Проверка управляющей программы на станке. Чпу тест
Тест для операторов станков с ЧПУ - Разработка текстовой документации
бугога - операторы наглеют, но мы их работы не знаем, поэтому проверить не можем.
что делать? спосити-памагити
^_^
1 руководящий документ и описание требований к профессии - ЕТКС №2 часть2 - там все написано: параграфы 64-67
2-й разряд
Характеристика работ. Ведение процесса обработки с пульта управления простых деталей по 12-14 квалитетам на налаженных станках с программным управлением с одним видом обработки. Установка и съем деталей после обработки. Наблюдение за работой систем обслуживаемых станков по показаниям цифровых табло и сигнальных ламп. Проверка качества обработки деталей контрольно-измерительными инструментами и визуально. Подналадка отдельных простых и средней сложности узлов и механизмов под руководством оператора более высокой квалификации.
Должен знать: принцип работы обслуживаемых станков с программным управлением; правила управления обслуживаемого оборудования; наименование, назначение, устройство и условия применения наиболее распространенных приспособлений, режущего, контрольно-измерительных инструментов; признаки затупления режущего инструмента; наименование, маркировку и основные механические свойства обрабатываемых материалов; основы гидравлики, механики и электротехники в пределах выполняемой работы; условную сигнализацию, применяемую на рабочем месте; назначение условных знаков на панели управления станком; правила установки перфолент в считывающее устройство; способы возврата программоносителя к первому кадру; систему допусков и посадок; квалитеты и параметры шероховатости; назначение и свойства охлаждающих и смазывающих жидкостей; правила чтения чертежей обрабатываемых деталей.
Примеры работ
1. Валы, рессоры, поршни, специальные крепежные детали, болты шлицевые и другие центровые детали с кривошипными коническими и цилиндрическими поверхностями - обработка наружного контура на двух координатных токарных станках.
2. Винты, втулки цилиндрические, гайки, упоры, фланцы, кольца, ручки - токарная обработка.
3. Втулки ступенчатые с цилиндрическими, коническими, сферическими поверхностями - обработка на токарных станках.
4. Кронштейны, фитинги, коробки, крышки, кожухи, муфты, фланцы фасонные и другие аналогичные детали со стыковыми и опорными плоскостями, расположенными под разными углами, с ребрами и отверстиями для крепления - фрезерование наружного н внутреннего контура, ребер по торцу на трех координатных станках.
5. Отверстия сквозные и глухие диаметром до 24 мм - сверление, цекование, зенкование, нарезание резьбы.
6. Трубы - вырубка прямоугольных и круглых окон.
7. Шпангоуты, полукольца, фланцы и другие аналогичные детали средних и крупных габаритов из прессованных профилей, горячештампованных заготовок незамкнутого или кольцевого контура из различных металлов - сверление, растачивание, цекование, зенкование сквозных и глухих отверстий, имеющих координаты.
3-й разряд
Характеристика работ. Ведение процесса обработки с пульта управления средней сложности и сложных деталей по 8-11 квалитетам с большим числом переходов на станках с программным управлением и применением трех и более режущих инструментов. Контроль выхода инструмента в исходную точку и его корректировка. Замена блоков с инструментом. Контроль обработки поверхности деталей контрольно-измерительными приборами и инструментами. Устранение мелких неполадок в работе инструмента и приспособлений. Подналадка отдельных простых и средней сложности узлов и механизмов в процессе работы.
Должен знать: устройство отдельных узлов обслуживаемых станков с программным управлением и особенности их работы; работу станка в автоматическом режиме и в режиме ручного управления; назначение и условия применения контрольно-измерительных инструментов и приборов; конструкцию приспособлений для установки и крепления деталей на станках с программным управлением; системы программного управления станками; технологический процесс обработки деталей; систему допусков и посадок; квалитеты и параметры шероховатости; организацию работ при многостаночном обслуживании станков с программным управлением; правила чтения чертежей обрабатываемых деталей и программы по распечатке; начало работы с различного основного кадра; причины возникновения неисправностей станков с программным управлением и способы их предупреждения.
Примеры работ
1. Втулки, валы, штоки, поршни, ступицы гребных винтов, шатуны, кольца, лабиринты, шестерни, подшипники и другие аналогичные центровые детали со ступенчатыми цилиндрическими поверхностями, канавками и выточками - токарная обработка наружного контура.
2. Корпуса, вкладыши, подшипники, крышки подшипников, обтекатели и кронштейны гребных винтов, кулачки распределительных валов, штампы и пресс-формы сложной конфигурации, лопатки паровых и газовых турбин с переменным профилем, матрицы - фрезерование и нарезание резьбы.
3. Корпуса компрессора и редуктора, крышки насосов редукторов, разделительных корпусов, упор, коробок приводов и агрегатов и другие средние и крупногабаритные корпусные детали - обработка торцовых поверхностей, гладких и ступенчатых отверстий и плоскостей.
4. Отверстия сквозные и глухие диаметром свыше 24 мм - сверление, рассверливание, развертывание, нарезание резьбы.
5. Рычаги, качалки, кронштейны, рамки и другие сложнопространственные детали - обработка наружных и внутренних контуров на трех координатных токарных станках.
6. Стаканы со сложными выточками, глухим дном и фасонными поверхностями и с отверстиями, изготовленные из пруткового материала, отливок и штамповок - обработка наружного и внутреннего контура на токарно-револьверных станках.
7. Шкивы, шестерни, маховики, кольца, втулки, диски, колеса зубчатые, стаканы - обработка на карусельных станках.
4-й разряд
Характеристика работ. Ведение процесса обработки с пульта управления сложных деталей по 7-10 квалитетам на станках с программным управлением. Обслуживание многоцелевых станков с числовым программным управлением (ЧПУ) и манипуляторов (роботов) для механической подачи заготовок на рабочее место. Управление группой станков с программным управлением. Установка инструмента в инструментальные блоки. Подбор и установка инструментальных блоков с заменой и юстировкой инструмента. Подналадка узлов и механизмов в процессе работы.
Должен знать: устройство, принципиальные схемы оборудования и взаимодействие механизмов станков с программным управлением, правила их подналадки; корректировку режимов резания по результатам работы станка; основы электротехники, электроники, механики, гидравлики, автоматики в пределах выполняемой работы; кинематические схемы обслуживаемых станков; организацию работ при многостаночном обслуживании станков с программным управлением; устройство и правила пользования контрольно-измерительными инструментами и приборами; основные способы подготовки программы; код и правила чтения программы по распечатке и перфоленте; определение неисправности в станках и системе управления; способы установки инструмента в инструментальные блоки; способы установки приспособлений и их регулировки; приемы, обеспечивающие заданную точность изготовления деталей; систему допусков и посадок; квалитеты и параметры шероховатости; правила чтения чертежей обрабатываемых деталей.
Примеры работ
1. Валы с нарезкой резьбы длиной до 1500 мм - токарная обработка.
2. Детали корпусные авиавинтов и авиаколес со сложной геометрической формой, с большим числом отверстий - фрезерование фасонного контура, сверление, зенкерование, растачивание.
3. Диафрагмы, диски, поршни, силовые кольца, фланцы и другие крупногабаритные детали - токарная обработка.
4. Диски компрессоров и турбин - обработка с двух сторон за две операции.
5. Каркасы оперения законцовок рулей, панели крыла и другие аналогичные детали с теоретическими контурами, карманами, подсечками, окнами, отверстиями - фрезерная обработка.
6. Кольца шарикоподшипников, инжекторы водяные и паровые, пресс-формы многоместные - токарная обработка.
7. Копиры, матрицы, пуансоны конфигурации - фрезерование.
8. Корпуса компрессоров и турбин, спрямляющие и направляющие аппараты, силовые кольца и фланцы и другие крупногабаритные кольцевые и дисковые детали с криволинейными коническими, цилиндрическими поверхностями - токарная обработка по наружному и внутреннему контуру.
9. Корпуса опорных подшипников, блоки цилиндров, валы коленчатые и судовые, винты гребные, статоры турбогенераторов, спицы гребных ледовых винтов, пресс-формы, кондуктора сложные, шкивы тормозные, муфты - обработка на расточных станках.
10. Корпуса судовых механизмов, компенсаторов, двигателей, приводов, коробок скоростей, гидроприводов, крышки, втулки тонкостенные - обработка на токарных и фрезерных станках.
11. Носки крыла, центроплана, пояса, балки, лонжероны, нервюры, окантовки, шпангоуты, панели и другие аналогичные детали с наличием переменной малки - фрезерование наружного и внутреннего контура с двух сторон.
12. Цилиндры паровых турбин, патрубки паровых турбин, доски трубные, каркасы и другие детали - сверление, развертывание и нарезание резьбы.
13. Шары и шаровые соединения, головки разные с многозаходной резьбой, валы с резьбой - токарная обработка.
§67. Оператор станков с программным управлением
5-й разряд
Характеристика работ. Ведение процесса обработки с пульта управления сложных деталей с большим числом переходов, требующих перестановок деталей и комбинированного крепления их по 6-7 квалитетам на станках с программным управлением. Обработка пробных деталей после наладки.
Должен знать: устройство и кинематические схемы различных станков с программным управлением и правила их наладки, правила настройки и регулировки контрольно-измерительных инструментов и приборов; способы установки и выверки деталей; основы теории резания металлов в пределах выполняемой работы; правила определения режимов резания по справочникам и паспорту станка; принципы калибровки сложных профилей; правила чтения чертежей обрабатываемых деталей.
Требуется среднее профессиональное образование.
Примеры работ
1. Валы с нарезкой резьбы длиной свыше 1500 мм - токарная обработка.
2. Гребенки, калибры резьбовые, червяки многозаходные - токарная обработка.
3. Коробки скоростей, корпуса двигателей и судовых механизмов - обработка на токарных и фрезерных станках.
4. Отверстия глубокие - сверление и нарезание резьбы на расточных станках.
6й разряд для данной профессии не предусмотрен
cccp3d.ru
Программное управление металлорежущими станками (СПО)
ТЕСТ
по дисциплине: Программное управление металлорежущими станками
вариант 1
Выберите правильный ответ:
1. Что представляет собой программа управления станком?
а) последовательность команд, обеспечивающих заданное функционирование рабочих органов станка;
б) подготовку станка и технической оснастки к выполнению технологической операции;
в) технологическая последовательность обработки заготовки.
2. Что содержит геометрическая информация, необходимая для обработки заготовки на станке, которую устройство ЧПУ получает от управляющей программы:
а) данные о скорости, подаче, номере режущего инструмента и т.д.;
б) координаты точек траектории движения инструмента;
в) изображение предмета и другие данные для его изготовления и контроля.
3. В каких системах программируется только цикл работы станка?
а) системы ЧПУ;
б) системы ГБОУ;
в) системы ЦПУ;
г) системы КГУ.
4. Как называется большой комплекс действий, направленных на подготовку, как нового, так и находящегося в эксплуатации оборудования к работе и на поддержание его в работоспособном состоянии?
а) монтажом;
б) наладкой;
в) настройка.
5. Кодирование – это …
а) условная запись структуры кадра управляющей программы с максимально возможным объёмом информации;
б) запись текста программы в виде специальных слов, каждое из которых представляет собой комбинацию буквы и числа;
в) аудиозапись текста на диске.
Соотнесите:
6. Узлы, входящие в состав станков с ЧПУ и группы, которые они составляют:
а) станины, стойки, колонны, поперечины;
б) стол, передняя и задняя бабки, ползун;
в) суппорт, револьверная головка, бабка инструментального шпинделя;
г) приводы в системах ЧПУ.
1) узлы, несущие заготовку и определяющие характер её в процессе обработки;
2) узлы, несущие инструмент и определяющие его положение относительно заготовки;
3) совокупность устройств, приводящих в движение рабочие органы станков с ЧПУ;
4) базовые детали.
Вставьте пропущенное слово:
7. Буква и следующее за ней число являются …
8. В качестве символов управляющих программах используются начальные буквы соответствующих терминов на …. языке.
9. …. декартовая система координат задает перемещение рабочих органов станка с ПУ.
10. Оси координат в станках с ЧПУ располагаются …. их направляющим?
Вспомните (ответьте на вопрос):
11. Как различают по способу подготовки и ввода управляющие программы?
12. Какой знак ставят в начале УП?
13. Какой язык низкого уровня представляет собой средство непосредственного общения с МП с помощью команд, представленных в условных мнемокодах?
14. Нарисуйте оси координат и обозначьте круговые перемещения, которые могут совершать инструмент или заготовка.
15. Прочтите: N5 G1 X40 Z-25.
Эталоны ответов
по дисциплине: Программное управление металлорежущими станками
вариант 1
1. а.
2. б.
3. в.
4. б.
5. б.
6. а-4, б-1, в-2, г-3.
7. словом.
8. на английском.
9. правая.
10. вдоль (параллельно).
11. ручные, машинные.
12. % .
13. Ассемблера.
14.
15. N5-номер кадра, G1- прямолинейное перемещение инструмента по оси X с координатой 40мм, по оси Z – 25мм.
ТЕСТ
по дисциплине: Программное управление металлорежущими станками
вариант 2
Выберите правильный ответ:
1. Что называют циклом обработки детали?
а) совокупность устройств, приводящих в движение рабочие органы металлорежущих станков;
б) совокупность перемещений, повторяющихся при обработке каждой детали.
2. Что содержит технологическая информация, необходимая для обработки заготовки на станке, которою устройство ЧПУ получает от управляющей программы:
а) данные о скорости, подаче, номере режущего инструмента и т.д.;
б) координаты точек траектории движения инструмента;
в) изображение предмета и другие данные для его изготовления и контроля.
3. В каком виде записываются команды управляющей программы?
а) в виде различных знаков;
б) в виде специальных слов, каждое из которых представляет собой комбинацию буквы и числа;
в) в виде технических терминов.
4. В каких системах управление осуществляется от программоносителя с геометрической и технологической информацией?
а) системы КГУ;
б) системы ГБОУ;
в) системы ЦПУ;
г) системы ЧПУ.
5. Формат – это …
а) условная запись структуры кадра управляющей программы с максимально возможным объёмом информации;
б) запись текста программы в виде специальных слов, каждое из которых представляет собой комбинацию буквы и числа.
Соотнесите:
6. Чем руководствуются при выборе режимов резания для станков с ЧПУ:
а) при табличном способе;
б) при графическом способе;
в) при расчетном способе.
1) номограммами;
2) компьютер;
3) нормативами.
Вставьте пропущенное слово:
7. В системе ЧПУ величина каждого хода исполнительного органа станка задаётся …..
8. В настоящее время наиболее распространенным кодом является код ИСО…?
9. УП заканчивается командой ….
10. Перемещение рабочих органов станка с ЧПУ в пространстве задается в …. декартовой системе координат.
Вспомните (ответьте на вопрос):
11. Как располагаются оси координат, по отношению друг к другу, в станках с ЧПУ?
12. Где указывают разработчики оборудования направление осей координат станка с ЧПУ?
13. Перечислите языки программирования?
14. Нарисуйте оси координат станков с ЧПУ и обозначьте их.
15. Прочтите: N6 G2 X68 Z-10 R10.
Эталоны ответов
по дисциплине: Программное управление металлорежущими станками
вариант 2
1. б.
2. а.
3. б.
4. г.
5. а.
6. а-3, б-1, в-2.
7. числом.
8. 7бит.
9. М30.
10. в прямоугольной.
11. под углом 90º.
12. в технической документации на станок, в разделе «Кинематическая схема».
13. Бейсик, Фортран, Алгол, Ада, Си, Паскаль.
14.
15. N6-номер кадра, G2- перемещение инструмента по радиусу по часовой стрелке по оси X с координатой 68мм, по оси Z – 10мм с радиусом R10мм.
www.metod-kopilka.ru
особенности, способы, причины и ремонт
Диагностика станков с ЧПУ – комплекс действий, направленный на обследование и выявление неисправностей в конструкции оборудования, оснащенного числовым программным управлением. Система ЧПУ обеспечивает автономную и полуавтономную работу станочных приборов. Сбои в работе агрегата могут повлиять как на качество обработки на станках с ЧПУ, так и на способность исправно выполнять поставленную задачу.
Особенности
Диагностика станочного оборудования с ЧПУ включает группу работ, выполнением которой должны заниматься специалисты.
Произвести диагностику вне сервисного центра своими руками сложно, и имеется вероятность неточного определения причины поломки.
Диагностика делится на два этапа:
- проверка состояния станка;
- проверка системы числового программного управления.
Первый этап предполагает выявление неисправностей в конструкции самого прибора. Чаще всего неисправности связаны с поломками механического типа. В таком случае производится разбор конструкции, устранение и замена неисправного элемента.
Второй этап более сложный, поскольку требует исследования задач на числовом программном управлении. Для его осуществления требуется обследовать заданную программу, программоноситель, а также оборудование, отвечающее за выполняемые работы.
Если агрегат используется на промышленном предприятии, его обслуживание проводят специальные службы. Компании, которые занимаются производством оборудования этого типа, проводят курсы, обучающие, как использовать приборы, а также как определить их неисправность. При продаже агрегата вместе с ним следует руководство, в котором указана компания, занимавшаяся его изготовлением.
При необходимости в данную компанию можно обратиться с целью прохождения обучающего курса, или же получения консультации по интересующему вопросу. Наладчик должен уметь самостоятельно осуществлять диагностику аппарата.
Способы
Системы ЧПУ отличаются по структуре и функциям. Несмотря на это методика проверки оборудования предполагает наличие общих действий. При этом виде диагностики, выделяется три этапа, которые должен осуществлять оператор:
- проверка работоспособности прибора;
- наладка агрегата;
- выполнение правил эксплуатации.
Проверка системы ЧПУ производится при помощи специальных тест-программ. При покупке заводских изделий они следуют в комплекте с прибором, и соответствуют его виду. Если используются микропроцессорные ЧПУ, тест-программы частично хранятся в памяти аппарата. В инструкции, которая следует в комплекте к станку, указывается и частота, с которой должна проводиться диагностика.
Тест-программа используется независимо от того, возникла неисправность, или нет.
Если же неисправность возникла, диагностика без нее не осуществляется. Основным признаком, который говорит о необходимости проведения диагностики, является неправильная обработка заготовок. Даже незначительные ошибки могут указывать на сбой. Тест-программа создана таким образом, чтобы после проверки оборудование вернулось в исходное состояние. Станки выполняют технологические команды, при которых записывается информация.
После окончания процедуры данные предоставляются оператору. Он сравнивает их со стандартными значениями, и определяет, какие из них не соответствуют норме. Наиболее частые погрешности, указывающие на наличие проблемы, связаны с частотой вращения шпинделя и сменой инструмента. Комплекс действий по выявлению неисправностей в работе агрегата, осуществляется тремя вариантами:
- на станке;
- с наличием стенда;
- без станка и стенда.
Использование тест-программы соответствует первым видам действий. Этот этап является самым простым. Используя его, нет необходимости производить разбор оборудования. Достаточно произвести запуск программы. Диагностика с наличие стенда почти не отличается. Вместо станка используется графопостроитель. Если станок и стенд отсутствуют, наладчику придется использовать органы индикации.
Причины и ремонт
После выявления неисправностей применяются способы их устранения. В ходе осмотра и проверки на точность определяются данные, которые указывают, настройку какого элемента следует произвести. Независимо от этого осуществляется наладка и смазка деталей, которые подвергаются нагрузке. Смазка осуществляется при помощи использования специального масла. Регулировка и ремонт предполагают:
- восстановление прямолинейности движения столов;
- уменьшение интервалов салазок;
- уменьшение интервалов столов.
Выполняется контроль силы натяжения ремней, цепей передачи, а также силы зажима крепежных деталей. Независимо от качества станка, после определенного периода использования начнут возникать неисправности в работе на станках.
Чаще всего аппарат с системами числового программного управления выходит из строя по вине:
- неправильно отрегулированных узлов и рабочего механизма;
- нарушения правил использования;
- перегрузки оборудования;
- неправильного ремонта устройства;
- износа или получения механических повреждений.
Комплексная диагностика включает и разбор станка, и использование тест-программы. Рекомендуется использовать эти виды диагностики, поскольку причин поломки прибора может быть несколько.
Профилактика
Диагностика проводится не только с целью обнаружения причин поломки, но и профилактического обслуживания устройства с ЧПУ. Какие именно действия должны проводиться с профилактическими работами, и как часто их нужно осуществлять, указано в инструкции к аппарату. Цель профилактики и обслуживания станка заключается в поддержании рабочего состояния деталей станка, уходе за ними, и решении проблем на раннем этапе.
В ходе профилактики:
- смазываются подвижные комплектующие фотосчитывающего прибора;
- смазываются вентиляторы охлаждения;
- конструкция оборудования очищается от пыли и загрязнений;
- воздушные фильтры вентиляционной системы очищаются или заменяются на новые;
- контакты и электронные блоки подвергаются чистке.
Если после профилактических действий возникли неисправности, требуется участие специалистов.
vseochpu.ru
Проверка управляющей программы на станке
После того как вы написали УП, проверили ее на компьютере и передали в память СЧПУ, необходимо провести тест программы обработки прямо на станке. Дело в том, что не все ошибки, содержащиеся в программе, могут быть распознаны инструментами верификации на компьютере. Вы можете легко увидеть, что фреза идет не в ту координату, но можете не заметить, что нет команды на включение вращения шпинделя или на подачу смазывающе-охлаждающей жидкости (СОЖ).
Но даже если в коде УП нет ни одной ошибки, оператор станка может случайно внести в корректора СЧПУ неверные значения длины и радиуса инструментов или ошибиться в «привязке» к детали, что неизбежно приведет к браку. Для того чтобы исключить любую ошибку, перед изготовлением реальной детали прямо на станке производят пробный прогон или тестовую обработку. В табл. 3.3 приведены типичные ошибки программиста или оператора станка с ЧПУ и их возможные последствия.
Таблица 3.3. Возможные ошибки программиста и оператора
Не включена подача СОЖ при обработке, когда это необходимо | Испорченный инструмент Ухудшение качества поверхности |
Неправильные режимы резания | Испорченный инструмент/ Заготовка сдвигается в приспособлении |
В инструментальном магазине станка находится неправильный инструмент | Деталь с неверными размерами (брак) |
Не включены обороты шпинделя при обработке | Испорченный инструмент/Испорченная заготовка |
Неправильный порядок выполнения операций. Например, сначала нарезание резьбы, затем сверление (должно быть наоборот) | Сломанный инструмент/ Испорченная заготовка |
В корректорах стоят неправильные значения | Испорченный инструмент или заготовка/ Деталь с неверными размерами (брак) |
Траектория перемещения инструмента пересекается с приспособлением | Сломанный инструмент/Испорченное приспособление |
При обработке нескольких карманов инструмент после обработки первого из них не был возвращен в безопасную позицию над деталью для перемещения к следующему карману | Испорченная деталь/ Сломанный инструмент |
Оператор станка неправильно «привязался» к обрабатываемой детали (неправильно установлена рабочая система координат) | Деталь с неверными размерами (брак)/ Испорченный инструмент/ Испорченная заготовка |
Тестовые режимы станка с ЧПУ
Большинство современных станков с ЧПУ имеют тестовые режимы для дополнительной проверки УП. Основной тестовой функцией является отработка УП на холостых ходах (Dry run). При запуске УП в этом режиме станок блокирует перемещения исполнительных органов по оси Z, по осям X и Y или по всем осям одновременно. Например, если ваш станок блокирует ось Z, то будут осуществляться перемещения по осям X и Y, при этом шпиндель будет вращаться как обычно. Это позволит вам спокойно посмотреть, как работает вся УП, без опасения «зарезаться» в материал заготовки. Вообще, поведение станка в этом режиме может быть различным, поэтому перед работой в режиме отработки УП на холостых ходах внимательно прочтите руководство оператора станка.
Режим покадровой отработки (Single block) предназначен для выполнения программы обработки по отдельным кадрам. СЧПУ приостанавливает работу в конце каждого кадра и ожидает, когда оператор нажмет клавишу Старт цикла для исполнения следующего кадра. Пользуясь этим режимом, легко увидеть, пришел ли инструмент в правильную позицию или в программе есть ошибка. Обычно режим покадровой отработки УП применяется совместно с режимом отработки УП на холостых ходах или при «поднятой» нулевой точке детали.
Может показаться, что перечисленные тестовые режимы станка с ЧПУ немного устарели в эпоху современных компьютеров и мощных программ верификации. С одной стороны, это так. Но, с другой стороны, эти режимы позволяют новому оператору проще и спокойнее учиться программированию обработки и реальной работе на станке.
Применяются и иные методы для цеховой проверки УП. Контролировать правильность перемещений в программе обработки оператору помогает экранный режим, который называется Distance to GO (Оставшееся расстояние). Многие СЧПУ имеют функцию отображения оставшегося расстояния перемещения по каждой из осей. Перейдя в этот режим, оператор видит, сколько миллиметров (дюймов) осталось переместиться инструменту в текущем кадре УП. К примеру, вы знаете, что фрезе нужно пройти до касания с поверхностью заготовки по оси Z 50 мм, а в строке Z экранного режима Distance to GO стоит 100 мм. Это означает, что фреза пройдет лишних 50 мм и врежется в материал заготовки. Таким образом, информация об оставшемся расстоянии перемещения позволяет оператору сравнивать фактическое и заданное расстояния перемещения визуально и дает возможность избежать серьезной ошибки.
Зачастую для проверки УП применяются методы, не использующие тестовых режимов станка с ЧПУ. Например, после установки рабочей системы координат («привязки» к детали) можно поднять нулевую точку на безопасную высоту над поверхностью заготовки. Эта высота должна быть немного больше, чем самое «глубокое» перемещение инструмента в данной УП. Таким образом, выполнение данной программы обработки ничем не будет отличаться от заданного, за исключением того, что инструмент будет «резать воздух».
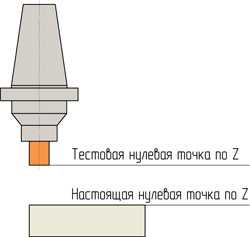
Рис. 3.11. Очень часто перед настоящей обработкой детали «поднимают» нулевую точку по оси Z и УП «прогоняют по воздуху»
Пожалуй, самым реалистичным способом проверки УП является настоящая обработка «ненастоящего» материала. Обработав заготовки из специального воска или пластика, вы поймете, что на самом деле делает ваша программа. При этом можно использовать очень высокие режимы резания и не бояться сломать инструмент или испортить заготовку из дорогостоящего металла.
Выбор того или иного способа проверки УП на станке зависит от многих факторов. Для начинающего программиста рекомендуется выполнять полную проверку. Профессионал же может ограничиться частичной проверкой или вообще проводить тесты УП только на персональном компьютере, используя инструменты бэкплота и твердотельной верификации. При написании программы и работе на станке с ЧПУ главное – быть внимательным и не торопиться, а в случае сомнений лучше обратиться к документации станка или за советом к специалисту.
Последовательность полной проверки УП
- Выполните графическую проверку кода программы на компьютере методами бэкплота и твердотельной верификации.
- Осуществите дополнительные проверки программы и настройки станка:
- все ускоренные перемещения выполняются над поверхностью заготовки на безопасном расстоянии;
- в УП номера инструментов и номера корректоров совпадают;
- инструмент, установленный в инструментальном магазине станка, соответствует инструменту, описанному в УП;
- инструмент надежно закреплен в патроне;
- в стойке ЧПУ находятся правильные значения компенсации длины и радиуса инструментов;
- назначены верные режимы резания;
- шпиндель вращается в правильном направлении;
- в УП присутствует команда на включение СОЖ при необходимости;
- операции обработки выполняются в правильном порядке;
- черновые операции производятся перед чистовыми операциями;
- заготовка надежно закреплена в приспособлении;
- инструмент перемещается от одного обрабатываемого элемента детали к другому на безопасном уровне по оси Z.
- Выполните графическую проверку программы на стойке ЧПУ, если это возможно.
- Отработайте УП на холостых ходах:
- включите режим покадровой отработки УП;
- уменьшите скорость рабочей подачи;
- сместите нулевую точку детали на безопасное расстояние над поверхностью заготовки и прогоните программу «по воздуху».
- Верните нулевую точку из безопасного положения в нормальное положение, отмените режим покадровой отработки УП и выполните обработку детали с уменьшенными рабочими режимами.
- Проверьте размеры детали. При необходимости произведите корректировку значений длины и радиуса инструментов или самой программы.
planetacam.ru
Тест 3. Методика программирования | ЧПУ
Лимит времени: 0
Информация
Тестирование для проверки знаний методики программирования.
Вы уже проходили тест ранее. Вы не можете запустить его снова.
Тест загружается...
Вы должны войти или зарегистрироваться для того, чтобы начать тест.
Вы должны закончить следующие тесты, чтобы начать этот:
Правильных ответов: 0 из 10
Время вышло
Вы набрали 0 из 0 баллов (0)
Рубрики
- Программирование подпрограмм 0%
- Программирование циклов 0%
- Сплайновые интерполяции 0%
-
Менее 60% правильных ответов. Тест не пройден.
-
Вы дали более 60% правильных ответов. Тестирование пройдено!
- С ответом
- С отметкой о просмотре
Возврат на главную
anna.stankin.ru
Тест "Программирование станков с ЧПУ"
1) Какой язык для программирования обработки на станках с ЧПУ является наиболее популярным?
ИСО 7 бит
ELAN-25
PROMPT
2) Что необходимо сделать в первую очередь после включения станка?
Переместить исполнительные органы в его нулевую точку для синхронизации с СЧПУ
Проверить хорошо ли закреплена заготовка
Выбрать инструмент для обработки
3) Какая точка является базовой для шпинделя?
Варианты ответов
Точка пересечения его диагоналей
Точка пересечения направляющих
Точка пересечения торца шпинделя с собственной осью вращения
4) Какие коды используются для определения рабочей системы координат?
Варианты ответов
G41-G49
G54-G59
G84-G89
5) Что такое рабочее смещение?
Расстояние от нуля станка до шпинделя
Расстояние от нуля станка до нуля детали вдоль определенной оси
Расстояние от шпинделя до нуля детали
6) Какой адрес указывает на соответствующий регистр компенсации длины инструмента?
D
H
L
7) В чем заключается программирование в абсолютных координатах?
Координаты точек отсчитываются от постоянного начала координат
Координаты последующей точки отсчитываются от предыдущей
Координаты точек отсчитываются от нулевой точки станка
8) В чем заключается программирование в относительных координатах?
Координаты точек отсчитываются от постоянного начала координат
Координаты последующей точки отсчитываются от предыдущей
Координаты точек отсчитываются от нулевой точки станка
9) При помощи каких кодов происходит переключение между относительными и абсолютными координатами?
G89, G90
G90, G91
G91, G92
10) Для чего в УП используются комментарии?
Довести до оператора станка определенную технологическую операцию
Задать определенные данные для обработки заготовки
Описать последовательность обработки
infourok.ru
Тест драйв ЧПУ драйверов TB6560
Продолжим нашу эпопею, дальше часть 3. Пришел последний драйвер, на ось Z вместе с контролером на опторазвязке. Последний думаю, долго мне вообще не пригодиться. Что то я погорячился с ним. Так как все мои предыдущие драйвера и этот в том числе с опторазвязкой на самих драйверах. Кто не читал мои предыдущие опусыВот часть первая и вторая.mysku.ru/blog/aliexpress/41551.htmlmysku.ru/blog/aliexpress/42324.html
В общем первый тест драйв, механический.
На почте думаю. хорошо попинали посылку, дабы проверить вложение на механическую прочность.
Дивитесь сами.
Ну что поделать. Видно душу отводят, когда их заваливают разными посылками. Сам заказ от этого продавца, шел без трека и почти 2 месяца. Хотя там еще контролер был с опторазвязкой и релюшками. Сервис никакой. Благодарю, что хоть вообще дошло. Два предыдущих, по сравнению с ним просто скоростники. пару недель.
В общем с содроганием достаем вложения в нее.
Видим такую картину.
Разрезаем антистатик и смотрим что у нас с платой.
Вроде как механический тест драйв плата прошла не плохо. Многие жалуются что у них электролиты повылетали и оторвались и переключатели набок загнули. Меня вроде как пронесло в этом плане.
Нас на мякине не возъмешь. Откручиваем радиатор и смотрим что там под ним.
Видим картину девственности, чипа. То есть термопаста напрочь отсутствует.
То ли, там у них она закончилась, то ли специально так сделано. Чтобы бычтрей сгорели и новые заказали. Маркетинг так сказать.
В общем достаем тюбик с пастой и небольшим равномерным слоем размазываем по поверхности чипа.
Вот теперь. как говорит мой старший сын «грамотно» Все закручиваем. Кстати когда откручивал, нужна была мощная отвертка, китайцы прямо с большим усилием закрутили. Видимо чтобы не каждый открутить смог.
Для любителей познакомится с элементной базой платы. специально сделал фото, где все хорошо видно.
Видим что даже оптроны стоят дорогие, быстрые, видимо замануха.
Ну что радостно берем этот драйвер и идем на дачу, ставить на ось Z и глядеть как он покажет себя в работе. Главное, не торопиться и ничего не перепутать в проводах. Не забыть проверить нужные перемычки на плате. Китайцы обычно выставляют на максимальные токи, дабы он сразу же и сгорел. Максимальные заявленные, это пиковые. Даже вообще не знаю для чего их вообще выставляют? Ради эксперимента что ли? Наш драйвер вроде как позволяет выставлять напругу максимальную 35 вольт и ток 3.5 А. Насчет напруги точно не скажу. Но ток такой лучше не следует вообще выставлять. Многие погорели на этом. Да и китайцы советуют в лоте и на самом девайсе все же 24 вольт.
В общем провода прицепили куда нужно, выставили перемычки. Микрошаг по максимуму, ток 2А. Подали питание и смотрим.
Светодиоды весело светятся красным, дыма нет. Радиатор нагревается.
Движок сразу же, закрутился в оба нужных нам направлениях, в ручном режиме.
Прямой и с реверсом. В зависимости от команды драйвера.
Значит ничего не перепутали. Будет и по коду правильно крутить.
Для новичков схемы различные подключения.
Наш вариант номер №2. Ранее писал что по первому варианту драйвер может просто глючить, как бы вы вокруг него с бубном не бегали. Китайцы упорно. почему то советуют вариант №1
Да еще забыл вам до кучи забросить печатную схему перемычек и режимов.
Можно её распечатать и где нибудь на корпусе повесить, чтобы не искать и была под рукой.
Выводы. ================================================================ Плюсы +++++++++++++++++ Цена Быстрые оптроны Много различных режимов, через переключатели Радиатор без покрытия краской
Минусы. — Этот драйвер более ощутимо нагревается. Разъемы не удобные, не съемные. Термопаста в моем экземпляре отсутствует.
Из всех трех драйверов более всего приятней крутит движки, все же наш «термобутерброд» то есть драйвер по первому моему обзору ссылка в самом начале.
Видно чип ТВ67 всё же не плохим оказался. Фирму можно с ним поздравить. Хотя он очень неказистый на вид, по сравнению с предыдущими. Я конечно усилил ему теплосъем. Хорошо если это сразу на заводе сделали. Потому что как сделано, не выдерживает никакой критики. Через термопрокладку и еще и верхней пластиковой крышке чипа.
У кого денег не обрез, покупайте «термобутеброд» Явно рулит и микрошаг на 1/32 есть.
Я кстати его и оставил по основным осям. Намного приятней работают и мягче.
Ну и по самому станку. Ниже выложу вам фото и видео в виде бонусной части. Хотел вам овчарку выложить, да ладно. Наслаждайтесь просмотром.
Бонусная часть
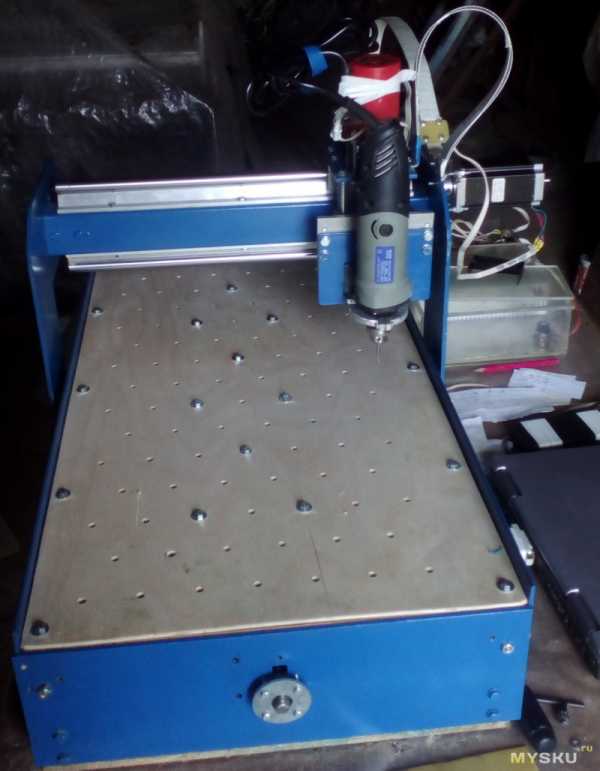
Как всегда пытливые задают вопросы в коментах. Наше дело на них отвечать.
Еще хочу заметить, что мы вообще не обсуждали серводвигатели и сервоконтролеры. К этой теме даже и не знаю как подойти вообще? Там такое будет… Для шаговых то, контролеры и драйверы, стали боле менее дешевыми. Зато сами то шаговые движки многим не по зубам… то есть деньгам. Поэтому покупают в притык самый дешевый, без запаса на механику и начинают мучится.
А вот с сервами, куча двигателей которые можно купить недорого. На портале Мастеровых, есть фанаты, которые разрабатывают высоковольтные сервоконтролеры и под шаговые, для станочников.
Для тех кто хочет идти более дальше.
Сервы или шаговые?
Немного теорииНа заре развития оборудования с числовым программным управлением (ЧПУ), под системой ЧПУ (СЧПУ) понимали электронный комплекс оборудования, довольно габаритный из-за больших размеров современной элементной базы. Управляющие программы (УП) вводились в оперативную память СЧПУ при помощи перфорированных карт, затем перфорированной ленты, затем при помощи магнитной ленты, или «вручную» с пульта оператора. Оперативная память СЧПУ того времени была небольшой (около 64 Кб) что в среднем позволяло разместить в ней программы на 2-3тысячи кадров. Это очень мало, особенно для 3 и более координатных систем, обработки рельефа. Поэтому большое значение придавалось оптимизации программы, применению дуговых интерполяций и подпрограмм. В то время вычислительная мощность компьютерной техники была довольно скромной и программые пакеты автоматизированной подготовки УП (CAMы) были доступны только крупным производственным предприятиям. Остальные писали УП «вручную», вычисляя координаты точек траектории инструмента с помощью логарифмических линеек или калькуляторов. По мере развития компьютерной техники и миниатюризации полупроводниковых элементов, Функции подготовки и ввода УП в оперативную память СЧПУ стали брать на себя промышленные компьютеры, а габариты СЧПУ уменьшились до размеров сравнимых с размерами бытовой техники.
В классическом понимании, в СЧПУ реализована схема управления следящим приводом, при котором сама координатная система состоит из: -приводных двигателей (синхронные, асинхронные, вентильные, постоянного тока, линейные), которые осуществляют позиционирование рабочего органа станка; -датчиков обратной связи (линейных-показания реального положения рабочего органа, круговых-показания угла поворота ротора двигателя). -системы согласования. При этом управление приводом в упрощенном виде осуществляется так: СЧПУ извлекает кадр управляющей программы из оперативной памяти, преобразует его в команды приводу, привод осуществляет требуемое перемещение, и параллельно этому идет контроль отработки по датчикам обратной связи и коррекция управляющего сигнала на двигатели в зависимости от того, насколько отличается реальное положение рабочего органа от требуемого.
Однако с появлением шаговых двигателей (ШД), стали появляться СЧПУ, предназначенные для управления приводом на базе ШД, при этом значительно изменились способы управления, что связано с принципом работы ШД. Дело в том, что ШД имеет некоторое количество фиксированных положений (шагов) ротора (наиболее часто 200) на оборот. Используя специальные электронные устойства — драйвера шагового двигателя (ДШД) можно получить поворот ротора на один шаг (1.8 градуса) за один управляющий импульс. Современные ДШД позволяют дробить физический шаг на различное (до 256) количество аппаратных микрошагов, повышая таким образом дискретность ШД или в переводе на линейные перемешения рабочего органа — уменшая минимальное программируемое перемещение. Управление приводом в упрощенном виде осуществляется так: СЧПУ извлекает кадр управляющей программы из оперативной памяти, преобразует его в количество шагов ШД, при этом не контролируется положение рабочего органа станка, а просто ведется подсчет импульсов ШД, косвенно получая при этом реальное положение рабочего органа. Поскольку эти два привода являются в какой-то мере конкурирующими, нелишним будет привести их сравнительную характеристику. Данная характеристика взята с сайта Одесской станкостроительной компании “ИнСтанкоСервис”. Поскольку компания на рынке более 15лет, информация, по моему мнению заслуживает внимания.Надежность
Шаговый двигатель: Шаговые двигатели отличаются высокой надежностью, так как в их конструкции отсутствуют изнашивающиеся детали. Рабочий ресурс двигателя зависит только от ресурса примененных в нем подшипников. Неоспоримым доказательством высокой надежности шаговых двигателей является тот факт, что при конструировании приводов необслуживаемых космических аппаратов, в большинстве случаев отдают предпочтение шаговым двигателям.Серводвигатель: Большинство современных бесколлекторных сервоприводов от известных производителей (Mitsubishi, Siemens, Omron …) отличаются высокой надежностью, порой сравнимой с надежностью шаговых двигателей, даже не смотря на значительно более сложное устройство сервопривода. Имеются более простые модели сервоприводов — коллекторной конструкции (со щетками). Применение коллекторного узла естественно снижает надежность сервоприводов данного типа. Но их пониженная надежность и необходимость периодического обслуживания в полной мере компенсируется более низкой стоимостью.Эффект потери шагов
Шаговый двигатель: Всем шаговым двигателям присуще свойство потери шагов. Данный эффект проявляется в некотором неконтролируемом смещении траектории перемещения инструмента, от необходимой траектории. При изготовлении простых деталей, имеющих малую длину траектории перемещения инструмента и при невысоких требованиях к изделию, в большинстве случаем данным эффектом можно пренебречь. Но при обработке сложных изделий (пресс-формы, резьба и т.п.) где длина траектории может достигать километров! данный эффект в большинстве случаев будет приводить к неисправимому браку. Данный эффект проявляется при выходе за допустимые характеристики двигателя, при неправильном управлении двигателем, а также при «проблемах» с механикой. Применение современных технологий управления шаговыми двигателями, с применением современной электроники, позволяет полностью устранить данный эффект.Серводвигатель: Эффект потери шагов у сервоприводов полностью отсутствует. Потому, что в каждом сервоприводе имеется датчик положения (энкодер), который постоянно отслеживает положение ротора двигателя и при необходимости выдает команды коррекции положения, на основании которых управляющая электроника, проанализировав данные, полученные с энкодера, вырабатывает необходимые сигналы управления на двигатель. Данный механизм называется обратной связью.Скорость перемещения Шаговый двигатель: При использовании шаговых двигателей в приводах подач станков с ЧПУ можно добиться скорости 150-300 мм/сек (бывает и больше, но это уже «экзотика»). При максимальных скоростях и при превышении допустимой нагрузки возможно проявление эффекта потери шагов.Серводвигатель: Приводы подач станков с ЧПУ на основе серводвигателей позволяют достигать высоких скоростей. Скорость холостого перемещения 0.5-1 м/c является нормальным явлением для сервоприводов.Динамическая точность Шаговый двигатель: Динамическая точность является определяющей характеристикой при обработке сложно-контурных изделий (пресс-формы, резьба и т.п.). Шаговые двигатели отличаются высокой динамической точностью, которая является следствием принципов работы шагового двигателя. Обычно, на хорошей механике, рассогласование не превышает 20мкм (1 мкм = 0.001 мм)Серводвигатель: Высококачественные сервоприводы имеют высокую динамическую точность до 1-2мкм и выше! (1 мкм = 0.001 мм). Для получения высокой динамической точности необходимо применять сервоприводы, предназначенные для контурного управления, которые точно отрабатывают заданную траекторию. Также существуют сервоприводы для позиционного управления. Приводы данного типа не предназначены для точной отработки траектории, от них требуется только точное попадание в конечную точку. Поэтому применение в станках с ЧПУ сервоприводов данного типа приводит к большим динамическим погрешностям. В таком случае погрешность воспроизведения заданного контура может достигать 0.3-1 мм, что приводит к эффекту «поклёванности» обработанной поверхности и искажению его формы. Более низкое качество обработки при применении позиционных сервоприводов в некоторых случаях компенсируется их более низкой стоимостью.Стоимость Шаговый двигатель: В шаговых двигателях применяются дорогостоящие редкоземельные магниты, а также, ротор и статор изготавливаются с прецизионной точностью, и поэтому по сравнению с общепромышленными электродвигателями шаговые двигатели имеют более высокую стоимость.Серводвигатель: Применение дорогостоящего датчика положения ротора, а также применение достаточно сложного блока управления обуславливает значительно более высокую стоимость, чем у шагового двигателя.Ремонтопригодность Шаговый двигатель: У шагового двигателя может выйти из строя только обмотка статора, а её замену может произвести только производитель двигателя, так как если двигатель даже только разобрать-собрать он уже не будет работать! Потому, что при разборке двигателя происходит разрыв магнитных цепей внутри двигателя и по этому происходит размагничивание магнитов. Поэтому после сборки двигателя требуется намагничивание внутренних магнитов на специальной установке.Серводвигатель: Поврежденный серводвигатель в большинстве случаев проще заменить, чем ремонтировать. Ремонту в основном подвергают только мощные двигатели, имеющие весьма высокую стоимость.Столкновение с препятствием Шаговый двигатель: Столкновение подвижных узлов станка с препятствием, в результате которого происходит остановка шагового двигателя, не взывает у него каких-либо повреждений.Серводвигатель: В станке на базе сервоприводов, при столкновении подвижных узлов с препятствием, управляющая электроника определяет, что произошло повышение нагрузки и для компенсации повышенной нагрузки повышает уровень тока, подаваемый на двигатель. При полной принудительной остановке на серводвигатель подается максимальный ток. Поэтому, если управляющая электроника не отслеживает подобную ситуацию, то возможно сгорание двигателя.Преимущества Шаговый двигатель: · Высокая надежность · Низкие требования к обслуживанию и к обслуживающему персоналу · Относительно низкая цена · Высокая динамическая точностьСерводвигатель: · Высокие динамические характеристики · Отсутствие эффекта потери шагов · Высокая перегрузочная способностьНедостатки Шаговый двигатель: · Падение крутящего момента на высокой скорости · Низкая ремонтопригодность · Возможность эффекта потери шаговСерводвигатель: · Высокая цена · Более сложное устройство · Повышенные требования к обслуживающему персоналу · Низкая ремонтопригодность · Требуется более бережное отношение к двигателю
mysku.ru