Как отжечь медь в домашних условиях. Как варить медь аргоном
Сварка меди аргоном - особенности и видео-уроки
Несмотря на то, что сварку меди можно произвести привычной ручной сваркой, с помощью металлических или угольных электродов, в последнее время, чаще всего используется — высокоэффективная сварка меди аргоном.
Универсальная аргоновая сварка позволяет без проблем варить крупногабаритные и мелкие детали из меди.
Как известно, из-за высокой тепло- и электропроводимости, а также высокой стойкости к агрессивным средам и коррозии медь применяют в энергетическом и химическом машиностроении.
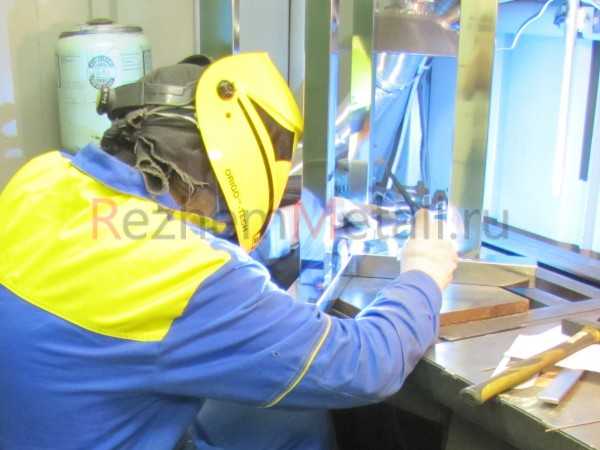
Фото процесса
А так как медь – очень хороший проводник, то и работа с ней требует довольно специфичного оборудования.
Сварка аргоном производится при прямой полярности и постоянном токе с помощью вольфрамового неплавящегося электрода. Температура аргонно-дуговой сварки должна достигать 300-400 градусов.
Прежде чем начать варить, дугу следует нагреть на графитовой или угольной пластинке. Не рекомендуется зажигать дугу сразу же на изделии, которое вы будете варить – это загрязнит электрод.
Необходимо помнить, что сварка меди аргоном осуществляется в вертикальном, потолочном или нижнем положениях.
Особенности работы с медью
Хотя сварку медных деталей можно производить с помощью специальных электродов, все-таки для этих целей лучше всего использовать неплавящиеся электроды из вольфрама.
Такие электроды хорошо «проваривают» швы, в отличие от сварки обычными электродами, они получаются прочными, ровными и чистыми.
Так как во время сварочных работ используется смесь газов: аргона и азота, то для безопасности сварка должна производиться только специально подготовленным сварщиком.
Вольфрамовые неплавящиеся электроды бывают нескольких видов: ЭВЛ и ЭВИ. ЭВЛ – это лаптанированные электроды, а ЭВИ – итерированные электроды.
Для сварки деталей из меди с помощью аргона используют именно итерированные электроды из вольфрама. Если толщина медных деталей свариваемых аргоном превышает 5 мм, то применяют обязательную разделку кромок.
Видео:
Следует знать, что для металла толщиной 5 – 12 мм используют одностороннюю разделку, а если толщина металла больше указанной, то разделывают обе кромки обрабатываемой детали.
Качество сварного шва также зависит от примесей, содержащихся в меди – чем чище медь, тем качественней шов. Кроме вольфрамовых электродов, также используется еще и присадочная проволока.
Присадочная проволока изолирует свариваемые детали от кислорода, который все же попадает в область сварки.

Таблица режимов сварки меди
Материал присадочной проволоки непременно должен соответствовать составу того металла, который предполагается варить..
В качестве присадки можно взять медную проволоку, которая содержит большое количество марганца. С одной стороны марганец надежно связывает поступающий в область сварки кислород, но с другой – примеси марганца снижают прочность сварного шва.
Поэтому в качестве присадки лучше всего использовать проволоку с содержанием каких-либо редкоземельных материалов.
Такие материалы полностью удаляют из швов кислород, но при этом не остаются в составе шва, как примеси марганца.
К сожалению, присадочная проволока из редкоземельных материалов весьма дорога, из-за чего немногие решаются ее использовать, отдавая предпочтение недорогой медной проволоке.
Преимущества использования аргона при работе с медью
Как уже говорилось выше, сварка меди аргоном считается самой чистой. При такой ее разновидности — почти не выделяются пары оксидов.
Во время аргоновой сварки на пол не падают раскаленные искры, которые могли бы повредить полы и настенные покрытия.
Таким образом, сварку аргоном можно проводить даже в жилых помещениях, не боясь при этом что-либо испортить или испачкать.
Еще одно неоспоримое преимущество аргоновой сварки – это качество. При сварке меди аргоном шов получается чистым и аккуратным, без шлаков и подрезов.
С помощью аргона можно на малых токах варить даже тонколистовые 0,5 мм изделия из меди.
К тому же, аргоновая сварка позволяет работать со сложными металлами, которые не поддаются обычной сварке, а также восстанавливать прежний объем детали, наплавляя металл поверх нее.
Видео:
Если у вас есть определенные знания в этой области, то можете произвести все работы самостоятельно, но перед этим — рекомендуется посмотреть видео сварки меди аргоном и приобрести соответствующее оборудование.Для домашнего использования идеально подойдет специальное многофункциональное оборудование.
Если же планируется больший объем сварочных работ, например, на производстве, то в данном случае потребуется приобрести несколько аппаратов, которые обладают разными функциональными возможностями.
rezhemmetall.ru
Сварка меди аргоном
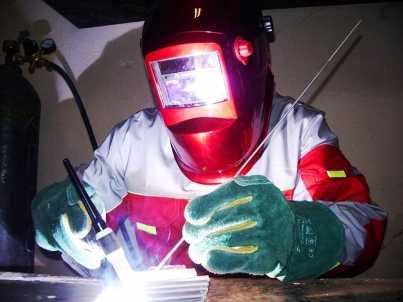
nanolife.info
Медь используется в химическом и энергетическом машиностроении благодаря тому, что она имеет высокую коррозионную устойчивость, а также устойчива в агрессивных средах. Эти свойства будут повышаться при повышении чистоты металла, что заставляет предъявлять к сварочному шву особые требования. Сваривание бронзы и латуни имеет много своих особенностей, но свойства чистой меди, присутствующей в этих сплавах, значительно утрачиваются. В зависимости от количества содержания примесей в сплаве, медь различается на пять основных марок:
Аргоновая сварка меди очень похожа на газовую, однако она имеет некоторые отличия и особенности, отличающие ее от других видов сварки. Главным элементом, с помощью которого производится сваривание, является инертный газ аргон. Сваривание производится с помощью неплавящегося вольфрамового электрода. Вольфрамовый электрод является главной составляющей сварочного аппарата. Этот электрод изготавливают из вольфрама по причине его тугоплавкости. Данный металл не боится высокой температуры, поэтому электроды, сделанные из него, считаются неплавящимися. Возле вольфрамового электрода расположено сопло, из которого выходит газ аргон. Аргон не пропускает воздух к сварочной ванне, что позволяет защитить сварочный процесс от факторов окружающей среды. Если воздух попадает на сварочный электрод, то он будет окисляться, а если воздух попадет на свариваемый металл, то он начнет гореть. В сравнении с газовой и электрической сваркой, у аргонодуговой сварки преимуществ намного больше. При сваривании меди аргоном в металле сварочного шва не скапливаются различные шлаки. С помощью аргона можно производить сваривание даже тонкого металла. Например, аргонодуговым сварочным аппаратом можно сваривать даже пластинки фольги. В случаях, когда требуется сваривание чугуна или алюминия, аргонодуговой аппарат приходится как раз кстати. На данный момент аргонодуговые сварочные аппараты широко применяются в автомастерских для ремонта автомобилей. Стоит обратить внимание, что аргонодуговое сваривание является самым надежным из всех остальных видов сварки. Сварочный шов после работы практически не заметен и сливается с металлом свариваемого изделия. Если потребуется, то в сварочный шов можно добавить другие металлы. Для выполнения такой задачи потребуется присадочная проволока. Обычно присадочную проволоку используют для укрепления сварочного шва. Аргонодуговым сварочным аппаратом можно сваривать не только медь, алюминий и чугун. В некоторых случаях данный тип сваривания используют для сварки серебра, золота и других драгоценных металлов. Сваривание получается наивысшего качества в случае, когда для работы используется чистый газ аргон.
|
3g-svarka.ru
Особенности сварки меди и ее сплавов
Введение
Медь активно применяется в промышленности, ювелирном деле и строительстве техники. Этот желтовато-красноватый металл знает каждый школьник и любой взрослый человек. Состыковка и пайка меди – это процессы, с которыми непременно сталкивается любой сварщик-профессионал или любитель.
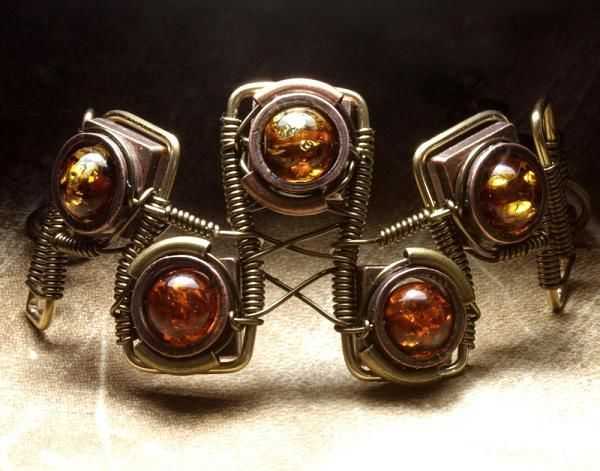
Оригинальные ювелирные изделия делают из меди
Свариваемость меди
Сварка меди – это достаточно сложный процесс, требующий от человека хорошего понимания ее химической чистоты и свойств. Небольшое содержание фосфора, серы или свинца увеличивает качество сваривания металла. Сварочные особенности:
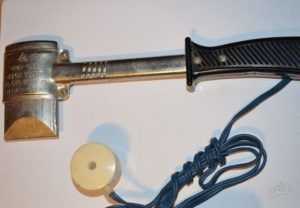
Специальный паяльник для медных изделий
- Медь склонна к окислению. В момент термической обработки на поверхности металла образовываются тугоплавкие окисления с последующим образованием трещин;
- Большая осадка при охлаждении;
- В разогретом состоянии металл хорошо поглощает газы (водород и кислород) из воздуха. Превышение концентрации сторонних газов увеличивает сложность сваривания. Процесс поглощения сторонних газов можно посмотреть на видео;
- Неоднородная структура приводит к образованию зернистости в процессе термической обработки;
- Из-за хорошей проводимости электричества медь требует специальных инструментов, способных развивать высокую мощность;
- Высокая температура плавления и текучесть сильно ограничивает возможности драгоценного металла к свариванию. Этот процесс можно проводить только на горизонтальной поверхности;
Для качественного процесса сварки медь необходимо подготовить и вооружиться специальным инструментом.
Доступные способы
Чтобы вы могли смотреть видео на телевизоре или компьютере во время изготовления сварных конструкций используют разные способы – дуговую ручную, сварку инвертором или вольфрамовыми электродами.
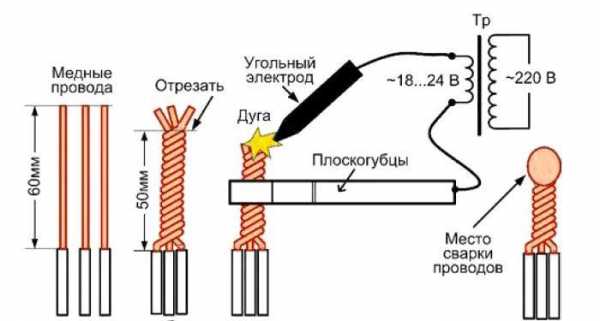
Сварка меди угольным электродом
Подготовка материала требует тщательной очистки. При помощи ацетона, ветоши и других растворителей удаляются все загрязнения, которые могут стать поставщиками вредных примесей – свинца и серы. Сварка меди не переносит присутствия жидкостей, жиров или масла.
После очищения с поверхности заготовки необходимо убрать окисленную пленку при помощи металлической щетки или сетки из нержавейки.
Инвертор для сварки меди
Для более тщательной обработки еще пользуются абразивным инструментом, с помощью которого добиваются идеальной полировки детали до блеска. Помните, что очистка детали является важным этапом, от которого зависит качество проделанного труда.
Детали с толстыми стенками (от 5 мм и больше) требуют дополнительно подогрева до 300-700 градусов, в этом заключается успешность процедуры сваривания меди. Особенно не рекомендуется пропускать этот пункт для массивных деталей. Чем больше размер заготовки, тем сильнее она нуждается в предварительном нагреве.
- Сварка металлическими покрытыми электродами
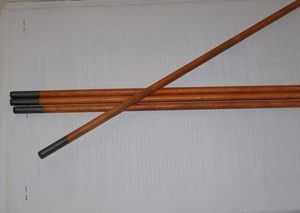
Графитовый электрод для сварки медных жил
При помощи таких электродов медь с толщиной стенок более 2 мм варят под углом в 60 градусов. Тоненький металл (от 3 до 5 мм) сваривается без разделки кромок – дополнительных надрезов на заготовке при помощи состыковки. Все работы проводятся только при помощи постоянного тока.
Для сварки медного изделия с толщиной стенок в 2 мм требуется электрод диаметром 2-3 мм и сила тока в 100 А. Элемент со стенками 8-10 мм нуждается в электроде 6-7 мм и постоянном токе в 400 А. К концу возни с толстой заготовкой необходимо уменьшить силу тока, чтобы предотвратить прожоги или прогорание поверхности.
- Сварка вольфрамовым электродом.
Время и практика показали, что этот метод является оптимальным. Швы, сделанные при помощи вольфрамовых электродов, отличаются аккуратностью и прочностью. Сварочные работы можно проводить в домашних условиях переменного тока. Так же, как и в первом способе, сила тока регулируется в зависимости от толщины медного изделия и диаметра электрода.
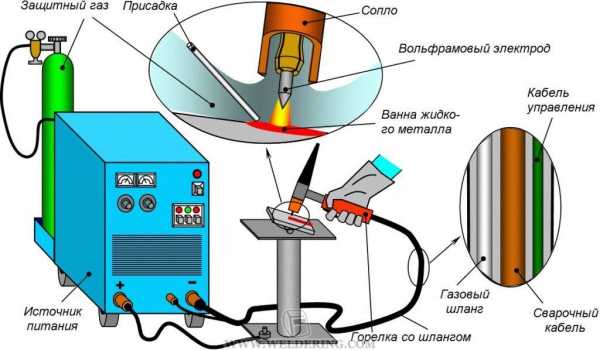
Схема процесса сварки ТИГ
Сварка меди аргоном, гелием и азотом практикуется для повышения качества сварочных швов. Стоит отметить, что технологические свойства газов отличаются, поэтому во время работы необходимо учитывать то, что азот требует меньшей силы тока. Во время работы с азотом на поверхности меди возникает парообразование, незначительно уменьшающее качество резки. Что же касается других качеств азота, то для сварки меди требуется почти в 2 раза больше газа. Именно по этой причине аргон чаще используется в сварочных работах с медными изделиями.
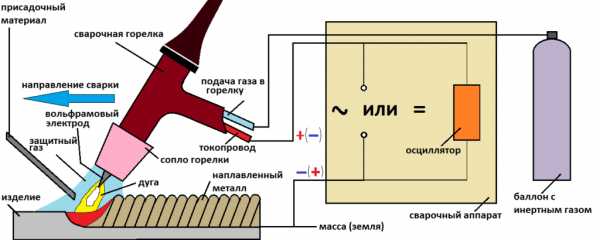
Схема аргоновой сварки
Аргоновая состыковка требует особых условий. Например, с медью нельзя работать непостоянным током. Для сварочного процесса требуется доступ к постоянному тому. Именно по этой причине аргоновая состыковка получила свое распространение только на промышленных объектах. В домашних условиях этот метод не практикуется.
Перед свариванием заготовку необходимо нагреть на угольной пластинке инвертором. Профессионалы не рекомендуют зажигать дугу прямо на изделии, чтобы не загрязнить электрод. Аргоновое сваривание доступно только в потолочном или вертикальном положении.
- Сварка полуавтоматом
Сварка меди возможна и в полуавтоматическом режиме. Для обеспечения лучшего качества рекомендуется использовать гелий, аргон или азот в качестве защиты поверхности металла от водорода и кислорода. Технология сварки полуавтоматом ничем не отличается от сваривания стали. Как и в первых случаях при сварке полуавтоматом медную заготовку с толстыми стенками необходимо качественно прогреть до 300-500 градусов. Электрод располагается к шву под углом 80 градусов.
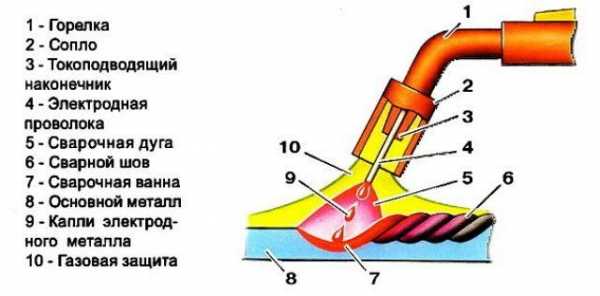
Сварка металлов полуавтоматом
Полуавтоматический метод сваривания требует пользования флюсом, который наносится на кромки присадочной проволоки. Время от времени электрод необходимо вставлять во флюс и продолжать сварочные работы. О том, как правильно использовать флюс можете посмотреть на видео или почитать в книгах. Такая технология поможет увеличить качество скрепления и уменьшит количество окислительных операций на поверхности заготовки.
В состав флюсов входит прокаленная бура вместе с добавками металлического магния и кремниевой кислоты. Использование флюсов вносит определенные трудности в сварочный процесс, а именно – высокий темп работы с металлической поверхностью. Кроме этого, движение руки должно быть непрерывным в одном направлении.
Аргоновая сварка меди
Свариваемость меди и ее сплавов
Медные сплавы типа бронзы и латуни в целом свариваются нормально. Стоит отметить, что латунь теряет значительную часть цинка из-за окислительных процессов и испарений.
Электрошлаковая сварка и ее применение
Для работы со сплавами часто используют инертные газы (аргон и гелий) вместе с присадочными проволоками, которые совпадают с химическим составом заготовки.
Для особо толстых сплавов применяют электрошлаковую сварку. Данный метод применяется для деталей, толщина стенок которых превышает 30 мм. Сварка меди и ее сплавов требует специальных пластинчатых электродов, с внешним видом которых можно ознакомиться на видео в интернете. Особенность электрошлакового способа состоит в том, что температура плавления флюса должна быть ниже плавления меди.
Такая технология позволяет добиться качественного и ровного шва при сварочных работах. Кроме этого, низкая температура плавления флюса не приводит к образованию шлаковой корки. Второй особенностью электрошлаковой сварки являются повышенные сварочные токи и высокая скорость подачи электрода (до 15 км/час).
Альтернативные методы
Медь является металлом с высоким показателем пластичности, поэтому небольшие медные проводки хорошо свариваются термокомпрессионной сваркой. Для изделий с большим сечением рекомендуется применять диффузную сварку в условиях вакуума. В таких условиях медь может свариваться практически с любыми металлическими и даже неметаллическими материалами.
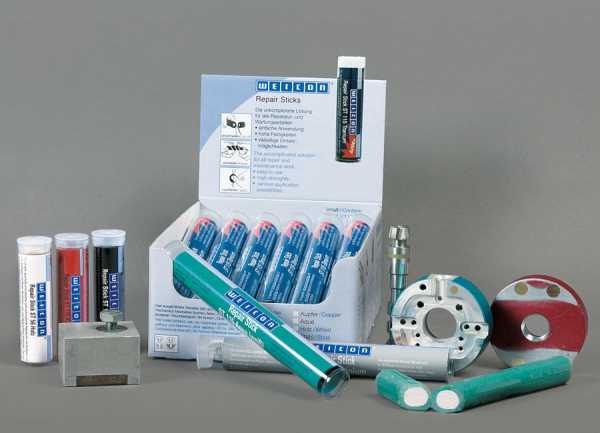
Холодная сварка хорошо скрепляет недвижимые детали
Холодную сварку можно применять в домашних условиях для грубого сваривания медных деталей. Сварка меди холодным способом способна обеспечить удовлетворительное электрическое сопротивление соединений. Для более качественной сварки медных деталей необходимо пользоваться энергетическими установками.
Заключение
Сваривание меди – это технологически сложный процесс, требующий от человека хорошего понимания физико-химических особенностей меди и умения пользоваться специальными инструментами.
Видео: Сварка меди полуавтоматом
ecology-of.ru
Аргонодуговая сварка меди | Мир сварки
Назначение
Настоящая инструкция распространяется на ручную аргонодуговую сварку меди.
Инструкцией надлежит руководствоваться при проектировании, разработке технологических процессов, изготовление, контроле и приемке сварных узлов.
Отступления (ужесточение или снижение требований) от настоящей инструкции могут быть внесены в технологическую документацию на изделие по согласованию с главным технологом и представителем заказчика.
Материалы, оборудование, приспособления, инструмент даны в приложениях №1 и №2.
Выполнение аргонодуговой сварки меди должно производиться дипломированными сварщиками при соблюдении правил техники безопасности, изложенных в инструкции по ТБ.
Подготовка деталей и сварочной проволоки к сварке
Обезжирить поверхность деталей, а также сварочную проволоку, методом протирки хлопчатобумажной тканью, смоченной в бензине. Разрешается выполнять обезжиривание деталей в соответствии с соответствующей технологической инструкцией.
Удалить напильником заусеницы с кромок свариваемых деталей.
Зачистить стальной щеткой до металлического блеска, с обеих сторон на ширину 15-20 мм, кромки деталей, изготовленных из листа или штамповкой.
Разрешается вместо зачистки выполнять травление по соответствующей технологической инструкции.
Присадочную проволоку травить по соответствующей технологической инструкции.
Обезжирить методом протирки хлопчатобумажной тканью, смоченной в бензине поверхность деталей после механической обработки.
Хранить детали и проволоку после обработки в чистом и сухом помещении не более трех суток до сварки. Если до сварки прошло более трех суток операции обезжиривания повторить.
Сборка, прихватка и сварка
Подготовить пост аргонодуговой сварки к работе, выполняя требования инструкции ТБ.
Подключить сварочную горелку к источнику постоянного тока для выполнения работ на прямой полярности.
Установить на оборудовании ориентировочной режим сварки согласно таблице 1.
Закрепить вольфрамовый электрод в горелке таким образом, чтобы вылет его из сопла горелки не превышал 5-12 мм.
Выключить подачу аргона за 6-10 с до начала сварки и приступить к работе.
Выполнить сварку технологических образцов.
Выключить подачу аргона на ранее чем через 10-15 с после окончания сварки.
Проверить качество сварки технологических образцов в соответствии с требованиями раздела «Контроль качества сварки» и произвести корректировку режима сварки, если в этом будет необходимость.
Установить свариваемый узел на рабочем столе сварщика в положении удобном для сварки.
Подать охлаждение на свариваемый узел, если это предусмотрено маршрутной картой.
Протереть кромки деталей бязевым тампоном, смоченным в растворителе.
Произвести прихватку кромок свариваемых деталей, если сборка узла выполнена с зазором более 0,5 мм, или если сборочно-сварочное приспособление не обеспечивает жесткой фиксации свариваемых деталей друг относительно друга.
Выполнить прихватку в виде отдельных точек начиная с участков наилучшего сопряжения кромок свариваемых деталей. Присадочный материал применять по мере надобности.
Произвести прихватку по всей длине свариваемого шва. Шаг между прихватами установить опытным путем.
Зачистить механическим путем до металлического блеска зону прихваток и сами прихватки.
Протереть зачищенные участки бязевым тампоном, смоченным в растворителе.
Приступить к сварке узла соблюдая следующие требования:
Производить сварку необходимо путем непрерывного перемещения вольфрамового электрода вдоль оси шва без остановок.
Наклонять горелку при сварке в сторону противоположную направления сварки таким образом, чтобы ось вольфрамового электрода составляла с осью сварного шва 60-80°.
Применять сварочную проволоку необходимо по мере надобности для выполнения расчетного размера шва.
Вносить, в зону сварки присадочную проволоку таким образом, чтобы угол между вольфрамовым электродом и присадкой составлял 90°.
Производить перекрытие начала шва при окончании сварки 10-20 мм, при возобновлении сварки, после случайного и вынужденного обрыва дуги, окончание шва перекрыть на 15-20 мм.
Произвести контроль ОТК сварных узлов и деталей после окончания работ согласно разделу «Контроль качества сварки».
Ориентировочные режимы сварки даны в таблице 1.
1,0 | 60-70 | 50-75 | 2,0 | 1,6-2,0 | 6-8 |
1,5 | 75-90 | 60-90 | 2,0 | 1,6-2,0 | 8-10 |
2,0 | 90-105 | 75-105 | 2,0 | 2,0-2,5 | 9-11 |
2,5 | 90-115 | 90-115 | 3,0 | 2,0-2,5 | 11-12 |
3,0 | 115-130 | 115-130 | 3,0 | 2,0-3,0 | 11-12 |
4,0 | 115-145 | 115-145 | 3,0 | 2,0-3,0 | 11-12 |
5,0 | 130-145 | 130-145 | 3,0 | 2,0-3,0 | 12-14 |
6,0 | 145-160 | 130-160 | 3,0 | 2,5-3,0 | 12-14 |
Контроль качества сварки
Выполнять сплошной контроль качества сварки внешним осмотром.
Производить осмотр сварных швов по всей длине с обеих сторон.
Произвести разбраковку дефектов сварных швов согласно требованиям таблицы 2.
Подваривать дефектные участки сварных швов допускается не более двух раз.
Непровары | Не допускаются. Устраняются повторной сваркой |
Поры, раковины диаметром 0,3-1 мм, но не более 5 шт на длине 100 мм шва | Не допускаются. Устраняются повторной сваркой |
Прожоги суммарной длиной не более 10% длины шва и шириной или диаметром не более ширины шва | Не допускаются. Устраняются повторной сваркой |
Трещины | Не допускаются. Устраняются повторной сваркой |
Скопление мелких пор диаметром не более 0,3 мм, но не более одного скопления на длине шва, при этом превышать 10 % швов длиной до 100 мм и 20 % для швов длиной более 100 мм | Допускаются |
Проплав в стыковых, угловых швах, не мешающий элементам дальнейшей сборки и не представляющий пористого провисания металла | Допускаются |
Вспомогательные материалы
- Вольфрам лантанированный в виде прутков ТУ-48-19-27-72.
- Аргон газообразный высший сорт или первый сорт ГОСТ 10157-73.
- Проволока сварочная марки М1 или М2 ГОСТ 16130-72.
- Бензин авиационный Б70 ГОСТ 1012-72.
- Ткань хлопчатобумажная бязевой группы ГОСТ 11680-76.
- Перчатки трикотажные ГОСТ 1108-74.
- Шкурка шлифовальная бумажная водостойкая ГОСТ 10054-75
- Бензин А-76 ГОСТ 2084-77 и «Галоша» ТУ 38-401-67-108-92.
Оборудование, приспособления, инструмент
- Источник питания для сварки в среде защитных газов типа ПС-300, ПСО-300, ПСО-500, ВКСМ-1000 или УДГ-101 с комплектом сварочных горелок, цанг, сопел.
- Реостат балластный типа РБ-200 или РБ-300.
- Ротаметр марки РМ-II или РМ-IV ГОСТ 13045-67.
- Редуктор кислородный типа РК-30, РК-50 или РК-14 ГОСТ 6268-78.
- Набор трубок резиновых технических тип 4 для подачи защитных газов и воды в горелку ГОСТ 5496-78.
- Шлем маска защитная сварочная с набором защитных сварочных стекол ЭС-100, ЭС-300, ЭС-500 ГОСТ 1361-69.
- Очки герметичные защитные ГОСТ 9496-60.
- Сборочно-сварочные приспособления.
- Напильник ГОСТ 1465-69.
- Щетки стальные из нержавеющей проволоки ∅0,2-0,3 мм для зачистки металла шва и деталей.
- Штангенциркуль ГОСТ 166-73.
weldworld.ru
Сварка меди аргоном – видео инструкция
Для соединения деталей из чистой меди применяется аргоно-дуговая сварка. Сварка меди аргоном позволяет обеспечить надежный и качественный шов. Количество содержащихся в меди примесей определяет способ сварного соединения медных конструкции. Для сварки чистой меди применяются вольфрамовые электроды и присадочная проволока. Защитная аргоновая среда позволяет снизить дуговой разряд, что немаловажно для конструкций малой толщины.
Особенности сварки меди
Аргоновая сварка меди производится током прямой полярности и электродами из латинированного вольфрама. Они обладают отличной устойчивостью в среде инертных газов. Для качественного наложения шва на элементах толщиной свыше 5 мм рекомендуется предварительный прогрев поверхности до 400 °С.
Для получения шва, по своим характеристикам идентичного основному материалу, применяются присадки М0 и М1 из чистой меди. Введенные в сварной шов присадки, содержащие раскислители и легирующие компоненты, значительно увеличивают механические свойства соединения. Однако легирующие компоненты могут снизить тепло и электропроводные свойства сварного шва, что недопустимо для ответственных соединений.
Таблицы режимов сварки меди неплавящимся электродом
Таблица состава флюсов для сварки меди и ее сплавов
Сварка меди аргоном – видео инструкция
Следует заметить, что при нарушении технологии аргоновой сварки меди в шве образуются воздушные поры, что существенно снижает прочность соединения.
Другие похожие статьиsvarkasite.ru
Как отжечь медь в домашних условиях, пайка аргоном
Отжиг стальных деталей
Чтобы облегчить механическую или пластическую обработку стальной детали, уменьшают ее твердость путем отжига. Так называемый полный отжиг заключается в том, что деталь или заготовку нагревают до температуры 900°С, выдерживают при этой температуре некоторое время, необходимое для прогрева ее по всему объему, а затем медленно (обычно вместе с печью) охлаждают до комнатной температуры.
Внутренние напряжения, возникшие в детали при механической обработке, снимают низкотемпературным отжигом, при котором деталь нагревают до температуры 500—600°С, а затем охлаждают вместе с печью. Для снятия внутренних напряжений и некоторого уменьшения твердости стали применяют неполный отжиг — нагрев до 750—760°С и последующее медленное (также вместе с печью) охлаждение.
Отжиг используется также при неудачной закалке или при необходимости перекаливания инструмента для обработки другого металла (например, если сверло для меди нужно перекалить для сверления чугуна). При отжиге деталь нагревают до температуры несколько ниже температуры, необходимой для закалки, и затем постепенно охлаждают на воздухе. В результате закаленная деталь вновь становится мягкой, поддающейся механической обработке.
Отжиг меди
Термической обработке подвергают и медь. При этом медь можно сделать либо более мягкой, либо более твердой. Однако в отличие от стали закалка меди происходит при медленном остывании на воздухе, а мягкость медь приобретает при быстром охлаждении в воде. Если медную проволоку или трубку нагреть докрасна (600° С) на огне и затем быстро погрузить в воду, то медь станет очень мягкой. После придания нужной формы изделие вновь можно нагреть на огне до 400° С и дать ему остыть на воздухе. Проволока или трубка после этого станет твердой. Если необходимо выгнуть трубку, ее плотно заполняют песком, чтобы избежать сплющивания и образования трещин.
Отжиг латуни позволяет повысить ее пластичность. После отжига латунь становится мягкой, легко гнется, выколачивается и хорошо вытягивается. Для отжига ее нагревают до 600° С и дают, остыть на воздухе при комнатной температуре.
Отжиг и закаливание дюралюминия
Отжиг дюралюминия производят для снижения его твердости. Деталь или заготовку нагревают примерно до 360°С, как и при закалке, выдерживают некоторое время, после чего охлаждают на воздухе. Твердость отожженного дюралюминия почти вдвое ниже, чем закаленного.
Приближенно температуру нагрева дюралюминиевой детали можно определить так: При температуре 350—360°С деревянная лучина, которой проводят по раскаленной поверхности детали, обугливается и оставляет темный след. Достаточно точно температуру детали можно определить с помощью небольшого (со спичечную головку) кусочка медной фольги, который кладут на ее поверхность. При температуре 400°С над фольгой появляется небольшое зеленоватое пламя.
Отожженный дюралюминий обладает небольшой твердостью, его можно штамповать и изгибать вдвое, не опасаясь появления трещин.
Закаливание. Дюралюминий можно подвергать закаливанию. При закаливании детали из этого металла нагревают до 360—400°С, выдерживают некоторое время, затем погружают в воду комнатной температуры и оставляют там до полного охлаждения. Сразу после этого дюралюминий становится мягким и пластичным, легко гнется и куется. Повышенную же твердость он приобретает спустя три-четыре дня. Его твердость (и одновременно хрупкость) увеличивается настолько, что он не выдерживает изгиба на небольшой угол.
Наивысшую прочность дюралюминий приобретает после старения. Старение при комнатных температурах называют естественным, а при повышенных температурах — искусственным. Прочность и твердость свежезакаленного дюралюминия, оставленного при комнатной температуре, с течением времени повышается, достигая наивысшего уровня через пять — семь суток. Этот процесс называется старением дюралюминия.
<<<Назад
Пайка или сварка алюминия? В чем разница и что лучше?
Во-первых, давайте рассмотрим определения. Сварка — это процесс получения соединений «все-в-одном» путем установления межатомных связей. Пайка представляет собой процесс объединения металлов в нагретом состоянии путем плавления сплава, плавильного припоя, такого как соединяемые металлы.
Другими словами, при сварке края сварных деталей расплавляются и затем замораживаются. При пайке обычный металл нагревается только до определенной температуры, и соединение получают путем поверхностной диффузии и химической реакции припоя и сплавленных металлов.
Итак, что лучше, пайка или алюминиевая сварка?
Чтобы ответить на этот вопрос, рассмотрите основные методы пайки и сварки алюминиевых сплавов, их преимущества и недостатки.
Алюминиевая сварка.
Четыре типа сварки наиболее часто используются при сварке алюминия:
1. Сварка электродом или сваркой ВИГ. В качестве электрода, который не потребляет, вольфрам используется со специальными легирующими добавками (лантан, церий и т. Д.).
Через этот электрод возникает электрическая дуга, которая расплавляет металл. Сварочная проволока вручную подается сварным бассейном. Весь процесс очень похож на обычную газовую сварку, только нагрев металла не осуществляется путем сжигания горелки, а электрической дугой в защитной среде. Такая сварка осуществляется исключительно в аргоновой или гелиевой среде или их смесях.
Есть ли разница между сварочным аргоном и гелием? Есть. Суть в том, что гелий обеспечивает более компактную дугу сгорания и, следовательно, более глубокое и более эффективное проникновение основных металлов. Гелий более дорогой, а его потребление намного выше, чем потребление аргона. Кроме того, гелий очень жидкий, что создает дополнительные проблемы при производстве, транспортировке и хранении.
Поэтому рекомендуется использовать его в качестве защитного газа только при сварке больших деталей, где требуется глубокое и эффективное плавление сварных кромок. На практике гелий редко используется в качестве инертного газа, так как почти такой же эффект проникновения может быть достигнут в аргоне, что увеличивает только сварочный ток. Сварка ВИГ алюминия, как правило, приводит к переменному току.
Почему при переменном токе? Все дело в оксиде алюминия, небольшое количество которого при сварке неизбежно присутствует во всех типах сварки. Дело в том, что температура плавления алюминия составляет около 660 градусов. Температура плавления оксида алюминия составляет 2060. Поэтому в сварном шве алюминиевый оксид не может плавиться — недостаточно температуры.
И не будет никакого руководства для высококачественного сварочного оксида. Что делать? Доход приходит к полярности обратной связи, которая имеет очень интересную особенность для очистки шва от ненужных примесей. Это свойство называется «катодная дисперсия». Однако сварочный ток с обратной полярностью имеет очень низкую мощность плавления. Поэтому дуга также содержит компоненты тока прямой полярности, которые предназначены для нечувствительности, но плавления металлов.
И обмен прямых и обратных полярных токов представляет собой переменный ток, который сочетает в себе как чистящие, так и плавильные свойства.
2. Сварка с помощью расходуемого электрода или полуавтоматическая сварка (сварка МИГ). Все это относится к этому типу сварки с той лишь разницей, что, как правило, единственной постоянной «очисткой» является замена полюсов дуговых потоков и не проходит через вольфрамовый электрод и непосредственно через сварочную проволоку, расплавленную при сварке.
Обычная полуавтоматическая машина используется для сварки, но с более высокими требованиями к подаче проволоки. Этот тип сварки характеризуется высокой производительностью.
третий
Ручная дуговая сварка электродами с покрытием (MMA-сварка). Он используется для сварки твердых деталей толщиной 4 мм и более. Он применяется к потоку обратной полярности и имеет шов низкого качества.
4. Газовая сварка алюминия. Его можно использовать только для ограниченного количества алюминиевых сплавов, который характеризуется отвратительным качеством шва. Это очень сложно и доступно далеко не каждому смертному.
На практике это почти не применяется.
Оставляя в одиночку экзотическую сварку (фрикционная сварка, сварка взрывом и плазма), качество сварного соединения и распространенность намного опережают формы, аргонодуговая сварка переменным током.
Он позволяет сваривать чистый алюминий, дюралюминий, силамин и т. Д., Сплавы от нескольких миллиметров до нескольких сантиметров. Кроме того, он является наиболее экономичным и единственно возможным для ядерной сварки и некоторых других алюминиевых сплавов.
Пайка алюминия
Обычно отделяется низкая температура (пайка мягкими соединениями) и высокая температура (пайка пайкой), тип пайки.
первый
Пайка алюминиевого мягкого припоя обычно выполняется с помощью обычного паяльника и может использоваться в качестве специального припоя для алюминия с высоким содержанием цинка и обычного свинцово-оловянного припоя. Основной проблемой такого типа пайки является борьба с легким алюминиевым оксидом. Чтобы нейтрализовать его, необходимо использовать различные типы флюсов, паяльных жиров и специальные типы пайки. В некоторых случаях поверхность алюминия покрыта гальваническим покрытием тонким слоем меди, который уже припаян традиционным пайкой припоя.
Однако использование гальванических покрытий далеко не технологически выполнимо и экономически целесообразно. В любом случае пайка алюминиевых сплавов при низких температурах довольно сложна, а качество паяных соединений, как правило, более чем среднее. Кроме того, из-за неоднородности металлов связанное соединение подвержено коррозии и всегда должно быть покрыто лаком или краской. Пайка мягкими муфтами не может использоваться для загруженных систем.
В частности, он не должен использоваться для ремонта радиаторов кондиционера, но может использоваться для ремонта двигателей радиатора.
второй
Высокотемпературная пайка алюминия. При пайке алюминиевых радиаторов на заводах используется пайка. Его характеристика заключается в том, что температура плавления припоя составляет всего 20-40 градусов ниже точки плавления самого металла. Для этой пайки, как правило, используется специальная высокотемпературная паста (например, нейлон), используемая для пайки, а затем спеченная в специальных печах в среде защитного газа.
Этот процесс пайки характеризуется высокой прочностью и низкой коррозионной стойкостью полученных соединений, поскольку припой используется в качестве композиции, близкой к основному металлу. Такой припой идеально подходит для тонкостенных изделий, но его технология довольно сложна и совершенно бесполезна при ремонте.
Второй тип высокотемпературной пайки алюминия — пайка газовым пламенем. В качестве припоя используются специальные самонарезающие стержни (например, HTS 2000, Castolin 21 F и т. Д.).
Для нагревания используют ацетилен, пропан и, предпочтительно, водородное пламя (гидролиз). Технология здесь следующая. Во-первых, пламя горелки нагревает металл, а затем паяльник осторожно заполняется в области пайки. Когда стержень расплавляется, пламя удаляется. Точка плавления стержня не намного ниже температуры базовой плиты, поэтому ее следует тщательно нагревать, чтобы она не удалялась.
Следует отметить, что этот тип припоя очень, очень дорогой, и его цена может достигать 300 долларов. за 1 килограмм. Как правило, он используется для местного ремонта.
Так что лучше?
Бейкер тает дома: шаг за шагом, видео
Пайка или сварка алюминия?Теперь мы можем ответить на этот вопрос. Если толщина металлов больше 0,2-0,3 мм, то используйте аргонодуговую сварку. В частности, аргоновая сварка простых сотовых излучателей бальзама, лотков, крыльев, кронштейнов, легкосплавных колес, рулевого механизма, головки двигателя и т. Д. Полученный сварной шов. Это монолитная, химически стойкая и прочная связь.
Если толщина металлов меньше 0,2-0,3 мм, лучше использовать высокотемпературную пайку алюминия. Во-первых, он используется для пайки радиаторов тонкой сотовой стенки из двигателя, которую очень трудно пить аргоном. Более низкая температура пайки мягким припоем лучше, если вообще не использовать, поскольку эти швы намного менее прочны и химически менее устойчивы.
Кроме того, кислотные флюсы, используемые в низкотемпературной пайке, могут за сравнительно короткое время уничтожить как обычные металлы, так и пайки
Большинство обычных металлов нельзя упрочнить термической обработкой. Однако почти все металлы упрочняются – до той или иной степени – в результате ковки, прокатки или гибки. Это называют наклепом или нагартовкой металла.
Отжиг является видом термической обработки для умягчения металла, который стал нагартованным — наклепанным, чтобы можно было продолжать его холодную обработку.
Холодная обработка: медь, свинец и алюминий
Обычные металлы весьма сильно различаются по своей степени и скорости деформационного упрочнения — наклепа или нагартовки.
Медь довольно быстро наклепывается в результате холодной ковки, а, значит, быстро снижает свою ковкость и пластичность. Поэтому медь требует частого отжига, чтобы ее можно было дальше обрабатывать без риска разрушения.
С другой стороны, свинец можно обрабатывать ударами молотка почти в любую форму без отжига и без риска его разрушения.
Свинец обладает таким запасом пластичности, который позволяет ему получать большую пластическую деформацию с очень малой степенью деформационного наклепа. Однако, медь хотя и тверже свинца, обладает в целом большей ковкостью.
Алюминий может выдерживать весьма большое количество пластической деформации в результате формовки молотком или холодной прокатки, прежде чем ему понадобится отжиг для восстановления его пластических свойств.
Чистый алюминий наклепывается намного медленнее, чем медь, а некоторые листовые алюминиевые сплавы являются слишком твердыми или хрупкими, чтобы позволять большой наклеп.
Холодная обработка железа и стали
Промышленное чистое железо можно подвергать холодной обработке до больших степеней деформации, прежде чем оно станет слишком твердым для дальнейшей обработки.
Примеси в железе или стали ухудшают способность металла к холодной обработке до такой степени, что большинство сталей нельзя подвергать холодной пластической обработке, кроме конечно, специальных низкоуглеродистых сталей для автомобильной промышленности. Вместе с тем, почти все стали можно успешно пластически обрабатывать в раскаленном докрасна состоянии.
Зачем нужен отжиг металлов
Точная природа процесса отжига, которому подвергают металл, в значительной степени зависит от назначения отожженного металла.
Существует значительное различие отжига по методам его выполнения между отжигом на заводах, где производят огромное количество листовой стали, и отжигом в небольшой автомастерской, когда всего лишь одна деталь требует такой обработки.
Если кратко, то холодная обработка – это пластическая деформация путем разрушения или искажения зеренной структуры металла.
При отжиге металл или сплав нагревают до температуры, при которой происходит рекристаллизация — образование вместо старых — деформированных и удлиненных — зерен новых зерен — не деформируемых и круглых. Затем металл охлаждают с заданною скоростью. Другими словами, кристаллам или зернам внутри металла, которые были смещены или деформированы в ходе холодной пластической обработки, дают возможность перестроиться и восстановиться в свое естественное состояние, но уже при повышенной температуре отжига.
Отжиг железа и стали
Железо и низкоуглеродистые стали необходимо нагревать до температуры около 900 градусов Цельсия, а затем давать возможность медленно охлаждаться для обеспечения максимально возможной «мягкости».
При этом принимают меры, чтобы предотвратить контакт металла с воздухом во избежание окисления его поверхности. Когда это делают в небольшой автомастерской, то для этого применяют теплый песок.
Высокоуглеродистые стали требуют аналогичной обработки за исключением того, что температура отжига для них ниже и составляет около 800 градусов Цельсия.
Отжиг меди
Медь отжигают при температуре около 550 градусов по Цельсию, когда меди разогрета до темно-красного цвета.
После нагрева медь охлаждают в воде или позволяют медленно охлаждаться на воздухе. Скорость охлаждения меди после нагрева при температуре отжига не влияет на степень получаемой «мягкости» этого металла. Преимущество быстрого охлаждения заключается в том, что при этом металл очищается от окалины и грязи.
Отжиг алюминия
Алюминий отжигают при температуре при температуре 350 градусов Цельсия.
Термическая обработка цветных сплавов
На заводах это делают в подходящих печах или соляных ваннах. В мастерской алюминий отжигают газовой горелкой. Рассказывают, что при этом деревянной лучиной трут по поверхности нагретого металла.
Когда дерево начинает оставлять черные следы, то это значит, что алюминий получил свой отжиг. Иногда вместо дерева применяют кусок мыла: когда мыло начинает оставлять коричневые следы, нагрев нужно прекращать. Затем алюминий охлаждают в воде или оставляют охлаждаться на воздухе.
Отжиг цинка
Цинк становиться снова ковким при температуре между 100 и 150 градусами Цельсия.
Это значит, что его можно отжигать в кипятке. Цинк нужно обрабатывать, пока он горячий: когда он охлаждается, то сильно теряет свою ковкость.
Медь находит широкое применение при изготовлении изделий различного назначения: сосудов, трубопроводов, электрораспределительных устройств, химической аппара- туры и т. д. Многообразие использования меди связано с ее особыми физическими свойствами.
Медь обладает высокой электропроводностью и теплопроводностью, устойчива в отношении коррозии. Плотность меди 8,93 Н/см3, температура плавления 1083°С, температура кипения 2360°С.
Трудности сварки меди обусловлены ее физико-химическими свойствами4. Медь склонна к окислению с образованием тугоплавких оксидов, поглощению газов расплавленным металлом, обладает высокой теплопроводностью, значительной величиной коэффициента линейного расширения при нагревании.
Склонность к окислению вызывает необходимость применения при сварке специальных флюсов, защищающих расплавленный металл от окисления ,и растворяющих образующиеся оксиды, переводя их в шлаки.
Высокая теплопроводность требует применения более мощного пламени, чем при сварке стали. Свариваемость Си зависит от ее чистоты, особенно ухудшают свариваемость Си наличие в ней В1, РЪ, 3 и Оз. Содержание рг в зависимости от марки Си колеблется от 0,02 до 0,15%, Ш и РЬ придают меди хрупкость и красноломкость.. Наличие в Си кислорода в виде оксида меди Си20 вызывает образование хрупких прослоек металла и трещин, которые появляются в зоне термического влияния.
Оксид меди образует с медью легкоплавкую эвтектику, которая обладает более низкой температурой плавления. Эвтектики располагается вокруг зерен меди и таким образом ослабляет связь между зернами.
На процесс сварки Си оказывает влияние не только кислород, растворенный в меди, но и кислород, поглощаемый из атмосферы. При этом наряду с оксидом меди СиаО образуется оксид меди СиО. При сварке оба эти оксида затрудняют процесс газовой сварки, поэтому их необходимо удалять с помощью флюса.
Водород и оксид углерода также отрицательно влияют на процесс сварки Си.
В результате их взаимодействия с оксидом меди СиаО образуются пары воды и углекислый газ, которые образуют поры в металле шва. Чтобы избежать этого явления, сварку меди необходимо выполнять строго нормальным пламенем. Чем "чище Си и чем меньше она содержит 0-2, тем лучше она сваривается.
По ГОСТ 859—78 промышленностью для изготовления сварных конструкций выпускается медь марок М1р, М2р МЗр, имеющая пониженное содержание Оа- (до 0,01%).
При газовой сварке Си нашли применение стыковые и угловые соединения, тавровые и нахлесточные соединения не дают хороших результатов.
Перед сваркой свариваемые кромки необходимо очистить от грязи, масла, оксидов и других загрязнений на участке не менее 30 мм от места сварки. Места сварки очищают вручную или механическим способом стальными щетками. Сварку меди толщиной до 8 мм выполняют без разделки кромок, а при толщине свыше 3 мм требуется Х-образна.я разделка кромок под углом 45° в каждой стороне стыка. Притупление делаетоя равным 0,2 от толщины свариваемого металла. В связи с повышенной жидкотеку честью меди в расплавленном состоянии тонкие листы сваривают встык без зазора, а листы свыше 6 мм сваривают на графитовых и угольных подкладках.
Мощность сварочного пламени при сварке меди толщиной до 4 мм выбирают из расчета расхода ацетилена 150—175 дм3/ч на 1 мм толщины свариваемого металла, при толщине до 8—10 мм мощность увеличивают до 175—225 дм8/ч.
При больших толщинах рекомендуется сварка двумя горелками — одной ведется подогрев, а другой — сварка. Для уменьшения теплоотвода сварку выполняют на асбестовой подкладке. Для компенсации больших потерь теплоты за счет отвода в околошовную зону применяют предварительный и сопутствующий подогрев свариваемых кромок.
Подогревают кромки одной или несколькими горелками.
Пламя для сварки Си выбирают строго нормальным, так как окислительное пламя вызывает сильное окисление, а при науглероживающем пламени появляются поры и трещины. Пламя должно быть мягким и направлять его следует под большим, чем при сварке стали, углом. Сварка проводится восстановительной зоной, расстояние от конца ядра до свариваемого металла 3—6 мм.
В процессе сварки нагретый металл должен быть все время защищен пламенем. Сварку выполняют как левым, так и правым способом, однако наиболее предпочтителен при сварке меди правый способ. Сварка ведется с максимальной скоростью без перерывов.
При сварке Си рекомендуется свариваемые изделия устанавливать под углом 10° к горизонтальной плоскости.
Сварка ведется на подъем. Угол наклона мундштука горелки к свариваемому изделию составляет 40—50°, а присадочной проволоки — 30—40°. При выполнении вертикальных швов угол наклона мундштука горелки составляет 30° и сварку ведут снизу вверх. При сварке меди не рекомендуется скреплять детали прихватками. Длинные швы сваривают в свободном состоянии обратноступенчатым способом.
Газовую сварку меди выполняют только за один проход.
На процесс газовой сварки Си оказывает большое влияние состав присадочной проволоки. Для сварки в качестве присадка применяют прутки и проволоку согласно ГОСТ 16130—72 следующих марок: М1, МСр1, МНЖ5-1, МНЖКТ5-1-0,2-0,2.
Error 503 Service Unavailable
Сварочная проволока МСр1 содержит 0,8—1,2% серебра. Диаметр присадочной проволоки выбирают в зависимости от толщины свариваемого металла и берут равным 0,5—0,75 8, где 5 — толщина металла, мм, но не более 8 мм.
Сварочная проволока должна плавиться спокойно, без разбрызгивания. Желательно, чтобы температура плавления присадочной проволоки была ниже температуры плавления основного металла. Для предохранения Си от окисления, а также для раскисления и удаления в шлак образующихся оксидов сварку осуществляют с флюсом. Флюсы изготовляют из оксидов и солей бора и натрия. Флюсы для сварки Си применяют в виде порошка, пасты и в газообразной форме Флюсы № 5 и 6, содержащие соли фосфорной кислоты, необходимо применять при сварке проволокой, не содержащей раскислителей фосфора и кремния.
Сварку Си можно выполнять и с применением газообразного флюса БМ-1, в этом случае наконечник горелки надо увеличить на один номер, чтобы снизить скорость нагрева и увеличить мощность сварочного пламени. При использовании газообразного флюса применяют установку КГФ-2-66. Порошкообразный флюс посыпают на место сварки на 40—50 мм по обе стороны от оси шва. Флюс в виде пасты наносят на кромки свариваемого металла и на присадочный пруток. Остатки флюса удаляют промывкой шва 2%-ным раствором азотной или серной кислоты.
Для улучшения механических свойств наплавленного металла и повышения плотности и.
пластичности шва после сварки металл шва рекомендуется проковывать. Детали толщиной до 4 мм проковьшают в холодном состоянии, а при большей толщине — при нагреве до температуры 550— 600°С.
Дополнительное улучшение шва после проковки дает термическая обработка — нагрев до 550—600°С и охлаждение в воде. Свариваемые изделия нагревают сварочной горелкой или в печи. После отжига металл шва становится вязким.
⇐ Предыдущая27282930313233343536Следующая ⇒
Дата публикования: 2015-01-26; Прочитано: 455 | Нарушение авторского права страницы
studopedia.org — Студопедия.Орг — 2014-2018 год.(0.001 с)…
Главная>>Сварка цветных металлов>>Сварки меди со сталью
Сварка меди и её сплавов со сталью. Как сваривать медь и сталь?
На практике сварка меди и стали, чаще всего, осуществляется в стыковых соединениях. В зависимости от характера конструкции, швы в таком соединении могут быть наружными и внутренними.
Для сварки латуни со сталью лучше всего подходит газовая сварка, а для сварки красной меди со сталью — электродуговая сварка металлическими электродами.
Хорошие результаты также получаются при сварке угольными электродами под слоем флюса и газовая сварка под флюсом БМ-1. Часто на практике выполняют газовую сварку латуни со сталью, используя медь в качестве присадочного материала.
Подготовку сварных кромок при одинаковой толщине цветного металла и стали выполняют так же, как и при сварке чёрных металлов.
Сварку листов, толщиной менее 3мм выполняют без разделки, а листов, начиная с 3мм — со скосом кромок.
При недостаточном скосе кромок, или при наличии загрязнений на торцах свариваемых деталей, хорошего провара добиться невозможно. Исходя из этого, при сварке деталей больших толщин, в которых выполнена Х-образная разделка, притупление делать не следует.
Сварка меди со сталью — задача сложная, но вполне выполнимая для наплавочных работ и сварки, например, деталей химической аппаратуры, медного провода со стальной колодкой.
Качество сварки таких соединений удовлетворяет требованиям, предъявляемым к ним. Прочность меди можно повысить путём введения в её состав до 2% железа. При большем количестве железа прочность начинает падать.
При сварке угольным электродом необходимо применять постоянный ток прямой полярности.
Напряжение электрической дуги равно 40-55В, а её длина, примерно, 14-20мм. Сварочный ток выбирается в соответствии с диаметром и качеством электрода (угольный или графитовый) и составляет в пределах 300-550А. Флюс используют такой же, как и для сварки меди, состав этих флюсов дан на этой странице.
Вводят флюс в зону сварки, засыпая его в разделку.
Способ сварки применяют "левый".
Наилучшие результаты при сварке медных шин со стальными получаются при сварке "в лодочку". Схема такой сварки показана на рисунке. Вначале выполняется подогрев медных кромок угольным электродом, а затем сварка с определённым положением электрода и присадочного прутка (см. рисунок). Скорость сварки составляет 0,25м/ч. Сварка меди с чугуном производится с помощью таких же технологических приёмов.
Приварку низколегированной бронзы малой толщины (до 1,5мм) к стали толщиной до 2,5мм можно осуществить внахлёст неплавящимся вольфрамовым электродом в среде аргона на автомате с подачей присадочной проволоки диаметром 1,8мм со стороны.
При этом очень важно направить дугу на нахлёстку со стороны меди. Режимы такой сварки: сила тока 190А, напряжение дуги 11,5В, скорость сварки 28,5м/ч, скорость подачи проволоки 70м/ч.
Медь и латунь хорошо свариваются со сталью стыковой сваркой с оплавлением.
При таком способе сварки стальные кромки оплавляются достаточно сильно, а кромки цветного металла незначительно. Учитывая это обстоятельство, и принимая в расчёт разность удельных сопротивлений этих металлов, принимают вылет для стали, равный 3,5d, для латуни 1,5d, для меди 1,0d, где d — диаметры свариваемых стержней.
Для стыковой сварки таких стержней методом сопротивления рекомендуют вылет, равный 2,5d для стали, 1,0d для латуни и 1,5d для меди. Удельное сопротивление осадки принимается в пределах 1,0-1,5 кг/мм2.
На практике часто возникает необходимость приварки шпилек диаметром 8-12мм из меди и её сплавов к стали, или стальных шпилек к медным изделиям.
Такую сварку осуществляют на постоянном токе обратной полярности под мелким флюсом марки ОСЦ-45 без предварительного подогрева.
Хорошо привариваются к стали или чугуну медные шпильки диаметром до 12мм или шпильки из латуни марки Л62, диаметром до 10мм при силе тока 400А.
А шпильки из латуни марки ЛС 59-1 для приварки не используют.
Стальные шпильки к медным и латунным изделиям привариваются плохо.
Как производится сварка меди в домашних условиях?
Если надеть на конец шпильки, диаметром до 8мм, медное кольцо высотой 4мм, то процесс сварки металлов протекает удовлетворительно. Такие же шпильки диаметром 12мм к брозе марки Бр. ОФ 10-1 привариваются хорошо. Для дуговой сварки меди и стали, наилучшие результаты обеспечивают электроды К-100.
Дополнительные материалы по теме:
Холодная обработка и отжиг металлов
Сварка медных труб
Сварка медных труб является сложным процессом, так как медь сваривается, довольно беспокойная. Выбор технологии для сварки медных труб в зависимости от цели сварных работ и необходимой герметизации сварного шва.
Сварка медных труб Вероятно, это два самых популярных способа: газовая и дуговая сварка.
Дуговая сварка делится на два метода, таких как сварка обычными и неуправляемыми электродами.
Газовая сварка меди Он используется для сварки медных и медных труб, а качество сварки очень велико.
Этот тип сварки означает широкое использование различных токов, которые удаляют оксидную пленку с металлической поверхности. Это дефект при сварке газом, поскольку полученный сварной шов имеет пористую структуру из-за образования пара потока во время нагрева, и сварка не будет герметизирована.
Лучшая сварка медных труб, когда при работе используются специальные электроды, которые позволяют получать высокую температуру сварки и горение.
Температура сварки при сварке должна быть высокой, потому что это более высокий, более чистый сварочный материал и более высокая теплопроводность. Эта технология также не позволяет получить полностью герметичный и высококачественный сварочный шов, так как крышка сварочного электрода останавливается, и прочность шва сильно капает.
Наиболее качественный метод сварки заключается в сварке в среде защитного газа с использованием летучего электрода из вольфрама.
В этом случае газ аргона действует как защитный газ, потому что он инертен. Использование азота позволяет производить сварной бассейн, но для уменьшения его глубины. Аргон позволяет получить узкий и глубокий сварной шов, который улучшит качество сварных деталей.
Из-за поступления кислорода в сварочный бассейн для достижения высокого качества работы, использовать медный провод, в качестве наполнителя.
Он должен содержать много кислородсвязывающих добавок. Одной из этих добавок является марганец.
Некоторые наполнители не дают желаемого результата, потому что некоторые из их включений изменяют свойства металла шва, делая его более хрупким или менее долговечным. Поэтому, чтобы избежать таких эффектов сварки, как снижение свойств сварочных металлов, необходимо использовать наполнители с добавлением редкоземельных металлов, использование которых позволяет достичь высокой чистоты сварного шва и улучшить его качество.
Единственными неудобствами использования редкоземельных металлов являются их высокие затраты, поэтому их необходимо приобрести в специализированных магазинах от производителей.
stroitel12.ru