Большая Энциклопедия Нефти и Газа. Основные прочностные характеристики стали
Механические свойства стали
Без сомнения наиболее важными свойствами сталей, благодаря которым они находят такое широкое применение, являются их механические свойства. Эти свойства включают комбинацию очень высокой прочности со способностью к значительному изменению формы, например, пластическому прогибу, перед окончательным разрушением. Чтобы характеризовать прочность и пластичность (меру пластического прогиба) сталей и других металлов разработаны различные методы испытаний.
Прочность сталей
Механические свойства сталей, как и других металлических материалов, чаще всего определяются с помощью испытания на растяжение. Испытание на растяжение заключается в приложении растягивающего усилия к образцу – чаще всего, в виде стержня – и измерении изменения длины образца при увеличении прилагаемого усилия (рисунок 1). Образец вырезают из интересующего материала или изделия. Результат испытания представляет собой диаграмму растяжения — график, на котором по вертикали откладывается напряжение (усилие на единицу площади образца), а по горизонтали – деформация (относительное изменение длины образца).
Рисунок 1 – Диаграмма напряжение-деформацияпри испытании образца на растяжение
При малых деформациях стержень ведет себя упруго – он «отпружинивает» обратно к своей исходной длине, если приложенные напряжения снимают. При напряжении выше величины, которую называют пределом текучести, стержень начинает деформироваться пластически. Это значит, что после снятия прилагаемых напряжений стержень уже не возвращается к своей исходной длине, а получает необратимое удлинение. Путем растяжения стержня до разрушения находят максимальное напряжение на диаграмме растяжения. Это максимальное напряжение называют прочностью при растяжении или временным сопротивлением растяжению материала, из которого был изготовлен образец.
Пластичность сталей
Если при простом испытании на изгиб металл разрушается только после большого пластического прогиба, то его считают пластичным. Если такого прогиба нет совсем или он незначительный – материал называют хрупким. Хорошая пластичность металла проявляется при испытании на растяжение высокой величиной удлинения образца и/или его сужения. Удлинение выражает в процентах увеличение длины образца после разрушения к его исходной длине (см. рисунок 1). Аналогично сужение выражает в процентах уменьшение площади образца по сравнению с его исходной площадью (рисунок 2).
Рисунок 2 – Диаграмма растяжения для хрупкого и пластичного металлов
Чаще всего механические свойства сталей в целом оценивают по трем показателям: пределу прочности, пределу текучести и удлинению. Пределы прочности и пластичности обычно выражают в мегапаскалях (МПа), удлинение – в процентах (%). Практически всегда с увеличением прочности металла или сплава его пластичность снижается.
Твердость сталей
При испытаниях на твердость механические свойства сталей оценивают путем внедрения в него при заданном усилии твердого материала, так называемого индентора (рисунок 3). Часто такой индентор изготавливают из алмаза. В результате испытания в материале образуется отпечаток – по его размерам судят от твердости стали: в испытании по Роквеллу — по глубине отпечатка, в испытаниях по Бриннелю и Викерсу – по его ширине.
Рисунок 3 – Схема испытания на твердость и его основные характеристики
Соотношение прочности и твердости сталей
В закаленных и отпущенных сталях наблюдается хорошая корреляция между пределом прочности и твердостью – по твердости можно оценивать прочность и наоборот. Для термически упрочненных сталей твердость 45 HRC и выше является обычным делом. Твердость 45 HRC соответствует прочности при растяжении 1480 МПа. Если сравнить это с самыми прочными промышленными сплавами алюминия, меди и титана, которые грубо имеют прочность соответственно 570, 1220 и 1350 МПа, то станет ясно, что сталь прочнее всех этих материалов.
Вязкость сталей
Важным механическим свойством стали является ее вязкость. Обычно термин вязкость применяют, как меру способности металла разрушаться нехрупко.
Характер разрушения – хрупкий или пластичный – хорошо рассматривать на примере ферритных сталей. Все металлы с объемноцентрированной кубической атомной решеткой – как и ферритные стали – имеют один общий недостаток. Они разрушаются хрупко при низких температурах, тогда как при достаточно высоких температурах разрушаются нормально – пластически. Температура перехода от пластического разрушения к хрупкому называется температурой вязко-хрупкого перехода. Она определяется как температура, ниже которой происходит хрупкое разрушение. Температуру хрупкого перехода можно в принципе определять испытанием на растяжение, но при одноосном растяжении ее величина значительно ниже, чем та, которую наблюдают в сложных стальных деталях. Опыт показал, что испытания на ударную вязкость по методу Шарпи намного лучше согласуются с опытными данными по хрупкому разрушению сложных деталей. Схема метода испытания на ударную вязкость по Шарпи показана на рисунке 4.
Рисунок 4 – Схема ударного испытания по методу Шарпи
Усталость сталей
Усталостное разрушение – это тип разрушения, который происходит в металлических деталях, которые подвергаются циклическим нагрузкам.
Рассмотрим ось на колесах, на которую «давит» довольно тяжелый груз. Это груз вызывает изгиб в центре в точке посередине между колесами, как показано схематически на рисунке 5.
Рисунок 5 – Смена сжимающих и растягивающих напряженияна поверхности вращающейся оси
Этот изгиб заставляет металл растягиваться в точке Т и сжиматься в точке С. Другими словами это означает, что в точке Т металл подвергается растягивающим напряжениям, а в точке С – сжимающим. Поэтому, поскольку ось вращается каждая точка посередине оси подвергается циклическим напряжениям – растягивающим, когда она находится внизу и сжимающим, когда вверху.
В хорошо спроектированной оси максимальные растягивающие напряжения будут далеко ниже предела текучести и все деформации, которые происходят на поверхности металла во время вращения, будут в упругой области, как это показано в нижней части рисунка 5.
Однако, если на поверхности металла есть маленькая царапина, то в этом месте поверхности возникает так называемая концентрация напряжений. Если величина напряжений в этой точке будет превышать предел текучести, то здесь может зародиться трещина. Каждый раз, когда ось делает оборот, эта трещина будет расти, пока не станет достаточно большой, чтобы привести к разрушению оси. Этот процесс называют усталостным разрушением или усталостью сталей. Способность стали сопротивляться циклическим напряжениях называют усталостной прочностью или циклической прочностью. Усталостные разрушения происходят в металлических деталях, которые подвергаются циклическим напряжениям, таких как вращающиеся детали, клапаны, пружины, а также вибрирующие детали, такие как самолетные крылья.
Источник: John D. Verhoeven, Steel Metallurgy for Non-Metallurgists, 2007
steel-guide.ru
Основные свойства и характеристики стали
В промышленном производстве для создания наиболее качественных материалов очень часто используют комбинации из нескольких химических элементов. Особенно распространен такой подход в металлургии, где получаемые сплавы способны работать в таких условиях, которые неподвластны чистым металлам.
Соединения нескольких элементов позволяет добиться уникальных свойств, которые необходимо в той или иной отрасли. Одним из наиболее распространенных сплавов является сталь. Она получается в результате соединения железа с углеродом. Также в массовую долю материала входит незначительное количество примесей. При необходимости в сплав вводят легирующие присадки или покрывают поверхность металла защитным слоем.
Химический состав стали
Свойства и характеристики стали зависят от количественного состава химических элементов в ее структуре. Углерод придает материалу твердости и вязкости, но его повышенное содержание приводит к хрупкости и ухудшает свариваемость. Наиболее качественная сталь получается после обработки отжигом, когда углерод внедряется в структуру металлической решетки железа на молекулярном уровне и образует устойчивое соединение цементит. Содержание кремния в сплаве повышает текучесть и прочность, а также упругость. Но избыток этого элемента ухудшает свариваемость и ударную вязкость. Марганец массовой долей до 2% позволяет повысить прочность материала. При большем процентном содержании сварка становится затруднительной.
Хром защищает сталь от окисления и значительно продляет срок ее эксплуатации. Но при неправильной термической обработке образует карбид, который препятствует сварке. Никель улучшает пластичность, вязкость и ковкость, а также является одним из немногих элементов, повышенное содержание которых не приводит к побочным эффектам. Молибден повышает термическую стойкость стали, а также предельно допустимые нагрузки, поэтому, активно используется в качестве присадок в конструкционных сплавах.
Ванадий улучшает вязкость и упругость, активно способствует процессу закалки, но ухудшает свариваемость. Вольфрам добавляет материалу твердости и стойкости при работе с высокими температурами. Титан повышает коррозийную стойкость стали, но его избыток может приводить к горячим трещинам при сварке. Медь повышает коррозионную стойкость и ковкость металла и не несет негативных эффектов при избытке. Кроме перечисленных элементов, наделяющих сталь положительными свойствами, есть и вещества, чье присутствие несет только негативную нагрузку.
Сера повышает ломкость материала при высоких температурах и затрудняет свариваемость. Фосфор влияет на повышение параметра ломкости при нормальных температурах и тоже ухудшает свариваемость. Азот, кислород и водород отрицательно влияют на прочность и приводят к быстрому старению стали. Содержание негативных элементов должно сводиться к минимуму, чтобы качество материала удовлетворяло потребностям рынка.
Характеристики стали
Твердость стали зависит от массовой доли углерода, а также количества специальных присадок. В основном твердые материалы используются в тех случаях, когда они не будут находиться под воздействием динамической нагрузки, так как с твердостью обычно повышается и хрупкость сплава. Предел прочности стали на растяжение составляет 60 килограммосил на миллиметр квадратный. Остальные значения прочностей напрямую зависят от марки материала. Стойкости к определенному виду негативного воздействия достигаются при помощи закалки металла или введения в сплав нужных присадок.
Предел прочности стали всегда отражается в маркировке, чтобы покупатель мог быстро выбрать нужный ему материал. Удельное сопротивление стали варьируется от 0,103 до 0,137 Ом*миллиметр в квадрате/метр. Величина зависит от количественного содержания химических элементов в сплаве. Для электротехнических сталей показатель сопротивления составляет 0,25-0,6 Ом*миллиметр в квадрате/метр. Столь высокое значение по сравнению с обычной сталью объясняется условиями эксплуатации и соответствует техническим требованиям. Расчетное сопротивление стали может быть разным даже для одной партии изделий, так как количество примесей распределяется не равномерно по всей структуре сплава.
Стальные проводники на практике применяются очень редко, так как есть металлы, обладающие гораздо лучшими параметрами, необходимыми для использования в электротехнике. А вот электротехническая сталь является одним из основных материалов, применяемых при изготовлении корпусов электроприборов и трансформаторов. Теплопроводность стали находится на высоком уровне, что позволяет с успехом использовать материал в отопительных системах. С ростом температуры этот показатель несколько снижается, но общие потери не критичны по сравнению с затратами энергии. Конечно, есть металлы и сплавы с гораздо более высокими параметрами теплопроводности, но их использование является нерентабельным ввиду больших затрат на их производство.
Удельная теплоемкость стали составляет 0,462 килоджоуля/килограмм*Кельвин. Это является неплохим показателем для металла. Данная характеристика показывает, сколько тепловой энергии необходимо передать телу, чтобы его температура изменилась на один градус. То есть, чем меньше этот показатель, тем быстрее нагревается вещество. Фактическое значение теплоемкости стали позволяет еще раз доказать оправданность ее использования в отопительных сетях. К тому же сталь очень хорошо сохраняет полученное тепло и медленно остывает, так что на поддержание температуры на нужном уровне понадобится меньше топлива.
Коэффициент трения сталь-сталь в состоянии покоя составляет 0,15 без использования смазки и 0,1 с ней. При скольжении этот параметр составит 0,15 и 0,05 соответственно. Химические свойства стали зависят от количественного и качественного содержания элементов в сплаве. При необходимости эксплуатации материала в агрессивной среде в его состав вводятся дополнительные присадки, позволяющие не допустить или сильно замедлить протекания разрушительных химических реакций.
promplace.ru
Механические свойства металлов. Механические свойства сталей. Механические свойства сплавов.
Основными механическими свойствами являются прочность, упругость, вязкость, твердость. Зная механические свойства, конструктор обоснованно выбирает соответствующий материал, обеспечивающий надежность и долговечность конструкций при их минимальной массе. Механические свойства определяют поведение материала при деформации и разрушении от действия внешних нагрузок.
В зависимости от условий нагружения механические свойства могут определяться при:
- Статическом нагружении – нагрузка на образец возрастает медленно и плавно.
- Динамическом нагружении – нагрузка возрастает с большой скоростью, имеет ударный характер.
- Повторно, переменном или циклическим нагружении – нагрузка в процессе испытания многократно изменяется по величине или по величине и направлению.
Для получения сопоставимых результатов образцы и методика проведения механических испытаний регламентированы ГОСТами.
Механические свойства металлов, сталей и сплавов. Прочность.
Прочность – способность материала сопротивляться деформациям и разрушению.
Испытания проводятся на специальных машинах, которые записывают диаграмму растяжения, выражающую зависимость удлинения образца Δl (мм) от действующей нагрузки Р, то есть Δl = f(P). Но для получения данных по механическим свойствам перестраивают: зависимость относительного удлинения Δl от напряжения δ.
Диаграмма растяжения материала
Рис 1: а – абсолютная, б – относительная; в – схема определения условного предела текучести
Проанализируем процессы, которые происходят в материале образца при увеличении нагрузки: участок оа на диаграмме соответствует упругой деформации материала, когда соблюдается закон Гука. Напряжение, соответствующее упругой предельной деформации в точке а, называется пределом пропорциональности.
Механические свойства металлов, сталей и сплавов. Предел пропорциональности.
Предел пропорциональности (σпц) – максимальное напряжение, до которого сохраняется линейная зависимость между деформацией и напряжением.
При напряжениях выше предела пропорциональности происходит равномерная пластическая деформация (удлинение или сужение сечения). Каждому напряжению соответствует остаточное удлинение, которое получаем проведением из соответствующей точки диаграммы растяжения линии параллельной оа.
Так как практически невозможно установить точку перехода в неупругое состояние, то устанавливают условный предел упругости, – максимальное напряжение, до которого образец получает только упругую деформацию. Считают напряжение, при котором остаточная деформация очень мала (0,005…0,05%). В обозначении указывается значение остаточной деформации (σ0.05).
Механические свойства металлов, сталей и сплавов. Предел текучести.
Предел текучести характеризует сопротивление материала небольшим пластическим деформациям. В зависимости от природы материала используют физический или условный предел текучести.
Физический предел текучести σm – это напряжение, при котором происходит увеличение деформации при постоянной нагрузке (наличие горизонтальной площадки на диаграмме растяжения). Используется для очень пластичных материалов.
Но основная часть металлов и сплавов не имеет площадки текучести.
Условный предел текучести σ0.2 – это напряжение вызывающее остаточную деформацию δ = 0.20%.
Физический или условный предел текучести являются важными расчетными характеристиками материала. Действующие в детали напряжения должны быть ниже предела текучести. Равномерная по всему объему пластическая деформация продолжается до значения предела прочности. В точке в в наиболее слабом месте начинает образовываться шейка – сильное местное утомление образца.
Механические свойства металлов, сталей и сплавов. Предел прочности.
Предел прочности σв – напряжение, соответствующее максимальной нагрузке, которую выдерживает образец до разрушения (временное сопротивление разрыву).
Образование шейки характерно для пластичных материалов, которые имеют диаграмму растяжения с максимумом. Предел прочности характеризует прочность как сопротивления значительной равномерной пластичной деформации. За точкой В, вследствие развития шейки, нагрузка падает и в точке С происходит разрушение.
Истинное сопротивление разрушению – это максимальное напряжение, которое выдерживает материал в момент, предшествующий разрушению образца (рисунок 2).
Истинное сопротивление разрушению значительно больше предела прочности, так как оно определяется относительно конечной площади поперечного сечения образца.
Истинная диаграмма растяжения
Рис. 2
Fк - конечная площадь поперечного сечения образца.
Истинные напряжения Si определяют как отношение нагрузки к площади поперечного сечения в данный момент времени.
При испытании на растяжение определяются и характеристики пластичности.
Механические свойства металлов, сталей и сплавов. Пластичность.
Пластичность – способность материала к пластической деформации, то есть способность получать остаточное изменение формы и размеров без нарушения сплошности. Это свойство используют при обработке металлов давлением.
Характеристики:
- относительное удлинение:
lо и lк – начальная и конечная длина образца;
Δlост – абсолютное удлинение образца, определяется измерением образца после разрыва.
- относительное сужение:
Fо – начальная площадь поперечного сечения;
Fк – площадь поперечного сечения в шейке после разрыва.
Относительное сужение более точно характеризует пластичность и служит технологической характеристикой при листовой штамповке.
Пластичные материалы более надежны в работе, так как для них меньше вероятность опасного хрупкого разрушения.
www.mtomd.info
Прочностная характеристика - сталь - Большая Энциклопедия Нефти и Газа, статья, страница 1
Прочностная характеристика - сталь
Cтраница 1
Прочностные характеристики стали, термически обработанной на сг0 2 75 кГ / ммг по данным [40], не изменяются под влиянием длительных ( до 10000 час. Для стали, термически обработанной на cr0i2: 65 кГ / мм2, длительные выдержки при 500 - 550 не дают разупрочнения. Ударная вязкость при 20 под влиянием длительных выдержек при 450 - 550 в нагруженном и ненагруженном состояниях испытывает только небольшие изменения, что позволяет считать сталь нечувствительной к тепловой хрупкости. [1]
Прочностные характеристики сталей повышенной и высокой прочности предопределяют значительную экономию металла и широкое их использование в массовом строительстве. [2]
Сравнение прочностных характеристик стали после ВТМО и обычной закалки при одной температуре отпуска не отражает реального повышения прочности, поскольку в результате ВТМО сталь имеет повышенную пластичность, а как известно, надежность работы любой детали в машине определяется в значительной степени способностью материала детали сопротивляться внезапным перегрузкам, которые зависят от пластичности материала. [3]
Повышение прочностных характеристик стали для сварных труб позволяет уменьшить толщину стенки и тем самым повысить экономическую эффективность производства. [4]
Благодаря улучшению прочностной характеристики стали в процессе обработки этот метод позволяет применять в качестве исходного материала для заготовки горячекатаную сталь вместо холоднотянутой, что дает дополнительную экономию от стоимости материала. [5]
Некоторое ухудшение прочностных характеристик стали ХН70ВМТЮ может быть объяснено химическими взаимодействиями стали, содержащей молибден, со стеклосмазкой с повышенным содержанием окиси бора. [7]
Температура также ограничивается прочностными характеристиками сталей, применяемых для изготовления лопаток и дисков турбин. [8]
НТМО еще больше повышает прочностные характеристики стали: о 2700 - 3000 Мн / мг. НТМО используют только для сталей с широкой зоной устойчивого аустенита. [9]
Максимальная твердость, определяющая прочностные характеристики стали и ее конструктивную прочность, получаемые при закалке, обусловлена содержанием углерода в стали. Однако максимальная твердость, которая может быть достигнута при закалке изделий, имеющих большие размеры, чем образцы, зависит также от массы этих изделий, часто не позволяющей получить в структуре 100 % мартенсита. [10]
На рис. 4.4 представлены прочностные характеристики стали ШХ15 в зависимости от твердости. HRC, которая получается в результате отпуска стали при 250 С. [12]
В оснс классификации положена прочностные характеристики стали труб, , воиетричеокие раэиери-попервчного сечения, максимальная стрела прогиба и длина арки. При разработке классификации учтено развитие упругопластическ / а. [13]
Кратковременное азотирование не влияет на прочностные характеристики стали, однако показатели пластичности и величина ударной вязкости существенно снижаются. [14]
Страницы: 1 2 3 4
www.ngpedia.ru
Основные механические свойства стали. Работа стали на растяжение
Главнейшими показателями механических свойств стали являются прочность, упругость и пластичность, характеризуемые напряжениями и удлинениями.
Прочность определяется сопротивляемостью материала внешним воздействиям. Упругость — это свойство материала восстанавливать свою первоначальную форму после снятия внешних нагрузок.
Пластичность — это свойство материала не возвращаться в свое первоначальное состояние после снятия внешних нагрузок, т. е. свойство получать остаточные деформации.
Зависимость между напряжениями и деформациями для различных материалов устанавливается опытным путем. Наиболее простым и надежным испытанием является испытание образцов на растяжение, которым и определяется прочность стали, а также ее упругие и пластические свойства.
«Проектирование стальных конструкций»,К.К.Муханов
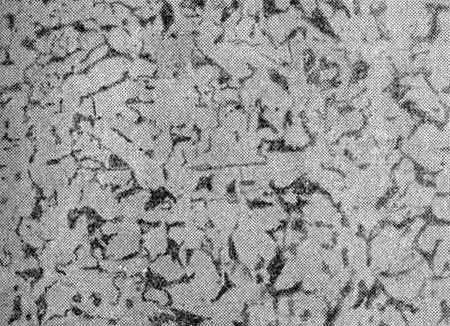
Малоуглеродистая сталь представляет собой однородное кристаллическое тело, состоящее из мелких кристаллов феррита, образующих зерна (Fe — чистое железо), и перлита (смесь цементита Fe3C с ферритом), расположенного главным образом по стыкам ферритных зерен и образующего как бы «сетку» или вкрапления между зернами. Структура стали Ст. 3 (микрошлиф Х 80) Перлит значительно тверже феррита и более хрупок….
При опытном изучении образцов на растяжение устанавливается значение предела текучести σт. При этом в образцах развиваются нормальные линейные напряжения, т. е. имеет место одноосное напряженное состояние. В случае сложного напряженного состояния (например, плоского напряженного состояния, когда образец растягивается в двух направлениях, или при совместном действии нормальных и касательных напряжений при изгибе) переход в пластическое состояние,…
Если подвергнуть образец растяжению, последовательно увеличивая нагрузку Р, и производить при этом замеры получающихся удлинений ∆l, то можно построить опытную диаграмму растяжения, откладывая удлинение в функции нагрузки. Для удобства сравнения эту диаграмму выражают в напряжениях и относительных удлинениях: где σ — нормальное напряжение; F — первоначальная площадь сечения образца; ε — относительное удлинение в процентах;…
www.ktovdome.ru
Предел прочности стали при сжатии и растяжении
Прочность металлических конструкций – один из важнейших параметров, определяющих их надежность и безопасность. Издревле вопросы прочности решались опытным путем — если какое-либо изделие ломалось — то следующее делали толще и массивнее. С 17 века ученые начали планомерное исследование проблемы, прочностные параметры материалов и конструкций из них можно рассчитать заранее, на этапе проектирования. Металлурги разработали добавки, влияющие на прочность стальных сплавов.
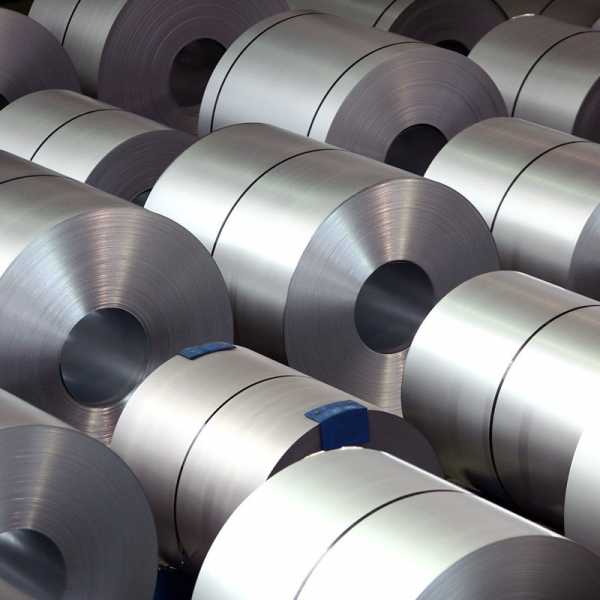
Предел прочности стали
Предел прочности
Предел прочности — это максимальное значение напряжений, испытываемых материалом до того, как он начнет разрушаться. Его физический смысл определяет усилие растяжения, которое нужно приложить к стрежневидному образцу определенного сечения, чтобы разорвать его.
Каким образом производится испытание на прочность
Прочностные испытания на сопротивление разрыву проводятся на специальных испытательных стендах. В них неподвижно закрепляется один конец испытываемого образца, а к другому присоединяют крепление привода, электромеханического или гидравлического. Этот привод создает плавно увеличивающее усилие, действующее на разрыв образца, или же на его изгиб или скручивание.
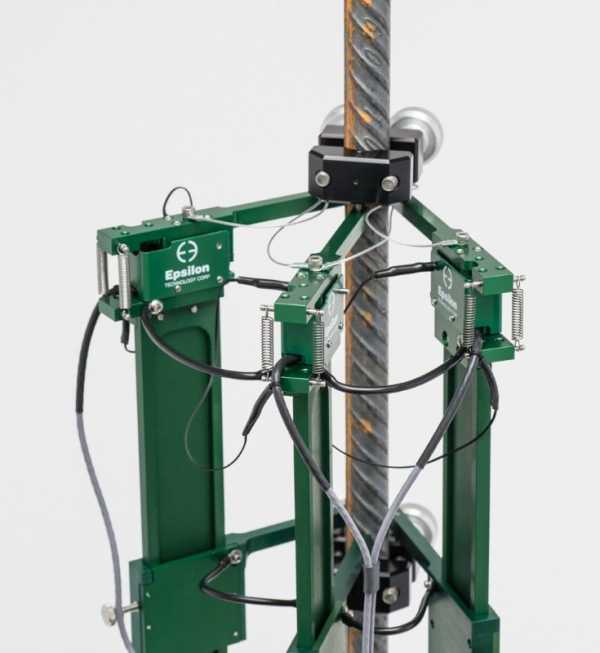
Испытание на разрыв
Электронная система контроля фиксирует усилие растяжения и относительное удлинение, и другие виды деформации образца.
Виды пределов прочности
Предел прочности — один из главных механических параметров стали, равно как и любого другого конструкционного материала.
Эта величина используется при прочностных расчетах деталей и конструкций, судя по ней, решают, применим ли данный материал в конкретной сфере или нужно подбирать более прочный.
Различают следующие виды предела прочности при:
- сжатии — определяет способность материала сопротивляться давлению внешней силы;
- изгибе — влияет на гибкость деталей;
- кручении – показывает, насколько материал пригоден для нагруженных приводных валов, передающих крутящий момент;
- растяжении.
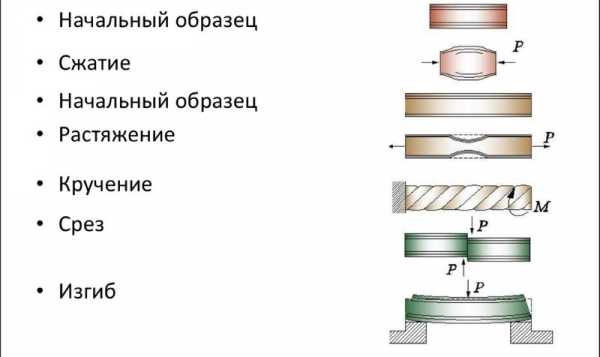
Виды испытаний прочности материалов
Научное название параметра, используемое в стандартах и других официальных документах — временное сопротивление разрыву.
Предел прочности стали
На сегодняшний день сталь все еще является наиболее применяемым конструкционным материалом, понемногу уступая свои позиции различным пластмассам и композитным материалам. От корректного расчета пределов прочности металла зависит его долговечность, надежность и безопасность в эксплуатации.
Предел прочности стали зависит от ее марки и изменяется в пределах от 300 Мпа у обычной низкоуглеродистой конструкционной стали до 900 Мпа у специальных высоколегированных марок.
На значение параметра влияют:
- химический состав сплава;
- термические процедуры, способствующие упрочнению материалов: закалка, отпуск, отжиг и т.д.
Некоторые примеси снижают прочность, и от них стараются избавляться на этапе отливки и проката, другие, наоборот, повышают. Их специально добавляют в состав сплава.
Условный предел текучести
Кроме предела прочности, в инженерных расчетах широко применяется связанное с ним понятие-предел текучести, обозначаемый σт. Он равен величине напряжения сопротивления разрыву, которое необходимо создать в материале, для того, чтобы деформация продолжала расти без наращивания нагрузки. Это состояние материала непосредственно предшествует его разрушению.
На микроуровне при таких напряжениях начинают рваться межатомные связи в кристаллической решетке, а на оставшиеся связи увеличивается удельная нагрузка.
Общие сведения и характеристики сталей
С точки зрения конструктора, наибольшую важность для сплавов, работающих в обычных условиях, имеют физико-механические параметры стали. В отдельных случаях, когда изделию предстоит работать в условиях экстремально высоких или низких температур, высокого давления, повышенной влажности, под воздействием агрессивных сред — не меньшую важность приобретают и химические свойства стали. Как физико-механические, так и химические свойства сплавов во многом определяются их химическим составом.
Влияние содержание углерода на свойства сталей
По мере увеличения процентной доли углерода происходит снижение пластичности вещества с одновременным ростом прочности и твердости. Этот эффект наблюдается до приблизительно 1% доли, далее начинается снижение прочностных характеристик.
Повышение доли углерода также повышает порог хладоемкости, это используется при создании морозоустойчивых и криогенных марок.
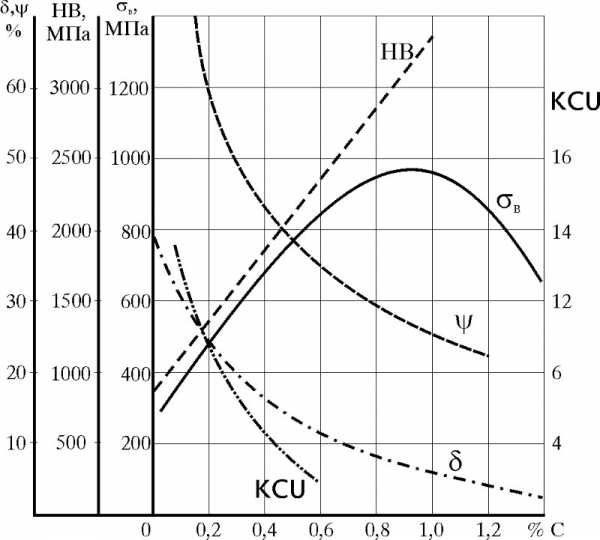
Влияние углерода на механические свойства стали
Рост содержания С приводит к ухудшению литейных свойств, отрицательно влияет на способность материала к механической обработке.
Добавки марганца и кремния
Mn содержится в большинстве марок стали. Его применяют для вытеснения из расплава кислорода и серы. Рост содержания Mn до определенного предела (2%) улучшает такие параметры обрабатываемости, как ковкость и свариваемость. После этого предела дальнейшее увеличение содержания ведет к образованию трещин при термообработке.
Влияние кремния на свойства сталей
Si применяется в роли раскислителя, используемого при выплавке стальных сплавов и определяет тип стали. В спокойных высокоуглеродистых марках должно содержаться не более 0,6% кремния. Для полуспокойных марок этот предел еще ниже — 0,1 %.
При производстве ферритов кремний увеличивает их прочностные параметры, не понижая пластичности. Этот эффект сохраняется до порогового содержания в 0,4%.
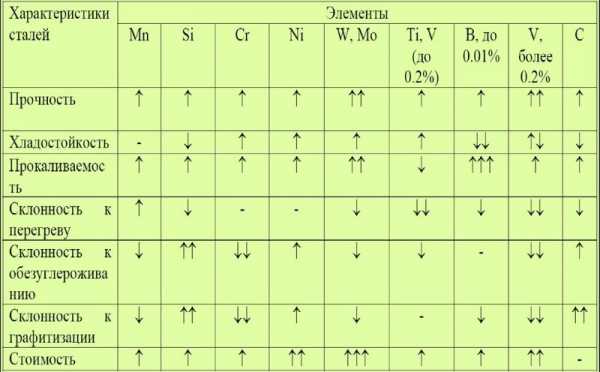
Влияние легирующих добавок на свойства стали
В сочетании с Mn или Mo кремний способствует росту закаливаемости, а вместе с Сг и Ni повышает коррозионную устойчивость сплавов.
Азот и кислород в сплаве
Эти самые распространенные в земной атмосфере газы вредно влияют на прочностные свойства. Образуемые ими соединения в виде включений в кристаллическую структуру существенно снижают прочностные параметры и пластичность.
Легирующие добавки в составе сплавов
Это вещества, намеренно добавляемые в расплав для улучшения свойств сплава и доведения его параметров до требуемых. Одни из них добавляются в больших количествах (более процента), другие — в очень малых. Наиболее часто применяю следующие легирующие добавки:
- Хром. Применяется для повышения прокаливаемости и твердости. Доля – 0,8-0,2%.
- Бор. Улучшает хладноломкость и радиационную стойкость. Доля – 0,003%.
- Титан. Добавляется для улучшения структуры Cr-Mn сплавов. Доля – 0,1%.
- Молибден. Повышает прочностные характеристики и коррозионную стойкость, снижает хрупкость. Доля – 0,15-0,45%.
- Ванадий. Улучшает прочностные параметры и упругость. Доля – 0,1-0,3%.
- Никель. Способствует росту прочностных характеристик и прокаливаемости, однако при этом ведет к увеличению хрупкости. Этот эффект компенсируют одновременным добавлением молибдена.
Металлурги используют и более сложные комбинации легирующих добавок, добиваясь получения уникальных сочетаний физико-механических свойств стали. Стоимость таких марок в несколько раз (а то и десятков раз) превышает стоимость обычных низкоуглеродистых сталей. Применяются они для особо ответственных конструкций и узлов.
Если вы нашли ошибку, пожалуйста, выделите фрагмент текста и нажмите Ctrl+Enter.
stankiexpert.ru
Свойства стали
Благодаря своим физическим, механическим и химическим свойствам сталь по праву является самым важным инженерным м конструкционным материалом.
Сталь – основной конструкционный материал
Наиболее важными свойствами стали являются ее хорошая формуемость – способность к обработке давлением – и прочность, высокие пределы прочности и текучести, а также хорошая теплопроводность. К этим выдающимся свойствам нержавеющие стали добавляют высокое сопротивление коррозии.
При выборе материала для конкретного изделия инженеры должны быть уверены, что он способен выдерживать эксплуатационные нагрузки на это изделие – механические и климатические. Понимание и контроль свойств материала является, поэтому, очень важным. Механические свойства стали могут легко контролироваться путем выбора соответствующего химического состава, технологии изготовления и термической обработки, которые обеспечивают окончательную микроструктуру стали.
Различное легирование и виды термической обработки, которые применяются при производстве стали, обеспечивают ей различные уровни прочности и других свойств. Это дает возможность добиваться удовлетворения требований соответствующих стандартов.
Механические свойства стали
Для описания и контроля свойств стали применяют различные системы их измерения. Например, предел прочности, предел текучести и пластичность определяют путем испытания образцов стали на растяжение. Вязкие свойства стали измеряют при ударных испытаниях специальных образцов стали. Твердость стали определяют через измерение сопротивления проникновения через ее поверхность твердого объекта, например, с алмазным наконечником.
Испытания на растяжение – это метод оценки конструкционных способности стали сопротивляться прилагаемым нагрузкам. Результат этих испытаний выражается в получении соотношения между напряжением и деформацией в образце в ходе испытания.
Физические свойства стали
Отношение между напряжением и деформацией в упругой области растяжения является мерой упругости материала. Это отношение называют модулем упругости или модулем Юнга. Высокое значение модуля Юнга является одним из самых важных свойств сталей. Обычно его значение составляет 190-210 ГПа или (19-21)×106 кГ/см2, что примерно в три раза больше, чем у алюминия.
К основным физическим свойствам стали относятся такие свойства материалов, как плотность, теплопроводность, модуль упругости, коэффициент Пуассона.
Типичными физическими свойствами сталей являются следующие:— плотность: ρ = 7,7-8,1 кг/дм3;— модуль упругости: Е = 190-210 ГПа;— коэффициент Пуассона: ν = 0,27-0,30;— теплопроводность: k = 11,2-48,3 Вт/мК;— тепловое расширение: α = 9-27×10-6 1/К.
steel-guide.ru