Гравитационное (классическое) литье алюминия в кокиль. Кокильное литье алюминия
Литье в кокиль: технология, преимущества, недостатки, изготовление
Литье в кокиль – это технологический процесс изготовления отливок путем заливания металлического расплава в многооборотные формы, выполненные из металла (сталь, чугун и пр.). Эту форму называют кокиль.
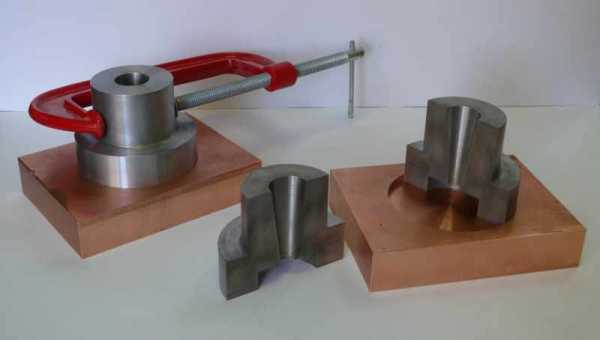
Грибовидный кокиль
Процесс литья в кокиль
Перед началом литья в кокиль металлического расплава необходимо выполнить операции технологического процесса по подготовке его к работе. Эта работа выполняется в несколько этапов.
- Поверхности кокиля и место стыков полуформ необходимо очистить от загрязнений, коррозии, масел.
- Выполняют проверку подвижности перемещающихся деталей, точность их установки и надежность крепления на местах для этого предназначенных.
- На этом этапе поверхности формы смазывают огнестойкими материалами. В этом качестве применяют специальные краски и смазки.
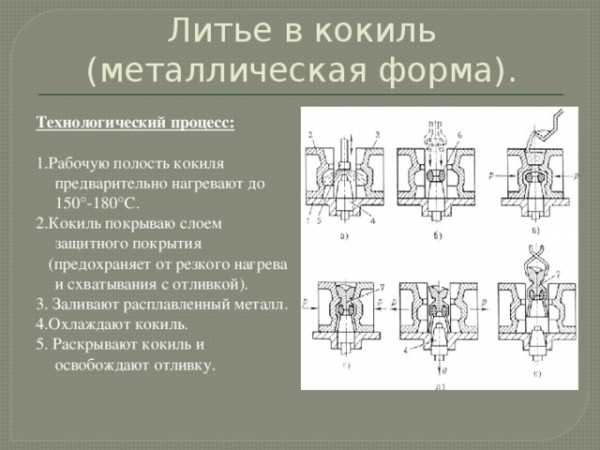
Технологический процесс литья в кокиль
Веществ, которые применяют при облицовке кокиля, зависят от марки заливаемого состава. Толщина покрытия зависит от необходимой скорости охлаждения отлитой заготовки. То есть, чем больше слой наносимой облицовки, тем заготовка будет медленнее охлаждаться. Огнестойкий слой призван решить еще одну задачу в процессе этого литья – обеспечить сохранность формы от скачка температуры во время заливки металла, а также оплавления ее частей и их схватывания с расплавом. В состав огнеупорной облицовки могут входить следующие материалы – кварц, глина, жидкое стекло, графит.
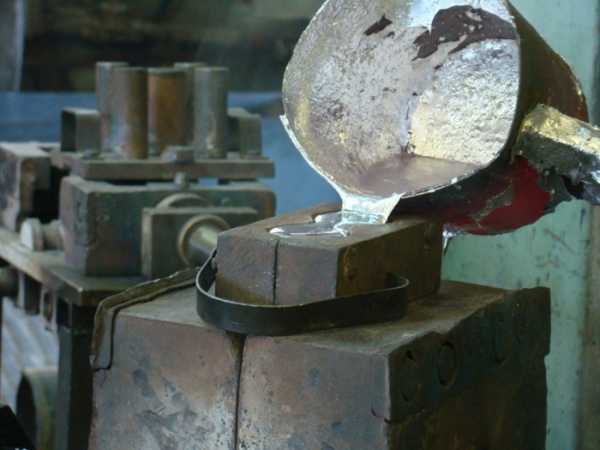
Процесс отлива в кокиль
Перед началом заливки металла форму прогревают до температуры порядка 200 градусов. Эта температура определяется маркой заливаемого металла и габаритов отливки.
Конструктивные особенности кокиля
Кокиль для литья – это многооборотная форма, изготавливаемая из металла. Несмотря на то что в такие формы могут использовать для получения отливок разных форм, их принципиальная конструкция одинакова. В состав кокиля для литья входят полуформы, плита, различные вставки и литейные стержни. С помощью последних, происходит формирование отливки. Для его центрирования и соединения применяют штыри. Непосредственно перед началом заливки полуформы фиксируют с помощью специальных замков. Металлический расплав подают в форму через систему литников.
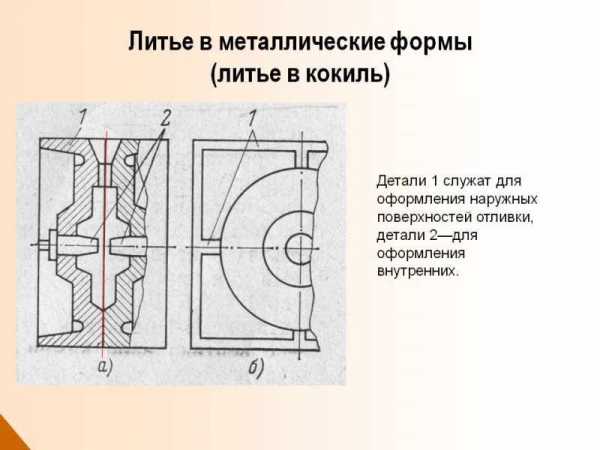
Литье в металлические формы (кокиль)
По мере заполнения кокиля излишки воздуха выводятся через воздуховодные каналы.
В литейном производстве применяют и другой вид форм – их называют вытряхными. Эти формы отличаются тем, что они неразъемные и применяются для отливок простой формы.
Процесс изготовление кокиля и используемые материалы
При изготовлении кокилей проектировщик должен руководствоваться марками сплава, которые будут заливаться в изготавливаемую форму. Разумеется, он должен учитывать и размер деталей, получаемых в результате литья в эту оснастку.
Так, при изготовлении деталей с небольшими габаритами из цветных металлов, чугуна и некоторых других материалов рекомендуется использовать для производства литейных форм серые чугуны 20 или 25. Для производства кокилей применяют и другие виды материалов. Надо отметить, что чем прочнее материал, например, сталь 15Л, тем выше стойкость формы. Для определенных марок металла формы производят из алюминия, но перед эксплуатацией этих кокилей рабочие поверхности анодируют.
Производство кокилей выполняют на оборудовании объемной штамповки. Но современное оборудование, работающее под управлением компьютера, например, токарно-фрезерный центр позволяет производить особо точные формы.
Преимущества и недостатки литья в кокиль
Литье этого типа, как и многие технологические процессы, обладают и преимуществами, и недостатками. Можно сравнить литье в кокильную оснастку с литьем в песчаные формы.
К основным преимуществам можно отнести то, что литье в металлические формы отличается от всех остальных качеством получаемых деталей, в частности, точностью. Применение песочных стержней позволяет выполнять отливки сложной формы.
Использование металлических кокилей позволяет повысить производительность труда на литейном производстве. Это обусловлено тем, что из производства исключены такие операции, как приготовление литьевой смеси, и чистки отливок.
Использование такого типа литья позволяет уменьшить припуски на дальнейшую механическую обработку. Такой подход позволяет снизить себестоимость готового изделия.
Такое свойство кокилей, как оборачиваемость позволяет механизировать процессы литья и последующей обработки отливок. Например, операция сборки этой оснастки может быть легко автоматизирована. Кроме того из процессов исключены факторы, которые могут отрицательно сказаться на качестве отливок, например, газопроницаемость смеси. Автоматизация литейных процессов регулировать технологические режимы литейных процессов, что приводит к изменению характера труда оператора литейного комплекса и повышению его безопасности.
Между тем при множестве достоинств литье этого класса имеет и ряд недостатков.
Кокиль обладает высокой стоимостью, это является следствием его конструктивной сложности и и высокой трудоемкости производства. Особенно это относится к оснастке, в которые отливают детали сложной геометрической конфигурации.
Литейная оснастка такого типа имеет ограниченную стойкость. Стойкость оснастки определяется количеством качественных отливок. При снижении качества, его просто направляют в утилизацию. Стойкость – это ключевой экономический показатель литья. Над повышением стойкости форм этого класса работают производители и проектировщики оборудования для литья в формы этого типа по всему миру.

Литье сплава в кокиль
Интенсивность охлаждения отливок в кокиле существенно выше, чем в песчаных или земляных оснастках. Это приводит к тому, что ограничена возможность изготовления отливок с тонкими стенками.
Поскольку эти оснастки не обладает достаточной податливостью – это может привести к появлению в отлитых деталях внутренних напряжений. Которые потом устраняют с помощью термообработки.
Область применения
Кокильное литье широко используют для производства отливок из черных и цветных металлов. На автоматизированном оборудовании, предназначенном для этой обработки металлов допустимо литье алюминия в кокиль, но при этом вес отливки не должен превышать 30 кг.
На неавтоматизированном оборудовании допустимо литье чугуна в кокиль, при этом масса отливки не должна превышать 12 тонн.
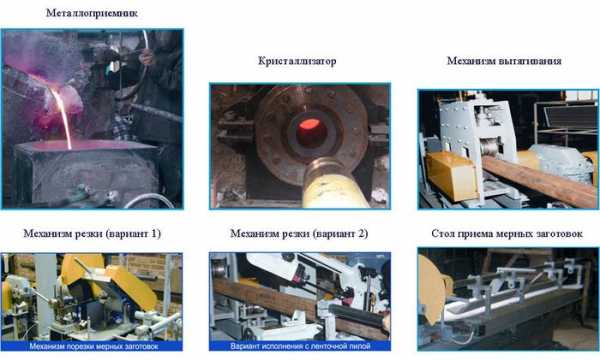
Этапы литья в кокиль
Сложно найти промышленную отрасль, в которой не применяют литье в кокиль. Эта технология позволяет изготавливать широкий круг деталей из различных металлов. Например, на электротехнических заводах их применяют для отливки деталей электрических машин, на предприятиях, которые выпускают силовые установки для автомобилей, эту технологию применяют для производства головок блока цилиндров или картеров защиты.
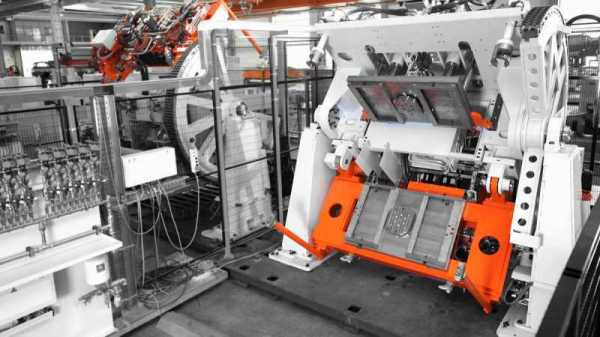
Кокильная литейная машина
Практика показывает, что чаще всего литье этого типа применяют в отношении алюминия и его сплавов. На втором месте стоит чугун и на третьем сталь.
Если вы нашли ошибку, пожалуйста, выделите фрагмент текста и нажмите Ctrl+Enter.
Литье алюминия и сплавов в кокиль
Сергей Валериевич, Пермь:
Недавно услышал о способе литья алюминия с использованием специальных металлических кокилей. Эта технология очень заинтересовала меня, поэтому хотелось бы подробнее узнать обо всех нюансах.
Ответ нашего эксперта:
Во время литья алюминия в кокиль горячий материал свободно заполняет специальные формы. Кроме воздействия силы тяжести, он не подвергается дополнительному давлению. На долю кокильного литья приходится до 40% от всего объема производства заготовок из цветных металлов. Это вызвано многочисленными преимуществами методики:
- повышенная точность отливок;
- высокая производительность;
- возможность многократного использования форм;
- процесс производства отличается высокой автоматизацией;
- отливаемые детали имеют стабильную структуру по всему объему;
- существует возможность комбинирования кокилей и песчаных стержней;
- в процессе литья отсутствуют трудоемкие операции выбивки форм, очистки заготовок от пригара;
- снижается объем вредных выбросов в окружающую среду;
- получаемые заготовки имеют отличные эксплуатационные свойства.
К недостаткам кокильного литья относят высокую трудоемкость и стоимость изготовления форм, повышенная склонность к появлению внутренних напряжений. Во время производства заготовки подвергаются интенсивному охлаждению. Поэтому данным способом невозможно получить тонкостенные протяжные отливки.
Сфера применения методики обширная. Ее преимущественно используют для изготовления деталей из алюминиевых, цинковых или магниевых сплавов. Иногда данную методику применяют для формировки тугоплавких материалов.
Технология кокильного литья выглядит следующим образом:
- Формы тщательно подготовляют к работе – очищают, проверяют надежность креплений, способность перемещения передвижных деталей.
- Инвентарь нагревают до температуры +150-280°С при помощи газовых горелок или электричества.
- На поверхность инвентаря наносят слой из огнеупорного покрытия – краски и облицовки.
- Кокиль нагревают до рабочей температуры, зависящей от состава сплава и перечня требуемых свойств.
- Устанавливают керамические или песчаные стержни. Половинки кокиля соединяются и фиксируются зажимами.
- Форму устанавливают в специальную кокильную машину, после чего осуществляют заливку сплава.
- Отливку охлаждают до заданной температуры. Кокиль раскрывают, извлекают стержни и удаляют готовую деталь.
- Из оливки выбивают песчаный стержень и устраняют другие дефекты.
- Цикл заливки повторяют по той же схеме. Периодически на поверхность инвентаря наносят новый слой огнеупорной краски.
Видео: Кокильное литье алюминиевых деталей
promzn.ru
Что такое кокиль? Изготовление кокиля. Литьё в кокиль
Что общего между закуской из морепродуктов и формой для литья? Тот, кто разбирается одновременно и в кулинарии, и в металлургии, вспомнить о названии «кокиль».
Во французской кухне им именуют горячее блюдо из рыбы, подаваемое в металлической посуде, напоминающей створку морской раковины. Чаша именуется кокильницей. В металлургии она выглядит иначе. Как именно? С этого начнем обзор.
Что такое кокиль?
Кокиль на фото, предстаёт как металлические сосуды различных форм и размеров. Все зависит от того, какую отливку нужно получить. В кокилях, к примеру, формируют чугунные изделия.
Бывают разъемные и неразъемные формы. Последние, называются вытряхными. Готовые изделия из них попросту вытрясают. Понятно, что литье должно иметь простые формы, иначе, застрянет в сосуде.
Разъемные кокили предназначены для отливки изделий сложных форм. От их сложности зависит количество разъемов. К тому же, бывают одно- и многоместные кокили. В последних, присутствуют несколько рабочих полостей. Это позволяет делать отливки в кокиль, экономя время, формируя сразу партию товара.
Поскольку в производственные кокили заливают не горячую еду, а расплавленные металлы, емкости должны быть устойчивыми к высоким температурам, причем неоднократным. Поэтому, для изготовления литейных форм подходит узкий круг материалов. Рассмотрим их.
Изготовление кокиля
Изготовление кокилей для литья ориентируется на то, с какими сплавами им предстоит взаимодействовать. Материал форм, так же, подбирается в соответствии с размерами заливок.
Так, для мелких и средних изделий из меди, алюминия, чугуна и сплавов магния используют кокили из СЧ20 и 25. Под аббревиатурами скрываются марки чугуна. 25-я соответствует перлитному, а 20-я – феррито-перлитному.
Расшифруем. Феррум – научное название железа. Перлит – горная порода вулканического происхождения. Собственно, сим состав 20-го и 25-го чугунов и ограничивается.
Оба сплава низколегированные, то есть, сторонних добавок в них минимум. По свойствам марки расходятся лишь в показателе модуля упругости. У 25-го чугуна он на 70 единиц больше.
Литье в кокили из чугунов ВЧ40 и ВЧ45 подходит и для изделий крупных форм. Отливают их, охлаждая воздухом, или смесью газов с водой. В качестве заливаемого в формы материала берутся серые чугуны. Они состоят из железа и углерода. Последний элемент частично преобразован в графит. Его хлопья и придают сплавам серый цвет.
Литье в кокиль формы особо крупной возможно, если емкость стальная. Для нее подойдут 5 марок сплава. Это стали: Cm3, 10, 20, 15-Л-11 и 15ХМЛ. Кокили из них подходят и для мелких, средних отливок. Главное, чтобы изделия создавались из чугуна, смесей с магнием и медью. Кокиль для алюминия тоже может быть стальным.
Из меди и ее сплавов делают кокили для отливки металлических стержней. Они могут быть любого состава. Медные стенки формы, как правило, тонкие и позволяют охлаждать заготовки водой.
Из сплавов алюминия высокопрочными и жароустойчивыми являются марки АЛ9 и АЛ11. Для кокилей берутся их анодированные версии. Так именуют сплавы алюминия с покрывающей их пленкой оксидов. Она защищает поверхности от коррозии и увеличивает их прочность.
Литье металлов в кокиль из алюминиевых сплавов марок 9 и 11 осуществляют ради получения мелких изделий. Они могут быть медными, или состоять все из того же алюминия. Стенки сосудов тонкие, поэтому легко охлаждаются водой.
Литье в кокиль
Технология литья в кокиль распространена. Свидетельство тому – цифры. Из цветных металлов, к примеру, в формах изготавливают 40% продукции. При ее изготовлении учитывают, что большинство сплавов дают при застывании усадку.
В расплавленном виде их объем больше. Поэтому, расчет кокиля ведется так, чтобы форма была шире конечного продукта. Разница в объемах равна показателю усадки конкретного сплава.
То есть, если форма предназначена для производства деталей из сплава алюминия определенной марки, залить в нее иной состав получится, но должного результата не будет.
Если в изготавливаемом товаре предусмотрены отверстия, их выполняют металлическими, или песочными стержнями. По окончанию процесса, их вынимают из изделия.
Песчаными, кстати, бывают и формы для отливки. Но, такие емкости одноразовые. Кокили же используются месяцами, годами. Стальные формы рассчитаны на 50-500 прогонок, чугунные – на 400-4 000.
Для заливки расплава в кокили используют литниковую систему. Она слагается из ряда каналов и резервуаров в форме. Их несколько, поскольку через один металлическая масса не заполнит кокиль равномерно, особенно, если он сложной конфигурации.
Присутствует в кокилях и вентиляция. Она нужна для удаления из внутренних камер воздуха и прочих газов. Останься они в форме, заняли бы часть ее объема, даже будучи сжатыми напирающими металлами. К тому же, присутствие в кокиле газов позволило бы им просочиться в состав сплава для отливки, изменив его характеристики, загрязнив.
Наличие в кокилях необходимых систем не говорит о возможности слепого пользования ими. Перед каждой заливкой проверяются проходимость каналов вентиляции и литников. Следует тщательно очистить внутренние полости формы. После, проверяют точность перемещения ее подвижных деталей и надежность креплений между частями кокиля.
Еще одна операция перед заливкой – нанесение на внутреннюю поверхность огнеупора. Его толщина высчитывается исходя из необходимой скорости остывания сплава. Для кокиля огнеупор несет сберегающую функцию, избавляя от резкого скачка температуры при заливке. Это продлевает жизнь форм.
Далее, учитывается способ литья. Так сплавы с выраженной жидкотекучестью не требуют дополнительного давления. А вот для вязких материалов оно не помешает. При этом, нужно учесть, что литье в кокиль под давлением дает большую усадку изделия. Поэтому, если сплав и без того склонен к резкому изменению объема, лучше провести формирование детали в обычных условиях.
Преимущества и недостатки литья в кокиль
У литья в кокили есть ряд минусов. Во-первых, формы дорогостоящи. Хоть их и можно использовать многократно, век кокилей, все же, недолог. Особенно короток он у емкостей для формирования деталей из стали.
Еще одна проблема работы с кокилями — трещины на готовых изделиях и коробление их поверхности. Это связано с высокими внутренними напряжениями, рождающимися в остужаемом расплаве.
Огрехи проявляются, если материал охлаждается неравномерно, или претерпевает структурные изменения. Не секрет, что сплав – это смешение разных компонентов. На температуры и прочие факторы они тоже реагируют по-разному.
Поэтому, к примеру, при равномерной прокалке стали мартенсит из нее соберется на наружном слое, а перлит устремится к центру. В итоге, создается ситуация лебедя, рака и щуки из басни Крылова. Растягивая деталь в разные стороны, компоненты «приводят» к образованию трещин.
Последним минусом применения кокилей является их газонепроницаемость. Между тем, для формирования некоторых изделий присутствие атмосферы необходимо. Поэтому, использование металлических форм для заливки сужает круг изделий, которые можно производить и сплавов, коими можно пользоваться.
При этом, выбор в пользу кокилей производители делают, зная о высокой точности деталей, получаемых в них. К тому же, при соблюдении технологии, из форм извлекаются изделия с идеально ровной и чистой поверхностью. Это дорогого стоит. Потребители готовы платить за качество, а значит, кокили продолжат заказывать на тысячах заводах по всему миру.
tvoi-uvelirr.ru
Литье алюминия в кокиль - его плюсы и минусы
Литье в кокиль — это вид литья, при котором расплавленный металл заливают под атмосферным давлением в специальную металлическую форму – кокиль. Отсюда и название вида литья. Данный вид отличается от других способом наполнения, при котором участвует исключительно сила тяжести, воздействующая на расплавленный металл.
Плюсы кокильного литья:
- Главной особенностью литья в кокиль является то, что металлический кокиль, в отличие песчаной формы, значительно лучше способен проводить тепло, что ускоряет затвердевание металла. Высокая интенсивность охлаждения металла, залитого в него, обуславливает существенное увеличение плотности структуры у конечного продукта, то есть его прочности.
- Как правило, форма для кокильного литья многоразовая и способна выдержать до 10 тыс. циклов отливки, что является большим плюсом, если речь заходит о стоимости производства больших партий.
- Метод литья в кокиль весьма популярен, но наибольшее применение он получил в машиностроение в производстве деталей для двигателя, где требуется высокая точность. Данная технология обеспечивает достаточно высокий уровень точности, при низких затратах на создание формовочных форм.
Минусы кокильного литья:
- Наиболее серьезным недостатком данного метода литья является сложность, а в некоторых случаях — невозможность отливки тонкостенных изделий, стенки которых толщиной менее 5 мм.
- Вторым ограничением данного литья является стоимость производства самих кокилей. Из-за чего экономически необоснованно применять его при малых партиях.
- Металлы, которые применяются при этом методе литья, должны обладать значительной устойчивостью к термическим ударам.
Типы конструкций кокилей:
- Разъёмный.
- Выбивной.
Процесс литья в кокиль:
Непосредственно сам процесс литья в кокиль начинается с обработки внутренней поверхности огнеупорными материалами, такими как жидкое стекло, графит или порошковые кварцы. Затем форму разогревают до 700 градусов, перед тем как залить в нее расплавленный металл.
Отличительными особенностями отливок, получаемых при литье алюминия в стальной кокиль, являются:
- Минимальные припуски на механическую обработку, или вообще не требующие таковой.
- Минимальная шероховатость необрабатываемых поверхностей и точность размеров.
- Четкость получаемая рельефа, позволяющая получать отливки с минимальной толщиной стенки 1,5мм.
- Низкая трудоемкость при изготовлении одной отливки и как результат быстрое выполнение заказов.
- Равномерная кристаллизации отливки, что позволяет получить отливку с плотным и мелкозернистым строением.
- Герметичность и высокие физико-механические свойства.
- Возможный минимальный вес отливок при изготовлении соответствует весу 70 грамм.
- Максимально возможный вес до 150 кг.
- Минимальная партия изделий от 100 штук.
- Время проектирования изготовления кокиля от двух недель.
- Разработки и изготовления многоместных кокилей.
meltcom.com.ua
Гравитационное (классическое) литьё алюминия в кокиль
Для крупносерийного выпуска алюминиевой продукции используются многочисленные методы получения отливок. Традиционным и широко распространенным на литейном производстве является метод гравитационного (классического) литья алюминия. Почему он называется гравитационным, в чем особенности и основные достоинства данного метода?
Гравитационное литьё сплавов из алюминия
Для выпуска изделий требуемых параметров используют специальную емкость — кокиль, в которую заливается расплавленная масса металла. После полного охлаждения готовую деталь можно легко извлечь и отправить на последующую механическую обработку. Кокиль обычно изготовлен из чугуна, благодаря чему допустимо его многоразовое применение до 10 тысяч циклов.
Если же речь идет о мелкосерийной или единичной продукции, в ход идут пластиковые и даже деревянные емкости, а также изготовленные из песка и глины с добавлением пластификаторов. Кокиль — это один из элементов литейной оснастки, кроме него требуются также различные стержни, модельные плиты и шаблоны, необходимые для производства деталей из алюминия со сложной геометрией.
Расплавленный металл под действием силы гравитации заполняет все полости оснастки, полностью копируя форму заданного изделия. После его извлечения на поверхности могут быть шероховатости или другие изъяны, избавиться от которых можно путем дальнейшей механической обработки.
Основные этапы классического литья
Кокиль нашел широкое распространение на литейных производствах по той простой причине, что алюминий относится к мягким пластичным металлам. Вылитые из него детали широко используются практически во всех сферах промышленности, например в машиностроении.
Сам процесс производства состоит из определенных стадий:
- подготовка оснастки;
- установка стержней;
- заливка жидкого металла;
- охлаждение и извлечение.
Изготовление оснастки является одним из наиболее ответственных этапов, так как форма должна с максимальной точностью повторять линии готового изделия. К счастью, сегодня есть достаточно функциональные программы и сложное оборудование для 3D моделирования и получения нужных форм.
Чтобы готовое изделие можно было легко извлечь из кокиля, его стенки тщательно очищают, а затем покрывают специальной облицовкой. Наличие малейших неровностей может привести к образованию дефектов.
Преимущества гравитационного литья
Почему именно данный способ нашел наибольшее распространение? Причин можно привести множество, но основная из них — относительная простота и дешевизна по сравнению с другими способами. А это отображается и на конечной стоимости отливок.
Из других достоинств отметим:
- точность, низкий уровень шероховатости;
- толщина стенок от 4 мм и более;
- выпуск деталей практически любых размеров;
- быстрое остывание алюминиевых сплавов.
Благодаря всем этим факторам можно значительно снизить себестоимость готовой продукции. Кроме того, все изделия полученные данным методом, проходят строгую систему ОТК, любой брак отправляется на переработку.
alm163.ru
Кокиль - это что такое?
Кокиль - это многоразовая форма для заливки металла. Она может быть как разъемной (состоять из двух частей), так и нет (вытряхной кокиль). Кокильное литье имеет ряд преимуществ перед оболочковым, однако есть и некоторые недостатки, к примеру, при литье чугуна отливки требуют дополнительной термической обработки.
Преимущества
Во время формирования отливки происходит интенсивная передача тепла из расплавленного металла в кокиль. Это в итоге дает более высокую плотность, лучшие механические свойства металла, высокую точность, лучшую структуру и меньшую шероховатость по сравнению с отливками из песчаных форм.
Процесс литья в кокиль отличается еще и тем, что металлическую форму (кокиль) можно использовать многократно. Она делается из материала высокой прочности, за счет чего рабочая поверхность формы выполняется более точно. Это повышает качество поверхности отливок, а за счет высокой теплопроводности кокиля отливки быстро застывают.
Еще одно преимущество кокильного литья перед использованием песчаных форм - это меньшая степень дальнейшей механической обработки получаемых отливок, а это сокращает расход материалов на формовку.
Здоровье и экология
Литье в кокиль в 2-3 раза повышает производительность труда, ведь из процесса исключаются такие трудоемкие операции, как подготовка смеси, очистка и формовка изделий. Так как производственные площади тоже снижаются, затраты на ремонт и строительство новых цехов становятся существенно меньше.
Из процесса устраняются многие вредные для здоровья рабочих операции, такие как выбивка форм, очистка отливок и их обрубка. Это способствует не только улучшению условий на производстве, но и уменьшению загрязнения окружающей среды.
Недостатки
Изготовление кокиля обходится достаточно дорого ввиду трудоемкости самого процесса. При наличии в отливках поднутрений стоимость кокиля увеличивается из-за необходимости усложнения конструкции: используются вставки, одноразовые песчаные и разъемные металлические стержни.
Срок работы кокиля определяется количеством отливок хорошего качества, которые в нем можно получить. Стойкость формы определяет экономическую целесообразность процесса, особенно в процессе литья стали и чугуна. Повышение срока эксплуатации кокилей является одной из главных технологических задач в этой сфере производства.
Из-за быстрого остывания и загустения расплава осложняется получение длинных тонкостенных изделий при литье в кокиль. Это приводит также к тому, что чугунные отливки приобретают твердый, отбеленный слой. Форма податлива, это может привести к образованию напряжений и трещин в отливках. При использовании одноразовых песчаных стержней снижается точность отливок, повышается шероховатость поверхности в месте контакта со стержнем.
Качество отливок
Отливка и форма взаимодействуют с высокой эффективностью. Отливка затвердевает и остывает в песчаной форме гораздо дольше, чем в кокиле, однако заполняемость у песчаной формы обычно лучше, что делает более трудоемким процесс производства путем кокильного литья отливок из нетекучих сплавов, а также вносит ограничения в такой параметр, как размер отливки и минимальная толщина стенки. Литье алюминия в кокиль (а также меди и других цветных металлов) является самым востребованным в России.
Однако в результате быстрого охлаждения можно получать непористую, мелкозернистую структуру, что увеличивает не только прочность, но и пластичность полученной отливки. При изготовлении изделий из чугуна путем кокильного литья возникает ряд проблем: из-за своеобразной кристаллизации в отливках возможно образование карбидов, феррито-графитной эвтектики. Это снижает ударную вязкость и износостойкость чугуна. Отбеленный поверхностный слой в таких отливках очень тверд, вследствие чего изделия пригодны для обработки резанием только после термической обработки (отжига), которая устраняет отбел.
Строение формы
Кокиль - это, как правило, две полуформы, которые крепятся фиксаторами (штырями), а непосредственно перед началом заливки расплавленного металла полуформы закрепляются замками. Прибыли осуществляют питание отливки через так называемые выпоры и вентиляционные пробки. Металлические формы без функции разъема называются вытряхными кокилями.
Перед тем как осуществлять заливку, рабочую поверхность формы обрабатывают слоем вещества, предохраняющего кокиль от теплового удара от резкого повышения температуры. Такая мера также предохраняет от схватывания отливки с формой.
Сталь и чугун
Отливка в кокиль стали и чугуна происходит с использованием пылевидного кварца, графита, жидкого стекла и огнеупорной глины в качестве огнеупорного покрытия. Перед заливкой кокиль должен быть нагрет до определенной температуры, которая зависит от толщины стенок отливки и используемого сплава.
Главное требование, которому должен отвечать материал кокиля, - это устойчивость к теплоударам, неизбежным при заливке расплавленного металла. Для изготовления форм используют серый чугун, высокопрочный чугун, конструкционную, углеродистую и легированную сталь, а также сплавы меди и алюминия.
Облицованный кокиль
Это разновидность технологии, в которой совмещают свои достоинства оболочковое и кокильное литье, а недостатки обоих способов сглаживаются. Эта технология характеризуется не только трещиностойкостью, но и податливостью, что позволяет изготавливать отливки высокой точности, а если сравнивать с оболочковым литьем, дорогостоящий формовочный материал расходуется минимально.
Облицованная металлическая форма изготавливается путем заполнения пространства между металлической моделью отливки и внутренней поверхности кокиля. Чаще всего используются пескодувный и заливной способы. Для заполнения берут песчано-смоляную смесь, в которой связующим элементом является фенолформальдегидная смола (2-2.6%) и уротропин (примерно 10% от массы), а также самозатвердевающие (связующий компонент - жидкое стекло) и керамические составы (связующий - этилсиликат). Кокиль и модель отливки, имеющие температуру от 200 градусов, передают тепло смеси, которая затвердевает и образует слой облицовки толщиной 3-5 мм. Обычные или оболочковые стержни служат для выполнения полостей в отливках.
Процесс литья
Кокиль, покрытый слоем огнеупорного материала, нагревается. Рабочая температура должна быть не менее двухсот градусов, но зависит не только от используемого для заливки сплава, но и от размеров отливки, толщины ее стенок и от свойств, которые от нее требуются. После нагревания в кокиль можно установить стержни, керамические или песчаные, если это, конечно, требуется по плану отливки, а затем полуформы соединяются и крепко запираются специальными зажимами. Если получение отливки происходит в кокильной машине, то используется ее собственный механизм запирания формы. После этих подготовительных мероприятий в кокиль можно заливать расплавленный металл.
Когда отливка уже приобрела некоторую прочность, из нее можно частично извлечь металлические стержни. Это впоследствии облегчает окончательное извлечение стержней из отливок ввиду уменьшения давления на них со стороны застывающего металла.
После того как отливка охладилась до нужной температуры, кокиль можно раскрыть. На этом этапе извлекаются металлические стержни, и отливки вынимаются из формы. Песчаные стержни выбиваются, прибыли, выпоры и литники обрезаются, а также производится контроль качества изделия, после чего весь процесс можно повторить.
Перед изготовлением новой отливки тщательно осматриваются плоскость разъема и поверхность кокиля. Огнеупорный состав наносится один-два раза за смену, однако в случае отслоения ее от рабочей поверхности необходимо восстановить слой.Кокиль необходимо снова довести до рабочей температуры, так как он сильно охлаждается за время, пока извлекается отливка. Если изделие тонкостенное, форма сильно охлаждается; если же изготавливаемая отливка была достаточно массивной, то кокиль мог нагреться выше рабочей температуры, и тогда используются специально предусмотренные системы охлаждения, так что перед следующей заливкой форма будет в любом случае охлажденной.
Кокильное литье не предполагает никаких сложных и продолжительных по времени действий, исключая процесс остывания отливки до нужной температуры. Большинство операций могут выполняться машинами в автоматическом порядке, что является одним из немаловажных преимуществом способа, но главное - то, что кокиль не одноразовая форма.
fb.ru
Кокили
Классификация конструкций кокилей
В производстве используют кокили различных конструкций. В зависимости от отсутствия или наличия поверхности разъема кокили бывают неразъемные (вытряхные) или разъемные.
Неразъемные, или вытряхные, кокили применяют в тех случаях, когда конструкция отливки позволяет удалять ее вместе с литниками из полости кокиля без его разъема. Обычно эти отливки имеют достаточно простую конфигурацию.
В случае разъемных кокилей расположение и число разъемов определяются необходимостью реализовать рациональное положение отливки в кокиле при заливке, разместить технологические элементы (литниковую систему, прибыли и др.), собрать форму и извлечь из нее без разрушения готовую отливку конкретной конструкции. В свою очередь, разъемы кокиля предопределяют выбор кокильной машины с соответствующим количеством и расположением механизмов, которые обеспечивают перемещение подвижных частей кокиля при его сборке и разборке.
По числу рабочих полостей (гнезд), определяющих возможность одновременного (с одной заливки) изготовления того или иного числа отливок, кокили разделяют на одноместные и многоместные.
В зависимости от способа охлаждения различают кокили с воздушным (естественным и принудительным), жидкостным (водяным, масляным) и комбинированным (водовоздушным и т.д.) охлаждением. Если воздушное охлаждение используют для малотеплонагруженных кокилей, то водяное охлаждение обычно применяют для высокотеплонагруженных кокилей, а также для повышения скорости охлаждения отливки или ее отдельных частей. Вода подается раздельно в обе половины кокиля, нижнюю плиту и верхнюю крышку.
Элементы конструкции кокилей
Конструктивное исполнение основных элементов кокилей – полуформ, плит, металлических стержней, вставок – зависит от конфигурации отливки и от особенностей установки кокиля на кокильную машину.
К основным элементам конструкции кокилей относят: формообразующие элементы – половины кокилей, нижние плиты (поддоны), вставки, стержни; конструктивные элементы – толкатели, плиты толкателей, системы нагрева и охлаждения кокиля и отдельных его частей, вентиляционная система, центрирующие штыри и втулки.
Корпус кокиля или его половины выполняют коробчатым с ребрами жесткости. Ребра жесткости на тыльной (не рабочей) стороне кокиля делают невысокими, толщиной 0,7 – 0,8 толщины стенки кокиля, сопрягая их галтелями с корпусом. Толщина стенки кокиля зависит от состава заливаемого сплава и его температуры, размеров и толщины стенки отливки, материала, из которого изготовляется кокиль, и его конструкции. Толщина стенки кокиля должна быть достаточной, чтобы обеспечить заданный режим охлаждения отливки, необходимую жесткость кокиля и минимальное его коробление при нагреве отводимой теплотой залитого расплава, а также стойкость против растрескивания.
Размеры и конструкция частей кокиля должны позволять размещать и закреплять его на плитах кокильной машины.
Стержни в кокилях могут быть песчаными и металлическими. Песчаные стержни для кокильных отливок должны обладать пониженной газотворностью и повышенной поверхностной прочностью. Первое требование обусловлено трудностями удаления газов из кокиля, второе – взаимодействием знаковых частей стержней с кокилем, в результате чего отдельные песчинки могут попасть в полость кокиля и образовать засоры в отливке. Стержневые смеси и технологические процессы изготовления песчаных стержней могут быть различными – сплошные и оболочковые стержни из холоднотвердеющих смесей и т.д. В любом случае использование песчаных стержней в кокилях вызывает необходимость организации дополнительной технологической линии для изготовления стержней в кокильном цехе. Однако, в конечном счете использование кокилей в комбинации с песчаными стержнями в большинстве случаев экономически оправдано.
Использование металлических стержней зависит от конструкции отливки и технологических свойств сплава. Их использование дает возможность повысить скорость затвердевания отливки, сократить продолжительность цикла ее изготовления, в отдельных случаях повысить механические свойства и плотность (герметичность) отливки. Однако при использовании металлических стержней возрастают напряжения в отливках, увеличивается опасность появления в них трещин из-за затруднения усадки.
Для надежного извлечения стержней из отливки они должны иметь ук-лоны 1 – 5о, хорошие направляющие во избежание перекосов, а также быть надежно зафиксированы в форме.
Во многих случаях металлические стержни делают водоохлаждаемыми изнутри. Водяное охлаждение стержня обычно включают после образования в отливке прочной корочки. При охлаждении размеры стержня сокращаются и между ним и отливкой образуется зазор, благодаря которому уменьшаются усилия при извлечении стержня из отливки.
Вентиляционная система должна обеспечивать направленное вытеснение воздуха из кокиля расплавом. Для выхода воздуха используют открытые выпоры, зазоры по плоскости разъема и между подвижными частями кокиля и специальные вентиляционные каналы. По плоскости разъема делают газоотводные каналы, направленные по возможности вверх. В местных углублениях формы при заполнении их расплавом могут образовываться воздушные мешки. В этих местах в стенке кокиля устанавливают вентиляционные пробки. При выборе места установки вентиляционных пробок необходимо учитывать последовательность заполнения формы расплавом.
Центрирующие элементы – контрольные штыри и втулки – предназначены для точной фиксации половин кокиля при его сборке. Обычно их количество не превышает двух и располагают их в диагонально противоположных углах кокиля.
Закрытие и запирание кокилей, устанавливаемых на машинах, осуществляется пневматическим или гидравлическим приводом подвижной плиты машины. Системы нагрева и охлаждения кокиля предназначены для поддержания заданного температурного режима процесса. Применяют электрический и газовый обогрев. Первый используется для общего нагрева кокиля, второй более удобен для общего и местного нагрева.
Материалы для кокилей
В процессе эксплуатации в кокиле возникают значительные термические напряжения как результат чередующихся резких нагревов при заливке, а также при затвердевании отливки и охлаждений при раскрытии кокиля и извлечении отливки, нанесении на рабочую поверхность огнеупорного покрытия. Кроме знакопеременных термических напряжений под действием переменных температур в материале кокиля могут протекать структурные изменения и химические процессы. Поэтому материалы, предназначенные для изготовления кокиля, особенно его частей, непосредственно соприка-сающихся с расплавом, должны хорошо противостоять термической устало-сти, иметь высокие механические свойства и претерпевать минимальные структурные превращения при температурах эксплуатации, обладать повышенной ростоустойчивостью и окалиностойкостью, характеризоваться минимальной диффузией отдельных элементов при циклическом воздействии температур, хорошо обрабатываться, быть недефицитными и недорогими.
Производственный опыт показывает, что для изготовления рабочих стенок кокилей пригодны следующие материалы, в достаточно полной мере соответствующие указанным требованиям:
- чугуны СЧ20, СЧ25 и др. – кокили для мелких и средних отливок из алюминиевых, магниевых, медных сплавов, чугуна, а также кокили с воздушным и водовоздушным охлаждением;
- чугуны ВЧ40, ВЧ45 и др. – кокили для мелких, средних и крупных отливок из чугунов: серого, высокопрочного, ковкого, кокили с воздушным и водовоздушным охлаждением;
- стали 10, 20, Ст3, стали 15Л, 15ХМЛ и др. – кокили для мелких, средних, крупных и особо крупных отливок из чугуна, стали, алюминиевых, магниевых, медных сплавов;
- медь и ее сплавы, легированные стали и сплавы с особыми свойствами – вставки для интенсивного охлаждения отдельных частей отливок, тонкостенные водоохлаждаемые кокили, массивные металлические стержни для отливок из разных сплавов;
- силумины АЛ9, АЛ11 и др. — водоохлаждаемые кокили с анодированной поверхностью для мелких отливок из алюминиевых и медных сплавов.
Наиболее широко для изготовления кокилей применяют серый и высокопрочный чугуны, так как эти материалы в достаточной мере удовлетворяют основным технологическим требованиям и сравнительно дешевы. Эти чугуны должны иметь феррито-перлитную структуру. Графит в серых чугунах должен иметь форму мелких изолированных включений. В этих чугунах не допускается присутствие свободного цементита, так как при нагревах кокиля произойдет распад цементита с изменением объема материала, в результате в кокиле возникнут внутренние напряжения, способствующие короблению, образованию сетки разгара, снижению его стойкости. В состав чугунов для кокилей с целью повышения их стойкости вводят до 1 % никеля, меди, хрома, а содержание вредных примесей (серы и фосфора) в них должно быть минимальным. Например, для изготовления кокилей с высокой теплонагруженностью рекомендуется серый чугун следующего химического состава, мас. %: 3,0 – 3,2 С, 1,3 –1,5 Si, 0,6 – 0,8 Мn, 0,7 – 0,9 Сu, 0,3 – 0,7 Ni, 0,08 – 0,1 Тi, не более 0,12 S, не более 0,1 Р.
Для изготовления кокилей широко используют также низкоуглеродистые стали марок 10, 20, а также стали, легированные хромом и молибденом, например, сталь марки 15ХМЛ. Эти материалы обладают высокой пластичностью, поэтому хорошо сопротивляются растрескиванию при эксплуатации.
Кокили для мелких отливок из алюминиевых сплавов иногда изготавливают также из алюминиевых сплавов (АЛ9 и АЛ11). Такие кокили анодируют, в результате чего на их рабочей поверхности образуется тугоплавкая износостойкая пленка оксида алюминия толщиной до 0,4 мм, температура плавления которой составляет около 2000оС. Высокая теплопроводность стенок кокиля из алюминия способствует быстрому отводу теплоты от отливки. Эти кокили обычно делают водоохлаждаемыми.
Медь также часто используют для изготовления рабочих стенок водоохлаждаемых кокилей. Из меди делают отдельные вставки, вкладыши в местах, где необходимо ускорить отвод тепла от отливки и тем самым управлять процессом ее затвердевания.
Стержни простой конфигурации изготовляют из конструкционных углеродистых сталей, а стержни сложной конфигурации – из легированных сталей. Для прочих деталей – осей, валов, болтов и т.д. – используют конструкционные стали.
Стойкость кокилей и пути ее повышения. Данный показатель измеряется числом отливок требуемого качества, полученных в данном кокиле до выхода его из строя. Приблизительная стойкость кокилей приведена в таблице 3.1.
Таблица 3.1 – Приблизительная стойкость кокилей
Основной причиной разрушения кокиля являются сложные термохимические процессы в материале кокиля, вызываемые неравномерным циклическим нагревом и охлаждением его рабочей стенки во всех трех ее измерениях (по толщине, длине и ширине). Это приводит к появлению неоднородного, изменяющегося с изменением температуры поля напряжений в стенке кокиля, вызывающего ее упругие и пластические деформации. Для последних характерны остаточные деформации и напряжения. Теоретически показано, что в поверхностном слое кокиля нереализованная термическая деформация обычно в 2 раза превосходит деформацию, соответствующую пределу текучести материалов при определенной температуре. Поэтому в каждом цикле термического нагружения (заливка – удаление отливки) деформация сжатия сменяется дефор-мацией растяжения, что приводит к термической усталости материала кокиля. Термические напряжения возникают также вследствие структурных превращений и роста зерна материала кокиля, протекающих тем интенсивнее, чем выше температура его нагрева. Способность кокиля выдерживать термические напряжения зависит от механических свойств его материала при рабочих температурах кокиля. Эти свойства резко снижаются при нагреве. Например, предел текучести стали 15 при нагреве до температуры 600оС уменьшается приблизительно в 3 раза.
Уровень возникающих в кокиле напряжений зависит также от конструкции кокиля – толщины его стенки, конструкции ребер жесткости и т.д. Например, тонкие ребра жесткости большой высоты приводят к появлению трещин на рабочей поверхности кокиля, а низкие ребра могут не обеспечить жесткость кокиля и привести к короблению.
Стойкость кокилей обеспечивается конструктивными, технологическими и эксплуатационными методами.
Конструктивные методы основаны на правильном выборе материалов для кокилей в зависимости от преобладающего вида разрушения, разработке рациональной конструкции кокиля.
Термические напряжения, приводящие к снижению стойкости кокиля, являются следствием нереализованной термической деформации: менее нагретые части кокиля (слои рабочей стенки, прилегающие к внешней нерабочей поверхности, ребра жесткости) препятствуют расширению нагревающейся металлом отливки части кокиля. Уменьшить напряжения можно, если термическая деформация нагретой части происходит беспрепятственно. Этого можно достичь, если расчленить рабочую стенку кокиля на отдельные элементы в продольном или поперечном направлениях. Тогда вследствие зазоров между элементами кокиля каждый из них при нагреве расширяется свободно.
Для повышения стойкости кокилей используют сменные вставки, оформляющие рабочую полость кокиля. Благодаря зазорам между корпусом и вставкой, термическая деформация вставки протекает свободно, возникающие в ней напряжения снижаются, стойкость кокиля возрастает. Наиболее эффективно использование сменных вставок в многоместных кокилях.
Технологические методы направлены на повышение стойкости поверхностного слоя рабочей полости, имеющего наибольшую температуру при работе кокиля. Для этого используют поверхностное легирование, алитирование, силицирование, термическую обработку различных видов, наплавку, напыление на рабочую поверхность материалов, повышающих стойкость кокиля. Каждый из этих способов предназначен для повышения стойкости кокиля к разрушениям определенного вида.
Рисунок 3.4 – Зависимость стойкости кокиля kзал от темпа работы m
Таблица 3.2 – Температура нагрева кокилей перед заливкой
uas.su