Отделочная обработка наружных цилиндрических поверхностей. Обработка цилиндрических поверхностей
Обработка наружных цилиндрических поверхностей | Токарные станки
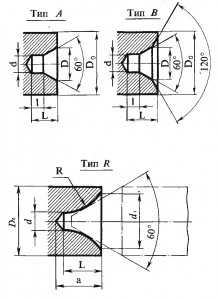
Рис. 1. Основные типы центровых отверстий. тип А-для заготовок, после обработки которых необходимость в центровых отверстиях отпадает. Тип В-для заготовок, которые обрабатываются в дальнейшем в закрепленных центрах: тип R-для заготовок точных деталей, обеспечивает надежный кольцевой контакт с поверхностью головки центра даже при некоторых перекосах
Центры. Заготовки валов, длина которых превышает диаметр в 5 и более раз, обычно обрабатывают с установкой коническими поверхностями центровых отверстий на центрах станка.
В качестве зажимных приспособлений используют: передний опорный центр, закрепляемый в шпинделе, и задний опорный центр, закрепляемый в пиноли задней бабки. Передний центр вращается вместе с заготовкой, а задний центр неподвижен, поэтому между заготовкой и задним центром возникает трение. Для уменьшения трения в цилиндрическую часть центрового отверстия заготовки со стороны задней бабки вводят густую смазку, которая от нагрева размягчается, попадает на конус центра и смазывает его.
На рис. 1 показаны основные типы центровых отверстий. Опорный центр (рис. 2) имеет
Рис. 2. Жетский опорный центр. 1-робочий конус, 2-хвостовик.
рабочий конус 1 с углом 60˚ (а для тяжелых станков 70˚ или 90˚) и хвостовик 2, выполненный по стандартному конусу Морзе (№ 2, 3, 4, 5, 6). Угол уклона конуса хвостовика 1 26˚. Для тяжелых станков хвостовик центра имеет метрический конус М60, М100 или М120 с углом уклона 1 30˚. Обычный или жесткий опорный центр применяют при сравнительно невысокой частоте вращения шпинделя (до 120 об/мин), так как между заготовкой и рабочим конусом центра возникает трение, что может привести к быстрому нагреву и износу центра. Работа с повышенной частотой вращения шпинделя ведется на износостойких центрах, у которых на рабочий конус наплавлен слой твердого сплава или впаян твердосплавный наконечник (рис. 3, я, б). Работа с высокой частотой вращения вызывает необходимость в установке вращающегося заднего центра, который имеет шпиндель, установленный в подшипниках. Для легких работ подшипники радиально-упорные шариковые, для повышенных нагрузок радиально-упорные роликовые.
Читать делее»
stankitokarnie.ru
Обработка внутренних цилиндрических поверхностей - Токарное дело
Обработка внутренних цилиндрических поверхностейКатегория:
Токарное дело
Обработка внутренних цилиндрических поверхностейОтверстия могут быть сквозные, глухие, нормальные и глубокие длиной свыше пяти диаметров отверстий. В зависимости от вида отверстия, его размеров, точности и параметров шероховатости обработанной поверхности для обработки отверстия применяют сверление, рассверливание, растачивание, зенкерование, развертывание, притирку и раскатывание (развальцовывание).
Рис. 1. Правна заготовки
Рис. 2. Типовые ошибни при заточ-не и установне прорезного и е) отрезного резца
Отверстия диаметром 30—60 мм раскатывают шариковым и роликовым раскатником. При этом диаметр отверстия увеличивается на 0,02—0,03 мм. Головка шарикового раскатника имеет оправку, упорный подшипник и конусные кольцы. Кольцо перемещается вдоль оси оправки и через кольцо поджимается пружиной, сжатие которой .регулируется гайкой с контргайкой. Обрабатывающие шарики находятся в сепараторе и расположены под углом 120° относительно друг друга. Квалитеты и параметры обработанной поверхности отверстия приведены в прилож. Державка с коническим хвостовиком с оправкой раскатника соединена штифтом.
В зависимости от требований, предъявляемых к точности обработанных отверстий, и их диаметров применяют различные виды инструментов.
Для сверления отверстий при обработке заготовок из материалов средней твердости применяют спиральные сверла с цилиндрическим и коническим хвостовиком; при обработке заготовок из материалов повышенной твердости — твердосплавные цельные сверла или сверла, оснащенные твердосплавными пластинами.
Рис. 187. Протачивание нанавни за один рабочий ход
Рис. 188. Схема обработни широких канавок
При сверлении в заготовках из чугуна отверстий глубиной не более двух-трех диаметров сверла применяют сверло с прямыми канавками. При рассверливании обычно применяют сборные сверла с многогранными неперетачиваемыми пластинами. При сверлении глубоких отверстий применяют сверла одностороннего резания. При сверлении отверстий диаметром более 50 мм в сплошном материале используют кольцевые сверла.
При сверлении отверстий сверла устанавливают в пиноль задней бабки или в резцедержатель. При этом используют крепежное приспособление, позволяющее работать как с ручной, так и механической подачей. Сверла с цилиндрическим хвостовиком перед установкой закрепляют в сверлильном патроне, который устанавливают в пиноль задней бабки. Сверла с коническим хвостовиком устанавливают в пиноль задней бабки с помощью переходных втулок, имеющих конус Морзе. При обработке сверла должны быть установлены строго по линии центров.
Рис. 189. Обработка торцовой поверхности и уступов
При обработке отверстия длиной более двух диаметров сначала сверлят его коротким сверлом, а затем длинным. Не допускается сверлить отверстие, имеющее глубину больше длины спиральной канавки сверла. При сверлении глухих отверстий используют шкалу, нанесенную на пиноли задней бабки. При отсутствии рисок на пиноли для определения глубины сверления к пиноли прикладывают масштабную линейку. При сверлении отверстий необходимо использовать СОЖ. При затуплении сверла появляется своеобразный скрежет. Наибольшее изнашивание сверла наблюдается по уголкам ленточки.
Рис. 190. Схема обработки уступов с применением упоров и плавающего центра
Рис. 191. Проверка расположения уступов
Рис. 192.
Рис. 193. Припусни на обработну торцов
Рис. 194. Подрезание торца отогнутым и уступов подрезным резцом
Отверстие диаметром свыше 30 мм обрабатывают за два рабочих хода. Сначала сверлят сверлом d — = 25 мм (рис. 200, ж), а затем рассверливают сверлом требуемого диаметра (рис. 200, з). В отливке или поковке рассверливать отверстие нельзя. Такие отверстия растачивают. Отверстия, глубина которых превышает диаметр сверла в 10 раз и более, сверлят при подводе СОЖ (рис. 200, и).
Растачивают отверстия расточными резцами. Углы заточки расточных резцов выбирают те же, что и у резцов для наружного точения, за исключением задних углов, которые имеют большие значения. Чем меньше диаметр отверстия, тем больше должен быть задний угол а. Вылет резца из резцедержателя делают больше на 5—10 мм глубины растачиваемого отверстия. При растачивании глубину глухого отверстия устанавливают по упору, риске, нониусу (рис. 201, в). При черновом растачивании резец устанавливают несколько ниже осевой линии, при чистовом — несколько выше осевой линии отверстия (рис. 201, г). При креплении тонкостенных втулок в патроне в них могут возникнуть деформации (рис. 202). Искажение формы отверстия можно обнаружить с помощью индикаторного нутромера, имеющего три точки касания (рис. 203).
Рис. 195. Виды отверстий
Рис. 196. Инструменты для обработки отверстий
Зенкеры по сравнению с расточными резцами обладают большой прочностью, поэтому обработку ими можно вести с большей подачей и глубиной резания. Для зенкерования отверстия диаметром до 35 мм применяют зенкеры с тремя режущими кромками и коническим хвостовиком. Для зенкерования отверстий диаметром до 100 мм используют насадные зенкеры, закрепленные на оправке.
При окончательной обработке отверстие развертывают. Развертку устанавливают точно по оси обрабатываемого отверстия. Развертку крепят в шарнирном устройстве. В зависимости от требуемой точности для развертывания применяют одну или несколько разверток (черновую 1 и чистовую 2).
Для получения поверхности отверстий 5 и 6-го квалитета точности при = 0,16…0,05 мм применяют притиры. При этом необходимо, чтобы отверстие предварительно было обработано до 6—8-го квалитета и имело Ra= 1,25…0,2 мм.
Рис. 197. Последовательность применения инструмента для сверления, растачивания и развертывания отверстий
Читать далее:
Обработка наружных и внутренних конических поверхностей
Статьи по теме:
1 2 3 4 5 6 7 8
Точение является самым распространённым и дешёвым методом обработки, который составляет примерно 70% от всего объёма лезвийной обработки. В ед. производстве применяют токарные универсальные станки, в мелкосерийном и серийном производстве – токарно-револьверные, в крупносерийном и массовом – токарные автоматы и полуавтоматы. Точность точения наружных поверхностей на токарных универсальных станках от 12 до 7 квалитета. Шероховатость поверхности 4-7 класс. Об-ка на токарно-револьверных станках, а также многошпиндельных станках обеспечивает точность обработки 12-10 квалитета, шероховатость 4-6 класс. В крупносерийном производстве и массовом производстве экономически выгодно точить поверхности точностью до 10(9) квалитета. Точные поверхности по 6-7 квалитету экономически выгодно шлифовать. Шероховатость поверхности 7-9 класс. Тонкое точение, которое выполняется на специальных операционных станках или токарных станках повышенной точности производится с малыми глубинами резания от 0,05-0,2 мм, малыми подачами от 0,03-0,1 мм и большими скоростями от 200 до 1000 м/мин. Фрезерование - процесс черн и получист обр-ки наружн. цилиндрич. пов-ей на спец. ст по методу ротор-фло когда РИ-фрезы, одна или несколько вращ-ся, а заг-ка установлена в центрах ось которой вертикальна, вращающаяся со скоростью круговой подачи. РИ вращается со скоростью резан до 200 м/мин. Процесс фрезерования обесп-ет точность обр-ки-12-10 квалитет, шер пов-ти-4-5 класс. Станки прим-ся в крупносер и масс пр-вах как прав, для обр-ки сложных деталей, имеющих не только цил. пов-ти, но и конические, фасонные. Процесс обр-ки на ст-ах произв-ся след. образ.В поз. III происх. снятие гот. дет, загрузка нов. заг-ки и процесс - в обратном направл. Зенкерование- процесс черн и получист обр-ки небольших по р-рам цилиндрич пов-ей типа бобышек, цапф в корпусных деталях и их обр-ке на агрег ст или автоматических линиях. Прим-ся в крупносер и масс пр-ве для обр-ки цилиндрических пов-ей. Точность обр-ки обесп-ется до 10 кв., шер-до 5 кл. Если диаметр большой - сборный зенкер (со вставными ножами, напайными пластинами.
Протягивание -процесс черн, чист и окончат (отдел.) обр-ки нар. цил. пов-ей на спец. ст спец. сборными протяжками, оснащен-ми тв. сплав. Протяжки по констр-ии м.б. призматич. или круглыми. Шер-ть пов-ти трудно обесп-ить (т.к. расст-ие м/д зубьями большое). Поэтому прим-ют протяжки с внутр. касан-ем (угол охвата > в неск. раз), но сложна в изготовлении. Обр-ка идет при вращающейся дет со скоростью круговой подачи. Точность обр-ки-7 кв, шер-7-8 кл. Примен-ся только в масс пр-ве, н-р при обр-ке шеек коленч вала. Шлифование - процесс чист и отделочной обр-ки пов-ей, преимущ-но закалённых, абраз. кругами. Обр-ка произв-ся на кругло-шлиф-ых ст, унив-ых, а также п/авт-ах и авт-ах. Унив-ые прим-ся в ед и мелкосер пр-ве. П/авт. и авт.-в крупносер и масс. Процесс шлиф-ия обесп-ет точн. обр-ки 9-6 кв, шер пов-ти 6-9 кл. Для гладких валиков, прутков исп-ют схему бесцентров. шлиф-ия, при этом обр-ка может выпол-ся м-дом прод-ой подачи или поперечной-для коротких заг-ок длиной не более 80 мм. Dmin=0,2мм, прутки меньшего Ø не вып-ся. Шлиф. в центрах может вып-ся по 3 сх.: 1.Сп-бом прод.подачи. 2. поп. подачи. 3. косой подачи (под.углом). Продольная подача-наиб-ее унив-на, прим-ся от ед до масс пр-ва, однако «-»-омл-ся низк.производит-сть,т.к для обр-ки дет треб-ся вып-ть неск.сот дв.ходов. Ползв-ет шлиф-ать дет. любой длины. Поперечная подача-прим-ся для дет.небольш.длины, для жёстких дет. у к-х длина обр-ки не более 80 мм. Выс.производит-сть, прим-ся в сер, крупносер и масс пр-вах. Косая: позв-ет шлиф-ать не только цилин. пов-ти, но и торец дет. Шлиф-ие, как прав, прим-ся при обр-ке закален. пов-ей с тв-ью больше 40HRC. Можно шлиф-ать и незакаленные стали и цветные металлы. Осуществляется при использовании СОТС (эмульсии). 1. Интенсиф-ция процесса шлиф-ия произв-ся увел-ем скорости рез. от 30-40 м/с до 50 м/с (скоростное шлиф-е) и выше 60-150 м/с (высокоскоростн. шлиф-ие), к-рые позв-ют получить класс шер-ти пов-ти 10-14, обр-ка произв-ся на спец. ст. «-»:выс. t-ры на пов-ти резан., что прив-ит к появлен. прижогов 2.Для ум-ия прижогов прим-ют подачу СОЖ ч/з поры круга, однако сп-б не нашёл широк. прим-ия,т.к треб. спец дорогие круги 3. Импульсное шлиф-ние позволяет сделать контакт И с дет-ью прерывистым, исп-я спец. профилирован. круги Шлиф-е повыш-ет точн.взаимн. положен. За счет того, что пов-ть абраз.круга прерывистая,то и контакт с пов-ью прерывистый (импульсный). Там, где контакта нет, дет остывает, след-но, ув-ить режимы рез.:подачу, … На шерох-ть не влияет. Влияет только на износ круга (повыш-ся производ-ть в 1,5-2 раза, повыш. износ. круга на 10 %). Суперфиниширование - процесс отделочной обр-ки цилиндр. пов-ти абразивными брусками на спец. ст. Абразивные бруски подпружинено крепятся к головке, к-ая в процессе обр-ки совершает дв-ие вдоль оси дет. с V подачи 0,2-0,5 мм /об дет-и, а также имеет колебательное дв-ие с частотой до 1000колеб в мин и амплитудой 2-5 мм, дет. в процессе обр-ки вращ-ся со скоростью круг. подачи (10-30 м/мин). Процесс обр-ки идёт с СОЖ (масло). В нач мом. обр-ки уд. давлен выс. и происх-ит с пов-ти съем Ме. 0,2-0,4 кг /см2 -удельн. давл. В конце обр-ки уд. давл постепенно ум-ся и бывают не в состоян-разорвать масляную плёнку. Процесс рез. останавл-ся автом-ки. Процесс суперфин-ия обесп-ет повышение точн. обр-ки, (р-ра и формы) до 5-6 кв, шер. пов-ти 10-12 кл, точн. взаимн. располож. не повыш-ся. Прим-ся в крупносер и масс пр-ве при обр-ке наиб. ответствен. пов-ей (шейки коленч. вала, опор шейки шп-ля под подш-ки качения, скольж.). Притирание-процесс отделочной обр-ки цилин. пов-ти на спец. ст-ах чугун-ми притирами(СЧ20), имеющими плоскую раб пов-ть, при этом дет. располаг-ся м/д двумя притирами в сепараторе, ось вращения к-го смещена по отношению к оси вращ-ия притиров. Расположение дет. в сепараторе под углом с эксц-том по отношен. к оси вращ. притира позв-ет получить сложн траектор дв-ия абраз-го зерна по пов-ти дет, а след, обеспечить выс. кач-во обр-ки (10-14 кл. шер), точн. обр-ки 5-6 кв. Перед притиран. дет д.б обраб-ны шлиф-ем или тонким точен, припуск под прит-е оставл-ся от 0,02 до 0,05мм(под суперфиниш.-0,01-0,02).Припуск в пределах доп-ка Точн взаим положен не повыш, проц. идёт с СОЖ(керос+маслом). Полирование-проц.отделочн. обр-ки пов-ти абразивн. порошками или пастами, нанесён-ми на мягк. войлочные или фетровые круги. Процесс идёт с СОЖ(в неб. кол-ве: керосин+маслом).Предпочт-ее исп-ать пасты,к-ые содержат спец.добавки, позволяющ. облегчить процесс резан, ускорить его и повысить кач-во обр-ки. Полир-ие произв-ся на спец. ст. В крупносер и масс пр-ве широко прим-ся полир-ие цилиндр.пов-ти абразивн. лентой на спец. ст. Полир-ие сложн.фасон. пов-ей в кр.сер и масс пр-вах вып-ся мягкими абраз. кругами на вулканитовой основе (связка-резина), сп-бов полир-ия цил, фасон. и плоских пов-ей в практ прим-ся много (св. 10 сп-ов). Энергоносителем, прижимающим абразивн.зёрна к пов-ти детали, м. б. ж-ть или сж. воздух под давлением, центробежн. силы, магн. поле и др. источники. Кроме того, процесс полир-ия может вып-ся без абразива-хим-ое и электрохим-ое полир-ие, анодно-механ-ое, ультразвук-ое. В проц. полир-ия происх-ит срезание гребешков, их стравливание или пластич. деформ. (ультразв. полир).В рез-те повыш-ся кл. шер-ти (10-14кл.), точн. р-ра и формы не повыш-ся. Пластическое деформирование Осуществляется шариками или роликами, установленными в специальные раскатники. При этом приложение нагрузки к шарикам и роликам может быть статическим или динамическим (наложение ультразвука). На модернизированных токарных станках или специальных раскатных станках с помощью специальных твердосплавных или алмазных (алмазное выглаживание) накатников. Поверхность детали должна быть предварительно обработана не ниже 4 класса шероховатости. Применяется для низко- и среднеуглеродистых сталей после операции нормализации или улучшения, для цветных металлов. Пластическое деформирование позволяет наклепать поверхностный слой, т.е. повысить его прочность (ΔНВ до 40%). В поверхностном слое создаются положительные напряжения сжатия, обеспечивающие повышение долговечности работы детали, сопротивляемости поверхности знакопеременным циклическим нагрузкам. Для ответственных дет в авиастр, ракет технике.
Жесткие ступенч. валы в ед пр-ве обраб-ся с исп-ем шаблонов, точность и произв-ть не высокие (грубее 16 кв.). В сер пр-ве обр-ку ведут на ток-винт. ст с исп-ем гидросуппорта, к-ый ставится вместо резцедержателя. От среднесер до масс пр-тв для обр-ки ступенч. валов исп-ют ток. п/авт. многорезцовые и гидрокопир-ые. Многорезцов. прим-ся, когда число ступеней не велико (не > 10), при большем числе ступ.эконом выгодн исп-ать гидрокоп. ст. Многорезц. и гидрокоп. ст. имеют 2 суппорта: прод-ый и поп-ый. С прод-го суппорта производиться точение цил-их ступеней, с поп-го суппорта произв-ся одновременная обр-ка точением фасок, канавок, подрезка торцов в р-р (т.е. выдерживают линейные р-ры). Автоматизацией обр-ки в мелкосер пр-ве явл-ся исп-ие ст. с ЧПУ, к-ые по программе обрабатывают последовательно одну за другой ступени,при этом колич-во проходов для обр-ки конкретн ступени может определяться спец-ой программой, имеющейся на станке. В мелкосер пр-ве часто исп-ют ток. гидрокопиров. полуавтоматы с цикловой СУ, когда программа набирается на пульте станка. Ст. позв-ют выполнять многопроходную обр-ку ступеней по копиру Возможные схемы обр-ки ступеней: 1) Рассм-им вар-ант обр-ки (вверху) в мелкосер. пр-ве (ст. с ЧПУ), обраб-ся каждая ступень послед-но. max жест-ть дет. при обр-ке каждой ступени. Кол-во проходов задает оператор или сам ст. 2) Проц. обр-ки дет. (внизу) для сер. пр-ва, массов. заг-ка будет иметь приближенную форму к гот. дет. Эконом-ки выгодно, если перепад м/д d2 - d1 > 5 мм на детали. 3) При обр-ке на многорезцовых ст каждый И обр-ет своют ступень. «-»: сх.: большая длина рабочего хода, кот-я опр-ся самой длинной ступенькой. Для ум-ия данного «-»-ка соврем-ые ст-ки позв-ют работать по сх. косого врезания (с углом 45°), когда max длина хода делится пополам.Многорезцов и гидрокопир ст-ки могут вып-ть черн, чист обр-ку, при этом суммарная глубина рез. от неск-их И-ов м.б. 15 мм и более. При черн. обр-ке ступенчат. заг-ки, когда вел-на припуска на каждой ступеньке не превышает 3 мм, точн. обр-ки-12 кв, шер пов-ти при подаче SО до 0,4 мм 4 кл. При больш. вел-ах подачи получим 3 кл. Последов-ая чист. обр-ка на ст обесп-ет 10 кв,шер-ость 5 класс.На гидрокопир.ст эконом-ки выгодно обр-ать с точностью до 9 кв, на многорезцов.-до 10 кв.
Сверление-основн. сп-б получ-ия отв-ий в сплошном Ме. Сверлен произв-ся РИ, сверлами, к-е по конструкции м/б перовые, спиральные, ружейные и пушечные, кольцевые и трубчатые. По кол-ву реж. кромок сверла м/б:1.однокромочн (ружейн и пушечн), 2.двухкромочные (перовые,спиральн)3.многокр (кольцев и трубч) Наиб. распр получили спирал. сверла, кот-е серийно вып-ся Ø-ом 0,2-55 мм. Спиральными сверлами обраб-ют, как прав, отв-ия с соотношением - l/d до 5 , обычные сверла - l/d до 5, спец-ые - l/d до 1. Обр-ка сверлением производ-ся в основном на вертикально-сверлильн. ст. Корпусные тяжелые дет. весом от 50 кг и более-на рад-но-сверл. или гориз.-расточных. Также можно сверлить отв-ия на ст ток. гр, агрег, и спец-х. Для повышен. глубины сверлен.отв-ий с l/d =10-15 прим-ют спец. сверла (шнековые, а также с подводом СОЖ ч/з тело сверла по винтовым отв-ям). Глубокие отв. сверлят при вращающейся дет: при этом в сл. увода сверла возникают силы, стремящиеся вернуть сверло в прямолинейное положение. В этом сл. стар-ся сверлить на ток. ст. (ед. пр-во), ток.-револьв.(среднесер.), сверла спец-ые. Сверление спец. сверлами обесп-ет точность обр-ки 12-13 кв, шер 3-4 кл. Сверлен отв. малого Ø по кондуктору обесп-ет точн обр-ки до 10 кв и шер 5 кл. Точн. межцентров расст-ий при сверлении по кондукторным втулкам ±0,2, ±0,1. Глубок. отв. сверлят ружей-ми и пушечными сверлами на спец. ст. для глубокого отв-ия. Обр-ка идет обяз-но при вращ-щейся дет. Сверло может вращ-ся или не вращ-ся, но всегда имеет дв-е подачи вдоль оси от гидроцилиндра, min Ø сверлен ружейн сверлами 3 мм (l/d = 200 и более). Пушечн. сверлами можно только рассверливать отв-ия, сверла в процессе обр-ки направляются по обработанной пов-ти, прижимаясь к ней усилиями рез. и частично сглаживая ее СОЖ подается под давлен от 20 до 80атм. Процесс сверлен обесп-ет точн отв-й 10 (9) кв, шер 5(6) кл. В процессе сверлен пушечн., ружейные сверла в начальн. момент направляются по кондукт. втулке. Если отв. малого Ø - тв.спл. сверла. Руж. и пуш. сверла изгот-ют централизовано. Зенкер-ие-процесс черн и получист обр-ки отв-й, предварит-но полученных литьем, штамп-кой или сверл-ем. Процесс зенкер-ия предпочт-ее, чем рассверлив-ие или точение отв-ий, т.к процесс более производит-ый в следствие большого числа реж. кромок, участвующих в работе (Ø 12-13 мм, min - 3 реж.кр.), т.к при зенкер-ии сним-ся небольшой припуск 2z=0,25d, т.е глубина рез. t=0,125d. Зенкер им. меньшие по р-рам струж. канавки, более выс. жесткость, след-но, исправляет положен. оси отв-ия в простр-ве. Черн. зенкер-ие черных отв-ий (получ-ых литьем или штамп-кой) обесп-ет точн. обр-ки 12 кв, шер 4 кл. Чист. зенкер-ие обесп-ет точн. обр-ки 10 кв, шер 5 кл. Для повышения кач-ва обр-ки и точн. межцентр. расст-ий до знач-ий ±0,1 зенкер-ие ведется с направлен по кондукторным втулкам. Направлен м.б. заднее (за реж. частью) и переднее (перед реж. частью) и комбинир-ое. Зенкер-ие глуб-их отв-ий произв-ся м-дом обратн подачи, когда стержень И-та раб-ет на растяжен. Зенкер протягивается ч/з отв. По такой же сх. производ-ся и развертывание глуб. отв-ий. Развертывание-процесс чист. обр-ки отв-ий РИ-развертками, к-е по конструкции м.б многолезвийные (или однолезвийные прим-ся для обр-ки глуб. отв-ий min Ø=3 мм), многолезв-е-2 мм. Разверт-е не повыш. точн. взаимн. располож,т.к И направл-ся по обработан. пов-ти, чтобы снимать min равном. припуск на сторону z 3-0,3мм. Разверт-ие отв-й малого Ø(до12 мм) можно вып-ть сразу после сверлен.Черн.разверт-ие-9кв, шер-6кл, чист. разверт.-7кв,шер-7кл. Однолезв. разверт обесп-ют более выс кач-во обр-ки (до 8 кл шер-ти-по стали).Глуб. отв-ия можно также развертыв. м-дом обратн подачи. В практике прим-ют проц. разверт-ия отв-ий Ø до 500 мм. Растачивание-самый унив-ый сп-б обр-ки, позв-ий обесп-ть точн. от 14до7 кв.min Ø отв-ия, кот. растач-ся в сер и кр.сер пр-ах=5 мм, в ед пр-ве от2мм.В этом сл.обр-ка произв-ся на коорд-но-расточ ст Растачивание на ток. ст. норм-ой точности обесп-ет: черн раст-ие -12кв, чист.-10 кв;оконч.- 8-9 кв, 7 кв точности, как прав, получают на ст повышенной точн. или спец алмазно-расточных ст. агрег-го типа, имеющих прод-ый стол. Расточные головки могут распол-ся с одной стороны или с 2-х сторон, что позв-ет расст-ть одновр-но соосно расп-ые отв-ия одновр-но с 2-х стор. Пр. Отв. в корпусе ред-ра под подш-ки в сборе с крышкой.Обычно исп-ся тв. спл. И. Фрезерование-прим-ся редко, как правило, на ст-ах с ЧПУ. Черн. обр-ка отв-ий большого Ø в корп. дет. произв-ся фрез-ем концев. фрез. по программе. Точнь обр-ки до 10 кв, шер. пов-ти до 5 кл. Протягивание-процесс черн, чист и отдел. обр-ки отв-ий многолезв. РИ-протяжкой. Как прав, протягивают отв-тия, предв-но получ-ые сверлен, зенкер-ем или растач-ем. При этом желат-но для направл. протяжки и снятия равном-го припуска по перим-ру отв-ия иметь перед протяг-ем точн. отв-ия 10 кв, а при протяг-ии шлиц. отв-ий и фасонных -9 кв. Протягивание обесп-ет повышен. точн. обр-ки до 7-8 кв, шер пов-ти 7-9 кл (при наличии выглажив-их зубьев у протяжки 7-8). Точн. взаимн. расп-ия отв-ий при пртяг-ии не повыш. S = 0,03-0,05мм/зуб. Протяг-ие дет. небольш р-ров произв-ся на гориз-прот.ст.; крупно-габарит. дет. на верт.-протяжн ст.
|
otnos.ru
Обработка наружных цилиндрических поверхностей
Производство Обработка наружных цилиндрических поверхностей
просмотров - 175
ОБРАБОТКА ЦИЛИНДРИЧЕСКИХ ПОВЕРХНОСТЕЙ
ПОВЕРХНОСТЕЙ ДЕТАЛЕЙ МАШИН
ЛЕКЦИЯ № 17
РАЗДЕЛ IV. МЕТОДЫ ОБРАБОТКИ ТИПОВЫХ
Первой технологической операцией является черновая обработка цилиндрической наружной поверхности. Закрепление заготовки производится в зависимости от формы, размеров и назначения детали. Оно должно быть прочным, так как на черновой операции резцы снимают стружку большой толщины, в связи с этим возникают значительные силы резания.
Резцы при черновом точении снимают стружку большого сечения при большой скорости резания. По этой причине резец должен быть прочным, а форма резца должна обеспечивать легкость съема стружки (рис. 17.1).
Рис. 17.1. Резец для черновой обработки
Проходные упорные резцы применяют для обработки заготовок с уступами небольших размеров. Главный угол в плане у таких резцов φ = 900, что уменьшает вибрации в процессе работы. Проходные резцы , используемые для обработки заготовок из стали и чугуна изготавливают из быстрорежущей стали или твердого сплава.
Обработку заготовок из стали с небольшой глубиной резания и относительно равномерным припуском производят резцами, оснащенными пластинами из сплавов Т14К8, Т15К6, Т15К6Т.
При черновой обработке заготовок из чугуна с неравномерным припуском применяют резцы с пластинами из твердых сплавов ВК2 и ВК4.
Величина переднего угла γ у резцов из быстрорежущей стали выбирается в зависимости от обрабатываемого материала и формы передней поверхности резца.
Задний угол α выполняют равным 120 при подачах до 0,2 мм/об и 80 – при больших подачах.
Главный угол в плане φ для резцов, предназначенных для обтачивания ступенчатых заготовок большой длины и малого диаметра, принимают 900. При обработке заготовок малой жесткости угол φ принимают равным 65 … 700, а для более жестких заготовок 30 … 600. Радиус резца при вершине при подачах до 0,2 мм/об, принимают 0,5 … 5 мм, а при подаче более 0,2 мм/об – 1 … 3 мм.
При чистовой обработке закрепление детали должно быть прочным, исключающим смещение ее в процессе обработки. Это позволит получить требуемое качество обработки поверхности детали.
Резцы при чистовой обработке должны обеспечивать заданную чистоту обработки поверхности детали. В соответствии с этими требованиями выбирают их форму (рис. 17.2).
а б
Рис. 17.2. Резцы для чистовой обработки: а – остроносый; б – широкий
Остроносые резцы (рис. 17.2, а) работают в обе стороны – как правый и левый. При чистовом обтачивании с большой подачей применяют широкие (рис. 17.2, б) резцы, которые называют лопаточными.
При выборе формы передней поверхности, передних и других углов резцов из быстрорежущих сталей для чистовой обработки можно пользоваться рекомендациями для резцов для черновой обработки. Для получения меньшей шероховатости передний угол резца должен быть больше.
Задний угол резца α при обтачивании заготовок из стали принимается, 120, а при обтачивании заготовок из серого чугуна – 100.
Существуют два метода точения наружных цилиндрических поверхностей.
Обтачивание методом радиальной подачи, который применяют при обработке коротких цилиндрических шеек канавочными или широкими резцами (рис. 17.3,а).
Обтачивание методом продольной подачи (рис. 17.3, б). Этот метод является наиболее распространенным методом обработки. Обрабатываемая деталь закрепляется в центрах или в патроне и вращается, а резцу сообщается движение подачи.
Цилиндрические поверхности обычно обтачивают в два или несколько рабочих ходов: сначала снимают начерно большую часть припуска (до 6 мм на диаметр), а затем снимают оставшуюся часть (до 1 мм на диаметр).
а б
Рис.17.3. Методы обтачивания цилиндрических поверхностей
Для получения необходимых размеров цилиндрической наружной поверхности пользуются лимбом поперечной подачи и устанавливают резец на нужный размер по методу пробных проходов. Такая обработка обеспечивает точность по 8 … 9 квалитетам. У многих современных токарных станков имеются продольные лимбы, которые позволяют получать продольные размеры с точностью до 0,2 мм. Производительность и точность обработки повышаются, если применять регулируемые упоры с самовыключением суппорта. При этом точность обработки продольных размеров достигает 0,08 … 0,15 мм.
При работе на скоростных режимах резания задние центры должны быть вращающимися. На универсальных станках применяют вставные (сменные) центры, на операционных и многооперационных станках вращающиеся центры встраивают в пиноли задних бабок, что существенно повышает их жесткость.
При обработке партии заготовок за один рабочий ход (рис. 17.4, а) резец, заранее установленный на размер d, не перемещают в поперечном направлении. После обтачивания заготовки по длине l ее снимают, а резец отводят в исходное положение для обработки следующей заготовки.
По такой схеме выполняют черновую, а иногда и получистовую обработку небольших партий заготовок за два установа. После обтачивания одной половины заготовки (рис. 17.4, б) ее переустанавливают в центрах и обрабатывают вторую половину заготовки (рис. 17.4, в).
Обработка наружных ступенчатых поверхностей. При черновой обработке ступенчатых заготовок, если в качестве заготовки выбран прокат, важно правильно выбрать последовательность обработки ступеней.
б
а
в
Рис. 17.4. Схемы обработки заготовки за один (а) и два (б, в) установа
Рассмотрим черновую обработку одного конца ступенчатого вала из проката диаметром 100 мм (рис. 17.5, а). Возможные варианты обработки приведены на рис. 17.5 б – д.
По первой схеме (рис. 17.5, б) каждая последующая ступень обрабатывается отдельно после обработки предшествующей ступени. При этом длина хода резца lр будет составлять 400 мм, длина вспомогательного хода инструмента lвсп = 400 мм. Глубина резания составляет от 11 до 3,5 мм. При обработке по второй схеме (рис.4.5, в) длина рабочего хода инструмента составит lр =550 мм, lвсп = 550 мм; по третьей схеме (рис. 4.5,г) lр = 650 мм, lвсп = 650 мм; по четвертой схеме (рис.17.5, д) lр = 800 мм, lвсп = 800 мм.
Наименьшая длина рабочего и вспомогательного хода инструмента получается при первой схеме обработки. Следовательно, эта схема обеспечивает наибольшую производительность. При этом при небольшой мощности станка работа с большой глубиной резания t = 3, … 11 мм невозможна. В этом случае наибольшая производительность будет достигаться по четвертой схеме обработки (рис. 17.5, д).
На рациональный выбор той или иной схемы обработки оказывает влияние и жесткость технологической системы.
Часто при обработке ступенчатых валов крайне важно подрезать уступы после продольного точения. В этих случаях чистовую обработку уступов проводят после обработки всех цилиндрических поверхностей ступенчатой заготовки (рис. 17.6, а).
Чистовую обработку ступенчатых валов целесообразно производить комбинированными резцами, по схеме, приведенной на рис. 17.6, б.
а
б
в г
д
Рис. 17.5. Схемы черновой обработки ступенчатых валов
б
а
Рис. 17.6. Схемы чистовой обработки ступенчатых валов
При обработке валов в центрах величина погрешностей от переустановок вала мала. При обработке в трехкулачковом патроне кулачки последнего для уменьшения биения протачивают на этом же станке, для чего твердость закаленных кулачков не должна превышать HRCэ 35 … 40.
В единичном производстве осевые размеры ступенчатых валов получают настройкой станка на каждый из них методом пробных рабочих ходов, каждый размер длины вала после обработки проверяют измерительным инструментом. Пробные рабочие ходы производят только при обработке первой детали партии. Остальные детали партии заготовок обрабатывают по соответствующим делениям лимбов или по установочным упорам.
Обработка заготовок по лимбам. Современные токарные станки выпускаются промышленностью с лимбами для настройки как поперечной, так и продольной подачи.
Лимб - ϶ᴛᴏ втулка с нанесенными на ней делениями. Предположим, что лимб разделен на 100 равных частей, а винт поперечной подачи имеет резьбу с шагом 5 мм. При полном обороте рукоятки винта͵ то есть на 100 делений лимба, резец переместится на 5 мм в поперечном направлении. В случае если же рукоятку винта повернуть на одно деление, то перемещение резца составит 5 : 100 = 0,05 мм.
Τᴀᴋᴎᴍ ᴏϬᴩᴀᴈᴏᴍ, чтобы проточить деталь с размера 55,2 до 53,4 мм, то есть на 1,8 мм, крайне важно переместить резец вперед на 0,9 мм. На окружности лимба продольной подачи нанесены деления с ценой 0,1 мм. Следовательно, если в начале резания установить лимб на нулевое деление, то определенному продольному перемещению суппорта с резцом соответствует поворот лимба на длину обрабатываемого участка детали. Такой способ обработки существенно сокращает время обработки, особенно деталей ступенчатой формы.
Обтачивание деталей с применением упоров. При обработке больших партий деталей продольное перемещение резца ограничивают продольными упорами, установленными на станине станка. Один упор устанавливают по первой детали вплотную к каретке суппорта͵ второй – на расстоянии длины обтачиваемого участка. При обработке последующих деталей нет крайне важности измерять ее длину, достаточно подвести суппорт к упору так, чтобы его коснулась каретка суппорта. Необходимо лишь периодически проверять, не произошло ли смещение упора или резца.
Обтачивание по копиру. Для повышения производительности в мелкосерийном производстве ступенчатые валы обрабатывают по копирам или шаблонам. Профиль рабочей поверхности копира соответствует профилю обрабатываемой детали.
Точение ступенчатых валов с помощью копировального приспособления осуществляется следующим образом. В центрах токарного станка закрепляют обрабатываемую заготовку. Резец обтачивает первую ступень вала, при этом сухарь, в котором крепится резец, скользит по копиру. Встретив на своем пути ступеньку копира, сухарь соскакивает на нее, резец под действием пружины отходит на расстояние равное глубине ступеньки копира, и начинает обтачивать вторую ступеньку вала и т. д. Для повышения производительности применяют гидрокопировальные устройства.
Смазывающе-охлаждающие жидкости (СОЖ), применяемые при обработке наружных цилиндрических поверхностей. Охлаждение при точении стали повышает стойкость резца, сохраняет его твердость, уменьшает износ, влияющий на точность обработки детали. Применение охлаждающей жидкости, содержащей маслянистые вещества, к примеру эмульсии, облегчает отделение стружки, вследствие чего обрабатываемая поверхность получается чистой.
При обработке заготовок из чугуна охлаждение, как правило, не применяют.
Для охлаждения обрабатываемых заготовок из низколегированных, инструментальных, легированных сталей и стальных отливок применяют эмульсию и сульфофрезол. Заготовки из бронзы и алюминия иногда охлаждают эмульсией и керосином, но чаще всего, обрабатывают без охлаждения.
Количество СОЖ, подводимое к месту резания при черновом точении должно составлять 10 … 12 л/мин. При чистовой обработке количество СОЖ, подаваемое в зону резания должно быть: эмульсии 10 … 12 л/мин, а сульфофрезола – 3 … 4 л/мин.
Читайте также
МЕТАЛЛОРЕЖУЩИЕ СТАНКИ И ИНСТРУМЕНТ МЕТОДЫ МЕХАНИЧЕСКОЙ ОБРАБОТКИ ЗАГОТОВОК. Различные формы обработанных поверхностей получаются в результате совместных перемещений заготовки и режущего инструмента. Различают следующие методы получения... [читать подробенее]
ОБРАБОТКА ЦИЛИНДРИЧЕСКИХ ПОВЕРХНОСТЕЙ ПОВЕРХНОСТЕЙ ДЕТАЛЕЙ МАШИН ЛЕКЦИЯ № 17 РАЗДЕЛ IV. МЕТОДЫ ОБРАБОТКИ ТИПОВЫХПервой технологической операцией является черновая обработка цилиндрической наружной поверхности. Закрепление заготовки производится в... [читать подробенее]
3.Методы обработки плоских поверхностей. 4. Виды финишной обработки. 5. Методы обработки зубьев цилиндрических зубчатых колес. 5. ЭЛЕКТРОФИЗИЧЕСКИЕ И ЭЛЕКТРОХИМИЧЕСКИЕ МЕТОДЫ ОБРАБОТКИ МЕТАЛЛОВ По сравнению с обычной обработкой металлов резанием, электрическая... [читать подробенее]
oplib.ru
Токарная обработка цилиндрических поверхностей
Цилиндрические поверхности обрабатывают при продольном перемещении продольного суппорта или верхнего суппорта. Внешние цилиндрические поверхности обрабатывают обычно проходными резцами, а внутренние расточными.
Приспособления для закрепления заготовок выбирают в зависимости от их формы и размеров. Заготовку типа вал зависимости от отношения ее длины к диаметру рекомендуется закреплять так:
при l / d <4 - в патроне;
при 4 ³ l / d <10 - в центрах;
при l / d> 10 ... 12 - в центрах по дополнительной опорой заготовки на кулачки движимого или недвижимого люнета.
2.2 Обработка конических поверхностей
Конические поверхности на токарном станке могут быть обработаны одним из следующих методов:
- Резцом с наклонно расположенной режущей кромкой;
- С помощью поворота верхней каретки суппорта (верхнего суппорта)
- Смещением задней бабки;
- С помощью копировальной линейки.
Резцом с наклонно расположенной режущей кромкой обрабатывают внешние 1 и 2 внутренних конические поверхности (рис. 38, а), длина которых не превышает 20 ... 25 мм.
С помощью поворота верхнего суппорта обрабатывают наружные и внутренние конические поверхности, длина которых не превышает длины хода верхнего суппорта. Направляющие верхнего суппорта устанавливают под углом j (6, рис. 38, г) к оси вращения заготовки, равный половине угла при вершине обрабатываемого конуса. Подача резца производится вручную.
Методом смещения корпуса задней бабки обрабатывают только внешние конические поверхности, у которых длина образующей сравнительно большая, а угол при вершине конуса не превышает 10 ... 12о. Заготовку в этом случае закрепляют в центрах, а корпус задней бабки смещают в поперечном направлении на величину h (рис. 38, в):
h = L × sin j,
где L - длина заготовки, мм;
j - половина угла при вершине конуса.
С помощью копировальной линейки можно обрабатывать внешние и внутренние конические поверхности большой длины, угол при вершине в которых не превышает 25 °.
На рис. 38, г показано строение одной из конструкций конусной линейки.
Основой конусной линейки служит кронштейн 5, прикрепленный болтами к продольным полозьев суппорта; в кронштейне имеются продольные направляющие в виде ласточкиного хвоста для основы линейки 7. В основу линейки ввернут стержень 8, который другим концом входит в отверстие кронштейна 10 и закрепляется в нем болтом 9.
Кронштейн 10 с помощью болтов 11 закрепляют на станине станка. На верхней плоскости основания линейки установлена конусная линейка 1, в которой сделана прямоугольный паз 6. В пазу находится ползунок 2, с которым с помощью болта 4 соединена тяга 3, второй конец тяги винтами соединен с поперечными салазками суппорта.
При использовании конусной линейкой поперечные салазки отделяют от винта поперечной подачи, для чего обычно винт поперечной подачи вынимают из суппорта. Конусную линейку устанавливают по одной из шкал, нанесенных на концах основы линейки, на угол j, равный половине угла при вершине конуса, обрабатывается, и закрепляют болтами. При продольном автоматическом или ручном перемещении суппорта ползунок 2 и резец перемещаются параллельно образующей обрабатываемого конуса. Необходимую глубину резания устанавливают ручным перемещением верхнего суппорта.
worldofscience.ru
Отделочная обработка наружных цилиндрических поверхностей
Поиск ЛекцийОбтачивание валов
Токарная обработка валов обычно включает черновые и чистовые операции. При черновом точении снимают большую часть припуска, работая с большей глубиной резания и большой скоростью движения подачи.
В единичном и мелкосерийном производствах обтачивание выполняется на токарных универсальных станках. При обработке ступенчатых валов используются различные схемы резания, например, представленная на рис. 1.4.
В схеме на рис. 1.4., в суммарная длина перемещения резца , т.е. меньше, чем в схеме на рис. 1.4., а. Однако, число рабочих и вспомогательных ходов больше.
Рис. 1.4. – Схемы обтачивания валов
При выборе схемы резания стремятся получить максимальную производительность и минимальную себестоимость операции. При этом учитывают размеры вала, способ простановки и контроля размеров, допуски и другие факторы.
Иногда при большой разнице в диаметрах ступеней стремятся как можно дольше не ослаблять вал и ступени наименьшего диаметра обтачивать в последнюю очередь.
При обтачивании длинных не жестких валов применяют неподвижные или подвижные люнеты. Неподвижный люнет устанавливается на станине станка. Подвижный люнет движется на суппорте и его кулачки следуют за резцом (рис. 1.5., а).
Если же необходимо обеспечить соосность обработанной поверхности с поверхностью 2 (рис. 1.5., б), то кулачки люнета располагают впереди резца на поверхности.
Рис. 1.5. – Схема обтачивания вала с использованием люнета
В настоящее время в мелкосерийном производстве используются станки с ЧПУ. Они позволяют автоматизировать цикл обработки, использовать повышенные режимы резания, повысить производительность, применить многостаночное обслуживание, сократить дефицит высококвалифицированной рабочей силы, уменьшить брак, сократить сроки подготовки производства.
В крупносерийном и массовом производствах для обтачивания валов применяют многорезцовые и гидрокопировальные станки и полуавтоматы. Обычно они имеют 2 суппорта – продольный и поперечный, служащие для подрезания торцов, растачивания канавок и фасонного точения.
Суппорты могут работать одновременно. На многорезцовых станках в случае необходимости применяют обтачивание с врезанием и последующей продольной подачей (рис. 1.6., б).
Рис. 1.6. – Схема обтачивания вала на многорезцовом полуавтомате
По сравнению с универсальными токарными станками, многорезцовые станки позволяют повысить производительность за счет сокращения длины рабочего хода, одновременной работой резцов, а также за счет устранения затрат времени на смену резцов, поворот резцедержателя и холостые перемещения суппорта.
На продольном суппорте гидрокопировального станка устанавливается 1 резец, который настраивается на размер только по одной шейке вала. Получение остальных размеров обеспечивается копиром и следящей системой. Одновременно сокращается число измерений, применяется более высокий режим резания, чем при работе с ручным включением подач.
Валы обтачиваются за один или несколько рабочих ходов, при этом смена копиров производится автоматически за счет поворота барабана с копиром.
В тех случаях, когда вал может быть обработан на гидрокопировальном и одношпиндельном многорезцовом полуавтомате, выбор оборудования делается на основании технико-экономического анализа.
При этом учитываются следующие соображения:
1. При многорезцовом обтачивании с делением длины обработки, длина рабочего хода меньше, чем при копировальной обработки.
2. Время наладки и подналадки гидрокопировальных станков значительно меньше, чем для многорезцовых станков.
3. Количество резцов и режимы резания на многорезцовых станках часто ограничиваются податливостью заготовки и недостаточной мощностью станка. На гидрокопировальном станке можно работать с большими скоростями подачи главного движения резания.
4. В связи с изложенным производительность гидрокопировальных станков во многих случаях выше.
5. На точность многорезцовой обработки влияют погрешности относительного расположения и неодинаковый износ резцов. При обработке одной поверхности несколькими резцами на границах участков образуются уступы. На гидрокопировальных станках эти погрешности отсутствуют, поэтому удается получать более высокую точность размеров и меньшую шероховатость.
Отделочная обработка наружных цилиндрических поверхностей
Для отделочной обработки наружных цилиндрических поверхностей применяют тонкое точение, шлифование, полирование, притирку, суперфиниш, обтачивание роликами и т.п.
Тонкое точение
Тонкое точение чаще применяется для отделочной обработки заготовок из цветных металлов и сплавов, реже для заготовок из стали и чугуна. Объясняется это трудностями шлифования цветных сплавов вследствие «засаливания» шлифовального круга.
Обработка производится алмазными, композитными, металлокерамическими резцами и резцами, оснащенными твердыми сплавами, при высоких скоростях главного движения резания, малых скоростях движения подач и глубинах резания.
Тонкое точение позволяет получить 6…7 квалитет точности обработки и шероховатость поверхности мкм.
Производительность обработки выше, чем при шлифовании. В крупносерийном и массовом производствах для тонкого точения применяют специальные быстроходные станки высокой точности и виброустойчивости.
Шлифование
Оно является основным методом чистовой обработки наружных цилиндрических поверхностей. Преимуществами шлифования является возможность исправления погрешностей заготовки после термообработки. При обычном тонком шлифовании осуществляется обработка по 6-7 квалитету точности, при шероховатости поверхности 1,2…0,3 мкм.
Тонкое шлифование дает 5 квалитет точности и шероховатость 0,16…0,8 мкм. Оно осуществляется малозернистым кругом при большой скорости его вращения, малой скорости вращения заготовки, малой глубине резания.
Шлифование осуществляется на кругло- и бесцентрошлифовальных станках с продольной подачей круга или по способу вращения (рис. 1.7.)
А – с продольной подачей; Б, В – по способу (методу) вращения
Рис. 1.7. – Схема шлифования на кругло-шлифовальном станке:
Шлифование по способу вращения более производительно, применяется в крупносерийном и массовом производстве при обработке цилиндрических и фасонных поверхностей.
Для одновременного шлифования нескольких шеек используются специальные станки, работающие несколькими кругами с целью сокращения вспомогательного времени при шлифовании, применяются устройства активного контроля, позволяющие измерять заготовки в процессе шлифования, а также устройства автоматической остановки станка при достижении заданного размера.
При бесцентровом шлифовании (рис. 1.8.) заготовка помещается между двумя шлифующими кругами, из которых один (большего диаметра) является шлифующим, а с другой – ведущим.
Рис. 1.8. – Схема бесцентрового шлифования
Шлифующий круг 1 вращается со скоростью 20-35 м/с, ведущий круг 2 – со скоростью 20-30 м/мин. Заготовка 3 ничем не закрепляется, но поддерживается опорой 4 со скосом, направленным в сторону ведущего круга.
Сила сцепления заготовки с ведущим кругом больше, чем со шлифующим. Это объясняется следующими причинами:
1. Увеличение силы резания при уменьшении скорости вращения круга
2. Изготовление ведущих кругов на связи, увеличивающей коэффициент трения между кругом и заготовкой.
За счет сцепления с ведущим кругом заготовка вращается с окружной скоростью, которая меньше окружной скорости ведущего круга всего на 1-3%.
При бесцентровом шлифовании с продольным движением подачи заготовки ось ведущего круга не параллельна оси шлифующего круга. Благодаря этому без специального механизма подачи обеспечивается перемещение заготовки со скоростью где - скорость вращения ведущего круга.
С увеличением угла скрещивания осей кругов производительность обработки возрастает, но качество поверхности ухудшается, поэтому обычно .
Для повышения точности обработки иногда выполняют сквозное шлифование за несколько рабочих ходов. В крупносерийном и массовом производствах обработка может выполняться последовательно на нескольких станках, соединенных в автолинию.
При бесцентровом шлифовании по способу врезания оси кругов чаще всего параллельны. Сначала ведущий круг отводится от шлифующего, и заготовка устанавливается на опору, затем ведущий круг подводится к заготовке и осуществляется поперечная подача до получения заданного размера.
По сравнению со шлифованием в центрах бесцентровое шлифование имеет следующие преимущества:
1. Отпадает необходимость центрирования заготовки, что особенно важно для деталей, обрабатываемых на револьверных станках и автоматах;
2. Значительно уменьшаются припуски на обработку, т.к., благодаря использованию в качестве технологической базы обрабатываемой поверхности, устраняется влияние на припуск погрешности зацентровки;
3. Отпадает необходимость использования люнетов при шлифовании длинных и тонких валов;
4. Бесцентрошлифовальные станки сравнительно легко автоматизируются и встраиваются в автолинию;
5. Обеспечивается более высокая производительность, чем при шлифовании в центрах;
6. Благодаря простоте управления станком, высокая точность достигается при средней квалификации шлифовщика;
7. Погрешность обработки, вызываемая износом круга, в 2 раза меньше, чем при шлифовании в центрах, т.к. износ круга непосредственно отражается на величине диаметра заготовки, а не на величине радиуса.
В то же время бесцентровое шлифование имеет определенные недостатки:
1. Затраты времени на наладку и регулировку таких станков достаточно велики и окупаются при больших партиях заготовок. Поэтому бесцентровое шлифование чаще всего применяют в автотракторной и подшипниковой промышленности.
2. шпоночные пазы, канавки, отверстия, разрывы обрабатываемой поверхности препятствуют нормальной работе и даже делают её невозможной.
3. При бесцентровом шлифовании трудно обеспечить круглость обрабатываемой поверхности.
4. Затрудняется достижение соосности шлифуемой поверхности с другими ранее обработанными поверхностями.
poisk-ru.ru
Обработка внешних цилиндрических поверхностей - Энциклопедия по машиностроению XXL
Технические условия изготовления втулок. Для получения точных размеров и форм втулок обработку внешней цилиндрической поверхности обычно производят по -2-му (и реже по 3-му) классу точности по посадкам, обеспечивающим требуемую величину натяга при запрессовке втулки в сопряжённую деталь, обработку внутренней цилиндрической поверхности — по 2-му классу точности по системе отверстия. Для ответственных сопряжений (втулки под поршневой палец быстроходного двигателя внутреннего сгорания) отверстия втулок обрабатывают по 1-му классу, а для грубых — по 3-му классу и ниже. Окончательный размер отверстия получают обычно после запрессовки втулки в место сопряжения. В зависимости от назначения соединения и от обработки после запрессовки разностен-ность втулок допускается в пределах 0,03— [c.144] ОБРАБОТКА ВНЕШНИХ ЦИЛИНДРИЧЕСКИХ ПОВЕРХНОСТЕЙ [c.646]При настройке станка следует стремиться к получению размера, лежащего ближе к нижнему предельному размеру (при обработке внешних цилиндрических поверхностей) и тогда большая часть поля допуска может быть использована для компенсации износа резца. [c.16]
Круглое внешнее шлифование обычно применяется для обработки наружных цилиндрических поверхностей. В этом случае обрабатываемая деталь, зажатая в центрах или в патроне станка, и шлифовальный круг осуществляют следующие движения [c.363]
Круглое внешнее шлифование в центрах применяется для обработки наружных цилиндрических поверхностей. В зависимости от конструкции станка оно может быть осуществлено разными способами. [c.390]
На первых двух позициях токарной обработки с одной установки базового торца и внешней цилиндрической поверхности наружного кольца роликоподшипника основными базами являются узкий торец и отверстие. На двух последующих позициях токарной обработки базами являются второй торец и наружная цилиндрическая поверхность. [c.455]
На первых двух позициях для токарной обработки с одной установки базового торца и внешней цилиндрической поверхности наружного кольца роликоподшипника базами являются узкий торец и отверстие. [c.350]
При базировании по внешней цилиндрической поверхности с установкой на призму для обработки плоскости в размер (рис. 8) предельные отклонения измерительной базы А и А" относительно установленного на размер инструмента А " определяются величиной А А" или разностью к —Н[ при этом е. = Л Л" = ОЛ —ОЛ" [c.39]
При наружном осмотре выявляются внешние дефекты трещины, следы грубой механической обработки на цилиндрической поверхности шейки и шипа цапфы, видимые невооруженным глазом (подрезы, глубокие риски и др. ). [c.52]
Для обработки отверстия и внешней цилиндрической поверхности с очень высокими требованиями к их концентричности рекомендуется применять оправки, показанные на рис. 4.15. Обработку в таких оправках производят следующим образом. Заготовку вкладывают [c.157]
Для обработки заготовок, устанавливаемых двумя внешними цилиндрическими поверхностями, применяют оправки, показанные на рис. 4.16. Центрируют заготовку цилиндрическим отверстием и конусными выступами, выполненными в оправке 2. Для центрирования одновременно по двум диаметрам цилиндрическое отверстие оправки должно иметь небольшую глубину (по образующей) 1—2 мм. [c.158]Рис. 4. 16 Оправка для обработки заготовок, устанавливаемых двумя внешними цилиндрическими поверхностями | ![]() |
При обработке нередко возникает такая ситуация, при которой по разным синтетическим схемам воспроизводятся поверхности, близкие по внешнему виду. Например, гиперболоид вращения и цилиндр становятся различными только при больших отклонениях в их форме. Структурные схемы для их воспроизведения отличаются только одним параметром — параллельностью образующей и размещением ее в одной или разных плоскостях. Чем меньше параметр, тем больше сходство поверхностей. Но если такой параметр есть, то цилиндр следует отнести к фиктивной поверхности, а гиперболоид вращения — к действительной поверхности. И только, зная действительное соотношение в движениях, можно прогнозировать нарастание или спад ошибок при обработке цилиндрических поверхностей. Упомянутый параметр имеет материализованное значение на станке и может быть выражен через износ или перекос направляющих суппортов. [c.420]
На фиг. 359 приведен типовой пример применения цифрового программного управления с прямоугольным циклом токарно-револьверного станка модели КРК 25 для обработки детали с внешними цилиндрическими ступенчатыми участками обрабатываемой поверхности и ступенчатым отверстием, а на фиг. 360 — пример применения двухмерного копирования для обработки конической шестерни. Цифровое управление прямоугольными циклами револьверного станка модели КРК 25 выполнено по схеме, показанной на фиг. 361. [c.388]
Металлизированные поверхности по своему внешнему виду и по некоторым свойствам подобны поверхностям литых материалов. Вид и характер поверхности определяются размерами зерен (распылом) и способом подготовки поверхности. Соответственно назначению изделий, могут применяться различные методы обработки металлизационного слоя и последующей термической обработки. Требуемого качества поверхности и точности размеров при обработке металлизированных изделий круглого сечения с учетом структуры металлизационного слоя можно достигнуть токарной обработкой или шлифованием в такой же степени, как и подвергавшихся обработке давлением или литых изделий. Сверление, долбление и строгание металлизационных покрытий применимы лишь при определенных условиях. Металлизация наружных и внутренних цилиндрических поверхностей применяется большей частью для деталей машин, которые перед их использованием должны пройти чистовую токарную обработку или шлифование с соблюдением размеров. [c.68]
Обтачивание цилиндрических поверхностей с револьверной головки рекомендуется совмещать с обработкой отверстий, а обработку фасок и внешних торцов деталей совмещать с отрезанием недопустимо совмещение отрезания с обдирочными или други.мн переходами, требующими значительных усилий. [c.276]
Обтачивание цилиндрических поверхностей револьверной головкой рекомендуется совмещать с обработкой отверстий, а обработку фасок и внешних торцов деталей совмещать с отрезкой [c.318]
Черновая и чистовая токарная обработка торца и отверстия и черновая обработка свободной части наружной цилиндрической поверхности при установке детали на торец и при центрирующем зажиме по внешней цилиндрической или конической поверхности. [c.217]
Есть стаканы, у которых фланец расположен на краю, где находится дно, а не со стороны открытого торца. Такие стаканы обрабатывают, как сложные втулки, причем в качестве чистовой базы принимают цилиндрическую поверхность фланца и его внешний торец. Из этого следует, что окончательная обработка фланца производится в первую очередь. Осевые размеры выдерживают от внешнего торца дна. Такое построение технологии позволяет механизировать получение этих размеров. [c.291]
Подготовленные с первой установки поверхности принимают за базу для дальнейшей обработки детали. При помощи этой базы подрезают внешний торец дна (рис. 219, г), а за ним второй торец фланца в размер (рис. 219, ), обтачивают наружную цилиндрическую поверхность (рис. 219, е). С третьей установки, для которой в качестве базы используются поверхности, обработанные со второй установки, растачивают начисто отверстие (рис. 219, ж) и начисто же подрезают открытый торец (рис. 219, з). [c.297]
При сжатии подобных цилиндрических заготовок из одного и того же металла, но разных по размеру сопротивление деформации тем больше, чем меньше размер образца. С. И. Губкин объясняет этот эффект тем, что для меньшего по размерам образца создаются в большей степени условия для всестороннего объемного сжатия за счет относительно более сильного развития контактной поверхности и возникновения относительно больших напряжений сжатия от сил контактного трения. Однако эффект увеличения напряжения — незначительный, и, видимо, более существенное значение фактора FjV обусловлено большей относительной развитостью поверхности и за счет этого более существенным воздействием внешней среды на пластичность и сопротивление деформации меньших по объему образцов. При этом на изменение пластичности и сопротивление деформации оказывают влияние 1) окружающая среда 2) состояние поверхности слоев, сформировавшихся по структуре и свойствам в результате обработки резанием 3) контактное трение и поверхностное натяжение. [c.480]
К числу таких нужно, в первую очередь, отнести заготовки, у которых преобладают плоские внешние и цилиндрические обрабатываемые поверхности. Трудоемкость различных способов обработки этих двух видов-поверхностей следует рассмотреть с учетом масштабов производства, точности изготовления и способа обработки. [c.458]
Для ферритных сталей заготовку очищают от окалины сначала механическим способом, а в дальнейшем — автоматически в процессе высадки все последующие операции проходят без повторного нагрева. Если обрабатываются аустенитные стали, то делают остановки после прошивки и удаления заусенцев черновой штамповки, а также после сверления и удаления дефектов с внешней поверхности, которые имеют форму небольших гофров или задиров. Для экструзии аустенитных сталей используют суспензию стекла, которой покрывают заготовки после механической обработки. Это предотвращает появление окалины, а также действует как смазка. Экструзией обычно можно получить более длинные и более толстостенные трубы, чем при горячем осаживании, а полые цилиндрические заготовки длиной до 1,15 м с толщиной стенки 11 см удлинить До 4,5 м. [c.65]
На рис. 9 показана зависимость высоты неровностей от усилия обкатывания при обработке внешней цилиндрической поверхности титана ВТЫ диаметром Дз = 47,5 мм и исходной шероховатостью по 6-му классу шаром диаметром , = 15 мм (5 = 0,097 мм/об 3=800 об/мин) обкатыванием (кривая I) и виброобкатыва- [c.37]
Приспособление предназначено для чистовой обработки косых пазов на внешней цилиндрической поверхности тонкостенного кольца 1 значительного диаметра. В связи с этим деталь центрирована и зажата с помощью-упругой мембраны 2. Зажимной механизм приводится в действие вращением червяка 3 при помощи электро- или пневмодрели, или вручную. [c.303]
Точность обработки кулачковых шайб характеризуется следующими данными для двигателей Райт Циклон 0-100 (венец внутренн его зацепления) допуск на толщину зубьев — 0,2 жл (модуль 2,54 лелс) боковой зазор в зубьях при зацеплении с эталонной шестерней (при номинальном расстоянии между центр, ми) — 0,15- -0,35 мм. Допуск на неконцентричность начальной окружности, периферической поверхности зубьев, осевого отверстия, ступицы внешней цилиндрической поверхности — до0,05лл биение торцов ступицы — до0,05 мм допустимое отклонение угла развала кулачков — до 0,5°. [c.304]
Установку заготовки подшипника (рис. 34, в) при растачивании отверстия производят по нижней 6 и торцовой 7 плоскостям с центровкой по аружной цилиндрической поверхности 8 призматическим зажимающим элементом 9. Эта схема позволяет точно выдержать размер Л, но не обеспечивает равностенность детали в вертикальной плоскости, так как оси отверстия и внешнего контура могут не совпадать. Требование равностенности удовлетворяется базированием детали по внешней цилиндрической поверхности при растачивании с последующей обработкой плоскости 6 от отверстия для выдерживания размера А. [c.60]
В результате пересмотра конструкции вилка заменена рычагом (фиг. 627, б) с таким расположением сопрягаемых поверхностей, при котором обработка сводится к сверлению отверстий и торцовке бобышек на сверлильном станке, исходя из того положения, что обработка внешних поверхностей прош,е и экономичнее обработки внутренних. Поэтому, например, канавки для смазки лучше делать не на внутренней поверхности цилиндрического отверстия (фиг. 628, а), а на наружной цилиндрической поверхности сопряженной деталй (фиг. 628, б). [c.606]
Отслаивание баббита. Трещины. Раковины и инородные включения Внешний осмотр. Простукн-ва.ше баббитовой поверхности латунным молотком массой 0.5 кг Допускается отсланввиие до 20% цилиндрической поверхности баббитовой заливки при условии отсутствия на отслоенной поверхности трещин и раковин. Не допускается,- трещины любых размеров и отслаивание баббита упорных буртов наличие раскрытых трещин, раковин и инородных включений в зоне угла контакта, равного 45 . Площадь одиночной наплавки при ремонте баббитовой заливки не более 2 дм Вырубка дефектны. мест. Наплавка баббита. Шабровка. При наличии недопустимых дефектов — перезалнака вкладыша. Механическая обработка [c.311]
Хонингование представляет собой обработку поверхностей абразивными брусками, закрепленными на внешней или внутренней поверхности хонинговальной головки, которая получает непрерывное вращение в одном направлении и возвратно-поступательное движение вдоль оси. Радиальная подача осуществляется периодическим расжатием брусков хона при обработке внутренних поверхностей и сжатием — для наружных (см. рис. 183, к). Хонингованием обрабатывают цилиндрические поверхности как гладкие, так и пересеченные шпоночными и щлицевыми канавками, а также некоторые виды конических, плоских и фасонных поверхностей. При работе бруски хона направляются предварительно обработанной поверхностью, поэтому точность хонингования мало зависит от точности станка, так как хон с помощью универсальных шарниров имеет возможность самоустановки. [c.264]
На чертеже конического зубчатого колеса обозначают внешний диаметр вершин зубьев до притупления кромки dae и внешний диаметр вершин зубьев после притупления кромки daet поскольку КиНус вершин зубьев и внешний делительный дополнительный конус на поверхности колеса не пересекаются. Они связаны цилиндрической поверхностью диаметром d ae- Наличие этой поверхности обусловлено тем, что часть цилиндрической поверхности заготовки длиной Л- сохраняется при обработке по конусу вершин зубьев и внешнему делительному дополнительному конусу. Величину 1 х для мелкомодульных конических зубчатых колес принимают равной 0,1 мм. Внешние диаметры вершин зубьев [c.313]
Метод формообразования внешних фасонных поверхностей цилиндрических деталей путем накатывания их вращающимся инструментом в холодном состоянии взамен обработки резанием довольно распространен. Ои широко применяется для накатки резьб, мелкошлицевых валов, рифлений, клейм и маломодульных зубчатых [c.620]
К окончательным отделочным процессам обработки деталей относится также обработка поверхностей без снятия стружки — пластическим деформированием. Обычно для этих целей применяют обкатывание гладки.ми роликами и шариками и нанесение рифлений на поверхность накатыванием специальными роликами с насечками, зубчики которых деформируют цилиндрические поверхности, придавая им рифленую поверхность, удобную для пользовашш при переключении и красивую внешне. [c.75]
Метод формообразования внешних фасонных поверхностей цилиндрических деталей путем накатывания их вращающимся инструментом в холодном состоянии взамен обработки их резанием получил значительное распространенпе. Он широко применяется для накатки резьб, мелкошлицевых валов, рифлений, клейм и маломодульных зубчатых колес. К преимуществам накатывания перед обработкой со снятием стружки относятся высокая производительность (например, при накатывании резьбы плашками она в 16 раз выше, чем при нарезании ее лерками), низкая стоимость обработки, экономия металла и наряду с этим повышение механической и усталостной прочности деталей. Более высокая прочность и износостойкость накатанных деталей обусловлена тем, что волокна металла прп формообразовании, например зубьев шестерен, пластическим деформированием не перерезаются, а вдавливаются, огибая контур зубчатой поверхности колеса, получающей прп этом наклеп. [c.245]
Методом круглого шлифования пользуются при обработке наружных цилиндрических и конических поверхностей. Методом плоского шлифования — при обработке плоскостей методом внутреннего шлифования — нри обработке цилиндрических и конических отверстий. Методом бесцентрового шлифования обрабатывают внешние и внутренние поверхности вращения. Фасонные поверхности шлифуют этими методами с подющью фасонных кругов. Для фасонной правки круга устанавливают дополнительный механизм. Кроме того, фасонное шлифование производят на специализированных фасонно-шлифовальных станках. [c.585]
В серийном производстве на токарный станок обычно поступает заготовка с начерно просверлерным отверстием и начисто обработанными наружной цилиндрической поверхностью и одним из торцов. Поэтому здесь за чистовую базу принимают цилиндрическую поверхность детали и начинают обработку с подрезания внешнего торца дна (см. рис. 201, з). В следующей операции производится окончательная обработка отверстия (рис. 201, н), которую можно выполнять комбинированным резцом, имеющим дополнительную режущую кромку а для снятия внутренней фаски. [c.277]
Зеркальная поверхность втулки проходит сложный процесс обработки. Цилиндрическая поверхность зеркала втулки после хонингования должна иметь овальность, конусность, бочкообраз-ность и корсетность не более 0,03 мм. Биение верхнего и нижнего внешних цилиндрических базовых поясов втулки относительно зеркала не должно превышать 0,03 мм. Посадочные бурты втулки и рубашки проверяют по краске, прилегание не менее 60% поверхности. Рубашку напрессовывают при нагреве до 100°С. Для проверки на герметичность цилиндр опрессовывают водой под давлением 4 кгс/см2. [c.35]
На рис. V-22 изборажена схема токарной обработки внутренних колец подшипника 307К1 на шестишпиндельном автомате. Заготовкой для колец служит труба. На автомате последовательно выполняются три операции (/-///). На операции I одновременно в двух позициях 1 м 2 происходит отрезка готового кольца, съем его и подача трубы до упора. На операции II (позиции 3 н 4) обтачивается наружная цилиндрическая поверхность, растачиваются отверстия и внешние фаски, прорезаются чашечными резцами паз и желоб. На операции III (позиции 5 к 6) производится окончательное обтачивание желоба, подрезка торца и снятие внутренней фаски. [c.150]
Операция значительно ускоряется, если при каждом следующем переходе направление обработки, а следовательно, и рисок будет под углом 60—90° к предыдущему. При шлифовании длинных цилиндрических деталей малого диаметра такой большой угол выдержать трудно, но хотя бы меньший угол (20—30°) выдержать нужно, иначе работа затруднится и замедлится. Часто оказывается далеко не безразличным для внешнего вида окончательно полированной детали, в каком направлении был сделан последний переход при шлифо-кяльной обработке лля плоских продолговатых деталей — это в большинстве случаев направление вдоль более длинной стороны, для цилиндрических поверхностей — по окружности. [c.132]
Участок состоит из фрезёрно-цеНтровального станка, двух токарных полуавтоматов, автоматического манипулятора и вспомогательных устройств. Фрезерно-и ентровальный станок обеспечивает обработку торцов и центральных отверстий. Токарный полуавтомат с системой ЧПУ Н22-1М обеспечивает обработку цилиндрических, конических и сферических поверхностей, прорезку канавок и нарезание резьбы. Автоматический манипулятор обеспечивает установку—снятие деталей и их межстаночное транспортирование при линейном расположении станков па участке. Грузоподъемность манипулятора — 160 кг, погрешность позиционирования не более 1мм при максимальной скорости перемещения отдельных звеньев 0,8—1,8 м/с. Манипулятор оснащен датчиками внешней информации и выполняет в адаптивном режиме широкий круг операций, включая поиск деталей в накопителе, измерения диаметра и длины заготовки, отбраковки заготовок с недопустимыми отклонениями размеров, перебазирование деталей, их промежуточное складирование и укладку в выходной таре. Программирование автоматического манипулятора осуществляется методом обучения. [c.31]
Зубошевннгованне дисковым шевером является наиболее распространенным и экономичным методом чистовой обработки зубьев незакаленных (с твердостью до ИКС 33) прямозубых и косозубых цилиндрических колес с внешним и внутренним зацеплением после зубофрезерования или зубодолбления. Шевингование применяют для повышения точности зубчатого зацепления, уменьшения параметра шероховатости поверхности на профилях зубьев, снижения уровня шума и т. д. Шевингованием можно повысить точность на одну-две степени. Точность шевингованных зубчатых колес достигает 6 —8-й степени, параметр шероховатости поверхности Ка = 0,8 -ь 2,0 мкм. Точность зубчатых колес в процессе шевингования зависит главным образом от их точности после зубофрезерования или зубодолбления и коэффициента перекрытия шевера с обрабатываемым колесом, который должен быть не менее 1,6. При шевинговании можно проводить продольную и профильную модификацию зуба. При образовании продольной бочкообразности исключается опасность концентрации нагрузки на концах зубьев. Модификация эвольвентного профиля зубьев позволяет уменьшить уровень шума и повысить срок службы зубчатой передачи. Модификацию формы зуба проводят также для компенсации деформации в процессе термической обработки. [c.349]
Зубохонингование применяют для чистовой отделки зубьев закаленных цилиндрических колес внешнего и внутреннего зацепления. Хонингование зубьев осуществляют на специальных станках. Закаленное обрабатываемое колесо вращается в плотном зацеплении с абразивным зубчатым хоном при угле скрещивания осей 10—15°. Поджим детали,к хону осуществляется пружиной с силой 150 — 450 Н. Зубчатое колесо, кроме вращения, совершает возвратно-поступательное движение вдоль оси. Направление вращения инструмента меняется при каждом ходе стола. Хонингование позволяет уменьшить параметр шероховатости поверхности до Яа = 0,32 мкм, удалить забоины и заусенцы размером до 0,25 мм, снизить уровень звукового давления на 2 — 4 дБ и повысить долговечность зубчатой передачи. В процессе хонингования погрешности в элементах зацепления устраняются незначительно при съеме металла порядка 0,01—0,03 мм на толщину зуба. Припуск под хонингование не оставляют. Частота вращения хона 180 — 200 об/мин, подача стола 180 — 210 мм/мин, число ходов стола четыре — шесть. Время хонингования зубчатого колеса автомобиля 30 — 60 с. Срок службы монокорундовых хонов при обработке зубчатых колес коробки передач автомобиля — 1500 — 3000 деталей. Зубчатые колеса, имеющие забоины и заусенцы перед хонингованием, целесообразно обкатывать на специальном станке или приспособлении между тремя накатниками под нагрузкой для устранения погрешностей профиля зубьев. Забоины и заусенцы на зубьях обрабатываемого колеса сокращают срок службы и вызывают преждевременную поломку зубьев хона. [c.353]
mash-xxl.info