Нарезание резьбы метчиком. Нарезка резьбы в чугуне
Резьба в чугуне | Справочник конструктора-машиностроителя
Всем хорошего денька!Необходим совет по восстановлению резьбовых отверстий в станине.Резьбовые отверстия М16 используются для крепления штампа к станине кривошипного пресса, напряжением в 130т.Нужно восстановить резьбу под тот же диаметр т.к.доступ к дальним крепежным отверстиям ограничен и рассверловка затруднительна!Обнаружил ремонтные спиральные резьбовые вставки HeliCoil., появился спрос к менеджеру — — Какова их крепость и долговечность, в ответ услыхал, что они вечные!!!Кто может сказать, это что за вставки и стоит ли их применить для ремонта?или посоветуйте способы для восстановления резьбы!
CRW_7753-7778_
Рассверлить отверстие под следующую резьбу, нарезать ее, в тормозной скобе рассверлить отверстие под новейший болт, подобрать новейший болт.Резьбу делать с тем же шагом, что и была.спасибо, а в этом нет «криминала»?ибо есть понятия у отдельных с кем я совещался, что так делать категорически невозможно, образа не нарезать в чугуне резьбу, образа болтов не подобрать итд.Вот и разрешил узнать у профессионалов
При рекламируемой вставке «увеличение отверстия фиксируемых деталей» НЕ происходит., который нельзя отменить ".А я о чём рассказываю, что желательно чтоб всё как было.Данные вставки в основном для потребностей, а здесь вторая проблема сто раз открути сто раз завинти и напряжения какие.уважаемый Desti откуда такая уверенность что именно так всё и будет, может разделитесь из своего эксперимента В принципе ничего новейшего в предоставленной технологии нету, скажем так дедовский метод, просто доведённый до ума.К примеру будуче студентом говорили случай восстановления трещины в фабричном котле методом заклёпывания, а здесь возможно даже на форуме обсуждалась такая тема, а потом оказывается есть немецкая контора мастер по подобным делам
Да уже, почесав в затылке, начал ремонтировать.Частично разобрал фартук (все, что касается гайки, остальное трогать не буду, наверное.Отломал полностью треснутую часть.Покрутил, возвратил на местечко, прижал струбцинами.Влазит максимум две шпильки М6 :(, причем под уголком, а не на разрыв, как желал.Уж чересчур полно потом различных дыр.Просверлил одно отверстие, нарезал резьбу.Для другого придется еще срезать кусочек с опоры зажима гайки (то, что слева маячит).Потом латунью заполню и зашлифую …За компанию просмотрел насосик, который дает на направляющие масло.Чего-то он не бросает.Потом точно шара не наверное быть?где, если должен?Members 2946 оповещений Город: Одесса Имя: Саня
Резцы уже есть готовые Р18, надо нарезать внутреннюю резьбу, втулка 1 шт. Нарезать рабочие не желают сказали либо сгорит либо любой ход, подтачивать надо.При каких выражениях можно нарезать на чугуне СЧ20 200 — 240 НВ внутреннюю трапецеидальную резьбу шаг 6 чтобы не сжечь его без охлаждения, или чем охлаждать (подручный вариант).Как быстрее будет резать ВК8 чем Р18 включая машинное время и переточки.Заказать новейший резец ВК6 — 8 это ругань и дополнительные проволочки.Насчет нарезки прямоугольного профиля наружную так и нарезали, на духовную даже нет канавочных резцов.Editor 4842 информаций Город: Львов — Тернополь Имя: Максим Когут
Народ не создавайте сами себе непреодорлимых проблемм — если есть возможность переточить болт и перерезать резьбу то нечего даже задумываться — РЕЗАТЬ однозначно.сам в близкое времечко занимался этим и никогда проколов небыло, главнейшее чтобы была технологическая возможность изготовить такойже болт с увеличеной резьбой.нарезать кривую резьбу можно только кривыми лапами в чугуне резьба играет ничем не худо чем в стали, и даже легче, только точно выберите сверло под резьбу используя таблицу данную Алексеем, я зачастую испльзую в похожих ситуациях метчики на единицу больше-тоесть если резьба была на восемь то перерезаю на девять, если на десять то на одинадцать …Короче в Вашей ситуации вообще проблеммы не замечаю, правда Вы не указали модель автомобиля …
spravconstr.ru
Способы восстановления резьбовых отверстий. Часть 2. – Резьбаделофф
Мы продолжаем рассматривать технологии восстановления сорванной резьбы в различных узлах и агрегатах, как автомобильной техники, так и в промышленном оборудовании. В первой части "Методы восстановления резьбы свечного колодца" мы начали обсуждать методику ремонта и разобрали преимущества, и недостатки представленных вариантов, как можно восстановить резьбу в головке под свечу зажигания.
Во второй части нашего обзора, будут в общих чертах рассмотрены способы восстановление различных резьбовых отверстий на практике.
И так, давайте разберемся, что делать если сорвал резьбу. Какие способы ремонта применяют различные ремонтные предприятия.
В ремонтном производстве применяют следующие способы восстановление резьбы:
- заварка отверстий с последующей нарезкой резьбы;
- установка ввертыша;
- сверление отверстий и нарезка резьбы на новом месте;
- обработка отверстия и нарезание резьбы увеличенного размера;
- применение полимерных материалов;
- установка резьбовой спиральной вставки.
Восстановление резьбы с применением сварки
Заварка резьбового отверстия с последующим нарезанием резьбы. Во всех случаях при заварке резьбовых отверстий сначала удаляют старую поврежденную резьбу путем рассверливания. В стальных деталях заварку отверстий производят газовой или электродуговой сваркой в защитных средах. Заварку в чугунных деталях производят газовой или электродуговой сваркой с общим или местным нагревом или в холодном состоянии. В качестве присадочного материала или электродов при горячей заварке применяют чугунные прутки с повышенным содержанием кремния, поршневые кольца из серого чугуна, электроды ЦЧ-4, ОЗЧ-1, МНЧ-1. Место заварки обрабатывают заподлицо с основным металлом, сверлят отверстие и нарезают резьбу в алюминии или чугуне номинального размера. Однако применение сварочных процессов вследствие большой зоны термического влияния приводит к появлению отбела, трещин и короблений детали, изменению структуры основного металла. Прочность восстановленной резьбы ниже новой.
Для заварки отверстий в алюминиевых деталях двигателя наибольшее применение получила аргонно-дуговая сварка специальными электродами из алюминиевой проволоки марки АК. Недостаток применения сварочных способов для, того чтобы восстановить резьбу в алюминии — активное поглощение расплавленным алюминием газов, что приводит к образованию пор в наплавленном слое. Большая усадка остывающего алюминия часто приводит к образованию трещин. От себя можем добавить, чтобы восстановить внутреннюю резьбу, например на блоке цилиндров двигателя, то необходимо произвести снятие детали и произвести дальнейший ее ремонт, что финансово будет не совсем выгодно.
Как восстановить сорванную резьбу используя футорки
Как восстановить резьбу в отверстии используя футорку (рис.1). Установка ввертыша может применяться, при восстановление резьбы если конструкция детали позволяет увеличивать отверстия. Этот способ ремонта резьбы трудоемок, стоимость ремонта высокая.
Сверление резьбового отверстия и нарезание резьбы на новом месте можно применять только для отдельных групп алюминиевых и чугунных деталей, у которых расположение резьбовых отверстий может быть изменено без нарушения взаимозаменяемости соединения (ступицы колеса, барабаны, фланцы) и способ ремонта резьбовых отверстий на ремонтный размер влечет за собой введение увеличенного размера и дополнительной обработки сопряженной детали.
Как восстановить внутреннюю резьбу спиральными вставками
За последние годы на ремонтных предприятиях для ремонта резьбовых отверстий широко распространен способ установки резьбовых спиральных вставок. Отечественный и зарубежный опыт изготовления спиральных вставок показал, что наилучшие результаты при восстановление резьбы, достигнуты при использовании нержавеющей стали.
рис.2 резьбовая вставка helicoil
Спиральные резьбовые вставки серийно изготавливают из проволоки с жесткими производственными допусками (рис.3). В таком виде спиральные вставки представляют строго концентрические внутренние и наружные резьбы.
Восстановленная резьба в чугуне имеет высокую износостойкость, обусловленную применением высококачественного материала спиральных вставок и наличием гладких поверхностей проволоки.
Сорванная резьба, отремонтированная обладает повышенной антикоррозионной стойкостью, исключающей возможность заедания резьб болтов и шпилек в результате атмосферных условий, так как отсутствует контактная коррозия в резьбовом соединении.
рис.4 восстановленная резьба
Такие резьбы имеют достаточный запас прочности при наличии термических напряжений, поскольку концентрированно подверженные тепловым напряжениям резьбовые соединения эффективно защищены от заедания и пригорания, образования окислов и окалин.
При подготовке материала часть картинок была взята с источника: http://www.base.polstr.ru
Текс материала был взят с сайта http://sxteh.ru/mess155.htm
rezbadeloff.ru
Нарезание резьбы | Сантехнапевы
Резьба - одно из гениальных изобретений человечества, хотя в последние годы учёные пытаются доказать, что принцип резьбового соединения человек не придумал, а подсмотрел в природе. Оказывается, есть некий представитель жуков у которого лапки крепятся к скелету при помощи подобия резьбового соединения! Может быть оно, конечно, и так, но, тем не менее, начало применения резьбы стало весьма знаковым событием в дальнейшем развитии человеческого общества. Переоценить значение резьбы для сантехнических нужд и вовсе не возможно. Найдётся, пожалуй, ничтожное количество сантехнических приборов, фитингов и инструментов не имеющих в своём конструктиве резьбы или резьбового соединения. Мне на ум приходят только фановые трубы, молоток да складной метр, используемый до эры рулеток. Хотя, встречаются и фановые трубы, соединяемые между собой и с фасонными частями по средством хомутов, имеющих резьбовые стяжки.
Поговорим сегодня о нарезании резьбы. Нарезание резьбы в заводских условиях это одно, а нарезание резьбы в условиях мастерской, а тем более в "полевых" условиях - совсем другое дело. Я говорю не о современном способе нарезания с использованием электрического инструмента, а о стародавних временах (хотя, не таких уж и стародавних), когда никакого электрического инструмента и в помине не было и резьба нарезалась ручным инструментом при помощи какой - то матери. Особенно увлекательно резать резьбу в "полевых" условиях: берём двое "шведок" (инструмент), лерку в держателе, трубу и вперёд. Главное в этом деле, чтобы никто не стоял сзади во избежание выхлопов при работе с трубами большого диаметра и, следовательно, повышенной нагрузке на организм. Возможно отравление газами. Зато, как я уже писал в одной из предыдущих статей, ни каких тренажёров не надо было.
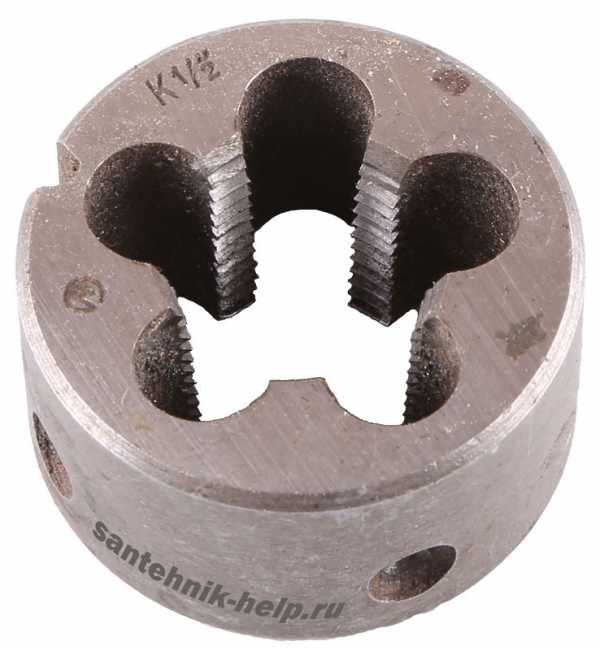
История нарезания резьбы начинается с плашек (ныне именуемых лерками) и клуппов. О трудностях, связанных с нарезанием резьбы и недостатком режущего инструмента, мы "узнаём" из гениального произведения Ильфа и Петрова "Двенадцать стульев" герой которого слесарь - интеллигент Виктор Михайлович Полесов сетует на недостаток плашек в 3/8 дюйма, которые сложно достать в условиях развивающегося народного хозяйства. Тем не менее, не смотря на все трудности, мы в настоящее время являемся свидетелями самоотверженного, тяжёлого труда предшественников - коллег по цеху образцы работы которых вызывают удивление и восхищение. Например, в здании Санкт - Петербургской Консерватории и в Театре при консерватории пожарный трубопровод имеет диаметр 100 мм и весь собран на резьбах с использованием различных фитингов. Представляете, сколько труда было затрачено! В здании Жилищного Коммитета Санкт - Петербурга пожарный водовод имеет диаметр 80 мм и, так же, собран на резьбах. Да, что там говорить, взять любое здание до и после военной постройки и везде инженерные коммуникации были собраны при помощи резьбовых соединений, кстати сказать, в некоторых местах с успехом работающих и в наше время. Честь и хвала труду наших предшественников, работавших, по нынешним меркам, как лохи, за идею, почти бесплатно. Это были люди по настоящему любившие свой город. К сожалению, в настоящее время такое чувство, как любовь относят только к себе самому и не к кому более. После Отечественной Войны, конечно же, пленные немцы здорово помогли в восстановлении народного хозяйства, не до конца ими же и разрушенного,но этот факт ни в коем случае не умаляет заслуг наших соотечественников.
Итак, всё началось с клуппов. На фото представлен типичный образчик данного семейства: - вес - 12 кг., размах "крыльев" - 1200 мм. Сей инструмент позволял нарезать резьбу от 1/2 дюйма до 2 дюймов, при установке соответствующих резцов: 1/2 - 3/4 дюйма - один комплект, 1 дюйм - 2 дюйма - другой так, как эти резьбы имеют один шаг резьбы. Для нарезания резьбы большего диаметра клупп выглядел, соответственно, ещё более внушительно. Развитие техники и появление в массовом строительстве сварки внесло свои коррективы и в развитие инструмента. Необходимость в нарезании резьбы большого диаметра резко сократилась, хотя и не отпала совсем. При монтаже трубопроводов большого диаметра к трубе приваривается патрубок с резьбой заводского изготовления. Такая технология здорово упростила и сократила время монтажа. Так же, заводские заготовки участков трубопроводов, практически, сократили до минимума необходимость нарезания резьбы на месте при новом строительстве. Но то, что смонтировано и введено в эксплуатацию всегда требует последующего технического обслуживания, ремонта и модернизации, а вот здесь нарезание резьбы практикуется по прежнему широко - не всегда и не везде есть возможность использования сварочного оборудования, что обусловлено не возможностью подключения электросварки, проблематичностью доставки поста газосварки да и требованиями техники пожарной безопасности. Так, что резьбонарезной инструмент ещё очень рано убирать на полку истории. Внедрение сварки сильно повлияло на размеры режущего инструмента. Следующая модефикация клуппа, представленного выше, имела уже совершенно другие размеры - он стал гораздо компактнее, имел в своей конструкции "трещётку", позволившую нарезать резьбу, практически, в любых условиях, даже самых стеснённых так, как процесс нарезания резьбы не требовал вращения инструмента вокруг заготовки, как в старом варианте. На ряду с клуппами использовались, конечно же, и старые добрые лерки во всевозможных держателях, в зависимости от фантазии токаря и использовались они гораздо чаще, чем клуппы. Клупп не получил такого широкого распространения, как лерка, не смотря на свои достоинства которые, кстати сказать, компенсировались недостатками, которых было не мало. Главным достоинством клуппов был конусный заход режущего инструмента чего не было у цилиндрических лерок. Были, правда, и конусные лерки, но они были очень редким явлением. Начало нарезания резьбы, заход на заготовку был самым проблематичным этапом работы - без снятой на трубе фаски очень не просто начать нарезание. У клуппа нет проблем с заходом на заготовку и нарезанием резьбы, но резьба эта резалась не за один проход, а за два - три, путём поджатия резцов от наметки резьбы до окончательного результата. Главным же недостатком клуппов, данной конструкции, было очень низкое качество самих резцов - они теряли свои режущие свойства уже после нескольких нарезок, а сменные резцы достать было очень проблематично. По этой причине и предпочитали пользоваться лерками, решая проблему захода тем или иным способом. Это сейчас, при наличии углошлифовальных машинок решить проблему с фаской на трубе просто (хотя и тут могут возникнуть проблемы с подключением), но эти машинки были не всегда. В мастерской фаску снимали при помощи точила, в "полевых" условиях при помощи напильника или, если это новая монтируемая труба, небольшой завальцовкой её края при помощи молотка на твёрдом основании (ступени лестничного пролёта). Гений токарного искусства произвёл на свет леркодержатель такой конструкции, которая позволяла преодолеть проблему захода режущей лерки на трубу без снятия фаски. Мне приходилось встречать леркодержатели различных конструкций, иногда весьма необычных и остроумных, призванных облегчить процесс нарезания резьбы.
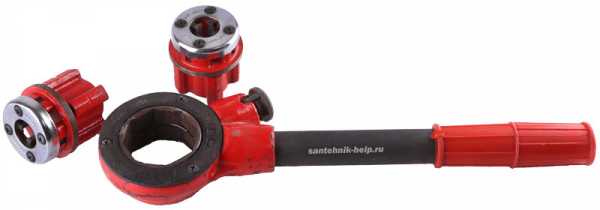
Дальнейшим этапом в совершенствовании резьбонарезного инструмента стало появление клуппов фиксированного размера, под каждый диаметр резьбы - свой клупп который вставляется в специальный механизм для вращения вначале ручной, а, затем, и электрический. Клуппы данной конструкции были импортными и имели гораздо более качественный материал режущего инструмента тем более, что в продаже появились и сменные резцы. Лерки потеряли свои лидирующие позиции, хотя есть работы, когда без них не обойтись. Необходимость в использовании лерки возникает в том случае, когда необходимо нарезать резьбу на очень коротком участке трубы, например у отвода или торчащей из стены. Длина трубы для нарезки клуппом определяется длиной его направляющей плюс ширина инструмента для удержания нарезаемой трубы от проворачивания. Иногда и этого оказывается много и, даже отрезав направляющую от клуппа (такое приходится иногда делать) не всегда можно решить поставленную задачу так, как клупп режет только в одном направлении и перевернуть его другой стороной нельзя. Вот в такой ситуации и приходит на выручку лерка, позволяющая нарезать резьбу, практически, на участке трубы любой длины.
В заключении хочу сказать несколько слов о технической стороне нарезания резьбы, а, именно, о предварительной оценке возможности выполнения той или иной работы. Работа с новыми трубами не представляет ни каких проблем, а вот подход к работе с трубами которые были в эксплуатации 20 лет и более, а в некоторых условиях эксплуатации и менее - очень серьёзное и ответственное дело - одно не ловкое движение и вы имеете массу проблем. Внешний вид трубы не всегда говорит о её истинном качестве. Иногда за отличным внешним видом труба скрывает такие тонкие стенки, что при нарезании резьбы они так и срезаются в виде проволоки. Старая труба требует особенно тщательного осмотра и оценки качества не только в месте нарезания резьбы, но и по всей длине, так как это качество может быть различным, особенно, если трубопровод имеет резьбовые соединения. В процессе работы с трубой к ней будут применяться физические, иногда, довольно не слабые, усилия и, не смотря на все предосторожности по удержанию трубы от проворачивания на 100% защитить трубу от физического воздействия не возможно и трубе самой придётся противодействовать вашим усилиям и на сколько она способна их выдержать вы и должны оценить.
Думайте и удачи вам.
P.S.
Считаю разговор, всё же, не полным без упоминания о внутренних резьбах. Хоть необходимость в их нарезании может возникнуть лишь раз в жизни, а может и не возникнуть вовсе, но тем не менее без них ни куда, вернее сказать: без их качественной заводской нарезки ни куда. Вот, для правки, встречающейся время от времени, не качественной внутренней резьбы и существует инструмент именуемый: метчик. Раньше, когда в магазинах не было в свободной продаже сантех - фитингов, метчик чаще всего приходилось использовать для изменения диаметра резьбы с 1/2 дюйма на 3/4 в футорках чугунных радиаторов. Выбора не было - поступала партия радиаторов с 1/2 дюймовыми футорками, а надо 3/4 вот и приходилось "пыхтеть". Работы эти производились, в основном, в мастерских и крайне редко на объекте так, как сверление отверстий под резьбу не так просто, как может показаться не посвященным. В месте проведения сантехнических работ метчик используется, в основном, для того что бы прогнать (очистить) старую резьбу для дальнейшего использования.
ПВН
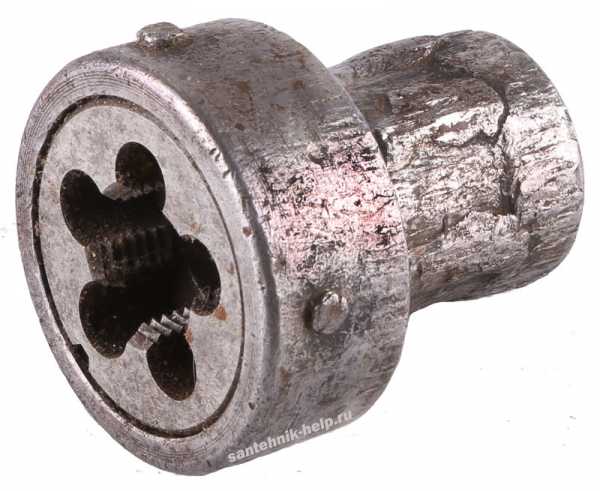
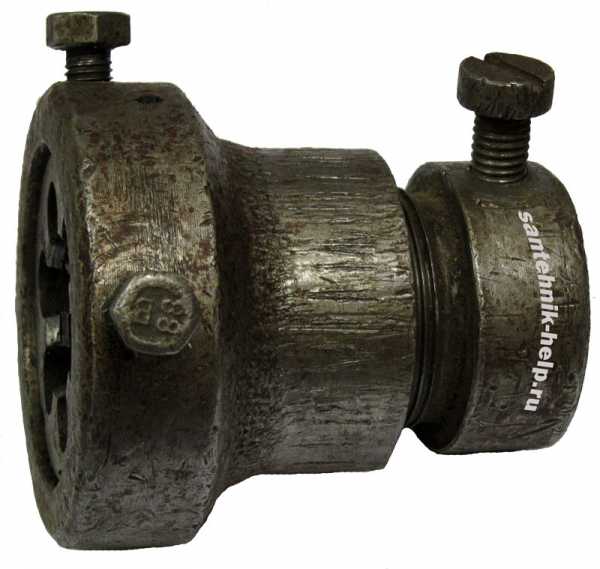
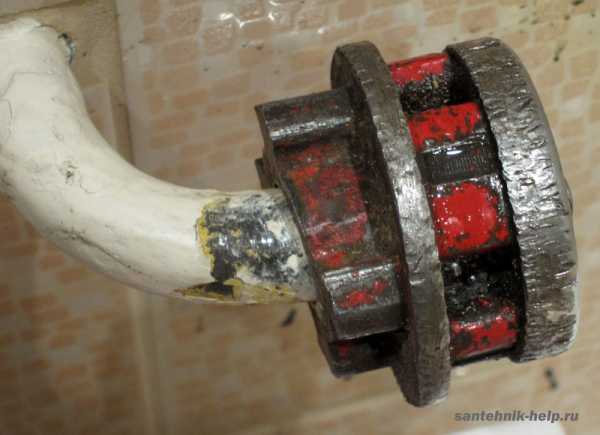
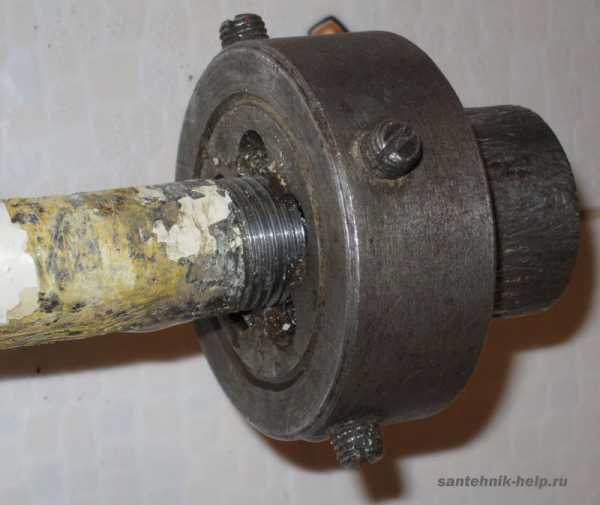
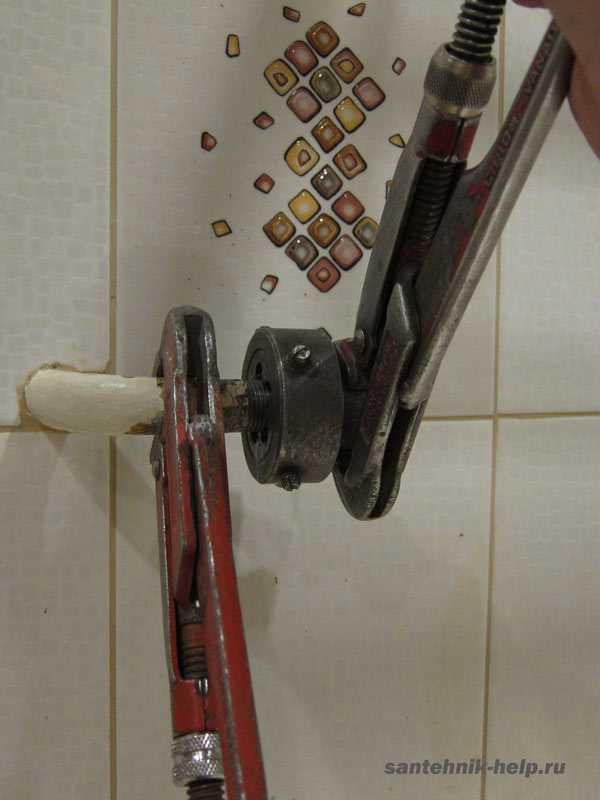
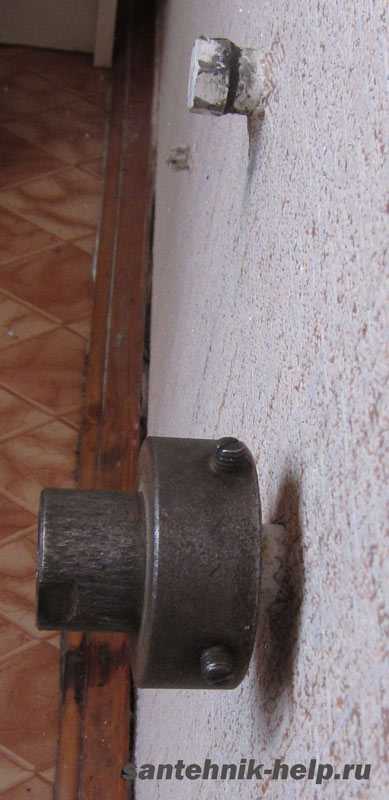
santehnapevi.ru
Зачем метчики делают первой и второй проходки, когда можно сделать единственный метчик одной проходки?
Так и делают. Ещё и третий бывает.
Для мягких металлов (материалов) можно, а для твёрдых ломаться будет.
Чтобы это понять, следует на практике попробовать нарезать резьбу сначала первым, а затем вторым, ну, и для сравнения сразу вторым. Если металл нормальный, то можно и метчик сломать, если сразу вторым нарезать. Когда по очереди, то легче резать.
это для крутизны! хороший слесарь, вторым метчиком в чугуне резьбу нарежет.
Метчики для двух проходов (первый и второй) предназначены для ручного нарезания резьбы, а однопроходные - станочные
А почему токарь сразу сантиметр не снимает с заготовки? А точит по миллиметрам..
Приходится и 3-м в глухом отверстии. Птичка по малому клюёт и склёвывает всё.Ещё спросите почему винтики практически везде накаткой делают, а для точных и оптических приборов режут резцом или леркой. Вот Вам и ответ. Дело в точности. Меня отец научил все болтики и гаечки с автомобиля проходить леркой и метчиком. И потом объяснил что кривая резьба с кривым сборщиком на кривом конвеере кривой компании автоваз закусит.
Верь только Костюку, остальные не знают и издеваюццо! Суть в том, что если сделать, как ты предлагаешь, только один метчик, то он будет быстро изнашиваться и, тем самым, нарезать "неправильную" резьбу, т. е. заваливать профиль резьбы. Поэтому и делают метчик первой проходки, он не столько режет резьбу, сколько готовит фронт работ для последующих метчиков, нарезая грубую резьбу (скорее даже кагбэ спиральную канавку) , зато медленнее тупится и изнашивается, метчики второй и третьей проходки доводят профиль резьбы "до кондиции". Можешь посмотреть на зубчики метчиков в увеличенном виде, и сразу станет все ясно.
С целью уменьшения крутящего момента при нарезании резьбы. Метчик очень непрочный инструмент. Если весь припуск одним метчиком снимать - поломка неизбежна. Не говорю о непрочных и хрупких металлах (дюраль, чугун, бронза, пластмассы - там всегда сразу последним режу - и всем рекомендую. Качество резьбы не сильно страдает. Для полимерных композитов вообще двумя метчиками резать не надо - все хуже будет. Ручные и машинно-ручные метчики они универсальны - т.е. не только для сквозных, но и для глухих отверстий предназначены. Для глухих отверстий режущая часть должна быть как можно короче (иначе у дна отверстия резьбы не будет), что и делается на этих метчиках. Короткая режущая часть - большая толщина среза на каждый зуб - большие усилия - поломка. Комплектом из двух-трех метчиков как бы увеличивают длину режущей части, уменьшая толщину срезаемого слоя каждым зубом метчика. Для коротких сквозных резьб (гаечные метчики) режущую часть делают длинной - длиннее, чем длина отверстия - т.е. припуск снимается последовательно режущей частью, которая вся никогда одновременно в работе не участвует. В этом случае комплект не нужен и на однокомплектном метчике момент небольшой будет. Для плашек проблемы поломки от крутящего момента не существует, хотя длина режущей части очень небольшая. Ну да, момент большой.Но вороток (для ручного резьбонарезания) просто имеет больший рычаг, чем вороток метчика.
touch.otvet.mail.ru
Как нарезать резьбу метчиком: подробная инструкция
Самый элементарный и часто встречающийся вариант скрепления деталей – резьбовое соединение. Казалось бы, что сделать его самостоятельно не составит никакого труда. На самом деле, правильная нарезка резьбы метчиком требует соблюдения многих правил, в противном случае качественного соединения в последующем не получится, а то и вовсе резьба не удастся или придет в негодность используемый инструмент. Как нарезать резьбу метчиком самостоятельно.
Подбор инструмента
Некачественное орудие труда – некачественная работа. Использование старых затупившихся или проржавевших метчиков или плашек чревато изломом их в процессе работы и плохой резьбой на детали. Помимо уже давно непригодных инструментов нужно избегать и тех, что непригодны с самого начала. К ним относятся все дешевые варианты неизвестного происхождения.
Помимо качества важен также их размер, а именно соотношение размеров используемого сверла и отверстия для него. Высчитать необходимые параметры можно благодаря формуле, но для облегчения этого процесса приведены примеры с точным соотношением:
- метрическая резьба М2 – диаметр сверла (метчика) 1,6 мм;
- м. р. М2,5 – д. с. 2,2 мм;
- м. р. М3 – д. с. 2,5 мм;
- м. р. М4 – д. с. 3,3 мм;
- м. р. М5 – д. с. 4,2 мм;
- м. р. М6 – д. с. 5 мм;
- м. р. М8 – д. с. 6,7 мм;
- м. р. М10 – д. с. 8,3 мм.
Смазка деталей
Этот момент очень важен, ведь благодаря нему используемый инструмент прослужит в разы дольше. Помимо этого он уменьшает вероятность поломки сверла внутри отверстия и снижает температуру разогретых кромок метчика. Но при выборе смазки обязательно нужно учитывать материал деталей, на которые наносится резьба:
- сталь, латунь – льняное масло;
- алюминий – керосин;
- медь – скипидар;
- бронза, чугун – без использования СОЖ (смазочно-охлаждающая жидкость).
В качестве смазки не рекомендуется использовать минеральные либо машинные масла. Их состав не позволяет мягко скользить поверхности метчика или плашки, поэтому резьба получится с шероховатостями.
Как нарезать резьбу метчиком: нарезка внутренней резьбы
О главных нюансах уже сказано, теперь можно перейти непосредственно к тому, как нарезать резьбу метчиком или плашкой. Пошагово этот процесс выглядит следующим образом:
Зажимаем в тисках обрабатываемую деталь.
Просверливаем отверстие под дальнейшую нарезку внутренней резьбы.
При помощи сверла, диаметр которого на несколько миллиметров больше планируемой резьбы, наносим фаску на край отверстия. Она необходима для более легкого вхождения метчика, а также для облегчения процесса ввинчивания винта в готовое изделие.
Вставляем в вороток (устройство для крепежа метчиков и плашек) черновой метчик.
Наносим на режущую часть смазку.
Вставляем в отверстие метчик и делаем три оборота.
После первых трех оборотов, делаем один оборот в обратную сторону. Таким образом, мы ломаем получающуюся в процессе нарезки стружку и она не будет мешать качественному и ровному нанесению резьбы.
Если отверстие в детали сквозное, необходимо сделать так, чтобы передняя часть метчика вышла полностью с обратной стороны. Не сделав этого, мы рискуем получить незаконченную резьбу.
Слом режущей части метчика в глухом отверстии
Если конец обломившейся детали полностью «утоплен» в отверстии, достать его будет очень сложно. Но поднабравшись терпения этого сделать все-таки реально. Вам потребуется парафин, продолговатая и тонкая деревянная палочка, азотная кислота. Парафином смазываем обрабатываемую деталь (защищаем от воздействия кислоты). Конец палочки смачиваем кислотой, просовываем его в отверстие и смазываем режущие кромки метрика. Как нарезать резьбу метчиком
Необходимо продолжать процедуру до тех пор, как края начнут расплавляться. После этого обломок либо выбивают молотком с обратной стороны детали, либо выковыривают пинцетом.
Как нарезать резьбу сметчиком: нарезка внешней резьбы
Взяв необходимую деталь, зажимаем ее в тиски. С одной стороны напильником делаем небольшую фаску, смазываем эту сторону маслом, керосином или скипидаром (в зависимости от материала).
В плашкодержатель вставляем и фиксируем плашку. Приставляем плашку к нужному концу трубы и в нужном нам направлении медленно вращаем одной рукой, второй рукой обязательно прижимаем верх плашки к трубе.
Когда плашка прочно села на трубу, проверьте ее перпендикулярность трубе, возьмитесь за плашкодержатель обеими руками и сделайте 3-4 оборота вперед, а потом пол оборота назад.
При нарезке внешней резьбы есть один нюанс, во время последних витков не делайте вращение назад, это позволит гайке прочно зафиксироваться на трубе.
Обратите внимание, свеженарезанную резьбу не стоит трогать голыми руками, на ней могут быть очень острые заусеницы и есть большая вероятность пореза.
Информация на заметку: Клупп для нарезки резьбы , Как крепить анкерный болт
Видео
рекомендуем похожие статьи
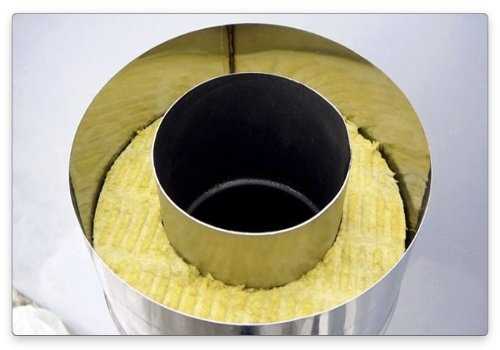
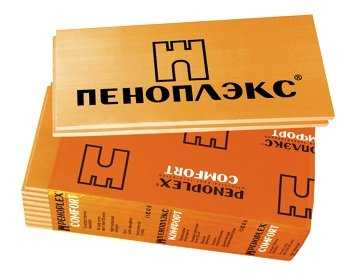
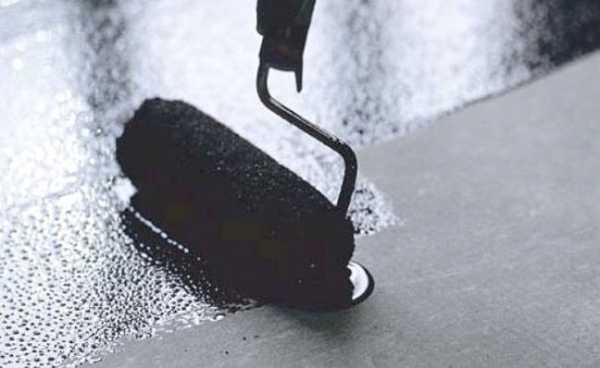
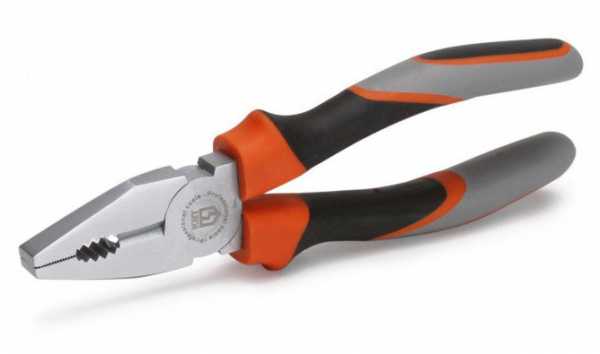
добавление комментария
stroitelinfo.ru
Нарезание резьбы метчиком | iCNC
05.08.2015Во время нарезания резьбы метчиком следует обращать внимание на свойства материала, из которого изготовлена заготовка, особенности используемого инструмента, возможности самого станка, а также правильно выбирать режимы резания. Примечательно, что во время нарезания резьбы нагрузка на каждый зуб метчика намного большая, чем нагрузка на режущую часть любого другого режущего инструмента, поскольку наблюдается постоянный контакт метчика с боковой кромкой резьбы. Во время нарезания резьбы одна из важнейших задач токаря – это организация незамедлительного и качественного отвода стружки, поскольку в противном случае значительно повышается вероятность деформации метчика. Кроме этого, отвод стружки дает возможность значительно повысить точность обработки и качество самой резьбы. Все эти нюансы создают немало трудностей для всех конструкторов и изготовителей режущего инструмента, поскольку они пребывают в постоянной гонке по повышению производительности, стойкости и стабильности обработки.
К разным материалам должны применяться разные метчики
На стадии проектирования метчиков для разных видов материалов производители в большинстве случаев лишь изменяют передний угол наклона, а также кривизну передней поверхности режущего элемента. Что касательно материалов, которые сложны в обработке, эти показатели имеют отрицательные или же нулевые значения, что дает возможность значительно повысить прочность режущей кромки. Стоит отметить, что большая кривизна на передней стороне метчика может спровоцировать появление задиров на резьбе, что значительно ухудшит качество обработки и приведет к появлению брака. Если говорить про обработку материалов, которые в конечном итоге дают сливную стружку, то в таком случае целесообразнее всего использовать метчики с положительными углами наклона передней режущей части, а также с большим значением кривизны передних поверхностей. Именно из-за таких особенностей метчиков стружка будет закручиваться и ломаться.
Еще одним немаловажным параметром геометрии метчика можно выделить задний угол. С целью обработки максимально твердых материалов применяют инструмент с большим задним углом, что дает возможность значительно уменьшить силу трения и обеспечить беспрепятственное попадание охлаждающей жидкости в зону непосредственного резания. Стоит отметить, что именно чрезмерно большой задний угол инструмента лишает его возможности самоцентрироваться в ходе нарезания резьбы. Если обрабатывать такого рода инструментом пластичные материалы, то это приведет к нарушению заданных размеров и спровоцирует появление брака.
Что касательно метчиков, которые ориентированы на нарезание резьбы в глухих отверстиях, то они отличаются между собой исключительно углами подъема винтовой линии. С целью нарезания резьбы в особо прочных материалах используют метчики с минимальным углом подъема винтовой линии. Именно благодаря этому удается обеспечить максимальную прочность непосредственно режущего инструмента. Чтобы эффективно нарезать резьбу в твердых металлах применяют резцы с минимально длиной режущей части, что значительно уменьшает силы резания. Если Вы заинтересованы в том, чтобы максимально повысить эффективность процесса нарезания резьбы, то очень важно обращать внимание не только на особенности режущего инструмента. Приведем пример, чтобы рассмотреть ситуацию более наглядно: Если Вы намерены нарезать резьбу в сером чугуне и станете использовать метчики для этого материала, то скорость обработки в таком случае возможна только на скорости резания в 10–15 м/мин, а при использовании современного режущего инструмента у Вас появится возможность повысить скорость резания вплоть до 75м/мин. Стоит отметить, что этот показатель скорости нарезания резьбы при условии использования нового оборудования максимален, поэтому обработка деталей на таких скоростях допустима только при определенных условиях. Если у Вас не будет возможность обеспечить внутренний подвод охлаждающей жидкости, то в этом случае целесообразно снизить скорость точения до 45 м/мин, поскольку стоит помнить о том, что при значительном перегреве быстрорежущей стали начинает значительно снижаться ее стойкость. Стоит отметить, что во время обработки небольших резьб порой может оказаться недостаточно скорости вращения шпинделя станка, а в случае обработки больших резьбовых элементов может не хватить мощности оборудования. Обратите внимание, что немаловажное значение на качество работы того или иного метчика может оказывать покрытие, которое на него наносится. Именно благодаря этим покрытиям удается значительно повысить стойкость резьбового инструмента и повысить резерв его производительность, то есть износостойкость.
Особенности твердосплавных метчиков
Известно, что твердосплавный инструмент практически полностью вытеснил инструменты из быстрорежущей стали, ориентированные на обработку точением, так вот метчики из этих сплавов также начинают пользоваться все большим распространением. Твердосплавные метчики обладают высокой хрупкостью, поэтому они не могут использоваться при воздействии больших нагрузок, чего нельзя сказать про аналогичный инструмент, изготовленный из быстрорежущей стали. Несомненно, этот факт можно отнести к весомым недостаткам, однако при этом эта категория метчиков прекрасно справляется с нарезанием резьбы в сером чугуне, алюминии и других материалах, в составе которых присутствует большое количество кремния. Дело в том, что во время работы с подобными материалами прослеживается максимальный абразивный износ режущей части метчика, а в случае применения твердосплавных метчиков, этот эффект не сможет причинить значительный вред инструменту и оборудованию в целом.
Благодаря многочисленным разработкам твердых мелкозернистых сплавов высочайшей прочности удалось создать метчики, обладающие действительно высокими параметрами прочности и износостойкости. Нередко эти инструменты используют для проведения обработки закаленных сталей, пластиков и даже жаропрочных металлов. Примечательно, что наибольшее распространение твердосплавные метчики получили по мере развития металлорежущего оборудования. Сегодня они широко используются для нарезания резьбы в самых прочных материалах.
Метод жесткого резьбонарезания
Для того чтобы в достаточной мере удалось повысить производительность обработки и качества изготавливаемой продукции обязательно следует использовать современное оборудование. С целью нарезания резьбы принято использовать лишь две категории станочного оборудования. К первой группе относятся станки, рассчитанные на сверление небольших отверстий, а также нарезания в них резьбы посредством специального инструмента. Частота вращения шпинделя в таких станках может достигать 6 000 оборотов в минуту. Ко второй группе относятся так называемые обрабатывающие центры, при помощи которых с каждым годом нарезается все большее количество резьбовых элементов. Отличительная особенность этого оборудования в возможности включения жесткого цикла нарезания резьбы, когда частота вращения шпинделя будет полностью синхронна относительно оси Z. Главное преимущество обрабатывающих центров в том, что для нарезания резьбы с их помощью больше не нужно использовать плавающих патронов для метчиков, при этом обработка может проходить на скорости от 2 000 до 3 0000 оборотов в минуту.
Такое оборудование в большинстве случаев комплектуется несколькими функциями, которые очень полезны во время нарезания резьбы, например, ускоренный вывод метчика из отверстия или же задание предельного момента во время нарезания резьбы. Эти функции предотвращают появление брака на производственной линии и при этом значительно повышают износостойкость инструмента. Если рассматривать работу на обрабатывающем центре с теоретической точки зрения, то вовсе не обязательно применять какие-либо средства для компенсации несоответствия шага метчика по оси Z. На практике же специалисты сходятся во мнении, что с целью компенсации погрешности при нарезании резьбы рациональнее всего применять специальные патроны для фиксации метчиков, например, SynchroFlex, в которых встроен специальный гибкий элемент. Главная особенность в этих патронах — показатель компенсирующей способности в пределах 0.5 миллиметрах.
i-cnc.ru
чем смазывать метчик при нарезки внутренней резьбы
Машинным маслом
Спец смазкой, но в отсутствии таковой, ВДшкой или маслом машинным. При нарезке резьбы необходимо периодически охлаждать инструмент. Рекомендуется использовать следующие вещества: при работе с алюминием и его сплавами – керосин, с медью – скипидар, со стальными деталями – эмульсию. Для таких металлов, как бронза или чугун, охлаждающие смазки можно не применять.
Смотря в каком материале нарезается резьба.
маслом машинным можно для машинок швейных например подобным
Я гидравлическим смазываю, машинное не стоит использовать. А сальцем не желаю.
Разный металл -разная смазка И сало и мел и масло машин.
Чем угодно, лишь бы склизкое было. В крайнем случае, можно мелом натереть.
Вообще то есть спец. мастика, но за неимением хоть соплями....
зависит же от скорости... если вручную - нафиг смазка, сталь мягче не станет, если прибором - смотри характеристики
Слюной иногда смазывают. Маслом (да хоть отработкой).
лучше сала не найдешь! сверла тоже смазывать можно!
Если сала не найдешь, то любым маслом.
Сталь режу с льняным маслом - пахнет немного, но всё остальное не даёт такой чистоты реза. Продаётся в любой аптеке. Алюминий и дюраль лучше резать с ВД-40.
Лучше чем сало ни для наружной ни для внутренней резьбы ничего не выдумано.. Эрзац-заменители - любое индустриальное, трансформаторное или вакуумное масло.. В самом крайнем случае - подсолнечное масло или маргарин.
Бытовым смазочным маслом для механизмов, любой густой смазкой типа Солидол, Литол, ЦИАТИМ-201, графитовой смазкой.
Я обычно литолом. А вообще практически любым машинным маслом.
Советую вам просто посмотреть таблицу смазочно-охлаждающих жидкостей для нарезания резьбы по ссылке: <a rel="nofollow" href="http://sverla.info/articles/kak-narezat-rezbu-metchikom/" target="_blank">http://sverla.info/articles/kak-narezat-rezbu-metchikom/</a>
touch.otvet.mail.ru