработке некрупных деталей.
Рис. 4. Зажимное приспособление многопозиционного станка, работающее от привода, установленного в загрузочной позиции.
При наличии индивидуальных поршневых двигателей у каждого из зажимных приспособлений многопозиционного станка к поворотному столу или барабану должен быть подведен сжатый воздух или масло под давлением. Устройство для подвода сжатого воздуха или масла аналогично описанному выше устройству вращающегося цилиндра. Применение подшипников качения в данном случае излишне, так как скорость вращения мала.
Каждое из приспособлений может иметь индивидуальный распределительный кран или золотник, либо для всех зажимных приспособлений может быть использовано общее распределительное устройство.
Рис. 5. Распределительное устройство поршневых приводов зажимных приспособлений многопозиционного стола.
Индивидуальные краны или распределительные устройства переключаются вспомогательными приводами, установленными в загрузочной позиции.
Общее распределительное устройство последовательно подключает поршневые приводы зажимных приспособлений по мере поворота стола или барабана. Примерная конструкция подобного распределительного устройства изображена на рис. 5. Корпус распределительного устройства, установленный соосно с осью вращения стола или барабана, вращается вместе с последними, а золотники вместе с осью остаются неподвижными. Золотник управляет подачей сжатого воздуха в полости, а золотник в полости зажимных цилиндров.
Сжатый воздух поступает по каналу в пространство между золотниками и направляется с помощью последних в соответствующие полости зажимных цилиндров. Отработанный воздух уходит в атмосферу через отверстия.
В полости сжатый воздух попадает через отверстие, дуговую канавку и отверстия. Пока отверстия соответствующих цилиндров совпадают с дуговой канавкой, в полости цилиндров поступает сжатый воздух. Когда при очередном повороте стола отверстие одного из цилиндров совместится с отверстием, полость этого цилиндра окажется связанной с атмосферой через кольцевую канавку, канал, кольцевую канавку и канал.
Полости тех цилиндров, в полости которых поступает сжатый воздух, должны быть связаны с атмосферой. Полости соединяются с атмосферой через каналы, дуговую канавку, каналы, кольцевую канавку и отверстие.
В полость цилиндра, находящегося в загрузочной позиции, должен поступать сжатый воздух, который подается через отверстие и каналы.
Таким образом, при повороте многопозиционного стола происходит автоматическое переключение потоков сжатого воздуха.
Аналогичный принцип используется и для управления потоками масла, подаваемого к зажимным приспособлениям многопозиционных станков.
Следует заметить, что подобные же распределительные устройства применяются и на станках для непрерывной обработки с вращающимися столами или барабанами.
Принципы определения усилий, действующих в зажимных приспособлениях. Зажимные приспособления, как правило, проектируются таким образом, чтобы усилия, возникающие в процессе резания, воспринимались бы неподвижными элементами приспособлений. Если те или иные силы, возникающие в процессе резания, воспринимаются подвижными элементами, то величина этих сил определяется на основе уравнений статики трения.
Методика определения сил, действующих в рычажных механизмах цанговых зажимных устройств, аналогична методике, применяемой при определении усилий включения фрикционных муфт с рычажными механизмами.
Читать далее:
Транспортирующие механизмы для подачи непрерывной заготовки
Статьи по теме:
pereosnastka.ru
НАЗНАЧЕНИЕ ЗАЖИМНЫХ УСТРОЙСТВ
Основы конструирования приспособлений
Основное назначение зажимных устройств приспособлений — обеспечение надежного контакта заготовки с установочными элементами, предупреждение ее смещения и вибраций в процессе обработки (рис. 35, а). Введением дополнительных зажимных устройств увеличивают жесткость технологической системы, что повышает точность и производительность обработки. На рис. 35, б показана схема установки заготовки а на опоры 1—6; помимо основного зажима Qt дополнительное устройство Q2 сообщает системе большую жесткость. Опора 7 выполняется самоустанавливающейся. Зажимные устройства используются также для обеспечения правильной установки и центрирования заготовки, выполняя функцию установочно-зажимных устройств. К ним относятся самоцентрирующие патроны, цанговые зажимы и другие устройства, показанные на рис. 35, виг.
Необходимость закрепления заготовки отпадает, если ее масса велика, а силы резания малы (например, при сверлении мелких отверстий в тяжелой станине), а также в том случае, когда силы, возникающие при обработке, прижимают заготовку к установочным элементам. Примеры обработки заготовок и сборки без закрепления показаны на рис. 36, а, б.
При обработке на заготовку действуют силы резания, объемные силы, а также силй второстепенного и случайного характера, предопределяя возможное смещение заготовки. По величине, направлению и месту приложения силы резания являются переменными факторами. При неустановившемся режиме (врезании инструмента) сила резания возрастает от нуля до максимума и уменьшается от максимума до нуля (сход инструмента). При установившемся режиме Она также не постоянна и изменяется в определенных пределах. Амплитуда колебаний силы резания в этом случае достигает 0,1 ее номинальной величины. Точка приложения силы резания в процессе обработки непрерывно перемещается по обрабатываемой поверхности, поэтому сила резания имеет не статический, а динамический характер. При обработке прерывистых поверхностей динамичность резания еще более возрастает. С затуплением инструмента сила резания увеличивается на 10—30 % и более.
На рис. 37, а показаны эпюры осевых сил Р0 и крутящих моментов Мкр при сверленли сквозного отверстия. При выходе
IQ a) ] J2 &
Ffg JWAI
Ж
Г)
Рис. 35. Зажимные устройства |
В) НС
Рис 36. Обработка (сборка) заготовок без закрепления
37. Эпюры:
Осевых сил и моментов при сверлении сквозного отверстия; б—равнодействующей при фрезеровании; — путь врезания сверла; T — глубина резаниясверла MKF несколько увеличивается. Сила закрепления должна определяться по этой стадии обработки. При сверлении отверстий глубиной более пяти диаметров увеличиваются Мкр и Р0, возрастает вероятность пакетирования стружки в канавках сверла и его поломки. Расчетные значения Мкр и Р0 в этом случае следует повышать в 1,5—2 раза. На рис. 37, б показаны эпюры равнодействующей сил резания при фрезеровании. При малой глубине резания (менее 2,5 мм) заготовка прижимается этой силой вниз, при большей глубине — отжимается вверх.
Объемные силы — сила тяжести заготовки, центробежные и инерционные силы — возникают при определенных условиях обработки. Сила тяжести заготовки действует и учитывается при ее установке на вертикальные или наклонно расположенные элементы; она создает различные условия закрепления, если обработка осуществляется в поворотных приспособлениях. В процессе обработки резанием масса заготовки непрерывно уменьшается и изменяется положение ее центра тяжести.
Центробежные силы возникают в процессе обработки при смещении центра тяжести заготовки относительно ее оси вращения. Величина действующих на заготовку центробежных сил и моментов (при динамическом дисбалансе) сопоставима с силами резания при чистовой обработке.
Инерционные силы (моменты) возникают и имеют значение; тогда, когда заготовка совершает возвратно-поступательное движение или вращается с большими угловыми ускорениями (например, при торможении шпинделя). При возвратно-поступательном движении сила инерции, действующая на заготовку,
Р = Am = т,
Где а — ускорение; т — масса заготовки.
При изменении угловой скорости момент, действующий на заготовку,
Где J — момент инерции заготовки; -^f - — угловое ускорение
Заготовки.
При постоянном угловом ускорении
M=.-f J.
Величины Р м М обычно малы по сравнению с силами и моментами резания. Лишь в случае чистовой обработки заготовок большой маесы и момента инерции их значения возрастают.
К второстепенным относятся силы, возникающие при отводе режущего инструмента (сверла, метчика, развертки)-.
J1. Предельные моменты, получаемые при различных конструктивных формах головок и рукояток винтов |
Смещение заготовки 1 (см. рис. 3, а) при выводе сверла из отверстия предупреждается пружинным зажимом в откидной крышке кондуктора 2. В результате этого обеспечивается заданная точность межосевого расстояния L. Необходимость закрепления базовой детали 1 (см. рис. 36, в), в которую запрессовывается втулка 2, определяется условием G > F, где G — сила тяжести детали 1 F — сила трения на поверхности штока 3, удерживающего втулку от падения при сборке.
При чистовом точении наблюдается ослабление силы затяжки кулачков под действием центробежной силы, достигающее 10 %. При черновой обработке влиянием этого фактора можно пренебречь.
Требования, предъявляемые к зажимным устройствам. Эти
Устройства должны быть надежными в работе, просты по конструкции и удобны в обслуживании; не должны деформировать закрепляемые заготовки и портить их поверхности; закрепление и открепление заготовок должно быть с минимальной затратой сил и времени; они должны обеспечивать равномерный зажим заготовок, особенно в многоместных приспособлениях; зажимные устройства не должны сдвигать заготовку при ее закреплении и по возможности воспринимать силы резания. Последним следует противопоставлять жесткие установочные элементы приспособления. Место приложения сил закрепления выбирают по условию наибольшей жесткости и устойчивости крепления и минимальной деформации заготовки. Для повышения точности обработки предпочтительны устройства, обеспечивающие постоянную силу закрепления*
В ручных зажимных устройствах сила на рукоятке не должна превышать 150 Н. Значения моментов, развиваемых рукой на маховичках и рукоятках различных конструкций и размеров, приведены в табл. 11. Средняя продолжительность закрепления заготовок различными зажимными устройствами: в трехкулачко - вом патроне ключом — 4 с; одним винтовым зажимом (ключом) —■ 4,5 с; штурвалом — 2,5 с; поворотом рычага — 2,5 с; маховичком или звездочкой — 2 с, поворотом рукоятки пневмо - и гидрокрана— 1,5 с. При необходимости увеличить число зажатий применяют приспособления с силовыми (пневматическими, гидравлическими) узлами.
Вновь изготовленное приспособление тщательно проверяют перед сдачей в эксплуатацию. Проверка предусматривает: внешний осмотр, контроль комплектности в соответствии с чертежом, правильность изготовления приспособления по основным элементам и сопряжениям (плавность и легкость …
Приспособления изготовляют различными методами. Универсальные приспособления выпускаются в значительном количестве для укомплектования новых станков и действующего станочного оборудования; значительная часть их стандартизована (трех - и четырехкулачковые патроны, плиты и другие …
На станках с программным управлением (ПУ) обрабатывают детали широкой номенклатуры малыми партиями. Характерным для этих станков является быстрая сменяемость партий, сложность и повышенная точность обработки деталей. Приспособления для станков с …
msd.com.ua
Установочно-зажимное приспособление - Большая Энциклопедия Нефти и Газа, статья, страница 1
Установочно-зажимное приспособление
Cтраница 1
Установочно-зажимные приспособления используют для крепления базовых деталей и узлов собираемого объекта. Они обеспечивают повышение производительности труда, позволяя выполнять сборку двумя руками без удерживания собираемого объекта. [2]
В качестве установочно-зажимных приспособлений используют оправки различных конструкций ( клиновые, самозажимные, конические, с упругой гильзой и с гидропластом), а также самоцентрирующие устройства для станков различных групп. Широкое применение получили призматические и кулачковые, плунжерные, цанговые и мембранные, гидропластовые и другие механизмы. [3]
При этом запроектированные установочно-зажимные приспособления должны быть быстродействующими и легко переналаживаться при смене деталей группы; групповая инструментальная наладка должна быть стабильной по составу режущего и вспомогательного инструмента; переналадка станка в связи с переходом к обработке другой детали должна быть простой и осуществляться с минимальными затратами труда; должна быть обеспечена полная загрузка. [4]
Детали закрепляются с помощью установочно-зажимных приспособлений и непосредственно на столе. [5]
На поверхности планшайбы закреплен корпус 2 установочно-зажимного приспособления. Между пневмоцилиндрами радиально расположены воздухораспределительные краны 6 с плунжерными золотниками. [6]
В отдельных случаях ( при одновременной обработке нескольких заготовок) применяют простейшие установочно-зажимные приспособления. [7]
Следовательно, основные резервы для повышения производительности труда скрыты в возможности дальнейшего совершенствования установочно-зажимных приспособлений и автоматизации обработки на фрезерных станках. [8]
Этот вариант может оказаться предпочтительным при достаточно большом объеме выпуска, когда изготовление сложных установочно-зажимных приспособлений для схем установок У41 ( см. рис. 5.34) и УЗЗ ( см. рис. 5.33, в) окупится за счет сокращений общего числа операций и, соответственно, сокращения суммарного оперативного и подготовительно-заключительного времени. [9]
Разжимные оправки различных конструкций ( включая конструкции с применением гидропласта) относятся к установочно-зажимным приспособлениям; они описаны на стр. [10]
Если основные базы скрытые, то в конструкции детали должна быть предусмотрена возможность их материализации желательно с применением самоцентрирующих установочно-зажимных приспособлений - другими поверхностями, которые уже занимают требуемое положение относительно соответствующих основных баз. [11]
Такое базирование выполняется значительно быстрее и применяется в массовом и серийном производстве, где в связи с этим широко используются всевозможные установочно-зажимные приспособления. [12]
Наиболее точной и производительной является настройка фрез на заданные размеры с помощью установов ( габаритов), предусматриваемых в конструкции установочно-зажимных приспособлений. У станов / ( рис. 8.10) представляет собой стальной закаленный угольник, жестко закрепленный на корпуве приспособления. [13]
Наиболее точной и производительной оказывается настройка на заданные размеры с помощью установов ( габаритов для фрез), предусматриваемых в конструкции установочно-зажимных приспособлений. [14]
Наиболее точной и производительной оказывается настройка на заданные размеры с помощью установов ( габаритов) для фрез, предусматриваемых в конструкции установочно-зажимных приспособлений. [15]
Страницы: 1 2
www.ngpedia.ru
ПРОСТЕЙШИЕ ЗАЖИМНЫЕ ПРИСПОСОБЛЕНИЯ. Основы фрезерования |
Закрепление заготовки на столе станка. При закреплении деталей непосредственно на столе станка пользуются прихватами с болтами, подкладными клиньями и домкратами.
На рис. 123 изображены различные типы прихватов. Прихват является самым распространенным. Отверстие 1 для болта сделано продолговатым, что дает возможность передвигать прихват относительно закрепленной детали. Такие отверстия сделаны у всех прихватов, изображенных на рис. 123. Винт 2 у прихвата II служит вместо подкладки под прихват. Выступ 3 у прихвата III, а также выступ 5 у прихвата IV дают возможность пользоваться прихватами без подкладок. Прихват III своим уступом 4 ложится на деталь. У прихвата IV снята фаска 6Г чтобы он не мешал работе фрезы при обработке соответствующих поверхностей деталей.
Часто приходится" применять прихваты с вытянутым концом- (прихваты У, VI » VII). Концы 7, 5 и 9 таких прихватов обычно заводят во впадины или опирают на выступы детали. Прихватом VIII можно пользоваться без подкладок.
Прихват IX удобен в тех случаях, когда в детали имеются впадины или выемки, куда выступом 10 вводят прихват. Очень удобен простой в изготовлении прихват X. Чтобы снять его, не нужно совсем свертывать гайку, а достаточно слегка ослабить ее и сдвинуть прихват в сторону.
На рис. 123, XI показано закрепление обрабатываемой детали 15 посредством прихвата 12, который одним концом опирается на деталь 15, а другим — на подкладку. Болт 14, плоская головка которого входит в Т-образный паз стола, проходит сквозь прихват. Завертывая ключом гайку 13, прижимают прихват к подкладке и так закрепляют деталь.
В качестве подкладок под прихваты пользуются различными брусками и другими подходящими по высоте деталями.
Весьма удобным в работе является переставной по высоте прихват, изображенный на рис. 123, XII. Переставляя дугообразный прихват 16, имеющий в центре продолговатое отверстие, им можно прижимать разнообразные по высоте заготовки.
Такой же переставной по высоте прихват показан на рис. 123, XIII. Подкладка прихвата выполнена в виде круглого диска 17, вращающегося на эксцентрично расположенной оси 18, проходящей через прорезь прихвата 19. В диске 17 просверлена шесть отверстий. В зависимости от требуемой высоты установки в то или иное отверстие устанавливают штифт 21, на который опирается прихват 19. Таким образом, прихват имеет три опоры: ось 18, штифт 21 и зажимаемую деталь 20. На рис. 123, XIV показан прихват в самом нижнем положении крепления. Зажим осуществляется болтом подобно прихвату на рис. 123, XI.
Некоторые детали можно надежно закрепить при помощи прижимов. На рис. 124 показан прижим 4У нижний конец которого 5 входит в Т-образный паз стола станка. Опорная губка / имеет такой же нижний конец 5, входящий в паз стола. Закрепляемые заготовки 2 зажимаются болтом 6, поджимающим подвижную губку 3. Для создания прижима книзу болт имеет наклон.
Несмотря на то, что крепление деталей на столе фрезерного станка является простейшим приемом, оно требует опыта.
При закреплении деталей на столе с помощью прихватов необходимо запомнить ряд основных правил:
1) болт, укрепляющий прихват, необходимо устанавливать возможно ближе к детали, для чего надо применять прихваты с продолговатыми отверстиями;
2) прихват должен опираться на подкладку одинаковой высоты с деталью;
3) конец прихвата, опирающийся на деталь, не должен находиться над той ее частью, которая не лежит плотно на столе;
4) грубое фрезерование детали следует производить при сильно затянутых болтах, а при чистовом фрезеровании гайки прижимных болтов следует слегка ослабить.
Закрепление заготовки в угольниках. При фрезеровании заготовки, две обрабатываемые стороны которой должны составлять прямой угол, пользуются угловой плитой, которую принято называть угольником.
На рис. 125, а изображена обыкновенная угловая плита. Стороны ее обработаны под прямым углом друг к другу. Заготовку закрепляют на угловой плите посредством прихватов или струбцинок. Угловые плиты больших размеров имеют ребра жесткости, скрепляющие полки.
На рис. 125,6 показана поворотная угловая плита, полки которой можно раздвигать на требуемый угол. Поворот полок производится вокруг оси болта 2 после освобождения гайки. Для установки полок на требуемый угол служит шкала 3. На рис. 125,6 полки плиты установлены под прямым углом.
На рис. 125, в показана универсальная угловая плита, допускающая поворот детали в двух плоскостях. Такие плиты часто применяют для обработки наклонных поверхностей (см. рис. 183).
Универсальная плита представляет собой поворотный вокруг горизонтальной и вертикальной осей стол 4 с тремя продольными Т-образными пазами для крепления заготовки. Поворот вокруг вертикальной оси осуществляется колодкой 5, закрепляемой под требуемым углом болтами 6. Поворот вокруг горизонтальной оси осуществляется рукояткой 2.
На рис. 126 показано крепление к угловой плите длинной и широкой, но сравнительно тонкой планки, подлежащей фрезерованию. Установочными базами планки являются поверхность 2 и торцовая поверхность 1. Угловая плита опорной плоскостью крепится к столу при помощи болтов, закладываемых в пазы стола фрезерного станка. Основание плиты имеет простроганный входящий в паз стола шип для установки плиты параллельно станине станка.
Прежде чем закреплять обрабатываемую деталь на угловой плите, следует тщательно проверить правильность установки самой плиты на столе станка. Грубая проверка положения производится так, как показано на рис. 127 внизу, т. е. измерением расстояния между вертикальной полкой 2 угловой плиты и кромкой ближайшего паза 3 стола станка. Расстояния Л и Б, измеренные линейкой 4, должны быть одинаковыми.
Для более точной проверки применяют рейсмас 1 (рис. 127, сверху). Иглу рейсмаса, закрепленную на фрезерной оправке, приближают к вертикальной полке угловой плиты поперечной подачей стола так, чтобы острие инструмента почти касалось полки плиты. После этого вручную сообщают столу медленную продольную подачу и смотрят, насколько изменяется просвет между острием иглы и полкой угловой плиты.
Если нет уверенности в правильности самой угловой плиты, т. е. в том, что обе полки ее расположены под углом 90° одна к другой, следует произвести эту проверку, пользуясь тем же рейсмасом, но сообщив столу станка вертикальную подачу. Только после проверки угольник накрепко прижимают к столу.
Более точно такую проверку можно сделать индикатором.
Заготовки устанавливают на угловой плите и закрепляют обычно при помощи струбцинок.
Иногда вертикальная полка угловой плиты имеет продолговатые вырезы (см. рис. 125, а и б), через которые пропускают прижимные болты, крепящие деталь к угловой плите при помощи прихватов.
Закрепление в призмах. Круглые детали для фрезерования в них шпоночных канавок, пазов и лысок удобно закреплять в призмах. Коротким деталям достаточно одной призмы. Если длина детали велика, приходится устанавливать на стол станка две призмы на некотором расстоянии друг от друга. Призмы закрепляют на столе станка прихватами, а обрабатываемые детали закрепляют в призмах при помощи струбцинок или прихватов.
На рис. 128 показано закрепление вала 2 на двух призмах 3. Призмы установлены на столе станка. Правильность положения оси каждой призмы обеспечивается сухарем в основании призмы, входящим в паз стола, как показано на рисунке справа. Закрепляют валы при помощи прихватов 1. Необходимо следить, чтобы прихваты опирались на закрепляемый вал над призмами во избежание прогиба вала. Под прихваты следует положить тонкий лист меди или латуни, чтобы не повредить поверхности вала. При закреплении в призмах установочной базой является наружная цилиндрическая поверхность вала.
На рис. 129 изображены универсальные тиски для зажима валов. В этих тисках установка вала производится при помощи призмы. Тиски можно располагать на столе фрезерного станка либо так, как показано на рис. 129, либо повернув их на 90°.
Эти тиски удобны тем, что годятся для станков как с горизонтальным, так и с вертикальным шпинделем.
Подлежащий обработке вал базируют цилиндрической поверхностью на призму 5 и вращением маховичка 1 зажимают его между губками 3 и 6, поворачивающимися соответственно вокруг пальцев 2 и 7.
Призма 5 может быть освобождена, вынута из тисков и повернута другой стороной при необходимости зажать вал большего диаметра. Упор 4 служит для базирования вала по длине.
Закрепление заготовки в тисках. Машинные тиски бывают различных размеров сообразно размерам станка, для которого они предназначены, и размерам деталей.
На рис. 130 изображены машинные поворотные тиски, которые крепят к столу фрезерного станка при помощи болтов, входящих в выемки плиты 2. На плите крепится поворотный корпус 1 тисков, закрепляемый в любом положении при помощи болта 3. Величину поворота корпуса 1 относительно плиты 2 определяют по шкале.
У тисков имеются неподвижная губка 4, подвижная губка 7, каленые планки 5 и 6 губок, прижимной винт 8 с квадратным концом 10, на который надевается рукоятка, направляющие 9, по которым перемещается подвижная губка 7.
Для закрепления деталей часто применяют машинные неповоротные тиски, отличающиеся от описанных выше поворотных тем, что у них отсутствует плита 2. Они крепятся к столу станка при помощи болтов, входящих в выемки корпуса 1 тисков.
Для фрезерования плоскостей под углом (скосы) применяют универсальные тиски, которые могут поворачиваться не только вокруг вертикальной оси, как поворотные машинные тиски, но и вокруг горизонтальной оси. Такие тиски удобны для инструментальных работ, но для обработки со снятием большой стружки m пригодны, так как не дают жесткого закрепления детали.
На рис. 131 показаны все три типа машинных тисков.
Для правильной установки тисков на столе фрезерного станка используют имеющиеся в основании тисков прямоугольные пазы, расположенные перпендикулярно один к другому, так называемый крестовый паз.
Перед установкой основание тисков и стол станка насухо протирают и вводят в средний паз стола два сухаря, входящих в продольный из тисков. Если тиски надо закрепить поперек стола, то сухари вставляют в поперечный паз основания тисков.
Затем в пазы стола вставляют прижимные болты с шайбами и гайками и закрепляют тиски болтами, используя имеющиеся в плите тисков прорези. При завинчивании гаек прижимных болтов надо завертывать их попеременно то с одной, то с другой стороны, так как полная затяжка сначала с одной стороны, а затем с другой не обеспечивает правильного закрепления тисков.
Если тиски не имеют крестового паза для правильной установки на столе станка, приходится производить выверку их расположения.
На рис. 132, а показана выверка тисков в том случае, когда необходимо расположить их так, чтобы губки были параллельны оси шпинделя станка. Тиски (в незакрепленном состоянии) ставят на столе станка так, чтобы фрезерная оправка в шпинделе плотно прилегала к неподвижной губке.
На рис. 132,6 показана выверка тисков, губки которых необходимо расположить так, чтобы они были перепендикулярны оси шпинделя станка. Тиски (в незакрепленном состоянии) располагают так, чтобы угольник, слегка зажатый в тисках, плотно прилегал, без просвета, к фрезерной оправке, закрепленной в гнезде шпинделя.
После того как тиски займут правильное положение, их накрепко прикрепляют болтами, как указано выше, к столу фрезерного станка.
Закрепляя деталь в тисках, надо развести их губки на ширину, большую ширины детали, протереть насухо губки и дно тисков. Если деталь или заготовка по высоте меньше высоты губок тисков, следует взять одну или две стальные подкладки с правильно обработанными параллельными плоскостями, протереть и положить между губками на направляющие тисков.
Установленная на подкладки деталь или заготовка должна быть выше губок тисков примерно на 10—15 мм. Положив заготовку на подкладку, надо поворотом рукоятки тисков зажать ее и, обстукивая медным или латунным молотком, удостовериться в надежном закреплении. При неплотном прилегании детали ее следует осадить ударами молотка и дополнительно закрепить.
На рис. 133, а показана установка детали на одной, а на рис. 133, б — на двух параллельных подкладках.
dlja-mashinostroitelja.info
Зажимное приспособление
Изобретение касается зажимного приспособления, в частности кабельного зажимного приспособления для техники дальней связи и передачи данных. Техническим результатом является создание зажимного приспособления, которое обеспечивает крепление изделий различных диаметров простым и надежным способом, не подвергая изделие недопустимо сильному сдавливанию. Для этого корпус зажима, состоящий из основной части и по крайней мере из одного зажимного рычага, в который вводится зажимаемое изделие, помещается в гильзу с выемками, с которыми входит в зацепление по крайней мере один из зажимных рычагов корпуса зажима. В результате поворота гильзы относительно неподвижной основной части по крайней мере один из зажимных рычагов уменьшает зажимающий внутренний диаметр (D) корпуса зажима. 5 з.п. ф-лы, 6 ил.
Изобретение касается зажимного приспособления, в частности, кабельного зажимного приспособления для техники связи и передачи данных.
Известны зажимные приспособления, такие как скобы для крепления трубчатой проводки или для крепления кабелей, которые позволяют крепить лишь трубы, шланги или кабели ограниченных диаметров. Зажимное приспособление может быть использовано лишь для узкого интервала диаметров. Зажимные изделия не защищены от сдавливания, причем величина сплющивания определяется исполнителями работ, а не ограничивается зажимным приспособлением. В патенте ФРГ DE 34 615 C1 описывается электрический штепсельный разъем, к которому крепится зажимом экранирующий контакт для обеспечения сквозного экранирования от кабеля к штепсельному разъему. При этом кабельный экран соединен с экранирующим контактом токопроводящим зажимным устройством. Это зажимное соединение осуществляется при помощи зажимного кольца или кабельного биндера. Также в данном случае достигается лишь недостаточная пригонка кабелей различных диаметров. Известно зажимное приспособление, в частности кабельное зажимное приспособление для техники связи и передачи данных, состоящее из корпуса зажима, включающего основную часть, в который вводится зажимаемое изделие, и гильзы (DE 34 17882 A1, 21.11.85, H 02 G 3/18). Задача изобретения состоит в создании такого зажимного устройства, которое обеспечивает крепление изделий различных диаметров простым и надежным способом, не подвергая изделие недопустимо сильному сдавливанию. Для решения поставленной задачи в зажимном приспособлении, в частности кабельном зажимном приспособлении для техники связи и передачи данных, состоящем из корпуса зажима, включающего основную часть, в который вводится зажимаемое изделие, и гильзы, корпус зажима, представляющий собой цельную штампованную деталь, имеет по меньшей мере один зажимной рычаг черновой вырубки и гильзу с по меньшей мере одной выемкой, при этом корпус зажима установлен с возможностью перемещения в гильзе и по меньшей мере один из зажимных рычагов корпуса входит в выемку гильзы и в результате поворота гильзы относительно неподвижного корпуса зажима по меньшей мере один из зажимных рычагов уменьшает зажимающий внутренний диаметр корпуса зажима. Выполненный согласно изобретению корпус зажима обеспечивает в соединении с выполненной в соответствии с изобретением гильзой снятие натяжения и/или полное экранирование /360o/ кабелей различных диаметров или вообще надежное крепление кабелей с различным диаметром при помощи одного зажимного приспособления. Выбор параметров зажимного рычага в зависимости от цели применения позволяет воздействовать на изделие или кабель с определенной силой, которая не может превышать заданный предел, и таким образом не возникает опасность недопустимо сильного сдавливания изделия. Диаметр корпуса зажима зажимного приспособления может быть изменен в широком диапазоне путем простого поворота гильзы. Зажимное приспособление создает разъемное соединение и может использоваться повторно. Согласно предпочтительному варианту выполнения изобретения зажимные рычаги выступают из корпуса зажима в разных плоскостях. В соответствии с другим преимущественным вариантом корпус зажима образует токопроводный экранирующий контакт. Корпус зажима имеет собачку, выполненную с возможностью входить в зацепление с расположенным внутри гильзы зубчатым механизмом. Основная часть корпуса зажима выполнена с возможностью соединяться с стопорно-усилительной гильзой. Основная часть корпуса зажима имеет круглую или многоугольную конструкцию. Другие варианты преимущественного выполнения изобретения представлены в зависимых пунктах формулы изобретения. Ниже приводится более подробное пояснение изобретения со ссылкой на представленные на чертежах примеры осуществления зажимного приспособления для кабелей, в частности: - фиг. 1 - подетальное изображение зажимного приспособления с круглой конструкцией корпуса зажима, - фиг. 2 - перспективное изображение корпуса зажима квадратной конструкции, - фиг. 3 - перспективное изображение гильзы, - фиг. 4 - изображение зажимного приспособления в разрезе с корпусом зажима квадратной конструкции, помещенным в гильзе, - фиг. 5 - изображение зажимного приспособления в разрезе согласно фиг. 4 со слегка сжатыми зажимными рычагами и - фиг. 6 - изображение зажимного приспособления в разрезе согласно фиг. 4 с сильно сжатыми зажимными рычагами для тонких кабельных жил. Кроме общего применения, зажимное приспособление используется, в частности, предпочтительно в технике дальней связи и передачи данных в качестве кабельного зажимного приспособления для экранированных кабелей. В соединении, например, с втулками RJ 45 предлагаемое зажимное приспособление обеспечивает надежное снятие натяжения и полное кабельное экранирование /360o/ к втулке. На фиг. 1 представлено зажимное приспособление для кабелей, которое в основном состоит из корпуса 1 зажима круглой конструкции, включающего основную часть 6 с зажимными рычагами 5, и гильзы 2 с клинообразными выемками 4. Соединение зажимного приспособления с непредставленной на чертеже втулкой RJ 45 может осуществляться через соединительную планку 9, которая соединена с корпусом 1 зажима и со стопорно-усилительной гильзой 10. Кабельный экран образует токоведущее соединение с токоведущим корпусом 1 зажима, который в свою очередь образует соединение через соединительную планку 9 с, например, экраном втулки RJ 45, что обеспечивает таким образом сквозное экранирование от кабеля к втулке. Стопорно-усилительная гильза 10 вставляется сверху через соединительную планку 9 таким образом, что два язычка 12 стопорно-усилительной гильзы 10 входят в две выемки 13 соединительной планки 9, предотвращая их таким образом от поворачивания. Стопорно-усилительная гильза 10 вместе с закрепленной на ней соединительной планкой 9 вводится в корпус 1 зажима и соединяется с ним ушками 14, которые загибаются наружу, прочно фиксируя таким образом соединительную планку 9 на корпусе 1 зажима. Образованный таким образом узел, состоящий из стопорно-усилительной гильзы 10, соединительной планки 9 и корпуса 1 зажима, вставляется в гильзу 2. В результате этого корпус 1 зажима устанавливается относительно гильзы 2. Не представленный на фиг. 1 кабель вставляется вместе с экраном в корпус 1 зажима и там путем поворота гильзы 2 против часовой стрелки в направлении 15 зажимается крепко зажимными рычагами 5 корпуса 1 зажима, которые входят в зацепление с выемками 4 гильзы 2. Основная часть 6 корпуса 1 зажима, как было показано выше, фиксируется относительно гильзы 2 и не изменяет своего положения при повороте гильзы 2, то есть основная часть 6 не поворачивается. При этом ушки 14 отогнуты и направлены к боковой поверхности гильзы и введены в канавку в крайнее положение в выемки. Изменение диаметра и вместе с ним зажимное воздействие на кабель являются результатом уменьшения диаметра между рычагами 5 зажима /фиг. 4-6/. При помощи одного единственного способа осуществления можно получить изменения диаметра, например, от 10 до 3 мм. На фиг. 2 представлен корпус 1 зажима, имеющий квадратную конструкцию исполнения. Основная часть 6 имеет подвижные рычаги 11, соединенные между собой /напрямую или с помощью шарнира наподобие пленочного шарнира/. Например, основная часть 6 может иметь четыре зажимных рычага 5 в четырех различных плоскостях, полученных, например, черновой вырубкой. Один из рычагов 11 изогнут, образуя собачку 7, которая после введения корпуса 1 зажима в гильзу 2 согласно фиг. 3 проходит в зацепление с расположенным внутри зубчатым механизмом 8 гильзы 2 и при повороте гильзы осуществляет дополнительную фиксацию корпуса 1 зажима в желательном положении в гильзе 2. Далее на фиг. 3 изображены четыре клинообразные выемки 4, в которые входят в зацепление четыре зажимные рычага 5 корпуса 1, зажима /фиг. 2/. На фиг. 4 показано зажимное приспособление в собранном виде. Корпус 1 зажима введен в гильзу 2 и зажимные рычаги 5 находятся в выемках 4 в свободном состоянии. Срез 16 /фиг. 3-6/ на верхнем краю гильзы 2 служит для определения положения гильзы. На фиг. 5 представлено зажимное приспособление с введенным кабелем 3 максимально возможного диаметра. Для натяжения или зажима кабеля 3 гильза 2 поворачивается насколько это позволяет диаметр кабеля. Вследствие этого зажимные рычаги 5 корпуса 1 зажима сжимаются и оказывают соответствующее давление на боковые поверхности выемок 4 в гильзе 2. На фиг. 6 показано зажимное приспособление с введенным кабелем 3, имеющим небольшой диаметр. Для натяжения кабеля 3 гильза 2 поворачивается до тех пор, пока зажимные рычаги 5 корпуса 1 зажима не останавливаются окончательно в выемках 4 гильзы 2. Служащая каркасом основная часть 6, корпуса 1 зажима остается совершенно неподвижной, в то время как зажимные рычаги 5 в результате поворота гильзы 2 сходятся и производят сжатие кабеля 3. При этом каждый раз точка соединения зажимных рычагов 5 с основной частью 6 служит центром вращения для поворота зажимных рычагов 5 против часовой стрелки в направлении 15, чтобы выйти на новый диаметр D зажима. Зажимное приспособление может быть изготовлено из подходящего синтетического материала, а корпус 1 зажима металлизирован или изготовлен из проводникового материала, если зажимное приспособление предусмотрено также в качестве кабельного зажимного приспособления для передачи кабельного экранирования. На наружной поверхности гильзы 2 могут быть предусмотрены захватные пазы.Формула изобретения
1. Зажимное приспособление, в частности кабельное зажимное приспособление для техники связи и передачи данных, состоящее из корпуса зажима, включающего основную часть, в который вводится зажимаемое изделие, и гильзы, отличающееся тем, что корпус зажима, представляющий собой цельную штампованную деталь, имеет по меньшей мере один зажимной рычаг черновой вырубки, а гильза выполнена с по меньшей мере одной выемкой, при этом корпус зажима установлен с возможностью перемещения в гильзе и по меньшей мере один из зажимных рычагов корпуса зажима входит в выемку гильзы и в результате поворота гильзы относительно неподвижного корпуса зажима по меньшей мере один из зажимных рычагов уменьшает зажимающий внутренний диаметр корпуса зажима. 2. Приспособление по п.1, отличающееся тем, что зажимные рычаги выступают из корпуса зажима в разных плоскостях. 3. Приспособление по одному из пп.1 и 2, отличающееся тем, что корпус зажима образует тонкопроводный экранирующий контакт. 4. Приспособление по п.1, отличающееся тем, что корпус зажима имеет собачку, выполненную с возможностью входить в зацепление с расположенным внутри гильзы зубчатым механизмом. 5. Приспособление по п.1, отличающееся тем, что основная часть корпуса зажима выполнена с возможностью соединяться со стопорно-усилительной гильзой. 6. Приспособление по п.1, отличающееся тем, что основная часть корпуса зажима имеет круглую или многоугольную конструкцию.РИСУНКИ
Рисунок 1, Рисунок 2, Рисунок 3, Рисунок 4, Рисунок 5, Рисунок 6www.findpatent.ru
ЭЛЕКТРИЧЕСКОЕ ЗАЖИМНОЕ ПРИСПОСОБЛЕНИЕ
Изобретение относится к электрическому зажимному приспособлению согласно ограничительной части пункта 1 формулы изобретения.
В инсталляционной электротехнике известны различные технологии и приспособления для установления электрических соединений. Часто используются зажимы, в которых проводники фиксируются в корпусах зажимов посредством завинчивания. При этом согласно одному из известных вариантов выполнения может осуществляться электрическое соединение двух и более проводников, в то время как согласно другому варианту выполнения выполненный соответствующим образом корпус зажима после закрепления вставленного проводника осуществляет электрическое соединение непосредственно, например, внутри электрического прибора. В корпусе зажима может быть установлена зажимная деталь/гайка, которая может перемещаться вверх и вниз с помощью винта, перемещаемого в корпусе зажима. Проводник, вставленный в корпус зажима, закрепляется, для чего зажимная деталь в промежуточном положении проводника привинчивается винтом к корпусу зажима.
Для защиты от прикосновения к электропроводящим деталям корпус зажима может быть окружен кожухом соответствующего электроприбора, причем винт зажима доступен через соответствующие отверстия кожуха. Для упрощения инсталляционных работ зажимы часто поставляются в открытом положении, в котором возможно введение проводника, так что эта технологическая операция на месте установки не требуется. Между местом изготовления и местом установки на зажим действуют разнообразные перемещения и вибрации, так что это открытое положение может быть надежно обеспечено лишь с помощью дополнительных устройств.
В известном решении используется так называемый винтовой тормоз, в котором ход винта затрудняется, для чего в определенном месте нарушается регулярность винтовой резьбы. Часто многократное использование винта приводит к необратимому повреждению резьбы или к ослаблению тормозного действия вплоть до его отказа.
Другая возможность заключается в зажиме винта в детали кожуха, установленной над зажимом. При этом деталь кожуха имеет меньшее проходное отверстие для инструмента по сравнению с головкой винта. Головка винта вращается относительно окантовки проходного отверстия, так что зажим происходит между деталью кожуха и корпусом зажима. Зажимное действие может быть усилено за счет эластичных материалов кожуха или благодаря окантовке со снятой фаской. Однако на практике оказалось, что этот вид зажима со временем может быть ослаблен в результате вибраций, и винт может сместиться в неопределенное положение внутри корпуса зажима. Точное позиционирование винта в открытом положении технологически может быть достигнуто лишь с помощью дорогостоящих и высокоточных инструментов.
Задача настоящего изобретения заключается в создании электрического зажимного приспособления, в котором винт зажима может фиксироваться в открытом положении надежно и просто.
Эта задача решается с помощью признаков, приведенных в пункте 1 формулы изобретения. Предпочтительные варианты выполнения раскрываются в описании, чертежах и зависимых пунктах формулы изобретения.
Изобретение согласно пункту 1 формулы изобретения имеет то преимущество, что позиционирование винта зажимного приспособления в открытом положении обеспечивается от начала производства и вплоть до его инсталляции. В открытом положении фиксирующий элемент оказывает в радиальном направлении на головку винта усилие, эффективно препятствующее самопроизвольному вращению винта. Кроме того, в открытом положении винта действует фрикционное соединение между фиксирующим элементом и головкой винта, а между верхней деталью кожуха и винтом в незначительной степени действует аксиальная составляющая усилия.
Зажимное приспособление содержит зажим с корпусом зажима, с перемещаемым в нем винтом и с зажимной деталью, а также установленную над винтом деталь кожуха с проходным отверстием, через которое обеспечивается доступ инструмента к винту. Проходное отверстие выполнено сужающимся по отношению к диаметру головки винта, благодаря чему предотвращается выпадение винта. Для этого проходное отверстие окружено окантовкой, в которую, в частности, интегрирован свободно вырезанный и/или выполненный эластичным фиксирующий элемент. Фиксирующий элемент может быть соединен с деталью кожуха в одно целое и, предпочтительно, проходить в направлении корпуса зажима перпендикулярно окантовке. При затягивании винта головка винта входит в контакт с фиксирующим элементом. При этом свободно перемещаемый до этого винт скользит с фрикционным замыканием вдоль фиксирующего элемента, который при этом радиально деформируется и/или перемещается наружу. Винт фиксируется благодаря свойствам эластичности материала и упругой отдаче опоры фиксирующего элемента.
Благодаря конструкции фиксирующего элемента поддается воздействию характер изменения усилия, действующего на винт. За счет длины и формы фиксирующего элемента может быть, например, достигнуто ступенчатое увеличение силы. Предпочтительно контактная поверхность фиксирующего элемента выполнена наклонной, причем целесообразной может быть многоступенчатая контактная поверхность, например, для изначально незначительного, а затем для максимального усилия.
Длина фиксирующего элемента существенно способствует тому, чтобы позиционирование винта в открытом положении технологически реализовывалось с незначительными затратами. Поскольку головка винта проделывает определенный путь вдоль фиксирующего элемента, с помощью соответствующей формы фиксирующего элемента в нескольких местах пути может быть определено достаточное удерживающее усилие. Таким образом, не требуется использования высокоточных инструментов, которые должны юстироваться по одной строго определенной контрольной точке останова.
Максимальный путь перемещения винта может ограничиваться окантовкой проходного отверстия или упором для фиксирующего элемента. Предпочтительным образом по краю проходного отверстия выполнены фаски, так что головка винта в открытом положении центрируется с одной стороны с помощью фиксирующего элемента, а с другой стороны с помощью фасок и/или окантовкой. В результате эффективно предотвращается перекашивание винта.
На эластичность фиксирующего элемента могут влиять свойства материала и форма соединения с деталью кожуха. Вариант конфигурации является результатом выполнения нескольких фиксирующих элементов вдоль окантовки.
Особенно предпочтительным является применение изобретения с несколькими рядом расположенными зажимами, закрываемыми общей деталью кожуха, которая не содержит на каждом зажиме отдельной точки крепления к остальному кожуху. Часто такие детали кожуха крепятся в одном центральном месте. В данном случае прежние решения являются проблематичными, поскольку в открытом положении эффективно могут быть зажаты максимум два винта. Третий винт зависит от линии зажима, заданной другими винтами, и в большинстве случаев прерывает эту линию, так что удовлетворительная фиксация всех винтов невозможна. Благодаря фиксирующему элементу согласно изобретению каждый зажим в отношении обеспечения открытого положения является самостоятельным. Несколько рядом расположенных винтов могут зажиматься в открытом положении независимо друг от друга, хотя деталь кожуха является цельной. При этом предпочтительной является продольная протяженность фиксирующего элемента. При этом возможна также комбинация с обычной технологией, причем, например, по меньшей мере фиксирующий элемент зажима, установленного по центру, должен иметь длинный путь зажима.
Зажимное приспособление пригодно для установочных электроприборов, таких как, например, штепсельных розеток или выключателей. Эти приборы монтируются из отдельных деталей кожуха, зажимов и крышек. При этом общая деталь кожуха может закрывать несколько зажимов и одновременно в достаточной мере обеспечивать открытое положение винтов.
Другие детали, признаки и преимущества изобретения раскрываются в нижеследующем описании предпочтительного примера выполнения изобретения со ссылкой на чертежи, на которых показано:
Фиг.1 - схематический вид в разрезе цоколя электрической штепсельной розетки с зажимным приспособлением,
Фиг.2 - увеличенный вид в разрезе цоколя штепсельной розетки и зажимного приспособления с незафиксированным винтом и
Фиг.3 - увеличенный вид в разрезе цоколя штепсельной розетки и зажимного приспособления с зафиксированным винтом.
На Фиг.1 изображен цоколь 1 штепсельной розетки в разрезе. Обычные передние крышки графически не изображены.
Цоколь 1 штепсельной розетки содержит опорное кольцо 2 и корпус кожуха 3, в котором установлены контактные гнезда 4 и заземляющая перемычка 5. Контактные гнезда 4 и заземляющая перемычка 5 соединены с зажимом 6, в котором может быть закреплена соответствующая (не показанная) жила электрического провода. Каждый зажим 6 содержит окружающий электропроводящий корпус 7 зажима и винт 8. Сбоку корпуса 7 зажима выполнено отверстие 9 для ввода жилы. В отверстии 10 верхней стенки 11 корпуса 7 зажима установлен с возможностью свободного перемещения винт 8. На резьбовом стержне 12 винта 8 установлена снабженная резьбой пластинчатая зажимная деталь 13, которая вводится в корпус 7 зажима с геометрическим замыканием, а при вращении винта 8 может перемещаться вверх и вниз. В результате вращения винта 8 вставленная жила может фиксироваться между зажимной деталью 13 и верхней стенкой 11 корпуса 7 зажима.
Над зажимами 6 находится плоскостная деталь 14 кожуха, закрывающая все зажимы 6 и соединенная с кожухом 3 цоколя 1 штепсельной розетки по центру в точке 15 крепления. Деталь 14 кожуха имеет над каждым зажимом 6 проходное отверстие 16, через которое с помощью инструмента возможен доступ к головке 17 винта 8.
Проходное отверстие 16 выполнено суженным по сравнению с диаметром головки 17 винта, благодаря чему предотвращается утеря винта 8. Для этого проходное отверстие 16 окружено окантовкой 18, в которую интегрирован по меньшей мере один фиксирующий элемент 19, который в изображенном примере выполнения является свободно вырезанным и эластичным.
Фиксирующий элемент 19 соединен с деталью 14 кожуха в одно целое и проходит в направлении корпуса 7 зажима с клинообразным сужением перпендикулярно окантовке 18. Соединение фиксирующего элемента 19 с деталью 14 кожуха является цельным и осуществляется без изменения поперечного сечения. Необходимая эластичность фиксирующего элемента 19 достигается, в частности, за счет использования термопластичных материалов.
Конструкция фиксирующего элемента 19 в отношении длины и положения или формы контактной поверхности 20 может определять путь зажима и зажимное усилие. При этом для реализации определенного характера изменения усилия предпочтительна, в частности, ступенчатая контактная поверхность 20. Максимальный путь перемещения винта 8 ограничивается окантовкой 18 проходного отверстия 16. Предпочтительным образом вблизи проходного отверстия выполнены фаски 21, так что головка 17 винта в открытом положении центрируется с одной стороны посредством фиксирующего элемента 19, а с другой стороны с помощью фасок 21 и/или окантовкой 18. В результате эффективно предотвращается перекашивание винта 8.
На Фиг.2 изображен неукомплектованный, незатянутый зажим 6 с неопределенным положением винта 8. Такая конфигурация в результате вибраций в любое время может изменять различные положения винта 8 и зажимной детали 13.
На Фиг.3 изображен неукомплектованный зажим 6 с определенным положением винта 8. При закручивании винта 8 головка 17 винта входит в контакт с фиксирующим элементом 19. При этом свободно перемещаемый до этого винт 8 скользит с фрикционным замыканием вдоль ступенчатой контактной поверхности 20 фиксирующего элемента 19, который при этом радиально деформируется и/или перемещается наружу. Благодаря свойствам эластичности материала и упругой отдаче опоры фиксирующего элемента 19 винт 8 фиксируется, причем головка 17 винта в открытом положении центрируется с одной стороны посредством фиксирующего элемента 19, а с другой стороны с помощью фасок 21 и/или окантовки 18.
Изобретение может быть использовано в случае всех рядом расположенных зажимов. Благодаря фиксирующему элементу 19 согласно изобретению каждый зажим 6 является самостоятельным в отношении обеспечения открытого положения. Рядом расположенные винты 8 могут зажиматься в открытом положении независимо друг от друга, хотя деталь 14 кожуха является цельной.
Перечень позиций
1 цоколь штепсельной розетки
2 опорное кольцо
3 корпус кожуха
4 контактные гнезда
5 заземляющая перемычка
6 зажим
7 корпус зажима
8 винт
9 отверстие
10 отверстие
11 стенка
12 резьбовой стержень
13 зажимная деталь
14 деталь кожуха
15 точка крепления
16 проходное отверстие
17 головка винта
18 окантовка
19 фиксирующий элемент
20 контактная поверхность
21 фаска
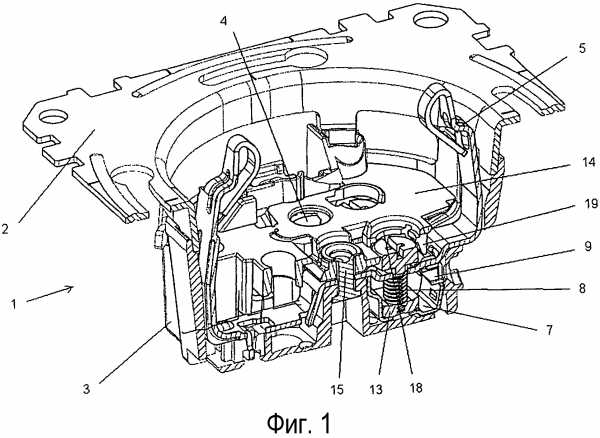
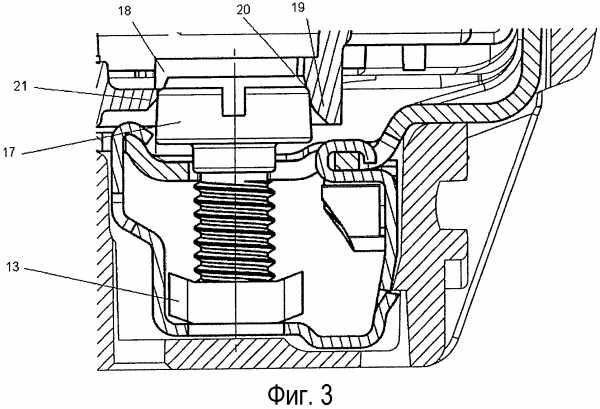
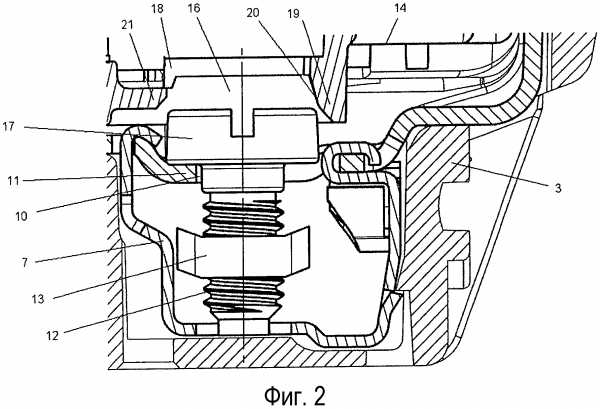
edrid.ru