Сверление точных отверстий дрелью. Секреты мастерства. Пробивка отверстий в металле
Пробивка отверстий в металле, пресс для ручной пробивки
Пробой отверстий и перфорация материала в виде листа или труб — это довольно востребованная операция. На сегодня существует несколько вариантов ее выполнения, которые отличаются друг от друга применяемым оборудованием, от которых зависит качество и параметры точности.
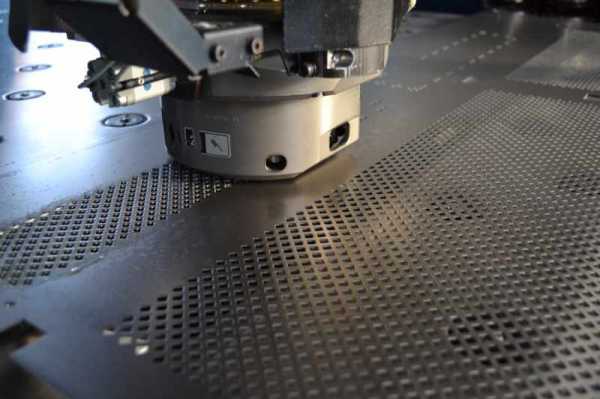
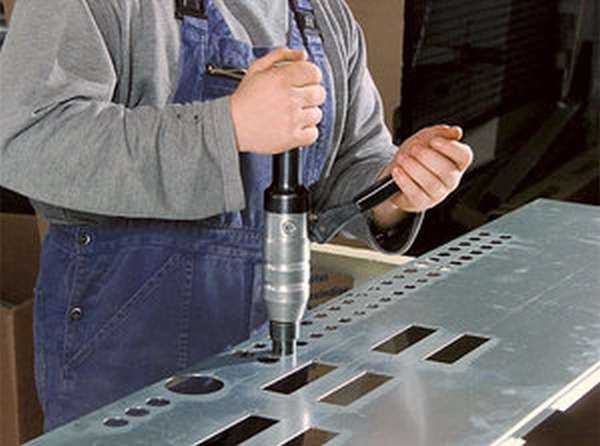
При изготовлении большого количества изделий, в том числе и декоративных металлических деталей. Довольно часто встречается потребность в таких операциях, как получение множества однотипных отверстий. Чаще всего их используют для крепления конструктивных элементов, но в ряде случаев их можно рассматривать как украшение.
Технолог, выбирая метод обработки детали, руководствуется требованиями нормативно — технической и конструкторской документации.
Так, при обработке листа металла толщиной от 0,5 до 4 мм оптимальным вариантом будет использование пробивки на специализированном оборудовании.
Пробивка отверстий и перфорация в чем разница
Кстати, довольно часто, пробивку листового металла именуют перфорацией. На самом деле этот процесс (пробивка отверстий) не более чем разновидность перфорации, которая включает в себя множество других способов.
Например, пробивка отверстий в профильном металле, например, трубе выполняют с помощью сверления или фрезерования. Кроме этого, для решения этой задачи применяют технический лазер, который позволяет получать отверстия в десятые доли миллиметра.
Виды оборудования
Оборудование, которое используют для получения отверстий можно разделить на «условно ручные», то есть те, которые нуждаются в постоянном присутствии оператора — станочника, и на автоматизированные, которые работают при минимальном участии человека. В качестве инструмента для пробивки отверстий в металле применяют различного вила пробойники, штампы и некоторые другие.
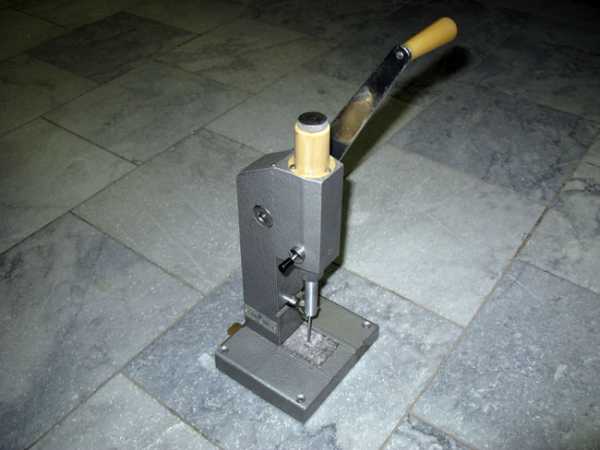
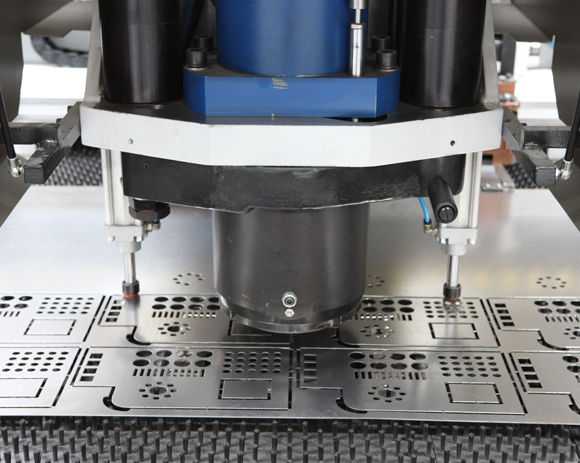
К первой группе относят оборудование, работающее от механического, гидравлического или другого вида привода. Вторые — это полностью автоматизированные станки, работающие под управлением ЧПУ, к примеру, координатно-просечные прессы или дыропробивной станок.
Ручной процесс
К ручным способам получения отверстий в металле можно отнести — сверление, пробивку. В качестве инструмента для пробивки отверстий в металле применяют сверла и соответствующее оборудование — сверлильные станки или ручные дрели. Для ручной пробивки инструмента применяют бородок и ударный инструмент (молоток, кувалда). Такой пробойник можно устанавливать на ручные прессы.
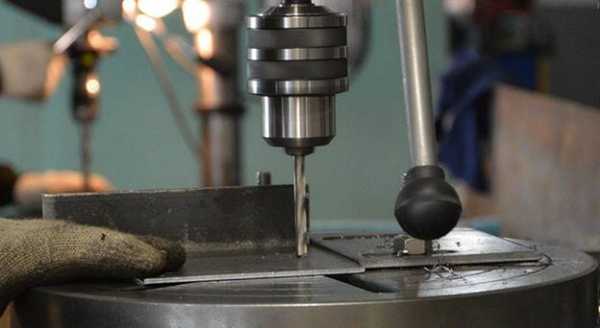
Ручной процесс пробивки
Сверление отверстий производят на сверлильных, фрезерных или токарных станках. В качестве рабочего инструмента применяют сверла. Для окончательного формования отверстия используют зенкера, цековки, развертки. С их помощью устраняют овалы, формируют фаски, повышают точность отверстия и чистоту поверхности.
Для пробивания отверстий в металле используют разные прессы — пневматические, гидравлические и пр. Усилия, развиваемые для эффективной работы штампа, состоящего из двух деталей (пуансона и матрицы), составляют от нескольких килограмм, до сотен, а то и тысяч тонн.
Пробивание отверстий на комбинированных пресс — ножницах
Нередко в производстве для получения отверстий применяют комбинированные пресс — ножницы.
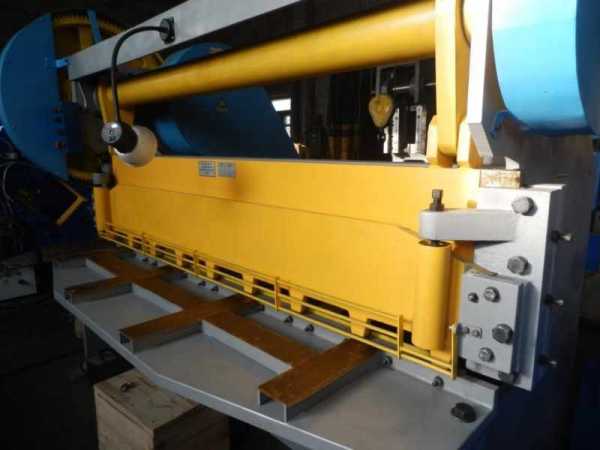
Пробивание отверстий на комбинированных пресс — ножницах
Это устройство состоит из нескольких механизмов, которые позволяют обрабатывать металлический профиль, к примеру, уголок, резать полосы металла, осуществлять вырубку в форме прямо- или треугольников и, само собой, на этих ножницах устанавливают инструмент для пробивки отверстий в металле. Как правило, он состоит из пуансона и матрицы. Пуансон имеет диаметр пробиваемого отверстия. Матрица имеет в своем теле отверстие, соответствующее размеру пуансона. Через нее происходит удаление отходов вырубки.
Следует отметить, что вышеперечисленные способы получения отверстий не отличаются высокой производительности, особенно, в условиях крупносерийного или массового производства. Появление автоматизированного оборудования позволяет устранить эту проблему.
Пробивание отверстий на прессах
Использование оборудования, работающего под управлением системы ЧПУ привело к снижению трудоемкости производственных процессов, соответственно это положительно отражается на стоимости готового изделия.Дело в том, что управляющая программа, которая вносится перед началом работы, содержит в себе точные данные относительно расположения отверстий на листе.
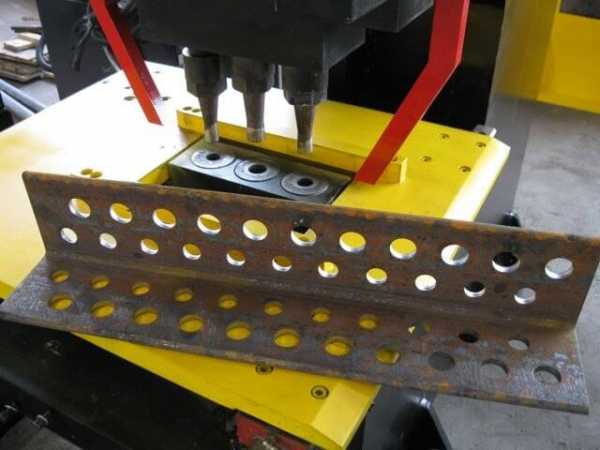
Пробивание отверстий на прессах
Например, револьверный пробивной станок оснащают барабаном, на котором установлены пуансоны (инструмент для пробивки отверстий в металле) обладающие разными размерами и формами. При работе, программа автоматически выбирает необходимый инструмент. Такое инженерное решение позволяет менять инструмент не, останавливая работу станка, и повышать скорость получения готового изделия. На оборудовании этого типа, возможно, получение до 1 500 отверстий в минуту.Получение готового изделия состоит из нескольких операций. Первая заключается в укладке листа металла на рабочий стол. Для закрепления ее на нем применяют зажимы разного типа.После того как установлен и закреплен оператор запускает управляющую программу. После этого начинается перемещение заготовки. По координатам, заданным в программе, в необходимой точке, происходит опускание прижимного устройства, фиксирующего лист в нужном месте. После прижима происходит удар, наносимый пробойником (пуансоном).
На инструментальном барабане может быть установлен поворотный инструмент, который существенно расширяет возможности станка и позволяет выполнять резку контуров сложных форм.Пресс для пробивки отверстий в металле позволяют выполнять, кроме пробоя, следующие операции:
- пулевка — выдавливание, получение кромок разной направленности;
- формовка;
- неокончательная пробивка.
Координатная пробивка металла
Такой способ получения отверстий подразумевает то, что отверстия будут получены в определенном последовательности. Эта операция может быть использована при изготовлении как простых деталей, так и довольно сложных металлоконструкций. Такая обработка листового металла требует от оборудования и управляющей программы высокой точности, так как ошибки в настройке и программном коде могут привести к получению некондиционной продукции.
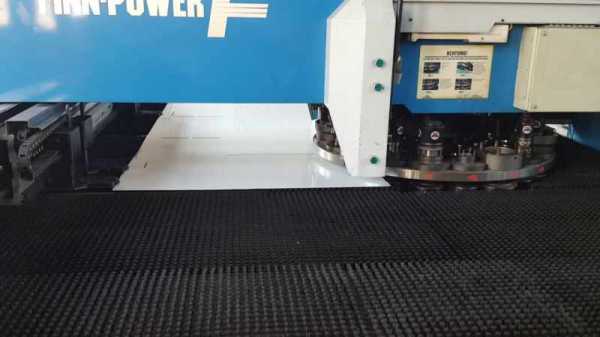
Координатная пробивка металла
Пробивка металла, как технологическая операция существует довольно давно, но в последние годы, благодаря появлению систем с числовым программным обеспечение, она существенно видоизменилась. Так, современное оборудование позволяет выполнять операции по пробою отверстий с точность их размещения до 0,05 мм. Координатно пробивное оборудование позволяет обрабатывать стали разных марок толщиной от 0,5 до 8 — 10 мм.Координатная пробивка металлического листа используется при производстве деталей корпусов, крепежных комплектов и пр. Для получения набора отверстий применяют серию ударов пуансона по листу. Порядок пробоя заносится в управляющую компьютерную программу. Кстати, использование компьютерных программ и соответствующего инструмента для пробивки отверстий в металле гарантирует качество готовых изделий.
Применение координатно — пробойных прессов для пробивки отверстий в металле обеспечивает многократное повышение скорости производства и поэтому его применяют для крупносерийного и массового производства деталей из металлического листа.
Недостатки технологии
Надо помнить о том, что качество получаемой продукции напрямую зависит от нескольких факторов, среди них которых — качество инструмента, настройки оборудования, добротности программного обеспечения, применяемого для создания управляющей программы.
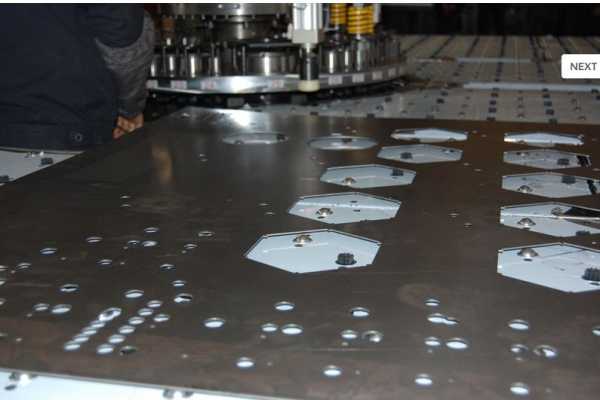
Координатная пробивка и ее недостатки
Но надо отметить, что в принципе, вне зависимости от способа получения группы отверстий, дефекты при ручной пробивке и автоматизированной одинаковы.
Смещение отверстий
Чаще всего при изготовлении группы отверстий можно встретить такой дефект, как смещение отверстий относительно друг друга или сторон листа. Этот дефект, может проявиться из-за ошибок в программе, неправильных настроек станка и пр.
Заусенцы
Этот дефект появляется вследствие того, что неправильно подобраны размеры пуансона и матрицы. Кроме того, заусенцы появляются в результате некачественной заточки инструмента.
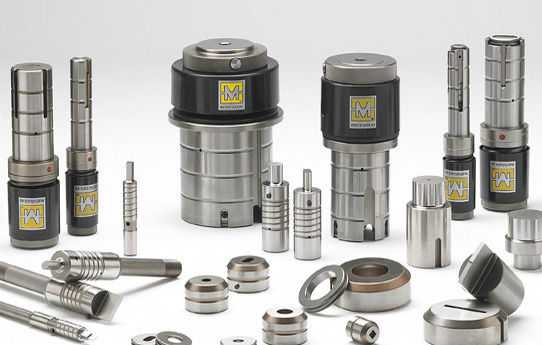
Пуансоны и матрицы
Борозды
Нередки случаи появления бород на поверхности отверстия вдоль его оси. Они вызваны наличием дефектов поверхности пуансона.
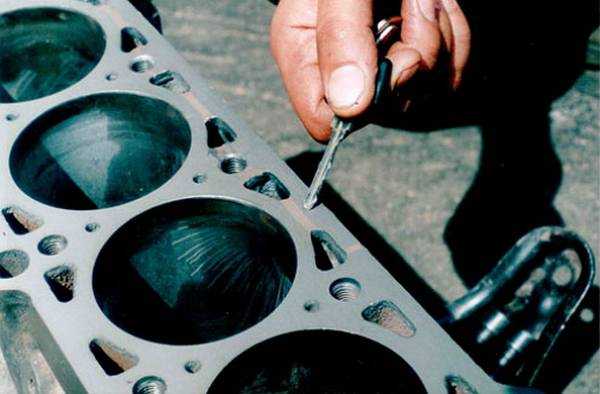
Борозды при пробивке металла
Трещины
Образование трещин на кромках пробиваемых отверстий вызвано тем, что их диаметр близок по размеру к толщине листа.
Расчет необходимого усилия пробивки
Процесс вырубки металла характеризуется тем, что в ходе этого процесса появляется довольно сложная схема нагрузки, которая концентрируется в районе места взаимодействия пуансона, прорубаемого материала и матрицы.
Пуансон изготавливают таким образом, что он входит в материал не всем своим торцем, а только внешней кольцевой частью. Ответное воздействие возникает со стороны матрицы. Причем давление, возникающее в зоне взаимодействия этих трех компонентов, распределяется неравномерно.
Другими словами, в процессе вырубки возникает пара сил, которые формируют круговой изгибающий момент. Под его воздействием лист изгибается. В результате этого изгиба зарождается давление, которое оказывает воздействие на пуансон, и на кромку матрицы. Кроме этого, необходимо учитывать и то, что под действием сил трения появляются касательные усилия.Как видно из выше сказанного, при пробивке возникает неоднородное силовое поле. Поэтому, при проведении расчетов применяют условную величину — сопротивление срезу.В результате, проведенных исследований, сопротивление зависит не столько от свойств металла, но и от уровня наклепа, толщины вырубки, зазоров в паре пуансон/матрица и скорости процесса вырубки.
Если вы нашли ошибку, пожалуйста, выделите фрагмент текста и нажмите Ctrl+Enter.
stankiexpert.ru
Пробивка отверстий в металле: особенности технологии
Пробивка отверстий в металле является одним из методов перфорации. За счет высокой производительности, относительной простоты выполнения и отличного результата он пользуется высокой популярностью.
Суть технологии
Чаще всего осуществляется пробивка отверстий в листовом металле толщиной 0,5–4 миллиметра, так как из-за особенностей конструкции используемого станка работа с трубами и более толстыми листами практически невозможна.
Сам процесс осуществляется с использованием пуансона – пробойника, изготовленного из твердых сплавов, и матрицы – перфорированной «подложки», на которой размещается заготовка. Пуансоны могут иметь разнообразные формы, что дает возможность нанесения перфорации различных видов.
Получаемые перфорированные листы могут использоваться в самых различных сферах и выступать деталями металлической мебели, каркасов рекламных конструкций, защитными кожухами и решетками.
Методы
Пробивка может осуществляться в ручном или автоматизированном режиме.
Ручной
В данном случае используются специализированные пресс-ножницы. Они могут иметь различный принцип действия: механический, пневматический или гидравлический, но результат будет всегда одинаков.
Процесс выглядит следующим образом:
- Производится разметка заготовки – керном размечаются центры будущих отверстий.
- Размеченный лист вручную перемещается по станине пресс-ножниц до совпадения разметки с центром пуансона.
- Производится запуск пресса – пуансон выдавливает часть металла из заготовки, оставляя ее в матрице.
Из-за ручного контроля данный метод не может обеспечить высочайшей точности и производительности, поэтому на крупных производствах используются автоматические станки с ЧПУ.
Автоматизированный
Для автоматической пробивки применяются высокопроизводительные координатно-пробивные прессы. Предварительно, еще до размещения на столе заготовки, в их память вносится программа, содержащая информацию о расположении и форме всех необходимых отверстий.
Современные станки также называют револьверными, так как они имеют вращающийся барабан, в котором установлены пуансоны различных форм и размеров. В зависимости от программы они автоматически сменяют друг друга без участия человека и остановки работы. Подобная конструкция позволяет производить до 1500 отверстий в минуту.
В отличие от ручного метода, лист-заготовка закрепляется на столе специальными зажимами, которые производят ее перемещение в плоскости согласно внесенной программе. При этом во время работы головка пресса сначала прижимает металлический лист специальным прижимным кольцом, обеспечивающим фиксацию рабочей области, а затем использует соответствующий пуансон.
Благодаря использованию поворотного инструмента станок также может использоваться для осуществления перфорации сложной формы. Кроме того, он обладает дополнительным функционалом и может производить пуклевку, формовку и неполную пробивку, что существенно расширяет возможности изготовления.
Особенности
Как и другие технологии, пробивка отверстий в листовом металле имеет определенные преимущества и недостатки.
К плюсам можно отнести:
- Высокую скорость производства с использованием станка с ЧПУ.
- Высокие показатели точности – до 0,05 миллиметра.
- Возможность ручной пробивки на небольших производствах практически без потери качества.
Присутствуют и минусы:
- Небольшой диапазон допустимых значений толщины заготовки.
- На толщинах, близких к максимальным, по краям отверстия могут образоваться неровности и заусенцы, требующие дополнительной обработки.
Несмотря на перечисленные недостатки, пробивка отверстий в металле пользуется стабильно высоким спросом в самых различных сферах производства и не спешит уступать другим методам перфорации.
stvybor.ru
Пробивка отверстий в металле - Сборка металлоконструкций
Пробивка отверстий в металлеКатегория:
Сборка металлоконструкций
Пробивка отверстий в металлеПробивка (продавливание) отверстий допускается для малоуглеродистой стали толщиной до 25 мм, низколегированной стали до 20 мм, высокопрочной стали до 12 мм включительно при температуре не ниже 0 °С. Отверстия, образованные пробивкой, имеют конусность и заусенцы, а также худшие механические свойства стали в зоне, прилегающей к отверстию. Поэтому в деталях, предназначенных для клепаных конструкций, работающих на динамическую нагрузку, а также деталях, требующих высокой точности расположения, отверстия пробивать не разрешается.
Для пробивки отверстий используют дыропробивные (эксцентриковые) комбинированные и кривошипные прессы.
Дыропробивной пресс типа К-2130 предназначен для пробивки отверстий в листовом, сортовом и фасонном прокате. Пресс состоит из С-образной стальной станины, имеющей в нижней части стол для крепления подушки с матрицей. В верхней части станины расположены направляющие, по которым двигается ползун. К нему прикреплен пуансонодержатель с пуансоном. Ползун включают на рабочий ход рукояткой включения пуансона или нажимом на ножную педаль. Пресс может работать на одиночных и непрерывных ходах.
Дыропробивной пресс К-2130 усилием 1000 кН — эксцентриковый и одноштемпельный, т. е. здесь сможет быть установлен один пуансон (штемпель) и, следовательно, за один ход можно пробить одно отверстие. В некоторых случаях применяют двухштемпель-ные и многоштемпельные прессы, предназначенные для одновременной пробивки двух и более отверстий. В этом случае пуансоны (штемпеля) располагаются в одной плоскости параллельно фронту пресса, на расстоянии 80…100 мм один от другого.
В качестве многоштемпельных применяют кривошипные прессы усилием 1600. . .8000 кН, так как эксцентриковые дыропробивные прессы выпускаются усилием 0,8… 1 МН, что обеспечивает пробивку за один ход только одного отверстия.
В мастерских и на заводах малой мощности для пробивки отверстий применяют комбинированные пресс-ножницы, которые могут пробивать отверстия и резать фасонный прокат.
Для пробивки отверстий деталь укладывают между пуансоном и матрицей. При включении пресса пуансон опускается вниз и прижимает деталь к матрице. Матрица закрепляется в подушке пресса неподвижно. Под давлением пуансона в детали возникают сжимающие и скалывающие напряжения, сконцентрированные по периметру режущих кромок пуансона и матрицы. Пуансон, преодолевая сопротивление, проникает в глубь толщины стали, выдавливая ее в отверстие матрицы. Величина проникновения пуансона в сталь с содержанием углерода 0,2% до полного скалывания составляет 40 % толщины стали.
Пуансон (штемпель) состоит из рабочей и хвостовой части, служащей для закрепления пуансона в пуансонодержателе пресса, вместе с которым он совершает возвратно-поступательное движение. Диаметр рабочей грани пуансона должен быть больше пробиваемой стали не менее чем на 2 мм. Диаметр режущей грани пуансона принимается равным номинальному размеру отверстия, а диаметр отверстия в матрице больше диаметра пуансона на величину зазора. Зазор, мм, для пробиваемой стали толщиной 4.. .8 мм составляет 0,7, толщиной 9. ..12 мм—1,2; 13… …17 мм—2; 18…19 мм—2,6; 20. ..21 мм — 2,65; 22.. .25 мм—3,6.
Рис. 1. Дыропробивной пресс: 1 — станина, 2 — подушка. 3 — пуансонодержатель, 4 — рукоятка включения
Пуансоны изготовляют с конусом на конце и без конуса. Пуансон без конуса применяют при пробивке отверстий без наметки по шаблонам. При пробивке отверстий по кернам конус пуансона входит в конусное углубление глубиной 2…3 мм, образованное при разметке или наметке на поверхности обрабатываемой стали кернером, закрепляет конец пуансона и повышает его устойчивость под действием сил продавливания. Чтобы уменьшить силы трения пуансона о стенку отверстия при пробивке, его рабочую часть делают конической и шлифуют с торца и по конической поверхности, образуя этим режущую кромку,
При пробивке отверстий очень важно, чтобы инструмент работал без поломок и в-ыкрашивания режущих кромок. Это зависит от качества стали, применяемой для изготовления инструмента, качества изготовления инструмента, термической обработки и марки пробиваемой стали.
Матрицы и штемпеля изготовляют из легированной инструментальной стали марок 5ХВ2С и Х12М или из инструментальной углеродистой марок У8А и У9А.
В зависимости от профиля стали, толщины, размеров и массы детали, серийности, требуемой точности, количества отверстий и их расположения отверстия пробивают по шаблону, наметке с применением приспособлений или специальных установок.
В листовых деталях площадью до 0,5 м2 и массой до 20 кг отверстия пробивают но шаблону на одноштемпельном прессе. Прессовщик накладывает шаблон на деталь, подает ее на стол пресса, совмещает отверстие на шаблоне со штемпелем пресса, пробивает отверстие в детали, передвигает ее и шаблон, снимает шаблон с детали, убирает деталь и укладывает ее в штабель или контейнер. В уголках длиной до 1 м и массой до 20 кг отверстия пробивают по шаблонам в такой же последовательности.
В листовых деталях площадью до 0,5 м2 и уголках длиной до 1 м отверстия пробивают по наметке на одноштемпельных прессах в такой последовательности. Прессовщик подает деталь на стол пресса, устанавливает деталь под штемпелем, совмещая острие штемпеля с керном на детали, пробивает отверстие в детали и передвигает ее для пробивки следующих отверстий. Затем снимает деталь с пресса и укладывает в штабель или контейнер. Работает прессовщик сидя.
Рис. 2. Схема пробивки отверстий: 1 — гайка для крепления пуансона, 2 — пуансон, 3 — конус, 4 — обрабатываемая сталь, 5 — плоскость скалывания. 6 — матрица, 7 — подушка, 8 — конусное углубление
Для пробивки отверстий по наметке в уголках большой длины, чтобы поддерживать и перемещать уголки, пресс оснащают с обеих сторон дисковыми роликами. Ролики устанавливают на стойках на расстоянии 1000… 1500 мм один от другого. Со стороны подачи уголков находится загрузочный стол, уровень которого немного выше уровня роликов. На загрузочный стол подают мостовым краном партию уголков, которые прессовщик и его помощник по одному укладывают полкой без отверстий между дисками роликов. Уголок легко перемещается по роликам, прессовщиком, который поочередно наводит и совмещает намеченные отверстия с конусом штемпеля. После продавливания отверстий уголок снимают мостовым краном и укладывают на прокладки в штабель.
Для продавливания отверстий во второй толке ‘пачку уголков с отверстиями возвращают на загрузочный стол и продавливают отверстия тем же способом, что и в первой полке.
При организации рабочего места для пробивки отверстий руководствуются следующими правилами.
Контейнеры с мелкими деталями устанавливают вблизи рабочего места со стороны, противоположной рукояткам управления. Площадки для складирования заготовок располагают у подающих роликовых конвейеров или столов, а готовых деталей — у приемных конвейеров или столов.
Перед началом работы проверяют пресс на холостом ходу, смазывают его, регулируют местное освешение так итобм свет не ослеплял прессовщика. Детали укладывают строго горизонтально к плоскости матрицы без перекосов и перегибов, особенно за этим следят при пробивке отверстий в больших листовых деталях, поддерживаемых с помощью мостовых кранов.
Сухарь пресса включают всегда полностью во избежание его обратного выталкивания. Чтобы пуансон не ломался, он должен входить в матрицу без перекосов. Шаблон для пробивки отверстий прикрепляют кляммерами, чтобы не повредить руки. После окончания работы и выключения пресса убирают рабочее место.
Рис. 3. Схема организации рабочего места при пробивке отверстий: 1,4 — дисковые ролики, 2 — загрузочный стол. 3 — дыропробивной пресс, 5 — штабель, 6 — прессовщик
Читать далее:
Гибка металлов при изготовлении конструкций
Статьи по теме:
pereosnastka.ru
Самодельный прошивень для пробивки отверстий в металле
Всем самоделкиным доброго времени суток.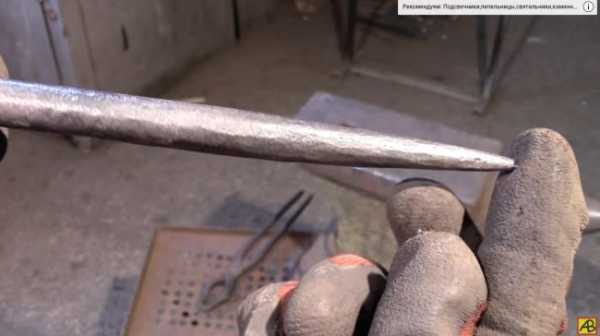
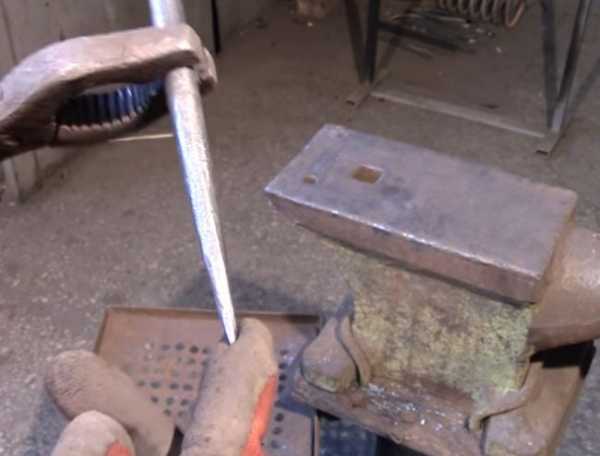
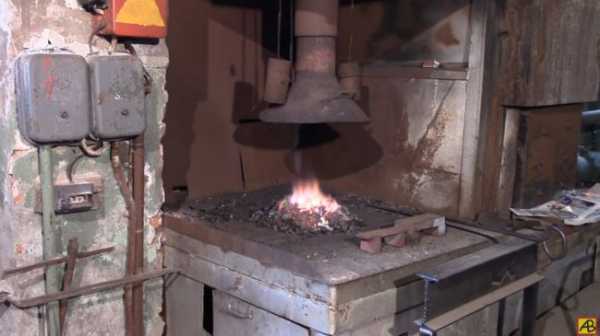
Материал, который автор будет использовать для изготовления этого инструмента. Андрей будет использовать автомобильную пружину.
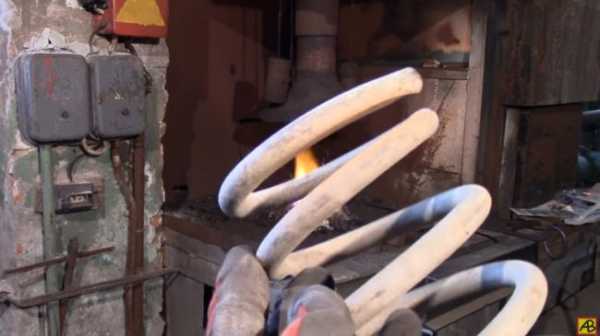
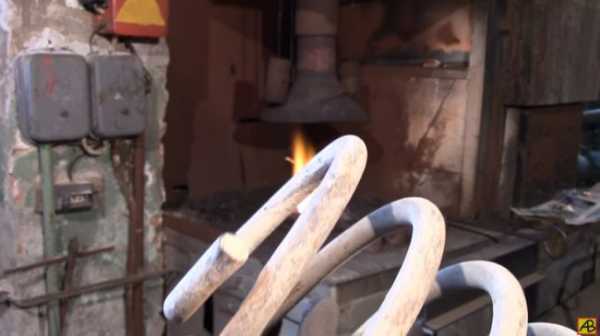
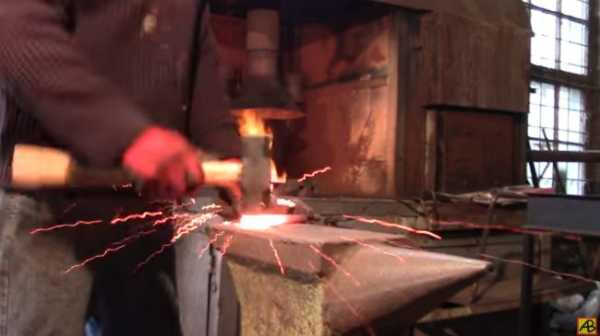
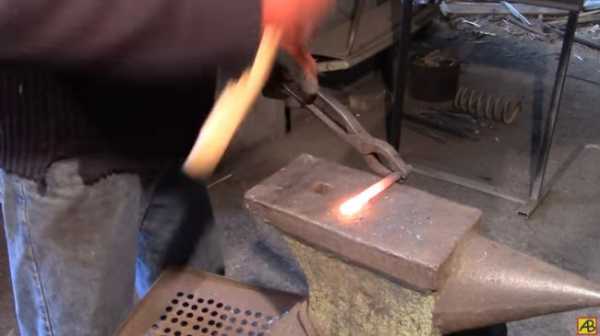
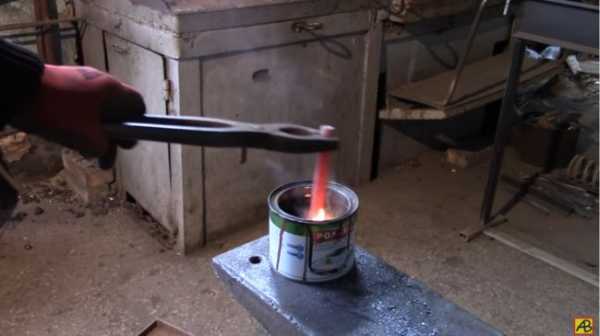
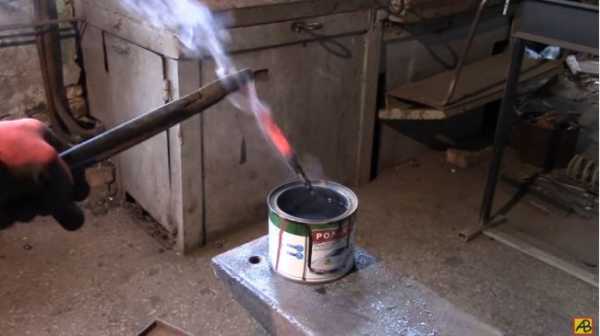
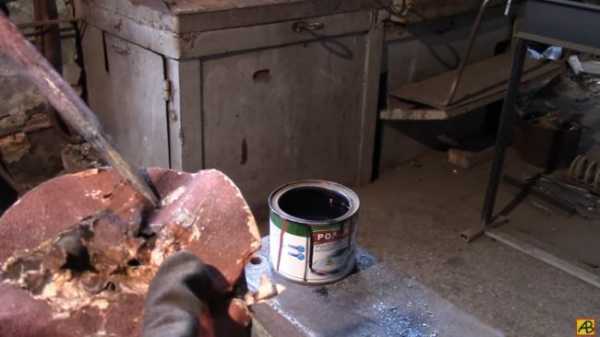
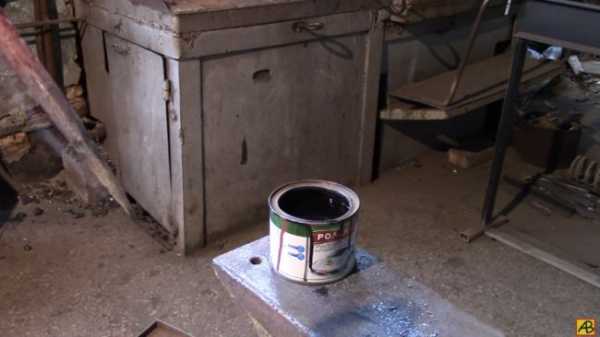
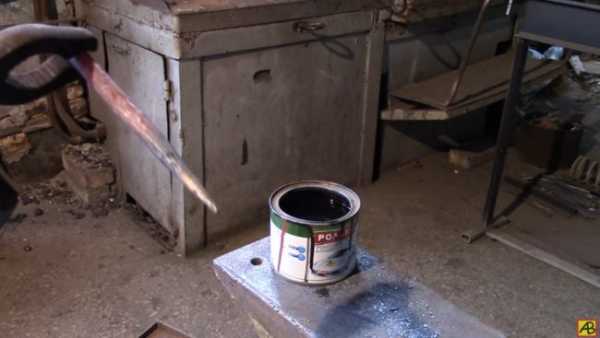
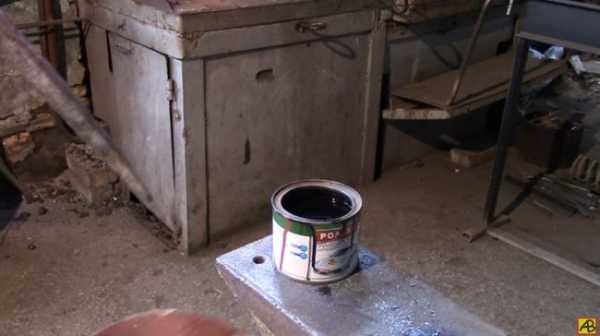
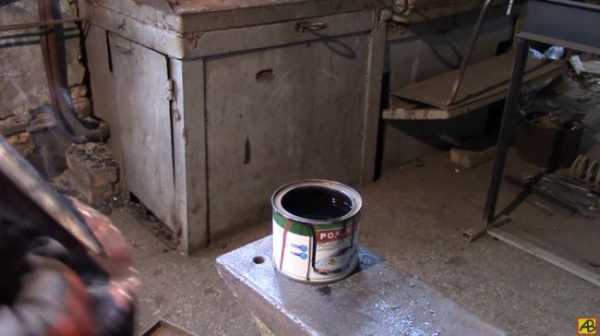
Еще немножко осталось, если надо нагреть, мы можем также с хвостовичка нагреть, что ускорит процесс отпуска металла.
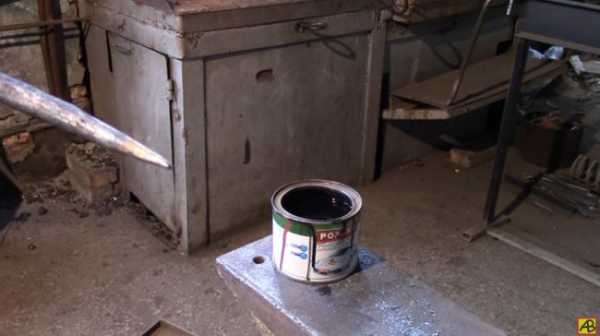
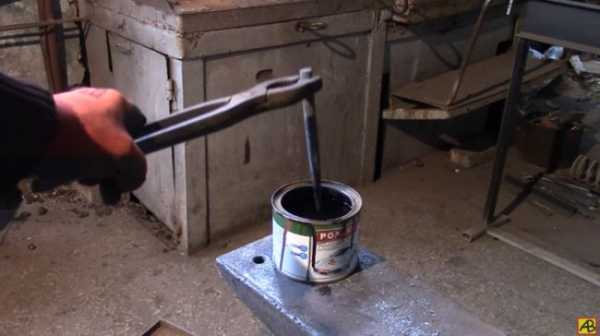
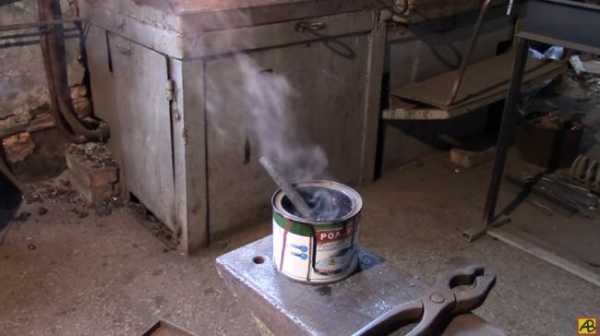
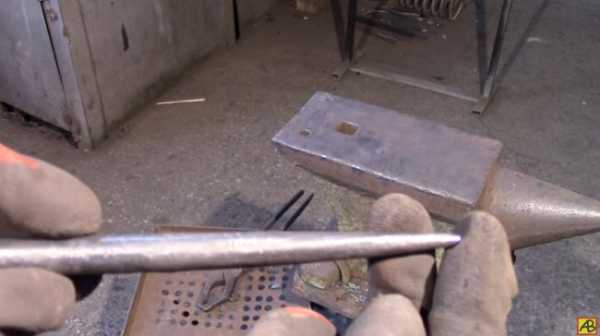
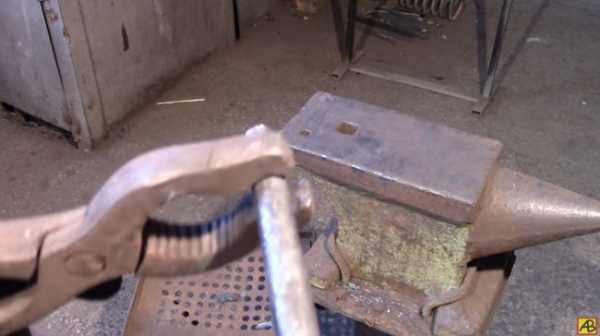
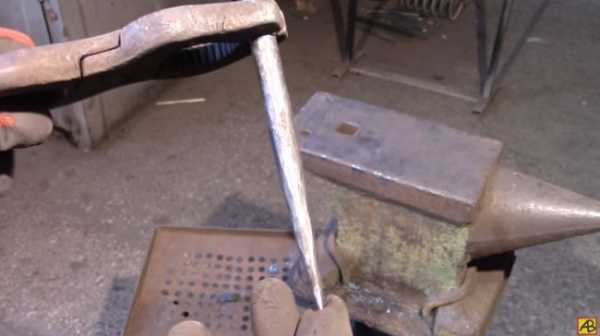
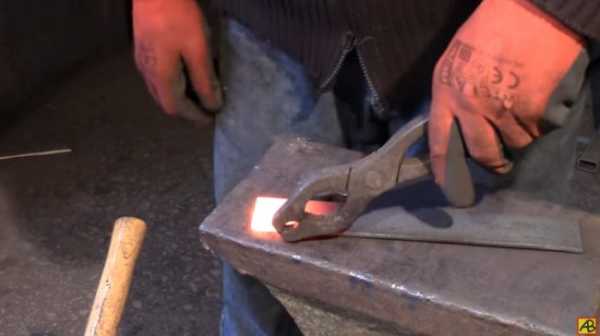
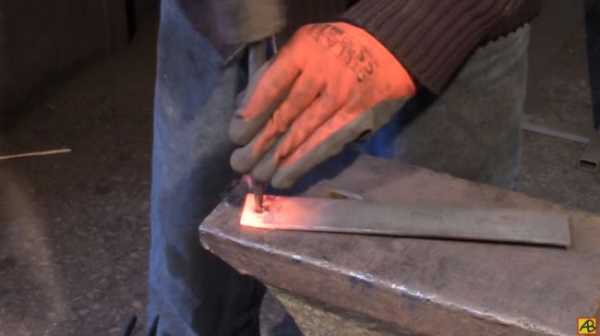
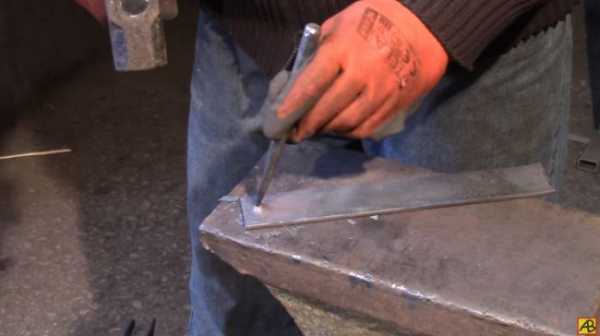
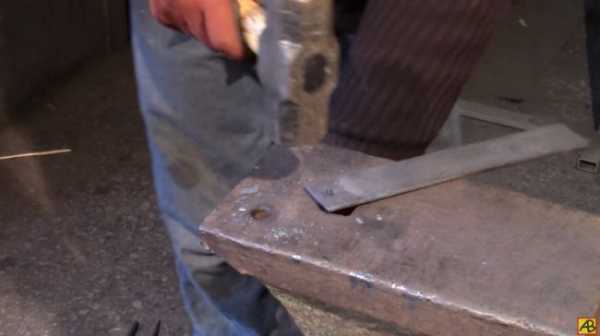
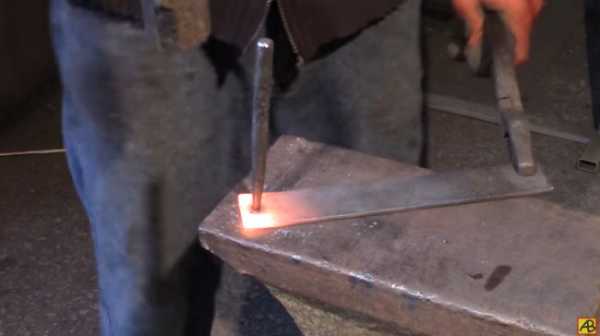
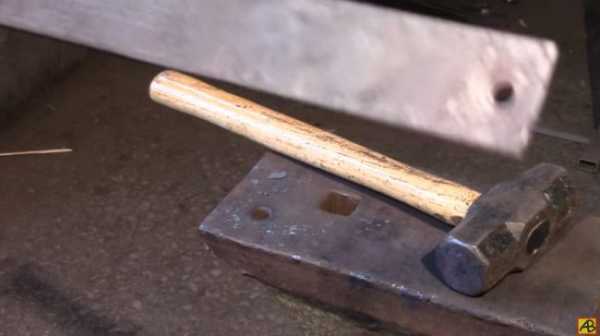
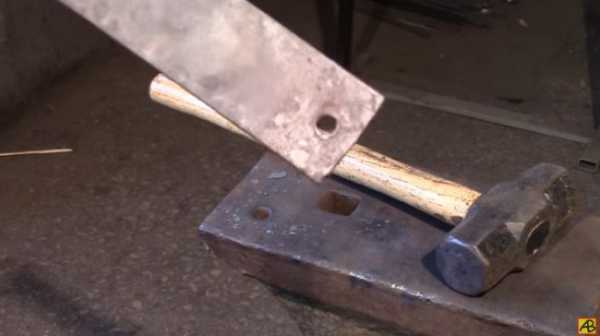
usamodelkina.ru
Назначение и способы пробивания отверстий в металле
Пробиванием (рис. 71, а) или, как иногда говорят, прокалыванием называется операция по получению отверстий в сплошном металле при помощи слесарного молотка и бородка (пробойника) при ручном способе или при помощи комплекта инструментов, состоящего из пуансона и матрицы при машинном способе.
Рис. 71. Пробивание отверстий: а — схема пробивания, б — отверстие с радиальными трещинами, в — разрез пробитого отверстияДля пробивания отверстий вводят металл между указанными инструментами и при вдавливании бородка или пуансона в металл происходит сначала его смятие (примерно на половину его толщины), а затем отрывание (скалывание) части металла, имеющей форму рабочих частей применяемых инструментов.
Пробивание отверстий в металле по сравнению со сверлением — операция более производительная. Однако получение отверстий пробиванием применяют не всегда при изготовлении металлических изделий. При пробивании отверстий в металле происходит наклеп, вызывающий нежелательную хрупкость металла вокруг отверстия, в результате чего образуются трудно обнаруживаемые глазом радиальные трещины (рис. 71,6). Радиальные трещины по окружности пробитого отверстия, кроме ослабления металла в этом месте, опасны еще и потому, что с них может начаться коррозия металла под влиянием влаги, кислот и других веществ. В этих же местах сосредоточиваются и наибольшие напряжения в металле при работе изготовленной конструкции. Указанные причины ограничивают применение пробивания отверстий.
Отверстия, полученные пробиванием, всегда имеют заусенцы на кромках. Кроме того, с одной стороны отверстия имеют несколько больший диаметр (рис. 71,в). Операция пробивания всегда заменяется сверлением в тех случаях, когда диаметр отверстия меньше толщины обрабатываемого металла, так как пуансон при этом обычно ломается.
В деталях металлических конструкций отверстия могут быть образованы пробиванием на полный или, как говорят, проектный диаметр, с последующей их обработкой развертыванием при сборке, или на неполный диаметр, т. е. уменьшенный против проектного (необходимого) на определенную величину, например от 2 до 4 мм с последующим их рассверливанием при сборке или монтаже.
Пробивание отверстий в металле осуществляют ручными инструментами, на комбинированных пресс-ножницах, а также на ручных пневматических, механических или гидравлических прессах. Для облегчения подводки и установки на пресс-ножницах и прессах в требуемом положении обрабатываемой детали необходима большая ее подвижность, что при малых ее размерах и весе без труда достигается обычно вручную, а при больших размерах и весе около комбинированных пресс-ножниц и прессов устанавливают специальные столы (шаровые) или роликовые транспортеры, по которым перемещают листовые детали (или полосы).
www.stroitelstvo-new.ru
Ручное пробивание отверстий в металле
Пробивание отверстий вручную (рис. 72, а) осуществляют ударами слесарного молотка по головке бородка (пробойника), предварительно установленного на месте будущего отверстия в металле. Этим способом пробивают отверстия диаметром от 1 до 8 мм в листовой стали с пределом прочности до 30 кг/мм2.
Бородки слесарные (рис. 72,6) изготовляют шести размеров (ГОСТ 7214—54): длиной L 85, 90, 100, 120, 150 и 175 мм, имеющих диаметр оттянутой рабочей конусной части d соответственно 1, 2, 3, 4, б и 8 мм. Средняя часть бородка имеет круглое сечение и гладкую поверхность. Поэтому бородок удобно держать в руке во время пробивания отверстия. Средняя часть бородка соответственно указанной длине L имеет диаметр D 6, 6, 8, 10, 12 и 16 мм.
Рис. 72. Пробивание отверстий вручную:а - схема пробивания, б - бородок, в - схема совмещения бородка с осевыми разметочными линиями, г - схема последовательности пробивания отверстий, д — пробивание отверстия по шаблонуГоловка бородка, являющаяся ударной частью, оттянута слегка на конус и края ее округлены. При такой форме ударной части сила удара слесарным молотком по бородку используется с наилучшим результатом, так как удары приходятся по центру ударной части и создается более устойчивое положение бородка во время пробивания.
Бородки изготовляют в основном из инструментальной углеродистой стали У7А. Рабочая часть бородков на длине всего конуса, т. е. примерно на 1/3 общей длины бородка, термически обработана до твердости HRC 52— 57, а головка на длине /, = 10—15 мм термически обработана до твердости HRC 32—40.
Слесарные молотки применяются двух типов: с круглым бойком и с квадратным бойком. Слесарные молотки с круглым бойком (ГОСТ 2310—54) изготовляют семи номеров. Молотки каждого номера характеризуются весом и габаритными размерами. Для пробивания отверстий обычно применяют молотки № 2 весом 400 Г и № 3 весом 500 Г.
Слесарные молотки с квадратным бойком изготовляют шести номеров. Для пробивания отверстий применяют молотки № 4 весом 400 Г и № 5 весом 500 Г.
Рабочие концы молотков — бойки термически обрабатывают до твердости HRC 49—56 на 1/5 общей длины молотка с обоих концов. Молотки надежно насаживают на деревянные ручки, изготовляемые из крепких пород Дерева (рябины, кизила, граба, клена или березы). Ручки должны быть без сучков и трещин, поверхности хорошо отшлифованы и покрыты олифой. Ручки имеют эллиптическое сечение, благодаря этому молотки хорошо удерживаются в руке. Длина ручки зависит от веса молотка: чем больше вес, тем длиннее ручка. Обычно для молотков весом 400 Г применяют ручки длиной 300 мм, а для молотков весом 500 Г — длиной 320—380 мм.
Отверстия пробивают вручную по разметке и по шаблону. При пробивании отверстий по разметке бородок устанавливают на размечаемом материале так, чтобы торец рабочей конусной части находился в пределах окружности размечаемого отверстия, т. с. не был сдвинут влево за точку А (рис. 72, б) или вверх за точку Б, или вправо за точку В, а также вниз за точку Г. Значительно ускоряет работу применение бородков с неглубокими рисками, сделанными на рабочей конусной части (см. рис. 72,6) сечение Л—Л. Бородок с такими рисками совмещают с осевыми разметочными линиями.
Отверстия пробивают вручную обычно начиная с середины детали и ведут в последовательности, показанной на рис. 72, г. Такой порядок пробивания способствует меньшей деформации пробиваемого материала.
Пробивание отверстий по шаблону (рис. 72, д) выполняют без предварительной разметки. На деталь накладывают шаблон, а затем деталь и шаблон стягивают струбцинами. Пробивание отверстий по шаблону производится быстрее, чем пробивание по разметке, так как при первом способе не требуется совмещать торец конусной части бородка с центром осевых линий на размечаемом металле.
www.stroitelstvo-new.ru
Сверление точных отверстий в металле дрелью. Секреты мастерства.
Всем доброго настроения! Сегодня рассмотрим вопрос — сверление точных отверстий дрелью в сплошном металле. Тема может показаться достаточно простой но все же, тут есть определенные секреты мастерства, овладев которыми вы будете сверлить отверстий с особой легкостью.
Сверление отверстий в металле с помощью дрели и специальных приспособлений.
В домашних условиях часто приходится сталкиваться с необходимостью сверления отверстий в металле для установки крепежных деталей и других механических частей. Хотя с помощью обычной ручной электродрели в некоторых случаях можно достаточно точно просверлить отверстия, однако для получения высокого качества работы следует использовать вертикально-сверлильный станок. Для изменения скорости вращения станка надо переставить приводной ремень с одного шкива на другой.
Выбор сверла.
Независимо от используемого сверлильного устройства, размер и форма просверленного отверстия определяются используемым сверлом. Цилиндрическое отверстие (иногда геометрически не совсем правильное) высверливается обычно спиральным сверлом. Это сверло представляет собой остроконечный металлический цилиндр со спиральным каналом, идущим вдоль оси сверла. В мягких металлах, например в алюминии и меди, такие сверла часто высверливают отверстия с зазубренными краями. Для сверления таких металлов можно использовать сверло для листового материала, которое выполнено в виде конуса и имеет сбоку одну режущую кромку.
Отверстия в металле всегда следует сверлить с помощью высокоскоростных сверл. Изготовленные из самых твердых сталей, эти сверла имеют диаметр от 0,5 мм до 25 мм и более.
Маркировка сверл и особенность конструкции.
Одним из вариантов маркировки сверл (соответственно размерам) является указание на них диаметра в миллиметрах. Для сверления углублений большого размера можно установить вместо сверла кольцевую пилу — цилиндр с зубьями, который может вырезать отверстия размером до 150 мм и глубиной до двух третей высоты самой пилы. Можно также использовать специальное сверло, отличающееся от обычного наличием удлиненной Г-образной режущей кромки. Выпускаются специальные сверла для сверления конических или цилиндрических углублений под головки крепежных деталей, например, болтов, заклепок или шурупов.
Для придания высверленному отверстию точных геометрических размеров, при условии, что диаметр этого отверстия не превышает 35 мм, необходимо обработать его разверткой. Такая обработка выполняется вручную или на станке. Ручные развертки представляют собой прямые сверла с четырьмя или более режущими кромками, которые по мере вращения постепенно обрабатывают внутреннюю поверхность отверстия. Станочные развертки устанавливаются в вертикально-сверлильных станках.
Точное сверление металла на станке.
При сверлении точных отверстий всегда следует использовать специальную смазочно-охлаждающую жидкость, которая уменьшает трение, и охлаждает сверло при работе. Кроме того, необходимо использовать струбцины и тиски для точной неподвижной установки обрабатываемого изделия. Дни маркировки места сверления следует использовать кернер, с помощью которого в месте сверления делается не большое углубление.
При сверлении на станке для определения положения отверстия нужно провести с помощью линейки две короткие линии, пересекающиеся под прямыми углами в центре отверстия. Для предотвращения соскальзывания сверла необходимо с помощью кернера и молотка сделать небольшое углубление в найденном центре.
Определение параметров вращения инструмента.
Определить необходимую скорость вращения и установить на станке вращение с этой скоростью. Для установки скорости вращения необходимо открыть крышку кожуха и ослабить натяжение ремня, отвинчивая ручку, закрепляющую двигатель в кожухе. Для изменения скорости двигатель подвигается вперед и переставляется ремень с одного уровня шкивов на другой в соответствии с необходимым изменением скоростей, которые определяются из фирменной таблички или инструкции по эксплуатации. Наименьшая скорость достигается при размещении ремня в самом нижнем положении – между самым маленьким шкивом двигателя и самым большим шкивом шпинделя. Наоборот, самая большая скорость достигается, когда ремень устанавливается в самых верхних шкивах. Далее необходимо убедиться, что ремень натянут в горизонтальном положении между шкивами, передвинуть двигатель в исходное положение и затянуть ручку, крепящую двигатель в кожухе.
Настройка инструмента и приспособления.
Перед началом сверления сверло устанавливается в патроне и затягивается. Не следует забывать о регулировке вертикального перемещения шпинделя, опуская сверло вдоль заготовки и перемещая стопор в нужную точку на градуированной шкале перемещения стопора. Шпиндель поднимается на высоту, достаточную для установки под сверлом заготовки, фиксируется в этом положении. Заготовка передвигается так, чтобы намеченное отверстие оказалось точно под сверлом. До начала сверления заготовка надежно зажимается.
Впоследствии необходимо опустить фиксатор гильзы шпинделя и включить сверлильный станок. Выдавить каплю охлаждающе-смазочной жидкости на углубление, опустить рычагом сверло и начать сверление. В процессе работы следует прилагать равномерное давление. Для удаление стружек и опилок используется щетка. Появление из высверливаемого отверстия дыма указывает на необходимость проверить цвет металлических стружек. Они должны быть белыми или соломенно-желтыми. Голубой цвет означает перегрев. В этом случае нужно добавить смазочно-охлаждающую жидкость или уменьшить скорость вращения. После окончания сверления необходимо медленно отпустить рукоятку подачи и выключить станок.
Сверление точных отверстий ручной дрелью в металле.
Если нет необходимости соблюдать точность при сверлении отверстий, которую обеспечивает вертикально-сверлильный станок, можно использовать мощную ручную электродрель. Однако если эта дрель не является многоскоростной, то при сверлении отверстий в металле ее следует включать на непродолжительные периоды времени путем кратковременных последовательных нажатий на выключатель.
Залог успеха в большинстве случаев зависит от того как держать дрель. Перед началом сверления заготовка зажимается в тиски или прижимается крепко к столу. Затем, не включая дрели, устанавливается конец сверла на точку, нанесенную кернером. Для того чтобы увеличить исходную точку, можно нескольку раз вручную повернуть патрон дрели, нажимая на сверло. После нанесения смазочно-охлаждающей жидкости включатся напряжение. Корпус дрели удерживается неподвижно левой рукой, правой рукой прижимается сам инструмент, когда дрель начнет увеличивать обороты. По возможности рядом с дрелью ставится вертикальный угольник, чтобы облегчить установку сверла в вертикальное положение. Это обеспечит более удобное сверление точных отверстий.
Если сверло не может углубиться в поверхность металлической заготовки, с помощью кернера наносится второе, большее, углубление в нужной точке.
Техника безопасности при работе с ручной дрелью.
При работе с дрелями нельзя пренебрегать правилами техники безопасности. Для предотвращения опасности несчастных случаев при сверлении металлических изделий необходимо строго придерживаться следующих указаний:
- запрещается сверлить изделие, которое удерживается только руками;
- запрещается работать с распущенными длинными волосами или в не застёгнутой свободной одежде, а также в перчатках, поскольку существует опасность захвата материала перчаток сверлом;
- не следует пренебрегать защитными очками;
- до включения станка следует убедиться в том, что сверло в патроне туго затянуто, а ключ вынут.
Рекомендую к просмотру вот это видео, для закрепления материала:
Пожалуй на этом закончим. Сверление точных отверстий в металле, пригодится не только в домашнем обиходе но и при выполнении производственных задач.
ВНИМАНИЕ! Напоминаю, что я принимаю гостевые посты на свой блог. Если вы хотите публиковать свои статьи на моем сайте пишите мне через форму обратной связи!Всем пока! Пишите свои комментарии и делитесь статьей через социальные сети, нажимая кнопочки внизу.
С вами был Андрей!
mextexnologii.ru