Стальная лента нагартованная – жесткость и прочность в действии. Нагартованная лента
Изготовление ленты стальной нагартованной
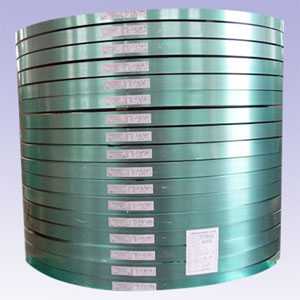
Лента стальная - изделие из холоднокатаной низкоуглеродистой стали, покрытое воском и тщательно обработанное по краям для улучшения условий эксплуатации. Лента покрывается антикоррозийным лаком. Покрытие облегчает протяжку, ускоряет процесс работы и удлиняет срок службы изделий. равномерному распределению веса в грузовой таре и предотвращения поломки и деформации грузов.
Лента стальная нагартованная отличается от простой стальной ленты специальным покрытием, увеличивающим ее прочность в разы. Нагартованная лента - изделие, покрытое слоем металла с помощью наклепа (центробежно-шарикового напыления).
Нагартованная лента прочная, не вязкая, непластичная, устойчивая к деформации и разрывам.
Нагартованная лента применяется в тех отраслях, где необходимы перевозки грузов нестандартных габаритов, подверженных частой деформации и смещениям. Там, где стальная лента лопнет или придет в негодность, нагартованная сохранит свою первоначальную прочность и форму.
Сфера применения ленты нагартованной достаточно широка. Ее используют для упаковки крупных грузов, которые быстро теряют первоначальную форму, подвержены ударам и падениям. Для упаковки нестойких к воздействию температурной среды предметам, рассыхающимся и склонным к деформациям деревянным видам упаковкам (деревянных овощехранилищах).
Металлическую нагартованную ленту используют для укрепления любой ящичной тары, для скрепления катушек, трубопровода, прикрепления утеплителя на пространствах, подверженных воздействию внешней среды, для закрепления груза на стационарных и мобильных платформах.
В ленте для скрепления перфорируются специальные отверстия, просечки, в которые крепятся пломбы или замозатягивающиеся замки. Лента из-за своей малой упругости лучше поддается скреплению при помощи механического или пневматического инструмента.
www.geliosmet.ru
Наклеп и нагартовка - упрочнение металла: особенности и отличия
Задача упрочнения поверхностного слоя металлического изделия является достаточно актуальной во многих случаях, ведь большая часть деталей машин и различных механизмов работает под воздействием значительных механических нагрузок. Решить такую задачу позволяет как наклеп, так и нагартовка, которые, несмотря на свою схожесть, все же имеют определенные различия.
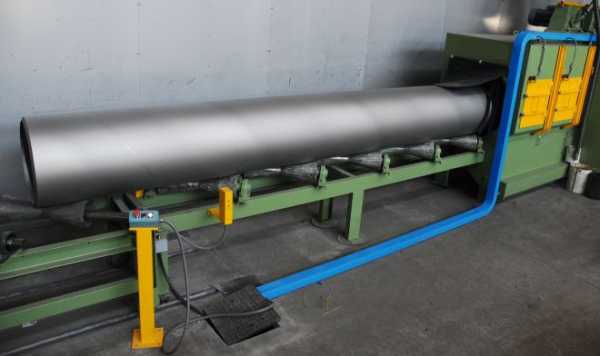
На производстве проблема упрочнения металлических поверхностей решается с помощью специального оборудования
Сущность наклепа и нагартовки
Наклеп металла является одним из способов упрочнения металлического изделия. Происходит это благодаря пластической деформации, которой такое изделие подвергают при температуре, находящейся ниже температуры рекристаллизации. Деформирование в процессе наклепа приводит к изменению как внутренней структуры, так и фазового состава металла. В результате таких изменений в кристаллической решетке возникают дефекты, которые выходят на поверхность деформируемого изделия. Естественно, эти процессы приводят и к изменениям механических характеристик металла. В частности, с ним происходит следующее:
- повышается твердость и прочность;
- снижаются пластичность и ударная вязкость, а также сопротивляемость к деформациям, имеющим противоположный знак;
- ухудшается устойчивость к коррозии.
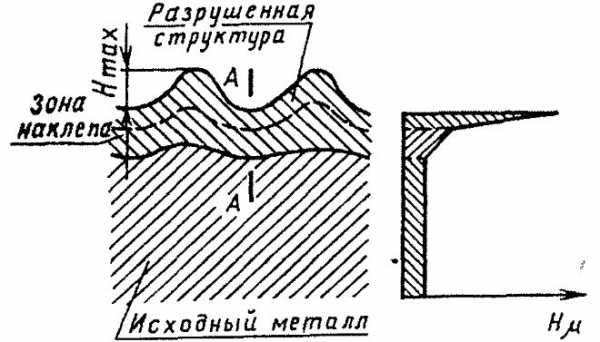
Упрочнение поверхности металла можно оценить по изменению микротвердости, уменьшающейся про мере удаления от поверхности
Явление наклепа, если оно относится к ферромагнитным материалам (например, к железу), приводит к тому, что у металла увеличивается значение такого параметра, как коэрцитивная сила, а его магнитная проницаемость снижается. Если наклепанная область была сформирована в результате незначительной деформации, то остаточная индукция, которой характеризуется материал, снижается, а если степень деформации увеличить, то значение такого параметра резко возрастает. Из положительных последствий наклепа следует отметить и то, что с его помощью можно значительно улучшить эксплуатационные характеристики более пластичных металлов, создающих значительное трение в процессе использования.
Наклепанный слой на поверхности металлического изделия может быть сформирован как специально, тогда такой процесс является полезным, так и неумышленно, в таком случае его считают вредным. Чаще всего неумышленное поверхностное упрочнение металлического изделия происходит в процессе обработки резанием, когда на обрабатываемый металл оказывается значительное давление со стороны режущего инструмента.
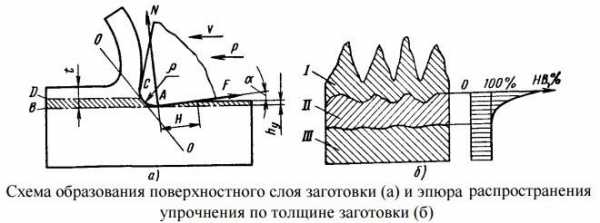
Упрочнение (наклеп) при обработке резанием
Увеличение прочности приводит к тому, что поверхность металла становится и более хрупкой, что является очень нежелательным последствием обработки.
Если формирование наклепа может произойти в результате как осознанных, так и неосознанных действий, то нагартовка всегда выполняется специально и является, по сути, полноценной технологической операцией, цель которой состоит в поверхностном упрочнении металла.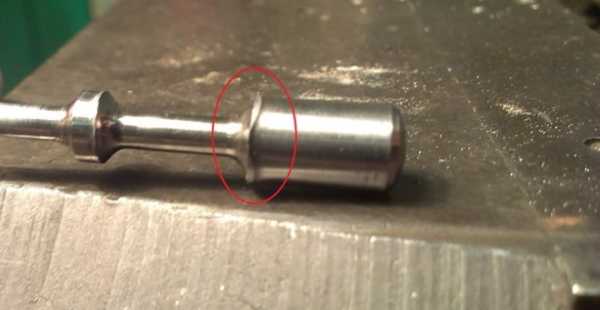
Деформационное уплотнение кромки этого затвора произошло в результате эксплуатации, значит – это наклеп
Типы наклепа
Различают два основных типа наклепа, которые отличаются процессами, протекающими при его формировании в материале. Если новые фазы в металле, характеризующиеся иным удельным объемом, сформировались в результате протекания фазовых изменений, то такое явление носит название фазового наклепа. Если же изменения, произошедшие в кристаллической решетке металла, произошли из-за воздействия внешних сил, они называются деформационным наклепом.
Деформационный наклеп, в свою очередь, может быть центробежно-шариковым или дробеметным. Для выполнения наклепа первого типа на обрабатываемую поверхность воздействуют шариками, изначально располагающимися во внутренних гнездах специального обода. При вращении обода (что выполняется на максимальном приближении к обрабатываемой поверхности) шарики под воздействием центробежной силы отбрасываются к его периферии и оказывают ударное воздействие на деталь. Формирование наклепа в дробеструйных установках происходит за счет воздействия на обрабатываемую поверхность потока дробинок, перемещающихся по внутренней камере такого оборудования со скоростью до 70 м/с. В качестве таких дробинок, диаметр которых может составлять 0,4–2 мм, для наклепа могут быть использованы чугунные, стальные или керамические шарики.
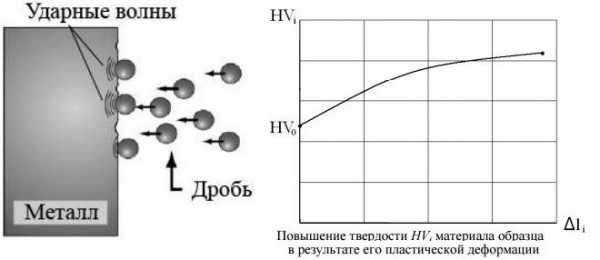
Схема традиционного деформационного наклепа и график повышения твердости материала
Для того чтобы понимать, почему нагартовка или формирование наклепа приводят к упрочнению металла, следует разобраться в процессах, которые протекают в материале при выполнении таких процедур. При холодной пластической деформации, происходящей под воздействием нагрузки, величина которой превышает предел текучести металла, в его внутренней структуре возникают напряжения. В результате металл будет деформирован и останется в таком состоянии даже после снятия нагрузки. Предел текучести станет выше, и его значение будет соответствовать величине сформировавшихся в материале напряжений. Чтобы деформировать такой металл повторно, необходимо будет приложить уже значительно большее усилие. Таким образом, металл станет прочнее или, как говорят специалисты, перейдет в нагартованное состояние.
При холодной деформации металла, протекающей в результате воздействия соответствующего давления (в процессе, например, наклепа), дислокации, составляющие внутреннюю структуру материала, начинают перемещаться. Даже одна пара движущихся дефектных линий, сформировавшихся в кристаллической решетке, способна привести к образованию все новых и новых подобных локаций, что в итоге и повышает предел текучести материала.
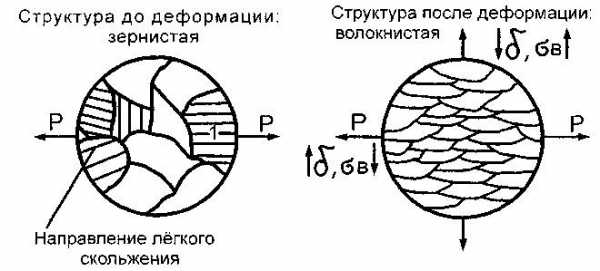
Изменение структуры поверхностного слоя в результате холодной деформации
Внутренняя структура металла при его деформировании в процессе выполнения наклепа или нагартовки претерпевает серьезные изменения. В частности, искажается конфигурация кристаллической решетки, а пространственное положение кристаллов, которые ориентированы беспорядочно, упорядочивается. Такое упорядочивание приводит к тому, что оси кристаллов, в которых они обладают максимальной прочностью, располагаются вдоль направления деформирования. Чем активнее будет выполняться деформирование, тем большее количество кристаллов примут подобное пространственное положение. Существует ошибочное мнение, что зерна, составляющие внутреннюю структуру металла, при его деформации измельчаются. На самом деле они только деформируются, а площадь их поверхности остается неименной.
Из всего вышесказанного можно сделать вывод о том, что в процессе выполнения нагартовки или наклепа изменяется кристаллическая структура стали или другого металла, в результате материал становится более твердым и прочным, но одновременно и более хрупким. Нагартованная сталь, таким образом, представляет собой материал, который специально был подвергнут пластической деформации для улучшения прочностных характеристик.Нагартовка и оборудование для нее
Выполнение нагартовки изделий из стали особенно актуально в тех случаях, когда имеется необходимость повысить их устойчивость к поверхностному растрескиванию, а также предотвратить протекание в нем усталостных процессов. Отраслями промышленности, в которых нагартованные изделия зарекомендовали себя особенно хорошо, являются авиа- и автомобилестроение, нефтедобыча, нефтепереработка и строительство.
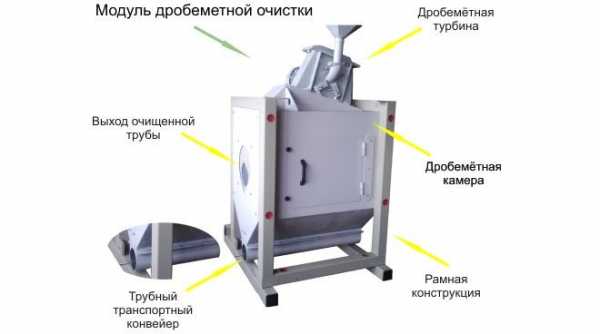
Устройство промышленной дробомётной установки для обработки труб
Такие методы упрочнения металлов, как контролируемый наклеп или нагартовка, могут быть реализованы при помощи различного оборудования, от качества и функциональности которого зависит результат выполняемых операций. Оборудование для нагартовки изделий из стали или других сплавов, которое сегодня представлено большим разнообразием моделей, может быть общего назначения или специального – для того, чтобы выполнять обработку деталей определенного типа (болтов, пружин и др.).
В промышленных масштабах нагартовка выполняется на автоматизированных устройствах, все режимы работы которых устанавливаются и контролируются за счет использования электронных систем. В частности, на таких станках автоматически регулируется как количество, так и скорость подачи дроби, используемой для выполнения обработки.

Дробометная установка для обработки листового и профильного металлопроката
Выполнение наклепа, при котором процесс его формирования контролируется, используется в тех случаях, когда изделие из стали нет возможности упрочнить при помощи термической обработки. Помимо нагартовки и наклепа повысить прочность поверхностного слоя металлического изделия могут и другие методы холодной пластической деформации. Сюда, в частности, относятся волочение, накатка, холодная прокатка, дробеструйная обработка и др.
Кроме стали, содержание углерода в которой не должно превышать 0,25%, такой способ упрочнения необходим изделиям из меди, а также некоторым алюминиевым сплавам. Нагартовке также часто подвергается лента нержавеющая. Ленту нагартованную применяют в тех случаях, когда обычная лента нержавеющая не способна справляться с воспринимаемыми нагрузками.
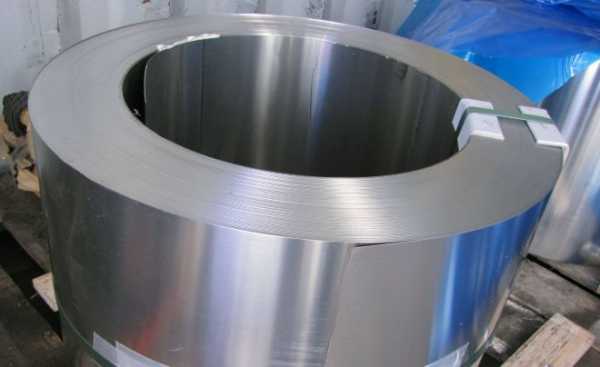
Нагартованная нержавеющая лента обладает более высокой прочностью с определенной потерей вязкости и пластичности
Наклеп, который сформировался на поверхности металлического изделия в процессе выполнения его обработки различными методами, можно снять, для чего используется специальная термическая обработка. При выполнении такой процедуры металлическое изделие нагревают, что приводит к тому, что атомы его внутренней структуры начинают двигаться активнее. В результате она переходит в более устойчивое состояние.
Выполняя такой процесс, как рекристаллизационный отжиг, следует учитывать степень нагрева металлической детали. Если степень нагрева незначительна, то в структуре металла снимаются микронапряжения второго рода, а его кристаллическая решетка частично искажается. Если интенсивность нагрева увеличить, то начнут формироваться новые зерна, оси которых сориентированы в одном пространственном положении. В результате интенсивного нагрева полностью исчезают деформированные зерна и формируются те, оси которых ориентированы в одном направлении.
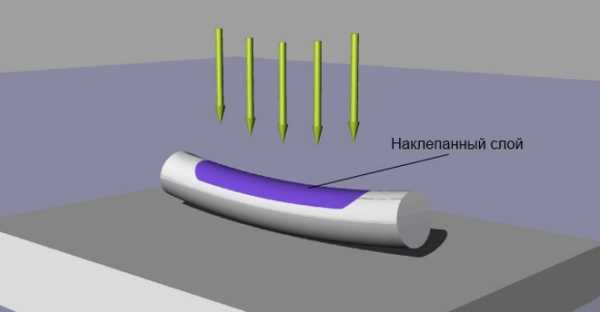
Ручная правка наклепом изогнутого вала
Существует также такая технологическая операция, как правка наклепом, при помощи которой металлический вал или лист приводятся в исходное состояние. Чтобы выполнить такую операцию, нацеленную на устранение несоответствий геометрических параметров их требуемым значениям, нет необходимости использовать специальный станок – ее выполняют при помощи обычного молотка и ровной плиты, на которую укладывается обрабатываемое изделие. Нанося таким молотком удары по изделию, форму которого требуется исправить, добиваются формирования на его поверхности наклепанного слоя, что в итоге приведет к достижению требуемого результата.
На видео ниже показан процесс упрочнения методом наклепа колес для железнодорожной техники в дробеметной установке.Оценка статьи:
Загрузка...Поделиться с друзьями:
met-all.org
Стальная лента нагартованная - ЛентаПак
Выбрать металлическая лента по параметрам, фото, стоимости.
Если взять обычную стальную полосу, которая на профессиональном жаргоне называется штрипс, и наклепать на нее дополнительный слой, то получится стальная лента нагартованная с отличными техническими показателями. Особая технология производства способствует повышению показателей прочности. Благодаря металлическому напылению лента утрачивает критерии пластичности и способность поглощать энергию нагрузки от ударов или деформации, что способствует ее эффективному использованию при упаковке грузов с большим весом и габаритами, при создании тары из дерева, при работе с материалами для утепления.
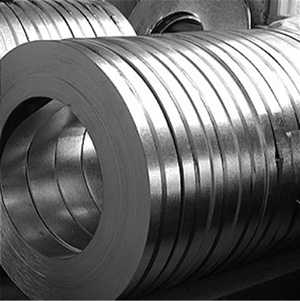
Технология производства предполагает наличие особого процесса гартования, при помощи которого улучшаются критерии жесткости и прочности. Как результат – возможность работы с тяжелыми грузами. Нагартованная лента неспособна к удлинению и растяжению. Однако перегрузки при сильных ударах могут стать причиной разрыва стальной ленты.
Данный вид стального материала обладает следующими показателями: - шириной в 16, 19, 20 или 30 мм; - толщиной в 0,5 или 1,0 мм; - в бухте может быть как 260, так 780 или 1430 м; - вес бухты составляет 20 60 и 110 кг; - нагрузка на разрыв может достигать 610, 730, 765 и 1100 кгс; - внутренний диаметр бухты составляет 260 мм.
Сегодня к привлекательным качествам нагартованной ленты, которую можно купить на сайте компании «ЛЕНТАПАК», относят не только ее крепкость, но и проверенность, даже в том случае, если речь идет о работе в условиях высоких температур.
В качестве антикоррозийного материала стальная лента нагартованная может покрываться цинком или краской черного цвета. Данное покрытие является элементом экономии, выражаемым в снижении количества упаковочных отходов, в том числе из-за коррозии. Если стальная лента нагартованная обладает достаточной жесткостью и прочностью, то иные варианты подобного материала могут быть очень гибкими, но не менее прочными.
lentapack.ru
способ производства стальной нагартованной ленты - патент РФ 2369649
Изобретение относится к прокатному производству, в частности к технологии изготовления стальной упаковочной ленты. Для получения требуемых механических свойств и качества поверхности ленты горячекатаную полосовую сталь толщиной 2,0-2,8 мм, содержащую, мас.%: 0,08-0,15 углерода, 0,05-0,10 кремния и 0,4-0,7 марганца, подвергают предварительному отжигу в колпаковых печах с выдержкой 4 ч при температуре t1=500°C и с выдержкой 10 ч при t2=560°C с общим временем нагрева 20 ч, а затем ведут холодную прокатку на конечную толщину h=0,5-1,0 мм, принимая величину суммарного обжатия , %, где 212, 2,3 - эмпирические параметры, полученные опытным путем при уставке номинальной толщины в чистовой клети непрерывного стана, после чего металл подвергают окончательному отжигу с нагревом до 400°С и выдержкой при этой температуре 10 ч, снижая в последующем, до окончания времени нагрева, температуру до 380°С, и отожженую ленту подвергают дрессировке с обжатием 0,2-0,7%.
Изобретение относится к прокатному производству и может быть использовано в технологии изготовления стальной нагартованной ленты, применяемой, например, для упаковки готового проката.
Технология производства узкого полосового проката (ленты) во многом идентична технологии для широкополосного проката, но имеет и ряд особенностей. Определения ленточной стали и ее прокатки приведены, например, в книге Д.Я.Гуревича «Краткий справочник прокатчика». М.: «Металлургия», 1955, с.145-146. Упаковочная лента делается из углеродистой стали, технология производства которой, включающая холодную прокатку, термообработку и дрессировку металла, достаточно подробно описана в книге В.Б.Бахтинова «Прокатное производство». М.: «Металлургия», 1987, с.337-346.
Известен способ изготовления ленты из нержавеющей мартенситно-стареющей стали, при котором перед холодной прокаткой ленту подвергают двойной правке растяжением с относительной степенью деформации 2 3% за проход, а прокатку ведут с уменьшением обжатия в каждом проходе в 1,3 2,0 раза (см. а.с. СССР № 998521, кл. С21D 9/52, опубл. в БИ № 7, 1983 г.). Однако этот способ не оговаривает технологию отжига и дрессировки полосового проката.
Наиболее близким аналогом к заявляемому способу является способ производства металлической ленты по а.с. СССР № 480457, кл. В21D 1/05, опубл. 10.10.75 г.
Этот способ включает холодную прокатку, термообработку и дрессировку тонкой ленты и характеризуется тем, что обжатие при прокатке принимают равным 50 75% и после каждых 15 25% обжатия осуществляют дополнительную правку полос. Известный способ также не приводит параметры отжига и дрессировки проката, что затрудняет получение требуемых механических свойств и качества поверхности ленты.
Технической задачей настоящего изобретения является получение требуемых механических свойств и качества поверхности стальной ленты.
Для решения этой задачи предлагаемый способ включает холодную прокатку, термообработку и дрессировку металла, а горячекатаную полосовую сталь толщиной 2,0 2,8 мм, содержащую 0,08 0,15 мас.% углерода, 0,05 0,10% кремния и 0,4 0,7% марганца, перед холодной прокаткой подвергают предварительному отжигу в колпаковых печах с выдержкой 4 ч при температуре t 1=500°С и с выдержкой 10 ч при t2=560°С с общим временем нагрева 20 ч, а затем прокатывают на конечную толщину 0,5 1,0 мм, принимая величину суммарного обжатия =212/(h+2,3), %, при уставке номинальной толщины в чистовой клети непрерывного стана, после чего металл подвергают окончательному отжигу с нагревом до 400°С и с выдержкой при этой температуре 10 ч, снижая в последующем, до окончания времени нагрева, температуру до 380°С, и термообработанную ленту подвергают дрессировке с обжатием 0,2 0,7%.
Приведенные параметры способа получены опытным путем и являются эмпирическими.
Сущность заявляемого технического решения заключается в оптимизации параметров технологии производства нагартованной ленты, т.е. поверхностно наклепанной (упрочненной) стальной полосы (см. «Толковый металлургический словарь» под ред. В.И.Куманина. М.: «Русский язык», 1989, с.177, 179). В результате этого получается лента, пригодная для упаковки сортового и листового проката при его транспортировке.
Опытную проверку предлагаемой технологии производства нагартованной ленты осуществляли в ОАО «Магнитогорский металлургический комбинат».
С этой целью перед холодной прокаткой стальной ленты на непрерывном стане 630 варьировали параметры предварительного отжига, при прокатке использовали разные величины , меняя уставку (т.е. межвалковый зазор) толщины в чистовой клети стана, варьировали параметры окончательного отжига и величину обжатия при дрессировке. Результаты опытов оценивали по выходу ленты с требуемыми мехсвойствами и качеством ее поверхности.
Наилучшие результаты (выход качественной ленты в пределах 99,1 99,7%) получены с использованием предлагаемой технологии; отклонения от рекомендуемых ее параметров ухудшали достигнутые показатели. Так, уменьшение времени выдержки, времени нагрева и температуры в колпаковых печах при предварительном отжиге вызывали необходимость уменьшения при прокатке (вследствие недостаточного разупрочнения стали при отжиге) для получения нагартованной ленты, что в ряде случаев приводило к получению проката с h>1,0 мм, хотя остальные требуемые параметры технологии соблюдались.
Увеличение времени выдержки и нагрева, а также температуры в печах приводили к получению ленты недостаточной прочности (не нагартованной), что наблюдалось и при уменьшении и увеличении уставки валков в чистовой клети. Уменьшение же величины уставки в отдельных случаях выводило конечную толщину h за пределы минусового допуска.
Снижение температуры окончательного отжига (менее 400°С) и времени выдержки при этой температуре (менее 10 ч), а также последующей температуры (менее 380°С) и повышение вызывали излишнее упрочнение прокатываемой полосы, что отрицательно сказывалось на ее продольном роспуске. Увеличение же этих параметров (кроме величины ) приводило в ряде случаев к получению не нагартованной ленты с в<780 МПа. При дрессировке с обжатием менее 0,2% прочность ленты снижалась, а при обжатии более 0,7% недопустимо ухудшалось качество поверхности готовой ленты.
Способ, выбранный в качестве ближайшего аналога, в опытах не проверялся по причинам, изложенным выше. Таким образом, опытная проверка подтвердила приемлемость найденного технического решения для достижения поставленной цели и его преимущество перед известным объектом.
Технико-экономические исследования показали, что использование настоящего изобретения при производстве нагартованной ленты позволит увеличить выход качественной продукции не менее чем на 3% при соответствующем росте прибыли от реализации проката с улучшенными свойствами.
Пример конкретного выполнения
Полосовая сталь, содержащая 0,12 мас.% углерода, 0,07% кремния и 0,5% марганца, перед холодной прокаткой подвергается предварительному отжигу в колпаковых печах с выдержкой 4 ч при t1=500°С и с выдержкой 10 ч при t2 =560°С с общим временем нагрева 20 ч.
При конечной толщине h=0,8 мм величина , т.е. исходная толщина полос должна быть равна .
Окончательный отжиг с нагревом до 400°С и выдержкой 10 ч при этой температуре со снижением температуры до 380°С. Обжатие при дрессировке 0,5%.
ФОРМУЛА ИЗОБРЕТЕНИЯ
Способ производства стальной нагартованной ленты, включающий предварительный отжиг горячекатаной полосовой стали толщиной 2,0-2,8 мм, содержащей, мас.% 0,08-0,15 углерода, 0,05-0,10 кремния, 0,4-0,7 марганца, в колпаковой печи при температуре t1 =500°С с выдержкой 4 ч и при t2=560°С с выдержкой 10 ч, с общим временем нагрева 20 ч, холодную прокатку на конечную толщину h=0,5-1,0 мм, принимая величину суммарного обжатия , %,где 212; 2,3 - эмпирические параметры, полученные опытным путем,при уставке номинальной толщины в чистовой клети непрерывного стана, окончательный отжиг с нагревом до 400°С и выдержкой при этой температуре 10 ч, снижая в последующем, до окончания времени нагрева, температуру до 380°С и дрессировку с обжатием 0,2-0,7%.
www.freepatent.ru
Наименование | Размер | Ед. изм. | Цена | Примечание |
Лента нагартованная | ||||
Лента нагартованная | 0,25 мм | тн | Договорная | нагартованная |
Лента нагартованная | 0,3 мм | тн | Договорная | нагартованная |
Лента нагартованная | 0,4 мм | тн | Договорная | нагартованная |
Лента нагартованная | 0,5 мм | тн | Договорная | нагартованная |
Лента нагартованная | 0,6 мм | тн | Договорная | нагартованная |
Лента нагартованная | 0,7 мм | тн | Договорная | нагартованная |
Лента нагартованная | 0,8 мм | тн | Договорная | нагартованная |
Лента нагартованная | 0,9 мм | тн | Договорная | нагартованная |
Лента нагартованная | 1,0 мм | тн | Договорная | нагартованная |
Лента нагартованная | 1,2 мм | тн | Договорная | нагартованная |
Лента нагартованная | 1,5 мм | тн | Договорная | нагартованная |
Лента нагартованная | 1,6 мм | тн | Договорная | нагартованная |
Лента нагартованная | 1,8 мм | тн | Договорная | нагартованная |
Лента нагартованная | 3,0 мм | тн | Договорная | нагартованная |
mosmetmarket.ru
Способ производства стальной нагартованной ленты
Изобретение относится к прокатному производству, в частности к технологии изготовления стальной упаковочной ленты. Для получения требуемых механических свойств и качества поверхности ленты горячекатаную полосовую сталь толщиной 2,0-2,8 мм, содержащую, мас.%: 0,08-0,15 углерода, 0,05-0,10 кремния и 0,4-0,7 марганца, подвергают предварительному отжигу в колпаковых печах с выдержкой 4 ч при температуре t1=500°C и с выдержкой 10 ч при t2=560°C с общим временем нагрева 20 ч, а затем ведут холодную прокатку на конечную толщину h=0,5-1,0 мм, принимая величину суммарного обжатия , %, где 212, 2,3 - эмпирические параметры, полученные опытным путем при уставке номинальной толщины в чистовой клети непрерывного стана, после чего металл подвергают окончательному отжигу с нагревом до 400°С и выдержкой при этой температуре 10 ч, снижая в последующем, до окончания времени нагрева, температуру до 380°С, и отожженую ленту подвергают дрессировке с обжатием 0,2-0,7%.
Изобретение относится к прокатному производству и может быть использовано в технологии изготовления стальной нагартованной ленты, применяемой, например, для упаковки готового проката.
Технология производства узкого полосового проката (ленты) во многом идентична технологии для широкополосного проката, но имеет и ряд особенностей. Определения ленточной стали и ее прокатки приведены, например, в книге Д.Я.Гуревича «Краткий справочник прокатчика». М.: «Металлургия», 1955, с.145-146. Упаковочная лента делается из углеродистой стали, технология производства которой, включающая холодную прокатку, термообработку и дрессировку металла, достаточно подробно описана в книге В.Б.Бахтинова «Прокатное производство». М.: «Металлургия», 1987, с.337-346.
Известен способ изготовления ленты из нержавеющей мартенситно-стареющей стали, при котором перед холодной прокаткой ленту подвергают двойной правке растяжением с относительной степенью деформации 2…3% за проход, а прокатку ведут с уменьшением обжатия в каждом проходе в 1,3…2,0 раза (см. а.с. СССР №998521, кл. С21D 9/52, опубл. в БИ №7, 1983 г.). Однако этот способ не оговаривает технологию отжига и дрессировки полосового проката.
Наиболее близким аналогом к заявляемому способу является способ производства металлической ленты по а.с. СССР №480457, кл. В21D 1/05, опубл. 10.10.75 г.
Этот способ включает холодную прокатку, термообработку и дрессировку тонкой ленты и характеризуется тем, что обжатие при прокатке принимают равным 50…75% и после каждых 15…25% обжатия осуществляют дополнительную правку полос. Известный способ также не приводит параметры отжига и дрессировки проката, что затрудняет получение требуемых механических свойств и качества поверхности ленты.
Технической задачей настоящего изобретения является получение требуемых механических свойств и качества поверхности стальной ленты.
Для решения этой задачи предлагаемый способ включает холодную прокатку, термообработку и дрессировку металла, а горячекатаную полосовую сталь толщиной 2,0…2,8 мм, содержащую 0,08…0,15 мас.% углерода, 0,05…0,10% кремния и 0,4…0,7% марганца, перед холодной прокаткой подвергают предварительному отжигу в колпаковых печах с выдержкой 4 ч при температуре t1=500°С и с выдержкой 10 ч при t2=560°С с общим временем нагрева 20 ч, а затем прокатывают на конечную толщину 0,5…1,0 мм, принимая величину суммарного обжатия εε=212/(h+2,3), %, при уставке номинальной толщины в чистовой клети непрерывного стана, после чего металл подвергают окончательному отжигу с нагревом до 400°С и с выдержкой при этой температуре 10 ч, снижая в последующем, до окончания времени нагрева, температуру до 380°С, и термообработанную ленту подвергают дрессировке с обжатием 0,2…0,7%.
Приведенные параметры способа получены опытным путем и являются эмпирическими.
Сущность заявляемого технического решения заключается в оптимизации параметров технологии производства нагартованной ленты, т.е. поверхностно наклепанной (упрочненной) стальной полосы (см. «Толковый металлургический словарь» под ред. В.И.Куманина. М.: «Русский язык», 1989, с.177, 179). В результате этого получается лента, пригодная для упаковки сортового и листового проката при его транспортировке.
Опытную проверку предлагаемой технологии производства нагартованной ленты осуществляли в ОАО «Магнитогорский металлургический комбинат».
С этой целью перед холодной прокаткой стальной ленты на непрерывном стане 630 варьировали параметры предварительного отжига, при прокатке использовали разные величины εε, меняя уставку (т.е. межвалковый зазор) толщины в чистовой клети стана, варьировали параметры окончательного отжига и величину обжатия при дрессировке. Результаты опытов оценивали по выходу ленты с требуемыми мехсвойствами и качеством ее поверхности.
Наилучшие результаты (выход качественной ленты в пределах 99,1…99,7%) получены с использованием предлагаемой технологии; отклонения от рекомендуемых ее параметров ухудшали достигнутые показатели. Так, уменьшение времени выдержки, времени нагрева и температуры в колпаковых печах при предварительном отжиге вызывали необходимость уменьшения εε при прокатке (вследствие недостаточного разупрочнения стали при отжиге) для получения нагартованной ленты, что в ряде случаев приводило к получению проката с h>1,0 мм, хотя остальные требуемые параметры технологии соблюдались.
Увеличение времени выдержки и нагрева, а также температуры в печах приводили к получению ленты недостаточной прочности (не нагартованной), что наблюдалось и при уменьшении εε и увеличении уставки валков в чистовой клети. Уменьшение же величины уставки в отдельных случаях выводило конечную толщину h за пределы минусового допуска.
Снижение температуры окончательного отжига (менее 400°С) и времени выдержки при этой температуре (менее 10 ч), а также последующей температуры (менее 380°С) и повышение εε вызывали излишнее упрочнение прокатываемой полосы, что отрицательно сказывалось на ее продольном роспуске. Увеличение же этих параметров (кроме величины εε) приводило в ряде случаев к получению не нагартованной ленты с σв<780 МПа. При дрессировке с обжатием менее 0,2% прочность ленты снижалась, а при обжатии более 0,7% недопустимо ухудшалось качество поверхности готовой ленты.
Способ, выбранный в качестве ближайшего аналога, в опытах не проверялся по причинам, изложенным выше. Таким образом, опытная проверка подтвердила приемлемость найденного технического решения для достижения поставленной цели и его преимущество перед известным объектом.
Технико-экономические исследования показали, что использование настоящего изобретения при производстве нагартованной ленты позволит увеличить выход качественной продукции не менее чем на 3% при соответствующем росте прибыли от реализации проката с улучшенными свойствами.
Пример конкретного выполнения
Полосовая сталь, содержащая 0,12 мас.% углерода, 0,07% кремния и 0,5% марганца, перед холодной прокаткой подвергается предварительному отжигу в колпаковых печах с выдержкой 4 ч при t1=500°С и с выдержкой 10 ч при t2=560°С с общим временем нагрева 20 ч.
При конечной толщине h=0,8 мм величина , т.е. исходная толщина полос должна быть равна .
Окончательный отжиг с нагревом до 400°С и выдержкой 10 ч при этой температуре со снижением температуры до 380°С. Обжатие при дрессировке 0,5%.
Способ производства стальной нагартованной ленты, включающий предварительный отжиг горячекатаной полосовой стали толщиной 2,0-2,8 мм, содержащей, мас.% 0,08-0,15 углерода, 0,05-0,10 кремния, 0,4-0,7 марганца, в колпаковой печи при температуре t1=500°С с выдержкой 4 ч и при t2=560°С с выдержкой 10 ч, с общим временем нагрева 20 ч, холодную прокатку на конечную толщину h=0,5-1,0 мм, принимая величину суммарного обжатия , %,где 212; 2,3 - эмпирические параметры, полученные опытным путем,при уставке номинальной толщины в чистовой клети непрерывного стана, окончательный отжиг с нагревом до 400°С и выдержкой при этой температуре 10 ч, снижая в последующем, до окончания времени нагрева, температуру до 380°С и дрессировку с обжатием 0,2-0,7%.
www.findpatent.ru
Нагартованные состояния алюминия по ANSI, EN и ГОСТ
Наклеп или нагартовка являются естественным следствием большинства деформационных операций алюминия и его сплавов. Иногда это называют еще деформационным упрочнением. Наклеп повышает прочность сплава, которая была достигнута в результате легирования и упрочняющей термической обработки. Для термически упрочняемых сплавов деформационное упрочнение может также повышать скорость выделения упрочняющей фазы.
Степень нагартовки
Нагартовку применяют для повышения прочностных свойств алюминия и алюминиевых сплавов, которые не упрочняются термической обработкой. Иногда эти сплавы – в основном сплавы серий 3ххх и 5ххх — называют в позитивном ключе: деформационно упрочняемыми. Основными «рычагами» для получения того или другого нагартованного состояния являются степень нагартовки — количество пластической холодной деформации и отжиг, полный или частичный – нагрев до температуры 350-400 °С при длительности, как правило, достаточной для полного прогрева.
Полный и частичный отжиг
Полный отжиг применяют для полного снятия нагартовки материала и приведения материала к состоянию с минимальными прочностными характеристиками и максимальными пластическим свойствами. Частичный отжиг выполняют для частичного снижения уровня прочностных свойств и повышения пластических для приведения материала готового изделия в заданное состояние.
Обозначение состояний алюминиевых сплавов
Для обозначения всех состояний алюминия и алюминиевых сплавов (и не только нагартованных) во всем мире широко применяется американская система обозначений, разработанная в свое время Американской Алюминиевой Ассоциацией.
- Первоначальная система обозначений состояний деформируемых алюминиевых сплавов изложена в американском стандарте ANSI h45.1.
- Эта система почти «один в один» принята международным стандартом ISO 2107 и европейским стандартом EN 515.
- Отечественные стандарты (ГОСТ) пока применяют свою систему обозначений состояний, которая значительно отличается от международной.
Состояние материала в горячепрессованном состоянии без дополнительных обработок – термических или деформационных – обозначается стандартах EN и ISO буквой F и никакие цифры за ней не следуют. В отечественных стандартах это состояние идет вообще без обозначения.
Состояние полностью отожженного материала обозначается буквой «О» (не ноль) по международной классификации состояний алюминия и алюминиевых сплавов или «М» — по отечественным ГОСТам. Буква О с дополнительной цифрой относится к отжигу со специальными условиями.
Все обозначения нагартованных состояний начинаются с латинской буквы «Н». За ней могут идти от 1 до 3 цифр.
Только нагартовка — серия Н1
Чисто нагартованные состояния без дополнительных обработок образуют серию Н1. Полностью нагартованным состоянием материала, которое обозначают Н18, называют состояние, полученное при холодной деформации эквивалентной относительному обжатию при прокатке 0,75. Относительное обжатие – это отношение разности толщин исходного и конечного листа к исходной толщине листа. Относительная вытяжка 0,75 будет достигаться, например, при исходной толщине 10 мм и конечной толщине 2,5 мм: (10 — 2,5)/10 = 0,75. Состояние Н19 обозначает изделия с еще большей степенью нагартовки, чем в состоянии Н18. Оно применяется, например, для ленты толщиной 0,30 мм из алюминиевого сплава 3104 для изготовления корпуса пивной банки. Состояния Н16, Н14 и Н12 получают при меньшем количестве холодной деформации и они представляют, соответственно, тричетвертинагартованное, полунагартованное и четвертьнагартованное состояния.
Состояния алюминия h211 и h212
При указании требований к механическим свойствам алюминия и алюминиевых сплавов часто употребляют обозначения состояний Н111 и Н112 из той же серии Н1. Состояние Н111 отличается от отожженного состояния О только небольшой степенью нагартовки, которую мог получить материал при правке или других технологических операциях. Состояние Н112 отличается от состояния F только небольшой степенью нагартовки (при горячей или холодной обработке), а также обязательным контролем механических свойств.
Нагартовка и отжиг — серия Н2
Серия Н2 относится к материалам, которые были нагартованы до более высокой степени, чем это нужно было бы для заданных прочностных свойств, а затем снижают эту «лишнюю» прочность снимают с помощью частичного отжига. С увеличением степени нагартовки вторая цифра возрастает от 2 до 8 аналогично чисто нагартованным состояния: Н22, Н24, Н26 и Н28.
На рисунке схематически показаны нагартованные состояния серий Н1 и Н2 при различной степени нагартовки и различных длительностях отжига при постоянной температуре. Бывают аналогичные графики в зависимости от температуры отжига. У состояний с одинаковыми вторыми цифрами пределы прочности – одинаковые, а предел текучести у состояний с частичным отжигом ниже, чем у чисто нагартованных состояний. График роста прочности от степени холодной деформации имеет выпуклость вверх. Это отражает тот факт, что первые стадии холодной деформации дают максимальный прирост прочности.
Серия Н3 — для сплавов алюминий-магний
Серия Н3 – состояния с нагартовкой и стабилизирующей обработкой: Н32, Н34, Н36 и Н38. Эту серию состояний применяют только для алюминиево-магниевых сплавов – сплавов серии 5ххх. Дело в том, что в нагартованном состоянии эти сплавы в течение некоторого времени могут терять, достигнутые нагартовкой прочностные свойства, за счет механизма естественного старения. Поэтому, если стабильность прочностных свойств важна, их часто нагревают до умеренных температур, например, 220 °С, чтобы завершить этот процесс старения, при этом несколько снизить прочность, но повысить пластичность и, тем самым, обеспечить последующую стабильность механических свойств и рабочих характеристик.
Нагартовка и лакировка — серия Н4
Серия Н4 применяется для нагартованных изделий с дополнительной лакировкой поверхности. Например, при изготовлении крышек пивных банок применяют ленту толщиной 0,26 мм из алюминиевого сплава 5182 в состоянии Н48 — полностью нагартованную и лакированную.
Состояния алюминиевых сплавов в стандартах ГОСТ
В старых, еще «советских», но действующих ГОСТах применяются свои обозначения нагартованных состояний. В ГОСТ 18475-82 на холоднодеформированные трубы, ГОСТ 7871-75 на сварочную проволоку и ГОСТ 21631-76 на листы предусмотрены следующие состояния материала:
- нагартованный (Н) и
- полунагартованный (П).
В ГОСТ 24767-81 на холодногнутые профили предусмотрено
- полунагартованное состояние с обозначением ½Н.
В относительно «свежем» ГОСТ 13726-97 на ленты к состоянием М и Н уже включают дополнительные состояния материала:
- четвертьнагартованный (Н1),
- полунагартованный (Н2) и
- тричетвертинагартованный (Н3).
Обозначения Н1, Н2 и Н3 имеют тут другой смысл, чем в стандартах ANSI, EN и ISO.
ГОСТ 18475-82 кроме этого предусматривает еще два состояния материала с участием нагартовки для термически упрочняемых сплавов АД31 и 1955:
- нагартованный после закалки и искусственно состаренный (ТН) и
- нагартованный после закалки и естественно состаренный (ТН1).
Это аналоги международных обозначений состояний Т8 и Т3, которые относятся к состояниям термически упрочняемых алюминиевых сплавов.
aluminium-guide.ru