Дуговая и кислородная резка металлов. Кислородно дуговая резка металла
Инструкционная карта 38 - Воздушно-дуговая и кислородно-дуговая резка
Категория:
Руководство газосварщика газорезчика
Инструкционная карта 38 - Воздушно-дуговая и кислородно-дуговая резкаУчебно-производственные задания. I — разделительная воздушно-дуговая резка, II — поверхностная воздушно-дуговая резка канавок, III — особенности кислородно-дуговой резки.
Цель заданий: научиться безопасным приемам и технике выполнения воздушно-дуговой и кислородно-дуговой резки, приобрести навыки ведения процессов дуговой резки с дополнительной подачей в зону реза воздуха или кислорода.
Организационные указания. Подготовить посты для резки, электрододержатели, компрессор для подачи воздуха, баллоны с газом для разделительной и поверхностной резки, угольные электроды типа ВДК — круглые (омедненные) диаметром 6, 8, 10, 12 мм и типа ВДП — плоские (омедненные) сечением 12X5 мм, стальные щетки, мел, молотки, зубила, защитные маски и щитки, спецодежду.
I. Разделительная воздушно-дуговая резка
Прямолинейная разделительная резка пластин
1. Разметить пластины мелом на полосы шириной 30—35 мм (толщина меловой полосы 10 —15 мм) и установить в удобное для резки положение.2. Выбрать электрод нужного диаметра и соответствующую силу тока.3. Закрепить угольный электрод в резаке для воз-душно-дуговой резки так, чтобы вылет электрода был 100—120 мм 4. Электрододержатель подключить к минусовому полюсу источника тока.5. Пустить сжатый воздух в резак и убедиться в том, что он свободно выходит из отверстий и распространяется вдоль поверхности электрода.6. Подвести электрод к кромке разрезаемой пластины под углом 45—60° к ее поверхности.7. Возбудить дугу и прорезать металл на всю толщину. Перемещать электрод с горящей дугой вниз до тех пор, пока конец электрода не выйдет -за нижнюю поверхность разрезаемой пластины на 3—5 мм.8. Перемещать электрод (без колебаний) в заданном направлении по мере прорезания металла. В процессе резки поддерживать постоянным угол наклона электрода к поверхности пластины. Не допускать увеличения выступающей части (конца) электрода более мм за нижнюю поверхность пластины; несоблюдение этого требования приводит к чрезмерному износу электрода.9. Менять положение электрода в электрододержа-теле по мере его сгорания.10. Зачищать периодически поверхности токопро-водящих губок резака с целью исключения нароста на них брызг металла и короткого замыкания резака с деталью.11. По окончании упражнений по резке резак с раскаленным электродом класть на изоляционный материал или подвешивать на специальном крючке.12. Огарки электродов собрать в специальную тару.
Особенности резки пластин толщиной 15—25 мм
1. Процесс воздушно-дуговой резки металла толщиной более 15 мм отличается характером движения конца электрода во время разделительной резки, применением повышенной силы тока и большего диаметра электрода.2. После возбуждения дуги на верхней кромке пластины нужно переместить конец электрода вниз (получить канавку), затем на большей скорости —вверх, в верхней точке — несколько вперед и опять вниз, т. е. совершать пилообразные движения концом электрода от верхних кромок к нижним.
Криволинейная разделительная резка
Резка углов и швеллеров
1. Разметить мелом уголки и швеллеры на отрезки шириной 30—40 мм.2. Установить образцы в удобное для резки положение.3. Порезать образцы на отрезки.4. Выбрать диаметр электрода исходя из толщины образцов. Определить силу тока для выбранного диаметра электрода.4.1. Возбудить дугу в точке при перпендикулярном расположении оси электрода к поверхности уголка 4.2. После прорезания металла на всю толщину перемещать резак по периметру уголка, располагая электрод перпендикулярно поверхности металла в каждый момент процесса резки.
Резка (вырезка) геометрических фигур
1. Разметить на листовом материале окружность, квадрат, многоугольник и другие фигуры.2. Выбрать диаметр электрода и параметры режима в зависимости от толщины металла.3. Вырезать последовательно отверстие, квадрат, многоугольник.3.1. Возбудить дугу над точкой и при неподвижном электроде прожечь отверстие. После этого перемещать резак равномерно по намеченной линии реза, электрод держать строго вертикально.3.2. Возбудить дугу над точкой, вырезать квадратное отверстие. Затем начать резку в точке и вырезать намеченную фигуру. Электрод держать в вертикальном положении. В углах квадрата и многоугольника несколько замедлять скорость резки с целью получения параллельных кромок.
Прожигание отверстий
1. Расположить пластину с намеченными будущими отверстиями в удобное для резки положение.2. Выбрать параметры режима.3. Возбудить дугу над разметкой. Через 1—2 с электрод перемещать вниз до получения сквозного отверстия (металл расплавляется и удаляется в жидком состоянии под действием давления дуги и давления потока поздуха).4. При необходимости получить диаметр отверстия заданных размеров (диаметр отверстия, получаемого при неподвижном электроде, обычно больше диаметра применяемого электрода на 1—3 мм) нужно совершать кольцеобразные движения по периметру получаемого отверстия.
Резка труб
1. Разметить трубу на кольца шириной 30—40 мм 2. Укрепить трубу в кулачках токарного станка или специального вращателя с изменяемой скоростью вращения.3. Выбрать режимы резки, зависящие в основном от толщины стенки трубы.4. Расположить резак строго в зените и перпендикулярно оси трубы.5. Включить вращатель (токарный станок), обеспечивающий равномерное вращение трубы.6. Возбудить дугу. Прожечь отверстие и, удерживая электрод в первоначальном положении, отрезать кольцо. Аналогично поступить с оставшимся отрезком трубы. При толщине металла до 15 мм конец электрода опускать в полость реза без колебаний. При резке металла больших толщин необходимо совершать пилообразные движения электродом.7. Выполнить контрольные резы. Разрезать под углом 45° уголок или швеллер и прорезать в нем 4—5 отверстий, сделать на отрезке трубы два параллельных реза под углом 45—60° к оси трубы.
II. Поверхностная воздушно-дуговая резка канавок
1. Нанести на поверхность пластины из углеродистой стали толщиной 20 мм меловые линии на расстоянии 30—40 мм друг от друга 2. Установить пластину в удобное для резки положение и подключать к ней положительный полюс источника тока.3. Вырезать узкую канавку.3.1. Взять угольный электрод диаметром мм. Закрепить его в резаке так, чтобы вылет электрода составлял 100—120 мм.3.2. Выбрать параметры режима по имеющимся таблицам.3.3. Пустить воздух в резак и убедиться, что он свободно вытекает из отверстий и распространяется вдоль поверхности электрода.3.4. Установить электрод под углом 35—40° к поверхности пластины и возбудить дугу.3.5. В процессе резки совершать два движения электродом: первое (быстрое) по направлению реза со скоростью выдувания расплавленного металла, второе — (более медленное) вниз, по мере обгорания конца электрода (рис. 6,6). При резке часть металла выдувается вперед на линию реза, а часть его располагается по обеим сторонам в виде тонкой, легко отделимой пленки.3.6. Перемещать электрод равномерно. Не касаться электродом металла, так как возможно местное науглероживание поверхности канавки.3.7. Уделять особое внимание скорости подачи электрода вниз. Она должна быть такой, чтобы нижний конец электрода в процессе резки был видимым и передний фронт плавления основного металла не препятствовал выдуванию расплавленного металла вперед (рис. в, в). При повышенной подаче электрода вниз на поверхности пластины образуется козырек, препятствующий свободному выдуванию жидкого металла вперед. При этом расплавленный металл попадает на электрод, рез зашлаковывается, а кромки канавки становятся волнистыми.4. Вырезать широкую канавку.4.1. Техника выполнения резки широкой канавки практически не отличается от техники резки узкой канавки, но электроду необходимо придать еще и третье движение — поперечное (колебание электродом поперек продольной оси канавки).4.2. Прорезать канавку шириной в 4—5 раз большую диаметра электрода, совершая поперечные колебания электродом.5. Выплавить дефектный участок основного или корневого шва.5.1. При вырезке дефекта корневого шва обратить внимание на то, что канавка должна быть узкой. Для этого рекомендуется использовать минимальный диаметр электрода (не более b мм). Кроме того, необходимо обеспечить плавные переходы в начале и конце канавки к «здоровому металлу» (рис. 8). Поэтому резку нужно начинать от краев дефекта и заканчивать в его середине.6. Изготовить контрольный образец. Выплавить пять канавок с возрастающей шириной и глубиной. Ширину канавки изменять от до 40 мм, глубину — от до 18 мм.
III. Особенности кислородно-дуговой резки
1. Применение струи технически чистого кислорода, направляемой на нагретый до температуры плавления металл, позволяет интенсифицировать окисление металла и удалять из разреза образующиеся оксиды.2. В качестве электродов используют стальные трубки с наружным диаметром 6, 8, 10, 12 мм и длиной 340— 400 мм. На трубки наносят специальные покрытия, обеспечивающие устойчивое горение дуги.3. Техника резки такая же, как и при воздушно-дуговой резке. Однако угол наклона электрода составляет 80—85° к обрабатываемой поверхности.4. При резке используют постоянный ток обратной полярности (диаметры электродов и мм) и переменный ток при резке электродами диаметром 10 и 12 мм.
Читать далее:
Инструкционная карта 39 - Аппаратура для плазменной резки
Статьи по теме:
pereosnastka.ru
Кислородно-дуговая резка | Строительный справочник | материалы - конструкции
При кислородно-дуговой резке металл вначале расплавляется электрической дугой, а затем сгорает в поступающей струе кислорода и выдувается. На рисунке приведена схема кислородно-дуговой резки.
В настоящее время существует несколько методов кислородно-дуговой резки. За рубежом (в США, Франции и Бельгии), например, нашел применение метод кислородно-дуговой резки при помощи стальных трубчатых электродов.
|
Схема кислородно-дуговой резки металла |
При этом способе резки металл нагревается дугой, возбуждаемой между трубчатым электродом и обрабатываемым изделием. Струя кислорода, поступающая из отверстия трубки, попадая на нагретую поверхность, окисляет металл по всей его толщине.
Электродами служат трубки из низкоуглеродистой или нержавеющей стали при наружном диаметре 5 — 7 мм. Внутренний диаметр трубки может быть 1 — 3,5 мм. Наружную поверхность электрода покрывают специальным покрытием, предохраняющим электрод от замыкания с обрабатываемым металлом при его опирании и перемещении. Кислородно-дуговую резку также выполняют и угольным электродом. Наиболее широкое распространение способ кислородно-дуговой резки нашел при подводных работах.
Использованы репродукции http://welding.su/gallery/ |
Схема оборудования поста для кислородно-дуговой резки стальным стержневым электродом: 1 — сварочный трансформатор, 2 — регулятор, 3 — рубильник, 4 — провода, идущие к держателю, 5 — электрододержатель, 6 — электрод, 7 — резак РГД-1-56, 8 — кислородный шланг, 9 — баллон с кислородом, 10 — редуктор |
Специальные способы резки
Содержание:
Сущность и основные условия резки
Кислородно-флюсовая резка
Газо-дуговая резка
Воздушно-дуговая резка
Плазменно-дуговая резка
Плазменная резка
Кислородно-дуговая резка
Подводная резка
Копьевая резка
Сущность процесса резки. Кислородная резка[1] стали, основана на свойстве железа гореть в струе чистого кислорода, будучи нагретым, до температуры, близкой к температуре плавления.
Температура загорания железа в кислороде зависит от состояния, в котором оно находится. Так, например, железный порошок загорается при 315° С, тонкое листовое или полосовое железо — при 930° С, а поверхность крупного куска стали — при 1200-1300° С. Горение железа происходит с выделением значительного количества тепла и может поддерживаться за счет теплоты сгорания железа.
Как показал анализ шлака, 30-40% удаленного из реза металла составляет не сгоревшее, а только расплавившееся железо; 90-95% окислов состоят из FeO.
Скорость реакции Fе + О = FеО пропорциональна
, где — давление кислорода в месте реакции. При повышении давления кислорода в струе процесс резки ускоряется за счет повышения скорости реакции окисления и за счет более быстрого удаления окислов из места разреза.Кроме подогрева металла до температуры горения в кислороде, подогревающее пламя выполняет еще следующие дополнительные функции:
- подогревает переднюю (в направлении резки) верхнюю кромку реза впереди струи режущего кислорода до температуры воспламенения, что обеспечивает непрерывность процесса резки;
- вводит в зону реакции окисления дополнительное тепло, покрывающее его потери за счет теплопроводности металла и в окружающую среду; это имеет особенно важное значение при резке металла малой толщины;
- создает защитную оболочку вокруг режущей струи кислорода, предохраняющую от подсоса в нее азота из окружающего воздуха;
- подогревает дополнительно нижнюю кромку реза, что важно при резке больших толщин.
Мощность подогревающего пламени зависит от толщины и состава разрезаемой стали и температуры металла перед резкой.
Металл нагревают на узком участке в начале реза, а затем на нагретое место направляют струю режущего кислорода, одновременно передвигая резак по намеченной линии реза. Металл сгорает по всей толщине листа, в котором образуется узкая щель. Интенсивное горение железа в кислороде происходит только в слоях, пограничных с поверхностью режущей струи кислорода, который проникает (диффундирует) в металл на очень малую глубину.
С момента начала резки дальнейший подогрев металла до температуры воспламенения происходит, в основном, за счет тепла реакции горения железа. При чистой, свободной от ржавчины и окалины поверхности, резка может продолжаться и без дополнительного подогрева. Однако лучше продолжать резать с подогревом, так как это ускоряет процесс.
Для заготовительной резки стали применяют кислород чистотой не ниже 98,5—99,5%. С понижением чистоты кислорода резка идет медленнее и требует большего расхода кислорода. Например, в пределах чистоты кислорода от 99,5 до 97,5% понижение чистоты на 1 % увеличивает расход кислорода на 1 м шва на 25—35%, а время резки — на 10—15%. Это особенно заметно при резке стали больших толщин. Применять для заготовительной резки кислород чистотой ниже 98,5% не следует, так как поверхность реза получается недостаточно чистой, с глубокими рисками и трудноотделяемыми шлаками (гратом).
Скорость резки, толщина металла, расход ацетилена в подогревающем пламени и эффективная мощность пламени связаны между собой зависимостью.
Производительность резки зависит также от распределения подогрева. Применение нескольких подогревающих пламен увеличивает скорость резки по сравнению с таковой при одном подогревающем пламени (при равных расходах ацетилена в обоих случаях). Общий предварительный подогрев металла при резке (до любой температуры) позволяет значительно увеличить скорость резки.
Основные условия резки. Для процесса резки металла кислородом необходимы следующие условия:
- температура горения металла в кислороде должна быть ниже температуры плавления, иначе металл будет плавиться и переходить в жидкое состояние до того, как начнется его горение в кислороде;
- образующиеся окислы металла должны плавиться при температуре более низкой, чем температура горения металла, и не быть слишком вязкими; если металл не удовлетворяет этому требованию, то кислородная резка его без применения специальных флюсов невозможна, так как образующиеся окислы не смогут выдуваться из места разреза;
- количество тепла, выделяющееся при сгорании металла в кислороде, должно быть достаточно большим, чтобы обеспечить поддержание процесса резки;
- теплопроводность металла не должна быть слишком высокой, так как иначе, вследствие интенсивного теплоотвода, процесс резки может прерываться.
При обычной кислородной резке высоколегированных хромистых и хромоникелевых нержавеющих сталей на поверхности реза образуется пленка тугоплавких окислов хрома, имеющих температуру плавления около 2000° С и препятствующих дальнейшему окислению металлов в месте реза. Поэтому кислородная резка этих сталей требует применения особых приемов и способов.
До разработки способа кислородно-флюсовой резки нержавеющих сталей пользовались приемами резки, основанными на создании вблизи поверхности реза участков металла с высокой температурой нагрева, способствующих расплавлению пленки окислов хрома. Это достигалось введением в разрез дополнительного тепла от сгорания присадки из малоуглеродистой стали. В качестве таковой использовалась стальная полоска, уложенная вдоль линии реза, или валик, наплавленный металлическим электродом. Выделяющееся при сгорании железа тепло, а также переходящее в шлак железо (полоски или наплавки) и его окислы способствуют разжижению и удалению окислов хрома. Этими способами можно было резать нержавеющую сталь небольшой толщины (10—20 мм), при этом качество реза и производительность низкие, резка протекает неустойчиво и часто прерывается.
Лучшие результаты получают при непрерывном введении в рез прутка из низкоуглеродистой стали диаметром 10—15 мм. При соответствующем навыке этим способом можно выполнять отрезку прибылей отливок толщиной до 400 мм. Существенным недостатком способа Ищется необходимость выполнения резки двумя рабочими: один должен быстро подавать пруток в зону резки, а второй — вести резку. При резке необходима повышенная мощность подогревающего пламени. Рез получается широким, скорость резки низкая (при толщине 40 мм — 100 мм/мин, при 80 мм — 70 мм/мин и при 200 мм — 20 мм/мин), а качество поверхности реза — плохое.
Лучшие результаты получают при электрокислородной резке нержавеющих сталей трубчатым стальным электродом, по которому проходит струя режущего кислорода, Этим способом можно резать непрерывно сталь толщиной до 10 мм. При резке стали толщиной 10—120 мм электроду придают зигзагообразное движение. Скорость резки при этом равна: при толщине 10 мм — 400 мм/мин, при 60 мм — 40 мм/мин, при 120 мм — 30 мм/мин. Высокая стоимость трубчатых электродов и значительное оплавление верхней кромки ограничивают применение этого способа.
Более совершенным способом резки высоколегированных нержавеющих сталей является кислородно-флюсовая резка. В качестве флюса применяют, как правило, железный порошок с зернами 0,1—0,2 мм. Сгорая в струе режущего кислорода, железный порошок выделяет дополнительное тепло, которое повышает температуру в месте реза. Вследствие этого тугоплавкие окислы остаются в жидком состоянии и, будучи разбавлены продуктами сгорания железа, дают жидкотекучие шлаки. Резка протекает с нормальной скоростью, а поверхность реза получается чистой.
Кислородная резка чугуна без флюса также затруднена, так как температура плавления чугуна ниже температуры горения железа. Содержащийся в чугуне кремний дает тугоплавкую пленку окиси, которая препятствует нормальному протеканию резки. При сгорании углерода чугуна образуется газообразная окись углерода, загрязняющая режущий кислород и препятствующая сгоранию железа.
Разрезать чугун можно без флюса, только применяя более мощное ацетиленокислородное пламя с избытком ацетилена. Ядро пламени должно иметь длину, равную толщине разрезаемого чугуна. Резка производится с поперечными колебательными движениями мундштука, создающими более широкий рез. При этом способе расходуется больше металла, кислорода и ацетилена, чем при резке стали, а разрез получается неровный, с оплавленными кромками. Поэтому для высококачественной резки чугуна также применяют кислородно-флюсовую резку.
Цветные металлы (медь, латунь, бронза) обладают высокой теплопроводностью и при их окислении кислородом выделяется количество тепла, недостаточное для дальнейшего развития процесса горения металла. При кислородной резке этих металлов также образуются тугоплавкие окислы, препятствующие резке. Поэтому кислородная резка бронзы и латуни возможна только с применением флюсов.
При резке чугуна в порошок добавляют феррофосфор или алюминиевый порошок и кварцевый песок. Скорость кислородно-флюсовой резки чугуна на 50—55% ниже скорости резки нержавеющей стали. При резке меди и бронзы во флюс добавляют феррофосфор, алюминий и кварцевый песок, а резку ведут с подогревом до 200—400 °С.
mirznanii.com
Дуговая резка | soedenimetall.ru
Способы резки плавящимся электродом.
Дуговая резка является одним из видов разделительной резки. Она основана на выплавлении металла из зоны резания теплотой электрической дуги, возбуждаемой между электродом и разрезаемым металлом. Этот способ широко применяется при строительно-монтажных работах для грубой разделки металла. Резку производят стальными электродами с качественным покрытием, но более тугоплавким, чем для сварки. Такое покрытие обеспечивает при резке образование небольшого козырька, закрывающего зону дуги. Козырек предохраняет электрод от короткого замыкания на разрезаемый металл, а также способствует более сосредоточенному нагреву металла и позволяет производительнее вести резку. В качестве покрытия применяют смесь, содержащую 70% марганцевой руды и 30% жидкого стекла. Толщина покрытия составляет 1… 1,5 мм. Успешно используются также электроды с покрытием ЦМ-7 и ЦМ-7с. Электроды диаметром 4. .6 мм являются наиболее рекомендуемыми. Ток при резке выбирают в пределах 50…60 А на 1 мм диаметра электрода. Источником питания дуги могут служить сварочные генераторы или сварочные трансформаторы. Дуговую резку применяют для разрезания металлов толщиной не более 30 мм; производительность низкая — при толщине разрезаемого металла 15 мм скорость резки не превышает 120…150 мм/мин. Расход электрода составляет 1,0…1,5 кг на 1 м разрезаемого металла.
Кислородно-дуговая резка отличается от дуговой тем, что на нагретый до плавления участок поверхности металла подают струю чистого кислорода. Кислород прожигает металл участка резания и выдувает образовавшиеся оксиды и расплавленный металл из полости реза. При сгорании металла выделяется дополнительная теплота, которая ускоряет процесс плавки и резки металла. Такой способ применяют для выполнения коротких разрезов в различных строительных конструкциях.
ВНИИавтогенмаш разработал способ ручной кислородно-дуговой резки резаком типа РГД. При этом способе резчик в правой руке держит электрододержатель, а в левой — резак. Возбудив дугу и нагрев металл до плавления, резчик нажимает на рукоятку кислородного клапана и направляет струю кислорода на разогретый металл, затем дугу и резак перемещает вдоль линии реза. Электродами служат стальные стержни диаметром 4…5 мм с покрытием ЦМ-7, ОММ-5, ОЗС-З и др. Ток в зависимости от диаметра электрода составляет 160…250 А. Этим способом можно разрезать металл толщиной до 50 мм. Металл толщиной 10…20 мм режут электродом диаметром 4 мм со скоростью 450…550 мм/мин. Расход кислорода составляет 100…160 л/мин. Углеродистые и низколегированные стали толщиной 50 мм режут электродом диаметром 5 мм со скоростью 200 мм/мин при расходе кислорода до 400 л/мин.
Важным преимуществом кислородно-дуговой резки является возможность сочетания резки со сварочными работами при монтаже различных строительных конструкций.
Способы резки неплавящимся электродом.
Применяются следующие виды дуговой резки неплавящимся электродом: разделительная резка неплавящимся электродом, воздушно-дуговая резка и плазменно-дуговая резка.
Разделительная резка производится неплавящимся электродом: угольным, графитовым или вольфрамовым. Угольные и графитовые электроды диаметром 12…25 мм позволяют разрезать металл толщиной до 100 мм. Резку производят постоянным током прямой полярности. Ток в зависимости от диаметра электрода составляет 40… 1000 А. Угольные электроды в процессе резки науглероживают кромки разреза и этим затрудняют последующую механическую обработку. Графитовые электроды дают более чистый разрез, дольше сохраняются и допускают большие плотности тока.
Воздушно-дуговая резка используется как для разделительной, так и для поверхностной резки. При этом способе между неплавящимся электродом и разрезаемым металлом возбуждают дугу. Теплотой дуги расплавляют металл участка резания, а струей сжатого воздуха непрерывно удаляют его из полости реза.
Рис. 1
Для воздушно-дуговой резки низкоуглеродистой и нержавеющей стали толщиной до 20 мм используют универсальный резак РВД-4А-66 (рис. 1: 1 — электрод, 2—головка, 3 — нажимной рычаг, 4 — корпус, 5 — кабель-шланг). Он имеет сменные угольные электроды диаметром 6… 12 мм. Ток достигает 400 А, а при кратковременном форсированном режиме — 500 А. Давление воздуха составляет 0,4…0,6 МПа. Расход воздуха при давлении 0,5 МПа не превышает 20 м3/ч. Масса резака — 1 кг. Процесс резки протекает устойчиво при питании резака постоянным током обратной полярности. При постоянном токе прямой полярности и при переменном токе процесс идет неустойчиво, производительность низкая при плохом качестве поверхности реза. Производительность резки зависит от тока. При токе 200 А за 1 ч работы можно удалить до 7 кг низкоуглеродистой стали, при токе 300 А — до 10 кг, а при 500 А — около 20 кг. Кроме того, с повышением тока снижается удельный расход электроэнергии с 3 кВт•ч/кг при токе 300 А до 2 кВт•Ч/кг при 500 А.
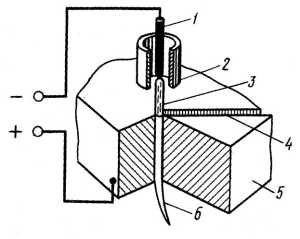
Рис. 2
Плазменно-дуговая резка является прогрессивным высокопроизводительным способом резки металлов. Она осуществляется глубоким проплавлением металла сжатой дугой в зоне резания и удалением частиц расплавленного металла газовым потоком. На рис. 2 представлена схема процесса. Дуга возбуждается и горит между вольфрамовым электродом 1 и разрезаемым металлом 5. Ток постоянный прямой полярности. Электрод находится внутри охлаждаемого медного мундштука 2. В канал мундштука под давлением подается плазмообразующий газ, струя которого сжимает столб дуги 3. Под действием дуги газ разогревается до высокой температуры, более 10 000°С, образуя плазму. Струя плазмы 6, имея высокую температуру и большую скорость истечения, проплавляет металл по линии реза 4 и выдувает расплавленный металл из полости реза.
Плазменно-дуговую резку можно применять для резки легированных и углеродистых сталей, чугуна, цветных металлов и их сплавов. Наиболее рационально и экономично применение ее при резке высоколегированных сталей, цветных металлов и их сплавов. Электроды изготовляют из лантанированного вольфрама ВЛ-15 или торированного вольфрама ВТ-15.
Плазмообразующими газами служат чистый аргон высшего сорта, технический азот 1 -го сорта, смесь аргона с техническим водородом, воздух.
Источниками питания дуги являются однопостовые сварочные преобразователи ПСЮ-500 и выпрямители ВКС-500. Для обеспечения повышенного напряжения холостого хода используют последовательное включение 2…3 преобразователей на одну дугу. Применяют также специальные источники питания плазменной дуги ИПГ-500-1 и выпрямители ВДГ-502.
Толщина разрезаемого металла в значительной степени зависит от напряжения. Например, при рабочем напряжении 75 В максимальная толщина резки алюминия достигает 25 мм, а при напряжении 250 В — 300 мм. Ток составляет 150…800 А.
Большое применение получили установки, в которых плазмообразующим газом служит воздух. К ним относится установка УПР-201, предназначенная для ручной плазменной резки металлов толщиной до 40 мм при температуре окружающей среды от +40 до —40°С. Установка состоит из источника питания, аппаратуры управления процессом резки и плазмотрона. Максимальный рабочий ток — 250 А. Давление воздуха — 0,5.-.0,8 МПа. Расход воздуха — 70… 100 м3/ч.
авов в строительно-монтажных условиях используют монтажный передвижной пост КПМ-1, смонтированный на одноосном автоприцепе ГАПЗ- 755А. Оборудование состоит из сварочного выпрямителя ВКС-500-1, компрессора, двух балластных реостатов РБ-300-1, горелки ГДС-150, резака РДП-2, баллонов с аргоном и азотом. Вентиляция на режиме резки — принудительная. Все оборудование поста защищено от атмосферных осадков металлическим кожухом. Пост выполняет сварку металла толщиной до 2,5 мм и резку меди (толщиной до 20 мм), стали (до 40 мм) и алюминия (до 50 мм). Масса передвижного поста — 1500 кг.
soedenimetall.ru
Технические характеристики способов резки металлов
Технические характеристики способов резки металлов
Резка металловДля разделения металла на части в практике применяется несколько способов резки, в частности: электродуговая, кислородная, кислородно-флюсовая, воздушно-дуговая, кислородно-дуговая, каждая из которых обладает своими специфическими особенностями.
Кислородная резка
Является основным способом разделения металлов, основанным на способности их сгорать в струе кислорода.Принципиальная схема процесса приведена на фиг. 16.
Схема процесса газовой резки
Практически кислородной резке обычным способом поддаются малоуглеродистые и среднеуглеродистые, низколегированные и легированные конструкционные и инструментальные стали. Резка подразделяется на ручную и машинную.Для образования подогревательного пламени используют как газообразные, так и жидкие горючие.С помощью кислородной резки можно вырезать детали любого очертания и формы, скашивать кромки листов под сварку, отрезать прибыли от стальных слитков и отливок, выплавлять поверхностные дефекты в слитках и отливках и т. п.Диапазон разрезаемых толщин — от 5 до 1000 мм и выше. Высокая чистота кромок реза, точность и большая скорость резания определили широкое применение этого способа разделения металла.
Кислородно-флюсовая резка
Этот процесс основан на введении в зону реакции окисления порошкообразного флюса, предназначенного для растворения тугоплавких пленок окислов (Cr2O3, SiO2 и др.). Применяется для металлов, не поддающихся обычному процессу кислородной резки. К числу этих металлов в первую очередь относятся высокохромистые и хромоникелевые жаропрочные и нержавеющие стали, серый чугун, а также цветные металлы и их сплавы.
В качестве флюса используется мелкозернистый железный порошок (размер зерен 0,1—0,5 мм) с добавками порошкообразного феррофосфора, алюминиевого порошка, буры технической, кварцевого песка, окалины и др.Резку можно производить ручным резаком, а также автоматами и полуавтоматами.В качестве горючего применяются газы и жидкости (керосин, бензин).
Дуговая резка
Основана на выплавлении металла теплом электрической дуги. Применяется как вспомогательный способ для грубого разделения металлов. Может производиться как на постоянном токе, так и на переменном угольными (лучше графитовыми) и металлическими электродами с толстыми покрытиями. Резка угольными и графитовыми электродами производится на постоянном токе прямой полярности.Как при угольных, так и при металлических электродах кромки реза получаются грубые, неровные, с наплывами и натеками.При помощи дуговой резки можно разделять любые металлы.
Воздушно-дуговая резка
При этом процессе металл в месте реза выплавляется теплом электрической дуги и выдувается струей сжатого воздуха, подаваемого через сопла резака вдоль электродного стержня (фиг. 17).
Схема процесса воздушно-дуговой резки
Резку производят угольными, графитовыми или (лучше) гра-фито-угольными электродами на постоянном токе прямой полярности. Воздушно-дуговая резка применяется для поверхностной обработки металлов, выплавки дефектов в сварных швах, разделки трещин и т. п., а также для разделительной резки нержавеющей стали, латуни и др.
Дуговая резка неплавящимся (вольфрамовым) электродом в аргоноводородной смеси
Этот способ является весьма эффективным процессом для резки алюминия и его сплавов. Особенностями его являются:1) высокое напряжение на дуге порядка 70 в, для чего требуется специальное оборудование постоянного тока с напряжением холостого хода не ниже 100 в и применение водорода, повышающего напряжение на дуге;2) высокая скорость резки, достигающая 8—10 м/мин при толщине металла 8—10 мм;3) необходимость автоматизации процесса и применения специальной горелки.
Кислородно-дуговая резка
При этом способе нагрев металла осуществляется электрической дугой, а выжигание его и выдувание продуктов сгорания — струей чистого кислорода. Резка может производиться металлическим трубчатым электродом с подачей кислорода в полость (фиг. 18)
Схема процесса кислородно-дуговой резки металлическим трубчатым электродом
или металлическими электродами с любым покрытием (ЦМ-7, ОММ-5, МЭЗ-04 и др.) при использовании резака РГД-1-56, что схематически показано на фиг. 19,
Схема установки РГД-1-56 для резки
а также угольным электродом с последовательным расположением дуги и кислородного сопла (фиг. 20).
Схема кислородно-дуговой резки с последовательным расположением дуги и кислородного сопла
Процесс резки угольным электродом может быть использован как для ручной, так и для автоматической резки. Процесс протекает устойчиво при применении графитовых электродов диаметром 6 мм, силе тока 150 а и напряжении на дуге 25 в. При меньшей силе тока наблюдаются обрывы дуги и прекращение процесса.Скорость резки, в сравнении с газовой, может быть увеличена, если чистота кислорода 99,5%. При ухудшении чистоты кислорода (ниже 98%) скорость резания сильно падает.При использовании мощной дуги (200—300 а) и введении в рез железного порошка возможно применение процесса для резки чугуна, аустенитных сталей и цветных металлов.
Резка проникающей плазменной дугой
Этот способ резки (см. схему на фиг. 21) является новым мощным средством разделения металлов. Здесь электрическая дуга между вольфрамовым неплавящимся электродом и разрезаемым металлом, сжатая в канале наконечника горелки потоком газов (обычно аргона и водорода), достигает высокой температуры (15 000° К и выше).
Схема резки проникающей (плазменной) дугой
Высокая температура достигается за счет того, что газ, проходя через столб сжатой дуги, почти полностью ионизируется, превращаясь в плазменную дугу, обладающую высокой концентрацией тепла и сильным плавящим действием. Имея вытянутую форму и малую площадь поперечного сечения, плазменная дуга проникает в глубь металла, расплавляя его на всю толщину. Этот способ применим для резки цветных и черных металлов толщиной до 70 мм и более.Резка легированных сталей плазменной дугой при толщине материала до 40 мм является более эффективной, чем кислородно-флюсовая.
pg-souz27.ru
Дуговая резка металлов.
Дугой также можно производить резку металла, выплавляя его из полости реза и предоставляя возможность свободно вытекать. Резка может быть произведена как угольным, так и металлическим электродом. Резка угольным электродом на постоянном токе дает лучшие результаты. Применяется нормальная или прямая полярность, т. е. на электроде минус, а на основном металле - плюс. Электроды лучше применять графитные, так как для заданной силы тока они могут быть меньшего диаметра и, таким образом снижать ширину реза; кроме того, графитные электроды медленнее обгорают при работе и расход их значительно меньше по сравнению с расходом электродов из амфорного угля. Основное внимание при резке угольной дугой нужно обращать на возможность быстрого, свободного и удобного вытекания расплавленного металла из полости реза.
Для резки угольной дугой применяются токи 400 - 1000 а. При толщинах металла до 12 мм резка угольной дугой может дать достаточно высокую производительность. С увеличением толщины металла производительность быстро падает, и при толщинах свыше 15 мм кислородная резка всегда производительнее. По качеству резки, чистоте кромок и ширине реза дуговой способ значительно уступает кислородному. На больших токах иногда применяют пластинчатые электроды прямоугольного сечения,
При резке металлическим электродом для стержня электрода пригодна любая, даже непригодная для сварки проволока из низкоуглеродистой стали; загрязнения металла проволоки не имеют особого значения. Электроды для резки покрываются обмазкой для повышения устойчивости дуги, замедления плавления электрода, изоляции электродного стержня от основного металла при введении электрода в полость реза, а иногда и для ускорения резки за счет окисления основного металла богатыми кислородом окислами, вводимыми в состав электродной обмазки.
Воздушно-дуговая резка. В этом способе металл расплавляется электрической дугой с неплавящимся электродом и расплавленный металл выдувается из полости реза потоком сжатого воздуха, подаваемого параллельно электроду. Воздушно-дуговой процесс чаще используется для поверхностной обработки или строжки металла, но может быть использован и для разделительной резки.
Окисление выдуваемого металла не очень значительно, и выдуваемые продукты на 80% состоят из металлического железа.
Резак для воздушно-дуговой резки представляет собой держатель электродов усиленной конструкции на большие токи; головка держателя имеет сопла для воздуха. Рукоятка держателя приспособлена для присоединения токоподводящего кабеля и воздушного шланга и имеет клапан или другое устройство для пуска и выключения воздуха. Сопла для выхода воздуха имеют форму небольших круговых отверстий или кольцевой щели, охватывающей электрод.
Специальные виды термической резки. При обычной кислородной резке, когда режущая струя направлена приблизительно нормально к поверхности металла, прорезается вся его толщина; здесь преследуется цель отделить или отрезать часть металла. Такая резка может быть названа разделительной. Возможен и другой способ использования режущей кислородной струи: она может быть направлена под очень малым углом к поверхности металла, почти параллельно ей . В этом случае струя кислорода выжигает на поверхности металла канавку овального сечения. Подобный метод называется кислородной обработкой, иногда кислородной строжкой или кислородной вырубкой металла.
Для кислородной обработки применяются специальные резаки, выпускаемые нашей промышленностью. Резак выбирает канавку шириной 15—50 мм, глубиной 2—20 мм со скоростью 1,5—10 м/мин, удаляя 1,0— 4,5 кг металла в минуту. Расход кислорода равен 200—300 л на 1 кг удаленного металла. Подобным резаком можно выбирать на поверхности металла канавки овального сечения, производя как бы грубую строжку. Повторный проход поверхности резаком со срезкой гребешков канавками уменьшенных размеров дает более чистую обработку. При правильной работе получается чистая и гладкая поверхность канавок.
Кислородную обработку можно уподобить механической обработке металла резанием, с заменой резца кислородным резаком Соответственно процессом кислородной обработки можно выполнить многие операции обработки резанием: строжку, обточку, расточку, нарезку грубой резьбы и т. п., когда достаточно грубой черновой обработки. Возможны также механизированные станки для кислородной строжки, обточки и т. п., требующие весьма незначительной мощности для перемещения резака вдоль обрабатываемой поверхности.
В настоящее время практическое применение кислородной обработки быстро расширяется. Кислородная обработка нашла довольно широкое применение на металлургических заводах для удаления и вырубки трещин, расслоений и других поверхностных дефектов в обжатых слитках. Удаление производится не только вручную, но и механизированным способом, на специальных машинах для огневой или кислородной зачистки. В этом случае удаляются не отдельные дефекты, а весь наружный слой металла толщиной около 3 мм по всей боковой поверхности слитка.
Своеобразным способом является резка кислородным копьем которое представляет собой толстостенную трубку достаточной длины, присоединенную к стволу или рукоятке. Трубка быстро сгорает во время работы и поэтому должна легко и удобно заменяться новой. Внутренний диаметр трубки 2—4 мм, наружный 8—10 мм. При слишком большом внутреннем диаметре в трубку закладывают стальные прутки, уменьшающие свободное сечение трубки и увеличивающие количество сгорающего металла копья. Процесс резки кислородным копьем заключается в прожигании металла струей кислорода, проходящей через стальную трубку, прижатую свободным концом к прожигаемому металлу. Резка производится без использования газового подогревательного пламени, которое заменяется довольно быстрым сгоранием металла самой трубки-копья до 0,5—1 м/мин. Начинается резка с подогрева места начала реза на металле или, что удобнее, с подогрева конца копья, например сварочной горелкой или дугой. При пропускании кислорода конец копья быстро загорается; дальнейший подогрев не нужен, и можно приступить к резке. Затем копье слегка прижимают к металлу и быстро углубляют в него со скоростью 0,15—0,40 м/мин, выжигая отверстие круглого сечения с гладкими стенками.
Расплавленный шлак выдувается из отверстия наружу избыточным кислородом и образующимися газами. При значительной глубине прожигаемого отверстия необходимо ставить изделие наклонно, облегчая вытекание шлаков из отверстия под действием силы тяжести. Копьем можно резать не только сталь, но и чугун, цветные металлы, затвердевшие шлаки, бетон, каменные породы и т. п. В подобных случаях резка происходит под тепловым воздействием горящего копья. Диаметр прожигаемого отверстия обычно составляет 20—60 мм, глубина его может быть доведена до 3 м. Давление кислорода на входе копья равно 5—7 атм, расход кислорода 30—60 мя/ч. Расход трубки быстро растет с глубиной отверстия.
Кислородное копье находит различное применение, например прожигание отверстий, леток в металлургических печах, шпуров в козлах и стальных блоках для подрыва их взрывчаткой, отверстий в бетоне и т. п. При резке кислородным копьем искры и брызги шлака разбрасываются на несколько метров, что вызывает необходимость защиты рабочих и устранения опасности пожара.
Рассмотрим специальный процесс кислородно-флюсовой резки, часто дающий хорошие результаты при резке металлов, для которых обычный метод кислородной резки малопригоден или совсем непригоден. Весьма благоприятным для кислородной резки сочетанием физико-химических свойств обладают технически чистое железо и обычная низкоуглеродистая сталь, которые с успехом режутся кислородом. Однако многие легированные стали плохо поддаются обычной кислородной резке, например все стали со значительным содержанием хрома, который при горении стали образует тугоплавкую окись хрома Сг203, преграждающую доступ кислорода к поверхности металла. К таким сталям принадлежат хромоникелевые нержавеющие и жаростойкие стали.
Для резки чугуна, цветных металлов, для которых применение кислородной резки нецелесообразно, разработан специальный процесс кислородно-флюсовой резки и создана необходимая аппаратура. Сущность этого процесса состоит в том, что вместе с режущим кислородом в зону резки вдувается порошкообразный флюс, вносимый во извещенном состоянии струей режущего кислорода. Флюс, подаваемый в зону резки, состоит главным образом из порошка металлического железа. Сгорая в струе кислорода, железный порошок дает дополнительное количество тепла, расплавляющее тугоплавкие окислы. Окислы железа, образующиеся при сгорании железного порошка, сплавляясь с окислами разрезаемого металла, образуют более легкоплавкий и жидкотекучий шлак, легче сдуваемый с поверхности металла и открывающий к ней доступ кислорода. Для получения флюса к железному порошку примешивают порошкообразные флюсующие добавки, облегчающие плавление и иытекание тугоплавких окислов из полости реза. Применяются также флюсы, и основном состоящие из двуокиси кремния SiO.,, например кварцевого песка. Количество флюсующих добавок зависит от состава разрезаемого металла.
Для кислородно-флюсовой резки необходимо иметь специальную аппаратуру: флюеопитатель и специальный кислородный резак с приспособлениями для подачи флюса. Нормальный флюеопитатель, выпускаемый нашей промышленностью, имеет небольшие размеры и весит около 40 кг. Расход флюса при резке специальных сталей колеблется от 1—2 кг для толщины 10 мм до 10—14 кг для толщины 200 мм на 1 пог. м реза. Флюс расходуется относительно экономнее при больших толщинах. Для малых толщин рекомендуется применять пакетную резку, выбирая оптимальную общую толщину металла. Кислородно-флюсовый способ позволяет успешно резать специальные стали, в том числе нержавеющие и жаростойкие, а также чугун и цветные металлы. Недостатком способа является значительный расход флюса.
Похожие статьи:
poznayka.org
Дуговая и кислородная резка металлов.
Поиск Лекций1. Цветные и черные металлы и их сплавы можно резать электродуговой или газовым пламенем, при дуговой резке металлов можно использовать как углеродистые так и металлические электроды. 2 В этих процессах , разделяющих и удаляющих, металлы осуществляется плавка металла теплом электродуги на месте реза.
3 Этот метод используется при разборке стальных структур и трубопроводных магистралей, резки металлолома, удаления вентиляционных систем из литья, резка цветных металлов, стали,чугуна, прожигание отверстий, а также для ремонтных и сборочных операций.
Прямая полярность обычно применяется при резке с использованием угольных электродов. Угольные электроды от 10-20 мм в диаметре ток может менятся от 400-800 А в зависимости от глубины резки. Использование металлических электродов улучшает качество резки и уменьшает глубину прорезки и производит качественную резку углов.
В различных способах газовой резки нужную температуру получают с помощью пламени, полученного при горении горючего газа. Два наиболее широко использованные процессы этого типа: непосредственно кислородно-газовая и кислородно – флюсовая резки, и химически флюсовая резка.
Кислородно – газовая резка основывается на способности определенных металлов гореть в кислороде с образованием большого количества тепла при плавке металла и образования окисей. Этот метод пригоден для резки только металлов, у которых температура горения ниже температуры плавления и температура плавления образованных окисей ниже самих металлов. Более того, окиси должны иметь текучесть.
Теплопроводимость металлов должна быть достаточно низкая, чтобы концентрировать тепло.
Углеродистые стали с содержанием углерода до 0,7 % и низколегированные стали режут этим методом.
Высоколегированная сталь предварительно нагревают перед резкой до 680-700 градусов. Металлы, которые нельзя эффективно разризать этим методом, это: литое железо,так как его точка плавления равна 1200 градусов, в то время как его температура горения составляет 1350 градусов, высоколегированный хром и хромоникелевая сталь, цветные сплавы, так как точка плавления их окисей выше их основных металлов.
Кислородно газовая резка выполняется обычным газосварочным оборудованием, исключение в том, что сварочная горелка заменяется режущей горелкой, которая вырабатывает газовую смесь предварительного нагрева и кислород для горения металла. Режущая горелка имеет взаимозаменяемые наконечники с предварительным нагревом и режущие сопла.
Точечная сварка.
Точечная сварка это популярная сварка сопротивлением, используется для соединения внахлест металлических листов толщиной 3 мм. Два электрода используются для соединения металлических листов вместе и чтобы пропустить через эти листы ток.
Преимущество этого метода включает значительное использование энергии, ограничивающие деформацию заготовки и осуществляя высокую скорость, легкую автоматизацию и не требует присадочного материала.
Прочность шва значительно меньше, чем при других сварочных методах, применение этого метода пригоден в некоторых случаях. Он интенсивно используется в автомобильной индустрии- обычные автомобили имеют несколько тысяч точечных швов, сделанных индустриальными работами. Особенный процесс под названием взрывная сварка может быть использована при точечной сварке нержавеющей стали.
Подобно точечной сварке, шовная сварка используется с двумя электродами, чтобы выполнить соединение листов под давлением и током. Однако вместо указанных электродов, роликовые электроды часто подаются к заготовке, делая возможным выполнить длинные не прерывистые швы. В прошлом, этот процесс использовался при производстве банок для напитков, а сейчас это использование намного ограничено. Другие методы сварки сопротивлением включают сварку вспышкой, рельефную и другие.
Сварка сопротивлением.
Сварка сопротивлением относится к процессам, которые используют электрически полученное тепло и давление для образования соединения между материалами. Такие процессы обычно относятся к соединениям металлов, а термин сварка сопротивлением можно использовать к пластическим соединениям. Этот тип сварки считают быстрым и эффективным, насколько выполняется тщательно. Ошибки во время такого процесса могут стать результатом проблем растрескивания, деформирования внешней поверхности и образованию пор.
Машины, обычно используемые для сварки сопротивлением, используют медные электроды. Они используются для добавки материалов с теплом, полученным электричеством.
Оператор машин не может контролировать количество тепла и период нагрева, сначало охлаждаются снаружи, в то время как внутренне расплавленные металлы более медленнее. По завершению этой фазы образуются соединения.
Обычно, чем выше точка плавления металла, тем меньше нужно тепла. Металл, который хорошо теплопроводим, так как алюминий требует больше тепла для сварки сопротивлением. Это благодаря тому, что тепло распространяется по металлу, вместо того, чтобы сохранятся в точке плавления.
Сварка сопротивлением требует силы. Давление удерживают слои металла вместе, когда они охлаждаются. Если это не выполняется, сцепление может никогда не возникнуть. Необходимость давления обычно поддерживается машиной, которая поддерживает электрический ток. Оператор машины может обычно также контролировать количества давления
.
Ультразвуковая сварка
Одна из самых популярных, ультразвуковая сварка используется для соединения тонких листов и проволоки, изготовленных из металла или термопластика их вибрацией на высокой скорости и под высоким давлением.
Используемое оборудование и методы подобны тем, что используются при сварке сопротивлением, но вместо электрического тока для получения энергии используют вибрации.
Свариваемые металлы при этом процессе не включают плавку материалов. Вместо этого шов образуется при использовании механической горизонтальной вибрации под давлением. Когда сваривается пластик, материалы должны иметь одинаковую температуру плавления, а вибрации образуются вертикально. Ультразвуковая сварка используется для изготовления электрических соединений из алюминия и меди, а также очень распространен процесс сварки полимеров.
Газовая сварка.
Самый распространенный газосварочный процесс – это сварка кислородом, также известная ацителеновая сварка. Это самый древний и самый обиходный сварочный процесс, но в последние годы он стал менее популярен в промышленном применении. Его все еще широко используют для сварки трубопроводов и труб, также при ремонтных работах. Он также часто применяется для создания и производства металлических изделий искусств. Ацетиленовое оборудование многообразно используется не только в некоторых видах сварки и стали, но также при пайке сварки латунью, металлическом нагреве ( для изгибов и деформирования), а также при кислородной резке.
Оборудование относительно недорогое и простое ,которое применяют в горении ацетилена в кислороде, чтобы получить температуру в 3100 градусов. Пламя, если оно меньше концентрировано, чем электрическая дуга, вызывает более медленное охлаждение шва, которое может привести к большому напряжению ( стрессу) и сварочным деформациям шва, хотя оно облегчает сварку высоколегированных сталей. Подобный процесс обычно называется кислородной резкой , обычно используют для резки металлов. Другие газосварочный процессы такие как: кислородно-ацетиленовая, кислородно – водородная, сварка под давлением газа,довольно похожи,хотя обычно отличаются только используемых газов. Водяная горелка обычно используется для сварки под давлением маленьких деталей, также как драгоценностей, газовая сварка также используется для сварки пластика,хотя нагреваемое вещество - воздух и температура намного ниже.
poisk-ru.ru