Виды и принцип работы подшипника. Устройство подшипник скольжения
Подшипники: виды, размеры, стандарты, маркировка
Подшипники — одно из ключевых изобретений, которое определило путь развития промышленности. Самый простой подшипник состоит из двух колец, вставленных одно в другое и предназначенное для поддержания и направления вращающегося вала.
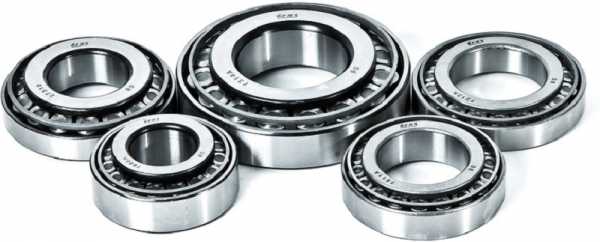
Внешний вид подшипника
Основные типы
Все подшипники могут быть разделены на две основные группы – подшипники качения и скольжения. Конструкция первых состоит из
- двух колец – внешнего и внутреннего;
- шариков;
- сепаратора, в котором установлены шарики.
- Подшипники скольжения имеют следующую конструкцию:
- внешняя обойма;
- внутренняя обойма, выполненная из материала с низким коэффициентом трения, например, тефлон (фторопласт).
Задача, которую призваны решать подшипники любого типа – это снижение трения между вращающимся и стационарными узлами агрегата. Это необходимо для снижения потерь энергии, нагрева и износа деталей, вызываемыми силой трения.
Подшипники скольжения
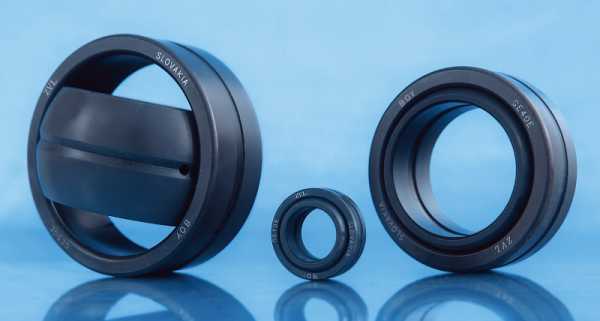
Сферические подшипники скольжения
Этот узел обычно выполняют в виде массивной опоры, изготовленной из металла. В ней проделывают отверстие, куда вставляют втулку или вкладыш, выполненный из материала с низким коэффициентом трения.Для повышения эффективности работы этого узла и снижения трения в него вводят жидкую или плотную смазку. Это приводит к тому, что вал отделяется от втулки пленкой маслянистой жидкости. Эксплуатационные параметры подшипника скольжения зависят от следующих параметров:
- Размера элементов, входящих в этот узел.
- Скоростью вращения вала и размера нагрузок, приходящихся на него.
- Густотой смазки.
Для обеспечения смазывания подшипника можно использовать любую вязкую жидкость – масло, керосин, эмульсии. В некоторых моделях подшипников скольжения для смазки применяют газы. Кроме, перечисленных материалов применяют и твердые, иногда их называют консистентные, смазки.
В некоторых конструкциях подшипников предусмотрена принудительная система смазки.
Подшипники качения
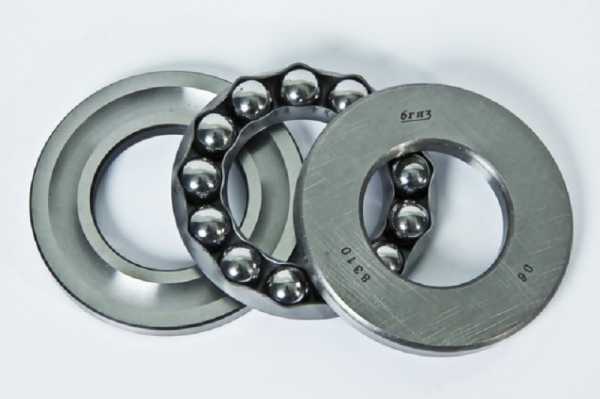
Внешний вид подшипника качения
В подшипниках этого типа трение скольжение подменяется трением качения. Благодаря такому решению происходит существенное снижение трения и износа.Подшипники качения имеют разнообразные конструкции и размеры. В качестве тел вращения могут быть использованы шарики, ролики, иголки.
Шарикоподшипники
Шарикоподшипники являются самым распространенным типом подшипников. Он состоит из двух колец, между которыми устанавливают сепаратор с предустановленными шариками определенного размера. Шарики перемещаются по канавкам, которые, при изготовлении тщательно шлифуют. Ведь для полноценной работы подшипника необходимо, чтобы шарики не проскальзывали, и при этом у них была существенная площадь опоры.Сепаратор, в который устанавливают шарики, обеспечивает их точное положение и исключает какой-либо контакт между ними. Производители выпускают изделия, которые укомплектованы двухрядными сепараторами.
Подшипники этого класса применяют при довольно небольших радиальных нагрузках и большом количестве оборотов рабочего вала.
Роликоподшипники
В подшипниках этого класса в качестве тел вращения применяют ролики различной формы. Они могут иметь форму цилиндров, усеченных конусов и пр. Производители освоили выпуск широкой номенклатуры роликовых подшипников с разными размерами колец и тел вращения.Конический роликоподшипник используют для работы при наличии разнонаправленных нагрузках (осевой и радиальной) и больших оборотах на валу. Конструктивно роликовый подшипник похож на шариковый. Он также состоит из двух колец, сепаратора и роликов. Размеры роликовых подшипников определены в ряде стандартов, которые имеют силу в нашей стране. Например, ГОСТ 8328-75 определяет конструкцию, маркировку и размеры подшипников с короткими роликами. А ГОСТ 4657-82 регламентирует размеры и конструкцию игольчатых подшипников. То есть на каждый вид подшипников существует свой ГОСТ.
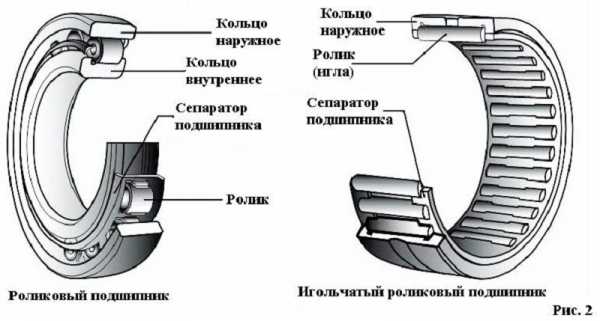
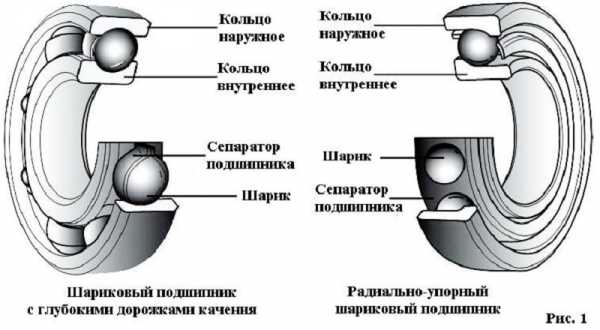
В этих нормативных документах приведены таблицы размеров подшипников, которыми должны руководствоваться конструкторы, при проектировании таких узлов.
Кстати, для облегчения жизни проектировщиков разработаны и успешно применяются справочники подшипников, в которых изложены принципы расчетов подшипниковых узлов, указаны размеры самих изделий и сопровождающих деталей, например, размеры заглушек.
Смазка
Эксплуатационный срок работы подшипников определяется износом тел качения и дорожек, расположенных в кольцах. Для продления срока службы подшипников применяют смазку, она может быть жидкой, например, в коробках передач станочного оборудования, или консистентной (твердой).
Нанесение смазки на подшипник Смазка, нанесенная на подшипникКроме износа деталей подшипника, не последнюю роль играет и рабочая температура в узле. Вследствие нее может происходить неравномерная тепловая деформация. Это может привести к повышению частоты проскальзывания, и снижается твердость материала, из которого они изготовлены.
Производители выпускают подшипники с закрытыми сепараторами. В такие изделия еще на стадии производства закладывают твердую смазку, которая гарантировано проработает весь ресурс.
Разновидности подшипников скольжения
Всего размеры и основные характеристики подшипников скольжения, изложены в соответствующих ГОСТ. Всего их насчитывается порядка шести десятков. Например, ГОСТ 11607-82 нормирует требования к разъемным корпусам подшипников скольжения, а ГОСТ 25105-82, предъявляет требования к вкладышам, которые устанавливают в корпуса подшипников скольжения.
Классификация подшипников скольжения
Изделия этого типа можно разделить на следующие основные типы:
- Одно- и многоповерхностные.
- Со смещением поверхностей.
- Радиальные.
- Осевые.
- Радиально-упорные.
Кроме того, подшипники можно различать по конструкции:
- Неразъемные, их называют втулочными.
- Разъемные, они состоят из двух деталей основного корпуса и крышки к нему.
- Встроенные, по своей конструкции, они составляют единое целое с корпусом механизма.
Нельзя забывать и о количестве точек подачи масла. Существуют подшипники с одним и несколькими клапанами. Кроме, приведенных классов можно назвать еще один – по возможности регулирований подшипника.
Конструкция подшипников скольжения не отличается сложностью. В состав конструкции могут входить два кольца. Одно из них (внутреннее) вращается в процессе работы. Вместо, тел вращения в устройствах этого типа применяют втулки, изготовленные из антифрикционных материалов. Для повышения эффективной работы в подшипники закачивают смазочные материалы.
Существуют два типа подшипников скольжения — гидростатические и гидродинамические. В изделиях первого типа смазка подается от масляного насоса. Вторые в этом плане удобнее, они сами могут выступать в роли насоса. Смазка будет поступать в них за счет разности давления между его компонентами.
Подшипники скольжения могут иметь, сферическое, упорное и линейное исполнения. Первые подшипники применяют в тех узлах, где преобладают низкие скорости вращения вала. Главное достоинство такого исполнения подшипников – это возможность передавать вращение даже при значительных перекосах валов.
Подшипники упорного исполнения применяют для работы там, где преобладают поперечные усилия. Довольно часто их монтируют в турбинах и паровых машинах.
Подшипники линейного исполнения исполняют роль направляющих. Кстати, их особенностью можно назвать их бесперебойную работу даже при постояннодействующих радиальных усилиях.
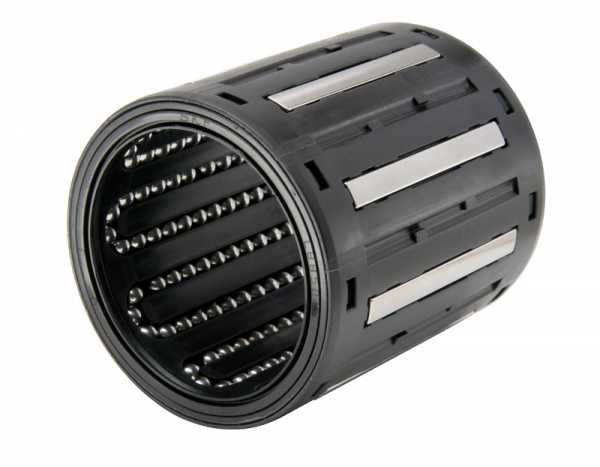
Подшипник линейного исполнения
Многолетняя, если не многовековая практика использования подшипников скольжения позволяет сделать выводы о достоинствах и недостатках этих конструкций.
- изделия этого класса обеспечивают надежную работу в условиях высоких скоростей вращения вала;
- обеспечение серьезных ударных и вибрационных усилий;
- довольно небольшие размеры;
- подшипники этого типа допустимо устанавливать в устройствах работающие в воде;
- некоторые модели позволяют выполнять настройку зазора и, таким образом, гарантируют точность установки оси вала.
Между тем, подшипникам скольжения присущи и определенные недостатки.
- в процессе эксплуатации необходимо постоянно контролировать уровень смазки;
- при недостаточной смазке и запуске возникает дополнительная сила трения;
- более низкий в сравнении с другими классами подшипников КПД;
- при производстве таких изделий применяют довольно дорогие материалы;
- при работе, подшипники этого класса могут генерировать излишний шум.
Стандарты подшипников скольжения
Одно из отличий подшипников от других типов деталей, применяемых в промышленности – это то, что они все стандартизированы. Выше было отмечено что на продукцию этого класса действует 60 ГОСТ, и это не считая ТУ и другой нормативной документации.ГОСТ не только нормирует конструкцию и размеры подшипников, но и порядок их обозначения на чертежах, в спецификациях и другой рабочей документации.
Кроме того, ГОСТ на технические условия подшипников регламентирует параметры допусков и посадок, которые обязаны соблюдать производители.
Маркировка
Маркировка подшипников – это параметры, которые показывают рабочие диаметры изделия (внутренний и внешний), конструктивные особенности. Все эти данные закодированы в наборе цифр и буквенных символов. Порядок кодировки, детальная расшифровка регламентирована в ГОСТах на подшипниковую продукцию. Так, кодировка шариковых и роликовых подшипников однорядных приведена в ГОСТ 3189-89.
В закодированном наименовании подшипника содержатся следующие данные:
- серия ширины;
- исполнение;
- тип изделия;
- группа диаметров;
- посадочный диаметр.
Кстати, важно понимать, что на территории нашей страны применяют две системы обозначения подшипников – ГОСТ и ISO.
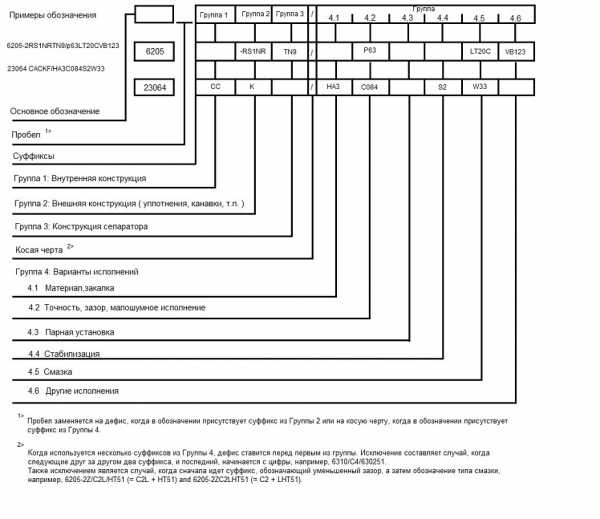
Пример расшифровки маркировки на подшипниках
Маркировка может быть нанесена на одно из колец. Если подшипник закрытого типа то маркировку наносят на уплотнение или защитном кольце.
Классы точности подшипников
Класс точности подшипника – это показатель, который характеризует максимальные отклонения значения размеров подшипника от номинала.
В некоторых устройствах при выборе подшипника потребитель руководствуется ценой на него, а остальные параметры для него не так критичны. В некоторых других случаях потребитель выбирает подшипник исходя из предельной скорости вращения, при которой не будут, проявляются такие явления, как вибрация и пр. Такие довольно жесткие условия предъявляются к изделиям, работающим на транспорте, станочным узлам, робототехнических комплексов.
В машиностроении существует зависимость между точностью обработки и ее стоимостью. То есть, чем точнее деталь, тем больше ее конечная цена.
Разделение подшипников по точности позволяет подобрать такое изделие, которое будет отвечать требованиям, которые предъявляет проектировщик и в то же время с приемлемой для потребителя ценой.
Класс точности описывает точность производства изделий. Для регулировки этого параметры существуют нормативы, определенные в ГОСТ и ISO. В них определены допуски на все размеры – диаметры, ширину, фаски и пр.
Назначение подшипников качения
Подшипники качения предназначены для поддержки вращающихся валов. Они нашли свое применение в машинах, разного типа, например, в подъемно-транспортных устройствах, технике, применяемой в сельском хозяйстве, судовых двигателях.
Магнитные подшипники
Магнитные подшипники, которые все чаще применяют в различных машинах и механизмах работает на основании принципа магнитной левитации. В результате реализации этого принципа в подшипниковой опоре отсутствует контакт между валом и корпусом подшипника. Существуют активное исполнение и пассивное.
Активные изделия уже в массовом производстве. Пассивные, пока еще находятся на стадии разработки. В них, для получения постоянного магнитного поля применяют постоянные магниты типа NdFeB.
Использование магнитных подшипников предоставляет потребителю следующие преимущества:
- высокая износостойкость подшипникового узла;
- применение таких изделий, возможно, в агрессивных средах в большом диапазоне внешней температуры.
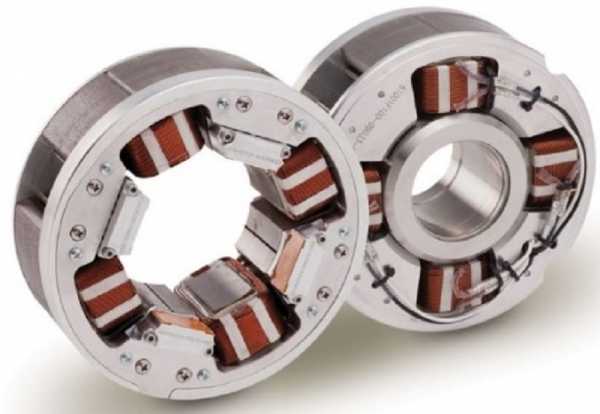
Бесконтактный магнитный подшипник
В то же время использование таких узлов влечет за собой некоторые сложности, в частности:
В случае пропадания магнитного поля, механизм неизбежно понесет повреждения. Поэтому для бесперебойной и безаварийной работы проектировщики применяют так называемые страховые подшипники. Как правило, в качестве страховочных применяют подшипники качения. Но они в состоянии выдержать несколько отказов системы, после этого требуется их замена, так будут изменены их размеры.
Создание постояннодействующего, а главное, устойчивого, магнитного поля сопряжено с созданием больших и сложных систем управления. Такие комплексы вызывают сложности с ремонтом и обслуживанием подшипниковых узлов.
Излишнее тепловыделение. Оно обусловлено тем, что обмотка нагревается в результате прохождения через нее электрического тока, в некоторых случаях, такой нагрев недопустим и поэтому приходится устанавливать системы охлаждения, что, разумеется, приводит к усложнению и удорожанию конструкции.
Где используются устройства скольжения
На самом деле сложно найти механизм, в котором не установлены подшипники скольжения. Даже на атомных подводных лодках, на подшипниках этого типа устанавливают гребные валы. Подшипники скольжения нашли широкое применение в станкостроении. В частности, в них устанавливают валы, по которым перемещается суппорт, резцедержатель и другие составные части станка.
Классификация подшипников качения
К подшипникам качения относят:
- шариковые;
- роликовые,
- упорные и многие другие.
Все они характеризуются высокими параметрами износостойкости и возможностью работы в условиях разнонаправленных нагрузок – осевых и радиальных.
Характеристики подшипников качения
К основным характеристикам подшипников качения можно отнести следующие:
Угловая скорость, подшипники качения могут показывать высокие значении этой скорости, особенно если сепараторы выполнены из цветного металла или полимеров.
Перекос вала. Допустимо то, что перекос может достигать от 15’ до 30’. Кроме того, подшипники качения способны воспринимать небольшие осевые усилия. Она не должна превышать 70% от неиспользуемой радиальной грузоподъемности.
Подшипники качения показывают минимальные потери на трение.
Каталог импортных подшипников FAG, INA, SKF, NSK, TIMKEN и др.
В мировой экономике подшипниковая отрасль занимает отдельное место, во много это обусловлено значимостью продукции ей выпускаемой.
В нашей стране такую продукцию выпускают на специализированных подшипниковых заводах. Но, в последнее время существенно увеличен импорт подшипников из рубежа. Их поставляют из разных стран мира – США, КНР, Германии и пр.
Для ознакомления с номенклатурой поставляемой продукции достаточно ознакомиться с каталогами подшипников, которые предлагают потребителям зарубежные производители — FAG, INA, SKF, NSK, TIMKEN и многие другие. Достаточно одного взгляда и можно понять всю величину номенклатуры предлагаемых подшипников.
Но при заказе импортной продукции необходимо понимать, что подшипники, поступающие из-за границы, должны соответствовать требованиям наших нормативов и иметь документы, подтверждающие их качество и безопасность в эксплуатации. Подшипники очень часто поделывают. Рекомендуем покупать подшипники только у авторизированных поставщиков.
Если вы нашли ошибку, пожалуйста, выделите фрагмент текста и нажмите Ctrl+Enter.
stankiexpert.ru
Виды и принцип работы подшипника
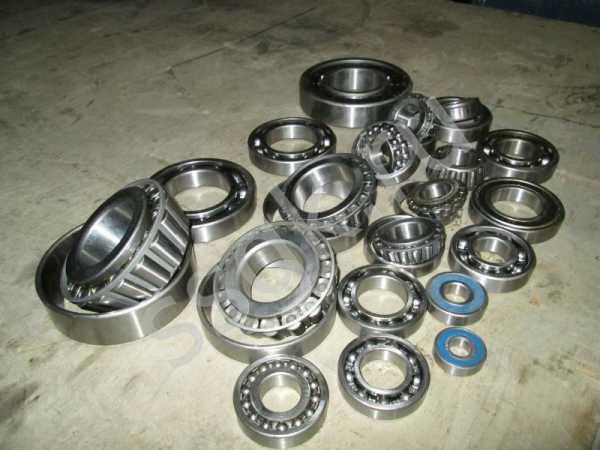
Подшипниками называются технические устройства, которые являются комплектующими опор вращающихся валов и осей. Они принимают на себя нагрузки, которые испытывают вал или ось, и передают эти нагрузки на корпус, раму и другие несущие части конструкции. При этом принцип работы подшипника заключается также в том, чтобы удержать в пространстве вал, обеспечить качание, вращение или же перемещение по прямой в определенном направлении с минимальной энергопотерей.
Качество подшипников в большой мере влияет на работоспособность, КПД и, соответственно, долговечность автомобиля.
На сегодняшний день наиболее широкое применение нашли такие подшипники:
— контактные, то есть те, которые имеют трущиеся поверхности, их называют подшипники скольжения и качения;
— бесконтактные, у которых нет трущихся поверхностей, — так называемые магнитные подшипники.
Соответственно, контактные подшипники различаются в зависимости от вида трения:
— подшипники скольжения — опорная поверхность вала или оси скользит по поверхности подшипника;
— подшипники качения — используется трение качения шариков, установленных между кольцами, одно из которых подвижное, а другое — статичное.
Подшипник скольжения: принцип работы
Подшипник скольжения состоит из корпуса с цилиндрическим отверстием, в котором вставлен вкладыш или втулка, изготовленная из антифрикционного материала (для этой цели нередко используются цветные металлы), а также смазывающее устройство. Между отверстием втулки и валом имеется зазор, благодаря которому вал может свободно вращаться.
Известно множество конструкций подшипников скольжения — сегментные, самоустанавливающиеся, самосмазывающиеся. Размеры шарнирных подшипников скольжения стандартизированы, и их выпускают сериями на производстве.
В соответствии с конструктивными особенностями и выполняемыми функциями различают три вида подшипников скольжения:
— сферические;
— упорные;
— линейные.
Сферические подшипники применяются при работе механизмов на малой скорости. Они могут работать даже при больших осевых перекосах и умеренных колебательных движениях. Корпус сферического подшипника скольжения может выдержать значительную осевую нагрузку.
Упорные подшипники разрабатывались для радиальных (поперечных) и малых осевых нагрузок. Их с успехом применяют в паровых и турбинных установках.
Линейные подшипники являются своего рода направляющими при линейном перемещении. Они используются при высокой скорости вращения, дают возможность работать в воде, при высокой вибрационной и ударной нагрузке, могут применяться на коленчатых валах, где требуются разъемные подшипники.
Ступичный подшипник
Ступичный подшипник является составляющей подвески. Он обеспечивает минимальное трение при вращении колес, комфортное, бесшумное и легкое движение автомобиля, надежен, имеет большой ресурс.
Ступичные подшипники работают в экстремальных условиях, которые характеризуются большими перепадами температуры, повышенной влажностью, воздействием антигололедных реагентов, высокими динамическими нагрузками — это связано прежде всего с ударами на неровной дороге рулевого управления, привода, тормозов. С этими особенностями эксплуатации связан принцип работы подшипника ступицы.
Специалисты рекомендуют регулярно, при каждом проведении диагностики автомобиля проводить тщательную проверку состояния ступичных подшипников — независимо от интервала, который рекомендует производитель.
Во время осмотра подшипников необходимо уделить внимание качеству вращения колес, которое у радиально-упорных шариковых подшипников не должно сопровождаться люфтами, а коническим роликовым подшипникам, наоборот, все же необходим небольшой люфт.
Кроме того, необходимо следить за уровнем шума, который не должен превышать допустимый. Трение при этом должно быть минимальным.
Поскольку конструкция такова, что часть ступичных подшипников снабжается многополюсным магнитным кольцом, нужно следить, чтобы при хранении или монтаже на подшипники не оказывалось воздействие никаких магнитных полей, поскольку вследствие такого влияния подшипники могут прийти в непригодность.
При монтаже подшипников необходимо учитывать, что полюсное кольцо всегда должно быть направлено по направлению к сенсору датчика оборотов.
gosindex.ru
Сборка подшипников скольжения и качения
Сборка подшипников скольжения и каченияКатегория:
Слесарно-механосборочные работы
Сборка подшипников скольжения и каченияСборка сборочных единиц с подшипниками скольжения — одна из самых ответственных операций сборки, от выполнения которой зависит точность и долговечность работы машины.
Сборка неразъемного подшипника скольжения заключается в запрессовке втулки в корпус, стопорении ее и пригонке отверстия по валу. При посадке втулки с натягом ее внутренний диаметр уменьшается. Для получения заданного размера внутреннюю поверхность втулки после запрессовки пришабривают по валу, калибруют, развертывают или растачивают.
После запрессовки втулку необходимо обработать так, чтобы обеспечивалась строгая соосность поверхностей скольжения. Соосность втулки проверяют эталонными скалками, калибрами или контрольными приспособлениями индикаторного типа. Кроме того, визуально проверяют поверхность скольжения на отсутствие царапин и других дефектов.
Плотность посадки втулки проверяют предварительно (контроль сопряженных деталей или контроль силы запрессовки) в процессе сборки. Коническую несущую поверхность втулки проверяют по краске эталонной скалкой или по окончательно обработанному валу.
Сборка разъемного подшипника скольжения состоит из следующих операций:— сопряжения вкладышей подшипников с корпусом;— проверки соосности рабочих поверхностей подшипников;— подгонки прилегания рабочих поверхностей вкладышей и вала;— регулирования необходимого монтажного зазора в подшипнике;— укладки вала в подшипнике.
Вкладыш подгоняют к корпусу по наружному диаметру, используя краску. Отпечатки краски должны занимать 70—80% поверхности подшипника. Сферические поверхности самоустанавливающихся вкладышей пригоняют к гнездам совместной притиркой.
Одновременно с подгонкой вкладышей выверяют соосность их с корпусом. Отклонение от соосности не должно превышать 0,15 мм. Соосность выверяют эталонным валом, контрольной линейкой и щупом, струной и штихмассом, а также оптическим способом (длина более 4 м).
Диаметр эталонного вала рассчитывают с учетом допустимых отклонений от соосности. При соответствии техническим условиям вал должен легко проходить во все втулки (гнезда вкладышей) подшипников и свободно вращаться.
Ребро линейки прикладывают к стенкам вкладышей, а зазор контролируют щупом. При проверке соосности струной (стальной проволокой диаметром 0,25—0,5 мм) один конец ее закрепляют на стойке, а второй — перекидывают через ролик и подвешивают груз для натяга струны. Ролик и стойка перемещаются в двух направлениях. Сначала струну устанавливают параллельно базовой поверхности корпуса, а затем, перемещая стойку и ролик в горизонтальной плоскости, добиваются совпадения струны с осями крайних подшипников. После этого по натянутой струне устанавливают все промежуточные опоры.
Рис. 1. Схемы проверки подшипников:
Для повышения точности при замерах струну натягивают на изолированных стойках и включают ее в электрическую цепь аккумуляторной батареи с лампочкой. Когда штихмасс соединяется со струной и корпусом подшипника, лампочка загорается.
После выверки соосности осей подшипников приступают к сборке и пригонке вкладышей к шейкам и шипам вала, которые предварительно протирают и покрывают тонким слоем краски. Вал устанавливают в закрепленные подшипники и проворачивают на три-четыре оборота. Окрашенные места вкладышей сшабривают. Сначала пришабривают поверхности нижних вкладышей, добиваясь равномерного расположения пятен контакта (т. е. 9—12 пятен на квадрат 25 х 25 мм). Количество пятен на квадрат 25 х 25 мм определяют наложением на внутреннюю поверхность подшипника целлулоидного шаблона, на котором нанесены линии, образующие квадрат.
Затем пришабривают внутренние поверхности верхних вкладышей. Для этого подшипники приходится собирать, устанавливая прокладки и затягивая гайки динамометрическим ключом. Повернув вал на три-четыре оборота, подшипники разбирают и окрашенные места верхних вкладышей сшабривают. Операцию повторяют несколько раз до тех пор, пока не будет достигнуто удовлетворительное распределение точек контакта.
Величину масляного зазора контролируют латунными пластинками необходимой толщины или свинцовыми проволочками. Пластинку или проволочки смазывают маслом и закладывают между вкладышем и шейкой вала. После затягивания подшипника динамометрическим ключом вал проворачивают от руки. При легком вращении диаметральный зазор должен быть меньше толщины пластинки. Если ощущается сопротивление проворачиванию, то зазор соответствует толщине пластины.
Необходимую величину зазора регулируют набором прокладок. Толщину набора прокладок устанавливают с учетом компенсации зазора при последующей эксплуатации машины. Для этой цели в комплект включают прокладки толщиной 0,05; 0,1; 0,15; 0,2; 0,3; 0,5; 0,8 мм. Вкладыши и крышки маркируют по корпусам подшипников.
Рис. 2. Проверка качества шабрения внутренних поверхностей вкладышей и подшипников скольжения целлулоидным шаблоном
После регулирования зазора окончательно затягивают гайки, крепящие крышки подшипников. Затягивание гаек проверяют рычагом и грузом, определяющим крутящий момент, величина которого указывается в сборочных картах.
Сборка сборочных единиц с подшипниками качения выполняется следующим образом. При монтаже подшипников необходимо создать зазоры, обеспечивающие свободное, без защемления шариков или роликов вращение подшипников. При слишком плотной посадке происходит расширение внутреннего кольца подшипника и сжатие его наружного кольца, в результате чего шарики или ролики защемляются и подшипник быстро выходит из строя. Чрезмерный зазор в посадочных местах также ухудшает работу подшипника: кольца его начинают проскальзывать, вызывая износ посадочных поверхностей и вибрацию механизма.
Рис. 3. Регулировка радиального зазора прокладками
Рис. 4. Порядок затягивания гаек подшипников и схема проверки вала на проворачивание
Перед сборкой подшипники тщательно промывают в смеси бензина и минерального масла или в обезвоженном чистом керосине. Промытые подшипники укладывают на чистую бумагу и просушивают или обдувают сжатым воздухом. Сразу после просушки их смазывают, покрывая тонким слоем масла все поверхности, особенно внутренние дорожки качения, шарики и ролики. Посадку подшипников на вал производят по системе отверстия, а в корпус – по системе вала.
Посадка подшипников на валы, в гнезда корпусов деталей может быть выполнена с помощью ручных, гидравлических или пневматических прессов, с подогревом в горячем масле 353 — 363 К (80 — 90 °С) или с охлаждением твердой углекислотой – сухим льдом (температура 348 – 353 К (минус 75 – 80 °Q.
Для напрессовки подшипника на шейку вала могут быть использованы ручные приспособления — монтажные стаканы и оправки. Применение оправок обеспечивает равномерную посадку подшипника на шейку вала, предотвращает перекос при установке и предохраняет подшипник от повреждений. Для напрессовок подшипников на валы, имеющие на конце резьбу, часто используют гаечные и винтовые устройства.
Для напрессовки и распрессовки крупных подшипников применяют гидравлическую гайку, которая состоит из корпуса и поршня. Поршень имеет две канавки для уплотнительных колец и перемещается в корпусе гайки под давлением масла, подаваемого ручным насосом по трубке. Корпус гайки внутри имеет метрическую или трапецеидальную резьбу.
Рис. 5. Приспособление для напрессовки подшипников: а – напрессовка подшипника с помощью оправки и ручного пресса; б — с мощью стакана 1 и кольца 2; в – с помощью ручной оправки
Рис. 6. Гаечное приспособление для напрессовки подшипников : 1 – гайка, 2 — корпус, 3 – шайба, 4 — ручка
Рис. 7. Винтовое приспособление для напрессовки подшипников: 1 – подшипник, 2 – вал, 3 – втулка, 4 – гайка, 5 – соединительный винт, 6 – переходная втулка, 7 – винт, 8 – шайба, 9 – корпус, 10 – ручка
Рис. 8. Приспособление гидравлическая гайка с насосом для запрессовки подшипников
При монтаже подшипников качения учитывают, что усилие запрессовки должно передаваться непосредственно на торец сопрягаемого кольца.
В упорных шарикоподшипниках кольца имеют разные диаметры — как наружные, так и внутренние. Чтобы подшипник работал нормально, при сборке всегда устанавливают кольцо с меньшим внутренним диаметром на валу, а кольцо с большим внутренним диаметром — в корпусе.
При установке вала в двух радиальных шарикоподшипниках один из них закрепляют неподвижно на валу и в корпусе, а второй — только на валу, потому что вал во время работы нагревается и его длина несколько возрастает. При удлинении вала подшипник перемещается в корпусе. Если закрепить оба подшипника неподвижно, вал, нагревшись, начнет туго поворачиваться и произойдет защемление шариков или роликов и оба подшипника могут быстро выйти из строя.
Запрессованный подшипник проверяют, поворачивая его вручную. Вращение подшипника должно быть плавным, без заеданий. При этом может прослушиваться незначительный равномерный шум. Проверяют также прилегание наружного кольца к бортику отверстия корпуса, а внутреннего кольца — к заплечику вала.
Подшипники стопорятся от осевого смещения на валу или в корпусе гайкой с шайбой, запорным кольцом, втулкой, крышкой, стопорными винтами.
Для выяснения эксплуатационных качеств шарикоподшипников необходимо проверять и регулировать радиальный и осевой зазоры. При малых и больших зазорах подшипники быстро изнашиваются. Регулирование зазоров в подшипниках — ответственная сборочная операция, так как неправильно установленный зазор часто может быть основной причиной преждевременного износа подшипников.
При сборке сборочных единиц с упорными и коническими роликовыми подшипниками осевой зазор регулируют прокладками, регулировочным болтом или регулировочной втулкой.
При регулировании зазора прокладками сначала зажимают крышку без прокладок до тех пор, пока вал не будет провертываться очень туго. Затягивая гайки или винты, вал нужно повернуть на несколько оборотов, чтобы ролики подшипника имели возможность правильно установиться. При зажатой до конца крышке зазора в подшипнике нет. Замеряя в этом положении в двух-трех местах зазор А между крышкой и корпусом и прибавляя к нему требуемое осевое перемещение вала С, определим толщину Т калиброванной прокладки, которую нужно подложить под крышку, т. е. Т= А + С.
Рис. 9. Схемы стопорения подшипников: а — крышкой, б — болтом в промежуточную крышку, в — втулкой б и угольником
При регулировании зазора в подшипнике болтом и гайкой сначала их затягивают до тугого провертывания вала (это показывает, что зазоры выбраны правильно). Затем по величине шага Р резьбы определяют, на какой угол Ф следует провернуть винт или гайку, чтобы получить требуемый зазор: ф = С/(Р- 360°).
Читать далее:
Применение при сборке уплотняющих устройств подшипников
Статьи по теме:
pereosnastka.ru
Виды, назначение и обозначения подшипников
Обозначения подшипников сегодня крайне активно используются в различных сферах современного производства, ведь это абсолютно незаменимая деталь, которая сегодня применяется в преимущественном большинстве самых разнообразных механизмов и узлов. На сегодняшний день их повсеместно используют во всем, начиная от миниатюрной техники бытового назначения и заканчивая огромными механизмами, использующимися в промышленном производственном оборудовании.
Ни одно современное предприятие, промышленный комплекс или же производственное объединение не может не использовать те или иные обозначения подшипников и сами изделия, которые при этом имеют ограниченный срок службы, и единственной причиной такого явления является то, что им просто нет какой-то конкретной альтернативы. В связи с этим бесперебойность и активность работы различных предприятий, а значит, и их экономическая эффективность непосредственно зависят от того, насколько своевременно поставляются и ставятся такие изделия в случае их износа.
История
Не все правильно понимают старую поговорку, говорящую о том, что все новое представляет собой просто давно забытое старое. Это бессмертное высказывание вполне подходит практически под любые современные технологии, и в частности, это касается подшипника, несмотря на то, что с тех времен, как появились первые обозначения подшипников, прошел уже огромный эволюционный путь, и изначально такие изделия выглядели далеко не так, как их сегодня представляют многие.
Если совсем глубоко окунаться в историю, то начать стоит с 3500 года до н.э., когда жители Древнего Египта использовали, хоть и достаточно примитивные, но в то же время для своего времени крайне эффективные опорные подшипники, в которых, правда, на тот момент еще не использовались шарики. Приблизительно в 700-м году до н.э. кельты уже прекрасно знали и достаточно активно использовали изделия, которые в наше время обозначения подшипников именуют как цилиндрические устройства качения.
Следующий шаг – 330 год до н.э., в котором один из известнейших инженеров Древней Греции Диад смог создать полноценную осадную машину, одним из основных элементов которой были достаточно примитивные подшипники. Данная машина представляла собой полноценный массивный таран, который мог без труда передвигаться при помощи роликовых направляющих. Именно так на практике был показан принцип, который несет в себе любой шариковый подшипник качения, то есть трение скольжения получилось заменить трением качения, благодаря чему машина смогла без труда выполнять поставленные перед ней задачи, используя гораздо меньше силы.
В 1490 году Леонардо да Винчи изобрел первый в мире чертеж подшипника качения. Стоит отметить тот факт, что данное изобретение вызвало самый настоящий фурор в кругах специалистов, но на самом деле с течением времени многие поняли, что на тот момент такому изделию просто не находилось практического применения.
В 1794 году произошло первое патентование подшипника качения, который является аналогом современного устройства. К сожалению, использованию этого образца на практике тоже не суждено было состояться, потому что для того, чтобы полноценно реализовать данную идею, нужно было иметь другие технические возможности, так как использование ручной полировки не позволяло добиться соответствующих результатов.
В 1839 году ученый из Америки по имени Исаак Бэббит изобретает специализированный сплав, с помощью которого начали производиться шарики, которые дальше включал в свой состав полноценный роликовый подшипник качения. Данный сплав включал в свой состав медь, сурьму, свинец и олово.
Далее произошел настоящий прорыв в области обоснованных с технической точки зрения конструкций подшипника, и преимущественное большинство из них, естественно, было запатентовано. В 1853 году Филлип Мориц Фишер конструирует первый в истории педальный велосипед, механизмы которого содержали в себе специализированный роликовый подшипник.
Последним действительно значимым для запуска повсеместного распространения и использования таких изделий событием стало то, что Фридрих Фишер создал в 1883 году машину, при помощи которой осуществлялось шлифование шариков, изготовленных из закаленной стали. При этом стоит отметить тот факт, что данная машина позволяла получить такой высокий уровень шлифования, который ранее был просто недостижим. За счет создания данной машины появился знаменитый на весь мир швейнфуртский подшипниковый завод, а в дальнейшем подобные изделия уже начали применяться практически повсеместно.
С тех пор непрерывно осуществлялось совершенствование технологий огромными темпами – закупалось более точное оборудование, начал проставляться номер подшипника, разрабатываться определенные стандарты производства. В конце концов мы видим знакомое многим изделия, без которого в наши дни практически невозможно представить себе современное производство.
Самыми востребованными и популярными в наше время можно назвать подшипники скольжения и качения, поэтому в данной статье мы разберем именно их использование.
Подшипники качения
Основным принципом данного подшипника является применение силы трения качения. Такое изделие имеет конструкцию, которая составляется из двух металлических колец с желобом, между которыми размещаются ролики, иглы или шарики, фиксирующиеся внутри сепаратора, размещенного между кольцами. Стоит отметить, что можно найти не один номер подшипника, предусматривающий возможность отсутствия сепаратора в его конструкции.
В чем их различия?
Современные подшипники качения принято классифицировать по нескольким основным признакам:
- Вид тел, которые используются для обеспечения того самого качения – роликовый/игольчатый или же шариковый подшипник;
- Тип возможной нагрузки – линейные, упорные, радиальные, радиально-упорные и шариковые винтовые передачи.
- Общее количество используемых элементов – от однорядных до многорядных.
- Возможность обеспечения компенсации того, что в конструкции отсутствует соосность втулки и вала – несамоустанавливающиеся и самоустанавливающиеся.
Преимущества
Существует целый ряд достоинств, которыми выгодно отличаются такие подшипники. ГОСТ устанавливает достаточно жесткие нормы производства таких изделий, соответствие которым должно обеспечивать следующие преимущества:
- Предельно высокий КДА, который обеспечивается за счет достижения минимальных потерь из-за трения.
- В разы, а в некоторых случаях даже в десятки раз уменьшенный момент трения по сравнению с подшипниками скольжения.
- Полное отсутствие какой-либо потребности в применении дорогостоящих цветных металлов, без которых не могли бы эффективно использоваться подшипники скольжения, что крайне положительно сказывается на изначальной себестоимости и, соответственно, конечной цене, которую имеют такие подшипники. ГОСТ при этом достаточно четко указывает требования к их производству, поэтому не приходится беспокоиться о том, что за меньшие деньги вы получите не столь качественное изделие.
- Возможность изготовления подшипников практически любых интересующих вас габаритов по направлению к оси, благодаря чему диапазон их применения значительно расширяется.
- Великолепные эксплуатационные параметры, а также полная неприхотливость в обслуживании в комбинации с относительной простотой замены.
- Предельно низкий расход смазки.
- Достаточно низкая стоимость, что представляет собой следствие слишком большой массовости производства таких изделий, а также количества используемых материалов.
- Довольно высокая степень взаимозаменяемости, что также положительно сказывается на общей простоте и величине скорости ремонта различного оборудования и машин.
Минусы
При этом нельзя не сказать о том, что даже обозначение импортных подшипников такого типа предусматривает наличие у них определенных недостатков, а именно:
- Относительно небольшой диапазон применения. В преимущественном большинстве случаев, если разбирать обозначения подшипников, расшифровка их характеристик четко указывает на их полную непригодность для применения в оборудовании, работающем на сверхвысоких скоростях и с большими вибрационными и ударными нагрузками, так как все это подобным изделиям неподвластно.
- Довольно большая масса и габариты в радиальном направлении.
- Отсутствие возможности создания полностью бесшумных подшипников из-за погрешности форм.
- Достаточно сложная установка всевозможных подшипниковых узлов.
- Нужно крайне внимательно относиться к тому, чтобы максимально точно устанавливать такие изделия, о чем свидетельствуют обозначения подшипников. Расшифровка основных параметров и практических примеров их использования говорит о том, что даже небольшие неточности в конечном итоге могут привести к выведению из строя всего узла.
- В процессе изготовления маленьких партий подшипников с нестандартными типоразмерами их стоимость увеличивается довольно сильно.
Подшипники скольжения
Обозначение подшипников по ГОСТ говорит о том, что устройства скольжения представляют собой корпус с отверстием, внутри которого находится смазочное приспособление и специализированная втулка, изготовленная из антифрикционного материала. Вращение вала осуществляется за счет зазора, предусмотренного между ним и отверстием. Стоит отметить тот факт, что расчету данного зазора уделяется особенное внимание, так как в противном случае просто не удастся обеспечить действительно эффективную работу данного изделия. Именно поэтому обозначение подшипников SKF и лого других крупнейших мировых производителей, как минимум, позволяет быть уверенным в том, что их характеристики соответствуют изделиям высокого уровня и не дадут сомневаться в эффективности применяемых изделий.
Трение скольжения в подобных изделиях разделяется на несколько основных категорий:
- Граничное. Смазочный материал покрывает изделие тонкой пленкой, в то время как подшипник с валом соприкасается на полную или же просто затрагивает участки на большой протяженности.
- Жидкостное. За счет применения слоя достаточно жидкой смазки исключается непосредственное непрерывное соприкосновение поверхностей подшипника и вала. Такой контакт может или полностью отсутствовать или же быть непостоянным в определенных участках.
- Газовое. За счет присутствия газовой прослойки между изделием и валом полностью исключается возможность их непосредственного соприкосновения.
- Сухое. Смазка не используется в принципе, а валы при этом полностью покрывают диаметры подшипников или же те ложатся на участки значительной протяженности.
В зависимости от типа используемого изделия может использоваться пластичная, жидкая, газообразная или же твердая смазка.
Классификация
Классификация таких изделий осуществляется в зависимости от следующих признаков:
- Форма отверстия – одноповерхностные или многоповерхностные; со смещенным центром или без смещения; со смещенной поверхностью или без смещения.
- Направления возникающей нагрузки – осевые, радиальные или же радиально-упорные.
- Количество используемых масляных клапанов – один или два и более.
- Конструкция – разъемные, неразъемные или же встроенные.
- Регулируемость – возможность регулировки или же ее отсутствие.
Преимущества
Если говорить об основных достоинствах таких изделий, всего их можно выделить несколько:
- Крайне широкий диапазон возможных сфер применения за счет того, что подшипники могут нормально работать даже на больших ударных и вибрационных нагрузках или же при достаточно высокой скорости.
- Достаточно высокая степень экономичности, если используется вал с большим диаметром.
- Возможность использования в виде разъемного подшипника.
- Возможность обеспечения регулировки зазора, благодаря чему может устанавливаться ось вала с предельной точностью.
Недостатки
При этом, естественно, у таких изделий есть и некоторые минусы:
- В отличие от того, как указывается обозначение подшипников качения, здесь не самый высокий КПД, так как присутствуют довольно существенные потери от трения.
- Нет возможности обеспечения нормальной работы без регулярного смазывания.
- Неравномерный износ цапфы и самого изделия.
- Достаточно высокая себестоимость из-за необходимости регулярного применения цветных металлов в процессе производства.
- Огромная трудоемкость в изготовлении.
Маркировка
Все изделия, которые изготавливаются на территории России, должны в обязательном порядке маркироваться производителями, причем устанавливается обозначение подшипников по ГОСТ. В маркировку любого современного подшипника входит семь цифр главного обозначения, а также несколько дополнительных знаков, которые располагаются слева или же справа от основного обозначения. При этом стоит отметить тот факт, что от основного дополнительная маркировка слева всегда должна отделяться дефисом, в то время как справа находится буквенное обозначение подшипников. При этом знаки в любом случае должны читаться только слева направо.
Левые знаки, которые включает в себя обозначение подшипников на чертеже, содержат в себе следующее:
- момент трения;
- категорию изделия;
- класс точности;
- группу радиального зазора.
Справа же указывается следующее:
- конструктивные изменения;
- материал, использующийся в процессе изготовления данных деталей;
- смазочный материал;
- температура отпуска;
- основные требования к обеспечению определенного уровня вибрации.
Диаметры
Если речь идет об обозначении диаметров, размер которых составляет не более 10 мм, то в таком случае рассматривается значение номинального диаметра, и единственным исключением здесь являются подшипники, имеющие отверстия с диаметром в диапазоне 0.6-2.5 мм, обозначение которых осуществляется дробным числом. В остальных ситуациях, если диаметр имеет дробное значение, то в таком случае обозначение будет иметь округленное до целого, в то время как на втором месте в обозначении данного изделия ставится цифра «5».
Подшипники, диаметр отверстия которых составляет 10, 12, 15 или же 17 мм, в своем обозначении диаметра имеют числа 00, 01, 02 или же 03 соответственно. Если же это отверстие, размер которого находится в диапазоне от 10 до 19 мм, но при этом не входит в перечисленный выше список, то в таком случае изделие обозначается ближайшим числом из вышеперечисленного, а в третьей позиции маркировки ставится цифра «9».
Если диаметр отверстия составляет 22, 28, 32 или же 500 мм, то в таком случае им указываются дробные значения. К примеру, изделие с диаметром 22 мм может иметь обозначение «602/22».
Если диаметр отверстия имеет целое или дробное число, не кратное пяти, то в таком случае они обозначаются в виде округленных до целого числа частных от деления настоящего диаметра на 5. При этом основное обозначение таких изделий включает в себя на третьем месте цифру «9».
Внутренний диаметр подшипников, имеющий отверстие более 500 мм, имеет обозначение, которое полностью совпадает с указанным значением диаметра отверстия, рассчитанного в миллиметрах.
Помимо всего прочего, указывается размерная серия подшипника, которая включает в себя сочетание серий ширин и диаметров для определения точных габаритов.
fb.ru
Подшипники скольжения
Для обеспечения вращения в различном оборудовании используются подшипники. Разновидностей их достаточно много, а выбор осуществляется с учётом параметров оборудования и технических характеристик самих подшипников. Более подробно рассмотрим подшипники скольжения.
Виды и комплектация подшипников скольжения
Конструктивно, подшипники скольжения, могут иметь несколько видов, а именно быть разъёмными и неразъёмными приспособлениями. Во многом особенности строения подшипника являются определяющими при его выборе.
В комплектацию неразъёмных подшипников скольжения входит:
1. Целостный корпус. 2. Втулка. 3. Деталь соединения.
В свою очередь подшипники скольжения разъёмного типа состоят из:
1. Разборный корпус. 2. Вкладыши. 3. Деталь соединения.
Втулки или вкладыши обычно производят из материалов обладающих высокими антифрикционными свойствами. А в качестве детали для соединительного элемента в подшипниках скольжения, чаще всего применяются вал, палец, цапфа или короткий валик.
Износ и ремонт подшипников скольжения
Основной причиной поломок подшипников скольжения является износ приспособления от интенсивной эксплуатации, происходящий в зоне трения, или же значительное ослабление втулки или вкладыша в плотно подогнанной конструкции приспособления. При возрастающем износе составляющих, соединение между ними становится менее плотным, вследствие чего, в подшипниках скольжения проявляются различные нагрузки, в том числе и ударные. Кроме того, износ комплектующих элементов подшипников скольжения, может привести к разрегулировке всего механического узла, а также утечки смазочных материалов.
В качестве восстановительных мер, при обнаружении недостатков необходимо устранить ослабление вкладышей (втулки) подшипников скольжения, или же довести зазор между элементами трения до обычного состояния. Соответственно выбор восстановительных мероприятий зависит от характера неполадок. Наиболее часто применяются следующие меры, направленные на уменьшение зазора между деталями трения в подшипниках скольжения:
1. Обработка деталей соединения до расчётных размеров, при этом кольцо подшипника уменьшается до соответствующего размера.
2. Замена соединительной детали с обработкой места посадки.
3. Проведение наращивания с целью восстановить прежние размеры элементов.
В процессе сборки подшипников скольжения достаточно важно соблюдать геометрические пропорции, достаточную плотность соединения, а также высокое качество поверхностей деталей трения.
Втулка подшипников скольжения
При восстановительных работах связанных с заменой втулки, необходимо провести следующие мероприятия, которые позволят избежать дополнительной обработки посадочного отверстия:
1. Необходимо точно соблюдать натяг при посадке. При несоблюдении его возможно образование слишком маленького смазочного зазора, а так же недостаточно плотной посадки.
2. Располагать втулку необходимо соблюдая совпадение смазочных отверстий.
3. Для образования посадки со значительным натягом необходимо произвести нагрев втулки, при этом охладив корпус.
Области применения подшипников скольжения:
1. Высокоскоростная аппаратура. Однако износ подшипников при этом весьма значителен. 2. В условиях, которые диктуют установку только разъёмного типа подшипников скольжения. 3. В случаях, когда работа проходит в условиях повышенной влажности или агрессивной кислотной среде. 4. Используются на валах, работающих с ударными и вибрационными нагрузками. 5. Устанавливаются на близко расположенных валах, во многом за счёт своих малых габаритов. 6. В тихоходных машинах и узлах, к которым не предъявляются высокие рабочие требования.
promplace.ru
Устройство подшипника | Справочник конструктора-машиностроителя
В чем причина быстрого увеличения импорта подшипников в Россию, способны ли российские производители подшипников конкурировать с ведущими зарубежными компаниями, какие трудности имеются в связях между торговыми компаниями и производителями подшипников, как отличить подделку от качественного подшипника?На сии и иные проблемы в интервью Порталу машиностроения ответил менеджер Дистрибьютора NTN - SNR в России, Андрей Ильченко.
Robowood_Twister_5XM.jpg
Подшипник скольжения — опора или ведущая механизма или машинки, в которой трение происходит при скольжении сопряжённых поверхностей.Радиальный подшипник скольжения представляет собой, который нельзя отменить цилиндрическое отверстие, в которое вставляется рабочий элемент — вкладыш, или втулка из антифрикционного материала и смазывающее устройство.Между валом и отверстием втулки подшипника имеется, который был перекрыт смазочным материалом, который позволяет свободно вращаться валу.Расчёт зазора подшипника, действующего в порядке разделения поверхностей трения смазочным слоем, производится на основе гидродинамической теории смазки.
Подшипники - это технические устройства, представляющие частью опор вращающихся осей и валов.Они воспринимают радиальные и осевые нагрузки, приложенные к валу или оси, и передают их на рамку, корпус или иные части конструкции.При этом они необходимы также удерживать вал в пространстве, обеспечивать вращение, шатание или линейное перемещение с наименьшими энергопотерями.От качества подшипников в важной степени зависит коэффициент полезного влияния, работоспособность и долговечность машины.
Подшипники скольжения электрических машин вмонтированы в подшипниковые щиты или выброшены за их границы и установлены в стойках, задаваемых на общем фундаменте со станиной машины.Конструктивно подшипники скольжения выполняют в облике целой или составной втулки ;новая заключается из двух половин ( вкладышей ), разъем — горизонтальный.Внутренняя поверхность втулки покрыта слоем антифрикционного сплава — баббита.В подшипниках скольжения применяют преимущественно кольцевую систему смазки.
vertu.jpg
В уплотнениях манжетного типа в качестве уплотняющего элемента используют кожаные, резиновые, пластмассовые и другие манжеты.Контакт уплотняющего элемента с валом делается либо при помощи тугих сил манжеты ( см.рис.100, и ), либо при помощи кольцевой пружины ( см.рис.100, к ), которая прижимает манжету к крутящемуся валу.Подобные манжетные уплотнения надежно действуют в самых трудных ситуациях и при любых смазках ( консистентных и слабых ).
4 Балансир.JPG
Наиболее распространенными являются следующие опорно - поворотные устройства, допускающие комбинированную ( и осевую, и лучевую ) нагрузку и выдерживающие опрокидывающий момент : С одним рядом шаров.С двумя рядами шариков – более высокого сечения.С перекрестными роликами ( подшипники с перекрестными роликами ) – для рослых нагрузок.С тремя рядами роликов – для весьма рослых нагрузок.Комбинированные - с одним или несколькими рядами шаров и роликов.
spravconstr.ru
Подшипники скольжения | Подшипники в России
Шарнирные подшипники скольжения — изделия, работающие по несколько иному принципу, чем привычные нам подшипники качения. Если в последних сила трения снижается за счет применения тел качения, которые имеют небольшую площадь контакта с дорожкой качения, то в шарнирных подшипниках это осуществляется за счет поверхностей скольжения сферической формы внутреннего и наружного кольца. Назначение подшипника скольжения — восприятие радиальных, осевых и комбинированных нагрузок в подвижных или неподвижных соединениях разнообразных машин и механизмов, при этом важнейшую роль при его функционировании играет смазка, которая не только обеспечивает минимальное трение, но и служит для отвода тепла от нагревающегося во время работы подшипника, прежде всего, если материалы подшипника скольжения — стали, а это большинство распространенных шарнирных подшипников. Чаще всего это стали ШХ-15, ШХ15СГ, нержавеющая 95Х18Ш и другие сплавы для подшипников скольжения.
Как правило, большинство потребителей имеют дело со сферическими шарнирными подшипниками, хотя есть и другие, например, линейные подшипники скольжения. В данном материале мы подробно рассмотрим именно сферические, поскольку исторически сложилось так, что они конструируются и выпускаются на тех же заводах, что и подшипники качения, да и купить их можно в тех же фирмах, где и подшипники качения.
Где купить
Данному вопросу на сайте посвящена отдельная статья — «Купить подшипники скольжения».
Конструкция подшипников скольжения
Подшипник скольжения состоит из корпуса (который может быть разъемным, т. н. «ломаным») и рабочего элемента — втулки, которая монтируется на вал. В последнее время выпускаются модификации с разборным наружным кольцом (корпусом), для облегчения монтажа (при этом отдельные части должны скрепляться проволокой на заводе). С различными особенностями конструкций (наличие канавок, отверстий для смазки, прорезей, разломов можно ознакомиться в статье «Виды подшипников скольжения«. Устройство подшипников скольжения постоянно совершенствуется, так, к примеру, если вы возьмете каталог подшипников скольжения, производимых во времена СССР, то не увидите там большинство из применяемых в настоящее время типов, и наоборот, большая часть представленных в нем модификаций уже снята с производства.
Смазка для подшипников скольжения
Как уже указывалось, смазка чрезвычайно важна для функционирования для этих изделий, ведь трение подшипников скольжения существенно выше, чем подшипников качения из-за большой площади контакта, она может быть жидкой (минеральные масла), пластичной (на основе лития, например, литол, или кальция, например, 158 Ф), твёрдой (графитовая, на основе дисульфида молибдена) игазообразной (различные инертные газы, азот). Чаще всего применяются жидкие и пластические смазки, причем предельное число оборотов у первых значительно выше.
Классификация подшипников скольжения
Изделия классифицируют по разным признакам. Традиционная классификация, принятая в нашей промышленности, описана в материале «Типы подшипников скольжения«, для импортных подшипников скольжения применяют более широкую, в первую очередь, на основании направления действующей нагрузки (аналогично подшипникам качения):
- радиальные
- упорные
- радиально-упорные;
Кроме того, данную группу можно разделить по тому, разъемны ли отдельные детали или нет (бывают также встроенные шарнирные подшипники), по возможности регулирования и т.д. В основном же, в нашей промышленности и транспорте применяются радиальные подшипники скольжения. Еще одной группой являются втулки скольжения.
Область применения подшипников скольжения
Радиальные подшипники скольжения массово применяются в отечественной промышленности, их устанавливают в различное производственное оборудование и транспортные средства. Наиболее часто они используются в грузовой технике и сельскохозяйственной технике. Размеры подшипников скольжения определяют узлы их эксплуатации, например, небольшие ШСП20 и ШСП30 применяются в комбайнах «Дон» и других (рулевая тяга, гидроцилиндры, шатуны), а крупные по размерам ШСЛ90, 100, 120 в поворотных цилиндрах и подвесках многотоннажных грузовиков и самосвалов. Применение подшипников скольжения особенно оправдано в узлах, где возникают тяжелые ударные или статические нагрузки, их можно эксплуатировать в экстремальных условиях, например, в воде, монтируются достаточно легко, однако у них есть и существенные недостатки. К последним можно отнести вес, невысокий КПД, большие расходы смазки.
ГОСТ на подшипники скольжения
Шарнирные подшипники выпускаются по ГОСТ, ТУ и ВНИПП. Основные ГОСТы, регламентирующие производство и эксплуатацию подшипников скольжения.
ГОСТ 7904-1-2001. Подшипники скольжения. Условные обозначения. Часть 1. Основные условные обозначения.
ГОСТ 7904-2-2001. Подшипники скольжения. Условные обозначения. Часть 2. Применение.
ГОСТ 4378-1-2001. Подшипники скольжения. Термины, определения и классификация. Часть 1. Конструкция, подшипниковые материалы и их свойства.
ГОСТ 4378-4-2001. Подшипники скольжения. Термины, определения и классификация. Часть 4. Расчетные параметры и их обозначения.
ГОСТ 18282-88. Подшипники скольжения машин. Термины и определения.
ГОСТ 28801-90. Подшипники скольжения. Кольца упорные. Типы, размеры и допуски.
ГОСТ 29201-91. Подшипники скольжения. Втулки из медных сплавов.
Подшипники скольжения каталог
Многие подшипники скольжения, производимые в нашей стране, уже вышли из употребления и производства, но разрабатываются новые, редкий каталог подшипников удовлетворяет реалиям сегодняшнего времени. Для получения подробной информации по подшипникам скольжения пользуйтесь поиском на нашем сайте (расположен в правом верхнем углу). Также вы можете скачать подробный каталог подшипников скольжения шведского производителя SKF. Это справочник на английском языке. Дополнительную информацию по другим маркам можно получить в разделе, посвященном импортным подшипникам (там же есть каталоги других производителей, цены на продукцию которых заметно ниже).
samip.ru