Гальваническое покрытие в домашних условиях. Гальваническое сверление
Электрохимическое сверление / Мастерская / НеПропаду
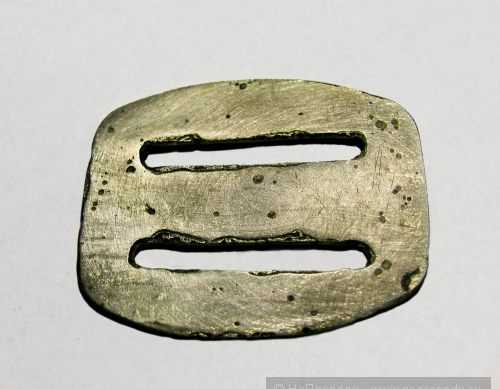
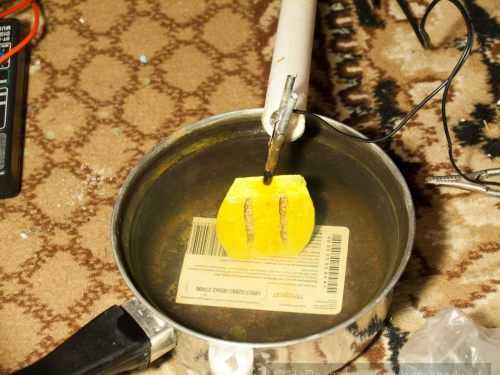
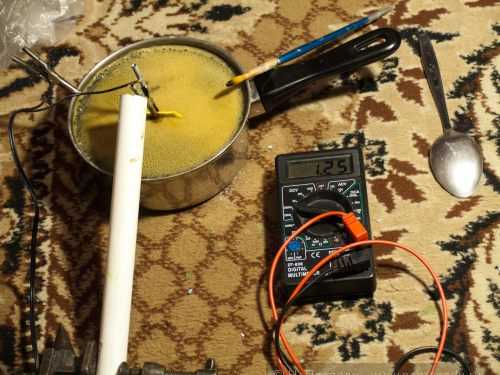
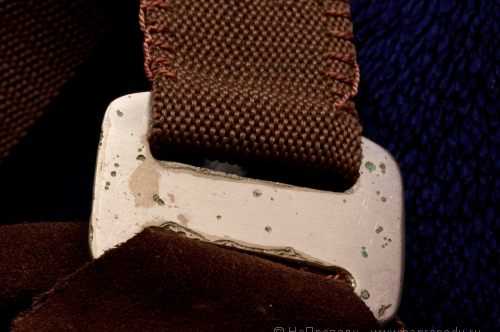
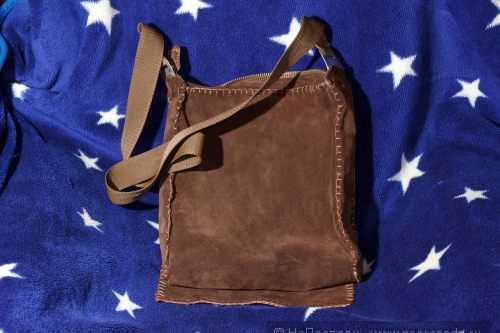
nepropadu.ru
Металлизация отверстий в картинках (часть ІІ, подготовка к гальванике)
Напоминаю: РАБОТАЕМ В ПЕРЧАТКАХ! Применительно к данному этапу ВАЖНО ПОМНИТЬ СЛЕДУЮЩЕЕ: 1. ЗАГОТОВКИ РУКАМИ КАСАТЬСЯ НЕЛЬЗЯ, ДАЖЕ В ПЕРЧАТКАХ! 2. ОТКРЫТАЯ ЕМКОСТЬ С АКТИВАТОРОМ ЯВЛЯЕТСЯ ИСТОЧНИКОМ АММИАКА! ДЕРЖИТЕ ГОЛОВУ ПОДАЛЬШЕ ОТ НЕЕ! Приборы и инструменты: 1. Электропечь или аэрогриль. От них требуется возможность оперативно регулировать температуру. Если у вас есть термостатированная (хотя бы до +-5 градусов) печь или печь способная выдерживать температуру по заданному профилю (например, покупная/самодельная печь для пайки SMD) это даже лучше. Если такой печи нет и, в лучшем случае, имеется лишь «показометр» в виде регулятора или термометра с точностью +- пол-слона, то понадобится так же термометр способный мерять температур в диапазоне до 200 градусов. Термопара и тестер вполне подойдут.
2. Медицинский зажим (лучше длинный). Кто не в курсе, эта штука выглядит вот так:
Материалы: 1. Моющее средство с мягким абразивом.
2. Моющее средство без абразива.
Вот тот комплект моющих средств, которым я сейчас пользуюсь:
3. Две мягких губки, одна используется с первым моющим средством, другая — со вторым. И путать их не желательно.
4. Самая мелкозернистая шкурка, какую удастся найти или абразивный брусок (твердый поролон с нанесенным абразивом) с наибольшим номером (то есть наименьшим размером зерна).
Подготовка платы к процессу активации делается так:
1. Сверлим все отверстия в заготовке, причем сразу нужного диаметра. Сверлить нужно твердосплавными сверлами и на станке (дремель со станиной для сверления вполне подходит, думаю, с аналогичной проксоновской конструкцией, равно как и с самодельными сверлильными станками проблем не будет тоже). Если сверлить несколько заготовок сразу или под заготовку подкладывать кусок ненужного стеклотекстолита, то заготовки не будут требовать зачистки отверстий совсем, так что шаг #3 можно пропустить. Следует помнить, что «подкладку» не стоит использовать дважды, в местах, где уже есть отверстия она работать не будет и появятся заусенцы. Ну и есть заметный риск сломать сверло.
2. Тщательно проверяем все отверстия на предмет попавшей стружки, завернувшихся заусенцев и прочего.
3. Зачищаем заготовку шкуркой или абразивным бруском. Особых усилий прикладывать не нужно, достаточно довести поверность меди непосредственно вокруг отверстий до уровня остальной меди (на ощупь отверстия перестают ощущаться как выступающие).
4. Тшательно промываем заготовку и проверяем чистоту отверстий. При необходимости отверстия нужно тщательно прочистить и еще раз промыть. На вид все отверстия одного диаметра должны выглядеть одинаково.
5. Моем заготовку губкой с абразивным моющим средством. Тщательно проходимся по всей поверхности заготовки, включая углы и края.
6. Тщательно промываем плату под струей воды. Когда моющее средство смыто с обеих сторон, еще раз проходимся струей воды по отверстиям, удерживая плату перпендикулярно струе, таким образом давая ей возможность промыть отверстия. По окончании промывки вода должна «липнуть» к заготовке, стекая с нее крайне неохотно. Если это не так, повторяем пункти #5 и #6 до получения нужного результата. На выходе этого шага заготовка выглядит примерно так:
Самый правый ряд отверстий (увы, его плохо видно даже на полноразмерной фотке) имеет диаметр 0.3.
7. Тщательно стряхиваем воду с заготовки и начинаем обрабатывать активатором. Для этого емкость с активатором открываем и удерживая заготовку за края или за углы не торопясь опускаем ее в активатор, но ни в коем случае не касаемся дна (там есть нерастворенный гипофосфит, который может вступать в реакцию с незащищенной медью). Через 2-3 секунды так же не торопясь приподнимаем заготовку так, что бы ее поверхность оказалась чуть выше поверхности активатора. При этом вокруг отверстий слой активатора быстро светлеет, поскольку активатора протекает в отверстия и слой тановится тоньше. Необходимо убедиться, что это произошло вокруг всех отверстий. Вокруг совсем мелких отверстий, типа 0.2-0.3-0.4, это происходит с некоторой задержкой, все-таки жидкости требуется некоторое время, что бы протечь через такое маленькое отверстие. Если этого не произошло, так же плавно опускаем заготовку в активатор на 2-3 секунды и так же плавно приподнимаем. Таких повторов имеет смысл делать 3-4, не больше и как только все отверстия смочились активатором, обработку следует закончить (см. следующий шаг). Если этого не произошло, то имеет место проблема с отверстиями, следует смыть активатор под струей воды и вернуться к шагу #4.
8. Как только все отверстия смочены активатором, поднимаем заготовку над активатором и поворачиваем одним углом вниз и даем возможность излишкам активатора стечь обратно в емкость. Касаясь углом заготовки стенки емкости с активатором (обеими сторонами) снимаем излишки жидкости. Особо усердствовать тут не надо, достаточно будет если активатор не будет капать сам с горизонтально расположенной заготовки. Отверстия продувать тоже не нужно. Если в каком-то из отверстий пленка активатора лопнула, ничего страшного, но самому что-либо делать для очистки отверстий не нужно.
9. Как только излишки активатора стекли в емкость, закрываем емкость с активатором, а заготовку наклоняем под разными углами, стараясь дать возможность активатору растечься как можно равномернее. В процессе заготовка потихоньку подсыхает и активатор перетекает все менее охотно. Как только активатор более-менее ровно распределен по поверхности можно переходить к термообработке. На выходе этого шага заготовка должна выглядеть примерно так:
10. Кладем плату в печь на подставки (я использую маленькие обрезки 2-мм стеклотекстолита), которые касаются заготовки только на самых краях (и ни в коем случае не на отверстиях). Сверху, при необходимости, устанавливаем спай термопары. Его нужно установить подальше от отверстий, но так, что бы он непосредственно касался платы.
11. Включаем нагрев и доводим температуру до 125 (+-5) градусов. При этой температуре заготовку нужно выдержать не менее 10 минут, лучше 12-15. К концу этого интервала плата приобретает следующий вид:
(сорри, из-за засветки от лампы аэрогриля сделать снимок получше не удается, а когда лампа гаснет, то тоже слишком темно, что бы увидеть цвет заготовки).
12. Доводим температуру до 175 (+-5) градусов и выдерживаем при такой температуре 5 минут, лучше 7-8.
13. По истечении времени выключаем печь и открываем крышку (но заготовку не трогаем) давая заготовке остыть. Заготовка при этом выглядит примерно так:
Как только ее температура опустится ниже 100 градусов, заготовку можна доставать. Для этого удобно пользоваться зажимом. Желательно не сильно усердствовать (зажимом довольно легко повредить фольгу на плате) и брать плату за самый край.
14. Слегка ополаскиваем плату в горячей, а затем в теплой воде. После этого снимаем зажим приступаем к отмывке.
15. На плату наливаем много моющего средства без абразива и мягкой губкой легонько начинаем отмывать (пока без воды). Затем переворачиваем плату и повторяем с другой стороны. Затем смываем пену полностью, ополаскиваем мочалку и снова наливаем моющее средство. Теперь мочалкой продавливаем моющее средство сквозь все отверстия, стараясь ничего не пропустить. Наконец смываем всю пену и промываем еще раз заготовку струей воды, стараясь промыть все отверстия. На выходе плата должна выглядеть примерно так:
Во время отмывки усилий прикладывать не нужно, так же не нужно отмывать все до единого пятна. Что смылось, то смылось, что нет, то нет. Попытка отмыть все вероятнее всего приведет к обрыву электрического контакта с медью в отверстиях и к браку. На простоту отмывки и качество заготовки на выходе напрямую влияет равномерность исходного слоя активатора. Применение абразивов на этом этапе также не желательно по той же причине.
Вот, собственно, и все, плата готова к гальванике.
P.S. Заготовка, на которой делались фотки, после 5 минут гальваники (3А/дм2):
Если присмотреться, можно заметить, что отверстия в плате имеют ровный слой меди. Крошечные участки не закрытые медью в самых больших отверстиях затянутся еще за 3-4 минуты.
Update Крупным планом:
До гальваники:
После гальваники:
Платы снимались еще мокрые, так что в отверстиях есть вода, она несколько мешает разглядеть подробности.
we.easyelectronics.ru
Чем сверлить керамогранит
Такие характеристики керамогранита как высокая прочность и изностойкость создают определенные трудности при его обработке. Также стоит отметить и высокую хрупкость искусственного камня, что исключает возможность ударного воздействия на него инструментом. Внутренняя и наружная облицовка дома, отделка лестниц и террас использует технологии потайного крепления, требующие создания отверстий разного диаметра.
Инструмент для сверления керамогранита
- Двухскоростная дрель.
- Специальная стойка.
- Станок для сверления.
Для работы с искусственным камнем рекомендуется использовать определенные виды коронок и сверл. Наиболее популярные из них:
- Спеченные кольцевые сверла.
- Коронки алмазные, имеющие гальваническое напыление.
- Алмазные сверла.
Выбирая чем сверлить керамогранит, стоит детально рассмотреть все три варианта. К первому типу относят инструмент, применяемый в работе с такими прочными материалами как бетон. С помощью спеченных кольцевых сверл можно проделать более 100 отверстий. Однако есть у них и слабые места - высокое торцевое давление и длительность создание одного отверстия (3-5 минут.)
Коронки алмазные с гальваническим напылением пользуются не меньшей популярностью. Их отличают по толщине стенок. В зависимости от требуемого диаметра отверстия следует выбирать толщину коронки. Данный вариант является самым доступным в экономическом плане. С помощью алмазных коронок создают крупные отверстия, к примеру, гнезда под сетевые или электрические розетки.
Алмазные сверла благодаря значительному содержанию алмазные зерен характеризуются высокой прочностью. Данным инструментом можно быстро создавать отверстия нужного диаметра. К примеру, для того, чтобы просверлить керамогранит толщиной 8 мм потребуется всего 30-50 секунд. В комплекте со специальным оборудованием алмазным сверлом можно просверлить до 350 отверстий. Для устройства отверстий увеличенного диаметра используют трубчатые сверла.
Если требуется проложить через керамогранитную плитку, к примеру, пластиковый кабель-канал или водопроводную трубу, можно использовать алмазное или твердосплавное сверло, при этом форма его наконечника может быть разной.
Общие правила сверления
- Сверление производится только с лицевой стороны плитки, потому как при выходе инструмента в большинстве случаев образуется скол вокруг отверстия.
- Сверло относительно поверхности искусственного камня должно находиться под прямым углом. Перекос инструмента может стать причиной повреждения, как самого сверла, так и материала.
- В работе следует использовать мощную электродрель на малых оборотах – это позволит минимизировать износ сверла и риск раскола плитки.
- Рекомендуется устанавливать дрель на стойку либо применять специальный станок. Это не только ускорит и упростит работу, но и продлит срок эксплуатации сверла. Лучшим выбором будет двухскоростная электрическая дрель. При этом в работе запрещается использовать ударный режим. Результатом может стать раскол плитки.
- Алмазное сверло по керамограниту нуждается в постоянном охлаждении. Позаботьтесь о том, чтобы во время работы на сверло подавалась вода. На предприятиях промышленности для этих целей предусмотрены системы подачи воды. Если работы проводятся в домашних условиях, воду можно подавать на сверло из обычной пластиковой бутылки, в крышке которой проделаны отверстия небольшого диаметра.
- Сверление должно осуществляться на ровной твердой поверхности, при этом нажим делают минимальный.
- Если диаметр создаваемого отверстия превышает 6 см, сначала следует работать меньшим сверлом на неполную глубину, а затем продолжить сверление инструментом большего диаметра.
Если в процессе работы с задней стороны плиты откололся небольшой кусок, во время укладки материала пустоту заполнит клеевой состав. При этом качество и эстетика керамогранита останутся без изменений.
aquagroup.ru
инженер поможет - Для чего нужно алмазное сверло
Алмазное сверло применяется при обработке такого высоко твёрдого материала, как керамогранит. Например, если нужно получить в плитке отверстие, то используют именно алмазные сверла. Но давайте я расскажу подробнее, о видах сверл которые применяются для сверления керамогранита. Очень часто для обработки используется алмазное сверло кольцевого вида.
Трубчатые алмазные сверла
Также иногда применяют трубчатые алмазные сверла, которые можно подобрать под любой размер. Если необходимо получить отверстие большого диаметра, то в этом случае используют кольцевую алмазную насадку с нужным диаметром.
Алмазные сверла
Разные производители режущего инструмента изготавливают сверла с совершенно разной геометрией режущей части и глубиной покрытия алмазом режущей части сверла.
Часто возникает вопрос: «Чем сверлить керамогранит и какой для этого лучше применять вспомогательный инструмент – дрель или перфоратор? Это не имеет никакого значения, просто при использовании перфоратора нужно выключить ударную функцию.
Лучше всего применять вместе с алмазным сверлом вспомогательный инструмент с возможностью регулировки частоты вращения. При получении отверстия в керамограните сверление нужно проводить по возможности на минимальных оборотах. При сверлении нужно постоянно обеспечивать вертикальное положение алмазного сверла, иначе перекос при резании очень часто приводит к повреждению плитки или инструмента, а иногда и к тому и другому. Уменьшить возможность перекоса можно закрепив дрель в любом держателе.
Для повышения качества сверления плитки, а также самого алмазного сверла, лучше всего всегда подкладывать кусок доски или ДСП под плитку, если это возможно. Кроме того обратите внимание, что кроме того, что алмазные свёрла по керамограниту не режут при высокой скорости резания, что их также еще нужно охлаждать для повышения стойкости инструмента.
Лучше всего, когда зона резания охлаждается постоянным потоком воды, но можно сделать небольшую лужицу, правда с некоторой периодичностью ее нужно пополнять. Для сверления на вертикальных поверхностях шприцом водичку нужно подливать, только тряпочку внизу прилепить, чтобы не запачкать пол.
Вырезание отверстия в керамограните с помощью шаблона
Шаблон прочно крепится на плитке или держателя дрели. Для этой цели можно использовать струбцины.
На вопрос как получить отверстие алмазным сверлом в керамограните есть, два ответ. Например, обрабатывать отверстие сразу на нужную глубину или сверлить не до конца. Во втором случае, можно просверлить алмазным сверлом 2/3 требуемой глубины, а после ударом со стороны лицевой поверхности плитки выбить образовавшуюся пробку.
Вид пробки при вырезании керамогранита
Для получения точного отверстия при сверлении нужно использовать специальный шаблон. Он изготавливается из ненужной плитки или вообще из любого материала, часто это обычная пластина, в которой просверлено отверстие с нужным диаметром.
В свое время проводил эксперименты и получил следующий опыт:
1. Перьевые алмазные сверла BOSH обороты 1200 + вода, без молотка - СЛОМАНЫ 3 шт, ПРОСВЕРЛЕНО ОТВЕРСТИЙ 1, затрачено времени 30 мин. Этот вариант ОЧЕНЬ УТОМИТЕЛЕН и очень дорого.
2. Перьевое сверло крестиком об.1200 + вода, без молотка - ПРОСВЕРЛЕНО ОТВЕРСТИЙ 1, затрачено времени 30 мин.Еще более утомительно, но сверло целое.
3. Алмазное трубчатое сверло об.2000 + вода, без молотка - ПРОСВЕРЛЕНО ОТВЕРСТИЙ 12, затрачено времени 1 мин на отверстие. ЛЕГКО, сверло целое. отверстие очень ровное.
4. Перфоратор+ бур на 12 за 50руб, без воды с молотком - ПРОСВЕРЛЕНО ОТВЕРСТИЙ 40, затрачено времени 5 сек на отверстие. ОЧЕНЬ ЛЕГКО, сверло целое. Плитка вся целая правда ближе 10 мм от края не сверлил. На входе, край отверстия немного сколот на конус, в моем случае не принципиально, закрывается крепежным ухом оборудования. Плитка должна быть уложена, на весу будет колоться. Последний вариант ,смею заметить, весьма рискован.
engcrafts.com
Описание процесса сверления отверстий и правила выполнения работ
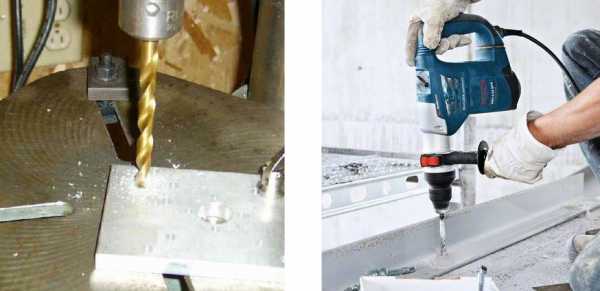
Сверлением называют процесс выполнения отверстий в сплошном материале (металл, дерево, пластмасса) с применением специального режущего инструмента – сверла. Точность обработки отверстий обычно не превышает 11-12 квалитета, а шероховатость поверхности находится в пределах от 25 до 80 мкм. С его использованием получают отверстия под крепежные винты, болты, заклепки и резьбовые шпильки. Полученные отверстия могут быть дополнительно обработаны путем рассверливания, зенкерования, развертывания и нарезания внутренней дюймовой или метрической резьбы. Таким методом выполняют сквозные или глухие отверстия. В том случае, когда деталь или заготовку нельзя установить в стационарный станок, или необходимо выполнить отверстие в труднодоступном месте, сверление отверстий производят с использованием электрических дрелей или пневматических ручных машин.
Операцию сверления отверстий на станке выполняют после его полной подготовки к рабочему процессу. При этом проверяют плавность хода шпинделя, наличие охлаждающей жидкости и ее подачу, исправность механизма подъема и опускания рабочего органа, наличие электрического освещения, исправность инструмента и отсутствие биений при вращении. Перед пуском станка деталь прочно закрепляют в тисках. При сверлении в детали отверстия с диаметром, превышающим 10 мм, тиски необходимо прочно прикрепить болтами к столу станка. В местах сверления деталь должна иметь точно размеченные места центров выполняемых отверстий, которые делают с помощью керна.
Операцию выполняют после проверки совмещения оси сверла с размеченным центром отверстия. Максимальная производительность и высокое качество обработки отверстий можно получить при правильном выборе режима, то есть сочетания скорости резания и подачи. Для этого необходимо точно подобрать диаметр сверла из стали с требуемыми характеристиками прочности и точно знать материал, из которого изготовлена подлежащая сверлению деталь. Высокую точность сверления отверстий и повышенную производительность рабочего процесса можно обеспечить использованием специального приспособления – кондуктора, в который вставлены закаленные втулки с точно выполненными размерами внутренних отверстий.
При сверлении отверстий в небольшой партии деталей вместо кондуктора можно использовать специально изготовленный шаблон с отверстиями, изготовленный в виде пластины, имеющей такие же контуры, как и у основной детали. Контуры самой детали и шаблона сначала совмещают, а затем оба изделия прочно скрепляют струбцинами.
Товары каталога:
Please enable JavaScript to view the comments powered by Disqus. comments powered bywww.rusbolt.ru
Гальваническое покрытие в домашних условиях.
Довольно часто, многие мастера, хотят защитить какую то деталь автомобиля или мотоцикла от коррозии. Можно конечно это сделать с помощью грунтовки и краски. Ну а что делать мастеру, если например разболталось (выработалось) посадочное место под подшипник в картере двигателя или коробки передач и его проворачивает. Как восстановить изношенную поверхность и нарастить её размер (диаметр)? Краска здесь не поможет.
Всё вроде бы довольно просто. Нужно нарастить поверхность детали гальваническим способом, то есть наложением тонкого слоя какого то металла, и если накладывать несколько тонких слоёв, то можно восстановить довольно глубокую выработку поверхности основного металла. Для покрытия металлической поверхности хромом или никелем, требуется сложное заводское оборудование, а так же куча вытяжных и вентиляционных систем, так как наложение этих блестящих металлов очень вредное для здоровья.
Предлагаю способ намного проще, который можно осуществить даже дома на кухне, и к тому же он безвредный. Не смотря на то, что этот способ не такой блестящий как никель или хром, зато он позволяет осуществить две важные функции. Это защита от коррозии стальной детали и восстановление её размера (если она изношена). Этим способом может воспользоваться каждый, даже двоечник по химии.
Для осуществления этого способа покрытия, необходимо купить в автомагазине немного обыкновенного электролита для аккумуляторов. Затем потребуется собрать немного металла, которым будет наноситься гальваническое покрытие. Этот металл стоек к коррозии и очень распространён — это цинк. Где его взять? Да везде. Вспомните сколько вы видели отработавших и валяющихся где попало батареек у себя и у друзей. Пособирайте их, и причём чем старее год выпуска батарейки, тем лучше у них цинк и проще его изъять. С помощью острого ножа, надрежьте корпус батарейки, и осторожно снимите цинк, как кожуру у мандарина, а затем промойте обрезки водой.
Теперь можно начинать сам химический процесс. Налейте в стеклянную или фарфоровую банку грамм 100- 150 электролита, а затем начинайте потихоньку (чтобы реакция проходила не слишком бурно) засыпать в него обрезки цинка. Вы увидите, что тут же начнётся химическая реакция, и в результате этого, образуется раствор сульфата цинка, который вам понадобится, а так же гремучий газ, состоящий из водорода и кислорода. Такой же газ выделяется и при зарядке аккумулятора и он очень взрывоопасен, поэтому проводите работы подальше от открытых источников огня и гоните курильщиков подальше. Если кому то лень возиться с электролитом, то можно поискать готовый сульфат цинка в магазинах химреактивов.
При добавлении кусочков цинка в электролит, он будет растворяться, и добавлять цинк нужно будет до тех пор, пока он не перестанет реагировать с кислотой (перестанет растворяться), то есть кислота расходуется на реакцию полностью и полностью «насытится» цинком. Так же, следует подготовить к покрытию металлические детали, которые вы собираетесь покрыть цинком. Очистите их от грязи и ржавчины, а если деталь декоративная, то желательно отполировать её до блеска, ведь любое гальваническое покрытие, в точности повторяет рельеф поверхности покрываемого металла. И если на поверхности есть царапины, то после покрытия, не важно чем, хоть хромом или никелем, все эти царапины будут видны на поверхности ещё лучше.
Кстати удалить всё ржавчину с поверхности металла можно не механическим, а химическим способом. Для этого следует опустить ржавую деталь в аккумуляторный электролит, соляную кислоту, можно даже в обыкновенный уксус. Но не в коем случае не в преобразователь ржавчины, как могут посоветовать местные знатоки, так как к образовавшейся от преобразователя плёнке фосфатов, цинк, да и хром тоже, никогда не пристанут. Преобразователем ржавчины следует пользоваться только тогда, когда вы хотите просто загрунтовать и покрасить деталь.
Продолжим работу. Подготовленный раствор сульфата цинка налейте в стеклянный или фарфоровый сосуд, размер которого зависит от размера детали, которую вы собираетесь покрыть цинком. Но если со стеклом или фарфором у вас проблемы, то можно использовать подходящее корытце, вырезанное из капроновой канистры.
Источник электропитания лучше всего использовать с регулировкой тока (переменным резистором) и амперметром, глядя на который удобно регулировать силу тока (Амперы). Большинство зарядных устройств имеют и амперметр и регулировку тока, поэтому можно использовать зарядное устройство и даже для зарядки аккумуляторов мотоцикла, так как ток для работы потребуется небольшой.
Сам принцип гальваники простой. Металл анода (кусочек цинка) под действием потока электронов переносится на катод (деталь). Анод переносится на деталь и утрачивается (растворяется), и его необходимо периодически менять, подвешивая на проволоке новый кусочек цинка. Подвешивая его, следите что бы в раствор электролита был погружён только кусочек цинка, но не проволока, к которой он прикручен. Иначе электролит загрязнится медью от проволоки, и в итоге коррозионная стойкость вашей детали намного ухудшится.
Ну а что же делать, если требуется покрыть цинком довольно большую поверхность, а подходящей ванны для этого нет? Существует довольно простой способ. Подготовьте анод так: обмотайте кусочек цинка ватой или марлей, смоченной в растворе сульфата цинка (см. фото ниже, а в качестве насыщенного раствора сульфата цинка используйте паяльную кислоту, которую можно купить на радиорынке) и подключите его к плюсу вашего источника постоянного тока (зарядного устройства), а минус к покрываемой детали. А если участок покрываемой детали невелик, то можно воспользоваться даже аккумулятором.
А как проверить необходимую величину силы тока? При нормальной величине тока, должно получится цинковое покрытие серого цвета. Если получается рыхлое покрытие чёрного цвета, то следует сразу уменьшить регулятором силу тока. Ну а если получается светло-серая поверхность детали, то следует немного увеличить силу тока. По опыту скажу, что обычно хватает силы тока всего в 0,5 — 1 Ампер.
В качестве индикатора тока и простейшего стабилизатора напряжения можно использовать обыкновенную лампочку на 12 вольт, которая при натирании детали не должна светиться слишком ярко. Лампочка подсоединяется в разрыв плюсового провода (наглядно это показано в видеоролике под статьёй). Если лампа светит слишком ярко, то следует немного ослабить силу тока.
После нанесения гальванического покрытия, готовую деталь хорошенько промойте водой. Ну а если вы использовали раствор сульфата цинка не от электролита, а от серной кислоты, то советую готовую деталь сначала ополоснуть раствором питьевой соды, чтобы нейтрализовать серную кислоту, а затем уже промыть деталь в воде.
Ну а как же восстановить размеры посадочного отверстия деталей? Ведь часто из-за этого многие выбрасывают картер, а картер или блок мотора — это номерная деталь, и восстановление её крайне важно. И если в блоке провернуло подшипник и посадочное отверстие потеряло размер (диаметр), то восстановить место подшипника в чугунном блоке, не составит труда описанным выше способом с помощью цинка, обёрнутого марлей.
Но корпуса коробок передач, всегда изготавливали из алюминиевого сплава, и блоки моторов новых автомобилей начали лить тоже из алюминия (гильзы цилиндров покрыты никасилем),который не так то просто чем либо покрыть. Существуют способы, но они дорогие и сложные, применимые только в заводских условиях. Но на то и существует этот сайт, чтобы любому мастеру можно было обойтись без сложного заводского оборудования. Выход есть всегда, и я всегда говорил, что металл не хуже пластилина и лепить из него можно всё что угодно.
С восстановлением посадочных отверстий под подшипники в стальных или чугунных корпусах (картерах) проблем не возникает, так как цинк на сталь или чугун накладывается хорошо. И подробно о восстановлении посадочного отверстия в передней бабке своего токарного станка ТВ- 4, я подробно показал в видеоролике чуть ниже.Ну а отверстие в алюминиевом картере покрыть не удастся, так как цинк на алюминий не ляжет, и ведь у нас же нет в арсенале супер дорогого напылителя металлов, или как я уже говорил, сложного гальванического оборудования, для покрытия алюминия. Оно нам и не нужно. Зато можно легко покрыть слоем, или слоями цинка наружную обойму подшипника. И если вы купите подшипник не какого то левака, а авторитетной фирмы (о правильном выборе подшипников читаем здесь), то он переживёт несколько кап-ремонтов мотора.
Чтобы раствор сульфата цинка не попал внутрь подшипника к шарикам или сепаратору, нужно закрыть подшипник с двух сторон резиновыми прокладками, и наложенными на них текстолитовыми пластинами (толщина 3 — 5 мм), и затем стянуть этот «бутерброд» болтом с гайкой, а потом подвести к наружной обойме подшипника минус источника постоянного тока.
Пластины должны быть именно из диэлектрика (текстолита, пластика и т.п.), а не из металла, иначе цинк будет расходоваться и на покрытие металлических пластин, и вам не хватит металла цинка. Так же советую купить подшипник закрытого типа, так больше гарантии, что кислота не попадёт внутрь к шарикам.
А затем покрыв подшипник цинком, перед установкой его в блок мотора, при желании всегда можно удалить острым ножом закрывающие подшипник герметичные шайбы, и подшипник в итоге станет открытого типа (это нужно, чтобы он смазывался маслом изнутри блока двигателя).
А можно не погружать подшипник в ванну, а покрыть его наружную обойму вторым более простым способом, с помощью натирания кусочком цинка, обёрнутого марлей и подключенного к плюсу источника постоянного тока.
Хочу так же заметить, что для восстановления размера детали (например обоймы подшипника), можно использовать медное покрытие. Как антикоррозийное покрытие медь использовать нельзя, а вот для восстановления размера — легко. К тому же сейчас в кастомайзинге мотоциклов, пошло модное направление, называемое олдскул (старая школа).
Так вот, для покрытия всевозможных трубок масло или бензо-проводов, различных мелких деталей, не только можно, а ещё и нужно использовать медное покрытие. После полировки таких деталей, ваш мотоцикл будет выглядеть не просто круто, а супер круто!!!
Ладно, я немного отвлёкся, кастомайзинг для меня больная тема, оно и понятно — творческих границ не существует. Вернёмся к банальному восстановлению размера деталей. Одно из достоинств медного покрытия, это то, что вам не потребуется возиться с кислотой. Так как медный купорос, а кто помнит из курса школьной химии, он же сульфат меди, из которого приготавливается раствор, очень легко найти и купить в хозяйственном магазине.
Ну и второе ощутимое достоинство при покрытии медью, это то, что вам не нужно будет разыскивать бэушные батарейки для анода. Ведь можно использовать медную пластинку, или просто пучок медных проводов, свёрнутых в кабель. В воде (лучше дистиллированной) нужно будет растворить максимальное количество порошка медного купороса. Силу тока подбирайте так же как я описал выше, при нанесении цинкового покрытия.
Как вы поняли, ничего сложного в такой науке как химия и нанесении гальванического покрытия в домашних условиях нет. И теперь для вас не существует проблема восстановления изношенной детали, и вы сможете восстановить любой картер, или просто защитить многие детали от коррозии. А мотоциклисты смогут довольно ярко освежить внешний вид своего мотоцикла. Ведь я согласен, что хром есть хром, но пора вносить разнообразие в дизайн.
Кстати, кто хочет восстановить цинковое покрытие оцинкованного кузова своего автомобиля, то читаем об этом вот эту статью, удачи всем и творческих успехов!
suvorov-castom.ru
Сверление и обработка ситалла »
Патент РФ №2319601
Рис.1
Рис.2
Акт 1
Алмазные инструменты «МонАлиТ» для обработки ситалла и других специальных материалов в оптической промышленности изготавливаются отечественным производителем по уникальной запатентованной технологии (Патент РФ № 2319601).Их отличает от других типов инструментов предельное наполнение рабочей части алмазными зернами, которые привариваются в вакууме друг к другу (рис.1). В результате их предельного наполнения алмазом (рис.2) ресурс инструмента «МонАлиТ» в разы превышает ресурс обычных алмазных инструментов, изготовленных методом гальванического нанесения или горячего прессования . Многолетние результаты разработки и внедрения алмазного специального инструмента «МонАлиТ» в области обработки оптического стекла, в том числе и корпусов лазерных гироскопов из ситалла показали большую эффективность этого инструмента и перспективность, что подтверждается многолетним сотрудничеством с лидерами этого направления в России.
Предприятие «РусАтлант» начиная с 2006 года успешно проводит с НПО «Полюс им. Стельмаха» и др., совместные работы по внедрению новых инструментов «МонАлиТ». Изучены конструкции лазерных гироскопов и основных деталей из ситалла типа корпус, моноблок, пластина, призма, подложка. Проведён конструкторско-технологический анализ и разработан типовой ряд специальных инструментов для обработки деталей из ситалла типа корпус, моноблок, пластина, призма, подложка
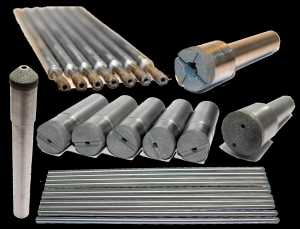
Выпускаются свёрла для обработки глубоких отверстий малых диаметров, вставки, тонкостенные сверла, конические наружные и внутренние зенкера, сферические торцевые фрезы,плоские радиальные и торцевые фрезы, чашечные, отрезные и профильные круги (Рис.4. Алмазные кольцевые сверла Ø1,5- Ø2,5 мм и чашка) Применение разработанных конструкций инструмента «МонАлиТ» по сравнению с гальваническим инструментом обеспечило повышение стойкости в среднем в 8 — 25 раз, при высокой точности обрабатываемых деталей. Например, кольцевое алмазное свёрло Ø2,4 мм при обработке глубоких главных каналов обеспечило обработку 80 корпусов датчика К5. При пересчёте в погонные метры было обработано 14 м каналов (см. Акт 1). В настоящее время на «РПЗ» все процессы механической обработки деталей лазерных гироскопов из ситалла переведены на обработку алмазным инструментом «МонАлиТ». Стало бесспорным, что алмазные инструменты «МонАлиТ» на металлической связке могут быть эффективно применены там, где алмазно-абразивные инструменты, изготавливаемые гальваническим закреплением алмазных зёрен и методом порошковой металлургии, не решают поставленных задач. Только с применением алмазного инструмента «МонАлиТ» может быть решена проблема комплексной автоматизации производства за счёт создания новых высокорентабельных, малозатратных технологий механической микрообработки на станках с программным управлением . Только для корпуса, насчитывающего 18 обрабатываемых отверстий, требуется 25 номиналов инструмента, а с учётом переходов, и центровочных инструментов — порядка 45 разных инструментов. Для обработки деталей из ситалла датчиков лазерных гироскопов типа корпус, моноблок, пластина, призма, подложка разработан комплект в составе 60 специальных алмазных инструментов , который успешно поставляется многие годы на РПЗ (Раменский приборостроительный завод, г. Раменское) который серийно выпускает корпуса лазерных гироскопов. (Акт 1). При этом достигается повышение производительности обработки в 2-3 раза, повышение стойкости по сравнению с гальваническим инструментом в 10-25 раз, улучшается качество обрабатываемой поверхности, улучшаются электрические параметры опто-электронных приборов: добротность, прецизионность, стабильность во времени.
Заказать инструменты можно по телефону и через электронную почту
Телефон: +7 (499) 745-09-12 моб. +7 916 385-01-02
Факс: +7 (499) 745-09-11
Email: [email protected]
Email: [email protected]
Доставка инструмента осуществляется для Москвы самовывозом, для других городов через транспортную компанию «Деловые линии» (либо иным способом по договоренности с заказчиком).
Применение
Инструменты «МонАлиТ» поставляются на многие заводы холдингов Швабе и Авионика, в частности на ОАО «НПО «ПОЛЮС» им. М.Ф.Стельмаха» г. Москва, ОАО «Лыткаринский завод оптического стекла», г.Лыткарино, ОАО «Красногорский завод им. С. А. Зверева», г.Красногорск, ОАО «Вологодский оптико-механический завод», г.Вологда, ОАО «Тамбовский завод «Электроприбор», «РПЗ» г.Раменское, «Электроприбор» г. Тамбов, «Темп-Авиа» г.Арзамас, «Алексадр» г. Рязань» «Утёс» г. Саратов.
monalit.ru