Сплавы с мелкозернистой структурой. Мелкозернистая структура
Мелкозернистая структура - Большая Энциклопедия Нефти и Газа, статья, страница 3
Мелкозернистая структура
Cтраница 3
Для получения мелкозернистой структуры проводят полный отжиг. При измельчении зерна снижается твердость стали, повышаются ее вязкость и пластичность, снимаются внутренние напряжения, улучшается обрабатываемость резанием. Изделия из такой стали реже выходят из строя при эксплуатации. Скорость нагрева в среднем составляет 100 С / ч, продолжительность выдержки - от 0 5 до 1 ч на 1 т нагреваемого металла. Из предыдущего известно, что в стали, нагретой выше критической температуры Ас3, мелкозернистый аустенит получается даже в том случае, если исходная структура крупнозернистая. [31]
При наличии мелкозернистой структуры возникает возможность упрочнения микрообъемов стали за счет выделения о-фазы в очень дисперсной форме. Мелкозернистая структура способствует также более равномерному распределению упрочняющих фаз, так как большая протяженность граничных зон облегчает процессы диффузии. С повышением температуры старения максимум сопротивляемости стали гидроэрозии смещается в сторону меньших выдержек при старении. Увеличение выдержки при повышенной температуре старения приводит к коагуляции избыточных фаз и снижению эрозионной стойкости стали. [32]
Для получения мелкозернистой структуры использовали осадку на молоте при 700 С и 30-мин отжиг при 1000 С. После такой обработки размер зерен был равен примерно 7 мкм, у - фаза находилась в основном в виде дисперсных частиц. Исследования показали, что дальнейший отжиг при 1000 С не приводит к значительному росту зерен - за 1 ч выдержки размер зерен увеличился только до 8 - 9 мкм. [34]
В случае мелкозернистой структуры подвижность дислокаций полностью блокируется границами зерен в поликристаллах из-за их разной ориентации, что не позволяет дислокациям, скользящим в одном кристалле, перейти в другой и приводит к скоплению их у границ зерен. Поэтому материалы с мелкокристаллической структурой имеют более высокие прочностные характеристики, чем монокристаллы с дислокационными включениями. [35]
Для получения мелкозернистой структуры в сталь вводят незначительное количество Ti, V, Al, которые образуют труднорастворимые мельчайшие частицы карбидов ( центров кристаллизации), препятствуют росту зерна и обеспечивают устойчивую мелкозернистость аустенита. [37]
Для получения мелкозернистой структуры, устранения химической и структурной неоднородности, уменьшения внутренних напряжений, понижения твердости стали для облегчения механической обработки производят отжиг или нормализацию. [38]
Керамическую плитку мелкозернистой структуры сортируют по цвету, форме и размерам, если из нее составляют образец определенного цвета и формы. Наиболее распространена плитка размером 10X10 см, укладываемая таким образом, чтобы пол был одно - или двухцветным. [40]
Для получения мелкозернистой структуры силумины необходимо модифицировать введением в жидкий сплав металлического натрия в количестве 0 1 % массы сплава или смеси хлористых и фтористых солей натрия и калия в количестве 2 - 2 5 % массы сплава. [42]
Для получения мелкозернистой структуры с целью повышения механических свойств сплавов применяют перегрев или модифицирование. Для измельчения зерна перегревом расплав нагревают в тигле до 850 - 900 С и выдерживают 15 - 20 мин до растворения тугоплавких соединений железа. При последующем быстром охлаждении до 700 С выделяются высокодисперсные частицы РеА12 являющиеся центрами кристаллизации. [43]
Обеспечивает получение равномерной мелкозернистой структуры, сообщает стали высокую прочность, пластичность и вязкост. [44]
За счет более мелкозернистой структуры изно - состойкость выше, чем у сплава ВК6, при не - сколько меньших эксплуатационной прочности и ] сопротивляемости ударам, вибрациям и выкра - пшзаншо. [45]
Страницы: 1 2 3 4
www.ngpedia.ru
Условия получения мелкозернистой структуры — Мегаобучалка
Стремятся к получению мелкозернистой структуры. Оптимальными условиями для этого являются: максимальное число центров кристаллизации и малая скорость роста кристаллов.
Размер зерен при кристаллизации зависит и от числа частичек нерастворимых примесей, которые играют роль готовых центров кристаллизации – оксиды, нитриды, сульфиды.
Чем больше частичек, тем мельче зерна закристаллизовавшегося металла.
Стенки изложниц имеют неровности, шероховатости, которые увеличивают скорость кристаллизации.
Мелкозернистую структуру можно получить в результате модифицирования, когда в жидкие металлы добавляются посторонние вещества – модификаторы,
По механизму воздействия различают:
1. Вещества не растворяющиеся в жидком металле – выступают в качестве дополнительных центров кристаллизации.
2. Поверхностно - активные вещества, которые растворяются в металле, и, осаждаясь на поверхности растущих кристаллов, препятствуют их росту.
Особенности строения металлического слитка
Схема стального слитка, данная Черновым Д.К., представлена на рис.3.7.
Рис. 3.7. Схема стального слитка
Слиток состоит из трех зон:
1. мелкокристаллическая корковая зона;
2. зона столбчатых кристаллов;
3. внутренняя зона крупных равноосных кристаллов.
Кристаллизация корковой зоны идет в условиях максимального переохлаждения. Скорость кристаллизации определяется большим числом центров кристаллизации. Образуется мелкозернистая структура.
Жидкий металл под корковой зоной находится в условиях меньшего переохлаждения. Число центров ограничено и процесс кристаллизации реализуется за счет их интенсивного роста до большого размера.
Рост кристаллов во второй зоне имеет направленный характер. Они растут перпендикулярно стенкам изложницы, образуются древовидные кристаллы – дендриты (рис. 3.8). Растут дендриты с направлением, близким к направлению теплоотвода.
Рис.3.8. Схема дендрита по Чернову Д.К.
Так как теплоотвод от незакристаллизовавшегося металла в середине слитка в разные стороны выравнивается, то в центральной зоне образуются крупные дендриты со случайной ориентацией.
Зоны столбчатых кристаллов в процессе кристаллизации стыкуются, это явление называется транскристаллизацией.
Для малопластичных металлов и для сталей это явление нежелательное, так как при последующей прокатке, ковке могут образовываться трещины в зоне стыка.
В верхней части слитка образуется усадочная раковина, которая подлежит отрезке и переплавке, так как металл более рыхлый (около 15…20 % от длины слитка)
Методы исследования металлов: структурные и физические
Металлы и сплавы обладают разнообразными свойствами. Используя один метод исследования металлов, невозможно получить информацию о всех свойствах. Используют несколько методов анализа.
Структурные методы исследования.
Применяют макроскопический и микроскопический анализ, рентгеноструктурный анализ.
Определение химического состава.
Используются методы количественного анализа.
1. Если не требуется большой точности, то используют спектральный анализ.
Спектральный анализ основан на разложении и исследовании спектра электрической дуги или искры, искусственно возбуждаемой между медным электродом и исследуемым металлом.
Зажигается дуга, луч света через призмы попадает в окуляр для анализа спектра. Цвет и концентрация линий спектра позволяют определить содержание химических элементов.
Используются стационарные и переносные стилоскопы.
2. Более точные сведения о составе дает рентгеноспектральный анализ.
Проводится на микроанализаторах. Позволяет определить состав фаз сплава, характеристики диффузионной подвижности атомов.
megaobuchalka.ru
Мелкозернистая структура - сплав - Большая Энциклопедия Нефти и Газа, статья, страница 1
Мелкозернистая структура - сплав
Cтраница 1
Мелкозернистая структура сплава получается путем интенсивного мокрого размола смеси и последующего спекания спрессованных изделий при пониженной температуре. [1]
В последних исследованиях установлено, что мелкозернистая структура сплавов образуется не в результате улучшения смачиваемости карбида титана связующей фазой с введением молибдена, а вследствие образования на начальной стадии спекания кольцевой структуры. [3]
Основные преимущества этого метода литья следующие: мелкозернистая структура сплава, получаемая вследствие большой скорости кристаллизации; повышенная плотность металла отливок и хорошие механические свойства их; снижение расхода металла. [4]
Благодаря этому коалесценция частиц твердого раствора происходит в меньшей мере и возможно получение более мелкозернистой структуры сплавов. [5]
Вольфрамовые твердые сплавы имеют твердость до 91 HRA, предел прочности при изгибе до 1700 МПа, красностойкость 800 - 850 С. Мелкозернистая структура сплава повышает его износостойкость, но уменьшает прочность, крупнозернистая - наоборот. Таким образом, например, в сплаве ВК6 - ОМ содержится 6 % кольбата, 2 % карбидов тантала и 92 % карбидов вольфрама с особо мелкозернистой структурой. [6]
Одним из методов получения сочетания высокой прочности, хорошей вязкости и свариваемости стали является уменьшение размера зерен, феррита. Мелкозернистую структуру сплавов можно сформировать принципиально различными способами - изменением температурных условий затвердевания слитка, легированием расплава элементами-модификаторами, определенной схемой пластического деформирования слитков и листов. [7]
Механизация и автоматизация обеспечивают высокую производительность при значительном снижении трудоемкости и стоимости отливок. Вследствие быстрого затвердевания получается мелкозернистая структура сплава, что определяет его высокие механические свойства. Отливки получают с высокой точностью по размерам и чистой поверхностью, что уменьшает или совсем исключает их последующую механическую обработку. [8]
Эффект же старения зависит от количества магния и кремния в сплаве, содержание которых можно держать на верхнем пределе. Повышенное содержание марганца в сплаве можно считать полезным, поскольку оно обеспечивает мелкозернистую структуру сплава. [9]
С из жидкого расплава одновременно выделяются кристаллы свинца и сурьмы. Выделяясь одновременно, они затрудняют рост друг друга, в результате чего образуется тонкая, мелкозернистая структура сплава - механическая смесь кристаллов свинца и сурьмы. [11]
Также печь может некоторое время эксплуатироваться без подачи очистного газа, в качестве которого в большинстве случаев используют аргон. В результате обработки металла инертным газом обеспечивается получение алюминия высокого качества, имеющего высокую чистоту, мелкозернистую структуру сплава, что обеспечивает повышение свойств отливок. [12]
Свойства сплавов зависят также от размеров зерен карбидной фазы, поэтому сплавы с размером зерен от 3 до 5 мкм относят к крупнозернистым и обозначают буквой В, например, сплав ВК8 - В. Сплавы, состоящие, в основном, из зерен размером менее 1 мкм, считают особо мелкозернистыми и обозначают буквами ОМ, например, ВК 10 - ОМ. Мелкозернистая структура сплава повышает его износостойкость, но уменьшает прочность, крупнозернистая - наоборот. [13]
Заливку обычно проводят в горячие формы сразу же после их прокаливания. Для тонкостенных отливок из стали форма должна иметь температуру 800 - 1000 С, для отливок из алюминиевых сплавов 300 - 400 С. Для толстостенных же отливок заливку производят в холодные формы для обеспечения более мелкозернистой структуры сплава. После охлаждения отливок сыпучие наполнители легко удаляют при опрокидывании опок, отверждающиеся наполнители - на вибрационных выбивных решетках. При этом оболочка легко отстает и удаляется от поверхности отливки. Удаление остатков керамической оболочки, в частности в полостях и отверстиях, и окончательную очистку поверхности отливок осуществляют в результате кипячения в 50 % - ном растворе едкого кали. [14]
Таким образом, кристаллизация указанных сплавов резко отличается от кристаллизации чистых металлов. Сплавы кристаллизуются в интервале температур, а чистые металлы - при постоянной температуре. Это объясняется тем, что при указанном сочетании компонентов и температуре 246 С из жидкого сплава одновременно выделяются кристаллы свинца и сурьмы. Образуясь одновременно, они затрудняют рост друг друга, в результате чего создается мелкозернистая структура сплава. Сплавы указанной концентрации называют эвтектическими. [15]
Страницы: 1
www.ngpedia.ru
Мелкозернистая структура - Большая Энциклопедия Нефти и Газа, статья, страница 2
Мелкозернистая структура
Cтраница 2
Мелкозернистая структура поковок в сыром их виде обеспечивается: а) соблюдением правильного температурного интервала ковки ( см. стр. [16]
Мелкозернистая структура осадков, получаемых и этих растворов, обычно обусловлена величиной катодной поляризации, которая в цианидных растворах при достаточном содержании свободного цианида значительно больше, чем в кислых растворах солей тех же металлов. [17]
Мелкозернистая структура области расплавления связана с модифицирующим действием в основном марганца и церия, оагулированные в основном металле кристаллы марганца во зремя расплавления оттесняются к границе твердой и жидкой раз. Присутствие последних наблюдается на микроструктуре се - Ьчения шва ( фиг. [18]
Мелкозернистую структуру в сталях можно получить рекристаллизацион-ным отжигом, что особенно существенно для сталей, в которых отсутствуют полиморфные превращения. [19]
Нежелательна мелкозернистая структура с равноосными зернами феррита и перлита. Полосчатая ферритно-перлитная структура недопустима в тех случаях, когда ширина ферритных полос превышает 50 мкм. [20]
Излом мелкозернистой структуры образуется в результате трения металла при повторно-переменных нагрузках в местах появления трещин и надрывов. Если здоровая часть сечения изделия не в состоянии выдержать приложенной нагрузки, наступает внезапное разрушение, при котором образуется излом крупнозернистой структуры. [21]
Сплавы мелкозернистой структуры с повышенным содержанием кобальта ( ВКШМ, ВК15М) используют для изготовления мелкоразмерных инструментов ( сверл, метчиков, концевых и прорезных фрез) для обработки труднообрабатываемых материалов всех групп. [22]
Имеет мелкозернистую структуру и высокое сопротивление износу, она нечувствительна к перегревам, надежна при прокаливании, имеет высокую прочность и вязкость. [23]
При мелкозернистой структуре чередованием хрупких фаз ( вторичного и структурно-свободного цементита, а также мартенсита) и более вязких составляющих ( аустенита и эвтектоида) создается возможность получения высоких механических свойств. [24]
При мелкозернистой структуре металла примеси распределяются равномернее, чем при крупнозернистой структуре, а это способствует повышению эрозионной стойкости сплава. Следует указать, что в сплавах, состоящих из однородных твердых растворов, разрушение начинается не только на границах, но и внутри зерен. При разрушении микрообъемов прочность обычно нарушается либо в местах скопления дефектов, вокруг которых концентрируются большие напряжения, либо в тех местах, где металл оказывает меньшее сопротивление пластической деформации и быстро разупрочняется. [26]
Для получения мелкозернистой структуры необходимо строго регулировать температуру заливки металла и создавать условия для равномерного охлаждения отливок. [27]
Для получения мелкозернистой структуры деформирование полуфабрикатов на готовый размер ( за последний нагрев) следует проводить при температуре, лежащей ниже температуры фазового превращения на 40 - 50 С. В процессе предыдущего деформирования должна быть разрушена литая структура и измельчено макрозерно. [28]
Для получения мелкозернистой структуры в сталь вводят незначительное количество Ti, V, Al, которые образуют труднорастворимые мельчайшие частицы карбидов ( центров кристаллизации), препятствуют росту зерна и обеспечивают устойчивую мелкозернистость а у стен и та. [29]
Для получения мелкозернистой структуры, устранения химической и структурной неоднородности, уменьшения внутренних напряжений, понижения твердости стали для облегчения механической обработки производят отжиг или нормализацию. [30]
Страницы: 1 2 3 4
www.ngpedia.ru
Сплавы с мелкозернистой структурой
Литая структура железоуглеродистых и других сплавов оказывает значительное влияние на свойства готовых изделий. Это влияние в наибольшей степени выражено в отливках и заготовках, полученных специальными способами литья и, прежде всего, непрерывными. Высокое качество расплавов — одно из важнейших условий производства мелкозернистых отливок, получаемых при высоких скоростях охлаждения.
Для получения расплавов при производстве мелкозернистых отливок специальными способами литья использовали преимущественно плавку в вакуумных печах шахтного типа. Перед разливкой проводили глубокую очистку от неметаллических включений и обработку расплава методами физического воздействия. Экспериментальные исследования структуры и свойств сплавов выполнены на образцах и отливках, полученных в металлических формах.
Исследовано также влияние термической и термомеханической обработки на свойства антифрикционных сплавов. Результаты механических испытаний ряда сплавов с мелкозернистой структурой, полученных в металлических формах с интенсивным охлаждением, приведены в таблице. С уменьшением размеров зерна от 120… 150 мкм до 0,5… 15 мкм установлено более высокое повышение относительного удлинения сплавов в отливках по сравнению с изменением предела прочности.
Для получения расплавов при производстве мелкозернистых отливок специальными способами литья использовали преимущественно плавку в вакуумных печах шахтного типа. Перед разливкой проводили глубокую очистку от неметаллических включений и обработку расплава методами физического воздействия. Экспериментальные исследования структуры и свойств сплавов выполнены на образцах и отливках, полученных в металлических формах.
Исследовано также влияние термической и термомеханической обработки на свойства антифрикционных сплавов. Результаты механических испытаний ряда сплавов с мелкозернистой структурой, полученных в металлических формах с интенсивным охлаждением, приведены в табл. 3.22. С уменьшением размеров зерна от 120… 150 мкм до 0,5… 15 мкм установлено более высокое повышение относительного удлинения сплавов в отливках по сравнению с изменением предела прочности.
Механические свойства мелкозернистых сплавов
Сплав | 120… 150 мкм | 45…75 мкм | 0,5…15 мкм | |||
σв, МПа | δ,% | σв, МПа | δ,% | σв, МПа | δ,% | |
Эвтектоидная сталь (0,8 % С) после закалки и отпуска при 200 °С | 720…900 | 16…10 | 920…1160 | 23…35 | 1350…1550 | 37…85 |
Высоколегированная сталь 130Г14МФАЛ после аустенизации | 910…1120 | 50…58 | 1160…1380 | 71…85 | 1580…1780 | 105…175 |
Магниевый сплав с содержанием 30,7 % Си и 0,35 % Pb после гомогенизации с закалкой и старения | 140…190 | 3…6 | 230…280 | 7,5…12,5 | 310…420 | 110…230 |
Латунь ЛЦ40Ф0,2А0,5 после термомеханической обработки | 220…280 | 12…20 | 350…410 | 25…33 | 430…540 | 55…120 |
Интенсивное охлаждение наряду с общим повышением качества отливок позволяет снижать необходимое количество легирующих добавок, получать отливки с мелким зерном, переходить на производство микро- легированных и модифицированных сплавов. Уже при скоростях охлаждения 102…103 К/с в водоохлаждаемых кокилях антифрикционные сплавы системы медь-свинец, содержащие 0,5 % легирующих компонентов, имеют мелкозернистую структуру (с размерами зерна 0,5… 15 мкм), обеспечивающую в отливках относительное удлинение более 100 %. Мелкозернистые структуры с размерами зерен 0,6… 15 мкм получены при литье в водоохлаждаемые формы бронзы БрХ0,6, латуни ДА 80-ЗЛ, многих алюминиевых и цинковых сплавов.
Более мелкую микроструктуру в сплавах получают специальным микролегированием и термической обработкой. Виды и режимы обработки зависят от природы сплавов. Сверхбыстрое охлаждение способствует переводу, например, медных, цинковых и алюминиевых сплавов в состояние структурной сверхпластичности. Одним из необходимых условий получения высокой пластичности является наличие в отливках сверхмелкого зерна. В таблице приведены составы ряда сверхпластичных цветных сплавов, обладающих ультрамелкозернистой структурой.
С каждым годом все большее применение получают мелкозернистые FeC-сплавы и композиции триботехнического назначения и эффективные методы термической, химико-термической и термогальванической обработки деталей машин, механизмов и технологической оснастки, работающих в условиях интенсивного трения, коррозионно-механического и ударно-абразивного износа. В заготовительных цехах машиностроительных предприятий новые инструментальные и конструкционные материалы и эффективные ресурсосберегающие малоотходные технологии используются для получения быстроизнашиваемых износостойких деталей и оснастки. В литейных, кузнечных цехах и других заготовительных цехах машиностроительных объединений особенно интенсивно используются индукторы и индукционные установки для ускоренного нагрева заготовок под закалку, нормализацию и другие виды термической обработки.
Индукторы выполняются с бетонированными секциями или со сборными жаропрочными изоляционными втулками из керамики. Впервые индукционные нагреватели типа КИН были использованы на заводе «Индуктор» (г. Новозыбков Брянской области) на основе разработок ВНИИТВЧ им. В.П. Вологдина (г. Санкт-Петербург). Их конструкция стала базовой при проектировании и изготовлении многих типов нагревателей для кузнечных, литейных и термических цехов. Хорошей компактностью и простотой обслуживания отличаются индукторы типа КИН, разработанные на «МАЗе» (г. Минск). Только в кузнечных цехах ПО «БелавтоМАЗ» установлено более 50 кузнечных индукционных нагревателей. Многие из них оборудованы системой автоматизированной загрузки заготовок.
Составы и области применения ультрамелкозернистых цветных сплавов
Наименование и состав сплавов по содержанию основных компонентов | Условия наступления сверхпластичности при статическом нагружении | Величина относительного удлинения, % | Область применения |
Алюминиевый сплав, содержащий 12 % кремния, 4 % меди и алюминий — остальное | При температуре 500 °С и мелкозернистой структуре отливок (величина зерна 0,5… 10 мкм) | 100…200 | В машиностроении в качестве литейного антикоррозионного сплава |
Медные сплавы, содержащие 10… 12 % алюминия, 1… 3 % железа и медь — остальное | При температуре более 830 °С и величине зерна 0,2… 15 мкм | 100…500 | В качестве литейного антифрикционного сплава в машиностроении |
Цинковые сплавы, содержащие 20…22 % алюминия, до 2 % меди, до 2 % магния и цинк — остальное | При температуре 250…275 °С и величине зерна до 10 мкм | 1500…3000 | В автомобильной и авиационной промышленности |
Титановый сплав с содержанием 6 % алюминия, 4… 6 % ванадия и титан — остальное | При размере зерен 0,05… 10 мкм и температуре 900…980 °С | 180…1000 | В авиационной промышленности |
На заводах ПО «Гомсельмаш» также используются индукционные и электроконтактные нагреватели при изготовлении заготовок и деталей кормоуборочных комбайнов из конструкционных и инструментальных сталей с массой до 30 кг. Индукционный и электроконтактный нагрев позволяет регулировать температуру и скорость нагрева при отсутствии окалины обезуглероженного слоя на деталях и повышенного угара при процессах закалки и нормализации.
Распространенный способ получения мелкозернистой структуры — рекристаллизационный отжиг холоднонаклепанного материала. При этом материал деформируют се= 30…50 % и медленно (v = 0,5 %) нагревают до температуры отжига. Размер зерна после такой обработки — не более 14 мкм. Более перспективным является метод скоростного нагрева наклепанного материала — таким способом удается значительно уменьшить размер зерна.
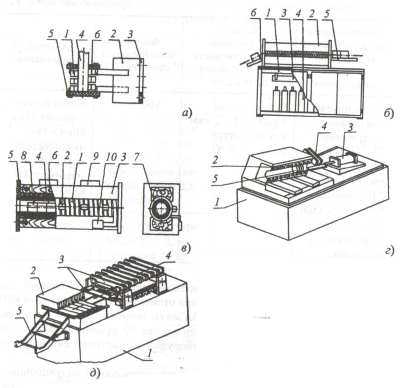
Экспериментальные исследования, проведенные на микролегированных литейных сталях типа 15М05Ф02Л и 20M05T03J1 с мелкозернистой структурой и карбонитридным упрочением, показали, что при использовании высоких скоростей охлаждения при термомеханической обработке, в антифрикционных изделиях увеличивается количество дефектов кристаллической решетки, повышаются прочность и износостойкость при низких температурах. После термомеханической обработки стали обладали высокой пластичностью (δ> 35 %) и динамической прочностью (σн> 1,5 МДж/м2).
Наиболее высокое повышение пластичности после термомеханической обработки получено на ряде эвтектических цветных сплавов, отливки из которых получены горячей экструзией, литьем под давлением на машинах с холодной камерой прессования и на валках с водяным охлаждением. Например, при температуре испытаний более 0,5 температуры плавления и скорости деформации 10-4… 10-2 с -1 эвтектические сплавы на основе цинка и алюминия с величиной зерна 0,5…7,5 мкм обладали относительным удлинением более 260 %. Испытания показали хорошую прирабатываемость сплавов алюминий-цинк в паре со сталями. Коэффициент трения у сплавов эвтектического состава уменьшается при снижении дисперсности структуры.
Материалы и сплавы с ультрамелкозернистой структурой обладают рядом важных свойств: высокой прочностью при низких (криогенных) температурах, сверхпластичностью при повышенных температурах, повышенной долговечностью при испытаниях на усталость вследствие затруднения образования усталостных трещин.
Для большинства условий воздействия изнашивающих нагрузок оптимальная износостойкость деталей и минимальный износ достигались при характерных для каждого конкретного случая структурных состояниях литого сплава с дисперсной структурой зерна. Показатели эксплуатационных свойств: коэффициент трения, его стабильность и износ — являются интегральными, определяемыми комплексом механических, теплофизических, химических и других свойств сплавов в отливках. При жестких режимах трения с высокими давлениями и скоростями величина износа в значительной степени определяется усталостной прочностью, теплостойкостью и термической стойкостью сплавов.
Для повышения дисперсности структуры литых заготовок, надежности и долговечности их работы большое значение имеет внедрение таких ЦСЛИТ-процессов (специальных способов литья с интенсивным теплоотводом), как КЛИТ-процесс — при литье в специальные кокили; ЦСЛИТ — при центробежном литье в окрашенные и водоохлаждаемые изложницы,
НЦЛНИТ-процесс — при непрерывно-циклическом литье намораживанием цилиндрических заготовок, НГЛНТ-процесс — при непрерывном горизонтальном литье в кристаллизаторах с интенсивным теплоотводом и других процессов, обеспечивающих высокие скорости охлаждения чугуна (от 102 до 105 °С/с), отличающихся многообразием теплового взаимодействия при кристаллизации и затвердевании отливок и профильных заготовок.
В таблице приведены характеристики микроструктуры и физикомеханических свойств ВЧШГ при использовании ряда ССЛИТ-процессов в производственных условиях.
При литье в кокиль (КЛИТ-процесс), способом непрерывно-циклического литья намораживанием (НЦЛНИТ-процесс) и центробежным способом в окрашенные изложницы (ЦСЛИТ-процесс) получены втулки из высокохромистых чугунов, высококачественные литые детали гильз цилиндров двигателей, тяжелонагруженные муфты, втулки и другие антифрикционные отливки. При замене центробежного литья в накатанные формы на ЦСЛИТ-процесс в отливках из антифрикционных чугунов типа АВЧ-1 и АВЧ-2 достигается повышение прочности до 530…680 МПа, ударной вязкости, износостойкости и плотности отливок с 7,18 до 7,27 г/см3 при значительном уменьшении содержания расхода легирующих компонентов.
Для изготовления износостойких профильных заготовок с бейнитно- мартенситной структурой на установках УНГЛ-2 по НГЛИТ-процессу разработаны комплексные лигатуры на основе Ni, Mo, Си, V, Са и РЗМ, которые вводятся в металлоприемник при заливке расплавленного чугуна с температурой 1430… 1470 °С в измельченном виде до фракции 0,5… 3,5 мм. Низколегированный износостойкий чугун, содержащий 0,2… 0,7 % Сг; 1,2…2,6 % Si; 0,3…0,7 % Mn; 0,35…0,85 % Си; 0,07…0,25 % Ni; 0,13…0,27 % N; 0,15…0,5 % Ti; 0,05…0,15 % V; 0,05…0,35 % Al; 0,02… 0,35 % W; 0,03…0,07 % Ca и 0,02…0,08 % РЗМ имел высокие значения микротвердости по сечению профильных заготовок: микротвердость Н50 в центре профиля 0 120 мм — 3100…3280 МПа, а в поверхностной зоне профиля Н50 — 3680…3790 МПа. Ударная вязкость на образцах 10 х 10 х 55 мм с надрезом 0,2 мм из профиля 0 30 мм составляет 26…34 Дж/см2.
При литье в оболочковые формы и центробежным способом в накатанные формы характеристики механических свойств были ниже. Продолжены исследования по изучению предела коррозионной усталости, ударной вязкости и других механических свойств и дисперсности перлита в отливках из медистых (содержание меди 1,07… 1,23 %) чугунов, полученных различными способами литья. Вместе с медью при легировании вводили и 0,2…0,3 % молибдена.
Мелкозернистая структура получена в медистых чугунах при односторонней направленной кристаллизации. Эффективное влияние на измельчение зерна в микролегированных чугунах и углеродистых сталях оказывают ниобий и титан.
Можно утверждать, что медистые чугуны обладают высокой износостойкостью при трении со смазкой без загрязнений по стали 45Л, высокопрочному чугуну ВЧ45 и графитизированной стали, содержащей 0,21 % титана.
Повышение содержания меди и молибдена в чугуне соответственно до 1,07… 1,28 % и 0,7… 1,1 % способствует измельчению структуры и повышению предела коррозионной усталости, является радикальным средством для получения чугунных отливок со специальными свойствами и для работы в экстремальных условиях эксплуатации.
Также Вам будет интересно:
chiefengineer.ru
Мелкозернистая структура - Большая Энциклопедия Нефти и Газа, статья, страница 1
Мелкозернистая структура
Cтраница 1
Мелкозернистые структуры, полученные при быстром охлаждении, имеют более высокие антифрикционные и механические свойства. [2]
Мелкозернистая структура повышает износостойкость стальных и чугунных деталей вследствие повышенного сопротивления деформированию. Установлено, что при трении фиксированных абразивов по стали У8 относительный износ ее с увеличением твердости понижается. [4]
Мелкозернистая структура способствует увеличению вязкости материала и повышает работоспособность мембран уже при обычной температуре, а исследование влияния зерна на сопротивление ползучести для различных материалов в дальнейшем может облегчить поиск недефицитных материалов для мембран, равноценных платине и палладию, которым отдается предпочтение из-за их удовлетворительного сопротивления ползучести. [5]
Мелкозернистая структура на поверхности детали повышает сопротивление усталости, что достигается модифицированием2 структуры. [6]
Мелкозернистая структура получается при нагреве холодного проката до 950 - 970 С. При этом повышается стойкость против меж-криеталлитной коррозии, но резко снижается стабильность свойств ( сопротивление ползучести) по сравнению с нормализацией при 1 100 С. TinNimC) при наличии в нем сг-фазы. [7]
Мелкозернистая структура, состоящая из феррита и перлита. [8]
Мелкозернистая структура во время затвердевания образуется при быстром охлаждении. [9]
Мелкозернистая структура также препятствует образованию трещин и улучшает стабильность размеров отливок. [10]
Мелкозернистая структура поковок в сыром их виде обеспечивается: а) соблюдением правильного температурного интервала ковки ( см. стр. [11]
Мелкозернистая структура полиамида 6, показанная на рпс. Кристаллы имеют не круглую, а продолговатую форму. [12]
Мелкозернистая структура отливки и внутренние напряжения создают многочисленные центры кристаллизации графита. Это существенно ускоряет I и II стадии графи-тизации. Процесс графитизации сокращается до 10 - 15 час. [13]
Мелкозернистая структура поковок в сыром их виде обеспечивается: а) соблюдением правильного температурного интервала ковки ( см. стр. [14]
Мелкозернистая структура осадков, получаемых и этих растворов, обычно обусловлена величиной катодной поляризации, которая в цианидных растворах при достаточном содержании свободного цианида значительно больше, чем в. [15]
Страницы: 1 2 3 4
www.ngpedia.ru
Строение металлического слитка. Условия получения мелкозернистой структуры. Транскристаллизация.
Схема стального слитка (см. также Заготовки для ковки. Слитки.), данная Черновым Д.К.
Процесс кристаллизации. Кристаллизация металлов. Кристаллизация стали.Кристаллизация веществ. Кристаллизация чистого металла. Температура кристаллизации.
Рисунок 1 — Схема стального слитка
1 — мелкокристаллическая корковая зона; 2 — зона столбчатых кристаллов; 3 — внутренняя зона крупных равноосных кристаллов
Кристаллизация корковой зоны идет в условиях максимального переохлаждения. Скорость кристаллизации определяется большим числом центров кристаллизации. Образуется мелкозернистая структура. Жидкий металл под корковой зоной находится в условиях меньшего переохлаждения. Число центров ограничено и процесс кристаллизации реализуется за счет их интенсивного роста до большого размера.
Теория сплавов. Основы теории сплавов.
Рост кристаллов во второй зоне имеет направленный характер. Они растут перпендикулярно стенкам изложницы, образуются древовидные кристаллы – дендриты (рисунок 2). Растут дендриты с направлением, близким к направлению теплоотвода.
Рисунок 2 — Схема дендрита по Чернову Д.К.
Так как теплоотвод от незакристаллизовавшегося металла в середине слитка в разные стороны выравнивается, то в центральной зоне образуются крупные дендриты со случайной ориентацией.
Зоны столбчатых кристаллов в процессе кристаллизации стыкуются, это явление называется транскристаллизацией. Для малопластичных металлов и для сталей это явление нежелательное, так как при последующей прокатке, ковке могут образовываться трещины в зоне стыка.
Дефекты кристаллического строения. Точечные дефекты.Дефекты кристаллического строения. Линейные дефекты. Теория дислокаций. Плотность дислокаций.
В верхней части слитка образуется усадочная раковина, которая подлежит отрезке и переплавке, так как металл более рыхлый (около 15…20 % от длины слитка).
Условия получения мелкозернистой структуры
При изготовлении слитков стремятся к получению мелкозернистой структуры. Оптимальными условиями для этого являются: максимальное число центров кристаллизации и малая скорость роста кристаллов.
Размер зерен при кристаллизации зависит и от числа частичек нерастворимых примесей, которые играют роль готовых центров кристаллизации – оксиды, нитриды, сульфиды. Чем больше частичек, тем мельче зерна закристаллизовавшегося металла.
Стенки изложниц имеют неровности, шероховатости, которые увеличивают скорость кристаллизации.
Мелкозернистую структуру можно получить в результате модифицирования, когда в жидкие металлы добавляются посторонние вещества – модификаторы.
По механизму воздействия модификаторы различают:
- Вещества не растворяющиеся в жидком металле – выступают в качестве дополнительных центров кристаллизации.
- Поверхностно — активные вещества, которые растворяются в металле, и, осаждаясь на поверхности растущих кристаллов, препятствуют их росту.
www.mtomd.info