Что такое суппорт в тормозной системе автомобиля. Из каких частей суппорт состоит
Из каких частей состоит суппорт. Токарно-винторезный станок
Из каких частей состоит суппорт. Токарно-винторезный станок
Суппорт токарного станка предназначен для закрепления на нем режущего инструмента и сообщения ему движения подачи при обработке.
Нижняя плита 1 cуппорта (рис. 7), называемая кареткой или продольными салазками, перемешается по направляющим станины механически или вручную. Резец при этом движется в продольном направлении (это и есть продольная подача). На верхней поверхности каретки имеются поперечные направляющие 12 в форме ласточкина хвоста, расположенные перпендикулярно к направляющим станины. На направляющих 12 перемещаются поперечные салазки 3 суппорта, посредством которых резец получает движение, перпендикулярное к оси шпинделя.
Рис 7. Суппорт токарно-винторезного станка
На верхней поверхности поперечных салазок 3 расположена поворотная плита 4 суппорта, которая закрепляется после поворота гайкой 10.
На верхней поверхности поворотной плиты расположены направляющие 5, по которым при вращении рукоятки 13 перемещается верхняя плита 11-верхние салазки суппорта.
Резцедержатели и резцовые головки
На верхней части суппорта устанавливают резцедержатель или резцовую головку для закрепления резцов.
Рис 8 - Резцедержатели
На мелких и средних станках применяют одноместный резцедержатель 5 (рис. 8, а). Нижняя часть 1 резцедержателя, имеющая Т-образную форму, закрепляется на верхней части суппорта гайкой, 4. Для регулирования положения режущей кромки по высоте центров в резцедержателе имеется подкладка 2, нижняя сферическая поверхность которой опирается на такую же поверхность колодки резцедержателя. Закрепляют резец в резцедержателе двумя болтами 3.
На крупных токарных станках применяют одноместные резцедержатели (рис. 8, б). В этом случае резец устанавливают на поверхность 7 верхней части суппорта и закрепляют планкой 2, затягивая гайку 4. Для предохранения болта 3 от изгиба планка 2 поддерживается винтом 5, опирающимся на башмак 6. При отвертывании гайки 4 пружина 1 приподнимает планку 2.
Чаще всего на токарно-винторезных станках средних размеров применяют четырехгранные поворотные резцовые головки (см. рис 7).
Резцовая головка 6 устанавливается на верхней части суппорта 11; в ней можно закрепить винтами 8 четыре резца одновременно. Работать можно любым из установленных резцов. Для этого нужно повернуть головку и поставить требуемый резец в рабочее положение. Перед поворотом головку необходимо открепить, повернув рукоятку 9, связанную с гайкой, сидящей на винте 7. После каждого поворота головку нужно снова зажать рукояткой 9.
Одним из важнейших достижений машиностроения в начале XIX века стало распространение металлорежущих станков с суппортами - механическими держателями для резца. Каким бы простым и, на первый взгляд, незначительным не казался этот придаток к станку, можно без преувеличения сказать, что его влияние на усовершенствование и распространение машин было так же велика, как влияние изменений, произведенных Уаттом в паровой машине. Введение суппорта разом повлекло за собой усовершенствование и удешевление всех машин, дало толчок к новым усовершенствованиям и изобретениям. Суппорт предназначен для перемещения во время обработки режущего инструмента, закрепленного в резцедержателе. Он состоит из нижних салазок (продольного суппорта) 1, которые перемещаются по направляющим станины с помощью рукоятки 15 и обеспечивают перемещение резца вдоль заготовки. На нижних салазках по направляющим 12 перемещаются поперечные салазки (поперечный суппорт) 3, которые обеспечивают перемещение резца перпендикулярно оси вращения заготовки (детали). На поперечных салазках 3 расположена поворотная плита 4, которая закрепляется гайкой 10. По направляющим 5 поворотной плиты 4 перемещаются (с помощью рукоятки 13) верхние салазки 11, которые вместе с плитой 4 могут поворачиваться в горизонтальной плоскости относительно поперечных салазок и обеспечивать перемещение резца под углом к оси вращения заготовки (детали). Резцедержатель (резцовая головка) 6 с болтами 8 крепится к верхним салазкам с помощью рукоятки 9, которая перемещается по винту 7. Привод перемещения суппорта производится от ходового винта 2, от ходового вала, расположенного под ходовым винтом, или вручную. Включение автоматических подач производится рукояткой 14.
Устройство поперечного суппорта показано на рисунке внизу. По направляющим продольного суппорта 1 ходовым винтом 12, оснащенным рукояткой 10, перемещаются салазки поперечного суппорта. Ходовой винт 12 закреплен одним концом в продольном суппорте 1, а другим - связан с гайкой (состоящей из двух частей 15 и 13 и клина 14), которая крепится к поперечным салазкам 9. Затягивая винт 16, раздвигают (клином 14) гайки 15 и 13, благодаря чему. выбирается зазор между ходовым винтом 12 и гайкой 15. Величину перемещения поперечного суппорта определяют по лимбу 11. К поперечному суппорту крепится (гайками 7) поворотная плита 8, вместе с которой поворачиваются верхние салазки 6 и резцедержатель 5. На некоторых станках на поперечных салазках 9 устанавливается задний резцедержатель 2 для проточки канавок, отрезки и других работ, которые могут быть выполнены перемещением поперечного суппорта, а также кронштейн 3 с щитком 4, защищающим рабочего от попадания стружки и смазочно-охлаждающей жидкости.
Суппорт токарного станка
Ремонт суппорта токарного станка
Оснащение металлорежущих станков суппортами, стало одним из величайших достижений машиностроительной индустрии XIX столетья. Суппортом называется подвижная часть агрегата, удерживающая металлообрабатывающий инструмент. В процессе обработки заготовки, суппорт передвигается по направляющим токарного станка, перемещая резец автоматически, либо ручным способом. Несмотря на видимую незатейливость, данный механизм сыграл важную роль в удешевлении станочных агрегатов, а также в дальнейшем их усовершенствовании.
Основными компонентами суппорта выступает каретка, продольные салазки, перемещающиеся по направляющим каретки (нижних салазок), верхние салазки резцедержатель, поворотная плита, привод, приводящий механизм в движение. Суппорты различаются по принципу расположения на станке, по направленности и особенностям перемещения (поперечные, продольные, качающиеся) и по виду конструкции резцовой головки (резцовые или револьверные).
Состояние направляющих суппорта определяет точность обработки изделия. В ходе эксплуатации станка, наряду с другими узлами машины, рабочие поверхности и комплектующие суппорта неизменно изнашиваются, в результате чего, станок утрачивает функциональность. Ремонт суппорта токарного станка может входить в состав операций, выполняемых при капитальном ремонте оборудования, либо являться самостоятельным мероприятием, направленным на устранение неисправностей механизма (см. " ").
Одной из наиболее трудоемких процедур, выступает восстановление направляющих каретки. Цель работы состоит в возврате параллельности и перпендикулярности поверхностей направляющих по отношению к соответствующим плоскостям, восстановлении соосности всех совмещаемых отверстий. При этом, важно сохранить полноценное зацепление шестерней фартука с аппаратурой механической подачи.
Ремонт суппорта токарного станка, связанный с восстановлением направляющих, относится к ответственным и сложным мероприятиям, требующим применения специального высокоточного оборудования. В наше конструкторское бюро поступают, как правило, токарные станки тяжелого и среднего класса, которые нуждаются не только в реставрации суппорта, но и в выполнении ремонтных работ, объединенных с другими узлами и механизмами агрегата. В подавляющем большинстве случаев, речь идет о капитальном ремонте.
Суппорт - важная часть токарного станка, фактически, выполняющая функцию руки рабочего, удерживающего резец и, перемещающего его вдоль заготовки. Правильное обслуживание механического держателя, позволит продлить срок его службы и издержать серьезных проблем с ремонтом.
Уход за суппортом подразумевает периодическую регулировку зазоров в направляющих, устранение люфтов, своевременную очистку или замену набивки сальников, регулярную смазку салазок и защиту их от механических повреждений.
Суппорт (см.рис.1а)предназначен для перемещения во время обработки режущего инструмента, закрепленного в резцедержателе. Он состоит из нижних салазок (продольного суппорта) 1, которые перемещаются по направляющим станины с помощью рукоятки 15 и обеспечивают перемещение резца вдоль заготовки. На нижних салазках по направляющим 12 перемещаются поперечные салазки (поперечный суппорт) 3, которые обеспечивают перемещение резца перпендикулярно оси вр
meetal.ru
Суппорт токарного станка.
Суппорт (см.рис.1а)предназначен для перемещения во время обработки режущего инструмента, закрепленного в резцедержателе. Он состоит из нижних салазок (продольного суппорта) 1, которые перемещаются по направляющим станины с помощью рукоятки 15 и обеспечивают перемещение резца вдоль заготовки. На нижних салазках по направляющим 12 перемещаются поперечные салазки (поперечный суппорт) 3, которые обеспечивают перемещение резца перпендикулярно оси вращения заготовки (детали). На поперечных салазках 3 расположена поворотная плита 4, которая закрепляется гайкой 10. По направляющим 5 поворотной плиты 4 перемещаются (с помощью рукоятки 13) верхние салазки 11, которые вместе с плитой 4 могут поворачиваться в горизонтальной плоскости относительно поперечных салазок и обеспечивать перемещение резца под углом к оси вращения заготовки (детали). Резцедержатель (резцовая головка) 6 с болтами 8 крепится к верхним салазкам с помощью рукоятки 9, которая перемещается по винту 7. Привод перемещения суппорта производится от ходового винта 2, от ходового вала, расположенного под ходовым винтом, или вручную. Включение автоматических подач производится рукояткой 14.
Рис. 1а. Суппорт токарного станка 16К20
Техкулачковый патрон
На токарных станках применяют двух-, трех- и четырехкулачковые патроны с ручным и механизированным приводом зажима. В двухкулачковых самоцентрирующих патронах закрепляют различные фасонные отливки и поковки; кулачки таких патронов, как правило, предназначены для закрепления только одной детали. В трехкулачковых самоцентрирующих патронах закрепляют заготовки круглой и шестигранной формы или круглые прутки большого диаметра. В четырехкулачковых самоцентрирующих патронах закрепляют прутки квадратного сечения, а в патронах с индивидуальной регулировкой кулачков - детали прямоугольной или несимметричной формы. Трехкулачковый самоцентрирующий патрон с ручным зажимом самое распросраненное устройство для крепления деталей на токарных станках.Обладая мощным, но чувствительным механизмом, патрон позволяет надежно крепить детали с высокой точностью их центрирования , как для выполнения высокорежимной обработки, так для более тонких работ. Токарный патрон может устанавливаться на шпиндель станка или устройства. Наиболее широко применяют трехкулачковый самоцентрирующий патрон (рисунок ниже). Кулачки 1, 2 и 3 патрона перемещаются одновременно с помощью диска 4. На одной стороне этого диска выполнены пазы (имеющие форму архимедовой спирали), в которых расположены нижние выступы кулачков, а на другой - нарезано коническое зубчатое колесо, сопряженное с тремя коническими зубчатыми колесами 5. При повороте ключом одного из колес 5 диск 4 (благодаря зубчатому зацеплению) также поворачивается и посредством спирали перемещает одновременно и равномерно все три кулачка по пазам корпуса 6 патрона. В зависимости от направления вращения диска кулачки приближаются к центру патрона или удаляются от него, зажимая или освобождая деталь. Кулачки обычно изготовляют трехступенчатыми и для повышения износостойкости закаливают. Различают кулачки крепления заготовок по внутренней и наружной поверхностям; при креплении по внутренней поверхности заготовка должна иметь отверстие, в котором могут разместиться кулачки.
studfiles.net
Что такое суппорт в тормозной системе автомобиля
Основной составляющей безопасного передвижения на автомобиле является, конечно, тормозная система. Ее надежность позволяет машине быстро снизить скорость или вовремя остановиться. Соответственно, нужно постоянно следить за исправностью всех участков тормозной системы, в частности, уделять внимание суппортам. Ведь именно они выполняют основную работу по преобразованию приложенной силы с педали тормоза на тормозной диск.
Определение суппорта
Суппорт, по определению, является узлом, предназначенным для крепления инструмента с возможностью его перемещения. Данный узел включает в себя специальный механизм и резцедержатель. Конструкция суппорта обеспечивает движение в направлении, заданном устройством. Чтобы понять, что такое суппорт в тормозной системе автомобиля, нужно понимать работу всей тормозной системы авто.
Здесь суппорт представляет собой гидравлический цилиндр с поршнем, образующим тормозное усилие автомобиля, и скобу, которая удерживает тормозные колодки. При нажатии водителем на педаль тормоза повышается давление тормозной жидкости на поршни, находящиеся в корпусе суппорта, которые, в свою очередь, прижимают тормозную колодку к тормозному диску или барабану. Таким образом происходит замедление или полная остановка автомобиля. В настоящее время используются тормозные суппорты двух видов: с фиксированным креплением и с плавающей скобой.
Фиксированная конструкция суппорта
Суппорт в данном случае надежно крепится на поворотном кулаке. При этом рабочие цилиндры располагаются с обеих сторон тормозного диска. В случае нажатия на педаль тормоза поршни прижимают колодки одновременно с двух сторон диска. Тормозные колодки в такой конструкции удерживаются в разведенном состоянии при помощи специальных пружин. Стоит отметить, что такая система торможения очень эффективна, поэтому часто используется для спортивных автомобилей или мощных автомобилей с большой массой.
Суппорт с плавающей скобой
В этом случае рабочий цилиндр с поршнем располагаются с одной стороны, при этом одна из тормозных колодок фиксируется в неизменном положении. При торможении поршень прижимает только одну колодку, вторая же прижимается к диску постепенно, двигаясь по направляющим. Как правило, изготовление деталей такого типа обходится дешевле, поэтому этот вид суппортов распространен на большинстве автомобилей.
Принцип работы
Задний суппорт выполняет функцию прижатия тормозных колодок к диску. В результате этого образовавшееся трение заставляет автомобиль замедлиться или остановиться. Такую же функцию выполняет и суппорт передний.
Обе эти детали имеют схожую конструкцию. Так как суппорты в своей работе постоянно подвергаются большим нагрузкам (постоянное трение и, как следствие, нагрев до высоких температур), они должны быть достаточно прочными и обладать высокой теплоотдачей.
Основные признаки и причины неисправностей
Немало автовладельцев узнают, что такое суппорт, только когда появляются первые признаки их неисправностей. Поэтому необходимо знать симптомы нарушения работы суппортов, встречающиеся чаще всего: появление скрипа, блокировка тормозов, увод машины в сторону при торможении, излишняя плавность или жесткость педали тормоза. Как правило, быстрее всего подвергаются износу колодки и тормозные диски. Это объясняется постоянным трением и нагревом этих деталей. Но не стоит забывать, что пыльники, сальники и манжета внутри корпуса тоже требуют должного внимания, ведь от них зависит герметичность системы. Из-за отсутствия должного ухода некоторые элементы и детали могут подвергаться коррозии и покрываться ржавчиной. Это может привести к заклиниванию подвижных частей механизма.
Ремонт суппортов
Большинство автопроизводителей вместо ремонта предлагают полную замену суппорта. Однако это достаточно дорогостоящая процедура даже для бюджетных автомобилей. Есть возможность восстановить суппорт с помощью ремкомплекта, куда входят все необходимые для этого элементы, включая пыльники и манжеты. Если автовладелец четко представляет себе, что такое суппорт, он вполне может самостоятельно произвести все необходимые манипуляции для его ремонта.
В первую очередь суппорт необходимо разобрать и оценить степень износа каждого элемента. Особое внимание стоит уделить направляющим, т. к. они обеспечивают необходимую подвижность деталей. В любом случае необходимо удалить с элементов суппорта следы коррозии и ржавчину, если таковые имеются. Для этого вполне достаточно зачистить нужные места тонкой наждачной бумагой. После этого необходимо обработать детали специальной смазкой и установить их на место. Для современных автомастерских не составляет труда и замена штуцеров и поршней суппорта, что позволяет значительно увеличить срок его эксплуатации.
Итак, если быть аккуратным и внимательным водителем, обеспечить безопасную работу тормозной системы, в частности суппортов, не составит труда. Главное, знать, что такое суппорт, и вовремя производить замену его расходных элементов.
fb.ru
Суппорт токарного станка
Суппорт
Одним из важнейших достижений машиностроения в начале XIX века стало распространение металлорежущих станков с суппортами - механическими держателями для резца. Каким бы простым и, на первый взгляд, незначительным не казался этот придаток к станку, можно без преувеличения сказать, что его влияние на усовершенствование и распространение машин было так же велика, как влияние изменений, произведенных Уаттом в паровой машине. Введение суппорта разом повлекло за собой усовершенствование и удешевление всех машин, дало толчок к новым усовершенствованиям и изобретениям. Суппорт предназначен для перемещения во время обработки режущего инструмента, закрепленного в резцедержателе. Он состоит из нижних салазок (продольного суппорта) 1, которые перемещаются по направляющим станины с помощью рукоятки 15 и обеспечивают перемещение резца вдоль заготовки. На нижних салазках по направляющим 12 перемещаются поперечные салазки (поперечный суппорт) 3, которые обеспечивают перемещение резца перпендикулярно оси вращения заготовки (детали). На поперечных салазках 3 расположена поворотная плита 4, которая закрепляется гайкой 10. По направляющим 5 поворотной плиты 4 перемещаются (с помощью рукоятки 13) верхние салазки 11, которые вместе с плитой 4 могут поворачиваться в горизонтальной плоскости относительно поперечных салазок и обеспечивать перемещение резца под углом к оси вращения заготовки (детали). Резцедержатель (резцовая головка) 6 с болтами 8 крепится к верхним салазкам с помощью рукоятки 9, которая перемещается по винту 7. Привод перемещения суппорта производится от ходового винта 2, от ходового вала, расположенного под ходовым винтом, или вручную. Включение автоматических подач производится рукояткой 14.
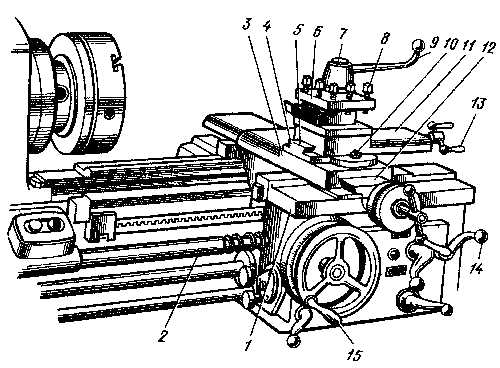
Устройство поперечного суппорта показано на рисунке внизу. По направляющим продольного суппорта 1 ходовым винтом 12, оснащенным рукояткой 10, перемещаются салазки поперечного суппорта. Ходовой винт 12 закреплен одним концом в продольном суппорте 1, а другим - связан с гайкой (состоящей из двух частей 15 и 13 и клина 14), которая крепится к поперечным салазкам 9. Затягивая винт 16, раздвигают (клином 14) гайки 15 и 13, благодаря чему. выбирается зазор между ходовым винтом 12 и гайкой 15. Величину перемещения поперечного суппорта определяют по лимбу 11. К поперечному суппорту крепится (гайками 7) поворотная плита 8, вместе с которой поворачиваются верхние салазки 6 и резцедержатель 5. На некоторых станках на поперечных салазках 9 устанавливается задний резцедержатель 2 для проточки канавок, отрезки и других работ, которые могут быть выполнены перемещением поперечного суппорта, а также кронштейн 3 с щитком 4, защищающим рабочего от попадания стружки и смазочно-охлаждающей жидкости.
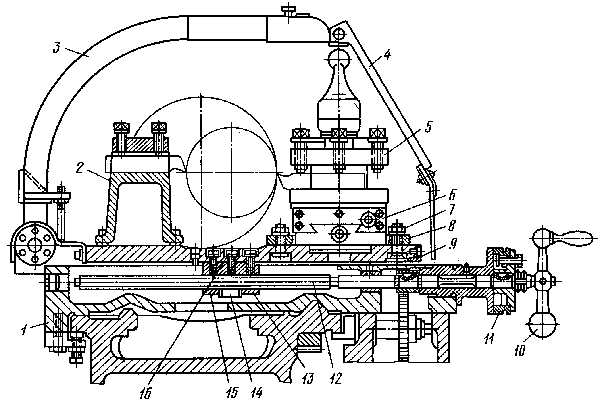
Поперечный суппорт
turner.narod.ru
Переборка суппорта: описание, особенности и устройство
Все системы автомобиля являются важными составляющими для комфортного и безопасного передвижения. Однако тормозная система заслуживает повышенного внимания, поскольку от нее зависит, насколько безопасным будет транспортное средство. А главным ее компонентом является суппорт, который время от времени приходит в негодность. Из-за наличия неисправности этого механизма невозможно своевременно остановить автомобиль. И только переборка суппорта сможет решить проблему.
Тормозная система представлена несколькими деталями, но ключевая роль отводится именно ему. Стоит рассмотреть этот компонент более подробно, выяснить, какими могут быть основные причины неисправности всей тормозной системы.
Барабанные тормоза
Автомобили обычно оснащаются дисковыми или барабанными тормозами. При этом суппорт как раз установлен на дисковую тормозную систему, в то время как в другой используется барабан. У каждой из систем есть свои преимущества и недостатки.
Минусами барабанных тормозов можно считать следующие моменты:
- Тормозной барабан при нагревании расширяется, из-за чего приходится прилагать существенные усилия.
- При замедлении автомобиля существует вероятность образования газов, которые играют роль смазки, что для тормозной системы очень критично и недопустимо.
- Барабанная конструкция склонна к «залипанию», в результате чего колеса постоянно находятся в режиме «торможения».
Многие производители старались хоть как-нибудь устранить эти недостатки или хотя бы свести их к минимуму. В конечном итоге стало ясно, что лучшим решением будет заменить их дисковой конструкцией тормозов. Однако небольшие автомобили бюджетной комплектации продолжают оснащаться барабанными тормозами, но только задних колес, а спереди уже дисковые.
Существенным плюсом барабанной системы можно считать низкую стоимость по сравнению с аналогами. К тому же они, находясь в задней части автомобиля, меньше подвергаются загрязнению.
Дисковые тормоза
У дисковой тормозной системы плюсов гораздо больше, о чем знает каждый, кто хоть раз занимался переборкой суппорта. И если барабанные тормоза представляют собой конструкцию закрытого типа, то здесь, наоборот, все открыто. Между тормозными колодками и диском проходит воздух, что позволяет охлаждать весь механизм. А благодаря сквозным отверстиям и специальным выемкам на диске исключается его загрязнение. Именно по причине закрытости барабанные тормоза «залипают», но в отношении дисковой конструкции данного недостатка просто не существует.
К сожалению, ничто в нашем мире не идеально, включая дисковые тормоза. И прежде всего главный недостаток кроется в высокой стоимости. Открытость тоже играет плохую шутку, ведь из-за этого диски подвергаются внешним механическим воздействиям (грязь, песок, пыль), результатом которого являются царапины.
Разновидности тормозного суппорта
Самыми распространенными система тормозного суппорта являются;
- фиксированная конструкция;
- суппорты с плавающей головкой.
Фиксированные механизмы появились раньше своих оппонентов. И переборка суппорта подобного типа не составляет труда. Конструкция их представляла собой металлический корпус с цилиндрами, расположенными напротив друг друга и в непосредственной близости от тормозного диска. Механизм закреплен на системе подвески (поворотный кулак) и постоянно находится в зафиксированном положении.
Когда колодки не задействованы, то они удерживаются специальными пружинами. Но как только водитель нажимает на педаль тормоза, они прижимаются к диску. Эффективная работа обеспечивается системой шлангов, патрубков и специальных трубок, благодаря которым тормозная жидкость подается во все цилиндры одновременно.
Фиксированная конструкция тормозного суппорта идеально подходит ко всем автомобилям с мощными моторами, способными развивать большой крутящий момент. В частности, это модели представительского класса и гоночные болиды. Такие механизмы производят всемирно известные компании, к примеру Brembo.
Суппорты с плавающей скобой отличаются тем, что в их конструкции одна из тормозных колодок зафиксирована, что можно заметить в ходе переборки суппорта, который закрепляется на внутренней части каждого колеса. В конструкцию, помимо цилиндра, включен кронштейн и поршень (один или два). При торможении поршень начинает прижимать колодку к диску, через какое-то время плавающая скоба сдвигается к поршню по направляющим. Благодаря этому задействуется вторая тормозная колодка.
Такая конструкция недорога в цене и при своих скромных размерах применяется в отношении недорогих автомобилей с простой комплектацией.
Принцип работы
Основная задача, которая возложена на суппорт, – это обеспечение необходимого усилия, чтобы замедлить или остановить транспортное средство. При каждом нажатии водителем педали тормоза в магистрали создается определенное давление. Оно передается к поршням суппорта, которые, в свою очередь, задействуют колодки. При этом механизм обеспечивает строго параллельное движение колодок относительно тормозного диска. В результате детали плотно сжимают диск, что и приводит к замедлению движения.
Но здесь есть один ключевой момент, о котором следует знать, прежде чем переходить к переборке переднего суппорта, – это трение. Поскольку колодки зажимают вращающийся диск, то нагрева не избежать. Причем это касается и самих колодок, и суппорта. Температура тормозной жидкости тоже увеличивается. Это обстоятельство ставит перед многими производителями выполнение серьезных требований.
Прежде всего суппорты должны изготавливаться из материала, который:
- имеет высокую прочность;
- отличается высокой степенью теплоотдачи;
- стоек к воздействию высокой температуры.
Последний пункт особенно важен, поскольку нагрев обычно приводит к деформации объектов.
Диагностика, основные признаки и причины поломки
Во время эксплуатации автомобиля происходит естественный износ элементов тормозной системы. А первым признаком того, что она нуждается в своевременном осмотре, может служить появление очень неприятного для большинства водителей скрипа. Чаще всего это указывает на неисправность суппорта. В этом случае тормозные колодки касаются диска не параллельно, что приводит к неравномерному их стиранию.
Список прочих признаков, из-за чего может понадобиться переборка тормозного суппорта:
- Существенные усилия, которое необходимо прикладывать водителю, чтобы полностью остановить автомобиль.
- При замедлении движения машину начинает неуклонно вести в сторону.
- Педаль тормоза нажимается чересчур легко.
- Наблюдается пульсация педали.
- Тормоза прихватываются.
Что же может служить причиной такого поведения суппорта? В большинстве случаев это происходит по вине прохудившегося пыльника, из-за чего внутрь попадает грязь и пыль. А по причине недостаточного количества смазки появляется ржавчина.
Профилактика
Неисправный автомобиль считается небезопасным, а автомобиль с неисправными тормозами уже представляет собой серьезную опасность в отношении других участников дорожного движения. И если закрались какие-либо признаки изнашивания тормозной системы, необходимо сразу же устранять их, а не игнорировать.
Для этого достаточно с определенным промежутком времени проводить визуальный осмотр всех элементов тормозной системы и производить переборку задних суппортов "Ауди" или любого другого автомобиля. Делать это можно самостоятельно или периодически загоняя автомобиль на СТО с целью плановой проверки.
Что касается самого промежутка, то следует проводить диагностику через каждый 30-40 дней. В ходе визуального осмотра особое внимание стоит уделять состоянию всех резиновых уплотнителей. Если есть небольшие разрывы, вовремя устранять неприятность, так как попавшие загрязнения приводят к преждевременному износу деталей.
Техническое обслуживание тормозной системы
Чтобы на автомобиле можно было совершать комфортные и безопасные поездки, необходимо, чтобы тормозная система всегда была в исправном состоянии. Для этого достаточно производить техническое обслуживание всех ее деталей.
Для ухода за суппортом его необходимо демонтировать, разобрать и смазать все движущие элементы. Ничего сверхсложного в этом нет, тем не менее всего лишь единицы занимаются переборкой суппортов "Ниссана".
Если водитель регулярно ездит на машине, возникает необходимость в полной замене тормозной жидкости. Производить это можно через каждые два года. Связано это с тем, что жидкость во время эксплуатации автомобиля способна притягивать влагу, из-за чего эффективность тормозной системы существенно падает.
Если визуальный осмотр выявил жидкие потеки, следует сразу же устранить проблему. Так можно избежать серьезной поломки всей системы и одновременно обезопасить себя и окружающих.
Тормозные колодки тоже заслуживают внимания и при явном износе тут же заменяются. Изделия многих производителей отличаются высокой степенью безопасности и качества. К тому же они делаются таким образом, чтобы колодки сигнализировали владельцу о своем техническом состоянии.
Ремкомплект
Для облегчения переборки суппорта "Лачетти" существуют специально предназначенные для него ремкомплекты. По сути, это набор мелких и запасных расходных деталей. Как правило, он состоит из:
- уплотняющих колец;
- направляющих;
- регулировочных винтов;
- регулировочных приспособлений;
- смазочных материалов.
В зависимости от марки машины и производителя набора, в состав могут ходить и прочие элементы, но перечисленные составляющие являются стандартным набором практически любого ремкомплекта.
Стоит заметить, что устройство переднего и заднего суппортов одной машины отличается. То есть придется приобретать два набора. При этом стоит выбирать тот вариант, который максимально подходит к автомобилю согласно его документации.
Обслуживание передних суппортов
Работу удобнее проводить на подъемнике или можно использовать домкрат. Приподнимается передняя часть автомобиля, и снимается колесо. Далее следует открутить нижний болт крепления суппорта и затем откинуть вверх его корпус. Производя переборку задних суппортов "Ауди С4", стоит оценить состояние колодок и при необходимости заменить их.
Затем нужно открутить верхнее крепление, шланг при этом можно не снимать. После чего выкрутить болты, которые удерживают скобу суппорта на кулаке. После снятия скобы можно переходить к извлечению поршня. Для этого нажать педаль тормоза – давление сделает все остальное. Следует тут же закупорить тормозную магистраль, к примеру болтом М12.
Нужно полностью разобрать суппорт и очистить его от грязи и смазать, что нужно. В процессе обслуживания использовать приобретенный ремкомплект для своего автомобиля. Все поврежденные детали заменяются новыми, а в завершение механизм собирается в обратной последовательности.
Обслуживание задних суппортов
Устройство задних суппортов немного отличается от передних, поскольку задние колеса связаны с ручным тормозом. Приподняв уже заднюю часть автомобиля, снимают оба колеса. Трос ручного тормоза нужно отсоединить, то же касается и шплинта, который соединяет между собой механизм ручника и суппорт.
В ходе переборки суппорта "Ауди А6" нужно сразу заглушить тормозную магистраль (подойдет тот же метод) и открутить крепежные элементы суппорта. Открывается доступ к колодкам, которые следует внимательно осмотреть.
Скобы тормозного механизма удерживаются болтами, прикрученными к рычагу подвески. Снимаем их тоже, а еще саму скобу вместе с фиксаторами и направляющими. В этом суппорте поршень можно снять плоскогубцами либо узкогубцами. В дальнейшем те же действия – оценка состояния деталей, замена уплотнителей при необходимости, смазка, есть ли утечка. После этого осуществляют сборку суппорта в обратном порядке, не забыв поставить колеса.
В заключение
Поскольку тормозная жидкость все равно прольется, необходимо проверить ее уровень в системе и долить, если нужно. Также в обязательном порядке прокачать тормоза. Вся работа не представляет ничего сложного, и справиться можно самостоятельно. Только проводить техническое обслуживание стоит при запланированной операции по замене тормозных колодок.
fb.ru
Суппорт
Одним из важнейших достижений машиностроения в начале XIX века стало распространение металлорежущих станков с суппортами - механическими держателями для резца. Введение суппорта разом повлекло за собой усовершенствование и удешевление всех машин, дало толчок к новым усовершенствованиям и изобретениям.
Суппорт предназначен для перемещения во время обработки режущего инструмента, закрепленного в резцедержателе. Он состоит из нижних салазок (продольного суппорта) 1, которые перемещаются по направляющим станины с помощью рукоятки 15 и обеспечивают перемещение резца вдоль заготовки. На нижних салазках по направляющим 12 перемещаются поперечные салазки (поперечный суппорт) 3, которые обеспечивают перемещение резца перпендикулярно оси вращения заготовки (детали).
На поперечных салазках 3 расположена поворотная плита 4, которая закрепляется гайкой 10. По направляющим 5 поворотной плиты 4 перемещаются (с помощью рукоятки 13) верхние салазки 11, которые вместе с плитой 4 могут поворачиваться в горизонтальной плоскости относительно поперечных салазок и обеспечивать перемещение резца под углом к оси вращения заготовки (детали).
Резцедержатель (резцовая головка) 6 с болтами 8 крепится к верхним салазкам с помощью рукоятки 9, которая перемещается по винту 7. Привод перемещения суппорта производится от ходового винта 2, от ходового вала, расположенного под ходовым винтом, или вручную. Включение автоматических подач производится рукояткой 14.
Устройство поперечного суппорта показано на рисунке ниже. По направляющим продольного суппорта 1 ходовым винтом 12, оснащенным рукояткой 10, перемещаются салазки поперечного суппорта. Ходовой винт 12 закреплен одним концом в продольном суппорте 1, а другим - связан с гайкой (состоящей из двух частей 15 и 13 и клина 14), которая крепится к поперечным салазкам 9. Затягивая винт 16, раздвигают (клином 14) гайки 15 и 13, благодаря чему выбирается зазор между ходовым винтом 12 и гайкой 15.
Величину перемещения поперечного суппорта определяют по лимбу 11. К поперечному суппорту крепится (гайками 7) поворотная плита 8, вместе с которой поворачиваются верхние салазки 6 и резцедержатель 5. На некоторых станках на поперечных салазках 9 устанавливается задний резцедержатель 2 для проточки канавок, отрезки и других работ, которые могут быть выполнены перемещением поперечного суппорта, а также кронштейн 3 с щитком 4, защищающим рабочего от попадания стружки и смазочно-охлаждающей жидкости.
Токарный станок имеет весьма древнюю историю, причем с годами его конструкция менялась очень незначительно. Приводя во вращение кусок дерева, мастер с помощью долота мог придать ему самую причудливую цилиндрическую форму. Для этого он прижимал долото к быстро вращающемуся куску дерева, отделял от него круговую стружку и постепенно давал заготовке нужные очертания. В деталях своего устройства станки могли довольно значительно отличаться друг от друга, но вплоть до конца XVIII века все они имели одну принципиальную особенность: при обработке заготовка вращалась, а резец находился в руках мастера.
Исключения из этого правила были очень редкими, и их ни в коем случае нельзя считать типичными для этой эпохи. Например, держатели для резца получили распространение в копировальных станках. С помощью таких станков работник, не обладавший особыми навыками, мог изготовлять затейливые изделия очень сложной формы. Для этого пользовались бронзовой моделью, имевшей вид изделия, но большего размера (обычно 2:
1). Нужное изображение получали на заготовке следующим образом.
Станок оборудовался двумя суппортами, позволявшими вытачивать изделия без участия руки работника: в одном был закреплен копировальный палец, в другом - резец. Неподвижный копировальный палец имел вид стержня, на заостренном конце которого помешался маленький ролик. К ролику копировального пальца специальной пружиной постоянно прижималась модель. Во время работы станка она начинала вращаться и в соответствии с выступами и впадинами на своей поверхности совершала колебательные движения.
Эти движения модели через систему зубчатых колес передавались вращающейся заготовке, которая повторяла их. Заготовка находилась в контакте с резцом, подобно тому, как модель находилась в контакте с копировальным пальцем. В зависимости от рельефа модели заготовка то приближалась к резцу, то удалялась от него. При этом менялась и толщина стружки. После многих проходов резца по поверхности заготовки возникал рельеф, аналогичный имевшемуся на модели, но в меньшем масштабе.
Копировальный станок был очень сложным и дорогим инструментом. Приобрести его могли лишь весьма состоятельные люди. В первой половине XVIII века, когда возникла мода на точеные изделия из дерева и кости, токарными работами занимались многие европейские монархи и титулованная знать. Для них большей частью и предназначались копировальные станки.
Но широкого распространения в токарном деле эти приспособления не получили. Простой токарный станок вполне удовлетворял всем потребностям человека вплоть до второй половины XVIII века. Однако с середины столетия все чаще стала возникать необходимость обрабатывать с большой точностью массивные железные детали. Валы, винты различной величины, зубчатые колеса были первыми деталями машин, о механическом изготовлении которых встал вопрос тотчас же после их появления, так как они требовались в огромном количестве.
Особенно остро нужда в высокоточной обработке металлических заготовок стала ощущаться после внедрения в жизнь великого изобретения Уатта. Изготовление деталей для паровых машин оказалось очень сложной технической задачей для того уровня, которого достигло машиностроение XVIII века.
Обычно резец укреплялся на длинной крючкообразной палке. Рабочий держал его в руках, опираясь как на рычаг на специальную подставку. Этот труд требовал больших профессиональных навыков и большой физической силы. Любая ошибка приводила к порче всей заготовки или к слишком большой погрешности обработки.
В 1765 году из-за невозможности рассверлить с достаточной точностью цилиндр длиной в два фута и диаметром в шесть дюймов Уатт вынужден был прибегнуть к ковкому цилиндру. Расточка цилиндра длиною в девять футов и диаметром в 28 дюймов допускала точность до "толщины маленького пальца".
С начала XIX века начался постепенный переворот в машиностроении. На место старому токарному станку один за другим приходят новые высокоточные автоматические станки, оснащенные суппортами. Начало этой революции положил токарный винторезный станок английского механика Генри Модсли, позволявший автоматически вытачивать винты и болты с любой нарезкой.
Нарезка винтов долго оставалась сложной технической задачей, поскольку требовала высокой точности и мастерства. Механики давно задумывались над тем, как упростить эту операцию. Еще в 1701 году в труде Ш. Плюме описывался способ нарезки винтов с помощью примитивного суппорта.
Для этого к заготовке припаивали отрезок винта в качестве хвостовика. Шаг напаиваемого винта должен был быть равен шагу того винта, который нужно было нарезать на заготовке. Затем заготовку устанавливали в простейших разъемных деревянных бабках; передняя бабка поддерживала тело заготовки, а в заднюю вставлялся припаянный винт. При вращении винта деревянное гнездо задней бабки сминалось по форме винта и служило гайкой, вследствие чего вся заготовка перемещалась в сторону передней бабки. Подача на оборот была такова, что позволяла неподвижному резцу резать винт с требуемым шагом.
Подобного же рода приспособление было на токарно-винторезном станке 1785 года, который был непосредственным предшественником станка Модсли. Здесь нарезка резьбы, служившая образцом для изготавливаемого винта, наносилась непосредственно на шпиндель, удерживавший заготовку и приводивший ее во вращение. (Шпинделем называют вращающийся вал токарного станка с устройством для зажима обрабатываемой детали.) Это давало возможность делать нарезку на винтах машинным способом: рабочий приводил во вращение заготовку, которая за счет резьбы шпинделя, точно так же как и в приспособлении Плюме, начинала поступательно перемещаться относительно неподвижного резца, который рабочий держал на палке.
Таким образом, на изделии получалась резьба, точно соответствующая резьбе шпинделя. Впрочем, точность и прямолинейность обработки зависели здесь исключительно от силы и твердости руки рабочего, направлявшего инструмент. В этом заключалось большое неудобство. Кроме того, резьба на шпинделе была всего 8-10 мм, что позволяло нарезать только очень короткие винты.
Винторезный станок, сконструированный Модсли, представлял собой значительный шаг вперед. История его изобретения так описывается современниками. В 1794-1795 годах Модсли, еще молодой, но уже весьма опытный механик, работал в мастерской известного изобретателя Брамы.
Перед Брамой и Модсли стояла задача увеличить число деталей, изготавливаемых на станках. Однако старый токарный станок был для этого неудобен. Начав работу по его усовершенствованию, Модсли в 1794 году снабдил его крестовым суппортом.
Нижняя часть суппорта (салазки) устанавливались на одной раме с задней бабкой станка и могла скользить вдоль ее направляющей. В любом ее месте суппорт мог быть прочно закреплен при помощи винта. На нижних салазках находились верхние, устроенные подобным же образом. С помощью них резец, закрепленный винтом в прорези на конце стального бруска, мог перемещаться в поперечном направлении.
Движение суппорта в продольном и поперечном направлениях происходило с помощью двух ходовых винтов. Подвинув резец с помощью суппорта вплотную к заготовке, жестко установив его на поперечных салазках, а затем перемещая вдоль обрабатываемой поверхности, можно было с большой точностью срезать лишний металл. При этом суппорт выполнял функцию руки рабочего, удерживающего резец. В описываемой конструкции, собственно, не было еще ничего нового, но она была необходимым шагом к дальнейшим усовершенствованиям.
Уйдя вскоре после своего изобретения от Брамы, Модсли основал собственную мастерскую и в 1798 году создал более совершенный токарный станок. Этот станок стал важной вехой в развитии станкостроения, так как он впервые позволил автоматически производить нарезку винтов любой длины и любого шага.
Слабым местом прежнего токарного станка было то, что на нем можно было нарезать только короткие винты. Иначе и быть не могло ведь там не было суппорта, рука рабочего должна была оставаться неподвижной, а двигалась сама заготовка вместе с шпинделем. В станке Модсли заготовка оставалась неподвижной, а двигался суппорт с закрепленным в нем резцом.
Для того чтобы заставить суппорт перемещаться на нижних салазках вдоль станка, Модсли соединил с помощью двух зубчатых колес шпиндель передней бабки с ходовым винтом суппорта. Вращающийся винт вкручивался в гайку, которая тянула за собой салазки суппорта и заставляла их скользить вдоль станины. Поскольку ходовой винт вращался с той же скоростью, что и шпиндель, то на заготовке нарезалась резьба с тем же шагом, что была на этом винте. Для нарезки винтов с различным шагом при станке имелся запас ходовых винтов.
Автоматическое нарезание винта на станке происходило следующим образом. Заготовку зажимали и обтачивали до нужных размеров, не включая механической подачи суппорта. После этого соединяли ходовой винт со шпинделем, и винтовая нарезка осуществлялась за несколько проходов резца. Обратный отход суппорта каждый делался вручную после отключения самоходной подачи. Таким образом, ходовой винт и суппорт полностью заменяли руку рабочего. Мало того, они позволяли нарезать резьбу гораздо точнее и быстрее, чем на прежних станках.
В 1800 году Модсли внес замечательное усовершенствование в свой станок - взамен набора сменных ходовых винтов он применил набор сменных зубчатых колес, которые соединяли шпиндель и ходовой винт (их было 28 с числом зубьев от 15 до 50).
На своем станке Модсли выполнял нарезку резьб с такой изумительной точностью и аккуратностью, что это казалось современникам почти чудом. Он, в частности, нарезал регулировочные винт и гайку для астрономического прибора, который в течение долгого времени считался непревзойденным шедевром точности. Винт имел пять футов длины и два дюйма в диаметре с 50-ю витками на каждый дюйм. Резьба была такой мелкой, что ее невозможно было рассмотреть невооруженным глазом. В скором времени усовершенствованный Модсли станок получил повсеместное распространение и послужил образцом для многих других металлорежущих станков. В 1817 году был создан строгальный станок с суппортом, позволивший быстро обрабатывать плоские поверхности. В 1818 году Уитни придумал фрезерный станок. В 1839 году появился карусельный станок и т.д.
studfiles.net
Суппорт токарного станка
Токарно-винторезный станок
Суппорт
Одним из важнейших достижений машиностроения в начале XIX века стало распространение металлорежущих станков с суппортами - механическими держателями для резца. Каким бы простым и, на первый взгляд, незначительным не казался этот придаток к станку, можно без преувеличения сказать, что его влияние на усовершенствование и распространение машин было так же велика, как влияние изменений, произведенных Уаттом в паровой машине. Введение суппорта разом повлекло за собой усовершенствование и удешевление всех машин, дало толчок к новым усовершенствованиям и изобретениям. Суппорт предназначен для перемещения во время обработки режущего инструмента, закрепленного в резцедержателе. Он состоит из нижних салазок (продольного суппорта) 1, которые перемещаются по направляющим станины с помощью рукоятки 15 и обеспечивают перемещение резца вдоль заготовки. На нижних салазках по направляющим 12 перемещаются поперечные салазки (поперечный суппорт) 3, которые обеспечивают перемещение резца перпендикулярно оси вращения заготовки (детали). На поперечных салазках 3 расположена поворотная плита 4, которая закрепляется гайкой 10. По направляющим 5 поворотной плиты 4 перемещаются (с помощью рукоятки 13) верхние салазки 11, которые вместе с плитой 4 могут поворачиваться в горизонтальной плоскости относительно поперечных салазок и обеспечивать перемещение резца под углом к оси вращения заготовки (детали). Резцедержатель (резцовая головка) 6 с болтами 8 крепится к верхним салазкам с помощью рукоятки 9, которая перемещается по винту 7. Привод перемещения суппорта производится от ходового винта 2, от ходового вала, расположенного под ходовым винтом, или вручную. Включение автоматических подач производится рукояткой 14.
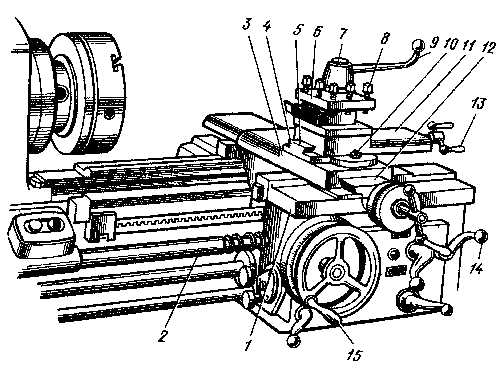
Устройство поперечного суппорта показано на рисунке внизу. По направляющим продольного суппорта 1 ходовым винтом 12, оснащенным рукояткой 10, перемещаются салазки поперечного суппорта. Ходовой винт 12 закреплен одним концом в продольном суппорте 1, а другим - связан с гайкой (состоящей из двух частей 15 и 13 и клина 14), которая крепится к поперечным салазкам 9. Затягивая винт 16, раздвигают (клином 14) гайки 15 и 13, благодаря чему. выбирается зазор между ходовым винтом 12 и гайкой 15. Величину перемещения поперечного суппорта определяют по лимбу 11. К поперечному суппорту крепится (гайками 7) поворотная плита 8, вместе с которой поворачиваются верхние салазки 6 и резцедержатель 5. На некоторых станках на поперечных салазках 9 устанавливается задний резцедержатель 2 для проточки канавок, отрезки и других работ, которые могут быть выполнены перемещением поперечного суппорта, а также кронштейн 3 с щитком 4, защищающим рабочего от попадания стружки и смазочно-охлаждающей жидкости.
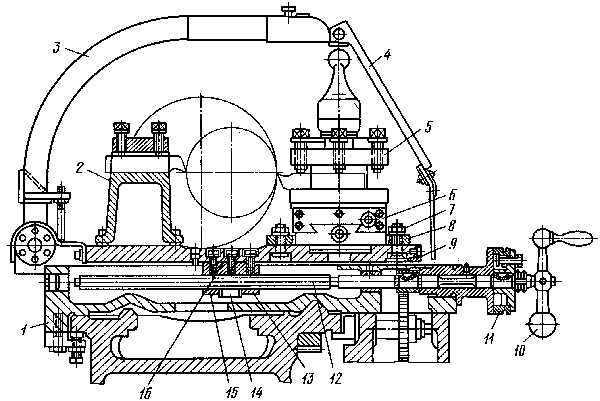
Поперечный суппорт
turnercraft.ru