Кинематическая схема токарного станка. Станок токарный схема
Схема токарного станка
Токарные станки составляют основную часть станочного парка многих металлообрабатывающих предприятий. Токарные станки используются для обработки внутренних и наружных поверхностей тел вращения. Режущим инструментом выступают резцы, сверла, развертки, зенкера, метчики и плашки. При помощи специальных приспособлений, таких как планшайбы, на токарных станках можно обрабатывать сложные и неправильные формы. Использование специальных устройств расширяет возможности оборудования, позволяет выполнять многие другие операции машинной обработки металла.
Расположение шпинделя — вала, на котором закрепляется патрон с обрабатываемой заготовкой, определяет всю конструкцию станка. Более распространены станки с горизонтальным расположением шпинделя, ими являются токарно-винторезные, револьверные, лоботокарные станки. Вертикальный шпиндель имеют токарно-карусельные станки, они предназначены для обработки низких заготовок большого диаметра.
Строение токарно-винторезного станка
Токарно-винторезные станки имеют максимальные технологические возможности из всего оборудования этой группы, что позволяет их эффективно использовать для изготовления небольших серий изделий. Конструкция этих станков была разработана в первой половине XIX века и с тех пор были внесены только небольшие изменения, касающиеся автоматизации оборудования.
Рис.: 1 – передняя бабка с коробкой скоростей, 2 – гитара сменных колес, 3 – коробка подач, 4 – станина, 5 – фартук, 6 – суппорт, 7 – задняя бабка, 8 – шкаф с электрообордованием.
Как и у большинства промышленного оборудования, основой этого станка выступает станина. Она выполняется литьем или сваркой и обязательно крепится к полу анкерными болтами. С левой стороны относительно рабочего на станине располагается передняя или шпиндельная бабка. Она представляет собой пустотелый корпус, в котором находятся, шестерни, шпиндель, подшипники, система смазки и переключения диапазонов. На передней панели бабки находятся многочисленные элементы управления станком. Шпиндель выходит из передней бабки в рабочую зону. На шпиндель устанавливаются приспособления для удержания заготовки, основная часть которых — патроны с разным количеством кулачков.
Ниже передней бабки располагается коробка подач. На её передней панели находятся регуляторы для управления подачей. Коробка подач передает вращение на фартук, располагающийся в центральной зоне станка, при помощи вала при обработке поверхностей или винта при нарезке резьбы. Винт располагается над валом, на большей части его длины нарезана червячная спираль. Вал имеет более короткую спираль червячной передачи, но большего диаметра. В фартуке находится механизм, который преобразует вращательное движение вала или винта в возвратно-поступательное движение суппорта.
Суппорт является элементом станка, на котором устанавливается основной инструмент. Нижние салазки суппорта перемещаются по продольным направляющим, расположенным на станине. Сверху находятся верхние салазки, они расположены перпендикулярно к нижним. Перемещающаяся по ним резцовая каретка имеет возможность повтора в горизонтальной плоскости. На ней находится резцедержатель, в котором закрепляется инструмент. Таким образом, конструкция суппорта и направляющих станины обеспечивает инструменту возможность продольного и поперечного движения, а также наклона относительно центра. Это позволяет обрабатывать инструментом цилиндрические и конические поверхности.
На противоположной стороне станка, с правой стороны, располагается задняя бабка. При обработке длинных заготовок она используется как вторая точка опора, помимо шпинделя. Также на ней размещается инструмент, выполняющий сверление или обработку осевого отверстия в заготовке.
Кинематическая схема токарно-винторезного станка
Главное движение станка осуществляется односкоростным асинхронным трехфазным двигателем, в редких случаях многоскоростным.
Движение с двигателя передается на коробку скоростей посредством клиноременной передачи. В коробке скоростей находится 6-8 валов с зубчатыми колесами. Валы для удобства нумеруются римскими цифрами, первым идет вал со шкивом, далее по кинематике. Выбирая используемые передачи, можно регулировать скорость вращения шпинделя в широких пределах. На токарных станках можно получить более 20 различных скоростей вращения шпинделя с закрепленной на ней заготовкой. Для обратного вращения шпинделя предусмотрены две фрикционные муфты.
Перемещение фартука через коробку подач производится либо напрямую от шпинделя, либо через звено повышения шага, которое находится в коробке скоростей. Оно состоит из трех зубчатых передач, понижающих частоту вращения. Далее находится механизм реверса, который обеспечивает возможность перемещения фартука с суппортом в оба направления.
Коробка подач обладает двумя кинематическими схемами. Первая предназначена для формирования дюймовой резьбы, она содержит одну фрикционную муфту и передает вращение на ходовой винт. Вторая схема предназначена для обработки поверхностей, нарезки метрических резьб. Она передает вращение на ходовой вал. Управление второй цепью производится тремя фрикционными муфтами.
Ряд зубчатых передач находится в фартуке. Они преобразуют вращение вала и винта в передвижение суппорта. Отдельной частью кинематической схемы станка выступает механизм быстрого перемещения суппорта. Он приводится в действие дополнительным электродвигателем посредством ременной передачи.
Условия приобретения и заказ
Купить станок, посмотреть его в работе, ознакомиться со складом станков - Вы можете, связавшись с нашими менеджерами по телефонам 8 (4822) 620-620 или заказать обратный звонок.
Также Вы можете подобрать и приобрести режущий инструмент и оснастку к станку, производства Тайваня, Израиля
Если остались вопросы, заполните форму ниже:
stankomach.com
Токарный станок ИТ-1М: технические характеристики, схемы
Токарный станок модели ИТ-1М является специализированным токарным оборудованием, разработанным для передвижных автомобильных мастерских Министерства обороны, размещавшихся в стандартных КУНГах. Габариты его рабочего пространства практически такие же, как и у самого массового советского токарного станка 16К20. При этом его вес почти в три раза меньше, а мощность главного двигателя составляет всего 3 кВт (против 11 кВт у 16К20).
Электропитание станка может осуществляться как от сети 220 В и 380 В, так и от автономного генератора. ИТ-1М является лучшей моделью для «гаражного использования», т.к. может обрабатывать детали того же габарита, что и промышленные токарные станки, но при этом запитывается от бытовой электросети. Помимо мобильной выпускалась и стационарная версия этого токарного станка, которая носит обозначение ИТ-1ГМ.
Технические характеристики
ИТ-1М является стандартным токарно-винторезным станком и может выполнять все виды обработки характерные для оборудования этого типа.
Его главная особенность — малая мощность главного привода при значительных размерах рабочего пространства.
При небольшом для своего класса весе токарный станок ИТ-1М обладает хорошей жесткостью и виброустойчивостью. Этим он обязан удачной конструкции станины — полой литой основы с перегородками и ребрами жесткости. Еще одним достоинством ИТ-1М является возможность увеличение диаметра обточки до 550 мм. Для этого в станине предусмотрена выемка со вставкой, которую извлекают при точении крупногабаритных заготовок.
Технические параметры станка вполне достаточны для работы в механообрабатывающих подразделениях небольших предприятий. Предельные диаметры обточки изделий в форме вала и диска зависят от размеров заготовки и составляют над:
- станиной – 400 мм;
- выемкой – 550 мм;
- суппортом – 225 мм.
Максимальная длина обработки на ИТ-1М равна 1400 мм (при удаленной вставке — 300 мм), диаметр проходного отверстия шпинделя — 36 мм. Цена деления лимбов на органах управления суппорта составляет 50 мкм, а поворотной шкалы — 1°.
Токарный станок ИТ-1М производился в двух модификациях: базовой и укороченной. В первом случае межцентровое расстояние бабок составляет 1400 мм, а во втором – 1000 мм. Базовая версия весит 1.33 тонны, укороченная легче на 190 кг: ее вес составляет 1.14 тонны.
Сферы применения станков
Не совсем обычное соотношение геометрии рабочего пространства и мощности главного привода токарного станка ИТ-1М объясняется тем, что изначально он разрабатывался по техническому заданию Министерства обороны как штатное оборудование для полевых авторемонтных подразделений Советской армии.
В состав армейской передвижной авторемонтной мастерской (ПАРМ) входило несколько единиц специальной техники, в том числе МРМ-М1 (мастерская ремонтно-механическая) на базе ЗИЛ-131. Она представляла собой КУНГ, в котором размещались электросиловая установка и несколько станков: токарно-винторезный, сверлильный, заточной и точильно-шлифовальный.
Основная специализация ПАРМов — техническое обслуживание и ремонт узлов и агрегатов колесной и гусеничной техники, а также ремонт и изготовление запчастей для других машин и механизмов. При таком направлении деятельности в основную номенклатуру токарной обработки на ИТ-1М входили следующие виды изделий:
- валы, валики, пальцы, втулки;
- диски, фланцы, эксцентрики;
- цилиндрические отверстия;
- посадочные отверстия в корпусных деталях;
- наружные и внутренние резьбы, выполняемые резцами и метчиками.
Помимо Министерства обороны основными потребителями передвижных авторемонтных мастерских являются предприятия нефтегазовой и горнодобывающей отрасли. Сейчас ПАРМЫ выпускают на базе автомобилей КАМАЗ и УРАЛ, при этом Миасский автомобильный завод в комплектации такой мастерской помимо швейцарско-китайского токарного станка Jet указывает и ИТ-1М (возможно, что это просто дань традиции).
Конструктивные особенности
Токарно-винторезный станок ИТ-1М имеет обычную для этого вида оборудования компоновку: станина с направляющими, передняя и задняя бабки и суппорт с резцовыми салазками. Среди его особенностей можно отметить вставку в станину, снятие которой позволяет обрабатывать заготовки большего габарита, а также небольшую мощность главного двигателя, что делает невозможным вести точение с большими глубинами резания. В паспорте станка указано, что на нем можно монтировать приспособления для фрезеровки плоскостей и пазов, а также выполнения расточных и шлифовальных операций.
Габаритные размеры рабочего пространства
Геометрия обработки у ИТ-1М практически такая же, как у и самых распространенных токарно-винторезных станков 1К62 и 16К20. Она позволяет обтачивать детали в форме вала длинной до 1400 мм и диаметром до 225 мм и детали в форме диска максимальным диаметром 400 мм (при вынутой вставке – до 550 мм). У укороченной версии этой модели предельная длина заготовки составляет 1000 мм.
Расположение и функционирование органов управления
Большинство органов управления токарного станка ИТ-1М смонтированы на его передней бабке. На ее верхней части находится панель с тумблерами (слева направо): переключатель выбора напряжения, выключатель двигателя охлаждения и автоматический выключатель, а в нижней части — рычаг выбора скорости шпинделя. Над ним в ряд располагаются три ручки, посредством которых устанавливается величина подачи, тип и шаг резьбы, а справа от него — рычаг управления вращением шпинделя (включение, реверс и торможение). Под панелью тумблеров находятся рукоятка выбора типа резьбы и ручка перебора.
На фартуке смонтированы следующие органы управления: маховичок позиционирования суппорта, ручка позиционирования каретки и поперечных салазок и ручка ходовой гайки. Над маховичком расположена ручка поперечного перемещения каретки, а над ней рычаг поворота и фиксации резцедержателя. Органы управления задней бабки немногочисленны: штурвал передвижения пиноли и рычаг ее зажима. Помимо этого, здесь же находится гайка, фиксирующая положение задней бабки.
Расположение составных частей
Как у и любого токарного станка, базовый компонент ИТ-1М — это станина с двумя рядами направляющих. Слева на ней смонтирована передняя бабка со шпиндельным узлом и шестеренчатыми механизмами, а справа — задняя бабка с пинолью. По направляющим перемещается суппорт с продольными и поперечными салазками и четырехпозиционым резцедержателем.
Движение к суппорту передается от механизма фартука, смонтированного на ходовом валу и ходовом винте, который через них принимает вращение от механизма коробки подач. Задняя бабка позиционируется вручную и фиксируется зажимной гайкой. Выдвижение пиноли также осуществляется вручную посредством вращения маховичка.
Электрическая схема
На токарном станке ИТ-1М для питания электродвигателей используется трехфазное напряжение 380 В и 220 В. Сигнальная и осветительная цепи запитаны от бортовой сети 12 В.
В состав электрооборудования станка входят следующие компоненты:
- главный электродвигатель;
- автоматический выключатель;
- переключатель реверса главного двигателя;
- пакетный переключатель напряжения главного двигателя;
- пакетный переключатель напряжения двигателя системы СОЖ;
- электродвигатель системы СОЖ;
- выключатель насоса СОЖ.
Помимо этого, на суппорте станка установлена лампа освещения на гибкой стойке с выключателем.
Скачать изображение в полном размере
Кинематическая схема
Кинематическая схема токарного станка подобна схемам других универсальных токарно-винторезных станков среднего габарита. Шпиндель получает вращение как напрямую от ведомого шкива, так и от системы переключаемых зубчатых колес. Коробка подач принимает движение от шпиндельного узла через систему сменных зубчатых колес и передает вращение механизму фартука через ходовой винт и ходовой вал.
Система шестерен фартука сообщает движение суппорту, обеспечивая его поперечное и продольное перемещение. Также к кинематической схеме станка относятся механизмы ручного перемещения его рабочих органов и устройства механической блокировки.
Скачать изображение в полном размере
Инструкция по эксплуатации
Единственной документацией, которая поставлялась вместе с токарным станком ИТ-1М, является брошюра под названием «Руководство по эксплуатации» объемом 66 страниц. Последней главой этого руководства является паспорт конкретного изделия с указанием комплекта поставки, отметками о приемке, консервации и упаковке, а также подписями ОТК и заказчика. Обращает на себя внимание, что приемо-сдаточные испытания проводились в «кузове-фургоне подвижной ремонтной мастерской типа МРМ».
В целом инструкция по эксплуатации достаточно традиционна и содержит общие виды, чертежи отдельных компонентов, указания по установке, настройке, наладке и эксплуатации, а также кинематическую и электрические схемы станка. Единственно, что обращает на себя внимание — это отсутствие информации о ремонтных циклах и составе работ по отдельным видам ремонтов.
Техника безопасности
В руководстве по эксплуатации токарного станка ИТ-1М присутствует раздел 2.1 «Меры безопасности», который содержит всего два предложения общего характера. В них указывается на необходимость проведения инструктажей и изучения руководства по эксплуатации перед тем, как приступить к работе на станке.
Остальные указания по мерам безопасности при эксплуатации станка включены в отдельные разделы первой и второй главы. Сюда относятся требования по заземлению, использованию ограждения, проверке блокировочных устройств, защите от стружки и т.п.
vseochpu.ru
Кинематическая схема токарного станка
Токарные станки
Устройство токарного станка
Токарные станкиразделяют на одношпиндельные, многошпиндельные, револьверные, карусельные, автоматы и полуавтоматы, многорезцовые, специализированные и др.
Каждый тип токарных станков имеет несколько моделей. Например, одношпиндельные токарно-винторезные станки выпускают моделей 1620, 1А62, 1К62, 1Е61МТ, 1В616 и т. д.; токарно-револьверные— моделей 1М36, 1336М и т. д.; многорезцовые полуавтоматы — моделей 1721, 1730, 1712П и т. д.; однорезцовые автоматы — моделей 1С616, 161А и т. д.
Рассмотрим устройство токарно-вннторезного станка модели 1К62 (рис. 1). Основные узлы станка: станина 15, передняя бабка 2 , задняя бабка 9, коробка подач 1 с ходовым винтом 13 и ходовым валиком 14, фартук 16 с механизмами подачи, суппорт 5 и электропривод. Кроме этих узлов станок имеет масляный насос для смазки механизмов станка, насос для подачи смазочно-охлаждающей жидкости и кнопочное или рычажное управление для пуска и остановки станка. Включение, выключение и реверсирование электродвигателя производится посредством реверсивного магнитного пускателя с помощью рукоятки.
Суппорт предназначен для закрепления резца и сообщения ему продольной или поперечной подачи. Основанием суппорта служат нижние (продольные) салазки (поз. 4, рис. 1), скользящие по направляющим станины токарного станка. Продольная механическая подача суппорта осуществляется включением рукоятки 17, а ручная — при помощи маховика 19. Укрепленный на суппорте резец будет при этом перемещаться параллельно оси шпинделя.
Для поперечной подачи суппорта вручную вращают рукоятку 18: при этом поперечные салазки вместе с верхней частью суппорта перемещаются перпендикулярно оси шпинделя, скользя по направляющим нижних салазок. На поперечных салазках закреплена поворотная часть суппорта с верхними салазками и резцедержателем 6. При необходимости верхние салазки можно повернуть на нужный угол при помощи поворотной части суппорта. Ручную подачу поворотной или верхней части суппорта осуществляют рукояткой 7.
Задняя бабка (см. рис. 1) служит для поддержания в центрах станка длинных деталей (L >> 4D), а также для закрепления режущего инструмента — сверл, зенкеров, разверток. Она состоит из чугунного корпуса, установленного на скользящей плите. В зависимости от длины обрабатываемой детали заднюю бабку устанавливают на станине в нужном месте при помощи соответствующих приспособлений.
В отверстие верхней части корпуса задней бабки вставляют пустотелый шпиндель — пиноль 8 с закрепленным в нем задним центром. При скоростном резании в пиноль вставляют вращающийся центр. Пиноль и задний центр можно перемещать в продольном направлении при помощи винта с маховиком 11. Закрепляют пиноль в определенном положении рукояткой 10.
|
При обтачивании конических заготовок корпус задней бабки станка можно смещать относительно основания в поперечном направлении посредством болта 12.
Главное движение и движение подачи осуществляются при помощи соответствующих приводов.
Привод главного движения(рис.2) состоит из электродвигателя 7, ременной передачи 2, коробки скоростей 4 и шпинделя 5. Вращение ведомого шкива трансмиссионного вала 1 - 1 передается коробке скоростей и шпинделю 5 (вал II-II). Коробка скоростей позволяет изменять числа оборотов шпинделя, обеспечивая наивыгоднейшие режимы резания.
Существуют два типа коробок скоростей — со ступенчатым и с бесступенчатым (плавным) регулированием чисел оборотов шпинделя.
Первые позволяют получить максимальное, минимальное и ряд промежуточных чисел оборотов, вторые — любое плавно изменяемое число оборотов.
В токарных станках со ступенчатым регулированием числа оборотов шпинделя применяют шестеренные коробки скоростей (рис. 2) или ступенчатые шкивы. Привод главного движения шестеренной коробки скоростей компактнее других типов приводов. На валу I-I расположен подвижной блок 3
|
из зубчатых колес z1 , z2 и z3. При помощи специальной рукоятки этот блок перемещается вдоль вала I-I и поочередно сцепляется с зубчатыми колесами z4, z5или z6, неподвижно закрепленными на втулке А, свободно сидящей на валу II - II. Зубчатые колеса z9 и z10 находятся в постоянном зацеплении с колесами z7 и z8 перебора III - III шестеренной коробки. При включении кулачковой муфты Б влево перебор III - III выключается и шпиндель, в зависимости от положения подвижного зубчатого блока, получает три значения чисел оборотов — n1, n2и n3.
Если число оборотов вала I - I обозначить n0, то
n1 = n0z0/z4, [1]
n2 = n0z2/z5, [2]
n3 = n0z3/z6, [3]
где z1/z4, z2/z5, z3/z6 — передаточные отношения.
При перемещении муфты Б вправо включается перебор III - III с передаточным отношением iпер =(z10/z8)х(z7/z9).
В результате шпиндель II - II получает еще три значения чисел оборотов.
Коробки скоростей с перебором имеют несколько групп чисел оборотов шпинделя. Значения чисел оборотов шпинделя в каждой группе изменяются по геометрической прогрессии, знаменатель которой имеет следующие значения: 1,06; 1,12; 1,26; 1,41; 1,58; 1,78 и 2. Чем меньше , тем меньше разность между числами оборотов в той или иной группе чисел и тем, следовательно, легче выбрать близкое к нужному число оборотов.
Преимущество привода главного движения с шестеренной коробкой скоростей — возможность передачи больших мощностей; при этом эффективная мощность на шпинделе при изменении его оборотов остается постоянной.
|
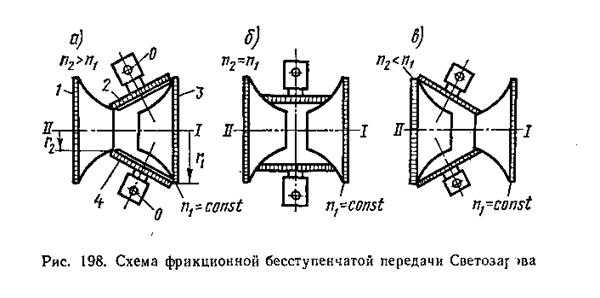
Коробки скоростей с бесступенчатым регулированием чисел оборотов шпинделя имеют конические шкивы, фрикционные, электрические, электромеханические и гидравлические приводы.
В ряде новых токарно-винторезных станков числа оборотов шпинделя изменяются при помощи фрикционного привода системы Светозарова.
На рис.3 показаны три характерных положения, обеспечивающих максимальное - а, среднее - би минимальное - взначения чисел оборотов шпинделя. Стальные фрикционные шайбы 1и 3 с шаровыми поверхностями насажены на пустотелые валы II и I. Вал I посредством муфты соединен с валом электродвигателя, от которого получает вращение шайба 3 с постоянным числом оборотов (n1=const). Распорные пружины, расположенные внутри валов I и II, прижимают шайбы 1 и 3к стальным каткам 2и 4. Каждый из них при помощи специальных механизмов может плавно поворачиваться в вертикальной плоскости относительно оси О на определенный угол.
При включении электродвигателя шайба 3передает вращение каткам 2и 4через фрикционную передачу, сообщающим это вращение шайбе 1. Число оборотов шайбы 1 зависит от отношения активных радиусов r1 и r2 и определяется по формуле
n2=n1 r1/r2. [4]
Изменяя положение катков, можно обеспечить плавное изменение чисел оборотов шпинделя между максимальным и минимальным значениями.
Бесступенчатый привод системы Светозарова позволяет получить диапазон регулирования чисел оборотов шпинделя: D = nmax/nminот 4 до 8. Применяя фрикционную передачу Светозарова в комбинации с трехступенчатой шестеренной коробкой скоростей, можно получить еще более широкий диапазон плавного регулирования чисел оборотов шпинделя.
Привод движения подачипредназначен для передачи движения от шпинделя к суппорту, а также для выбора величины подачи и изменения ее направления.
Движение привода подачи осуществляется от конечного звена привода главного движения — шпинделя. Зубчатое колесо реверсивного механизма насажено на шпиндель или на промежуточный вал, связанный со шпинделем отдельной зубчатой передачей. Иногда источником движения привода подач служит отдельный электродвигатель.
|
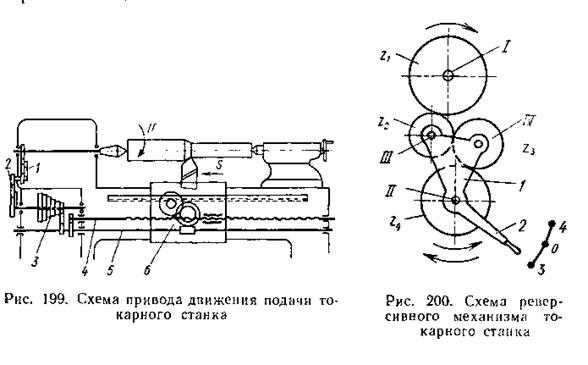
Привод движения подачи токарного станка (рис. 4) состоит из реверсивного механизма 1, гитары 2 сменных зубчатых колес, коробки подач 3 с ходовым винтом 4 и ходовым валиком 5, фартука 6.
Реверсивный механизм предназначен для изменения направления вращения ходового винта или ходового валика, обеспечивая перемещение суппорта с резцом справа налево или слева направо.
Конструкция реверсивного механизма может быть различной. В токарных станках в качестве такого механизма чаще всего применяют трензель с цилиндрическими зубчатыми колесами (рис.5). Зубчатое колесо z1закреплено на шпинделе I, а колесо z2 — на валу II, которым обычно служит вал гитары сменных зубчатых колес. Зубчатые колеса z2 и z3 свободно укреплены на пальцах III и IV обоймы 1 с рукояткой 2. Обойма установлена на валу II и при помощи рукоятки может поворачиваться относительно вала, занимая положение 3, 0или 4. Колеса z2, z3 и z4 находятся в постоянном зацеплении друг с другом.
Если рукоятку 2поставить в положение 3 (как показано на рис.5), то зубчатые колеса z1-z4 будут находиться в последовательном зацеплении и вал II получит вращение, обратное вращению шпинделя. Ставя рукоятку 2в положение 4, вводим в зацепление колеса z1-z3-z4 и вал II получит то же направление вращения, что и шпиндель. В положении 0рукоятки зубчатые колеса z2 и z3 выходят из зацепления с колесом z1 и вращение от шпинделя на вал II не передается — трензель выключен.
|
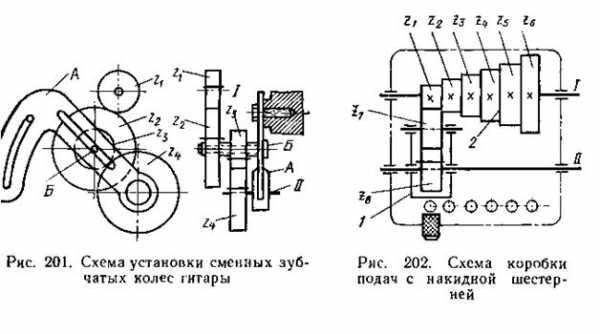
Гитара привода подачи токарного станка представляет механизм, состоящий из набора сменных зубчатых колес и особого устройства, называемого собственно гитарой. Она позволяет изменять число оборотов привода подачи.
В токарных станках используют три способа установки сменных зубчатых колес гитары: одно-, двух- и трехпарную.
Наиболее часто применяемая двухпарная передача (рис.6) имеет четыре зубчатых колеса z1— z4, которые передают вращение от вала I трензеля на вал II коробки передач. Зубчатое колесо г1 закреплено на валуI, а колесо z4 — на валу II; колеса z2 и z3 находятся на общей втулке со шпонкой и помещаются на пальце Б.
Для получения новых передаточных отношений межосевое расстояние изменяют перемещением пальца Б по прямолинейному пазу и поворотом гитары А относительно оси вала II по дуговому пазу. Передаточное отношение сменных зубчатых колес гитары
iгит = (z1/z2).(z3/z4) [5]
Коробка подач, расположенная с передней стороны станка под бабкой, позволяет переключением рычагов быстро изменять подачу. В токарных станках чаще всего применяют коробки подач с накидной шестерней (рис.7). Механизм представляет блок 2 зубчатых колес z1 — z6, насаженный на вал I. На валу I скользящей шпонкой закрепляют колесо z8 и обойму 1. Накидная шестерня z7 находится в постоянном зацеплении с колесом z8 и крепится в обойме 1. Передачу обычно осуществляют от ведущего вала I к ведомому II. Накидную шестерню можно сцепить с любым зубчатым колесом блока 2 поворотом обоймы 1 относительно вала II и перемещением ее вдоль вала в соответствующее фиксируемое положение.
|
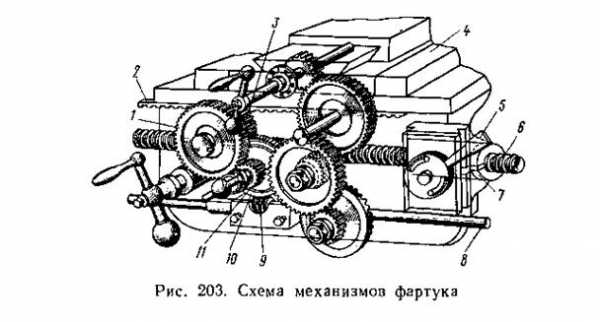
Фартук прикреплен к нижней части каретки суппорта. Заключенные в фартук механизмы подачи служат для преобразования вращательного движения, получаемого от ходового винта или ходового валика, в поступательное движение (подачу) суппорта, на котором закреплен резец. В фартуке имеется система червячных и зубчатых передач (рис. 8). При нарезании резьбы используют ходовой винт 6. При выполнении других токарных работ движение подачи осуществляется через ходовой валик 8, имеющий червяк 9 на скользящей шпонке. Червяк получает вращательное движение и, кроме того, может перемещаться вдоль валика. Вращение червяка передается червячному зубчатому колесу 10 и расположенному па одной оси с ним цилиндрическому зубчатому колесу 11, которое находится в зацеплении с колесом 1, передающим вращение соосному с ним колесу 3. Это колесо катится по неподвижной рейке 2, прикрепленной к станине токарного станка, заставляя перемещаться суппорт 4, связанный с фартуком. В результате вращательное движение ходового валика преобразуется в продольное поступательное движение суппорта.
Имеющиеся в фартуке механизмы могут преобразовывать вращательное движение ходового валика в поперечное движение резца.
При нарезании резьбы ходовой валик 8 отключается от остальных частей механизма фартука.
Ходовой винт 6 имеет разъемную гайку 7 (называемую маточной). При включении рукоятки 5 половинки разъемной гайки плотно охватывают вращающийся ходовой винт, вследствие чего гайка, а вместе с ней и суппорт осуществляют поступательное движение; при выключении рукоятки половинки гайки расходятся, освобождая винт и останавливая суппорт.
Токарные автоматы
Для выполнения ряда токарных работ применяют полуавтоматы и автоматы.У токарных полуавтоматов автоматизированы обычно только рабочие операции по обработке детали (снятие стружки резцом), а вспомогательные операции (установка и закрепление обрабатываемой заготовки, освобождение и снятие ее со станка, пуск станка, контроль размеров обрабатываемой детали и т. д.) выполняются вручную. У автоматов автоматизирован весь цикл обработки детали.
У станков-автоматов различные операции автоматизированы при помощи механических, гидравлических, электрических, пневматических, электронных и смешанных устройств (систем). Работа этих устройств регламентируется программным устройством с применением перфолент или счетно-решающих машин (в системе программного управления).
Рассмотрим схему устройства и работы токарного автомата модели 1С616 (рис. 15 а). Автомат предназначен для обработки валов в центрах по автоматическому циклу (с загрузкой заготовок и разгрузкой деталей) с применением гидрокопирования по программному управлению.
Станок установлен на двух пустотелых тумбах. В левой тумбе 1 смонтирована коробка скоростей с рукоятками для установки числа оборотов шпинделя. Коробка скоростей имеет 12 ступеней чисел оборотов шпинделя (от 90 до 2240 об/мин). В правой тумбе 12 расположено гидрооборудование станка (гидропривод). Выше левой тумбы размещен механизм программирования 16 со штоком 15, получающим перемещение от фартука 14. Механизм программирования 16 (рис. 15,б) подает электрические команды при автоматическом цикле работы. Электрический контакт осуществляется щетками, расположенными на движущейся каретке, через упоры, закрепленные на плите. Каретка со щетками, проходя над упорами, дает соответствующие команды («Подача», «Быстрый обратный ход», «Стоп» и т. д.).
Фартук, получает поступательное движение от ходового валика 13, который в свою очередь получает подачу от отдельного гидромотора МГ-152 с редуктором, смонтированного на правом торце станины. На фартуке расположена панель электроуправления для пуска и остановки станка, а также быстрого хода каретки.
В шпиндельной бабке 3 размещен шпиндель 2 с гидроцилиндром 2а для зажима заготовки, подаваемой на центры станка. С другой стороны заготовка зажимается задней бабкой 8 при помощи гидроцилиндра 8а. Последний осуществляет осевое перемещение пиноли задней бабки.
Заготовки поступают на загрузочный приемник 4 с цепной передачей I7, движение которой сообщает гидроцилиндр 4а через храповик 18. В соответствии с заданной программой заготовка при помощи механизма проталкивания 19 с гидроцилиндром 19а, укрепляемого на заднем торце шпиндельной бабки, проталкивается планками по лотку заготовок к автооператору 7. Последний имеет два подающих механизма с лотками (один над другим) с гидроцилиндрами 7а. Заготовка с нижнего лотка подается на линию центров станка; перед этим верхний лоток убирает готовую деталь, поднимая ее на уровень лотка готовых деталей. Поступившая на линию центров заготовка при помощи гидроцилиндров 8а и 2а зажимается и закрепляется в патроне специальным устройством — цангой (помещается в патроне).
После настройки станка, зажатия и закрепления заготовки пакетный выключатель на щите шкафа 9 с электрооборудованием ставят в положение «Автоматическая работа» и кнопкой «Пуск» (на панели фартука включают главное движение (главный электродвигатель) и движение подачи (подвод гидрокопировального суппорта 6 к заготовке и щупа к копиру). С включением подачи последующие команды выполняются механизмом программирования через упоры плиты и каретку.
Гидрокопировальный суппорт (типа СГП2) (взамен поворотной части обычного суппорта) установлен на токарном автомате под углом 60° к оси центров станка. Гидросуппорт действует по схеме однокоординатного копирования с заданной продольной подачей. В качестве копира применяют плоский стальной шаблон.
При подаче очередной заготовки на нижний лоток механизм проталкивания при помощи пальца 5, находящегося на уровне лотка готовых деталей, проталкивает детали по лотку и подает на лоток сбрасывателя 10, установленного на направляющих станины правее задней бабки. Получив очередную деталь, сбрасыватель при помощи гидроцилиндра 10а опускается, наклоняет лоток и сбрасывает готовую деталь на приемник 11.
|
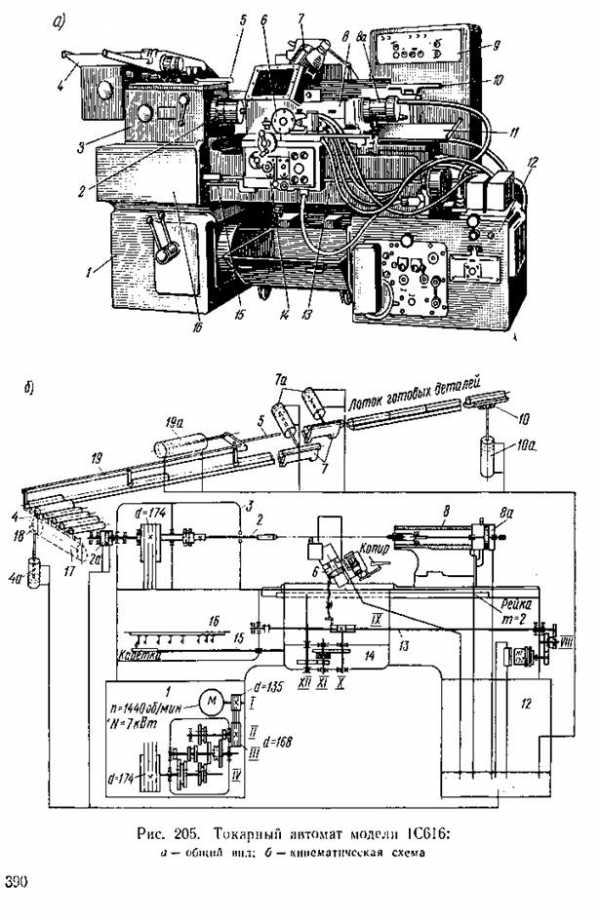
Токарно-затыловочные станки
Общие сведения
Токарно-револьверные станки применяют в серийном производстве для обработки деталей сложной конфигурации из прутков или из штучных заготовок. В зависимости от этого токарно-револьверные станки делят на прутковые и патронные. На токарно-револьверных станках можно выполнять почти все основные токарные операции. Применение этих станков рационально в том случае, если по технологическому процессу обработки детали требуется последовательное применение различных режущих инструментов (резцов, сверл, разверток, метчиков и т. д.).
Инструменты в необходимой последовательности крепят в соответствующих позициях револьверной головки и резцедержателях поперечных суппортов. Все режущие инструменты устанавливают заранее при наладке станка, и в процессе обработки их поочередно или параллельно вводят в работу.
По конструкции револьверной головки станки делят на станки с вертикальной (рисунок 20,а) и горизонтальной (рисунок 20 б и в) осями вращения револьверной головки. Револьверные головки бывают цилиндрическими и призматическими.
Рис. 20 – Револьверные головки
Типажом станков предусмотрен ряд токарно-револьверных станков с наибольшим диаметром обрабатываемых прутков 16, 18, 25, 40, 65 и 100 мм. Патронные токарно-револьверные станки выпускают с наибольшим диаметром обрабатываемой заготовки от 160 до 630 мм. В токарно-револьверных станках частота вращения и подача переключаются в основном с помощью командоаппаратов, а также штекерных устройств.
Основными размерами, характеризующими прутковые револьверные станки, являются наибольший диаметр обрабатываемого прутка и диаметр отверстия шпинделя, а размерами, характеризующими станки для работы в патроне, — наибольший диаметр обрабатываемой в патроне заготовки над станиной и над суппортом. К основным размерам также относят максимальное расстояние от переднего конца шпинделя до передней грани или торца револьверной головки и наибольшее перемещение головки.
Преимуществами токарно-револьверных станков по сравнению с токарными являются возможность сокращения машинного времени в результате применения многорезцовых державок и одновременной обработки детали инструментами револьверной головки и поперечного суппорта и сравнительно малые затраты вспомогательного времени в результате предварительной наладки станка на обработку несколькими инструментами.
Мальтийский механизм.
В токарно-револьверных станках дискретный поворот револьверной головки достигается за счет использования мальтийского механизма (рис. 21).
Мальтийский крест, устройство для преобразования непрерывного вращения в прерывистое. Мальтийский механизм — одна из составных частей механических систем станков-автоматов, кинопроекционных аппаратов и установок, в которых необходимы периодические остановки в движении, например, для выполнения определённой технологической операции, выдержки кадра и т.п. Применяются мальтийский механизм с внешним и внутренним зацеплением. В мальтийском механизме с внешним зацеплением (рис. 21) при вращении ведущего звена (кривошипа) 1 его палец 2 в точке А входит в прорезь 3 ведомого звена (креста) 4 и, скользя в ней, поворачивает крест. В точке В палец выходит из прорези. Крест останавливается и остаётся неподвижным, пока палец кривошипа, продолжая своё движение, не переместится снова в точку А, где войдёт в следующую прорезь креста, и т. д. Для фиксации креста, т. е. предотвращения самопроизвольного поворота креста во время остановки, кривошип снабжен запирающим цилиндрическим выступом 5 с выемкой, а крест очерчен дугами окружностей (это придаёт ему сходство с мальтийским крестом — эмблемой Мальтийского ордена, откуда и произошло название механизма). Поворот креста возможен только тогда, когда его луч совмещен с выемкой выступа. Обычно кресты изготовляют с числом прорезей Z от 3 до 12. За один оборот кривошипа происходит поворот креста на 1/Z часть оборота. При вращении кривошипа с постоянной угловой скоростью отношение времени движения креста к времени его остановки равно отношению длин дуг ÈАСВ к ÈАС'В или (Z — 2)/(Z + 2). Для увеличения продолжительности остановок кривошипу сообщают переменную скорость вращения: большую во время поворота креста и малую вплоть до остановки креста. Если же требуется сократить время остановок, кривошип снабжают несколькими пальцами.
Мальтийские механизмы с внутренним зацеплением отличаются плавностью поворота креста и имеют небольшие габариты.
В узлах металлообрабатывающих станков находят применение пространственные мальтийские механизмы, предназначенные для передачи вращения на вал, скрещивающийся с ведущим валом обычно под углом 90°.
Рисунок 21 – Мальтийский механизм с внешним зацеплением:
w1 и w2 угловые скорости ведущего и ведомого звеньев
Лобовые токарные станки
Для обработки коротких заготовок большого диаметра в единичном производстве и в ремонтных мастерских применяют лобовые токарные станки. На них обтачивают наружные цилиндрические и конические поверхности, подрезают торцы, протачивают канавки, растачивают внутренние отверстия и др. У лобовых станков сравнительно малая длина и большой (до 4 м) диаметр планшайбы. Лобовой станок 1А693 Краматорского станкостроительного завода показан на рисунок 22. Техническая характеристика приведена в таблице 3.
Таблица 3
Техническая характеристика станка
Наибольшее расстояние между центрами, мм | |
Наибольший диаметр обрабатываемой заготовки, мм | |
Наибольшая масса заготовки, кг | |
Частота вращения шпинделя, мин-1 | 0,8—63 |
Мощность привода шпинделя, кВт | |
Масса, кг |
Из-за невысокой точности, сложности установки заготовки, а также низкой производительности лобовые станки применяют редко. Они вытеснены более совершенными карусельными станками.
Карусельные станки
Карусельные станки применяют для обработки тяжелых деталей большого диаметра, но сравнительно небольшой длины. На них можно обтачивать и растачивать цилиндрические и конические поверхности, подрезать торцы, прорезать кольцевые канавки, сверлить, зенкеровать, развертывать и др. Основными размерами карусельных станков считают наибольшие диаметр и высоту обрабатываемой на станке заготовки. При этом каждая последующая по размеру модель станка позволяет обрабатывать заготовку, в 1,25 раза большую по диаметру, чем предыдущая, т. е. у карусельных станков принят знаменатель размерного ряда j = 1,26.
![]() | ![]() | ![]() | |||||
Рисунок 22 – Лобовой станок 1А693 | Рисунок 23 – Одностоечный карусельный станок 1512 | Рисунок 24 – Двухстоечный карусельный станок 1525 | |||||
В передней бабке 4, жестко закрепленной на плите 1, размещена коробка скоростей. Основание 2 суппорта с продольными направляющими и заднюю бабку 6 можно переставлять по плите в требуемые положения и закреплять на ней болтами, головки которых входят в пазы плиты. Обрабатываемую заготовку закреп-ляют на планшайбе 5 в кулачках или с помощью прихватов и болтов (при необходимости ее поддерживают центром задней бабки). Движение подачи осуществляется от отдельного электродвигателя; суппорту 3 можно сообщать продольное и поперечное движение подачи. | Станина 1 одностоечного карусельного станка жестко скреплена со стойкой 9, имеющей вертикальные направляющие для перемещения по ним траверсы 6 и бокового суппорта 10 с четырехместным резцедержателем 12. На станине на круговых направляющих расположена планшайба 2 для установки на ней обрабатываемых деталей или приспособлений. Коробка скоростей размещена внутри станины. На горизонтальных направляющих траверсы может перемещаться вертикальный револьверный суппорт 5 с пятипозиционной револьверной головкой 4. Привод подач револьверного и бокового 10 суппортов осуществляется от коробок подач 7 и II. Револьверный суппорт можно перемещать вручную маховичками 8, а боковой — маховичками 13. Станком управляют с пульта 3. | Двухстоечный карусельный станок 1525 имеет следующие основные узлы: стол 1, планшайбу 2, стойки 5 и II, скрепленные между собой балкой 10. По вертикальным направляющим стоек с помощью вертикальных ходовых винтов 6 и 12 от отдельного электродвигателя может перемещаться траверса 8. По ее горизонтальным направляющим могут перемещаться два вертикальных револьверных суппорта 7 и 9. Суппорты приводятся в движение двумя одинаковыми коробками подач 4 и 13. В обычном исполнении станок не имеет бокового суппорта. С подвесной кнопочной станции 3 дистанционно управляют станком. Маховичками 14 осуществляют ручное перемещение суппортов. | |||||
Рисунок 25 – Кинематическая схема станка 1512
По компоновке карусельные станки подразделяют на одно- и двухстоечные, представленные на рисунках 23 и 24.
Двухстоечные станки предназначены для обработки деталей диаметром свыше 2000 мм. Карусельные станки, на которых обрабатывают детали диаметром свыше 6300 мм, выпускают поштучно, и их принято называть уникальными.
Одностоечный карусельный станок 1512 предназначен для токарной обработки крупных деталей типа корпусов, маховиков и т.п. Техническая характеристика приведена в таблице 4. Кинематическая схема показана на рисунке 25
Таблица 4
Техническая характеристика станка
Диаметр планшайбы, мм | |
Размеры обрабатываемых заготовок, мм: диаметр высота | До 1250 До 1000 |
Частота вращения планшайбы, мин-1 | 5—250 |
Подача суппортов, мм/об | 0,07—12,5 |
Мощность электродвигателя главного движения, кВт | |
Частота вращения электродвигателя главного движения, мин-1 |
Токарные станки
Устройство токарного станка
Токарные станкиразделяют на одношпиндельные, многошпиндельные, револьверные, карусельные, автоматы и полуавтоматы, многорезцовые, специализированные и др.
Каждый тип токарных станков имеет несколько моделей. Например, одношпиндельные токарно-винторезные станки выпускают моделей 1620, 1А62, 1К62, 1Е61МТ, 1В616 и т. д.; токарно-револьверные— моделей 1М36, 1336М и т. д.; многорезцовые полуавтоматы — моделей 1721, 1730, 1712П и т. д.; однорезцовые автоматы — моделей 1С616, 161А и т. д.
Рассмотрим устройство токарно-вннторезного станка модели 1К62 (рис. 1). Основные узлы станка: станина 15, передняя бабка 2 , задняя бабка 9, коробка подач 1 с ходовым винтом 13 и ходовым валиком 14, фартук 16 с механизмами подачи, суппорт 5 и электропривод. Кроме этих узлов станок имеет масляный насос для смазки механизмов станка, насос для подачи смазочно-охлаждающей жидкости и кнопочное или рычажное управление для пуска и остановки станка. Включение, выключение и реверсирование электродвигателя производится посредством реверсивного магнитного пускателя с помощью рукоятки.
Суппорт предназначен для закрепления резца и сообщения ему продольной или поперечной подачи. Основанием суппорта служат нижние (продольные) салазки (поз. 4, рис. 1), скользящие по направляющим станины токарного станка. Продольная механическая подача суппорта осуществляется включением рукоятки 17, а ручная — при помощи маховика 19. Укрепленный на суппорте резец будет при этом перемещаться параллельно оси шпинделя.
Для поперечной подачи суппорта вручную вращают рукоятку 18: при этом поперечные салазки вместе с верхней частью суппорта перемещаются перпендикулярно оси шпинделя, скользя по направляющим нижних салазок. На поперечных салазках закреплена поворотная часть суппорта с верхними салазками и резцедержателем 6. При необходимости верхние салазки можно повернуть на нужный угол при помощи поворотной части суппорта. Ручную подачу поворотной или верхней части суппорта осуществляют рукояткой 7.
Задняя бабка (см. рис. 1) служит для поддержания в центрах станка длинных деталей (L >> 4D), а также для закрепления режущего инструмента — сверл, зенкеров, разверток. Она состоит из чугунного корпуса, установленного на скользящей плите. В зависимости от длины обрабатываемой детали заднюю бабку устанавливают на станине в нужном месте при помощи соответствующих приспособлений.
В отверстие верхней части корпуса задней бабки вставляют пустотелый шпиндель — пиноль 8 с закрепленным в нем задним центром. При скоростном резании в пиноль вставляют вращающийся центр. Пиноль и задний центр можно перемещать в продольном направлении при помощи винта с маховиком 11. Закрепляют пиноль в определенном положении рукояткой 10.
|
При обтачивании конических заготовок корпус задней бабки станка можно смещать относительно основания в поперечном направлении посредством болта 12.
Главное движение и движение подачи осуществляются при помощи соответствующих приводов.
Привод главного движения(рис.2) состоит из электродвигателя 7, ременной передачи 2, коробки скоростей 4 и шпинделя 5. Вращение ведомого шкива трансмиссионного вала 1 - 1 передается коробке скоростей и шпинделю 5 (вал II-II). Коробка скоростей позволяет изменять числа оборотов шпинделя, обеспечивая наивыгоднейшие режимы резания.
Существуют два типа коробок скоростей — со ступенчатым и с бесступенчатым (плавным) регулированием чисел оборотов шпинделя.
Первые позволяют получить максимальное, минимальное и ряд промежуточных чисел оборотов, вторые — любое плавно изменяемое число оборотов.
В токарных станках со ступенчатым регулированием числа оборотов шпинделя применяют шестеренные коробки скоростей (рис. 2) или ступенчатые шкивы. Привод главного движения шестеренной коробки скоростей компактнее других типов приводов. На валу I-I расположен подвижной блок 3
|
из зубчатых колес z1 , z2 и z3. При помощи специальной рукоятки этот блок перемещается вдоль вала I-I и поочередно сцепляется с зубчатыми колесами z4, z5или z6, неподвижно закрепленными на втулке А, свободно сидящей на валу II - II. Зубчатые колеса z9 и z10 находятся в постоянном зацеплении с колесами z7 и z8 перебора III - III шестеренной коробки. При включении кулачковой муфты Б влево перебор III - III выключается и шпиндель, в зависимости от положения подвижного зубчатого блока, получает три значения чисел оборотов — n1, n2и n3.
infopedia.su
Станки токарной группы
9
1.Токарные станки 2
1.1. Устройство токарного станка 2
Рис. 1. Общий вид токарного станка модели 1К62 3
Рис.4 Схема привода подачи токарного Рис.5 Схема реверсивного 6
Рис.6 Схема установки сменных зуб- Рис.7 Схема коробки подач 7
1.2. Кинематическая схема токарного станка 9
1.3. Основные виды токарных работ 12
2. Токарные автоматы 17
3.Токарно-затыловочные станки 21
3.1 Основные сведения о затыловании. 21
3.2 Универсальный токарно-затыловочный станок 1Б811 22
4 Токарно-револьверные станки 23
4.1 Общие сведения 23
4.2 Токарно-револьверные станки с вертикальной осью револьверной головки. 24
4.3 Токарно-револьверный станок 1Г340П с горизонтальной осью револьверной головки 24
4.4 Мальтийский механизм. 26
5Лобовые токарные и карусельные станки 27
5.1 Лобовые токарные станки 27
5.2 Карусельные станки 27
6.Выполнение основных технологических операций токарной обработки. 31
6.1Обтачивание, подрезание и отрезание заготовок 31
Обтачивание гладких наружных цилиндрических поверхностей. 31
Обработка плоских торцовых поверхностей и уступов. 33
Вытачивание наружных канавок и отрезание. 38
6.2 Сверление и расверливание оверстий на токарном станке 38
Выбор режима резания при сверлении. 42
6.2 Зенкерование, развертывание и растачивание оверстий. 42
1.Токарные станки
1.1. Устройство токарного станка
Токарные станки разделяют на одношпиндельные, многошпиндельные, револьверные, карусельные, автоматы и полуавтоматы, многорезцовые, специализированные и др.
Каждый тип токарных станков имеет несколько моделей. Например, одношпиндельные токарно-винторезные станки выпускают моделей 1620, 1А62, 1К62, 1Е61МТ, 1В616 и т. д.; токарно-револьверные— моделей 1М36, 1336М и т. д.; многорезцовые полуавтоматы — моделей 1721, 1730, 1712П и т. д.; однорезцовые автоматы — моделей 1С616, 161А и т. д.
Рассмотрим устройство токарно-вннторезного станка модели 1К62 (рис. 1). Основные узлы станка: станина 15, передняя бабка 2 , задняя бабка 9, коробка подач 1 с ходовым винтом 13 и ходовым валиком 14, фартук 16 с механизмами подачи, суппорт 5 и электропривод. Кроме этих узлов станок имеет масляный насос для смазки механизмов станка, насос для подачи смазочно-охлаждающей жидкости и кнопочное или рычажное управление для пуска и остановки станка. Включение, выключение и реверсирование электродвигателя производится посредством реверсивного магнитного пускателя с помощью рукоятки.
Суппорт предназначен для закрепления резца и сообщения ему продольной или поперечной подачи. Основанием суппорта служат нижние (продольные) салазки (поз. 4, рис. 1), скользящие по направляющим станины токарного станка. Продольная механическая подача суппорта осуществляется включением рукоятки 17, а ручная — при помощи маховика 19. Укрепленный на суппорте резец будет при этом перемещаться параллельно оси шпинделя.
Для поперечной подачи суппорта вручную вращают рукоятку 18: при этом поперечные салазки вместе с верхней частью суппорта перемещаются перпендикулярно оси шпинделя, скользя по направляющим нижних салазок. На поперечных салазках закреплена поворотная часть суппорта с верхними салазками и резцедержателем 6. При необходимости верхние салазки можно повернуть на нужный угол при помощи поворотной части суппорта. Ручную подачу поворотной или верхней части суппорта осуществляют рукояткой 7.
Задняя бабка (см. рис. 1) служит для поддержания в центрах станка длинных деталей (L >> 4D), а также для закрепления режущего инструмента — сверл, зенкеров, разверток. Она состоит из чугунного корпуса, установленного на скользящей плите. В зависимости от длины обрабатываемой детали заднюю бабку устанавливают на станине в нужном месте при помощи соответствующих приспособлений.
В отверстие верхней части корпуса задней бабки вставляют пустотелый шпиндель — пиноль 8 с закрепленным в нем задним центром. При скоростном резании в пиноль вставляют вращающийся центр. Пиноль и задний центр можно перемещать в продольном направлении при помощи винта с маховиком 11. Закрепляют пиноль в определенном положении рукояткой 10.
Рис. 1. Общий вид токарного станка модели 1К62
1 – коробка подач; 2 – передняя бабка; 3 – рукоятка установки чисел оборотов шпинделя; 4 – нижние салазки суппорта; 5 – суппорт; 6 – резцедержатель; 7 – рукоятка подачи поворотной части суппорта; 8 – пиноль задней бабки; 9 – задняя бабка; 10 – рукоятка закрепления пиноли; 11 – маховик продольного перемещения пиноли; 12 – болт; 13 – ходовой винт; 14 – ходовой валик; 15 – станина станка; 16 – фартук; 17 – рукоятка включения продольной механической подачи; 18 и 19 – рукоятки продольной и поперечной ручной подач; 20 – рукоятка реверсирования шпинделя; 21 – рукоятка установки величины подачи.
При обтачивании конических заготовок корпус задней бабки станка можно смещать относительно основания в поперечном направлении посредством болта 12.
Главное движение и движение подачи осуществляются при помощи соответствующих приводов.
Привод главного движения (рис.2) состоит из электродвигателя 7, ременной передачи 2, коробки скоростей 4 и шпинделя 5. Вращение ведомого шкива трансмиссионного вала 1 - 1 передается коробке скоростей и шпинделю 5 (вал II-II). Коробка скоростей позволяет изменять числа оборотов шпинделя, обеспечивая наивыгоднейшие режимы резания.
Существуют два типа коробок скоростей — со ступенчатым и с бесступенчатым (плавным) регулированием чисел оборотов шпинделя.
Первые позволяют получить максимальное, минимальное и ряд промежуточных чисел оборотов, вторые — любое плавно изменяемое число оборотов.
В токарных станках со ступенчатым регулированием числа оборотов шпинделя применяют шестеренные коробки скоростей (рис. 2) или ступенчатые шкивы. Привод главного движения шестеренной коробки скоростей компактнее других типов приводов. На валу I-I расположен подвижной блок 3
Рис. 2. Схема привода главного движения токарного станка с шестеренной коробкой скоростей.
из зубчатых колес z1 , z2 и z3. При помощи специальной рукоятки этот блок перемещается вдоль вала I-I и поочередно сцепляется с зубчатыми колесами z4, z5 или z6, неподвижно закрепленными на втулке А, свободно сидящей на валу II - II. Зубчатые колеса z9 и z10 находятся в постоянном зацеплении с колесами z7 и z8 перебора III - III шестеренной коробки. При включении кулачковой муфты Б влево перебор III - III выключается и шпиндель, в зависимости от положения подвижного зубчатого блока, получает три значения чисел оборотов — n1, n2 и n3.
Если число оборотов вала I - I обозначить n0, то
n1 = n0z0/z4, [1]
n2 = n0z2/z5, [2]
n3 = n0z3/z6, [3]
где z1/z4, z2/z5, z3/z6 — передаточные отношения.
При перемещении муфты Б вправо включается перебор III - III с передаточным отношением iпер =(z10/z8)х(z7/z9).
В результате шпиндель II - II получает еще три значения чисел оборотов.
Коробки скоростей с перебором имеют несколько групп чисел оборотов шпинделя. Значения чисел оборотов шпинделя в каждой группе изменяются по геометрической прогрессии, знаменатель которой
имеет следующие значения: 1,06; 1,12; 1,26; 1,41; 1,58; 1,78 и 2. Чем меньше
, тем меньше разность между числами оборотов в той или иной группе чисел и тем, следовательно, легче выбрать близкое к нужному число оборотов.
Преимущество привода главного движения с шестеренной коробкой скоростей — возможность передачи больших мощностей; при этом эффективная мощность на шпинделе при изменении его оборотов остается постоянной.
Рис. 3. Схема фрикционной бесступенчатой передачи Светозарова
Коробки скоростей с бесступенчатым регулированием чисел оборотов шпинделя имеют конические шкивы, фрикционные, электрические, электромеханические и гидравлические приводы.
В ряде новых токарно-винторезных станков числа оборотов шпинделя изменяются при помощи фрикционного привода системы Светозарова.
На рис.3 показаны три характерных положения, обеспечивающих максимальное - а, среднее - б и минимальное - в значения чисел оборотов шпинделя. Стальные фрикционные шайбы 1 и 3 с шаровыми поверхностями насажены на пустотелые валы II и I. Вал I посредством муфты соединен с валом электродвигателя, от которого получает вращение шайба 3 с постоянным числом оборотов (n1=const). Распорные пружины, расположенные внутри валов I и II, прижимают шайбы 1 и 3 к стальным каткам 2 и 4. Каждый из них при помощи специальных механизмов может плавно поворачиваться в вертикальной плоскости относительно оси О на определенный угол.
При включении электродвигателя шайба 3 передает вращение каткам 2 и 4 через фрикционную передачу, сообщающим это вращение шайбе 1. Число оборотов шайбы 1 зависит от отношения активных радиусов r1 и r2 и определяется по формуле
n2=n1 r1/r2. [4]
Изменяя положение катков, можно обеспечить плавное изменение чисел оборотов шпинделя между максимальным и минимальным значениями.
Бесступенчатый привод системы Светозарова позволяет получить диапазон регулирования чисел оборотов шпинделя: = nmax/nmin от 4 до 8. Применяя фрикционную передачу Светозарова в комбинации с трехступенчатой шестеренной коробкой скоростей, можно получить еще более широкий диапазон плавного регулирования чисел оборотов шпинделя.
Привод движения подачи предназначен для передачи движения от шпинделя к суппорту, а также для выбора величины подачи и изменения ее направления.
Движение привода подачи осуществляется от конечного звена привода главного движения — шпинделя. Зубчатое колесо реверсивного механизма насажено на шпиндель или на промежуточный вал, связанный со шпинделем отдельной зубчатой передачей. Иногда источником движения привода подач служит отдельный электродвигатель.
Рис.4 Схема привода подачи токарного Рис.5 Схема реверсивного
станка механизма токарного станка
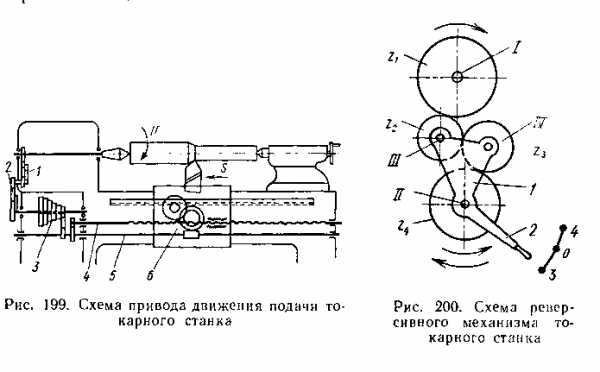
Привод движения подачи токарного станка (рис. 4) состоит из реверсивного механизма 1, гитары 2 сменных зубчатых колес, коробки подач 3 с ходовым винтом 4 и ходовым валиком 5, фартука 6.
Реверсивный механизм предназначен для изменения направления вращения ходового винта или ходового валика, обеспечивая перемещение суппорта с резцом справа налево или слева направо.
Конструкция реверсивного механизма может быть различной. В токарных станках в качестве такого механизма чаще всего применяют трензель с цилиндрическими зубчатыми колесами (рис.5). Зубчатое колесо z1 закреплено на шпинделе I, а колесо z2 — на валу II, которым обычно служит вал гитары сменных зубчатых колес. Зубчатые колеса z2 и z3 свободно укреплены на пальцах III и IV обоймы 1 с рукояткой 2. Обойма установлена на валу II и при помощи рукоятки может поворачиваться относительно вала, занимая положение 3, 0 или 4. Колеса z2, z3 и z4 находятся в постоянном зацеплении друг с другом.
Если рукоятку 2 поставить в положение 3 (как показано на рис.5), то зубчатые колеса z1-z4 будут находиться в последовательном зацеплении и вал II получит вращение, обратное вращению шпинделя. Ставя рукоятку 2 в положение 4, вводим в зацепление колеса z1-z3-z4 и вал II получит то же направление вращения, что и шпиндель. В положении 0 рукоятки зубчатые колеса z2 и z3 выходят из зацепления с колесом z1 и вращение от шпинделя на вал II не передается — трензель выключен.
Рис.6 Схема установки сменных зуб- Рис.7 Схема коробки подач
чатых колес гитары. с накидной шестерней
Гитара привода подачи токарного станка представляет механизм, состоящий из набора сменных зубчатых колес и особого устройства, называемого собственно гитарой. Она позволяет изменять число оборотов привода подачи.
В токарных станках используют три способа установки сменных зубчатых колес гитары: одно-, двух- и трехпарную.
Наиболее часто применяемая двухпарная передача (рис.6) имеет четыре зубчатых колеса z1 — z4, которые передают вращение от вала I трензеля на вал II коробки передач. Зубчатое колесо г1 закреплено на валуI, а колесо z4 — на валу II; колеса z2 и z3 находятся на общей втулке со шпонкой и помещаются на пальце Б.
Для получения новых передаточных отношений межосевое расстояние изменяют перемещением пальца Б по прямолинейному пазу и поворотом гитары А относительно оси вала II по дуговому пазу. Передаточное отношение сменных зубчатых колес гитары
гит = (z1/z2).(z3/z4) [5]
Коробка подач, расположенная с передней стороны станка под бабкой, позволяет переключением рычагов быстро изменять подачу. В токарных станках чаще всего применяют коробки подач с накидной шестерней (рис.7). Механизм представляет блок 2 зубчатых колес z1 — z6, насаженный на вал I. На валу I скользящей шпонкой закрепляют колесо z8 и обойму 1. Накидная шестерня z7 находится в постоянном зацеплении с колесом z8 и крепится в обойме 1. Передачу обычно осуществляют от ведущего вала I к ведомому II. Накидную шестерню можно сцепить с любым зубчатым колесом блока 2 поворотом обоймы 1 относительно вала II и перемещением ее вдоль вала в соответствующее фиксируемое положение.
Рис.8 Схема механизма фартука
Фартук прикреплен к нижней части каретки суппорта. Заключенные в фартук механизмы подачи служат для преобразования вращательного движения, получаемого от ходового винта или ходового валика, в поступательное движение (подачу) суппорта, на котором закреплен резец. В фартуке имеется система червячных и зубчатых передач (рис. 8). При нарезании резьбы используют ходовой винт 6. При выполнении других токарных работ движение подачи осуществляется через ходовой валик 8, имеющий червяк 9 на скользящей шпонке. Червяк получает вращательное движение и, кроме того, может перемещаться вдоль валика. Вращение червяка передается червячному зубчатому колесу 10 и расположенному па одной оси с ним цилиндрическому зубчатому колесу 11, которое находится в зацеплении с колесом 1, передающим вращение соосному с ним колесу 3. Это колесо катится по неподвижной рейке 2, прикрепленной к станине токарного станка, заставляя перемещаться суппорт 4, связанный с фартуком. В результате вращательное движение ходового валика преобразуется в продольное поступательное движение суппорта.
Имеющиеся в фартуке механизмы могут преобразовывать вращательное движение ходового валика в поперечное движение резца.
При нарезании резьбы ходовой валик 8 отключается от остальных частей механизма фартука.
Ходовой винт 6 имеет разъемную гайку 7 (называемую маточной). При включении рукоятки 5 половинки разъемной гайки плотно охватывают вращающийся ходовой винт, вследствие чего гайка, а вместе с ней и суппорт осуществляют поступательное движение; при выключении рукоятки половинки гайки расходятся, освобождая винт и останавливая суппорт.
studfiles.net
1А616 схема электрическая | Описание электросхемы токарного станка
Электрооборудование
На станке установлены два трехфазных электродвигателя:
Электродвигатель ДГ привода главного движения типа А02-41-4 мощностью 4,0 кВт, 1450 об/мин, 220/380 в.
Электронасос ДО для подачи охлаждающей жидкости к резцу - типа ПА 22 мощностью 0,12 кВт, 2800 об/мин, 220/380 в.
Станки изготавливаются с электрооборудованием, рассчитанным для работы при напряжении 880 в, как в силовых цепях, так и в цепях управления.
Лампа местного освещения питается напряжением 36 в от понижающего трансформатора Т.
Согласно условиям заказа станки могут быть изготовлены с рабочим напряжением 220 или 500 в,
Описание схемы электрической
Перед пуском станка рукоятка вводного выключателя ВВ ставится в положение "включено", рукоятка управления - в среднее положение.
Рисунок - Схема станка 1А616
Шпиндель пускают в ход и останавливают включением и отключением электродвигателя ДГ, который управляется двумя магнитными пускателями КР-КП, переключателем ПУ и валиком с двумя рукоятками на три положения: верхнее - рабочий ход, среднее - стоп и нижнее - обратный ход.
Отключение электродвигателя ДГ сопровождается торможением - магнитный пускатель КТ включает в статорную обмотку электродвигателя постоянный ток от выпрямителя ВС.
В момент остановки электродвигателя реле контроля скорости вращения PC отключает магнитный пускатель КТ.
Для контроля степени загрузки электродвигателя ДГ в корпус передней бабки встроен указатель нагрузки. Стрелка указателя не должна находиться длительное время правее зачерченной части шкалы.
Описание схемы управления главным приводом станка модели 1А616К
Электросхема управления предназначена для переключения ступеней чисел оборотов и реверсирования шпинделя станка,
Для ступенчатого переключения чисел оборотов применена автоматическая коробка скоростей типа АКС109Д6.3, выполненная на электромагнитных муфтах ЭТМ. Коробка имеет 9 скоростей.
Пуск и останов шпинделя производится включением и отключением электродвигателя Ml, который управляется пускателями К1 и К2, переключателем П2 и валиком с двумя рукоятками на три положения:
- верхнее — рабочий ход
- среднее - стоп
- нижнее - обратный ход
Управление АКС осуществляется галетным переключателем, установленном на передней стенке шпиндельной бабки, а торможение шпинделя транзисторным блоком задержки БЗ и реле Р2.
В блоке БЗ для увеличения постоянной времени (R=C) применена транзисторная схема управления репе Р2. Транзисторы Т1 и Т2 включены по схеме с общим коллектором. Регулировка постоянной, времени (выдержки) производится шунтированием входного сопротивления резистором R5.
www.stanoktehpasport.ru