Слоистые пластики: свойства и применение. Пластик древесный
Древесно-слоистый пластик — Википедия
Материал из Википедии — свободной энциклопедии
Древесно-слоистый пластик (ДСП) Не путать с «Древесно-стружечной плитой», которую также иногда упрощённо обозначают аббревиатурой ДСП, хотя для древесно-стружечных плит имеется своя аббревиатура — ДСтПДреве́сно-слои́стый пластик (ДСП) (бакелитовая фанера, дельта-древесина) — материал, представляющий собой древесно-полимерный композит, изготавливаемый из листов лущеного шпона (берёзы и других пород, толщиной 0,35—0,65 мм, влажностью 6—10 %), склеенных синтетическими смолами резольного типа под давлением и температурой[1].
Области применения
Антифрикционные свойства, стойкость к воздействию агрессивных сред, абразивов; стабильность при сверхнизких температурах (–270 °С), механическая прочность, водостойкость, диэлектрические свойства позволяют применять ДСП в различных областях техники, таких как:
- Узлы трения.
- Зубчатые колеса.
- Закрытые и открытые металло-полимерные зубчатые передачи.
- Вкладыши подшипников скольжения.
- Для изготовления пуленепробиваемых дверей, банковского оборудования.
- Криогенная и космическая техника.
- В судостроительной промышленности для изготовления дейдвудных подшипников гребных валов.
- Для изготовления затворов гидротехнических сооружений.
- В авиационной технике лопасти; винты вертолётов.
- В транспортном машиностроении: настил полов в автобусах, троллейбусах, трамваях; направляющие эскалаторов метрополитена.
- В строительстве.
- В электротехнической промышленности для изготовления изоляторов, деталей трансформаторов высокого напряжения, выпрямителей (заменяет стеклопластик, текстолит и гетинакс).
- Для изготовления деталей машин текстильной промышленности.
- Как самосмазывающий антифрикционный материал, материал в качестве ползунов лесопильных рам и других аналогичных деталей.
- В металлургическом оборудовании.
- В горнодобывающем оборудовании.
Видео по теме
Марки ДСП
В зависимости от расположения волокон древесины шпона в смежных слоях и назначения древесные слоистые в России пластики изготовляют следующих марок:
- ДСП-А;
- ДСП-Б; ДСП-Б-э; ДСП-Б-м; ДСП-Б-т; ДСП-Б-о;
- ДСП-В; ДСП-В-э; ДСП-В-м;
- ДСП-Г; ДСП-Г-м.
Буквы А, Б, В, Г указывают порядок укладки шпона в пластике:
- А — волокна древесины шпона во всех слоях имеют параллельное направление или каждые 4 слоя с параллельным направлением волокон древесины шпона чередуются с одним слоем, имеющим направление волокон под углом 20—25° к смежным слоям.
- Б — каждые 8—12 слоев шпона с параллельным направлением волокон древесины шпона чередуются с одним слоем, имеющим перпендикулярное направление волокон древесины к смежным слоям.
- В — волокна древесины шпона в смежных слоях взаимно перпендикулярны.
- Г — волокна древесины шпона в смежных слоях последовательно смещены на угол 45°.
Буквы э, м, т и о определяют назначение материала:
- э — для изготовления конструкционных и электроизоляционных деталей аппаратуры высокого напряжения, электрических машин, трансформаторов, ртутных выпрямителей и т. п.
- м — как самосмазывающий антифрикционный материал, материал в качестве ползунов лесопильных рам и других аналогичных деталей
- т — для изготовления деталей машин текстильной промышленности
- о — как конструкционный и антифрикционный материал.
Размеры
Древесные слоистые пластики изготовляют прямоугольной формы в виде листов толщиной менее 15 мм и плит толщиной 15—60 мм, длиной 700—5600 мм, шириной 950—1500 мм.
Свойства
- Плотность — 1,3 г/см³
- Предел прочности:
- при сжатии — 100—180 МПа
- при растяжении — 140—280 МПа
- при изгибе — 150—280 МПа
- Прочность при скалывании по шву — 11—15 МПа
- Ударная вязкость — 25—80 кДж/м²
- Твердость по Бринеллю — 250 МПа
- Водопоглощение за 24 ч — 5—15 %
- Электрическая прочность:
- поперек слоев — 26—32 МВ/м
- вдоль слоев — 3—13 МВ/м
Древесно-слоистые пластики стойки в трансформаторном масле, уксусном альдегиде, моторном топливе, бутаноле, стироле; нестойки в окислителях, сильных кислотах и щелочах. Перерабатывают в изделия механической обработкой на обычных станках со специальными инструментами.
Технологический процесс изготовления
Получают последовательно пропиткой шпона толщиной 0,3—0,8 мм лиственных пород древесины (обычно березы) фенолоформальдегидной смолой или крезолоформальдегидной смолой в открытых ваннах или автоклавах (0,4—0,8 МПа), сушкой при ступенчатом нагревании до 90 °С, сборкой полученных препрегов в пакеты и прессованием их на этажных прессах (до 20 МПа, 150 °С) и обрезкой в размер.
Примечания
- ↑ ГОСТ 13913-78 «Пластики древесные слоистые (ДСП). Технические условия»
См. также
Литература
- Химический энциклопедический словарь. — М.: Советская энциклопедия, 1983. — 792 с.
- Шейдин И. А., Пюдик П. Э. Технология производства древесных пластиков и их применение. — М., 1971.
- Баженов В. А., Карасев Е. И., Мерсов Е. Д. Технология и оборудование производства древесных плит и пластиков. — М., 1980.
- И. А. Шулепов, Ю. Г. Доронин. Древесные слоистые пластики. — М.: Лесная промышленность, 1987.
- ГОСТ 13913-78 «Пластики древесные слоистые. Технические условия».
- ГОСТ 20966-75 «Пластик древесный слоистый марки ДСП-Б-а. Технические условия».
Ссылки
wikipedia.green
Древесно-слоистый пластик - это... Что такое Древесно-слоистый пластик?
Не путать с «Древесно-стружечной плитой», которую также иногда упрощённо обозначают аббревиатурой ДСП, хотя для древесно-стружечных плит имеется своя аббревиатура ДСтП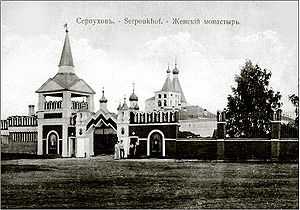
Древе́сно-слои́стый пла́стик (ДСП) — материал, представляющий собой древесно-полимерный композит, изготавливаемый из листов лущеного шпона (берёзы и других пород, толщиной 0,35-0,65 мм, влажностью 6-10 %), склеенных синтетическими смолами резольного типа под давлением и температурой [1].
Области применения
Антифрикционные свойства, стойкость к воздействию агрессивных сред, абразивов; стабильность при сверхнизких температурах (-270 С°), механическая прочность, водостойкость, диэлектрические свойства позволяют применять ДСП в различных областях техники, таких как:
- Узлы трения
- Зубчатые колеса
- Закрытые и открытые металло-полимерные зубчатые передачи
- Вкладыши подшипников скольжения
- Для изготовления пуленепробиваемых дверей, банковского оборудования
- Криогенная и космическая техника
- В судостроительной промышленности
- для изготовления дейдвудных подшипников гребных валов
- Для изготовления затворов гидротехнических сооружений
- В авиационной технике
- лопасти
- винты вертолетов
- В транспортном машиностроении
- В строительстве
- В электротехнической промышленности для изготовления изоляторов, деталей трансформаторов высокого напряжения, выпрямителей (заменяет стеклопластик, текстолит и гетинакс).
- Для изготовления деталей машин текстильной промышленности
- Как самосмазывающий антифрикционный материал, материал в качестве ползунов лесопильных рам и других аналогичных деталей
- В металлургическом оборудовании
- В горнодобывающем оборудовании
Марки ДСП
В зависимости от расположения волокон древесины шпона в смежных слоях и назначения древесные слоистые пластики изготовляют следующих марок:
ДСП-А;
ДСП-Б; ДСП-Б-э; ДСП-Б-м; ДСП-Б-т; ДСП-Б-о;
ДСП-В; ДСП-В-э; ДСП-В-м;
ДСП-Г; ДСП-Г-м.
Буквы А, Б, В, Г указывают порядок укладки шпона в пластике.
А — волокна древесины шпона во всех слоях имеют параллельное направление или каждые 4 слоя с параллельным направлением волокон древесины шпона чередуются с одним слоем, имеющим направление волокон под углом 20-25° к смежным слоям.
Б — каждые 8-12 слоев шпона с параллельным направлением волокон древесины шпона чередуются с одним слоем, имеющим перпендикулярное направление волокон древесины к смежным слоям.
В — волокна древесины шпона в смежных слоях взаимно перпендикулярны.
Г — волокна древесины шпона в смежных слоях последовательно смещены на угол 45°.
Буквы э, м, т, о определяют назначение материала.
э — для изготовления конструкционных и электроизоляционных деталей аппаратуры высокого напряжения, электрических машин, трансформаторов, ртутных выпрямителей и т. п.
м — как самосмазывающий антифрикционный материал, материал в качестве ползунов лесопильных рам и других аналогичных деталей
о — как конструкционный и антифрикционный материал.
Размеры
Древесные слоистые пластики изготовляют прямоугольной формы в виде листов толщиной менее 15 мм и плит толщиной от 15 до 60 мм. Длиной от 700 до 5600 мм, шириной от 950 до 1500 мм.
Свойства
Плотность | 1,3 г/см3, |
предел прочности при сжатии | 100—180 МПа, |
предел прочности при растяжении | 140—280 МПа |
предел прочности при изгибе | 150—280 МПа |
прочность при скалывании по шву | 11—15 МПа |
ударная вязкость | 25—80 кДж/м2 |
твердость по Бринеллю | 250 МПа |
водопоглощение за 24 ч | 5—15 % |
электрическая прочность поперек слоев | 26—32 МВ/м |
электрическая прочность вдоль слоев | 3—13 МВ/м |
Древесно-слоистые пластики стойки в трансформаторном масле, уксусном альдегиде, моторном топливе, бутаноле, стироле; нестойки в окислителях, сильных кислотах и щелочах. Перерабатывают в изделия механической обработкой на обычных станках со специальными инструментами.
Технологический процесс изготовления
Получают последовательно пропиткой шпона толщиной 0,3—0,8 мм лиственных пород древесины (обычно березы) фенолоформальдегидной смолой или крезолоформальдегидной смолой в открытых ваннах или автоклавах (0,4—0,8 МПа), сушкой при ступенчатом нагревании до 90 °С, сборкой полученных препрегов в пакеты и прессованием их на этажных прессах (до 20 МПа, 150 °С) и обрезкой в размер.
Нормативные документы на древесные слоистые пластики
- ГОСТ 13913-78 Пластики древесные слоистые. Технические условия
- ГОСТ 20966-75 Пластик древесный слоистый марки ДСП-Б-а. Технические условия
Литература
- Шейдин И. А., Пюдик П. Э., Технология производства древесных пластиков и их применение, М., 1971
- Баженов В. А., Карасев Е. И., Мерсов Е. Д., Технология и оборудование производства древесных плит и пластиков, М., 1980
- И. А. Шулепов, Ю. Г. Доронин, Древесные слоистые пластики. — М.: Лесная промышленность, 1987.
См. также
Примечания
- ↑ ГОСТ 13913-78 Пластики древесные слоистые (ДСП). Технические условия
Ссылки
Химический Энциклопедический Словарь. Гл. ред. И. Л. Кнунянц. — М.: Советская энциклопедия, 1983—792 с.
dic.academic.ru
Древесные слоистые пластики (ДСП) - Справочник
В строительстве часто нужны материалы, обладающие строением фанеры, но намного превосходящие её физическими свойствами. И такие материалы есть ― это бакелитовая фанера и целый ряд древесно-слоистых пластиков (ДСП). Не следует путать их с древесно-стружечными плитами, имеющими в написании одинаковую аббревиатуру ― ДСП, так как строение и свойства их абсолютно разные.
Технология изготовления древесно-слоистых пластиков
Их можно назвать композитными древеснополимерными материалами, главными компонентами которых являются древесина и термореактивные смолы. Термореактивные смолы ― искусственные вещества, которые при нагреве и повышенном давлении теряют эластичность и твердеют. Изготовление состоит из следующих стадий:
- - шпон пропитывается спиртовым раствором смол (возможно с модификаторами, для получения каких-либо дополнительных свойств;
- - пропитанный шпон подсушивается при 65-90°С;
- - из листов шпона собираются пакеты, для получения определённых свойств соседние листы располагают либо перпендикулярно, либо параллельно, либо под углами 30-45-60°;
- - пакет прессуют про давлении до 20 МПа и температуре 145°С;
- - давление и температура снижаются постепенно.
Если пластик имеет толщину до 15 мм, то это ― листовой материал; если толще 15 мм, ― это плита. Плиты из древесно-слоистого пластика могут иметь толщину до 6 см.
Виды древесно-слоистых пластиков
Вообще-то древесно-слоистый пластик делится на два типа:
- цельный, в котором склеивается шпон листами одинаковой длины;
- составной, в котором в одном слое могут быть склеены листы шпона разной длины.
Дальнейшая классификация учитывает эти типы, количество слоёв шпона, направление волокон, некоторые свойства или сферу применения:
- - ДСП-А ― пластик, в котором через каждые четыре слоя с продольными волокнами укладывается один слой шпона с положением волокон под углом 20-25°.
- - ДСП-Б, где через 10-20 продольных слоёв укладывают один поперечный, добиваясь определенных свойств пластика.
- - ДСП-В, в котором продольные и поперечные слои постоянно чередуются.
- - ДСП-Г, волокна которых в смежных листах находятся под 45°.
Если в маркировке после заглавных букв идут прописные, они означают: а ― авиационный; э ― электроизоляционный; м ― антифрикционный; т ― используемый в текстильных машинах.
Применение слоистых пластиков
Прочность их поразительна. Изделия из слоистого пластика используются для производства зубчатых колёс, вкладышей подшипников скольжения, применяются в затворах на гидротехнических сооружениях. Полы в автобусах и винты вертолётов ― это тоже древесный пластик. Как диэлектрик он не заменим в трансформаторах ВН.
Из него изготавливают пуленепробиваемые двери и стены банковских хранилищ, а так как он выдерживает температуру, близкую к абсолютному нулю, то применяется в арктических и антарктических широтах, в криогенной технике и в космосе.
Древесный слоистый пластик можно пилить, строгать, сверлить и т.д., но это не обработка дерева. Ближе эти операции и инструменты для них к обработке цветных металлов.
Уже упоминалось, что такая же аббревиатура у древесностружечной плиты. Её также получают при высоких давлении и температуре, но на её производство идёт не шпон, а стружки, опилки, щепа. В качестве связующего выступают формальдегидные смолы. Плита имеет однородный состав и отличается прочностью. Её не трудно обрабатывать, она хорошо держит гвозди, шурупы, саморезы.
Еще о изделиях на основе лесометериалов:
- Древесно-цементные стройматериалы
- Древесноволокнистые плиты (ДВП)
- Лущеные, строганные и колотые лесоматериалы
- Измельчённая древесина и продукция из неё
- Методы защиты древесины от гниения, возгорания и поражения древогрызущими насекомыми
- Фанера. Виды фанеры и технологии их изготовления
- Все о деревянных домах
загрузка...
www.megastroika.biz
Слоистые пластики: свойства и применение
В системах изоляции сложных устройств и конструкций, к которым предъявляются повышенные эксплуатационные требования, используют специальные композитные материалы. Как правило, это не универсальные, а узкоспециализированные изделия, ориентированные на работу в экстремальных тепловых и влажностных условиях. К таким изоляторам относят следующие слоистые пластики: гетинакс, текстолит, стеклотекстолит, а также их модификации. Благодаря сочетанию прочностных и теплоизоляционных качеств такие композиты могут применяться в ответственных по назначению конструкциях, устройствах и приборах.
Применение слоистых пластиков
Спектр областей использования таких полимеров весьма разнообразен. Это и станкостроение, и авиационная техника, и производственные отрасли, а также строительство и химическая промышленность. Всюду, где требуется использование электротехнической изоляции, применяют материалы такого рода. При этом нельзя говорить об их универсальности. Отмечается широкий диапазон модификаций, в которых представлены слоистые пластики. Применение каждой версии состава ориентируется на конкретную сферу. Например, гетинакс подходит для изготовления недорогих компонентов в электротехнических приборах, а древесно-слоистые материалы благодаря жесткой структуре используются в технических механизмах. Довольно обширна область применения текстолита, которая охватывает и электротехническую промышленность, и нефтехимические комплексы, а также мелкое приборостроение.
Из чего производят слоистые пластики?
Слоистый пластик представляет собой композиционный материал, в основе которого - полимерное связующее вещество. Для укрепления функциональной базы также применяют послойно расположенное армирующее наполнение. Иными словами, слоистые пластики – это комбинация из двух основных компонентов, представленных связующим и наполнителем. В качестве первого ингредиента используются смолы синтетического происхождения. Это могут быть полиэфирные, эпоксидные, феноло-формальдегидные и другие вещества. Также распространено применение полимеров, среди которых - кремнийорганические и фторопластовые материалы. Что касается наполнения, то эту задачу может выполнять традиционное сырье в виде асбестовых и целлюлозных бумажных волокон.
Характеристики слоистых пластиков
В классическом исполнении слоистый пластик представляет собой листовой материал, который укладывается по типу обычных облицовочных панелей. Реже встречаются тканевые разновидности. По толщине листы могут составлять от 0,4 до 50 мм, в зависимости от разновидности и состава изолятора. Также разнообразны размеры по длине и ширине. Стандартная панель стеклотекстолита, к примеру, в среднем имеет параметры 1200х1000 мм. Рабочие качества, которыми обладают слоистые пластики, выражаются способностью выдерживать разные температурные режимы. Опять же, средний коридор для типового пластика такого рода варьируется от -60°С до 120°С. При условии включения дополнительных модификаторов этот диапазон может расширяться.
Свойства стеклотекстолита
Эксплуатационные качества данного пластика определяются его составом, в который входит несколько пластов стеклоткани, склеивающихся по технологии горячего прессования. Связующим в данном случае выступает термореактивный эпоксифенольный компонент. К базовым свойствам, которыми наделяются слоистые пластики этого типа, можно отнести высокую теплостойкость, защищенность от негативных воздействий влажности и механическую прочность. Кроме того, в отличие от многих композитов, стеклотекстолит является экологически безвредным материалом, что расширяет область его применения. Также его привлекательности на рынке способствуют повышенные диэлектрические качества и долговечность.
Свойства гетинакса
Еще одна распространенная вариация слоистого пластика, которая используется в качестве электроизоляционного материала. Рабочие свойства этого композита определяет бумажная основа, обработанная смесью из фенольных или эпоксидных смол.
Данный пластик не может похвастаться сочетанием таких качеств, как механическая стойкость и способность справляться с экстремальными температурами. Тем не менее податливая в плане обработки основа позволяет формировать печатные платы любых размеров. Кроме того, это самые дешевые слоистые пластики, что и обусловило их широкое распространение в приборостроении. Из такого материала, в частности, выпускают штампованные компоненты для технического обеспечения низковольтной бытовой аппаратуры.
Свойства текстолита
Материал формируется из хлопчатобумажных тканей посредством горячего прессования с добавлением термореактивных связующих фенолформальдегидной группы. Именно применение тканевой основы обеспечило текстолиту высокую прочность при сжатии, а также ударную вязкость. Основа легко поддается обработке путем сверления, резке и штамповке. Это качество материала обусловило его применение в производстве технологических элементов, которые пребывают под действием электрических и механических нагрузок.
При этом существует несколько категорий, на которые разделяются товарные слоистые пластики. Свойства первой категории выражаются в виде повышенной электрической изоляции, что позволяет применять материал и в воздушной среде, и в трансформаторном масле. Вторая категория отличается повышенными механическими качествами, поэтому из пластика этой группы чаще изготавливают детали, на которые оказываются физические нагрузки. Существуют и специальные модификации текстолита, рассчитанные на применение в условиях повышенных температур.
Свойства древесно-слоистых пластиков
Главным конструкционным отличием изоляционных материалов этого типа является использование в качестве наполнителя древесной основы. В частности, композит дополняется листами лущеного шпона толщиной порядка 0,3-0,6 мм. С полимерами природный материал связывается посредством резольных синтетических смол. В итоге комбинированный материал обретает улучшенные антифрикционные свойства, устойчивость к агрессивным средам и даже абразивам, которым не могут противостоять другие слоистые пластики.
Свойства, применение и эксплуатационные требования в данном случае обуславливаются сочетанием целого комплекса характеристик. Выражаются рабочие качества материала не только физической защищенностью, но и влагостойкостью, диэлектрическими качествами, а также сохранением стабильности при сверхнизкой температуре на уровне -250 °С. Что касается использования, то древесно-слоистые материалы успешно интегрируются в механизмы узлов трения, подшипники скольжения, гидротехнические затворы и другие технические системы.
Заключение
Современные композиты изначально разрабатывались с целью получения высокопрочных материалов, которые могли бы заменить некоторые металлические сплавы. В итоге строительная сфера смогла обрести альтернативу традиционной арматуре в виде стеклопластиковых стержней. В свою очередь, слоистые пластики стали неплохой заменой традиционным изоляторам. Они не используются там, где принято укладывать минеральную вату или пробковые панели, но специализированные ниши, в которых недостаточно характеристик обычных средств такого типа, активно осваивают новые слоистые полимеры. Впрочем, не исключено и будущее вхождение таких изоляторов в сегмент бытового использования. Во всяком случае, экологическая безвредность стеклотекстолита этому может поспособствовать.
fb.ru
ДСП - древесно-слоистый пластик
Древе́сно-слои́стый пластик (ДСП) — материал, представляющий собой древесно-полимерный композит, изготавливаемый из листов лущеного шпона (берёзы и других пород, толщиной 0,35-0,65 мм, влажностью 6-10 %), склеенных синтетическими смолами резольного типа под давлением и температурой [1]. Производство древесного слоистого пластика аналогично производству фанеры с той только разницей, что все слои шпона пропитываются крезол- или феноло-формальдегидной смолой.
Пропитка пакетов шпона осуществляется путем их погружения в ванну или в автоклавах под давлением, для чего листы шпона предварительно помещают в специальные кассеты или контейнеры так, чтобы направление волокон было вертикальным. Существует также способ нанесения концентрированной смолы горячими вальцами на горячий, нагретый до 1200С, шпон, который затем выдерживается в течение 20 мин для лучшего проникновения смолы. Содержание смолы должно составлять 16...24 %.
Пропитанный шпон сушат в камерах периодического действия или конвейерных сушилках при температуре не более 75 °С до влажности 3...7 % с целью удаления летучих веществ из смолы и шпона. Смола должна высохнуть, но не отвердеть. В настоящее время созданы линии, на которых операции пропитки и сушки шпона совмещены.
Пропитанные и высушенные листы шпона собирают в пакеты по определенной схеме, зависящей от видов ДСП.
Области применения[править исходный текст]
Антифрикционные свойства, стойкость к воздействию агрессивных сред, абразивов; стабильность при сверхнизких температурах (-270 С°), механическая прочность, водостойкость, диэлектрические свойства позволяют применять ДСП в различных областях техники, таких как:
Узлы трения.
Зубчатые колеса.
Закрытые и открытые металло-полимерные зубчатые передачи.
Вкладыши подшипников скольжения.
Для изготовления пуленепробиваемых дверей, банковского оборудования.
Криогенная и космическая техника.
В судостроительной промышленности:
для изготовления дейдвудных подшипников гребных валов.
Для изготовления затворов гидротехнических сооружений.
В авиационной технике:
лопасти;
винты вертолётов.
В транспортном машиностроении:
настил полов в автобусах, троллейбусах, трамваях;
направляющие эскалаторов метрополитена.
В строительстве.
В электротехнической промышленности для изготовления изоляторов, деталей трансформаторов высокого напряжения, выпрямителей (заменяет стеклопластик, текстолит и гетинакс).
Для изготовления деталей машин текстильной промышленности.
Как самосмазывающий антифрикционный материал, материал в качестве ползунов лесопильных рам и других аналогичных деталей.
В металлургическом оборудовании.
В горнодобывающем оборудовании.
Марки ДСП[править исходный текст]
В зависимости от расположения волокон древесины шпона в смежных слоях и назначения древесные слоистые пластики изготовляют следующих марок:
ДСП-А;
ДСП-Б; ДСП-Б-э; ДСП-Б-м; ДСП-Б-т; ДСП-Б-о;
ДСП-В; ДСП-В-э; ДСП-В-м;
ДСП-Г; ДСП-Г-м.
Буквы А, Б, В, Г указывают порядок укладки шпона в пластике.
А — волокна древесины шпона во всех слоях имеют параллельное направление или каждые 4 слоя с параллельным направлением волокон древесины шпона чередуются с одним слоем, имеющим направление волокон под углом 20-25° к смежным слоям.
Б — каждые 8-12 слоев шпона с параллельным направлением волокон древесины шпона чередуются с одним слоем, имеющим перпендикулярное направление волокон древесины к смежным слоям.
В — волокна древесины шпона в смежных слоях взаимно перпендикулярны.
Г — волокна древесины шпона в смежных слоях последовательно смещены на угол 45°.
Буквы э, м, т, о определяют назначение материала.
э — для изготовления конструкционных и электроизоляционных деталей аппаратуры высокого напряжения, электрических машин, трансформаторов, ртутных выпрямителей и т. п.
м — как самосмазывающий антифрикционный материал, материал в качестве ползунов лесопильных рам и других аналогичных деталей
т — для изготовления деталей машин текстильной промышленности
о — как конструкционный и антифрикционный материал.
Размеры[править исходный текст]
Древесные слоистые пластики изготовляют прямоугольной формы в виде листов толщиной менее 15 мм и плит толщиной от 15 до 60 мм. Длиной от 700 до 5600 мм, шириной от 950 до 1500 мм.
Свойства
Свойство Значение
Плотность 1,3 г/см3,
предел прочности при сжатии 100—180 МПа,
предел прочности при растяжении 140—280 МПа
предел прочности при изгибе 150—280 МПа
прочность при скалывании по шву 11—15 МПа
ударная вязкость 25—80 кДж/м2
твердость по Бринеллю 250 МПа
водопоглощение за 24 ч 5—15 %
электрическая прочность поперек слоев 26—32 МВ/м
электрическая прочность вдоль слоев 3—13 МВ/м
Древесно-слоистые пластики стойки в трансформаторном масле, уксусном альдегиде, моторном топливе, бутаноле, стироле; нестойки в окислителях, сильных кислотах и щелочах. Перерабатывают в изделия механической обработкой на обычных станках со специальными инструментами.
Технологический процесс изготовления[править исходный текст]
Получают последовательно пропиткой шпона толщиной 0,3—0,8 мм лиственных пород древесины (обычно березы) фенолоформальдегидной смолой или крезолоформальдегидной смолой в открытых ваннах или автоклавах (0,4—0,8 МПа), сушкой при ступенчатом нагревании до 90 °С, сборкой полученных препрегов в пакеты и прессованием их на этажных прессах (до 20 МПа, 150 °С) и обрезкой в размер.
studfiles.net
Секреты древесно-пластикового композита или как сделать дерево жидким
К сожалению, всем нам известный и столь распространенный во всем мире пластик содержит вредные для здоровья человека вещества. Более того, в его производстве используются нефтепродукты. Однако до недавнего времени альтернативы этому дешевому материалу фактически не было. Конечно, новые конструкционные материалы появляются постоянно. Это клееная фанера, древесностружечные и древесноволокнистые плиты. Есть свои новинки и в бетонной индустрии, металлургии, стекольной промышленности. Тем не менее, по стоимости, а, значит, и доступности им все-таки далековато до пластика.
Вначале нового тысячелетия ученым удалось создать принципиально новый конструкционный материал, который в ближайшие десятилетия может практически полностью заменить привычный пластик. Это термопластичный древесно-полимерный композит (ДПКТ или ДПК), а в простонародье – «жидкое дерево». В его производстве используются первичное (вторичное) сырье ПП, ПЭ или ПВХ плюс древесные добавки (древесная мука, прочие растительные волокна) и вспомогательные присадки. Эффект превзошел все ожидания. Новейший материал не только экологичен (содержание серы сокращено на 90%), но и, сочетая в себе лучшие свойства дерева и пластмассы, сохранил относительно низкую себестоимость.
По оценкам экспертов, ежегодный рост продаж ДПК в мире составляет около 20%. Так что же это за чудо, которого так долго ждали архитекторы, конструкторы и производственники? Попробуем разобраться.
Применение и обработка
Благодаря своим свойствам древесно-полимерный композит отлично применяется в самых различных областях. Материалы отличаются однородностью и гладкостью поверхности, пластичностью, стойки к атмосферному и биологическому воздействию, а срок эксплуатации даже в жестких уличных условиях достигает 50 лет.
Всё это позволяет использовать ДПК в производстве различных архитектурных и строительных материалов: плинтусов, вагонки, подоконников, профилей, декоративных элементов, а также наполнителей.
Изготавливают из ДПК и готовые к использованию изделия: ламинат, напольные покрытия, мебельные листы, мебель, кабельные коробки, многокамерные оконные профили и даже декинг – профиль для изготовления причалов и пирсов.
Физико-механические свойства древесно-полимерного композита предоставляют широкие возможности для его обработки. Материал не теряет своей формы и прочности, приняв в себя до 4% влаги. Из него можно изготавливать облегченные, пустотелые вещи. Монтируется он как с помощью гвоздей и шурупов, так и на специальные защелки.
А ещё, ДПК можно фанеровать шпоном, ламинировать пленками и листовыми пластиками, красить любыми красками и лаками, получать различные декоративные эффекты, добавляя пигменты в композицию и пр.
Полученные из ДПК изделия легко поддаются механической обработке. Они легко пилятся, сверлятся, режутся, клеятся, свариваются друг с другом, гнутся (после предварительного нагрева горелкой), а, если в состав материала добавлена мука из мягких пород дерева или целлюлозосодержащие отходы, то это придает изделию ещё и повышенную пластичность.
Наконец, ДПК, помимо эстетичности, который ему придает внешний вид, приятен и для обоняния, обладая легким древесным запахом.
Технология производства
Для изготовления древесно-полимерного композита используется ряд компонентов. В первую очередь это, конечно, измельченное древесное или целлюлозосодержащее сырье. То есть это может быть не только древесина, но и кукуруза, рис, соя, солома, бумага, опилки и пр. Второй основной составляющей ДПК являются синтетические связующие. К ним относятся: полиэтилен, пропилен ПВХ и др. Остальные компоненты – это дополнительные добавки, состав которых варьируется в зависимости от предназначения будущего изделия. К наиболее распространенным относятся: красители, пигменты, антиоксиданты, противоударные модификаторы, свето- и термостабилизаторы, антипирены и антисептики для защиты от огня и гниения, гидрофобные добавки для устойчивы к сырости, вспенивающие агенты для снижения плотности ДПК.
Объем древесных частиц в материале может составлять от 30 до 70%, а их размер от 0,7 до 1,5 мм. Тонкие фракции используются в производстве готовых профилей, не требующих дополнительной обработки поверхности. Средние подходят под покраску или отделку шпоном. Грубые – для технических целей.
Объем синтетических связующих также варьируется и может составлять от 2 до 55%. Зависит это опять же от предназначения будущего изделия. Что касается дополнительных добавок, то их объем в материале не превышает 15%.
Кстати, не так давно немецким разработчикам удалось изготовить «жидкое дерево» идеального качества. Специалисты института Фраунгофера создали его из лигнина. Этот материал получают из древесины. ДПК под названием Arboform является абсолютно не токсичным продуктом. Более того, если обычный древесно-полимерный композит можно перерабатывать 3-4 раза, то этот до 10 раз. К чему мы это? Дело в том, что в Китае индустрия по производству ДПК разрастается как нигде в мире. И, если в Европе и США созданные материалы проходят серию тестирований, то в Поднебесной себя этим не утруждают и поставляют на рынок, в том числе международный, продукт не самого лучшего качества.
Теперь об оборудовании для производства ДПК. В его стандартный состав входят: экструдер двухшнековый, фильера формовки, стол калибрации и охлаждения, тянущее устройство, отрезное устройство по длине, деление по ширине (при необходимости) и укладчик. Вся линия отличается компактностью, а управление ей, обычно, полностью автоматизировано. В комплектации некоторых моделей присутствуют также: мельница (измельчитель сырья) автозагрузчик сырья, и смеситель.
Производителями таких линий и модулей являются в основном китайские компании. Лидеры среди них – WPC, Zhangjiagang City Boxin Machinery и др. Качество техники достойного уровня, тем более, что основные узлы для них производятся европейскими машиностроительными заводами.
Владислав Пермин, специально для Equipnet.ru
www.equipnet.ru
Древесно-слоистый пластик — WiKi
Древесно-слоистый пластик (ДСП) Не путать с «Древесно-стружечной плитой», которую также иногда упрощённо обозначают аббревиатурой ДСП, хотя для древесно-стружечных плит имеется своя аббревиатура — ДСтПДреве́сно-слои́стый пластик (ДСП) (бакелитовая фанера, дельта-древесина) — материал, представляющий собой древесно-полимерный композит, изготавливаемый из листов лущеного шпона (берёзы и других пород, толщиной 0,35—0,65 мм, влажностью 6—10 %), склеенных синтетическими смолами резольного типа под давлением и температурой[1].
Области применения
Антифрикционные свойства, стойкость к воздействию агрессивных сред, абразивов; стабильность при сверхнизких температурах (–270 °С), механическая прочность, водостойкость, диэлектрические свойства позволяют применять ДСП в различных областях техники, таких как:
- Узлы трения.
- Зубчатые колеса.
- Закрытые и открытые металло-полимерные зубчатые передачи.
- Вкладыши подшипников скольжения.
- Для изготовления пуленепробиваемых дверей, банковского оборудования.
- Криогенная и космическая техника.
- В судостроительной промышленности для изготовления дейдвудных подшипников гребных валов.
- Для изготовления затворов гидротехнических сооружений.
- В авиационной технике лопасти; винты вертолётов.
- В транспортном машиностроении: настил полов в автобусах, троллейбусах, трамваях; направляющие эскалаторов метрополитена.
- В строительстве.
- В электротехнической промышленности для изготовления изоляторов, деталей трансформаторов высокого напряжения, выпрямителей (заменяет стеклопластик, текстолит и гетинакс).
- Для изготовления деталей машин текстильной промышленности.
- Как самосмазывающий антифрикционный материал, материал в качестве ползунов лесопильных рам и других аналогичных деталей.
- В металлургическом оборудовании.
- В горнодобывающем оборудовании.
Марки ДСП
В зависимости от расположения волокон древесины шпона в смежных слоях и назначения древесные слоистые в России пластики изготовляют следующих марок:
- ДСП-А;
- ДСП-Б; ДСП-Б-э; ДСП-Б-м; ДСП-Б-т; ДСП-Б-о;
- ДСП-В; ДСП-В-э; ДСП-В-м;
- ДСП-Г; ДСП-Г-м.
Буквы А, Б, В, Г указывают порядок укладки шпона в пластике:
- А — волокна древесины шпона во всех слоях имеют параллельное направление или каждые 4 слоя с параллельным направлением волокон древесины шпона чередуются с одним слоем, имеющим направление волокон под углом 20—25° к смежным слоям.
- Б — каждые 8—12 слоев шпона с параллельным направлением волокон древесины шпона чередуются с одним слоем, имеющим перпендикулярное направление волокон древесины к смежным слоям.
- В — волокна древесины шпона в смежных слоях взаимно перпендикулярны.
- Г — волокна древесины шпона в смежных слоях последовательно смещены на угол 45°.
Буквы э, м, т и о определяют назначение материала:
- э — для изготовления конструкционных и электроизоляционных деталей аппаратуры высокого напряжения, электрических машин, трансформаторов, ртутных выпрямителей и т. п.
- м — как самосмазывающий антифрикционный материал, материал в качестве ползунов лесопильных рам и других аналогичных деталей
- т — для изготовления деталей машин текстильной промышленности
- о — как конструкционный и антифрикционный материал.
Размеры
Древесные слоистые пластики изготовляют прямоугольной формы в виде листов толщиной менее 15 мм и плит толщиной 15—60 мм, длиной 700—5600 мм, шириной 950—1500 мм.
Свойства
- Плотность — 1,3 г/см³
- Предел прочности:
- при сжатии — 100—180 МПа
- при растяжении — 140—280 МПа
- при изгибе — 150—280 МПа
- Прочность при скалывании по шву — 11—15 МПа
- Ударная вязкость — 25—80 кДж/м²
- Твердость по Бринеллю — 250 МПа
- Водопоглощение за 24 ч — 5—15 %
- Электрическая прочность:
- поперек слоев — 26—32 МВ/м
- вдоль слоев — 3—13 МВ/м
Древесно-слоистые пластики стойки в трансформаторном масле, уксусном альдегиде, моторном топливе, бутаноле, стироле; нестойки в окислителях, сильных кислотах и щелочах. Перерабатывают в изделия механической обработкой на обычных станках со специальными инструментами.
Технологический процесс изготовления
Получают последовательно пропиткой шпона толщиной 0,3—0,8 мм лиственных пород древесины (обычно березы) фенолоформальдегидной смолой или крезолоформальдегидной смолой в открытых ваннах или автоклавах (0,4—0,8 МПа), сушкой при ступенчатом нагревании до 90 °С, сборкой полученных препрегов в пакеты и прессованием их на этажных прессах (до 20 МПа, 150 °С) и обрезкой в размер.
Примечания
- ↑ ГОСТ 13913-78 «Пластики древесные слоистые (ДСП). Технические условия»
См. также
Литература
- Химический энциклопедический словарь. — М.: Советская энциклопедия, 1983. — 792 с.
- Шейдин И. А., Пюдик П. Э. Технология производства древесных пластиков и их применение. — М., 1971.
- Баженов В. А., Карасев Е. И., Мерсов Е. Д. Технология и оборудование производства древесных плит и пластиков. — М., 1980.
- И. А. Шулепов, Ю. Г. Доронин. Древесные слоистые пластики. — М.: Лесная промышленность, 1987.
- ГОСТ 13913-78 «Пластики древесные слоистые. Технические условия».
- ГОСТ 20966-75 «Пластик древесный слоистый марки ДСП-Б-а. Технические условия».
Ссылки
ru-wiki.org