Газовый резак: виды, назначение и особенности эксплуатации. Приспособление для резки металла резаком
Газовый резак по металлу
Резка с помощью газа – операция не столь сложная, в сравнении с другими работами, поэтому для ее выполнения не нужны высокие квалификации. Для ее выполнения чаще других используется пропановый резак, поскольку газ имеет невысокую стоимость и весьма эффективен в работе. Этим оборудованием режут металлические листы, различной толщины, узлы и детали, вплоть до заготовок ювелирных украшений. Газовый резак по металлу широко используется, как на производстве, так и в быту. Оборудование действует за счет сгорания обрабатываемого материала, окислы выдуваются с помощью струи газа.
Устройство газового резака
Резак газовый представляет собой конструкцию из ствола и наконечника. Если наконечник имеет локальную конструкцию, то ствол состоит из следующих элементов:
- рукоять, обустроенная ниппелями, для соединения с газовым и кислородным рукавом;
- корпус с вентилями регуляции;
- смесительная камера;
- инжектор;
- трубы для подачи газовых сред.
Ствол крепится к корпусу с помощью накидной гайки.
Разновидности газовых резаков
Данное оборудование принято классифицировать по нескольким критериям.
По виду рабочего газа:
- ацетиленовый;
- пропановый;
- метановый и другие.
По технологии смешивания газов и кислорода:
- инжекторные;
- безинжекторные.
По назначению:
- универсальные;
- для работы под водой;
- для формирования отверстий;
- для разрезания толстых металлических листов и другие.
По видам резания:
- кислородно-флюсовый;
- разделительный;
- копьевый;
- поверхностный.
Преимущества газового оборудования для резки:
- резание в любом направлении металлических изделий и листов, толщиной до 30 см;
- компактный газовый резак прост в использовании;
- оборудование устойчиво;
- устройство имеет компактные размеры и небольшую массу, существуют мини модели;
- устройства прекрасно выдерживают удары обратного направления;
- невысокая стоимость готового оборудования позволяет иметь свой резак каждому домашнему мастеру;
- простая конструкция позволяет сделать резак своими руками;
- простая настройка интенсивности работы горелки.
Это оборудование имеет набор характеристик, которые обеспечивают продолжительную и надежную эксплуатацию, в том числе легкая заменимость всех элементов. Допустима установка аналоговых запасных частей. Газовый резак мини
Мини газовый резак по металлу представляет собой модель портативного автогена или зажигалки с дюзой резака. Работает устройство по тождественному принципу. После нажатия на клапан газ протекает через маленькое отверстие и попадает в дюзу уже с ускорением. Струя поджигается пьезоэлементом, образуется пламя, которое приобретает форму конуса. Портативный газовый резак нагревается незначительно, ее можно спокойно держать голой рукой. Газ довольно быстро заканчивается, поскольку емкость для него – небольшая. Зарядка портативного газового резака выполняется от цангового баллона.
Газовый резак своими руками
Переносной газовый резак имеет простую конструкцию, что позволяет мастерам делать их своими руками. Для работы вам понадобятся:
- обычная капельница, которую можно приобрести в любой аптеке;
- игра для накачивания спортивного мяча, оптимально – футбольного, будет использована в качестве наконечника;
- бутылка из пластика;
- баллон для газа можно демонтировать из зажигалки;
- проволока из меди;
- термопистолет;
- набор инструментов.
Процесс изготовления резака своими руками выполняется последовательно:
- на игле от мяча нужно сделать напильником надрез на расстоянии 1,5-2 см от конца;
- у иглы от капельницы, которая будет подавать воздух, нужно отрезать острый конец, а затем на расстоянии 2 см от края, загнуть под углом в 45 градусов и вставить в надрез, сделанный на игле для мяча;
- две иглы фиксируют между собой с помощью проволоки, паяльника и олова;
- капельницу надевают на концы иголок, при этом демонтировать колесики не нужно, впоследствии они станут регулировочными вентилями;
- затем нужно сделать сопло резака своими руками, здесь придется немного поусердствовать, поскольку диаметр капельницы меньше, чем у этого элемента;
- далее нужно сделать своими руками баллон для воздуха из 1,5-2-литровой пластиковой бутылки, для этого на ее дне нужно сделать отверстие для соска автошины, который закрепляется гайкой;
- герметичность можно обеспечить любым клейким составом, выдерживающим высокие температуры;
- в верхней части бутылки делается отверстие под капельницу, куда капельница и устанавливается – это система подачи сжатого воздуха;
- аналогично устанавливается емкость на иглу для накачки мяча – это система подачи газа;
- ограничители капельницы приоткрываются, поджигается выходящий газ, пламя нужно отрегулировать до голубого цвета, что обозначает температурный режим в 1,5 тысячи градусов;
- таким пламенем можно резать метал, толщиной в 1 мм.
Не стоит думать, что данная конструкция – одноразовая. При правильном уходе она прослужит вам годы.
Как настроить газовый резак
Данное оборудование собирается и настраивается легко, но если вы новичок, лучше проконсультироваться со специалистами, например, на форумах. Основное – это соблюдать технику безопасности. Обычный резак собирается следующим образом:
- Сначала устанавливаются редукторы. Синий – для кислородного баллона. Здесь нужно осмотреть вентиль на предмет масленых следов, наличие которых может привести к взрыву. Красный редуктор предназначен для баллона с газом. Обязательно проверьте состояние прокладок.
- Проверьте штуцер на целостность и отсутствие дефектов, при необходимости его можно поправить напильником.
- Подобрать трубки согласно резьбе, также осмотреть на предмет дефектов. Они соединяются с редукторами посредством хомутов. Следует помнить, что кислородный шланг нельзя продувать газом, и – наоборот. Также запрещено менять их.
- На штуцер нужно установить клапан удара.
- Если резак инжекторный, нужно проверить инжекцию, это можно сделать пальцем, если он притягивается на штуцере – все в порядке.
- Далее соединяют трубку с газом. При работе с пропаном устанавливается давление 0,5. Соотношение кислорода рассчитывается, как 1/10.
- Приоткрывается кислород и пропан, смесь газов поджигается.
- Теперь нужно поднести пламя к металлу и добавить кислород, до момента, когда появляются коронки.
При завершении работы вентили нужно закрыть. Если в процессе резки пламя затухнет, нужно отключить приток пропана, а подачу кислорода увеличить на несколько секунд. Поскольку, если перекрыть кислород – создается взрывоопасная ситуация.
Поделись с друзьями
0
0
0
0
svarkalegko.com
Газовый резак: виды, назначение и особенности
Основным назначением аппаратов для газового раскроя металла является смешивание горючих веществ (жидкостей или газов) с кислородом для получения струи высокотемпературного пламени. В отличие от сварочной горелки, газовый резак снабжен трубкой и запорно-регулирующей арматурой для подачи кислорода режущей струи, а также имеет особое устройство головки.
Классификация аппаратов
Газовые резаки имеют достаточно много видов и классифицируются по таким признакам:
- тип резки: поверхностные и разделительные;
- назначение: ручные и механизированные;
- вид горючего: ацетиленовые, пропановые, метановые, керосиновые;
- конструкция: наличие или отсутствие инжектора;
- кислородная подача: низкого и высокого давления;
- тип мундштука: многосопловые и щелевые;
- мощность: малая (< 10 см разрезаемого металла), средняя (< 20 см) и высокая (> 20 см).
Сегодня разными производителями выпускается более десятка модификаций подобного оборудования, однако конструктивно они мало чем отличаются между собой. Для таких устройств характерно наличие ручки с вентилями для изменения подачи пламеобразующих газов, и наконечника с головкой, в которой происходит образование пламени.
На рисунке представлен пример газового резака фирмы KRASS
Внешне резак и сварочная горелка имеют много общего. Как отмечалось выше, основное отличие заключается в отсутствии у последней подачи кислорода режущей струи и другое устройство головки. Больше о горелках можно прочитать в статье: горелка газовоздушная для газопламенной обработки материалов.
Газовый резак инжекторного типа
Инжекторные устройства позволяют использовать горючий газ низкого, среднего и высокого давления. Проходя через инжектор, подогревающий кислород, реализует в смесительной камере эффект разрежения, вследствие чего осуществляется подсос газа. Далее смесь поступает в головку, а из нее подается в шлицевые каналы внутреннего мундштука.
Комплектация аппарата может состоять из 6 внутренних мундштуков (№№ 0-5), которые обеспечивают раскрой металла толщиной до 20 см при работе с ацетиленом, и 7 внутренних мундштуков (№№ 0-6) для толщин 0,3-30 см при работе с пропаном-бутаном. Данное оборудование также может комплектоваться разными модификациями наружных мундштуков (№1 для диапазона толщин 0,3-10 см; №2 для 10-30 см).
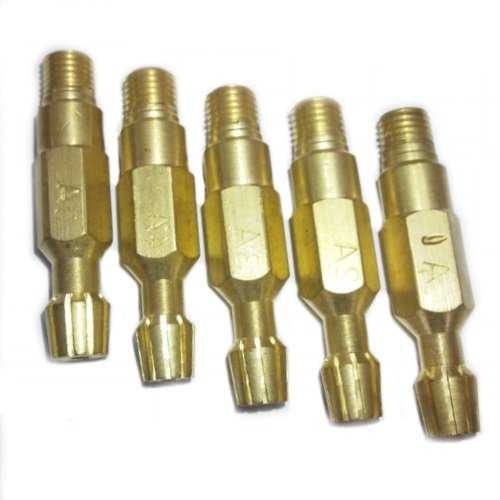
На рисунке представлены внутренние мундштуки
Для обработки углеродистых и низкоуглеродистых сталей толщиной до 10 см применяется инжекторный газовый резак Р3П-100 «Krass», который выпускается как для работы с ацетиленом, так и с пропаном-бутаном. Для более толстой стали (до 30 см) используется P3П-300 «Krass», работающий с ацетиленом, пропаном и метаном. Кстати, статьи о технических газах Вы можете прочитать в этом разделе.
Внутрисопловое смешение
В устройствах с внутрисопловым смешением смесь образуется в шлицевых каналах между наружной гильзой и внутренним мундштуком. Подача режущего кислорода осуществляется рычажным клапаном, а подогревающего и горючего газа – регуляторами, которые установлены на рукоятке.
Данное оборудование выпускается в 3-х исполнениях: для работы с ацетиленом, пропаном и природным газом. Поскольку газ смешивается не у рукоятки, как в инжекторных устройствах, а в головке, такие аппараты имеют повышенный уровень безопасности. Вместе с тем, подобный принцип действия требует более сложной конструкции, что приводит к увеличению стоимости приспособления. Также для стабильной работы требуется повышенное давление горючего газа – от 20 кПа.
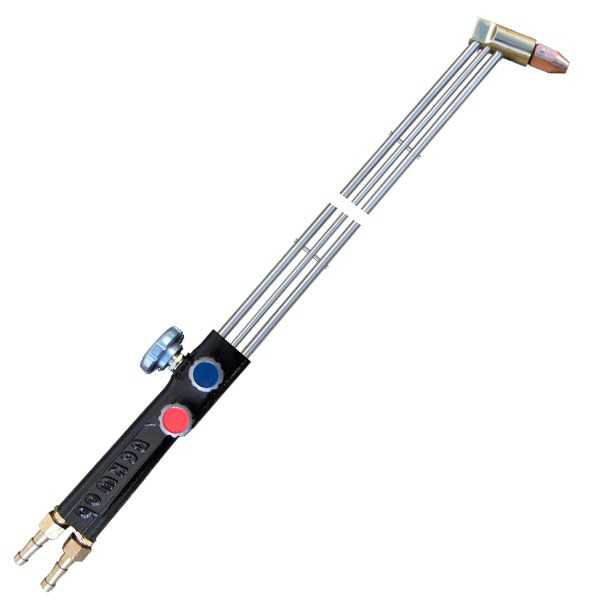
Устройства с внутрисопловым смешением
Керосино-кислородные резаки
Оборудование для резки металла, работающее на керосине, обладает конструктивными отличиями от газовых аппаратов, поскольку для получения пламени необходимо превращение жидкости в газообразное состояние. Данный процесс осуществляется в испарителе, подогрев керосина в котором реализуется с помощью специального подогревающего сопла.
Горючее подается из бачка по маслобензостойкому шлангу под давлением 30 кПа. Емкость снабжена предохранительным клапаном и ручным насосом, и с учетом конструкции позволяет залить до 8 л горючего. Устройство такого типа имеет востребованность при работе в полевых условиях.
Что нужно знать при работе с резаками
Прежде нужно знать принцип работы и классификацию этих устройств. Для этого можете посмотреть видео ниже:
- Каждый маховик вентиля имеет маркировку газа, подачу которого он регулирует.
- Стрелками на вентиле указывается направление при открытии и закрытии («О» — открытие, «З» — закрытие).
- На сменном мундштуке указывается индекс газа («А» — ацетилен, «П» — пропан, «М» — метан).
- Гайка кислородного штуцера имеет правую резьбу, а горючего газа – левую.
- Детали, соприкасающиеся с ацетиленом до камеры смешения, не изготавливаются из меди и медесодержащих сплавов (>65%).
Также советуем посмотреть видео о том, как выбрать данное устройство:
В компании «Промтехгаз» можно приобрести качественные резаки фирмы «Krass», которые осуществляют газовую резку металла (до 30 см), а также заправить баллон пропаном по оптимальной цене.
xn--80affkvlgiu5a.xn--p1ai
как выбрать газовый резак для ручной кислородной резки, цена
Ручная газовая или кислородная резка металлов пользуется огромной популярностью по многим причинам. Этот способ металлообработки позволяет в первую очередь быстро и достаточно качественно (при наличии определённого опыта) выполнить раскрой без нарушения структуры материала по краям реза.
Кроме того, цена резки металла резаком вручную всегда невысока, работать можно даже с металлами большой толщины, а само место работы можно организовать практически в любом месте: на складе, в гараже, в цеху предприятия, на улице. Сам принцип резки заключается в том, что в струе чистого подаваемого под давлением кислорода металл сгорает и этой же струёй из зоны реза из рабочей зоны выдувом удаляются все продукты окисления и шлаки.
Оборудование для резки металла резаком
- Резак – газовая горелка со специальными каналами, через которые подводится горючая смесь. По своей конструкции все подобные устройства очень похожи, разница может состоять только в размерах проходных каналов и мундштука.
- Газовые баллоны (чаще всего используется ацетилен и кислород, также может быть использован природный газ, керосин, пропан).
- Смеситель горючего газа и окислителя.
- Регулятор давления.
- Шланги.
Резаки для ручной резки металла кислородом при этом основа всего комплекта оборудования.
Они классифицируются сразу по нескольким признакам:
1. По виду резки (она может быть поверхностной, кислородно-фосфорной, разделительной).
2. По виду горючего:
- Кислородный – инжекторный аппарат, образование струи в котором происходит за счёт кислорода (благодаря пламени только 15 %),
- Ацетиленовый аппарат для газокислородной резки – устройство, работающее при подаче по отдельным линиям ацетилена и кислорода (за счёт высокой температуры горения газа таким агрегатом можно выполнять резку металла большой толщины),
- Пропановый позволяет работать как с чёрными, так и с цветными металлами, отличается высокой производительностью, безопасностью и надёжностью в работе,
- Керосиновый аппарат способен к резке углеродистой стали до 200 мм;
3. По принципу работы:
- Безинжекторные.
- Инжекторные (последние создают максимальную скорость кислородной струи, что позволяет существенно повысить качество полученной горючей смеси).
Работа такого резака состоит из нескольких этапов: смешивания паров горючего газа и кислорода, образования пламени, которое необходимо для подогрева металла до нужной температуры, подачи кислорода под давлением в зону резки.
Как выбрать резак для кислородной резки металла?
В зависимости от вида планируемых работ можно выбрать резак Р1 для работы с металлом толщиной до 100 мм, Р2 при резке металла резаком толщиной до 200 мм или Р3, соответственно, для 300 мм материала. Для того, чтобы определить качество предлагаемого производителем устройства, в первую очередь обращают внимание на соответствие исполнения мундштука и других деталей установленным нормам.
Материалы изготовления основных деталей резака
Наружный и внутренний мундштук должны быть выполнены из хромистой бронзы или меди. Нередко в качестве материала для изготовления этой детали используется латунь, но в этом случае стоит иметь в виду, что срок службы такого элемента конструкции сразу сократится в 3-4 раза. Латунь в качестве материала для внутреннего мундштука может быть использована только в том случае, если планируется работа на метановых или пропан-бутановых смесях (температура горения в этом случае будет почти на 1000 ˚С ниже в сравнении с ацетиленом).
Сам газовый резак для резки металла может быть изготовлен из меди, латуни или нержавеющей стали. Окраска поверхности аппарата не допускается в принципе из соображений безопасности: под таким покрытием могут быть скрыты дефекты самого металла, пайки. При этом никакого функционального значения или защитных свойств у такого покрытия нет. Также рекомендуется выбирать оборудование со шпинделем из нержавеющей стали. Широко распространённая латунь для этого элемента не подходит, так как срок его службы при этом составит не более 1000 циклов (против 45 000 циклов для нержавейки).
Как выгодно вложить средства — особенности выбора резака
Резаки для кислородной резки металла обязательно должны иметь разъёмные соединения, для того чтобы пользователь имел возможность заменить изношенные детали, удалить засоры. В некоторых случаях предлагаются моноблочные аппараты, которые всегда неудобны в обслуживании и практически не поддаются ремонту.
Также очень важным моментом является то, что резка металла резаком всегда сопровождается необходимостью покупки газа. Для того, чтобы изначально исключить вероятность перерасхода материала (и соответственно, своих средств) стоит обратить внимание на соответствие нормы расхода технологического газа, указанного в паспорте аппарата требованиям ГОСТ 5191-79.
Согласно нормативным параметрам, норма расхода газа и кислорода зависит от номера мундштука и максимальной толщины металла, с которыми они могут работать.
На любой газовый резак для резки металла в продаже должны иметься запасные части, которые можно будет купить при необходимости замены. Важно сразу уточнить этот момент, чтобы не купить одноразовый аппарат. Даже если мундштук (расходный материал для любого резака) при необходимости можно изготовить самостоятельно, то с другими элементами конструкции это сделать не удастся. А одноразовый инструмент не самое лучшее вложение средств.
steelguide.ru
технология, необходимое оборудование, техника безопасности
Кислородную резку металлов (в литературе можно встретить термин «автогенная резка») активно применяют в промышленности для нарезки листового материала из стали и иных сплавов на заготовки необходимой длины. Также данная технология применяется при проведении ряда ремонтных работ и работ по демонтажу конструкций. Популярность ее обусловлена сравнительной простотой и низкой стоимостью оборудования, а также высокой степенью безопасности. Статья содержит сведения о самой технологии, о необходимом оборудовании и основах техники безопасности при проведении кислородной резки металлов и других материалов.
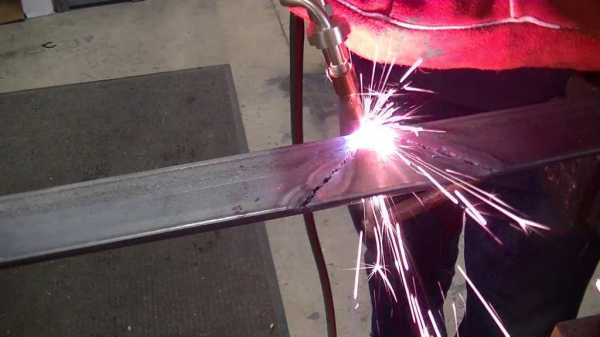
Основы технологии
Перед началом резания металл рекомендуется нагреть пламенем горелки. Это касается лишь материалов с большим сечением. Упомянутое пламя появляется вследствие реакции кислорода с газом. Если пренебречь этой рекомендацией, то металл неизбежно поведет, произойдет коробление. Впрочем, если геометрическая форма нарезаемых кусков не важна, например, при осуществлении работ по демонтажу сооружений из строительных сталей, а также при нарезании тонкостенных листов, допускается газовая сварка и кислородная резка металла без предварительного подогрева изделий.
Высокие температуры в зоне резания достигаются путем сжигания кислорода высокой степени очистки из баллона. В металлических резервуарах под очень высоким давлением содержится от 99 до 99,8 % кислорода. Если для подогрева используется кислород обычной чистоты (грубо говоря, атмосферный воздух), то для эффективной кислородной резки металла нужен именно кислород высокой чистоты.
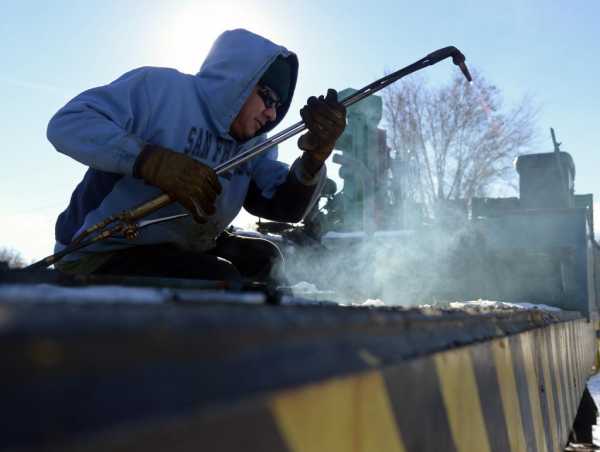
Подготовка поверхности
Если стоит задача распилить на транспортируемые куски крупный объект, который подлежит утилизации, то подготовкой поверхности можно и не заниматься. Резак справится с этой задачей в кратчайшие сроки. Другое дело – производство новых изделий. В этом случае важно получить качественную линию разреза, чистую от окалины и других нежелательных включений. Кислородной резке металла предшествует тщательная очистка материала.
Существует большое количество методов устранения загрязнений. Наиболее популярные из них – прогрев поверхности газовым пламенем и механическая очистка. Первый способ наиболее прост. Он позволяет эффективно устранять окалину – злейшего врага газосварщика. Сущность его заключается в прогреве поверхности металла до критических температур. Второй метод является более затратным и требует наличия специального оборудования (пескоструйные машины, скребки, щетки и так далее) и квалифицированного рабочего персонала.
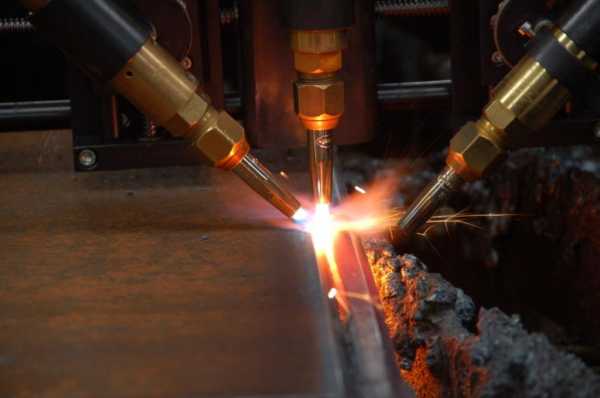
Требования к материалам
Кислородно-флюсовой резке металлов могут подвергаться далеко не все марки стали и сплавы. Одними из главных условий являются температура плавления и температура воспламенения. Для нормального протекания процесса первый показатель должен быть значительно выше второго. Понятно почему: в противном случае материал будет оплавляться, а не сгорать, что приведет к образованию потеков. Линия реза будет иметь неаккуратный вид, зачастую это делает невозможной дальнейшую обработку детали на механообрабатывающих станках в результате смещения баз. Кроме того, такой слой металла может иметь плохие механические и физические свойства.
Определенные элементы, добавляемые в состав сталей в качестве примесей, могут оказывать отрицательное воздействие на процесс кислородно-пропановой резки металла. Так наиболее обрабатываемыми считаются стали, содержание углерода в которых не превышает 0,3 %. Скорость резки при увеличении содержания углерода не уменьшается, однако сталь становится склонной к перегреву, закалке поверхностного слоя и образованию закалочных трещин, которые могут послужить концентраторами напряжений и привести к хрупкому разрушению всей заготовки.
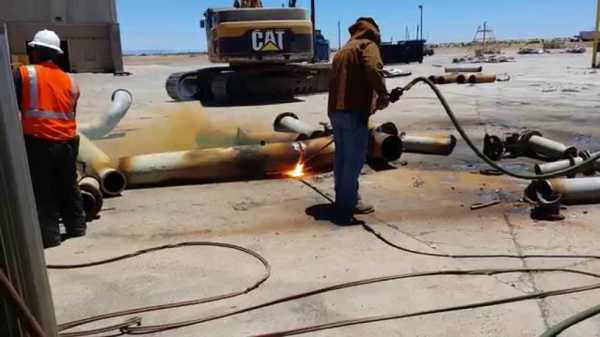
Ручная резка
Газовая кислородная резка металла, в зависимости от степени автоматизации и механизации, подразделяется на механизированную и ручную.
Ручную сварку целесообразно использовать в условиях мелкосерийного и единичного производства, а также при проведении работ по демонтажу конструкций и сооружений. Идеально подходит для вырезания заготовок из труб, устранения литников с литых изделий и так далее.
Оборудование кислородной резки металлов и сплавов отличается высокой мобильностью, простотой в эксплуатации и надежностью. Благодаря этим качествам эта технология является наиболее распространенной как на промышленных предприятиях, так и в ремонтных организациях.
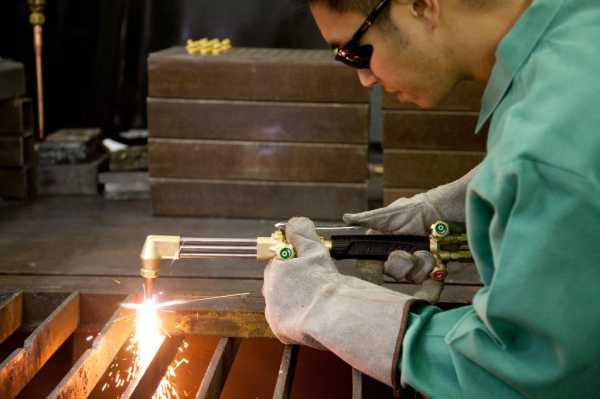
Механизация процесса
За последние десятилетия робототехника развивалась очень стремительно. Сегодня роботы применяются практически повсеместно. И кислородно-дуговая резка металлов – не исключение. В настоящее время оборудованием для резки с числовым программным управлением уже никого не удивишь. Эти аппараты могут оснащаться несколькими кислородными резаками для резки металла, что значительно повышает их и без того высокую производительность. Все ведущие зарубежные машиностроительные холдинги и компании уже давно активно внедряют подобную технику в свои производственные цепочки, стараются не отставать и отечественные компании. Уровень механизации сварочных работ в среднем составляет порядка 80 %.
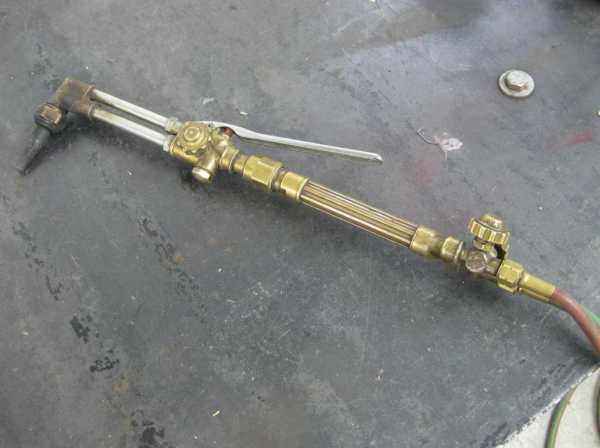
Сущность кислородно-флюсовой резки металла
Традиционная резка подходит далеко не для всех материалов. Например, сталь, легированная хромом с никелем, плохо поддается резке. Аналогичная проблема возникает и при нарезании цветных металлов и чугунов.
Тогда на выручку приходит кислородно-флюсовая технология. Сущность ее заключается в следующем. В зону резания подается порошок флюса. Это вещество в процессе резания воспламеняется и сгорает, выделяя при этом большое количество тепла, что делает возможным оплавление тугоплавких карбидов, боридов и оксидов металлов.
Оборудование для кислородно-флюсовой резки
Можно сказать, что для этого вида резки металла используется обычное стандартное оборудование, дополнительно оснащенное устройством для подачи флюса (так называемый флюсопитатель и кислородный резак для резки металла с подачей флюса). Самыми распространенными установками такого типа являются приборы конструкции научно-исследовательского института Автогенмаш «УРХС». Это оборудование предназначается для резки сталей с высоким содержанием хрома и других легирующих элементов.
Такое оборудование использовать и для механизированной резки, оснастив станок устройством подачи флюса.
Приемы кислородно-флюсовой резки
Техника не отличается от уже ставших традиционными приемов классической кислородной резки. Сам процесс может осуществляться как руками, так и механизированным путем с использованием вспомогательных средств, роботов и приспособлений. Она также может быть как разделительной, так и поверхностной. Рекомендуется применять для раскроя и нарезания сталей с высоким содержанием хрома и никеля (то есть для тугоплавких сталей).
Особенности кислородно-флюсовой резки чугуна
При сгорании флюс выделяет много тепла. Настолько много, что происходит так называемый отбел чугуна. Сущность этого явления заключается в том, что углерод переходит из свободного состояние в связанное. Иными словами, атомы углерода на определенном участке образуют с атомами металла химическое соединение. Это сопровождается ухудшением механическим свойств чугуна (увеличивается твердость, он становится более хрупким). В результате ускоренного прогрева и охлаждения, на поверхности появляются трещины, которые могут вызвать разрушение изделия.
Решить проблему позволяет предварительный прогрев металла и регулирование скорости его охлаждения. Справиться с такими задачами под силу лишь рабочему с высокой квалификацией и большим опытом в проведении подобных работ.
Особенности кислородно-флюсовой резки цветных металлов и сплавов
Как и чугун, медь необходимо подогревать перед тем, как начать ее резать. Нагрев осуществляется до температуры 800–900 градусов по Цельсию. Медь обладает высокой теплопроводностью, поэтому резка без предварительного подогрева приведет к значительным короблениям, пространственным искажениям и браку.
Сплавы на основе меди с другими элементами (латунь, бронза и так далее) также необходимо подогревать. Однако температура предварительного нагрева не должна превышать 500 градусов Цельсия.
Преимущества и минусы технологии кислородной резки
По сравнению с другими, альтернативными методами раскроя листового материала разных марок сталей, данная технология отлично подходит для разрезания по кривым линиям, для вырезания отверстий большого диаметра. Также этот метод позволяет получать глухие отверстия.
Вторым, и весьма значительным, преимуществом является простота в использовании оборудования. Газовый резак имеет небольшую массу, благодаря чему сварщик может длительное время работать с ним, при этом не уставая. Это положительно сказывается на производительности.
Газ является сравнительно доступным и дешевым видом топлива. И это третье преимущество.
Весьма существенны недостатком технологии является взрывоопасность используемых веществ. Поэтому не допускается нарушения технологической дисциплины. Игнорирование правил техники безопасности может привести к тяжелым последствиям.
Правила эксплуатации кислородного редуктора для резки металла
Перед подключением редуктора рабочий обязан убедиться в отсутствии загрязнений на резьбовых поверхностях. При наличии таковых необходимо обработать загрязненные поверхности керосином или растворителем. Лишь после продувки системы и удаления всех посторонних частиц и элементов, которые могут попасть в редуктор и нарушить его работу, можно накидывать и закреплять гайку на редуктор.
Таким же образом происходит установка и других редукторов.
Пуск газов осуществляется плавным открытием вентиля баллона. Если никаких отклонений от работы не наблюдается, вентиль можно открывать полностью. Если редуктор начнет греться, аномально шуметь, необходимо немедленно перекрыть маховик кислородного баллона для резки металла.
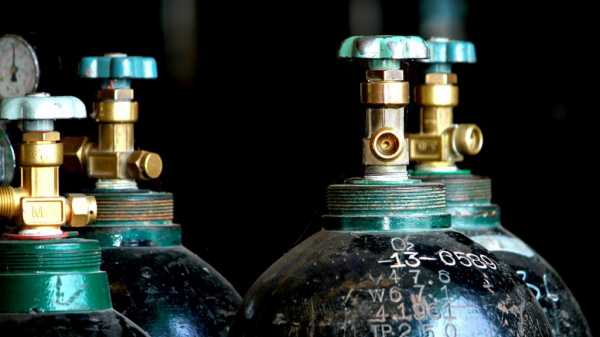
Техника безопасности при проведении работ
После подготовительных работ необходимо убедиться в отсутствии утечек газов. Это может быть очень опасно. Лишь после этого можно зажечь резак и отрегулировать пламя.
Если необходимо сделать небольшую паузу в работе (не более двух-трех минут), то достаточно лишь перекрыть вентиль резака. В том случае, если работы прекращаются на длительное время, необходимо перекрыть редуктор и вентиль газового баллона.
Ко всем работам по кислородной резке металла допускаются лишь рабочие, прошедшие все необходимые инструктажи.
Запрещено проводить любые работы вблизи от взрывоопасных резервуаров и легковоспламеняющихся материалов. Если работы выполняются в небольших закрытых пространствах, то рабочие должны регулярно отдыхать и дышать свежим воздухом.
Сварочные работы на производстве, которые выполняются систематически (не временного характера) должны проводиться в специально оборудованных помещениях. При этом площадь одного рабочего места – не менее четырех метров квадратных. Проходы между рабочими местами должны быть не менее 0,8 метра.
Помещения должны быть оборудованы мощной вытяжкой вредных веществ. Ее производительность должна составлять 2500–3000 м3 на 1 м3 сжигаемого газа.
В том случае, если в одном помещении (цехе) оборудовано более десяти рабочих мест сварщиков, газ должен поступать на них не из баллонов, а централизованно из газораспределительной станции. Допускается подача газов из действующих газопроводов.
Баллоны с рабочим газом допускается транспортировать лишь с защитными колпаками. Они предотвратят вентиль от повреждений и загрязнений. Запрещено транспортировать баллоны на большие расстояния руками. Для этих целей нужно применять специальные приспособления и тележки. Удары баллонов о землю или друг о друга недопустимы.
В кислородном баллоне для резки металла при нарушении технологии и порядка работы может образоваться взрывоопасная смесь газа с кислородом. Поэтому необходимо с ответственностью подходить к регулировке редукторов.
fb.ru
Инструменты для резки металла: какое бывает оборудование
Монтажные и отделочные работы нередко сопровождаются дополнительными операциями, связанными с подготовкой тех или иных материалов. И если пластик с древесиной, к примеру, легко подкорректировать обычными инструментами плотника за пару минут, то металлические заготовки в силу жесткости структуры требуют куда больше усилий. Конечно, для работы с профилем и листовыми изделиями не обязательно обращаться к профессиональной технике. Но следует изначально понимать нюансы использования конкретного инструмента для резки металла, чтобы на выходе получилась заготовка, соответствующая ожиданиям.
Холодная и горячая резка – в чем отличия?
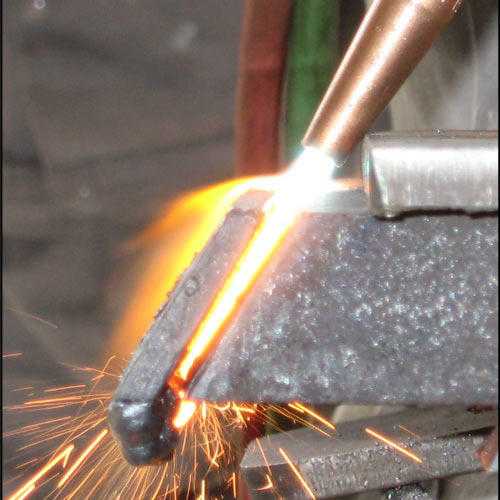
На базовом уровне следует разделить два принципиально разных подхода к обработке металла. Это холодная и горячая резка. В чем заключается разница? В случае с холодной обработкой целевая заготовка не подвергается изменению структуры для облегчения дальнейшего физического воздействия на нее. Как правило, это механические способы резки, при которых функциональный орган (зубец, резчик, коронка) должен быть выполнен из более стойкого материала, чем рабочая заготовка. Горячие способы обработки обычно предполагают термическое воздействие на материал до состояния плавления. Какие инструменты применяются при резке металла таким способом? В большинстве случаев используют полноформатные станки с автогеном, но и для бытового применения выпускаются технические средства горячей обработки. В эту группу входят сварочные аппараты, а последнее время становятся все доступнее и лазерные устройства для резки.
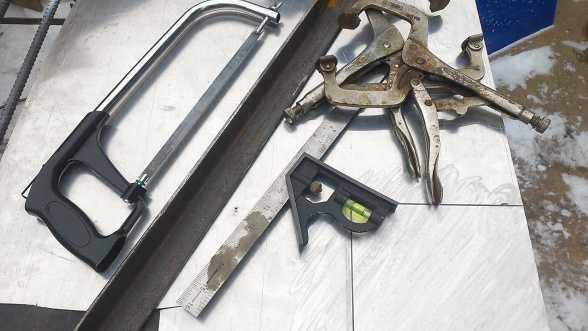
В этой категории можно выделить ручные и станочные агрегаты, предназначенные для раскроя металлических листов. Твердотельные заготовки толщиной более 20-25 мм ручными инструментами обычно не режутся. К ним относятся ножницы и ножовки по металлу. Что касается станочного оборудования, то его представляют стационарные пилы, ленточные обрабатывающие станки и шлифовальные машины. Причем сама по себе операция резки в станочном оборудовании редко представлена в единственном числе. Как правило, она является базовой, но ее также дополняют функции сверления, расточки, торцевания и т. д. Несмотря на очевидное превосходство платформенных мощных агрегатов, ручной инструмент для резки металла может потребоваться в решении несложных и деликатных операций. Например, если в удалении от розетки на стройплощадке нужно будет аккуратно подрезать край металлического листа. Использовать для этой задачи крупногабаритную пилу на станине нецелесообразно.
Классификация ножниц по металлу
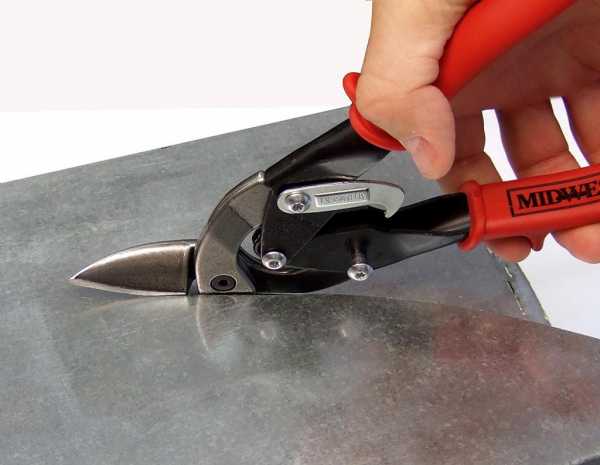
Данный инструмент тоже бывает разным. Простейшие конструкции позволяют осуществлять раскрой тонкого листового металла, используя ручное усилие. В отличие от обычных ножниц, их режущие части выполняются из высокопрочной инструментальной стали. Рукоятки, в свою очередь, имеют пластиковые накладки с ребристой поверхностью для более цепкого хвата. Для более ответственных операций применяют электрический инструмент для резки металла с силовым приводом. Ножничный механизм представлен насадкой с небольшим вращающимся роликом. В действие его приводит двигатель мощностью до 500 Вт в среднем. К преимуществам этого инструмента относится не только высокая производительность, но и точность. Оператор может резать листы толщиной порядка 1,5 мм, оставляя ровные края.
Резка металла ножовкой
Классическая пила с тонким и узким полотном по-прежнему сохраняет актуальность. На фоне мощного электроинструмента такая ножовка выигрывает низким ценником, простой конструкцией и возможностью получения аккуратного распила. В современных моделях для полотна используется закаленная или инструментальная сталь, позволяющая резать трубы, куски арматуры и профильные заготовки. Причем большинство ножовок имеют унифицированные механизмы фиксации пилки, поэтому сохраняется возможность применения разных по формату полотен с ориентацией на особенности рабочего материала. Основу же данного инструмента для резки металла нужно подбирать исходя из ее функциональности. Учитывать следует силу натяжения и диапазон настройки по длине.
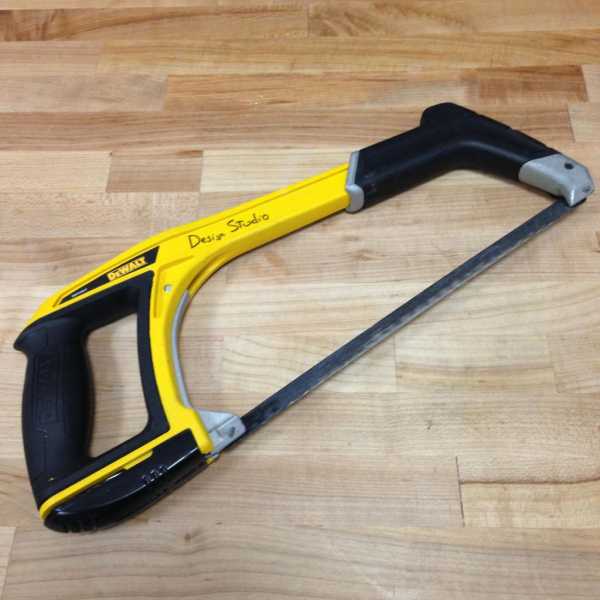
Особенности плазменной резки
Обработку такого типа реализуют специальные модели сварочных аппаратов. В качестве целевого материала применяются разные металлы от мягкого алюминия до титана и углеродистых сплавов. Но использовать данный метод рекомендуется только при наличии как минимум базовых навыков сварочных работ. Плазмотрон – это электрический инструмент для резки металла, в котором важную роль играет сила тока. В ходе подготовки рассчитывается ее потенциал, приходящийся на 1 мм заготовки. Причем для разных видов металла эта величина будет разной. Так, сталь и чугун режется при 4 А, а цветные сплавы рекомендуется обрабатывать с настройкой под 6 А.
Особенно новичкам необходимо продумать и вопросы безопасности в ходе рабочего процесса. Защита обеспечивается не только от электрического тока, но и от температурного воздействия с ультрафиолетовым излучением. Поэтому с данным инструментом для резки металла рекомендуется работать в специальной экипировке, дополненной щитком сварщика. На ногах тоже должны быть соответствующие штаны с обувью на случай неосторожного обращения с расплавом.
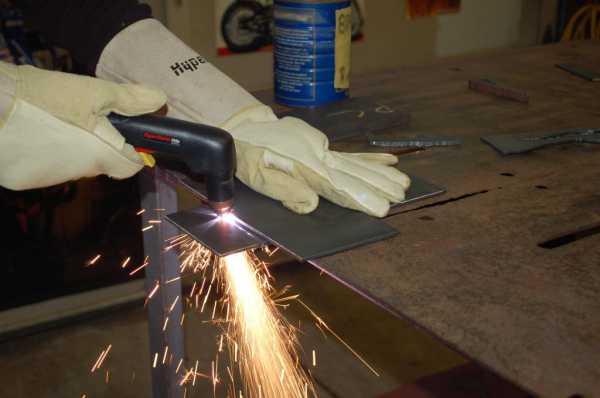
Ленточные станки для резки металла
Для обработки металлических заготовок повышенной твердости используют мощное станочное оборудование. Ленточная пила в этом классе – одно из самых эффективных решений, так как зубья пильных полотен выигрывают в показателях прочности даже у дисков болгарки. Также конструкция оборудования позволяет справляться с крупными заготовками толщиной более 100 мм. Например, стержень диаметром в 100 мм средняя по производительности машина обработает со скоростью 50-70 см2/мин. Выгодна резка металла механизированным инструментом данного типа и в плане экономии целевого материала. Толщина ленты составляет всего 1,3 мм в среднем, поэтому расход стружки будет небольшим. Если сравнивать экономию в отходах с ручными способами резки, то разница достигнет 3-4 раза.
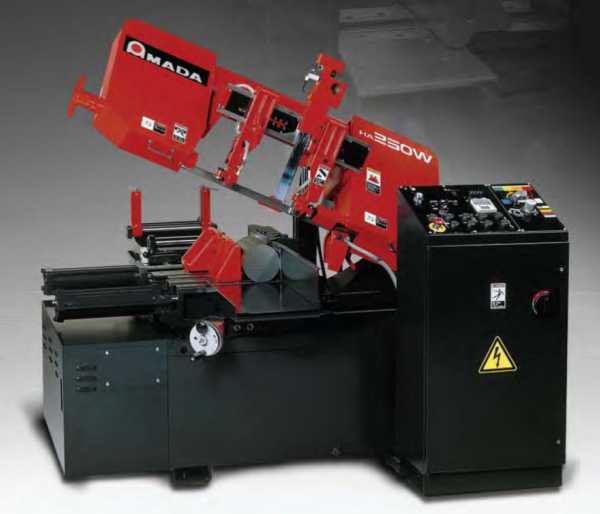
Гидроабразивная резка
Это высокотехнологичное оборудование, которое преимущественно используют на крупных металлообрабатывающих предприятиях. Особенности гидроабразивных станков заключаются в принципе работы. Резка выполняется не механическими элементами, и не тепловым воздействием, а смесью абразива и воды. Через специальное сопло на целевую область подается струя под большим давлением. На подходе канала к поверхности заготовки к нему подключается линия подачи микрочастиц песка и металла. В итоге направление гидроабразивной струи осуществляет раскрой с высокой степенью точности. Размер самих частиц может составлять несколько микрон, а толщина заготовки достигает 200 мм. К слову, ручные инструменты, применяемые при резке металла, ориентируются в основном на тонколистный прокат. И даже повышение мощности с изменением конструкции оборудования с целью приема больших заготовок вовсе не гарантирует качество раскроя. В свою очередь, гидроабразивные станки с ЧПУ реализуют операцию под контролем программной аппаратуры с комплексной задачей параметров резки.
Заключение
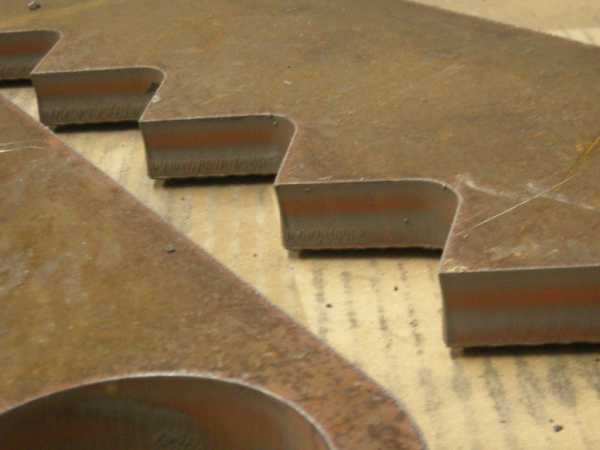
Выбор подходящего способа обработки металла зависит от конкретных целей. В некоторых случаях важна будет скорость резки материала в больших объемах и без высоких требований к качеству. Для таких задач используют механические станки с подходящей под формат заготовки конструкцией. Ручной инструмент для резки листового металла чаще применяют в бытовых условиях. Таким образом могут подготавливаться заготовки для кровли, обшивки хозяйственных построек и т.д. Самые же технологически и функционально продвинутые агрегаты демонстрируют принципиально другие подходы к решению подобных задач. Это в первую очередь гидроабразивное и плазменное оборудование, сочетающее в себе такие качества, как высокая производительность, точность и экономность.
fb.ru
Инструменты для газовой резки (резаки)
Газовый резак УРШ-66 разработан и внедрен новатором Г. Г. Шеффером.Отличительной особенностью резака УРШ-66 является раздельная подача горючего газа, режущего и подогревающего кислорода и размещение смесительной камеры и инжектора в головке резака. Кроме того, внутренний канал инжектора выполнен конусным с уменьшенным на выходе отверстием. Конструкция резака экономична и исключает возможность обратных ударов пламени (воспламенение горючей смеси в каналах резака).
’ Через рукоятку 1 резака (рис. 61) пропущены трубка подачи кислорода 3 и трубка подачи горючего газа 13. Трубки впаяны в корпус распределительного узла 12. Подача горючего газа включается вентилем 2. По трубке 11 газ попадает в смесительную камеру головки 8. Кислород поступает в камеру распределительного узла 12 и оттуда при открытом вентиле 4 по трубке 10 через инжектор попадает в смесительную камеру. Этот кислород, смешиваясь с горючим газом, проходит через наружный мундштук 9 и образует подогревающее пламя.
При открывании вентиля 5 кислород начинает поступать через трубку 6, головку 8 и внутренний мундштук в зону реза, образуя режущую струю. В резаке возможны замена, регулировка и прочистка инжектора, которые осуществляются через отверстие в головке, закрытое винтом 7.
Рис. 61. Газовый резак УРИР66.
Резак позволяет производить резку стальных листов толщиной от 5 до 450 мм и может работать на ацетилене и его заменителях. Всасывание и смешивание газов в головке, раздельный подвод горючего газа и подогревающего кислорода к головке, применение инжектора с плавно сужающимся отверстием позволяют сократить расход газа на 15—20% и повысить производительность резки на 28%.
Конструкция резака компактна и технологична. Масса резака 1,0 кг.
Газовый резак с автоматическим клапаном разработан новаторами В. В. Пановым и Л. В. Корнильевым. Резак обеспечивает экономию горючего газа в процессе резки. Кроме того, резак оснащен мембранными уплотнениями запорных газовых вентилей и имеет облегченную конструкцию.
Головка резака принципиально не отличается от головки резака УРШ-66. Однако с целью уменьшения массы трубка подогревающего кислорода резака расположена в трубке для подачи горючего газа.
Рис. 62. Автоматический клапан к газовому резаку.
Автоматический клапан подачи горючего газа (рис. 62) состоит из корпуса 1, заглушки 3, гайки 5, прокладок 2 и 6, мембраны 7, шарика 8 и седла 10. В корпусе выполнены три канала. Канал 12 соединен с полостью трубки подачи режущего кислорода. Каналами 9 и 11 соединяются части трубки подачи горючего газа.
Работа клапана состоит в следующем. При закрытом вентиле режущего кислорода (в режиме предварительного подогрева) горючий газ, поступая в канал 9, поднимает запорный шарик и поступает в канал 11 с необходимым для подогревающего пламени расходом. После разогрева металла до требуемой температуры открывают вентиль режущего кислорода, который одновременно поступает в канал 12 и через отверстие 4 воздействует на мембрану 7 и прижимает шарик к седлу. Так как в седле имеется канавка, то горючий газ продолжает поступать в канал 11, однако в уменьшенном примерно в 2 раза объеме. Размер канавки выбирается таким, чтобы поступающего горючего газа было достаточно для поддержания процесса резки.
Конструкция газового вентиля с мембранным уплотнением показана на рис. 63. Особенностью конструкции является то, что газовая полость изолирована от резьбового соединения маховика 11 мембраной 7, установленной в гнезде корпуса 1 и прижатой резьбовым кольцом 9 через уплотнительное кольцо 8. В газовой полости между мембраной и седлом 5 расположен шарик 2, поджатый снизу пружиной 4. При повороте маховика 11 по часовой стрелке цилиндрический хвостовик его через мембрану прижимает шарик к седлу, который и перекрывает газовый канал. При повороте маховика против часовой стрелки торец цилиндрического хвостовика отходит от диафрагмы. Пружина поднимает шарик и освобождает отверстие в седле, при этом газ поступает из канала 3 в канал 6 и далее в зону резки. Стопорный винт 10 определяет крайнее верхнее положение маховика. В вентиле, который применяется в трубопроводе для режущего кислорода, пружина 4 может, отсутствовать, так как давление кислорода достаточно для поднятия шарика.
В табл. 3 приведены результаты сравнительных ис- Рис. 63. Газовый вентиль с мембранным уплотнением.
пытаний описываемого резака и резака «Пламя-62» при резке листов из малоуглеродистой стали марки Ст. 3 толщиной 5, 12, 40 и 70 мм. Резка осуществлялась при помощи газорезательного полуавтомата типа «Радуга» с максимальной подогревающей способностью пламени.
Анализ результатов испытаний показывает, что газовый резак новой конструкции обеспечивает снижение расхода ацетилена в среднем на 47% практически без снижения скорости резки. Примененные в нем вентили показали надежную работу в течение длительного времени эксплуатации.
Техническая характеристика
Рабочее давление кислорода, кгс/см2 .... 3—7 Рабочее давление ацетилена, кгс/см2 .... 0,07—0,5
Толщина разрезаемого металла, мм.....3—200
Расход ацетилена при подогреве, м3/ч .... 0,5—0,8
Расход ацетилена при резке, м3/ч......0,3—0,6
Масса резака, кг . . ...........-. 0,82
Регулируемый резак (рис. 64), разработанный и внедренный новаторами М. Э. Васильевым и В. С. Шумским, позволяет повысить производительность при резке.
Известно, что резка тонколистового металла обычными ручными резаками сопряжена со значительными трудностями, связанными с необходимостью настройки и поддержания требуемой температуры нагрева в зоне резки. При использовании резаков, имеющих головки с двумя параллельными выходными каналами, температура нагрева регулируется наклоном оси выходных каналов к плоскостям реза. При наклоне резака удлиняется длина режущей кислородной струи, что снижает производительность качества резки. Кроме того, такой способ требует высокой квалификации и большого напряжения в процессе работы.
Регулируемый резак создан на базе промышленной газосварочной горелки типа «Малютка» и имеет преимущества перед существующими. В корпусе 5 упомянутой горелки сбоку впаяна камера 12, соединенная с каналом для подачи кислорода. В камеру встроен двухпозиционный вентиль 14. К камере 12 при помощи накидной гайки 11 присоединен наконечник 10 с мундштуком 9. Наконечник 7 с мундштуком 8, который присоединен к корпусу гайкой 6, служит для получения подогревающего пламени. Конструкция резака позволяет изменять расстояние между подогревающим и режущим каналами мундштуков. Это достигается поворотом наконечников 7 и 10 при слегка ослабленных гайках 6 и
11. Расстояние между мундштуками выбирается в обратной зависимости от толщины разрезаемого металла: чем тоньше металл, тем больше расстояние между мундштуками. Для установки необходимого расстояния могут быть использованы простейшие шаблоны.
Таблица 3 Результаты сравнительных испытаний газового резака Пламя-62 и резака с автоматическим клапаном
Рис. 64. Регулируемый резак.
Настройка резака осуществляется следующим образом. К трубке 1 подводят кислород, а к трубке 2 — горючий газ. Далее устанавливают требуемое расстояние между мундштуками. После этого открывают вентили 13 и 4, зажигают подогревающее пламя и подводят его к поверхности металла. Затем указательным пальцем руки, держащей рукоятку 3, быстро поворачивают вентиль 14, а пламя перемещают вдоль реза справа налево. Струя режущего кислорода, двигаясь за подогревающим пламенем, режет металл.
Рис. 65. Резак для кислородно-флюсовой резки.
Таблица 4 Рекомендуемые составы порошкообразных флюсов для резки различных материалов
Резак для кислородно-флюсовой резки высоколегированных хромистых, хромоникелевых сталей, чугунов и цветных металлов, разработанный новатором Г. С. Скрипченко, показан на рис. 65. Он выполнен на базе промышленного резака типа «Пламя». В рукоятке 4, кроме имеющихся трубок 1 я 2, вмонтирована трубка 3 с вентилем 5 и трубкой 6. На конце трубки 6 закреплено гайкой 8 сопло 9. Хомутиком 7 трубка 6 прикреплена к наконечнику резака. Трубка 3 соединена шлангом с флюсопитателем.
Достоинством этого резака является простота в изготовлении и надежность в работе.
В табл. 4 приведены некоторые рекомендуемые составы порошкообразных флюсов для резки различных материалов.
Автор - svarka
mgplm.org