Способ контроля паяемости металлизированных отверстий печатных плат. Проверка на паяемость печатных плат
Паяемость выводов электронных компонентов
Технологии в электронной промышленности №4'2010
Заказать этот номерПроблема улучшения качества паяных соединений и повышения надежности изделий электроники вызывает необходимость применения эффективных методов контроля паяемости выводов электронных компонентов и финишных покрытий печатных плат. Методы должны обеспечивать автоматизацию контроля, высокую достоверность и возможность применения в промышленности для широкого круга электронных компонентов.
Выбор метода оценки паяемости
Проблемы формирования качественных паяных соединений в технологии электронных модулей имеют особую актуальность по целому ряду причин. Операции сборки и монтажа являются до сих пор самыми трудоемкими и занимают до 50-70% общей трудоемкости изготовления изделий. Микроминиатюризация электронных компонентов, применение поверхностного и комбинированного монтажа, создание функционально сложных микроэлектронных устройств, в частности, сверхбольших интегральных микросхем и быстродействующих микропроцессоров — все это вызывает особые трудности при формировании соединений.
Высокую функциональную сложность и степень интеграции невозможно реализовать без принципиального совершенствования системы контактных соединений. Освоение электронных сборок V поколения — многокристальных модулей (тонкопленочных многослойных гибридных конструкций, выполненных на керамических, кремниевых или металлических подложках, к которым бескорпусные кристаллы присоединяются методами пайки) — повысило количество выводов в 100 раз по сравнению с технологией монтажа в отверстия [1]. Традиционные процессы монтажа не обеспечивают высокого процента выхода годных изделий с плотным монтажом. Статистические данные показывают, что 50-80% всех отказов в ИЭ происходит вследствие дефектов соединений, причем стоимость обнаружения и исправления отказа на этапе сборки блока обходится в 100 раз дешевле, чем при испытаниях аппаратуры [2]. Качество паяных соединений во многом зависит от свойств покрытий деталей и выводов электронных компонентов.
Переход на бессвинцовые припои при монтаже электронных модулей ставит ряд задач по обеспечению хорошей смачиваемости поверхностей, оптимизации температурных профилей нагрева, контролю качества соединений. Обеспечение этих требований невозможно без разработки высокоэффективных и производительных методов контроля, особое место среди которых занимают методы контроля паяемости.
Паяемость — это способность материала смачиваться расплавленным припоем и образовывать с ним качественное паяное соединение. Паяемость определяется физико-химической природой материалов и припоя, способом и режимами пайки, флюсующими средами, условиями подготовки паяемых поверхностей и т. д. Для образования паяного соединения необходимо и достаточно смачивания поверхности металла расплавом припоя, что определяет возможность дальнейшего образования между ними химических связей. Паяное соединение должно иметь низкое переходное электрическое сопротивление, герметичность и требуемую прочность при различных условиях работы.
Паяемость выводов компонентов трудно оценить визуально, к тому же опыт показывает, что покрытия теряют паяемость при хранении. Постепенная диффузия меди в оловянное покрытие или припой приводит к образованию интерметаллических соединений, которые, увеличиваясь на паяемых поверхностях, вызывают отсутствие смачивания. Поэтому необходимо проверять паяемость таких поверхностей после хранения с целью обеспечения высокой надежности и выхода годных изделий на операциях пайки.
Для оценки паяемости предложены различные методы испытаний, которые можно подразделить на следующие виды: растекание припоя, погружение в припой, время смачивания, высота мениска и сила смачивания. Критическая оценка различных методов испытаний позволяет правильно выбрать материалы при пайке для получения высокой надежности соединений и обеспечить минимальный брак на операциях пайки (табл. 1).
Таблица 1. Методы испытаний на паяемость для электронных компонентов
Оцениваемый параметр | Площадь растекания припоя | Высота капли припоя | Время смачивания | Высота мениска | Сила смачивания |
Информативность | ■ | ■ | ■ | ■ | ■ |
Достоверность | □ | ■ | □ | □ | ■ |
Оперативность | □ | □ | □ | □ | ■ |
Точность | □ | □ | □ | □ | ■ |
Применимость для различных типов компонентов | □ | □ | ■ | ■ | ■ |
Примечание. ■ — полное соответствие результатов; □ — неполное соответствие результатов
В методе на растекание припоя на тестовые образцы наносят определенный объем припоя и флюса, затем образцы нагревают до заданной температуры. Величина площади растекания припоя зависит от типа флюса, основного металла и состава припоя. После растекания припоя образец охлаждается. Площадь может быть измерена либо планиметром, либо увеличена на экране микроскопа для облегчения измерений и повышения их достоверности. Коэффициент растекания припоя по поверхности образца определяют как [3]:
Kp = Sp/Sc, (1)
где Sp, Sc — площади растекшегося припоя и дозированной заготовки припоя.
Если известна площадь растекания и объем припоя, то значение теоретического контактного угла капли припоя на поверхности определяют, используя выражение:
θ = 7,12 V/√Sp3, (2)
где θ — угол в градусах; V — объем припоя.
Выражение предполагает, что объем припоя небольшой, гравитационное воздействие отсутствует и позволяет дать количественную оценку паяемости. Отличной паяемости соответствуют значения θ < 10°, Kp > 1, хорошей — 10° < θ < 25°, удовлетворительной — θ < 90°.
Величина контактного угла и площадь растекания зависят от массы заготовки припоя (рис. 1) [4]. Растекание припоя по поверхности образца часто носит неправильный характер вследствие неоднородности химических и физических свойств испытываемых поверхностей, а также различной степени их очистки. При испытаниях гальванических оловянных покрытий с толстыми оксидными пленками показано, что припой растекался под ними, что затрудняло контроль площади. Поэтому метод оценки площади растекания может дать значительную погрешность.
Рис. 1. Зависимость контактного угла от диаметра площади растекания и массы припоя
Разновидностью метода растекания является определение коэффициента растекания по максимальной высоте расплавленного припоя на поверхности:
Kp = (D -Hp)/D, (3)
где D — диаметр сферы, имеющий объем, эквивалентный используемому припою; Нр — высота капли припоя после растекания (рис. 2).
Рис. 2. Схема определения коэффициента растекания припоя: 1 — основной металл; 2 — припой; 3 — дозированная заготовка
Однако этот метод больше подходит там, где площадь растекания припоя приблизительно круглая. Учитывая, что в реальных условиях пайки высота «лежащей» капли расплавленного припоя Нпр всегда меньше диаметра гипотетической сферы припоя D и высоты дозы припоя Нр, то для более точного расчета коэффициента растекания припоя предложено выражение [5]:
Kp = (Нпр-Нр)/Нпр, (4)
где Нпр — высота «лежащей» капли расплавленного припоя, определяемая как:
Здесь σ — поверхностное натяжение припоя, g — ускорение силы тяжести, ρ — плотность припоя.
Методы погружения являются наиболее ранними испытаниями на паяемость, поскольку выводы компонента просто погружаются сначала во флюс, а затем в расплавленный припой, и по степени покрытия их припоем оценивается паяемость. Выводы компонента с помощью установки (рис. 3) выдерживают в ванне 1-2 с, затем удаляют из ванны, охлаждают и очищают изопропиловым спиртом.
Рис. 3. Схема установки для погружения выводов компонентов в припой: 1 — ванна с припоем; 2 — компонент; 3 — возвратная пружина; 4 — двигатель; 5 — кулачок для задержки образца в припое; 6 — микровыключатель
Рис. 4. Внешний вид выводов транзисторов после погружения в припой
Испытания на время смачивания позволяют воспроизводить довольно точно условия операции массовой пайки и могут быть использованы для определения качества пайки выводов элементов. Для проверки на паяемость материалов выводов электронных компонентов предложен метод шарика припоя (glob test). Определенный объем припоя (зависящий от размера испытываемого провода) расплавляется на нагретом блоке, а офлюсованный вывод горизонтально опускается в шарик припоя, расщепляя его надвое (рис. 5а). Время, в течение которого припой обтечет провод и в конечном итоге закроет верх провода, является временем смачивания. Для обнаружения тенденции к несмачиванию необходимо удалить провод из шарика припоя, стереть излишек припоя и повторить испытания. Для имитации длительного хранения выполняют искусственное старение в течение 16 часов при 155 °С на воздухе.
Рис. 5. Схема (а) и прибор (б) контроля времени смачивания выводов компонентов
На нагретый столик 1 укладывают дозу припоя, которая, расплавляясь, образует каплю 2. К капле подводят вывод 3, который делит ее на две части. По мере нагрева вывода припой начинает его смачивать и обтекать. В момент полного смыкания над выводом припой касается зонда 4, и отсчет времени прекращается (рис. 5а). Такие приборы выпускаются фирмой Multicore (Великобритания) и Wazau (Германия) (рис. 5б).
Для определения паяемости выводов компонентов применяют более простой — мениско-метрический метод, заключающийся в измерении высоты мениска припоя, поднявшегося по выводу над зеркалом ванны под действием сил поверхностного натяжения. Высоту мениска над зеркалом припоя измеряют с помощью специальной оптической головки или бинокулярного микроскопа. Высота мениска обратно пропорциональна контактному углу смачивания. Чем больше высота мениска, тем лучше смачивание. Это следует из формулы [6]:
где Рф — плотность флюса; H — высота мениска припоя на выводе, Fжф — сила, действующая на границе «жидкий припой - флюс»; θ — угол смачивания.
Для измерения высоты мениска применяют установку, состоящую из миниатюрной ванны с припоем, сменных держателей для закрепления компонентов, микроскопа для замера высоты мениска, щупа для настройки микроскопа на уровень припоя и пульта управления. Ванну с припоем ПОС 61 разогревают до температуры 240.250 °C, время выдержки вывода в припое — 2-3 с в зависимости от диаметра вывода. Микроскоп устанавливают так, чтобы нулевая линия шкалы микроскопа располагалась между концом щупа и его изображением в зеркале припоя. После этого щуп удаляют и закрепляют в держателе компонент, выводы которого перед испытанием рихтуют, обезжиривают растворителем и сушат.
По достижении рабочей температуры в ванне включают электродвигатель перемещения держателя и, наблюдая в микроскоп за мениском припоя на выводе, определяют по шкале микроскопа его высоту, по которой судят о паяемости (табл. 2).
Таблица 2. Оценка паяемости по высоте мениска припоя
Высота мениска припоя, мм | Оценка паяемости |
0,95-0,65 | Хорошая |
0,55-0,40 | Удовлетворительная |
Менее 0,40 | Неудовлетворительная |
Менискометры фирмы Metronelec (Швейцария) имеют диапазон измерения высоты подъема мениска 0-1,5 мм с погрешностью ±0,05 мм. Производительность контроля — до 30 шт./ч. Оценка паяемости выводов по высоте мениска трудоемка и имеет значительную погрешность.
Смачивание поверхности расплавленным припоем сопровождается постепенным уменьшением контактного угла по мере изменения в силе поверхностного натяжения вследствие взаимодействия припоя и основного металла. Следовательно, измеряя поверхностное натяжение припоя, можно оценить паяемость. Метод баланса смачивания (Wetting Balance Test) состоит в прямом измерении сил смачивания и работы адгезии. Исследуемый образец 1, закрепленный на датчике 2, погружается в ванну с припоем 7, которая с помощью привода 6, управляемого системой 5, движется вверх (рис. 6а). Датчик тензометрического типа преобразует усилие в электрический сигнал, который через тензометрический усилитель 3 подается на самописец 4.
Рис. 6. Схема (а) и прибор (б) менискографического контроля
Пока образец не нагрет, смачивание отсутствует, мениск припоя вогнут вниз, на образец действует только выталкивающая сила припоя F:
Fa = S*h*g, (7)
где S — площадь образца, h — глубина погружения.
При полном смачивании в точке В значение силы смачивания равно F1, при отрыве образца в точке С сила смачивания достигает F2 (рис. 7). Скорость погружения образцов выбирается в пределах 0,2-0,4 мм/с, время погружения 4-5 с, глубина — 0,8-2,0 мм. Мерой паяемо-сти служат сила F1 и время t1, за которое она достигает этого значения. Косинус краевого угла смачивания находят по формуле:
cosθ = (Fl+Fa)/F2· (8)
Рис. 7. Кривая менискографического контроля силы смачивания
Процесс смачивания носит релаксационный характер, и изменение силы смачивания описывается уравнением [7]:
где f0 — натяжение смачивания, равное максимальному значению силы смачивания на единицу длины периметра нижнего торца образца; τ — время релаксации смачивания; t — время, отсчитываемое от момента контакта образца с расплавом.
Время релаксации τ определяют как время достижения силы смачивания, равной [(e-1)/e]f0,. Величина натяжения смачивания:
f0 = σcosθ· (10)
Этот метод введен в европейские и международные стандарты (MIL, DIN, JIN, IPC) и применяется для оценки паяемости разнообразных покрытий, образцов печатных плат, выводных и чиповых компонентов, эффективности активированных флюсов и бессвинцовых припоев.
Менискографы выпускаются фирмами Metronelec (Швейцария) и General Electric (Англия). Менискограф MeniscoST60 Wetting Balance (рис. 6б) обеспечивает глубину погружения образцов в расплав припоя от 0,1 до 1,0 мм с шагом 0,1 мм со скоростью от 1 до 50 мм/с. Время выдержки и наблюдения составляет от 1 до 30 с. Хорошей смачиваемости соответствуют значения поверхностного натяжения припоя от 350 до 450 мН/м, а менее 200 мН/м указывает на неудовлетворительную паяемость. Тензометрический метод контроля паяемости позволяет изучать процессы длительностью не менее 1·10-3 с с чувствительностью 5·10-5 Н. Точность измерения f составляет ±(2-3)%, τ — ±5%, точность расчета краевого угла смачивания O — ±1°, σ — ±(4-5)%.
Значения натяжения смачивания оловянно-свинцовым припоем для различных типов покрытий приведены в таблице 3 [8].
Таблица 3. Параметры смачивания покрытий оловянно-свинцовым припоем
Покрытие (медный подслой) | Натяжение смачивания, мН/м |
Золото 99,99 | 270 |
Золото - олово (80) | 140 |
Золото - серебро (68) | 200 |
Золото - медь (70) | 400 |
Палладий | 450 |
Родий | 100 |
Олово химическое | 480 |
Олово электрохимическое матовое | 480 |
Олово электрохимическое блестящее | 270 |
Никель химический | 260 |
Никель гальванический | 280 |
Никель гальванический блестящий | 240 |
Никель - фосфор (90) | 200 |
Никель - бор | 150 |
Олово - никель (70) | 60 |
Олово - свинец (60) | 480 |
Параметры смачивания безвыводных электронных компонентов поверхностного монтажа, а именно их контактных площадок, оцененные менискографическим методом, зависят от типа барьерного слоя и качества слоя лужения. Время смачивания находится в пределах 0,5-2,0 с, а натяжение смачивания — в пределах 400-440 мН/м [9].
Методика испытаний выводов на паяемость с помощью менискографа также имеет некоторые недостатки. Время смачивания связано со скоростью погружения образца в припой и зависит от ряда факторов: массы образца, теплопроводности материала, активности флюса, состояния поверхности торца образца и других. В результате данные по силе смачивания и времени смачивания могут не коррелировать или даже противоречить друг другу.
Предложена методика и прибор оценки паяе-мости по обобщенному параметру, в качестве которого взята площадь петли гистерезиса смачивания (рис. 8), имеющая размерность работы. Эта работа, отнесенная к единице облуженной поверхности образца, получила название «работа облуживания» Wo6rl. Для получения петли гистерезиса после достижения заданной глубины погружения движение образца реверсируют и при этом регистрируют когезионную силу [10]. Параметры смачивания различных поверхностей в присутствии флюса ФКСп приведены в таблице 4. Снижение натяжения смачивания и увеличение работы облуживания свидетельствует об ухудшении паяемости поверхности.
Рис. 8. Диаграмма изменения силы смачивания во время испытаний
Таблица 4. Параметры смачивания оловянно-свинцовым припоем ПОС 61
Параметр | Латунь Л63 | Медь | Золото | Серебро |
Натяжение смачивания, мН/м | 238 | 221 | 260 | 165 |
Время смачивания, с | 1,0 | 1,6 | 1,0 | 2,5 |
Работа облуживания, Дж/м2 | 0,12 | 0,27 | 0,135 | 0,25 |
Лучше всего смачиваются припоем оловянные химические и матовые покрытия. Гальванические блестящие покрытия отличаются высокой чистотой поверхности, что значительно увеличивает время релаксации смачивания. Наличие до 3% фосфора в никелевом химическом покрытии, а также его пористость обуславливают некоторое замедление смачивания и увеличение краевого угла до 58° [11].
Хорошей паяемостью обладают золотое и серебряное покрытия, а также покрытия Pd, Sn-Pb и Au-Cu. По никелевым сплавам спир-токанифольные флюсы имеют низкую активность, а также образуют трудно удаляемые остатки на паяемых поверхностях. Для увеличения активности по медным и никелевым поверхностям необходимо использовать активированные флюсы на основе этиленгликоля, содержащие поверхностно-активные вещества и активаторы в виде щавелевой кислоты и гидрохлоридов, производных бензиламина. Такие флюсы обладают в 1,6-2 раза большей активностью, чем флюс ФКСп, а его остатки легко удаляются с поверхности деталей промывкой в теплой проточной воде.
Существенным отличием свинцовых и бессвинцовых сплавов является их время смачиваемости (табл. 5) [12]. Время смачиваемости сплава Sn-Pb-Ag при температуре 245 °C составляет 8 мс. При увеличении температуры на 15 °C время смачиваемости уменьшится всего до 7 мс. Время смачиваемости SAC при температуре 245 °C составляет 460 мс, а при температуре 260 °C оно резко уменьшается до 10 мс. Более длительное время смачиваемости требует более длительного и интенсивного нагрева, что увеличивает энергозатраты. Необходимо использовать более мощные печи с двумя зонами пикового нагрева.
Таблица 5. Параметры смачиваемости оловянных сплавов
Тип сплава | Со свинцом | Без свинца | Без свинца | |||
Sn-Pb-Ag | Sn-Ag-Cu | Sn-Ag | ||||
Температура плавления, °С | 179 | 217 | 221 | |||
Температура в печи, °С | 245 | 260 | 245 | 260 | 245 | 260 |
Натяжение смачивания, мН/м | 311 | 304 | 315 | 319 | 307 | 345 |
Время смачивания, мс | 8 | 7 | 460* | 10 | 720* | 124* |
Примечание. * Большие энергозатраты на нагрев из-за длительной смачиваемости.
Исследования параметров смачивания наиболее распространенными бессвинцовыми припоями — Sn-3,4Ag-4,8Bi, Sn-4,0Ag-0,5Cu, Sn-3,5-Ag и Sn-0,7Cu — поверхностей печатных плат показало, что на свежеприготовленных образцах сила смачивания составляет 4,7-5,2 мН, а время смачивания — 2-3 с. После двух циклов нагрева в связи с ростом оксидной пленки SnO2 сила смачивания снижается до 2 мН, а время смачивания растет до 8-10 с [12]. Сравнение параметров смачивания оловянными припоями различных финишных покрытий печатных плат (лужение, NiAu, серебрение и органическое паяемое покрытие (OSP)) приведено в таблице 6.
Таблица 6. Сравнение параметров смачивания оловянными припоями покрытий печатных плат
Припой | Максимальная сила смачивания | Время смачивания |
Sn37Pb | Sn > Ag = OSP > NiAu* | Sn = Ag = OSP = NiAu |
Sn3,4Ag4,8Bi | Sn > Ag>NiAu > OSP | Sn = Ag = NiAu > OSP |
Sn3,8Ag0,7Cu | Ag > NiAu > Sn > OSP | Sn > NiAu > Ag > OSP |
Sn3,5Ag | Ag > NiAu > Sn > OSP | Ag = NiAu = Sn > OSP |
Sn0,7Cu | Sn > NiAu > Ag > OSP | NiAu > Sn = Ag > OSP |
Примечание. * Лучше > хуже.
В бессвинцовом процессе флюс должен обеспечить смачиваемость наиболее трудно смачиваемых припоев и металлических поверхностей контактных площадок и компонентов при более высокой температуре, поэтому его активность должна быть выше. Более активный флюс уменьшает число оксидов и улучшает смачиваемость.
Выводы
Для обеспечения высокого качества паяных соединений в электронике необходимы совершенные и оперативные методы контроля паяемости выводов и контактных площадок электронных компонентов. Современный метод баланса сил смачивания припоями позволяет объективно и достаточно точно оценить паяемость выводов различных типов электронных компонентов, финишных покрытий контактных площадок для различных припоев и флюсов при заданной температуре формирования соединений. Этот метод может успешно применяться в промышленности, что позволяет значительно сократить брак после пайки.
Литература
- Ли Н.-Ч. Технология пайки оплавлением, поиск и устранение дефектов: поверхностный монтаж, BGA, CSP и flip-chip технологии. М.: ИД «Технологии», 2006.
- Manko H. H. Solders and Soldering: materials, design, production and analysis for reliable bonding. N. Y., 2000.
- ГОСТ 23904-79. Пайка. Метод определения смачивания материалов припоем.
- Wassink K. R. J. Soldering in Electronics. Ayr, Scotland, Electrochem. Publ., 2002.
- Ланин В. Л., Хмыль А. А. Контроль паяемости выводов элементов радиоэлектронной аппаратуры // Неразрушающий контроль и системы управления качеством сварных и паяных соединений. Материалы семинара. М.: ЦРДЗ, 1992.
- Городецкая М. С., Казаков Н. И. Метод оценки паяемости выводов электрорадиоэлементов и микросхем // Обмен опытом в радиопромышленности. 1982. Вып. 11.
- Бородина Е. К., Крашенников М. Г. Контроль паяемости металлических покрытий // Заводская лаборатория. 1989. Т. 53. № 11.
- Груев И. Д., Матвеев Н. И., Сергеева Н. Г. Электрохимические покрытия изделий радиоэлектронной аппаратуры. М.: Радио и связь, 1988.
- Becker G. Solderability Testing of Surface-Mount Devices // Electronic Packaging and Production. 1987. V. 27. No 10.
- Подлесных В. Г., Ткачев М. А., Радковский С. Г. Контроль паяемости по обобщающему параметру // Электронная техника. Сер. 7. 1981. Вып. 3.
- Емельянов В. А., Ланин В. Л., Кушнер Л. К., Хмыль А. А. Оценка паяе-мости гальванических покрытий токопроводящих элементов электронной аппаратуры // Электронная техника. Сер. 7. 1990. Вып. 3.
- Левданский А. Изменение технологического процесса при переходе на бессвинцовую пайку // Технологии в электронной промышленности. 2006. № 1.
- Sattiraju S. V., Dang B., Johnson R. W., Li Y., Smith J. S., Bozack M. J. Wetting Characteristics of Pb-Free Solder Alloys and PWB Finishes // IEEE Trans. on Electronics Packaging Manufacturing. 2002. Vol. 25. No 3.
tech-e.ru
Паяемость печатных плат и компонентов — критерий надежности функционирования электрических схем
Технологии в электронной промышленности №8'2008
Заказать этот номерКачество функционирования и степень надежности современных электронных сборочных узлов порой оставляет желать лучшего. Какие меры возможно и необходимо принять на этапе выбора типа паяемых печатных плат, компонентов и применяемых для пайки материалов, с целью повышения качества производимой электронной продукции? Определение на данном этапе будущего качества производимой продукции, по сути, является прогнозированием надежности. Следовательно, такие возможности позволяют вносить своевременные коррективы в процесс производства и снижать затраты на переработку, которая необходима при наличии бракованных экземпляров или партий. В статье рассмотрены возможности современного оборудования по определению одного из наиболее важных критериев определения качества функционирования электронной продукции — паяемости — на примере системы MUST 3 компании GEN 3 Systems (Великобритания).
Почему необходимо определение паяемости?
Паяемость печатных плат и компонентов является одним из наиболее значимых критериев при определении качества будущей производимой продукции. Как известно, образование непропаянных областей (мест) влечет за собой отказ в функционировании электронного узла на ранней стадии.
Возможна проверка на наличие непропаянных мест после окончания процесса пайки, «постфактум». Такой метод, безусловно, важен при проверке соответствия качества выпускаемого оборудования. Тем не менее, определение паяемости печатных плат и компонентов позволяет определить качество пайки еще до начала процесса, с точностью, соответствующей международным стандартам IPC J-STD-002B и IPC J-STD-003A.
Так, определение паяемости дает возможность прогнозирования ожидаемого качества пайки, а также своевременного внесения корректировок в отношении материалов, применяемых на контактных поверхностях плат и контактах паяемых компонентов:
- Паяемость печатной платы характеризует способность контактных поверхностей печатной платы, прилегающих областей и монтажных отверстий легко смачиваться припоем и сопротивляться сложным условиям процесса пайки.
- Паяемость компонентов характеризует соответствие существующим требованиям и позволяет выявить отклонения, например невозможность пайки.
- Паяемость может быть определена на этапе производства печатных плат, в процессе их приемки заказчиком или непосредственно перед началом пайки.
Характеристики паяемости
Основные параметры, определяющие паяемость,— это:
- смачивание;
- тепловая характеристика;
- сопротивляемость нагреву в процессе пайки.
Под смачиванием понимают реакцию между припоем и основанием, то есть вступление припоя в молекулярный контакт с основанием (печатной платой).
Тепловая характеристика есть совокупность данных о термической массе и теплопроводимости.
Сопротивляемость нагреву в процессе пайки обусловлена материалами компонента и основания.
Метод измерения паяемости
Первоначально применялся следующий способ: погружение вывода компонента, предназначенного для пайки, в емкость с нагретым до рабочей температуры припоем и визуальная оценка степени смачиваемости. Но данному методу присущи такие недостатки, как неточность измерений, ненадежность, отсутствие количественной характеристики.
Альтернативным методом стало определение паяемости путем вычисления значений силы поверхностного натяжения рабочего материала (припоя). Использование такого метода позволяет получить количественную характеристику паяемости, достичь высокой точности и обеспечить надежность и повторяемость измерений.
Для определения паяемости проводятся следующие измерения:
- тест капли припоя;
- проникаемость припоя сквозь монтажные отверстия;
- измерение мениска при погружении;
- поверхностное натяжение при вращении;
- измерение баланса смачивания;
- измерение баланса смачивания паяемых компонентов.
Наиболее информативным из применяемых измерений является измерение баланса смачивания паяемых компонентов. Этот метод реализован в системе MUST 3.
Принцип измерения паяемости системой MUST 3
Реализованный в системе метод позволяет получить количественное выражение паяемости, в миллиньютонах (путем измерения силы поверхностного натяжения припоя). Также данный метод позволяет тестировать мельчайшие компоненты. Международными стандартами определены данные, которые должны быть получены в результате измерений. Как правило, результат измерений представляется в виде графика зависимости силы от времени (так называемые «кривые смачивания»).
Суть кривых смачивания четко прослеживается на рис. 1–5.
Рис. 1. Момент соприкосновения контакта с поверхностью припоя
Рис. 2. Вогнутый мениск, экстрему
Рис. 3. Фаза плавучести (начало смачивания)
Рис. 4. Фаза смачивания
Рис. 5. Фаза стабилизации значения смачивания (уменьшение силы поверхностного натяжения)
На рис. 6 приведена типовая «кривая смачивания».
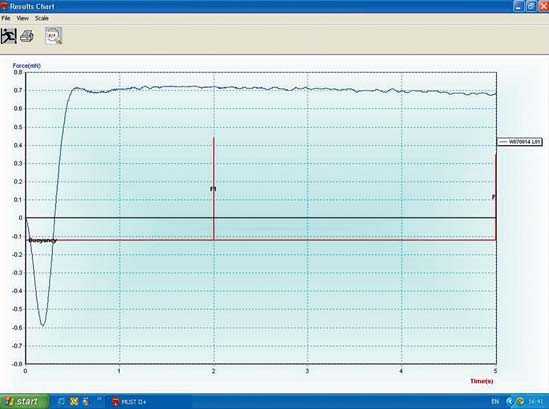
Рис. 6. Пример «кривой смачивания»
Вся полученная количественная информация отображается также в виде таблиц данных (рис. 7). В таблице содержится информация, определенная требованиями стандартов: значения контрольных отрезков времени, силы в соответствующие моменты измерений, несмачиваемость, а также статус (соответствие/ несоответствие).
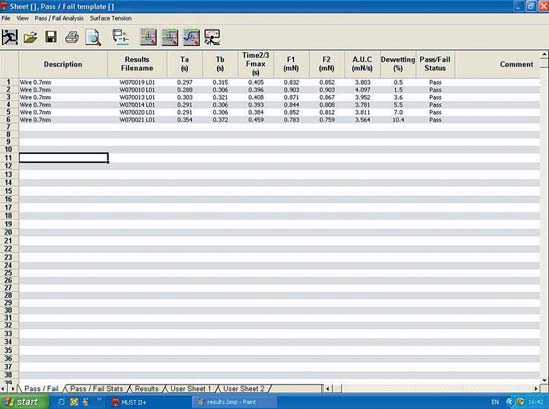
Рис. 7. Количественная информация, отображенная в виде таблицы
Описание системы
MUST = многоосновная универсальная система измерения паяемости. Прототип системы впервые был представлен для пользователей в 1970-х. В настоящее время насчитывается около 2000 пользователей MUST во всем мире. MUST 3 продолжает определять стандарты измерений, которые были разработаны Национальной физической лабораторией (Великобритания) в сотрудничестве с Gen 3 Systems. Система является эталонной в области тестирования паяемости и, что немаловажно, — наиболее гибкой из представленных на рынке.
Основные характеристики системы:
- Высокоточное выравнивание + видеосистема (опция).
- Лучшая система для измерения силы.
- Дружественный интерфейс с Windows XP и возможностью использования SPC.
- Критерий соответствия/несоответствия данных.
- Гибкость: – обычные, выводные компоненты; – компоненты поверхностного монтажа до 0201 включительно; – разъемы плат.
Рабочая зона системы, в которой происходит процесс тестирования, изображена на рис. 8.
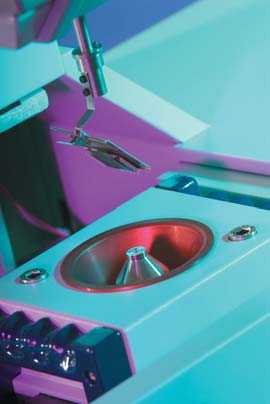
Рис. 8. Рабочая зона системы
Система MUST 3 является первым оборудованием, в котором применяется метод тестирования капли припоя: 4 мм; 3,2 мм; 2 мм; 1 мм.
Преимущества данного метода:
- максимальная точность для меньших компонентов;
- полезен для компонентов с ограниченной областью смачивания;
- повторяемость тестов многовыводных компонентов;
- соответствует промышленным стандартам IEC/IPC/JIS.
Точностные характеристики системы MUST 3
Глубина погружения — 0–30 мм (с точностью до 0,01 мм), скорость погружения — 0–30 мм/с (с точностью до 0,05 мм/с). Кроме того, система является эталонной, поскольку стандарты определения паяемости были разработаны и утверждены на этапе ее проектирования, при сотрудничестве Gen 3 Systems и Национальной Физической лаборатории (Великобритания).
В системе MUST 3 применяется рассмотренный метод тестирования капли припоя. Все, что необходимо для проведения измерений,— комплект ванн, шариков припоя (свинцово-оловянного и бессвинцового), флюс, ПО для ПК на базе Windows, а также комплект рабочих принадлежностей. Все это включено в комплект системы (рис. 9, 10).
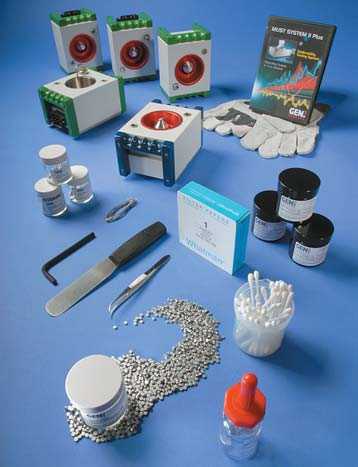
Рис. 9. Комплект системы для проведения измерений
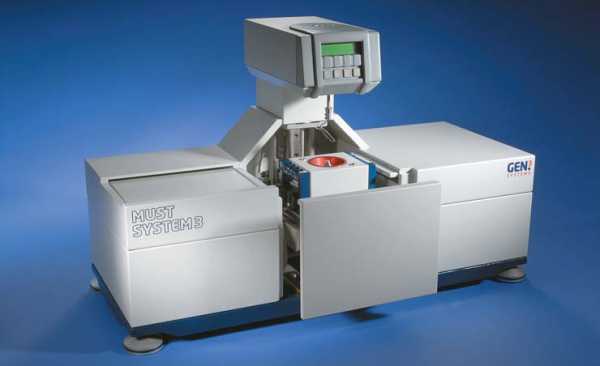
Рис. 10. Система измерения паяемости MUST 3
Заключение
По результатам статистического анализа причин отказов в работе электронных сборочных узлов можно судить, насколько велико значение мероприятий, направленных на повышение надежности их функционирования и вероятности безотказной работы.
Определение надежности электрических схем представляет собой совокупность тестов, установленных международными стандартами. Для эффективного определения качества электрических схем необходимо сложное, высокопрецизионное оборудование.
Представляется наиболее перспективным применение оборудования, разработанного на основании существующих стандартов.
Тестовое оборудование компании GEN 3 Systems на этапе разработки сыграло определяющую роль в установлении стандартов определения качества электрических схем и, таким образом, представляет собой эталон средств измерений.
Скачать статью в формате pdftech-e.ru
ПАЙКА И КОНТРОЛЬ ПЕЧАТНЫХ ПЛАТ — КиберПедия
3. Пайка на печатных платах. Общие сведения. Пайка волной припоя. Пайка в парогазовой среде. Пайка инфракрасным нагревом. Конвекционная пайка. Другие методы пайки. Припойная паста. Технология нанесения припойной пасты. Технологии изготовления трафаретов. Процесс трафаретной печати. Очистка плат после пайки.
4. Контроль в сборочном производстве печатных плат. Автоматическая оптическая инспекция. Рентгеновские контрольные технологические установки. Электрический контроль. Тестирование многослойных ПП. Платы для ВЧ-схем. Методы тестирования сборок. Внутрисхемное тестирование. Функциональное тестирование. Ремонт печатных плат.
Производство печатных плат на заключительной стадии сборочно-монтажных операций включает в себя следующие основные этапы: оплавление припоя с помощью печей или в машинах; отмывка плат; выходной контроль; ремонт дефектных плат, если он возможен; влагозащита плат; упаковка.
Пайка на печатных платах
Общие сведения. Пайка представляет собой распространенный способ монтажа компонентов в производстве радиоэлектронных узлов. При этом обеспечивается и механическое крепление выводов компонентов, и электрическое контактирование в соответствии с электрической принципиальной схемой. При пайке две металлические детали (или детали с металлическим покрытием) соединяются при помощи припоя - третьего металла или сплава. Соединяемые детали не расплавляются сами, расплавляется только припой. Поэтому пайка имеет более щадящий тепловой режим для деталей, чем сварка. Для получения качественного паяного соединения, обладающего хорошими электропроводящими и прочностными свойствами, необходимо обеспечить несколько условий:
1. Получить чистые металлические поверхности у соединяемых деталей (удалить загрязнения и пленки окислов) с помощью технологического флюса;
2. Нагреть припой выше точки плавления;
3. Обеспечить вытеснение флюса с помощью наступающего припоя;
4. Обеспечить растекание жидкого припоя по металлической поверхности;
5. Обеспечить диффузию атомов из твердой металлической фазы в жидкий припой и наоборот – образование сплавных зон.
Среди припоев в радиоэлектронике наиболее широкое распространение получили припои на основе композиции олова и свинца (ПОС). Сплав имеет особую точку, называемую точкой эвтектики. В этой точке температура кристаллизации припоя составляет 183 °С, что значительно ниже точек плавления Sn и Pb (232 °С и 327 °С).
Флюс является материалом, под воздействием которого происходит быстрое и совершенное смачивание металлической поверхности соединяемых деталей расплавленным припоем благодаря влиянию сил поверхностного натяжения. Кроме того, флюс обладает свойством растворения и удаления окисных слоев на контактируемых металлах и защиты очищенной поверхности от нового окисления. Остатки флюса должны легко удаляться, быть не изменять электрические параметры исходного материала и не вызывать коррозии. Распространены флюсы на основе органических кислот из смол хвойных пород деревьев (канифоль). Известно и большое количество синтетических материалов.
ПОС обладает практически оптимальными свойствами для РЭА: хорошей смачиваемостью, прочностью, пластичностью, удобной точкой плавления, коррозионной стойкостью, усталостной прочностью, и, наконец, стоимостью.
Появление на ПП поверхностно монтируемых компонентов существенно изменило технологию пайки. Пайка волной припоя была внедрена в середине прошлого века и до настоящего времени является единственным групповым методом пайки компонентов, устанавливаемых в отверстия ПП. Она выполняется чаще всего погружением обратной стороны платы с выступающими выводами в ванну с припоем. Для пайки плат со смешанным монтажом (компоненты, монтируемые в отверстия с одной стороны платы и простые, монтируемые на поверхность с другой) был разработан метод пайки двойной волной припоя.
Для пайки поверхностно монтируемых компонентов была разработана технология оплавления дозированного припоя. Методами трафаретной печати припой в виде пасты наносится на контактные площадки ПП, затем на него устанавливаются компоненты. В ряде случаев припойную пасту просушивают после нанесения с целью удаления из ее состава летучих ингредиентов или предотвращения смещения компонентов непосредственно перед пайкой. Оплавление припоя и получение паяных соединений происходит в нагревательном устройстве.
Пайка в парогазовой фазе (ПГФ), пайка расплавлением дозированного припоя с помощью инфракрасного нагрева (ИК-пайка), пайка в конвекционных печах, лазерная пайка.
Пайка волной припоя применяется только для пайки компонентов в отверстиях плат (традиционная технология), хотя некоторые изготовители утверждают, что с ее помощью можно производить пайку поверхностно монтируемых компонентов с несложной конструкцией корпусов, устанавливаемых на одной из сторон ПП.
Процесс пайки прост. Платы, установленные на транспортере, подвергаются предварительному нагреву, исключающему тепловой удар на этапе пайки. Затем плата проходит над волной припоя. Сама волна, ее форма и динамические характеристики являются наиболее важными параметрами оборудования для пайки. С помощью сопла можно менять форму волны. В настоящее время каждый производитель использует свою собственную форму волны (в виде греческой буквы «омега», Z-образную, Т-образную и др.). Могут варьироваться направление и скорость движения потока припоя, достигающего платы, но они должны быть одинаковы по всей ширине волны. Регулируется также угол наклона транспортера для плат. Некоторые установки для пайки оборудуются дешунтирующим воздушным ножом, который обеспечивает уменьшение количества перемычек припоя. Нож располагается сразу же за участком прохождения волны припоя и включается в работу, когда припой находится еще в расплавленном состоянии на ПП. Узкий поток нагретого воздуха, движущийся с высокой скоростью, уносит с собой излишки припоя, тем самым, разрушая перемычки и способствуя удалению излишков припоя.
Когда появились ПП, с обратной стороны которых устанавливались поверхностные компоненты, их пайка производилась волной припоя. При этом возникло множество проблем, а именно: непропаи и отсутствие галтелей припоя из-за эффекта затенения другими компонентами, преграждающими доступ волны припоя к соответствующим контактным площадкам, а также наличие полостей с захваченными газообразными продуктами разложения флюса, мешающих доступу припоя. Потребовалось изменить технологический процесс пайки волной, внедрив вторую волну припоя. Первая волна делается турбулентной и узкой, исходит из сопла под большим давлением. Турбулентность и высокое давление потока припоя исключает формирование полостей с газообразными продуктами разложения флюса. Однако турбулентная волна все же образует перемычки припоя, которые разрушаются второй, более пологой волной с малой скоростью истечения. Вторая волна устраняет перемычки припоя, а также завершает формирование галтелей. Для обеспечения эффективности пайки параметры каждой волны должны быть регулируемыми, волны должны иметь отдельные насосы, сопла и блоки управления.
Пайка двойной волной припоя применяется в настоящее время для одного типа ПП: с традиционными компонентами на лицевой стороне и простыми компонентами (чипами и транзисторами) на обратной. Некоторые компоненты (даже пассивные) могут быть повреждены при погружении в припой во время пайки. Поэтому важно учитывать их термостойкость и принимать меры предосторожности: применять поверхностно монтируемые ИС, не чувствительные к тепловому воздействию; снизить скорость транспортера; проектировать ПП таким образом, чтобы исключить эффект затенения. Хорошо разнесенные, не загораживающие друг друга компоненты способствуют попаданию припоя на каждый требуемый участок платы, но при этом снижается плотность монтажа. При высокой плотности монтажа с помощью данного метода практически невозможно пропаять поверхностно монтируемые компоненты с четырехсторонней разводкой выводов.
Пайка в парогазовой среде (ПГФ) с расплавлением дозированного припоя применима только к сборкам с поверхностным монтажом. Суть процесса: специальная жидкость нагревается до кипения, затем ее пары конденсируются на ПП, отдавая скрытую теплоту парообразования открытым участкам сборки. При этом припойная паста расплавляется и образуется паяное соединение между выводом компонента и контактной площадкой платы. Когда температура платы достигает температуры жидкости, процесс конденсации прекращается, тем самым заканчивается и нагрев пасты. Повышение температуры платы от ее начальной температуры до температуры расплавления припоя осуществляется очень быстро и не поддается регулированию. Поэтому необходим предварительный подогрев платы с компонентами для уменьшения термических напряжений в компонентах и местах их контактов с платой. Температура расплавления припоя также не регулируется и равна температуре кипения используемой при пайке жидкости. Такой жидкостью является инертный фторуглерод (например, FC-70).
В первых установках для пайки в ПГФ применялись две рабочих жидкости. С целью предотвращения утечки паров дорогого фторуглерода и припоя поверх основной технологической среды из инертного фторуглерода создавалась дополнительная технологическая среда из более дешевого фреона. Основной недостаток этих установок состоял в том, что на границе двух технологических сред происходило образование различных кислот и для защиты ПП требовались системы их нейтрализации. Затем стали выпускаться установки для пайки в ПГФ конвейерного типа, встраиваемые в технологические сборочно-монтажные линии. Такие установки имеют относительно небольшие входное и выходное отверстия, позволяющие реализовать систему с одной технологической средой.
Пайка инфракрасным нагревом (ИК-пайка) аналогична пайке в ПГФ, за исключением того, что нагрев платы с компонентами производится не парами жидкости, а ИК-излучением. Основным механизмом передачи тепла, используемым в установках пайки с ИК-нагревом, является излучение. В отличие от пайки в ПГФ, в процессе пайки с ИК-излучением скорость нагрева регулируется изменением мощности каждого излучателя и скорости движения транспортера с ПП. Поэтому термические напряжения в компонентах и платах могут быть снижены посредством постепенного нагрева сборок.
Инфракрасные печи применяются при изготовлении несложных плат. Обусловлено это тем, что инфракрасный тип нагрева имеет ряд отрицательных эффектов. Наиболее существенно влияют на работу следующие:
- количество энергии излучения, поглощаемой компонентами и платами, зависит от поглощающей способности материалов, из которых они изготовлены. Поэтому нагрев осуществляется неравномерно в пределах монтируемого устройства;
- высокие элементы могут закрывать более низкие, создавая «тень», где высока вероятность непропая;
- некоторые элементы корпусом могут закрывать свои собственные выводы (кристаллоносители без выводов или с J-образными выводами).
В некоторых установках для пайки с ИК-нагревом вместо ламп ИК-излучения применяются панельные излучающие системы. Излучение такой системы не нагревает непосредственно компоненты на сборке, а поглощается технологической средой (воздух или газ), которая в свою очередь передает тепло на ПП за счет конвекции. Этот способ пайки устраняет ряд недостатков, присущих пайке с ИК-нагревом, таких, как неравномерный прогрев отдельных частей сборки и невозможность пайки компонентов в корпусах, непрозрачных для ИК-излучения. Панельные излучатели обеспечивают намного меньшую скорость нагрева, чем традиционные источники ИК-излучения.
Конвекционная пайка лишена недостатков, связанных с теплопередачей излучением. Но управлять горячим воздухом труднее и технически сложнее. Конвекционная пайка реализуется в камерных или конвейерных печах. Камерные печи используются в лабораторных условиях, в единичном или мелкосерийном производстве. Конвейерные печи встраиваются в сборочные линии и используются, как правило, в крупносерийном производстве.
В камерных печах отработка профиля пайки осуществляется путем изменения температуры внутри камеры со временем, в конвейерных – перемещением платы по конвейеру через несколько зон печи (зоны нагрева и охлаждения). Как правило, максимальная температура, при которой происходит непосредственно оплавление пасты, составляет 210÷220 °C. Плата находится в печи при максимальной температуре в течение всего нескольких секунд, после чего производится ее охлаждение.
В ряде случаев применяется пайка в инертной среде, при которой осуществляется впуск азота в рабочую область печи. Эта операция используется для сведения к минимуму окислительного процесса. Однако необходимо оценивать необходимость этой операции. В случае если процесс пайки длится небольшой промежуток времени, припой не успеет окислиться, так как в его состав входит флюс, обеспечивающий растворение окислов на поверхности частиц порошка припоя. Пайка в инертной среде потребует большого расхода азота, что повлечет за собой использование азотной станции с существенными дополнительными расходами. Использование азотной среды при конвекционной пайке оправдано только в условиях серийного производства при изготовлении сложных модулей, требующих высокого качества исполнения.
Другие методы пайки. Метод пайки расплавлением дозированного припоя с помощью нагретого приспособления разработан в Японии применительно к изделиям бытовой электроники с невысокой плотностью монтажа. ПП с компонентами помещается на теплопроводящий транспортер, содержащий набор специальных пластин, температура которых контролируется. Пластины подбираются по габаритам компонента, прижимают выводы к контактным площадкам и передают тепло для оплавления припоя. Метод рекомендован к применению для пайки ТАВ корпусов и flat-pack, имеющих весьма тонкие выводы, подверженные изгибанию. Во время прижима осуществляется разогрев соединения до точки оплавления припоя по запланированному графику, а затем идет процесс охлаждения паяного контакта, и только затем убирается инструмент. Процесс последовательный, достаточно медленный, однако обеспечивает надежную пайку для ответственных и дорогих деталей.
Пайка расплавлением дозированного припоя с помощью лазерного излучения также является последовательным процессом. Для нагрева соединений применяются твердотельные либо газовые лазеры. Главное достоинство лазерной пайки заключается в том, что пучок лазерной энергии хорошо фокусируется. Метод особенно эффективен для пайки термочувствительных компонентов и компонентов с малым шагом выводов. Некоторые из наиболее сложных сборок на платах (например, центральные процессоры вычислительных машин) размером 254x305 мм могут иметь до 10000÷15000 паяных соединений. Главным здесь является качество и надежность паяных соединений, а не производительность установки.
На качество паяных соединений узла влияет множество факторов, в том числе и выбранный конструктором вариант размещения компонентов. Корпуса для больших и сверхбольших интегральных микросхем изготавливаются из материалов, которые должны обеспечивать хороший теплоотвод от корпуса ИМ в процессе эксплуатации. Низкое тепловое сопротивление корпуса, большая масса и теплоемкость крупных корпусов не позволяют получить одинаковую температуру в области выводов при пайке малых и больших корпусов, расположенных на плате в непосредственной близости. Такой эффект необходимо иметь в виду и технологу, и конструктору.
Припойная паста. Для нанесения методом трафаретной печати через металлический трафарет или для нанесения дозатором разрабатываются различные варианты паяльных паст. Характеристики припойных паст в первую очередь определяются их составом.
Припойные пасты представляют собой смесь мелкодисперсного порошка материала припоя со связующей жидкой основой, в которую входит флюс. Содержание порошка припоя составляет приблизительно 88% от веса пасты. Состав паст выражают через соотношение ингредиентов материала припоя. Так, например, 63/37 означает содержание в составе материала припоя 63% олова и 37% свинца.
Характеристики частиц материала припоя в пасте оказывают существенное влияние на качество паяного соединения. Наиболее важным параметром является размер частиц припоя. Если припойная паста наносится на ПП через сеточный трафарет, рекомендуется применять припойную пасту, у которой максимальный размер частиц припоя составляет половину размера ячейки трафарета. Форма частиц материала припоя также оказывает влияние на процесс трафаретной печати. Частицы припоя сферической формы облегчают процесс трафаретной печати и позволяют получать хорошую воспроизводимость технологического процесса от одной партии изделий к другой при формировании рисунка припойной пасты. Наличие в пасте частиц другой формы может способствовать появлению загрязнений, затрудняющих процесс печати, и ускорению процессов окисления материалов припоя. Пульверизация расплавленного припоя, с помощью которой наиболее просто получить порошкообразные припои, образует частицы преимущественно сферической формы.
Флюс в составе припойных паст служит не только для активации металлических поверхностей, удаления с них окислов и предотвращения окисления припоя в процессе пайки, но и обеспечивает требуемую растекаемость и изменение вязкости со временем при нанесении припойной пасты на ПП. Если состав припойной пасты имеет недостаточную вязкость, она будет растекаться, что приведет к потере точности рисунка. Для уменьшения растекания пасты можно увеличить процентное содержание в ней порошка припоя или изменить химический состав флюса путем введения в него специальных вяжущих добавок (загустителей). Но здесь нужно соблюдать меру, ибо в противном случае может произойти закупорка сопла дозатора или ячеек трафарета.
Флюс должен удалять окислы с контактируемых металлических поверхностей при пайке. Для эффективного протекания этого процесса очень важно правильно выбрать необходимый температурно-временной режим пайки (температурный профиль). Если во время разогрева платы температура повышается слишком быстро, то растворитель, входящий в припойную пасту в составе флюса, быстро испаряется, что приводит к потере активности флюса, неравномерному расплавлению припоя, разложению или выгоранию его компонентов. Если же нагревательный цикл завершен преждевременно, то окислы в местах паяных соединений могут быть не полностью удалены.
Для избегания окисления припоя формирование слоя припойной пасты рекомендуется производить в химически инертной атмосфере. Хранение пасты рекомендуется осуществлять в прохладном месте с температурой от +5 до +10 °С. Минимальный срок хранения паяльной пасты с флюсом при такой температуре составляет 6 месяцев с даты производства. Перед применением емкость с пастой необходимо выдержать при комнатной температуре до полной стабилизации в течение 2÷8 часов. Не рекомендуется открывать холодную емкость, это может вызвать конденсацию влаги и ухудшение параметров паяльной пасты. Категорически не допускается подогрев пасты нагревательными приборами.
Как правило, паяльные пасты с флюсом полностью готовы к применению и не требуют дополнительных разбавителей. Паяльная паста, которая не была использована в течение рабочей смены, не должна смешиваться со свежей пастой. Остатки пасты рекомендуется складывать в отдельную тару и использовать в начале следующей смены. Не рекомендуется использовать пасту, которая находилась на трафарете две рабочих смены. Если устройство трафаретной печати не использовалось в течение четырех часов, рекомендуется произвести полную очистку трафарета от остатков паяльной пасты.
Распространенными материалами выводов и внешних контактов электронных компонентов являются золото, серебро, палладий-серебро, медь, луженая медь, и припойная паста должна выбираться таким образом, чтобы исключить выщелачивание этих материалов. Большинство паяльных паст с флюсом обладают хорошими клеящими свойствами, достаточными для удержания компонентов после установки до пайки в течение до 8 часов. Клеящие свойства пасты зависят от температуры и влажности, поэтому рекомендуется произвести испытания для определения максимального времени удержания пастой компонентов в условиях реального производства. Печатные платы могут быть запаяны в течение 24 часов после нанесения паяльной пасты без ухудшения качества пайки, высокая температура и влажность могут сокращать это время.
Рекомендуемые режимы процесса пайки для наиболее популярных сплавов Sn63/Pb37 и Sn62/Pb36/Ag2, входящих в состав паст, таковы:
1) стадия предварительного нагрева от 20 до 140 °С, скорость нагрева 1 °С/сек;
2) стадия предварительной сушки от 140°С до 160°С, скорость нагрева 0,5 °С/сек;
3) стадия пайки от 160 до 215 °С, скорость нагрева 2 °С/сек.
Более длительное время стадии пайки может улучшить качество паяного соединения, уменьшить количество и сделать более инертными остатки флюса после пайки. Более короткое время пайки может также дать хорошие результаты, однако в этом случае возможно увеличение количества остатков флюса после пайки. Рекомендуется обеспечить время выдержки выше температуры плавления (+183 °С) в пределах от 30 до 60 сек. Минимальная пиковая температура в зоне пайки должна быть не менее 210 °С в течение 5 сек. Увеличение скорости повышения температуры на стадии предварительного нагрева может привести к увеличению остатков флюса после пайки и ухудшению внешнего вида паяного соединения. Этот косметический дефект полностью устраняется при отмывке остатков флюса.
Вышеуказанные рекомендации служат для первоначальной установки режимов пайки. Конкретные режимы пайки определяются технологом исходя из конструкции печатной платы и оборудования для пайки.
Технология нанесения припойной пасты. Процесс нанесения паяльной пасты зависит от большого числа составляющих:
- от характеристик оборудования – принтеров, держателей плат и др.;
- от трафаретов – формы и размеров отверстий, качества стенок отверстий, толщины трафарета;
- от параметров процесса нанесения пасты – скорости, угла атаки, давления и жесткости ракеля, скорости отделения трафарета, зазора между трафаретом и платой;
- от припойной пасты – размера частиц, объемного содержания металла, вязкости пасты, подвижности флюса;
- от параметров рабочего помещения – температуры, влажности, пыли.
Припойная паста может наноситься с помощью механических устройств для трафаретной печати (ручной способ), с помощью автоматических принтеров, с помощью дозаторов.
Дозаторы – устройства последовательной обработки, паста наносится по программе в определенном объеме на заданные точки ПП. Автоматический дозатор представляет собой рабочий стол, на который крепится обрабатываемая плата. Над рабочим полем перемещается дозатор, который осуществляет нанесение материалов на плату, для управления используется персональный компьютер. Ключевые параметры дозаторов: скорость дозирования (до 15 тыс. точек в час) и максимальный формат обрабатываемой платы (до 450x450 мм). Как и любой последовательный процесс, такой способ нанесения пасты занимает гораздо больше времени, чем трафаретная печать. Однако для дозатора не требуется разрабатывать и изготавливать трафарет. При малых объемах производства (единичные платы) для нанесения материалов можно применять и ручное дозирование.
Если на производстве изготавливается большое число конструкций плат при малом их количестве, то целесообразно применять метод дозирования, особенно при лабораторном производств, так как стоимость изготовления трафаретов (по одному на каждую сторону каждой разновидности плат) может оказаться больше стоимости изготовления самих плат. В случае промышленного производства, напротив, нанесение материалов методом дозирования нежелательно из-за низкой скорости процесса по сравнению с трафаретной печатью. На крупносерийных производствах стоимость трафаретов не вносит заметного вклада в общие расходы.
Устройства трафаретной печати могут быть как ручными, так и автоматическими.
Ручной принтер представляет собой сравнительно простое устройство: на металлической раме закрепляется трафарет, после чего раму крепят к рабочему столу, на котором находится плата, давление на ракель осуществляется оператором вручную. В автоматических принтерах все операции – совмещение трафарета и печатной платы, осуществление приводного давления на ракель, дозирование припойной пасты на трафарет – выполняются автоматически. Эти устройства могут работать как автономно, так и в составе производственной линии. Основные параметры автоматических принтеров: максимальный формат платы, который может достигать значения 510х510 мм, и скорость перемещения ракеля (до 150 мм/с).
Очистка плат после пайки. Обычная ПП содержит много внутренних полостей (в том числе и под компонентами), имеющих выход на поверхность через узкие вертикальные зазоры между компонентами или их выводами. Эти полости способны удерживать продукты разложения флюса и другие загрязнения, которые могут стать источниками коррозии или причиной проникновения внутрь корпусов компонентов веществ, вызывающие повышенные токи утечки. Усиленные попытки очистить плату, например, с помощью органических растворителей, сами по себе могут вызвать механические повреждения или коррозию.
Как правило, загрязнения бывают либо полярными (ионы), либо неполярными. Свободные ионы, особенно электроотрицательные, обладающие высокой химической активностью, быстро вступают в реакцию с металлом коммутационных дорожек и вызывают коррозию. Неполярные загрязнения ухудшают адгезию припоя, свойства защитного покрытия и электрический контакт для функционального испытания микросборки.
Органические растворители в соответствии с их очистной способностью можно разделить на три группы. Гидрофобные - не смешиваются с водой, используются для растворения органических загрязнений, например канифоли и жиров. Гидрофильные - смешиваются с водой, растворяют полярные и неполярные соединения, причем последние в меньшей степени, чем гидрофобные растворители. Азеотропные - представляют собой в основном смесь вышеуказанных типов растворителей. В их состав обязательно входят такие ингредиенты, как фреон-113 или тетрахлордифторэтан, с добавками спиртов и стабилизирующих ингредиентов.
Очистка изделий с применением растворителей может быть реализована погружением плат в ванну с растворителем, равномерным по полю платы или направленным в виде струй опрыскиванием, либо комбинацией обоих методов. Может применяться ультразвуковое перемешивание при очистке плат в ванне с растворителем. На эффективность очистки может повлиять ряд факторов, в том числе расположение компонентов. Компоненты должны размещаться на поверхности платы таким образом, чтобы их корпуса не загораживали друг друга при движении потока растворителя. Прерывания движения платы и остановки во время пайки волной припоя должны быть сведены к минимуму, чтобы флюс нигде не задерживался в полостях платы. Если используются чувствительные компоненты, рекомендуется обрабатывать микросборки в потоке растворителя. При этом необходимо обеспечить максимальную однородность потока растворителя, а интервал времени между пайкой и очисткой уменьшить до минимума.
cyberpedia.su
Входной контроль – важнейший этап подготовки производства
1 марта
Среди стандартных процессов подготовки сборочно-монтажного производства одно из важнейших мест занимает входной контроль комплектующих — и печатных плат, и компонентов. Цель настоящей статьи — представить обзор основных методов входного контроля, сферу их применения, требования к процедурам, возможные проблемы и методы их решения.
Достаточно ли внимания вы уделяете входному контролю печатных плат? Наиболее полные критерии оценки качества изготовления печатных плат приведены в стандарте IPC-A-600G. Для визуальной оценки отдельных параметров возможно также использование стандарта IPC-A-610D RU.Наиболее распространенные дефекты печатных плат, которые могут быть обнаружены на этапе входного контроля, приведены в таблице 1. Дальнейшие действия, предпринимаемые при обнаружении того или иного дефекта, должны опираться на производственные стандарты предприятия.
Таблица 1. Виды дефектов печатных плат, которые могут быть обнаружены на этапе входного контроля
Пример дефекта |
Описание дефекта |
Механическое повреждение печатной платы. Сколы по краю платы, повреждение паяльной маски и диэлектрика | |
Дефект изготовления печатной платы — монтажное отверстие заполнено припоем | |
Дефект изготовления печатной платы — монтажные отверстия заполнены паяльной маской. Установка компонентов невозможна | |
Дефекты изготовления печатной платы: 1) Смещение рисунка паяльной маски относительно размещения контактных площадок. 2) Переходные отверстия полностью не заполнены паяльной маской. Потенциальные ловушки для остатков флюса при отмывке печатных узлов. 3) Чрезмерное утоньшение паяльной маски на контактных площадках переходных отверстий | |
Образование пустот под паяльной маской. Возможно ее отслоение в процессе последующих технологических операций | |
Неудовлетворительное качество финишного покрытия/повреждение финишного покрытия контактной площадки | |
Дефект изготовления печатной платы — нарушение геометрии контактной площадки | |
Дефект изготовления печатной платы — дефектная металлизация контактной площадки переходного отверстия | |
Дефект финишного покрытия (низкое качество лужения) — перемычка припоя в неположенном месте | |
Дефект изготовления печатной платы — перетрав проводников | |
Дефект изготовления печатной платы — разрыв проводников под паяльной маской | |
Дефект изготовления печатной платы — отслоение металлизации от контактной площадки | |
Дефект изготовления печатной платы: 1) Нарушение покрытия паяльной маски, 2) Вкрапление частиц металлизации, 3) Замыкание проводников | |
Дефект изготовления печатной платы — деформация. Существует высокая вероятность повреждения оборудования для сборки печатных плат. Максимальная деформация по диагонали не должна превышать 0,75% |
Деформация печатных плат является одним из наиболее распространенных дефектов базовых материалов. Насколько опасны эти дефекты? Какие существуют допуски на деформацию? Как произвести измерения и определить степень пригодности печатных плат к сборке? Эти и другие вопросы будут рассмотрены ниже.Многие производители электронных изделий необоснованно пренебрегают дефектами, вызванными изгибом и скручиванием печатных плат. Например, нам неоднократно приходилось слышать такие фразы: «С помощью прижимных планок и поддержки снизу мы можем компенсировать деформацию печатных плат». Действительно, названным способом во многих случаях можно компенсировать небольшую деформацию печатных плат. Однако применение плат, имеющих существенную деформацию, может стать причиной поломки дорогостоящего оборудования (см. рис. 1—3) или многочисленных производственных дефектов.
![]() |
Рис. 1. Дефект печатной платы: продольная деформация — изгиб. Автоматизированная сборка таких плат невозможна |
![]() |
Рис. 2. Дефект печатной платы: деформация по диагонали — скручивание. При движении по конвейеру правый нижний край печатной платы «заехал» на прижимную планку — возможно повреждение оборудования при установке компонентов |
![]() |
Рис. 3. Пример повреждения автомата установки компонентов. Сломан шток установочной головки (указано красной стрелкой) |
Нормативные требования
«Общий стандарт по конструированию печатных плат» IPC-2221A гласит: «Если нет иных указаний в основном чертеже, максимальное значение изгиба (см. рис. 1) и скручивания (см. рис. 2) не должно превышать 0,75% для плат с применением технологии поверхностного монтажа компонентов и 1,5% для плат, используемых для всех других технологий монтажа. Используемые при сборке мультиплицированные печатные платы и групповые заготовки, которые затем разделяются, должны также соответствовать указанным требованиям».
Оценка деформации
Оценка производится измерениями в соответствии со стандартом IPC-TM-650, «Метод 2.4.22».
Требуемое оборудование
– плоская поверхность;– микрометр.
Проведение испытаний (изгиб)
Поместите образец печатной платы на плоскую поверхность. Надавите на образец для его выпрямления, измерьте его длину (Д) и ширину (Ш) (см. рис. 4)
Рис. 4. Внешнее измерение |
Поместите образец печатной платы на плоской поверхности выпуклой стороной вверх.Придавите каждый край с обеих сторон для полного контакта с поверхностью (см. рис. 5).
Рис. 5. Измерение изгиба |
где ИД — процент изгиба по длине; ИШ — процент изгиба по ширине; RД — измеренный максимальный зазор поперек длины платы; RШ — измеренный максимальный зазор поперек ширины платы.Сравните полученные результаты с данными стандарта IPC-2221A.
Проведение испытаний (скручивание)
Поместите образец на плоскую поверхность. Надавите на образец для его выпрямления, измерьте образец по диагонали (D). Поместите образец печатной платы таким образом, чтобы три угла касались плоской поверхности.Измерьте зазор между четвертым углом и плоской поверхностью микрометром и запишите измеренный результат как R.Рассчитайте процентное отношение скручивания по формуле:
,
где R — размер зазора; D — величина диагонали образца1.Сравните полученные результаты с данными стандарта IPC-2221A.
Часто встречаются ситуации, когда клиенты, сталкиваясь с неудовлетворительной паяемостью печатных плат (см. рис. 6—9), задают вопросы о том, какие материалы для пайки (припой, флюс или паяльную пасту) лучше выбрать для устранения проблем. Однако борьба с возникшей проблемой не способствует ее предотвращению. «Сражаясь» с дефектом, вы не устраняете причину его возникновения, тем самым увеличивая себестоимость изделий и снижая их надежность в процессе эксплуатации.
![]() |
Рис. 6. Неудовлетворительная паяемость контактных площадок |
![]() |
Рис. 7. Неудовлетворительная паяемость контактных площадок и монтажных отверстий |
![]() |
Рис. 8. Отсутствие паяемости контактных площадок с покрытием (NiAu) |
![]() |
Рис. 9. Неудовлетворительная паяемость контактных площадок, припой не смачивает контактные площадки и собирается в шарики |
Метод Е — моделирование процесса поверхностного монтажа с применением оловянно-свинцового припоя
Данный метод контроля имитирует реальные условия для пайки печатных плат методом оплавления, изготовленных для технологии поверхностного монтажа.
Требуемое оборудование
Устройство трафаретной печати/трафарет. Для проведения теста конструкция трафарета должна соответствовать рисунку контактных площадок печатной платы и требованиям стандарта IPC-7525A; толщина трафарета должна удовлетворять требованиям таблицы 2.
Таблица 2. Выбор толщины трафарета
Номинальная толщина трафарета, мм |
Шаг выводов ИС, мм |
0,10 |
<0,50 |
0,15 |
0,50...0,65 |
0,20 |
>0,65 |
Тестовый образец
Тестовый образец печатной платы должен быть частью печатной платы или целой платой. Тестовый образец должен быть выборкой из испытываемой партии плат. Образец должен тестироваться в условиях, максимально приближенных к условиям реального процесса сборки печатных узлов. Обращение с тестовым образцом должно быть аккуратным и исключать возможность его загрязнения или механического повреждения контактных поверхностей.
Оборудование для пайки оплавлением
Для оплавления припоя должна использоваться ИК-/конвекционная печь или система парофазной пайки. Температуры, приведенные в таблице 3, соответствуют температуре/длительности пребывания для паяльной пасты.
Таблица 3. Выбор параметров процесса оплавления
Тип печи |
Температура, °C1 |
Время, с |
Парофазное оплавление |
215.219 |
30...60 (контакт при оплавлении) |
ИК/конвекционная паяльная печь |
Предварительный нагрев 150...170 |
50.70 |
Оплавление 215...230 |
1В зависимости от размеров и толщины тестового образца для достижения температуры пайки, указанной в таблице 3, может потребоваться дополнительное время.
Оборудование для визуального контроля
Визуальный контроль осуществляется с помощью стереомикроскопа с 10-кратным увеличением.
Процедура контроля
Нанесите паяльную пасту через трафарет на тестовый образец печатной платы. Произведите оплавление паяльной пасты в печи на рекомендуемых режимах. После завершения процесса пайки произведите очистку поверхности печатной платы от остатков флюса с помощью подходящей промывочной жидкости.
Критерии оценки
Минимум 95% поверхности каждой контактной площадки должно иметь равномерное покрытие припоем (см. рис. 10). Остальная поверхность может иметь незначительные области, не смоченные припоем, или проколы при условии, что данные дефекты не сконцентрированы в одном месте (см. рис. 11).
![]() |
Рис. 10. Хорошая паяемость; контактные площадки полностью смочены припоем без проколов |
![]() |
Рис. 11. Удовлетворительная паяемость; области, не смоченные припоем, не превышают 5% площади покрытия припоем контактной площадки |
Трудно найти предприятие, которое хоть раз в своей практике не столкнулось с проблемой неудовлетворительной паяемости выводов электронных радиоэлементов (ЭРЭ), как показано на рисунках 12 и 13.
![]() |
Рис. 12. Выводы оптрона частично смочены припоем |
![]() |
Рис. 13. Вид вывода оптрона (детализация рис. 12) сбоку. Вывод оптрона погружен в припой, но угол смачивания вывода припоем >90°, что свидетельствует о неудовлетворительной паяемости вывода |
Причин возникновения данного дефекта много: от неправильного выбора технологических материалов и режимов пайки до нарушения условий хранения или бракованных комплектующих. И все же наиболее часто подобные проблемы связаны именно с нарушением условий/сроков хранения элементов или поставкой некачественных компонентов. Эта часть статьи будет посвящена двум наиболее важным и часто задаваемым вопросам: методике оценки паяемости выводов ЭРЭ и критериям оценки качества.
Предварительный анализ
Контроль ЭРЭ на паяемость может осуществляться как в обязательном порядке (выборочный входной контроль), так и в случае обнаружения большого количества дефектов в процессе сборки печатных узлов (см. рис. 12 и 13). Безусловно, проведение выборочного входного контроля является более предпочтительным по сравнению со вторым случаем, т.к. в случае обнаружения ЭРЭ с неудовлетворительной паяемостью можно предпринять превентивные меры и не допустить лавинообразного нарастания числа дефектов при пайке.
Тем не менее, если вы столкнулись с дефектами, аналогичными приведенным на рисунках, перед принятием решения о необходимости проведения испытаний по контролю паяемости ЭРЭ необходимо забракованные печатные узлы подвергнуть общему предварительному анализу. Если неудовлетворительная паяемость выводов наблюдается практически на всех типах компонентов, то, в первую очередь, необходимо подвергать исследованию качество применяемых технологических материалов и параметры техпроцесса. Если же проблема проявляется только на одном типе ЭРЭ, то исследованию подвергаются уже сами компоненты.
Подробно методика проведения испытаний на паяемость ЭРЭ рассмотрена в стандарте IPC/EIA/JEDEC J-STD-002С «Методы оценки паяемости выводов компонентов, контактов, проушин, клемм и проводов». В данном стандарте приведено более 10-ти методов контроля паяемости выводов ЭРЭ для поверхностного монтажа и монтажа в отверстия с использованием свинцовой и бессвинцовой технологии пайки. Мы же остановимся подробно только на одном методе контроля паяемости компонентов поверхностного монтажа.
Метод моделирования процесса поверхностного монтажа с применением оловянно-свинцового припоя
В данном методе для компонента поверхностного монтажа имитируются реальные условия пайки методом оплавления.
Требуемое оборудование
Устройство трафаретной печати/трафарет. Для проведения теста конструкция трафарета должна соответствовать рисунку контактных площадок печатной платы и требованиям стандарта IPC-7525A, толщина трафарета должна удовлетворять требованиям таблицы 2.
Подложка для испытаний
Для проведения испытания используется керамическая подложка (не смачиваемая припоем) номинальной толщиной 0,635 мм. Возможно использование других типов подложек.
Оборудование для пайки оплавлением
Для оплавления припоя должна использоваться ИК-/конвекционная печь или система парофазной пайки. Температуры, приведенные в таблице 3, соответствуют температуре/длительности пребывания для паяльной пасты.
Оборудование для визуального контроля
Визуальный контроль осуществляется с помощью стереомикроскопа с 10-кратным увеличением. Для контроля компонентов с малым шагом выводов или контактных поверхностей (с шагом 0,5 мм или меньше) увеличение в процессе контроля должно быть не менее 30 крат.
Процедура
1. Нанесите паяльную пасту на подложку для испытаний через металлический трафарет одним плавным движением с помощью металлического или полиуретанового ракеля. 2. Аккуратно, стараясь не размазать отпечаток пасты, снимите трафарет. 3. Убедитесь в том, что геометрия полученного отпечатка соответствует выводам тестируемого компонента. 4. Произведите установку тестируемого компонента на отпечатки паяльной пасты на подложке. 5. Используя увеличительное оборудование, убедитесь в точности позиционирования компонента. 6. Поместите подложку с компонентом в печь и произведите оплавление. 7. После оплавления аккуратно извлеките подложку с компонентом из печи и дайте ей остыть до комнатной температуры. 8. Удалите компонент(ы) с подложки. Выводы компонента могут слегка прилипать к подложке из-за остатков флюса. 9. Перед визуальным контролем все видимые остатки флюса необходимо удалить с помощью рекомендуемой отмывочной жидкости со всех выводов компонента.
Критерии оценки
Критерием качества паяемости является равномерное, непрерывное и бездефектное покрытие припоем минимум на 95% металлизированных участков (областей) вывода компонента, являющихся критичными с точки зрения формирования паяного соединения (см. рис. 14—17).
![]() |
Рис. 14. Критичные области вывода компонента — В (нижние и боковые поверхности вывода на высоту 2Т со стороны пятки вывода). Паяемость верхней части вывода не регламентируется |
Рис. 15. Критичные области вывода компонента — А и В (нижние и боковые поверхности вывода на высоту толщины вывода). Паяемость верхней части и торца вывода (области С и С1) не регламентируется. Допускается наличие оголенного базового металла вывода компонента в торце (область С1) |
![]() |
Рис. 16. Критичная зона А (металлизированная область на нижней стороне компонента) и В (2/3 высоты боковой металлизации компонента) |
![]() |
Рис. 17. Каждый шариковый контакт должен быть покрыт слоем припоя (ровный, гладкий припой без несмоченных зон) |
![]() |
Рис. 18. Хорошая паяемость, не менее 95% контактных поверхностей имеют гладкое, равномерное и блестящее покрытие |
![]() |
Рис. 19. Удовлетворительная паяемость, контактные поверхности имеют небольшие области, не покрытые припоем |
![]() |
Рис. 20. Неудовлетворительная паяемость, контактные поверхности имеют значительное количество точечных отверстий в покрытии и области, не покрытые припоем |
Вы можете скачать эту статью в формате pdf здесь.
www.russianelectronics.ru
Паяемость печатных плат и компонентов — критерий надежности функционирования электрических схем
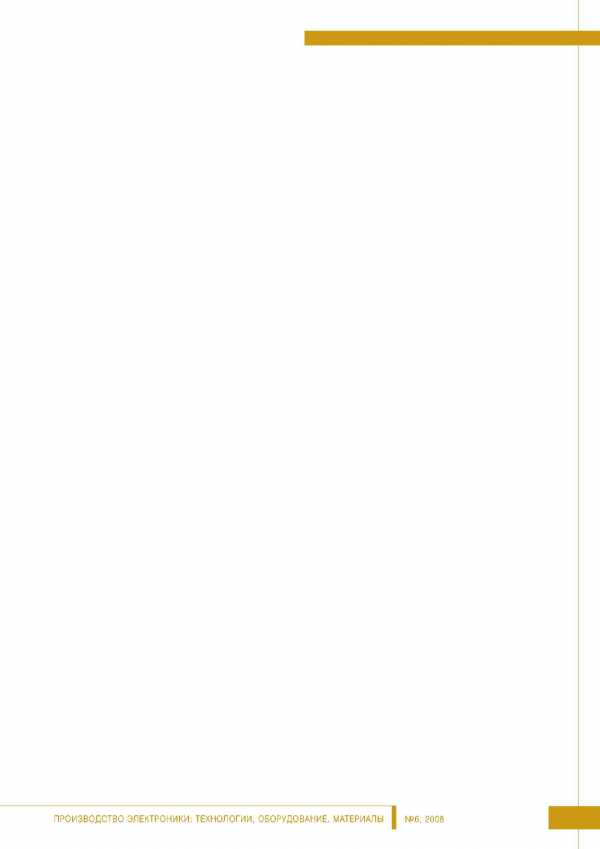
ПРОИЗВОДСТВО ЭЛЕКТРОНИКИ: ТЕХНОЛОГИИ, ОБОРУДОВАНИЕ, МАТЕРИАЛЫ
33
№ 6, 2008
монтаж компонентов
Качество функционирования и степень надежности современных электронных сборочных узлов порой оставляет
желать лучшего. Какие меры следует принять на этапе выбора типа паяемых печатных плат, компонентов и приме-
няемых для пайки материалов с целью повышения качества производимой электронной продукции? Определение
качества производимой продукции на этом этапе, по сути, является прогнозированием надежности. Следовательно,
такие возможности позволяют вносить своевременные коррективы в процесс производства и снижать затраты на
переработку, требуемую при наличии бракованных экземпляров или партий. В статье рассмотрены возможности со-
временного оборудования по определению одного из наиболее важных критериев определения качества функциони-
рования электронной продукции — паяемости — на базе системы MUST 3 компании GEN 3 Systems (Великобритания).
Зачем определять паяемость?
Паяемость печатных плат и ком-
понентов является одним из наиболее
значимых критериев при определении
качества будущей производимой про-
дукции.
Как известно, образование не-
пропаянных областей (мест) влечет
за собой отказ в функционировании
электронного узла на ранней стадии.
Возможной является проверка на
наличие непропаянных мест после
окончания процесса пайки. Такой ме-
тод, безусловно, важен при проверке
соответствия качества выпускаемого
оборудования. Тем не менее опреде-
ление паяемости печатных плат и
компонентов позволяет определить
качество пайки еще до начала про-
цесса с точностью, соответствую-
щей
международным
стандартам
IPC J-STD-002B и IPC J-STD-003A.
Так, определение паяемости дает
возможность прогнозировать ожида-
емое качество пайки, а также своев-
ременно вносить корректировку в от-
ношении материалов, применяемых
на контактных поверхностях плат и
контактах паяемых компонентов.
Паяемость печатной платы ха-
рактеризует способность контактных
поверхностей печатной платы, при-
легающих областей и монтажных от-
верстий легко смачиваться припоем
и сопротивляться сложным условиям
процесса пайки. Паяемость компо-
нентов характеризует соответствие
существующим требованиям и позво-
ляет выявить отклонения, например
невозможность пайки.
Паяемость определяется на эта-
пе производства печатных плат, в
Артем Рогачев
, специалист отдела технологического оборудования, «УниверсалПрибор»
паяемость печатных плат и компонентов —
критерий надежности функционирования
электрических схем
процессе их приемки заказчиком
или непосредственно перед началом
пайки.
Характеристики паяемости
Основными параметрами, опреде-
ляющими паяемость, являются:
– смачивание;
– тепловая характеристика;
– сопротивляемость нагреву в
процессе пайки.
Под
смачиванием
понимают
реакцию между припоем и осно-
ванием, т.е. вступление припоя в
молекулярный контакт с основани-
ем (печатной платой). Тепловая ха-
рактеристика есть количественное
отражение способности паяемых
компонентов изменять собственную
температуру при внешнем тепловом
воздействии. Сопротивляемость на-
греву в процессе пайки обусловлена
материалами компонента и основа-
ния.
метод иЗмерения паяемости
Первоначально применялся сле-
дующий способ измерения паяемо-
сти: погружение вывода компонента,
предназначенного для пайки, в ем-
кость с нагретым до рабочей темпе-
ратуры припоем, и визуальная оценка
степени смачиваемости.
Данный метод обнаружил такие
недостатки как неточность измере-
ний, ненадежность, отсутствие коли-
чественной характеристики.
Альтернативным методом стало
определение паяемости путем вычис-
ления значений силы поверхностного
натяжения рабочего материала (при-
поя).
Использование такого метода по-
зволяет получить количественную
характеристику паяемости, достичь
высокой точности и обеспечить на-
дежность и повторяемость измере-
ний.
Для определения паяемости про-
водятся следующие измерения:
– тест капли припоя;
– проникаемость припоя сквозь
монтажные отверстия;
– измерение мениска при погру-
жении;
– поверхностное натяжение при
вращении;
– измерение баланса смачивания;
– измерение баланса смачивания
паяемых компонентов.
Наиболее информативным из при-
меняемых измерений является изме-
рение баланса смачивания паяемых
компонентов. Этот метод реализован
в системе MUST 3.
принцип иЗмерения паяемости
системой MUST 3
Реализованный в системе метод
позволяет получить количественное
выражение паяемости в миллинью-
тонах (путем измерения силы по-
верхностного натяжения припоя).
Также данный метод позволяет те-
стировать мельчайшие компонен-
ты. Международными стандартами
определены данные, получаемые в
результате измерений. Как правило,
результат измерений представляется
в виде графика зависимости силы
от времени (т.н. «кривые смачива-
ния»).
Суть кривых смачивания четко
прослеживается на рис. 1— 5.
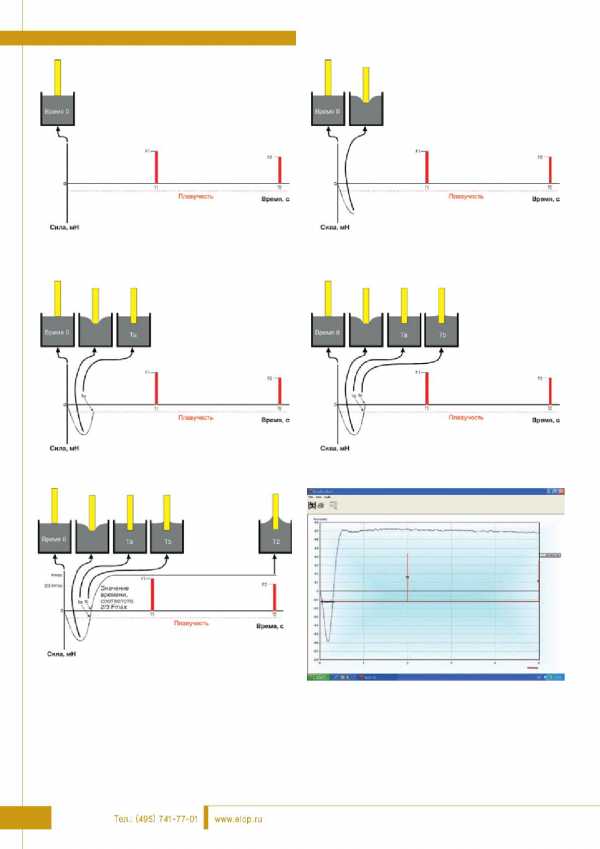
Тел.: (495) 741-77-01
34
www.elcp.ru
монтаж компонентов
Рис. 3. Фаза плавучести (начало смачивания)
Рис. 4. Фаза смачивания
Рис. 6. Образец кривой смачивания
Рис. 5. Фаза стабилизации значения смачивания (уменьшение
силы поверхностного натяжения)
Ниже приведена типовая кривая смачивания (см. рис. 6).
Вся полученная количественная информация отобра-
жается также в виде таблиц данных. В таблице содержится
информация, определенная требованиями стандартов, на-
пример значения контрольных отрезков времени, силы в
соответствующие моменты измерений, несмачиваемость,
а также статус (соответствие/несоответствие).
Рис. 1. Момент соприкосновения контакта с поверхностью припоя
Рис. 2. Вогнутый мениск, экстремум силы натяжения
(несмачиваемость)
описание системы
Прототип системы MUST (многоосновной универсаль-
ной системы измерения паяемости) впервые был представ-
лен в 1970-х гг. В настоящее время во всем мире насчитыва-
ется около 2000 пользователей MUST. MUST 3 продолжает
определять стандарты измерений, которые были разрабо-
таны Национальной физической лабораторией (Велико-
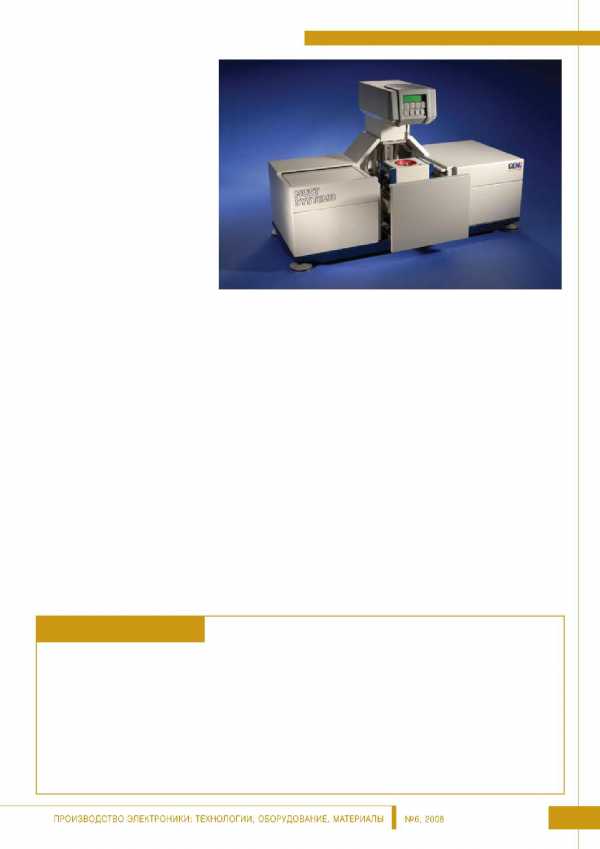
ПРОИЗВОДСТВО ЭЛЕКТРОНИКИ: ТЕХНОЛОГИИ, ОБОРУДОВАНИЕ, МАТЕРИАЛЫ
35
№ 6, 2008
монтаж компонентов
британия) в сотрудничестве с Gen 3
Systems (см. рис. 7). Система являет-
ся эталонной в области тестирования
паяемости и, что также немаловажно,
является наиболее гибкой системой
из представленных на рынке.
Основные характеристики систе-
мы следующие.
1. Высокоточное выравнивание +
видеосистема (опция).
2. Лучшая система для измерения
силы.
3. Дружественный интерфейс с
Windows XP и возможностью исполь-
зования SPC.
4. Критерий соответствия/несоот-
ветствия данных
5. Гибкость:
– обычные, выводные компо-
ненты;
– компоненты
поверхностного
монтажа до 0201 включительно;
– разъемы плат.
Система MUST 3 является первым
оборудованием, в котором применя-
ется метод тестирования капли при-
поя размером 4; 3,2; 2 и 1 мм.
Преимуществами данного метода
являются:
– максимальная точность для
меньших компонентов;
– применение в случае с компо-
нентами с ограниченной областью
смачивания;
– повторяемость тестов многовы-
водных компонентов;
– соответствие
промышленным
стандартам IEC/IPC/JIS.
точностные Характеристики
системы MUST 3
Глубина погружения: 0...30 мм (с
точностью до 0,01 мм), скорость по-
гружения 0...30 мм/с (с точностью до
0,05 мм/с).
Кроме того, система является эта-
лонной, поскольку стандарты опреде-
ления паяемости были разработаны и
утверждены на этапе ее проектирова-
ния при сотрудничестве Gen 3 Systems
и Национальной физической лабора-
тории.
В системе MUST 3 применяется
рассмотренный выше метод тестиро-
вания капли припоя.
Все, что необходимо для прове-
дения измерений — комплект ванн,
шариков припоя (свинцово-оло вян-
ного и бессвинцового), флюс, ПО для
ПК на базе Windows, а также комп лект
рабочих принадлежностей. Все это
включено в комплект системы.
Заключение
По результатам статистическо-
го анализа причин отказов в работе
электронных сборочных узлов можно
судить, насколько велико значение
Рис. 7. Система измерения паяемости MUST 3
мероприятий, направленных на по-
вышение надежности их функцио-
нирования, вероятности безотказной
работы.
Определение надежности элек-
трических схем представляет собой
совокупность тестов, определенных
международными стандартами. Для
эффективного определения качест-
ва электрических схем необходимо
сложное, высокопрецизионное обо-
рудование.
Представляется наиболее перспек-
тивным применение оборудования,
разработанного на основании суще-
ствующих стандартов.
Тестовое оборудование компании
GEN 3 Systems на этапе разработки
сыграло определяющую роль в уста-
новлении стандартов определения
качества электрических схем и, таким
образом, являет собой эталон средств
измерений.
новости рынка
Компания Florida CirTech, известный разработчик химиче-
ских составов и материалов, используемой в производстве
печатных плат, предлагает новый материал — CK300, который
она характеризует как «убийцу катализатора» (Catalyst Killer).
Материал позволяет минимизировать пропуски и
background при нанесении электролитического никеля и
иммерсионного золота (процесс ENIG, Electroless Nickel
Immersion Gold), удаляет осадок палладия в процессе элек-
тролитического осаждения меди, предохраняет монтажные
(крепежные) отверстия от меди.
Материал CK300, при использовании фирменного ноу-хау
до применения ENIG, позволяет решить ряд проблем, связан-
ных с этим процессом.
Американская компания Florida CirTech (Greeley, штат
Колорадо) специализируется на разработке специальных
химических составов и материалов, используемых при изго-
товлении печатных плат. Компания предлагает широкий ряд
химических продуктов, от систем для удаления фоторезистов
(Photoresist strippers) до электролитического осаждения меди
(Electroless Copper) и различных покрытий. Будучи участником
программы Genesis Materials, компания предлагает не содер-
жащие VOC жидкие фоторезисты, LPI паяльные маски и чер-
нила для надписей. Производство компании аттестовано на
соответствие ISO 9001.
www.russianelectronics.ru
CK300 — «убийца» катализатора
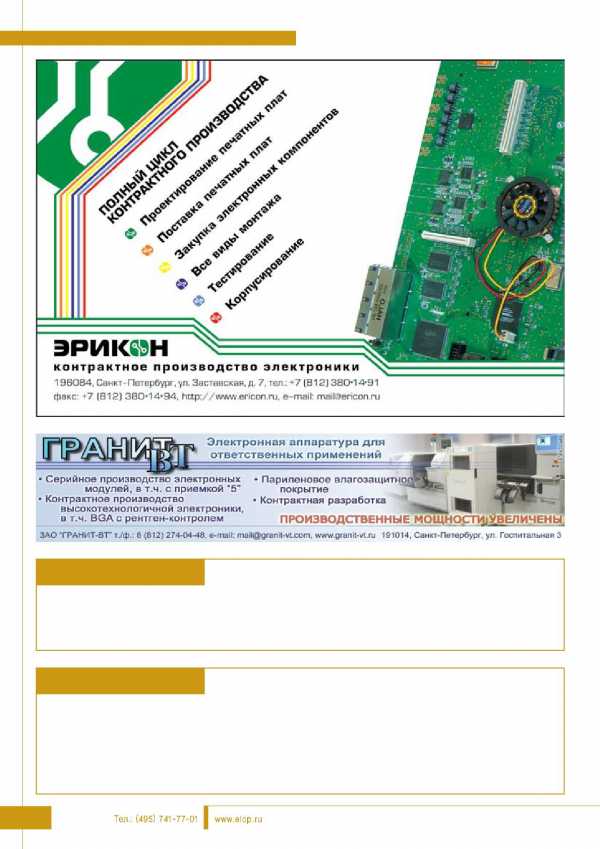
Тел.: (495) 741-77-01
36
www.elcp.ru
монтаж компонентов
новости рынка
Компания Juki Automation Systems, производитель
сборочно-монтажного оборудования, сообщает о рекордных
результатах III квартала 2008 г. Суммарный рост составил
более 35%, продажи оборудования для установки SMT ком-
понентов выросли почти на 40%, приборов для селективной
пайки — более чем на 20%.
Боб Блэк (Bob Black), президент и генеральный директор
Juki, говорит: «Все мы, работающие в компании, хотим вы-
разить благодарность нашим клиентам, благодаря которым
стало возможным достичь столь выдающихся результатов».
Компания отмечает, что основной вклад в результаты продаж
2008 года внес высокоскоростной автомат установки компо-
нентов FX-3.
www.russianelectronics.ru
Juki сообщает о рекордных темпах роста продаж
новости рынка
Шведская компания Civa, поставщик печатных плат, открыла
технологический офис в Санкт-Петербурге, в котором предлага-
ет услуги по подготовке CAM прототипов, а также оптимизации
плат под массовое производство. Компания специализируется
на быстрой разработке и поставке прототипов печатных плат.
Выбор пал на С.-Петербург, поскольку в этом городе
действует несколько университетов, готовящих кадры вы-
сокой квалификации.
www.russianelectronics.ru
Civa открыла офис в санкт-петербурге
www.russianelectronics.ru
Паяемость печатных плат и компонентов — критерий надежности функционирования электрических схем
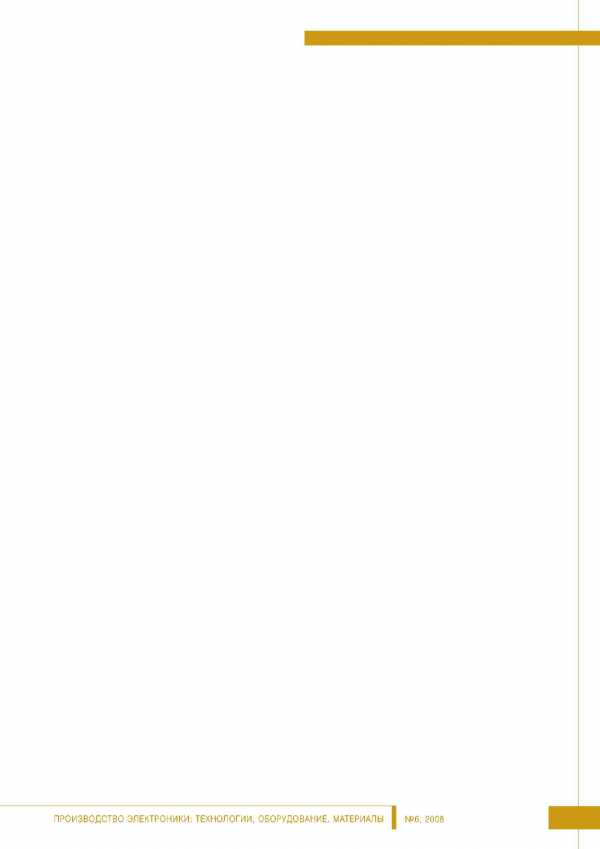
ПРОИЗВОДСТВО ЭЛЕКТРОНИКИ: ТЕХНОЛОГИИ, ОБОРУДОВАНИЕ, МАТЕРИАЛЫ
33
№ 6, 2008
монтаж компонентов
Качество функционирования и степень надежности современных электронных сборочных узлов порой оставляет
желать лучшего. Какие меры следует принять на этапе выбора типа паяемых печатных плат, компонентов и приме-
няемых для пайки материалов с целью повышения качества производимой электронной продукции? Определение
качества производимой продукции на этом этапе, по сути, является прогнозированием надежности. Следовательно,
такие возможности позволяют вносить своевременные коррективы в процесс производства и снижать затраты на
переработку, требуемую при наличии бракованных экземпляров или партий. В статье рассмотрены возможности со-
временного оборудования по определению одного из наиболее важных критериев определения качества функциони-
рования электронной продукции — паяемости — на базе системы MUST 3 компании GEN 3 Systems (Великобритания).
Зачем определять паяемость?
Паяемость печатных плат и ком-
понентов является одним из наиболее
значимых критериев при определении
качества будущей производимой про-
дукции.
Как известно, образование не-
пропаянных областей (мест) влечет
за собой отказ в функционировании
электронного узла на ранней стадии.
Возможной является проверка на
наличие непропаянных мест после
окончания процесса пайки. Такой ме-
тод, безусловно, важен при проверке
соответствия качества выпускаемого
оборудования. Тем не менее опреде-
ление паяемости печатных плат и
компонентов позволяет определить
качество пайки еще до начала про-
цесса с точностью, соответствую-
щей
международным
стандартам
IPC J-STD-002B и IPC J-STD-003A.
Так, определение паяемости дает
возможность прогнозировать ожида-
емое качество пайки, а также своев-
ременно вносить корректировку в от-
ношении материалов, применяемых
на контактных поверхностях плат и
контактах паяемых компонентов.
Паяемость печатной платы ха-
рактеризует способность контактных
поверхностей печатной платы, при-
легающих областей и монтажных от-
верстий легко смачиваться припоем
и сопротивляться сложным условиям
процесса пайки. Паяемость компо-
нентов характеризует соответствие
существующим требованиям и позво-
ляет выявить отклонения, например
невозможность пайки.
Паяемость определяется на эта-
пе производства печатных плат, в
Артем Рогачев
, специалист отдела технологического оборудования, «УниверсалПрибор»
паяемость печатных плат и компонентов —
критерий надежности функционирования
электрических схем
процессе их приемки заказчиком
или непосредственно перед началом
пайки.
Характеристики паяемости
Основными параметрами, опреде-
ляющими паяемость, являются:
– смачивание;
– тепловая характеристика;
– сопротивляемость нагреву в
процессе пайки.
Под
смачиванием
понимают
реакцию между припоем и осно-
ванием, т.е. вступление припоя в
молекулярный контакт с основани-
ем (печатной платой). Тепловая ха-
рактеристика есть количественное
отражение способности паяемых
компонентов изменять собственную
температуру при внешнем тепловом
воздействии. Сопротивляемость на-
греву в процессе пайки обусловлена
материалами компонента и основа-
ния.
метод иЗмерения паяемости
Первоначально применялся сле-
дующий способ измерения паяемо-
сти: погружение вывода компонента,
предназначенного для пайки, в ем-
кость с нагретым до рабочей темпе-
ратуры припоем, и визуальная оценка
степени смачиваемости.
Данный метод обнаружил такие
недостатки как неточность измере-
ний, ненадежность, отсутствие коли-
чественной характеристики.
Альтернативным методом стало
определение паяемости путем вычис-
ления значений силы поверхностного
натяжения рабочего материала (при-
поя).
Использование такого метода по-
зволяет получить количественную
характеристику паяемости, достичь
высокой точности и обеспечить на-
дежность и повторяемость измере-
ний.
Для определения паяемости про-
водятся следующие измерения:
– тест капли припоя;
– проникаемость припоя сквозь
монтажные отверстия;
– измерение мениска при погру-
жении;
– поверхностное натяжение при
вращении;
– измерение баланса смачивания;
– измерение баланса смачивания
паяемых компонентов.
Наиболее информативным из при-
меняемых измерений является изме-
рение баланса смачивания паяемых
компонентов. Этот метод реализован
в системе MUST 3.
принцип иЗмерения паяемости
системой MUST 3
Реализованный в системе метод
позволяет получить количественное
выражение паяемости в миллинью-
тонах (путем измерения силы по-
верхностного натяжения припоя).
Также данный метод позволяет те-
стировать мельчайшие компонен-
ты. Международными стандартами
определены данные, получаемые в
результате измерений. Как правило,
результат измерений представляется
в виде графика зависимости силы
от времени (т.н. «кривые смачива-
ния»).
Суть кривых смачивания четко
прослеживается на рис. 1— 5.
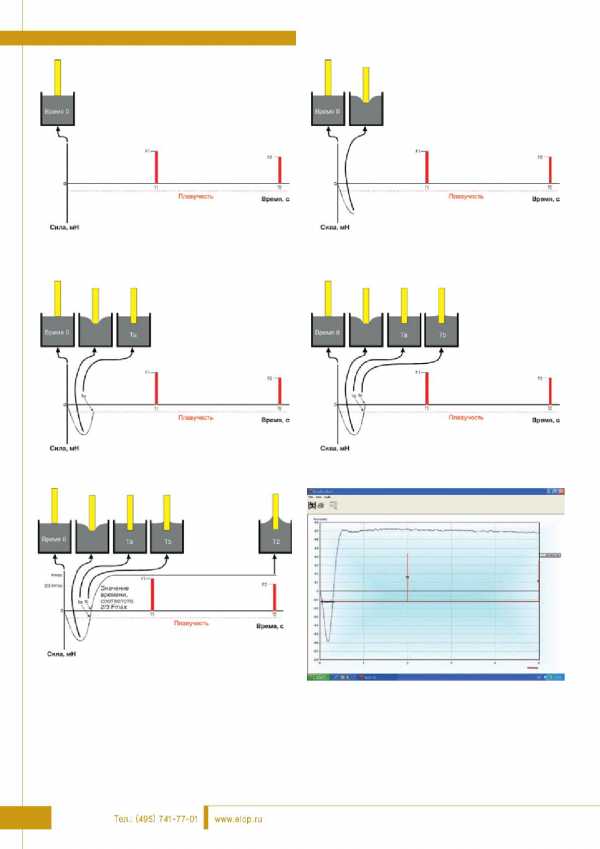
Тел.: (495) 741-77-01
34
www.elcp.ru
монтаж компонентов
Рис. 3. Фаза плавучести (начало смачивания)
Рис. 4. Фаза смачивания
Рис. 6. Образец кривой смачивания
Рис. 5. Фаза стабилизации значения смачивания (уменьшение
силы поверхностного натяжения)
Ниже приведена типовая кривая смачивания (см. рис. 6).
Вся полученная количественная информация отобра-
жается также в виде таблиц данных. В таблице содержится
информация, определенная требованиями стандартов, на-
пример значения контрольных отрезков времени, силы в
соответствующие моменты измерений, несмачиваемость,
а также статус (соответствие/несоответствие).
Рис. 1. Момент соприкосновения контакта с поверхностью припоя
Рис. 2. Вогнутый мениск, экстремум силы натяжения
(несмачиваемость)
описание системы
Прототип системы MUST (многоосновной универсаль-
ной системы измерения паяемости) впервые был представ-
лен в 1970-х гг. В настоящее время во всем мире насчитыва-
ется около 2000 пользователей MUST. MUST 3 продолжает
определять стандарты измерений, которые были разрабо-
таны Национальной физической лабораторией (Велико-
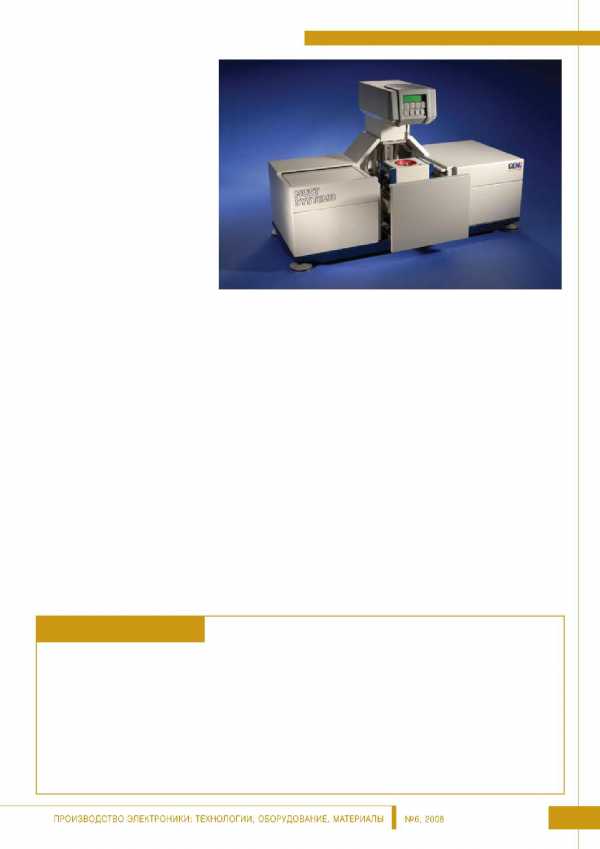
ПРОИЗВОДСТВО ЭЛЕКТРОНИКИ: ТЕХНОЛОГИИ, ОБОРУДОВАНИЕ, МАТЕРИАЛЫ
35
№ 6, 2008
монтаж компонентов
британия) в сотрудничестве с Gen 3
Systems (см. рис. 7). Система являет-
ся эталонной в области тестирования
паяемости и, что также немаловажно,
является наиболее гибкой системой
из представленных на рынке.
Основные характеристики систе-
мы следующие.
1. Высокоточное выравнивание +
видеосистема (опция).
2. Лучшая система для измерения
силы.
3. Дружественный интерфейс с
Windows XP и возможностью исполь-
зования SPC.
4. Критерий соответствия/несоот-
ветствия данных
5. Гибкость:
– обычные, выводные компо-
ненты;
– компоненты
поверхностного
монтажа до 0201 включительно;
– разъемы плат.
Система MUST 3 является первым
оборудованием, в котором применя-
ется метод тестирования капли при-
поя размером 4; 3,2; 2 и 1 мм.
Преимуществами данного метода
являются:
– максимальная точность для
меньших компонентов;
– применение в случае с компо-
нентами с ограниченной областью
смачивания;
– повторяемость тестов многовы-
водных компонентов;
– соответствие
промышленным
стандартам IEC/IPC/JIS.
точностные Характеристики
системы MUST 3
Глубина погружения: 0...30 мм (с
точностью до 0,01 мм), скорость по-
гружения 0...30 мм/с (с точностью до
0,05 мм/с).
Кроме того, система является эта-
лонной, поскольку стандарты опреде-
ления паяемости были разработаны и
утверждены на этапе ее проектирова-
ния при сотрудничестве Gen 3 Systems
и Национальной физической лабора-
тории.
В системе MUST 3 применяется
рассмотренный выше метод тестиро-
вания капли припоя.
Все, что необходимо для прове-
дения измерений — комплект ванн,
шариков припоя (свинцово-оло вян-
ного и бессвинцового), флюс, ПО для
ПК на базе Windows, а также комп лект
рабочих принадлежностей. Все это
включено в комплект системы.
Заключение
По результатам статистическо-
го анализа причин отказов в работе
электронных сборочных узлов можно
судить, насколько велико значение
Рис. 7. Система измерения паяемости MUST 3
мероприятий, направленных на по-
вышение надежности их функцио-
нирования, вероятности безотказной
работы.
Определение надежности элек-
трических схем представляет собой
совокупность тестов, определенных
международными стандартами. Для
эффективного определения качест-
ва электрических схем необходимо
сложное, высокопрецизионное обо-
рудование.
Представляется наиболее перспек-
тивным применение оборудования,
разработанного на основании суще-
ствующих стандартов.
Тестовое оборудование компании
GEN 3 Systems на этапе разработки
сыграло определяющую роль в уста-
новлении стандартов определения
качества электрических схем и, таким
образом, являет собой эталон средств
измерений.
новости рынка
Компания Florida CirTech, известный разработчик химиче-
ских составов и материалов, используемой в производстве
печатных плат, предлагает новый материал — CK300, который
она характеризует как «убийцу катализатора» (Catalyst Killer).
Материал позволяет минимизировать пропуски и
background при нанесении электролитического никеля и
иммерсионного золота (процесс ENIG, Electroless Nickel
Immersion Gold), удаляет осадок палладия в процессе элек-
тролитического осаждения меди, предохраняет монтажные
(крепежные) отверстия от меди.
Материал CK300, при использовании фирменного ноу-хау
до применения ENIG, позволяет решить ряд проблем, связан-
ных с этим процессом.
Американская компания Florida CirTech (Greeley, штат
Колорадо) специализируется на разработке специальных
химических составов и материалов, используемых при изго-
товлении печатных плат. Компания предлагает широкий ряд
химических продуктов, от систем для удаления фоторезистов
(Photoresist strippers) до электролитического осаждения меди
(Electroless Copper) и различных покрытий. Будучи участником
программы Genesis Materials, компания предлагает не содер-
жащие VOC жидкие фоторезисты, LPI паяльные маски и чер-
нила для надписей. Производство компании аттестовано на
соответствие ISO 9001.
www.russianelectronics.ru
CK300 — «убийца» катализатора
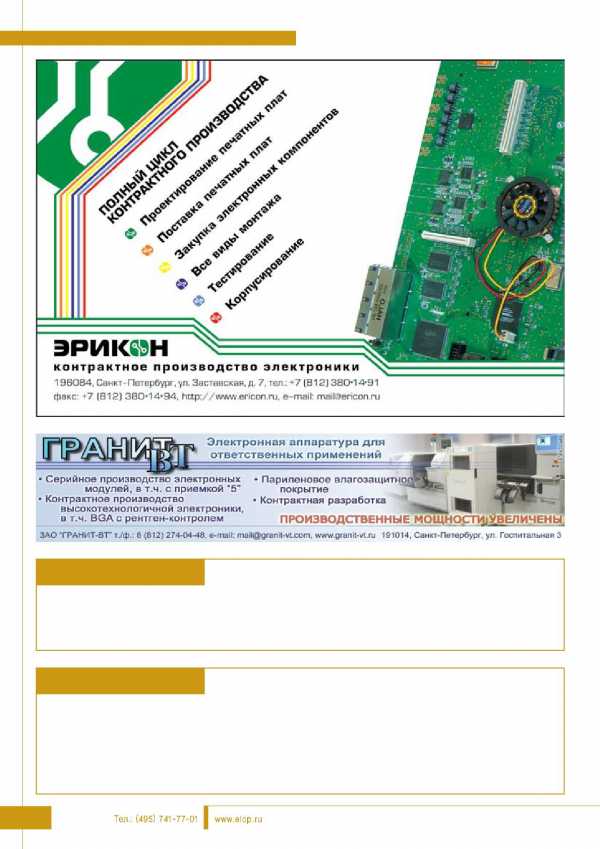
Тел.: (495) 741-77-01
36
www.elcp.ru
монтаж компонентов
новости рынка
Компания Juki Automation Systems, производитель
сборочно-монтажного оборудования, сообщает о рекордных
результатах III квартала 2008 г. Суммарный рост составил
более 35%, продажи оборудования для установки SMT ком-
понентов выросли почти на 40%, приборов для селективной
пайки — более чем на 20%.
Боб Блэк (Bob Black), президент и генеральный директор
Juki, говорит: «Все мы, работающие в компании, хотим вы-
разить благодарность нашим клиентам, благодаря которым
стало возможным достичь столь выдающихся результатов».
Компания отмечает, что основной вклад в результаты продаж
2008 года внес высокоскоростной автомат установки компо-
нентов FX-3.
www.russianelectronics.ru
Juki сообщает о рекордных темпах роста продаж
новости рынка
Шведская компания Civa, поставщик печатных плат, открыла
технологический офис в Санкт-Петербурге, в котором предлага-
ет услуги по подготовке CAM прототипов, а также оптимизации
плат под массовое производство. Компания специализируется
на быстрой разработке и поставке прототипов печатных плат.
Выбор пал на С.-Петербург, поскольку в этом городе
действует несколько университетов, готовящих кадры вы-
сокой квалификации.
www.russianelectronics.ru
Civa открыла офис в санкт-петербурге
www.russianelectronics.ru
Способ контроля паяемости металлизированных отверстий печатных плат
ОПИСАНИЕ
ИЗОБРЕТЕНИЯ
К АВТОРСКОМУ СВИДЕТЕЛЬСТВУ
Союз Советских
Социаиистических
Республик (11)904930 (61) Дополнительное к авт. свид-ву (22) Заявлено 040778 (21) 2640383/25-27 с присоединением заявки № (23) Приоритет
Опубликовано 1502.82. Бюллетень ¹ 6
Дата опубликования описания 15.02.82 (51) М. Кл.з
В 23 К 1/00
Н 05 К 3/34
Государствеиный комитет
СССР по делам изобретеиий и открытий (53) УДК 621. 791 ° . 3 (088. 8) (72) Авторы изобретения
Ю.П. Тризна и Ю.А. Идельс (71) Заявитель (54) СПОСОБ КОНТРОЛЯ ПАЯЕМОСТИ МЕТАЛЛИЗИРОВАННЫХ
ОТВЕРСТИИ ПЕЧАТНЫХ ПЛАТ ь а -к—
Изобретение относится к пайке, в частности к способам контроля паяемости, и может быть использовано при изготовлении и пайке печатных плат.
Известен способ определения паяемости металлизированных отверстий печатных плат, согласно которому измеряют время заполнения отверстий расплавленным припоем и по нему судят о паяемости (1).
Известен также способ контроля паяемости металлизированных отверстий печатных плат, согласно которому в отверстие вводят сверху зонд, а снизу подводят каплю расплавленного припоя и измеряют время поднятия расплавленного припоя до зонда и по измеренному времени судят о паяемости 12) .
Оба способа основаны на том, что скорость затекания припоя зависит от качества подготовки поверхности.
Пояемость в обоих случаях определяется в секундах.
Недостатки этих способов заключаются в том, что после проведения измерения припой кристаллизуется в отверстиях, что приводит к необходимости введения дополнительной операции — извлечения припоя из отверстий перед пайкой. Кроме того, при проведении измерений, а также при извлечении припоя из отверстий металлизация подвергается температурным воздействиям, которые повышают вероятность возникновения нарушения ее адгезионной прочности.
Цель изобретения — повышение производительности и исключение температурного воздействия на металлизацию.
Поставленная цель достигается тем, что металлизированные отверстия облучают ультрафиолетовым излучением, регистрируют величину фотоэлектронной эмиссии, возникающей на стенках отверстий, и паяемость отверстий
20 определяют из соотношения где P — паяемость, с;
25 d u h — диаметр и высота контроли15уемого отверстия, соответственно, см;
I — регистрируемый поток фотоэлектронов имп/с;
К вЂ” коэффициент, величина кото904930 рого меняется в пределах
500-1000 в зависимости от материала стенок отверстия.
Физическая сущность способа состоит в том, что величина фотоэлектронной эмиссии зависит от пленок окислов и загрязнений, находящихся на стенках метадлизированных отверстий и определяющих качество подготовки их поверхности к пайке. При этом металлизированные отверстия не вступают в контакт с расплавленным припоем, что дает возможность повысить производительность и исключить нарушения адгеэии металлизационного слоя к поверхности платы.
На чертеже изображена принципи- 15 альная схема устройства, реализующего предлагаемый способ.
Электрод 1, помещенный внутри металлизированного отверстия 2 печатной платы 3, служит для регистра- Щ ции фотоэлектронов, возникающих при облучении стенок отверстия ультрафиолетовым осветителем 4. Металлизация отверстия заземпяется при помощи контакта 5. усилитель 6 и линейный интенсиметр 7 служат для измерения потока фотоэлектронов.
При облучении стенки отверстия 2 ультрафиолетовым излучением возникает фотоэлектронная эмиссия. На
ЗО электрод 1 подается высокий (1000 В) положительный потенциал. В электрическом поле, образующемся между электродом 1 и металлизацией отВеРстия 2, фотоэлектроны ускоряются по направлению к электроду 1, что позволяет осуществить их регистрацию по возникающим импульсным изменениям потенциала электрода 1, усиливаемым усилителем 6 и регистрируемым схемой линейного интенсиметра 7, 40
Пример. Производят измерение паяемости печатной платы, имеющей металлизированные отверстия диаметром 1 = 0,15 см при толщине платы
h = 0,15 см. Стенки отверстий обслуживают припоем ПОС-61,при этом значение коэффициента K составляет 620.
Паяемость рассчитывают по приведенной формуле.
Результаты измерений хорошо согласуются со значениями паяемости, полученными на той же плате по измерению времени затекания припоя в те же отверстия.
Формула изобретения
Способ контроля паяемости металлизированных отверстий печатных плат, отличающийся тем, что, с целью повышения производительности и исключения температурного воздействия на металлизацию, металлизированные отверстия облучают ультрафиолетовым излучением, регистрируют величину фотоэлектронной эмиссии, возникающей на стенках отверстий, и определяют паяемость отверстий из соотношения ь Ф
PK ——
3 Ь"+ д" где Р - паяемость, с;
dPh - диаметр и высота контролируемого отверстия, соответстВЕННО, СМ1
Е - регистрируемый поток фотоэлементов, имп/с; .К вЂ” коэффициент, величина которого меняется в пределах
500-1000 в зависимости от материала стенок отверстия.
Источники информации, принятые во внимание при экспертизе
1. Патент Cf11A Р 3857290, кл. 6 01 N 13/02, 1972.
2. Авторское свидетельство СССР
Ф 464988, кл. Н 05 К 3/34, 1973.
Составитель Ф. Конопелько
Редактор Л. Алексеенко Техред М.Гергель Корректор Г. Orap
Заказ 225/20
Тираж 1150 Подписное
ВНИИПИ ГосУдарственного комитета СССР по делам изобретений и открытий
113035, Москва, X-35, Раушская наб., д. 4/5
Филиал ППП Патент, г. Ужгород, ул. Проектная,4
www.findpatent.ru