Быстрорежущая сталь. Быстрорежущая сталь
Быстрорежущая сталь - это... Что такое Быстрорежущая сталь?
Лит.: Геллер Ю. А., Инструментальные стали, 2 изд., М., 1961.
А. П. Гуляев.
Большая советская энциклопедия. — М.: Советская энциклопедия. 1969—1978.
- Быстродействие
- Быстротвердеющий цемент
Смотреть что такое "Быстрорежущая сталь" в других словарях:
быстрорежущая сталь — Инструментальная высоколегированная сталь, сохраняющая высокую твёрдость при нагреве до 600 °С. Инструментальная сталь, относящаяся к карбидному (ледебуритному) классу. Маркируется путем простановки в начале марки буквы «P», за… … Справочник технического переводчика
БЫСТРОРЕЖУЩАЯ СТАЛЬ — высоколегированная инструментальная сталь (5,5 19% W, а также Cr, V, Mo, C, иногда Co), обладающая высокой твердостью и красностойкостью. Режущий инструмент из быстрорежущей стали подвергается закалке и многократному отпуску … Большой Энциклопедический словарь
Быстрорежущая сталь — Быстрорежущие стали легированные стали, предназначенные, главным образом, для изготовления металлорежущего инструмента, работающего при высоких скоростях резания … Википедия
быстрорежущая сталь — высоколегированная инструментальная сталь (5,5 19% W, а также Cr, V, Mo, С, иногда Со), обладающая высокой твёрдостью и красностойкостью. Режущий инструмент из быстрорежущей стали подвергается закалке и многократному отпуску. * * * БЫСТРОРЕЖУЩАЯ… … Энциклопедический словарь
быстрорежущая сталь — greitapjovis plienas statusas T sritis chemija apibrėžtis Įrankinis plienas, turintis 0,73–1,12% C, 1,50–18,50% W, 1,0–3,0% V, 3,0–4,4% Cr, 0,50–8,50% Co, 1,0–9,0% Mo, nedidelius kiekius Mn, Si, Ni. atitikmenys: angl. high speed steel rus.… … Chemijos terminų aiškinamasis žodynas
БЫСТРОРЕЖУЩАЯ СТАЛЬ — см. в ст. Инструментальная сталь … Большой энциклопедический политехнический словарь
БЫСТРОРЕЖУЩАЯ СТАЛЬ (самопальная) — специальная сталь, основными характерными примесями к рой являются хром (3 4,5%) и вольфрам (11 20%). Иногда вводятся кобальт, ванадий, молибден. Особенность Б. с. состоит в том, что она сохраняет твердость и не теряет режущей способности (не… … Технический железнодорожный словарь
инструментальная быстрорежущая сталь — [high speed tool steel] высоколегированная (W, Mo, V, Co и др.) сталь, обычно содержащая 0,9 1,1 % С и предназначенная для изготовления режущего инструмента, работающего при высокой скорости резания и разогреве контактных поверхностей > 650 750… … Энциклопедический словарь по металлургии
Сталь (сплав железа с углеродом) — Сталь (польск. stal, от нем. Stahl), деформируемый (ковкий) сплав железа с углеродом (до 2%) и др. элементами. С. ‒ важнейший продукт чёрной металлургии, являющийся материальной основой практически всех отраслей промышленности. Масштабы… … Большая советская энциклопедия
Сталь — (Steel) Определение стали, производство и обработка стали, свойства сталей Информация об определении стали, производство и обработка стали, классификация и свойства сталей Содержание Содержание Классификация Характеристики стали Разновидности… … Энциклопедия инвестора
dic.academic.ru
Быстрорежущая сталь — WiKi
Истории создания
Сверло с покрытием из нитрида титанаДля обточки деталей из дерева, цветных металлов, мягкой стали резцы из обычной твердой стали были вполне пригодны, но при обработке стальных деталей резец быстро разогревался, скоро изнашивался и деталь нельзя было обтачивать со скоростью больше 5 м/мин[1].
Барьер этот удалось преодолеть после того, как в 1858 году Р. Мюшетт получил сталь, содержащую 1,85 % углерода, 9 % вольфрама и 2,5 % марганца. Спустя десять лет Мюшетт изготовил новую сталь, получившую название самокалки. Она содержала 2,15 % углерода, 0,38 % марганца, 5,44 % вольфрама и 0,4 % хрома. Через три года на заводе Самуэля Осберна в Шеффилде началось производство мюшеттовой стали. Она не теряла режущей способности при нагревании до 300 °C и позволяла в полтора раза увеличить скорость резания металла — 7,5 м/мин.
Спустя сорок лет на рынке появилась быстрорежущая сталь американских инженеров Тэйлора и Уатта. Резцы из этой стали допускали скорость резания до 18 м/мин. Эта сталь стала прообразом современной быстрорежущей стали Р18.
Ещё через 5—6 лет появилась сверхбыстрорежущая сталь, допускающая скорость резания до 35 м/мин. Так, благодаря вольфраму было достигнуто повышение скорости резания за 50 лет в семь раз и, следовательно, во столько же раз повысилась производительность металлорежущих станков.
Дальнейшее успешное использование вольфрама нашло себе применение в создании твердых сплавов, которые состоят из вольфрама, хрома, кобальта. Были созданы такие сплавы для резцов, как стеллит. Первый стеллит позволял повысить скорость резания до 45 м/мин при температуре 700—750 °C. Сплав вида, выпущенный Круппом в 1927 году, имел твердость по шкале Мооса 9,7—9,9 (твердость алмаза равна 10).
В 1970-х годах в связи с дефицитом вольфрама быстрорежущая сталь марки Р18 была почти повсеместно заменена на сталь марки Р6М5 (так называемый «самокал», самозакаливающаяся сталь), которая, в свою очередь, вытесняется безвольфрамовыми Р0М5Ф1 и Р0М2Ф3.
Характеристики быстрорежущих сталей
Горячая твердость
При нормальной температуре твердость углеродистой стали даже несколько выше твердости быстрорежущей стали. Однако в процессе работы режущего инструмента происходит интенсивное выделение тепла. При этом до 80 % выделившегося тепла уходит на разогрев инструмента. Вследствие повышения температуры режущей кромки начинается отпуск материала инструмента и снижается его твердость.
После нагрева до 200 °C твердость углеродистой стали начинает быстро падать. Для этой стали недопустим режим резания, при котором инструмент нагревался бы выше 200 °C. У быстрорежущей стали высокая твердость сохраняется при нагреве до 500—600 °C. Инструмент из быстрорежущей стали более производителен, чем инструмент из углеродистой стали.
Красностойкость
Если горячая твердость характеризует то, какую температуру сталь может выдержать, то красностойкость характеризует, сколько времени сталь будет выдерживать такую температуру. То есть насколько длительное время закаленная и отпущенная сталь будет сопротивляться разупрочнению при разогреве.
Существует несколько характеристик красностойкости. Приведем две из них.
Первая характеристика показывает, какую твердость будет иметь сталь после отпуска при определенной температуре в течение заданного времени.
Второй способ охарактеризовать красностойкость основан на том, что интенсивность снижения горячей твердости можно измерить не только при высокой температуре, но и при комнатной, так как кривые снижения твердости при высокой температуре и комнатной идут эквидистантно, а измерить твердость при комнатной температуре, разумеется, гораздо проще, чем при высокой. Опытами установлено, что режущие свойства теряются при твердости 50 HRC при температуре резания, что соответствует примерно 58 HRC при комнатной. Отсюда красностойкость характеризуется температурой отпуска, при которой за 4 часа твердость снижается до 58 HRC (обозначение K4р58).
У7, У8, У10, У12 | 150—160 | 1 | |
Р9 | 580 | 4 | |
У7, У8, У10, У12 | 200—220 | 1 | 59 |
Р6М5К5, Р9, Р9М4К8, Р18 | 620—630 | 4 |
Сопротивление разрушению
Кроме «горячих» свойств, от материала для режущего инструмента требуются и высокие механические свойства; под этим подразумевается сопротивление хрупкому разрушению, так как при высокой твердости (более 60 HRC) разрушение всегда происходит по хрупкому механизму. Прочность таких высокотвердых материалов обычно определяют как сопротивление разрушению при изгибе призматических, не надрезанных образцов, при статическом (медленном) и динамическом (быстром) нагружении. Чем выше прочность, тем большее усилие может выдержать рабочая часть инструмента, тем большую подачу и глубину резания можно применить, и это увеличивает производительность процесса резания.
Химический состав быстрорежущих сталей
Р0М2Ф3 | 1,10—1,25 | 3,8—4,6 | — | 2,3—2,9 | 2,6—3,3 | — |
Р6М5 | 0,82—0,90 | 3,8—4,4 | 5,5—6,5 | 4,8—5,3 | 1,7—2,1 | < 0,50 |
Р6М5Ф2К8 | 0,95—1,05 | 3,8—4,4 | 5,5—6,6 | 4,6—5,2 | 1,8—2,4 | 7,5—8,5 |
Р9 | 0,85—0,95 | 3,8—4,4 | 8,5—10,0 | < 1,0 | 2,0—2,6 | — |
Р18 | 0,73—0,83 | 3,8—4,4 | 17,0—18,5 | < 1,0 | 1,0—1,4 | < 0,50 |
Изготовление и обработка быстрорежущих сталей
Быстрорежущие стали изготавливают как классическим способом (разливка стали в слитки, прокатка и проковка), так и методами порошковой металлургии (распыление струи жидкой стали азотом)[3]. Качество быстрорежущей стали в значительной степени определяется степенью её прокованности. При недостаточной проковке изготовленной классическим способом стали наблюдается карбидная ликвация.
При изготовлении быстрорежущих сталей распространенной ошибкой является подход к ней как к «самозакаливающейся стали». То есть достаточно нагреть сталь и охладить на воздухе, и можно получить твердый износостойкий материал. Такой подход абсолютно не учитывает особенности высоколегированных инструментальных сталей.
Перед закалкой быстрорежущие стали необходимо подвергнуть отжигу. В плохо отожженных сталях наблюдается особый вид брака: нафталиновый излом, когда при нормальной твердости стали она обладает повышенной хрупкостью.
Грамотный выбор температуры закалки обеспечивает максимальную растворимость легирующих добавок в α-железе, но не приводит к росту зерна.
После закалки в стали остается 25—30 % остаточного аустенита. Помимо снижения твердости инструмента, остаточный аустенит приводит к снижению теплопроводности стали, что для условий работы с интенсивным нагревом режущей кромки является крайне нежелательным. Снижения количества остаточного аустенита добиваются двумя путями: обработкой стали холодом или многократным отпуском[3]. При обработке стали холодом её охлаждают до −80…−70 °C, затем проводят отпуск. При многократном отпуске цикл «нагрев — выдержка — охлаждение» проводят по 2—3 раза. В обоих случаях добиваются существенного снижения количества остаточного аустенита, однако полностью избавиться от него не получается.
Принципы легирования быстрорежущих сталей
Высокая твердость мартенсита объясняется растворением углерода в α-железе. Известно, что при отпуске из мартенсита в углеродистой стали выделяются мельчайшие частицы карбида. Пока выделившиеся карбиды ещё находятся в мельчайшем дисперсном рассеянии (то есть на первой стадии выделения при отпуске до 200 °C), твердость заметно не снижается. Но если температуру отпуска поднять выше 200 °C, происходит рост карбидных выделений, и твердость падает.
Чтобы сталь устойчиво сохраняла твердость при нагреве, нужно её легировать такими элементами, которые затрудняли бы процесс коагуляции карбидов. Если ввести в сталь какой-нибудь карбидообразующий элемент в таком количестве, что он образует специальный карбид, то красностойкость скачкообразно возрастает. Это обусловлено тем, что специальный карбид выделяется из мартенсита и коагулирует при более высоких температурах, чем карбид железа, так как для этого требуется не только диффузия углерода, но и диффузия легирующих элементов. Практически заметная коагуляция специальных карбидов хрома, вольфрама, молибдена, ванадия происходит при температурах выше 500 °C.
Красностойкость создается легированием стали карбидообразующими элементами (вольфрамом, молибденом, хромом, ванадием) в таком количестве, при котором они связывают почти весь углерод в специальные карбиды, и эти карбиды переходят в раствор при закалке. Несмотря на сильное различие в общем химическом составе, состав твердого раствора очень близок во всех сталях, атомная сумма W+Mo+V, определяющая красностойкость, равна примерно 4 % (атомн.), отсюда красностойкости и режущие свойства у разных марок быстрорежущих сталей близки. Быстрорежущая сталь, содержащая кобальт, превосходит по режущим свойствам остальные стали (он повышает красностойкость), но кобальт очень дорогой элемент.
Маркировка быстрорежущих сталей
В советских и российских марочниках сталей марки быстрорежущих сталей обычно имеют особую систему обозначений и начинаются с буквы «Р» (rapid — быстрый). Связано это с тем, что эти стали были изобретены в Англии, где такую сталь называли «rapid steel». Цифра после буквы «Р» обозначает среднее содержание в ней вольфрама (в процентах от общей массы, буква В пропускается). Затем указывается после букв М, Ф и К содержание молибдена, ванадия и кобальта. Инструменты из быстрорежущей стали иностранного производства обычно маркируются аббревиатурой HSS (High Speed Steel).
Применение
В последние десятилетия использование быстрорежущей стали сокращается в связи с широким распространением твёрдых сплавов. Из быстрорежущей стали изготавливают в основном концевой инструмент (метчики, свёрла, фрезы небольших диаметров) В токарной обработке резцы со сменными и напайными твердосплавными пластинами почти полностью вытеснили резцы из быстрорежущей стали.
По применению отечественных марок быстрорежущих сталей существуют следующие рекомендации.
- Сталь Р9 рекомендуют для изготовления инструментов простой формы, не требующих большого объёма шлифовки, для обработки обычных конструкционных материалов. (резцов, фрез, зенкеров).
- Для фасонных и сложных инструментов (для нарезания резьб и зубьев), для которых основным требованием является высокая износостойкость, рекомендуют использовать сталь Р18 (вольфрамовая).
- Кобальтовые быстрорежущие стали (Р9К5, Р9К10) применяют для обработки деталей из труднообрабатываемых коррозионно-стойких и жаропрочных сталей и сплавов, в условиях прерывистого резания, вибраций, недостаточного охлаждения.
- Ванадиевые быстрорежущие стали (Р9Ф5, Р14Ф4) рекомендуют для изготовления инструментов для чистовой обработки (протяжки, развёртки, шеверы). Их можно применять для обработки труднообрабатываемых материалов при срезании стружек небольшого поперечного сечения.
- Вольфрамомолибденовые стали (Р9М4, Р6М3) используют для инструментов, работающих в условиях черновой обработки, а также для изготовления протяжек, долбяков, шеверов, фрез.
Примечания
- ↑ Мезенин Н. А. Занимательно о железе. — М.: «Металлургия», 1972. — 200 с.
- ↑ Марочник сталей и сплавов / В. Г. Сорокин, А. В. Волосникова, С. А. Вяткин, и др. Под общ. ред. В. Г. Сорокина. — М.: Машиностроение, 1989. — 640 с.
- ↑ 1 2 Гуляев А. П. Металловедение. Учебник для втузов. 6-е изд., перераб. и доп. — М.: «Металлургия», 1986. — 544 с.
Литература
- Технология конструкционных материалов. Под ред. А. М. Дальского. — М.: «Машиностроение», 1958.
Ссылки
ru-wiki.org
Быстрорежущая сталь — Википедия
Быстроре́жущие ста́ли — легированные стали, предназначенные, главным образом, для изготовления металлорежущего инструмента, работающего при высоких скоростях резания.
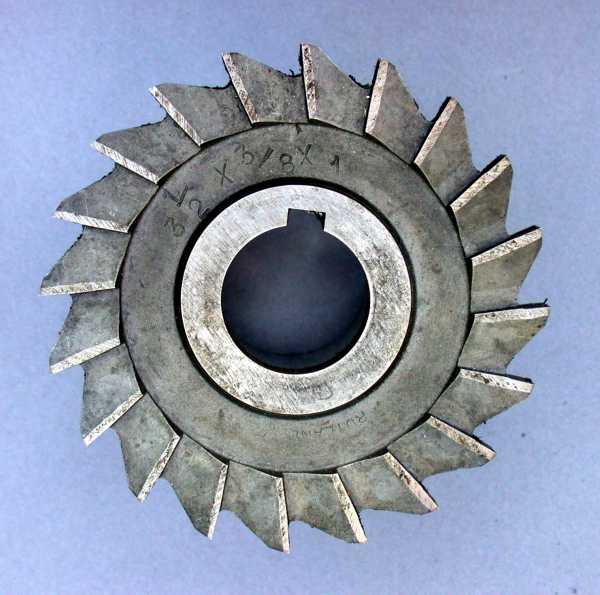
Быстрорежущая сталь должна обладать высоким сопротивлением разрушению, твёрдостью (в холодном и горячем состояниях) и красностойкостью.
Высоким сопротивлением разрушению и твердостью в холодном состоянии обладают и углеродистые инструментальные стали. Однако инструмент из них не в состоянии обеспечить высокоскоростные режимы резания. Легирование быстрорежущих сталей вольфрамом, молибденом, ванадием и кобальтом обеспечивает горячую твердость и красностойкость стали.
Истории создания[править]
Сверло с покрытием из нитрида титанаДля обточки деталей из дерева, цветных металлов, мягкой стали резцы из обычной твердой стали были вполне пригодны, но при обработке стальных деталей резец быстро разогревался, скоро изнашивался и деталь нельзя было обтачивать со скоростью больше 5 м/мин[1].
Барьер этот удалось преодолеть после того, как в 1858 году Р. Мюшетт получил сталь, содержащую 1,85 % углерода, 9 % вольфрама и 2,5 % марганца. Спустя десять лет Мюшетт изготовил новую сталь, получившую название самокалки. Она содержала 2,15 % углерода, 0,38 % марганца, 5,44 % вольфрама и 0,4 % хрома. Через три года на заводе Самуэля Осберна в Шеффилде началось производство мюшеттовой стали. Она не теряла режущей способности при нагревании до 300 °C и позволяла в полтора раза увеличить скорость резания металла — 7,5 м/мин.
Спустя сорок лет на рынке появилась быстрорежущая сталь американских инженеров Тэйлора и Уатта. Резцы из этой стали допускали скорость резания до 18 м/мин. Эта сталь стала прообразом современной быстрорежущей стали Р18.
Еще через 5—6 лет появилась сверхбыстрорежущая сталь, допускающая скорость резания до 35 м/мин. Так, благодаря вольфраму было достигнуто повышение скорости резания за 50 лет в семь раз и, следовательно, во столько же раз повысилась производительность металлорежущих станков.
Дальнейшее успешное использование вольфрама нашло себе применение в создании твердых сплавов, которые состоят из вольфрама, хрома, кобальта. Были созданы такие сплавы для резцов, как стеллит. Первый стеллит позволял повысить скорость резания до 45 м/мин при температуре 700—750 °C. Сплав вида, выпущенный Круппом в 1927 году, имел твердость по шкале Мооса 9,7—9,9 (твердость алмаза равна 10).
В 1970-х годах в связи с дефицитом вольфрама быстрорежущая сталь марки Р18 была почти повсеместно заменена на сталь марки Р6М5 (так называемый "самокал", самозакаливающаяся сталь), которая, в свою очередь, вытесняется безвольфрамовыми Р0М5Ф1 и Р0М2Ф3.
Характеристики быстрорежущих сталей[править]
Горячая твердость[править]
При нормальной температуре твердость углеродистой стали даже несколько выше твердости быстрорежущей стали. Однако в процессе работы режущего инструмента происходит интенсивное выделение тепла. При этом до 80 % выделившегося тепла уходит на разогрев инструмента. Вследствие повышения температуры режущей кромки начинается отпуск материала инструмента и снижается его твердость.
После нагрева до 200 °C твердость углеродистой стали начинает быстро падать. Для этой стали недопустим режим резания, при котором инструмент нагревался бы выше 200 °C. У быстрорежущей стали высокая твердость сохраняется при нагреве до 500—600 °C. Инструмент из быстрорежущей стали более производителен, чем инструмент из углеродистой стали.
Красностойкость[править]
Если горячая твердость характеризует то, какую температуру сталь может выдержать, то красностойкость характеризует, сколько времени сталь будет выдерживать такую температуру. То есть насколько длительное время закаленная и отпущенная сталь будет сопротивляться разупрочнению при разогреве.
Существует несколько характеристик красностойкости. Приведем две из них.
Первая характеристика показывает, какую твердость будет иметь сталь после отпуска при определенной температуре в течение заданного времени.
Второй способ охарактеризовать красностойкость основан на том, что интенсивность снижения горячей твердости можно измерить не только при высокой температуре, но и при комнатной, так как кривые снижения твердости при высокой температуре и комнатной идут эквидистантно, а измерить твердость при комнатной температуре, разумеется, гораздо проще, чем при высокой. Опытами установлено, что режущие свойства теряются при твердости 50 HRC при температуре резания, что соответствует примерно 58 HRC при комнатной. Отсюда красностойкость характеризуется температурой отпуска, при которой за 4 часа твердость снижается до 58 HRC (обозначение K4р58).
У7, У8, У10, У12 | 150—160 | 1 | 63 |
Р9 | 580 | 4 | |
У7, У8, У10, У12 | 200—220 | 1 | 59 |
Р6М5К5, Р9, Р9М4К8, Р18 | 620—630 | 4 |
Сопротивление разрушению Кроме «горячих» свойств, от материала для режущего инструмента требуются и высокие механические свойства; под этим подразумевается сопротивление хрупкому разрушению, так как при высокой твердости (более 60 HRC) разрушение всегда происходит по хрупкому механизму. Прочность таких высокотвердых материалов обычно определяют как сопротивление разрушению при изгибе призматических, не надрезанных образцов, при статическом (медленном) и динамическом (быстром) нагружении. Чем выше прочность, тем большее усилие может выдержать рабочая часть инструмента, тем большую подачу и глубину резания можно применить, и это увеличивает производительность процесса резания.
Химический состав быстрорежущих сталей[править]
Р0М2Ф3 | 1,10—1,25 | 3,8—4,6 | — | 2,3—2,9 | 2,6—3,3 | — |
Р6М5 | 0,82—0,90 | 3,8—4,4 | 5,5—6,5 | 4,8—5,3 | 1,7—2,1 | < 0,50 |
Р6М5Ф2К8 | 0,95—1,05 | 3,8—4,4 | 5,5—6,6 | 4,6—5,2 | 1,8—2,4 | 7,5—8,5 |
Р9 | 0,85—0,95 | 3,8—4,4 | 8,5—10,0 | < 1,0 | 2,0—2,6 | — |
Р18 | 0,73—0,83 | 3,8—4,4 | 17,0—18,5 | < 1,0 | 1,0—1,4 | < 0,50 |
Изготовление и обработка быстрорежущих сталей[править]
Быстрорежущие стали изготавливают как классическим способом (разливка стали в слитки, прокатка и проковка), так и методами порошковой металлургии (распыление струи жидкой стали азотом)[3]. Качество быстрорежущей стали в значительной степени определяется степенью её прокованности. При недостаточной проковке изготовленной классическим способом стали наблюдается карбидная ликвация.
При изготовлении быстрорежущих сталей распространенной ошибкой является подход к ней как к «самозакаливающейся стали». То есть достаточно нагреть сталь и охладить на воздухе, и можно получить твердый износостойкий материал. Такой подход абсолютно не учитывает особенности высоколегированных инструментальных сталей.
Перед закалкой быстрорежущие стали необходимо подвергнуть отжигу. В плохо отожженных сталях наблюдается особый вид брака: нафталиновый излом, когда при нормальной твердости стали она обладает повышенной хрупкостью.
Грамотный выбор температуры закалки обеспечивает максимальную растворимость легирующих добавок в α-железе, но не приводит к росту зерна.
После закалки в стали остается 25—30 % остаточного аустенита. Помимо снижения твердости инструмента, остаточный аустенит приводит к снижению теплопроводности стали, что для условий работы с интенсивным нагревом режущей кромки является крайне нежелательным. Снижения количества остаточного аустенита добиваются двумя путями: обработкой стали холодом или многократным отпуском[3]. При обработке стали холодом её охлаждают до −80…−70 °C, затем проводят отпуск. При многократном отпуске цикл «нагрев — выдержка — охлаждение» проводят по 2—3 раза. В обоих случаях добиваются существенного снижения количества остаточного аустенита, однако полностью избавиться от него не получается.
Принципы легирования быстрорежущих сталей[править]
Высокая твердость мартенсита объясняется растворением углерода в α-железе. Известно, что при отпуске из мартенсита в углеродистой стали выделяются мельчайшие частицы карбида. Пока выделившиеся карбиды еще находятся в мельчайшем дисперсном рассеянии (то есть на первой стадии выделения при отпуске до 200 °C), твердость заметно не снижается. Но если температуру отпуска поднять выше 200 °C, происходит рост карбидных выделений, и твердость падает.
Чтобы сталь устойчиво сохраняла твердость при нагреве, нужно её легировать такими элементами, которые затрудняли бы процесс коагуляции карбидов. Если ввести в сталь какой-нибудь карбидообразующий элемент в таком количестве, что он образует специальный карбид, то красностойкость скачкообразно возрастает. Это обусловлено тем, что специальный карбид выделяется из мартенсита и коагулирует при более высоких температурах, чем карбид железа, так как для этого требуется не только диффузия углерода, но и диффузия легирующих элементов. Практически заметная коагуляция специальных карбидов хрома, вольфрама, молибдена, ванадия происходит при температурах выше 500 °C.
Таким образом, красностойкость создается легированием стали карбидообразующими элементами (вольфрамом, молибденом, хромом, ванадием) в таком количестве, при котором они связывают почти весь углерод в специальные карбиды, и эти карбиды переходят в раствор при закалке. Несмотря на сильное различие в общем химическом составе, состав твердого раствора очень близок во всех сталях, атомная сумма W+Mo+V, определяющая красностойкость, равна примерно 4 % (атомн.), отсюда красностойкости и режущие свойства у разных марок быстрорежущих сталей близки. Быстрорежущая сталь, содержащая кобальт, превосходит по режущим свойствам остальные стали (он повышает красностойкость), но кобальт очень дорогой элемент.
Маркировка быстрорежущих сталей[править]
В советских и Российских марочниках сталей марки быстрорежущих сталей обычно имеют особую систему обозначений и начинаются с буквы «Р» (rapid — быстрый). Связано это с тем, что эти стали были изобретены в Англии, где такую сталь называли «rapid steel». Цифра после буквы «Р» обозначает среднее содержание в ней вольфрама (в процентах от общей массы, буква В пропускается). Затем указывается после букв М, Ф и К содержание молибдена, ванадия и кобальта. Инструменты из быстрорежущей стали иностранного производства обычно маркируются аббревиатурой HSS (High Speed Steel).
В последние десятилетия использование быстрорежущей стали сокращается в связи с широким распространением твёрдых сплавов. Из быстрорежущей стали изготавливают в основном концевой инструмент (метчики, свёрла, фрезы небольших диаметров) В токарной обработке резцы со сменными и напайными твердосплавными пластинами почти полностью вытеснили резцы из быстрорежущей стали.
По применению отечественных марок быстрорежущих сталей существуют следующие рекомендации.
- Сталь Р9 рекомендуют для изготовления инструментов простой формы, не требующих большого объема шлифовки, для обработки обычных конструкционных материалов. (резцов, фрез, зенкеров).
- Для фасонных и сложных инструментов (для нарезания резьб и зубьев), для которых основным требованием является высокая износостойкость, рекомендуют использовать сталь Р18 (вольфрамовая).
- Кобальтовые быстрорежущие стали (Р9К5, Р9К10) применяют для обработки деталей из труднообрабатываемых коррозионно-стойких и жаропрочных сталей и сплавов, в условиях прерывистого резания, вибраций, недостаточного охлаждения.
- Ванадиевые быстрорежущие стали (Р9Ф5, Р14Ф4) рекомендуют для изготовления инструментов для чистовой обработки (протяжки, развёртки, шеверы). Их можно применять для обработки труднообрабатываемых материалов при срезании стружек небольшого поперечного сечения.
- Вольфрамомолибденовые стали (Р9М4, Р6М3) используют для инструментов, работающих в условиях черновой обработки, а также для изготовления протяжек, долбяков, шеверов, фрез.
- ↑ Мезенин Н. А. Занимательно о железе. — М.: «Металлургия», 1972. — 200 с.
- ↑ Марочник сталей и сплавов / В. Г. Сорокин, А. В. Волосникова, С. А. Вяткин, и др. Под общ. ред. В. Г. Сорокина. — М.: Машиностроение, 1989. — 640 с.
- ↑ Ошибка цитирования Неверный тег <ref>; для сносок gul не указан текст
- Гуляев А. П. Металловедение. Учебник для втузов. 6-е изд., перераб. и доп. — М.: «Металлургия», 1986. — 544 с.
- Технология конструкционных материалов. Под ред. А. М. Дальского. — М.: «Машиностроение», 1958.
wp.wiki-wiki.ru
обработка, марки, изготовление сверл и резцов
Существует огромное количество различных металлов, которые обладают своими определенными достоинствами и недостатками. Быстрорежущие стали зачастую применяются для изготовления инструментов, которые должны обладать повышенной прочностью, некоторых ответственных деталей. Рассмотрим особенности этого сплава подробнее.
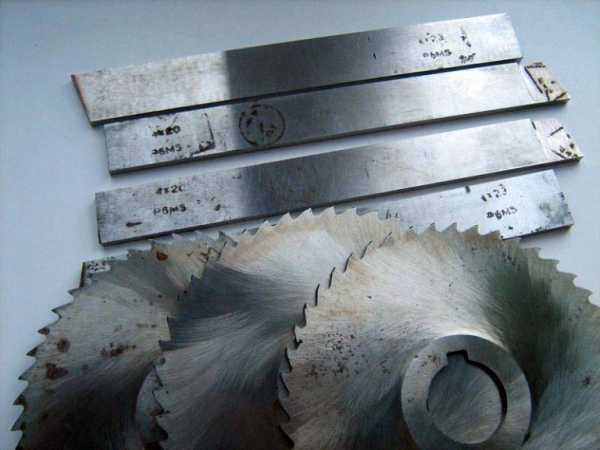
Быстрорежущие стали
Характеристики быстрорежущих сталей
Быстрорежущие стали – сплавы, которые имеют достаточно большое количество легированных добавок. За счет добавления различных химических веществ свойства металла серьезно меняются. Рассматривая характеристики следует отметить, что материал подобного типа специально создается для эксплуатации при высоком показателе трения, который возникает на момент резания. Состав быстрорежущей инструментальной стали существенно повышает твердость металла, за счет чего он может работать на повышенной скорости.
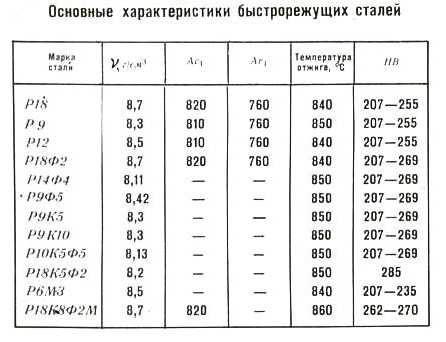
Основные характеристики быстрорежущих сталей
Характеристики быстрорежущей стали следующие:
- Высокая твердость. Рассматривая основное назначение подобного металла следует учитывать, что он может использоваться для обработки деталей или заготовок путем резания. Как показывают проведенные тесты, качественная быстрорежущая сталь сохраняет свои основные эксплуатационные качества при нагреве инструмента даже до температуры 6000 градусов Цельсия. Кроме этого быстрорежущая сталь обычного качества может иметь даже меньшую твердость в сравнении с обычным углеродистым металлом.
- Повышенная стойкость к высокой температуре. Устойчивость к воздействию повышенной температуры определяет то, как долго инструмент сможет работать без изменения своих эксплуатационных качеств. Из-за слишком высокого показателя трения металл может нагреваться, что становится причиной изменения кристаллической решетки. В результате основные свойства быстрорежущей стали могут существенно измениться. Как правило, нагрев становится причиной повышения пластичности и снижения твердости, за счет чего износ поверхности проходит намного быстрее.
- Устойчивость к разрушению. Режущий инструмент, который может работать на высокой скорости, должен обладать повышенной механической устойчивостью. Кроме этого инструмент может работать при высоком показателе подачи, что позволяет работать на большой глубине резания.
Именно химический состав быстрорежущей стали определяет ее основные эксплуатационные качества.
Классификация и маркировка быстрорежущих сталей
Все быстрорежущие стали классифицируются непосредственно по химическому составу, для чего проводится расшифровка маркировки. Инструментальные стали быстрорежущие делятся на следующие три группы:
- Сплавы с полезными примесями, в которых процентное содержание кобальта не более 10%, а вольфрама 22%. Маркировка металла этой группы следующая: P10M4Ф3К10 и Р6М5Ф2К8 и другие.
- Сплавы, в составе которых не более 5% кобальта и до 18% вольфрама. Виды быстрорежущей стали этой группы следующие: Р9К5, Р10Ф5К5 и другие.
- Варианты исполнения металла, расшифровка которых определяет процентное содержание кобальта и вольфрама более 16%. Представителями этой группы можно назвать марки Р9 и Р18, Р12 и Р6М5.
При применении подобного металла получающаяся кромка не реагирует на механическое воздействие, по всей длине показатель твердости остается неизменным и металл не выкрашивается. Вышеприведенная классификация быстрорежущей стали определяет то, при какой скорости резания и подаче может использоваться сплав.
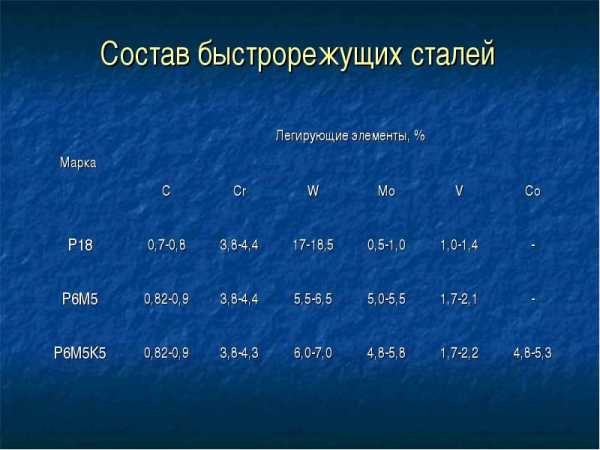
Состав быстрорежущих сталей различных марок
Рассматривая обозначение быстрорежущей стали следует уделить внимание тому, что первая буква для обозначения этой группы «Р». Цифра, которая идет первой в обозначении указывает процесс вольфрама в составе. Далее могут идти буквы, обозначающие легирующие элементы. Стоит учитывать, что расшифровка металла указывает на точное содержание определенных легирующих элементов, которые изменяют эксплуатационные качества материала.
Область применения различных марок быстрорежущих сталей
Рассматривая применение износостойкого металла следует уделить внимание тому, что конкретный состав металла определяет его эксплуатационные качества. Инструмент изготовленный из подобного металла может выдерживать длительную эксплуатацию.
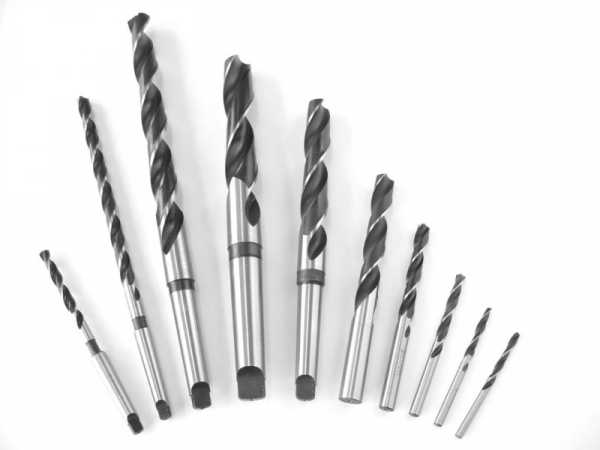
Режущий инструмент из быстрорежущей стали
Область применения достаточно обширна:
- Изготовление сверл. Сверла имеют достаточно сложную форму и конструкцию, которая получается путем литья.
- Изготовление резцов. Сегодня для удешевления резцов их основная часть изготавливается из недорого металла, и только режущая кромка из износостойкого материала.
- Изготовление напаек для режущего инструмента. В некоторые случаях режущая кромка сменная.
- Изготовление фрез. Фрезы также получаются методом литья расплавленного металла.
Материал может использоваться для получения инструмента, который будет выдерживать высокую нагрузку.
Сегодня, при повсеместной установке станков с ЧПУ, режущий инструмент повышенной устойчивости является единственным выходом из сложившейся ситуации, когда высокие скорости обработки создают проблемы.
Особенности термической обработки быстрорежущих сталей
Для увеличения эксплуатационных качеств быстрорежущей стали могут применяться стандартные методы обработки. Однако при этом учитывается состав металла. Примером назовем то, что процесс закалки предусматривает нагрев среды до температуры, которая позволяет обеспечить условия для растворения различных примесей и добавок.
После того, как обработка быстрорежущей стали была завершена, в сплаве остается до 30% аустенита, что существенно повышает теплопроводность и твердость.
Для уменьшения показателя аустенита в структуре могут применяться две технологии:
- Для повышения качества термической обработки нагрев проводится в несколько этапов. При этом выдержка проводится при определенной температуре, а также проводится многократный отпуск.
- Отпуск подразумевает охлаждение заготовки до низкой температуры, которая часто составляет — 800 градусов Цельсия.
- Закалка должна проводится при достаточно высокой температуре, так как только в этом случае происходит полное перестроение кристаллической решетки.
- Для охлаждения используется самая различная среда. Примером назовем применение масла иди соляных ванн. Обычная вода становится причиной появления самых различных дефектов, к примеру, трещин или окалин. После этого приходится выполнять дополнительную обработку для удаления дефектов.
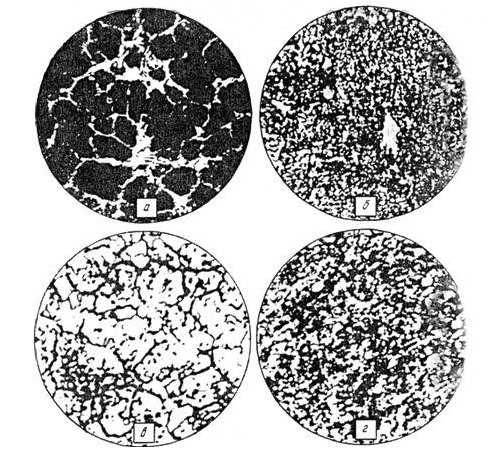
Микроструктура быстрорежущей стали Р6М5: а) литое состояние; б) после ковки и отжига; в) после закалки; г) после отпуска
Кроме этого улучшение характеристик проводится следующим образом:
- Проводится насыщение поверхностного слоя цинком. Для того чтобы оказать требуемое воздействие на поверхность подобная операция предусматривает нагрев поверхности до 5600 градусов Цельсия. Выдержка может проходить в течение от 5 до 30 минут.
- Также может происходить насыщение поверхности азотом. Чаще всего подобная процедура проводится в газовой среде. Выдерживается заготовка или деталь в течении 10-40 минут, температура нагрева варьирует в пределе 550-6600 градусов Цельсия.
- В некоторых случаях химический состав металла изменяется путем сульфидирования поверхности. Подобным образом можно повысить твердость и прочность поверхности.
- В качестве дополнительной обработки на поверхность напыляется различный материал. За счет этого существенно изменяются эксплуатационные качества инструмента или детали.
Сегодня часто встречается ситуация, когда поверхность обрабатывается паром, что позволяет существенно повысить характеристики поверхностного слоя. Зачастую дополнительная обработка проводится в случае, когда режущая кромка была полностью подготовлена.
Если вы нашли ошибку, пожалуйста, выделите фрагмент текста и нажмите Ctrl+Enter.
stankiexpert.ru
Быстрорежущая сталь Википедия
Быстроре́жущие ста́ли — легированные стали, предназначенные, главным образом, для изготовления металлорежущего инструмента, работающего при высоких скоростях резания.
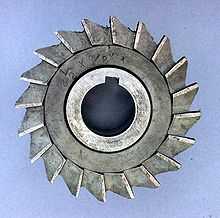
Быстрорежущая сталь должна обладать высокими сопротивлением разрушению, твёрдостью (в холодном и горячем состояниях) и красностойкостью.
Высокими сопротивлением разрушению и твердостью в холодном состоянии обладают и углеродистые инструментальные стали. Однако инструмент из них не в состоянии обеспечить высокоскоростные режимы резания. Легирование быстрорежущих сталей вольфрамом, молибденом, ванадием и кобальтом обеспечивает горячую твердость и красностойкость стали.
Истории создания
Сверло с покрытием из нитрида титанаДля обточки деталей из дерева, цветных металлов, мягкой стали резцы из обычной твердой стали были вполне пригодны, но при обработке стальных деталей резец быстро разогревался, скоро изнашивался и деталь нельзя было обтачивать со скоростью больше 5 м/мин[1].
Барьер этот удалось преодолеть после того, как в 1858 году Р. Мюшетт получил сталь, содержащую 1,85 % углерода, 9 % вольфрама и 2,5 % марганца. Спустя десять лет Мюшетт изготовил новую сталь, получившую название самокалки. Она содержала 2,15 % углерода, 0,38 % марганца, 5,44 % вольфрама и 0,4 % хрома. Через три года на заводе Самуэля Осберна в Шеффилде началось производство мюшеттовой стали. Она не теряла режущей способности при нагревании до 300 °C и позволяла в полтора раза увеличить скорость резания металла — 7,5 м/мин.
Спустя сорок лет на рынке появилась быстрорежущая сталь американских инженеров Тэйлора и Уатта. Резцы из этой стали допускали скорость резания до 18 м/мин. Эта сталь стала прообразом современной быстрорежущей стали Р18.
Ещё через 5—6 лет появилась сверхбыстрорежущая сталь, допускающая скорость резания до 35 м/мин. Так, благодаря вольфраму было достигнуто повышение скорости резания за 50 лет в семь раз и, следовательно, во столько же раз повысилась производительность металлорежущих станков.
Дальнейшее успешное использование вольфрама нашло себе применение в создании твердых сплавов, которые состоят из вольфрама, хрома, кобальта. Были созданы такие сплавы для резцов, как стеллит. Первый стеллит позволял повысить скорость резания до 45 м/мин при температуре 700—750 °C. Сплав вида, выпущенный Круппом в 1927 году, имел твердость по шкале Мооса 9,7—9,9 (твердость алмаза равна 10).
В 1970-х годах в связи с дефицитом вольфрама быстрорежущая сталь марки Р18 была почти повсеместно заменена на сталь марки Р6М5 (так называемый «самокал», самозакаливающаяся сталь), которая, в свою очередь, вытесняется безвольфрамовыми Р0М5Ф1 и Р0М2Ф3.
Характеристики быстрорежущих сталей
Горячая твердость
При нормальной температуре твердость углеродистой стали даже несколько выше твердости быстрорежущей стали. Однако в процессе работы режущего инструмента происходит интенсивное выделение тепла. При этом до 80 % выделившегося тепла уходит на разогрев инструмента. Вследствие повышения температуры режущей кромки начинается отпуск материала инструмента и снижается его твердость.
После нагрева до 200 °C твердость углеродистой стали начинает быстро падать. Для этой стали недопустим режим резания, при котором инструмент нагревался бы выше 200 °C. У быстрорежущей стали высокая твердость сохраняется при нагреве до 500—600 °C. Инструмент из быстрорежущей стали более производителен, чем инструмент из углеродистой стали.
Красностойкость
Если горячая твердость характеризует то, какую температуру сталь может выдержать, то красностойкость характеризует, сколько времени сталь будет выдерживать такую температуру. То есть насколько длительное время закаленная и отпущенная сталь будет сопротивляться разупрочнению при разогреве.
Существует несколько характеристик красностойкости. Приведем две из них.
Первая характеристика показывает, какую твердость будет иметь сталь после отпуска при определенной температуре в течение заданного времени.
Второй способ охарактеризовать красностойкость основан на том, что интенсивность снижения горячей твердости можно измерить не только при высокой температуре, но и при комнатной, так как кривые снижения твердости при высокой температуре и комнатной идут эквидистантно, а измерить твердость при комнатной температуре, разумеется, гораздо проще, чем при высокой. Опытами установлено, что режущие свойства теряются при твердости 50 HRC при температуре резания, что соответствует примерно 58 HRC при комнатной. Отсюда красностойкость характеризуется температурой отпуска, при которой за 4 часа твердость снижается до 58 HRC (обозначение K4р58).
У7, У8, У10, У12 | 150—160 | 1 | 63 |
Р9 | 580 | 4 | |
У7, У8, У10, У12 | 200—220 | 1 | 59 |
Р6М5К5, Р9, Р9М4К8, Р18 | 620—630 | 4 |
Сопротивление разрушению
Кроме «горячих» свойств, от материала для режущего инструмента требуются и высокие механические свойства; под этим подразумевается сопротивление хрупкому разрушению, так как при высокой твердости (более 60 HRC) разрушение всегда происходит по хрупкому механизму. Прочность таких высокотвердых материалов обычно определяют как сопротивление разрушению при изгибе призматических, не надрезанных образцов, при статическом (медленном) и динамическом (быстром) нагружении. Чем выше прочность, тем большее усилие может выдержать рабочая часть инструмента, тем большую подачу и глубину резания можно применить, и это увеличивает производительность процесса резания.
Химический состав быстрорежущих сталей
Р0М2Ф3 | 1,10—1,25 | 3,8—4,6 | — | 2,3—2,9 | 2,6—3,3 | — |
Р6М5 | 0,82—0,90 | 3,8—4,4 | 5,5—6,5 | 4,8—5,3 | 1,7—2,1 | < 0,50 |
Р6М5Ф2К8 | 0,95—1,05 | 3,8—4,4 | 5,5—6,6 | 4,6—5,2 | 1,8—2,4 | 7,5—8,5 |
Р9 | 0,85—0,95 | 3,8—4,4 | 8,5—10,0 | < 1,0 | 2,0—2,6 | — |
Р18 | 0,73—0,83 | 3,8—4,4 | 17,0—18,5 | < 1,0 | 1,0—1,4 | < 0,50 |
Изготовление и обработка быстрорежущих сталей
Быстрорежущие стали изготавливают как классическим способом (разливка стали в слитки, прокатка и проковка), так и методами порошковой металлургии (распыление струи жидкой стали азотом)[3]. Качество быстрорежущей стали в значительной степени определяется степенью её прокованности. При недостаточной проковке изготовленной классическим способом стали наблюдается карбидная ликвация.
При изготовлении быстрорежущих сталей распространенной ошибкой является подход к ней как к «самозакаливающейся стали». То есть достаточно нагреть сталь и охладить на воздухе, и можно получить твердый износостойкий материал. Такой подход абсолютно не учитывает особенности высоколегированных инструментальных сталей.
Перед закалкой быстрорежущие стали необходимо подвергнуть отжигу. В плохо отожженных сталях наблюдается особый вид брака: нафталиновый излом, когда при нормальной твердости стали она обладает повышенной хрупкостью.
Грамотный выбор температуры закалки обеспечивает максимальную растворимость легирующих добавок в α-железе, но не приводит к росту зерна.
После закалки в стали остается 25—30 % остаточного аустенита. Помимо снижения твердости инструмента, остаточный аустенит приводит к снижению теплопроводности стали, что для условий работы с интенсивным нагревом режущей кромки является крайне нежелательным. Снижения количества остаточного аустенита добиваются двумя путями: обработкой стали холодом или многократным отпуском[3]. При обработке стали холодом её охлаждают до −80…−70 °C, затем проводят отпуск. При многократном отпуске цикл «нагрев — выдержка — охлаждение» проводят по 2—3 раза. В обоих случаях добиваются существенного снижения количества остаточного аустенита, однако полностью избавиться от него не получается.
Принципы легирования быстрорежущих сталей
Высокая твердость мартенсита объясняется растворением углерода в α-железе. Известно, что при отпуске из мартенсита в углеродистой стали выделяются мельчайшие частицы карбида. Пока выделившиеся карбиды ещё находятся в мельчайшем дисперсном рассеянии (то есть на первой стадии выделения при отпуске до 200 °C), твердость заметно не снижается. Но если температуру отпуска поднять выше 200 °C, происходит рост карбидных выделений, и твердость падает.
Чтобы сталь устойчиво сохраняла твердость при нагреве, нужно её легировать такими элементами, которые затрудняли бы процесс коагуляции карбидов. Если ввести в сталь какой-нибудь карбидообразующий элемент в таком количестве, что он образует специальный карбид, то красностойкость скачкообразно возрастает. Это обусловлено тем, что специальный карбид выделяется из мартенсита и коагулирует при более высоких температурах, чем карбид железа, так как для этого требуется не только диффузия углерода, но и диффузия легирующих элементов. Практически заметная коагуляция специальных карбидов хрома, вольфрама, молибдена, ванадия происходит при температурах выше 500 °C.
Красностойкость создается легированием стали карбидообразующими элементами (вольфрамом, молибденом, хромом, ванадием) в таком количестве, при котором они связывают почти весь углерод в специальные карбиды, и эти карбиды переходят в раствор при закалке. Несмотря на сильное различие в общем химическом составе, состав твердого раствора очень близок во всех сталях, атомная сумма W+Mo+V, определяющая красностойкость, равна примерно 4 % (атомн.), отсюда красностойкости и режущие свойства у разных марок быстрорежущих сталей близки. Быстрорежущая сталь, содержащая кобальт, превосходит по режущим свойствам остальные стали (он повышает красностойкость), но кобальт очень дорогой элемент.
Маркировка быстрорежущих сталей
В советских и российских марочниках сталей марки быстрорежущих сталей обычно имеют особую систему обозначений и начинаются с буквы «Р» (rapid — быстрый). Связано это с тем, что эти стали были изобретены в Англии, где такую сталь называли «rapid steel». Цифра после буквы «Р» обозначает среднее содержание в ней вольфрама (в процентах от общей массы, буква В пропускается). Затем указывается после букв М, Ф и К содержание молибдена, ванадия и кобальта. Инструменты из быстрорежущей стали иностранного производства обычно маркируются аббревиатурой HSS (High Speed Steel).
Применение
В последние десятилетия использование быстрорежущей стали сокращается в связи с широким распространением твёрдых сплавов. Из быстрорежущей стали изготавливают в основном концевой инструмент (метчики, свёрла, фрезы небольших диаметров) В токарной обработке резцы со сменными и напайными твердосплавными пластинами почти полностью вытеснили резцы из быстрорежущей стали.
По применению отечественных марок быстрорежущих сталей существуют следующие рекомендации.
- Сталь Р9 рекомендуют для изготовления инструментов простой формы, не требующих большого объёма шлифовки, для обработки обычных конструкционных материалов. (резцов, фрез, зенкеров).
- Для фасонных и сложных инструментов (для нарезания резьб и зубьев), для которых основным требованием является высокая износостойкость, рекомендуют использовать сталь Р18 (вольфрамовая).
- Кобальтовые быстрорежущие стали (Р9К5, Р9К10) применяют для обработки деталей из труднообрабатываемых коррозионно-стойких и жаропрочных сталей и сплавов, в условиях прерывистого резания, вибраций, недостаточного охлаждения.
- Ванадиевые быстрорежущие стали (Р9Ф5, Р14Ф4) рекомендуют для изготовления инструментов для чистовой обработки (протяжки, развёртки, шеверы). Их можно применять для обработки труднообрабатываемых материалов при срезании стружек небольшого поперечного сечения.
- Вольфрамомолибденовые стали (Р9М4, Р6М3) используют для инструментов, работающих в условиях черновой обработки, а также для изготовления протяжек, долбяков, шеверов, фрез.
Примечания
- ↑ Мезенин Н. А. Занимательно о железе. — М.: «Металлургия», 1972. — 200 с.
- ↑ Марочник сталей и сплавов / В. Г. Сорокин, А. В. Волосникова, С. А. Вяткин, и др. Под общ. ред. В. Г. Сорокина. — М.: Машиностроение, 1989. — 640 с.
- ↑ 1 2 Гуляев А. П. Металловедение. Учебник для втузов. 6-е изд., перераб. и доп. — М.: «Металлургия», 1986. — 544 с.
Литература
- Технология конструкционных материалов. Под ред. А. М. Дальского. — М.: «Машиностроение», 1958.
Ссылки
wikiredia.ru
Быстрорежущая сталь - основа инструментальных материалов
Автор: редакционная статья
Категории: металлообработка
Определение. История. Характеристики. Применение.
Быстрорежущая сталь
Быстрорежущие стали — легированные стали, предназначенные, главным образом, для изготовления металлорежущего инструмента, работающего при высоких скоростях резания.
Быстрорежущая сталь должна обладать высоким сопротивлением разрушению, твёрдостью (в холодном и горячем состояниях) и красностойкостью.Высоким сопротивлением разрушению и твердостью в холодном состоянии обладают и углеродистые инструментальные стали. Однако инструмент из них не в состоянии обеспечить высокоскоростные режимы резания. Легирование быстрорежущих сталей вольфрамом, молибденом, ванадием и кобальтом обеспечивает горячую твердость и красностойкость стали.
Истории создания
Для обточки деталей из дерева, цветных металлов, мягкой стали резцы из обычной твердой стали были вполне пригодны, но при обработке стальных деталей резец быстро разогревался, скоро изнашивался и деталь нельзя было обтачивать со скоростью больше 5 м/м.Барьер этот удалось преодолеть после того, как в 1858 году Р. Мюшетт получил сталь, содержащую 1,85 % углерода, 9 % вольфрама и 2,5 % марганца. Спустя десять лет Мюшетт изготовил новую сталь, получившую название самокалки. Она содержала 2,15 % углерода, 0,38 % марганца, 5,44 % вольфрама и 0,4 % хрома. Через три года на заводе Самуэля Осберна в Шеффилде началось производство мюшеттовой стали. Она не теряла режущей способности при нагревании до 300 °C и позволяла в полтора раза увеличить скорость резания металла — 7,5 м/мин.Спустя сорок лет на рынке появилась быстрорежущая сталь американских инженеров Тэйлора и Уатта. Резцы из этой стали допускали скорость резания до 18 м/мин. Эта сталь стала прообразом современной быстрорежущей стали Р18.Еще через 5—6 лет появилась, сверхбыстрорежущая сталь, допускающая скорость резания до 35 м/мин. Так, благодаря вольфраму было достигнуто повышение скорости резания за 50 лет в семь раз и, следовательно, во столько же раз повысилась производительность металлорежущих станков.Дальнейшее успешное использование вольфрама нашло себе применение в создании твердых сплавов, которые состоят из вольфрама, хрома, кобальта. Были созданы такие сплавы для резцов, как стеллит. Первый стеллит позволял повысить скорость резания до 45 м/мин при температуре 700—750 °C. Сплав вида, выпущенный Круппом в 1927 году, имел твердость по шкале Мооса 9,7—9,9 (твердость алмаза равна 10).В 1970-х годах в связи с дефицитом вольфрама быстрорежущая сталь марки Р18 была почти повсеместно заменена на сталь марки Р6М5, которая в свою очередь вытесняется безвольфрамовыми Р0М5Ф1 и Р0М2Ф3.
Характеристики быстрорежущих сталей
Горячая твердость
Твердость инструментальных сталей при повышенных температурахНа рисунке приведены кривые, характеризующие твердость углеродистой и быстрорежущей инструментальных сталей при повышенных температурах испытаний. При нормальной температуре твердость углеродистой стали даже несколько выше твердости быстрорежущей стали. Однако, в процессе работы режущего инструмента, происходит интенсивное выделение тепла. При этом до 80 % выделившегося тепла уходит на разогрев инструмента. Вследствие повышения температуры режущей кромки начинается >отпуск материала инструмента и снижается его твердость.После нагрева до 200 °C твердость углеродистой стали начинает быстро падать. Для этой стали недопустим режим резания, при котором инструмент нагревался бы выше 200 °C. У быстрорежущей стали высокая твердость сохраняется при нагреве до 500—600 °C. Инструмент из быстрорежущей стали более производителен, чем инструмент из углеродистой стали.
Красностойкость
Если горячая твердость характеризует то, какую температуру сталь может выдержать, то красностойкость характеризует, сколько времени сталь будет выдерживать такую температуру. То есть насколько длительное времязакаленная и отпущенная сталь будет сопротивляться разупрочнению при разогреве.Существует несколько характеристик красностойкости. Приведем две из них.Первая характеристика показывает, какую твердость будет иметь сталь после отпуска при определенной температуре в течение заданного времени.Второй способ охарактеризовать красностойкость основан на том, что интенсивность снижения горячей твердости можно измерить не только при высокой температуре, но и при комнатной так как кривые снижения твердости при высокой температуре и комнатной идут эквидистантно, а измерить твердость при комнатной температуре, разумеется, гораздо проще, чем при высокой. Опытами установлено, что режущие свойства теряются при твердости 50 HRC при температуре резания, что соответствует примерно 58 HRC при комнатной. Отсюда красностойкость характеризуется температурой отпуска, при которой за 4 часа твердость снижается до 58 HRC.
Характеристики теплостойкости углеродистых и красностойкости быстрорежущих инструментальных сталей | |||
Марка стали | Температура отпуска, °C | Время выдержки, час | Твердость, HRCэ |
У7, У8, У10, У12 | 150—160 | 1 | 63 |
Р9 | 580 | 4 | |
У7, У8, У10, У12 | 200—220 | 1 | 59 |
Р6М5К5, Р9, Р9М4К8, Р18 | 620—630 | 4 |
Сопротивление разрушению
Кроме «горячих» свойств от материала для режущего инструмента требуются и высокие механические свойства; под этим подразумевается сопротивление хрупкому разрушению, так как при высокой твердости (более 60 HRC) разрушение всегда происходит по хрупкому механизму. Прочность таких высокотвердых материалов обычно определяют как сопротивление разрушению при изгибе призматических, не надрезанных образцов, при статическом (медленном) и динамическом (быстром) нагружении. Чем выше прочность, тем большее усилие может выдержать рабочая часть инструмента, тем большую подачу и глубину резания можно применить, и это увеличивает производительность процесса резания.Химический состав быстрорежущих сталей
Химический состав некоторых быстрорежущих сталей | ||||||
Марка стали | C | Cr | W | Mo | V | Co |
Р0М2Ф3 | 1,10—1,25 | 3,8—4,6 | — | 2,3—2,9 | 2,6—3,3 | — |
Р6М5 | 0,82—0,90 | 3,8—4,4 | 5,5—6,5 | 4,8—5,3 | 1,7—2,1 | < 0,50 |
Р6М5Ф2К8 | 0,95—1,05 | 3,8—4,4 | 5,5—6,6 | 4,6—5,2 | 1,8—2,4 | 7,5—8,5 |
Р9 | 0,85—0,95 | 3,8—4,4 | 8,5—10,0 | < 1,0 | 2,0—2,6 | — |
Р18 | 0,73—0,83 | 3,8—4,4 | 17,0—18,5 | < 1,0 | 1,0—1,4 | < 0,50 |
Изготовление и обработка быстрорежущих сталей
Быстрорежущие стали изготавливают как классическим способом (разливка стали в слитки, прокатка и проковка), так и методами порошковой металлургии (распыление струи жидкой стали азотом). Качество быстрорежущей стали в значительной степени определяется степенью ее прокованности. При недостаточной проковке изготовленной классическим способом стали наблюдается карбидная ликвация.При изготовлении быстрорежущих сталей распространенной ошибкой является подход к ней как к «самозакаливающейся стали». То есть достаточно нагреть сталь и охладить на воздухе, и можно получить твердый износостойкий материал. Такой подход абсолютно не учитывает особенности высоколегированных инструментальных сталей.Перед закалкой быстрорежущие стали необходимо подвергнуть отжигу. В плохо отожженных сталях наблюдается особый вид брака: нафталиновый излом, когда при нормальной твердости стали она обладает повышенной хрупкостью.Грамотный выбор температуры закалки обеспечивает максимальную растворимость легирующих добавок в α-железе, но не приводит к росту зерна.После закалки в стали остается 25—30 % остаточного аустенита. Помимо снижения твердости инструмента, остаточный аустенит приводит к снижению теплопроводностистали, что для условий работы с интенсивным нагревом режущей кромки является крайне нежелательным. Снижения количества остаточного аустенита добиваются двумя путями: обработкой стали холодом или многократным отпуском. При обработке стали холодом ее охлаждают до −80…−70 °C, затем проводят отпуск. При многократном отпуске цикл «нагрев — выдержка — охлаждение» проводят по 2—3 раза. В обоих случаях добиваются существенного снижения количества остаточногоаустенита, однако полностью избавиться от него не получается.
Принципы легирования быстрорежущих сталей
Высокая твердость мартенсита объясняется растворением углерода в α-железе. Известно, что при отпуске из мартенсита в углеродистой стали выделяются мельчайшие частицы карбида. Пока выделившиеся карбиды еще находятся в мельчайшем дисперсном рассеянии (то есть на первой стадии выделения при отпуске до 200 °C), твердость заметно не снижается. Но если температуру отпуска поднять выше 200 °C, происходит рост карбидных выделений, и твердость падает.Чтобы сталь устойчиво сохраняла твердость при нагреве, нужно ее легировать такими элементами, которые затрудняли бы процесс коагуляции карбидов. Если ввести в сталь какой-нибудь карбидообразующий элемент в таком количестве, что он образует специальный карбид, то красностойкость скачкообразно возрастает. Это обусловлено тем, что специальный карбид выделяется из мартенсита и коагулирует при более высоких температурах, чем карбид железа, так как для этого требуется не только диффузия углерода, но и диффузия легирующих элементов. Практически заметная коагуляция специальных карбидов хрома, вольфрама, молибдена, ванадияпроисходит при температурах выше 500 °C.Таким образом, красностойкость создается легированием стали карбидообразующими элементами (вольфрамом, молибденом, хромом, ванадием) в таком количестве, при котором они связывают почти весь углерод в специальные карбиды и эти карбиды переходят в раствор при закалке. Несмотря на сильное различие в общем химическом составе, состав твердого раствора очень близок во всех сталях, атомная сумма W+Mo+V, определяющая красностойкость, равна примерно 4 % (атомн.), отсюда красностойкости и режущие свойства у разных марок быстрорежущих сталей близки. Быстрорежущая сталь, содержащая кобальт, превосходит по режущим свойствам остальные стали (он повышает красностойкость), но кобальт очень дорогой элемент.
Маркировка быстрорежущих сталей
В советских и российских марочниках сталей марки быстрорежущих сталей обычно имеют особую систему обозначений и начинаются с буквы «Р» (rapid — быстрый). Связанно это с тем, что эти стали были изобретены в Англии, где такую сталь называли «rapid steel». Цифра после буквы «Р» обозначает среднее содержание в ней вольфрама (в процентах от общей массы, буква В пропускается). Затем указывается после букв М, Ф и К содержание молибдена, ванадия и кобальта. Инструменты из быстрорежущей стали иностранного производства обычно маркируются аббревиатурой HSS (High Speed Steel).
Применение
В последние десятилетия использование быстрорежущей стали сокращается в связи с широким распространением твёрдых сплавов. Из быстрорежущей стали изготавливают в основном концевой инструмент (метчики, свёрла, фрезы небольших диаметров) В токарной обработке резцы со сменными и напайными твердосплавными пластинами почти полностью вытеснили резцы из быстрорежущей стали.По применению отечественных марок быстрорежущих сталей существуют следующие рекомендации.
- Сталь Р9 рекомендуют для изготовления инструментов простой формы не требующих большого объема шлифовки, для обработки обычных конструкционных материалов. (резцов, фрез, зенкеров).
- Для фасонных и сложных инструментов (для нарезания резьб и зубьев), для которых основным требованием является высокая износостойкость, рекомендуют использовать сталь Р18 (вольфрамовая).
- Кобальтовые быстрорежущие стали (Р9К5, Р9К10) применяют для обработки деталей из труднообрабатываемых коррозионно-стойких и жаропрочных сталей и сплавов, в условиях прерывистого резания, вибраций, недостаточного охлаждения.
- Ванадиевые быстрорежущие стали (Р9Ф5, Р14Ф4) рекомендуют для изготовления инструментов для чистовой обработки (протяжки, развёртки, шеверы). Их можно применять для обработки труднообрабатываемых материалов при срезании стружек небольшого поперечного сечения.
- Вольфрамомолибденовые стали (Р9М4, Р6М3) используют для инструментов, работающих в условиях черновой обработки, а также для изготовления протяжек, долбяков, шеверов, фрез.
www.metaljournal.com.ua
← Вернуться в оглавление БЫСТРОРЕЖУЩАЯ СТАЛЬТеплостойкие стали высокой твердости, называемые быстрорежущими или быстрорезами, – группа высоколегированных инструментальных сталей, которые благодаря составу и специальным режимам термообработки на вторичную твердость имеют очень высокое иносо- и красностойкость(до 550 – 600°С). Они сочетают теплостойкость (600-700˚С) с высокой твердостью (HRC 63-70) и повышенным сопротивлением пластической деформации. В результате применениябыстрорежущих сталей стало возможным увеличить скорость резания в 2-4 раза (а более новых сталей с интерметаллидным упрочнением даже в 5-6 раз) и повысить стойкость инструментов в 10-40 и более раз по сравнению с получаемыми для инструментов из нетеплостойких сталей. Эти преимущества проявляются при резании: с повышенной скоростью, т.е. в условиях нагрева режущей кромки, или при меньшей скорости, но с высоким давлением. Для понимания особенностей свойств и области использования их важно, что снижение их твердости на HRC 2-4 по сравнению с получаемой максимальной может сопровождаться ухудшением вязкости, прочности и износостойкости. Быстрорежущая сталь необходима в использовании в состоянии высокой твердости и при работе без больших динамических нагрузок. Теплостойкость быстрореза создается специальным легированием и закалкой с очень высоких температур: 1200-1300˚С. Основные легирующие элементы – вольфрам или вольфрам вместе с молибденом. Многочисленные быстрорежущие стали целесообразно различать по главному свойству: умеренной, повышенной и высокой теплостойкости. Стали умеренной и повышенной теплостойкости имеют относительно высокое содержание углерода (≥0,6-0,7%) и одинаковую природу упрочнения; вторичная твердость создается выделением карбидов при отпуске. Быстрорежущая сталь умеренной теплостойкости сохраняют твердость HRC 60 после нагрева (4ч) до 615-620˚С. Они пригодны для резания сталей и чугунов с твердостью до HB 250-280, т.е. большинства конструкционных материалов, и используются наиболее широко (78-80% от общего производства быстрорежущих сталей). Характерными представителями этой группы являются стали Р18 и более рационально легированные: вольфрамовые (сталь Р12) и вольфрамомолибденовые (сталь Р6М5). Стали повышенной теплостойкости имеют высокое содержание или углерода (азота) или же их легируют дополнительно кобальтом. Они сохраняют твердость HRC 60 после нагрева 630-650˚С. Стойкость инструментов при правильном использовании этих сталей в 1,5-4 раза выше, чем у сталей умеренной теплостойкости. Стали высокой теплостойкости сохраняют твердость HRC 60 после нагрева 700-730˚С. Природа их упрочнения принципиально другая – за счет выделения интерметаллидов. Эти стали при правильном назначении, например для резания многих труднообрабатываемых материалов, обеспечивают повышение стойкости в 10-15 и более раз. Маркировка быстрорежущих сталей: Число после буквы «Р» указывает на среднее содержание вольфрама (в процентах от общей массы, буква В пропускается). Затем после букв М, Ф и К указывают процент молибдена, ванадия и кобальта. 1.Химический состав быстрорежующих сталей (ГОСТ 19265-73)
По составу быстрорежущая сталь делится на фольфрамовую (Р9, Р12, Р18, Р18Ф2), высокованадиевую (Р9Ф5, Р14Ф4), кобальтовую (Р9К5, Р9К10), кобальтованадиевую (Р10К5Ф5, Р18К5Ф2). Находят также применение малолегированные быстрорежущие стали Р7Т, вольфрамомолибденовые (Р6М3 и Р6М5Ф, кобальтованадиевые Р6М3К5Ф2, Р9М4К5Ф2 и Р18К8Ф2М и др. 2.Химический состав быстрорежующих сталей (негостированные)
Сортамент выпускаемых быстрорежущих сталей: прутки горячекатаные и кованные – круглые и квадратные, полоса; прутки круглые повышенной отделки поверхности и повышенной точности размеров; холоднокатаная лента. 3.Основные свойства быстрорежущих сталей в исходном состоянии поставки
Назначение быстрорежущих сталей
Применяются для производства металлорежущего инструмента, рассчитанного на высоскоростной режим резания. Легирование быстрорежущих сталей вольфрамом, молибденом, ванадием и кобальтом обеспечивает твердость и жаростойкость стали. Маркировка быстрорежущих сталей: Число после буквы «Р» указывает на среднее содержание вольфрама (в процентах от общей массы, буква В пропускается). Затем после букв М, Ф и К указывают процент молибдена, ванадия и кобальта. ↑ В начало страницы ← Вернуться в оглавление |
strprofi.ru