Легированный чугун: марки, свойства и применение. Коррозионностойкий чугун марки
Коррозионно-стойкие чугуны
Высокой коррозионной стойкостью при температуре до 200 °С и воздействии концентрированных кислот, растворов щелочей и солей, кроме фтористоводородной кислоты и фтористых соединений, обладают ферросилиды марок ЧС13, ЧС15 и ЧС17.
Опыт изготовления из этих сплавов простых по конфигурации деталей центробежных и поршневых насосов, компрессоров и трубопроводной арматуры, а также деталей трубопроводов для перекачки агрессивных сред и теплообменников и использования их на химических предприятиях показывает, что ферросилиды являются эффективными конструкционными материалами. Особо высокой коррозионной стойкостью в серной, соляной и азотной кислотах, водных растворах щелочей и солей при местных перепадах температур в теле литых деталей до 30 °С, при отсутствии динамических и пульсирующих нагрузок обладают легированные молибденом ферросилиды марок ЧС15М4 и ЧС17МЗ.
Детали из ферросилида в ряде случаев обладают более высокой коррозионной стойкостью, чем чугуны марок ЧН20Д2ХШ и ЧН19ХЗШ, используемые в нефтедобывающей и нефтеперерабатывающей промышленности и для изготовления немагнитных деталей.
Ферросилиды и другие высококремистые сплавы железа в литом состоянии отличаются высокой коррозионной стойкостью, но имеют низкие показатели временного сопротивления и пластичности. Низкая вязкость допускает применение ферросилида, содержащего 0,5…1,5 % углерода, 12…18 % кремния и 0,3…1,5 % марганца, лишь в тех случаях, когда отливки подвергаются только статическим нагрузкам. Ударная вязкость ферросилидов снижается с повышением содержания в отливках кремния, в частности с 0,055 Дж/мм2 при 10 % кремния и до 0,02 Дж/мм2 при 15 % кремния.
В отливках из нелегированных ферросилидов отмечается большое количество силицидов железа (Fe3Si2), являющихся хрупкими составляющими структуры. Линейная усадка сплавов колебалась от 1,7 до 2,3 %. Могут иметь место газовая пористость и газовые раковины. Форма графита — преимущественно пластинчатая. Плотность отливок – 6500…7000 кг/м3. Структура, полученная после модифицирования такого расплава 0,02…0,08 % магния или РЗМ, измельчается, а графит приобретает сфероидизированную форму. Дополнительная присадка молибдена, никеля и сурьмы в количестве 0,2… 1,2 % упрочняет матрицу, благоприятно влияет на форму силицидов, увеличивает плотность сплава и способствует повышению пластичности сплавов в отливках. При комплексном модифицировании ферросилидов хромом и сурьмой (в количестве 0,78 и 0,12 % соответственно), молибденом и бором, титаном и медью в структуре обнаруживаются сложные карбиды, обеспечивающие повышение эксплуатационной стойкости в условиях гидроабразивного изнашивания. Изменение формы хрупкой фазы — силицидов и связывание их в компактные сложные карбиды повышают механические характеристики чугуна: временное сопротивление, пластичность, твердость и износостойкость. Установлена также высокая коррозионная стойкость ферросилидов с компактными сложными карбидами, которую они проявляют в сильноагрессивных жидких средах.
Поскольку для ряда областей техники не разработаны конструкционные материалы, которые успешно могут заменить ферросилид, использование комплексного модифицирования может быть рекомендовано в качестве меры, обеспечивающей на 30…50 % повышение прочностных и пластических свойств. После длительной выдержки легированного ферросилида в 23…37 %-ном растворе соляной кислоты скорость коррозии составляет 0,12…4,30 г/м2 в сутки, в то время как скорость коррозии нелегированного ферросилида в таких средах составляет 5,16…8,42 г/м2.
Повышение структурной однородности ферросилидов, содержащих 12 — 17 % кремния, в результате получения компактных сложных карбидов и сферодизированного графита в литых изделиях — эффективный способ увеличения гидроабразивной и коррозионной стойкости рабочих колес, улиток, крыльчаток и других массовых деталей насосов, используемых в химической промышленности.
Можно предположить, что упрочение и повышение износостойкости этого сплава связаны с легированием твердого раствора — кремнистого феррита, измельчением структурных составляющих и изменением характера выделений графита.
В стандартных сплавах ферросилида кремнистый феррит имеет микротвердость 6150…6210 МПа, а при использовании комплексного легирования молибденом, медью и никелем микротвердость феррита повышается до 7270…8390 МПа. При этом значительно повышается стойкость отливок в условиях газоабразивного износа и в агрессивных средах.
Сплавы, легированные 2,7…3,5 % никеля и 0,7…1,3 % молибдена, имеют высокую стойкость в газоабразивных средах с температурой 550 — 800 °С, а коррозионная стойкость сплава С15НЗМД в контрольных агрессивных средах соответствовала 4-6-му баллу по ГОСТ 13819-68. Высокую коррозионную стойкость этого сплава можно объяснить повышенной плотностью, измельченным литым зерном и мелкодисперсными включениями графита.
В таблице приведены данные о физико-механических и эксплуатационных свойствах легированных ферросилидов, рекомендованных для износостойких и коррозионно-стойких отливок. Недостатком этих сплавов является низкая динамическая прочность, поэтому для повышения надежности отливок может быть использовано армирование. Для арматуры используют стали, которые хорошо силицируются.
Физико-механические свойства ферросилидов (кремнистых чугунов)
Марка чугуна | Временное сопротивление, МПа | Ударнаявязкость, МДж/м2 | Интенсивность газоабразивного износа при 800 °С, мг/(м2гс) | Потеря массы при кавитационном износе, мг | Коррозионная стойкость, баллы |
ЧС15Д | 120…140 | 0,030…0,035 | 5,1…5,7 | 43…48 | 5…6 |
ЧС15ДЗМ | 135…155 | 0,037…0,042 | 3,8…4,5 | 32…37 | 4…5 |
ЧС15НЗМД | 150…170 | 0,042…0,047 | 3,0…3,6 | 22…25 | 4 |
ЧС15НЗД2М | 155…175 | 0,045…0,050 | 2,8…3,4 | 19…23 | 4 |
Также Вам будет интересно:
chiefengineer.ru
Коррозионностойкие чугуны - Справочник химика 21
Химический состав и механические свойства низколегированного коррозионностойкого чугуна (ГОСТ 11849—66) [c.60]Коррозионностойкие чугунные трубы покрывают слоем толщиной около 0,07 мм, получаемым методом погружения. Если прокладка труб ведется в грунтах с высокой коррозионной активностью, то применяют усиленные покрытия, толщина которых может составлять от 0,1 до 0,15 мм. Для защиты чугунных труб, прокладываемых в особо агрессивных грунтах, применяют также цинкование и покрытия из пластмасс. [c.137]
Глава XVI. КОРРОЗИОННОСТОЙКИЕ ЧУГУНЫ [c.238]
Коррозионностойкие чугуны можно разделить на два класса серые чугуны с феррито-графитовой или аустенито-графитовой структурой и белые чугуны со структурой феррита. Важное значение имеет форма распределения углерода. В серых чугунах углерод находится в виде графита пластинчатого, чешуйчатого, глобулярного или шаровидного. Наибольшей коррозионной стойкостью в растворах электролитов обладают модифицированные чугуны с шаровидным графитом. В белых чугунах углерод находится в форме карбидов. [c.70]
Из белых коррозионностойких чугунов имеют применение высокохромистые чугуны (0,5—2,0 % С, 0,5—2,5 % 51, 8—30 % Сг) как жаростойкие и кислотостойкие материалы. Коррозионная стойкость обеспечивается аустенитной основой, содержание хрома в которой должно быть не менее 12—13 %. [c.71]
К коррозионностойким чугунам относят также высокохромистые чугуны, которые содержат 25-35 % Сг, 1-2 % С, до 20 % Si. Иногда для улучшения коррозион- [c.59]
Жаростойкий и коррозионностойкий чугун [c.51]
ОтлиВ(Ки из серого чугуна (ГОСТ 1412—70) применяются для изготовления крышек, опор и других деталей аппаратов и машин при давлении среды в них не более 1,0 МПа и температуре среды от —15 до +250° С. Отливки из коррозионностойкого чугуна (ОСТ 43-108 Главхиммаш) применяются для изготовления деталей, работающих в растворах щелочей при давлении не более 1,0 МПа и температуре от —15 до -1-300°С. Для деталей, работающих в среде печных или гене раторных газов, а также в коррозионных средах при повышенных температурах (до 500- 600°С), могут применяться отливки из жаростойкого и коррозионностойкого чугуна (ГОСТ 7769—63 и ГОСТ 11849—66). [c.48]
Жаростойкий и коррозионностойкий чугун ЧН15Д7Х2 (ГОСТ 11849—85) применяют при изготовлении узлов и деталей, работающих при температурах от+100 до +600 С и агрессивных средах. [c.66]
Большое значение в качестве материалов хрупких мембран имеют легированные чугуны, обладающие высокой химической стойкостью к кислотам, щелочам и другим агрессивным средам. Коррозионностойкие чугуны Ф15 и Ф17 стойки, например, в серной кислоте, а также в азотной кислоте до температуры ее кипения, в сухом и влажном хлоре, сероуглероде, синильной кислоте, в растворах хлористого аммония, альдегидах и водороде. Низколегированные чугуны типа СЧЩ-1 и СЧЩ-2 очень стойки в щелочах. Чугуны с аустенит-ной структурой типа нирезист, высоколегированные никелем, например чугун ЖЧНДХ 15-7-2, могут успешно применяться для предохранительных мембран, работающих в растворах и жидкостях, нагретых до 400° С. [c.107]
В пром-сти выплавляют также легир. чугуны со спец. физ.-хим. св-вами, иапр. коррозионностойкие чугуны, легированные N1 и Си кислотоутюрные и щелочеупорные, легированные Сг и N1 жаростойкие, легированные А1, 51, Мо антифрикционные, легированные 51, Мп, Сг и Си. Получают обычно легир. чугуны спец. доводками в ковше, электропечах и вагранках (термич. обработка, добавление ферросплавов и др.). [c.133]
При изготовлении деталей химических аппаратов широко применяются низколегированные, высококремнистые (ферросилиды), кремнемолибденовые (анти-хлоры), аустенитные (нирезист и никросилал), высокохромистые чугуны. Они в основном подвержены электрохимической коррозии. Чугуны, содержащие в больших количествах связанный углерод, являются более коррозионностойкими. Чугун с шаровидной формой графита является более коррозионнрстой-ким и износостойким, чем чугун с пластинчатым графитом [85, 123]. [c.59]
В отечественной практике наибольшее распространение получили низколегированные коррозионностойкие чугуны. марок ЧНХТ, ЧНШШ, ЧН1ХМД (табл. 24). предназначенные для эксплуатации при повышенных температурах и газовых средах, и щелочестойкие чугуны марки СЧЩ 1 и СЧЩ 2 (табл. 25), коррозионная стойкость которых в расплавленных щелочах натрия, калия и их водных растворах приведена в табл. 26 [88, 118]. [c.59]
Из-за высоких механических свойств, хорошей плотности, износостойкости эти чугуны применяют для изготовления деталей центробежных насосов, вентиляторов, тройников, роликов барабанных вакуум-фильтров, мешалок оборудования с перемешивающими устройствами и др. НИИхиммашем разработан высокохромистый износо- и коррозионностойкий чугун марки ЧХ12Н7Р2, применяемый для изготовления втулок червячно-отжимных прессов, грязевых насосов, отделочных вальцов бумагоделательных машин и других деталей, работающих в условиях повышенных температур (400—500° С). В химическом машиностроении также применяется чугун марки ИЧХ16МЗ. [c.65]
НОИ структурами, получаемыми изотермической зака.гкой,— наиболее высокой усталостной прочностью (табл. 2). Св-ва чугунов в значительной мере определяются хим. составом, технологией получения, условиями охлаждения, наличием легирующих элементов и др. По циклической вязкости чугун с шаровидным графитом занимает промежуточное положение между серым чугуном и сталью. В. ч. в зависимости от структуры относятся к износостойким чугунам или коррозионностойким чугунам. Сопротивление коррозионному разрушению В. ч. выше, чем сопротивление серого чугуна с пластинчатым графитом. Нелегированные перлитные чугуны характеризуются меньшей коррозионной стойкостью, чем ферритные. Увеличение содержания кремния (особенно нри одновременном легирова- [c.228]
Коррозионпостойкие чугуны иснользуют в хим. и нефтехим. нром-сти. Из них изготовляют детали двигателей и узлов, эксплуатируемых в нагретых кислотах, влажном паре и морской воде (см. также Коррозионностойкий чугун). К жаропрочным чугунам относятся чугуны, легированные преим. никелем, хромом, [c.688]
Компоненты Тип 1 (15% никеля) Тип 2 (20% никеля) Тип 3 (30% никеля) Тип 4 (жаро- и коррозионностойкий чугун 30-5-5) Тип 5 (миновар) [c.149]
Из легированных чугунов остальных типов следует упомянуть чугаль — алюминиевый чугун, обладающий высокой окалиностойкостью и повышенной прочностью при высоких температурах, а также коррозионностойкие чугуны нирезист и никросилал, распространенные за рубежом. В табл. 13 приводится химический состав легированных чугунов иностранных марок. [c.38]
Жаростойкий и коррозионностойкий чугун ЧН15Д7Х2 (ГОСТ 11849—66) применяют для изготовления деталей, работающих при повышенных температурах (от +100 До +600° С) в агрессивных средах. [c.23]
chem21.info
Сравнительные данные по скорости коррозии: нержавеющий чугун, обыкновенный серый чугун, углеродистая сталь, нержавеющая стальИмейте в виду, что ржавчина сама по себе замедляет скорость коррозии - поэтому, чем толще, тем лучше :) Таблица 1. Сравнительные данные по скорости коррозии чугуна и стали в растворах солей и щелочей.
Таблица 2. Сравнительные данные по скорости коррозии чугуна и стали в кислотах
Таблица 3. Сравнительные данные по скорости коррозии чугуна и стали в воде.
|
www.dpva.ru
Легированный чугун: марки, свойства и применение
Легированный чугун - это материал, который производится методом плавки в доменных печах. В нем может находиться разное количество углерода. В зависимости от количественного содержания этого вещества, выделяют два вида чугуна. Первый называют передельным, или белым, а второй - серым, или литейным.
Описание видов чугуна
Первый тип - это передельный чугун. Так называется материал, в котором углерод представлен в виде такого вещества, как цементит. В изломе он имеет белый цвет, откуда и пошло его название. Характеризуется такой чугун высокой твердостью и хрупкостью. Он очень плохо поддается механической обработке. При этом около 80 % всего выплавляемого чугуна является белым. Основное предназначение этого типа материала - это дальнейшая переплавка в сталь.
Серый легированный чугун - это металл, в котором углерод представлен в виде пластичного графита. В изломе его цвет - серый, что также определило его название. Хрупкость и твердость такого чугуна меньше, чем у белого, но при этом он намного лучше поддается механической обработке.
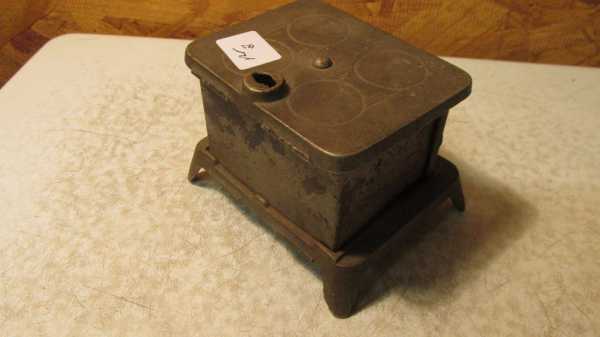
Свойства легированного чугуна этого типа состоят в следующем:
- Во-первых, он отлично сопротивляется нагрузкам сжимающего типа.
- Во-вторых, этот металл нечувствителен к дефектам поверхностного типа, а также отличается тем, что неплохо противостоит усталостному разрушению.
Однако литейный легированный чугун обладает достаточно слабой ударной вязкостью, а также низкой пластичностью. Из-за этих двух недостатков применять такой материал в конструкционных целях достаточно сложно.
Общее описание марок серого чугуна
На сегодняшний день существуют такие марки легированного чугуна серого типа: СЧ 10, СЧ 15, СЧ 18, СЧ 20 и еще несколько других. Буквы СЧ в маркировке обозначают, что это именно серый чугун, а следующие две цифры указывают на предельную нагрузку, которую может выдержать металл при растяжении. Предел прочности в таком случае измеряется в МПа.
Разновидности серого чугуна
Литейный легированный чугун имеет несколько подтипов. Одним из них стал ковкий чугун. Такое условное название получил материал, который отличается тем, что он более мягкий и вязкий, чем серый. Получают его из белого чугуна. Для этого используют процедуру отжига, которая длится достаточно долго. Маркировка здесь примерно такая же, к примеру КЧ 30-6, КЧ 33-8, КЧ 37-12. Буквы указывают на то, что этот чугун ковкий, а следующие две цифры определяют предел прочности на растяжение. А вот что касается последней одной или двух цифр, то они характеризуют максимальное относительное удлинение, которое измеряется в процентах.
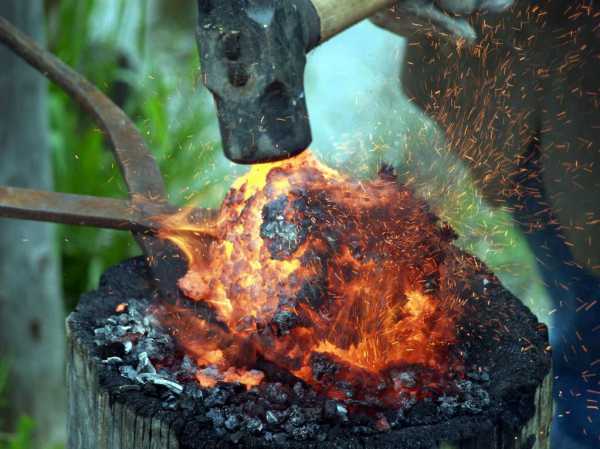
Еще один подтип литейного легированного чугуна - модифицированный. Для того чтобы его получить, необходимо добавить к серому специальные элементы. Добавляются такие модификаторы до разливки вещества. В качестве добавок могут использовать алюминий, кремний, кальций и другие. Эти присадки значительно увеличивают количество центров кристаллизации. Другими словами, они способствуют значительному измельчению графита.
Благодаря таким добавкам специальный легированный чугун отличается более высокими прочностными характеристиками, меньшей хрупкостью, повышенной стойкостью к образованию трещин. Стоит добавить, что все лучшие сорта этого сплава получают именно из такого модифицированного материала.
Виды легированного сплава
Что означает легированный чугун? Легирование - это операция по введению в состав материала различных примесей, которые способны улучшить его характеристики. Для чугуна такими добавками стали титан, хром, ванадий и другие. Введение в состав легирующих элементов может увеличить такие характеристики, как прочность, твердость, износостойкость, стойкость к коррозии и множество других.
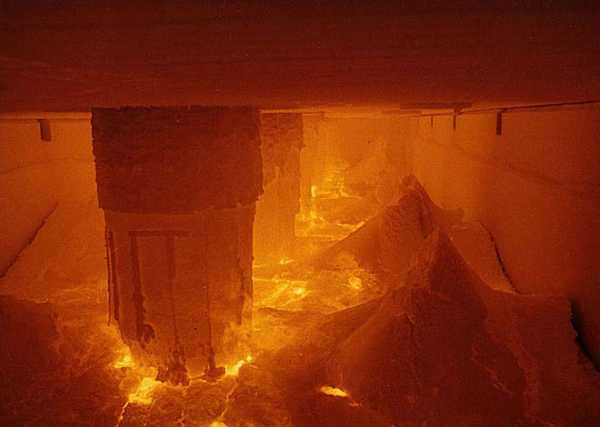
На сегодняшний день, в зависимости от количества легирующих элементов чугуна, можно выделить три его типа:
- Если присадки содержатся в количестве до 2,5 % от всей массы, то это низколегированный чугун.
- Среднелегированными называют те материалы, содержание веществ в которых находится в пределах от 2,5 до 10 %.
- Последний тип - высоколегированные, если содержание модификаторов суммарно превышает 10 %.
Вещества для легирования, маркировка
По ГОСТу легированный чугун должен содержать определенное количество веществ для использования в определенной сфере. Кроме того, маркировка также является стандартной. К примеру, ЧН15Д7Х - это высокопрочный сплав, в котором содержится 15 % никеля, 7 % меди и примерно 1 % хрома. Как можно заметить, в маркировке легирующие элементы отмечаются одной буквой, после которой идет цифра, указывающая на количественное содержание добавки. Однако может быть и так, что цифра отсутствует, как после хрома. Это означает, что содержание вещества в составе - около 1 %.
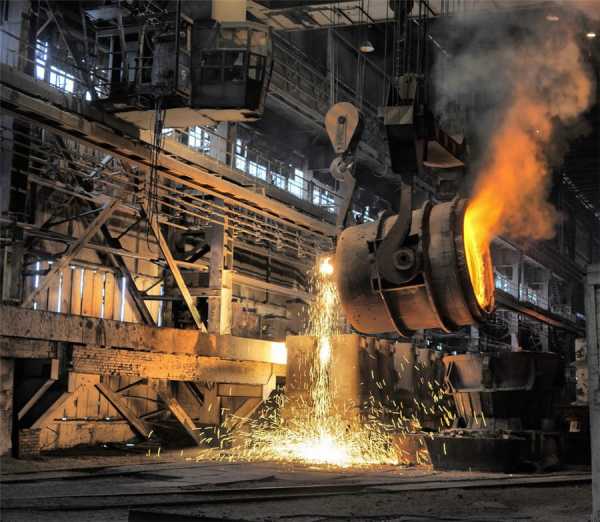
Что касается изготовления такого чугуна, то обходится оно достаточно недорого. При этом конечный продукт обладает достаточно высокими эксплуатационными свойствами. Благодаря этим двум факторам область применения описываемого материала постоянно увеличивается.
Виды легированного сплава
Естественно, что добавление в состав какого-либо вещества будет увеличивать какую-либо определенную характеристику. Поэтому различают несколько классов легированных материалов.
Так, чугун может быть износостойким. Материал, относящийся к этой группе, отличается тем, что у него повышенная сопротивляемость к истиранию, которое возникает во время трения поверхности. К этой категории можно отнести антифрикционный и фрикционный чугун. Первый из названных отличается очень низким коэффициентом трения. Благодаря этому основное применение легированного чугуна названного вида - это производство таких деталей, как подшипники скольжения, вкладыши для них и прочие детали со схожими требованиями.
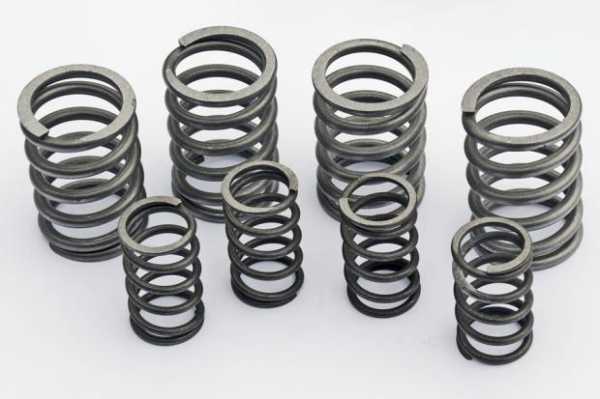
Фрикционный же материал, наоборот, характеризуется достаточно высоким коэффициентом трения, а потому чаще всего он применяется в производстве тормозных устройств для самых разных механизмов, оборудования и т. д.
Нержавеющий чугун
Многие знают о том, что существует металл, который называют нержавеющим. На самом деле, это не совсем точное определение. Просто такие сплавы отличаются тем, что стойкость к коррозии у них достаточно высокая. Наибольшее распространение названный чугун получил в кораблестроении. Если ввести в состав железа более 12 % хрома в качестве легирующего элемента и максимально снизить содержание углерода, то в результате получится именно такой сплав.
Наиболее распространенными его марками стали ЧНХТ, ЧН1ХМД, ЧН15Д7Х2. Они отличаются тем, что сохраняют высокую стойкость к коррозии даже в условиях агрессивной окружающей среды, имеют хорошую сопротивляемость к кавитации и износу в пароводяной среде.
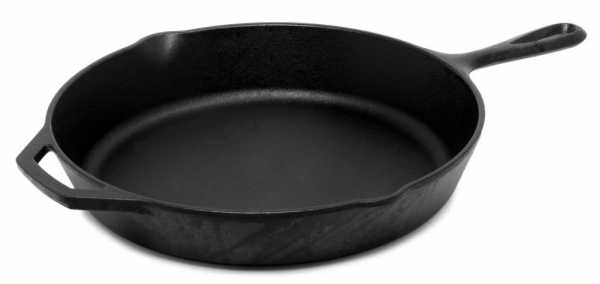
Небольшой, но все же довольно востребованной группой является жаропрочный чугун. Основное преимущество материала заключается в том, что он достаточно плохо поддается окислению, а также отлично сохраняет свои качества в условиях повышенных температур.
Введение меди
В настоящее время все чаще и чаще начинают применять чугун с добавлением меди. Внедрение этой добавки в сплав значительно улучшает его литейные качества. Лучше всего это сказывается на жидкотекучести материала. Кроме этого, значительно уменьшается склонность к появлению трещин и усадочной пористости.
Внедрение 0,5 % Cu (меди) делает чугун достаточно пригодным, чтобы отливать из него такие детали, у которых толщина стенок будет составлять от 10 до 25 мм. Если необходимо увеличить толщину стенок у будущих элементов, то придется повышать и количественное содержание меди, а также ее комплексов. Тут стоит отметить, что эффект от добавления меди можно усилить, если в сплав ввести такие элементы, как сурьма или висмут.
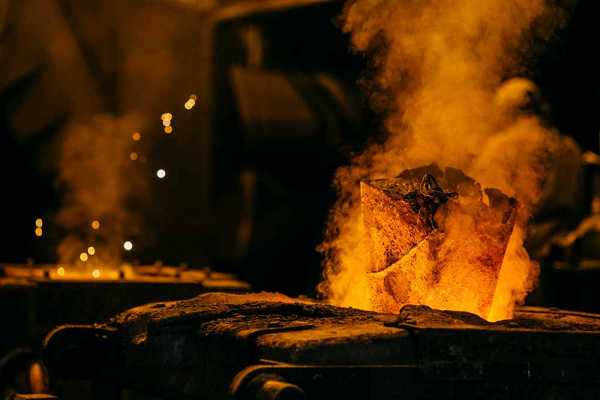
Если же углеродный эквивалент будет увеличиваться, то влияние меди на кристаллизацию графита уменьшается. Легирование чугуна медью может также предотвратить отбеливание в поверхностных слоях, а также значительно повышает твердость к середине. Это довольно заметно при выплавке гильз цилиндров, головок блоков из чугуна и других элементов.
Комплексно-легированный чугун
Для того чтобы успешно выплавлять чугун, который можно использовать для отливки гильз цилиндров, необходимо использовать не только разнообразные ферросплавы, но и индукционную печь. Чтобы осуществлять отливку таких деталей, используется марка ИЧХН4, ЧН1ХМД и ЧНМШ и несколько других типов. Отличительная их особенность заключается в том, что выплавка всех деталей осуществляется в тонкостенный или массивный кокиль.
Игольчатая структура и высокопрочный материал
Небольшая разновидность серого чугуна, который принадлежит к группе износостойких, - это материал с игольчатой структурой. Степень легирования у такого материала достаточно низкая. Содержание в нем кремния и углерода также достаточно низкое. В данном случае количественное содержание таких веществ, как медь, молибден, никель и некоторых других модификаторов, увеличивается в зависимости от требуемой в результате толщины стенок, а также в зависимости от способа литья, который будет использоваться.
Еще одна разновидность - это высокопрочный материал. Это небольшая разновидность серого чугуна, который отличается содержанием шаровидного графита. Для того чтобы получить такую структуру, в сплав необходимо ввести магний, церий и висмут. Добавление именно этих трех легирующих элементов превращает пластичный графит литейного материала в шаровидный. Отличается такой вид тем, что его механические качества значительно выше, чем у других типов чугуна. На сегодняшний день выпускается примерно 10 разнообразных марок сплава названной категории. Такой материал можно отлично использовать в судостроении вместо ковкого типа. А наиболее распространенным видом высокопрочного чугуна является магниевый (с большим количеством магния в составе).
fb.ru
Коррозионная стойкость чугуна
Коррозионное разрушение чугуна вызывается электрохимическими, реже, чисто химическими процессами. Коррозия может быть равномерной, местной, межкристаллитной избирательной.
В общем случае коррозия оценивается обычно как скорость уменьшения массы материала и выражается в г/(м2∗ч) или в мм/год. В зависимости от этих потерь различают классы стойкости при коррозии в сильно- и среднеагрессивных средах (табл. 1).
г/(м2∗q) | мм/год | ||
1 | Вполне стойкие | <0,1 | <0,12 |
2 | Достаточно стойкие | 0,1-1,0 | 0,12-1,2 |
3 | Относительно стойкие | 1,0-3,0 | 1,2-3,6 |
4 | Малостойкие | 3,0-10,0 | 3,6-12,0 |
5 | Нестойкие | >10,0 | >12,0 |
Сопротивление коррозии зависит как от особенностей металла, так и от внешних факторов — состава и температуры среды, доступа кислорода, движения раствора или газа относительно металла. В частности, повышение температуры и скорости движения среды увеличивает скорость коррозии.
К факторам, связанным с особенностями металла, относятся структура, химический состав, шлаковые и газовые включения, напряжения н состояние поверхности.
По сопротивлению коррознн серые чугуны с пластинчатым и шаровидным графитом в различных средах могут быть отнесены к различным классам стойкости (табл. 2), В сравнительно чистом и сухом воздухе эти чугуны весьма стойки благодаря образованию пассивирующей пленки (скорость коррозии ~0,025 мм/год). Коррозия начинает возрастать при загрязнении атмосферы, главным образом сернистыми газами. При этом состав и тип чугуна, в частности форма графита и характер матрицы, оказывают сравнительно небольшое влияние. Единственным элементом, полезным в этих условиях, является медь.
Роль состава и структуры чугуна также не очень велика при коррозии в природных, промышленных, лечебных и морских водах, хотя чугун марок ВЧ, особенно перлитный, обладает более высокой коррозионной стойкостью в морской воде, чем чугун марок СЧ. Главное влияние в этих условиях, как и при атмосферной коррозии, оказывают состав среды и плотность отливок. Растворы солей, гидраты которых придают воде кислотный характер, значительно ускоряю коррозию, а соли, дающие при гидролизе щелочные растворы, замедляю коррозионный процесс.
В условиях подземной коррозии существенное влияние оказывают так факторы, как состав и электрическое сопротивление почвы, характер контакта, наличие блуждающих токов и др. В частности, с увеличением электрического сопротивления почвы с 100—200 до 20 000 Ом∗см скорость коррозии уменьшается в 3 раза. Несколько большее сопротивление коррозии в почве оказывают чугуны марок КЧ и ВЧ, особенно в агрессивной среде.
Белый | — | — | — | 0,045 | — | — | — | — | — |
Серый | 0,141 | 0,242 | 0,267 | 0,03-0,09 | 0,0185 | 0,084 | 30,7 | 26,7 | 25,8 |
Высокопрочный: | |||||||||
ферритный | 0,181 | 0,285 | 0,216 | 0,025-0,105 | 0,01 | 0,077 | — | — | — |
ферритно-перлитный | 0,181 | 0,235 | 0,257 | — | — | 0,083 | — | — | — |
перлитный | 0,141 | 0,220 | 0,285 | 0,05-0,07 | 0,012 | 0,084 | — | — | — |
Ковкий | — | — | — | 0,045-0,08 | — | — | — | — | — |
Коррозионно-стойкий типа неризист 4Н15Д7 | — | — | 0,049 | 0,02 | — | — | 0,152 | 0,3 | 21,3 |
Кремнистый типа ЧС15, ЧС15МЧ | — | — | — | — | — | — | 0,125 | 0,125 | — |
*1 При испытании в проточной морской воде скорость коррозии превышает аналогичные данные в простой воде. Скорость коррозии 1 г/(м2∗ч) = 1,2мм/год |
В общем случае для этих чугунов коррозионная стойкость повышается по мере измельчения графита и уменьшения его количества, при однофазной структуре матрицы, а также при уменьшении содержания Si, S, Р. Повышают сопротивление коррозии модифицирование, а также легирование Сu (до 1,4%), Ni (до 3,0%), Сr (до 1,0%). Для работы в щелочной среде рекомендуются чугуны, содержащие 0,8—1,0% Ni и 0,6—0,8% Сr или 0,35—0,5% Ni и 0,4—0,6% Сr.
Однако при воздействии на металл сильных реагентов, кислот и щелочей следует применять высоколегированные чугуны. В этих случаях основное значение приобретает химический состав чугуна. Роль структуры, особенно формы выделения графита, значительно меньше. При прочих равных условиях наилучшими являются аустенитная или ферритная структура. Компактный или пластинчатый графит мало различаются по своему влиянию, если последний разобщен, сравнительно невелик и равномерно распределен.
Повышение сопротивления чугуна коррозии в агрессивных средах достигается легированием элементами, которые обладают высоким потенциалом (Cu, Ni, Мо) и являются более устойчивыми, либо способны образовать защитные пассивирующие пленки (Сг, Si, А1) в гой или иной среде, либо обладают обоими этими свойавами.
Химическая стойкость чугуна в кислотах резко увеличивается при содержании кремния ~1,5%. Сплавы ЧС15, ЧС17 стойки в азотной, фосфорной, уксусной и, что особенно важно, в серной кислоте при любых концентрациях и температуре и в смеси HN03 и h3S04. Ферросилиды стойки также в растворах солей, но легко корродируют под воздействием соляной кислоты, крепких щелочей и фтористых соединений. Для повышения стойкости в кислоте НСl сплавы легируют до 4,0% Мо (ЧС15М4, ЧС17МЗ). Эти сплавы известны под названием антихлор. Антихлор устойчив в соляной кислоте любой концен. трации при всех температурах, в азотной кислоте любой концентрации, в лимонной, пикриновой, серной и фосфорной кислотах, перекиси водорода четыреххлористом углероде, железно) купоросе. Недостатком этих сплавов является большая хрупкость, плохая обрабатываемость и низкие механические свойства. Поэтому применяют ферросилиды только в условиях, когда необходима низкая скорость коррозии, не выше 0,25 мм/год.
В условиях воздействия щелочей используют обычно чугуны, легированные никелем (хромом). Наилучшие результаты достигаются при использовании высоколегированных чугунов типа неризист (например, ЧН15Д7Х2). Эти чугуны стойки также в холодных разбавленных растворах серной кислоты. В соляной кислоте чугун этого типа менее стоек, а в азотной — нестоек (см. табл. 2).
При большом содержании хрома (12—35%) чугун оказывается химически стойким во многих средах, кислотах, щелочах, солях и особенно в азотной кислоте благодаря образованию оксидной пассивирующей пленки. В соляной кислоте оксидная пленка на этих сплавах разрушается вследствие воздействия хлоридов.
metiz-bearing.ru
Коррозионно-стойкий чугун с шаровидным графитом
Изобретение относится к литейному производству, в частности к составам коррозионностойких чугунов с шаровидным графитом. Может использоваться для производства рабочих органов грунтовых и песковых насосов и гидромашин, перекачивающих абразивные пульпы, смеси и суспензии. Коррозионностойкий чугун с шаровидным графитом содержит, мас.%: углерод 3,2-4,0; кремний 1,5-3,0; марганец 0,8-3,5; хром 7,0-10,0; никель 2,0-4,0; бор 0,2-0,4; ванадий 0,4-1,0; молибден 0,1-0,5; титан 0,1-0,4; алюминий 0,05-0,2; церий 0,03-0,2; магний 0,02-0,1; кальций 0,05-0,2; железо - остальное. Чугун обладает повышенной устойчивостью к воздействию коррозионно-абразивных сред. 2 табл.
Изобретение относится к литейному производству, а именно к изысканию коррозионностойкого чугуна с шаровидным графитом для производства деталей, предназначенных для работы в условиях гидроабразивного износа, в частности для изготовления рабочих органов грунтовых и песковых насосов и гидромашин, перекачивающих абразивные пульпы, суспензии и смеси.
Известен износостойкий чугун, содержащий, мас.%: углерод 3,0-3,7; кремний 0,5-3,0; марганец 0,2-1,5; хром 4,0-15,0; никель 4,0-8,0; фосфор до 0,4; сера до 0,15; железо остальное (см. патент США №2662011, кл.75-128, 1953). Недостатком этого чугуна является низкая концентрация растворенного хрома (до 6%) в его металлической основе. В связи с этим на поверхности изделий из него не образуется коррозионностойкая пассивирующая пленка. В результате чего он имеет низкую устойчивость к воздействию коррозионно-абразивных сред.
Известен хромоникелевый чугун с шаровидным графитом (см., например, описание к патенту РФ №2234553, С1, 7 С22С 37110, 2004 г), выбранный в качестве прототипа по содержанию входящих компонентов и имеющих следующий состав, мас.%: углерод 3,2-4,0; кремний 1,4-2,5; марганец 0,4-1,2; хром 7,0-10,0; никель 2,5-5,5; бор 0,2-0,4; ванадий 0,6-1,0; алюминий 0,05-0,15; церий 0,05-0,20; магний 0,3-0,12; кальций 0,05-0,20; железо остальное.
В металлической основе указанного хромоникелевого чугуна с шаровидным графитом концентрация растворенного хрома достигает 11,8%. Благодаря этому он приобретает первую границу устойчивого пассивного состояния. Однако максимальная коррозионная стойкость у Fe-C сплавов обеспечивается, когда их основа содержит более 12% хрома [1].
Задачей предложенного изобретения является увеличение концентрации растворенного хрома (более 12%) в металлической основе хромоникелевого чугуна с шаровидным графитом с целью повышения устойчивости изделий из него к воздействию коррозионно-абразивных сред.
Технический результат, достигаемый при реализации предложенного технического решения, состоит в повышении коррозионной стойкости чугуна при снижении его себестоимости, предназначенного для изготовления отливок сложной конфигурации, например колес рабочих насосов для перекачки абразивных смесей, пульп и суспензий.
Указанный технический результат обеспечивается тем, что в предложенном хромоникелевом чугуне с шаровидным графитом, содержащем: углерод, кремний, марганец, хром, никель, бор, ванадий, алюминий, церий, магний, кальций, железо, дополнительно введен молибден и титан при следующем соотношении компонентов, мас.%: углерод 3,2-4,0; кремний 1,5-3,0; марганец 0,8-3,5; хром 7,0-10,0; никель 2,0-4,0; бор 0,2-0,4; ванадий 0,4-1,0; молибден 0,1-0,5; титан 0,1-0,4; алюминий 0,05-0,2; церий 0,03-0,2; магний 0,02-0,1; кальций 0,05-0,2; железо остальное.
Введение в состав предложенного чугуна молибдена позволяет увеличить концентрацию растворенного хрома в его металлической основе за счет частичного замещения молибденом атомов хрома в карбидной фазе.
Введение молибдена менее 0,1% не обеспечивает повышение концентрации растворенного хрома в металлической основе; увеличение содержания молибдена свыше 0,4% вызывает выделение карбидов молибдена типа Мо2С, что не обеспечивает повышение концентрации хрома в металлической основе чугуна и, соответственно, его коррозионной стойкости.
Добавка в состав предложенного чугуна титана способствует увеличению концентрации растворенного хрома в его металлической основе за счет частичного замещения титаном атомов хрома в карбидной фазе.
Введение титана менее 0,1% не обеспечивает повышения концентрации растворенного хрома в металлической основе; увеличение содержания титана свыше 0,4% вызывает выделение карбидов титана TiC, что не обеспечивает повышение концентрации хрома металлической основе чугуна и, соответственно, его коррозионной стойкости.
Увеличение содержания марганца в чугуне позволяет повысить его концентрацию в аустените.
Введение марганца в количестве менее 0,8% не обеспечивает повышения достаточной концентрации марганца в аустените, что способствует частичному распаду аустенита при охлаждении в троостит, обладающему низкой коррозионной стойкостью. Это влечет за собой резкое снижение устойчивости хромоникелевого чугуна с шаровидным графитом к воздействию коррозионно-абразивных сред, вследствие чего срок службы изделий из него сокращается. Увеличение содержания марганца свыше 3,5% вызывает выделение карбидов марганца типа Мn3С, что повышает хрупкость чугуна и ухудшает обработку отливок резанием.
Уменьшение содержания никеля в чугуне позволяет понизить себестоимость изготовления литья.
Введение никеля в количестве менее 2,0% не обеспечивает достижения достаточной концентрации никеля в аустените, что способствует частичному распаду аустенита при охлаждении в коррозионно-неустойчивый троостит. Увеличение содержания никеля свыше 4,0% способствует повышению доли остаточного аустенита в металлической основе чугуна, в результате чего понижается его твердость.
Плавку чугуна проводят в индукционных или дуговых электропечах с использованием стандартных шихтовых материалов. Легирующие элементы - никель, молибден, хром и ванадий вводят в металлозавалку. После расплавления шихты и перегрева чугуна до 1450-1500°С на зеркало расплава вводят кремний и марганец в виде 75%-ного ферросилиция и 60%-ного ферромарганца. Затем присаживают алюминий и кальций (в виде 20%-ного силикокальция). Магний в составе сфероидизирующей присадки, а также церий, бор и титан в виде ферроцерия, ферробора и ферротитана вводят на дно разливочного ковша перед выпуском жидкого металла из печи.
В таблице 1 приведен химический состав известного и предложенного чугунов. В таблице 2 приведены их механические свойства и стойкость в агрессивно-абразивных средах.
Техническим результатом является, как видно из данных таблицы 2, более высокая концентрация хрома в металлической основе и, соответственно, более высокая коррозионная стойкость и износостойкость предлагаемого чугуна в сравнении с прототипом.
Временное сопротивление чугуна при изгибе (σизг) определяли на цилиндрических образцах (⌀30×340 мм) при расстоянии между центрами опор 300 мм (ГОСТ 27208-87).
Твердость по Роквеллу определяли на приборе ТК-2М по ГОСТ 9013-59.
Микрораспределение хрома в металлической основе чугуна изучали на микроанализаторе MS-46 «Cameca».
Коррозионную стойкость в сернокислотной среде определяли по потере массы образцов после испытания продолжительностью 75 часов по ГОСТ 5272-50.
Концентрация серной кислоты составляла 0,02%, а рН среды 4,5.
Износостойкость в условиях гидроабразивного изнашивания определяли методом чашечного шлифования на стенде конструкции ЦНИИТМАШ. В процессе испытания образцы (⌀10×110 мм) перемещаются в гидроабразивной пульпе, состоящей из абразива и воды при соотношении 2:1,3 (по объему). В качестве абразива использовали электрокорунд зернистостью 0,6-1,5 мм. Длительность испытания - 1,5 часа. Частота вращения диска составляла 500 об/мин-1 и контролировалась стробоскопическим тахометром, линейная скорость перемещения образца составляла 4,7 м/сек-1.
Применение предлагаемого хромоникелевого чугуна с шаровидным графитом для отливок, имеющих сложную конфигурацию, например колес рабочих насосов для перекачки абразивных смесей, пульп и суспензий, позволяет существенно (на 30-40%) увеличить срок службы деталей в эксплуатации при снижении себестоимости их изготовления на 20-30%.
Таблица 1 | ||||||||||||||
Чугун | № плавки | Содержание химических элементов, мас.% | ||||||||||||
С | Si | Mn | Cr | Ni | V | Mo | Ti | В | Се | Mg | Ca | Al | ||
Пред-лага-емый | 11 | 3,2 | 0,5 | 0,8 | 3,0 | 2,0 | 0,4 | 0,1 | 0,1 | 0,2 | 0,03 | 0,02 | 0,05 | 0,05 |
12 | 2,7 | 1,8 | 2,2 | 8,5 | 33,0 | 0,7 | 0,8 | 0,35 | 0,3 | 0,12 | 0,06 | 0,13 | 0,13 | |
13 | 4,0 | 3,0 | 3,5 | 10,0 | 4,0 | 1,0 | 0,5 | 0,4 | 0,4 | 0,2 | 0,1 | 0,2 | 0,2 | |
Прототип | 1 | 3,6 | 1,9 | 0,8 | 8,5 | 4,0 | 0,8 | - | - | 0,3 | 0,12 | 0,8 | 0,1 | 0,3 |
Таблица 2 | |||||
№ плавки | Содержание хрома в металлической основе, % | Прочность, МПа | Твердость, HRC | Скорость коррозии в сернокислой среде, г/м2·н | Коэффициент относительной износостойкости в условиях гидроабразивногоизноса |
11 | 12,2 | 905 | 62 | 0,44 | 6,8 |
12 | 12,8 | 910 | 63 | 0,41 | 7,0 |
13 | 13,4 | 902 | 64 | 0,38 | 7.2 |
1 | 11,8 | 900 | 62 | 0,55 | 6,4 |
Источники информации
1. Томашев Н.Ф., Чернова Г.Л. Коррозия и коррозионностойкие сплавы. М.: Металлургия, 1973. - 232.
Коррозионно-стойкий чугун с шаровидным графитом, содержащий углерод, кремний, марганец, хром, никель, бор, ванадий, алюминий, церий, магний, кальций и железо, отличающийся тем, что он дополнительно содержит молибден и титан при следующем соотношении компонентов, мас.%:
углерод | 3,2-4,0 |
кремний | 1,5-3,0 |
марганец | 0,8-3,5 |
хром | 7,0-10,0 |
никель | 2,0-4,0 |
бор | 0,2-0,4 |
ванадий | 0,4-1,0 |
молибден | 0,1-0,5 |
титан | 0,1-0,4 |
алюминий | 0,05-0,2 |
церий | 0,03-0,2 |
магний | 0,02-0,1 |
кальций | 0,05-0,2 |
железо | остальное |
www.findpatent.ru
Износостойкие (антифрикционные ) чугуны
Обозначают сочетанием букв АЧС, АЧК, АЧВ. Буквы С, К, В обозначают вид чугуна: серый, ковкий, высокопрочный. Цифра обозначает номер чугуна.
Для легирования антифрикционных чугунов применяют хром, никель, медь, титан.
Жаростойкие и жаропрочные чугуны
Обозначают набором заглавных букв русского алфавита и следующими за ними букв. Буква «Ч» - чугун.
Буква «Ш», стоящая в конце марки означает шаровидную форму графита. Остальные буквы означают легирующие элементы, а числа, слежующие за ними, соответствуют их процентному содержанию в чугуне.
Жаростойкте чугуны применяют для изготовления деталей контактных аппаратов химического оборудования, работающих в газовых средах при температуре 900-11000 С.
Коррозионностойкие чугуны
Короозионностойкие чугуны обладают высокой стойкостью в газовой, воздушной и щелочных средах.Их применяют для изготовления деталей узлов трения, работающих при повышенных температурах.
Примеры обозначения и расшифровки
1. СЧ15 – серый чугун, временное сопротивление при растяжении 150Мпа.
2. КЧ45-7 – ковкий чугун, временное сопротивление прирастяжении 450Мпа, относительное удлинение 7%.
3. ВЧ70 – высокопрочный чугун, временное сопротивление при растяжении 700 МПА
4. АЧВ – 2 – антифрикционный высокопрочный чугун, номер 2.
5. ЧН20Д2ХШ – жаропрочный высоколегированный чугун, содержащий никеля 20%, 2% меди, 1% хрома, остальное – железо, углерод, форма графита – шаровидная
6. ЧС17 – коррозионностойкий кремниевый чугун, содержащий 17% кремния, остальное –железо, углерод.
Стали
Сталь - сплав железа с углеродом, содержащий углерода не более 2,14 %, а также ряд других элементов.
Классификация
Для правильного прочтения марки необходимо учитывать ее место в классификации стали по химическому составу, назначению, качеству, степени раскисления
По химическому составу стали подразделяют на углеродистые и легированные.
Стали по назначению делят на конструкционные, инструментальные и стали специального назначения с особыми свойствами.
Стали по качеству классифицируют на стали обыкновенного качества, качественные, высококачественные и особо высококачественные.
Классификация по степени раскисления.Стали по степени раскисления классифицируют на спокойные, полуспокойные и кипящие.
Таблица 1. – Классификация сталей Стали. По химическому составу | |||
Углеродистые | Легированные | ||
низкоуглеродистые (до 0,25% С), среднеуглеродистые (0,25-0,6% С высокоуглеродистые (более 0,6% С). | низколегированную (с суммарным содержанием легирующих элементов до 2,5%), среднелегированную (от 2,5до 10%) и высоколегированную (свыше 10%). | ||
По назначению | |||
Инструментальные | Конструкционные | ||
По качеству (содержанию вредных примесей) | |||
обык-новенного качества содержат до 0,06% S и 0,07% Р, | качественные — до 0,035% S и 0,035% Р | высококачественные - не более 0,025% S и 0,025% Р, | особо высококачественные - не более 0,015% S и 0,025% Р. |
Конструкционные стали– стали, предназначенные для изготовления различных деталей, узлов механизмов и конструкций.
Инструментальные стали– стали, применяемые для обработки материалов резанием или давлением, а также для изготовления измерительного инструмента
Специальные стали— это высоколегированные (свыше 10%) стали, обладающие особыми свойствами - коррозионной стойкостью, жаро-стойкостью, жаропрочностью, износостойкостью и др.
Углеродистые стали
К углеродистым сталям относят стали, не содержащие специально введенные легирующие элементы.
Конструкционные углеродистые стали
Стали углеродистые обыкновенного качества (сталь с достаточно высоким содержанием вредных примесей S и P) обозначают согласно ГОСТ 380-94.
Эти наиболее широко распространенные стали поставляют в виде проката в нормализованном состоянии и применяют в машиностроении, строительстве и в других отраслях.
Углеродистые стали обыкновенного качества обозначают буквами Ст и цифрами от 0 до 6. Цифры—это условный номер марки. Чем больше число, тем больше содержание углерода, выше прочность и ниже пластичность.
Перед символом Ст. указывают группу гарантированных свойств: А, Б, В. Если указание о группе отсутствует, значит предполагается группа А. Например, СТ3; БСт4; ВСт2.
Сталь обыкновенного качества выпускается также с повышенным содержание марганца (0,8-1,1% Mn)/ В этом случае после номера марки добавляется буква Г. Например, БСТ3Гпс.
После номера марки стали указывают степень раскисления: кп - кипящая, пс - полуспокойная, сп - спокойная сталь. Например, ВСт3пс.
Примеры обозначения и расшифровки
1. БСТ2кп –сталь конструкционная углеродистая обыкновенного качества, группы Б, поставляемая с гарантированным химическим составом, номер 2, кипящая.
2. СТ5Гпс –сталь конструкционная обыкновенного качества , группы , поставляемая с гарантированными механическими свойствами, номер 5, содержание марганца до 1%, полуспокойная.
3. ВСт3сп- сталь конструкционная углеродистая обыкновенного качества, группы В, поставляемая с гарантированным химическим составом и механическими свойствами, номер 3, спокойная.
Обозначение углеродистых качественных конструкционных сталей
Качественная конструкционная сталь – сталь с заметно меньшим содержанием серы, фосфора и других вредных примесей. Обозначается согласно ГОСТ 1050-88.
Сталь маркируют двузначными числами, которые обозначают содержание углерода в сотых долях процента, и поставляют с гарантированными показателями химического состава и механических свойств. По степени раскисления сталь подразделяют на кипящую (кп), полуспокойную (пс), спокойную (без указания индекса). Буква Г в марках сталей указывает на повышенное содержание марганца (до 1%).
Примеры обозначения и расшифровки
1. Сталь 05кп –сталь конструкционная низкоуглеродистая, качественная, содержащая углерода 0,05%, кипящая.
2. Сталь 25 - сталь конструкционная низкоуглеродистая, качественная, содержащая углерода 0,25%, спокойная.
3. Сталь 60Г - сталь конструкционная среднеуглеродистая, качественная, содержащая углерода 0,6%, марганца 1%, спокойная.
Автоматные стали. Обозначение автоматных сталей
По ГОСТ 1414-75 эти стали маркируют буквой А и цифрами, показывающими среднее содержание углерода в сотых долях процента.
Применяют следующие марки автоматной стали: А12,А20, АЗО, А40Г. Из стали А12 готовят неответственные детали, из стали других марок — более ответственные детали, работающие при значительных напряжениях и повышенных давлениях. Сортамент автоматной стали предусматривает изготовление сортового проката в виде прутков круглого, квадратного и шестигранного сечений. Эти стали не применяют для изготовления сварных конструкций.
Котельные стали. Стали листовые для котлов и сосудов, работающих под давлением, применяют для изготовления паровых котлов, судовых топок, камер горения газовых турбин и других деталей. Они должны работать при переменных давлениях и температуре до 450"С. Кроме того, котельная сталь должна хорошо свариваться. Для получения таких свойств в углеродистую сталь вводят технологическую добавку (титан) и дополнительно раскисляют ее алюминием. Выпускают следующие марки углеродистой котельной стали 12К, 15К, 16К, 18K.20K.22Kc содержанием в них углерода от 0,08 до 0,28%. Эти стали поставляют в виде листов с толщиной до 200 мм и поковок в состоянии после нормализации и отпуска.
Примеры обозначения и расшифровка
АС12ХН – сталь автоматная легированная, низкоуглеродистая, содержащая 0,12 % углерода, 1% хрома и никеля.
Инструментальные углеродистые стали
Обозначение инструментальных углеродистых сталей
Инструментальный углеродистые стали маркируют в соответствии с ГОСТ 1435-90.
Инструментальные углеродистые стали выпускают следующих марок: У7.У8ГА.У8Г, У9, У 10, У 11, У 12 и У 13. Цифры указывают на содержание углерода в десятых долях процента. Буква Г после цифры означает, что сталь имеет повышенное содержание марганца. Марка инструментальной углеродистой стали высокого качества имеет букву А.
Примеры обозначения и расшифровки
1. У12 – сталь инструментальная, высокоуглеродистая, содержащая 1,2% углерода, качественная.
2. У8ГА - сталь инструментальная, высокоуглеродистая, содержащая 0,8% углерода, 1% марганца, высококачественная
3. У9А - сталь инструментальная, высокоуглеродистая, содержащая 0,9% углерода, высококачественная.
Легированные стали
Легированной называют сталь со специально введенным одним или более легирующим элементом.
Обозначение легированных сталей
Легированные стали маркируются комбинацией цифр и заглавных букв алфавита. В обозначении нет слова «сталь» или символа «Ст». Например, 40Х, 38ХМ10А, 20Х13. Первые две цифры обозначают содержание углерода в сотых долях процента. Следующие буквы являются сокращенным обозначением элемента. Цифры, стоящие после букв, обозначают содержание этого элемента в целых процентах. Если за буквой не стоит цифра, значит содержание этого элемента до 1%.
Таблица 4. – Обозначение элементов.
Ю-Al Алюминий | C-Si Кремний | А- N Азот |
Р-В Бор | Г- Mn Марганец | Д –Cu Медь |
Ф-V Ванадий | М-Мо Молибден | Е-Se Селен |
В-Wвольфрам | Н-Ni Никель | Ц-Zr Цирконий |
Ж-Fe Железо | T-Ti Титан | Б-Nb Ниобий |
К- Co Кобальт | Та - Тантал | Х-Cr Хром |
Для изготовления измерительных инструментов применяют X, ХВГ.
Стали для штампов: 9Х, Х12М, 3Х2Н8Ф.
Стали для ударного инструмента: 4ХС, 5ХВ2С.
Легированные стали с особыми свойствами.
1. Коррозионностойкие стали.
Коррозионностойкой (или нержавеющей) называют сталь, обладающую высокой химической стойкостью в агрессивных средах. Коррозионностойкие стали получают легированием низко- и среднеуглеродистых сталей хромом, никелем, титаном, алюминием, марганцем. Антикоррозионные свойства сталям придают введением в них большого количества хрома или хрома и никеля. Наибольшее распространение получили хромистые и хромоникелевые стали.
Например, хромистые стали 95Х18, 30Х13, 08Х17Т.
Хромоникелевые нержавеющие имеют большую коррозийную стойкость, чем хромистые стали, обладают повышенной прочностью и хорошей технологичностью в отношении обработки давлением.
Например, 12Х18Н10Т, 08Х10Н20Т2.
2. Жаростойкие обладают стойкостью против химического разрушения в газовых средах, работающие в слабонагруженном состоянии.
3. Жаропрочные стали – это стали, способные выдерживать механические нагрузки без существенных деформаций при высоких температурах. К числу жаропрочных относят стали, содержащие хром, кремний, молибден, никель и др.
Например, 40Х10С2М, 11Х11Н2В2МФ.
4. Износостойкие – стали, обладающие повышенной стойкостью к износу: шарикоподшипниковые, графитизированные и высокомарганцовистые.
Особенности обозначения подшипниковых сталей.
Маркировка начинается с буквы Ш, цифра, стоящая после буквы Х, показывает содержание хрома в десятых долях процента.
Маркировка начинается с буквы Ш, цифра, стоящая после буквы Х, показывает содержание хрома в десятых долях процента.
Например, ШХ9, ШХ15ГС.
Примеры обозначения и расшифровки
1.40ХГТР – сталь конструкционная, легированная, качественная, содержащая 0,4% углерода и по 1% хрома, марганца, титана, бора, остальное- железо и примеси.
2. 38Х2МЮА - сталь конструкционная, легированная, высококачественная, содержащая 0,38% углерода, 2% % хрома, 1% молибдена, алюминия, остальное- железо и примеси.
3. ХВГ - сталь конструкционная, легированная, качественная, содержащая 1% углерода и по 1% хрома, марганца, остальное – железо и примеси.
4. ШХ15 – сталь подшипниковая, инструментальная, качественная, содержащая 1% углерода, 1,5% хрома, остальное-железо.
5. Р10К5Ф5 – сталь быстрорежущая, инструментальная, качественная, содержащая 1% углерода, 10 % вольфрама, 5% кобальта, 5% ванадия, остальное-железо
Контрольные вопросы
1. В чем отличие ВЧ35 от СЧ35?
2. Какова цель легирования чугунов?
3. Может ли ковкий чугун быть антифрикционным?
4. Почему жаростойкий чугун может быть одновременно и коррозионностойким? Примеры маркировки.
5. Чем чугун отличается от стали?
6. Что такое сталь?
7. Как маркируют углеродистые стали обыкновенного качества?
8. Может ли Сталь 45 иметь индекс «кп» и группу Б? Дайте название этой стали
9. Что такое У8, У8А?
10. Является ли сталь Р6М5 высоколегированной и почему? Дайте название этой стали.
11. Какие стали относят к легированным сталям с особыми свойствами?
12. Сравните сталь А20 и 10.
13. Для чего стали легируют хромом, никелем?
14. Может ли сталь быть без примесей?
15. Как маркируют углеродистые конструкционные качественные стали?
Занятие 24. Практическая работа № 4(часть 2): «Расшифровка марок конструкционных материалов». Сплавы цветных металлов.
1.Цель работы:1.1. Закрепить знания по условному обозначению марок сплавов на основе цветных металлов согласно ГОСТ;1.2. Закрепить знания по определению основных свойств сплавов на основе цветных металлов в соответствии с маркировкой и химическим составом2.Пояснение к работеДеформируемые сплавы.К неупрочняемым термической обработкой относятся сплавы:- алюминия с марганцем марки АМц;- алюминия с магнием марок АМг; АМгЗ, АМг5В, АМг5П, АМг6.Из них изготовляют бензиновые баки, проволоку, заклепки, а также сварные резервуары для жидкостей и газов, детали вагонов.В группе деформируемых алюминиевых сплавов, упрочняемых термической обработкой, различают сплавы:• нормальной прочности;• высокопрочные сплавы;• жаропрочные сплавы;• сплавы для ковки и штамповки.Сплавы нормальной прочности.
К ним относятся сплавы системы Алюминий + Медь + Магний (дуралюмины), которые маркируются буквой Д. Дюралюмины (Д1, Д16, Д18) характеризуются высокой прочностью, достаточной твердостью и вязкостью. Для упрочнения сплавов применяют закалку с последующим охлаждением в воде. Дуралюмины широко используются в авиастроении: из сплава Д1 изготовляют лопасти винтов, из Д16 – несущие элементы фюзеляжей самолетов, сплав Д18 – один из основных заклепочных материалов.Высокопрочные сплавы алюминия (В93, В95, В96) относятся к системе Алюминий+Цинк+Магний+Медь. В качестве легирующих добавок используют марганец и хром, которые увеличивают коррозионную стойкость и эффект старения сплава. Для достижения требуемых прочностных свойств, сплавы закаливают с последующим старением. Из этих сплавов изготовляют высоконагруженные наружные конструкции в авиастроении – детали каркасов, шасси и обшивки.Жаропрочные сплавы алюминия (АК4-1, Д20) имеют сложный химический состав, легированы железом, никелем, медью и другими элементами. Детали из жаропрочных сплавов используются после закалки и искусственного старения и могут эксплуатироваться при температуре до 300°С.Сплавы для ковки и штамповки (АК2, АК4, АК6, АК8) относятся к системе Алюминий+Медь+Магний с добавками кремния. Сплавы применяют после закалки и старения для изготовления средненагруженных деталей сложной формы (АК6) и высоконагруженных штампованных деталей – поршни, лопасти винтов, крыльчатки насосов и др.Литейные сплавы.
Для изготовления деталей методом литья применяют алюминиевые сплавы систем Al-Si, Al-Cu, Al-Mg. Для улучшения механических свойств сплавы легируют титаном, бором, ванадием. Главным достоинством литейных сплавов является высокая жидкотекучесть, небольшая усадка, хорошие механические свойства.
Медь и ее сплавыЛатуни – сплавы меди, а которых главным легирующим элементом является цинк. В зависимости от содержания легирующих компонентов различают:-простые (двойные) латуни;-многокомпонентные (легированные) латуни.Простые латуни маркируют буквой «Л» и цифрами, показывающими среднее содержание меди в сплаве.Например, сплав Л90 – латунь, содержащая 90 % меди, остальное – цинк.В марках легированных латуней группы букв и цифр, стоящих после них, обозначают легирующие элементы и их содержание в процентах.Например, сплав ЛАНКМц75-2-2,5-0,5-0,5 – латунь алюминиевоникелькремнистомарганцевая, содержащая 75 % меди, 2 % алюминия, 2,5 % никеля, 0,5 % кремния, 0,5 % марганца, остальное – цинк.В зависимости от основного легирующего элемента различают алюминиевые, кремнистые, марганцевые, никелевые, оловянистые, свинцовые и другие латуни.Бронзы – это сплавы меди с оловом и другими элементами (алюминий, марганец, кремний, свинец, бериллий). В зависимости от содержания основных компонентов, бронзы делятся на:оловянные, главным легирующим элементом которых является олово;безоловянные (специальные), не содержащие олова.Бронзы маркируют буквами «Бр» и буквенные индексы элементов, входящих в состав. Затем следуют цифры, обозначающие среднее содержание элементов в процентах (цифру, обозначающую содержание меди в бронзе, не ставят).Например, сплав марки БрОЦС5-5-5 означает, что бронза содержит олова, свинца и цинка по 5 %, остальное – медь (85 %).Деформируемые оловянные бронзы содержат до 8 % олова. Эти бронзы используют для изготовления пружин, мембран и других деформируемых деталей.Литейные бронзы содержат свыше 6 % олова, обладают высокими антифрикционными свойствами и достаточной прочностью; их используют для изготовления ответственных узлов трения (вкладыши подшипников скольжения).Специальные бронзы включают в свой состав алюминий, никель, кремний, железо, бериллий, хром, свинец и другие элементы. В большинстве случаев название бронзы определяется основным легирующим компонентом.Химические элементы, используемые при легировании, обозначают в марках медных сплавов следующими индексами
1. А- алюминий; 9. З- золото 17. О -олово2. Вм- вольфрам 10. К- кобальт 18. С- свинец3. В- висмут; 11. К- кремний 19. Сн- селен4. В- Ванадий 12. Мг- магний 20. Ср- серебро5. Км- кадмий; 13. Мц- марганец 21. Су- сурьма6. Гл- галлий; 14. М- медь 22. Ти- титан7. Г- германий 15. Мш- мышьяк 23. Ф- фосфор;8. Ж- Железо 16. Н- никель 24. Ц- цинк.
3.Задание3.1. Прочитайте краткие теоретические сведения.3.2. Перечертите таблицу № 1на чистый лист бумаги.3.2. Перепишите из таблицы №1 столбец варианта, заданного преподавателем (5 позиций).3.3. В соответствующей графе позиции таблицы № 1 расшифруйте условное буквенное и цифровое обозначение заданных марок сплавов.3.4. Укажите 2 наименования деталей автомобиля, изготовленных из заданных марок сплавов.3.5. Письменно ответьте на контрольные вопросы3.5.1. Как классифицируются латуни?3.5.2. Как классифицируются бронзы?3.5.3. Как классифицируются алюминиевые сплавы?4.Содержание отчета.Отчёт должен содержать4.1. Дату проведения практической работы4.2. Название практической работы.4.3. Заполненную таблицу № 14.4.Ответы на контрольные вопросы.
Занятие 25. Практическая работа № 5: «Выбор материала для изготовления деталей».
Цель работы:1.Закрепить знания основных свойств машиностроительных материалов (конструкционных, технологических и эксплуатационных).2. Закрепить знания по определению необходимых свойств материалов для изготовления конкретных деталей в зависимости от назначения и выполняемых функций.Пояснение к работеКраткие теоретические сведения.Физико-механические свойства конструкционных материалов подразделяются на:-конструкционные;-технологические;-эксплуатационные.Конструкционные свойства определяют прочность и долговечность машины ее узлов и деталей, к ним относятся:Прочность — это способность конструкции сопротивляться разрушению при действии на нее внешних сил (нагрузок).Жесткость — способность элемента конструкции сопротивляться деформации.Упругость — это способность твердого деформируемого тела восстанавливать свою форму и объем после прекращения действия внешних нагрузок.Пластичность — это свойство твердого деформируемого тела до разрушения необратимо изменять свою форму и объем от действия внешних сил.Твердость – способность материала оказывать сопротивление деформированию и разрушению при местных контактных воздействиях.Вязкость — это свойство оказывать сопротивление за счет трения происходящего при перемещении элементарных частиц тела относительно друг друга в процессе деформирования. Отметим,Ползучесть — это явление, характеризующее изменения во времени величин деформаций и напряжений в теле при действии статических нагрузок.Выносливость — это явление, которое характеризуется чувствительностью и изменениями прочностных свойств материалов в зависимости от числа циклов нагружения.Ударная вязкость характеризует надежность материала, его способность сопротивляться хрупкому разрушениюЭксплуатационные свойства характеризуют способность материала работать в конкретных условиях, к ним относятсяизносостойкость – способность материала сопротивляться поверхностному разрушению под действием внешнего трения;коррозионная стойкость – способность материала сопротивляться действию агрессивных кислотных и щелочных сред;жаростойкость – способность материала сопротивляться окислению в газовой среде при высокой температуре;жаропрочность – это способность материала сохранять прочность и твердость при высоких температурах;хладостойкость– способность материала сохранять пластические свойства при отрицательных температурах;антифрикционность – способность материала прирабатываться к другому материалу.Технологические свойства характеризуют способность материала подвергаться различным способам холодной и горячей обработки.Технологические свойства позволяют производить формоизменяющую обработку и получать заготовки и детали машин, к ним относятся:Литейные свойства определяются способностью расплавленного металла или сплава к заполнению литейной формы (жидкотекучесть), степенью химической неоднородности по сечению полученной отливки (ликвация), а также величиной усадки – сокращением линейных размеров при кристаллизации и дальнейшем охлаждении.Способность материала к обработке давлением – это способность материала изменять размеры и форму под влиянием внешних нагрузок не разрушаясь (обработка без снятия стружки). Листовой материал испытывают на перегиб и вытяжку сферической лунки. Проволоку испытывают на перегиб, скручивание, на навивание. Трубы испытывают на раздачу, сплющивание до определенной высоты и изгиб. Критерием годности материала является отсутствие дефектов после испытания.Свариваемость – это способность материала образовывать неразъемные соединения требуемого качества при сварке.Обрабатываемость резанием – характеризует способность материала поддаваться обработке режущим инструментом. Технологические свойства часто определяют выбор материала для конструкции.При выборе материала для создания конструкции необходимо учитывать конструкционные, технологические и эксплуатационные свойства.Содержание отчета.1. Прочитайте краткие теоретические сведения.2. Ознакомьтесь с заданным вариантом задания.
3. Проанализируйте условия работы детали.
4. Сформулируйте требования к свойствам материала детали.
5. Выберите материал для изготовления детали.
6. Заполните таблицу.
7. Письменно ответьте на контрольные вопросы.
Занятие 26. Практическая работа № 6: «Изучение микроструктуры чугунов».
Цель:Сформировать понимание строения чугунов, их разновидности и причину различия свойств.
Похожие статьи:
poznayka.org