Автоматическая сварка под флюсом — режимы сварки, параметры и порядок расчета. Источники питания сварки под флюсом
Сварка под флюсом
На первый взгляд может показаться, что одно из основных преимуществ сварки под флюсом — возможность получения большой глубины проплавления свариваемого металла — противоречит условиям сварки тонколистовой стали. Однако при определенных условиях сварка под флюсом допускает регулирование глубины проплавления металла, начиная от долей миллиметра, и поэтому хорошо известные ее достоинства могут быть использованы для сварки тонколистовой стали.
Успешное внедрение в производство сварки под флюсом изделий из тонколистовой стали стало возможным, главным образом, благодаря применению тонкой сварочной проволоки. Известны примеры сварки тонколистовой стали и обычной электродной проволокой диаметром, например, 4 мм. Однако в этом случае удавалось сваривать сталь толщиной не менее 3—4 мм при условии весьма тщательной сборки изделия.
Для сварки тонколистовой стали большое значение имеет применение приспособлений, облегчающих точную сборку изделия и обеспечивающих надежное поджатие к свариваемому стыку медной или флюсомедной подкладки, флюсовой подушки и т. п. Опыт показывает, что производительность автоматической сварки изделий из тонколистовой стали со сравнительно короткими швами зависит не столько от машинной скорости сварки, сколько от затрат времени на подготовительные и вспомогательные операции. Поэтому важной задачей является разработка эффективно действующих сборочных и сборочно-сварочных приспособлений.
Чем меньше величина тепловой энергии, передающейся от дуги основному металлу в процессе сварки, тем меньше глубина его проплавления и, следовательно, тем более тонкий металл можно сваривать без прожогов. Тепловая энергия, передаваемая основному металлу, может быть уменьшена за счет уменьшения мощности дуги или увеличения скорости ее перемещения по свариваемому соединению.
Для сварки тонколистовой стали в основном применяют уменьшение мощности дуги, а не увеличение скорости сварки. Это в значительной мере объясняется тем, что применение больших скоростей сварки (более 150—200 м/час) связано с жесткими требованиями к точности поддержания режима сварки, необходимостью тщательной очистки свариваемых кромок, с очень точной сборкой стыков, в ряде случаев со специальным наклоном изделия и электрода и т. п. При указанных скоростях сварки металл шва может быть поражен порами, поперечными трещинами и другими дефектами. Если при этом учесть, что производительность сварки тонколистовой стали, как указывалось выше, главным образом, зависит от затрат времени на установочные и подготовительные операции, то станет ясным, почему увеличение скорости не стало основным способом уменьшения погонной тепловой энергии.
Устойчивость процесса сварки
При сварке тонколистовой стали равномерность глубины проплавления имеет особенно важное значение. Если сваривая сталь толщиной более 4—5 мм, можно допустить колебание глубины проплавления в пределах ± 1 мм, не опасаясь возникновения прожогов, то в случае сварки тонких листов стали такое же колебание совершенно недопустимо.Равномерность глубины проплавления зависит от устойчивости режима сварки, главным образом, от колебаний сварочного тока. Колебания скорости сварки, а также напряжения дуги сказываются в меньшей степени. Исходя из этого, для сварки тонколистовой стали следует рекомендовать сварочные автоматы с постоянной скоростью подачи электродной проволоки, так как они обеспечивают практически почти постоянные значения тока при колебании напряжения в сети или случайных изменениях длины дуги в процессе сварки. При этом сохраняются почти постоянной глубина проплавления, а также количество наплавляемого металла. Сварочные головки с регулируемой скоростью подачи электродной проволоки в тех же условиях не обеспечивают постоянство тока и поэтому применять их не рекомендуется.
Понижение мощности дуги, требующееся для сварки тонколистовой стали, может быть осуществлено только до определенного предела, зависящего от диаметра электродной проволоки. Дальнейшее снижение мощности резко ухудшает устойчивость процесса сварки и приводит к неудовлетворительному формированию шва. В случае сварки переменным током этот предел достигается при значительно большей мощности дуги, чем в случае сварки постоянным током обратной полярности. Поэтому сварку тонколистовой стали рекомендуется осуществлять постоянным током обратной полярности (положительный полюс присоединен к электроду). В табл. 1 приведены полученные опытным путем значения минимально-допустимых сварочных токов для электродной проволоки различных диаметров при сварке под флюсом АН-348 постоянным током обратной полярности.
Таблица 1
Как следует из табл. 1, для обеспечения устойчивого горения дуги при понижении ее мощности необходимо увеличивать плотность тока в электроде, что практически достигается путем уменьшения диаметра электродной проволоки. Эту таблицу можно использовать для выбора диаметра электродной проволоки при сварке на заданном режиме.
При рассмотрении условий устойчивого горения электрической дуги пользуются ее статическими вольтамперными характеристиками. Вольтамперной характеристикой называется зависимость между током и напряжением дуги при постоянной ее длине. На фиг. 1 приведены такие характеристики для дуг различной длины. Каждая вольт- амперная характеристика дуги состоит из нескольких участков: падающего (с ростом тока напряжение падает), почти горизонтального (жесткий участок) и растущего (с ростом тока напряжение увеличивается). В зависимости от условии сварки, дуге соответствует тот или иной участок характеристики. Так, например, при сварке неплавящимся угольным или вольфрамовым электродом, при ручной сварке качественными электродами, при автоматической сварке под флюсом со сравнительно небольшой плотностью тока и в некоторых других случаях характеристика сварочной дуги является падающей с переходом к жесткой. При сварке под флюсом или в защитной газовой среде с повышенной плотностью тока в плавящейся электродной проволоке характеристика дуги становится растущей.
Если дуга имеет падающую вольтамперную характеристику, то устойчивое ее горение возможно только при том условии, что внешняя характеристика сварочного генератора также будет падающей, т. е. напряжение холостого хода генератора значительно превышает напряжение дуги при сварке.
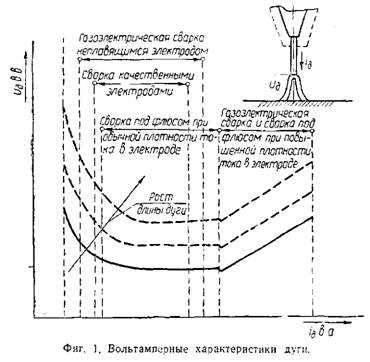
С ростом плотности тока в плавящемся электроде изменяются свойства сварочной дуги. Эти изменения настолько существенны, что позволяют предъявить совершенно другие требования к характеристикам источников питания постоянного тока.
Еще в 1950 г. в Институте электросварки им. Е. О. Па- тона было доказано, что при повышении плотности тока в плавящемся электроде может быть получен устойчивый процесс сварки при использовании в качестве источника питания генератора постоянного тока с жесткой внешней характеристикой (напряжение холостого хода генератора практически равно напряжению дуги при сварке). В отечественной и зарубежной практике в последние годы такие генераторы нашли широкое применение.
Генераторы с жесткими внешними характеристиками значительно более экономичны, чем обычные сварочные генераторы с крутопадающими характеристиками и высоким напряжением холостого хода, так как пропорционально снижению напряжения холостого хода генератора снижаются затраты на активные материалы, уменьшается вес генератора и его стоимость.
Чем больше скорость подачи электродной проволоки п меньше сварочный ток, тем труднее возбудить дугу путем непосредственной подачи электродной проволоки к изделию. Опыт показывает, что при использовании обычных сварочных генераторов с крутопадающей внешней характеристикой в ряде случаев этот способ возбуждения дуги практически оказывается неосуществимым. Совершенно иное наблюдается в случае применения генераторов с жесткими внешними характеристиками. Резкое нарастание тока при закорачивании электрода на изделие обеспечивает безотказное возбуждение дуги. Короткое замыкание не наносит ущерба генератору, так как тонкая электродная проволока выполняет роль плавкой вставки в цепи, ограничивая время протекания и величину тока короткого замыкания.
В тех случаях, когда генераторы с жесткими внешними характеристиками по какой-либо причине не могут быть применены для сварки тонкого металла, следует применять генераторы с весьма пологопадающими характеристиками, т. е. с большой величиной тока короткого замыкания.
Чем резче изменяется ток в цепи при случайных изменениях длины дуги, тем интенсивнее протекают процессы саморегулирования и тем быстрее восстанавливается заданный режим сварки. Генераторы с крутопадающими внешними характеристиками дают значительно меньшие изменения тока при случайных колебаниях длины дуги, чем генераторы с пологопадающими, жесткими или растущими характеристиками, благодаря чему обеспечивают большую устойчивость процесса сварки тонкой электродной проволокой.
Весьма характерно влияние внешних характеристик генераторов на процесс сварки и формирование шва при изменении величины зазора в соединении. Опыт показывает, что в случае питания дуги от генераторов с жесткой или пологопадающей внешней характеристикой можно допустить большие по величине зазоры в стыке, не нарушая нормального формирования шва. Такое же явление наблюдается при увеличении плотности тока в электроде.
Таблица 2
В табл. 2 приведены режимы сварки стыковых соединений стали толщиной 3 мм, собранных с постепенно возрастающим зазором от 0 до 5 мм при длине образцов 500 мм. Образцы сваривались электродной проволокой диаметром 3 мм при питании от генератора с крутопадающей внешней характеристикой и генератора с пологопадающей характеристикой. Один из образцов был сварен электродной проволокой диаметром 1,6 мм при питании от генератора с крутопадающей характеристикой. Как следует из табл. 2 и фиг. 2, где изображены образцы сварных соединений, в случае внешней характеристики генератора, приближающейся к жесткой (пологопадающей), а также в случае большей плотности тока в электроде (меньший диаметр электрода), максимальный зазор, при котором еще происходит правильное формирование шва, значительно больше.
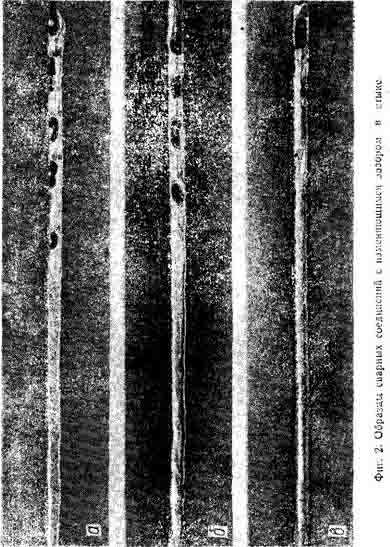
Не следует считать, что приведенные в таблице максимальные зазоры могут быть рекомендованы как допустимые при сборке стыков. В данном случае имеет место плавное возрастание зазора, что не равноценно резким изменениям зазоров, которые могут наблюдаться в практике.
Влияние формы внешней характеристики, а также плотности тока на формирование швов при сварке с зазорами в стыке связано, по-видимому, с изменением интенсивности процессов саморегулирования.
При автоматической сварке стыкового соединения одно из активных пятен дуги расположено на расплавленном металле ванны, заполняющей разделку. В отдельные моменты времени скорость перемещения ванны расплавленного металла может отличаться от скорости движения электрода вдоль стыка. Одной из причин этого бывает изменение величины зазора между свариваемыми кромками или изменение зазора между подкладкой и свариваемыми листами.
При увеличении зазора в стыковом соединении или возникновении большего зазора между подкладкой и свариваемыми листами скорость перемещения ванны расплавленного металла уменьшается. Так как скорость движения электрода при этом остается прежней, имеет место рост дугового промежутка. Резкое увеличение дугового промежутка вызывает обрыв дуги и нарушение процесса сварки. При плавном удлинении дуги процесс может не нарушиться, активное пятно успеет занять новое положение, обеспечивая восстановление прежней длины дуги.
Увеличение интенсивности саморегулирования дуги, имеющее место в случае применения генераторов с жесткими внешними характеристиками или при повышенной плотности тока в электроде, в известных пределах может предотвратить возникновение прожогов. Благодаря интенсивному саморегулированию значительное удлинение или обрывы дуги не будут наблюдаться при отставании ванны жидкого металла в месте увеличившегося зазора. При этом длина дуги будет поддерживаться постоянной и опасный участок с увеличенным зазором может быть пройден без нарушения процесса сварки (без обрывов дуги, прожогов и пр.). Этот участок от остальной части шва будет отличаться только меньшим усилением шва или даже полным отсутствием усиления.
Как известно из практики автоматической сварки под флюсом, с увеличением плотности тока в электроде глубина проплавления заметно возрастает. Например, при сварке на токе 500 а увеличение плотности тока приблизительно в 3 раза, за счет уменьшения диаметра электродной проволоки от 5 до 3 мм, вызывает увеличение глубины проплавления на 25%. Так как переход к сварке тонкой электродной проволокой связан с еще большим увеличением плотности тока в электроде, то возникает опасение, не может ли интенсивный рост глубины проплавления в этом случае стать препятствием на пути применения тонкой электродной проволоки и повышенной плотности тока для сварки тонколистовой стали. Проведенные опыты показали, что это опасение несостоятельно.
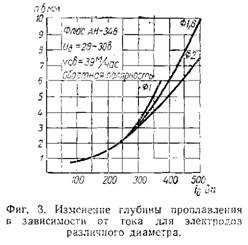
На фиг. 3 приведен график зависимости глубины проплавления от диаметра электродной проволоки. Как видно из графика, рост глубины проплавления с увеличением плотности тока (уменьшением диаметра электрода) наблюдается только при сварке на токах, превосходящих 300—350 а. Что же касается интересующего пас диапазона токов, применяемых для сварки тонкой стали (до 300—350 а), то в нем увеличение плотности тока не вызывает изменения глубины проплавления. Это объясняется некоторыми особенностями, отличающими маломощные электрические дуги от дуг большей мощности.
Также по теме:
Сварка стальных листов. Методы сварки тонких листов стали.
Сварочные станки. Оборудование для сварки тонколистовой стали.
svarder.ru
Сварка под флюсом (SAW) | Сварка и сварщик
При сварке под флюсом сварочная дуга горит между изделием и торцом сварочной проволоки. По мере расплавления проволока автоматически подается в зону сварки. Дуга закрыта слоем флюса. Сварочная проволока перемещается в направлении сварки с помощью специального механизма (автоматическая сварка) или вручную (полуавтоматическая сварка).
Под влиянием тепла дуги основной металл и флюс плавятся, причем флюс образует вокруг зоны сварки эластичную пленку, изолирующую эту зону от доступа воздуха. Капли расплавляемого дугой металла сварочной проволоки переносятся через дуговой промежуток в сварочную ванну, где смешиваются с расплавленным основным металлом. По мере перемещения дуги вперед металл сварочной ванны начинает охлаждаться, так как поступление тепла к нему уменьшается. Затем он затвердевает, образуя шов. Расплавляясь, флюс превращается в жидкий шлак, который покрывает поверхность металла и остается жидким еще некоторое время после того, как металл уже затвердел. Затем шлак затвердевает, образуя на поверхности шва шлаковую корку.
Одной из разновидностей этого способа сварки является сварка по флюсу. При этом используется значительно меньшая толщина слоя флюса, чем при сварке под флюсом. Дуга горит в условиях свободного доступа воздуха. Расплавляемый металл проволоки при переходе через дуговой промежуток не имеет шлаковой защиты. Металл сварочной ванны и шов покрыты тонким слоем шлака. При сварке по флюсу металл значительно хуже защищен от воздуха, чем в процессе сварки под флюсом. Кроме того, излучение дуги и интенсивное выделение дыма и паров оказывают вредное действие на обслуживающий персонал. Этот способ сварки используется для сварки алюминия и его сплавов.
Оборудование для сварки под флюсом: характеристики источника питания, тип тока
Промышленность выпускает два типа аппаратов для дуговой сварки под флюсом:
- С постоянной скоростью подачи электродной проволоки, не зависимой от напряжения на дуге (основанные на принципе саморегулирования сварочной дуги) – для сварки проволокой до 3 мм
- С автоматическим регулированием напряжения на дуге и зависимой от него скоростью подачи электродной проволоки (аппараты с авторегулированием) – для сварки проволокой диаметром более 3 мм.
В сварочных головках с постоянной скоростью подачи при изменении длины дугового промежутка восстановление режима происходит за счет временного изменения скорости плавления электрода вследствие саморегулирования дуги. При увеличении дугового промежутка (увеличение напряжения на дуге) уменьшается сила сварочного тока, что приводит к уменьшению скорости плавления электрода. Уменьшение длины дуги вызывает увеличение сварочного тока и скорости плавления. В этом случае используют источники питания с жёсткой вольтамперной характеристикой (см. статью Вольт-амперная характеристика дуги).
В сварочных головках с автоматическим регулятором напряжения на дуге нарушение длины дугового промежутка вызывает такое изменение скорости подачи электродной проволоки (воздействуя на электродвигатель постоянного тока), при котором восстанавливается заданное напряжение на дуге. При этом используют аппараты с падающей вольтамперной характеристикой.
Аппараты этих двух типов отличаются и настройкой на заданный режим основных параметров: сварочного тока и напряжения на дуге. На аппаратах с постоянной скоростью подачи заданное значение сварочного тока настраивают подбором соответствующего значения скорости подачи электродной проволоки. Напряжение на дуге настраивают изменяя напряжение холостого хода внешней характеристики источника питания.
На аппаратах с авторегулированием напряжение на дуге задается на пульте управления и автоматически поддерживается постоянным во время сварки. Заданное значение сварочного тока настраивают изменением крутизны внешней характеристики источника питания.
Настройка других параметров режима сварки (скорости сварки, вылета электрода, высоты слоя флюса и др.) аналогична для аппаратов обоих типов и определяется конструктивными особенностями конкретного аппарата.
Конструкция соединения для сварки под флюсом
Форму разделки кромок для механизированной сварки под флюсом выбирают в зависимости от толщины свариваемых изделий и в соответствии с:
- ГОСТ 8713-79 "Швы сварных соединений. Автоматическая и полуавтоматическая сварка под флюсом. Основные типы и конструктивные элементы"
- ГОСТ 11533-75 "Автоматическая и полуавтоматическая сварка под флюсом. Соединения сварные под острыми и тупыми углами"
- ГОСТ 16098-70 "Швы сварных соединений из двухслойной коррозионно-стойкой стали"
- ГОСТ 15164-78 "Сварные соединения и швы. Электрошлаковая сварка. Основные типы и конструктивные элементы".
Область применения сварки под флюсом
Механизированная сварка под флюсом является одним из основных способов сварки плавлением. Если в первые годы освоения сварку под флюсом применяли только при изготовлении сварных конструкций из низкоуглеродистых сталей, то сейчас успешно сваривают низколегированные, легированные и высоколегированные стали различных классов, сплавы на никелевой основе. Освоена сварка под флюсом титана и его сплавов. Под флюсом сваривают медь и ее сплавы, а также алюминий и алюминиевые сплавы. Изделия, полученные сваркой под флюсом, надежно работают при высоких температурах и в условиях глубокого холода, в агрессивных средах, в вакууме и в условиях высоких давлений.
Наиболее выгодно использовать механизированную сварку под флюсом при производстве однотипных сварных конструкций, имеющих протяженные швы и удобных для удержания флюса. Экономически целесообразнее сваривать под флюсом металл толщиной от 1,5 - 2,0 до 60 мм. Нецелесообразно сваривать конструкции с короткими швами.
Технологии сварки под флюсом одной или несколькими проволоками
Существуют разновидности сварки под флюсом, когда в некоторых случаях целесообразно применение двухдуговой или многодуговой сварки. При этом дуги питаются от одного источника или от отдельного источника для каждой дуги. При сварке сдвоенным (расщепленным) электродом дуги, горящие в общую ванну, питаются от одного источника. Это несколько повышает производительность сварки за счет повышения количества расплавленного электродного металла.
Электроды по отношению к направлению сварки могут быть расположены последовательно или перпендикулярно. При последовательном расположении глубина проплавления шва несколько увеличивается, а при перпендикулярном уменьшается. Второй вариант расположения электродов позволяет выполнять сварку при повышенных зазорах между кромками. Изменяя расстояние между электродами, можно регулировать форму и размеры шва. Удобно применение этого способа при наплавочных работах. Однако недостатком способа является некоторая нестабильность горения дуги.
При двухдуговой сварке используют два электрода (при многодуговой несколько). Дуги могут гореть в общую или раздельные сварочные ванны (когда металл шва после первой дуги уже полностью закристаллизовался). При горении дуги в раздельные сварочные ванны оба электрода обычно перпендикулярны плоскости изделия. Изменяя расстояние между дугами, можно регулировать термический цикл сварки, что важно при сварке закаливающихся сталей. Эта схема позволяет вести сварку на высоких скоростях, в то время как применение повышенного тока при однодуговой сварке приводит к несплавлениям - подрезам по кромкам шва. При двухдуговой сварке вторая дуга, горящая в отдельную ванну, электродом, наклоненным углом вперед (угол α=45-60°), частично переплавляет шов, образованный первой дугой, и образует уширенный валик без подрезов. Для питания дуг с целью уменьшения магнитного дутья лучше использовать разнородный ток (для одной дуги - переменный, для другой - постоянный).
weldering.com
§ 2. Источники питания сварочной дуги.
Для дуговой сварки используется как постоянный, так и переменный ток. Источниками постоянного токаявляютсягенераторы постоянноготока исварочные выпрямители– селеновые, германиевые и кремниевые.
Генераторы постоянного тока изготовляют стационарными и передвижными с приводом от электродвигателя и от двигателя внутреннего сгорания.
При сварке переменнымтоком преимущественно используютсварочные трансформаторы, которые распространены шире, чем генераторы. Сварочные трансформаторы проще в изготовлении и эксплуатации , имеют небольшой вес и меньшую стоимость, более высокий кпд и значительно долговечнее.
Источники постоянного токаизготавливаютоднопостовымиимногопостовыми, апеременноготолькооднопостовыми.
§ 3. Ручная дуговая сварка.
Производится сварочными электродами, подача которых в дугу и перемещение вдоль заготовки выполняется вручную рукой сварщика. Для удержания электрода и подвода к нему тока сварщик пользуется электрододержателем. Для защиты от светового и ультрафиолетового излучения дуги лицо сварщика закрывается предохранительным щитком или маской с тёмными стеклами, а тело и руки – брезентовой спецодеждой и рукавицами. Рабочее место сварщика помещается в специальной кабине.
Электродыдля ручной сварки представляют собойпроволочные стержнис нанесённым на них покрытием. Стержень электрода изготавливается из специальной сварочной проволоки повышенного качества, с пониженным содержаниемPиS. ГОСТ предусматривает 56 марок проволоки диаметром 0,3…12 мм.
Схема процесса сварки следующая: дуга горит между стержнем электрода и основным металлом. Стержень плавится и расплавленный металл каплями стекает в сварочную ванну. Вместе со стержнем плавится покрытие электрода, образуя газовую защитную атмосферу вокруг дуги и шлаковую ванну на поверхности расплавленного металла. По мере движения дуги происходит затвердевание сварочной ванны и образование сварного шва. Жидкий шлак по мере остывания образует на поверхности шва твёрдую шлаковую корку.
Ручная дуговая сварка широко применяется в производстве металлоконструкций для сварки различных материалов малых и средних толщин (от 2…30 мм). Особенно она выгодна и удобнапри выполнениикоротких и криволинейныхшвов в любых пространственных положениях (нижнем, вертикальном, потолочном), а также при наложении швов в труднодоступных местах. Недостаток – низкая производительность.
§ 4. Автоматическая дуговая сварка под флюсом.
При этой сварке используется процесс, принципиально отличающийся от ручной сварки покрытыми электродами. Характерные особенностиавтоматической сварки заключается в следующем:
сварка ведётся непокрытой электродной проволокой;
защита дуги и сварочной ванны осуществляется флюсом;
подача и перемещение электродной проволоки механизирована.
Дуговая сварка под флюсом производится автоматическими сварочными головками или самоходными тракторами, перемещающимися непосредственно по изделию. Основным их назначением является подача электродной проволоки в дугу и поддержание постоянного режима сварки в течение всего процесса.
Преимущества: повышение производительности сварки в 20…25 раз, повышение качества сварных соединений и уменьшение себестоимости 1 м сварного шва.
studfiles.net
Автоматическая сварка под флюсом - режимы сварки и основные параметры
Все нужные работнику значения обозначаются в ТУ на сварку того или иного изделия. Если такие данные отсутствуют, то оптимальные параметры режима сварки подбираются опытным (экспериментальным) путем на образцах из того же металла (сплава). Существует несколько методик получения неразъемных соединений, но при автоматизации процесса чаще всего выбирается сварка электродуговая под флюсом. Такая технология считается наиболее эффективной. О ее режимах, порядке расчетов основных величин и пойдет речь.
Примечание. Сварка под флюсом в автоматическом режиме целесообразна, если толщина обрабатываемого изделия (мм) в пределах 5 – 50.
Особенности
- Тщательная подготовка кромок образцов (раздела). Наличие инородных фракций делает структуру шва пористой, что провоцирует в дальнейшем образование трещин по всей его длине.
- Автоматическая сварка ведется сразу же по окончании обработки кромок скрепляемых деталей.
- Повышенные требования к металлам (и основы, и стержня электрода).
Параметры режимов сварки под флюсом
Характеристики тока (полярность, величина)
Они напрямую отражаются на форме сварного шва. К чему приводит повышение величины тока?
- За счет более интенсивного расплавления металлов (кромок деталей и стержня электрода) объем сварочной ванны возрастает. Это связано с повышением температуры в рабочей зоне.
- Увеличивается давление дуги на расплав (жидкую субстанцию), который частично выдавливается из-под электрода, и глубина ее проникновения в металл основы становится больше. Следовательно, существует прямая зависимость между глубиной проплава (hi) и силой тока сварки (Iсв).
hi = к Iсв, где к – коэффициент, зависящий от полярности тока, типа флюса и сечения электрода. Некоторые его значения приведены в таблице.
Подразумевается, что сварка ведется при включении с прямой полярностью. Смена ее на обратную, с применением флюсов, увеличивает глубину проплавления в среднем на 45%. Работа переменным током – примерно на ¼.
Параметры дуги
Длина (lд). Рекомендуемое ее значение указывается в паспорте на электроды. От его неизменности в ходе сварки зависит, прежде всего, ширина получаемого шва.
Напряжение (Uд). Зависит от длины. Для дуги при сварке под флюсом справедлива формула Uд = а (напряжение источника питания) + b (падение U на единицу длины дуги) х lд.
Скорость сварки
Она влияет на процентное содержание основного металла в получившемся шве и его форму. При изменении скорости меняется и пространственная ориентация дуги (угол наклона относительно поверхности ванны). Здесь наблюдается взаимосвязь между несколькими параметрами – диаметр электрода, напряжение дуги и сила тока.
При автоматизации процесса скорость сварки выбирается в пределах 35 (±5) м, на начальном этапе – 20.
Дополнительные параметры
- Диаметр проволоки электрода. При автоматической сварке под флюсом рекомендуемые значения – от 2 до 6 мм.
- Скорость ее подачи в рабочую зону.
- Компонентный состав флюса.
- Вылет электрода.
- Пространственная ориентация шва.
Порядок расчета режимов автоматической сварки
Далее – лишь общая последовательность действий, независимо от марки стали, вида флюса и используемых электродов.
- Выбираются исходные данные – требуемый тип неразъемного соединения, толщина материала, особенности станочного оборудования (производительность, мощность).
- Составляется чертеж (в разрезе и в масштабе) будущего шва и определяются его параметры.
- Вычисляются оптимальные значения силы тока, диаметра электрода, скорость его подачи.
- Рассчитывается скорость автоматической сварки.
- Определяется площадь провара. Если все проделано правильно, ее значение должно быть идентично шву на чертеже. Допустимые отклонения – не более ± 10%. При несоблюдении этого условия корректировке в первую очередь подлежат параметры дуги (напряжение) и скорость автоматизированной сварки.
В статье всего лишь общая информация, дающая начальное понятие об особенностях и режимах сварки под флюсом автоматом. Многое зависит от сорта стали (марки), используемого флюса и ряда других факторов. Начинающему сварщику не менее важно научится правильно находить соответствующие таблицы, которые помогают сделать необходимые расчеты режима.
ismith.ru
Особенности автоматической сварки под флюсом
- Содержимое:
- Что такое сварка под флюсом
- Сварочный флюс – что это
- Режимы сварки под флюсом
- Где применяется сварка флюсом
- Преимущества и недостатки сварки
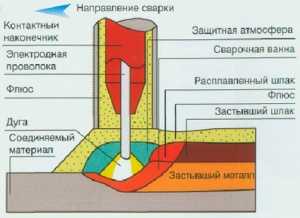
Что такое сварка под флюсом
Сущность сварки под флюсом сводится к тому, что дуга между сварной проволокой и обрабатываемым материалом горит под слоем гранулированного порошка. Под воздействием температуры электрод и гранулы расплавляются. В результате, вокруг сварной ванны создается эластичная пленка, полностью перекрывающая доступ воздуха и защищающая от негативного воздействия дугу и расплавленный металл.Компоненты флюса по мере остывания превращаются в шлак покрывающий шов. После окончания работ, наплавленная корка легко отстает от металла и удаляется механическим методом. Оставшийся флюс собирается и используется в дальнейшем.
Оборудование для сварки под флюсом можно разделить на две категории:
- Роботизированная автоматическая сварка под слоем флюса угловых швов и ровных поверхностей. Направление, скорость движения электрода задает машина. Роботизированный способ отличается максимальным качеством наложения сварного шва, прочностью соединения и скоростью работы.В последнее время широко используется так называемая тандемная сварка - когда два электрода располагаются в одной плоскости параллельно друг другу. Технология автоматической сварки под флюсом в тандеме, существенно увеличивает качество сварного шва и скорость выполняемых работ.Еще одним преимуществом тандемного метода является быстрое возбуждение дуги, а также минимальный размер сварочной ванны.
- Полуавтоматическая сварка. Сварную проволоку направляет сварщик, он же контролирует вылет электрода. Подача проволоки осуществляется автоматически. От мастера требуется выбрать скорость и угол наклона электрода, а также подобрать наиболее подходящую мощность напряжения дуги.
Техника автоматической сварки под слоем флюса подробно описана в ГОСТ 8713 79. В нормах прописаны виды сварных соединений, обеспечивающие максимальную прочность конструкции. Санитарные нормы и требования к технике безопасности указываются в ГОСТ 9087 81.
Сварочный флюс – что это
По сути, флюс, это гранулированный порошок с диаметром от 0,2 до 4 мм, используемый для защиты дуги, сварной ванны и наплавляемого металла, от вредного внешнего воздействия.Во время проведения работ создается флюсовая подушка, основным предназначением которой является:
- Создать надежную защиту сварочной ванны, в виде газового облака и шлака, от воздействия негативных факторов: сырости, пыли, низкой температуры воздуха и т.д.
- Обеспечить стабильную дугу, во время которой будет осуществляться непрерывный процесс формирования шва в сварочной ванне.
- Улучшить качество соединения и обеспечить сварной шов необходимыми свойствами.
- Вывести примеси из металла в зону шлакообразования.
- Способ производства. Существуют плавленые и неплавленые разновидности флюса. Первые, рудоминеральные, предварительно плавятся в печи, после подвергаются дополнительному прокаливанию и формированию в гранулы. Неплавленые или керамические флюсы производят путем смешивания минералов и ферросплавов с добавлением жидкого стекла.
- Химический состав сварочного флюса. Существуют оксидные, солеоксидные и солевые материалы. Каждый из видов порошка используется для определенной цели.
- Область применения сварки под флюсом. Для сварки низколегированных сталей применяют оксидные материалы. Во время работ по переплавке шлака, обработки высоколегированных или углеродистых сталей, а также цветных металлов применяют солевые флюсы. Так как в составе электрода отсутствуют оксиды, обеспечивается чистота шва и сохраняется пластичность соединения. Солевые материалы используют для работ с титаном.
Расход флюса зависит от химического состава и способа производства материала. Также на количество затрат влияет мощность сварочного тока, напряжение дуги и скорость проведения работ.
Наиболее экономичным считается сварочное оборудование для автоматической сварки под флюсом. Блок управления станка рассчитывает оптимальную скорость движения электрода, а также мощность и силу тока. Дефекты сварки под флюсом, в частности, по причине человеческого фактора, сведены к нулю.При ручной работе с полуавтоматом вносят дополнительные коэффициенты нормирования сварки, связанные с пространственным положением шва и его длиной. Если длина соединения не более 20 см, учитывают коэффициент изменений равный 1,2; от 20-50 см 1,1; свыше полуметра поправка равна 1. Полученный результат помогает точно рассчитать время, необходимое для проведения работ, а также высчитать расход флюсового материала.
Основными причинами образования пор при сварке является водород и азот. При использовании флюса создается защитное облако, не дающее этим веществам вступить в реакцию с расплавленным металлом.
Режимы сварки под флюсом
Особенностью процесса сварки под флюсом является необходимость точного расчета нескольких важных параметров, оказывающих влияние на затраты флюса:- Род и полярность тока. Источники питания для сварки под флюсом могут быть трансформаторного и инверторного типа. Инвертор использует принцип двойного преобразования электрического тока, в результате давая на выходе стабильные высокочастотные показатели, что приводит к уменьшению расхода порошка.
- Напряжение сварной дуги.
- Диаметр используемой проволоки. Во время сварки флюсовый порошок расходуется на создание шлакового слоя вокруг шва. Соответственно, чем толще используемая проволока и стыки соединения, тем больше нужно будет гранул для защиты. Плавленые сварочные флюсы, как правило, расходуются быстрее, чем керамические. Работы с разделкой кромок также требуют больших затрат флюсового порошка.
- Скорость ведения электрода. Механизированная сварка экономнее, так как обеспечивается стабильная скорость движения электрода, отсутствуют рывки.
- Толщина обрабатываемого материала.
- Отходы сварочного флюса. В результате проведения работ, на шве образуется определенное количество защитного шлакового слоя. Расход гранулированного флюсового порошка в определенной мере зависит от того, какое количество отходов получается на выходе.
Режимы автоматической сварки под флюсом, а также параметры необходимые для выполнения работ полуавтоматом, можно рассчитать по существующим таблицам, находящимся в инструкции по эксплуатации сварного оборудования.
Где применяется сварка флюсом
В свое время характеристики процесса сварки с использованием флюса произвели настоящую революцию в промышленности. Первоначально, способ сварочных работ предназначался только для обработки низкоуглеродистой стали. Сегодня производители флюсов заявляют о возможности применения порошка практически для любых, в том числе тугоплавких сталей и металлов, тяжело поддающихся обработке.Металлургические процессы при сварке позволили использовать полностью механизированные установки и полуавтоматы для следующих целей:
- Сварка кольцевых швов. Основной сложностью процесса является необходимость удержать сварную ванну и избежать растекания металла. Для выполнения работ используют станки ЧПУ. Может потребоваться ручная подварка.
- Сварка вертикальных швов. Выполняется с принудительным или свободным формированием шва. Лучшие характеристики прочности соединения были достигнуты при работе с металлами 20-30 мм.
- Сварка труб малого и большого диаметра. Первоначально с помощью полностью автоматических станков научились варить трубы небольшого диаметра, но впоследствии с развитием технологии обработки, получилось освоить метод позволяющий проводить работы с материалом большого диаметра. Характеристики используемого оборудования обеспечили необходимую прочность соединения и позволили ускорить процесс сборки труб для нефте- и газопроводов.
Проведение всех производственных работ строго регламентируется в соответствии с существующей технологической картой сварки. Любые нарушения приводят к серьезным штрафным санкциям.
Преимущества и недостатки сварки
Можно выделить некоторые преимущества сварки под флюсом:Производительность. По сравнению с обычной ручной сваркой, скорость работ увеличена в 5-10 раз.
- Качество шва. Флюс предотвращает разбрызгивание стали, обеспечивает защиту от появления пор в шве. Особенностью сварки высоколегированных сталей является необходимость защиты от попадания на поверхность шлака и капель расплавленного металла. Работы с помощью флюсового порошка создают оптимальные условия для обработки деталей.
- Экономия. Расход электроэнергии по сравнению с обычной электродной сваркой меньше приблизительно на 30%.
- Универсальность. Флюсовый порошок позволяет варить металлы разной плотности и структуры. Метод сварки подойдет для цветных металлов, низкоуглеродистый сталей, титана и т.д.
- Ограниченная маневренность автоматов.
- Возможность проведения работ с максимальным отклонением от плоскости не более 10-15°.
- Влияние характеристик флюса на качество проводимых работ. Остатки порошка механизированным образом убираются в хранилище и используются повторно. Сухой порошок быстро впитывает влагу. Чтобы обеспечить высокие характеристики шва, потребуется контроль влажности флюса.Проверку делают с помощью забора порошка, высушивания при температуре 105°С. После контрольный образец взвешивают. Если разница составляет более 0.1% от массы невысушенного состава, весь порошок отправляют на сушку.
Некоторые виды сварочных работ рекомендовано проводить только с использованием флюса. Применение гранулированного порошка позволяет сократить расходы электроэнергии и улучшить качество и прочность сварочного шва в несколько раз.
stroy-plys.ru
Источники питания для сварки под флюсом
Какой должна быть внешняя ВАХ источника питания дуги для сварки под флюсом [c.107]Для сварки под флюсом используют источники питания дуги переменного и постоянного тока, обеспечивающие силу тока от 50 до 2000 А с падающей вольт-амперной характеристикой и продолжительностью включения 100 %. Механизмы подачи электродной проволоки не имеют существенных отличий от аналогичных устройств для других способов сварки. Состоят они из двигателя постоянного тока с редуктором и содержат одну или более пар подающих и правящих роликов в зависимости от диаметра подаваемой проволоки. Для подачи одновременно двух проволок используют двойные механизмы. Проволоки в этом случае могут располагаться поперек стыка деталей или вдоль его друг за другом. Скорость подачи проволоки может изменяться специальными устройствами в зависимости от напряжения на дуге автоматически или независимо вручную. [c.139]
Электрошлаковая сварка осуществляется также постоянным током. В этом случае используются источники питания с жесткими (пологопадающими) внешними характеристиками, обладающие достаточно широким диапазоном регулирования напряжения, применяемые для сварки под флюсом и многопостовой дуговой сварки. Так, достаточно широкое применение нашел сварочный выпрямитель ВДУ-1602 УЗ. [c.150]Шланговый полуавтомат, состоящий из узлов полуавтомата ПДЩ-500, предназначенного для сварки под флюсом. Состоит из сварочной горелки (пистолета) с гибким кабелем и шлангами механизма подачи сварочной проволоки шкафа распределительного устройства и источника питания сварочным током (техническая характеристика приведена в табл. 4) [c.433]
Пример 2. Выбрать источник питания переменного тока для сварки под флюсом в автоматическом режиме на переменном токе силой 800 А. [c.52]
В книге описаны электрические, магнитные и тепловые свойства сварочной дуги изложены данные о конструкциях современных сварочных автоматов и полуавтоматов для сварки под флюсом и в атмосфере защитных газов приведены краткие сведения по устройству и обслуживанию источников питания дуговой сварки освещены вопросы сварки цветных металлов и сплавов описаны методы контроля и испытания сварных соединений и конструкций. [c.223]
Трактор АДС 1000-2 рассчитан на сварку электродной проволокой диаметром 3—6 мм силой тока до 1200 А. Скорость сварки равна 15—70 м/ч. Применяется обычно для сварки под флюсом переменным током. В качестве источника питания может использоваться трансформатор ТСД-1000-3. Без флюса и электродной проволоки масса трактора около 60 кг. [c.205]
Участки I и II ВАХ соответствуют режимам сварки, применяемым при ручной сварке плавящимся покрытым электродом, а также неплавящимся электродом в среде защитных газов. Механизированная сварка под флюсом соответствует II области и частично захватывает III область при использовании тонких электродных проволок и повышенной плотности тока, сварка плавящимся электродом в защитных газах соответствует III области ВАХ. Для питания дуги с падающей или жесткой ВАХ применяют источники питания с падающей или пологопадающей внешней характеристикой. Для питания дуги с возрастающей ВАХ применяют источники тока с жесткой или возрастающей внешней характеристикой. [c.57]
К общепромышленным относятся источники питания для ручной дуговой сварки покрытыми электродами, а также для механизированной сварки под флюсом. [c.95]
Для питания дуги с жесткой характеристикой применяются источники тока с падающей внешней характеристикой (ручная дуговая сварка, автоматическая сварка под флюсом, сварка в защитных газах неплавящимся электродом). Взаимосвязь статической характеристики дуги 1 и падающей характеристики источника питания дуги 2 приведена на рис. 18.7. [c.378]
Для выполнения автоматической сварки под флюсом используется комплект оборудования, включающий в себя источник питания, сварочный аппарат, механическое оборудование и приспособления, обеспечивающие необходимую точность сборки изделия. Этот комплект называется сварочной установкой. [c.394]
Трансформаторы снабжены фильтрами для подавления радиопомех. Кроме применения для автоматической и полуавтоматической сварки под флюсом, трансформаторы ТСД-1000-3 и ТСД-2000-2 применяются в качестве источника питания для термической обработки сварных соединений из легированных и низколегированных сталей. [c.144]
Для ручной дуговой сварки применяют любые источники питания с крутопадающей внешней характеристикой для автоматической н полуавтоматической сварки под флюсом — источники питания большой мощности с пологопадающими, а иногда с жесткими характеристиками для сварки в углекислом газе — источники-питания постоянного тока с жесткими или возрастающими характеристиками. [c.62]
В универсальных однопостовых выпрямителях ВСУ-300 и ВСУ-500 при помощи дросселя насыщения могут быть получены жесткие, пологопадающие и крутопадающие характеристики. Следовательно, они могут служить источниками питания для автоматической сварки под флюсом, сварки в защитных газах и ручной дуговой сварки. Технические данные выпрямителей типа ВСУ приведены в табл. 30. [c.81]
При автоматической сварке под флюсом с саморегулированием дуги, когда статическая характеристика дуги также жесткая, внешняя характеристика источника питания для повышения интенсивности саморегулирования должна быть пологопадающей (рис. 33, кривая 3). [c.51]
Третья буква — способ сварки (Ф — под слоем флюса, Г — в среде защитных газов, У — универсальный источник питания для нескольких способов сварки). Отсутствие буквы на третьем месте соответствует ручной сварке покрытыми электродами. [c.28]
Различают источники питания для ручной дуговой сварки (РДС) штучным электродом, для полуавтоматической и автоматической сварки сплошной или порошковой проволокой в защитных газах или под слоем флюса одно-или многопостовые, использующие энергию электрической сети или двигателей внутреннего сгорания источники общепромышленного назначения и специализированные, созданные для решения конкретных технологических задач. [c.219]
Сварочные выпрямители типа ВСУ и ВДУ являются универсальными источниками питания дуги. Они предназначены для питания дуги при автоматической и полуавтоматической сварке под флюсом, в защитных газах, порошковой проволокой, а также при ручной сварке. Выпрямители ВСУ, кроме обычных—блока трехфазного понижающего трансформатора и выпрямительного блока, имеют дроссель насыщения с четырьмя обмотками. Переключением этих обмоток можно получать жесткую, пологопадающую и крутопадающую внешние характеристики. Выпрямители ВДУ основаны на использовании в выпрямляющих силовых обмотках управляемых вентилей —тиристоров. Схема управления тиристорами позволяет получать необ-.ходимый для сварки вид внешней характеристики, обеспечивает широкий диапазон регулирования сварочного тока и стабилизацию режи.ма сварки при колебаниях напряжения питающей сети. [c.32]
Аргоно-дуговая и автоматическая сварка под флюсом титана производится на постоянном токе прямой полярности с использованием сварочной аппаратуры и источников питания дуги, применяющейся при газоэлектрической и автоматической сварке под флюсом сталей. Для уменьшения склонности к росту зерна в зоне термического влияния сварку титана следует производить с малой погонной энергией. [c.87]
Подавляющее больщинство источников питания, выпускаемых в СССР, имеет общее назначение как для однодуговой ручной сварки плавящимся электродом открытой дугой, так и для автоматической сварки под флюсом. В соответствии с большим разнообразием режимов сварки источники питания выпускаются различной мощности, регламентируемой ГОСТ. Каждый источник питания рассчитывается на определенное номинальное рабочее напряжение и соответствующий номинальный ток при заданной относительной продолжительности работы (ПР) или относительной продолжительности включения (ПВ) в прерывистом режиме. [c.56]
При автоматической сварке под флюсом статическая характеристика дуги также жесткая, но для обеспечения саморегулирования сварочного процесса статическая характеристика источника питания должна быть пологопадающей или жесткой. [c.13]
ИСТОЧНИКИ ПИТАНИЯ для РУЧНОЙ ДУГОВОЙ и АВТОМАТИЧЕСКОЙ СВАРКИ ПОД ФЛЮСОМ [c.85]
Эти многопостовые источники питания применяют для ручной дуговой сварки, автоматической сварки под флюсом и сварки в среде защитного газа. Они обеспечивают централизованное питание сварочных постов. [c.88]
При многопостовом питании каждый сварочный пост подключается к шинопроводу через отдельное балластное сопротивление. Схема подключения показана на рис. 8.20. Многопостовой источник (В) обслуживает п сварочных постов (СП1—СП ) через общий шинопровод (ШП). Каждый сварочный пост подключен к шинопроводу через балластное сопротивление (РБ), с помощью которого регулируют силу сварочного тока и получают падающую вольт-амперную характеристику для сварки. Для ручной дуговой сварки и сварки под флюсом выходное напряжение источника питания дуги обычно не изменяют. Многопостовые источники для сварки в углекислом газе отличаются тем, что в них имеется несколько выходных шинопроводов на разные напряжения холостого хода. Каждый сварочный пост в этом случае подключают к соответствующему шинопроводу с соответствующим напряжением. [c.150]
Флюсы для сварки титана относятся к разряду так называемых бескислородных, составленных на основе тугоплавюк фторидов и хлоридов щелочных и щелочноземельных металлов. Они должны обеспечивать устойчивое горение дуги, хорошее формирование шва, легкую отделимость шлаковой корки, отсутствие в шве шлаковых включений н других дефектов. В Институте электросварки им. Е. О. Патона АН УССР разработаны плавленые флюсы серии АНТ. Флюс АНТ-7, основным компонентом которого является фтористый кальций, обладает высокой температурой плавления (около 1380 С), что очень важно при сварке кольцевых швов и сварке электродной проволокой больших диаметров при больших плотностях тока. Использование этого флюса расширило область применения автоматической сварки. Для сварки используют стандартные источники питания автоматическая сварка под флюсом выполняется с большими скоростями (до 50—60 м/ч), что энергетически выгодно. [c.85]
В последние годы предприятиями России выпчскается значительное количество нового сварочного оборудования. Основу этого оборудования для сварки плавлением составляют источники питания для сварки штучными электродами, полуавтоматы и автоматы для сварки в среде защитных газов и под флюсом, а также установки для имп льсно-дуго-вой, плазменной и лазерной сварки и полуавтоматы и автоматы для термической резки. Наиболее систематизированные данные о сварочном оборудовании изложены в /7/. Выбор оборудования для сварочных операций в значительной мере определяется гфиня1Ъ1м способом сварки, но при этом необходимо руководствоваться следующими соображениями. [c.25]
Оборудование для сварки под флюсом состоит из электрической и механической частей. В электрическую часть входят источник питания дуги, сварочная цепь и цепь управления, в механическую — механизм подачи электродной проволоки, флюса н держателя. Перемещение изделия относительно дуги, кантовка свариваемых изделий, уборка флюса и др. производятся с помощью вспомогательного сварочного оборудования (стендов, маиппуляторов, вращателей, кантователей п др.). [c.86]
Полуавтоматы для сварки в защитных газах выполняются в основном по той же конструктивной схеме, что и полуавтоматы для сварки под флюсом. Полуавтомат состоит из легкой сварочной головки, переносного механизма подачи электродной проволоки, шкафа управления и специального источника питания постоянного тока. Отличительная особенность его — нали- [c.78]
При отсутствии специального сварочного оборудования и источников питания можно применять установки с однопроволочной электродной системой. В этом случае в качестве сварочной головки используются различные проволоко-подающие механизмы, например, головки от шланговых полуавтоматов, головки автоматов, предназначенных для сварки под флюсом и др. Источником тока могут служить любые сварочные трансформаторы или машины постоянного тока соответствующей мощности. [c.44]
Для сварки под флюсом на переменном токе автоматы серии АДФ укомплектованы сварочными трансформаторами ТДФ-1002, ТДФ-1601 и ТДФЖ-2002. Для сварки под флюсом и в среде защитного газа на постоянном токе автоматы серии АДФ и АДГ укомплектованы универсальными выпрямителями ВДУ-505 или ВДУ-1201. Высокое качество сварных изделий достигается совокупной стабилизацией выходных параметров автоматов данного типа и источников питания, которыми укомплектованы эти автоматы. [c.147]
Сварочные трансформаторы Сварочные трансформаторы являются широко распространенными однопостовыми источниками питания переменного тока для ручной дуговой сварки штучными электродами, автоматической сварки под флюсом, а также для аргонодуговой сварки неплавяшимся электродом (в виде установок). [c.55]
Источник питания для ручной дуговой сварки плавящимся электродом и автоматической сварки под флюсом должен иметь падающую внешнюю характеристику. Жесткая характеристика источников питания (рис. 56, кривая 3) необходима при выполнении сварки в защитных газах (аргоне, углекислом газе, гелии) и некоторыми видами. порошковых проволок, например ЭПС-15/2. Для сварки в защитных газах допустимы также источники питания с пологовозрастающи-м и в н е ш н и м и характеристиками (рис. 56, кривая 4). [c.136]
Источники питания для автоматической и механизированной сваркв под флюсом должны иметь пологопадающую характеристику, для сварки в защитных газах — жесткую или пологопадающую. [c.111]
Источники питания дуги классифицируют по следующим признакам роду тока —на источники постоянного и переменного тока общепромышленного назначения количеству одновременно подключаемых сварочных постов — на однопостовые и многопостовые назначению — на источники для ручной дуговой сваркн покрытыми электродами автоматической и механизированной сварки под флюсом сваркн в защитных газах электрошлаковой сварки плазменной сварки и резки источники специального назначения (для сварки трехфазной дугой, импульснодуговой сварки и др.) принципу действия и конструктивному исполнению специализированные источники питания в установках. [c.112]
Эле1кт1рическая дуговая сварка на постоянном токе получила-за последние годы весьма широкое развитие. Постоянный ток. применяется для сварки в полевых условиях при отсутствии-электроэнергии, при шланговой сварке под флюсом, для сварки плавящимся электродом в среде углекислого газа и аргона, для сварки легированных сталей а также во м.ногих случаях, где требуется особая стабильность процесса сварки. В результате за последние годы производство источников питания постоянного тока увеличилось с 15 до 22% от общего количества источников питания для дуговой сварки и в ближайшие годы это количество будет доведено до 30%. [c.9]
Источниками питания автоматов для дуговой сварки под флюсом служат сварочные трансформаторы, агрегаты (преобразовате- [c.88]
Очень важным вопросом для всех видов автоматической сварки является обеспечение промышленности источниками питания. Применяются сварочные трансформаторы ТСД-1000 для питания автоматических установок под флюсом, ТТСД-1000 — специально для сварки трехфазной дугой, генераторы ЗД-7,5-30, на которых могут быть без большого труда получены жесткие и возрастающие вольт-амперные характеристики для сварки в среде защитных газов при больших плотностях токов. Ряд исследований проводится по обеспечению промышленности источниками питания, удовлетворяющими техническим требованиям сварки под флюсом и в особенности в среде защитных газов. [c.285]
Многопостовой источник питания постоянного тока (рис. 71) для ручной дуговой сварки и автоматической сварки под флюсом, обслуживающий п сварочных постов (СП — СПп), получает питание через шинопровод ШП от выпрямителя В. Сварочный ток г-го поста регулируется постовым (балластным) переменным сопротивлением (ПБПС). [c.82]
mash-xxl.info
Источники питания электрической дуги постоянного тока для ручной и автоматической сварки под флюсом.
Для выполнения ручной, полуавтоматической и автоматической сварки стыков трубопроводов в качестве источника питания используют передвижные сварочные агрегаты, которые состоят из однопостового сварочного генератора постоянного тока и приводного двигателя (внутреннего сгорания), смонтированных на общей раме и соединяемых эластичной муфтой. Кроме этого на строительных площадках и сварочных базах вместо двигателя внутреннего сгорания используют электродвигатель, а так же выпрямители.
Сварочные вентильные генераторы с падающими вольт-амперными характеристиками ГД-2х2505, ГД-2х250, ГД-4х2502 входят в комплект двухпостовых и четырех постовых передвижных установок АС22.1, АС22, АС23, АС-41, УСТ-22. Сварочные агрегаты с вентильным генератором используют для ручной и автоматической сварки под флюсом. Вентильный генератор представляет собой индуктор повышенной частоты 500Гц с выпрямителем. Наклон внешней вольтамперной характеристики обеспечивают за счет падения напряжения в обмотках и вентильном блоке генератора. Основное преимущество индукторного генератора состоит в отсутствии коллектора, силовых щеток, возможности дистанционного регулирования сварочного тока, получении более высокого КПД (60-70%), меньшей мессе. Генератор ГД-2х2504 используют для питания двух постов ручной дуговой сварки, а генератор ГД-4Х2504 – для питания четырех постов. В конструкции генераторов предусмотрены выводы для прокалки электродов и шлифовальных машинок.
Источники питания с жесткой характеристикой применяют при многопостовой ручной сварке под флюсом с балластными реостатами типов РБ-201, РБ-3027, РБ-306, РБ-501 для регулирования тока на одном посту. Реостаты работают на открытом воздухе.
Для того чтобы стабильно горела электрическая дуга необходимо, чтобы вольтамперная характеристика источника питания соответствовала источнику сварки.
1 – падающая вольтамперная характеристика, используется для ручной сварки, сварки под флюсом.
2- жесткая вольтамперная характеристика, используется для источников питания газоэлектрической сварки.
3 – пологовозрастающая вольтамперная характеристика, используется для сварки в среде аргона и гелия.
Передвижные сварочные агрегаты постоянного тока.
Бензиновый двигатель – генератор постоянного тока
Дизельный двигатель – генератор постоянного тока
Марки бензиновых: АДБ 2502 → 500 А, АДБ 3122 У1 → 315 А, АДБ 3123 У1→ 315 А, ПАС-400У1→ 400 А.
Марки дизельных: АДД 3112 У1 → 315 А; АДД 3114 У1 → 315 А
АДД 4001 У1 → 400 А; АДД 4003 У1 → 400 А; АДД 502 У1 → 315-500 А
students-library.com