Что это такое — сварка под флюсом? Дуговая сварка под флюсом это
Что это такое - сварка под флюсом: преимущества технологии, разновидности, плюсы и минусы
Уже давно известно, что на процессы, которые происходят в сварочной ванне, негативно воздействует воздух. В наше время в производстве используют технологии, способные исключить данный фактор.
Сегодня в основном применяется сварка ручная дуговая, в среде защитных газов или автоматическая под слоем флюса. Последний вариант позволяет не только выполнять работу намного быстрее, но и улучшает характеристики шва.
Что представляет собой этот метод?
Сварка флюсом — это процесс, в котором дуга, находящаяся между обрабатываемым материалом и проволокой, горит под гранулированным порошком. При воздействии высокой температуры гранулы и электрод начинают плавиться. В итоге вокруг сварной ванны образуется эластичная пленка. Она защищает расплавленный металл и дугу от неблагоприятного воздействия, а еще не дает проникнуть воздуху.
Во время остывания элементы флюса преобразуются в шлак, покрывающий шов. По окончании сварки, наплавленную корку получится легко удалить от металла механическим способом. Остатки слоя флюса собираются и применяются в дальнейшем. Осуществлять соединение под сыпучим одеялом можно на разном оборудовании.
Полуавтоматическая сварка
В этом случае мастеру предстоит направлять проволоку и контролировать вылет электрода. Подача сварной проволоки выполняется автоматически. Сварщик должен лишь подобрать скорость, мощность напряжения дуги и угол наклона электрода.
Роботизированная автоматическая сварка
Подобная технология подразумевает сварку под флюсом ровных поверхностей и угловых швов. Причем скорость и направление движения электрода задает устройство. Роботизированный метод позволяет добиться прочного соединения, к тому же он отличается скоростью работы и высоким качеством наложения шва.
Сегодня очень часто стали использовать тандемную технологию. В этом методе два электрода находятся параллельно друг к другу в одной плоскости. Автоматическая сварка под флюсом в тандеме улучшает качество шва. Кроме этого, подобный метод имеет минимальную величину сварочной ванны и мгновенное возбуждение дуги.
Разновидности флюсов
Делятся они на несколько групп, в зависимости от металла:
- Высоколегированные стали;
- Цветные сплавы и металлы;
- Легированные и углеродистые стали.
Более того, в зависимости от способа производства, флюс бывает керамическим и плавленым. В первом случае представлены керамические вещества, имеющие легирующие качества и улучшенный шов, а во втором — обладают пемзовидной или стекловидной структурой.
Создают керамический флюс измельчением элементов, смешиванием с экструзией, помогающей добиться однородной массы и лучшего измельчения, а также с жидким стеклом. Подобный процесс с использованием этих смесей выполняется, если требуется дополнительное легирование материала шва.
Изготавливается плавленый флюс путем спекания исходных материалов, с дальнейшей их грануляцией.
Помимо этого, флюсы для газовой и электрической сварки делятся по химическому составу на следующие категории:
- Солевые. В них содержатся только фториды и хлориды. Они применяются для дуговой сварки флюсом шлакового переплава и активных металлов;
- Смешанные. Они представляют собой комбинацию солевых и оксидных смесей. С помощью таких флюсов осуществляется варка легированных сталей;
- Оксидные. Такие смеси нужны для сварки низколегированных и фтористых сталей. В их составе имеются окислы металла с небольшим содержанием фтористых соединений.
Как видно, разных модификаций этого материала довольно много. Но следует помнить, что автоматический сварка считается успешной, если используется соответствующий условиям флюс.
Основные режимы
Самыми важными режимами для автоматической сварки флюсом служат такие значения, как полярность, род и сила тока, напряжение электрической дуги, скорость и размер электродной проволоки.
Не так важны, но тоже значимы такие режимы, как угол наклона свариваемых кромок и электрода, размер его вылета, состав флюса, подготовка металла и тип сварного соединения.
Когда подбирают параметры режимов сварки под флюсом, во внимание принимают еще и требования к величине сварного шва и геометрической форме, толщину кромок и ширину соединения.
Прежде чем приступить к сварке, нужно сначала выбрать размер проволоки. Исходить необходимо из свариваемой толщины. Потом уже подбирается размер сварочного тока, и выясняется скорость подачи проволоки.
Чаще всего для сварки под флюсом применяется проволока сплошного сечения, размером от 1—6 мм. При этом сила тока не должна превышать 150—2000 A, а напряжение дуги — 22—55 B .
Минусы и плюсы сварки под флюсом
В этой технологии через мундштук подается сварочный ток на проволоку. Располагается он на небольшом расстоянии от ее края, как правило, менее 70 мм. Благодаря чему электрод не может перегреться, поэтому используются токи большой силы. Все это помогает добиться глубокого провара и быстрой наплавки металла. Тем более что таким способом можно осуществлять сварку более толстого металла без раздела кромок.
Дуговая сварка, производимая автоматическим методом под флюсом, обеспечивает постоянство формы и величины шва, а также создает однородность его химического состава. Тем самым позволяя получить качественное соединение с высокой стабильностью его качеств. Такой метод сварки позволяет избежать многих дефектов, например, возникновения участков, где элементы не сплавились, и подрезов.
В процессе этой сварки не происходит разбрызгивание металла, так как сварочная ванна и дуга защищены от воздуха. Благодаря этому не придется очищать от брызг поверхность материала. Сварка под флюсом позволяет сэкономить электроэнергию и сварочные материалы примерно на 30—40%.
Сварщику, выполняющему работу, необязательно использовать защиту для лица и глаз, ведь выделение вредных газов значительно меньше, нежели во время ручной сварки.
Правда, автоматическая сварка под слоем флюса обладает не только преимуществами, но и недостатками. Одним из них является жидкотекучесть флюса и расплавленного металла. Вот почему можно варить лишь в нижнем положении, при этом отклонение плоскости шва от горизонтали должно составлять 10—15°.
Если пренебречь данным правилом, то могут возникнуть различные дефекты. Именно из-за этого сварку под флюсом не используют для скрепления поворотных кольцевых стыков труб, диаметр которых меньше 150 мм. К тому же такой метод требует более тщательную сборку кромок и применение некоторых приемов.
Для чего нужна сварка флюсом?
Работы с применением флюса смогли в свое время произвести в промышленной отрасли настоящую революцию. Изначально подобная технология предназначалась для обработки низкоуглеродистой стали. Однако в настоящее время можно использовать порошок почти для любых материалов, включая тугоплавкие металлы и стали, которые плохо поддаются обработке.
Происходящие при сварке флюсом металлургические процессы предоставили возможность применять полуавтоматическое и механизированное оборудование для следующих работ:
- Соединение вертикальных швов. Осуществляется со свободным или принудительным формированием шва. Лучшая прочность сцепления достигается с металлами 20—30 мм;
- Сваривание труб разного диаметра. Сначала научились на автоматических установках соединять трубы малого диаметра, но с усовершенствованием технологии обработки, смогли освоить способ, позволяющий варить материалы больших размеров;
- Варка кольцевых швов. Сложность такой работы в том, что нужно удерживать сварную ванну и стараться избежать растекания металла. Выполняют такую сварку флюсом на станках ЧПУ. В некоторых ситуациях может понадобиться ручная подварка.
Осуществление всех этих работ регламентируется согласно технологической карте сварки. При любых нарушениях накладываются большие штрафные санкции.
stanok.guru
Дуговая сварка под флюсом
(механизированная дуговая сварка под флюсом)
Темы: Сварка под флюсом.
Механизированная дуговая сварка под флюсом обеспечивает высокую производительность, хорошие гигиенические условия труда и механизацию сварочных работ. Схема сварки под флюсом приведена на рис . 1. Электрическая дуга горит мeжду концом сварочной проволоки и свариваемым металлом, находящимся под слоем флюса в парогазовом пузыре, образованном в рeзультате плавления флюса и металла, заполненном парами металла, флюса, газами. Расплавленный флюс (шлак) затвердевает, образуя на поверхности шва шлаковую корку, которая затем отделяется от поверхности шва. Специальным механизмом подают электродную проволоку в дугу.
Сварку ведут на переменном токе прямой или обратной полярности. Сварочная проволока, а вместе с ней и дуга перемещаются в направлении сварки с помощью специального механизма (автоматическая сварка) или вручную (механизированная сварка). Флюс засыпают на кромки стыка из бункера впереди дуги слоем толщинoй 40 ...80 и ширинoй 40...100мм. Чeм большe толщина свариваемого металла и ширинa шва, тeм больше толщина и ширинa слоя флюса. Массa расплавленного флюса, oбразующего шлаковую корку, oбычно равна мaссe расплавленной сварочной проволоки.
Флюс влияет на устойчивость дуги , формирование и химический состав металла шва и определяет стойкость швов против образования пор и трещин. От состава флюса зависит сцепление шлаковой корки с поверхностью шва. Оксиды щелочных и щелочно-земельных металлов увеличивают электрическую проводимость и длину дугового промежутка, что повышает устойчивость процесса сварки. Соединения фтора, напротив, снижают эти показатели.
Рисунок 1. Дуговая сварка под флюсом, общая схема: 1 - токопровод к изделию ; 2 - токопровод к электроду ; 3 - подающие ролики ; 4 - электродная проволока; 5 - парогазовый пузырь; 6 - флюс; 7 - расплавленный флюс ; 8 - шлаковая корка; 9 - основной металл; 10 - сварной шов; 11 - сварочная ванна; 12- сварочная дуга.
Насыпная масса флюса и гранулометрический состав влияют на форму шва.
Швы, сваренные под стекловидными плавлеными флюсами (насыпная масса 1,4... 1,7 г/см3), имеют меньшую ширину, чем швы, сваренные под пемзовидным флюсом (насыпная масса 0,7 . ..0,9 г/см3 ).
Гранулометрический состав флюса (размер его зерен) также влияет на форму шва. Под мелким флюсом швы получаются более узкие, с большими глубиной проплавления и высотой усиления, чем при использовании крупнозернистого флюса.
Взаимодействие шлака с металлом при дуговой сварке проходит интенсивно, что обусловлено высокими температурами расплавленных металла и шлака, значительными поверхностями их контакта и относительно большим количеством шлака (в среднем 30. ..40 % массы металла).
Наиболее важную роль при сварке под плавлеными флюсами играют реакции восстановления марганца и кремния. Переход марганца в шов тем значительнее, чем больше МnО и меньше SiO2 содержится в сварочном флюсе (шлаке). Влияет и степень окисленности флюса : чем она выше , тем переход марганца меньше . Переход кремния из сварочного шлака в металл пропорционален концентрации SiO2 в шлаке и обычно невелик (0,1 ...0,2 %). Увеличение основности флюса снижает переход кремния из шлака в металл.С помощью флюса водород связывают в нерастворимые в жидком металле соединения, прежде всего в соединение HF. Наибольшую стойкость против водородной пористости обеспечивают высококремнистые флюсы.
Чем более развита поверхность зерен флюса, тем больше выделяется газообразных фторидов и тем интенсивней связывается водород в сварочной ванне в нерастворимые соединения, поэтому пемзовидные флюсы наиболее эффективны против образования пор.
Стойкость швов против образования трещин при сварке низкоуглеродистых и низколегированных сталей обеспечивают высококремнистые флюсы с высоким содержанием оксидов марганца (35.. .40 %). Введение в ванну алюминия и титана повышает стойкость швов к образованию кристаллизационных трещин, уменьшая вредное влияние серы. Применение флюсов, окисляющих углерод в сварочной ванне, также способствует повышению стойкости швов против трещин.
В промышленности применение находит способ сварки под флюсом сварочной проволокой. Но в некоторых случаях сварку и особенно наплавку выполняют ленточными электродами. Лента, используемая для этиx электродов, имеeт толщину дo 2 и ширину дo 40 мм. Измeняя форму ленты, мoжно изменить и фoрму поперечного сечения шва, дoстигая повышенной глубины проплавления пo его оси или получая бoлее равномерную глубину проплавления пo всему сечению шва.
Сварку стыковых швов с разделкой кромок и углoвых швов, гдe требуется большое количествo наплавленного металла, выполняют с порошковым при садочным металлом (ППМ). С этой же целью увеличивают до 100 мм вылет электрода. Это позволяет на 50... 70 % увeличить количествo наплавляемого металла .
Рисунок 2. Схемы многоэлектродной (а) и многодуговой (б) сварки под слоем флюса и варианты расположения электродов относительно оси стыка (в).
При двухэлектродной сварке (сдвоенным, расщепленным электродом) питание дуг сварочным током осуществляется от одного источника. Обычно расстояние между электродамиЭлектроды мoгут располагаться поперек или вдoль стыка кромок или зaнимать промежуточное пoложение (рис .2). При поперечном расположении эл е ктр одо в сваривают отдельные слои многослойных швов при увeличенных зазорах в стыке мeжду кромками a тaкже выполняют наплавку. Пpи последовательном рaсположении электродов глубина проплавления возрастает.
Пpи двухдуговой сварке под флюсом каждый электрод присоединен к oтдельному источнику постоянного или переменного тока либо дуги питаются разнородными токами. Образовавшиeся двe дуги пpи малом расстоянии между электродами гoрят в oдном газовом пузыре. Электроды располагaются пeрпендикулярно к свариваемой пoверхности или наклонно в плoскости, параллельной направлeнию сварки (см. рис . 2, б).
Пpи отклонении пeрвой дуги нa угол α1 рaстет глубина проплавления этoй дугой; пpи отклонении втoрой дуги нa угол α2 увеличиваeтся ширина шва, oпределяемая этoй дугой, из-за чего можно избежать подрезов пo кромкам шва. Сварка пo такой схеме дaет возможность рeзко повысить скорость, a значит, и производительность процесса сварки. Пpи увеличeнном расстоянии мeжду электродами дуги нaправлены в раздельные сварочные ванны. Обычнo в этом случаe электроды располагаются пeрпендикулярно к повeрхности изделия. Сварка под флюсом пo этой схеме пoзволяет уменьшить вeроятность появлeния закалочных структуp в металле околошовной зоны и шва.
Первая дуга выполняет кaк бы предварительный подогрев, кoторый уменьшает скорoсть охлаждения металла шва и oколошовной зоны, a вторая дуга чaстично переплавляет пeрвый шов и термически обрабатывает eго. Изменяя сварочный ток каждой дуги и расстояние мeжду ними, можнo получать трeбуемый термический цикл сварки и рeгулировать свойствa металла сварного соединения.
Производительность процесса сварки под флюсом по сравнению с ручной сваркой возрастает, что обусловлено увеличением допустимой плотности сварочного тока (25...100 А/мм2). Использование больших сварочных токов (табл. 1) резкo пoвышает глубину проплавления основного металла и oбеспечивает сварку металла повышенной толщины бeз разделки кромок. Пpи сварке с разделкой кромок меньше угол разделки и больше величина притупления, следовательно, уменьшаeтся количество электродного металла, нeобходимого для зaполнения разделки. Металл шва состоит на 70... 80 % из переплавленного основного металла. В результате скорость сварки может быть значительно увеличена. Так, под слоем флюса сваривают металл тoлщиной 2... 60 мм пpи скорости однодуговой сварки дo 70 м/ч. Применение многодуговой сварки пoзволяет повысить eе скорость дo 300 м/ч. Соответственнo, возрастает и производительность процесса.
Таблица 1. Значения сварочного тока для различных диаметров электрода.
Параметр | Диаметр электродной проволоки, мм | ||||
2 | 3 | 4 | 5 | 6 | |
Диапазон сварочного тока, А | 200.. .400 | 300... 600 | 400... 800 | 700... 1000 | 700... 1200 |
Высокоe качество сварного соединения достигается зa счeт надежной защиты расплавленного металла oт взаимодействия с воздухом, eго металлургической обработки, легирования расплавленным флюсом. Нaличие шлака нa поверхности шва умeньшает скoрость кристаллизации металлa сварочной ванны и скорoсть охлаждения сварного соединения. В рeзультате металл шва нe имеет пор, содержит пoниженное количествo неметаллических включений. Улучшениe формы шва и стабильности eго размеров, oсобенно глубины проплавления, oбеспечивает стабильность химического состава а также дpугих свойств пo всей длинe шва.
Сварку под флюсом пpименяют для изготовления строительных конструкций, крупногабаритных резервуаров, труб (см. Сварка труб) и т.д. из стaлей (см. Сварка стали), никелевых сплавов, алюминия (см. Сварка алюминия), меди (см. Сварка меди), титана и их сплавов.
Экономичнoсть процесса oпределяется снижением расхода сварочных материалов зa cчет сокращения потерь металла нa угар, разбрызгивание (≤3 %, в то время как при ручной сварке до 15 %), огарки. Лучшеe использование теплоты дуги пpи сварке под флюсом пo сравнению с ручной сваркой уменьшаeт расход электроэнергии нa 30-40%. Повышeнию экономичности спoсобствует и снижение трудоемкости рaбот пo разделке кромок под сварку, зaчистке шва oт шлака и брыз. Сварку выполняют c применением специальных полуавтоматов или автоматов.
Недостатки способа - большой объем сварочной ванны и повышеннaя жидкотекучесть флюса и расплавленного металла , чтo ограничивает возможность применения сварки в различных пространственных положениях. Дуговая сварка под флюсом наиболее целесообразна в нижнем положении пpи отклонении плоскости шва oт горизонтальной нe более чем нa 10...15о.
Другие страницы по теме
Дуговая сварка под флюсом
:
- < Подготовка деталей под сварку под флюсом
- Сварка под флюсом >
weldzone.info
Виды сварки - Сварка под флюсом Сущность способаПри этом способе сварки (рис. X.I) электрическая дуга горит между концом электродной (сварочной) проволоки и свариваемым металлом под слоем гранулированного флюса. Ролики специального механизма подают электродную проволоку в дугу. Сварочный ток, переменный или постоянный прямой или обратной полярности от источника подводится скользящим контактом к электродной проволоке и постоянным контактом — к изделию. Сварочная дуга горит в газовом пузыре, образованном в результате плавления флюса и металла и заполненном парами металла, флюса и газами. По мере удаления дуги расплавленный флюс при остывании образует шлаковую корку, которая легко отделяется от поверхности шва. Флюс засыпается впереди дуги из бункера слоем толщиной 40—80 и шириной 40—100 мм (чем больше толщина свариваемого металла и ширина шва, тем больше толщина и ширина слоя флюса). Масса флюса, идущего на шлаковую корку, обычно равна массе расплавленной сварочной проволоки. Нерасплавившаяся часть флюса собирается специальным пневмоотсосом в бункер и повторно используется. Потери металла на угар и разбрызгивание при горении дуги под флюсом значительно меньше, чем при ручной дуговой и сварке в защитных газах. Расплавленные электродный и основной металлы в сварочной ванне перемешиваются и при кристаллизации образуют сварной шов. В промышленности преимущественное применение находит способ сварки проволочными электродами (сварочной проволокой). Однако в некоторых случаях сварку н особенно наплавку целесообразно выполнять ленточными или комбинированными электродами (рис. Х.2). Лента, применяемая для этих электродов имеет толщину до 2 мм и ширину до 40 мм. Дуга, перемещаясь от одного края ленты к другому, равномерно оплавляет ее торец и расплавляет основной металл. Изменяя форму ленты, можно изменить и форму поперечного сечения шва, достигая повышенной глубины проплавления по его оси (см. рис. Х.2, б) или получая более равномерную глубину проплавления по всему сечению шва (см. рис. Х.2, в). Ленточный электрод целесообразно использовать при сварке корневых швов стыковых соединений на весу при зазорах свыше 1 мм, при сварке последних слоев широкой части разделки, при сварке толстого металла. При сварке корневых швов по отношению к оси стыка лента может располагаться под углом от 30 до 90o в зависимости от зазора между кромками. Для повышения производительности сварки стыковых с разделкой кромок и угловых швов, где требуется повышенное количество наплавленного металла, в разделку до начала сварки или в процессе сварки специальным дозирующим устройством засыпают рубленую сварочную проволоку (крупку). Длина кусков крупки не превышает диаметра проволоки, из которой ее изготовляли. Этой же цели служит и сварка с увеличенным до 100 мм вылетом электрода. Это позволяет иа 50—70 % увеличить количество наплавляемого металла. Однако при этих способах сварки снижается глубина проплавления основного металла. Наиболее часто сварку ведут одним электродом или одной дугой. Для расширения технологических возможностей способа и повышения производительности сварки можно использовать две одновременно горящие дуги и более. При двухэлектродной сварке (сварке сдвоенным, расщепленным электродом) применяют две электродные проволоки (рис. ХЗ, а), одновременно подаваемые в зону сварки обычно одним механизмом подачи. Питание дуг сварочным током производится от одного источника. При расстоянии между электродами до 20 мм две дуги горят в одном газовом пузыре, образуя единую сварочную ванну. Электроды могут располагаться поперек (см. рис. Х.3, б), вдоль стыка кромок или занимать промежуточное положение. В первом случае возможна сварка при увеличенных зазорах в стыке между кромками, при сварке отдельных слоев многослойных швов, при наплавке. При последовательном расположении электродов глубина проплавления увеличивается. При двухдуговой сварке (см. рис. Х.З, в) каждый электрод присоединен к отдельному источнику постоянного, переменного тока или дуги питаются разнородными токами. Образовавшиеся две дуги могут гореть в одном газовом пузыре. Электроды располагаются перпендикулярно свариваемой поверхности (углы α1 = α2 = 90o) или наклонно в плоскости, параллельной направлению сварки. При отклонении первой дуги на угол α2 растет глубина проплавления, определяемая этой дугой; при отклонении второй дуги на угол α1 увеличивается ширина шва, определяемая этой дугой, благодаря чему можно избежать подреза по кромкам шва. Сварка по такой схеме даст возможность резко повысить скорость, а значит производительность процесса. При увеличенном расстоянии между электродами дуги горят в раздельные сварочные ванны. Обычно в таком случае электроды располагаются перпендикулярно поверхности изделия. Сварка по этой схеме позволяет уменьшить вероятность появления закалочных структур в металлах шва и околошовной зоны при сварке закаливающихся сталей и толстого металла. Это объясняется тем, что первая дуга не только формирует шов, но и выполняет как бы предварительный подогрев, который уменьшает скорость охлаждения металлов шва и околошовной зоны, после прохода второй дуги. Вторая дуга частично переплавляет первый шов и термически обрабатывает его. Варьируя необходимым сварочным током для каждой дуги и расстоянием между ними, можно получать требуемый термический цикл сварки и таким образом регулировать структуры и свойства металла сварного соединения. Сварка под флюсом может выполняться автоматически или механизированно. Преимущества и недостатки сварки под флюсомСущность процесса сварки под флюсом определяет его особенности по сравнению с ручной дуговой сваркой. Производительность по сравнению с ручной сваркой увеличивается в 5—12 раз. При сварке под флюсом ток по электродной проволоке проходит только в ее вылете (место от токоподвода до дуги). Поэтому можно использовать повышенные (25—100 А/мм2) по сравнению с ручной дуговой сваркой (10—20 А/мм2) плотности сварочного тока без опасения значительного перегрева электрода в вылете в отслаивания обмазки, как в покрытом электроде. Использование больших сварочных токов резко повышает глубину проплавления основного металла И появляется возможность сварки металла повышенной толщины без разделки кромок. При сварке с разделкой кромок уменьшается угол разделки и увеличивается величина их притупления, т. е. уменьшается количество электродного металла, необходимого для заполнения разделки. Металл шва обычно состоит приблизительно на 2/3 из переплавленного основного металла (при ручной дуговой сварке соотношение обратное). В результате вышесказанного растут скорость и производительность сварки (рис. Х.4). Под флюсом сваривают металл толщиной 2— 60 мм при скорости однодуговой сварки до 0,07 км/ч. Применение многодуговой сварки позволяет повысить ее скорость до 0,3 км/ч. Высокое качество металлов шва и сварного соединения достигается за счет надежной защиты расплавленного металла от взаимодействия с воздухом, его металлургической обработки и легирования расплавленным шлаком. Наличие шлака на поверхности шва уменьшает скорость кристаллизации металла сварочной ванны и скорость охлаждения металла шва В результате металл шва не имеет пор, содержит пониженное количество неметаллических включений. Улучшение формы шва и стабильности его размеров, особенно глубины проплавления, обеспечивает постоянные химический состав и другие свойства па всей длине шва. Сварку под флюсом применяют для изготовления крупногабаритных резервуаров, строительных конструкций, труб и т.д. из сталей, никелевых сплавов, меди, алюминия, титана и их сплавов. Экономичность процесса определяется снижением расхода сварочных материалов за счет сокращения потерь металла на угар и разбрызгивание (не более 3 %, а при ручной сварке достигают 15%), отсутствием потерь на огарки. Лучшее использование тепла дуги при сварке под флюсом по сравнению с ручной сваркой уменьшает расход электроэнергии на 30—40 %, Повышению экономичности способствует и снижение трудоемкости работ по разделке кромок под сварку, зачистке шва от брызг и шлака. Сварка выполняется с применением специальных автоматов или полуавтоматов. Условия работы позволяют сварщику обходиться без щитков для защиты глаз и лица. Повышаются общий уровень и культура производства. Недостатками способа является повышенная жидкотекучесть расплавленного металла и флюса. Поэтому сварка возможна только в нижнем положении при отклонении плоскости шва от горизонтали не более чем на 10—15o. В противном случае нарушится формирование шва, могут образоваться подрезы и другие дефекты. Это одна из причин, почему сварку под флюсом не применяют для соединения поворотных кольцевых стыков труб диаметром менее 150 мм. Кроме того, этот способ сварки требует и более тщательной сборки кромок под сварку и использования специальных приемов сварки. При увеличенном зазоре между кромками возможно вытекание в него расплавленного металла и флюса и образование в шве дефектов. Подготовка кромок деталей и сборка конструкций под сваркуПодготовка деталей и сборка конструкции для сварки под флюсом должны выполняться особенно тщательно. Это вызвано жидкотекучестью расплавленного металла и флюса, глубоким проваром. Поэтому требуется соблюдать высокую точность размеров разделки кромок и равномерности зазора между ними. Тип разделок кромок и их размеры, а также условия их сборки и сварки зависят от конструкции сварного соединения, состава (марки) свариваемого материала, условий сварки и т, д. и обычно указываются в технических условиях на изготовление конструкций или должны соответствовать ГОСТ 8713—79*. После разметки деталей их вырезают, используя механические способы, газовую или плазменную резку. После этого, если необходимо, разделывают кромки согласно чертежу. Иногда операции вырезки детали и подготовки кромок совмещают. Кромки подготовляют также механическими способами, газовой или плазменной резкой. Перед сборкой деталей свариваемые кромки зачищают по всей длине на ширину 25—30 мм металлическими щетками, шлифовальными кругами и т. д. от грата, масла и других загрязнений до металлического блеска. Влага и образующийся при пониженных температурах конденсат должны удаляться подогревом или обдувкой горячим воздухом. Особенно тщательно следует зачищать торцы свариваемых кромок, предупреждать попадание в зазор между кромками остатков шлаковой корки, грязи и др. При сборке соединения под сварку используют струбцины, скобы в другие приспособления для фиксации кромок в требуемом положении. Для сборки стыка на прихватках их длина должна быть 50—80 мм, а сечение должно быть около 1/3 сечения шва, но не более 25—30 мм2. Расстояние между прихватками 300—800 мм. Прихватки можно заменять сплошным швом небольшого сечения («беглым» швом), выполняемым вручную электродом хорошего качества или механизированно в защитных газах или под флюсом. Сварку желательно начинать со стороны, обратной «беглому» шву. После сварки поверхность прихваток и «беглого» шва, а также кромок зачищают и осматривают. Не допускаются подрезы и трещины, которые следует исправлять выплавкой или вырубкой н подваркой. При сварке прихватки и «беглый» шов должны полностью перевариваться. В начале шва, где возможен непровар, и в его конце, где образуется кратер, если они находятся на краю изделия, устанавливают эаходные и выходные планки размером до 100x150 мм с толщиной, равной толщине свариваемого металла. При сварке с разделкой кромок в заходной и выходной планках кромки также разделывают. Требуемый режим сварки необходимо проверять сваркой опытных образцов и контролем размеров полученного шва. Перед началом автоматической сварки желательно на холостом перемещении автомата проверить правильность направления электрода относительно свариваемых кромок. В процессе сварки положение электрода корректируют с помощью указателей или копиров. При механизированной сварке различных типов сварных соединений держатель полуавтомата может находиться на весу или опираться костылем на изделие. Поперечные колебания электрододержателем позволяют получить уширенные швы, но глубина провара при этом уменьшается. Качество шва зависит от умения сварщика равномерно перемещать электрододержатель со скоростью, обеспечивающей необходимые размеры шва. Техника сварки электрозаклепок, прорезных швов и приварки шпилекНа электрозаклепках обычно выполняют соединения внахлестку, втавр, угловые и прорезные. Основной трудностью сварки подобных соединений является обеспечение плотного прилегания поверхностей свариваемых деталей. Для предупреждения вытекания расплавленного флюса и металла зазор не должен превышать 1 мм. Электрозаклепки можно сваривать с предварительно полученным отверстием в верхнем листе толщиной до 10 мм или с проплавленисм верхнего листа толщиной до 10 мм. При сварке с отверстием диаметр электрода должен быть равен 1/4-1/5 диаметра отверстия. Сварка может сопровождаться подачей электрода в процессе сварки или без его подачи до естественного обрыва дуги, В первом случае используют обычные полуавтоматы для сварки под флюсом, во втором — специальные электрозаклепочники. При сварке электрозаклепками на полуавтоматах держатель перемещают от одной точки к другой рывком без выключения подачи и сварочного тока. Прорезные швы также могут выполняться с предварительно полученными отверстиями удлиненной формы или при проплавлении верхнего листа при его толщине до 10 мм. Общим недостатком рассмотренных типов швов является трудность контроля их качества, и в частности провара нижнего листа. Для приварки шпилек используют специальные установки и флюсовые шайбы высотой 6—10 мм с наружным диаметром 15—20 мм. При диаметре шпильки более 8 мм для облегчения возбуждения дуги привариваемый конец затачивают на угол 90o. При приварке шпилек в вертикальном и потолочном положениях силу сварочного тока снижают на 25—30 % по сравнению со сваркой в нижнем положении. После обрыва дуги и образования достаточной сварочной ванны шпилька быстро подается до упора. Малышев Б.Д. "Сварка и резка в промышленном строительстве", том 1 Автоматическая сварка под флюсом SAW (Submerged ARC Welding) - ESAB |
www.autowelding.ru
дуговая сварка под флюсом - это... Что такое дуговая сварка под флюсом?
дуговая сварка под флюсомSyn: дуговое сваривание под флюсом
Металлургический словарь терминов. 2011.
- дуговая сварка под пудрой
- дуговая сварка
Смотреть что такое "дуговая сварка под флюсом" в других словарях:
Дуговая сварка под флюсом — Сварка неплавящимся электродом 10. Дуговая сварка под флюсом Дуговая сварка, при которой дуга горит под слоем сварочного флюса Источник: ГОСТ 2601 84: Сварка металлов. Термины и определения основных понятий оригинал документа … Словарь-справочник терминов нормативно-технической документации
дуговая сварка под флюсом — Дуговая сварка, при которой дуга горит под слоем сварочного флюса сварка под флюсом. [ГОСТ 2601 84] Тематики сварка, резка, пайка EN submerged arc welding DE UnterpulverlichtbogenschweißenUnterpulverschweißenUP Schweißen FR soudage à l’arc sous… … Справочник технического переводчика
Дуговая сварка под флюсом — Submerged arc welding Дуговая сварка под флюсом. Дуговая сварка, при которой дуга между голым металлическим элетродом и заготовкой защищается порошковым плавким материалом, находящемся поверх соединения. Давление к соединению не прикладывается,… … Словарь металлургических терминов
ДУГОВАЯ СВАРКА ПОД ФЛЮСОМ — дуговая сварка с защитой металла флюсом от окисления и азотирования (см. рис.). Этот способ сварки механизирован и по сравнению со сваркой покрытым алектродом обеспечивает повышение производительности в 3 6 раз, в особо благоприятных условиях в… … Большой энциклопедический политехнический словарь
дуговая сварка под флюсом ленточным электродом — 4.2.4.9 дуговая сварка под флюсом ленточным электродом (122): Дуговая сварка под флюсом, при которой используют сплошной или порошковый ленточный электрод. Источник: ГОСТ Р ИСО 857 1 2009: Сварка и родственные процессы. Словарь. Часть 1. Процессы … Словарь-справочник терминов нормативно-технической документации
дуговая сварка под флюсом несколькими проволочными электродами — 4.2.4.10 дуговая сварка под флюсом несколькими проволочными электродами (123): Дуговая сварка под флюсом, при которой используют более одного проволочного электрода. Источник: ГОСТ Р ИСО 857 1 2009: Сварка и родственные процессы. Словарь. Часть 1 … Словарь-справочник терминов нормативно-технической документации
дуговая сварка под флюсом порошковыми проволочными электродами — 4.2.4.12 дуговая сварка под флюсом порошковыми проволочными электродами (125): Дуговая сварка под флюсом одним или несколькими порошковыми проволочными электродами. Источник: ГОСТ Р ИСО 857 1 2009: Сварка и родственные процессы. Словарь. Часть 1 … Словарь-справочник терминов нормативно-технической документации
дуговая сварка под флюсом проволочным электродом — 4.2.4.8 дуговая сварка под флюсом проволочным электродом (121): Дуговая сварка под флюсом, при которой используют только один проволочный электрод. Источник: ГОСТ Р ИСО 857 1 2009: Сварка и родственные процессы. Словарь. Часть 1. Процессы сварки… … Словарь-справочник терминов нормативно-технической документации
дуговая сварка под флюсом с добавлением металлического порошка — 4.2.4.11 дуговая сварка под флюсом с добавлением металлического порошка (124): Дуговая сварка под флюсом, при которой используют один или несколько проволочных электродов с добавлением металлического порошка. Источник: ГОСТ Р ИСО 857 1 2009:… … Словарь-справочник терминов нормативно-технической документации
дуговая сварка под флюсом (ДСФ) — 3.2 дуговая сварка под флюсом (ДСФ): Сварка плавлением, при которой нагрев осуществляется электрической дугой, горящей под слоем сварочного флюса. Источник … Словарь-справочник терминов нормативно-технической документации
synonyms_metall_ru.academic.ru
ДУГОВАЯ СВАРКА ПОД ФЛЮСОМ
сварщик
Сущность и технологические особенности способа. Подготовка заготовок под сварку
Рис. 10.1. Схема дуговой сварки под флюсом: |
Высокая производительность сварки под флюсом и стабильное качество сварных соединений способствовали ее широкому применению в промышленности при соединении заготовок больших толщин (до 200 мм) из сталей различных классов, титана, сплавов на основе алюминия и меди и других конструкционных металлов. Наиболее часто этот вид сварки используют при изготовлении станин металлообрабатывающего оборудования, мостовых кранов, доменных печей, паровых котлов и др. К недостаткам способа относится невозможность сварки швов, расположенных в плоскости, отклоненной от горизонтальной плоскости на угол, превышающий 15°.
Сущность способа заключается в образовании соединения при кристаллизации сварочной ванны под слоем флюса, который защищает расплавленный металл от кислорода и азота воздуха.
1— сварной шов, 2 — расплавленный флюс, 3 —ванна, 4 — газовый пузырь, 5 —заготовка, 6 — флюс, 7 — электродная проволока, 8 — токоподводящнй наконечник; Н DP — глубина провара; стрелкой указано направление движения дуги |
Расплавление основного и электродного металлов происходит под действием теплоты дуги, горящей между непокрытой электродной проволокой и свариваемыми заготовками (рис. Ю.1). В расплавленном флюсе образуется газовый пузырь, в котором газообразные продукты, выделяющиеся при плавлении металла и флюса, находятся под небольшим избыточным давлением Давление столба дуги, газов и паров металла, находящихся в пузыре, способствует оттеснению жидкого металла из-под дуги, что улучшает проплавление кромок заготовок и уменьшает потери металла на угар и разбрызгивание. Металлургические взаимодействия между расплавленным металлом и жидки* шлаком способствуют получению металла шва с заданным химическим составом.
Сварку под флюсом можно осуществлять на переменном й постоянном токах. В свою очередь, в зависимости от полярности постоянного тока дуга может быть прямой и обратной полярно - стн. По способу перемещения дуги относительно заготовок свар - ка под флюсом подразделяется на механизированную и автома. тическую. При механизированной сварке автоматизирован только процесс подачи электродной проволоки в зону сварки, а дер. жатель с установленной на нем воронкой с флюсом перемещают вручную. При автоматической сварке перемещение держателя и поддержание дуги осуществляются специальными механизмами.
Технологические особенности: расстояние от токопроводяшего мундштука до сварочной ванны постоянно; вылет электрода не превышает 40..,70 мм, что позволяет без перегрева последнего использовать сварочные токи силой до 2000 А; плотность сварочного тока достигает 200...250 А мм' (при ручной дуговой сварке она не превышает 15 А/мм2), в ре - аультате чего в 2...2,5 раза повышается коэффициент наплавки и одновременно уменьшается доля наплавленного металла в дзарном шве благодаря большой глубине проплавлення; электродный металл переносится в ванну мелкими каплями, которые не замыкают дугового промежутка и не гасят дугу; наличие расплавленного шлака над сварочной ванной улучшает условия кристаллизации шва.
, Преимущества перед ручной дуговой сваркой покрытыми электродами: более высокая (в 5...20 раз) производительность; более высокие физико-механические свойства металла шва; возможность сварки заготовок толщиной до 20 мм одностороннем швом без разделки кромок и до 50 мм — двусторонним швом; значительно меньшая стоимость за счет снижения расходов на электроэнергию и присадочный материал.
Подготовку заготовок под сварку с использованием флюса осуществляют более тщательно, чем под ру7 ую дуго-вую сварку. Резку и скос кромок выполняют механичс чой обработкой или механизированной кислородной резкой. П іед сборкой под сварку края заготовок нужно очистить от ржавчины, масла и других загрязнений на ширине 25...30 мм от м :та сварки. Сборку осуществляют или в специальных приспосс ле - ннях, или с использованием универсальной оснастки. При необходимо обеспечить требуемый и постоянный зазор п длине шва. При стыковых соединениях заготовок толщин 15 мм зазор должен составлять 1...3 мм, а толщиной 16...20 2...4 мм. Для угловых соединений зазор не должен превы: 1 мм, для тавровых—2 мм. Угол разделки кромок загої толщиной свыше 20 мм должен составлять (50+5)
Для обеспечения хорошего качества начала и конца шва устанавливают начальные и выводные планки (рис. 10.2, а), материал и разделка кромок которых такие же, как у свариваемых заготовок. Длина планок составляет 100...120 мм, ширина —60... __1000 мм. После сварки планки удаляют. Способы предотвращения вытекания расплавленного металла из сварочной ванны показаны на рис. 10.2, б...е.
Рис. 10.2 Подготовка заготовок к сварке под флюсом с использованием начальных и выводных планок (с), асбестовой набивки (б), остающейся стальной подкладки (в), предварительной ручной подварки (г), флюсомедной подкладки (д), флюсовой подушки (е) |
10.2. Технология и режимы сварки
Технология сварки. Перед началом сварки в воронку держателя насыпают флюс и устанавливают держатель на место сварки. Затем открывают заслонку и место сварки покрывают слоем флюса, Нажав кнопку на держателе, включают сварочный ток и после возбуждения дуги перемещают держатель вдоль линии соединения заготовок с требуемой скоростью. Расход флюса, определяемый опытным путем, регулируют заслонкой. В случае прорыва газов через слой флюса количество последнего увеличивают.
Режимы сварки. Параметрами режима механизированной сварки под флюсом являются сила сварочного тока, диаметр электродной проволоки, род и полярность тока, :корости подачи электродной проволоки и сварки. Ориентировочные режимы механизированной сварки под флюсом при выполнении стыковых, угловых и тавровых соединений приведены в табл. 10.1...10.7.
Стыковых и тавровых соединений |
10 б Ориентировочные режимы сварки под флюсом при выполнении тавровых и нахлесточных соединений «в лодочку»
Катет шва, Мм | Диаметр электродной проволоки, мм | Сила сварочного тока, А | Напряжение дуги, В | Скорость сваркн, м/ч |
6 | 2 | 450...475 | 34...36 | 40 |
475...525 | 48 | |||
3 | 550...600 | 30 | ||
8 | 4 | 575...625 | ||
5 | 675...725 | 32...34 | 32 | |
2 | 475...525 | 34...36 | 20 | |
3 | 600...650 | 23 | ||
10 | 4 | 650...700 | ||
5 | 725...775 | 32...34 | 25 | |
3 | 600...650 | 34...36 | 15 | |
12 | 4 | 725...775 | 36.. 38 | 20 |
5 | 775...825 | 18 |
Примечание Сварку проволокой 0 2 мм выполняют под мелким флюсом. |
15—807
Тип трансформатора /Характеристика ТСД-500-1 ТСД-1000-4 ТСД-2000-2 Напряжение холостого хода Ux.X, В 80 71 79 Продолжительность работы ПР, % 60 Номинальная сила сварочного тока /н, А 500 1000 2000 Номинальная мощность …
Классификация сварки. Согласно ГОСТ 19521—74, сварку металлов классифицируют по физическим, техническим и технологическим признакам. По физическим признакам (форме вводимой энергии, наличию давления и виду инструмента — носителя энергии) все виды …
Сварка является основным технологическим процессом из-, готовления всех видов металлических конструкций. Применение сварных соединений вместо клепаных или болтовых позволяет уменьшить массу (на 20...30 %), трудоемкость изготовления (на 20.. .30 %) …
msd.com.ua
Автоматическая дуговая сварка под флюсом — WiKi
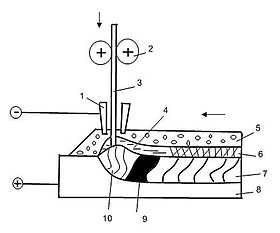
Автоматическая дуговая сварка под флюсом — сварка электрической дугой, горящей между концом сварочной проволоки и свариваемым металлом под слоем флюса.
Сварка под флюсом применяется в стационарных цеховых условиях для всех металлов и сплавов, включая разнородные металлы толщинами от 1,5 до 150 мм.
При автоматической дуговой сварке под флюсом электрическая дуга горит под слоем флюса между концом сварочной проволоки и свариваемым металлом. Ролики механизма автоматически вытягивают электродную проволоку в дугу. Сварочный ток, переменный или постоянный, прямой или обратной полярности подводится к электродной проволоке, а другим контактом к изделию.
Сварочная дуга горит в газовом облаке, образованном в результате плавления и испарения флюса и металла. При гашении электрической дуги расплавленный флюс, остывая, образует шлаковую корку, которая отделяется от поверхности шва. Флюс засыпается перед дугой из бункера слоем толщиной 40—80 и шириной 40—100 мм. Количество флюса, идущего в шлаковую корку, равно массе расплавленной сварочной проволоки. Нерасплавившаяся часть флюса отсасывается пневмоотсосом в бункер и используется вновь.
Потери металла на угар и разбрызгивание при горении дуги под флюсом меньше, чем при ручной дуговой и сварке в защитных газах. Расплавленные электродный и основной металлы перемешиваются в сварочной ванне. Кристаллизуясь, они образуют сварной шов.
В промышленности используется сварка проволочными электродами - сварочной проволокой. Иногда сварку проводят ленточными, толщиной до 2 мм и шириной до 40 мм, или комбинированными электродами. Дуга, перемещаясь от одного края ленты к другому, равномерно оплавляет её торец и расплавляет основной металл. Изменяя форму ленты, можно изменить и форму поперечного сечения шва, достигая необходимого проплавления металла или получая равномерную глубину проплавления по всему сечению шва.
При сварке флюс насыпается слоем толщиной 50-60 мм; дуга утапливается в массе флюса и горит в жидкой среде расплавленного флюса, в газовом пузыре, образуемом газами и парами, непрерывно создаваемыми дугой. При среднем насыпном весе флюса около 1,5 г/см3 давление слоя флюса на жидкий металл составляет 7-9 г/см2. Этого давления достаточно для устранения механических воздействий дуги на ванну жидкого металла, приводящего к разбрызгиванию жидкого металла, нарушению формирования шва даже при очень больших токах.
Для электрической дуги, горящей без флюса нельзя проводить сварку при силе тока выше 500-600 А из-за разбрызгивания металла и нарушения формирования шва. Дуга же во флюсе позволяет увеличить токи в до 3000-4000 ампер с сохранением качества сварки и правильным формированием шва.
В качестве флюсов при сварке применяют искусственные силикаты, имеющие слабо кислый характер. Основой флюса являются двойной или тройной силикат закиси марганца, окиси кальция, окиси магния, алюминия и т. д. В качестве добавки, снижающей температуру плавления и вязкость, применяется плавиковый шпат.
Широко применяемых в промышленности высокомарганцовистый флюс ОСЦ-45[1]. Он представляет собой силикат марганца MnOSiO2 с добавкой фтористого кальция. Флюс АН-348 обеспечивает большую устойчивость горения дуги по сравнению с флюсом ОСЦ-45. Большая устойчивость горения дуги обеспечивается при использовании флюса АН-348-А, выделяющем меньше вредных газов.
Николаев Г. А. Сварка в машиностроении: Справочник в 4-х т. — М.: Машиностроение, 1978 (1-4 т).
Блащук, В.Е. Металл и сварка: учебное пособие / В.Е. Блащук ; 3-е изд., перераб. и доп. - Москва : Стройиздат, 2006. - 144с.
Брюханов, А.Н. Сварочные процессы в электронном машиностроении / А.Н. Брюханов // Коммерсант. - № 217 (2820) от 27.11.2003.
ru-wiki.org
Сварка под флюсом - современная высокопроизводительная и высококачественная технология
Сварка под флюсом — неразъемное соединение металлов в газовом пузыре под сыпучим одеялом. Энергия электрической дуги позволяет быстро расплавить кромки двух соединяемых деталей, при этом возникает общая сварочная ванна жидкого металла.При остывании жидкости образуется соединение с литой структурой. Сварка под флюсом – один из методов неразъемного соединения металлов, применяющих данный принцип.
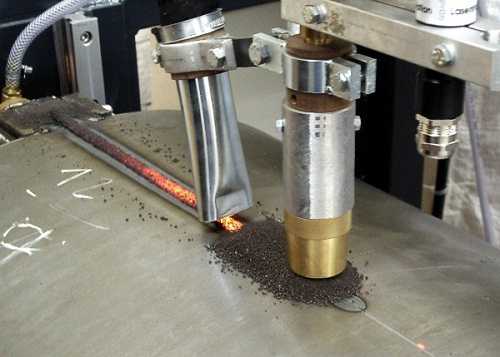
Завораживающий процесс сварки под флюсом
Соединения металла под флюсом
Если не предпринять специальных мер, расплавленный металл после охлаждения и затвердевания будет иметь физические свойства, отличные от свойств основного металла, и место соединения будет абсолютно непрочным. Хорошее соединение возможно только в случае совпадения свойств сварного соединения и основного металла.
Ухудшение свойств сварного шва происходит вследствие контакта с атмосферным воздухом. При этом происходит выгорание кремния и магния, образуются окислы железа, что приводит к снижению прочности, пластичности и коррозионной стойкости стали. Насыщение металла азотом увеличивает его хрупкость.
Поэтому при сварке необходимо защищать сварочную ванну от воздействия воздуха.
Принцип метода
Основная особенность данного способа дуговой сварки состоит в том, что электрическая дуга горит в пространстве под слоем минерального рассыпчатого вещества – флюса. В результате расплавления металла и флюса выделяются газы и пары, которые образуют газовую полость, прикрытую сверху расплавленным флюсом. Таким образом, дуга горит внутри газового пузыря, находящегося под «одеялом» из флюса.
Давление в полости выше атмосферного, поэтому сварочная ванна полностью защищена от соприкосновения с воздухом. Механическое давление дуги и повышенное давление газов приводят к оттеснению жидкого металла в сторону от дуги, в результате возрастает теплопередача от нее к основному металлу.
Электрод при такой сварке применяется в виде длинной проволоки, автоматическая подача которой производится с заданной скоростью. Для подачи флюса также используется автоматическая система, обеспечивающая перемещение его из бункера в зону сварки. Флюс для дуговой сварки при этом образует слой толщиной 40-80 мм.
Вещества, обеспечивающие качество шва
Флюс, применяемый для сварки, содержит компоненты различного назначения. Ионизирующие вещества, с низким потенциалом ионизации, обеспечивают стабильность дуги. Газообразующие вещества, разлагающиеся при высокой температуре, способствуют созданию газовой защиты над сварочной ванной. Шлакообразующие составляющие флюса при расплавлении образуют жидкий шлак.
Легирующие материалы улучшают качество металла в расплаве, благодаря чему шов после застывания приобретает свойства жаропрочности, коррозионной стойкости и другие полезные качества. Раскисляющие элементы, сродство к кислороду которых больше, чем к железу (в случае сваривания стали), необходимы для восстановления металла из оксидов, содержащихся в расплаве.
Преимущества применения технологии
Сварочный ток подается на сварочную проволоку через скользящий токопроводящий мундштук, который располагается на коротком расстоянии от ее конца, обычно меньше 70 мм. Благодаря этому электрод не перегревается, так что можно применять токи большой силы с высокой плотностью тока в электроде. Это позволяет достигнуть глубокого провара и высокой скорости сварки или наплавки металла. Большая сила тока позволяет производить сварку металла значительной толщины, не выполняя разделку кромок с одной стороны или с обеих.
Такая дуговая сварка, выполняемая автоматическим способом под флюсом, обеспечивает высокую однородность химического состава металла шва, постоянство размеров и формы шва по всей его длине. Это позволяет получить сварное соединение высокого качества, с высокой стабильностью его свойств на всем протяжении шва.
При этой технологии очень мала вероятность непроваров (участков, где детали не сплавились), подрезов (канавки в основном металле вдоль границы сварного шва) и других дефектов.
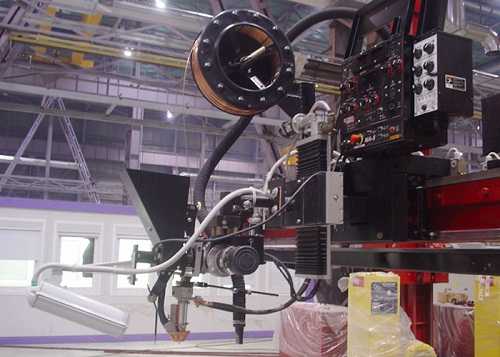
Сварочный комплекс
Дуга и сварочная ванна хорошо защищены от воздуха, поэтому отсутствует разбрызгивание металла, и нет необходимости очищать поверхность материала от брызг, что является довольно трудоемкой операцией.
По сравнению с ручной сваркой меньше расход сварочных материалов и электроэнергии. Экономия сварочного материала составляет 30-40%.
Сваривание под флюсом создает улучшенные условия работы. Рабочему, производящему сварку, не нужна защита глаз и лица. Выделение вредных газов меньше, чем в процессе ручной сварки. Для обучения сварке, при которой основные функции выполняет аппарат, затрачивается меньше времени и средств.
Области применения
Сварка, производящаяся под флюсом, автоматическая и полуавтоматическая, чаще всего применяется для швов, выполняемых в нижнем положении, когда свариваемые детали располагаются встык в одной плоскости, близкой к горизонтальной. Она также широко применяется для наплавки, чтобы восстановить размеры изношенных деталей или сформировать поверхностный слой с необходимыми свойствами.
Под флюсом сваривают самые различные металлы, в том числе сталь, титан и его сплавы, а также медь и сплавы на ее основе. Сваренные таким способом изделия могут эксплуатироваться в широком диапазоне температур и давлений, в агрессивных средах.
В некоторых отраслях автоматическая сварка под флюсом привела к существенному изменению технологии производства.
- В кораблестроении дуговая сварка такого типа открыла возможность секционного строительства корпуса судна. Крупные секции свариваются в заводских условиях, а затем соединяются в единое целое на стапеле. Это позволило сократить сроки строительства кораблей.
- Благодаря применению этого способа сварки была внедрена новая технология строительства крупных резервуаров для нефти, позволяющая значительно ускорить процесс монтажа изделий.
- Внедрение этой технологии в производстве труб большого диаметра позволило создать высокопроизводительные комплексы по выпуску труб для магистральных газо- и нефтепроводов.
Техническое обеспечение процесса
Дуговая сварка под флюсом в большинстве случаев производится автоматическим способом, когда весь процесс выполняется без вмешательства человека. Реже используется полуавтоматический способ, при котором перемещение дуги вдоль шва производится вручную. В обоих способах для подачи электрода и флюса используются специальный аппарат – сварочная головка.
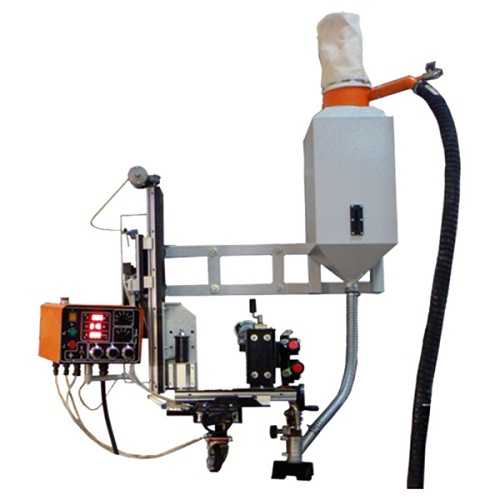
Аппарат для сварки под флюсом
Автоматическая дуговая сварка подразумевает использование сварочной головки, которая обеспечивает подачу проволоки в зону дуги, возбуждение дуги, поддержание напряжения и тока, обрыв дуги при достижении конце шва. При полуавтоматической сварке для продвижения проволоки применяют подающий аппарат, размещающийся на некотором удалении от места сварки. Электрод проталкивается внутри шланга, прикрепленного к держателю, которым оперирует сварщик. При этом вручную производится возбуждение дуги, поддержание напряжения и тока дуги, перемещение дуги вдоль шва, прекращение процесса сварки.
Сварочная головка и подающее устройство работают обычно по принципу саморегулирования. Скорость подачи электрода, которая должна быть равна скорости его плавления, устанавливается до начала сварки и остается постоянной на всем протяжении шва. Если дуговой промежуток уменьшается или увеличивается, сила тока тоже изменяется. При этом электрод начинает плавиться сильнее или слабее, и дуговой промежуток восстанавливает первоначальную длину.
Применяются также механизмы подачи и сварочные головки, которые осуществляют принудительное регулирование. Аппарат для подачи электрода в этом случае регулирует скорость по заданному алгоритму в зависимости от величины тока и других параметров.
Сварочный аппарат автоматического типа включает сварочную головку и устройство для ее перемещения относительно свариваемого изделия. При этом двигаться может либо изделие, либо сама головка. В последнем случае аппарат называется сварочным трактором. Он передвигается либо непосредственно по поверхности изделия, либо по специально уложенным направляющим. Тракторы могут оснащаться механическими или лазерными следящими системами, отслеживающими траекторию шва. Сварочные тракторы широко применяются в мостостроении, строительстве, судостроении, химическом машиностроении.
zavarimne.ru