Лист холоднокатаный – основные свойства и особенности производства. Кто создал прокатный стан позволявший производить листовую сталь
МИРОВАЯ ИСТОРИЯ. МЕТАЛЛУРГИЯ. Кто создал прокатный стан позволявший производить листовую сталь
История изобретения прокатного стана | Великие открытия человечества
После того, как выплавили сталь и из нее отлили огромные слитки стали, их нужно превратить в станок, двигатель, рельсы, балки или другие изделия разных форм и размеров. Для этого слитку нужно придать удобную для производства деталей форму в виде бруса с разным поперечным сечением, балки, проволоки, стального листа и т. д. Все это делается на прокатных станках. Процесс раскатки металла стальными валками, которые вращаются навстречу друг другу, называют прокаткой. Между валками существует зазор, куда они втягивают, а затем обжимают металл, вытягивая его в длину и уменьшая в ширину. Благодаря этому улучшается структура металла и исчезают мелкие поры, которые были в слитке.
Впервые изобразил и описал принцип работы ручного прокатного стана, имевшего плоские валики, Леонардо да Винчи в 1495 году. На оси приводного нижнего валка было червячное колесо. Валок вращался с помощью массивной рукоятки путем червячной передачи. На стане получали тонкие равномерные оловянные листы. В XVI веке появились и калиброванные валки для прокатки различных профилей. Прокатные станы использовали при создании тонких листов из мягкого металла (свинца, олова, золота, меди и серебра), которые прокатывали без предварительного нагрева вручную. Прокатка в горячем состоянии появилась только в начале XVIII столетия. Вначале прокатывали железные тонкие листы, с 1769 г. начали делать проволоку.
Первый прокатный стан для прокатывания железных болванок предложил Корт, разрабатывая метод пудлингования. Из печи крица подавалась под молот, где ее проковывали, а потом пропускали через вальцы. Постепенно вытесняя ковку, прокатка становится одним из важнейших звеньев производственного процесса. В XIX веке значительно усовершенствовалась техника проката, что было связано с возрастающим строительством железных дорог и потребностью в рельсах, вагонных колесах и т. д. Валки, которые вращались в противополож
pellete.ru
МИРОВАЯ ИСТОРИЯ. МЕТАЛЛУРГИЯ: anton_montana
ОРИГИНАЛНачну я свою историю издали. Попалась мне картинка на которой лежит себе валяется кабелеукладчик Сименсов "Фарадей". «Фарадей» (CS Faraday) — судно компании Siemens Brothers, построено в 1874 году компанией C. Mitchell & Company Ltd. на верфях в Ньюкасле. Названо в честь Майкла Фарадея.За 50 лет эксплуатации в качестве кабелеукладчика «Фарадей» уложил 50 000 морских миль кабеля. В 1924 году судно было продано на слом, однако борта толщиной в 1 дюйм затрудняли работу разборщиков, поэтому Faraday стал угольным блокшивом, названным Analcoal, в Алжире и принадлежащим Англо-Алжирской угольной компании. В 1931 году блокшив был переведён в Гибралтар. В 1941 году судно стало Военно-морским складским судном в Сьерра-Леоне. В 1950 году «Фарадей» вернулся в Англию, где и был разобран на Южно-уэльской верфи."
Чудесная и удивительная судьбы для одного из первых цельнометалических винтовых судов огромного размера. Длинна - 111 метров, водоизмещение 4197. Соизмерим например с крейсером "Аврора". чуть меньше.Конечно же, мне эта картинка напомнила судьбу еще одного знаменитого кабелеукладчика. Даже еще большего по размерам."Great_Eastern", сделанного еще раньше.
Как оказалось огромных железных кораблей в это время появилось много! Но что интересно это все не корабли, это гражданские суда!Вот это огромное железное судно - рудовоз!
А вот корабль, броненосец того же времени.
В средине 19 века не только суда огромные железные появляются. Знаменитый Брюннель строит сложнейший мост целиком из стального проката. Этот мост стоит до сих пор и им пользуются! Мост "короля Альберта".
Это фото как бы стройки моста, я практически не нашел других фото, но и по этой много вопросов возникает.
Самое главное проявления высоких металлургических технологий это железнодорожный транспорт и на фотографиях средины 19 века мы видим развитую систему железных дорог, паровозы и классические колесные пары у вагонов.
Везде сталь и прокат!А вот с оружием вышла какая то незадача - пушки бронзовые или чугунные, винтовки гладкоствольные в основном, с капсульным запалом, практически кремневые.
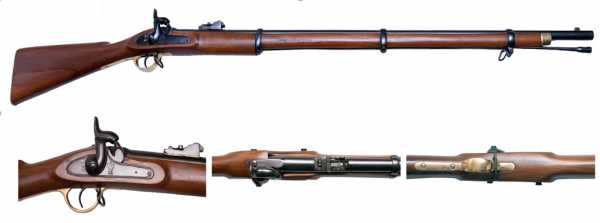
Вот пушка на борту гигантского стального корабля "Левиафан", вернее судна, которое для пушек ну ни как не приспособлено!
Для меня это не понятный парадокс, ведь всегда все новшества особенно в металлургии реализовывались в оружии. Что мы и видим сейчас, да и в начале 20 го века - пушки из стали, дредноуты огромные, бронепоезда и винтовки и прочее прочее прочее.Я решил углубиться в историю металлургии конца 18 века - начало 19 го.Как оказалось Россия была лидером в мировой металлургии!Вот например история Верхнеисетского металлургического завода - http://todaynews24.ru/ural/2011/45/s-sobolem-na-klejme/Я приведу один неожиданный кусочек из статьи..."В начале XIX века мировую славу принесла заводу новая продукция — листовое кровельное железо. Его покупали Англия, Франция, Америка и их колонии. Только в Америку ежегодно вывозилось не менее 300 тыс. пудов продукции. «Визовским» железом были крыты крыши Лондонского парламента и собора Парижской богоматери. В торговом мире верх-исетское железо было известно как «яковлевское», имело клеймо «А.Я.Сибирь» с изображением соболя и высоко ценилось за отменные качества: было гладким, глянцевым, не требовало покраски, «по сто лет на крыше стояло». После пожара 1812 года в Москве его поставили на все крыши пострадавшего города."Кто не понял - это стальной листовой прокат и если верить написанному очень высокого качества - нержавел и не требовал покраски.В статье мне попалась любопытное местечко что в 1918 году все старое оборудование было вывезено, кем и куда не понятно. Но это другая песня...То есть прокат был и оборудование было и делали прокат еще в начале 19 века. Я писал недавно про прокат в древнеримских постройках - тавровые балки Пантеона.Но ведь по официальной истории все не так!!!Меня зацепила одна статейка про историю прокатного стана...https://ru.wikipedia.org/wiki/Прокатный_стан..."С развитием железнодорожного транспорта значительно увеличилась потребность в прокатной продукции. Первые рельсы были чугунными, однако в начале XIX века в Англии перешли на производство железных рельсов. В 1828 году появился первый прокатный стан для прокатки рельсов из пудлингового железа, а с 1825 года начали прокатывать рельсы из бессемеровской стали. Рельсы были главным продуктом прокатного производства. Помимо рельсов надо было производить различные детали паровозов, броня требовалась и для развития флота, в котором деревянные корабли заменялись металлическими бронированными."
ЭТО ПРОСТО ПРЕЛЕСТЬ КАКАЯ ТО!!! Бессемеру в 1825 году было всего 12 лет!!! Двенадцать!!!Я понимаю что мальчик мог быть умным... но не настолько же! Генри Бессемер (англ. Henry Bessemer; 19 января 1813, Чарлтон, графство Хартфордшир — 15 марта 1898, Лондон) — английский инженер-изобретатель, известный своими изобретениями и революционными улучшениями в области металлургии[3]; член Лондонского королевского общества с 1879 года.https://ru.wikipedia.org/wiki/Бессемер,_ГенриЧто такое Бессемеровский процесс, я напомню читателям.Жидкий чугун заливают в конвектор Бессемера и продувают через него воздух. Кислород воздуха вступает во взаимодействие с углеродом чугуна, образуется СО2 и выделяется энергия которая резко повышает температуру расплава, из горла конвектора вырывается сноп пламени и искр, оп ля и сталь готова!
Дальше сталь разливают по формам и сразу, пока она не остыла и пластична подают на прокатный стан.ВНИМАНИЕ!!! САМАЯ ГЛАВНАЯ ФИШКА!!! Если сталь остынет она уже не прокатывается, она уже очень плотная!!! Прокатный стан принимает сталь от разлива сразу. Именно прокат горячей стали делает её и твердой и упругой так как прокат упорядочивает кристалическую решетку и создает волокна которые укладываются вдоль по прокату. Но стоит только стали остыть - это уже совсем другое дело! Сталь снова надо нагревать, что бы она стала доступна и ковке и прокату. Так и делают - при прокате сталь многократно нагревают по мере проката в специальной печи.Устройство для проката стали называют блюмингом и слябингом!Первый прокатный стан в России заработал по официальной истории на Сормовском заводе в 1871 году https://ru.wikipedia.org/wiki/Прокатный_станПервые блюминги появились в 70х годах 19 века - Впервые трио-станы были применены для обжатия бессемеровских слитков в США А. Холлеем (1871). В последующие годы Джон и Джордж Фриц, а также А. Холлей там же построили механизированные трио-блюминги для прокатки слитков небольшой массы. В Англии Рамсботомом был сконструирован (1880) дуо-реверсивный стан с переменным направлением вращения валков для прокатки слитков до 5 т и более. Широкое распространение дуо-реверсивный стан получил благодаря электрическому реверсивному приводу, предложенному К. Ильчнером (1902). В СССР блюминги изготовляют с 1931; первый произведенный в СССР (по немецким чертежам) блюминг введён в эксплуатацию на Макеевском металлургическом заводе (1933). В конце 1940-х гг. советскими учеными и инженерами (А. И. Целиков, А. В. Истомин и др.) была разработана первая собственно советская конструкция блюминга (работа была удостоена в 1951 г. Сталинской премии 2-й степени).
Конечно сталь можно ковать, молотками и кувалдами можно ковать меч, топор, ножик но не рельс!!! И не кровельное железо и не дюймовый лист обшивки корабля.Ну хорошо, мне один читатель насоветовал что раньше то были большие молоты от водяного привода или паровой машины и им то ковать можно все что угодно! Вот например такой молот и ковка...Этот тип механических молотов имеет один существенный недостаток, он виден хорошо на фото - молот падает на наковальню под углом и из за этого сильно ограничены его возможности!
Да именно так и сковали башню на первых броненосцах и мониторах времен гражданской войны в США!Вот один из "изобретателей" типа Брюнеля - все и сразу, отец всех паровозов и прочее...Джеймс Несмит (англ. James Nasmyth; 19 августа 1808, Эдинбург — 7 мая 1890, Лондон) — шотландский астроном и инженер, сын шотландского художника Александра Несмита (англ.), изобретатель парового молота и гидравлического пресса.https://ru.wikipedia.org/wiki/Несмит,_Джеймс
Токмо не очень понятно что он там ковал... если Бессемер не изобрел еще своего способа получения стали в товарных объемах!
Вот паровые молоты
Французский царь молот.
Но и все равно рельс молотом не сковать, и изогнутый корабельный рангоут. По этому придумали гидравлические прессы. Но это опять же в лучшем случае вторая половина 19 века!Теперь я предлагаю посмотреть, а как же добывали руду по официальной истории в 19 веке в эпоху фотографии. Руду ведь надо не просто выкопать её надо еще и доставить к печи.
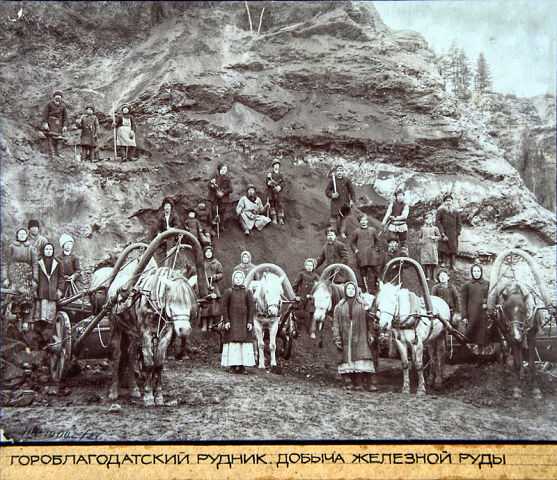
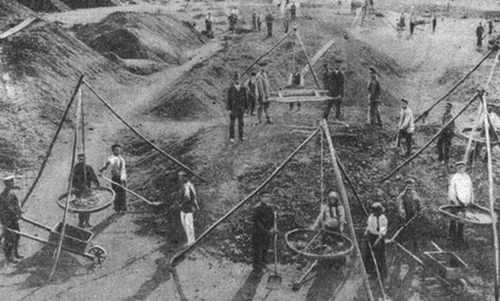
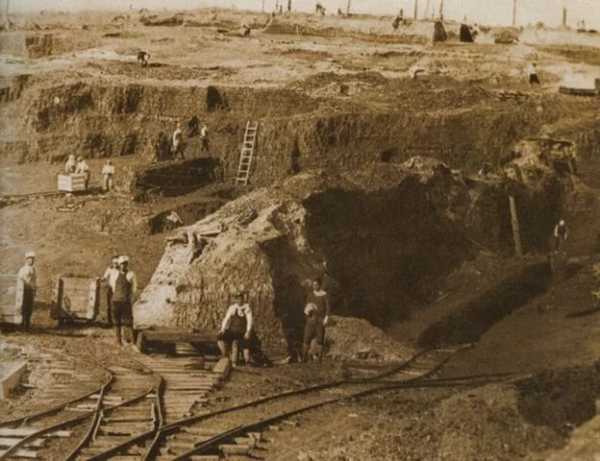
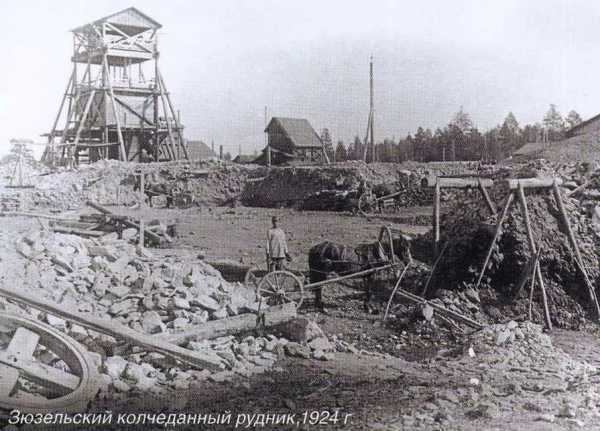
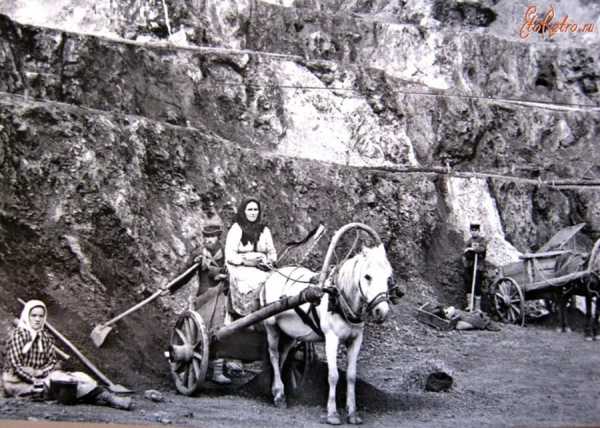
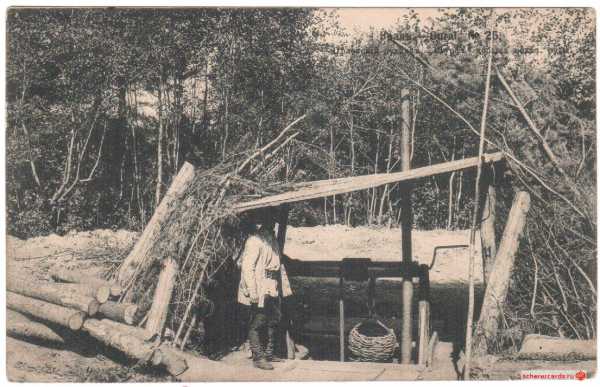
Да с такой добычей ладно если на ножик с топором каждому крестьянину железа наделаешь! Англия или Франция на фотографиях ни чем особым не отличается точно такие же шахтеры с фонарем на башке и лошадью и тележкой, не более 500кг. Не надо забывать что карьеры то в земле и лошадь везет нагруженную телегу вверх! То есть до появления экскаваторов и большегрузных машин или хотя бы до железной дороги на рудник речи нет о больших объёмах добычи руды. Железо должно быть очень очень дорогим! Но мы видим просто наплевательское отношение к железному лому - корабли валяются на берегу и их ни кто не разбирает на куски. Почему? Сделать смогли, а разобрать нет? Один из первых вопросов возникает сразу - а чем резать сталь?Газовая сварка и резка металлов появилась опять же в конце 19 века и опять во Франции - http://te.zavantag.com/docs/221/index-7518.html?page=4Но позвольте, а как же резали рельсы, чем же обрезали края, чем вообще резали металл до конца 19 века. Вон же делали корабли в средине 19 века??? Зубилом что ли дюймовый лист резали? Да есть гидравлические ножницы но это опять же конец 19 века! Пилы из инструментальной стали это конец 19 века https://ru.wikipedia.org/wiki/Инструментальная_сталь ....с карбидом вольфрама это вообще 20й век.Но и это все не самое главное.Вот как вы думаете, что делали с металЛическим ломом, ну вот сломался паровой котел или сделали не так деталь к кораблю или рельсы кривые прокатали, что делали со всеми этими железками, железо же денег стоит! Естественный ответ - на переплавку! Даже из истории ВОВ все помнят как подбитые танки и прочее не нужное ломаное оружие отправляли на перевлавку... это же железо!Так вот оказывается до великого изобретения Мартена Пьера Эмиля - регенеративной пламенной печи, металлолом плавить не могли!!! Еще раз - МЕТАЛЛОЛОМ ПЛАВИТЬ НЕ МОГЛИ!!!Нагреть и перековать рельс в саблю или лопату можно, а вот сделать новый рельс толще например уже не могли, или собрать старые рельсы и сделать из них корабль не могли. Так говорит официальная история металлургии!В Германии и прочих Англиях способ этот называют Семенс - Мартеновский. Вот Мартен...
А вот Вильгельм Сименс, это один из братьев великой семейки.
В некоторых статьях их даже путают http://www.metaljournal.com.ua/martin-emile/Дело в том что якобы теорию придумал Сименс, а сделал первую печь Мартен. Судьба Мартена странная, его признали только в конце 19 века и даже наградили перед смертью. Фотографий его мало.Самое удивительное то что печь и способ плавки не сложный - смесь из руды чугуна и металлолома нагревается горением регенеративного газа, который получать умели еще чуть ли не с конца 18 века! Но еще более странно, что варка стекла происходит точно в таких же печах по тем же самым принципам!Но стекло то известно с древнейших времен!!!История с Сименсами интересна тем, что корабль из железа прокладывал тысячи километров кабеля, который покрыт стальным прокатом - оплетка, кабель по которому, как оказалось невозможно было передавать сигналы так как он затухал... и все это было до изобретения настоящего способа получать сталь в промышленных объемах, сталь хорошего качества.Дело в том что как оказалось Бессемеровский или Томасовский способ продувки чугуна воздухом не давал хорошего качества сталь. Бессемеровский способ "нашел свое новое воплощение" когда в 20 веке научились получать кислород и стали продувать чугун чистым кислородом!!! https://rutlib.com/book/17422/p/28
Судя по тому, что наследие предков смогли освоить полностью только к началу 20 века и сразу же кинулись делать оружие. Начало 19 века технологически я оцениваю как конец 19...минимум! Так что на чем там Наполеон свои армии возил на телегах или по ЖД это еще тот вопросец! А то вот рассуждаем, что не мог он миллионную армию через Белорусские болота с пушками протащить! Хрен его знает что там было в этом начале 19 века. Ну а за 50 лет до первых фотографий можно такого настрогать что ой ой ой! Я помню как в 90 за одну зиму дачные поселки лишались все проводов, алюминевых кастрюль и прочего цвет мета. Да что говорить то - люки с дорог тащили в металлолом, раз и нет люка, одна дырка на дороге! так что прокладывал кабель Сименс в 1856 году на "Левиафане" и "Фарадее" или вытаскивал его это еще бабушка на двое сказала.
PS: Ах да... почему же я назвал Мартена святым? Есть такой святой в католической церкви - Луи́ Марте́н (фр. Louis Joseph Aloys Stanislaus Martin; 22 августа 1823, Бордо, Франция — 29 апреля 1894, Арньер-сюр-Итон, Франция) — святой Римско-Католической Церкви, отец святой Терезы из Лизье, муж святой Мари-Зели Мартен. Вот собственно ни чем другим он как бы не прославился кроме как муж святой и отец святой. С чего бы это? Однако что то уж очень он похож на Мартена металлурга судьба которого очень обделила, умер он в жестокой бедности не защитив свои патенты, все Сименсы прибрали. Но это так... для интриги, должна же быть интрига в моем ЖЖ? :::-)))
anton-montana.livejournal.com
Прокатный листовой стан
Изобретение относится к горной металлургии, в частности к оборудованию прокатных цехов, и может быть использовано для холодной прокатки и дрессировки листов. Цель изобретения - улучшение качества проката путем устранения продольных линий на полосе. Выточки на рабочих валках 6 и 7 служат для возможного размещения и разгрузки напряженных участков полосы 12. Эти участки возникают вследствие затруднения расширения полосы в поперечном направлении. В выточках полоса имеет возможность упруго изгибаться, что позволяет сохранить ее структуру без разрушения кристаллической решетки и качество полосы возрастает. 2 ил.
СОЮЗ СОВЕТСКИХ
СОЦИАЛИСТИЧЕСКИХ
РЕСПУБЛИК (l9) 01) (51)5 В 21 В 1/22
ОПИСАНИЕ ИЗОБРЕТЕНИЯ
К А ВТОРСКОМУ СВИДЕТЕЛЬСТВУ
ГОСУДАРСТВЕННЫЙ КОМИТЕТ
ПО ИЗОБРЕТЕНИЯМ И ОТКРЫТИЯМ
ПРИ ГКНТ СССР (21) 4482471/23-02 (22) 16.09.88 (46) 15. 08. 90. Бюл . Р 30 (71) Институт черной металлургии и Карагандинский металлургический комбинат (72) П.Я.Скичко, В.А.Скумс, В.Д.Петров, Г.В.Левыкин, А.А.Ниденс и В.С.Лисин (53) 621.771.237.06.07 (088.8) (56) Королев А.А. Конструкция и расчет машин и механизмов прокатных станов. М., 1969, с. 106-108.
Виткин А.И., Галкин Д.П., Берлин Б.И. Основы теории и технология производства белой жести. М.: Металлургия, 1978, с. 43, 44, 2 (54) ПРОКАТНЫЙ ЛИСТОВОЙ СТАН (57) Изобретение относится к горной металлургии, в частности к оборудованию прокатных цехов,и может быть использовано для холодной прокатки и дрессировки листов. Цель изобретения — улучшение качества проката путем устранения продольных линий на полосе. Выточки на рабочих валках 6 и 7 служат для возможного размещения и разгрузки напряженных участков полосы 12. Эти участки возникают вследствие затруднения расширения полосы в поперечном направлении. В выточках полоса имеет возможность упруго а изгибаться, что позволяет сохранить ее структуру бе э ра зрушения кристаллической решетки, и качество полосы возрастает. 2 ил.
1585028
Изобретение относится к черной металлургии, в частности к оборудованию прокатных цехов, и может быть использовано для холодной прокатки и дрессировки листов, Цель изобретения — улучшение качества проката путем устранения продольных линий на полосе.
На фиг. 1 схематически изображен 10 прокатный листовой стан; на фиг. 2 рабочие валки предпоследней и последней клетей.
Прокатный листовой стан содержит разматыватель 1., натяжные устройства 2 и 3, клети 4 и 5 с установленными в них рабочими 6 и 7 и опорными
8 и 9 валками и моталку 10, на- поверхности рабочих валков 6 и 7 предпоследней 4 и последней 5 клети выполне- 20 ны кольцевые выточки 11, причем кольцевые выточки 11 на поверхности рабочих валков 7 последней клети 5 выполнены со смещением относительно кольцевых выточек 11 на рабочих вал- 25 ках 6 предпоследней клети 4, например, на полшага расстояния между выточками 11. Кольцевые выточки 11 выполнены глубиной, равной 0,002-0,003, шириной 0,01-0,015, а расетояние меж- 3
Прокатный листовой стан работает следующим образом.
При вращении рабочих валков 6 и .7, опирающихся на опорные валки 8 и 9 и находящихся в клетях 4 и 5, прокатка полосы 12 производится одновременно в обоих клетях 4 и 5.
Переднее натяжение полосы 12 осу- @ ществляется натяжным устройством 2, а заднее - натяжным устройством 3.
Сматывается полоса из разматывателя
1 и наматывается на моталку 10. Рабо.чие валки б предпоследней клети 4 прокатывают полосу 12 цилиндрическими поверхностями 13 бочки валка, которые находятся между выточками
11, а рабочие валки 7 последней клети 5 прокатывают такими же поверхностями 13 недокатанные участки полости 12.
При этом обе клети 4 и 5 должны быть чистовыми и настроенными на прокатку полосы одной и той же толщины.
Выточки 11 на рабочих валках 6 и 7 служат для возможного размещения и разгрузки напряженных участков полосы
12, так как в этом случае тонкая полоса имеет возможность упруго изгибаться, находясь в выточках и этим самым сохранять свою структуру без разрушения кристаллической решетки.
Подтверждением эффективности предлагаемого устройства служит прокатка узких полос, при которой дефект продольных линий на полосе отсутствует.
На примере листопрокатного стана, где длина бочки рабочего валка Ь =
1400 мм, получим: глубина кольцевой выточки h = (0,002-0,003) L = — (0,002-0,003) 1400 = 2,8 — 4,2 мм, ширина Ь = (0,01-0,015) L = (0,01-0,015) 1400 = 14-21 мм, расстояние между выточками b = (0,1-0, 15) — (О, 1-0, 15) 1400 = 140-210 мм.
Хотя расстояние между продольными линиями на стане наблюдалось 1
100-150 мм, в предлагаемом устройстве оно принято большим, равным 1
140-210 мм, и это целесообразно потому, что участки полосы длиной 1 на стане находились в стесненном положении по оси рабочего валка с двух сторон, а в предлагаемом устройстве — с обеих сторон имеются разгрузочные кольцевые выточки. Несмотря на весьма малые обжатия, особенно при дрессировке, лист между чистовыми клетями имеет незначительные коробоватости после прокатки в предпоследней клети, которые устраняются при прокатке в последней клети.
Формула изобретения
Прокатный листовой стан, содержащий разматыватель, натяжные устройства, клети с установленными в них рабочими валками с кольцевыми выточками, опорными валками и моталку, о т— л и ч а ю шийся тем, что, с целью улучшения качества проката путем устранения продольных линий на полосе, выточки валков последней и предпоследней клетей выполнены глубиной 0,002-0,003, шириной 0,010,015, расстоянием между ними, равным 0,1-0, 15 длины бочки валка, и с одинаковым шагом, при этом выточки валков последней клети смещены относительно выточек валков предпоследней клети на полшага.
1585028
f3 11
r3 11
Составитель Г.Ростов
Техред Л. Сердюкова
Корректор А.Обручар
Редактор Т.Парфенова
Заказ 2289 Тираж 409 Подписное
ВНИИПИ Государственного комитета по изобретениям и открытиям при ГКНТ СССР
113035, Москва, Ж-35, Раушская наб., д. 4/5
Производственно=издательский комбинат "Патент", r. Ужгород, ул. Гагарина, 101
www.findpatent.ru
Станы холодной прокатки
Донбасская государственная машиностроительная академия
Кафедра –
Автоматизированные металлургические машины и оборудование
ПОЯСНИТЕЛЬНАЯ ЗАПИСКА
к курсовой работе по дисциплине
"Технологические линии и комплексы металлургических цехов"
Выполнил
студент группы МО-03-2 А.С. Селедцов
Руководитель работы: Э.П. Грибков
2007
г.Краматорск
Реферат
Расчётно-пояснительная записка содержит стр., 2 таблицы,3 источника, 3 рисунка.
Основная задача данной курсовой работы – выбор цеха холодной прокатки, прокатного стана и разработка технологического процесса для производства листа шириной 1400мм и толщиной 0,35мм из стали 08кп производительностью 800 тысяч тонн в год.
В ходе выполнения работы были рассмотрены станы холодной прокатки различной конструкции и производительности (реверсивные и непрерывные).
Для производства заданного проката был выбран Непрерывный стан 2030 Новолипецкого металлургического комбината. Описание его оборудования так же приводится в расчётно-пояснительной записке.
Графическая часть курсовой работы содержит план расположения оборудования цеха непрерывного стана и графики загрузки клетей прокатного стана.
цех холодная прокатка сталь производительность
ПРОКАТНЫЙ СТАН. НЕПРЕРЫВНЫЙ ТРАВИЛЬНЫЙ АГРЕГАТ. ШЕСТЕРЁННАЯ КЛЕТЬ. ОБЖАТИЕ. СИЛА ПРОКАТКИ. МОЩНОСТЬ ПРОКАТКИ. ЛЕТУЧИЕ НОЖНИЦЫ. МОТАЛКА. ОЧАГ ДЕФОРМАЦИИ. РОЛЬГАНГ.
Содержание
Введение
1 Станы холодной прокатки
1.1 Непрерывный стан 2500 Магнитогорского металлургического комбината
1.2 Непрерывный стан 1700 Мариупольского металлургического комбината им. Ильича
2 Непрерывный стан 2030 Новолипецкого металлургического комбината
3 Расчет энергосиловых параметров холодной прокатки. Математическое обеспечение
4 Определение технологических режимов прокатки листа 0.35×1400
5 Расчет производительности стана
6 Рекомендации по совершенствованию технологии прокатки
Заключение
Перечень ссылок
Приложение А – Графики распределения параметров прокатки по проходам
Приложение Б –Программа для расчёта энергосиловых параметров процесса прокатки
Введение
Основная часть получаемой стали проходит через прокатные цеха и лишь незначительное количество через литейные и кузнечные цеха. Поэтому развитию прокатного производства уделено большое внимание.
Курс «Технологические линии и комплексы металлургических цехов» является специальной дисциплиной, которая формирует у студентов профессиональные знания в области теории и технологии непрерывных металлургических линий и агрегатов.
В результате выполнения курсовой работы должны быть выполнены следующие разделы:
- разработать и описать технологические процессы в целом по участкам (агрегатам) и по отдельным операциям с проработкой вопросов непрерывности технологии;
- осуществить выбор по заданной производительности и размерам поперечного сечения листового проката стана холодной листовой прокатки, из существующих конструкций;
- произвести расчет распределения обжатий по проходам в клетях прокатного стана;
- выполнить расчеты усилий прокатки в каждой клети прокатного стана и мощности электроприводов;
- определить годовую производительность стана;
Выполнить автоматизацию технологических режимов обжатий.
В ходе выполнения курсовой работы закрепляются и расширяются знания, полученные при изучении курса «ТЛКМЦ», появляются навыки в выборе производственного оборудования, расчетах технологических режимов обжатий и энергосиловых параметров прокатки, использование при расчетах электронно-вычислительной техники.
1 Станы холодной прокатки
Способом холодной прокатки получают ленты, листы и полосы наименьшей толщины и шириной до 4600...5000мм.
Основными параметрами широкополосных станов является длина бочки рабочей клети (в непрерывных станах последней клети).
Для производства листовой холоднокатаной стали применяют реверсивные одноклетевые и последовательные многоклетевые станы.
По заданию наиболее подходящими являются 3 стана:
[ 3 ]
1.1 Непрерывный стан 2500 Магнитогорского металлургического комбината
Цех введен в эксплуатацию в 1968 г. Оборудование стана расположено в семи пролетах (рисунок 1).
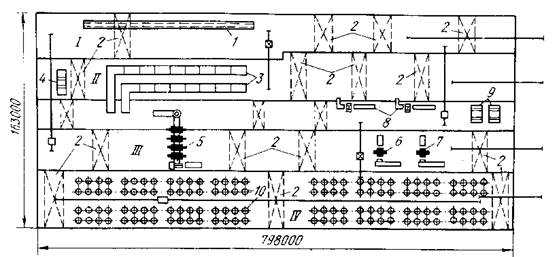
Рисунок 1. Схема основного технологического оборудования стана 2500 Магнитогорского металлургического комбината:
I - пролет склада горячекатаных рулонов, II - пролет НТА, III - пролет стана, IV - пролет колпаковых печей; 1 - конвейер передаточный горячекатаных рулонов, 2 - мостовые краны, 3 - непрерывно-травильные агрегаты, 4 - агрегат поперечной резки горячекатаных рулонов, 5 - рабочая линия стана, 6 - дрессировочный стан, 7 - дрессировочный стан 1700, 8 и 9 - агрегаты продольной и поперечной резки, 10 - колпаковые печи.
Стан предназначен для прокатки в холодном состоянии полос сечением (0,6-2,5) х (1250-2350) мм в 30-т рулон внутренним диаметром 800 мм, наружным 1950 мм из сталей 08Ю, 08кп, 08пс (ГОСТ 9045-80), сталей 08 - 25 всех степеней раскисления с химическим составом по ГОСТ 1050-74 и Ст0 - Ст3 кипящей, полуспокойной и спокойной (ГОСТ 380-71).
1.2 Непрерывный стан 1700 Мариупольского металлургического комбината им. Ильича
Первая очередь цеха холодной прокатки введена в эксплуатацию в 1963 г., оборудование стана расположено в 12 пролетах (Рисунок 2).
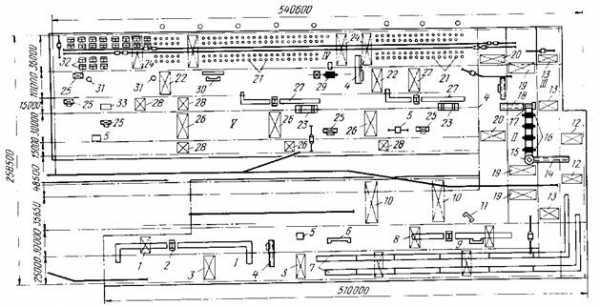
Рисунок 2. Схема расположения основного технологического оборудования стана холодной прокатки 1700 Мариупольского металлургического комбината им. Ильича:
I - склад горячекатаных рулонов, II - пролет стана, III - машинный зал, IV - пролет газовых колпаковых печей, V - склад готовой продукции; 1, 3, 8, 10, 12, 13, 19, 20, 22, 24, 26, 28 - мостовые краны, 2 - агрегат поперечной резки, 4 - конвейеры передаточные с кантователями, с5 - агрегаты упаковки пачек листов, 6 - ножницы, 7 - непрерывно-травильные агрегаты (НТА), 9 - комбинированный агрегат резки, 11 - гильотинные ножницы, 14 - конвейер подачи рулонов к стану, 15 - разматыватель, 16 - рабочая линия станов, 17 - моталка, 18 - конвейер отводящий, 21 - одностопные колпаковые печи, 23 - пакетирующие столы, 25 - весы, 27 - дрессировочные агрегаты, 29 - дрессировочная клеть, 30 - агрегат продольной резки, 31 - агрегаты упаковки рулонов, 32 - двухстопные колпаковые печи, 33 - пакетировочный пресс
Стан предназначен для холодной прокатки полос сечением (0,4-2,0) х (700-1500) мм в рулонах из сталей углеродистых обыкновенного качества (кипящей, спокойной, полуспокойной): Ст1, Ст2, Ст3, Ст4, Ст5; углеродистых качественных конструкционных: 08кп, 08пс, 10кп, 10пс, 10, 15кп, 15пс, 15, 20кп, 20пс, 20, 25, 30, 35, 40, 45; нестареющих 08Ю, 08Фкп; электротехнической стали.
Кипящие и спокойные стали поставляются по ГОСТ: 16523-70, 9045-70, 3560-73, 17715-72, 14918-69, 19851-74 и техническим условиям с химическим составом по ГОСТ 380-71 и 1050-74. Электротехническая сталь поставляется по ГОСТ 210142-75. [ 2 ]
2 Непрерывный стан 2030 Новолипецкого металлургического комбината
Из рассмотренных станов наиболее подходящим является Непрерывный стан 2030
Непрерывный пятиклетевой стан холодной прокатки 2030 предназначен для прокатки полос толщиной 0,35-2,0 мм при бесконечном режиме и 0,35-3,5 мм при порулонном из углеродистых и конструкционных сталей. При стане размещены: склад горячекатаных рулонов, травильное отделение, участок отделки горячекатаной продукции, термическое отделение и участки для отделки холоднокатаных листов и покрытий (рисунок 3).
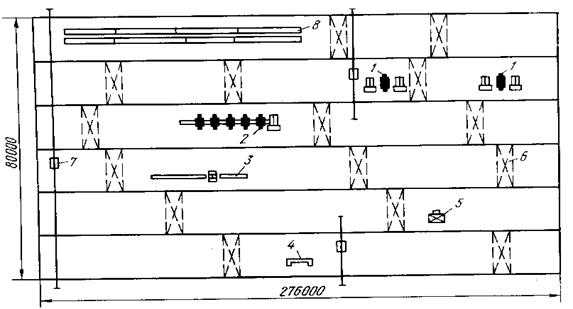
Рисунок 3. Схема основного технологического оборудования стана холодной прокатки 2030 Новолипецкого металлургического комбината:
1 - дрессировочные станы 2030; 2 - линия стана 2030; 3 - агрегат резки полосы; 4 - гильотинные ножницы; 5 - весы; 6 - мостовые краны; 7 - передаточная тележка; 8 - агрегаты непрерывного травления.
Подготовка металла к прокатке
Заготовкой для прокатки служат горячекатаные травленые полосы в рулонах, поступающие со стана 2000 горячей прокатки. Толщина полосы 1,8-6,0 мм, ширина 900-1850 мм.
В цехе установлены два агрегата непрерывного травления для удаления механической ломкой и химическим растворением в растворах соляной кислоты окалины с поверхности горячекатаных полос из углеродистой стали, свернутых в рулон.
Основные габариты агрегата: ширина 12 м, высота 10,95 м, длина 323 м, заглубление 9,6 м. Каждый агрегат включает: разматыватель рулонов, стыкосварочную машину, накопитель, ванны для травления, нейтрализации, промывки и очистки полос, сушильный агрегат, а также установку регенерации растворов.
Горячекатаные рулоны мостовым краном подают в вертикальном положении на устройство для транспортировки, кантуют в горизонтальное положение и выдают на приемную часть разматывателя.
В устройство для транспортировки рулонов входят: пластинчатый длиной 49,2 м транспортер с шагающими балками для 14 рулонов, измеритель ширины, кантователь грузоподъемностью 440 кН, транспортер с шагающей балкой для трех рулонов, машина для удаления обвязочной ленты, загрузочный цепной конвейер для пяти рулонов общей длиной 19,4 м (скорость транспортирования 9 м/мин), гидравлическая установка для обеспечения устройств транспортировки рулонов гидравлическим маслом с давлением 14 МПа.
Входная часть предназначена для размотки рулонов, обрезки передних и задних концов, вырезки дефектов, сварки полос встык для получения непрерывной полосы перед травлением. Загрузочная тележка имеет привод подъема от двух гидроцилиндров 280/160 и 1200 мм, привод перемещения - от 12-кВт двигателя постоянного тока.
Консольный четырехступенчатый разматыватель предназначен для размещения рулона, центрования по оси травильной линии и размотки полосы сверху. Отгибатель переднего конца полосы, тянущий и правильный агрегат служат для подачи переднего конца полосы от разматывателя до гильотинных ножниц, правки полосы и после обрезки подачи к сварочной машине. Толщина разрезаемого на ножницах металла 6,0 мм, ширина 1950 мм, максимальное усилие реза 625 МН, ход подвижного ножа 100 мм.
mirznanii.com
Как производят листовой металл
Как только человечество научилось обрабатывать металлы, оно научилось и производить листовую продукцию из них. Бронзовые пластины, например, использовались в качестве защитной брони. Современные способы и технологии обработки металла позволяют использовать продукцию металлопрокатной промышленности для производства сложных металлоконструкций, классических продуктов металлопроката и сырья для других отраслей промышленности. Возможности использования листового металла (листа нержавеющей стали) просто огромны. К примеру, это идеальный материал для строительства ангаров или крытых павильонов.
Безотходное производство – один из принципов работы современного предприятия. Особенно преуспели в организации таких производств в Японии. Там сумели устроить производственный цикл так, что отходов от нарезки металла практически не остается, и, в конечном итоге, используется весь произведенный материал. Нашим металлообрабатывающим предприятиям стоит использовать такой рациональный подход к делу.
Ранее, на большинстве наших предприятий, при конечной нарезке листов стали, в виде отходов оставались полосы металла. Современные технологии и грамотный подход к организации производства позволяют полностью переработать лист. Дополнительные детали и элементы вырабатываются из остатков и полос металла, ранее считавшихся отходами. Отдача от стандартного листа нержавеющей стали становится гораздо эффективнее.
Возможности современных предприятий металлопрокатной отрасли позволяют производить листовой металл по требованию и пожеланию заказчика. Безусловно, следует придерживаться принятых в нашей стране норм и стандартов при выполнении конкретных заказов.
Наше предприятие может полностью обеспечить требуемые заказчиком объемы, наших мощностей и профессионализма для этого вполне достаточно. Листы нержавеющей стали, полосы или уголок – весь ассортимент листового проката, сделанный с наивысшим качеством и в должный срок, может произвести наше предприятие.
Особенности листового производства
Многообразие размеров и форм, обширная область использования металлопроката – это результат многолетнего усовершенствования технологий и создание современного высокоточного оборудования. Нержавеющую сталь перерабатывают в несколько форм заготовок: листы, полосы, квадраты и круги. Одной из универсальных форм является лист. При изготовлении листовой стали применяется своя, особая технология, состоящая из нескольких важных этапов. Эти этапы имеют свои конкретные задачи – достижение высоких показателей прочности, долговечности, соблюдения установленных размеров и толщины листа.Одним из основных этапов при производстве листа является его охлаждение. Лист из нержавейки, проходя по толстолистовому стану, охлаждается в процессе продвижения по различным составляющим стана – шлепперам, рольгангам и транспортерным линиям. На станах конструкций, выпущенных ранее, листы охлаждают на цеховых плитах или в штабелях. Это служит одним из видов термической обработки листов, так называемый самоотпуск. Такой процесс насколько снижает допустимые пределы текучести и прочности на несколько кг на 1мм2, и повышает относительное удлинение. Ударная вязкость при таком способе остается неизменной. Такой способ охлаждения при необходимости применяется и на станах современной конструкции.
Охлаждению в ускоренном порядке подвергаются листы стали, которые необходимо испытать на ударную вязкость. В процессе такого охлаждения фиксируется получаемое при прокатке зерно и повышается результат ударной вязкости, особенно при минусовых значениях температур. Для более быстрого охлаждения всю поверхность листа обрабатывают водой с помощью распылителя, затем проводят обдувку воздухом. На толстолистовых прокатных станах современной конструкции, сразу за чистовой клетью, монтируется закалочная роликовая машина. Помимо своего прямого предназначения эта машина применяется и для более быстрого охлаждения листов перед их нормализацией в потоке.
В результате охлаждения листа улучшаются самые важные свойства стали. Последующие этапы прокатки и обработки снимают внутреннее напряжение металла и происходят некоторые изменения в структуре, повышающие свойства нержавеющей стали до должного уровня. Главное требование к процессу охлаждения, проводимому любым отработанным способом – это равномерное охлаждение всей поверхности листа по сечению и по всей плоскости поверхности.
Похожие статьи
znaytovar.ru
Эволюция прокатного стана. Листовой прокат. (Часть первая)
В центре повествования прокатные станы для горячего формования листового проката, как пример наиболее типичного представителя тяжелой металлургии в данной области.
Листовой прокат стал одним из основных видов сырья машиностроительной промышленности еще на заре индустриальной эпохи. Первые изделия на основе листовых заготовок производили методом горячей ручной ковки со времен первых Египетских фараонов. С тех пор и вплоть до середины 18-го века мало что изменилось в технологии обработки металлов. На помощь кузницам пришли водяные, а позже паровые молоты. Горны стали крупнее, а инструмент несколько более высокого качества.
В середине 18-го века был изобретен прокатный стан для горячего проката металлов, в первую очередь, стали. В те времена еще не было достаточно совершенных паровых машин для привода прокатных станов, да и общий уровень развития промышленности мало подходил для серийного изготовления крупных механизмов. Переворот произошел после изобретения паровой машины Уатта в начале 19-го века и первых индустриальных революций. Лидерами в этой области тогда являлись Великобритания, Пруссия, Франция, Бельгия и несколько других Европейских государств.
Первые прокатные станы представляли собой массивную конструкцию на основе литой станины с рамкой для монтажа валков, отсюда произошло название “клеть”. Масса первых станов достигала 10-15 тонн без паровой машины. Применение многоступенчатых редукторов с трапециевидными или эвольвентным зацеплением позволяло использовать двигатели небольшой мощности, всего 5-12 л.с. Но, все равно, водяной мельницы было явно мало для замены паровой машины, что и объясняет начало широкого внедрения прокатного стана в металлообрабатывающую промышленность только в 30-е годы 19-го века. Большая масса при малой производительности были обусловлены хрупкостью литой чугунной станины и малой частотой вращения валков. Большие скорости вращения валков (более 12 оборотов в минуту) и высокие нагрузки на заготовку были затруднительны в реализации по причине примитивности и низкого качества подшипников скольжения, применяемых в тех механизмах.
Позже, станину и клеть прокатного стана стали производить клепкой из уголка или простейшего швеллера методом ручной клепки. Такие станы имели в 1,5-2 раза меньшую массу при той же производительности и ресурсе. В конце 19-го века прокатные станы производили заводы более 30 стран мира, а для крепления основных элементов стали применять электродуговую сварку, что резко повысило ресурс при снижении стоимости и массы стана.
Одна из причин низкой производительности первых прокатных станов заключается в малой температуре нагрева заготовки, всего 500-600*С. Что было обусловлено малой прочностью материала валков и отсутствием водяного охлаждения валков. Сегодня валки производят из высококачественных легированных сталей, которые не изменяют своих прочностных свойств при нагреве до 900-1000*С. Это позволяет значительно повысить производительность станов, в том числе, при глубокой деформации заготовки за один проход. В середине 19-го века стали использовать станы с большим количеством клетей. До этого приходилось после одного прохода подхватывать заготовку краном и при помощи ручной тали доставлять в исходную точку, повторяя процесс проката. Это не только снижало качество изделий из-за многократного длительного нагревания заготовки, но и в разы уменьшало производительность производственной линии.
metallurg-invest.dp.ua
Лист холоднокатаный стальной – тонкости его изготовления + Видео
1 Лист холоднокатаный – ГОСТ и общие сведения
Холодная прокатка используется в тех случаях, когда требуется получить тонкие (менее 1 миллиметра) и высокоточные по параметрам листы и полосы стали, что недостижимо при применении горячекатаной технологии. Также прокат в холодном состоянии обеспечивает высокое качество физико-химических характеристик и отделки поверхности изделия.
Указанные достоинства обуславливают активное использование данного вида тонколистового проката и в цветной, и в черной металлургии наших дней (примерно половина тонколистового проката сейчас – это именно холоднокатаные листы).
Рекомендуем ознакомиться
Недостатком такой схемы является то, что она намного более энергоемка, нежели горячая прокатка. Вызвано это явлением наклепа (иначе говоря – деформации) стали в процессе проката, снижающего пластичные параметры конечного продукта. Для их восстановления приходится дополнительно осуществлять отжиг металла. Кроме того, описанный тип проката имеет технологию с немалым количеством различных переделов, для выполнения которых требуется использовать многообразное и технически сложное оборудование.
В цветной металлургии холоднокатаный процесс незаменим для выпуска медных, алюминиевых листов, полос и лент малой толщины. Чаще же всего он применяется для обработки конструкционных низкоуглеродистых сталей шириной до 2300 мм и толщиной не более 2,5 мм, без которых не может обойтись современное автомобилестроение. Прокаткой холодного типа производят практически все виды жести, а также:
- конструкционные низколегированные стали (в частности, трансформаторная и динамная электротехническая и нержавеющая сталь) – 45, 40Х, 09Г2С, 20, 65Г, 08кп, 08пс и др.;
- кровельные листы;
- травленый и отожженный декапир (металл для изготовления эмалированных изделий).
Согласно ГОСТ 9045–93, 19904–90 и 16523–97 тонколистовая продукция делится на различные типы в зависимости от:
- плоскостности: ПВ – высокая, ПО – особо высокая, ПН – нормальная, ПУ – улучшенная;
- точности: ВТ – высокая, АТ – повышенная, БТ – нормальная;
- качеству поверхности: высокая и особо высокая, а также повышенная отделка;
- виду кромки: О – обрезная, НО – необрезная;
- виду отпуска потребителям: в рулонах и в листах.
2 Как изготавливается холоднокатаный листовой прокат?
Такой прокат получают из горячекатаных листов (их толщина может достигать 6 мм, минимум – 1,8 мм), которые подаются в рулонах на участок холодной прокатки. Исходный материал на своей поверхности имеет оксиды (окалину). Их требуется удалять в обязательном порядке, так как оксиды снижают качество поверхности х/к листа за счет вдавливания в него. Также окалина вызывает ранний выход из строя прокатных валков. Понятно, что первым этапом технологической операции выпуска холодного проката становится удаление с горячекатаных листов этой самой окалины по одной из двух методик:
- механической: суть метода заключается в применении дробеструйной обработки поверхности полосы либо осуществлении ее пластической деформации;
- химической: окалину растворяют в кислотах.
Как правило, сейчас оба указанных метода используются комбинированно. Сначала проводится механическая обработка листов (предварительный этап) в агрегатах пластического растяжения, затем – химическая (основной) в травильных ваннах, содержащих соляную или серную кислоту. Более эффективным выглядит травление с применением соляной кислоты. Она быстрее справляется с вредными оксидами, обладая большей активностью. Да и качество поверхности металла после ее использования получается намного лучше. Кроме всего прочего, в промывных ваннах она полнее и легче удаляется с полос, что снижает себестоимость холоднокатаного листового проката.
После протравки рулонный материал подается на непрерывный стан (с четырьмя либо пятью клетями) холодной прокатки, в составе которого есть:
- разматыватели;
- ножницы;
- моталки;
- петлеобразующий механизм;
- стыкосварочный агрегат;
- летучие ножницы.
На цепном транспортере стальные рулоны отправляются в разматыватель, где они затягиваются в тянущие ролики. Оттуда полосы уходят на валки клети, оснащенной комплексом регулирования толщины полосы и нажимной гидромеханической установкой (гидроцилиндры, нажимной винт, толщиномер, месдоза, насос, регулирующее и управляющее устройство).
Полосы проходят через все клети, предусмотренные на стане, в которых выполняется их обжатие по заданным параметрам, а затем отправляются на барабан моталки (намотка на него осуществляется при помощи захлестывателя). После этого оборудование начинает функционировать на полную мощность со скоростью прокатки не менее 25 метров в секунду (все предыдущие операции производятся на скорости до 2 м/с, которую именуют заправочной). Когда в разматывателе остается не более двух витков полосы, стан вновь переводится в режим заправочной скорости.
Чтобы восстановить пластичность стали и устранить наклеп на холоднокатаных листах (он после процедуры холодной деформации неизбежен), выполняют рекристаллизационный отжиг при температуре около 700 градусов Цельсия. Процедура проходит в протяжных печах (они работают по непрерывной схеме) либо в колпаковых.
Затем сталь подвергается дрессировке – небольшое (от 0,8 до 1,5 процентов) финальное обжатие, необходимое для придания х/к листам заданных параметров. Полосы толщиной от 0,3 мм дрессируются в один пропуск. Данная операция характеризуются следующими положительными свойствами:
- увеличение прочности стали;
- снижение коробоватости и волнистости металлических полос;
- создание качественного микрорельефа поверхности;
- уменьшение (незначительное) предела текучести.
Самое же главное, что после дрессировки на поверхности листов не появляются линии сдвига (в противном случае они обязательно проступают в процессе штамповки).
3 Возможные дефекты при производстве листов методом холодной прокатки
Изъяны х/к листов отличаются разнообразием, зачастую они присущи определенному типу холоднокатаной продукции. В связи с тем, что толщина таких листов существенно меньше, чем у горячекатаных, чаще всего их дефекты связаны с волнистостью, продольной и поперечной разнотолщинностью, коробоватостью и некоторыми другими факторами, обусловленными несоблюдением точности форм и параметров проката. Разнотолщинность, в частности, вызывается следующими причинами:
- прокатка без требуемого натяжения конца полосы;
- изменение (из-за нагрева) сечения валков и температуры заготовки;
- неоднородная структура валков.
Нередко встречается и такой дефект, как нарушение сплошности стали (появление плены, трещин, дыр, расслоений, рваной кромки). Он обычно обусловлен невысоким качеством начальной заготовки. Также достаточно часто фиксируются отклонения по физико-химическим параметрам и структуре металла, которые возникают из-за нарушения режимов термообработки листов.
tutmet.ru